750-at003A_2014-3_Application Guidelines for 12-Pulse Operation of PowerFlex
7353基本配置
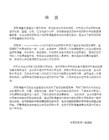
基本命令:
ENT:创建
ED:修改
DLT:删除
RTRV:查看
4.2 查看软件版本
查看软件版本在那个 OSWP中;
REPT-OPSTAT-OSWP::ALL
4.3 查看具体的版本号
RTRV-MEM::OSWP-1
.....................................................
.....................................................
ent-vcl::ltvcl-1-1-1-31-8-81:::;
ent-vcl::ltvcl-1-1-1-32-8-81:::;
DEFROUTER=X.X.X.X为管理的网关
4.6 设置管理VLAN,以及管理模式(INBAND)
SET-MGNT::COM::::MGNTCVLAN=353,MGNTSVLAN=,MGNTPBIT=4,MGNTMODE=INBAND;
MGNTCVLAN=353为管理的VLAN,MGNTPBIT=4为管理的优先级
..................Байду номын сангаас....................................
ENT-VLAN::CVLAN-3095:::CFGMODE=RESBRG;
ENT-VLAN::CVLAN-3096:::CFGMODE=RESBRG;
5.3. 将PROFILE关联至一线并激活该线
IPADDR=X.X.X.X为管理的IP地址,,NETMASK=X.X.X.X为管理IP的掩码
NPort 6150 6250 Series Quick Installation Guide

P/N: 1802061500016 *1802061500016*NPort 6150/6250 Series Quick Installation GuideEdition 9.0, November 2016Technical Support Contact Information/supportMoxa Americas:Toll-free: 1-888-669-2872 Tel: 1-714-528-6777 Fax: 1-714-528-6778 Moxa China (Shanghai office): Toll-free: 800-820-5036 Tel: +86-21-5258-9955 Fax: +86-21-5258-5505 Moxa Europe:Tel: +49-89-3 70 03 99-0 Fax: +49-89-3 70 03 99-99 Moxa Asia-Pacific:Tel: +886-2-8919-1230 Fax: +886-2-8919-1231 Moxa India:Tel: +91-80-4172-9088 Fax: +91-80-4132-10452016 Moxa Inc. All rights reserved.OverviewThe NPort 6150/6250 series secure serial device servers provide reliable serial-to-Ethernet connectivity for a wide range of serial devices. The NPort 6150/6250 support TCP Server, TCP Client, UDP, andPair-Connection operation modes to ensure the compatibility of network software. In addition, the NPort 6150/6250 also support Secure TCP Server, Secure TCP Client, Secure Pair-Connection, and Secure Real COM modes for security critical applications such as banking, telecom, access control, and remote site management.Package ChecklistBefore installing a NPort 6150/6250 secure device server, verify that the package contains the following items:• 1 NPort 6150 or NPort 6250•Power adapter (does not apply to -T models)• 2 wallmount ears•Documentation and software CD•Quick installation guide (this guide)•Warranty cardOptional Accessories•DK-35A: DIN-rail mounting kit (35 mm)•DIN-rail power supply•CBL-RJ45M9-150: 8-pin RJ45 to male DB9 cable•CBL-RJ45M25-150: 8-pin RJ45 to male DB25 cableNOTE: Please notify your sales representative if any of the above items are missing or damaged.Hardware IntroductionNPort 6150NPort 6250Reset Button—Press the Reset Button continuously for 5 sec to load factory defaults. Use a pointed object, such as a straightened paper clip or toothpick, to press the reset button. This will cause the Ready LED to blink on and off. The factory defaults will be loaded once the Ready LED stops blinking (after about 5 seconds). At this point, you should release the reset button.LED IndicatorsAdjustable pull high/low resistor for RS-422/485 (150 K Ω or 1 K Ω)Jumpers are used to set the pull high/low resistors. The default is 150 kΩ. Short the jumpers to set this value to 1 kΩ. Do not use the 1 kΩ setting with RS -232 mode, since doing so will degrade the RS-232 signals and shorten the communication distance.Hardware Installation ProcedureSTEP 1: Connect the 12-48 VDC power adaptor to the NPort 6150 andthen plug the power adaptor into a DC outlet.STEP 2: For first-time configuration, use a cross-over Ethernet cable toconnect the NPort 6150 directly to your computer’s Ethernet cable. For connecting to a network, use a standardstraight-through Ethernet cable to connect to a hub or switch.STEP 3: Connect the NPort 6150’s serial port to a serial device.Placement OptionsThe NPort 6150/6250 can be placed flat on a desktop or other horizontal surface. In addition, you may use the DIN-rail or wallmount options, as illustrated below.WallmountDin RailSoftware Installation InformationThe Documentation and software CD contains the user’s manual, NPort Search Utility, and the PComm Lite Suite. Insert the CD into yourcomputer’s CD-ROM drive and follow the on-screen instructions. Please refer to the user’s manual for additional details on using the NPort Search Utility and PComm Lite.Pin Assignments and Cable WiringTwo serial cables for connecting the NPort 6150 to a serial device can be purchased separately. The wiring diagrams for the two cables are shown below.。
安装说明书:PowerFlex 750 系列选件模块

Installation InstructionsOriginal InstructionsPowerFlex 750-Series Option ModulesCatalog Numbers 20-750 Series and 20-750 Series -XTSummary of ChangesThis publication contains the following new or updated information. This list includes substantive updates only and is not intended to reflect all changes. These instructions cover the installation of the option modules that are listed in the Compatible Ports figure and table. For wiring and jumper settings for these modules, see the PowerFlex® 750-Series I/O, Feedback, and Power Option Modules Installation Instructions, publication 750-IN111. For information on access to the drive control pod and how to install network communication and safety option modules, see the publications that are listed in Additional Resources .Option module catalog numbers that are used in this publication are for the standard protection versions. Select option modules are available with corrosive gas protection and contain an "XT" catalog number suffix.The instructions in this publication apply to both standard and XT option modules unless otherwise noted.TopicPage Summary of Changes 1Compatible Ports2Option Module Installation2Using Option Modules 20-750-S1 / 20-750-S4 with Option Modules 20-750-DENC-1 / 20-750-UFB-13Auxiliary Power Supply (20-750-APS) Installation3Option Module Installation Next to a PROFIBUS Option Module 411-Series and 22-Series I/O Module Installation4TopicPage Updated the S1 Row of the Compatible Ports table.2Added an Important statement regarding dielectric grease covers on XT option modules in the Option Module Installation section2Added an example figure to show the protective cover removal for edge connectors with dielectric grease in the Option Module Installation section3IMPORTANTOnly one safety option module can be installed at a time. Simultaneous safety option installations are not supported.2Rockwell Automation Publication 750-IN002K-MU-P - May 2021PowerFlex 750-Series Option Modules Installation InstructionsCompatible PortsOption Module InstallationT o install an option module, follow these steps1.Press the module edge connector firmly into the desired port.2.Tighten the top and bottom retaining screws.Option Module Cat. No. 20-750-PowerFlex 753 Drives PowerFlex 755 DrivesPowerFlex 755T DrivesFrame 1 Ports Frame 2…7 Ports Frame 1 Ports Frame 2…10 Ports Frame 5...15 Ports 65465465487654876541132C-2R, 1133C-1R2T,1132D-2RNoYesYesYesYesYesNoYesYesYesYesYesYesYesYesYesYesYesYes1132C-2R, 1133C-1R2T, 1132D-2Rwith 20-750-ATEX installed (1)(1)For detailed instructions on installation of 11-Series I/O with the ATEX option module, see the PowerFlex 750-Series ATEX User Manual, publication 750-UM003.No Yes Yes No Yes Yes No Yes Yes No No No Yes Yes No No No Yes Yes2262C-2R, 2263C-1R2T, 2262D-2R No Yes Yes Yes Yes Yes No Yes Yes Yes Yes Yes Yes Yes Yes Yes Yes Yes Yes APS See Page 3See Page 3See Page 3YesNo No No No Yes No No No No DENC-1(2)No Yes Yes Yes Yes Yes No Yes Yes No No Yes Yes Yes No No Yes Yes Yes ENC-1No Yes Yes Yes Yes Yes No Yes Yes Yes Yes Yes Yes Yes Yes Yes Yes Yes Yes S Yes Yes Yes Yes Yes Yes Yes Yes Yes Yes Yes Yes Yes Yes Yes Yes Yes Yes Yes S1(2)(2)See Using Option Modules 20-750-S1 / 20-750-S4 with Option Modules 20-750-DENC-1 / 20-750-UFB-1.YesNoYesYesYesNoYes No Yes No No Yes Yes No No No Yes Yes Yes S3/S4(2)(3)(3)Must be installed in port 6 for integrated motion.Not Supported Yes No Yes No No Yes Yes Yes No No Yes Yes Yes UFB-1Not SupportedNoYesYesNoNoYesYesYesNoNoYesYesYesATTENTION:•Electric shock hazard. Verify that all sources of AC and DC power are de-energized and locked out or tagged out in accordance with the requirements of ANSI/NFPA 70E, Part II.•To avoid an electric shock hazard, verify that the voltage on the bus capacitors has discharged before performing any work on the drive. Measure the DC bus voltage at the +DC and -DC terminals or test points. The voltage must be zero.For the location of the terminal block and test point sockets, see the manual for your drive:•PowerFlex 750-Series AC Drives Installation Instructions, publication 750-IN001.•PowerFlex 750-Series Products with TotalFORCE® Control Installation Instructions, publication 750-IN100.•PowerFlex 755TM IP00 Open Type Kits Installation Instructions, publication 750-IN101.•In Safe Torque Off mode, hazardous voltages may still be present at the motor. To avoid an electric shock hazard, disconnect power to the motor and verify that the voltage is zero before performing any work on the motor.IMPORTANTFor XT option modules, protective covers on connectors must be removed before installation. To maintain corrosion resistance, do not touch dielectric grease on circuit board connectors.For additional information on dielectric grease and protective covers, see the PowerFlex 750-Series Products with TotalFORCE Control Hardware Service Manual, publication 750-TG100, Chapter 1: Dielectric Grease Application20-750-APS20-750-S20-750-S120-750-2262C-2R 20-750-2263C-1R2T20-750-E NC-120-750-D E NC-120-750-U F B-120-750-1132C-2R 20-750-1133C-1R2T 20-750-S320-750-S4Rockwell Automation Publication 750-IN002K-MU-P - May 20213PowerFlex 750-Series Option Modules Installation Instructionsa.Recommended torque = 0.45 N•m (4.0 lb•in)b.Recommended screwdriver = T15 Hexalobular Using Option Modules 20-750-S1 / 20-750-S4 with Option Modules 20-750-DENC-1 / 20-750-UFB-1Auxiliary Power Supply (20-750-APS) InstallationA connector cable is provided with the Auxiliary Power Supply option module for use in PowerFlex 753 drives and in PowerFlex 755 Frame 1 drives. The cable is used to connect the module to the backplane when installed on the upper control pod brackets.IMPORTANTDo not overtighten the retaining screws.IMPORTANTWhen a Safe Speed Monitor option module (catalog number 20-750-S1), or a PowerFlex 755/755T Integrated Safety Functions option module (catalog number 20-750-S4), is used with a Dual Incremental Encoder option module (catalog number 20-750-DENC-1), or a Universal Feedback Encoder option module (catalog number 20-750-UFB-1), you must install both modules on the same backplane (ports 6, 5, 4).Only the 20-750-S1 and the 20-750-DENC-1 are depicted in the illustration to the right.IMPORTANTDo not use the Auxiliary Power Supply option module with PowerFlex 755 Frame 8 and larger drives. See the PowerFlex 750-Series AC Drives Installation Instructions, publication 750-IN001, for information on the connection of an external power supply to a PowerFlex 755 Frame 8 and larger drive.(Grease is Opaque - Shown Shaded for Example Only)NOTE : This figure is for illustrative purposes only. The specific4Rockwell Automation Publication 750-IN002K-MU-P - May 2021PowerFlex 750-Series Option Modules Installation InstructionsOption Module Installation Next to a PROFIBUS Option ModuleDo not allow the lower T15 Torx™ mounting screw (Detail A) on a new module to contact the metal cable connector of an installed PowerFlex 20-750-PBUS PROFIBUS option module. Electrical contact of the two metal parts can cause faulty operation. Perform these steps to help prevent contact. If a PowerFlex 20-750-PBUS PROFIBUS option module is not in that port, disregard these steps.1.Remove the lower T15 Torx mounting screw (Detail A) from the new module being installed. To remove the captive T15 Torx screw, the module must be removed to back the screw out of the mounting clip.2.Replace the larger T15 Torx screw with the smaller spare T8 Torx mounting screw that was shipped with the PowerFlex 20-750-PBUS PROFIBUS option module.11-Series and 22-Series I/O Module InstallationDetail A20-750-2262C-2R (24V DC)20-750-2263C-1R2T (24VDC)ATTENTION: When used in an Integrated Motion onEtherNet/IP™ network application for firmware revisions 12 and later, both the 11-Series and 22-Series I/O modules must be installed in port 7 only. You cannot use the ATEX option module with the 11-Series I/O module in port 7 when used in an Integrated Motion on EtherNet/IP application.20-750-1132C-2R (24V DC)20-750-1133C-1R2T (24V DC)20-750-1132D-2R (120V DC)Rockwell Automation Publication 750-IN002K-MU-P - May 20215PowerFlex 750-Series Option Modules Installation InstructionsAdditional ResourcesThese documents contain additional information concerning related products from Rockwell Automation®.Y ou can view or download publications at /global/literature-library/overview.page .ResourceDescriptionPowerFlex 750-Series I/O, Feedback, and Power Option Modules Installation Instructions, publication 750-IN111Provides drive compatibility, jumper settings, terminal designations, wiring examples for analog and digital I/O, feedback, and auxiliary power options option modules.PowerFlex 750-Series Products with TotalFORCE Control Hardware Service Manual, publication 750-TG001.Provides detailed information on:• Preventive maintenance • Component testing• Hardware replacement proceduresNetwork Communication Option Module Installation Instructions, publication 750COM-IN002Provides information on the installation of PowerFlex 750-Series Network Communication modules.PowerFlex 750-Series AC Drives Installation Instructions, publication 750-IN001Provides information on the mechanical and electrical installation of PowerFlex 750-Series drives.PowerFlex 750-Series Products with TotalFORCE Control Installation Instructions, publication 750-IN100Provides information on the mechanical and electrical installation of PowerFlex 750-Series products with TotalFORCE control.PowerFlex 755TM IP00 Open Type Kits Installation Instructions, publication 750-IN101Information on the installation of PowerFlex 755TM IP00 / Open Type kits in customer-sourced enclosures.PowerFlex 750-Series Safe Speed Monitor Option Module Safety Reference Manual, publication 750-RM001These publications provide detailed information on installation, set-up, and operation of the 750-Series safety option modules.PowerFlex 750-Series Safe Torque Off Option Module User Manual, publication 750-UM002PowerFlex 750-Series ATEX Option Module User Manual, publication 750-UM003PowerFlex 755 Integrated Safety - Safe Torque Off Option Module User Manual, publication 750-UM004PowerFlex 755/755T Integrated Safety Functions Option Module User Manual, publication 750-UM005Industrial Automation Wiring and Grounding Guidelines, publication 1770-4.1Provides general guidelines for installing a Rockwell Automation industrial system.Product Certifications website rok.auto/certificationsProvides declarations of conformity, certificates, and other certification details.Publication 750-IN002K-MU-P - May 2021 | Supersedes Publication 750-IN002J-MU-P-July 2019Copyright © 2021 Rockwell Automation, Inc. All rights reserved. Printed in the U.S.A.Rockwell Otomasyon Ticaret A.Ş. Kar Plaza İş Merkezi E Blok Kat:6 34752 İçerenköy, İstanbul, Tel: +90 (216) 5698400 EEE Yönetmeliğine UygundurPN-630034DIR 10006123460Allen-Bradley, expanding human possibility, FactoryTalk, and Rockwell Automation are trademarks of Rockwell Automation, Inc.Trademarks not belonging to Rockwell Automation are property of their respective companies.*PN-630034*PN-630034Your comments help us serve your documentation needs better. If you have any suggestions on how to improve our content, complete the form at rok.auto/docfeedback .For technical support, visit rok.auto/support .Waste Electrical and Electronic Equipment (WEEE)Rockwell Automation maintains current product environmental compliance information on its website at rok.auto/pec .At the end of life, this equipment should be collected separately from any unsorted municipal waste.Rockwell Automation SupportUse these resources to access support information.Documentation FeedbackYour comments help us serve your documentation needs better. If you have any suggestions on how to improve our content, complete the form at rok.auto/docfeedback .Technical Support Center Find help with how-to videos, FAQs, chat, user forums, and product notification updates.rok.auto/supportKnowledgebaseAccess Knowledgebase articles.rok.auto/knowledgebase Local Technical Support Phone Numbers Locate the telephone number for your country.rok.auto/phonesupport Literature LibraryFind installation instructions, manuals, brochures, and technical data publications.rok.auto/literature Product Compatibility and Download Center (PCDC)Download firmware, associated files (such as AOP, EDS, and DTM), and access product release notes.rok.auto/pcdc。
AVID FOD Receiver User's Guide

FOD Receiver User’s Guide Rev 3, 07/18/2013General DescriptionThe AVID FOD (Foreign Object Detection) Receiver is a standard WPC V1.1 wireless power receiver (5.0W) that has been calibrated and characterized to accurately measure and report received power information. This RX device is useful for testing transmitter devices, for characterizing and optimizingV1.1 (and newer) transmitter’s FOD functionality, and for doing Qi pre-compliance testing.Here are the main features of the AVID FOD Receiver:- Fully functional V1.1 Qi Receiver- Uses “naked” RX coil as specified for TPR#5 in the WPC Part 3 spec. Coil is isolated from the electronics and mounted in plastic frame that mates with the foreign object holders for good alignment - Factory calibrated and characterized using calibrated AVID FOD Transmitter- Accurately measures and reports PPR (received power) values per WPC V1.1 spec- Calculates and sends additional 16-bit PPR values (proprietary packet 0x28) that can be decoded and reported using the AVID FOD Transmitter and AVID V1.1 Sniffer- Programmable PPR offset and internal loads (DIP switch settings)- External load board (included) has minimum, maximum and in-between loads for testing and characterizing transmitters and for running Qi pre-compliance tests- Supports internal loads up to 2.0 Watts in 0.25 Watt increments (DIP switch settings) and external loads up to 5.0 Watts maximum.AVID FOD Receiver, Top ViewAVID FOD Receiver, Side and Bottom ViewsAVID Receiver Load BoardBasic Setup and OperationTo operate the FOD Receiver, first set the DIP switches on top of the unit to program the internal loadand the PPR offset values (see below) as desired. The FOD receiver can be operated using internalloads up to 2.0 Watts, but AVID recommends leaving the Load DIP switches all off and connecting the external load board to the output screw terminals for testing because this will isolate the load from the receiver and keep the electronics at a more even temperature. Next, place the FOD Receiver on any Qi transmitter for characterization and testing.The “Power” and “Status” LEDs on top of the FOD Receiver indicate the operational state of the receiver. The Power LED will light solid blue as long as the receiver is receiving enough power from the transmitterto power up its internal electronics. The Status LED will light solid green when the receiver is receiving enough power to supply the internal or external load and to regulate its output voltage to +5.0V. Whenthe FOD Receiver is first placed on a transmitter, it connects a minimum internal load of 100 ohms (to ensure robust communications). Next the receiver adjusts its bridge voltage to about 5.8V and then connects the internal or external load and disconnects the minimum 100 ohm load. If an external load is connected to the terminal block on the receiver and current flow is detected through the output, all internal loads are disconnected otherwise the internal load programmed on the DIP switches is left connected.Once the load is connected, the receiver will send error messages to regulate the output to +5.0V +/- 5%. The FOD Receiver should operate normally on any Qi transmitter (base station). If the FOD Receiver is powered up and regulating its output voltage, the status LED will remain green or amber. If the FOD Receiver cannot regulate its output voltage the status LED will turn off. If an error occurs (see below) the status LED will blink red. To maintain good power measurement accuracy, always make sure theFOD Receiver is not operated on or near metal desks or other large metal objects during testing.Below are brief descriptions of the functionality supported by the FOD Receiver: Function DescriptionPower LED Solid blue when FOD Receiver receives sufficient power from the transmitter to power its internal circuitryStatus LED Solid green when FOD Receiver receives sufficient power from the transmitter to power its internal load and regulate to +5.0V +/-5% Solid amber when FOD Receiver receives sufficient power from the transmitter to power an external load and regulate to +5.0V +/-5% Blinking red indicates various error codes (see quick start guide below)VBRIDGE Pin Rectified bridge voltage measurement test point COMM Pin Communication modulator digital signal test point GND Pins Internal circuitry ground referenceTEST DIP Switches PPR offset multiplier (6 bits) 0 to 63. This value is multiplied by the PPR offset step size to get the resulting PPR offset value in mWCOMM DIP Switches PPR step size (2 bits). This value is multiplied by the PPR offset multiplier to get the resulting PPR offset value in mW00 = -5 mW, 01 = -10 mW, 10 = +5 mW, 11 = +10 mWLOAD DIP Switches Internal load (4 bits) 0 to 8 (positions 9-15 reserved)This value is multiplied by 0.25 to get the resulting internal load in Watts If external load >= 0.25W is sensed, all internal loads are switched offTerminal Block For connecting external loads. When operating properly the FOD Receiver will provide +5.0V +/- 5% at this outputExternal Load Board Can be used to connect and switch on/off various external loads for characterizing V1.1 transmitters and running FOD pre-compliance testsV1.1 Transmitter (Base Station) FOD CharacterizationV1.1 QI compliant transmitter (base station) product developers can use the AVID FOD Receiver tool and the AVID external load board (or user supplied load) to characterize and adjust the transmitter power measurements. The FOD Receiver has been characterized using the AudioDev WPC approved V1.1 Test Transmitter and the results show good correlation between transmitted power and received power to within about 50 mW accuracy over a 0.25 W to 6.0 W load range.If the transmitter under test has a means of providing an indication of its transmitted power values during power transfer, then it is possible to use the AVID FOD Receiver to characterize the transmitter’s power loss measurements and FOD thresholds.To use the AVID FOD Receiver to characterize a transmitter, use the following procedure:1) Connect the external load board to the FOD Receiver terminal block and switch on the 0.25 Wload only. The on position for the switches is toward the edge of the load board.2) Place the FOD Receiver on the transmitter, center aligned, and record the transmitted power andreceived power values. If the transmitter does not already provide the received power values to the user, the AVID Qi Sniffer V1.1 can be used to capture the received power values including16-bit high resolution values reported by the AVID FOD Receiver.3) Repeat step 2 at several external load points such as at 1.0 W increments up to 5.0 W.4) Plot the received power vs. transmitted power values for each load point. The data should showgood correlation. If the difference is greater than 100 mW at any of the load points, makeadjustments to the transmitter to improve the power measurements.Base Station Qi Pre-Compliance TestingV1.1 QI compliant transmitter (base station) product developers can use the AVID FOD Receiver tool, the AVID external load board (or electronic load), and a set of WPC defined Foreign Objects to run Qi FOD Part 3 pre-compliance tests. AVID Technologies supplies (separately) the WPC defined foreign objects with an alignment frame and spacers that can be used for this testing.The Part 3 Base Station FOD compliance tests use two test receivers: TPR#5 and TPR#6. These receivers use a low-loss coil with no shield to minimize parasitic losses.TPR#5 is configured to output 5.0V +/-20% and to use a received power window size of 64 ms and a window offset size of 16 ms. TPR#5 is also configured to over report its received power values by 235 mW. During the WPC interim extension period in effect until May 2014, TPR#5 shall instead over report its received power values by 35 mW:TPR#5 PPR = (PPM+235)TPR#5 (INT) PPR = (PPM+35) ** Use this equation during the WPC interim periodPPM is the actual received power determined by the test receiver by measuring its load power and adding estimated parasitic power losses.TPR#6 is identical to TPR#5 except TPR#6 is configured to under report its received power values by 15 mW. During the WPC interim extension period in effect until May 2014, TPR#6 shall instead under report its received power values by 115 mW.TPR#6 PPR = (PPM-15)TPR#6 (INT) PPR = (PPM-115) ** Use this equation during the WPC interim periodBase Station Thermal Compliance TestingThe Part 3 Base Station FOD thermal compliance tests consist of measurements that check the temperature rise (at +25 deg C ambient) of four different WPC defined foreign objects while they are placed between the test receiver (TPR#5) and the base station during power transfer. Each object has an allowed temperature limit as defined in the table below.WPC Defined Foreign Objects:LimitObject Configuration Temperature#1 Steel disc centered 60 deg C#2 Aluminum ring centered 60 deg C#3 Aluminum foil centered 80 deg C#4 Steel disc offset 15.5 mm 60 deg CIf any of the foreign objects reaches or exceeds the temperature limits above during testing, the transmitter’s FOD measurements, thresholds, or reaction time may need to be adjusted to meet compliance.To use the AVID FOD Receiver to emulate TPR#5 and run the foreign object thermal pre-compliance tests on a base station, use the following procedure:1) Set the DIP switches on the AVID FOD Receiver to emulate TPR#5 as follows:TEST = 000111 (PPR offset multiplier = 7)COMM = 10 (PPR offset step = +5 mW)LOAD = 0000 (no internal load)2) Connect the external load board to the FOD Receiver and switch on the 0.25W (100 ohm) loadonly on the far left of the load board near the terminal block connector.3) Connect foreign object #1 (steel disc) K-type thermocouple connector to a suitable thermometeror DMM that can measure temperature of a K-type thermocouple.4) Fit the clear plastic alignment frame on top of the foreign object holder.5) Place the foreign object and alignment frame on the base station under test and align the centerof the foreign object holder with the center of the base station transmitter coil. The AVID foreign object holders have score marks that indicate the center lines.6) Place the AVID FOD Receiver in the alignment frame on top of the foreign object and make surethe receiver and foreign object are still center aligned with the transmitter coil.7) Increase the load on the external load until the transmitter hits its power loss (FOD) threshold andterminates (or lowers) its transmitted power. If you are using the AVID supplied external loadboard, leave the 0.25W load switched on, switch on the variable (0.24 W to 1.38 W) load, andslowly adjust the potentiometer until right at the point the power loss threshold is hit.8) Reduce the external load by 50 mA. If you are using the AVID supplied external load board thiscan be accomplished by switching off the 0.25W (100 ohm) load.9) Run the transmitter for 10 minutes (or until the transmitter terminates power transfer) and recordthe temperature of the foreign object.If the transmitter terminates power transfer before 10 minutes during any of these tests, repeat steps 6 and 7 above and reduce the load slightly until the transmitter runs for 10 minutes OR until the minimum load of 0.25 W (50.0 mA) is reached. At the minimum load, if the transmitter still terminates power before 10 minutes, the temperature of the object is recorded at the point where power transfer was terminated. The steps above are repeated as follows:- Using object #1 with 2.0 mm spacer placed between the foreign object and the AVID FOD receiver- Using object #1 with 5.0 mm spacer placed between the foreign object and the AVID FOD receiver- Using foreign object #2- Using foreign object #3- Using foreign object #4The steel disc objects present lower power losses and temperature rises than the other objects. For the steel objects, the thermal test may run for the full 10 minutes. The transmitter FOD power loss threshold should be set to keep the temperature of the objects below the limit at the end of the 10 minute test.The aluminum foil and ring objects present higher power losses and temperature rises than the steel discs. For these objects, even at the minimum 50 mA load the thermal test may not run the full 10 minutes before the transmitter reaches its FOD power loss threshold. In this case the transmitter FOD threshold and reaction time should be adjusted to keep the foreign object temperature below the limit when the threshold is reached and the transmitter either terminates or reduces power.If the transmitter can be adjusted to keep the foreign objects below the temperature limits for all of the above tests, then the product will likely pass the FOD thermal compliance tests at an approved Qi compliance lab. If not, adjust the transmitter FOD power loss thresholds and reaction time accordingly.Base Station Guaranteed Power Compliance TestingThe Part 3 Base Station FOD guaranteed power compliance test consists of a measurement that checks to make sure the base station under test can deliver 5.0 Watts to a test receiver (TPR#6) that has no foreign object present, but is simulating power loss into a foreign object by under reporting its received power.To use the AVID FOD Receiver to emulate TPR#6 and run the guaranteed power pre-compliance tests on a base station, use the following procedure:1) Set the DIP switches on the AVID FOD Receiver to emulate TPR#6 as follows:TEST = 010111 (PPR offset multiplier = 23)COMM = 00 (PPR offset step = -5 mW)LOAD = 0000 (no internal load)2) Connect the external load board to the FOD Receiver and switch on the 0.25W load only.3) Place the FOD Receiver on the base station and make sure it is center aligned with thetransmitter coil. Wait until the base station begins power transfer.4) Switch on the 1W load on the external load board. Allow the base station to continue powertransfer for 10 seconds.5) Switch on the 2W load on the external load board. Allow the base station to continue powertransfer for 10 seconds.6) Switch on the 3W load and switch off the 0.25W and 1W loads on the external load board (total =5W load). Allow the base station to continue power transfer for 5 minutes.7) Measure the voltage at the terminal block output on the FOD Receiver and make sure it isbetween 4.75V and 5.25V (regulation tolerance of the FOD Receiver).If the voltage measured in step 7 is between 4.75V and 5.25V, then the product will likely pass the FOD guaranteed power compliance tests at an approved Qi compliance lab. If the voltage is not between4.75V to5.25V, make adjustments to the base station device to improve the power transfer performance and repeat the tests above.NOTE: AVID FOD TOOLS ARE NOT APPROVED FOR FINAL QI COMPLIANCE TESTING. THEY ARE DESIGNED TO BE USED FOR DEVELOPMENT AND PRE-COMPLIANCE TESTING BY CUSTOMERS DESIGNING and PROTOTYPING WPC V1.1 WIRELESS POWER PRODUCTS.AVID FOD Receiver Quick Start Guide:Quick Start Guide ***************************SYSTEM MONITORING:VBRIDGE: (5.0V +/-0.5V)Receiver DC Bridge VoltageCOMM. (0 -3.3V Logic)Modulation Signal5V, 0-1A OUTPUT:Internal load is disabledwhen external load (>0.25W)is connected.CONFIGURATION SWITCHES:TEST Position 1-6PPR offset multiplierLOAD Position 1-4Selects internal load0-2W, in 0.25W StepsCOMM Position 5PPR offset polarityPosition 6PPR offset step sizeAll switches can be changedduring run time.STATUS LED:©2013 AVID Technologies, Inc. All rights reserved.FOD Receiver。
portal

Validating file. Please wait...............Saved the current configuration to mainboard device successfully. Configuration is saved to device successfully.[H3C]dis cu#version 5.20, Release 3507P26#sysname H3C#domain default enable system#telnet server enable#oap management-ip 192.168.0.100 slot 1#password-recovery enable#vlan 1#vlan 34#vlan 200#vlan 999#vlan 4052#domain systemaccess-limit disablestate activeidle-cut disableself-service-url disable#user-group system#local-user adminpassword cipher $c$3$F6LNBGUy7zxhw4izofH0C2HA0k9VS1w4 authorization-attribute level 3service-type telnet#interface Bridge-Aggregation1port link-type trunkport trunk permit vlan all#interface NULL0#interface Vlan-interface34ip address 10.3.4.101 255.255.255.0#interface Vlan-interface4052ip address 192.168.209.101 255.255.255.0 #interface GigabitEthernet1/0/1port access vlan 200poe enable#interface GigabitEthernet1/0/2port access vlan 4052poe enable#interface GigabitEthernet1/0/3poe enable#interface GigabitEthernet1/0/4port access vlan 4052poe enable#interface GigabitEthernet1/0/5poe enable#interface GigabitEthernet1/0/6 description to-7600port link-type trunkport trunk permit vlan allpoe enable#interface GigabitEthernet1/0/7poe enable#interface GigabitEthernet1/0/8port access vlan 4052poe enable#interface GigabitEthernet1/0/9#interface GigabitEthernet1/0/10#interface GigabitEthernet1/0/11port link-type trunkport trunk permit vlan allport link-aggregation group 1#interface GigabitEthernet1/0/12port link-type trunkport trunk permit vlan allport link-aggregation group 1#nqa entry imclinktopologypleaseignore pingtype icmp-echodestination ip 192.168.100.254frequency 270000#ip route-static 0.0.0.0 0.0.0.0 192.168.209.1#snmp-agentsnmp-agent local-engineid 800063A20370F96D8118ABsnmp-agent community read h3csnmp-agent community write imcsnmp-agent community read publicsnmp-agent community write privatesnmp-agent sys-info version all#nqa schedule imclinktopologypleaseignore ping start-time now lifetime 630720000 #user-interface aux 0user-interface vty 0 4authentication-mode schemeuser-interface vty 5 15#return[H3C]<3024><3024><3024>dis cu#version 5.20, Release 3507P26#sysname 3024#domain default enable portal#telnet server enable#port-security enable#portal server portal ip 192.168.209.200 key cipher $c$3$hI0qpjiWBdD5Asw7cpDacwkbgk9ocgDm url http://192.168.209.200:80/portal server-type imcportal free-rule 0 source interface Bridge-Aggregation1 destination anyportal free-rule 1 source ip 211.140.13.0 mask 255.255.255.0 destination ip anyportal free-rule 2 source ip any destination ip 211.140.13.188 mask 255.255.255.255portal free-rule 3 source ip any destination ip 192.168.209.200 mask 255.255.255.255portal free-rule 4 source ip 192.168.209.200 mask 255.255.255.255 destination ip anyportal free-rule 5 source ip 192.168.209.100 mask 255.255.255.255 destination ip anyportal free-rule 6 source ip any destination ip 192.168.209.100 mask 255.255.255.255portal free-rule 8 source ip any destination ip 10.3.4.0 mask 255.255.255.0#oap management-ip 192.168.0.101 slot 0#password-recovery enable#vlan 1#vlan 34#vlan 999#vlan 4052#radius scheme portalprimary authentication 192.168.209.200primary accounting 192.168.209.200key authentication cipher $c$3$f3AMNfceeVWyUC1DW5FSsB/Li1rGjDDbkey accounting cipher $c$3$fEEGh7pf1vLtweIlSg62vWe/GCcQ1dbHuser-name-format without-domainnas-ip 10.3.4.100#domain portalauthentication portal radius-scheme portalauthorization portal radius-scheme portalaccounting portal radius-scheme portalaccess-limit disablestate activeidle-cut disableself-service-url disabledomain systemauthentication portal localauthorization portal localaccounting portal localaccess-limit disablestate activeidle-cut disableself-service-url disable#dhcp server ip-pool vlan999network 10.254.254.0 mask 255.255.255.0gateway-list 10.254.254.1#user-group systemgroup-attribute allow-guest#local-user adminpassword cipher $c$3$XQrqH02hvTAssns+VgofFByAQm6rJqHM authorization-attribute level 3service-type telnetservice-type weblocal-user h3cpassword cipher $c$3$aeu7k2p37APDUvXOu4U8EVfn2re4ug== service-type portal#wlan rrmdot11a mandatory-rate 6 12 24dot11a supported-rate 9 18 36 48 54dot11b mandatory-rate 1 2dot11b supported-rate 5.5 11dot11g mandatory-rate 1 2 5.5 11dot11g supported-rate 6 9 12 18 24 36 48 54#wlan service-template 1 clearssid H3C-WIFIbind WLAN-ESS 1service-template enable#interface Bridge-Aggregation1port link-type trunkport trunk permit vlan all#interface NULL0#interface Vlan-interface1#interface Vlan-interface34ip address 10.3.4.100 255.255.255.0 portal server portal method directportal domain portalportal nas-ip 10.3.4.100#interface Vlan-interface999ip address 10.254.254.1 255.255.255.0#interface Vlan-interface4052ip address 192.168.209.100 255.255.255.0 nat outbound 3000#interface GigabitEthernet1/0/1port link-type trunkport trunk permit vlan allport link-aggregation group 1#interface GigabitEthernet1/0/2port link-type trunkport trunk permit vlan allport link-aggregation group 1#interface WLAN-ESS1port access vlan 34#nqa entry imclinktopologypleaseignore ping type icmp-echodestination ip 10.3.4.253frequency 270000#wlan ap-group default_groupap 1ap 2#wlan ap 1 model WA2620i-AGN id 1serial-id autoradio 1service-template 1radio enableradio 2service-template 1radio enable#wlan ap 2 model WA2620i-AGN id 2serial-id 219801A0CMC144001080radio 1service-template 1radio enableradio 2service-template 1radio enable#wlan ipsmalformed-detect-policy defaultsignature deauth_flood signature-id 1signature broadcast_deauth_flood signature-id 2signature disassoc_flood signature-id 3signature broadcast_disassoc_flood signature-id 4signature eapol_logoff_flood signature-id 5signature eap_success_flood signature-id 6signature eap_failure_flood signature-id 7signature pspoll_flood signature-id 8signature cts_flood signature-id 9signature rts_flood signature-id 10signature addba_req_flood signature-id 11signature-policy defaultcountermeasure-policy defaultattack-detect-policy defaultvirtual-security-domain defaultattack-detect-policy defaultmalformed-detect-policy defaultsignature-policy defaultcountermeasure-policy default#ip route-static 0.0.0.0 0.0.0.0 192.168.209.1#snmp-agentsnmp-agent local-engineid 800063A2035CDD70F5DB7Fsnmp-agent community read h3csnmp-agent community write imcsnmp-agent sys-info version allsnmp-agent target-host trap address udp-domain 10.254.254.3 params securityname h3c snmp-agent target-host trap address udp-domain 192.168.209.200 params securityname h3c v2csnmp-agent target-host trap address udp-domain 10.254.254.3 params securityname imc snmp-agent target-host trap address udp-domain 192.168.209.200 params securityname imcv2csnmp-agent trap enable default-route#dhcp enable#nqa schedule imclinktopologypleaseignore ping start-time now lifetime 630720000 #user-interface con 0user-interface vty 0 4authentication-mode schemeuser privilege level 3#return<3024>添加业务vlan的控制器的ip地址添加控制器的ip接入设备添加接入策略添加接入服务添加接入用户添加业务vlan的ip网断添加控制器设备的Ip添加控制器的端口。
Z-Active 差分探头系列 P7313、P7380A、P7360A、P7340A 数据手册说明书

Z-Active™Differential Probe FamilyP7313•P7380A •P7360A •P7340A DataSheetFeatures &Bene fitsSignal Fidelity>12.5GHz Bandwidth (P7313,Typical)>8.0GHz Bandwidth (P7380A,Typical)>6.0GHz Bandwidth (P7360A,Typical)>4.0GHz Bandwidth (P7340A,Typical)Extended Linear Dynamic Range 1.25V p-p at 5x Attenuation (P7313)4V p-p at 25x Attenuation (P7313)2V p-p at 5x Attenuation (P7380A,P7360A,P7340A)5V p-p at 25x Attenuation (P7380A,P7360A,P7340A)Low Probe Loading DC Input Resistance 100k ΩDifferential 50k ΩSingle Ended AC LoadingZ min >200Ωout to 10GHz (P7313)Z min >290Ω,4GHz to 8GHz (P7380A,P7360A,P7340A)VersatilityMake Differential or Single-ended (Ground-referenced)Measurements*1Solder-down CapabilityHandheld Probing with Variable Spacing and Compliance Fixtured Probing Interchangeable Tip-Clip™Assemblies Connect to a Variety of Devices Economical TekConnect ®InterfaceApplicationsExamples Include,but are not Limited To:PCI-Express I and II,Serial ATA II,USB 2.0,DDRII,DDRIII,Fireware 1394b,Rambus,XAUI*1For details,please see application note 60W-18344-0,“Making Single-ended Measurements with DifferentialProbes.”1981Data SheetZ-Active™Probing Architecture Leads the Way for High-speed Probing Applications Tektronix has created a revolutionary Z-Active probe architecture that sets the industry benchmark for signalfidelity.Tektronix active probe architecture preserves high bandwidth while providing improved connectivity with low loading.The Z-Active architecture is a hybrid approach composed of a distributed attenuator topology feeding an active probe amplifier.The Z-Active probes use a tiny passive probe tip element that is separate from the amplifier,extending the usable reach of the probe.In traditional active probes,adding this much length can introduce signalfidelity problems.However this architecture maintains high DC input resistance and presents a higher AC impedance than previous probe architectures.It accomplishes this while providing significant length between the probe body and the probe attachment point to the DUT.This architecture provides the best of both worlds:high DC impedance like existing active probes and the stable high-frequency loading of Z0probes.Signal FidelityYou can be confident in the signalfidelity of your measurements because the Z-Active architecture provides:High BandwidthExcellent Step ResponseLow LoadingHigh CMRRExtended Linear Dynamic RangeExtended Linear Dynamic RangeMany of today’s logic signals and serial bus signals require the capabilityto measure up to several volts peak to peak.These voltage levels may easily be viewed with the Z-Active architecture probes(P7380A,P7360A, and P7340A)with the extended linear dynamic range.With a2.0V p-p linear dynamic input range at the5x attenuation setting,you can accurately measure DDR II and III,Firewire1394b,and PCI-Express I and II signals at reduced noise levels.In addition the25x attenuation setting’s linear dynamic input voltage range can be used up to5.0V p-p for accessing even larger signal swings found during transition times.ConnectivityThe Z-Active probe design allows the probe to easily switch between soldered,handheld,orfixtured applications.This family of probes uses Tip-Clip™assemblies,an interchangeable probe tip system that enables customers to configure their probe with the optimal tip for their application.These detachable assemblies make it possible to replace a tip for a fraction of the cost formerly associated with such hardware changes.The several lengths and variable spacing of the assemblies provideflexibility for adapting to vias and other test points of differing sizes.With Tektronix Tip-Clip assemblies,Monday’s solder-in probe can become Tuesday’s handheld tool,simply by switching tips. ValueThe combination of the Z-Active architecture and the Tip-Clip assemblies provide superior signalfidelity at a cost-effective price.The inexpensive Tip-Clip assemblies enable full-performance solder connections at a very low price per connection.Over the life of a probe this can add up to significant savings in the cost of operation.Performance You Can Count OnDepend on Tektronix to provide you with performance you can count on.In addition to industry-leading service and support,this product comes backed by a one-year warranty as standard.Z-Active™Differential Probe Family—P7313•P7380A•P7360A•P7340ACharacteristicsCharacteristic P7340A P7360A P7380A P7313Bandwidth(Typical)>4GHz>6GHz>8GHz>12.5GHzRise Time(10%-90%)(Guaranteed)<100ps<70ps<55ps<40psRise Time(20%-80%)(Typical)<70ps<50ps<35ps<25psAttenuation5x or25x,user selectableDifferential Input Range±1.0V(5x)±2.5V(25x)±0.625V(5x)±2.0V(25x)Linearity Error for Differential Input Dynamic Range(Typical)±0.5%for-0.5V to+0.5V(5x)±1.0%for-0.75V to+0.75V(5x)±2.0%for-1.0V to+1.0V(5x)±0.5%for-1.5V to+1.5V(25x)±1.0%for-2.5V to+2.5V(25x)±2.0%for-3.0V to+3.0V(25x)±0.25%for-0.5V to+0.5V(5x)±0.75%for-0.625V to+0.625V(5x)±0.5%for-1.6V to+1.6V(25x)±1.0%for-2.0V to+2.0V(25x)Operating Voltage Window+5.0V to-3.0V+4.0V to-3.0V Offset Voltage Range+4.0V to-3.0VDC Input Resistance100kΩAC Loading(Differential Z min)>290Ω>200ΩNoise<31nV/√Hz(5x)<75nV/√Hz(25x)CMRR>50dB at1MHz>35dB at1GHz>20dB at4GHz >50dB at1MHz>35dB at1GHz>20dB at6GHz>50dB at1MHz>35dB at1GHz>20dB at8GHz>50dB at1MHz>35dB at1GHz>20dB at6GHz>15dB at12.5GHzNondestructive Input Range±15VInterface TekConnect®Cable Length 1.5m 1.5m 1.2m 1.2m Ordering InformationP7313>12.5GHz Z-Active Differential Probe for TekConnect®Interface. P7380A>8.0GHz Z-Active Differential Probe for TekConnect®Interface.P7360A>6.0GHz Z-Active Differential Probe for TekConnect®Interface.P7340A>4.0GHz Z-Active Differential Probe for TekConnect®Interface.All Include:One-year warranty,plus see Standard Accessories table.3Data SheetStandard AccessoriesDescriptionP7340AP7360AP7380AP7313Reorder Part NumberPouch,Nylon Carrying Case with Inserts1each 1each 1each 1each 016-1952-xx Qty 1Accessory Performance Summary and Reorder Sheet1each 1each 1each 1each 001-1389-xx Qty 1020-2640-xx Qty 1–Opt.L0020-2648-xx Qty 1–Opt.L5User Manual -Printed.Includes Reply Card and CD 1each1each1each1each040-2649-xx Qty 1–Opt.L7BNC (M)-to-Minigrabber Adapter 1each 1each 1each 1each 013-0342-xx Qty 1Anti-static Wrist Strap 1each 1each 1each 1each 006-3415-xx Qty 1Magnifying Glasses 1each 1each 1each 1each 378-0486-xx Qty 1Calibration Data Report 1each 1each 1each 1each Opt.D1Handheld Probe Adapter 1each 1each 1each1each 015-0717-xx 1eachP7313:020-2636-xx 1eachP7380A:020-2557-xx 1eachP7360A:020-2690-xx Accessory Box and Contents1each P7340A:020-2690-xx Attachment Kit1each 1each 1each 1each 016-1953-xx Qty 1Velcro Fastening Strap 10each 10each 10each 10each –Velcro Fastening Dots 10each 10each 10each 10each –Adhesive Tip-Clip Tape*2(Strip of 10)3each 3each 3each 3each –Color Band Kit (2ea.of 5colors)1each 1each 1each 1each 016-1948-xx Qty 1Short Flex,Small Resistor Tip-Clip Assembly 2each 2each 3each 3each 020-2600-xx Qty 10Medium Flex,Small Resistor Tip-Clip Assembly 2each 2each 3each 3each 020-2602-xx Qty 10Long Flex,Small Resistor Tip-Clip Assembly 2each 2each 3each 3each 020-2604-xx Qty 10Variable Spacing Tip-Clip Kit 3each 3each 3each 3each 020-2596-xx (Kit of 3)Square Pin Adapter Tip-Clip 1each 1each 1each 1each 020-2701-xx (Kit of 3)Tip-Clip Ejector*23each 3each 3each 3each –020-2639-xx Qty 10HBW Straight Flex Tip-Clip Assembly –––3each020-2657-xx Qty 5020-2638-xx Qty 10HBW Right-Angle Flex Tip-Clip Assembly –––3each 020-2656-xx Qty 5Wire Replacement Kit–––1each 020-2644-xx Qty 1Short Flex,Large Resistor 1/8W Tip-Clip Assembly––3each –020-2601-xx Qty 10Long Flex,Large Resistor 1/8W Tip-Clip Assembly––3each –020-2605-xx Qty 10Medium Flex,Large Resistor 1/8W Tip-Clip Assembly2each2each3each–020-2603-xx Qty 10*2Tip-Clip Ejectors and Tip-Clip Tape are shipped standard with the 020-xxxx-xx Tip-Clip Assembly Kits.Recommended AccessoriesDescriptionP7360P7380P7313Part NumberProbe Positioner Yes Yes Yes PPM100Probe PositionerYes Yes Yes PPM203B PPM203B,PPM100Adapter Fixture Yes Yes Yes 013-0339-xx P7340A:067-0419-xx P7360A:067-0419-xx P7380A:067-0419-xx Calibration Fixture Yes Yes YesP7313:067-1616-xxDSA8200Series TekConnect ®Probe Interface Yes Yes Yes 80A03Deskew FixtureYes Yes Yes 067-1586-xx Real-time Spectrum Analyzer TekConnect Probe AdapterYes Yes YesRTPA2AZ-Active™Differential Probe Family—P7313•P7380A•P7360A•P7340AService OptionsOpt.CA1–Single Calibration or Functional Verification.Opt.C3–Calibration Service3Years.Opt.C5–Calibration Service5Years.Opt.D3–Calibration Data Report3Years(with Opt.C3).Opt.D5–Calibration Data Report5Years(with Opt.C5).Opt.G3–Complete Care3Years(includes loaner,scheduled calibration and more). P7360A,P7380A onlyOpt.G5–Complete Care5Years(includes loaner,scheduled calibration and more). P7360A,P7380A onlyOpt.R3–Repair Service3Years.Opt.R5–Repair Service5Years.Language OptionsOpt.L0–English Manual.Opt.L5–Japanese Manual.Opt.L7–Simplified Chinese Manual.Additional Service Products Available During Warranty (DW)or Post Warranty(PW)P7313-CA1–Single Calibration or Functional Verification.P7313-R1PW–Repair Service Coverage1-year Post Warranty.P7313-R2PW–Repair Service Coverage2-year Post Warranty.P7313-R3DW–Repair Service Coverage3Years(includes product warranty period); 3-year period starts at time of customer instrument purchase.P7313-R5DW–Repair Service Coverage5Years(includes product warranty period); 5-year period starts at time of customer instrument purchase.P7340A-CA1–Single Calibration or Functional Verification.P7340A-R1PW–Repair Service Coverage1-year Post Warranty.P7340A-R2PW–Repair Service Coverage2-year Post Warranty.P7340A-R3DW–Repair Service Coverage3Years(includes product warranty period);3-year period starts at time of customer instrument purchase.P7340A-R5DW–Repair Service Coverage5Years(includes product warranty period);5-year period starts at time of customer instrument purchase.P7360A-CA1–Single Calibration or Functional Verification.P7360A-R1PW–Repair Service Coverage1-year Post Warranty.P7360A-R2PW–Repair Service Coverage2-year Post Warranty.P7360A-R3DW–Repair Service Coverage3Years(includes product warranty period);3-year period starts at time of customer instrument purchase.P7360A-R5DW–Repair Service Coverage5Years(includes product warranty period);5-year period starts at time of customer instrument purchase.P7380A-CA1–Single Calibration or Functional Verification.P7380A-R1PW–Repair Service Coverage1-year Post Warranty.P7380A-R2PW–Repair Service Coverage2-year Post Warranty.P7380A-R3DW–Repair Service Coverage3Years(includes product warranty period);3-year period starts at time of customer instrument purchase.P7380A-R5DW–Repair Service Coverage5Years(includes product warranty period);5-year period starts at time of customer instrumentpurchase.Tektronix is registered to ISO9001and ISO14001by SRI Quality SystemRegistrar.Product(s)complies with IEEE Standard488.1-1987,RS-232-C,and with TektronixStandard Codes and Formats.5Data SheetZ-Active™Differential Probe Family—P7313•P7380A•P7360A•P7340A7Data Sheet Contact Tektronix:ASEAN/Australasia(65)63563900Austria0080022554835*Balkans,Israel,South Africa and other ISE Countries+41526753777Belgium0080022554835*Brazil+55(11)37597627Canada180********Central East Europe and the Baltics+41526753777Central Europe&Greece+41526753777Denmark+4580881401Finland+41526753777France0080022554835*Germany0080022554835*Hong Kong4008205835India0008006501835Italy0080022554835*Japan81(3)67143010Luxembourg+41526753777Mexico,Central/South America&Caribbean52(55)56045090Middle East,Asia,and North Africa+41526753777The Netherlands0080022554835*Norway80016098People’s Republic of China4008205835Poland+41526753777Portugal800812370Republic of Korea00180082552835Russia&CIS+7(495)7484900South Africa+41526753777Spain0080022554835*Sweden0080022554835*Switzerland0080022554835*Taiwan886(2)27229622United Kingdom&Ireland0080022554835*USA180*********European toll-free number.If not accessible,call:+41526753777Updated10February2011For Further Information.Tektronix maintains a comprehensive,constantly expandingcollection of application notes,technical briefs and other resources to help engineers workingon the cutting edge of technology.Please visit Copyright©Tektronix,Inc.All rights reserved.Tektronix products are covered by U.S.and foreign patents,issued and rmation in this publication supersedes that in all previously published material.Specification and price change privileges reserved.TEKTRONIX and TEK are registered trademarks ofTektronix,Inc.All other trade names referenced are the service marks,trademarks,or registered trademarksof their respective companies.02Oct201151W-17891-12。
VI TELEFILTER Filter Specification TFS 360A 1 5

VI TELEFILTER Vectron International Inc.Potsdamer Straße 18 267 Lowell Road D 14 513 TELTOW / Germany Hudson, NH 03051 / USA Measurement condition Ambient temperature:23°C Input power level:0dBm Terminating impedancesfor input:360 Ω // - 1,05 pF for output:360 Ω // - 1,05 pF Coupling coil:91 nHCharacteristics Remark:Reference level for the relative attenuation a rel of the TFS 360 A is the minimum of the pass band attenuation a min . The minimum of the pass bandattenuation a min is defined as the insertion loss a e . The centre frequency f o is the arithmetic mean value of the upper and lower frequencies at the 1.5 dB filter attenuation level relative to the insertion loss a e . The nominal frequency f N is fixed on 360 MHz without tolerance. The given values for the relative attenuation a rel and for the group delay ripple have to be reached at the frequencies given below also if the centre frequency f o is shifted due to the temperature coefficient of frequency TC f in the operating temperature range and due to a production tolerance for the centre frequency f o .D a t atyp. value tolerance/limit_____________________________________________________________________________________________________Insertion loss a e = a min -max. 5,0dB (Reference level)_____________________________________________________________________________________________________Nominal frequency f N-360,00MHz _____________________________________________________________________________________________________Pass band ripple f N ± 67,7kHz BW -max.1,5dB_____________________________________________________________________________________________________Relative attenuationa relf N ± 0,4MHz…f N ± 0,6MHz -min. 29dB f N ± 0,6MHz…f N ± 0,8MHz -min. 42dB f N ± 0,8MHz…f N ± 1,6MHz -min. 50dB f N ± 1,6MHz…f N ± 3,0MHz -min. 45dB f N ± 3,0MHz…f N ± 115MHz -min. 52dB_____________________________________________________________________________________________________Group delay ripple GD f N ±67,76kHz -max. 2,0µs_____________________________________________________________________________________________________Input power level -max. 10dBm _____________________________________________________________________________________________________Operating temperature range - 20 °C ... + 75 °C Storage temperature-35 °C …+ 85 °C__________________________________________________________________________________________Temperature coefficient of frequency TCca. - 0.036 ppm/K²__________________________________________________________________________________________Frequency inversion temperature + 20 °C_____________________________________________________________________________________________________Generated:Checked / approved:VI TELEFILTER Vectron International Inc.Potsdamer Straße 18 267 Lowell Road D 14 513 TELTOW / Germany Hudson, NH 03051 / USA Construction, pin configuration and 50 Ω - matching network(All dimensions in mm)Pin 1Sym. Output Pin 5Sym. Input Pin 2Sym. Output Pin 6Sym. Input Pin 3External Coil Pin 7GroundPin 4Package Ground Pin 8Package ground50 Ohm Test circuit 150 Ohm Test circuit 2VI TELEFILTER Vectron International Inc.Potsdamer Straße 18 267 Lowell Road D 14 513 TELTOW / Germany Hudson, NH 03051 / USA Stability CharacteristicsAfter the following tests the filter shall meet the whole specification:1. Shock:500g, 18 ms, half sine wave, 3 shocks each plane;DIN IEC 68 T2 - 272. Vibration:10 Hz to 500 Hz, 0,35 mm or 5g respectively, 1 octave per min, 10 cycles per plan, 3 plans;DIN IEC 68 T2 - 63. Damp heat:25 °C to 55°C / 95% r.H. / 10 cycles (cycle)DIN IEC 68 - 2 – 30 Db4. Resistance tosolder heat (reflow):max. 2 times reflow process;for temperature conditions refer to the attached "Air reflow temperature conditions" on page 4;PackingTape & Reel:IEC 286 - 3, with exception of value for N and minimum bending radius;tape type II , embossed carrier tape with top cover tape on the upper side;max. pieces of filters per reel:3000Real of empty components at start:min 300 mm Real of empty components at start including leader:min 500 mm Trailermin 300 mmTape (all dimensions in mm)W : 12 ± 0,3Po : 4 ± 0,1Do : 1,5 + 0,1F : 5,5 ± 0,1G (min) : 0,75P2 : 2 ± 0,05P1 : 4 ± 0,1D1(min) : 1,5Ao : 5,3 ± 0,1Bo : 5,3 ± 0,1E : 1,75 ± 0,1NW 1W 2Reel (all dimensions in mm):A : 330W1 : 12,4 +2W2 (max) : 18,4N (min) : 50C : 13 ± 0,25The minimum bending radius is 45 mm. The mounting surface of the filters faces the bottom side of the embossed carrier tape.The marking of the filters is able to read if the view is directed on the upper side of the carrier tape with the sprocket holes on the right side of the tapeUser direction of feedAir reflow temperature conditions1st and 2nd air reflow profileName:p re-heating periods m ain-heating periods peak temperatureTemperature:150 °C - 170 °C over 200 °C 255 °C ± 5 °CTime:60 sec. - 90 sec.20 sec. - 25 sec.Tolerance of temperatures: ± 5 °Ctime / sec. temperature / °C t ime / sec. temperature / °C023140160VI TELEFILTER Vectron International Inc. Potsdamer Straße 18 267 Lowell RoadD 14 513 TELTOW / Germany Hudson, NH 03051 / USA10341501612046160164306017017040801801805010319020560121195230701342002558014320523090150210205100154215180110156220165120158230140130159240120HistoryVersion Reason of Changes Name Date1.5 Change date code from month to week Dr. Wall17.03.2000Change errors in tape an reel informationRemove ‘Construction and Pin Connection’ from page 1Guarantee better values for stability characteristic1.6 Tape drawing with part position added.André du Hamél12.04.2001 VI TELEFILTER Vectron International Inc. Potsdamer Straße 18 267 Lowell RoadD 14 513 TELTOW / Germany Hudson, NH 03051 / USA。
NETGEAR AC750 WiFi Range Extender 产品说明书

Boost your existing WiFiOverviewNETGEAR AC750 WiFi Range Extender boosts your existing network range, delivering AC dual band WiFi up to 750 Mbps. It works with any standard WiFi router & is ideal for HD video streaming & gaming. Get the connectivity you need for iPads®, smartphones, laptops & more.• Dual band WiFi up to 750 Mbps• Supports new 802.11ac & b/g/n WiFi devices • External antennas for better performanceRANGEDUAL BAND AC750AC750 WiFi Range Extender—802.11ac Dual Band GigabitData SheetEX6100Simultaneous Dual Band WiFiExtend 2.4 & 5GHz WiFi up to 750Mbps & reduce interference.FastLane™ TechnologyUse both WiFi bands to establish one super high-speed connection; ideal for HD streaming & gaming.More WiFi StandardsCreate faster access for 802.11 b/g/n & ac WiFi devices.Gigabit Ethernet PortConnect a wired device like Blu-ray® player,game console, smart TV or streaming player to your WiFi network.External AntennasFor better WiFi coverage.Two WiFi ModesExtender mode to boost existing WiFi.Access Point mode to create new AC WiFi access.Smart LED indicators help find the best extenderplacement for optimal WiFi coverage while displaying real-time, extender network status.Easy, secured connection at the push of a button for either WiFi Range Extender modeor Access Point mode setup.Existing WiFiSometimes your router does not provide the WiFi coverage you need.ExtenderBoosts the range of your existing WiFi & creates a stronger signal in hard-to-reach areas.Network ConnectionsSecure Connection (WPS)Power on/o Extender or Access Point mode switch Gigabit Ethernet portSmart LED indicatorsAC750 WiFi Range Extender—802.11ac Dual Band Gigabit Data SheetEX6100 WiFi Analytics AppHow strong is your WiFi signal? Use the NETGEAR WiFi Analytics app & get advanced analytics to optimize your existing or newly extended WiFi network. Check your network status, WiFi signal strength, identify crowded WiFi channels & much more!Here’s what you can do with the WiFi Analytics App!• Get a network status overview• Check WiFi signal strength• Measure WiFi channel interference• Keep track of WiFi strength by location• and more...Scan to install appThis product comes with a limited warranty that is valid only if purchased from a NETGEAR authorized reseller.*90-day complimentary technical support following purchase from a NETGEAR authorized reseller.1Works with devices supporting WPS.Data throughput, signal range, and wireless coverage per sq. ft. are not guaranteed and may vary due to differences in operating environments of wireless networks, including without limitation building materials and wireless interference. Specifications are subject to change without notice.The product may not be compatible with routers or gateways with firmware that has been altered, is based on open source programs, or is non-standard or outdated.NETGEAR, and the NETGEAR Logo are trademarks of NETGEAR, Inc. Mac and the Mac logo are trademarks of Apple Inc. Any other trademarks herein are for reference purposes only. ©2016 NETGEAR, Inc.NETGEAR, Inc. 350 E. Plumeria Drive, San Jose, CA 95134-1911 USA, /supportD-EX6100v2-0AC750 WiFi Range Extender—802.11ac Dual Band Gigabit Data SheetEX6100Package Contents• AC750 WiFi Range Extender (EX6100 v2) • Installation guidePhysical Specifications• Dimensions: 4.80 x 2.91 x 1.50 in (122 x 74 x 38 mm)• Weight: 0.47 lb (0.213 kg)Warranty• NETGEAR 1-year limited warrantySecurity• WiFi Protected Access® (WPA/WPA2—PSK) and WEPStandards• IEEE® 802.11 b/g/n 2.4GHz • IEEE 802.11 a/n/ac 5GHz• One (1) 10/100/1000 Mbps Gigabit Ethernetport with auto-sensing technologySupport• 90-day complimentary technical support*Ease of Use• CD-less setup—great for mobile devices • Push ‘N’ Connect using WPS 1System Requirements• 2.4 and/or 5GHz 802.11 a/b/g/n/ac WiFi router or gateway• Microsoft® Internet Explorer® 5.0, Firefox® 2.0 or Safari® 1.4 or Google Chrome 11.0 browsers or higher。
- 1、下载文档前请自行甄别文档内容的完整性,平台不提供额外的编辑、内容补充、找答案等附加服务。
- 2、"仅部分预览"的文档,不可在线预览部分如存在完整性等问题,可反馈申请退款(可完整预览的文档不适用该条件!)。
- 3、如文档侵犯您的权益,请联系客服反馈,我们会尽快为您处理(人工客服工作时间:9:00-18:30)。
Application TechniqueApplication Guidelines for 12-Pulse Operation of PowerFlex 750-Series AC Drives2Rockwell Automation Publication 750-AT003A-EN-P - March 2014Application Guidelines for 12-Pulse Operation of PowerFlex 750-Series AC DrivesImportant User InformationRead this document and the documents listed in the additional resources section about installation, configuration, and operation of this equipment before you install, configure, operate, or maintain this product. Users are required tofamiliarize themselves with installation and wiring instructions in addition to requirements of all applicable codes, laws, and standards.Activities including installation, adjustments, putting into service, use, assembly, disassembly, and maintenance are required to be carried out by suitably trained personnel in accordance with applicable code of practice.If this equipment is used in a manner not specified by the manufacturer, the protection provided by the equipment may be impaired.In no event will Rockwell Automation, Inc. be responsible or liable for indirect or consequential damages resulting from the use or application of this equipment.The examples and diagrams in this manual are included solely for illustrative purposes. Because of the many variables and requirements associated with any particular installation, Rockwell Automation, Inc. cannot assume responsibility or liability for actual use based on the examples and diagrams.No patent liability is assumed by Rockwell Automation, Inc. with respect to use of information, circuits, equipment, or software described in this manual.Reproduction of the contents of this manual, in whole or in part, without written permission of Rockwell Automation, Inc., is prohibited.Throughout this manual, when necessary, we use notes to make you aware of safety considerations.Labels may also be on or inside the equipment to provide specific precautions.Allen-Bradley, PowerFlex, Rockwell Software, and Rockwell Automation are trademarks of Rockwell Automation, Inc.Trademarks not belonging to Rockwell Automation are property of their respective companies.WARNING: Identifies information about practices or circumstances that can cause an explosion in a hazardous environment,which may lead to personal injury or death, property damage, or economic loss.ATTENTION: Identifies information about practices or circumstances that can lead to personal injury or death, property damage, or economic loss. Attentions help you identify a hazard, avoid a hazard, and recognize the consequence.IMPORTANTIdentifies information that is critical for successful application and understanding of the product.SHOCK HAZARD: Labels may be on or inside the equipment, for example, a drive or motor, to alert people that dangerousvoltage may be present.BURN HAZARD: Labels may be on or inside the equipment, for example, a drive or motor, to alert people that surfaces mayreach dangerous temperatures.ARC FLASH HAZARD: Labels may be on or inside the equipment, for example, a motor control center, to alert people topotential Arc Flash. Arc Flash will cause severe injury or death. Wear proper Personal Protective Equipment (PPE). Follow ALLRegulatory requirements for safe work practices and for Personal Protective Equipment (PPE).Application Guidelines for 12-Pulse Operation of PowerFlex 750-Series AC Drives Document Scope The scope of this document is to provide application guidelines for 12-pulseoperation of PowerFlex 750-Series, frames 6…10, 400V…690V AC input drives.While several different transformer configurations are possible, only thecommonly used delta-delta-wye transformer, which provides 30 degree phaseshift between the two sets of secondary windings is addressed. The guidelinesinclude sizing of the transformer and rectifier, grounding considerations, pre-charge, and circuit protection recommendations.Drive Harmonics and Impact on Supply Network Standard AC drive topologies consist of AC-DC-AC power conversion with a 3-phase, 6-pulse rectifier bridge consisting of diodes or SCRs. An AC drive is a non-linear load on the utility power supply; a buffered (with AC line reactor or DC link choke) 6-pulse bridge generates close to 40% current total harmonic distortion (THD). In addition, harmonic currents produced by a rectifier are the cause of voltage THD at the secondary of the transformer that feeds other loads as well – generally referred to as a point of common coupling (PCC). The extent of voltage distortion depends on the stiffness of the power supply (kVA rating and impedance of the transformer or generator). The stiffness of the power supply is measured by the short circuit ratio, which is the ratio of the available short-circuit current to the rated full load current.The one-line diagram in Figure1 illustrates a typical industrial plant with AC drive loads, and different PCC where harmonic distortion measurements could be made. The dominant harmonics for 6-pulse, 12-pulse and 18-pulse rectifiers are {5th, 7th}, {11th, 13th} and {17th, 19th} respectively.Figure 1 - Typical Power Distribution with Harmonic Distortion Measurement PointsRockwell Automation Publication 750-AT003A-EN-P - March 20143Application Guidelines for 12-Pulse Operation of PowerFlex 750-Series AC DrivesFigure2 is the equivalent circuit for power distribution of Figure1. Non-linearloads are represented by current sources at multiple characteristic harmonicfrequencies.Figure 2 - Non-linear Load Current SourcesThe harmonic current magnitudes in Figure2 depend on the source stiffness andany internal or external buffering (DC link choke or AC line reactor) in the ACdrive. When the harmonics currents generated by non-linear loads flow throughthe system impedances, voltage distortion is created. This affects other loadsconnected at the PCC nodes. With a generator source that has high internalimpedance (typically 25%), significant voltage distortion could be created bynon-linear loads, which could adversely affect other loads at the PCC nodes.Background voltage distortion, such as pre-existing voltage harmonics or voltageunbalance, can also affect the current harmonic distortion of non-linear loads.This is particularly true for multi-pulse rectifiers that rely on special transformerconfigurations to generate phase-shifted voltages, as will be discussed later in thisdocument for 12-pulse drive systems.Harmonics standards, such as IEEE 519-1992, specify maximum current THDand limits for individual harmonic current magnitudes (Table 10.3 of IEEE519-1992), and voltage THD (Table 10.2 of IEEE 519-1992) at the PCC, as afunction of the short-circuit ratio. While PCC in this definition refers to PCC1shown in Figure1, customers may expect conformance to the specifications atPCC2 or PCC3 shown in Figure1, where linear and non-linear loads areconnected.The detrimental effects of harmonics include increased losses in powerdistribution and generators, de-rating of transformers due to harmonic currents,and susceptibility of loads to voltage distortion. T o determine transformer de-rating, a quantity called the K-factor, defined as follows, is used (I1 is thefundamental current and I n is the harmonic current of order n). The K-factor for6-pulse and 12-pulse drives is about 6 and 2 respectively, while it is nearly equal tothe ideal value of 1 for 18-pulse drives. Background voltage distortion andunbalance will affect this significantly, particularly for 12-pulse and 18-pulsedrives that require special phase-shifting transformer configurations.4Rockwell Automation Publication 750-AT003A-EN-P - March 2014Application Guidelines for 12-Pulse Operation of PowerFlex 750-Series AC DrivesT ransformer de-rating as a function of K-factor is shown in Figure3.Figure 3 - Transformer De-rating for Non-linear LoadsRockwell Automation Web-Based Harmonics Simulation ToolsW eb-based harmonics simulation tools provided by Rockwell Automation are part of a suite of simulation tools hosted by T ransim® T echnology Corporation. Users are only required to have an internet connection and a web browser to run the simulation on a remote server. All Rockwell Automation employees and distributors have access to the tool and must connect from within the Rockwell Automation firewall.The web-based simulation tools can be accessed at:/rockwellCurrently, there are two harmonics simulation tools, which are intended for different applications as described below.Spreadsheet-Based Harmonics Calculator ToolThe harmonics calculator is a spreadsheet based tool, which uses look-up tables to estimate the voltage and current harmonics at different nodes in a network consisting of multiple linear and non-linear loads. Only numerical outputs are provided including checks for conformance to harmonics standards. This tool is more flexible than the harmonics simulator tool in terms of the load configurations that can be simulated.ܭ=Σ(݊I݊I1/)2ܰ2Σܰ2(I݊I1/)2Rockwell Automation Publication 750-AT003A-EN-P - March 201456Rockwell Automation Publication 750-AT003A-EN-P - March 2014Application Guidelines for 12-Pulse Operation of PowerFlex 750-Series AC DrivesThe harmonics calculator doesn’t take into account the effects of pre-existing voltage distortion or unbalance. Interaction between loads is also not considered. The harmonic contributions of different loads arenumerically added, without considering phase shift. Hence, the results are conservative.The system configuration can be specified on the landing page for the harmonics calculator tool, as shown in Figure 4. The Notes tab has useful information on how to use the program, criteria for pass/fail and assumptions made to calculate harmonics. The Tutorial tab has an illustrative example with instructions on how to use system one-line diagrams to enter data into the harmonics calculator.Figure 4 - Web-based Harmonics Calculator Tool Data Input PageThe General Parameters section, bottom left in Figure 4, are default values and should work in most applications. The Notices section is active after a simulation run and includes design checks (for example, transformer rating exceeded) and useful information like Active Filter current rating required to meet targetcurrent THD.Rockwell Automation Publication 750-AT003A-EN-P - March 20147Application Guidelines for 12-Pulse Operation of PowerFlex 750-Series AC DrivesDifferent topologies of 6-pulse, 12-pulse and 18-pulse drives can be specified, as shown in Figure 5. For the delta-delta-wye 12-pulse transformer, the ISO xfmr option can be used. This tool doesn’t consider the effect of transformerimpedance mismatch and circulating currents, which will be explained later in this document.Figure 5 - Web-based Harmonics Calculator Tool, 6-pulse, 12-pulse and 18-pulse Drive ConfigurationsApplication ExampleThis application example demonstrates the effect of multi-pulse rectifiers on voltage and current distortion.For a system consisting of a 2 MVA utility transformer, 1.5 MVA usertransformer and 700 Hp, 6-pulse load (buffered with DC link choke), the voltage and current THD at the 3 PCC points as identified in Figure 4, conformance to the IEEE 519 standard, and the active filter current rating required to meet target current THD of 5% at PCC1 and PCC2 are shown in Figure 6 on page 8.Application Guidelines for 12-Pulse Operation of PowerFlex 750-Series AC DrivesThe Results (top) section in Figure6 shows voltage and current THD at 3 PCCnodes. The Intermediate calculations (bottom) section shows intermediatecalculations for harmonic currents, voltages and active filter current ratingrequired to meet 5% current THD.Figure 6 - Harmonics Calculator Simulation Results for 6-pulse Drive Load8Rockwell Automation Publication 750-AT003A-EN-P - March 2014Application Guidelines for 12-Pulse Operation of PowerFlex 750-Series AC Drives The results of a 700 Hp drive with a 12-pulse rectifier (delta-delta-wye isolation transformer) are shown in Figure7. Note that the 12-pulse rectifier considerably reduces current and voltage distortion, and helps meet the IEEE 519 limits for current THD at PCC1 and PCC2 (limit is 8% based on the short-circuit ratio). The Results (top) section in Figure7 shows the voltage and current THD at 3 PCC nodes. The Intermediate Calculations section show the intermediate calculations for harmonic currents, voltages and active filter current rating required to meet 5% current THD.Figure 7 - Harmonics Calculator Simulation Results for 12-pulse Drive LoadRockwell Automation Publication 750-AT003A-EN-P - March 2014910Rockwell Automation Publication 750-AT003A-EN-P - March 2014Application Guidelines for 12-Pulse Operation of PowerFlex 750-Series AC DrivesHarmonics Circuit Simulator ToolThe harmonics simulator is a circuit simulation tool with one or two load branches. Each of the loads can be set to be of a specific type. W aveforms of voltage and current at different points of common coupling aregenerated along with numerical values for voltage and current THD, and checks for conformance to harmonics standards.The one-line diagram of the system that is simulated is shown in Figure 8. On each branch, the load can only be of a certain type; currently only 6-pulse or 18-pulse drives are supported on each individual transformer. Pre-existing distortion at the output of the utility transformer, 5thharmonic and voltage unbalance, can be set. T ransformer B can be set to either delta-delta or delta-wye. T o simulate a 12-pulse load, 6-pulse loads must be added on each transformer, and T ransformer B must be set to delta-delta.Figure 8 - Web-based Harmonics Circuit Simulation Tool Data Input PageW aveforms of voltage and current at the output of T ransformer A, voltage and current THD are shown in Figure9.Figure 9 - Harmonics Simulator Results for 6-pulse, Single-branch Load12-pulse Drive Configurations There are two main configurations of 12-pulse systems; true 12-pulse, and quasi12-pulse systems, as shown in Figure 10. In the true 12-pulse system, 3-phasevoltages from the utility transformer are converted to two sets of 3-phase voltages with 30 degrees of phase shift between the sets. Each set of 3-phase voltages arefed to a full wave bridge rectifier, whose DC output has 12 pulses perfundamental line cycle. A common method to achieve the 30 degrees of phaseshift is to use a transformer with delta and wye secondary windings.In the quasi 12-pulse system, two separate 3-phase drive loads are fed by acommon transformer. The 3-phase voltages to one load are phase shifted by 30degrees from the other. For perfect harmonic cancellation and to achieve 12-pulse harmonic performance at the primary of the transformer, the loads mustbalanced.Figure 10 - 12-pulse System ConfigurationsTrue 12-pulse SystemQuasi 12-pulse SystemHarmonic Cancellation in 12-pulse Drive ConfigurationsThe predominant line current harmonics in a 3-phase, 6-pulse rectifier are the 5th and 7th harmonics of the fundamental. In a 12-pulse system, for both true12-pulse and balanced loads on quasi 12-pulse, the 5th and 7th harmonics are cancelled as demonstrated in the phasor diagram of Figure11. Then, the dominant harmonics are the 11th and 13th, which are significantly lower in amplitude than the 5th and 7th. However, pre-existing voltage distortion and unbalance will significantly affect the performance of any 12-pulse system, as will be shown later.Figure 11 - Cancellation of 5th and 7th Harmonics in a 12-pulse Drive(a)(b)12-pulse Configurations for PowerFlex 750-Series Drives, Frames 6 (10)For PowerFlex 750-Series drives, frames 6…10, several different 12-pulse configurations are possible, as shown in Figure12, and Figure13 and Figure14 on page 15.In the configuration shown in Figure12, which is also similar to the configuration shown in Figure13 and Figure14, using the delta-delta-wye transformer and two rectifier bridges, a 12-pulse DC bus supply is created. Although shown specifically for frames 6...8, this configuration can be used to achieve true 12-pulse input for any combination of frames 6...10 DC input drives on the DC bus. With a diode rectifier front-end, integral pre-charge is required in the DC input drives, which is present on PowerFlex 750-Series frames 6 (10)drives.Quasi 12-pulse operation with AC input frames 6…10 drives can be achieved by distributing the load evenly between the delta and wye secondary windings. Figure 12 - External Rectifier Bridges for PowerFlex 750-Series Frames 6…8 Drives with DC InputFigure 13 - external Rectifier Bridges for PowerFlex 750-Series Frame 9 Drive with DC InputFigure 14 - External Rectifier Bridges for PowerFlex 750-Series Frame 10 Drive with DC InputRecommendations for sizing the AC line reactor are provided in T ransformer,AC Line Reactor and Rectifier Sizing on page 17.For a true 12-pulse configuration (as shown in Figure 12…Figure 14) the system can be solidly grounded or high resistance grounded at the neutral point of the wye secondary winding as shown in Figure 15. Since the delta secondary winding is not galvanically isolated from the wye secondary winding because of theinterconnection at the DC bus, it should not be separately grounded using agrounding transformer, as would typically be done for a single transformer with delta secondary winding.With the wye secondary neutral solidly grounded, the system behaves like asolidly grounded system. If the circuit protection on the wye winding were toopen (blown fuse or tripped circuit breaker), the rectifier on the delta secondary winding must also be disconnected from its supply and/or the inverters on theDC bus must be disabled. A fault must be enunciated.The co-ordination of protection between the delta and wye secondary windings described above also applies to a high resistance grounded system. In this case, the system must be equipped with a suitable ground fault detection device to indicate the presence of a fault.Figure 15 - True 12-pulse Drive GroundingFor quasi 12-pulse configurations, the delta winding must be groundedseparately, either solidly grounded or high resistance grounded, using a grounding transformer.On high resistance grounded and ungrounded systems, common-modecapacitors and transient suppression device networks must not be connected to ground. This is covered in more detail in Fusing, T ransient Over-voltageProtection and Common-Mode Jumper Recommendations on page 20.Solid ground on wye secondary winding High resistance ground on wye secondary windingFor 12-pulse configurations that have diode bridge rectifiers, the DC input drives must have integral pre-charge. PowerFlex 750-Series, frames 6…10 drives with DC input all have integral pre-charge. On frames 6 and 7, the pre-charge circuit consists of a resistor in the +DC bus with SCR bypass and an anti-parallel diode for regenerative current flow. On frames 8…10, pre-charge resistors are placed on both +DC and –DC, with a Molded Case Switch (MCS) for bypass.If SCR bridge rectifiers that have phase angle controlled pre-charge are used, then they must have independent means to synchronize to the phase shifted voltages. PowerFlex SCR Bus Supplies have this feature when two master units are used. See the PowerFlex SCR Bus Supply User Manual, publication 20S-UM001, for further information and particular parameter settings required for 12-pulse operation.Transformer, AC Line Reactor and Rectifier Sizing In this section, guidelines for sizing the transformer, AC line reactor and rectifier are provided. While the guidelines are based on certain assumptions for background voltage distortion (3% 5th harmonic voltage and 1% line unbalance), more severe background voltage distortion can result in higher continuous rating requirements for these components.Rectifier and AC Line Reactor SizingFor the true 12-pulse configuration of Figure12, the causes of current unbalance between the two rectifier bridges are:a.Fundamental voltage mismatch between delta and wye windings. Theturns ratio between the delta and wye windings must ideally be .Since this is a non-integral ratio, the output voltages will not be perfectly balanced.b.Impedance mismatch between the delta and wye windings due todifferences in the number of turns and winding geometry. This asymmetry also presents different commutation inductances to the rectifier bridges.c.Pre-existing 5th harmonic voltage has a different phase relationship withrespect to the fundamental on the delta and wye secondaries.d.Source voltage unbalance affects the delta and wye secondaries differently,due to the phase shift between them.The extent of current unbalance can be reduced by adding an AC line reactor to each bridge. The impedance of the reactor minimizes the effect of impedance asymmetry between the delta and wye secondary windings, and helps to reduce the current unbalance caused by voltage unbalance or pre-existing voltage distortion. A line reactor sized at 3% impedance based on the rated voltage and current of one rectifier bridge is sufficient.3:1For rectifier sizing, the worst case pre-existing distortion assumed is 3% of 5th harmonic distortion and 1% voltage unbalance. This results in worst case current sharing of 65%:35%. For example, if the total RMS AC input current for the drive is 100 A with 6-pulse input, each rectifier bridge must be sized for 65 A. Current unbalance as a function of pre-existing voltage unbalance and distortion is shown in Figure 16 for the 12-pulse configuration of Frames 6…10 with DC input. The line reactor is required to ensure low ripple on the DC bus of the DC input drives and to balance the currents between the rectifier bridges when the input voltages are unbalanced or have significant harmonic distortion.If the drive’s RMS AC input current for 6-pulse operation is I line_6P (For drive input current ratings, see the PowerFlex 750-series AC Drives T echnical Data, publication 750-TD001), then the line reactor inductance (L AC ) required is determined as follows, where V LL is the AC RMS voltage of each secondary winding and f line is the line frequency:Figure 16 - Current Unbalance with AC Line Reactor Voltage distortion at the primary side of the transformer can vary fromapproximately 4% THD with utility source to about 10% THD with generator source (typical impedance of 25%). This must be considered for other loads connected at the point of common coupling (PCC1 in Figure 1 on page 3 and Figure 2 on page 4).C u r r e n t U n b a l a n c e (%)Transformer Sizing and SpecificationsT ransformer kVA rating is based on worst case current unbalance between the delta and wye secondary windings.Given that the drive’s input AC RMS current for 6-pulse input is I line_6P and with the worst case unbalance of 65:35 between the two rectifier bridges, the total kVA rating of the transformer is determined as follows. The AC RMS voltage of each secondary winding is V LL. Since each secondary winding carries 6-pulse currents, an appropriate de-rating factor is applied:Further, the open circuit voltage of the secondary windings must be matched. The impedance of the transformer must be between 4…6%. The K-factor of the transformer must be greater than 6 to handle the harmonic currents.The selection of PowerFlex SCR bus supplies for true 12-pulse operation of PowerFlex 750-Series, frames 6…10 drives, along with Bulletin 1321 line reactor catalog numbers and minimum transformer kVA is provided in PowerFlex SCR Bus Supply Selection Chart for 12-pulse Operation of PowerFlex 750-Series, Frames 6…10 Drives on page 21.Electrostatic Shielding:If the voltage on the primary side of the transformer is greater than twice the secondary voltage, an electrostatic shield between the primary and secondary windings is strongly recommended to prevent transients on the high voltage side from propagating to the secondary windings. An electrostatic shield reduces the capacitive coupling between the primary and secondary, and must be tied to ground. In addition, it is also recommended that the neutral of the wye secondary winding be solidly grounded. However, high resistance grounding with proper choice of resistance value to limit secondary transient voltage to ground is also acceptable. For quasi 12-pulse systems, the delta winding must be solidly grounded or high resistance grounded using a grounding transformer.Fusing, Transient Over-voltage Protection and Common-Mode Jumper Recommendations The recommended method for fusing and transient overvoltage protection is illustrated in Figure17. The AC line fuses, typically high speed semiconductor fuses, should be integral to the rectifier bridge and are intended for short circuit protection of the rectifier power device. PowerFlex SCR bus supplies have AC fuses (on the 400 A and 600 A units, the fuses are on the AC line; on the 1000 A unit, the fuses are in series with each SCR device). If the rectifier bridge includes an integral capacitor bank, DC bus fuses should be placed after the capacitor bank and before the interconnection to the system DC bus, to prevent faults from cascading. PowerFlex SCR bus supplies do not have integral capacitor banks; however, the units rated at 400 A and 600 A have integral DC fuses, whereas the 1000 A unit does not have DC fuses.Metal oxide varistors (MOV) are used for transient overvoltage protection and should be part of the rectifier power structure. PowerFlex SCR bus supplies have integral MOVs.Fuses or circuit breakers should be used for branch circuit protection, with ratings in accordance with the NEC in the United States or local electrical codes as applicable. This is to protect each transformer secondary winding and the cabling to the rectifier bridge from overloads and short-circuits. The current rating to use for selection of the branch circuit protective device is 0.65I line_6P, where a 65%:35% split is assumed for current sharing between the two rectifier bridges, and I line_6P is the drive’s rated input RMS current for 6-pulse operation. If the secondary wye winding of the transformer is not solidly grounded, then any common mode capacitor networks on the AC line or DC bus (on both the rectifier bridges and the drives on the DC bus), and the MOVs must be disconnected from ground. For instructions on how to disconnect the MOVs and common mode capacitors, see the PowerFlex SCR Bus Supply User Manual, publication 20S-UM001, and the PowerFlex 750-Series AC Drives Installation Instructions, publication 750-IN001.T o achieve compliance with the EMC directive of IEC, the AC system must be solidly grounded at the wye secondary and the common mode capacitor networks must be connected to ground.Figure 17 - 12-pulse Drive Branch Circuit Protection, Fusing and Transient Overvoltage ProtectionApplication Guidelines for 12-Pulse Operation of PowerFlex 750-Series AC DrivesPowerFlex SCR Bus Supply Selection Chart for 12-pulse Operation of PowerFlex 750-Series, Frames 6…10 DrivesTable1…Table4, beginning on page 22, provide the PowerFlex SCR bus supply and Bulletin 1321 line reactor catalog numbers, ratings for input branch circuit protection devices, and the kVA rating of the delta-delta-wye transformer for use with PowerFlex 750-Series, frame 6…10 drives.The ratings specified in the tables are based on maximum voltage unbalance of 1% and 5th harmonic distortion of 3%, which is a conservative estimate of worst case power quality. However, if the voltage unbalance or harmonic distortion exceeds these values, then the current unbalance between the rectifier bridges will exceed the assumptions made in Table1…Table4, requiring higher current rating for the rectifier, transformer and branch circuit protective device. Please contact Rockwell Automation T echnical Support for assistance in sizing the components.Rockwell Automation Publication 750-AT003A-EN-P - March 201421。