三现五原则培训讲义
品质的三现五原则
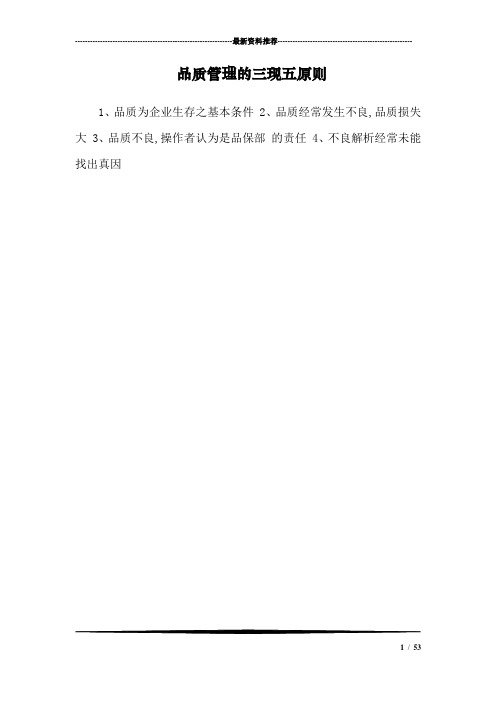
---------------------------------------------------------------最新资料推荐------------------------------------------------------品质管理的三现五原则1、品质为企业生存之基本条件2、品质经常发生不良,品质损失大3、品质不良,操作者认为是品保部的责任4、不良解析经常未能找出真因1/ 531、了解并运用三现五原则解析手法,真正改善重要品质问题2、解决问题→持续有效解决问题→不再是问题3、解决客诉品质问题挑战“零不良”---------------------------------------------------------------最新资料推荐------------------------------------------------------ 三、三现现物三现现状现场3/ 53现状把握确认项目1、机种、零件名称/号码 2、发生场所/环境/使用条件 3、发生的现象/问题 4、发生日期 5、引擎号码---------------------------------------------------------------最新资料推荐------------------------------------------------------ 现状把握确认项目6、发生件数/严重性 7、行驶里程/耐久性 8、制造日期/批重性 9、出车日期/库存性 10、不良品品质确认5/ 53现状把握确认项目11、量产中品质水准确认 12、开发阶段品质水准比对 13、设计变更履历 14、其他异常履历 15、标准确认(图面、作业、控制计划、检验标准…)---------------------------------------------------------------最新资料推荐------------------------------------------------------ 四、五原则五原则7/ 531、把握现况现状把握目的针对问题,全盘调查事实掌握变异(机遇/非机遇原因) 归纳可疑方向---------------------------------------------------------------最新资料推荐------------------------------------------------------ 1、把握现况 - 5W2H–类型、种类、受影响的部分。
三现五原则教材

为了使在调查过程中不要遗漏有用的信息和重要事实,要 多听、多看(严禁带有成见)在确认过程中尽可能地使用(3 现实主义),在进行原因分析时,要最大限度使用“特性要素 图”
现状把握举例:
1、 3、 4、 6、 机种、型号 2、 发生状况:(市场、公司内) 问题发生时的现象或(当事人的)申诉 发生年月日 5、 发生件数 对发生问题机种或是零部件的处置结果。
五原则三----对策实施
临 时 对 策 适 当 对 策 (防止恶化扩大) 永 久 对 策 (避免再发) •已流入市场处理 •库存成品处理 •半成品处理 •不良品处理 •制造面、流出 面之治本对策 •水平展开对策 •工程作业者 •进料检验者 •市场服务者 (品质通报)
对策情报传达
适当的对策(对策内容、效果预测PPA)
為什 麼之 飾條素材 五層 產生縮水 分析
2
目視檢查時 未檢查
3
無檢查基準
4
加熱不均 勻 模具損壞
5
溫度控 制損壞 未按規 定檢查
射出時素材加熱 飾條素材表 變形 面NG 模具與飾條間隙 過大
1、五層分析是三現五原則原因解析之濃縮重點內容。 2、五層分析是同說故事一樣,故事必須連貫。 3、五層分析是三現五原則單之中心思想及佈局。
不良实物
不良发生的状况, 包括使用状况 不良品发生的原 地、环境因素
五原则一--------现状把握
现状把握目的 针对问题,全盘调查事实掌握变异(机遇/非机遇原因)归纳可 疑方向 对事实的把握(现在生产的该零部件的品质状况、现象、问题 内容、发生次数、5W2H处置内容)
现状把握内容
1、问题点的概要(信息的收集、整理)例,针对部品或工程。 2、问题再现试验的结果 3、现行品的品质状况 4、发生的对象范围 5、利用绘图、图表、柱状图使问题明确化。 6、将可能想到的原因、内容,详尽的进行整理,在记录上明 确的记载。
解决问题的五原则-培训资料

•填入内容:
•1、零件确认结果 • ①故障品写真 • ②故障品确认结果:尺寸、材质等与图纸规定事项的对比,直接 找 • 出在何处、怎样不好、有何变化、 良品与不良品的特征和变 化 • 点比较、信息收集、整理 • ③对象范围、批次、生产日期把握 • ④工序中现正生产的零部件的品质状况、良品批次确认(根据 • X•-①R不管良理品图制、造工工程序能条力件 直方图对现状进行把握) •2、全•②工不序良品检证制(造对年月全日工序确认,…查等,找用不工序良系发列生、工时序间和系列流整出理工。序)
•
(WHAT)什么-问题的症状,尽可能地使用图表等工具将问题表达清楚.
•
(WHEN)何时-记入问题发生的日期
•
(WHERE)何地-记入问题发生的场所
•
(WHY)为什么-具体的内容
•.2H: (HOW)怎么样-(问题)是怎么样被发现的
•
(HOW MANY)什么程度-(问题)发生的量、程度
解决问题的五原则-培训资料
解决问题的五原则-培训 资料
2020/12/7
解决问题的五原则-培训资料
•五 原 则 的 定 义
•“五原则”是指从“三现主义”(现场、现物、现 实)出发,分五个步骤解决问题。
•1 •充分掌握事实情况 •2 •查明真正的原因
•五个步骤是 •3 •实施切实的对策 :
•4 •确认所采取的对策是否有效
•5 •反馈到发生问题的源流
关部门传达。
•写好五原则报告表的关键:运用五原则手法解决问题
•6、减少问题再次发生的次数
解决问题的五原则-培训资料
•五原则的填写说明-发 生 状 况(现象、投诉内容、发生件数、处置内容)
•填写目标: •1、为体现到下一个行动、目标 •2、为更鲜明体现部品、部位, 应直接写下事实现象,并如实写 明该时的动机、变化
三现五原则对策法培训教材

控制计划、试验规范、标准样品等。
4.保证不会再发:真因→对策→回馈标准
10
七:解析对策应再现验证证明
疑问点:你如何知道解析不良原因是正确的吗? 思 考:科学的实验是最好的证明→再现试验。
分析方法:正向再现与反向再现。
1.正向:将不良要因排除(不良条件修正)后会制造出良品。 2.反向:以不良条件生产会制造出不良品。 若上述二项再现试验结果结果与假设违背,则肯定所解 析出的不良原因必定有偏差。
6
三:解析对策不能增加不必要成本 疑问点:利润很高吗?增加成本没关系吗? 说明:
1.利润=售价-成本。成本增加,自然利润降低。
2.解析对策成本面结果有三种: a.成本增加:需有增加的合理理由
b.成本不变动:
c.成本下降:理想状态 3.成本增加部份由供应商吸收,虽然不影响现有利 润,但总体成本仍是增加,也不是好的对策。
解析对策必须考虑成本
7
四、解析对策不应以变更设计来改善制程变异
疑问: 1.变更设计就不会有问题了吗? 2.变更设计可能有新问题,甚至比现在的问题更严重。 3.制程中4M问题未改善,变更设计就不会发生相同的 问题吗? 说明: 1.设计者的设计思路不详,不能更改设计。 2.原设计时,经过耐久的验证及市场的考验,其可靠度 很高。 3.未依图面制作及未依原设计制作而产生的问题(市怨、 厂异…)经常发生。 4.依图面设计制作有保障。
临时对策的执行成效
永久对策的执行成效 *零件的品质特性(制程能力的改善) *完成品的品质水准 *耐久品质水准确认 *市场品质状况确认 *图面 *零件检验标准 *作业标准 *试验规范 *限度样品
4. 效果确认
实际品质水准 效果确认
标准类反映 5. 源流回馈 (标准化) S.O.P修订
质量管理中的三现五原则(解决问题的经典套路)

质量管理中的三现五原则(解决问题的经典套路)质量管理中的三现五原则(解决问题的经典套路)2020-08-05 17:00今天,九脑汇学院就来说⼀说质量管理中三现五原则,所谓三现即:现物、现状、现场,包含这三点,希望这份资料能对⼤家有所收获。
三现主义企业常见的缺乏“三现主义”的现象:等待⽣产现场的联系或⽣产现场对于技术、品质、资材等部门服务、指导、指⽰、供应的等待。
等待下级的汇报,任务虽已布置,但是没有检查,没有监督。
不主动去深⼊实际调查研究,掌握第⼀⼿资料,只是被动地听下级的汇报,没有核实,然后作决定或向上级汇报,瞒天过海没有可信度,出了问题,责任往下级⾝上⼀推。
注:“三现主义”的缺乏是等待中的最致命原因之⼀,严重影响⽣产现场⼯作的及时解决。
现场不要只坐在办公室决策,⽽是要⽴即赶到现场,奔赴第⼀线。
现场是⽣机勃勃的,每天都在变化,不具备正确的观察⽅法,你就没法感觉它的变化,包括异常。
现物管理的最重要的概念是“总是以事实为基础⽽⾏动”,解决问题要求你找到事实真相。
因为只有⼀个真理存在,最通⽤的⽅法是“到问题中去,并客观地观察其过程”。
观察你看不到的地⽅,这时,事实将出现。
要发现其变化的原因,仔细观察事实。
当你这样做时,隐藏的原因将会出现,这样做,你可以提⾼发现真相的能⼒。
现实解决问题需要你⾯对现实,把握事实真相。
我们需要⽤事实解决问题,⽽事实总是变化⽆常的,要抓住事实就要识别变化,理想与实际总是有很⼤的差距。
很多问题如果我们不亲临现场,不调查事实和背景原因,就不能正确认识问题。
但为什么会发⽣那样的问题呢?我们要多问⼏次“为什么”,对“现物”、“现实”进⾏确认。
五原则五原则是指从三现主义(现场、现物、现实)出发,分五个步骤来解决问题:五原则的重要思想:①从“三现主义” (现场、现物、现实)出发解决任何问题都应当最先掌握现场、现物、现实中有⽤的实际情况。
如果没有掌握实际情况。
那么,从⼀开始就⾛弯路,⾛得越远,误差越⼤,当然最终得不出真正的结论。
品质管理的三现五原则讲课文档

4.要因:半成品因台车太小不慎流入后工程
对策:台车修改加大 5.要因:修护车辆,等待时间长
对策:等待时间提供杂志阅读
第三十七页,共五十三页。
11、要因 对策案例练习
6. 要因:涂装后之成品受落尘污染 对策:将成品以防尘套保护
7. 要因:锁付之螺丝易松动 对策:螺丝追加LOCKTITE涂布
品质管理的三现五原则
第一页,共五十三页。
品质管理的三现五原则
第二页,共五十三页。
1、品质为企业生存之基本条件 2、品质经常发生不良,品质损失大 3、品质不良,操作者认为是品保部
的责任 4、不良解析经常未能找出真因
第三页,共五十三页。
1、了解并运用三现五原则解析
手法,真正改善重要品质问
题 2、解决问题→持续有效解决问
直觉+经验≠事实
100个直觉或经验不如1个数据
分析方法:科学的根据=实验数据
~ 有实验的数据才能决定新的标准。
~ 要去试验出焊道加长2mm及模温提高10℃是作
业最好的条件。
第二十四页,共五十三页。
2、以偏概全
疑 问 点:以1、2个数据来判断,可靠吗? 思 考 点:~ 1、2个数据不能代表全部的不
良。 ~ 以偏概全可能仅会解决某比例之
第七页,共五十三页。
现状把握确认项目
11、量产中品质水准确认 12、开发阶段品质水准比对
13、设计变更履历 14、其他异常履历 15、标准确认(图面、作业、控制计
划、检验标准…)
第八页,共五十三页。
四、五 原 则
五原则
第九页,共五十三页。
1、把握现况 现状把握目的
针对问题,全盘调查事实 掌握变异(机遇/非机遇原因) 归纳可疑方向
三现五原则培训讲义

五原则
1.
◎现状把握的目的 1.真对问题全面调查事实. 2.掌握变异. 3.归纳可疑方向
查明要因 真因追查
5W分析 特性要因图 再现试验 NG再现试验 OK再现实验
2.
问题 要因 真因 查明真因
不良原因 流出原因
≈
何谓三现五原则
≈
适当对策
*已留入市场处理
临时对策
*库存成品处理 *半成品处理 *在库物料处理
标准化
S.O.P修正
*试验规范 *限度样品
三现五原则对策注意事项 1.无科学根据DATA之解析对策
2.以偏盖全之解析对策
3.增加不必要成本之解析对策
4.以变更设计改善制程变异之改善对策 5.变化点分析不明确之解析对策 6.无回馈标准之解析对策 7.无再现之解析对策
8.无三现之解析对策
9.无制程面、流出面检讨之解析对策 10.五层分析内容不连续解析对策
一.没有科学根据DATA 问题点:常发生的直觉判断 焊接强度不足 对策:加锡 正确吗? 焊接器件不粘锡 对策:焊接温度提升10度 没问题吗?
思 考:加锡/提高烙铁温度10度如何得来的? 直觉+经验≠事实 100个直觉或经验不如1个数据
分析方法:科学的根据=实验数据 有实验的数据才能决定新的标准. 要去试验出加锡及温度提高10度是最好的作业条件.
三现五原则讲义
前
一.背景
言
1.品质是企业生存的基本条件. 2.品质经常发生异常.成本损失大. 3.品质不良,操作人员总是认为是品管部门的责任. 4.不良解析经常找不到真因.
二.基本想法
1.籍由提高三现五原则解析能力.真正改善重要的品质问题点. 2.解决问题 持续有效的解决问题 不再是问题
三现五原则讲义

七:再現試驗證明
疑 問 點:你如何知道解析不良原因是正確的嗎? 思 考:科學的實驗是最好的證明→再現試驗。
分析方法:正向再現與反向再現
1.正向:將不良要因排除(不良條件修正)後會製 造出良品。 2.反向:以不良條件生產會製造出不良品。 若上述二向再現結果與假設違背,則肯定所解析 出之不良原因必定有偏差。 3.不良品再現
QC OK 工程表
OK OK
知識 為 不了解重點 何 新 左 手 前 不熟練 椅 未檢查 椅 檢具 背 晃 檢出力 動 未製作
標準文件
太寬鬆
設備
未規劃
2.查明原因(再現試驗、原因分析)
3.適當的對策(對策內容、對策後實際效果確認) 4.對策本案所費工時
NO 發生不良原因 對策內容 擔當 期限 蔡 正 欽 05/ 03/ 28 確認結果
三.目的:
1.交貨品質100PPM↓ 2.市場品質問題挑戰“零不良”
三現五原則
市怨編號 反應單位 反應者 K0504001 廠異編號 張 木 信 主管 管制單位 品 質 檢 查 課 承辦者 主管 尤 宏 文 游 家 齊 製 品 NY 技 術 反應日期 94 年 04 月 22 日 課 對策 單位 4PT D 指派對策者 PL
疑 問 點:1.為何會流出?為何會製造?為何設備檢不出?
2.流出面之解析對策經常被疏忽。
思
考:顧客所反應之問題必定製造面、流出面共同發生,僅
對策製造或流出面並能徹底解決問題。
分析方法:1.製造面→分析4M之變化點→真因對策。
2.流出面→a.分析製程中之流程→作業環境、作業檢
驗工程標準 b.分析檢驗之流出、出貨檢驗標準、限度 樣品、自動檢測、防呆裝置。 PS:為何會檢驗不出來。
- 1、下载文档前请自行甄别文档内容的完整性,平台不提供额外的编辑、内容补充、找答案等附加服务。
- 2、"仅部分预览"的文档,不可在线预览部分如存在完整性等问题,可反馈申请退款(可完整预览的文档不适用该条件!)。
- 3、如文档侵犯您的权益,请联系客服反馈,我们会尽快为您处理(人工客服工作时间:9:00-18:30)。
对产出面或流出面作对策是不能完全解决问题的。
分析方法:1.制造面:分析4M之变化,查出真因对策
2.流程面:分析制程之流程。主要从作业环境、作业、检查工
程标准、限度样品。自主检查及防呆装置方面入手。
十. 五层分析
意义:为什么要做五层分析。其目的就是要找出不良的真正原因。
六.未回馈标准 问题点: 如何保证以后不会再发?这样对策就不会再发了吗?欠缺了什么?
思考点: 1.作业者不知道、不清楚,则不良点仍然生。所以让作业人员 明白如何才能作出良品是非常重要的。 2.
标准回馈明 确 作业人员知 道如何去做 作员人员品 质意识提升
3.作业标准四项重点:内容、手顺、时间、结果 4.重要标准类:作业标准、图面、零件检验标准、QC工程表 试验规范、标准样品。 5.保证不会再发:真因 对策 回馈标准
三.增加不必要的成本 问题点: 利润很高吗?增加成本没关系吗? 说 明: 1)利润=售价-成本 成本上升,自然利润下降 2)解析对策成本面结果有三种 A.成本上升,需有上升的合理原因,需检讨合理性
B.成本不变动
C.成本下降(非常棒) 3)成本上升的部分由供应商吸收,虽然不影响系统,但对总体成 本还是上升,亦非好的对策.
说 明:1.未三现可能会得到错误的信息,或疏略掉重要的资讯
2.有三现才能相信自已,说服别人。
3.选择性事实:三现的目的在于针对问题全面掌握事实。而未 三现可能只知道部分事实。
解析对策必须遵守三现原则
九.制造面、流出面检讨 问题点: 1.为何会生产出来? 为何会流出去? 为何检测不出来?
2.流出面的问题检讨常被疏忽。
制程变异需从制程面去改善
五.变化点分析不清楚 问题点: 1.以前为何不发生,现在才发生?
一定是那里发生了变异,变化点在那里?
思考点: 不良点一定隐藏于变化点中
分析方法: 4M1D中寻找真因
人【MAN】:人员是否有变更,是否有按标准作业,人员士气等 机【MACHINE】:设备、模、治、检、工具是否有调整、变更 料【MATERIAL】:材料是否有变化、前工序流入不良件 法【METHOD】:标准是否有规定,标准是否明确 设计【DESIGN】:是否有设计变更
解析对策必须考虑成本面
四.以变更设计改善制程变异 问题点: 1.变更设计就不会有问题了吗?
2.新设计有新的问题,甚至比现在的问题更严重
3.制程中4M问题没有改变,新设计就不会发生相同的问题吗?
说 明: 1.设计原理不详,不能改变设计.
2.原设计经过耐久试验及市场考验,其可靠度可以信赖 3.未依原始的图纸及原始的设计理念改善问题经常会发 生报怨(市场报怨、客户投述)
一.没有科学根据DATA 问题点:常发生的直觉判断 焊接强度不足 对策:加锡 正确吗? 焊接器件不粘锡 对策:焊接温度提升10度 没问题吗?
思 考:加锡/提高烙铁温度10度如何得来的? 直觉+经验≠事实 100个直觉或经验不如1个数据
分析方法:科学的根据=实验数据 有实验的数据才能决定新的标准. 要去试验出加锡及温度提高10度是最好的作业条件.
永久对策 对策情报传达
制造面、流出面之根本对策 水平展开之对策 生产作业人员 进料检验人员 市场服务人员(品质通报)
对策内容之效 果确认 效果确认
临时对策之执行成效 永久对策之执行成效 *零件之品质物性
实际品质水准 之效果确认
*完成品之品质水准 *耐久品质水准 *市场品质状况确认
标准类反应
*图面 *零件检验标准 *作业标准
五原则
1.
◎现状把握的目的 1.真对问题全面调查事实. 2.掌握变异. 3.归纳可疑方向
查明要因 真因追查
5W分析 特性要因图 再现试验 NG再现试验 OK再现实验
2.
问题 要因 真因 查明真因
不良原因 流出原因
≈
何谓三现五原则
≈
适当对策
*已留入市场处理
临时对策
*库存成品处理 *半成品处理 *在库物料处理
二.以偏盖全 问题点: 用1、2个数据来判断、可靠吗? 思 考: 1、2个数据不能代表全部的不良 以偏盖全可能只解决一部分的不良,而不是所有的不良 没有彻底的解决问题,不良还会再次发生 分析方法:利用品管统计学来掌握解析手法之可靠性。问题的解 析与效果确认,皆可用品管统计手法。 1.掌握品质的准确程度 A.平均数 B.中值 2.掌握品质均匀程度 A.全距 B.最大值(MAX) 最小值(MIN) C.标准差 3.掌握制程的品质能力 A.CP值 B.CPK值
1.达成品质目标. 2.市场品质问题挑战 “零不良”.
何谓三现五原则
三现 现物 现场 现状 事实把握
*机种、产品名称/品号 *发生场所/环境/使用条件 *发生现象/问题 *发生日期 *发生的件数/严重性 *使用时程/耐久性 *制造日期/批量性 *出货日期/库存性 *不良现物品质确认 *量产中品质水准确认 *开发阶段品质水准确认 *设计变更履历 *其它异常履历 *标准确认(图纸/SOP…….) 4M分析
七.再现验证 问题点: 你如何知道解析的不良原因是正确呢?
思考点: 科学的实验是最好的证明
再现试验
分析方法: 正向再现与反向再现
1.正向:将不良要因排除后会制造出良品 2.反向:以不良条件生产会产出不良品 若上述两项再现结果与假设违背,则肯定所解析的不良原因必 定是有偏差.
八.无三现之解析对策 问题点: 有到现场去看吗?有实际的产品实物、实地的确认吗?
三现五原则讲义
前
一.背景
言
1.品质是企业生存的基本条件. 2.品质经常发生异常.成本损失大. 3.品质不良,操作人员总是认为是品管部门的责任. 4.不良解析经常找不到真因.
二.基本想法
1.籍由提高三现五原则解析能力.真正改善重要的品质问题点. 2.解决问题 持续有效的解决问题 不再是问题
三.目的
五层分析是三现五原则原因解析之浓缩的重点内容。
五层分析如同写故事一样,故事必须连贯。
标 题 零件图号 发 起 人 签发日期
部
零件名称 审 批 人 请于 年 月 日前返回
门 制作
年
五 原 则 表
月 日 审核 批准
接 收 人
ቤተ መጻሕፍቲ ባይዱ
年 月 日 确认 批准
发生状况(发生件数、发生现象、处置情况等)
时间
一、现况把握(不良品的确认、批次跟踪、要因分析)
标准化
S.O.P修正
*试验规范 *限度样品
三现五原则对策注意事项 1.无科学根据DATA之解析对策
2.以偏盖全之解析对策
3.增加不必要成本之解析对策
4.以变更设计改善制程变异之改善对策 5.变化点分析不明确之解析对策 6.无回馈标准之解析对策 7.无再现之解析对策
8.无三现之解析对策
9.无制程面、流出面检讨之解析对策 10.五层分析内容不连续解析对策
二、查明原因(再现试验、发生机理、发生原因、流出原因) 三、合适对策(发生对策、流出对策)
四、检查对策效果(量化的实际效果)
1、WHY
2、WHY
3、WHY
4、WHY
5、WHY
五、横向展开、反馈到源头(系统)