硫化氢汽提塔腐蚀分析与应对措施
加氢装置脱硫化氢汽提塔的腐蚀与对策

引用格式:孙开俊,庄 强.加氢装置脱硫化氢汽提塔的腐蚀与对策[J].石油化工腐蚀与防护,2022,39(4):21 24. SUNKaijun,ZHUANGQiang.CorrosionofH2Sstripperinhydrogenationunitanditscountermeasures[J].Corrosion&ProtectioninPetrochemicalIndustry,2022,39(4):21 24.加氢装置脱硫化氢汽提塔的腐蚀与对策孙开俊,庄 强(中国石化扬子石油化工有限公司,江苏南京 210048)摘要:脱硫化氢汽提塔是加氢装置分馏单元腐蚀性介质含量最高、腐蚀问题最为严重的设备。
某石化公司因原料变化对硫化氢汽提塔的进料段进行设计调整,运行一个周期后发现进料段第5至8层区域筒体和内构件发生严重腐蚀。
通过观察腐蚀形貌、腐蚀风险评估,结合工艺运行参数及露点温度核算,认为硫化氢汽提塔进料段附近区域腐蚀为汽蚀和高温H2S/H2腐蚀,且因改造后材质未能同步升级等因素所致。
提出了材质升级、进料分布结构优化和工艺运行调整等改进措施,可减缓腐蚀发生。
关键词:加氢装置;脱硫化氢汽提塔;腐蚀分析;汽蚀;防腐蚀措施收稿日期:2022 02 16;修回日期:2022 06 22。
作者简介:孙开俊(1984—),工程师,毕业于南京工业大学化工过程机械专业,主要从事加氢装置设备技术管理工作。
E mail:sunkj01.yzsh@sinopec.com基金项目:中国石化科技开发项目“双超加氢反应器在200万吨/年渣油加氢装置上的应用”(10GKC008) 在加氢装置反应产物中含有硫化氢、氨和氯化氢等腐蚀性物质,为排除隐患以保障装置安全,一般在分馏单元设置脱硫化氢汽提塔脱除这些腐蚀性介质。
脱硫化氢汽提塔是加氢装置分馏单元腐蚀性介质含量最高、腐蚀最严重的设备[1 4]。
某炼化公司3.7Mt/a汽柴油加氢装置,主要加工直馏煤油、直馏柴油和焦化汽油,并生产石脑油和柴油。
湿硫化氢腐蚀

二级入口气阀固定螺栓的设计材质为3Cr13, 硬度要求HB280-320。断裂固定螺栓含Cr量 5.967%,硬度高达HRC58.6(相当于HV676)。 且1Cr13、2 Cr13、3 Cr13金相组织为马氏 体,对SSCC最敏感,这样高硬度(远高于 HB235)与敏感的马氏体组织的螺栓在瓦斯 HS+H2O的作用下,
11、 胜利炼油厂FCC吸收解吸塔解吸段塔壁氢鼓
泡开裂。(材质A3,1968年投用,1972年发现HB)
12、 胜南京炼油厂FCC吸收解吸塔降液板使用半
年后出现HB,一个周期后HB处开裂。
13、 胜利炼油厂FCC吸收解吸气后冷凝器壳体使 用不到一年出现氢鼓泡、鼓泡开裂和焊缝开裂。 (T=45℃,P=1 Mpa,介质含H2S6%,CN 0.1%及 少量水分,材质为16Mn)。
2、冷高分底(D102)排污水管线大小头开裂。 2001
年3月7日发现开裂,高压水和H2S喷出。由于发现用 时,未发生次生恶性事故。实际运行一年零三个月, 材质为A234/A234M-910 WPB,碳钢锻件,运行介质 为H2S+NH3+H2O,其中H2S含量34284PPm,NH3含 量为19599PPm,温度为45度,压力为15.6MPa.
扩展造成。
9、 1975年四川气田,16Mn螺旋焊管在试压 仅几个小时后即发生两次爆炸。分析结果是, 焊管补焊处产生马氏体过硬组织,未退火处 理,硬度有的高达RC38-42,因而发生应力 腐蚀快速破裂。以后改为退火处理,硬度降
至RC22以下,未再发生问题。
10、 洛阳炼油厂1#催化气体脱硫装置的溶 剂再生塔(1984年投用,上下SM41B+SUS321, 中间A3R),前13个周期(约12年)运行良 好,1996年4月第14周期开工蒸汽试压时发 现中间段开裂泄漏2次。裂纹位置在降液板
汽提及制硫设备腐蚀原因分析及对策
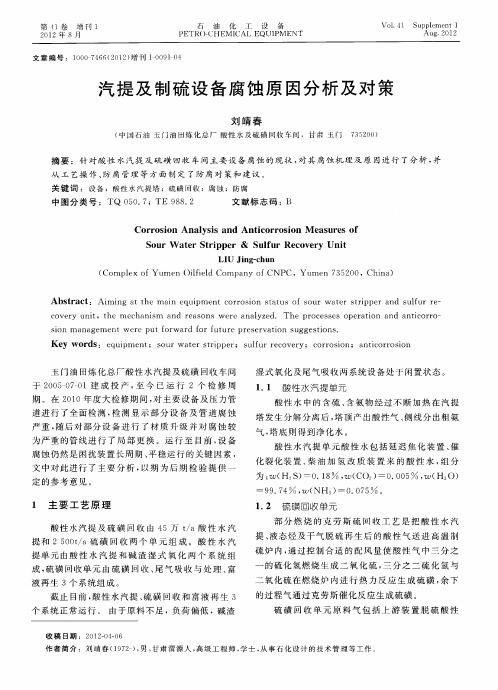
的硫 化 氢燃烧 生 成 二 氧化 硫 , 三分 之 二硫 化 氢 与
二氧化 硫 在燃烧 炉 内进行 热 力 反 应 生成 硫 磺 , 下 余 的过程 气 通过克 劳斯 催化 反应 生成硫 磺 。 硫 磺 回 收 单 元 原 料 气 包 括 上 游 装 置 脱 硫 酸 性
c v r t t e me h n s a e s o e y uni, h c a i m nd r a ons w e e a l z d. T h o e s s o r to nd a tc r r na y e e pr c s e pe a i n a n ior o so a g m e e e p o w a d f r f t e pr s r a i ug s i s i n m na e ntw r utf r r o u ur e e v ton s ge ton .
LI Ji g c n U n - hu ( m pl x o um e ( ife d Com pa fCN PC , Y u e 5 0 Co e fY n )li l ny o m n 73 2 0,Chi a n)
A b t a t Ai n t t e ma n e u p e t c r o i n s a u f s u t r s rp e n u f r r sr c : mi g a h i q i m n o r so t t s o o r wa e t i p r a d s lu e
第 4 1卷 增 刊 1 21 O 2年 8月
石
油
化
工
设
备
PE TR( 一 ) CHEM I CAI QUI E PM ENT
V o . Sup e e 1 41 plm nt1 A u .2 2 g 01
蜡油加氢装置硫化氢汽提塔的腐蚀与防护
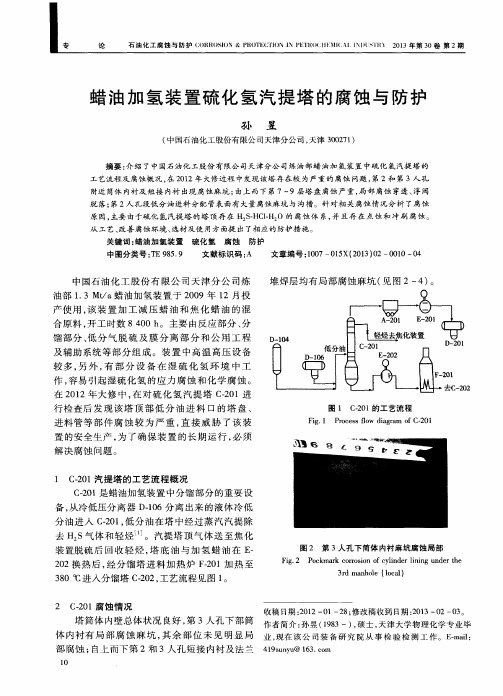
堆 焊层 均 有 局部 腐 蚀 麻坑 ( 见 图 2~ 4 ) 。
馏部分 、 低 分 气 脱 硫 及 膜 分 离 部 分 和 公 用 工 程 及 辅 助 系统 等 部 分 组 成 。装 置 中 高 温 高 压 设 备 较多 , 另外 , 有 部 分 设 备 在 湿 硫 化 氢 环 境 中 工
装 置脱 硫 后 回收 轻 烃 , 塔 底油 与加氢蜡 油在 E 一 2 0 2换 热 后 , 经分馏塔进料加热炉 F 一 2 0 1加 热 至 3 8 0℃进 入分馏 塔 C - 2 0 2 , 工艺 流程见 图 1 。
2 C 一 2 0 1腐蚀情 况
图 2 第 3人 孔 下 简体 内衬 麻坑 腐严 重 , 直 接 威 胁 了 该 装
置 的安全 生 产 , 为 了确 保 装 置 的长 期 运 行 , 必 须
解 决 腐蚀 问题 。 1 C . 2 0 1 汽 提 塔的 工艺流 程概 况
C - 2 0 1是蜡 油加氢 装 置 中分馏 部 分 的重 要 设
备, 从冷 低压 分 离器 D . 1 0 6分 离 出来 的液 体 冷 低 分油进入 C . 2 0 1 , 低 分 油 在塔 中经 过 蒸 汽 汽 提 除 去 H , s气 体 和 轻 烃 j 。汽提 塔 顶 气 体 送 至 焦 化
MS+2H + 2C1 一 MCl 2+H2 S
腐 蚀 的严重程 度 看 , 应 该 进 一 步计 算 或 调 整塔 顶 温度 , 因为湿 H s溶 液 中 的腐 蚀 和温 度 关 系 比较 复杂 , 一方面, 温度升高, H : s在 水 中的 溶 解 度 降 低, 可 以减 弱腐 蚀 ; 但 另一 方面 , 温度 升高 , 金属 与
9s un y u@ 1 6 3. C O I n 部 腐蚀 ; 自上 而下 第 2和 3人 孔 短接 内衬 及法 兰 41
高温硫化氢腐蚀
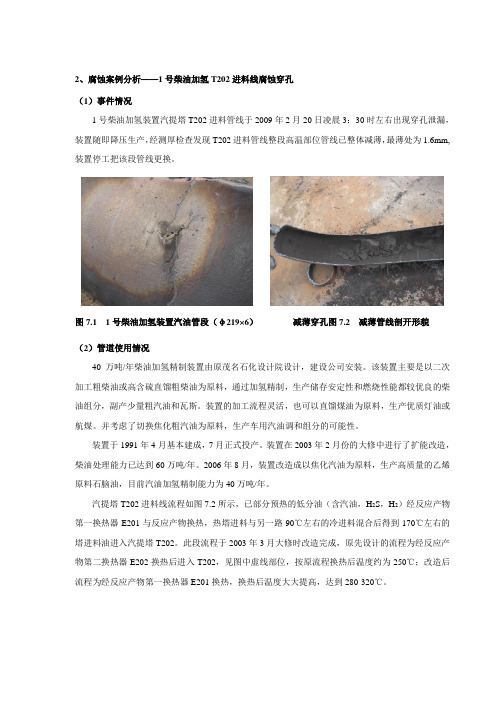
2、腐蚀案例分析——1号柴油加氢T202进料线腐蚀穿孔(1)事件情况1号柴油加氢装置汽提塔T202进料管线于2009年2月20日凌晨3:30时左右出现穿孔泄漏,装置随即降压生产,经测厚检查发现T202进料管线整段高温部位管线已整体减薄,最薄处为1.6mm,装置停工把该段管线更换。
图7.1 1号柴油加氢装置汽油管段(φ219×6)减薄穿孔图7.2 减薄管线剖开形貌(2)管道使用情况40万吨/年柴油加氢精制装置由原茂名石化设计院设计,建设公司安装。
该装置主要是以二次加工粗柴油或高含硫直馏粗柴油为原料,通过加氢精制,生产储存安定性和燃烧性能都较优良的柴油组分,副产少量粗汽油和瓦斯。
装置的加工流程灵活,也可以直馏煤油为原料,生产优质灯油或航煤。
并考虑了切换焦化粗汽油为原料,生产车用汽油调和组分的可能性。
装置于1991年4月基本建成,7月正式投产。
装置在2003年2月份的大修中进行了扩能改造,柴油处理能力已达到60万吨/年。
2006年8月,装置改造成以焦化汽油为原料,生产高质量的乙烯原料石脑油,目前汽油加氢精制能力为40万吨/年。
汽提塔T202进料线流程如图7.2所示,已部分预热的低分油(含汽油,H2S,H2)经反应产物第一换热器E201与反应产物换热,热塔进料与另一路90℃左右的冷进料混合后得到170℃左右的塔进料油进入汽提塔T202。
此段流程于2003年3月大修时改造完成,原先设计的流程为经反应产物第二换热器E202换热后进入T202,见图中虚线部位,按原流程换热后温度约为250℃;改造后流程为经反应产物第一换热器E201换热,换热后温度大大提高,达到280-320℃。
图7.3 1号柴油加氢装置T202进料管段示意图对此段管线全面测厚显示,图7.3中红色所示的管段均整体减薄至1.5mm-2.8mm,穿孔的泄漏点就是在此管段的一个弯头前;而冷料线加入以后的管段厚度为5mm-7mm,属于正常厚度范围。
常减压装置腐蚀分析与防护措施
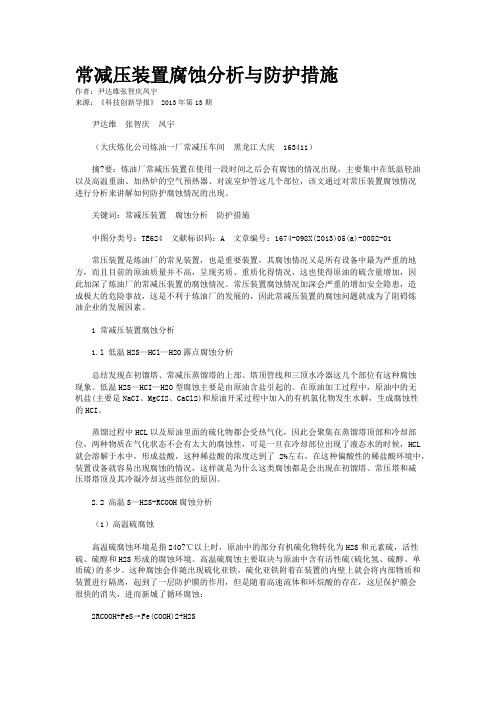
常减压装置腐蚀分析与防护措施作者:尹达维张智庆凤宇来源:《科技创新导报》 2013年第13期尹达维张智庆凤宇(大庆炼化公司炼油一厂常减压车间黑龙江大庆 163411)摘?要:炼油厂常减压装置在使用一段时间之后会有腐蚀的情况出现,主要集中在低温轻油以及高温重油、加热炉的空气预热器、对流室炉管这几个部位,该文通过对常压装置腐蚀情况进行分析来讲解如何防护腐蚀情况的出现。
关键词:常减压装置腐蚀分析防护措施中图分类号:TE624 文献标识码:A 文章编号:1674-098X(2013)05(a)-0082-01常压装置是炼油厂的常见装置,也是重要装置,其腐蚀情况又是所有设备中最为严重的地方,而且目前的原油质量并不高,呈现劣质、重质化得情况,这也使得原油的硫含量增加,因此加深了炼油厂的常减压装置的腐蚀情况。
常压装置腐蚀情况加深会严重的增加安全隐患,造成极大的危险事故,这是不利于炼油厂的发展的,因此常减压装置的腐蚀问题就成为了阻碍炼油企业的发展因素。
1 常减压装置腐蚀分析1.l 低温H2S—HCl—H2O露点腐蚀分析总结发现在初馏塔、常减压蒸馏塔的上部、塔顶管线和三顶水冷器这几个部位有这种腐蚀现象。
低温H2S—HCI—H2O型腐蚀主要是由原油含盐引起的。
在原油加工过程中,原油中的无机盐(主要是NaCI、MgCI2、CaCl2)和原油开采过程中加入的有机氯化物发生水解,生成腐蚀性的HCI。
蒸馏过程中HCL以及原油里面的硫化物都会受热气化,因此会聚集在蒸馏塔顶部和冷却部位,两种物质在气化状态不会有太大的腐蚀性,可是一旦在冷却部位出现了液态水的时候,HCL 就会溶解于水中,形成盐酸,这种稀盐酸的浓度达到了2%左右,在这种偏酸性的稀盐酸环境中,装置设备就容易出现腐蚀的情况,这样就是为什么这类腐蚀都是会出现在初馏塔、常压塔和减压塔塔顶及其冷凝冷却这些部位的原因。
2.2 高温S—H2S-RCOOH腐蚀分析(1)高温硫腐蚀高温硫腐蚀环境是指240?℃以上时,原油中的部分有机硫化物转化为H2S和元素硫,活性硫、硫醇和H2S形成的腐蚀环境。
硫化氢汽提塔顶的腐蚀与对策
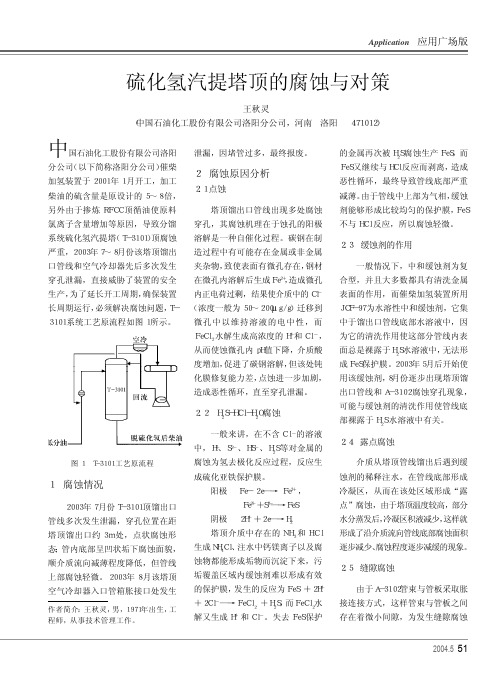
穿孔泄漏,直接威胁了装置的安全 在微孔内溶解后生成Fe2+,造成微孔
生产,为了延长开工周期,确保装置 内正电荷过剩,结果使介质中的 Cl-
长周期运行,必须解决腐蚀问题,T- (浓度一般为 50~200µg/g)迁移到
3101 系统工艺原流程如图 1 所示。 微孔中以维持溶液的电中性,而
FeCl2 水解生成高浓度的 H+ 和 Cl -, 从而使蚀微孔内 pH 值下降,介质酸
Application 应用广场版
硫化氢汽提塔顶的腐蚀与对策
王秋灵 (中国石油化工股份有限公司洛阳分公司, 河南 洛阳 471012)
中国石油化工股份有限公司洛阳 泄漏,因堵管过多,最终报废。
分公司(以下简称洛阳分公司)催柴 加氢装置于 2001 年 1 月开工,加工 柴油的硫含量是原设计的 5~8 倍,
除塔顶馏出口管线和空冷管 束材质升级外,其他部位仍采用 了碳钢。
3.2 改进空冷结构形式
管束与管板胀接方式的缺点是 容易 发 生 缝 隙 腐 蚀 , 新 空 冷 改 进 为强度焊接,采用钨极氩弧焊以 保 证 焊接质量,管头用焊接材料 08Cr2AlMo 堆焊 φ25mm × 3mm 的 环状焊肉,以增加管端的腐蚀裕量, 消除了缝隙腐蚀的可能性;管箱采 用全熔透结构,焊接完毕后进行整
3 采取对策
3.1 材质升级
塔顶馏出口管线材质为 20# 优 质碳钢,抗 HCl 腐蚀能力较差,材质 升级为 1Cr18Ni9Ti,Cr 元素可提高 不锈钢的耐点蚀能力、钝化和再钝 化能力,Ni 元素增加钢材的韧性和 化学稳定性,Ti 元素可增加钢材抗 晶间腐蚀能力。
空冷管束材质由 20# 碳钢更新 为抗硫化氢及氯化氢应力腐蚀开裂 能力较强的 08Cr2AlMo,并且其硬 度较低(HB 不大于 150),具有良好 的可焊性和制造性能。
重整预加氢腐蚀与防腐问题的探讨
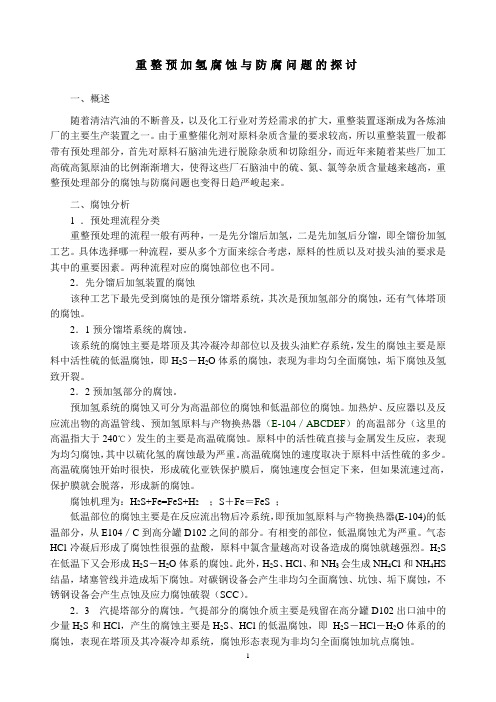
重整预加氢腐蚀与防腐问题的探讨一、概述随着清洁汽油的不断普及,以及化工行业对芳烃需求的扩大,重整装置逐渐成为各炼油厂的主要生产装置之一。
由于重整催化剂对原料杂质含量的要求较高,所以重整装置一般都带有预处理部分,首先对原料石脑油先进行脱除杂质和切除组分,而近年来随着某些厂加工高硫高氮原油的比例渐渐增大,使得这些厂石脑油中的硫、氮、氯等杂质含量越来越高,重整预处理部分的腐蚀与防腐问题也变得日趋严峻起来。
二、腐蚀分析1 .预处理流程分类重整预处理的流程一般有两种,一是先分馏后加氢,二是先加氢后分馏,即全馏份加氢工艺。
具体选择哪一种流程,要从多个方面来综合考虑,原料的性质以及对拔头油的要求是其中的重要因素。
两种流程对应的腐蚀部位也不同。
2.先分馏后加氢装置的腐蚀该种工艺下最先受到腐蚀的是预分馏塔系统,其次是预加氢部分的腐蚀,还有气体塔顶的腐蚀。
2.1预分馏塔系统的腐蚀。
该系统的腐蚀主要是塔顶及其冷凝冷却部位以及拔头油贮存系统,发生的腐蚀主要是原料中活性硫的低温腐蚀,即H2S-H2O体系的腐蚀,表现为非均匀全面腐蚀,垢下腐蚀及氢致开裂。
2.2预加氢部分的腐蚀。
预加氢系统的腐蚀又可分为高温部位的腐蚀和低温部位的腐蚀。
加热炉、反应器以及反应流出物的高温管线、预加氢原料与产物换热器(E-104/ABCDEF)的高温部分(这里的高温指大于240℃)发生的主要是高温硫腐蚀。
原料中的活性硫直接与金属发生反应,表现为均匀腐蚀,其中以硫化氢的腐蚀最为严重。
高温硫腐蚀的速度取决于原料中活性硫的多少。
高温硫腐蚀开始时很快,形成硫化亚铁保护膜后,腐蚀速度会恒定下来,但如果流速过高,保护膜就会脱落,形成新的腐蚀。
腐蚀机理为:H2S+Fe=FeS+H2;S+Fe=FeS ;低温部位的腐蚀主要是在反应流出物后冷系统,即预加氢原料与产物换热器(E-104)的低温部分,从E104/C到高分罐D102之间的部分。
有相变的部位,低温腐蚀尤为严重。
- 1、下载文档前请自行甄别文档内容的完整性,平台不提供额外的编辑、内容补充、找答案等附加服务。
- 2、"仅部分预览"的文档,不可在线预览部分如存在完整性等问题,可反馈申请退款(可完整预览的文档不适用该条件!)。
- 3、如文档侵犯您的权益,请联系客服反馈,我们会尽快为您处理(人工客服工作时间:9:00-18:30)。
硫化氢汽提塔腐蚀分析与应对措施
摘要:渣油加氢装置汽提塔属于装置硫化氢浓度最高的设备,汽提塔顶气主
要组成是轻烃和硫化氢,轻烃中携带少量氨,高浓度硫化氢和氨环境中的设备,
随着使用时间的延长,极易出现老化,腐蚀的概率会逐渐增大,设备腐蚀如果发
生泄漏,将直接影响安全生产,泄漏出的硫化氢、轻烃等会导致人员中毒和设备
着火爆炸等事故。
关键词:汽提塔高浓度硫化氢轻烃中毒腐蚀
1.设备概述
某公司渣油加氢装置采用CLG公司的上流式+固定床渣油加氢脱硫工艺技术,以哈萨克斯坦、南疆及北疆原油的减压重蜡油和减压渣油为原料,分为反应和分
馏系统,反应系统为两个系列,采用单开单停设计,分馏部分采用主汽提塔+分
馏塔流程,在汽提塔除去轻烃和硫化氢,降低分馏塔材质要求。
2.腐蚀原因分析
2.1汽提塔铵盐结晶造成的垢下腐蚀。
目前本装置汽提塔顶温度的控制指标
是130-180℃,汽提塔顶气主要组成是轻烃和硫化氢,轻烃中携带部分氨,会发
生如下反应:
NH3+H2S——NH4HS
硫氢化铵的结晶温度在150℃左右,正好和塔顶操作温度一致,因而流出物
在塔顶空冷器内被冷却过程中,容易在汽提塔顶挥发性线及后路设备形成铵盐结晶,沉积后结垢,引起垢下腐蚀,进而形成腐蚀穿孔,造成汽提塔顶空冷器泄漏。
2017年6月26日,渣油装置汽提塔顶空冷器EA-3003泄漏,两系列停工至退守
状态,装置停工检修。
2017年11月22日,发现渣油装置汽提塔顶空冷器EA-3003泄漏,23日工艺降低汽提塔顶操作压力,带压堵漏,堵漏后没有泄漏。
2.2管道弯头处冲刷腐蚀。
影响此形式腐蚀的主要因素有:①氨和硫化氢的
浓度,浓度越大,腐蚀越严重;②管内流体的流速,流速越高,腐蚀趋剧烈。
根
据对汽提塔顶介质和操作工艺的分析,在目前塔顶压力下,可以判断塔顶气相流
动速度确实很高,在弯道部分会直接发生冲刷,造成管道的冲刷腐蚀。
2020年11月2日,测定EA3001出口西侧第一个回弯头减薄至2.4mm,不利
于装置安全生产,需要隔离EA3001西侧空冷更换减薄处管线。
2.3 H2S-NH3-H20型腐蚀。
第一,汽提塔C-3001采用气体蒸汽进行气体,操
作不稳定时,难免会有水分带至塔顶;第二,反应系统由于操作原因,也会带水
至汽提塔,当汽提塔顶有NH4HS存在时,就能发生H2S-NH3-H20型腐蚀。
这种腐
蚀的区域一般在高流速或湍流区及死角的部位,发生的温度范围在38~204℃之间,正好是气体塔空冷器的温度区间。
2.4当系统中有水、酸性化合物等存在时,极易发生湿硫化氢,其中以水的
影响尤其严重。
根据国家质量技术监督局1999年颁发的《压力容器安全技术监
察规定》中对湿硫化氢应力腐蚀环境的定义,结合本装置汽提塔的特性,分析得
出在汽提塔顶发生的反应形式为湿硫化氢腐蚀中的均匀腐蚀。
它由电化学腐蚀引
起的表面腐蚀,使设备壳壁均匀减薄。
电化学腐蚀和反应产生的氢原子扩散至钢
中引起的。
机理如下:
H2S H++HS-
HS- H++S2-
Fe Fe2++2e(阳极反应)
Fe2++S2- FeS
Fe2++HS- FeS +H+
2H++2e 2H
H2 (阴极反应)
向钢中扩散
根据平时的化验分析数据得知,汽提塔顶硫化氢含量经常高至20000mg/L以上,高浓度的硫化氢很容易造成设备腐蚀。
3.解决方法
3.1针对由H2S引起设备腐蚀,根据实验,NH3和H2S的摩尔浓度的乘
积>0.04%或<0.01%腐蚀性都较大,只有在0.01%~0.04%范围内腐蚀性较小,
所以在操作中,最好把NH3和H2S浓度的乘积的百分比控制在0.01~0.04%之间。
一般易发生腐蚀部位是形成湍流区弯头等处,若有Cl-及氧气的存在,会加
速腐蚀。
腐蚀的速度与介质的流速也有关系,速度过慢,腐蚀介质易集存加剧腐蚀;流速过快,冲刷与NH4HS共同作用腐蚀也会加剧。
因此要选择合适的流速而
且一定要避免偏流,在投用时就应注意。
碳钢内介质流速为4.3~6.1m/s。
下面
是高压空冷发生腐蚀的条件:
摩尔浓度[H2S]·[NH3]<0.07,不会发生腐蚀
当介于0.07~0.2之间时也能出现腐蚀
当大于0.5时,肯定发生腐蚀
高分酸性水中NH4HS浓度≯4%,出现腐蚀的可能性较小。
对于在高温部位注软化水,在保证注水量足够的前提下要保证总注水量的20%在该部位为液态。
高压空冷一般选用16MnR(HIC)或碳钢,碳钢使用温度应<200℃,不然会发生氢腐蚀(纳尔逊曲线)。
根据以上腐蚀原理,本公司渣油加氢装置正在进行气体塔顶系统注水的技改,并在近期完成投用。
3.2防止高温硫化氢腐蚀办法有:①控制循环气中硫化氢浓度,不要超过规
定范围;②选用抗硫化氢腐蚀的钢材或采取防腐措施,如用不锈钢金属衬里或用
渗铝钢等。
防止湿硫化氢腐蚀的措施有:对介质中硫化氢含量较低、腐蚀不太严重的,
往往采用普通碳素钢,适当加大腐蚀裕度量,并在制造程序上加入消除应力的焊
后热处理。
对腐蚀性中等的场合,可选用抗HIC的钢材,国外应用最为普遍的是SA516-Gr.65,70(HIC)(与16MnR相似)。
3.3加注缓蚀剂。
所谓缓蚀剂,就是添加少量药剂到腐蚀介质中,能够显著
减缓金属腐蚀速度的物质。
缓蚀剂可以吸附在金属表面上,形成单分子抗水性保
护层,多数缓蚀剂带有含氧、硫等原子的官能团,这些极性官能团吸附在金属表面,形成单分子保护膜,极性官能团和金属原子借它们之间的电子对结合,而缓
蚀剂分子中的羟基覆盖在金属表面则形成分子膜的外层,将金属和腐蚀性水相隔
离开来,避免了金属表面与酸性介质接触,同时能部分中和流体中的酸性物质,
调节流体的酸度,达到保护金属的目的。
由于分馏系统存在H2S等活性硫对设备具有腐蚀作用,为了防止腐蚀的发生,保护设备,本装置在汽提塔顶设置了缓蚀剂加注流程,由上游加氢裂化装置统一
调和后送至塔顶,加注过程严格按照工艺指标,达到保护设备的需求。
3.4材质升级。
随着设备长时间使用后,它的使用寿命明显下降,设备材质
的消耗增大,抗防腐蚀性能减弱,一些相对薄弱的部位就会发生腐蚀,导致高浓
度的硫化氢发生泄漏。
这些问题基本上都是无法避免的,只能通过科研手段,逐
渐的升级材质,或者在保证安全和成本的基础上,增加维修频率和更换频率,彻
底消除设备故障带来的隐患,本装置通过分析研判,2018年大检修期间,对汽提
塔顶空冷器进行更换。
3.5工艺改造。
由于由于汽提塔顶空冷器EA-3003硫化氢含量非常高,设备
的腐蚀是很难避免,尤其是长周期运行,为了保证效益,减少了检修频率,腐蚀
程度、疲劳程度会更加严重,导致高浓度的硫化氢发生泄漏。
因此,从补救方向
出发,如果设备存在泄漏,怎样把风险降到最低,在最低的时间控制事态的扩大,
2020年本装置在汽提塔顶空冷器EA-3003出入口增加手阀,在设备发生泄漏时,
能够第一时间切除该设备,并进行放空,氮气置换,置换合格后进行检修,对泄
漏空冷管束封堵,这样操作,检修时间短,不会影响装置正常生产,不会留下隐患。
参考文献:
[1] 古华山,徐胜,崔志峰,等.硫化氢汽提塔腐蚀检查与腐蚀分析[J].石油化工腐蚀与防护,2019,36(2):9-12.
[2] 陈洪刚.加氢精制装置湿硫化氢腐蚀与防护[J].石油化工腐蚀与防护,2009,26(4):19-21.。