硫化曲线教材
硫化曲线t10和t90

硫化曲线t10和t90硫化曲线是用来描述橡胶在硫化过程中的变化规律的一项重要指标。
其中,t10和t90分别表示橡胶硫化过程中10%和90%硫化完成所需的时间。
本文将对硫化曲线中的t10和t90进行详细探讨,旨在帮助读者深入了解橡胶硫化的过程和特点。
1. 硫化曲线简介硫化曲线是通过在一定温度下跟踪记录橡胶硫化过程中的硫化度变化而得到的一条曲线。
它可以帮助我们了解橡胶在硫化过程中的行为和性能变化。
2. t10的意义与描述t10是硫化曲线中的一个重要参数,它表示橡胶硫化过程中10%硫化完成所需的时间。
一般来说,t10的数值越小,说明橡胶硫化速度越快,反之则表示硫化速度较慢。
3. t90的意义与描述t90是硫化曲线中的另一个重要参数,它表示橡胶硫化过程中90%硫化完成所需的时间。
与t10相似,t90的数值越小,说明橡胶硫化速度越快,反之则表示硫化速度较慢。
4. 影响t10和t90的因素橡胶硫化的过程受多种因素的影响,这些因素也会对硫化曲线中的t10和t90产生影响。
主要的影响因素包括硫化剂种类和用量、硫化温度、硫化时间等。
5. t10和t90的应用由于t10和t90可以反映出橡胶硫化速度的快慢,因此在橡胶制品的生产过程中具有重要的应用价值。
生产者可以通过控制硫化剂和硫化条件,合理调整t10和t90的数值,以满足不同用途橡胶制品的要求。
6. 硫化曲线的优化通过优化硫化剂的选择和合理控制硫化条件,可以有效提高硫化曲线中的t10和t90数值,进而改善橡胶制品的性能。
例如,使用高效硫化体系和适当的硫化温度,可在保持硫化速度的同时,避免橡胶材料受到过度硫化而引起的性能变化。
7. 硫化曲线的测试方法硫化曲线的测试是通过在实验室中使用硫化仪进行的。
根据硫化曲线测试结果,可以计算得到t10和t90的数值,进而进行相关的分析和判断。
总结:硫化曲线中的t10和t90是描述橡胶硫化过程的重要指标,通过对其数值的分析和研究,可以帮助我们更好地了解橡胶硫化的过程和特点。
硫化曲线教材

硫化曲线教材Company number:【0089WT-8898YT-W8CCB-BUUT-202108】硫变仪以及硫化曲线的介绍------ 硫变仪原理简介、硫化曲线解读(教材)1. 硫化的定义及示意图:图:高分子链的支化与交联示意图(a)无规支化高分子;(b)梳形高分子;(c)星形高分子;(d)交联网络2. 定义:橡胶硫化测试仪,简称为硫变仪,是指在橡胶硫化过程中连续测定胶料硫化性能的全部变化,并具有较高的测试精度的仪器,生产橡胶制品的厂家可以用它进行橡胶的均匀性、重现性、稳定性的测试。
并且进行橡胶配方设计和检测,目前主要应用于批量生产橡胶硫化特性的检测和管控。
3. 分类:根据其有无转子分为:有转子流变仪、无转子流变仪.有转子流变仪及无转子流变仪的主要区别:有转子流变仪测试时试样温度达到稳定所需要时间长;而无转子则较快。
有转子的转子与胶料产生的磨擦力也计入胶料剪切模量的数据中,对数据的重现性有一定的影响。
4、硫化曲线实验原理从流变学的观点可以说,迄今为止,各种流变仪所采用的原理本质上是一致的,即模压在模腔内的试样连续的承受恒定的小振幅和低频率的正弦剪切变形,由测力传感器测定剪切应力,以转矩单位表示,即胶料的剪切模量,当试样规格、厚度、振幅角和实验温度一定时,所测定的剪切应力与交联点密度成正比关系,记录下的剪切应力—时间的曲线便是硫化曲线。
.硫化曲线参数:ML ——最低转矩,N·m (kgf·cm )MH ——到达规定时间之后仍然不出现平坦曲线或最高转矩的硫化曲线,所达到的最高转矩N·m(kgf·cm )TS1——从实验开始到曲线由最低转矩上升 N·m (kgf·cm )时所对应的时间,MINTS2——从实验开始到曲线由最低转矩上升 N·m(kgf·cm)时所对应的时间,MINTC(x)——试样达到某一硫化程度所需要的时间,即试样转矩达到ML+X(MH-ML)时所对应的时间,MIN(注:如X取值,即TC50,X取.9,即TC90).硫检参数的意义:ML:表示胶料的流动性,ML越低,流动性越好,反之,越差。
橡胶硫化培训教材

2.2 欠硫阶段(又称预硫阶段)
硫化起步与正硫化之间的阶段称为欠硫阶段。在此阶段,
由于交联度较低,橡胶制品应具备的性能大多还不明显。尤其
是此阶段初期,胶料的交联度很低其性能变化甚微,制品没有 实用意义。但是到了此阶段的后期,制品轻微欠硫时,尽管制
品的抗张强度、弹性、伸长率等尚未达到预想水平,但其抗撕
裂性、耐磨性和抗动态裂口性等则优于正硫化胶科。因此,如 果要求后几种性能时,制品可以轻微欠硫。
2.3 正硫阶段
在多数情况下,制品在硫化时都必须达到适当的交
联度。达到适当交联度的阶段叫正硫化阶段,即正硫阶 段。在此阶段,硫化胶的各项物理机械性能并非在同一 时间都达到最高,而是分别达到或接近最佳,其综合性 能最好。此阶段所取的温度和时间称为正硫化时间和正 硫化温度。
末硫化胶受到较长时间的外力作用时,主要发生 塑性流动,橡胶分子基本上没有回到原来位置的倾向。
橡胶硫化后,交联使分子或链段固定,形变受到网络
的约束,外力作用消除后,分子或链段力图回复原来 沟象和位置,所以硫化后橡胶表现出很大的弹性。交
联度的适当,增加这种可逆的弹性回复表现得更为显
著。
式中w为弹性,ρ为橡胶密度;T为绝对温度,Mc为两个相邻交联 随间橡胶分子的平均分子量;R为气体常数;λ1、 λ2 、 λ3为 试片在三个拉伸方向上的伸长率。
1.3 抗
张
强
度
抗张强度与定伸强度和硬度不同,它不随交联点数目的增加
而不断地上升。例如使用硫黄硫化的橡胶,当交联度达到适当值 后,如若继续硫化,其抗张强度反而下降。在硫黄用量很高的硬
质橡胶中,抗张强度下降后又复上升,一直达到硬质胶水平时为
止。如图所示。
上述现象可解释为:在软质橡胶区,其抗张强度随结合硫(比 例于交联度)的增加而增加。当结合硫继续增加时,对于结晶性橡 应(如天然橡胶),由于结合硫的增多使分子链在拉伸时结晶或取 向受到阻,引起抗张强度下降;对于非结晶性橡胶(丁苯橡胶), 则因交联相当多而又不规则,网状结构容易发生局部应变过度, 使单个链或交联键产生断裂,导致抗张强度下降。当结合硫进一 步不断增加时,交联数和环化结构也不断增加抗张强度又复上升, 直至成为硬质橡胶。
硫化曲线介绍精编

硫化曲线介绍精编 Document number:WTT-LKK-GBB-08921-EIGG-22986一. 流变仪之各种曲线之原理:1. S*粘弹曲线的原理:根据转子或转盘转动时,因胶料架桥作用所产生之扭矩变化曲线。
S*= S’2+S”2δ=ab-ac2. S’弹性曲线的原理:S’=S* X cosδ,S’ 可得到相关之加硫条件参数。
3. S”粘性曲线的原理:S”=S* X sinδ ,S” 可得到相关之粘性参数。
粘性曲线可看出橡胶之加工性。
4. Loss Angle 动的损失角曲线的原理:δ=ab-ac5. tan δ粘弹性比值曲线:tan δ=S”/S’6. 上、下模温度曲线:测试进行中温度变化记录曲线。
7. 硫化速率曲线:架桥过程中相邻两点间之斜率值之曲线。
8. 粘弹综合曲线:S*= S’2+S”2二. 流变仪图形及数据之判读及运用:流变仪之标准硫化曲线如下:S* S’S ” δab ac δ a c b其中共分为三大区:1. 第一区为加工区:在此一时间内橡胶具有可塑性。
此段时间愈长愈易于加工,但产能将降低,扭力值愈低橡胶流动性愈好。
2. 第二区为硫化区:在此一时间内为架桥过程。
以相同的材料而言此段时间愈长,物性通常会较佳。
3. 第三区为物理性质区:此一区段可判读成品之物理性质。
由曲线中可得数据说明如下:时间扭力1.焦烧时间(TS – Time of Scorch):一般而言国人的习惯此数据取2,这个时间通常称之为加工安全时间,也就是超过此时间橡胶已架桥失去了流动性,这是衡量模内流动时间的尺度,在低温下,它是衡量加工性能的指数,它与门尼焦烧相似。
事实上,如果流变仪和门尼试验的温度相同时,流变仪的TS2和门尼的TS35有密切关系。
以TS2为例,其定义为最低扭力值加2个单位所对应的时间:MS2=ML+2 ?此点所对应的时间(TS)2.硫化时间(TC – Time of Curing):一般而言国人的习惯此数据取90,这个时间通常称之为最适加硫时间,也就是说当加硫至此一时间就可自模具中将成品取出,其定义为加硫至90%所需之时间,其计算公式为:MC90=(MH-ML)*90%+ML?此点所对应之时间(TC)3.最低扭力值(ML – Min Torque):此数据可作为加工特性之参考。
橡胶制品的硫化过程及对应曲线图

橡胶制品的硫化过程及对应曲线图
橡胶硫化过程:
完整的硫化体系主要有硫化剂、活化剂、促进剂组成
诱导阶段:先是硫磺、促进剂、活化剂的相互作用,是氧化锌在胶料中溶解度增加,活化促进剂,是促进剂与硫磺之间反应生成一种活性更大的中间产物。
对应硫化曲线→焦烧阶段:操作焦烧时间、剩余焦烧时间。
它的长短关系到生产加工安全性,决定于胶料配方成分,主要受促进剂的影响。
操作焦烧时间:橡胶加工过程中由于热积累效应所消耗掉的焦烧时间。
剩余焦烧时间:胶料在模型中加热保持流动性的时间。
交联阶段:可交联的自由基(或离子)与橡胶分子链产生反应,生成交联键对应硫化曲线→热硫化阶段:时间长短决定于温度和胶料配方。
温度越高,促进剂用量越多,硫化速度也越快。
曲线的斜率大小代表硫化反应速度,斜率越大,硫化反应速率
越快,生产效率越高。
网络形成阶段:此阶段的前期,交联反应已趋形成,初始阶段的交联键发生短化、重排和裂解反应,最后网络趋于稳定,获得网络相对稳定的硫化胶。
对应硫化曲线→平坦硫化阶段:网络形成的前期,交联反应已基本完成,继而发生交联键的重排、裂解等反应,胶料强力曲线出现平坦期,平坦硫化时间取决于胶料配方。
对应硫化曲线→过硫化阶段:网络形成的后期,存在着交联的重排,由于此时主要是交联键及键段的热裂解反应,因此胶料的弹力性能显著下降。
-。
硫化曲线教材
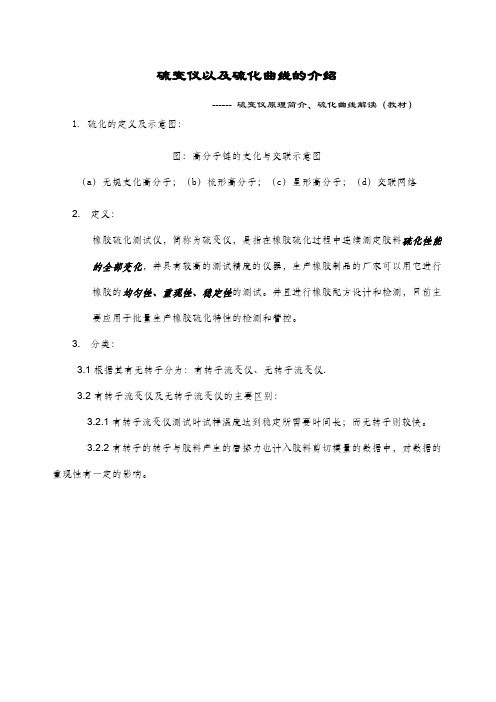
硫变仪以及硫化曲线的介绍------ 硫变仪原理简介、硫化曲线解读(教材)1. 硫化的定义及示意图:图:高分子链的支化与交联示意图(a)无规支化高分子;(b)梳形高分子;(c)星形高分子;(d)交联网络2. 定义:橡胶硫化测试仪,简称为硫变仪,是指在橡胶硫化过程中连续测定胶料硫化性能的全部变化,并具有较高的测试精度的仪器,生产橡胶制品的厂家可以用它进行橡胶的均匀性、重现性、稳定性的测试。
并且进行橡胶配方设计和检测,目前主要应用于批量生产橡胶硫化特性的检测和管控。
3. 分类:3.1根据其有无转子分为:有转子流变仪、无转子流变仪.3.2有转子流变仪及无转子流变仪的主要区别:3.2.1有转子流变仪测试时试样温度达到稳定所需要时间长;而无转子则较快。
3.2.2有转子的转子与胶料产生的磨擦力也计入胶料剪切模量的数据中,对数据的重现性有一定的影响。
4、硫化曲线4.1实验原理从流变学的观点可以说,迄今为止,各种流变仪所采用的原理本质上是一致的,即模压在模腔内的试样连续的承受恒定的小振幅和低频率的正弦剪切变形,由测力传感器测定剪切应力,以转矩单位表示,即胶料的剪切模量,当试样规格、厚度、振幅角和实验温度一定时,所测定的剪切应力与交联点密度成正比关系,记录下的剪切应力—时间的曲线便是硫化曲线。
4.2.硫化曲线参数:ML ——最低转矩,N·m (kgf·cm )MH ——到达规定时间之后仍然不出现平坦曲线或最高转矩的硫化曲线,所达到的最高转矩N·m(kgf·cm )TS1——从实验开始到曲线由最低转矩上升0.1 N·m (kgf·cm )时所对应的时间,MINTS2——从实验开始到曲线由最低转矩上升0.2 N·m(kgf·cm)时所对应的时间,MINTC(x)——试样达到某一硫化程度所需要的时间,即试样转矩达到ML+X(MH-ML)时所对应的时间,MIN(注:如X取值0.5,即TC50,X取.9,即TC90)4.4.硫检参数的意义:ML:表示胶料的流动性,ML越低,流动性越好,反之,越差。
硫化曲线介绍
一. 流变仪之各种曲线之原理:1. S 粘弹曲线的原理:根据转子或转盘转动时,因胶料架桥作用所产生之扭矩变化曲线.S= S’2+S”2δ=ab-ac2.S’弹性曲线的原理:S’=S X cosδ,S’ 可得到相关之加硫条件参数.3. S”粘性曲线的原理:S”=S X sinδ ,S” 可得到相关之粘性参数.粘性曲线可看出橡胶之加工性.4.Loss Angle 动的损失角曲线的原理:δ=ab-ac 5.tan δ粘弹性比值曲线:tan δ=S”/S’ 6.上、下模温度曲线:测试进行中温度变化记录曲线. 7.硫化速率曲线:架桥过程中相邻两点间之斜率值之曲线. 8. 粘弹综合曲线:S= S’2+S”2二. 流变仪图形及数据之判读及运用:流变仪之标准硫化曲线如下:S* S’S δab ac δ a c b扭力其中共分为三大区:1. 第一区为加工区:在此一时间内橡胶具有可塑性.此段时间愈长愈易于加工,但产能将降低,扭力值愈低橡胶流动性愈好.2. 第二区为硫化区:在此一时间内为架桥过程.以相同的材料而言此段时间愈长,物性通常会较佳.3. 第三区为物理性质区:此一区段可判读成品之物理性质.由曲线中可得数据说明如下:1. 焦烧时间TS – Time of Scorch :一般而言国人的习惯此数据取2,这个时间通常称之为加工安全时间,也就是超过此时间橡胶已架桥失去了流动性,这是衡量模内流动时间的尺度,在低温下,它是衡量加工性能的指数,它与门尼焦烧相似.事实上,如果流变仪和门尼试验的温度相同时,流时间扭力变仪的TS2和门尼的TS35有密切关系.以TS2为例,其定义为最低扭力值加2个单位所对应的时间:MS2=ML+2 此点所对应的时间TS2. 硫化时间TC – Time of Curing :一般而言国人的习惯此数据取90,这个时间通常称之为最适加硫时间,也就是说当加硫至此一时间就可自模具中将成品取出,其定义为加硫至90%所需之时间,其计算公式为:MC90=MH-ML90%+ML 此点所对应之时间TC3.最低扭力值ML – Min Torque :此数据可作为加工特性之参考.最低扭力与在同样试验温度下之门尼粘度成正比,通常此值愈低愈易于加工,但也容易产生毛边.4. 最高扭力值MH – Max Torque :此数据可作为成品物性之参考.最高扭力值是衡量在试验温度下,只改变促进剂时,胶料剪切模数或硬度的尺度,也是衡量定伸强度和交联密度变化的有效尺度.5. 加硫指数CRI – Cure Rate Index :总加硫时间,即CRI=100/T90-T2.这是计算硫化反应速度的指针.6. 动的损失角Loss Angle :橡胶粘弹性比值之Tan δ,高分子本身具有粘弹特性,举例来说,一条橡皮筋原本长度为1公分当施以一外力时长度变为5公分,当外力消失时长度并非变为原来的1公分,而是是变为公分,而这公分的差值在流变机上,由于是作摇摆运动所以称之为动的损失角,详细说明可参考第四大项.一般而言高能量吸收如橡胶振动吸收器的材料其tan δ值需愈高,高弹力如橡胶带的材料其tan δ值需低一点.7. 新的硫变仪提供新的粘性曲线及弹性曲线,此分离出之两种曲线可更明确的看出材料之加工特性及,产品之物理性,下列几例说明这种特性: a. 图中比较2种不同Cis 含量之丁二烯橡胶,图中硫化开始前的粘性曲线S”相当不同.因此虽然最终产品性质可能相同,但现场预期将有不同的加工特性,这是传统流变仪所无法提供解析的.加工特性区 加硫区 物理性质区 2 1 1 2 S 1. 96~98% Cis2. 93% CisCis 含量对于BR 粘弹性质之效应b. 图中为相同NR 配方中3种不同级别碳黑的比较.硫化曲线S’都很相似,但粘性曲线S”则有明显差别,此时,粘性曲线可能指出假使误用碳黑,则完全硫化橡胶则有潜在的现场问题.这些问题无法透过单独硫化曲线而查觉.碳黑级别对于NR 粘弹性质的效应c.S’ S MDR S ” VS. Goodrich Flexometer Flexometer Heat Builup, Deg. cM D R S ” d N m a t 160o C N550 N330 N220Cured NR由上图可看出当使用不同种类的碳黑时,S”值也会不同,压缩升热之升温值也会不同,图示使用碳黑N220时其温升较高.d.由上图可看出未硫化橡胶混练程度不同,会产生不同的Tan δ值,其口型膨胀率也会不同.e.%MPT Die Swell, 100o C,30 1/sec Heat Builup, Deg. M D R T a n (δ) a t 150o C Carbon Black Levels Tan(δ) VS. Die SwellM D R T a n (δ) a t 150oC Uncured NR由上图可看出未硫化橡胶碳黑用量不同,会产生不同的Tan δ值,其口型膨胀率也会不同.f.由上图可看出硫化橡胶S”高时,其反弹系数愈低. %MPT Die Swell, 100o C,30 1/sec Heat Builup, Deg. MDR S ” VS. Dunlop ReboundM D R S ” d N m a t 160o C % Rebound Resilience。
硫化曲线培训
山 东 龙 跃 橡 胶 有 限 公 司
Shangdong LongYue Rubber Co.,Ltd.
硫化曲线模拟图
实时直角曲线
从第1步至5 步内温一直 保持198度 蒸压14以上 从第6步开始 蒸汽、氮气进, 内温下降氮压 24以上
运行信息显示
轮胎规格 左热板温度 右热板温度 左模套温度 右模套温度 左 内 内 温 温 压
硫பைடு நூலகம்进度
96%
返 回 主 窗 口
硫化机介质动作步序模拟图
硫化工序介质条件范围
依据:QG/LY-GY-007-2013 《关于车间工序介质条件的规定》
注:标准值是指硫化实际要求值,动力出口可根据机台值调整输出。 单位:压力=MPa;温度=°C 项 目 一定定型 二次定型 热板蒸汽 外套蒸汽 压力 压力 温度 温度 压力 胶囊内蒸汽 温度 胶囊内氮气 氮气纯度 后充气压力 氮气回收 动力水 压力 纯度 压力 压力 压力 198 2.4 ≥99.995% 0.2 0.5 2.2 ±2.0 ±0.1 NA ±0.05 0.01 ±0.3 内压压力表 三针记录 控制阀 设定压力表 控制阀 设定压力表 回收罐内 压力记录表 管道末端 压力记录表 标准值 0.06 0.08 170/175 170/175 1.4 允许公差 ±0.03 ±0.03 ±2.0 ±2.0 ±0.05 内压压力表 三针记录 测量位置与标准仪器 控制阀 设定压力表 控制阀 设定压力表 控制阀 控制阀 三针记录 三针记录
/ 174.9 176.0 175.0
175.0
142.0 148.0 0.41
中间会有两 次蒸汽排凝 第3、第5步
右 内
左 囊 计 数
右 囊 计 数 硫化机位置 硫化机状态 硫化步序号 当前步剩余时间 硫化延时时间(分) 硫化剩余总时间
橡胶的硫化曲线分析
橡胶的硫化反应历程硫化历程是橡胶大分子链发生化学交联反应的过程包括橡胶分子与硫化剂及其他配合剂(主要是活性剂、促进剂)之间发生的一系列化学反应以及在形成网状结构时伴随发生的各种副反应。
硫化仪无转子硫化仪的结构示意图硫化曲线分成四个阶段,即1)焦烧阶段:热硫化开始前的延迟时间2)热硫化阶段:硫化反应的交联阶段,其斜率代表反应速度3)平坦硫化阶段:交联反应基本结束,熟化阶段(短化、重排、裂解),性能最佳4)过硫化阶段:胶料硫化在此阶段,可能出现三种形式1、焦烧期(ab段)焦烧期(诱导期):从胶料放入模具至出现轻微硫化的整个过程所需要的时间叫硫化诱导期,又称为焦烧时间。
焦烧(scorch):加有硫化剂的混炼胶在加工或停放过程中产生的早期硫化现象。
焦烧现象本质是硫化,胶料局部交联。
胶料焦烧后,流动性明显变差,甚至不能流动,后续加工工序无法正常进行。
诱导期反应了胶料的加工安全性。
诱导期短,加工安全性差;诱导期太长,会降低生产效率。
表征参数ts1——焦烧时间(scorchtime),从开始加热起,至胶料的转矩由最低值上升0.1N.m所需要的时间。
tc10——焦烧时间,从开始加热起,至胶料的转矩由最低值上升10个单位所需要的时间。
焦烧时间又分为操作焦烧时间:胶料在加工或停放过程中由于热积累效应所消耗的焦烧时间;剩余焦烧时间:胶料在模具内保持流动的时间。
操作焦烧时间长,剩余焦烧时间就短2、热硫化期(BC段)由焦烧点到工艺正硫化点(C点)所经历的阶段,即硫化反应过程的交联反应期。
曲线快速上升。
热硫化期特性参数:tc90——工艺正硫化时间,从开始加热起,至胶料的转矩由最低值上升90个单位所需要的时间。
斜率k——反映胶料硫化速度快慢,斜率越大,硫化速度越快CRI——加硫指数【CRI=100/(tc90—ts1)】,min-1,反映胶料硫化速度快慢,CRI值大,硫化速度快。
3、平坦硫化期(cd段)曲线保持水平所经历的时间长短,反映胶料在硫化过程中性能稳定性的高低。
硫化体系PPT学习教案
异裂:⊕S8⊙(两性离子) 亲电加成 适用胶种:NR、SBR、BR、NBR、IIR、EPDM、IR、TPI
.
应用场合:常温下或温度要求不太高的场合下使用的橡胶制品。
特 点:与橡胶的反应速度较快,反应温度较低,硫化胶 的强度高,动态疲劳性好,耐热、耐老化性较差,硫黄粉 容易喷霜,价格便宜,是橡胶制品中使用最多的硫化剂。
第24页/共82页
第二节、硫化体系助剂
一、硫化剂(curing agent)
硫化剂:又称交联剂,是指能够将橡胶线型大分子交联成网状
结构的一类物质。
作用:进行交联反应,使橡胶线型分子网络化。是配方中不可
缺少的最重要的配合剂。
主要硫化剂:
制法 硫铁矿煅烧,得硫块再粉碎
1、硫黄 硫黄粉
(最常用)
石油尾气分离出H2S,氧化再还原
第20页/共82页
(五)硫化曲线的应用
(1)测定某一胶料的硫化特性参数; (2)研究胶料及配合剂硫化返原性及抗返原性; (3)研究胶料中硫化助剂的分散均匀性; (4)研究橡胶共混体系硫化同步性; (5)研究防焦剂的作用效果; (6)研究新型助剂对胶料硫化特性的影响 (7)研究胶料硫化与发泡速度的匹配性(发泡硫化仪) ; (8)提供信息,协助配方设计人员调整配方。
后发现,硫化剂除硫磺外,还有其他品种如过氧化物、树 脂、有机胺、金属氧化物等也可以使橡胶硫化,开发了非 硫硫化体系。
第4页/共82页
三、橡胶硫化反应过
程
促 进 剂
硫黄
促 进 剂 多 硫 化 物
橡胶
橡 胶 大 分 子 多 硫
分解
大 分 子 自 由 基
橡胶
交 联 反
活 化 剂
活 性 中 间 体
- 1、下载文档前请自行甄别文档内容的完整性,平台不提供额外的编辑、内容补充、找答案等附加服务。
- 2、"仅部分预览"的文档,不可在线预览部分如存在完整性等问题,可反馈申请退款(可完整预览的文档不适用该条件!)。
- 3、如文档侵犯您的权益,请联系客服反馈,我们会尽快为您处理(人工客服工作时间:9:00-18:30)。
硫变仪以及硫化曲线的介绍
------ 硫变仪原理简介、硫化曲线解读(教材)
1. 硫化的定义及示意图:
图:高分子链的支化与交联示意图
(a )无规支化高分子;(b )梳形高分子;(c )星形高分子;(d )交联网络
2. 定义:
橡胶硫化测试仪,简称为硫变仪,是指在橡胶硫化过程中连续测定胶料硫化性能的全部变化,并具有较高的测试精度的仪器,生产橡胶制品的厂家可以用它进行橡胶的均匀性、重现性、稳定性的测试。
并且进行橡胶配方设计和检测,目前主要应用于批量生产橡胶硫化特性的检测和管控。
3. 分类:
根据其有无转子分为:有转子流变仪、无转子流变仪.
有转子流变仪及无转子流变仪的主要区别:
有转子流变仪测试时试样温度达到稳定所需要时间长;而无转子则较快。
有转子的转子与胶料产生的磨擦力也计入胶料剪切模量的数据中,对数据的重现性有一定的影响。
4、硫化曲线
实验原理
从流变学的观点可以说,迄今为止,各种流变仪所采用的原理本质上是一致的,即模压在模腔内的试样连续的承受恒定的小振幅和低频率的正弦剪切变形,由测力传感器测定剪切应力,以转矩单位表
示,即胶料的剪切模量,当试样规格、厚度、振幅角和实验温度一定时,所测定的剪切应力与交联点密度成正比关系,记录下的剪切应力—时间的曲线便是硫化曲线。
.硫化曲线参数:
ML ——最低转矩,N·m (kgf·cm )
MH——到达规定时间之后仍然不出现平坦曲线或最高转矩的硫化曲线,所达到的最高转矩N·m(kgf·cm)
TS1——从实验开始到曲线由最低转矩上升N·m(kgf·cm)时所对应的时间,MIN
TS2——从实验开始到曲线由最低转矩上升N·m(kgf·cm)时所对应的时间,MIN
TC(x)——试样达到某一硫化程度所需要的时间,即试样转矩达到ML+X(MH-ML)时
所对应的时间,MIN(注:如X取值,即TC50,X取.9,即TC90)
.硫检参数的意义:
ML:表示胶料的流动性,ML越低,流动性越好,反之,越差。
MH:表征胶料的胶料的剪切模量、硬度、定伸强度和交联密度,一般MH越低,硬度越低,MH越高,硬度越高。
TS2:表征胶料的操作安全性,TS2越短,表示胶料越容易发生死料,产品在生产时容易产生缺料不良。
反之,TS2越长,虽然操作安全性提高,但是产效会变低,成本会增加很多,故TS2对胶料的
加工、配方设计具有很重要的意义。
TC90:主要用来评估胶料在成型生产时的一次加硫条件,TC90过长表示硫化速度偏慢,会导致产品硬度低,产效低。
5. 流变仪的试验影响因素
试验温度
硫化既然是一种化学反应过程,无疑温度对反应速度是一个重要因素。
随着温度提高其诱导期缩短,硫化速度加快.当温度相当高时配方中原材料变量的信息受到掩盖. 胶料硫化过程是一个在一定温度和压力作用下受力的过程。
如果温度或压力稍有变化,就会对测量的硫化曲线产生很大影响。
目前,压力一般较容易控制。
通过带有压力表的硫化仪就可以达到稳定的压力。
供给硫化仪的气压必须在任何时候都高于硫化仪所设定的额定气压。
而温度控制是各厂家一直强调的主要技术指标。
我厂硫化仪采用进口温控表,模腔温度波动≤±0.1℃,温度恢复时间≤2min。
硫化仪的振荡频率:大部分国内使用的硫化仪都采用100转/分钟的转动频率。
转动速度对硫化仪的影响主要是使得测量的过程加快。
相对于最早3转/分钟的设备来说,100转/分钟在测量时更加适用于高温快检等方面使用。
各种频率测量的硫化数据结果不同,但都可以用于橡胶硫化的检测。
硫化仪的摆动角度:
按照标准,有转子硫化仪的摆角应为1°或3°;无转子硫化仪的摆动角度应为1°或°,初配置均为1°。
摆动角度对于硫化数据的影响和频率相似,各种角度测量的硫化数据结果不同,但都可以用于橡胶硫化的检测。
角度越大,施加于胶样上的扭矩就越大,测量得到的数据就越大,当增至某一临界值时,会引起产品和转子打滑,试样产生破裂。
对于特别软的橡胶宜采用大角度的摆动。
反之,硬胶采用小一些的摆动角度就可。
总之,选用不同摆角的目的都是为了能更清楚的显示测量数据。
现在所有数据都是计算机或单片机计算,数据再小也可以分辨,对于一般橡胶硫化来说,变化角度的实用性不大,标配角度足以适用于所有橡胶。
其他
除上述三个主要影响因素外,还有像试样承受压力、转子或模腔的脏污、模腔的形状、试样的体积对测量均有不同程度的影响.。