我说精益管理之D阶段
精选精益生产之现场管理
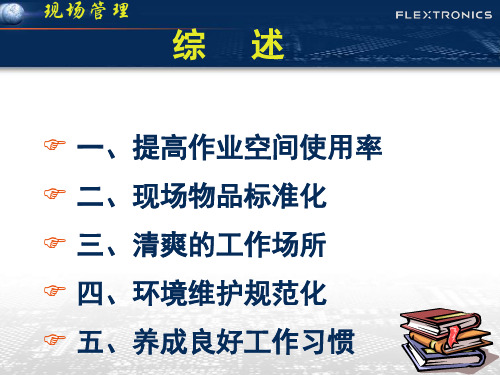
现场管理
总结
现场管理
一、提高作业空间使用率 二、现场物品标准化 三、清爽的工作场所 四、环境维护规范化 五、养成良好工作习惯
演讲完毕,谢谢观看!
(1)宽敞的工作场所变得窄小; (2)架、柜被杂物占据减少了使用价值 (3)寻找物品困难,浪费时间; (4)物品摆放杂乱,导致盘点失准。
现场管理
一、提高作业空间使用率
2、整理的内容
(1)将要和不要的东西分开;
(2)处理不要的东西: 丢弃、出售、循环..
(3)管理要的东西: 根据使用的频率
现场管理
一、提高作业空间使用率
3、整理的要领
(1)对工作场所要全面检查; (2)制定“要”和“不要”的标准; (3)将不要的物品清除出现场; (4)根据使用频率管理需要的物品; (5)制定废弃物处理方法; (6)坚持每日检查
现场管理
一、提高作业空间使用率
整理的要点
将需要和不需要的东西分开;
丢弃或处理不需要的东西;
清除脏污,保持工作场所干净亮丽。 稳定生产品质,消除隐患,减少工业 伤害 1、实施清扫(SEISO)的必要性:
(1)任何污物都可能降低效率,引发意外
(2)清洁之目的在于检查现场;
(3)通过检查,保持现场的最佳状态
现场管理
三、清爽的工作场所
2、清扫的内容:
(1)划定范围,分配工作;
(2)清理场地器材,及时发现潜在问题; (3)执行改善措施,确定清扫重点; (4)建立清洁规则,保持现场整洁。
现场管理
三、清爽的工作场所
3、清扫的实施要领:
(1)建立责任区;
(2)执行例行扫除,清理脏污; (3)调查污染源,排除或隔离; (4)建立清扫基准,确定规范。
精益管理在工程项目建设中的应用

精益管理在工程项目建设中的应用说到“精益管理”,大家可能都会想起那些高效的工厂生产线或者严谨的流程图,感觉似乎跟“工程项目建设”有点不搭边。
但实际上,精益管理在工程项目中可是大有可为!想象一下,工地上工人们忙得不亦乐乎,工期一天天逼近,资源又紧张,谁不想把效率提高,省时省力呢?这时候,精益管理就像一位经验丰富的“老司机”,指引着大家在这条高速公路上平稳行驶。
你看啊,精益管理的核心就是“去除浪费”,这不仅仅是说物料的浪费,人的时间、管理的失误、沟通的低效甚至是等待的浪费,通通都得剔除。
这就好比你在盖房子的时候,原本可以一步到位的设计,结果因为沟通不畅,结果搞得头重脚轻;或者本来可以少走几个弯路,结果因为信息不对称,反而多走了好几圈。
浪费,大家肯定不想看到吧?咱们再举个例子吧。
想象一下,一个大型建筑工地,施工团队每天都得处理各种各样的工作,哪有时间去浪费呢?一些小的细节就能决定大局。
比如说,有一项工程,原本需要五个工人做,结果因为精益管理的实施,流程一优化,效率一提升,五个工人也能缩短到三个人。
看似小小的调整,实际上节约了大量的人力、时间和成本。
这不仅仅是数字上的提升,背后是每一位工人心态的转变,是团队精神的体现。
你想啊,大家都能节省时间,生活上也能轻松一点,不是更好?再有,精益管理强调的“持续改进”这一点也是特别重要的。
就好像工地上的每一位负责人,每天都得紧盯进度,不断调整方法,不断优化流程。
哪怕是一点点小小的调整,过段时间累积下来,也能节省不少成本和时间。
这种“微创新”的精神,你不觉得挺有意思的吗?每个小小的进步都能让团队更强大,整个项目建设也能更顺利。
就算碰到点问题,精益管理也会给你带来解决问题的思路——那就是“事不过三”,犯了错要赶紧总结,找出原因,防止再次发生。
还有一点非常重要:精益管理的核心并不是单纯地追求速度,而是追求速度和质量的平衡。
你看,如果把施工速度提上去,但质量没保障,那最后验收的时候麻烦可大了。
精益管理我们应该怎样做

精益管理我们应该怎样做前几位同事已经对“精益管理理念”、“精益管理是目标实施体系”、“精益管理是管理工具、多种措施集合”、“精益管理是好的习惯、继承和发扬现代管理手段”等4个题目作了精彩的宣讲,使大家明确精益管理不能与之前管理工作相割裂,而是现代管理对我们提出了更高的要求;精益管理不是空中楼阁,而是在我们原有的“严、细、实、恒”良好管理基础之上的精益求精。
目前,工厂在精益思想的指导下制定了精益目标、措施体系,接下来就是关键的一个环节,要将这些精益目标、措施体系落实到实际行动上。
我们说基层是重点,一线是舞台,员工是主角,那么作为主角,我们每一个员工该如何落实、怎样去做呢?我认为要通过“知行合一、立足岗位”这两方面去做,切实把精益目标、措施体系落实到实际行动上,从而实现精益管理的目标。
一、知行合一在精益管理过程中,我们最终要达到的目的是将管理思想转化为行为习惯。
作为工厂管理部门首先要知道、了解公司、工厂的精益管理工作目标、工作方案、措施体系,主动接受、严格执行制度。
作为员工要用目标、标准约束自己的行为,真正把自己摆进精益管理过程中,做到知行合一。
我们欣喜地看到我厂各部门规划得很好,落的很实,在与实业公司的一名管理人员交谈的时候,说到签状的事情,该管理人员说他们正在将部门的精益目标进行细化,分解落实。
这就说明他们做得很好,是真正做到知行合一。
做为企业员工,应该如何来做,从而达到知行合一,我们应该做到以下三点。
(一)真知“精”就是少投入、少消耗资源、少花费时间;“益”就是多产出,多创造价值。
精益管理就是用最少的投入创造最大的价值,实现企业效益最大化。
因此,我们企业员工要增强精益管理意识,把精益管理理念落实到实际中,要结合车间生产实际,在“精”的方面,力求做到少投入、少消耗资源、少花费时间,包括要少投入生产方面的人力物力,少消耗水电等的资源,少花费生产时间,以少来增加效益。
在“益”的方面,要考虑通过何种方法、采取何种措施,做到多产出,多创造价值,以多来实现效益。
精益六西格玛黑带课程-D阶段-SIPOC

DMAIC
SIPOC
核心流程:
Suppliers
(Providers of the required resources)
Inputs
(Resources required by the process)
流程主人:
Process
(Top level description of activity)
• 流程的需求 • 供应商 • 流程输出测量
S
供应商
需求
需求
输入边界
输出边界
I
P OC
输入
流程
输出
顾客
一个提供输出以满足顾客需求的过程的描述 (明确的或暗示的)
定义流程的起始和终止边界.
交付的产品或服务,满足或超过顾客的需求.
接受输出的人, 和对输出提出需求但不接受产品的人.
对流程输出的可量化的期望. 输出必须是可测量的,需要与顾客的要求相
流程主人: 格林上校
流程名称: 流程所有者:
准备和发射 格林上校
Customers (输出的受益者)
Suppliers (资源的提供者)
Inputs (流程需要的资源)
Process (活动的高级别描述y)
Outputs
需求
(流程的交付结果)
国王
目标
需求
1.每次发射时间<2分钟 2.投射误差<1英寸
DMAIC
皇家炮队案例—模拟弹弓
DMAIC
发射球
发射杯 发射杆
定位杆 伸缩带
发射角
限位孔
销钉
地面或桌子
基本问题分析
格林上校知道什么?
国王不高兴、不满意
皇家炮队的表现没有达到国王的期望
精益管理理念课件

执行、C(Check)检查、A(Action)标准化。 对总结检查的结果进行处理, 成
功的经验加以肯定并适当推广、 标准化;失败的教训加以总结, 未解决的问题放到下一个PDCA
P (改善计划)
A (标准化)
D (改善实施)
循环里。
C (效果验证)
四、PDCA
PDCA是一种解决问题,持续改善的工具和
生产过剩带来的危害
△生产过剩会掩盖生产过程中隐藏着的 急待改善的各种问题和不合理成分。
设计 不良
机械 故障
产品 不良
材料 不良
产 不均
资金 占用大
△生产过剩除了会滞留大量资金、产生多 余的利息支出外,还会引发新的连锁性浪 费:
l 原材料、零部件、电能、气能等过早 消耗;
l 工位器具增加;
l 搬运工、搬运设备增加;
项 目 单件生产方式 大批量生产方式
精益生产方式
产品特点
设备和工 装
作业分工 与作业内
容 对操作工
人 要求 库存水平 制造成本
完全按顾客要求 标准化,品种单一 通用、灵活、便宜 专用、高效、昂贵
粗略、丰富 细致、简单、重复
懂设计制造 有较高操作技能
不需要专业技能
高
高
高
低
品种多样化、系列 化
柔性高、效率高
结束
三、快速转换
快速转换是一种调整技术, 它可以在保证质量及 稳定性的前提下, 明显缩短机器安装及调整的转换 时间。通过快速转换, 可以减少库存量, 降低前置时 间, 提高设备使用效率, 使按计划生产的要求更容易 达到。
四、PDCA
PDCA是一种解决问题,持续改善的工具和
手段,其具体含义为: P(Plan)计划、D(Do)
精益管理知识题库

精益管理知识竞赛题库第一环节(个人必答题)第一轮1、拉动体系是允许材料、产品在 B 库存,或在最底限度在制品库存的情况下流动.A、有B、没有C、不确定D、有一点2、实行“看板方式”的基础是: A .A、准时化B、自动化C、流水线生产D、均衡化生产3、对零件的加工投入超出客户需求部分的浪费属于 D 浪费。
A、不良品B、等待C、搬运D、过度加工4、丰田生产方式的基本思想是 D 。
A、围绕品质、效率、效益三大主线B、提高生产效率C、彻底杜绝浪费D、准时化、自働化5、如果要将“目视化管理"作为丰田生产方式的管理手段,首先就要B 。
A、熟悉标准作业表B、推进5S活动C、开展TPM活动D、开展创意改善提案6、“没有最好,只有更好”体现了精益生产的 A 原则A、尽善尽美原则B、价值原则C、价值流原则D、流动原则7、TPM管理中认为故障就是 C 。
A、人故意使设备发生障碍B、设备设计中的障碍C、设备运用中的障碍D、设备改造中的障碍8、下列不属于丰田公司三不原则的是 D 。
A、不接受不良品B、不生产不良品C、不流出不良品D、不改变不良品第二轮1、定品、定位、定量是整顿的关键因素.(√)2、当设备在使用过程中出现异常时应立即停止作业,填写故障维修单通知保全班。
(×)3、T.T是指产品生产节拍;C。
T是指产品的生产周期。
(√)4、5S管理的前3S阶段(整理、整顿、清扫)是打造基础的阶段。
(√)5、山脊图表示各要素作业的顺序、时间。
(√)6、外部物流主要指供应物流和销售物流.(√)7、准时化的作用是解决“库存”在物资和财务上的负担。
(√)8、自主保全是以设备保全部门为中心,由设备专业人员开展的预防为主的生产保全活动。
(×)第三轮1、一个企业最基层、最活跃的组织是班组。
2、精益生产两大支柱是准时化、自动化。
3、整顿是对需要的物品按照便于使用的原则有条理地摆放,即实施定置管理.4、价值流包括一个产品从原始设计、制造过程,到收到货款等各步骤所包含的增值与非增值的所有活动。
“精益”之感悟
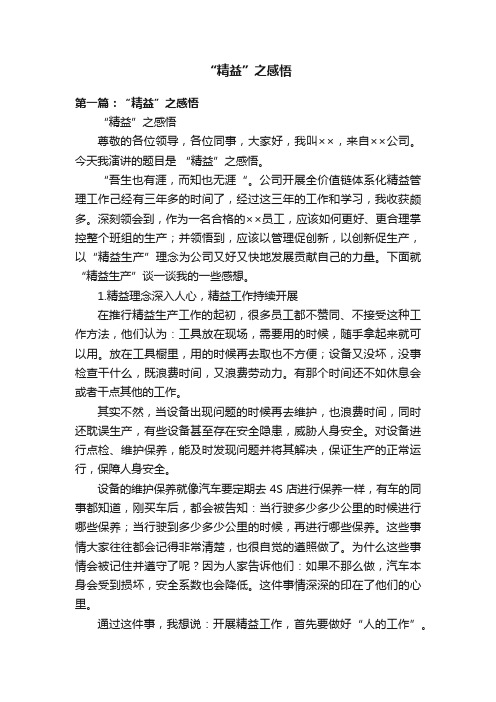
“精益”之感悟第一篇:“精益”之感悟“精益”之感悟尊敬的各位领导,各位同事,大家好,我叫××,来自××公司。
今天我演讲的题目是“精益”之感悟。
“吾生也有涯,而知也无涯“。
公司开展全价值链体系化精益管理工作己经有三年多的时间了,经过这三年的工作和学习,我收获颇多。
深刻领会到,作为一名合格的××员工,应该如何更好、更合理掌控整个班组的生产;并领悟到,应该以管理促创新,以创新促生产,以“精益生产”理念为公司又好又快地发展贡献自己的力量。
下面就“精益生产”谈一谈我的一些感想。
1.精益理念深入人心,精益工作持续开展在推行精益生产工作的起初,很多员工都不赞同、不接受这种工作方法,他们认为:工具放在现场,需要用的时候,随手拿起来就可以用。
放在工具橱里,用的时候再去取也不方便;设备又没坏,没事检查干什么,既浪费时间,又浪费劳动力。
有那个时间还不如休息会或者干点其他的工作。
其实不然,当设备出现问题的时候再去维护,也浪费时间,同时还耽误生产,有些设备甚至存在安全隐患,威胁人身安全。
对设备进行点检、维护保养,能及时发现问题并将其解决,保证生产的正常运行,保障人身安全。
设备的维护保养就像汽车要定期去4S店进行保养一样,有车的同事都知道,刚买车后,都会被告知:当行驶多少多少公里的时候进行哪些保养;当行驶到多少多少公里的时候,再进行哪些保养。
这些事情大家往往都会记得非常清楚,也很自觉的遵照做了。
为什么这些事情会被记住并遵守了呢?因为人家告诉他们:如果不那么做,汽车本身会受到损坏,安全系数也会降低。
这件事情深深的印在了他们的心里。
通过这件事,我想说:开展精益工作,首先要做好“人的工作”。
以培训为先导,充分发挥精益生产管理者的“桥梁”作用。
通过宣传和培训来提高员工对精益生产的了解和认知,激发他们参与精益生产的积极性,使精益生产的理念深入人心。
只有这样,精益生产工作才能持续、长效地开展下去。
JIT精益生产实务-D

CWMC 国慧顾问
作业顺序
设定作业顺序应考虑的因素: · 工作量的均衡性 · 工作量再分配的可行性 · 双手使用方式 · 双脚站立位置 设定作业顺序可以避免员工作业的随意性。 合理地设定作业顺序能使操作者安全地、有效地、 自信地按照标准进行生产,从而保证质量和生产效率。
(三)质量安定化 (四)切换安定化 (五)现场安定化 课程五 JIT技术 · 平稳化生产 课程六 JIT技术 · 适时化生产 课程七 JIT技术 · 自主管理活动ຫໍສະໝຸດ CWMC 国慧顾问
目录
练习1 练习2 练习3 练习4 练习5 练习6 练习7 羊年造牛 分纸 生产效率计算 中国一号 空中耐力 空中蜕变 钎焊的烦恼
CWMC 国慧顾问
例
产距时间
早会10min 准备 5min 每日有效工作时数: 标准出勤时间8H即480min 非生产时间 85min 有效工作时间 395min 市场需求量: 1000台
工休10min
中餐40min
工休10min
整理 5min 晚会 5min
CWMC 国慧顾问
“水蜘蛛”作业的效果
☆ 动作质量提高 ☆ 作业时间缩短 ☆ 生产速度稳定 ☆ 生产持续进行 ☆ 便于员工多能化 ☆ 成套供应避免错装漏装 ☆ 把握生产进度 ☆ 把握实际产距时间
CWMC 国慧顾问
“水蜘蛛”作业实施步骤
CWMC 国慧顾问
顾
回
Just In Time
适品 ·适量 ·适时 适时化 生产 平稳化 生产 安定化 生产
流线化 生产
CWMC 国慧顾问
人员安定化管理 设备安定化管理 安定化 生产 质量安定化管理
切换安定化管理
- 1、下载文档前请自行甄别文档内容的完整性,平台不提供额外的编辑、内容补充、找答案等附加服务。
- 2、"仅部分预览"的文档,不可在线预览部分如存在完整性等问题,可反馈申请退款(可完整预览的文档不适用该条件!)。
- 3、如文档侵犯您的权益,请联系客服反馈,我们会尽快为您处理(人工客服工作时间:9:00-18:30)。
我说精益管理之D阶段
定义(Define),界定核心流程和关键顾客,站在顾客的立场,找出对他们来说最重要的事项,也就是「品质关键要素」(Critical to Quality,CTQ)。
厘清团队章程,以及核心事业流程。
D阶段的任务可描述为:发起项目→定义流程→确定客户需求→定义关键流程输出变量
在D阶段中,一个好的问题描述(项目背景)就是一个好的项目开始,这是作为一个传统项目报告首先要向听取报告人所展示的内容,要对选择此项目做一个简要的陈述,目的在于让听取报告的人了解我们为什么选择此项目作为本次研究的项目,其意义在于哪里。
其大致要阐述是何问题,何处发生,何时发生,问题的严重度……。
在选择项目之后,要确定项目的研究范围,每个项目报告都有不同的差异,它可定义为物理范围、流程范围、生产工艺范围等等,根据项目的不同而进行选择。
在确定项目的研究范围中关键因素常用到的一种工具称之为为“SIPOC”。
SIPOC模型是一代质量大师戴明提出来的组织系统模型,是一门最有用而且最常用的,用于流程管理和改进的技术。
是过程管理和改进的常用技术,作为识别核心过程的首选方法。
SIPOC其中每个字母各代表:Supplier 供应商;Input 输入;Process 流程;Output 输出;Client 客户。
(1)供应商(Supplier)——向核心流程提供关键信息、材料或其它资源的组织。
之所以强调“关键”,是因为一个公司的许多流程都
可能会有为数众多的供应商,但对价值创造起重要作用的只是那些提供关键东西的供应商。
如研究降低CNG综合电耗项目中,我们的关键供应商为供气上游、供电局。
(2)输入(Input)——供应商提供的资源等。
通常会在SIPOC 图中对输入的要求予以明确,例如输入的某种材料必须满足的标准,输入的某种信息必须满足的要素等。
(3)流程(Process)——使输入发生变化成为输出的一组活动,组织追求通过这个流程使输入增加价值。
(4)输出(Output)——流程的结果即产品。
通常会在SIPOC 图中对输出的要求予以明确,例如产品标准或服务标准。
输出也可能是多样的,但分析核心流程时必须强调主要输出甚至有时只选择一种输出,判断依据就是哪种输出可以为顾客创造价值。
(5)顾客(Customer)——接受输出的人、组织或流程,不仅指外部顾客,而且包括内部顾客,例如材料供应流程的内部顾客就是生产部门,生产部门的内部顾客就是营销部门。
对于一个具体的组织而言,外部顾客往往是相同的。
SIPOC的优点:能展示出一组跨越职能部门界限的活动;不论一个组织的规模有多大,SIPOC图都可以用一个框架来勾勒其业务流程;有助于保持“全景”视角。
其意义在于它将过去一直被人们当作组织以外的部分即客户和供应商,与组织主体部分放在一起,作为一个整体来研究;同时SIPOC系统特别强调系统的目标与系统的密不可分。
在D阶段中另一项重要的任务就是明确客户之声,客户之声(voice of client VOC)是指用来描述客户需求以及他们对你的产品或者服务的认识,如集团或者提供的精益管理项目的选题应是通过各成员公司、各员工进行统计得到的结论。
客户之声有助于组织确定提供什么样的产品服务;确定这些产品和服务的关键特征和规格;确定客户满意度的关键驱动因素等等。
最终将客户之声转换成关键质量特性,如在降低CNG综合电耗中,关键质量特性为压缩每千方天然气电耗及电耗成本。
在完成以上内容之后,D阶段任务基本结束,在D阶段最后需要确定的就是一只高效的团队,整个团队需明确目标及其任务,分工明确,项目计划明确,以便项目顺利进展。
以上内容仅与大家进行交流,如有纰漏请大家批评指正。
车用燃气事业部
纪鑫铜。