E1立辊轧机
本钢1700mm热连轧E1立辊轧机改造

E 立辊 轧机 的基础 。 构有混凝土结构和制作钢结构底座 1 结 方 式 。预先制造 好钢结构底 座基础 , 利用原有 地脚螺栓 固 定, 这种方式 , 工方便 、 施 工期 短、 运行 可靠 。因此 , 1轧机 E
轧 机 , 行技 术改 造 。 进 1 问 题 的 分 析 及 改 造 的 对 策
整体 更新 改 造 El 辊 轧 机 需 安 装 在 R1轧 机 的 前 面 , 立
利 用原有设 备和基础 的条 件、 用最短 的安 装工期 , E1立 是
辊 轧 机 改 造成 功 的 关键 。 11 E . i立辊 轧机 基 础 的 结 构 形 式
圈 2 E 轧机机架与 R 轧机机 架的安装结构示意 l l
1 Rl 机 机 架 } 一平 键 ;- 1组斛 键 ‘ 一 轧 2 3 4 E 一 l轧 机 机 架
每根地脚螺栓施加 5 0 N 的预 紧力 锁紧螺纹 。 1k
1 3 E1 辊 轧 机 机 架 的 固定 方 式 . 立
基 础 采 用 钢结 构 底 座 基 础 结 构
1 2 地 脚 螺 栓 接 长 的方 法 .
E1 轧机基础采 用钢结构底座后 , 利用原有地脚螺
栓 固定 设 备 。 脚螺 栓 露 出 部 分 , 度不 够 。 用螺 纹 接 长 地 长 采 地 脚 螺 栓 的 方 式 , 作 一 根 有 内 、 螺 纹 的螺 栓 , 端 为 内 制 外 一 螺 纹 M6 , 一 端 为 外 螺 纹 M 7 , M6 4另 2用 4内螺 纹 端 拧 在 地 脚 螺栓上 , 地脚螺栓接 长 , 定钢结构底座基础 ( 把 固 详见 图 1 。 )
热轧板带轧机立辊压下油缸结构优化设计

热轧板带轧机立辊压下油缸结构优化设计摘要: E1立辊轧机位于R1四辊粗轧机入口侧,用于控制板坯的宽度和形状,同时将板坯的边部由铸态组织变为轧态组织,避免在水平轧制中产生边裂,同时有破鳞的作用。
E1立辊轧机侧压装置分布于轧机传动侧和操作侧,两侧侧压装置共同作用可调整轧辊的开口度,每侧由安装在机架上的立辊压下AWC液压缸与相应侧的平衡液压缸共同调整轧辊的位置。
关键字:热轧;AWC油缸;结构改造一、绪论1、侧压装置原理侧压装置油缸部分主要油缸为4个AWC油缸和2个侧压平衡缸组成,AWC油缸和侧压平衡缸提供侧压主要动力。
4个AWC油缸将立辊向轧制中心推动,2个侧压平衡缸将立辊往两侧回拉,以消除间隙。
2、近期AWC系统故障处理汇总及分析2017年5月以来,AWC油缸发生多起前端盖密封漏油、前后端盖螺丝崩断、前后端盖漏油故障,这些故障处理时间都较长,严重影响生产节奏。
现针对现场使用实际,拟对AWC油缸结构进行部分改造。
二、AWC油缸现场使用情况分析1、AWC油缸受力分析AWC油缸通过两个半圆法兰固定安装在轧机牌坊上,AWC油缸受力分析,油缸受力示意图如下:(1)粗轧AWC控制由4台AWC液压缸及其控制系统构成。
工作侧2台AWC缸、传动侧2台AWC缸。
每台AWC缸由1台三级伺服阀控制。
通过计算机控制伺服阀进油或者回油,从而控制立辊的开合,实现AWC与SSC控制。
(2)油缸安装形式解析:油缸安装在立辊牌坊的孔内,安装时油缸从牌坊外侧装入牌坊孔内,油缸与牌坊孔只存在同心关系,缸筒外壁与牌坊孔无磨擦力约束。
半圆块螺栓紧固安装在牌坊上,半圆块卡住油缸缸筒安装位,两者会有部分静磨擦力,但可忽略不计,油缸有杆腔端盖端面与半圆块接触。
(3)油缸工作过程受力分析:立辊开度调节是由伺服阀控制进入AWC油缸无杆腔的液压油量来控制活塞杆的伸出/缩回进行精确调整,当AWC缸活塞杆动作到指定位置,封油柱完成,在轧制过程中油缸缸筒与无杆腔油液、无杆腔端盖、活塞杆、活塞环,近似可看作刚性结构,承受轧制负载。
FE1立辊

F1E立辊轧机I 用途:将粗轧后的板坯配合精轧机一起轧制成成品带钢。
II 结构简图、设备组成及用途:F1E立辊轧机由主传动装置、立辊机架装配、左右侧辊缝调整装置、轧辊轴承、吊具、配管及平台等部件组成。
立辊主传动采用立式交流电机上传动型式,由2台立式电机通过主传动减速机驱动立辊实现轧制。
立辊辊缝调整装置用于移动立辊调整立辊开口度,以满足轧制程序表中所列压下规程的要求。
辊缝的予设定是通过被分别设在立辊轧机的操作侧、传动侧的压下液压缸来完成的。
两侧压下采用液压同步,设位移传感器、压力传感器、测压仪。
与水平辊采用微张力控制、左、右主传动电气同步。
III 技术数据:中间坯料规格:厚度:30~ 60mm宽度:1200~2000mm最大轧制力1500KN最大轧制力矩315KN·M最大轧制速度0~1.3~3.2m/s轧辊开口度1150~2150mm轧辊直径Φ570~630mm辊身长度250mm轧辊材质60CrNiMo 锻钢主传动电机(立式) 2×370KW 200/500 r/min主传动减速机减速比i=5.28侧压压下速度(单侧)30~ 60 mm/s侧压液压缸φ350/φ300×1400 mm液压缸系统工作压力20Mpa压下量:Max 5mm(坯厚60 mm时)侧压平衡缸ф100/ф56×25mm平衡缸系统工作压力20Mpa(差动)速度80 mm/s主传动轴:十字头万向接轴接轴提升缸ф140/ф80×600mm工作压力16Mpa速度50 mm/sIV 工作方式:1 主传动为连续续工作制。
VI 电气、自动化控制及连锁:1、F1E立辊与F1水平辊轧机进行微张力控制。
2、两台主传动电机进行电气同步控制。
3、侧压开口度精度0.5-1mm。
4、两侧侧压液压同步精度1mm。
正常工作时,侧压平衡缸随动。
(杆腔保持衡压力)5、换辊时:主传动准确停车,侧压缸带动轧辊到接轴垂直位置,用接轴提升缸将接轴收缩550mm与轧辊脱开。
(完整版)E1立辊轧机
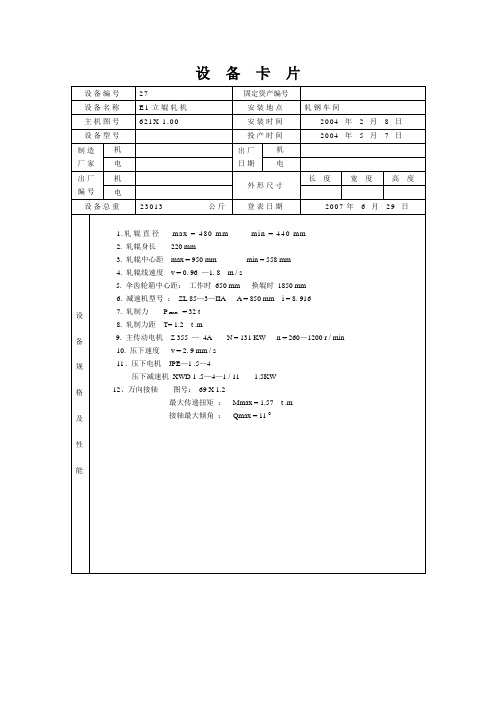
设备编号
27
固定资产编号
设备名称
E1立辊轧机
安装地点
轧钢车间
主机图号
621X 1.00
安装时间
2004年2月8日
设备型号
投产时间
2004年5月7日
制造厂家
机
出厂日期
机
电
电
出厂编号
机
外形尺寸
长度
宽度
高度
电
设备总重
23013公斤
登表日期
2007年6月29日
设
备
规
格
及
性
能
1.轧辊直径max = 480 mm min = 440 mm
2.轧辊身长220 mm
3.轧辊中心距max = 950 mm min = 558 mm
4.轧辊线速度v = 0. 96—1. 8 m / s
5.伞齿轮箱中心距:工作时650 mm换辊时1850 mm
6.减速机型号:ZL 85—3— A A = 850 mmi = 8.916
7.轧制力Pmax= 32 t
最大传递扭矩:Mmax = 1.57 t .m
接轴最大倾角:Qmax = 110
主要备件更换记录
更换日期
名称
图号
材质
更换原因(注明是在大、中、小修或抢修事故更换)
保养检修记录
检查日期
主要检修内容
记事及遗留问题
设备事故登记
单位名称:车间名处理情况
停产时间
8.轧制力距T= 1.2 t .m
9.主传动电机Z 355—4A N = 131 KW n = 260—1200 r / min
10.压下速度v = 2. 9 mm / s
粗轧区域设备参数
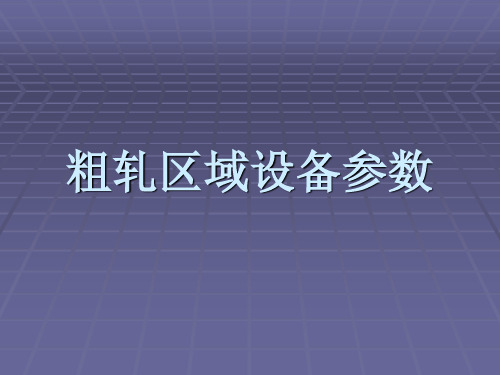
R1/R2轧机前后推床作用 R1/R2轧机前后推床作用
推床位于热连轧生产线粗轧机机前、 推床位于热连轧生产线粗轧机机前、机后工作辊道上方其作用是把在辊道 运输中跑偏的钢坯推正,对中轧制线并送入粗轧机进行多道次轧制, 运输中跑偏的钢坯推正,对中轧制线并送入粗轧机进行多道次轧制,以减 少或避免钢坯出现镰刀弯,对粗轧机轧制板型的好坏起着重要作用。 少或避免钢坯出现镰刀弯,对粗轧机轧制板型的好坏起着重要作用。推床 采用电气或液压伺服阀控制,当推板在完成对坯料对中的功能后,可以迅 采用电气或液压伺服阀控制,当推板在完成对坯料对中的功能后, 速退开, 速退开,以防止由于镰刀弯过大或不规整钢坯在轧制时对推板产生过大侧 向力而使推杆弯曲, 向力而使推杆弯曲,破坏设备。
高压水除鳞的重要性
钢坯在高温状态下被氧化, 钢坯在高温状态下被氧化,在其表面形成一 层致密的氧化铁皮(鳞皮)。 )。在轧制前如果不能 层致密的氧化铁皮(鳞皮)。在轧制前如果不能 将这层氧化铁皮除去, 将这层氧化铁皮除去,在轧制过程中它们会被轧 辊压入到带钢表面,影响其表面质量。 辊压入到带钢表面,影响其表面质量。残留的氧 化铁皮也会加速轧辊的磨损, 化铁皮也会加速轧辊的磨损,降低轧辊的使用寿 如带钢需要酸洗时, 命。如带钢需要酸洗时,残留的氧化铁皮会增加 酸洗的难度,增加酸耗。因此,在钢坯轧制前, 酸洗的难度,增加酸耗。因此,在钢坯轧制前, 必须除去表面的氧化铁皮。 必须除去表面的氧化铁皮。利用高压水的机械冲 击力来除去氧化铁皮(高压水除鳞) 击力来除去氧化铁皮(高压水除鳞)的方法是目 前最通行有效的作法。 前最通行有效的作法。
除磷后效果
除磷前效果
R1机前运输辊道 R1机前运输辊道
R1机前运输辊道由:联轴器、冷却水系统、 R1机前运输辊道由:联轴器、冷却水系统、 机前运输辊道由 甘油润滑系统、螺栓紧固、 甘油润滑系统、螺栓紧固、电机等部件组 成。 简要性能:型式: Φ 简要性能:型式:交流单独传动
薄板坯连铸连轧(6)—鞍钢ASP(2150)

薄板坯连铸连轧(6)—鞍钢ASP(2150) 2006-12-19鞍钢集团公司结合其三炼钢厂易地改造,在鞍钢西部地区新建了一条年产量为500万t的2150mm ASP连铸连轧生产线。
该工程分2期实施:一期建1#、2#步进式加热炉,1架四辊可逆式粗轧机R1,1台切头飞剪,7机架精轧机组( F7机架预留),1套层流冷却装置,1#、2#2台卷取机;二期再建3#加热炉、3#卷取机。
鞍钢2150mm ASP生产线工艺布置如图1所示。
图1 鞍钢2150mmASP生产线工艺布置图1—1#加热炉;2—2#加热炉;3—3#加热炉;4一E1立辊轧机;5一Rl粗轧机;6一E2立辊轧机;7一保温罩;8一飞剪;9一精轧前立辊轧机;10一精轧机组;l1一层流冷却装置;12一卷取机产品品种及原料生产的品种有:低碳钢、碳素结构钢、低合金钢、管线钢、深冲钢、耐候钢等。
成品带钢厚1.8~25.4mm、宽1000~2000mm、钢卷内径为Φ762mm、外径为Φ1100~Φ2100mm、最大卷重37.3t。
原料为连铸坯,连铸坯厚135、170、200mm,标准坯厚135mm,宽1000~2000mm,长15~18m,最大坯重37.9t。
主要工艺装备(1)加热炉。
设有3座步进梁式炉(其中3#加热炉二期实施),热装板坯入炉温度≥800℃,也可常温冷装,板坯出炉温度为1200~1250℃,加热能力为400t/(h·座)(热装)。
(2)高压水除鳞箱。
其上、下各有2排喷水集管,高度可调,高压水出口压力为23MPa,喷嘴有4×26个。
(3)E1、E2立辊轧机。
其型式为附着上部驱动式(带液压AWC),最大单道次侧压量50mm,轧辊尺寸Φ1200/Φ1lOOmm×430mm,最大轧制力3800kN,轧制速度0~5.89m/s,主电机功率AC1200kW×2,转速200/400r/min。
(4)Rl粗轧机。
为四辊可逆式,工作辊尺寸为Φ1250/Φ1150mm×2150mm,支撑辊尺寸为Φ1650/Φ1500mm×2150mm,最大轧制力50000kN,道次最大压下量50mm,主电机功率10000kW ×2 AC,转速40/9Or/min,轧制速度0~ 5.89m /s。
1580mm F1E立辊轧机
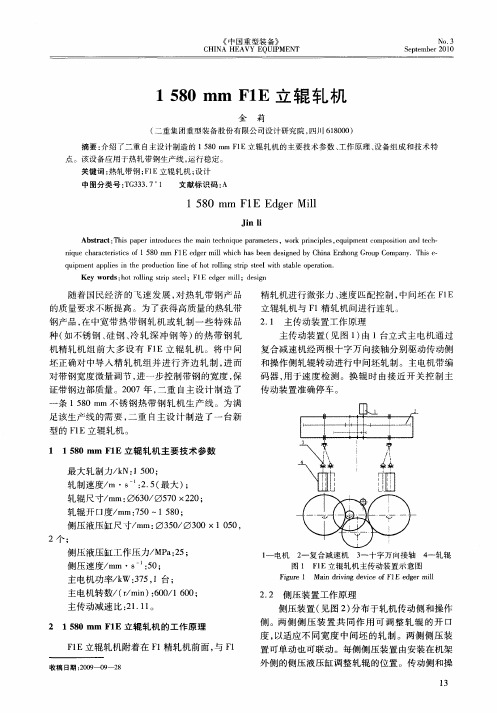
传 动装 置准 确停 车 。
. .
条 15 0 m 8 m不 锈 钢 热 带 钢 轧 机 生产 线 。为 满 足该 生产线 的需 要 , 重 自主设 计 制 造 了一 台新 二 型的 n E立 辊轧 机 。
’
1、 m 』
.
。
,
/
1 .
d
-
《 国重 型装 备 》 中 C N A YE UP N HIA HE V Q IME T
No 3 . Se tm r2 0 p e e 01
15 0mm 1 立 辊 轧 机 8 F E
金 莉
( 重 集 团 重 型 装 备 股 份 有 限公 司设 计 研 究 院 , 二 四川 6 80 ) 10 0
u q h rc e i i f15 0 hm e g rmi ih h sb e e i n d b h n r h n o p C mp n . hs — t e c a a t r t s o 8 i F1 d e l whc a e n d sg e y C i a E z o g Gr u o a y F i e u sc E l q ime t p l si h r d e in l e o o o l g sr te i tb e o e ain u p n p i n t e p o u t i f t l n ti s lw t sa l p rt . a e o n h r i p e h o
侧 压液 压缸 尺 寸/ 30 30X100 mm: 5/ 0 5 ,
2个 ;
侧 压液 压缸 工作 压力/ a2 MP :5;
侧 压速 度/ m ・ ~:0 a r S 5;
立辊轧机的工作原理

立辊轧机的工作原理立辊轧机是一种常用的金属加工设备,用于将金属坯料通过辊轧加工的方式,加工成所需的形状和尺寸。
立辊轧机的工作原理主要包括进料、轧制和出料三个步骤。
首先是进料过程。
金属坯料通过输送装置送入立辊轧机的工作区域。
在进料过程中,需要确保坯料的位置准确,并通过调整进料辊轴的位置来控制进料量。
进料辊轴的转速也需要根据加工需求进行调整。
接下来是轧制过程。
轧制是立辊轧机的核心工作步骤。
在轧制过程中,金属坯料被夹持在上下两个辊轮之间,通过上下两个辊轮的旋转来施加力量,使金属坯料发生塑性变形。
辊轮的旋转速度和方向可以通过控制系统进行调节,以实现所需的轧制效果。
在轧制过程中,金属坯料会逐渐变薄并改变形状。
通过调整辊轮之间的间隙大小,可以控制金属坯料的厚度和形状。
辊轴的材质和表面处理也会影响轧制效果。
辊轴通常由高强度合金钢制成,并经过热处理和表面硬化处理,以提高耐磨性和使用寿命。
最后是出料过程。
经过轧制后,金属坯料从辊轮之间的间隙中出来,成为加工后的金属板材或金属杆料。
出料过程需要确保金属坯料的顺利出料,并通过输送装置将其送离工作区域。
立辊轧机的工作原理主要依靠辊轮的旋转运动和辊轴之间的力学作用,对金属坯料进行塑性变形,从而实现金属加工的目的。
通过调整辊轮的转速和方向,以及辊轴之间的间隙大小,可以控制金属坯料的厚度和形状,满足不同加工需求。
立辊轧机是一种利用辊轮旋转和力学作用对金属坯料进行塑性变形的金属加工设备。
它的工作原理主要包括进料、轧制和出料三个步骤。
通过调整辊轮的转速、方向和辊轴之间的间隙大小,可以实现对金属坯料的精确控制,满足不同加工需求。
立辊轧机在金属加工行业中有着广泛的应用,对于提高生产效率和产品质量具有重要作用。
- 1、下载文档前请自行甄别文档内容的完整性,平台不提供额外的编辑、内容补充、找答案等附加服务。
- 2、"仅部分预览"的文档,不可在线预览部分如存在完整性等问题,可反馈申请退款(可完整预览的文档不适用该条件!)。
- 3、如文档侵犯您的权益,请联系客服反馈,我们会尽快为您处理(人工客服工作时间:9:00-18:30)。
设备编号
27
固定资产编号
设备名称
E1立辊轧机
安装地点
轧钢车间
主机图号
621X 1.00
安装时间
2004年2月8日
设备型号
投产时间
2004年5月7日
制造厂家
机
出厂日期
机
电
电
出厂编号
机
外形尺寸
长度
宽度
高度
电
设备总重
23013公斤
登表日期
2007年6月29日
设
备
规
格
及
性
能
1.轧辊直径max = 48轧辊身长220 mm
3.轧辊中心距max = 950 mm min = 558 mm
4.轧辊线速度v = 0. 96 —1. 8 m / s
5.伞齿轮箱中心距:工作时650 mm换辊时1850 mm
6.减速机型号:ZL 85—3—IIA A = 850 mm i = 8. 916
7.轧制力Pmax= 32 t
最大传递扭矩:Mmax = 1.57 t .m
接轴最大倾角:Qmax = 110
主要备件更换记录
更换日期
名称
图号
材质
更换原因(注明是在大、中、小修或抢修事故更换)
保养检修记录
检查日期
主要检修内容
记事及遗留问题
设备事故登记
单位名称:车间名称:记录人:
事故名称
发现日期
事故分析原因及处理情况
停产时间
8.轧制力距T= 1.2 t .m
9.主传动电机Z 355 — 4A N = 131 KW n = 260—1200 r / min
10.压下速度v = 2. 9 mm / s
11 .压下电机JPE—1 .5—4
压下减速机XWD 1 .5—4—1 / 11 1.5KW
12、万向接轴图号:69 X 1.2