加工中心对刀原理及方法
加工中心如何对刀步骤详解,会这六步妈妈再也不担心不会对刀了

加⼯中⼼如何对⼑步骤详解,会这六步妈妈再也不担⼼不会对⼑了⾸次使⽤数控加⼯中⼼对⼑存在疑问,随后⼩编就将如何对⼑告诉⼤家吧。
1,回零(返回机床原点)对⼑之前,⼀定要进⾏回零(返回机床原点)的操作,刹车于清除掉上次操作的坐标数据。
注意:X,Y,Z三轴都需要回零。
2,主轴正转⽤“ MDI”模式,通过输⼊指令代码使主轴正转,并保持中等旋转速度。
然后换成“⼿轮”模式,通过转换调节进⾏进⾏机床移动的操作。
3,X向对⼑⽤⼑具在⼯件的右边轻轻的碰下,将机床的相对坐标清零;将⼑具沿Z向提起,再将⼑具移动到⼯件的左边,沿Z向下到之前的同⼀⾼度,移动⼑具与⼯件轻轻接触,将⼑具提起,记下机床相对坐标的X值,将⼑具移动到相对坐标X的⼀半上,记下机床的绝对坐标的X值,并按(INPUT)输⼊的坐标系中即可(发那科系统输⼊“ X0。
”并按“测量”也可以)。
想学ug编程请加Q群699197696群⽂件下载ug学习100G学习资料。
4,Y向对⼑⽤⼑具在⼯件的前⾯轻轻地碰下,将机床的相对坐标清零;将⼑具沿Z向提起,再将⼑具移动到⼯件的后⾯,沿Z向下到之前的⾼度,移动⼑具与⼯件轻轻接触,将⼑具提起,记下机床相对坐标的Y值,将⼑具移动到相对坐标Y的⼀半上,记下机床的绝对坐标的Y值,并按(INPUT)输⼊的坐标系中即可(发那科系统输⼊“ Y0。
”按“测量”也可以)。
5,Z向对⼑将⼑具移动到⼯件上要对Z向零点的表⾯,慢慢移动⼑具⾄与⼯件上表⾯轻轻接触,记下此时的机床的坐标系中的Z向值,并按(INPUT)输⼊的坐标系中即可(发那科系统输⼊“ Z0。
”按“测量”也可以)。
6,主轴停转先将主轴停⽌转动,并把主轴移动到合适的位置,调取加⼯程序,准备正式加⼯。
龙门加工中心的角度铣头对刀的使用方法【技巧】
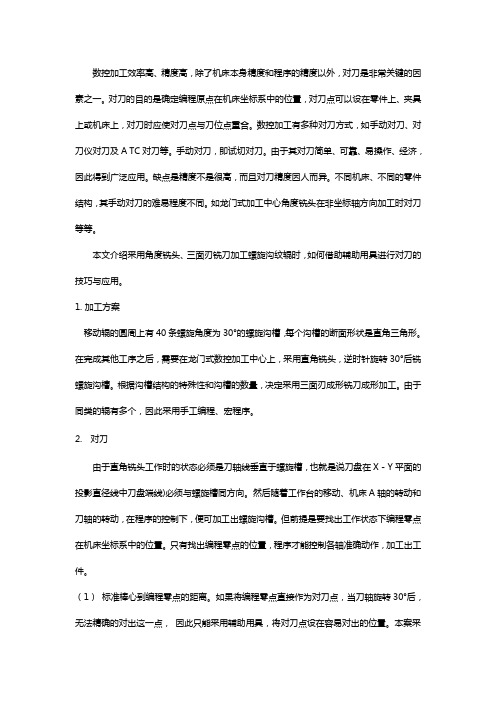
数控加工效率高、精度高,除了机床本身精度和程序的精度以外,对刀是非常关键的因素之一。
对刀的目的是确定编程原点在机床坐标系中的位置,对刀点可以设在零件上、夹具上或机床上,对刀时应使对刀点与刀位点重合。
数控加工有多种对刀方式,如手动对刀、对刀仪对刀及A TC对刀等。
手动对刀,即试切对刀。
由于其对刀简单、可靠、易操作、经济,因此得到广泛应用。
缺点是精度不是很高,而且对刀精度因人而异。
不同机床、不同的零件结构,其手动对刀的难易程度不同。
如龙门式加工中心角度铣头在非坐标轴方向加工时对刀等等。
本文介绍采用角度铣头、三面刃铣刀加工螺旋沟纹辊时,如何借助辅助用具进行对刀的技巧与应用。
1. 加工方案移动辊的圆周上有40条螺旋角度为30°的螺旋沟槽,每个沟槽的断面形状是直角三角形。
在完成其他工序之后,需要在龙门式数控加工中心上,采用直角铣头,逆时针旋转30°后铣螺旋沟槽。
根据沟槽结构的特殊性和沟槽的数量,决定采用三面刃成形铣刀成形加工。
由于同类的辊有多个,因此采用手工编程、宏程序。
2.对刀由于直角铣头工作时的状态必须是刀轴线垂直于螺旋槽,也就是说刀盘在X-Y平面的投影直径线中刀盘端线)必须与螺旋槽同方向。
然后随着工作台的移动、机床A轴的转动和刀轴的转动,在程序的控制下,便可加工出螺旋沟槽。
但前提是要找出工作状态下编程零点在机床坐标系中的位置。
只有找出编程零点的位置,程序才能控制各轴准确动作,加工出工件。
(1)标准棒心到编程零点的距离。
如果将编程零点直接作为对刀点,当刀轴旋转30°后,无法精确的对出这一点,因此只能采用辅助用具,将对刀点设在容易对出的位置。
本案采用圆形标准棒的圆心作为对刀点,具体对刀步骤如下:将一个标准棒固定到工作台面任何位置,为方便可固定在工件附近。
将百分表固定在轴上(机床主轴),测得标准棒X方向最外缘点到移动辊端的距离L,又根据已知的标准棒直径和螺旋槽起点到辊端的距离h算出标准棒心到编程零点的距离X为L+h-d/2。
加工中心对刀与刀具补偿操作教程

加工中心对刀与刀具补偿操作教程时间:2012-05-30 作者:模具联盟网点击: 1479 评论:0 字体:T|T一、对刀对刀方法与具体操作同数控铣床。
二、刀具长度补偿设置加工中心上使用的刀具很多,每把刀具的长度和到 Z 坐标零点的距离都不相同,这些距离的差值就是刀具的长度补偿值,在加工时要分别进行设置,并记录在刀具明细表中,以供机床操作人员使用。
一般有两种方法:1、机内设置这种方法不用事先测量每把刀具的长度,而是将所有刀具放入刀库中后,采用 Z 向设定器依次确定每把刀具在机床坐标系中的位置,具体设定方法又分两种。
( 1 )第一种方法将其中的一把刀具作为标准刀具,找出其它刀具与标准刀具的差值,作为长度补偿值。
具体操作步骤如下:①将所有刀具放入刀库,利用 Z 向设定器确定每把刀具到工件坐标系 Z 向零点的距离,如图 5-2 所示的 A 、 B 、 C ,并记录下来;②选择其中一把最长(或最短)、与工件距离最小(或最大)的刀具作为基准刀,如图 5-2 中的 T03 (或 T01 ),将其对刀值 C (或 A )作为工件坐标系的 Z 值,此时 H03=0 ;③确定其它刀具相对基准刀的长度补偿值,即 H01= ±│ C-A │, H02= ±│ C-B │,正负号由程序中的 G43 或 G44 来确定。
④将获得的刀具长度补偿值对应刀具和刀具号输入到机床中。
( 2 )第二种方法将工件坐标系的 Z 值输为 0 ,调出刀库中的每把刀具,通过 Z 向设定器确定每把刀具到工件坐标系 Z 向零点的距离,直接将每把刀具到工件零点的距离值输到对应的长度补偿值代码中。
正负号由程序中的 G43 或 G44 来确定。
2、机外刀具预调结合机上对刀这种方法是先在机床外利用刀具预调仪精确测量每把在刀柄上装夹好的刀具的轴向和径向尺寸,确定每把刀具的长度补偿值,然后在机床上用其中最长或最短的一把刀具进行 Z 向对刀,确定工件坐标系。
数控车床对刀的原理及方法之欧阳音创编

一、数控车床对刀的原理:对刀是数控加工中的主要操作和重要技能。
在一定条件下,对刀的精度可以决定零件的加工精度,同时,对刀效率还直接影响数控加工效率。
仅仅知道对刀方法是不够的,还要知道数控系统的各种对刀设置方式,以及这些方式在加工程序中的调用方法,同时要知道各种对刀方式的优缺点、使用条件等。
一般来说,数控加工零件的编程和加工是分开进行的。
数控编程员根据零件的设计图纸,选定一个方便编程的工件坐标系,工件坐标系一般与零件的工艺基准或设计基准重合,在工件坐标系下进行零件加工程序的编制。
对刀时,应使指刀位点与对刀点重合,所谓刀位点是指刀具的定位基准点,对于车刀来说,其刀位点是刀尖。
对刀的目的是确定对刀点,在机床坐标系中的绝对坐标值,测量刀具的刀位偏差值。
对刀点找正的准确度直接影响加工精度。
在实际加工工件时,使用一把刀具一般不能满足工件的加工要求,通常要使用多把刀具进行加工。
在使用多把车刀加工时,在换刀位置不变的情况下,换刀后刀尖点的几何位置将出现差异,这就要求不同的刀具在不同的起始位置开始加工时,都能保证程序正常运行。
为了解决这个问题,机床数控系统配备了刀具几何位置补偿的功能,利用刀具几何位置补偿功能,只要事先把每把刀相对于某一预先选定的基准刀的位置偏差测量出来,输入到数控系统的刀具参数补正栏指定组号里,在加工程序中利用T 指令,即可在刀具轨迹中自动补偿刀具位置偏差。
刀具位置偏差的测量同样也需通过对刀操作来实现。
生产厂家在制造数控车床,必须建立位置测量、控制、显示的统一基准点,该基准点就是机床坐标系原点,也就是机床机械回零后所处的位置。
数控机床所配置的伺服电机有绝对编码器和相对编码器两种,绝对编码器的开机不用回零,系统断电后记忆机床位置,机床零点由参数设定。
相对编码器的开机必须回零,机床零点由机床位置传感器确定。
编程员按工件坐标系中的坐标数据编制的刀具运行轨迹程序,必须在机床坐标系中加工,由于机床原点与工件原点存在X向偏移距离和Z向偏移距离,使得实际的刀尖位置与程序指令的位置有同样的偏移距离,因此,须将该距离测量出来并设置进数控系统,使系统据此调整刀具的运动轨迹,才能加工出符合零件图纸的工件。
数控加工中心对刀原理及设置方法探讨

’ I与 应 用
学 术 论 坛
数控加工 中心对刀原理及设置方法探讨
葛 莹
( 安徽蚌埠机 电技师学院 安徽蚌埠 2 3 3 0 0 0 )
摘要: 在我 国高等教 育大众化 不断推进 的形势下提 高学生动 手 实操 能力成 为 高职 院校 培养符合社 会 需求人 才的重要手段 。 文章采用理论 结合 实 践 的方 法, 就数控加 工 中心对 刀方 法及应 用进 行 了总结 与分析, 提 高学 生动手 实操 能 力方 面提供 有益 借鉴 。 关键 词: 数控识 码: A 文章编 号: 1 0 0 7 — 9 4 1 6 ( 2 0 1 3 ) 1 1 - 0 2 1 9 - 0 1
随着 人类科技的进 步, 机械产品的产品质量 和复杂程度越来越 方法3 : 算出此时X坐标值 除以2 的值( 以a 表示) , 注意+ / - 号, 同 高。 因此数控机床应运而生 , 成为提高产品质量和生产效率的重要 上方法进入NG 5 4 , 输入x a , 按软键盘【 测量】 , 用这种方法就可 以不用 工具。 而数控加工 中心刀具与工件坐标系 的建立是数控加工 中的重 将刀具移至工件 中心 。 要 内容之一 , 建立 正确 的工件坐标系 , 可 以保证系统正常 的执行程 第 四步 , 按 上述 步骤 和 方 法 对 Y 轴 分 中并 设 置 G 5 4 的 Y。 2. 1 . 2 用纸 片X、 Y方 向 上 的 对 刀方 法 序, 避免 发生各种机床的误动作 , 造成刀具 、 机 床损 坏 , 甚至可能伤 ( 1 ) 将机床操作模 式切换为“ 手轮模式” , 用手轮方 式进行对刀 。 害人员等重大事故 。 因此, 如何正确地进行对刀 , 就成为我们在教学 ( 2 ) 装夹好刀具 , 注意刀具的伸出长度在 与工件 、 夹具不干涉的情 况 实操 中必须解决 的问题 。 下, 尽量伸 出来短 , 以增强刀具的刚性 。 ( 3 ) 纸片对刀方法原理同寻边 1数 控加 工 中 的 对 刀原 理分 析 器对刀原理 , 但有以下3 个应注意的 问题 : 1 ) 在安装并校正好 的毛坯 工件在机床上 定位装夹后 , 必 须确定工件在机 床上的正确位 四个侧 面及 上表面粘 上有油 的薄 纸片 ; 2 ) 使主轴 中速旋转( 6 0 0~ 置, 以便 与机 床原 有的坐标系联系起来。 确定工件具体位置 的过程 8 0 0 P R M) ; 3 ) 若铣刀接触到工件侧面的纸片 , 纸片会随着 主轴的旋转 就是通过对刀来实现的 , 而这个过程的确定也就是在确定工件 的编 而移动 。 当然也可 以用一只手调节手轮 , 另一只手不停拉动纸片 , 直 程坐标系( 即工件坐标系) , 编程加工都是参照这- i ' -  ̄标系来进行 的。 到拉动纸片时 , 纸片上有划痕 或划破的痕迹 , 就说明刀具与工件表 在零件 图纸上建立工件坐标系, 使零件上 的所有几何元素都有确定 面 已接触到了 , 但此 种方法刀具是不能旋转 的。 的位置 , 而工件坐标系原点是以零件 图上的某一特征点为原点建立 2 . 2 Z方 向 对 刀 法 与 应 用 坐标系 , 使得编程坐标系与工件坐标系 重合 。 2. 2. 1 用Z轴 设 定 器Z方 向对 刀 方 法 对刀操作主要包含三个关键点: 一是刀具上 的刀位点与对刀点 ( 1 ) Z 轴设定器有一 定高度 , 一般是5 0 -1 0 0 am之 间, r 首先 需将 重合 ; 二是编程原点与机床参考 点之 间建立某种联系 ; 三是通过数 Z 轴设定器调好零位 。 对刀时 , 将 设定器放在工件上表面上。 ( 2 ) 移 控代码指令确定刀位点与工件坐标系位置。 其中刀位点是刀具上的 动刀具 , 注意此时主轴 不能旋转 , 使 刀尖渐渐靠近并接触z 轴设定 个基准 点( 车刀 的刀 位点 为刀尖 , 平头立铣刀 的刀 位点为端面 中 器 , 使表针对… 0, 此处我 们假定使用 的z 轴设定器高度为5 0 am, r 然 心, 球头刀的刀位点通常为球心) , 刀位点相对运动 的轨迹就是编程 后进入  ̄ ] 1 G 5 4 页面 , 输入Z 5 0 , 按软键盘[ 测量】 。 轨迹 , 而 对 刀 点 就 是 加 工零 件 时 , 刀具 上 的 刀位 点相 对 于 工件 运 动 2. 2 . 2 用 滚 刀 Z方 向 对 刀 方 法 的起 点。 多数 情况下, 对刀点应选在工件坐标系的原点上 , 这不仅有 我们用一把刀具放在工件上表面上 , 注意此时主轴 不能旋转 , 利于保证对刀精度 , 也可 以将对刀点或对刀基准设在 夹具定位元件 使刀尖渐渐靠近并接触我们滚动放在工件表面上的刀具。 此处我们 上, 有利于零件 的批量 加工 。 假设用 的是 1 6 am的刀具 , r 然后进入 ̄ I J G 5 4 页面 , 输入Z 1 6 . , 按软 在数控立 式铣 加工 中 t i ,  ̄ I 工 操作 中 , 对刀的方法 比较多 , 本文 键盘[ 测量】 。 就常用的几种对刀方法 的实践应用 , 作 以下探讨 。 2 . 2 . 3 用纸 片Z 方 向对 刀方 法 方法1 : 我们在 工件上表面粘上有油的纸片 , 此时刀具用 中速旋 2加 工 中心 的对 刀方 法及 其 应 用 转, 当刀具接触工件上表面粘油的纸片 , 纸片会随着刀具的旋转而 2 . 1 X、 Y方 向 对 刀 法 与 应 用 移动 , 此处我们假设纸片 的厚度为0 . 1 mm, 然后进入到G5 4 页面, 输 2 . 1 . 1利用寻边器x、 Y方向上的对 刀方法 入Z 0 . 1 . , 按软键盘[ 测量】 。 ( 1 ) 在工作 台上用平 口钳夹好工件 , 注意装平、 装正、 装实的六字 方法2 : 我们在工件上表面放上纸片 , 此时刀具不能旋转 , 用一 原则 , 还需根据零件的加工深度确定好工件伸 出平 口钳 的高度 , 以 只手调节手轮 , 另一只手不停拉动纸片 , 直到拉动纸片时, 纸片上有 免加工 中过切平 口钳 台面 。 ( 2 ) 装夹好寻边器。 寻边器对刀精度较高 , 划痕 或划破 的痕迹 , 此处 我们假设纸片 的厚度为0 . 1 am, r 然后进入 操作 简便 、直观、应用广泛 。 采用寻边器对 刀要求定位基准面应有  ̄ J I G5 4 页面 , 输入 z 0 . 1 . , 按软键盘[ 测量 】 。 较好的表面粗糙 度和直线度 , 确保对刀精度。 ( 3 ) 屏幕上机床坐标切 此外 , 关于Z 向对刀 , 我们也可以使用标 准量块对刀 , 其原理和 换为相对 坐标界面。 ( 4 ) 将机床操作模式切换为“ 手轮模式 ” , 用手轮 方 法 是 相 通 的 。 方式进行对 刀。 ( 5 ) 对X轴分中, 具体 步骤为 : 第一步 , 移动工作台 , 使 寻边器通过调节x 轴 工作 台的移动速度渐渐 靠近并接触工件左侧 3结 语 面, 如果是偏置式寻边器 , 就看上下棒体是否 同心 , 如果是 电子式寻 综上所述 , 在当前工业生产当 中, 数控机床应用 已获得了广泛 边器 , 就会发出警报声及亮警示灯。 第二步, 提刀 , 并将此时的X 坐标 的应用 。 因此 , 一些 高职 院校开设 的机 电工程相 关专业为培养学生 值清零( 在屏幕上输入X, 按软键[ 起源】 ) 。 第三步 , 步骤 与第一步相 同, 动手实操能力 , 也购买了数控机床设备。 在教学实践 当中, 我们应不 使刀 具接 触工件的右侧面 , 提刀。 常采用的方法有 以下三种 : 断积累经验 , 就常见 的问题及解决方法加 以总结 , 从 而更好地提高 方法1 : 算 出此时x 坐标值 除以2 的值 , 并把刀具移至该点 , 则此 学生动手实操能力。 本文就加工 中心操作中常用的对刀 方法与技巧 时刀位点所在 位置 即为工件x向的中点 , 按MD I 键盘 上的O F F S E T 进行了分析与探讨 , 希望 能为相 关研究起到抛砖 引玉 的作用 。 S E T TI NG键 , 按软 键[ 坐 标系】 进入 工件坐标 系界面 , 将 光 标 移 至 参 考 文 献 G 5 4 , 输入X0 , 按软键盘【 测量】 。 1 ] 岳玲. 数控加工 中对刀 问题的处理[ J ] . 宁夏机械. 2 0 0 6 ( 0 4 ) . 方法 2 : 算出此时X 坐标值 除以2 的值 ( 以a 表示) , 在屏幕 上输入 [ [ 2 ] 张跃平. 在铣床 上刃磨铣刀 的简易方法[ J ] . 科技信息. 2 0 1 0 ( 1 3 ) X a , 按软键颐 定】 , 则相对坐标X= 0 的位置即为工件x向的 中点 , 将刀 具移动到x坐标 为零 的点 , 设置G 5 4 的X同方法1 。
数控工艺第五章第二节数控车削加工件的装夹及对刀

( 2 ) 尺寸标注方法分析 零件图上尺寸标注方法应适应数控车床加工的特点,应以同 一基准标注尺寸或直接给出坐标尺寸。这种标注方法既便于编程,
又有利于设计基准、工艺基准、测量基准和编程原点的统一。
( 3 ) 精度及技术要求分析 对被加工零件的精度及技术要求进行分析是零件工艺性分析
的重要内容,只有在分析零件尺寸精度和表面粗糙度的基础上,
一般来说,编程原点的确定原则为: ( l ) 将编程原点选在设计基准上并以设计基准为定位基准,这样可避免 基准不重合而产生的误差及不必要的尺寸换算。如图5-33 所示零件,批量 生产,编程原点选在左端面上。 ( 2 ) 容易找正对刀,对刀误差小。如图5-33 ,若单件生产,G92 建立工 件坐标系,选零件的右端面为编程原点,可通过试切直接确定编程原点在z 向的位置,不用测量,找正对刀比较容易,对刀误差小。
的坐标值就是指刀位点的坐标值;自动编程时程序输出的
坐标值就是刀位点在每一有序位置的坐标数据,刀具轨迹 就是由一系列有序的刀位点的位置点和连接这些位置点的 直线(直线插补)或圆弧(圆弧插补)组成的。
( 2 ) 起刀点它是刀具相对零件运动的起点,即零件
加工程度开始时刀位点的起始位置,而且往往还是程序 运行的终点。有时也指一段循环程序的起点。
编程原点安装后的位置采用其他方法对刀确定。
5.3 数控车削加工工艺制定
工艺分析是数控车削加工的前期工艺准备工作。 工艺制定得合理与否,对程序编制、机床的加工效率 和零件的加工精度都有重要影响。因此,应遵循一般 的工艺原则并结合数控车床的特点,认真而详细的制
定好零件的数控车削加工工艺。其主要内容有:分析
零件图纸、确定工件在车床上的装夹方式、各表面的 加工顺序和刀具的进线路线以及刀具、夹具和切削用 时的选择等。
数控铣床(加工中心)对刀方法的研究与实践
数控铣床(加工中心)对刀方法的研究与实践作者:聂小春汪菊英孙晓辉来源:《科技资讯》 2012年第32期聂小春汪菊英孙晓辉(广州工程技术职业学院广东广州 510450)摘要:本文结合使用数控铣床、加工中心(采用FUNAC0i-mate数控系统)的实际经验,控讨了几种常用的数控铣床(加工中心)的对刀方法。
关键词:刀位点工件坐标系对刀方法调刀补中图分类号:TG547 文献标识码:A 文章编号:1672-3791(2012)11(b)-0047-01我们在数控铣床(加工中心)上自动加工零件前,首先一定要确定工件坐标系,这个坐标系是编程人员以工件上的某一点为坐标原点建立的一个坐标系,是用来定义工件形状和刀具相对工件运动的坐标系。
那么如何在机床上确定工件坐标系呢,这就是本文所要探讨的对刀问题。
对刀是数控铣床(加工中心)加工中的主要操作和重要技能,所谓对刀就是使刀具的刀位点与工件坐标系原点重合,也即就是测量工件坐标系原点与机床原点之间的偏移距离(工件坐标系原点在以刀位点为参照的机床坐标系里的坐标值)。
对刀的方法有很多种,本文以数控铣床、加工中心(采用FUNAC0I-mate数控系统)为例介绍几种常用的对刀方法,本文约定以工件坐标系原点在工件上表面中心处为例。
1 用分中棒X、Y方向上的对刀方法(1)在工作台上用平口钳夹好工件,注意装平、装正、装实的六字原则,还需根据零件的加工深度确定好工件伸出平口钳的高度,以免加工中过切平口钳台面。
(2)装夹好分中棒;(分中棒又叫寻边器,是在CNC数控加工中,用于精确确定被加工工件的中心位置的一种检测工具,因为生产的需要分中棒有不同的类型,如光电式偏置式等,比较常用的是偏置式。
应用光电式分中棒分中时,不需要主轴旋转,精度可达±0.005 mm,应用偏置式分中棒分中时,主轴以400~600 RPM的速度转动)。
(3)屏幕上机床坐标切换为相对坐标界面。
1.1 将机床操作模式切换为“手轮模式”,用手轮方式进行对刀1.2 对X轴分中,具体步骤为(1)移动工作台,使分中棒通过调节X轴工作台的移动速度渐渐靠近并接触工件左侧面,如果是偏置式分中棒,就看上下棒体是否同心,如果是电子式分中棒,就会发出警报声及亮警示灯。
数控加工技术培训教材.pdf
国内�华中系统�见图 1�6�、航天系统、广州数控系统、大森系统
图 1�6
6
健雄职业技术学院
数控加工技术
国外�西门子系统�见图 1�7�、发那科系统�见图 1�8�、三菱系
统、飞利浦系统、发格系统
机床带系统�美国�幸辛那提、法道、哈斯
日本�马扎克、森精机、新日本、戴维
德国�德马吉、科宝
瑞士�米克朗
有自动化仓库。
�4�有管理信息系统�如刀具与机床的利用率报告
5、计算机集成制造系统 CIMS
有三个系统�
�1�CAD/CAM 系统�产品造型
性能分析、仿真 生成
程序
�2�CAP/CAC 系统�计算机辅助生产计划与计算机辅助生产控
制系统�对加工过程进行计划、调度与控制。�1�+�2�完成无图纸
加工。
�3�工厂自动化系统�实现产品的自动装配、测试�材料的自
动运输处理�工厂管理的自动化。�1�+�2�+�3�=无人工厂数控
机床是最基本的工作单位。
五、几个基本概念
1、数控�一种自动化控制技术�用数字信号控制机床的运动和加工
过程。
2、数控机床�采用了数控技术的机床�或者说是装备了数控系统的
机床。
3、数控系统�一种程控系统�能逻辑的处理输入到系统中具有特定
4
图 1�7
图 1�8
3、伺服系统�是数控系统的执行机构�它接受数控系统的指令信息�按
指令信息的要求控制执行部件的进给速度、方向和位移。它包括�
�1�进给伺服系统�进给运动的执行机
构�包括位置控制单元、速度控制单元、
执行电动机�见图 1�9�、测量回馈单元
等部分�见图 1�10�。
数控铣床/加工中心刀具的对刀方法和技巧
数控铣床/加工中心刀具的对刀方法和技巧以宇龙数控加工仿真软件为教学手段,介绍了SIEMENS 802D数控系统不同工件原点G54-G59建立工件坐标系的方法和技巧,为教学实施提供了有效途径。
标签:仿真软件数控对刀工件坐标系工件坐标系又称编程坐标系,是编程人员为方便编写数控程序人为建立的坐标系,一般建立在工件上或零件图样上,通过对刀操作将工件原点在机床坐标系中的位置(偏移量)输入到数控系统相应的储存器(G54、G55等)中,以实现机床坐标系与工件坐标系的重合。
本文以SIEMENS 802D数控系统为例,详细介绍了数控铣床/加工中心的对刀方法和技巧。
1 SIEMENS 802D数控铣床/加工中心刀具的对刀方法在数控编程教学中,工件坐标系原点的设定一般有两种情况:一是建立在工件上表面中心;二是建立在工件上表面角点上。
下面以工件原点设定在工件上表面中心为例说明对刀方法。
1.1 X、Y轴对刀铣床及加工中心通常借助寻边器、刚性靠棒等基准工具在X,Y方向对刀。
笔者仅针对刚性靠棒进行具体说明。
在菜单栏点击“机床/基准工具…”,弹出基准工具对话框,就能看到图1所示的左右排列的刚性靠棒和寻边器。
刚性靠棒通过检查塞尺松紧方式来对刀,具体过程如下(笔者拟用把零件放在基准工具左侧(正面视图)的方式进行说明)。
X轴方向对刀:Y方向对刀采用同样的方法。
1.2 Z轴对刀在系统面板上选择用来保存工件坐标原点的位置(此处同样选择G54);在“设置位置Z0”文本框中输入塞尺厚度,并按下回车键;点击软键“计算”,就能得到工件坐标系原点的Z分量在机床坐标系中的坐标,此数据将被自动记录到参数表中。
2 SIEMENS 802D数控铣床刀具的对刀技巧在数控编程课程教学中,应用宇龙数控仿真加工软件练习对刀操作,在学生熟练掌握了对刀操作后,在后面学习过程中,没有必要每次都进行对刀操作,有必要进行简化。
2.1 工件上表面中心为工件原点在放置零件时,弹出对话框中,上、下、左、右不要移动,直接点击退出。
加工中心操作中常用对刀方法比较
关键词 : 对刀仪 ; z向设定器 ; 试切法 ; 机上对 刀
0 引 言
数控 加工 中心刀 具 与工件 坐 标 系 的建立 是 数控 加 工 中 的重 要 内容 之一 ,建 立 正确 的工 件 坐标 系 ,可 以保 证 系统 正 常 的执 行程
点在机 床 坐标 系 中的位 置 。其 几种 常用 的对 刀 方法 介绍 如下 。
G0 un三主 。 i 比较
简正豪 高 飞
( 昌工 学院, 南 江西 南 昌 3 0 0 ) 3 1 8 摘
技巧 。
要: 主要对 加工中心水平方 向常用对刀、 加工 中心 z向对 刀进 行了分析 , 比较 了几种 常见对 刀方 法, 并 阐述 了它们 相互间 的实用 范围及
22 机 上 对 刀 .
寻 边器 也称 为 电子 感应 器 , 操作 过程 与 试切 对 刀 法相 似 , 其 只 偿 ; 是将 刀 具换 成 了 寻边器 , 动 距离 是 寻边 器触 头 的半 径 , 此这 种 移 因 方法 简 捷 , 刀 精度 较 高 。 使用 寻 边器 时 , 对 在 是人 为 目测 定位 , 随机 误差 较 大 , 需要 重 复操 作几 次来 确 定 正确 的位 置 , 其重 复 定位 精 度
13 . 采 用 寻 边 器 对 刀
() 得 值 , 5测 即刀 具直 径 , 该尺 寸可 用 作刀 具半 径补 偿 ; () 得 z值 , 6测 即刀 具 长 度 尺 寸 4 该 尺 寸 可用 作 刀 具 长 度 补 , () 测 得尺 寸输 入 加工 中心 的 刀具补 偿 页面 ; 7将 () 被测 刀 具从 对 刀仪 上取 下后 , 8将 即可装 上加 工 中心 使用 。
1 加 工 中心 水平 方 向常 用对 刀
- 1、下载文档前请自行甄别文档内容的完整性,平台不提供额外的编辑、内容补充、找答案等附加服务。
- 2、"仅部分预览"的文档,不可在线预览部分如存在完整性等问题,可反馈申请退款(可完整预览的文档不适用该条件!)。
- 3、如文档侵犯您的权益,请联系客服反馈,我们会尽快为您处理(人工客服工作时间:9:00-18:30)。
加工中心对刀原理及方法
-CAL-FENGHAI.-(YICAI)-Company One1 2
一线员工职业技能等级鉴定 申报论文
(高级技师)
题目:数控加工中心刀具对刀原理方法及其应用!
2016 年 4 月 18 日
单 位: 姓 名: 申报工种:
密级:保密 摘要 数控加工操作中的对刀好坏不仅直接影响到加工零件的精度,还会影响数控机床的操作。 对刀的过程牵涉到一系列的步骤,在实际操作中往往会出现一些具体的问题,因此通过对数控加工中心对刀的基本原理、对刀的方法并结合具体的数控加工中心的操作特点对对刀方法进行了阐述。
关键词:数控加工中心;对刀原理;对刀方法 目录 摘要 ........................................................................................................... 错误!未定义书签。
绪论 .......................................................................................................................................... 4
一、对刀基本原理 ................................................................................................................ 5
二、对刀基本方法及运用 ................................................................................................... 5
、 用对刀探头对刀.............................................................................................. 6 用机外对刀仪对刀.......................................................................................... 6 用对刀器对刀…………………………………………………………………………………………………..… 7 用试切法对刀……………………………………………………………………………………………………..8 结论.............................................................................................................................. 11 参考文献...................................................................................................................... 12 绪论 数控加工操作中的对刀好坏不仅直接影响到加工零件的精度,还会影响数控机床的操作。 当工件坐标系确定之后,还要确定刀位点在工件坐标系中的位置。也就是确定工件坐标系与机床坐标系之间的关系,要让刀具在数控程序的控制下使加工对象相对于定位基准有正确的尺寸关系。 由于数控机床所用的刀具各种各样,刀具寸也极不统一。在编制加工中心数控程序时,一般不考虑刀具规格及安装位置,加工前由操作者通过对刀将测出的刀具在主轴上的伸出长度及其直径等补偿参数输入数控系统,进行刀具补偿,通常把这一过程称为对刀。 对刀的过程牵涉到一系列的步骤,如对刀基本原理、对刀方法的选择和对刀参数的设置等等。 在实际操作中往往会出现一些具体的问题,因此通过数控加工中心对刀的基本原理、对刀的方法并结合具体的数控加工中心的操作特点对对刀方法进行了阐述。 一:对刀基本原理 数控加工是通过NC程序精确地、自动地控制刀具,使之相对于工件的运动按照人们预先设计的轨迹或位置进行。程序是在工件坐标系中编写的,编程人员以工件坐标系为基准编写,而刀具加工工件是在数控机床上进行的,如何确定工件坐标系与机床坐标系之间的位置关系,需要通过对刀来完成,具体就是确定刀具的刀位点在工件坐标系中的起始位置,通常把这个位置称为对刀点。 对刀点是刀具相对于工件运动的起点。 由于程序段从该点开始执行,所以对刀点又称为“起刀点”或“ 程序起点”’往往也作为程序的终点。 对刀点的选择原则是1: 便于数学处理和简化程序编制; 2:在机床上容易找正,在加工中便于检查;3: 引起的加工误差要小. 根据前两条,对于绝对坐标系统的数控机床,对刀点可选择在机床坐标系的原点上,或距机床坐标系原点为某一确定的点上。4:对刀点应尽量选在零件的设计基准或工艺基准上。 要确定对刀点在工件坐标系中的起始位置,则需要首先确定刀位点。刀具刀位点是指刀具在机床上的位置。 对于不同的刀具,刀位点选择是不同的。 对立铣刀和端面铣刀而言,刀位点为其底面中心;对于球头铣刀,则为球头的球心;对于车刀、镗刀和钻头等刀具来说,则为其刀尖或钻尖。对刀时应使对刀点和刀位点重合。 二:对刀基本方法及应用 对刀方法有好几种,在应用的时候不是千篇一律的,要针对不同情况采用不同的对刀方法灵活使用,这样才能收到好的效果。下面简图要介绍几种常用的对刀方法。 用对刀探头对刀 每把刀具用对刀探头对好,刀具长度数据会自动记录到刀具列表中。 在设置工件零点时取任意刀具作为基准,把其刀尖移到工件零点位置设置工件零点,此时Z轴方向坐标值要减去作为基准刀的刀长值才为其Z轴工件零点坐标系。 现在很多数控加工中心上都装备了对刀探头,使用对刀探头对刀可免去测量时产生的误差,大大提高对刀精度。 由于使用对刀探头可以自动计算各把刀的刀长和刀宽的差值,并将其存入系统中,在加工另外的零件的时候就只需要设置工件零点Z轴坐标系即可,这样就大大节约了时间。 用机外对刀仪对刀 用机外对刀仪测量其刀具的长度和半径,然后输入到刀具列表中作为刀具长度补偿值,此时在设置工件零点时也取任意刀具作为基准,把其刀尖移到工件零点位置设置工件零点,此时Z轴方向坐标值要减去作为基准刀的刀长值才为其Z轴工件零点坐标系。 机外对刀是指刀具在安装之前事先在对刀仪上进行预调整和测量出实际尺寸值,然后将所测数据输入到相应寄存器。 目前对刀仪种类很多,有直接接触式测量和光屏投影放大测量,从读数方法看,有圆盘刻度或游标读数,也有用光学读数的或数字显示器读数的,目前还有用计算机显示和打印输出测量值的对刀仪(如德国的目的。ZOLLER对刀仪、瑞士的TPR3 对刀仪等),对刀时刀具放在对刀仪的刀座上,用光学(或其它接触测量仪) 测出刀位点相对刀具定位基准的偏差值。如图1所示就是显示器读数的对刀仪,将刀具安装在刀座上后调整X或Z,如图2所示使百分表指针对到零,就可在显示器上看到刀具直径和长度上的数据, 采用机外对刀仪对刀可以大大节省机床的对刀时间,提高数控机床的使用效率。
图1 机外对刀仪 图2 :用对刀器对刀 用任意一把刀具作为基准刀,在某一固定位置把此刀的刀具长度补偿数值设为某一固定数据( 最好设为0),其他的刀具长度补偿数值以此刀为基准相对于基准刀的固定位置长短,在基准刀的固定数据上加减。在设置工件零点时,把基准刀具刀尖移到工件零点位置设置工件零点,此时Z轴方向坐标值就为工件的Z轴零点坐标系值。使用时先将对刀器、工作台及工装表面等擦净,先校正基准刀,如图3所示当基准刀向下压到对刀器测量面时,对刀器指示灯会
百分表指到零 X向
Y向 显示器 亮,这时把机床显示屏上相对坐标Z方向清零,设定基准刀刀具长度补偿数值为0,再将所需要用的刀具依次在对刀器上同对基准刀方法一样对刀,与基准刀相比较长短来设定该刀的刀具长度补偿数值,然后将所得到数值输入到所对应刀具号的长度补偿位置即可。
图3 对刀器
在设定坐标系时(即在设置工件零点时),把基准刀刀尖移到工件零点位置,此时Z轴方向坐标值就为工件的Z轴零点坐标系值,表4 为该工件的Z轴零点坐标系G54, 试切法对刀 在没有上述方法的时候,试切法对刀也是实用的一种对刀方法,此方法比较简单,其具体操作方法:先将工件坐标系的 Z 值输为 0 , 然后把工件和刀具装夹完毕,驱动主轴旋转,如图4所示把所需要的刀具移至工件零点上,然后把机械坐标系Z轴数据写输入到相应刀具的长度补偿值代码中。以下是NKR前轮毂在加工中心上
对刀器 对刀器
测量面
刀具 钻内外五孔的程序和试切对刀法. O5000(NKR) M66 G40 G80 N1 M6 T1 G90 G0 G54 Y0 M13 G43 H1 Z160 T7 S1500 G98 G81 F280
G0 Z160 M9 M5 G80 N2 M6 T7 G90 G0 G54 Y0 M13 G43 H7 Z160 T2 S 1600 G98 G76 F320