烧结余热回收
宝钢烧结冷却废气余热回收现状与潜力

( 宝钢 股份有 限公 司炼 铁厂 )
摘 要 阐述了宝钢股份烧结 工序 冷却废气 余热 回收的发展 和现状 ,介绍 了宝钢烧结 实行废
气余热回收的有效措施。为最 大限度回收废气余热 ,降低烧 结工序能 耗 ,分析 了进 一步提高
烧结废气余 热回收水 平的潜力 ,提 出了相应技术思路 。 关键词 烧 结 余热回收 余热锅 炉 余热发 电 工序能耗
Ke wo d sn e ig wa t e tr c v r w t e t b i r wa t e tp w rg n r t n ttl y rs it r s e h a e o e y n s a e h ol s e h a o e e e a o oa a e i
e e g o s mpto n r y c n u i n
长流程钢铁联合企业中,铁矿石烧结是必不 可少的一个工序。烧结生产过程中 , 从机尾经热 破碎卸下的烧结矿 温度高达 70— 0 % ,为便 5 80
结矿冷却废气与烧结烟气带走 了烧结生产过程大 约 5 % 的热 量 ,且 前 者 一般 都 多 于后 者 。宝 钢 0 股份本部厂区内,余热显热资源存在于炼铁 、炼 钢、轧钢与发 电四个系统。其中,属于炼铁系统 的烧结 工 序余 热 资源 约 占总余 热显 热 资源 的
1. % ,其 中烧 结矿 显 热 占 1% ,烧 结 烟 气 显 88 0
于烧结矿 的整粒筛 分和输送贮存需将 其冷却至 10 以下。烧结矿冷却过程 中,烧结矿显热大 5℃ 部分转变为冷却废气余热 ,即固态载体余热转化 为气态载体余热。烧结矿冷却废气 中高温部分可
达 30 4 0 5 — 0 ℃,这是钢铁企业 内重 要 的余热资 源。 日 本为研究钢铁企业节能极限曾设定典型的
烧结余热回收的实践

热风 点火 助燃 : 我公 司在 九十 年代 设 计
的如 马钢 3 0 烧 结机 和上钢 一 厂 1 0 0m 3 m2
热、 保温 热 风两 个系 统 。鼓 风 环冷机 给料 端 排 出的废气 温度 可 达到 3 0 3 0 。 了保 O~ 5℃ 为 护 风机 和烧 嘴 ,尤其 是 防止烧 嘴堵塞 ,冷 却 废 气 进 入 点 火器 前 ,分 别 通 过 重力 除 尘 器
度 6 ~ 0 ℃,其 余热 同收 在设 计上 是成 功 0 10
柳 钢 2 5 烧 结机 自 2 0 6 m 0 5年 开始 采用 热 风烧 结技 术 , 质量 明显提 高 , 产 节能显著 。
三 、 北敬业 2 01 烧 结机余热 河 3 1 12
发 电
随着 近 年 来 低温 废 气 余 热 锅 炉 技术 和
炉 、高炉混 合煤 气 ,系 国 内 首次使用 ,其热
值偏低 , 不能完全满足烧结要求。 然而利用
热 风助燃 点火 及 预热 混合 料 , 仅可 以提高 不 点火温 度 、节 约能 耗 、改善 烧 结矿 质量 、提 高烧 结 矿产 量 , 可 以减少 粉 尘 对厂 区环 境 还
的污染 。
的, 为烧 结 厂使用 低热 值燃 料 开辟 了新 的途 径 , 曾获得 上海 市 的奖励 。
二、 柳钢 2 5 烧结机热风烧结 6 m2
柳钢 2 5 结机 于 20 6m 烧 0 5年 3月投 入 生 产 。 结 余热 回收利 用技 术 是采用 热风 烧 烧 结 , 2 0 鼓风 环冷 机 的高温 热废 气送 往 将 8m 烧结 机点 火保温 后面 的密封 罩 内, 用 了无 采 动 力 的热 风烧 结技 术 , 利用 环 冷机 的鼓风 正 压 与烧结 料面 负压 的压 差 , 使烧 结表 层继 续
烧结厂余热利用技术简介

烧结厂余热利用技术简介1. 引言烧结是一种将粉煤灰、石灰石或其它成分相似的原料通过加热使之部分熔化,然后回结固化成块状的冶金过程。
这个过程产生的高温烟气和废热在烧结厂通常都被排放到大气中。
然而,随着对能源资源的需求和环境保护意识的增强,如何有效利用烧结厂的余热已成为研究和开发的重点。
本文将简要介绍几种常见的烧结厂余热利用技术,并分析其优点和局限性。
2. 烧结厂余热利用技术2.1 热交换器技术热交换器技术是一种常见的烧结厂余热利用技术。
热交换器可以将高温烟气中的热能传递给废水、蒸汽或其他介质,以实现能量的回收和利用。
热交换器通常包括换热管道和换热器设备。
热交换器技术的优点在于可以提供连续的热能供应,并减少对外部能源的需求。
然而,此技术的局限性在于热交换器设备的成本较高,维护困难,并且对脏污、腐蚀性介质敏感。
2.2 ORC技术ORC技术(有机朗肯循环)是一种将烧结厂余热转化为电力的技术。
ORC系统通过将高温烟气中的热能转移到有机工质中,然后通过有机工质的蒸汽驱动涡轮发电机产生电力。
与传统蒸汽发电系统相比,ORC技术可以在较低的温度下工作,提高了热能转化的效率。
此外,ORC技术还可以通过调整有机工质的选用来适应不同温度下的余热利用。
然而,该技术需要较高的初投资成本,并且对有机工质的选择和运行维护要求较高。
2.3 废热蒸汽利用技术废热蒸汽利用技术是一种将烧结厂余热转化为蒸汽以供其他生产过程使用的技术。
在烧结厂中,产生的高温烟气可以通过余热锅炉将废热转化为蒸汽,然后再将蒸汽输送到其他工序中进行能量回收。
废热蒸汽利用技术可以减少对外部能源的需求,并提高能源利用效率。
然而,该技术的缺点在于需要较大的设备投资,且对蒸汽管道的要求较高。
3. 总结烧结厂余热利用技术是一种重要的能源回收利用手段,可以减少环境污染,降低能源消耗,提高能源利用效率。
本文介绍了几种常见的烧结厂余热利用技术,并分析了它们的优点和局限性。
无论是热交换器技术、ORC技术还是废热蒸汽利用技术,都需要根据具体的烧结厂情况和需求来选择和应用。
烧结余热能量回收驱动技术
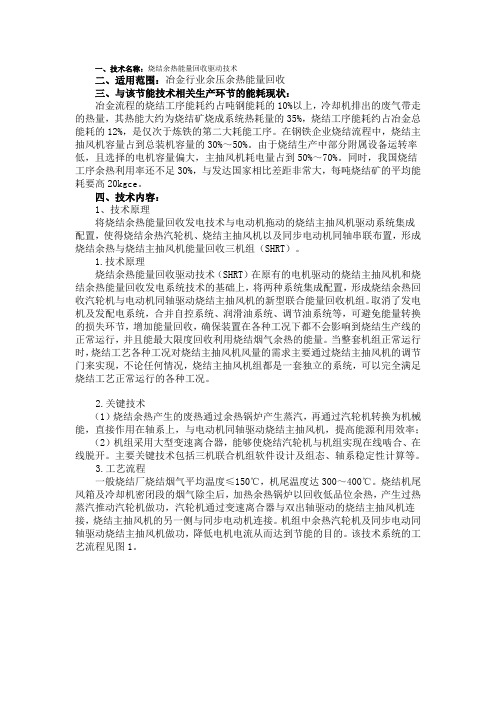
一、技术名称:烧结余热能量回收驱动技术二、适用范围:冶金行业余压余热能量回收三、与该节能技术相关生产环节的能耗现状:冶金流程的烧结工序能耗约占吨钢能耗的10%以上,冷却机排出的废气带走的热量,其热能大约为烧结矿烧成系统热耗量的35%,烧结工序能耗约占冶金总能耗的12%,是仅次于炼铁的第二大耗能工序。
在钢铁企业烧结流程中,烧结主抽风机容量占到总装机容量的30%~50%。
由于烧结生产中部分附属设备运转率低,且选择的电机容量偏大,主抽风机耗电量占到50%~70%。
同时,我国烧结工序余热利用率还不足30%,与发达国家相比差距非常大,每吨烧结矿的平均能耗要高20kgce。
四、技术内容:1、技术原理将烧结余热能量回收发电技术与电动机拖动的烧结主抽风机驱动系统集成配置,使得烧结余热汽轮机、烧结主抽风机以及同步电动机同轴串联布置,形成烧结余热与烧结主抽风机能量回收三机组(SHRT)。
1.技术原理烧结余热能量回收驱动技术(SHRT)在原有的电机驱动的烧结主抽风机和烧结余热能量回收发电系统技术的基础上,将两种系统集成配置,形成烧结余热回收汽轮机与电动机同轴驱动烧结主抽风机的新型联合能量回收机组。
取消了发电机及发配电系统,合并自控系统、润滑油系统、调节油系统等,可避免能量转换的损失环节,增加能量回收,确保装置在各种工况下都不会影响到烧结生产线的正常运行,并且能最大限度回收利用烧结烟气余热的能量。
当整套机组正常运行时,烧结工艺各种工况对烧结主抽风机风量的需求主要通过烧结主抽风机的调节门来实现,不论任何情况,烧结主抽风机组都是一套独立的系统,可以完全满足烧结工艺正常运行的各种工况。
2.关键技术(1)烧结余热产生的废热通过余热锅炉产生蒸汽,再通过汽轮机转换为机械能,直接作用在轴系上,与电动机同轴驱动烧结主抽风机,提高能源利用效率;(2)机组采用大型变速离合器,能够使烧结汽轮机与机组实现在线啮合、在线脱开。
主要关键技术包括三机联合机组软件设计及组态、轴系稳定性计算等。
烧结环冷余热回收拖动烧结主抽风机技术

烧结环冷余热回收拖动烧结主抽风机技术近年来,随着钢铁冶炼行业先进节能技术不断涌现,烧结、环冷机余热回收水平有很大幅度提高。
本文对我公司总包的一个烧结环冷余热回收拖动烧结主抽风机项目的创新技术进行介绍。
标签:烧结余热利用;余热锅炉;拖动;烧结主抽风机一、项目概况河北某铸业有限公司现有一条114㎡和一条120㎡烧结生产线,配套环冷机冷却面积均为140㎡。
为了充分利用烧结环冷余热资源,最大限度的降低综合能耗,该公司决定建设烧结环冷余热利用项目。
二、建设内容和范围(1)环冷余热蒸汽锅炉系统;(2)烧结余热蒸汽锅炉系统;(2)一套6.0MW 拖动汽轮机系统,包括:汽轮机系统、变速离合器;(3)一套烧结主抽风机系统设计(含电机);(4)烟风管道、环冷机风罩密封改造系统;(5)配套除盐水系统范围内的水箱和除盐水泵;(6)配套的循环水系统;(7)配套给排水系统,包括:工业水、生活水、消防水以及雨排水等设计;(8)自动控制系统,包括:余热锅炉、汽轮机组及循环水站系统控制,控制部分采用分散控制系统;(9)电气系统,包括:动力控制、过电压保护、照明网络等系统。
三、烧结环冷余热回收系统本工程热力系统的设计遵守“温度對口、梯级利用”的原则。
余热回收部分:在烧结线旁分别设置烧结余热锅炉和环冷余热锅炉。
烧结锅炉烟气来自烧结机大烟道温度较高的几个风箱,进入烧结锅炉换热产生饱和蒸汽,送入环冷锅炉进行过热。
环冷机一、二段部分高、中温热风汇合后进入环冷锅炉换热,产生1.15MPa、310℃的过热蒸汽和0.28MPa、170℃的补汽。
动力部分:为烧结线主抽风机配置一套烧结主抽风机拖动系统,选用1台6.0MW带补汽式纯凝汽轮机,利用余热回收部分产生的高、低压过热蒸汽推动汽轮机,通过变速离合器与同步电机联合拖动烧结主抽风机。
1、设计规模两台环冷余热蒸汽锅炉和两台烧结余热蒸汽锅炉,共产生1.15MPa、310℃蒸汽33.6t/h;产生0.28MPa、170℃的低压蒸汽6t/h;一套6.0MW工业汽轮机拖动系统。
余热回收的计算公式
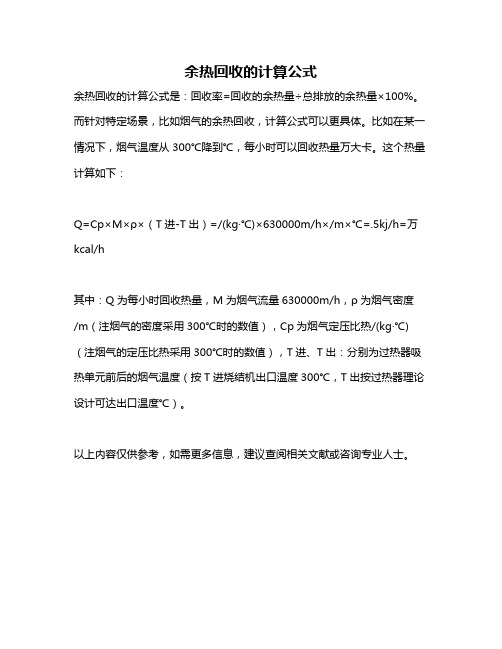
余热回收的计算公式
余热回收的计算公式是:回收率=回收的余热量÷总排放的余热量×100%。
而针对特定场景,比如烟气的余热回收,计算公式可以更具体。
比如在某一情况下,烟气温度从300℃降到℃,每小时可以回收热量万大卡。
这个热量计算如下:
Q=Cp×M×ρ×(T进-T出)=/(kg·℃)×630000m/h×/m×℃=.5kj/h=万kcal/h
其中:Q为每小时回收热量,M为烟气流量630000m/h,ρ为烟气密度/m(注烟气的密度采用300℃时的数值),Cp为烟气定压比热/(kg·℃)(注烟气的定压比热采用300℃时的数值),T进、T出:分别为过热器吸热单元前后的烟气温度(按T进烧结机出口温度300℃,T出按过热器理论设计可达出口温度℃)。
以上内容仅供参考,如需更多信息,建议查阅相关文献或咨询专业人士。
烧结余热回收利用途径

压 ,以使 电耗 达 到经济 状态 。
— —
采 用节 能型机 电设 备 。
1 3 余热 回收 利用 .
回收冷 却装 置余 热及烧 结热 废气余 热 。
在 “ ・ ”期 间 ,通过 产 业政 策调 整 ,淘 汰 十 五 小型落 后 的烧结 生产 线 ,单机规 模 大型化 ,优化 工 艺流程 及 采用节 能 型设备 ,强化 操作 管理 等 ,使 我
1 1 工 艺 方 面 改 善 .
— —
显热 和冷 却机 废气 显热 。烧结 烟气 平均 温度一 般不
超 过 1 0 ,所 含显 热 占总热量 的约 2 ,机 尾烟 5℃ 3
改善 原料 透气性 。采用厚 料层 烧结 ;添 加
气 温度 达 3 0C~4 0 0。 O ℃。冷却 机废气 温度 在 1 0 0 ℃
表 1 日本 及 韩 国 部 分 烧 结 厂 余 热 回 收 系 统 情 况
— —
点火 炉前 预热混 合料 。将冷 却机 热废 气 于
点 火前抽 过烧 结料 层 ,对 上层 混合料 进行 预热 、干
燥 。如津 西 钢 铁 公 司 2 0m 6 结 机 均 采 0 、2 5m 烧 用 此种 预热方 式 ,可降低 固体 燃耗 2 g t S ~3k / ・ 。 点 火 炉 后 进 行 热 风 烧 结。据 沙 钢 3
投 资 较 低 ,但 换 热 效 率 也 较 低 ,蒸 汽 产 生 量 少 ,
2 0 0 0  ̄4 0m 烧结 机 产 汽 量 为 1 ~ 1 / 。因 烧 结 O 6th 生 产过 程需 消耗蒸 汽 ,如混 合料预 热 、机头 除尘 器
科技成果——烧结余热能量回收驱动技术(SHRT技术)

科技成果——烧结余热能量回收驱动技术(SHRT技术)适用范围钢铁行业冶金行业余压余热能量回收行业现状冶金流程的烧结工序能耗约占吨钢能耗的10%以上,冷却机排出的废气带走的热量,其热能大约为烧结矿烧成系统热耗量的35%,烧结工序能耗约占冶金总能耗的12%,是仅次于炼铁的第二大耗能工序。
在钢铁企业烧结流程中,烧结主抽风机容量占到总装机容量的30%-50%。
由于烧结生产中部分附属设备运转率低,且选择的电机容量偏大,主抽风机耗电量占到50%-70%。
同时,我国烧结工序余热利用率还不足30%,与发达国家相比差距非常大,每吨烧结矿的平均能耗要高20kgce。
目前该技术可实现节能量6万tce/a,减排约16万tCO2/a。
成果简介1、技术原理将烧结余热能量回收发电技术与电动机拖动的烧结主抽风机驱动系统集成配置,使得烧结余热汽轮机、烧结主抽风机以及同步电动机同轴串联布置,形成烧结余热与烧结主抽风机能量回收三机组(SHRT)。
2、关键技术(1)烧结余热产生的废热通过余热锅炉产生蒸汽,再通过汽轮机转换为机械能,直接作用在轴系上,与电动机同轴驱动烧结主抽风机,提高能源利用效率;(2)机组采用大型变速离合器,能够使烧结汽轮机与机组实现在线啮合、在线脱开。
主要关键技术包括三机联合机组软件设计及组态、轴系稳定性计算等。
3、工艺流程一般烧结厂烧结烟气平均温度≤150℃,机尾温度达300-400℃。
烧结机尾风箱及冷却机密闭段的烟气除尘后,加热余热锅炉以回收低品位余热,产生过热蒸汽推动汽轮机做功,汽轮机通过变速离合器与双出轴驱动的烧结主抽风机连接,烧结主抽风机的另一侧与同步电动机连接。
机组中余热汽轮机及同步电动同轴驱动烧结主抽风机做功,降低电机电流从而达到节能的目的。
主要技术指标烧结环冷系统:220m2;配套余热回收汽轮机:5000kW;烧结主抽风机:SJ22000;电机:8000kW,余能利用效率提高5%。
技术水平该技术已获得2项目实用新型专利。
- 1、下载文档前请自行甄别文档内容的完整性,平台不提供额外的编辑、内容补充、找答案等附加服务。
- 2、"仅部分预览"的文档,不可在线预览部分如存在完整性等问题,可反馈申请退款(可完整预览的文档不适用该条件!)。
- 3、如文档侵犯您的权益,请联系客服反馈,我们会尽快为您处理(人工客服工作时间:9:00-18:30)。
烧结余热回收
■我国烧结工序能耗约占企业总能耗15%,仅次于炼铁工序,比国外先进指标高出20%以上。
主要原因之一是余热资源回收与利用水平低。
■烧结余热回收做得好的国家是日本,住友和歌山钢厂的4号烧结机生产每吨烧结矿可回收蒸汽量110~120 kg,其中低压蒸气为175℃(0.78MPa),中压蒸汽375℃(2.55MPa),吨矿回收电力20kWh,工序能耗40kgce/t。
■我国马钢引进日本川崎余热发电技术,2台328m2 烧结机余热发电,2005年9月投产,装机容量17.5MW,吨矿发电10kWh,年发电0.7亿kWh,经济效益4000万元以上,年节约3万tce;济钢1台320m2烧结机国产化余热发电系统,2007年1月投产,装机容量10MW,吨矿发电17kWh,年发电0.7亿kWh。
废气温度低,且变化频繁
废气流量大,漏风率高
梯级回收,区分余热质量
煤调湿
“煤调湿”(CMC)是“装炉煤水分控制工艺”(coal moisture control process)的简称,是将炼焦煤料在装炉前去除一部分水分,保持装炉煤水分稳定在6%左右,然后装炉炼焦的一种煤预处理工艺。
煤调湿有严格的水分控制措施,能确保入炉煤水分恒定。
煤调湿以其显著的节能、环保和经济效益受到普遍重视。
美国、前苏联、德国、法国、日本和英国等都进行过不同形式的煤调湿试验和生产,尤其是日本发展最为迅速。
截至2009年底,日本现有的16个焦化厂51组(座)焦炉中,其中有36组(座)焦炉配置了煤调湿装置,占焦炉总数的70.5%。
煤调湿技术的效果是:
1)降低炼焦耗热量、节约能源。
采用煤调湿技术后,煤料含水量每降低1%,炼焦耗热量相应降低62.0MJ/t(干煤)。
当煤料水分从11%下降至6%时,炼焦耗热量相当于节省了62.0×(11-6)=310MJ/t(干煤)=10.6kgce/ t(干煤)。
2)提高焦炉生产能力。
由于装炉煤水分的降低,使装炉煤堆密度增加,干馏时间缩短,因此,焦炉生产能力可提高4%~11%。
3)改善焦炭质量。
焦炭的冷态强度DI 可提高1%~1.5%,反应后强度CSR提高1%~3%。
4)扩大炼焦用煤资源。
在保证焦炭质量不变的情况下,可多配弱黏结煤8%~10%。
5)减少氨水处理量。
装炉煤水分若降低约5%,则可减少1/3的剩余氨水量,相应减少1/3的蒸氨用蒸汽量,同时也减轻了废水处理装置的生产负荷。
6)延长焦炉炉体寿命。
因煤料水分稳定在6%水平上,使得煤料的堆密度和干馏速度稳定,焦炉操作趋于稳定,从而起到保护炉体、延长焦炉寿命的作用。
7)节能的社会效益。
减少温室效应,平均每t入炉煤可减少约35.8kg的CO2排放量。
我国焦化厂炼焦煤含水量普遍偏高,年平均含水在11%左右。
每万吨水进入焦炉,在焦炉中汽化要耗费大约3.9×1010kJ的热能,相当于约1300吨标准煤。
如果采用煤调湿装置,不仅降低炼焦耗热量、减少温室气体排放,而且能提高焦炭产量和质量,并降低成本。
由于装炉煤水分的降低,大大减少所需处理的酚氰废水量。
建议和发展方向
1)在用高炉煤气加热焦炉的钢铁企业焦化厂应大力推广以焦炉烟道废气为热源的煤调湿技术;
2)在用焦炉煤气加热焦炉的独立焦化厂应推广以低压蒸汽为热源的煤调湿技术。
能源管控中心
管理系统的工作机制
能源管理系统(EMS)体现在企业全程的能源监控设施的一整套硬件中,更关键的是体现一种能源的系统管理模式。
实现能源系统的分散控制、集中管理、优化分配。
通过EMS 可以达到如下目标:
㈠、可以减少能源中心定员,节约成本,提高工作效率。
㈡、调度管理人员可以更全面地了解能源系统,提高能源管理水平。
㈢、及时发现能源系统故障,加快故障处理速度,使能源系统更安全。
㈣、使能源系统的运行监视、操作控制、数据查询、信息管理实现图形化,直观化和定量化。
宝钢EMS系统1991年投入使用。
吨钢综合能耗和BFG煤气的放散率两个指标每年平均降低1.6%,据估算,其中有50%应归于能源中心的节能贡献,按6年间平均750kg/t计算,每年节支8.8万吨标煤,约折合人民币2530万元。
由于该系统着眼于全厂的能源在线跟踪管理,对煤气等的综合利用意义重大,在达到节能目的同时,降低了工厂排放气体中有害气体含量,降低气体中粉尘含量,环保效益与社会效益显而易见。
高炉综合节能技术—高风温、高富氧?
•优化高炉炉料技术
进一步提高球团配比和烧结矿、焦炭的强度等冶金性能,少用或不用块矿,大幅度提高入炉矿铁品位,降低SiO2含量、燃料灰份和入炉料粉率的技术。
•进一步提高喷煤量降低入炉焦比的冶炼技术
提高风温技术(蓄热式双预热技术的开发、热风炉新型耐火材料与新型结构等);适应大喷煤量的8-12%高富氧技术;喷枪及风口等关键设备技术;突破理论临界喷煤极限量的工艺操作技术;在高风温、高富氧率和大喷煤量条件下的低焦比冶炼技术。
•低硅生铁冶炼技术
精料条件下的SiO2还原反应控制技术;低SiO2活度、低熔点、低粘度、高流动性、高脱硫能力渣系的开发,稳定铁水硅含量的低硅生铁冶炼技术。
•进一步延长高炉寿命技术
开发新型结构冷却壁及其合理的高炉炉型,以及不同材质、不同结构的冷却壁在高炉内的分布形式;炉衬(尤其是炉缸)侵蚀在线监测与预报技术;软水密闭循环冷却技术、炉衬与冷却器快速修复技术;新型耐火材料等。
•高炉专家系统的应用技术
高炉操作智能专家指导系统;与高炉专家系统相关的监测技术;与专家系统开发有关的数据处理技术和软件平台等。
•综合节能技术
大型高炉干式除尘余压压差发电技术(TRT,发电量≥35KWh/t铁),全高炉煤气发电技术,含铁粉料的回收技术,余热回收技术,节水技术。
•高炉大型化及其强化冶炼技术
大型高炉的合理炉型的优化技术,高压操作技术,适应于高冶炼强度和高压操作的炉顶设备和鼓风及喷煤设备,精料、高风温、高富氧率、高喷煤量的相互匹配的优化操作技术。
•高风温技术(1230℃—1300℃)
新型长寿热风炉的结构设计、蓄热式燃气与助燃空气双预热技术与新型耐火材料的开发。
•高炉能源转换及生产清洁能源技术
高硫煤的应用技术,高炉煤气联合循环发电技术。
•高炉处理社会废弃物技术
高炉处理废塑料、废轮胎、木屑技术;高炉焚烧可燃性粒化垃圾的技术开发。