锻造加热规范
第3章锻造的加热改

3.4锻造的加热规范
钢材与小钢坯的加热规范:
直径为200~350mm的碳素结构钢坯(含碳量大 于0.45~0.50%)和合金结构钢坯,采用三段加 热规范。
3.4锻造的加热规范
钢材与小钢坯的加热规范:
对于导温性差、热敏感性强的高合金钢坯(如高 铬钢、高速钢),则需采取低温装炉,装炉温度 为400~6500C。
3.2金属加热过程中的变化
3.2.4应力的变化
温度应力
定义:由于温度不均而产生的内应力 原因:坯料加热时表面和中心之间存在温度差, 表面受压应力,中心部位受拉应力。
钢材加热时心部产生裂纹的倾向较大
3.2金属加热过程中的变化
3.2.4应力的变化
组织应力
定义:由于相变前后组织的比容发生而引起的内应力
3.5 金属的少、无氧化加热
目的 实现方法
减少金属的氧化烧损 (烧损量小于5%)和脱 碳,限制氧化皮厚度在 0.05~0.06mm以下。 提高加热质量,提高锻 件的尺寸精度和表面质 量、提高模具寿命。
1.快速加热 2.少无氧化火焰加热 3.介质保护加热
3.5 金属的少、无氧化加热
3.5.1快速加热 1火焰加热法的辐射加热和对流快速加热 2电加热法的感应电加热和接触式电加热
3.2.1 氧化、脱碳 2、脱碳
概念 坯料在加热时,其 表层的碳和炉气中 的氧化性气体以及 某些还原性气体发 生化学反应,造成 坯料表层的含碳量 减少。 影响因素 1.坯料化学成分 2.炉气成分 3.加热温度 4.加热时间 防止措施 1.快速加热 2.控制加热炉气 的性质 3.炉内应保持不 大的正压力 4.介质保护加热
3.2金属加热过程中的变化
3.2.3 导温性的变化
第二章 锻造加热规范(WPS)

脱碳过程中: 炉气中的氧向钢内扩散; 钢中的碳则向外扩散。
●脱碳的结果
钢表层变成含碳量低的脱碳层。 当脱碳层深度超过锻件加工余量时: 会使零件表面的硬度和强度降低; 影响零件的使用性能。 严重时会发生锻造龟裂(网状裂纹)现 象。
⒈影响脱碳因素
⑴钢的化学成分
当钢中含碳量愈高,其脱碳层愈深; W等合金元素也会加剧钢的脱碳。 所以高碳工具钢、轴承钢、高速钢及 弹簧钢脱碳严重。 ⑵炉气成分 炉气成分中脱碳能力最强的介质是 H2O,其次是CO2和O2 。
⒊火焰加热分类 ⑴燃油加热
⑵燃煤加热
⑶燃气加热
㈡电加热
利用电能转换为热能对金属进行 加热的方法。
⒈电加热优点
●升温快; ●炉温容易控制; ●氧化脱碳少,加热质量好; ●生产条件好,便于实现机械化和自 动化。
⒉电加热缺点
●对毛坯尺寸形状变化的适应性不够 强; ●设备结构复杂,投资费用较大。
⒊电加热分类
把热能传给坯料表面 → 由表面向中心
进行热传导→ 使整个坯料加热。
⒈火焰加热优点
●燃料来源方便; ●加热费用较低(一次能源); ●对坯料的适应性强。 广泛应用于各种大、中、小型坯 料的加热。
⒉火焰加热缺点:
●工作条件差; ●加热速度较慢; ●加热质量较难控制; ●热效率低(如许多热量都被烟气带 入大气中)。
②感应电加热优点
●加热速度快,加热质量好; ●温控准确,金属烧损较少; ●操作简单,工作稳定; ●便于实现机械化和自动化,生产条件好。
③感应电加热缺点
●设备投资费用高; ●感应器对坯料尺寸适应范围较窄; ●电能消耗较大。
第二节 钢料加热缺陷 及防止措施
钢料在加热过程中可能产生的缺陷:
第3章锻造的加热改讲解
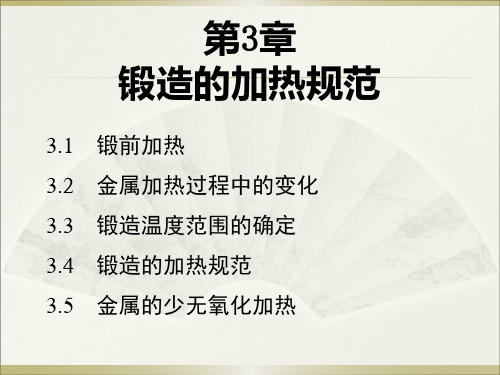
利用燃料燃烧时所产生的热量,通过对流、辐射加热坯料。
优点
燃料来源方便、 加热炉修造容易、 加热费低、适应 性强。
缺点
劳动条件差, 加热速度慢, 质量低、热效 率低。
应用范围
大、中、小 型坯料
3.1 锻前加热
2、电加热 利用电能转换热能来加热坯料。
•电阻加热
电阻炉加热
接触电加热
•感应加热
3.2.4应力的变化
如果坯料在加热过程的某一温度下,内应力 超过它的强度极限,就要产生裂纹。
产生裂纹的原因: 温度应力 组织应力 残余应力
3.2金属加热过程中的变化
3.2.4应力的变化
温度应力
定义:由于温度不均而产生的内应力 原因:坯料加热时表面和中心之间存在温度差,
表面受压应力,中心部位受拉应力。
3.1 锻前加热
电阻炉加热原理:利用电 流通过炉内的电热体产生 的能量,加热炉内的金属 坯料。
电热体材料: 铁铬铝合金 碳化硅元件 镍铬合金 二硅化钼
适用于低于 1100度
使用温度可高 于1350度
图3.1 电阻炉原理图 1-电热体 2-坯料 3-变压器
3.1 锻前加热
●接触电加热原理:
以低电压(一般为2~15V)大电流直接通 过金属坯料,由坯料自身电阻在通过电流 时产生的热量加热金属坯料。
●优点:
速度快、烧损少、加热范围不受限制、热 效率高、耗电少、成本低、设备简单、操 作方便、使用于长坯料的整体或局部加热 的优点。
●缺点:
对坯料的表面粗糙度和形状尺寸要求严格。
加热温度的测量和控制也比较困难。
概念
坯料在加热时,其 表层的碳和炉气中 的氧化性气体以及 某些还原性气体发 生化学反应,造成 坯料表层的含碳量 减少。
锻造及锻后热处理工艺规范
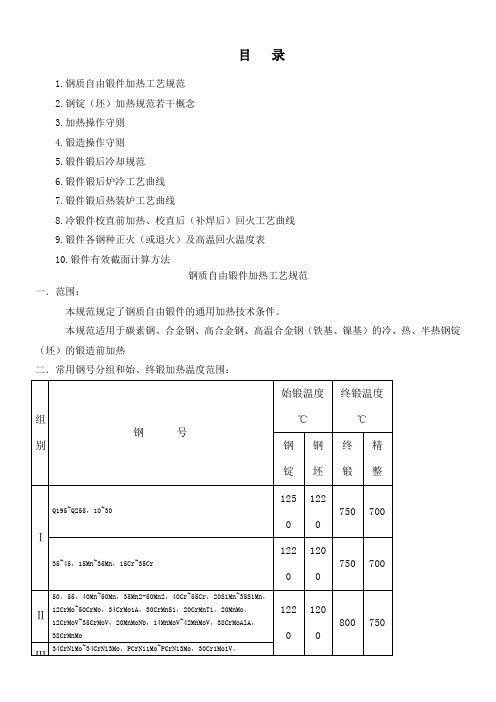
目录1.钢质自由锻件加热工艺规范2.钢锭(坯)加热规范若干概念3.加热操作守则4.锻造操作守则5.锻件锻后冷却规范6.锻件锻后炉冷工艺曲线7.锻件锻后热装炉工艺曲线8.冷锻件校直前加热、校直后(补焊后)回火工艺曲线9.锻件各钢种正火(或退火)及高温回火温度表10.锻件有效截面计算方法钢质自由锻件加热工艺规范一.范围:本规范规定了钢质自由锻件的通用加热技术条件。
本规范适用于碳素钢、合金钢、高合金钢、高温合金钢(铁基、镍基)的冷、热、半热钢锭(坯)的锻造前加热二.常用钢号分组和始、终锻加热温度范围:注1:始锻温度为锻前加热允许最高炉温,由于钢锭的铸态初生晶粒加热时过热倾向比同钢号钢坯小,故两者的锻前加热温度相差20℃~30℃;注2:根据产品的特性、锻件技术条件、变形量等因素,始锻温度可以适当调整;注3:本规范未列入的钢种,可按化学成分相近的钢号确定;注4:重要的、关键产品的、特殊材质的钢号,其加热工艺曲线由技术部编制;注5:几种不同的钢种,不同尺寸的钢锭(或坯料),在同一加热炉加热时,要以合金成分高的,尺寸大的钢锭(或坯料)为依据编制加热工艺曲线。
三.冷钢坯。
钢锭加热规范:钢锭(坯)加热规范若干概念1.钢锭(坯)入炉前的表面温度≥550℃的称为热钢锭,400~550℃的称为半热钢锭(坯),≤400℃的称为冷钢锭。
2.锻件半成品坯料的加热平均直径计算原则:δ -壁厚 H- 高度或长度 D- 外径1)实心圆类:当D>H时,按H计算;当D<H时,按D计算。
2)筒类锻坯:H>D 当H>δ时,按1.3δ计算。
3)空心盘(环)类:H<D当H>δ时,按δ计算;当H<δ时,按H计算。
3.为了避免锻件粗晶组织,最后一火的始锻温度可按其剩余锻造比(Y)确定:Y=1.3~1.6 最高加热温度1050℃Y<1.3 最高加热温度950℃4.不同钢种不同规格的坯料同炉加热时,装炉温度和升温速度均按较低的选用,保温时间按较长的选用。
锻造加热规范(严选优质)
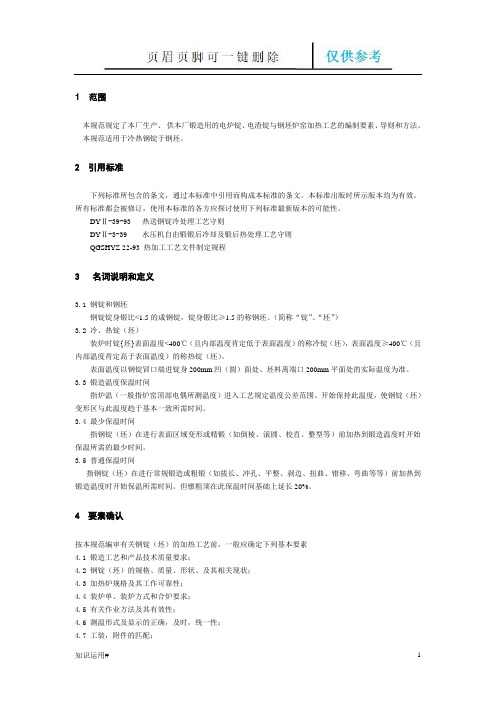
1 范围本规范规定了本厂生产、供本厂锻造用的电炉锭、电渣锭与钢坯炉窑加热工艺的编制要素、导则和方法。
本规范适用于冷热钢锭于钢坯。
2 引用标准下列标准所包含的条文,通过本标准中引用而构成本标准的条文。
本标准出版时所示版本均为有效。
所有标准都会被修订,使用本标准的各方应探讨使用下列标准最新版本的可能性。
DYⅡ-39-93 热送钢锭冷处理工艺守则DYⅡ-3-39 水压机自由锻锻后冷却及锻后热处理工艺守则QGSHYZ 22-93 热加工工艺文件制定规程3 名词说明和定义3.1 钢锭和钢坯钢锭锭身锻比<1.5的成钢锭,锭身锻比≥1.5的称钢坯。
(简称“锭”、“坯”)3.2 冷、热锭(坯)装炉时锭{坯}表面温度<400℃(且内部温度肯定低于表面温度)的称冷锭(坯),表面温度≥400℃(且内部温度肯定高于表面温度)的称热锭(坯)。
表面温度以钢锭冒口端进锭身200mm凹(圆)面处、坯料离端口200mm平面处的实际温度为准。
3.3 锻造温度保温时间指炉温(一般指炉窑顶部电偶所测温度)进入工艺规定温度公差范围、开始保持此温度,使钢锭(坯)变形区与此温度趋于基本一致所需时间。
3.4 最少保温时间指钢锭(坯)在进行表面区域变形或精锻(如倒棱、滚圆、校直、整型等)前加热到锻造温度时开始保温所需的最少时间。
3.5 普通保温时间指钢锭(坯)在进行常规锻造或粗锻(如拔长、冲孔、平整、剥边、扭曲、错移、弯曲等等)前加热到锻造温度时开始保温所需时间。
但镦粗须在此保温时间基础上延长20%。
4 要素确认按本规范编审有关钢锭(坯)的加热工艺前,一般应确定下列基本要素4.1 锻造工艺和产品技术质量要求;4.2 钢锭(坯)的规格、质量、形状、及其相关现状;4.3 加热炉规格及其工作可靠性;4.4 装炉单、装炉方式和合炉要求;4.5 有关作业方法及其有效性;4.6 测温形式及显示的正确,及时,统一性;4.7 工装,附件的匹配;4.8 作业环境适应性。
锻造工艺学3锻造的热规范
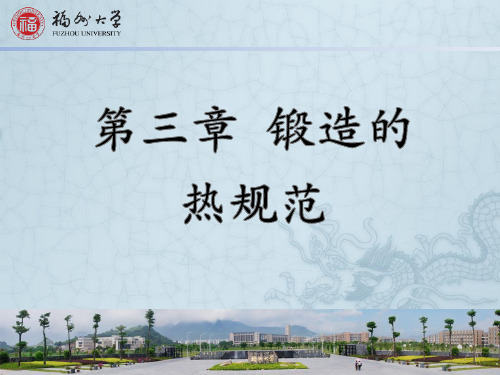
温度,T
共晶点
铁素体 0.15 碳钢
铸铁
39
一、始锻温度 ● 保证无过烧; ● 低于固相线150-250℃; ● 考虑材料种类(钢锭、钢材) ● 考虑打击速度(高速成形的热效应)。
晶粒之间失去联系,材料失去塑性和强度
27
2、防止过烧的措施
遵守加热规范 控制加热温度 特别要控制出炉温度及在高温时的停留时间
28
五、裂纹 (受力导致开裂) 开裂原因?
1、温度应力 2、组织应力 3、残余应力
29
1、温度应力
坯料加热过程中,因温度场分布不均匀,造成坯 料各处的不均匀膨胀,从而在坯料各部分之间产生了 相互制约的内应力(温度应力)。
35
3-3 金属的加热规范
36
几个概念:
1)装炉温度 2)加热速度 3)均热保温 4)加热时间 5)始锻温度、终锻温度、锻造温度范围
37
3-4 锻造温度范围的确定
基本原则: 合理的锻造温度范围,应保证金属具有良好的塑
性和较低的变形抗力。并在此条件下尽量扩大锻造温 度范围,以减少加热火次。 ● 具体锻造温度范围应根据铁碳相图来确定
5
火焰 加热
6
火焰 加热
7
2、电加热
优点:劳动条件好,便于实现机械化自动化, 升温快,加热质量容易控制
缺点:适应性差,设备复杂,费用高
8
电加热分类、各自的应用范围
电加热
电阻加热
感应加热
电阻炉加热 接触电加热 盐浴炉加热 工频 中频 高频
高频:100K-1000K Hz 工频:50 Hz 中频:500-10K Hz
14
钢的化学成份: ⑴ 含碳量大于0.3%氧化皮减少(C 与O 反 应生成还原性气体CO); ⑵ 合金元素:Cr、Ni、Al、Mo能减缓氧化 (生成致密的氧化膜,透气性小),Ni、 Cr含量为13-20%则几乎无氧化。
大型锻件锻造加热规范

水压机锻件锻造加热规范一表1是常用锻钢的锻造温度范围,表2是常用锻钢的分组。
对表1,表2 中未列入的钢种,按化学成份相近的钢号确定。
二表3是热锻钢锻造加热规范。
热锻钢是指表面温度》550'C的钢锭或钢坯。
对于温度在400至550E之间者,应先按下表规定均热后,再按热锻钢加热。
表面温度低于400C,截面大于1000mm的热锻钢,由车间技术组或现场值班人员临时制定专用加热曲线。
注:钢锭表面温度采用高温计或红外线测温仪测量。
测量部位在钢锭冒口线以下100mm左右的凹面上。
三、表4至衰6是各组冷锻钢锻造加热规范冷锻钢是指在常温下存放的钢锭或钢坯,对于放在露天跨的冷锻钢,冬季(当年11月至下年2月)入炉加热前,需先吊至车间内避风处放2至3天后再入炉加热。
I.表列升温时间是总加热时间组成部份(总加热时间=升温时间+保温时间)。
对于热锻钢加热,在保证总加热时间的前提下,升温时间可根据实际加热情况缩短,但保温时间则应相应增长。
2•当具备采用高温计(或红外线测温仪)测定料温的条件时,对于热锻钢加热的升温时间及冷锻钢加热经750C保温后的升温时间的确定,可按实际升温时间计。
实际升温时间是指从开始升温到采用高温计测定料温的确达到始锻温度止这一段加热时间。
保温时间仍按表列值要求。
3.采用“ WHF '法锻造时转子及与转子质量要求相当(主要是指超声波探伤要求)的重要锻件,保温时间按表列值的2 倍计,其余锻件按表列值的1.5 倍计,采用“ JTS”法锻造时保温时间均按表列值的1. 2倍计。
4•进行镦粗的I、U、川组钢,,保温时间应按表列值增加30% .对于压钳口工序,各组钢的保温时间均可按表列值减少30-40%。
5、热锻钢的再加热,返炉时其表面温度》1100C时,,保温时间可按表列值减少40—50%,若表面温度在1000-1100C时,保温时间可按表刮值减少30-40%。
当需要执行此规定时,锻坯返炉的表面温度,由车间现场值班人员和中间检查人员共同确认。
锻造工艺学-3-锻造的热规范

9
3-2 加热时产生的缺陷及防止措施
表层缺陷:氧化、脱碳、裂纹 内部缺陷:过热、过烧、裂纹
10
一、氧化
钢在加热时,表面上的合金元素与炉气中的氧化 性气体(O2,CO2,H2O和SO2)发生化学反应,形成氧 化皮。
氧化实质上是一种扩散过程:铁以离子状态从内 部向表面扩散,氧以原子状态吸附到钢坯表面,并向 内部扩散。
35
3-3 金属的加热规范
36
几个概念:
1)装炉温度 2)加热速度 3)均热保温 4)加热时间 5)始锻温度、终锻温度、锻造温度范围
37
3-4 锻造温度范围的确定
基本原则: 合理的锻造温度范围,应保证金属具有良好的塑
性和较低的变形抗力。并在此条件下尽量扩大锻造温 度范围,以减少加热火次。 ● 具体锻造温度范围应根据铁碳相图来确定
30
2、组织应力(相变应力)
具有相变的材料在加热过程中,表层先相变,心 部后相变,且相变前后组织的比容发生变化,由此引 起的应力叫组织应力。
31
加热过程中随着温度升高,表层先相变,由珠光 体转变为奥氏体,比容减小,表层受拉心部受压。此 时组织应力与温度应力反向,使总的应力数值减小。
随着温度的继续升高,心部相变,此时组织应力 心部受拉表层受压。组织应力方向与温度应力相同, 使总的应力数值增大,但此时钢料已接近高温,一般 不会造成开裂。
击韧性,因此要尽量避免产生魏氏组织。
43
44
终锻温度:
低碳钢:奥氏体、铁素体双相区 中碳钢:奥氏体单相区 高碳钢:奥氏体、渗碳体双相区
注意:高碳钢终端温度为何选在奥氏体、渗碳 体双相区?
45
3-5 锻后冷却
一、冷却方法
● 空冷 ● 坑冷(箱冷) ● 炉冷 各种冷却方法的根本区别在于冷却速度的不同
- 1、下载文档前请自行甄别文档内容的完整性,平台不提供额外的编辑、内容补充、找答案等附加服务。
- 2、"仅部分预览"的文档,不可在线预览部分如存在完整性等问题,可反馈申请退款(可完整预览的文档不适用该条件!)。
- 3、如文档侵犯您的权益,请联系客服反馈,我们会尽快为您处理(人工客服工作时间:9:00-18:30)。
1 范围
本规范规定了本厂生产、供本厂锻造用的电炉锭、电渣锭与钢坯炉窑加热工艺的编制要素、导则和方法。
本规范适用于冷热钢锭于钢坯。
2 引用标准
下列标准所包含的条文,通过本标准中引用而构成本标准的条文。
本标准出版时所示版本均为有效。
所有标准都会被修订,使用本标准的各方应探讨使用下列标准最新版本的可能性。
DYⅡ-39-93 热送钢锭冷处理工艺守则
DYⅡ-3-39 水压机自由锻锻后冷却及锻后热处理工艺守则
QGSHYZ 22-93 热加工工艺文件制定规程
3 名词说明和定义
3.1 钢锭和钢坯
钢锭锭身锻比<1.5的成钢锭,锭身锻比≥1.5的称钢坯。
(简称“锭”、“坯”)
3.2 冷、热锭(坯)
装炉时锭{坯}表面温度<400℃(且内部温度肯定低于表面温度)的称冷锭(坯),表面温度≥400℃(且内部温度肯定高于表面温度)的称热锭(坯)。
表面温度以钢锭冒口端进锭身200mm凹(圆)面处、坯料离端口200mm平面处的实际温度为准。
3.3 锻造温度保温时间
指炉温(一般指炉窑顶部电偶所测温度)进入工艺规定温度公差范围、开始保持此温度,使钢锭(坯)变形区与此温度趋于基本一致所需时间。
3.4 最少保温时间
指钢锭(坯)在进行表面区域变形或精锻(如倒棱、滚圆、校直、整型等)前加热到锻造温度时开始保温所需的最少时间。
3.5 普通保温时间
指钢锭(坯)在进行常规锻造或粗锻(如拔长、冲孔、平整、剥边、扭曲、错移、弯曲等等)前加热到锻造温度时开始保温所需时间。
但镦粗须在此保温时间基础上延长20%。
4 要素确认
按本规范编审有关钢锭(坯)的加热工艺前,一般应确定下列基本要素
4.1 锻造工艺和产品技术质量要求;
4.2 钢锭(坯)的规格、质量、形状、及其相关现状;
4.3 加热炉规格及其工作可靠性;
4.4 装炉单、装炉方式和合炉要求;
4.5 有关作业方法及其有效性;
4.6 测温形式及显示的正确,及时,统一性;
4.7 工装,附件的匹配;
4.8 作业环境适应性。
5 钢锭(坯)加热曲线和应用导则
5.1 钢锭(坯)锻造温度范围分三类控制,见表3。
5.2 冷锭(坯)加热见表4、表5。
5.3 热锭(坯)加热见表6,表7。
5.4 未列入钢种的有关工艺参数可根据其产品技术要求、成分、导热、导温性和其他一些理化特性以及塑性变形特点、临界变形量要求等,以相似及偏于安全的原则加以选用。
有特殊要求时应以专用加热工艺(该工艺编审程序按QS/SHYZ22-93中A、B类执行)为准。
5.5 装炉量多、装炉方式特殊、合炉件成分复杂、火次不同等复杂情况下,在安全。
可靠的原则下按最大直径、最复杂件、最高要求选择基本工艺,并对初始的有关参数,按成分、出炉顺序、锻压区域及内容、锻压时的钢锭(坯)的动态冷却速度、终锻技术要求等等作适当调整。
6 钢锭(坯)截面的当量直径计算
6.1 圆形
6.1.1 轴类(长度L)直径D)以其最大直径为准计算
6.1.2 饼类(直径D)厚度H):
D≤1.5H时以D为准计算,
D>1.5H时以1.5H为准计算。
6.2 矩形(见图1)
6.2.1 方块类(A≤1.5B)以A为准计算。
6.2.2 扁方类(A>1.5B)以1.5B为准计算。
6.3 空心件(见图2)
H≤T时以1.2H为准计算。
H>T以1.5T为准计算。
6.4 钢锭的当量直径按(冒口端锭身直径+底部端锭身直径)/2计算
图1图2
7 补充规定
7.1 因各种原因在按加热工艺曲线标明的锻造温度下保温结束而无法出炉施压、炉窑温度保持在≥1050℃时,在原保温时间基础上再延长保温的时间极限规定如下(在此时间内允许随时出炉锻压)。
7.1.1 本火次锻比<1.2的常规柜变钢种钢坯及无相变钢种(如护环)钢锭(坯),应竟可能降温,若必须延长,最多可在原保温时间基础上延长20%;
表3 钢种类别及对应锻造温度范围表
表4 (Ⅰ、Ⅱ类钢种)冷钢锭(坯)加热规范
表5 (Ⅲ类钢种)冷钢锭(坯)加热规范。