橡胶加工工艺学
硅橡胶结构性能与加工工艺

硅橡胶结构性能与加工工艺硅橡胶是一种用途广泛的高性能弹性材料,由于其优良的耐高温性能、耐化学品腐蚀性能以及优异的电绝缘性能,使其在许多工业领域有着重要的应用。
本文将对硅橡胶的结构、性能以及加工工艺进行详细介绍。
一、硅橡胶的结构硅橡胶是由硅原子(Si)和氧原子(O)交替排列形成的链状结构。
其中硅原子的每个价电子与一个有机基团相连,通常选择甲基基团(CH3),这样就形成了亚甲基硅氧链。
硅橡胶的结构可以分为两种形式:直链型和交联型。
直链型硅橡胶中,硅氧链上的甲基基团较少,因此具有较高的流动性和可塑性,适用于注塑和挤出成型等加工工艺。
交联型硅橡胶中,硅氧链上的甲基基团交联成三维网络结构,使得硅橡胶具有良好的弹性和耐用性。
二、硅橡胶的性能1.耐高温性能:硅橡胶具有出色的耐高温性能,可在-60℃至+230℃的温度范围内保持其弹性和可塑性,适用于高温环境下的密封和绝缘材料。
2.耐化学品腐蚀性能:硅橡胶具有良好的耐化学品腐蚀性能,能够抵御酸、碱、溶剂等多种化学物质的侵蚀。
3.电绝缘性能:硅橡胶具有优异的电绝缘性能,能够有效隔离电流和防止电击。
4.耐候性能:硅橡胶具有较好的耐候性能,可长时间暴露在户外环境下而不受到损伤。
5.低温弹性:硅橡胶在低温下仍能保持良好的弹性,不易变脆。
三、硅橡胶的加工工艺硅橡胶的加工工艺主要包括热压成型、挤出成型、注塑成型以及涂覆成型等。
1.热压成型:将硅橡胶原料加热到一定温度,然后放入热压机中,在一定的温度和压力下进行成型。
热压成型适用于制造硅橡胶板材或异形件。
2.挤出成型:将硅橡胶颗粒放入挤出机中,在高温和高压下挤出成型。
挤出成型适用于制造硅橡胶管、线和条形材料等。
3.注塑成型:将硅橡胶颗粒装入注塑机中,加热熔化后注入模具中进行成型。
注塑成型适用于制造硅橡胶零件和产品。
4.涂覆成型:将硅橡胶原料薄涂在基材上,再进行固化和剪切成型。
涂覆成型适用于制造硅橡胶薄膜和涂层。
加工硅橡胶时需要注意的一些问题包括:温度控制、成型周期、硫化剂的选择、硅橡胶的配方等。
橡胶的工艺流程
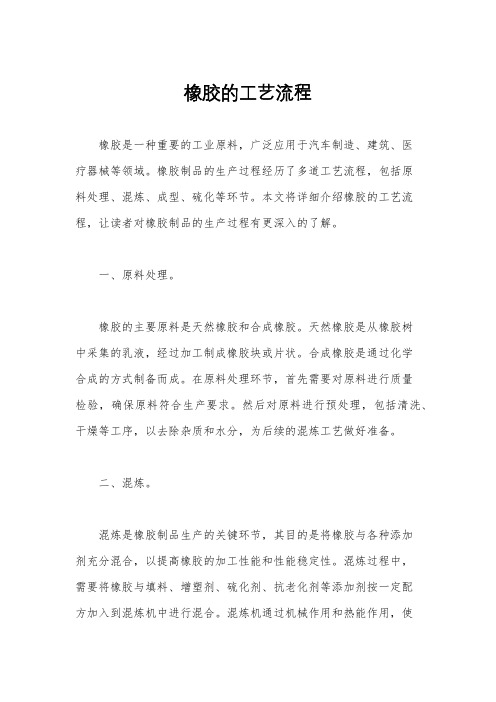
橡胶的工艺流程橡胶是一种重要的工业原料,广泛应用于汽车制造、建筑、医疗器械等领域。
橡胶制品的生产过程经历了多道工艺流程,包括原料处理、混炼、成型、硫化等环节。
本文将详细介绍橡胶的工艺流程,让读者对橡胶制品的生产过程有更深入的了解。
一、原料处理。
橡胶的主要原料是天然橡胶和合成橡胶。
天然橡胶是从橡胶树中采集的乳液,经过加工制成橡胶块或片状。
合成橡胶是通过化学合成的方式制备而成。
在原料处理环节,首先需要对原料进行质量检验,确保原料符合生产要求。
然后对原料进行预处理,包括清洗、干燥等工序,以去除杂质和水分,为后续的混炼工艺做好准备。
二、混炼。
混炼是橡胶制品生产的关键环节,其目的是将橡胶与各种添加剂充分混合,以提高橡胶的加工性能和性能稳定性。
混炼过程中,需要将橡胶与填料、增塑剂、硫化剂、抗老化剂等添加剂按一定配方加入到混炼机中进行混合。
混炼机通过机械作用和热能作用,使各种添加剂均匀分散在橡胶中,形成均匀的橡胶混合料。
三、成型。
混炼后的橡胶混合料需要进行成型,以得到所需的橡胶制品。
成型过程根据不同的制品要求,可以采用压延、挤出、注塑等不同的成型方法。
在成型过程中,需要根据产品的形状和尺寸,选择合适的模具和成型设备,将橡胶混合料加工成所需的形状,如轮胎、密封圈、橡胶管等。
四、硫化。
硫化是橡胶制品生产中的重要工艺环节,通过硫化可以使橡胶获得良好的物理性能和耐热耐老化性能。
硫化过程是将成型后的橡胶制品放入硫化炉中,加热并加入硫化剂,使橡胶分子间发生交联反应,从而增强橡胶的强度和弹性。
硫化时间和温度根据不同的橡胶制品和硫化体系有所不同,需要根据实际情况进行调整。
五、检验与包装。
最后,经过硫化的橡胶制品需要进行质量检验,包括外观质量、尺寸精度、物理性能等方面的检测。
合格的橡胶制品经过检验后,将进行包装和存储,待出厂销售或使用。
总结,橡胶制品的生产过程经历了原料处理、混炼、成型、硫化等多道工艺流程,每道工艺环节都对最终产品的质量和性能有着重要的影响。
橡胶板生产工艺

橡胶板生产工艺
橡胶板生产工艺是指将橡胶原材料经过一系列加工工序,制成橡胶板的过程。
橡胶板常用于橡胶制品、汽车垫片、橡胶地板等领域,具有耐磨、耐腐蚀、耐高温等优点。
以下是橡胶板生产的一般工艺流程:
1. 橡胶混炼:橡胶原材料经过粉碎、过筛、称量等工序,与多种辅助剂如硫化剂、促进剂、防老剂等混合,通过混合机械(如橡胶开炼机)进行混炼。
混炼的目的是使橡胶与各种辅助剂充分分散均匀,增加橡胶的可加工性和物理力学性能。
2. 橡胶成型:将混炼好的橡胶料送入橡胶压延机、橡胶挤出机等设备中进行橡胶板的成型。
这些设备通常通过加热和加压的方式,使橡胶料在模具中流动、填充,并在后续冷却硫化时保持所需的形状和尺寸。
3. 橡胶硫化:成型好的橡胶板需要经过硫化工艺,以使橡胶物质发生交联反应,提高橡胶的力学强度和耐磨性。
硫化通常使用高温(约150-180℃)和硫化剂(如硫化钠)进行,时间和温度需要根据橡胶材料的种类和厚度来确定。
4. 表面处理:硫化后的橡胶板通过去除表面毛糙、清洁、修整等工序,以改善橡胶板的外观质量和表面平整度。
5. 检测和质量控制:对成品橡胶板进行检测,如检查尺寸、硬度、抗拉强度、耐磨性等物理力学性能,并根据相关标准对产品质量进行评价和判定。
6. 包装和储存:合格的橡胶板经过包装,如用塑料薄膜封装,以便于保护和储存。
以上是橡胶板生产的一般工艺流程,具体工艺步骤和参数会根据不同的橡胶材料和产品要求而有所不同。
此外,生产过程中还需要注意环保问题,采取相应的措施减少污染物排放和能源消耗,以满足环保要求。
橡胶加工工艺

橡胶的简介
★增塑剂(物理和化学增塑) 目的: 1. 使生胶软化,增加可塑性便于加工,减少动力
消耗; 2. 润湿炭黑等粉状配合剂,提高混炼效果,增加
制品柔软性和耐寒性; 3. 增进胶料的自粘性和粘性。
9
橡胶的简介
★填充剂 补强填充剂提高硫化橡胶的强力,撕裂强度, 定伸强度,耐磨性等物理机械性能。 炭黑、白炭黑、活性陶土、苯乙烯树脂、木质 素等。 惰性填充剂增加胶料体积,节约成本,改善加 工性能。 云母粉、滑石粉、硫酸钡。
3
橡胶的简介
橡胶的作用
橡胶是橡胶工业的重要原料,用以制造轮 胎、胶管、胶带、胶辊等各种橡胶制品。橡胶 还广泛用于电线电缆、纤维和纸加工、石棉以 及塑料改性等方面。世界橡胶耗量中,约80%用 于橡胶工业。在橡胶制品中,轮胎是其典型的 代表性产品,轮胎的用胶量约占全部橡胶耗用 量的50%~70%。
4
橡胶的简介
★硫化剂 硫化剂是一类使橡胶由线形长链分子转变为网状大分子的 物质,这种转变称为硫化。 硫化剂:硫磺、一氯化硫、硒、碲及其氯化物、硝基 化物、有机过氧化物以及某些金属氧化物。
6
橡胶的简介
★硫化促进剂 硫化促进剂可促进橡胶的硫化作用,降低硫化所需温 度,缩短硫化时间,并改善硫化胶的物理机械性能。 硫化促进剂的种类很多。无机类硫化促进剂(如氧化 铅,氧化镁等)硫化效果较差,已被淘汰。目前主要 使用有机类硫化促进剂,
19
橡胶的塑炼和混炼
❖ 混炼示意图
橡胶的塑炼和混炼
❖ 混炼示意图
后辊
前辊
橡胶的塑炼和混炼
❖ 混炼示意图
后辊
前辊
橡胶的塑炼和混炼
后辊
前辊
橡胶的塑炼和混炼
后辊
密封圈等橡胶件的加工工艺
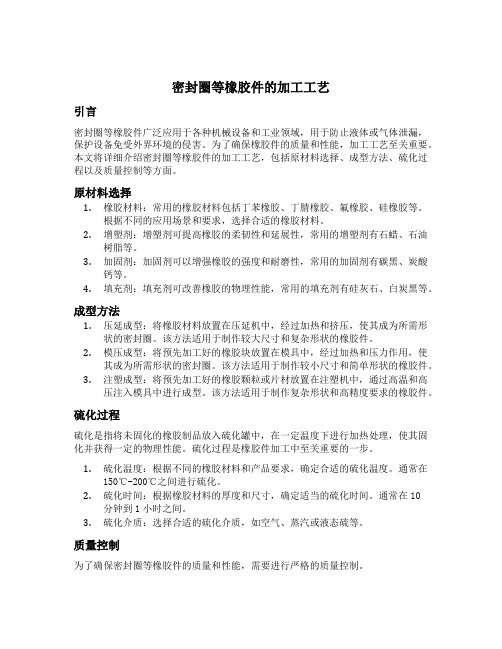
密封圈等橡胶件的加工工艺引言密封圈等橡胶件广泛应用于各种机械设备和工业领域,用于防止液体或气体泄漏,保护设备免受外界环境的侵害。
为了确保橡胶件的质量和性能,加工工艺至关重要。
本文将详细介绍密封圈等橡胶件的加工工艺,包括原材料选择、成型方法、硫化过程以及质量控制等方面。
原材料选择1.橡胶材料:常用的橡胶材料包括丁苯橡胶、丁腈橡胶、氟橡胶、硅橡胶等。
根据不同的应用场景和要求,选择合适的橡胶材料。
2.增塑剂:增塑剂可提高橡胶的柔韧性和延展性,常用的增塑剂有石蜡、石油树脂等。
3.加固剂:加固剂可以增强橡胶的强度和耐磨性,常用的加固剂有碳黑、炭酸钙等。
4.填充剂:填充剂可改善橡胶的物理性能,常用的填充剂有硅灰石、白炭黑等。
成型方法1.压延成型:将橡胶材料放置在压延机中,经过加热和挤压,使其成为所需形状的密封圈。
该方法适用于制作较大尺寸和复杂形状的橡胶件。
2.模压成型:将预先加工好的橡胶块放置在模具中,经过加热和压力作用,使其成为所需形状的密封圈。
该方法适用于制作较小尺寸和简单形状的橡胶件。
3.注塑成型:将预先加工好的橡胶颗粒或片材放置在注塑机中,通过高温和高压注入模具中进行成型。
该方法适用于制作复杂形状和高精度要求的橡胶件。
硫化过程硫化是指将未固化的橡胶制品放入硫化罐中,在一定温度下进行加热处理,使其固化并获得一定的物理性能。
硫化过程是橡胶件加工中至关重要的一步。
1.硫化温度:根据不同的橡胶材料和产品要求,确定合适的硫化温度。
通常在150℃-200℃之间进行硫化。
2.硫化时间:根据橡胶材料的厚度和尺寸,确定适当的硫化时间。
通常在10分钟到1小时之间。
3.硫化介质:选择合适的硫化介质,如空气、蒸汽或液态硫等。
质量控制为了确保密封圈等橡胶件的质量和性能,需要进行严格的质量控制。
1.原材料检验:对采购回来的原材料进行检验,包括外观、密度、拉伸强度等指标。
2.成型工艺控制:严格控制成型工艺参数,如温度、压力、时间等,以确保产品尺寸和形状符合要求。
橡胶生产六大工艺
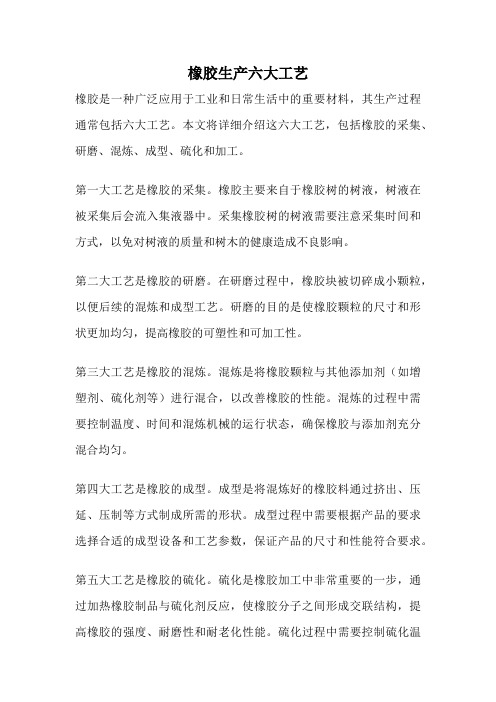
橡胶生产六大工艺橡胶是一种广泛应用于工业和日常生活中的重要材料,其生产过程通常包括六大工艺。
本文将详细介绍这六大工艺,包括橡胶的采集、研磨、混炼、成型、硫化和加工。
第一大工艺是橡胶的采集。
橡胶主要来自于橡胶树的树液,树液在被采集后会流入集液器中。
采集橡胶树的树液需要注意采集时间和方式,以免对树液的质量和树木的健康造成不良影响。
第二大工艺是橡胶的研磨。
在研磨过程中,橡胶块被切碎成小颗粒,以便后续的混炼和成型工艺。
研磨的目的是使橡胶颗粒的尺寸和形状更加均匀,提高橡胶的可塑性和可加工性。
第三大工艺是橡胶的混炼。
混炼是将橡胶颗粒与其他添加剂(如增塑剂、硫化剂等)进行混合,以改善橡胶的性能。
混炼的过程中需要控制温度、时间和混炼机械的运行状态,确保橡胶与添加剂充分混合均匀。
第四大工艺是橡胶的成型。
成型是将混炼好的橡胶料通过挤出、压延、压制等方式制成所需的形状。
成型过程中需要根据产品的要求选择合适的成型设备和工艺参数,保证产品的尺寸和性能符合要求。
第五大工艺是橡胶的硫化。
硫化是橡胶加工中非常重要的一步,通过加热橡胶制品与硫化剂反应,使橡胶分子之间形成交联结构,提高橡胶的强度、耐磨性和耐老化性能。
硫化过程中需要控制硫化温度和时间,以及硫化剂的种类和用量,确保橡胶制品的质量。
最后一大工艺是橡胶的加工。
加工是指对硫化好的橡胶制品进行后续处理,包括修整边角、打磨表面、安装配件等。
加工的目的是使橡胶制品的外观更加美观,尺寸更加精确,以满足客户的需求。
通过以上六大工艺,橡胶从采集到最终成品的过程得以完整实现。
这些工艺相互衔接,每个环节都至关重要,对橡胶制品的质量和性能有着重要影响。
因此,在橡胶生产过程中,需要严格控制每个工艺的参数和操作方法,确保橡胶制品达到设计要求,并具有优良的性能和可靠的质量。
总结起来,橡胶生产的六大工艺包括采集、研磨、混炼、成型、硫化和加工。
这些工艺环环相扣,每个环节都不可或缺。
只有在每个工艺环节都严格把控,才能生产出优质的橡胶制品。
橡胶加工工艺期末复习重点

补强剂是炭黑。
26. 生胶即尚未被交联的橡胶,由线形大分子或者带支链的线性大分子 39. 炭黑按制造方法可分为炉法炭黑、槽法炭黑、热裂解炭黑、新工艺
构成。
炭黑。
27. 生胶随温度的变化有三态,即玻璃态、高弹态和粘流态。
40. 白炭黑的化学成分是二氧化硅,可分为气相法和沉淀法两大类,其
28. 橡胶按来源与用途可分为天然橡胶和合成橡胶两大类。
补强效果次于炭黑。
29. 合成橡胶分为通用合成橡胶和特种合成橡胶两大类。
41. 橡胶发生老化的主要因素有热氧老化、光氧老化、臭氧老化和疲劳
30. 天然橡胶大分子链结构单元是异戊二烯。
老化。
31. 产量最大的一种合成橡胶是丁苯橡胶,其结构单元是苯乙烯和丁二 42. 橡胶的增塑实际上就是增塑剂低分子与橡胶高分子聚合物形成分子
胶为完全饱和性橡胶,不能用硫磺来硫化,必须用过氧化物来硫化。 17. 橡胶配方五大体系:生胶体系、硫化体系、补强填充体系、防护体
5. 丁基橡胶(IIR)由异丁烯与少量异戊二烯单体在低温下共聚而成
系、增塑体系
6. 丁腈橡胶耐气透性良好(有极性的缘故),但电绝缘性不好,属于半导 18. 生胶和混炼胶可塑度的测定通常有三种方法:压缩法、旋转扭力法
51. 化学结构和含硫量能影响硫化特性
污染,保证胶料的混炼质量,将某些配合剂、促进剂等事先以较大比
二、判断题
例与液体软化剂混合制成膏状混合物。
1. 粉末橡胶指粒径在 1 毫米以下的粉末状橡胶。
9. 母炼胶:将在通常混炼条件下短时间内难以混合均匀且混炼生热量多,
三、名词解释
能耗较大的某些配合剂以较大的比例事先与生胶单独混合制成组分比
橡胶或橡胶制品在加工贮存和使用的过程中由于受内外因素的综合作用如热氧臭氧金属离子电离辐射光机械力等使性能逐渐下降以至于最后丧失使用价值这种现象称为橡胶的老化
橡胶加工工艺基础知识
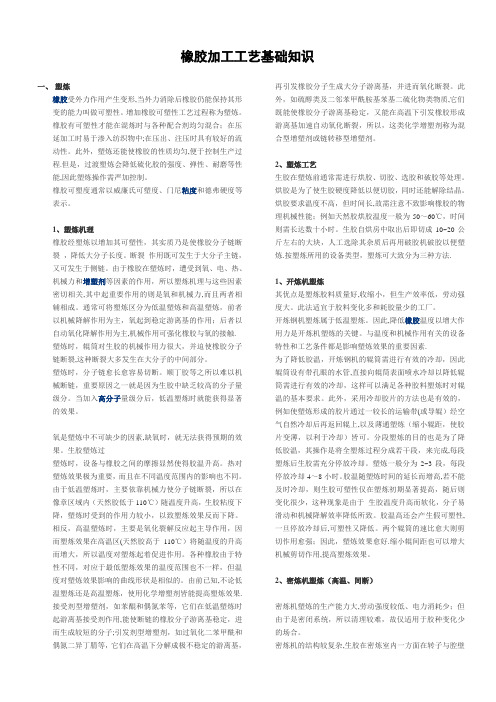
橡胶加工工艺基础知识一、塑炼橡胶受外力作用产生变形,当外力消除后橡胶仍能保持其形变的能力叫做可塑性。
增加橡胶可塑性工艺过程称为塑炼。
橡胶有可塑性才能在混炼时与各种配合剂均匀混合;在压延加工时易于渗入纺织物中;在压出、注压时具有较好的流动性。
此外,塑炼还能使橡胶的性质均匀,便于控制生产过程.但是,过渡塑炼会降低硫化胶的强度、弹性、耐磨等性能,因此塑炼操作需严加控制。
橡胶可塑度通常以威廉氏可塑度、门尼粘度和德弗硬度等表示。
1、塑炼机理橡胶经塑炼以增加其可塑性,其实质乃是使橡胶分子链断裂,降低大分子长度。
断裂作用既可发生于大分子主链,又可发生于侧链。
由于橡胶在塑炼时,遭受到氧、电、热、机械力和增塑剂等因素的作用,所以塑炼机理与这些因素密切相关,其中起重要作用的则是氧和机械力,而且两者相辅相成。
通常可将塑炼区分为低温塑炼和高温塑炼,前者以机械降解作用为主,氧起到稳定游离基的作用;后者以自动氧化降解作用为主,机械作用可强化橡胶与氧的接触.塑炼时,辊筒对生胶的机械作用力很大,并迫使橡胶分子链断裂,这种断裂大多发生在大分子的中间部分。
塑炼时,分子链愈长愈容易切断。
顺丁胶等之所以难以机械断链,重要原因之一就是因为生胶中缺乏较高的分子量级分。
当加入高分子量级分后,低温塑炼时就能获得显著的效果。
氧是塑炼中不可缺少的因素,缺氧时,就无法获得预期的效果。
生胶塑炼过塑炼时,设备与橡胶之间的摩擦显然使得胶温升高。
热对塑炼效果极为重要,而且在不同温度范围内的影响也不同。
由于低温塑炼时,主要依靠机械力使分子链断裂,所以在像章区域内(天然胶低于110℃)随温度升高,生胶粘度下降,塑炼时受到的作用力较小,以致塑炼效果反而下降。
相反,高温塑炼时,主要是氧化裂解反应起主导作用,因而塑炼效果在高温区(天然胶高于110℃)将随温度的升高而增大,所以温度对塑炼起着促进作用。
各种橡胶由于特性不同,对应于最低塑炼效果的温度范围也不一样,但温度对塑炼效果影响的曲线形状是相似的。