第7章统计过程控制20091012
统计过程控制

统计过程控制第一章概述第一节预防与考查惯例的制造业,差不多上把测量操纵投入到考查。
进货考查——过程考查——最终考查。
用考查或从新考查来剔除不合格品(平日说的“逝世后验尸”)。
这种方法是落后的,也是白费的。
因为把大年夜量的时刻、人力、材料投入到临盆不必定有效的产品或办事中。
要幸免白费的有效方法——预防(平日说的“病前先检查,小病先吃药”)。
制造业预防的最好方法——统计技巧。
二次世界大年夜战时,美国军需资显现大年夜量问题。
美国当局颁布了三项战时质量操纵标准:Z1。
1 《质量操纵指南》Z1,2 《数据分析用操纵图法》Z1。
3 《工序操纵用操纵图法》强迫履行。
订货合同中规定质量治理要求条目,不然撤消订货资格。
“统计质量治理时期”即把质量治理的“终端”移止“工序”,把全数考查改为随机抽样考查。
把抽样考查的数据分析制造成“操纵图”。
对工序进行加工监控。
从而杜绝过程中大年夜量不合格的产生。
20世纪60年代,世界上专门多国度也大年夜力推广统计过程对临盆等过程进行操纵。
取得了专门好的成效。
第二节过程操纵体系有反馈的过程操纵体系模型图1 过程操纵体系1.过程——合营工作以产生输出的供方、临盆者、人、设备、输入材料、方法和情形及应用输出的顾客的集合。
过程的机能取决于:①供方和顾客间的沟通。
②过程设计及实施的方法。
③运作和治理的方法。
2.有关机能的信息:与机能有关的最有效的信息是研究过程本质以及内涵的变更。
始终留意过程而不是产品的成果。
3.对过程采取方法:对重要的特点采取方法。
采取方法包含改变操作(人、机、料、法、环、测)。
4.对输出采取方法:对输出检测并改正不相符规范的产品,不分析过程中的根来源差不多因,平日是最不经济的。
第三节全然概念1.变差1.1 定义:过程的单个输出之间弗成幸免的差别。
1.2 分类:1.2.1 固有变差(通俗变差):仅由通俗缘故造成的过程变差。
用σR/d2来估量。
(过程处于“受控”状况)。
1.2.2专门变差:由专门缘故造成的变差。
统计过程控制

1、统计过程控制(SPC)包含两方面:①利用控制图分析过程的稳定性;②计算过程能力指数,对过程质量进行评价。
主要工具就是控制图。
2、SPC发源于美国。
休哈特《加工产品质量的经济控制》标志着过程控制的开始。
3、统计过程诊断(SPD)是20世纪80年代发展起来的。
4、世界上第一张控制图是美国休哈特在1924年提出来的不合格率(p)控制图5、小概率事件原理:小概率事件在一次实验中几乎不可能发生,若发生判断为异常。
6、控制图是用于监控过程质量是否处于统计控制过程的图7、常规控制图包括中心线、控制限、描点序列。
控制限的作用就是区分偶然波动与异常波动。
8、偶因是过程固有的,始终存在的,对质量的影响微小,但难以除去。
异因不是过程国有的,有时存在,有时不存在,对质量影响打,但不难除去。
9、过程处于统计状态控制时,只有偶因,而无异因产生的变异;点子落在控制限外的概率很小。
10、为控制产品不合格数,可选用的控制图有p图和np图11、为控制产品有瑕疵数,可选用的控制图有c图和u图12、根据5M1E内容,当人、机、料、法、测、环任何一个变动时,控制限需重新制定。
一、常规控制图的分类及应用场合:计数值控制图包括计件值和计点值控制图二、X−R图:(国标规定先作R图)计算步骤:1、取预备数据①取20~25个子组②子组大小一般为4或5,过程稳定性好的话,子组间隔可以扩大。
③同一子组的数据必须在同样的生产条件下取得,故要求在短间隔内来取。
2、计算各个子组的平均是X i和极差R i3、计算样本总均值X̿与平均样本极差R4、计算R图控制限、X控制限,并作图。
5、将子组中的预备数据(R i)在R图中打点,判稳。
若稳进行步骤6;若不稳,除去可查明原因后转入步骤3,即重新计算X̿与R6、将子组中的预备数据(X i)在X图中打点,判稳。
若稳进行步骤;若不稳,除去可查明原因后转入步骤3,即重新计算X̿与R7、计算过程能力指数并检验其是否满足技术要求若过程能力指数满足技术要求,则转入步骤8;若过程能力指数不满足技术要求,则需调整过程直至满足技术要求为止;8、延长X−R的控制线,作控制用控制图,进行日常管理。
统计过程控制
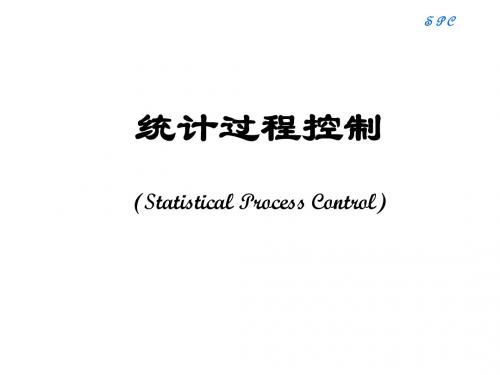
常,恢复过程的稳定,从而达到持续改进和保证质量的
目的。
3
SPC
什么是控制图
• 用于分析和判断工序或过程是否处于稳定状态而使用
( x )2 2 2
e
( x , 0)
x随机变量
-- 平均值 -- 标准差
23
SPC
1.2 正态分布的参数—— 、
不同 、 相同
相同、
不同
、相互独立
24
SPC
1.3 正态分布的特点:
• • 曲线以 x = 直线为轴,左右对称 曲线与横坐标轴所围成的面积等于1,也说随机变量x落在 (-∞,+∞)的概率为1 其中: 在 ± 范围内的面积占68.26 % 在 ±2范围内的面积占95.45 % 在 ±3范围内的面积占99.73 %
当np>=5时,二项分布趋向于正态分布
28
SPC
2.3 二项分布的均值、方差和标准差 • 均值:E(X)= np • 方差:Var(X)=np(1-p) • 标准差: *
np(1 p )
二项分布的均值、标准差相互关联
29
SPC
3、泊松分布
3.1二项分布的极限分布——泊松分布P(λ)
• 分布列
– 过程结果的反馈控制
7
SPC
• Spc的核心 是把质量控制的重心前移,重视事前预防和有序的全 过程质量控制及持续改进,全方位地满足用户要求。 • Spc的特点 是对过程进行系统的、全过程的控制,要求全员参加, 人人有责 强调用科学的方法(理论:统计技术;工具:控制 图),来保证全过程的预防
统计过程控制讲义

收集此類數 據管制圖表 稱為:計量值
管制圖
計數值管制圖
P管制圖(n相等時)
日期 項目
3/ 1
3/2
3/3
3/4
ቤተ መጻሕፍቲ ባይዱ
3/5
3/6
3/7
…
3/2 3/2 3/2 3/2 3/2
1
2
3
4
5
合計
檢查數
10 0
100
100
100
100
100
100
…
100 100 100 100 100
³¡ ªù ¦W ºÙ : ³¡ ªù ¾á ·í :
¤ ¨® ¶¡ §õ °¶ ©¾
¨î µ{
¶i ®Æ
´¡ ¥ó
²Õ ¸Ë
»s «~ «~ ½è ¯S ©Ê
¨î µ{ ºÞ ¨î ¶µ ¥Ø
¿é ¥X q¹ À£
¿ü ¦y
¿ü ¤Õ
¥\ ¯à î¨ ¯B °_ °ª «×
¿ü ¯]
¤¸ ¥ó ¸} ªø «×
³¡ ªù ¾á ·í :
§õ °¶ ©¾
¨î µ{
´¡ ¸Ë ¤¸ ¥ó
²Ä ¤@ ¦¸ ®û ¿ü
°Å ¸}
²Ä ¤G ¦¸ ®û ¿ü
ÂI ÀË ¶µ ¥Ø ºÞ ¨î ¶µ ¥Ø
®û ¿ü ¿ü ÂI ¤£ ¨}
¤¸ ©Ê ¥ó
Ìå
¤¸ Ñà ¥ó
м
®ñ ¤Æ
¤¸ ¥ó ¸}
ü¿ «× lÄ
¥» ¤½ ¥q
Äv ª§ ¼t ®a
相關關系
³Æª`
¤ñ ³W®æ ¤ñ ³W®æ ¤ñ ³W®æ
第7章统计过程控制20091012

质量管理学
• 小概率原理 所谓小概率原理,即认为小概率事件一般是不会发生的 。由准则可知,若X服从正态分布,则X的可能值超出控 制界限的可能性只有0.27%。因此,一般认为不会超出控 制界限。 小概率原理又称为实际推断原理,当然运用小概率原理也 可能导致错误,但犯错误的可能性恰恰就是此小概率。 • 反证法思想 一旦控制图上点子越出界限线或其他小概率事件发生,则 怀疑原生产过程失控,也即不稳定,此时要从5MIE去找原 因,看是否发生了显著性变化。
μ+3σ
质量特性值
μ-3σ
μ
图5-2正态分布图
μ+3σ
也可以理解为,如果抽取少数产品, 则测得的质量特性值应均落在μ+ 3σ范 围内;如果有特性值落在+ 3σ的界限外, 可以认为过程出现系统性原因,X的分布 发生了偏离。这就是休哈特控制图的3σ O 原理。
12
μ μ+3σ
子组号 图5-3质量特性值分布示意图
控制图定义: 是对过程质量特性值进行测定、记录、评估和监察 过程是否处于控制状态的一种用统计方法设计的图。
3
2014年4月29日12时7分
7.1 控制图的基本原理
常规的控制图包括以下两部分:
质量管理学
(1)控制图应包括完整的“标题”信息:
什么 哪里 谁 零件/产品/服务的名称和编号/标识; 操作/过程步骤信息,名称/标识; 操作者和评价者;
2014年4月29日12时7分 10 控制图基于时间的统计和概率方法提供了必要且足够的方法判定过程是否有特殊原因存在。
质量管理学
控制图的设计原理
正态性假定 3σ 原理 小概率原理 反证法思想 • 正态性假定 • 任何生产过程生产出来的产品,其质量特性值总会存在一 定程度的波动,当过程稳定或者说受控时,这些波动主要 是由5MIE的微小变化造成的随机误差。此时,绝大多数质 量特性值均服从或近似服从正态分布。这一假定,称之为 正态性假定。
统计过程控制

1、统计过程控制(SPC)包含两方面:①利用控制图分析过程的稳定性;②计算过程能力指数,对过程质量进行评价。
主要工具就是控制图。
2、SPC发源于美国。
休哈特《加工产品质量的经济控制》标志着过程控制的开始。
3、统计过程诊断(SPD)是20世纪80年代发展起来的。
4、世界上第一张控制图是美国休哈特在1924年提出来的不合格率(p)控制图5、小概率事件原理:小概率事件在一次实验中几乎不可能发生,若发生判断为异常。
6、控制图是用于监控过程质量是否处于统计控制过程的图7、常规控制图包括中心线、控制限、描点序列。
控制限的作用就是区分偶然波动与异常波动。
8、偶因是过程固有的,始终存在的,对质量的影响微小,但难以除去。
异因不是过程国有的,有时存在,有时不存在,对质量影响打,但不难除去。
9、过程处于统计状态控制时,只有偶因,而无异因产生的变异;点子落在控制限外的概率很小。
10、为控制产品不合格数,可选用的控制图有p图和np图11、为控制产品有瑕疵数,可选用的控制图有c图和u图12、根据5M1E内容,当人、机、料、法、测、环任何一个变动时,控制限需重新制定。
一、常规控制图的分类及应用场合:计数值控制图包括计件值和计点值控制图二、图(国标规定先作R图)计算步骤:1、取预备数据①取20~25个子组②子组大小一般为4或5,过程稳定性好的话,子组间隔可以扩大。
③同一子组的数据必须在同样的生产条件下取得,故要求在短间隔内来取。
2、计算各个子组的平均是和极差3、计算样本总均值与平均样本极差4、计算图控制限、5、将子组中的预备数据()在R图中打点,判稳。
若稳进行步骤6;若不稳,除去可查明原因后转入步骤3,即重新计算与6、将子组中的预备数据()在图中打点,判稳。
若稳进行步骤;若不稳,除去可查明原因后转入步骤3,即重新计算与7、计算过程能力指数并检验其是否满足技术要求若过程能力指数满足技术要求,则转入步骤8;若过程能力指数不满足技术要求,则需调整过程直至满足技术要求为止;8、延长的控制线,作控制用控制图,进行日常管理。
统计过程控制(SPC)

解:
于是,过程能力指数为:
过程能力不够充分,从图2发现分布中心μ=0.1968与规范中心M=(TU+TL)/2=0.1720有偏离,应进行调整。调整后,Cp值会有所提高。
单侧规范情况的过程能力指数
01
只有上限要求,而对下限没有要求: 只适用于的范围:
02
只有下限要求,而对上限没有要求: 只适用于的范围:
4
3
6
5
判稳准则的分析 判稳准则的思路
打一个点未出界有两种可能性:
► 过程本来稳定 ► 漏报 (这里由于α小,所以β大),故打一个点子未出界不能立即判稳。
在点子随机排列的情况下,符合下列各点之一判稳:
01
► 连续25个点,界外点数d=0;
02
► 连续35个点,界外点数d<0;
03
► 连续100个点,界外点数d<2。
0.1821
0.1828
0.0086
18
0.1812
0.1585
0.1699
0.168
0.1694
0.0227
19
0.1700
0.1567
0.1694
0.1702
0.1666
0.0135
20
0.1698
0.1664
0.17
0.16
0.1666
0.01
图1
μ’
μ
图2-7 正态曲线随着标准差变化
σ=2.5
σ=1.0
σ=0.4
y
x
不论μ与σ取值为何,产品质量特性值落在[μ-3σ,μ+3σ]范围内的概率为99.73%。 图2-8 正态分布曲线下的面积
统计过程控制

统计过程控制一般特性:只要是合格就可以;关键特性:不仅仅合格,还要尽可能接近目标值。
检验分类:计数型:检验时仅分为合格、不合格; 计量型:检验时可确定值的大小。
基本概念:特KPG安全、法规配合、功能KCC第一章持续改进及统计过程控制概述应用统计技术来控制产生输出的过程时,才能在改进质量、提高生产率、降低成本上发挥作用第一节预防与检测检测-------- 容忍浪费预防-------- 避免浪费第二节过程控制系统过程共同工作以产生输出的供方、生产者、人、设备、输入材料、方法和环境以及使用输出的顾客之集合。
过程性能取决于:1.供方和顾客之间的沟通;2. 过程设计及实施的方式;3. 动作和管理方式。
过程控制重点:过程特性过程控制步骤:确定特性的目标值;监测我们与目标值的距离是近还是远;对得到的信息作出正确的解释,确定过程是在正常的方式下运行; 必要时,采取及时准确的措施来校正过程或刚产生的输出;监测采取措施后的效果,必要时进一步分析及采取措施。
注:仅对输出进行检验并随之采取措施,只可作为不稳定或没有能力的过程的临时措施。
不能代替有效的过程管理。
第三节变差:普通及特殊原因任何过程都存在引起变差的原因,产品的差距总是存在。
虽然单个的测量值可能全都不同,但形成一组后它们趋于形成一个可以描述的分布的图形。
(例图)影响因素:普通原因:难以排除,具有稳定、可重复的分布;此时输出可以预测。
特殊原因:必须排除,偶然发生、影响显著;此时将有不可预测方式影响输出。
生产过程控制就是要清除系统性因素(特殊原因)第四节局部措施和对系统采取措施局部措施:针对特殊原因由直接操作人采取适当纠正措施。
此时大约可纠正15%勺过程问题。
系统措施:解决变差的普通原因,由管理人员来采取措施。
此时大约可纠正85%勺过程问题。
采取措施类型不正确,将给机构带来在的损失,劳而无功,延误问题的解决第五节过程控制和过程能力过程控制系统的目标:对影响过程的措施作出经济合理的决定,处理好两种变差原因的风险。
- 1、下载文档前请自行甄别文档内容的完整性,平台不提供额外的编辑、内容补充、找答案等附加服务。
- 2、"仅部分预览"的文档,不可在线预览部分如存在完整性等问题,可反馈申请退款(可完整预览的文档不适用该条件!)。
- 3、如文档侵犯您的权益,请联系客服反馈,我们会尽快为您处理(人工客服工作时间:9:00-18:30)。
R=最高-最低
5
2014年4月29日12时7分
(2)控制图部分
质量管理学
它是根据统计原理,在坐标纸上作出两条控制界限和一条中心线,然后 把按时间顺序抽样所得的质量特性值(或样本统计量)以点子的形式依次描 在图上,从点子的动态分布来分析生产过程的质量及其趋势的图形。如下:
垂直轴—代表质量特性值或其样本统计量; 水平轴—代表按时间顺序抽取的样本号; 中心线(CL,Central Line)
A4步骤 A5步骤
R=均值R= UCL=D
4
1 不要对过程做不必要的改 变 2 在此表后注明在过程因素 (人员、设备、材料、方 法、环境或测量系统)所 做的调整。
R=
LCL=D
3
R=
*
极差(R图)
6-8 6-9 6-10 6-11 6-12 6-15 6-16 8 10 12 14 8 10 12 14 8 10 12 14 8 10 12 14 8 10 12 14 8 10 12 14 8 .65 .75 .75 .60 .70 .60 .75 .60 .65 .60 .80 .85 .70 .65 .90 .75 .75 .75 .65 .60 .50 .60 .80 .65 .65 .70 .85 .80 .70 .75 .75 .80 .70 .80 .70 .75 .75 .70 .70 .80 .80 .70 .70 .65 .60 .55 .80 .65 .60 .70 .65 .75 .80 .70 .65 .75 .65 .80 .85 .60 .90 .85 .75 .85 .80 .75 .85 .60 .85 .65 .65 .65 .75 .65 .70 .65 .85 .70 .75 .85 .85 .75 .75 .85 .80 .50 .65 .75 .75 .75 .80 .70 .70 .65 .60 .80 .65 .65 .60 .60 .85 .65 .75 .65 .80 .70 .70 .75 .75 .65 .80 .70 .70 .60 .85 .65 .80 .60 .70 .65 .80 .75 .65 .70 .65 3.50 3.85 3.80 3.40 3.75 3.65 3.65 3.60 3.90 3.35 3.75 3.80 3.60 3.55 4.10 3.75 3.80 3.35 3.50 3.10 3.30 3.45 3.50 3.20 3.30 .70 .77 .76 .68 .75 .73 .73 .72 .78 .67 .75 .76 .72 .71 .82 .75 .76 .67 .70 .62 .66 .69 .70 .64 .66 .20 .20 .10 .15 .20 .25 .15 .20 .20 .20 .40 .20 .05 .25 .15 .15 .15 .15 .20 .05 .30 .20 .15 .10 .10 *样本容量小于7时,没有极差的下控制限
质量管理学
控制图的分类
(1)根据控制图的数据性质不同,控制图可以分为计量控制 图和计数控制图。
(2)根据控制图的用途和应用场合不同,控制图分为分析用 控制图和管理用控制图。
8
2014年4月29日12时7分
质量管理学
三、控制图的理论依据
- 过程质量的两种变异 普通原因→随机性变异→偶然波动;
特殊原因→系统性变异→异常波动;
- 通过样本观测值以图的形式检测过程是否存在特殊原因的一种 方法。 - 过程质量特性值在只受普通因素影响时服从正态分布。
9
2014年4月29日12时7分
质量管理学
注: “点出界就判异”小概率事件实际上不发生,若发生即 判异常。 控制图就是统计假设检验的图上作业法。
直方图用图形表示了过程变差的分布,通过它可以研究过程其分布形式,以及确认过程变差 控制图在识别特殊原因方面是否优于直方图? 是是单峰的、对称的,是否符合正态分布。特殊原因有可能在不改变其单峰性和对称性的情 况下改变过程,同样一个非正态分布也有可能没有特殊原因,但它的分布是非对称的。
13
2014年4月29日12时7分
四、两类错误
质量管理学
应用控制图判断生产是否稳定,实际上是利用样本数据 进行统计推断。既然是统计推断,就可能出现两类错误:
第一类错误是将正常的过程判为异常,既生产仍处于统计
控制状态,但由于偶然性原因的影响,使得点子超出控制限,
虚发警报而将生产误判为出现了异常。处于控制状态的样品有
0.27%的可能落在3σ控制界限外,即犯错误的可能性在 1000 中约有 3 次。犯这类错误的概率称为第Ⅰ类风险,记作α。
第二类错误是将异常判为正常,生产已经处于非统计控制
状态,但点子没有超出控制限,而将生产误判为正常,这是漏
发警报。把犯这类错误概率称为第Ⅱ类风险,记作β。
14
2014年4月29日12时7分
质量管理学
第一类错误:虚发警报.把工序正常判为异常 • 生产者风险 α/2 ß
USL/TU UCL
第二类错误: 漏发警报把 异常判为正常 消费者风险
LCL
α/2
LSL/TL
公差界限与控制界限区别: 公差界限区分合格与不合格,控制界限则用以区分偶然皮波动与异常波。控 制界限<公差界限
15
2014年4月29日12时7分
2014年4月29日12时7分 10 控制图基于时间的统计和概率方法提供了必要且足够的方法判定过程是否有特殊原因存在。
质量管理学
控制图的设计原理
正态性假定 3σ 原理 小概率原理 反证法思想 • 正态性假定 • 任何生产过程生产出来的产品,其质量特性值总会存在一 定程度的波动,当过程稳定或者说受控时,这些波动主要 是由5MIE的微小变化造成的随机误差。此时,绝大多数质 量特性值均服从或近似服从正态分布。这一假定,称之为 正态性假定。
影响两类错误的因素:
1.控制界限的大小
质量管理学
如果扩大控制界限可以减小第Ⅰ类风险,例如将范围从μ±3σ扩展到μ±5σ, 则有 P ( |X-μ| ≤ 5 σ)=99.9999% P ( |X-μ|>5 σ)=0.0001% 此时α=0.0001%,即一百万次约有一次犯第一类错误。但是,由于将控制限从 3σ扩展到5σ,因而使第Ⅱ类风险增大,即β增大。如果缩小控制限,则可以减 少犯第二类错误的概率β,但会增加犯第一类错误的概率α。一般来说,当样本 大小为定数时,α越小则β越大,反之亦然。因此,控制图控制限的合理确定, 应以两类错误所造成的总损失最小为原则。实践证明,能使两类错误总损失最小 的控制限幅度大致为3σ。因此选取μ±3σ作为上下控制限是经济合理的。 2.样本量n的大小 当3σ控制区域一定时,样本量n增大,β减小,控制图的检出力增大。
控制图定义: 是对过程质量特性值进行测定、记录、评估和监察 过程是否处于控制状态的一种用统计方法设计的图。
3
2014年4月29日12时7分
7.1 控制图的基本原理
常规的控制图包括以下两部分:
质量管理学
(1)控制图应包括完整的“标题Fra bibliotek信息: 什么 哪里 谁 零件/产品/服务的名称和编号/标识; 操作/过程步骤信息,名称/标识; 操作者和评价者;
4 5
子组容量 A2 2 1.88 3 1.02 4 .73 5 .58 6 .48 7 .42 8 .37 9 .34 10 .31
D3 * * * * * .08 .14 .18 .22
D4 3.27 2.57 2.28 2.11 2.00 1.92 1.86 1.82 1.78
在确定过程能力之前, 过程必须受控。
CHAPTER OUTLINE 7.1 控制图的基本原理 7.2 控制图的选用与绘制
7.3 过程能力分析 7.4 过程性能指数 7.5 多变异分析 案例
1
7
质量管理学
统计过程控制
2014年4月29日12时7分
质量管理学
SPC的现状与发展
SPC(Statistical Process Control)
如何
多少 何时
使用的测量系统,名称/号码,单位(刻度);
子组容量,均衡的/根据样本决定的; 抽样方案(频率和时间)
4
2014年4月29日12时7分
质量管理学
X-R 控 制 图 --初 始 研 究
工厂:XXX 机器编号:XXX X=均值X= .95 .90 .85 .80 .75 .70 .65 .60 .55 .50 .50 .40 .30 .20 .10 .00 日期 时间 1 读 2 3 数 和
X= 和 读数数量
部门:XXX 日期:6/8-6/16 UCL=X+A
2 R=
工序:弯曲夹片 特性:间隙、尺寸“A” LCL=X-A
2 R=
计算控制限日期
工程规范:.50—.90mm 样本容量/频率: 5/2h
零件号:XXX 零件名称:XXX
均值(X图)
对 特殊 原因 采取 措施 的说 明 任何超出控制限的点 连续7点全在中心线之上或 之下 连续7点上升或下降 任何其它明显非随机的图 形 采 取措 施的 说明
11
2014年4月29日12时7分
质量管理学
3σ原理
当生产过程中仅有偶然性原因存在时, 质量特性值X服从正态分布,即X~N(μ,σ2) 。 则根据正态分布的概率性质,有 P{μ - 3 σ < X< μ + 3 σ }=99.73 % 即,从过程中测得的产品质量特性值 X有 99.73%在μ+ 3σ的范围内,
1924年休哈特(W.A.Shewhart)提出控制图
SPD(Statistical Process Diagnosis)
1980年张公绪教授提出选控控制图系列; (Cause-Selecting Control Charts Series) 1982年张公绪教授首创两种质量诊断理论; (Diagnostic Theory with Two Kinds of quality)