【文献综述】流化床操作参数优化的研究进展
流化床煤气化技术的分析研究进展

流化床煤气化技术的研究进展煤气化技术有多种分类法,按煤的进料状态可分为干块进料、干粉进料和煤浆进料。
煤层中燃料运动状态,可分为固定床<亦称移动床)、流化床、气流床和熔融床. 按床层压力等级,可分为低压< < 0.3MPa)、中压<0.3 MPa ~4.5 MPa)和高压< > 4.5MPa)。
按排渣状态,可分为干法<固态)、熔聚和熔渣<液态)。
目前,应用较广泛的煤气化技术有如下几种:1)加压固定床气化技术加压鲁奇炉是典型的加压固定床气化技术,技术成熟,能利用高灰分煤,并且能在2.41 MPa 压力下运行,适合合成液体燃料合成所需要的操作压力,可节约投资和能耗,但过程中产生大量的焦油和酚。
为克服上述缺点,又进行了新的开发,主要技术升级包括进一步提高压力、提高温度和两段引气。
2)流化床气化技术温克勒气化工艺是典型的流化床技术,最早用于工业生产,第一台工业生产装置于1926 年投入运行。
这种炉型存在严重的缺陷,只能利用高活性褐煤,排灰含碳多,飞灰带出碳损失严重,致使碳利用率降低。
针对这些问题开发了新的流化床技术,如高温温克勒<HTW)、灰熔聚气化<KRW ,U-gas)和循环流化床气化工艺。
3)水煤浆气流床气化技术水煤浆气流床气化又称湿法进料气流床气化,其中Texaco 炉是一种率先实现工业化的水煤浆气流床气化技术,其进料方式简单,工程问题较少,具有大的气化能力,可以实现高压力<8 MPa ~ 10MPa)操作。
但冷煤气效率较低,氧耗较高。
为了降低过程氧耗,提高冷煤气效率,在Texaco 气化技术基础上发展了两段进煤煤气化工艺。
4)干粉进料气流床气化技术干粉进料气流床气化技术相对湿法进料具有氧耗低,煤种适应广和冷煤气效率高等优点. 其代表技术有Shell,Prenflo 和日立气流床等。
Shell SCGP 工艺是在K-T炉的基础上所开发的加压K-T气化炉。
流化床换热技术在合成氨反应中应用与优化
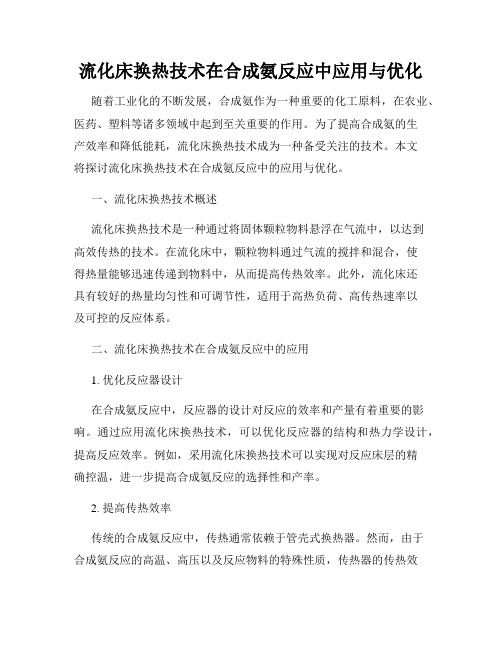
流化床换热技术在合成氨反应中应用与优化随着工业化的不断发展,合成氨作为一种重要的化工原料,在农业、医药、塑料等诸多领域中起到至关重要的作用。
为了提高合成氨的生产效率和降低能耗,流化床换热技术成为一种备受关注的技术。
本文将探讨流化床换热技术在合成氨反应中的应用与优化。
一、流化床换热技术概述流化床换热技术是一种通过将固体颗粒物料悬浮在气流中,以达到高效传热的技术。
在流化床中,颗粒物料通过气流的搅拌和混合,使得热量能够迅速传递到物料中,从而提高传热效率。
此外,流化床还具有较好的热量均匀性和可调节性,适用于高热负荷、高传热速率以及可控的反应体系。
二、流化床换热技术在合成氨反应中的应用1. 优化反应器设计在合成氨反应中,反应器的设计对反应的效率和产量有着重要的影响。
通过应用流化床换热技术,可以优化反应器的结构和热力学设计,提高反应效率。
例如,采用流化床换热技术可以实现对反应床层的精确控温,进一步提高合成氨反应的选择性和产率。
2. 提高传热效率传统的合成氨反应中,传热通常依赖于管壳式换热器。
然而,由于合成氨反应的高温、高压以及反应物料的特殊性质,传热器的传热效率存在一定的局限性。
而采用流化床换热技术,可以提高传热效率,有效减少热负荷损失,降低了能源的消耗。
3. 减少热点和局部温差传统的合成氨反应中,热点和局部温差是常见的问题,会导致反应不均匀和产物选择性下降。
流化床换热技术通过悬浮颗粒物料的自身运动性质,使得热量能够更加均匀地传递到反应系统中,有效减少了热点和局部温差的问题,提高了反应的均匀性和产物的选择性。
三、流化床换热技术在合成氨反应中的优化1. 优化颗粒物料的选择合成氨反应中,选择合适的颗粒物料对流化床换热技术的运行效果有着重要的影响。
颗粒物料的大小和形状可以影响颗粒床的流动性和气固传热效果。
因此,在优化合成氨反应中的流化床换热技术时,应充分考虑颗粒物料的选择。
2. 优化气体流速流化床换热技术中的气体流速对传热效果有着重要的影响。
2024年流化床技术市场发展现状

2024年流化床技术市场发展现状引言流化床技术是一种常见的固体颗粒与气态流体接触的传质传热方式。
近年来,随着工业化进程的快速推进,流化床技术在多个领域中得到了广泛应用。
本文将对流化床技术在市场上的发展现状进行探讨,并分析其潜在的发展前景。
1. 流化床技术的概述流化床技术是一种通过将固体颗粒置于气态流体中,通过调节气流使固体颗粒呈现流动状态的传质传热方式。
流化床技术具有高传质传热效率、均匀性好、操作灵活等优点,因此被广泛应用于化工、能源、环境保护等领域。
2. 流化床技术在化工行业的应用2.1 催化剂反应流化床技术在催化剂反应中具有重要作用。
通过控制流化床内的气体流速和温度等参数,可以实现反应过程的高效进行,并提高产品的选择性和收率。
2.2 固体颗粒干燥由于流化床技术可以提供大面积的固体颗粒与气流的接触,因此在固体颗粒干燥领域有着广泛的应用前景。
流化床干燥可以提高干燥速度和均匀性,并降低能耗。
2.3 固体颗粒的冷却流化床技术在固体颗粒冷却领域也有着广泛的应用。
通过控制冷却介质的温度和流速,可以实现对固体颗粒的快速冷却,并满足不同颗粒的冷却要求。
3. 流化床技术在能源领域的应用3.1 燃烧技术流化床技术在煤炭、生物质等能源的燃烧领域有着广泛的应用。
通过调节气体流速和温度,可以实现燃料的高效燃烧,并降低氮氧化物等污染物的排放。
3.2 气化技术流化床技术在煤炭、生物质气化领域也有着重要作用。
通过控制气化介质的温度和流速,可以实现固体燃料的高效气化,生产合成气等高附加值产品。
3.3 燃气脱硫流化床技术在燃气脱硫过程中具有独特的优势。
通过将固体吸附剂引入流化床中,可以实现燃气中硫化物的高效去除,并减少对环境的污染。
4. 流化床技术市场的现状与前景当前,流化床技术在化工、能源等领域中已经取得了显著的应用成果。
然而,与发达国家相比,我国在流化床技术的研发和应用方面仍存在一定差距。
随着国家对环境保护和高效能源的要求越来越高,流化床技术市场具有广阔的发展前景。
生物质流化床气化技术应用研究现状

生物质流化床气化技术应用研究现状随着能源危机的不断加剧和环保意识的增强,生物质成为可再生能源的重要来源之一。
而生物质流化床气化技术作为一种高效利用生物质的能源转化技术,在国内外得到了广泛的应用和研究。
本文就生物质流化床气化技术的应用研究现状进行探讨。
一、生物质流化床气化技术概述生物质流化床气化技术是利用流化床反应器对生物质进行气化反应,使其转化为气体燃料的一种技术。
在流化床内,生物质颗粒被高速气流悬浮并与气体直接接触,因此可以在较低的反应温度下实现生物质的完全气化。
同时,流化床内部的湍流和固体与气体之间的热和质量传递可以进一步提高反应效率。
生物质流化床气化技术具有以下优点:1、资源丰富、可持续。
生物质是可再生资源,来源广泛,包括木材、农作物秸秆、林木剩余物、木薯渣等等。
2、环保效益好。
与传统能源相比,生物质气化产生的二氧化碳排放量低,可以减少对环境的污染。
3、经济效益明显。
生物质气化技术可以实现生物质的高效利用,产生的气体燃料可以替代传统的能源,对于推动节能减排、环境友好的经济模式具有积极的意义。
二、生物质流化床气化技术的应用研究现状1、研究进展在国内外,生物质流化床气化技术得到了广泛应用和研究。
研究人员通过实验室试验和大规模试验,对生物质气化反应的反应温度、反应压力、流化床粒径、生物质种类等参数展开了研究。
在反应温度方面,过高或过低的温度都会导致反应效率的降低。
研究表明,适宜的反应温度一般在800℃-900℃之间。
在生物质种类方面,各种不同的生物质具有不同的物理和化学性质,因此生物质流化床气化反应的效率受到生物质种类的影响。
研究表明,木材和秸秆等较为常见的生物质可以被有效气化。
2、应用场景生物质流化床气化技术在电力、燃气、化工等多个行业中得到了应用。
其中,电力是生物质流化床气化技术的主要应用领域。
在电力领域,生物质流化床气化技术已经得到了广泛的应用。
利用生物质气化产生的气体燃料发电可以替代传统的化石燃料发电,具有环保节能的优势。
流化床换热技术在氨气合成反应中应用与优化
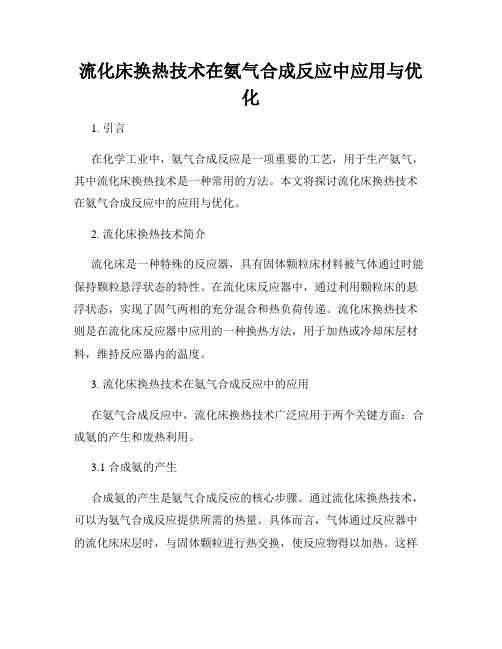
流化床换热技术在氨气合成反应中应用与优化1. 引言在化学工业中,氨气合成反应是一项重要的工艺,用于生产氨气,其中流化床换热技术是一种常用的方法。
本文将探讨流化床换热技术在氨气合成反应中的应用与优化。
2. 流化床换热技术简介流化床是一种特殊的反应器,具有固体颗粒床材料被气体通过时能保持颗粒悬浮状态的特性。
在流化床反应器中,通过利用颗粒床的悬浮状态,实现了固气两相的充分混合和热负荷传递。
流化床换热技术则是在流化床反应器中应用的一种换热方法,用于加热或冷却床层材料,维持反应器内的温度。
3. 流化床换热技术在氨气合成反应中的应用在氨气合成反应中,流化床换热技术广泛应用于两个关键方面:合成氨的产生和废热利用。
3.1 合成氨的产生合成氨的产生是氨气合成反应的核心步骤。
通过流化床换热技术,可以为氨气合成反应提供所需的热量。
具体而言,气体通过反应器中的流化床床层时,与固体颗粒进行热交换,使反应物得以加热。
这样一来,反应物在流化床内得到充分混合和加热,有利于催化剂的活性提高和反应速率的增加,从而提高氨气合成的效率。
3.2 废热利用氨气合成反应产生的副产物中含有大量的废热。
通过流化床换热技术,这些废热可以被回收并利用。
在反应器底部或侧面设置换热器,将流化床床层中产生的废热传递给其他需要加热的介质,如蒸汽产生装置。
这样做不仅可以提高热能利用效率,还可以减少能源消耗,降低生产成本。
4. 流化床换热技术的优化为了充分发挥流化床换热技术的优势,需要进行一系列的优化措施。
4.1 催化剂选择选择合适的催化剂对于流化床换热技术的应用至关重要。
催化剂应具有高催化活性、较长的寿命和良好的热稳定性。
此外,催化剂还应具备较低的阻力,以保证气体在流化床内的流动性能。
4.2 进料气体的控制进料气体的控制对于氨气合成反应及流化床换热技术的稳定运行非常重要。
合理调节进料气体的流量、压力和温度,可以确保反应器内的气固两相保持较好的分布和热负荷传递效果。
流化床参数
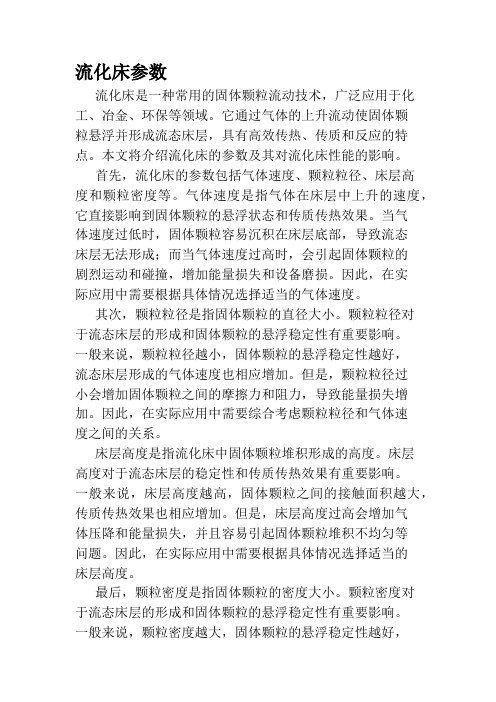
流化床参数流化床是一种常用的固体颗粒流动技术,广泛应用于化工、冶金、环保等领域。
它通过气体的上升流动使固体颗粒悬浮并形成流态床层,具有高效传热、传质和反应的特点。
本文将介绍流化床的参数及其对流化床性能的影响。
首先,流化床的参数包括气体速度、颗粒粒径、床层高度和颗粒密度等。
气体速度是指气体在床层中上升的速度,它直接影响到固体颗粒的悬浮状态和传质传热效果。
当气体速度过低时,固体颗粒容易沉积在床层底部,导致流态床层无法形成;而当气体速度过高时,会引起固体颗粒的剧烈运动和碰撞,增加能量损失和设备磨损。
因此,在实际应用中需要根据具体情况选择适当的气体速度。
其次,颗粒粒径是指固体颗粒的直径大小。
颗粒粒径对于流态床层的形成和固体颗粒的悬浮稳定性有重要影响。
一般来说,颗粒粒径越小,固体颗粒的悬浮稳定性越好,流态床层形成的气体速度也相应增加。
但是,颗粒粒径过小会增加固体颗粒之间的摩擦力和阻力,导致能量损失增加。
因此,在实际应用中需要综合考虑颗粒粒径和气体速度之间的关系。
床层高度是指流化床中固体颗粒堆积形成的高度。
床层高度对于流态床层的稳定性和传质传热效果有重要影响。
一般来说,床层高度越高,固体颗粒之间的接触面积越大,传质传热效果也相应增加。
但是,床层高度过高会增加气体压降和能量损失,并且容易引起固体颗粒堆积不均匀等问题。
因此,在实际应用中需要根据具体情况选择适当的床层高度。
最后,颗粒密度是指固体颗粒的密度大小。
颗粒密度对于流态床层的形成和固体颗粒的悬浮稳定性有重要影响。
一般来说,颗粒密度越大,固体颗粒的悬浮稳定性越好,流态床层形成的气体速度也相应增加。
但是,颗粒密度过大会增加固体颗粒之间的摩擦力和阻力,导致能量损失增加。
因此,在实际应用中需要综合考虑颗粒密度和气体速度之间的关系。
综上所述,流化床参数包括气体速度、颗粒粒径、床层高度和颗粒密度等,它们对于流化床性能有重要影响。
在实际应用中需要根据具体情况选择适当的参数组合,以达到高效传热、传质和反应的目标。
循环流化床锅炉的特点及其运行中的优化调整

循环流化床锅炉的特点及其运行中的优化调整摘要循环流化床锅炉作为一种相对新兴的炉型具有常规的锅炉无法相比的优势和突出的特点,结合循环流化床锅炉的特点和燃烧、传热特性,对于充分发挥其优势,提高运行的经济性尤为重要。
关键词循环流化床锅炉燃烧和传热运行优化调整一、循环流化床锅炉的特点(1)燃料适应性广,几乎可以燃烧各种煤,这对充分利用劣质燃料具有重大意义。
(2)环保效益突出,低污染—由于该炉系中温[(850-900)℃]燃烧和分级送风[二次风率(40%~50%)],在这种状况下非常有利于炉内脱硫和抑制氮氧化物(N0x)。
脱硫剂随固体物料多次循环,所以具有较高的脱硫效率(Ca/S比为2时,脱硫效率可达90%),使烟气中的S02和N0x的排放量很低,环保效益显著。
(3)负荷调节性能好,循环流化床锅炉比常规锅炉负荷调节幅度大得多,一般在30-110%,这一特点非常适应热负荷变化较大的热电厂。
(4)燃烧强度大和传热能力强—由于未燃烬碳粒随固体物料的多次循环,使飞灰含碳量下降,保证了燃烧效率高,可与煤粉炉媲美。
(5) 造价相对便宜,由于燃烧热强度大,循环流化床锅炉可以减少炉膛体积,降低金属消耗。
(6)灰渣综合利用性能好,炉内燃烧温度低,灰渣不会软化和粘结,活性较好,可以用于制造水泥的掺合料或其它建筑材料,有利于综合利用。
(7)存在着磨损、风帽损坏快、自动化水平要求高、理论和技术尚不成熟,运行方面还没有成熟的经验。
二、循环流化床锅炉的燃烧和传热特性(一)燃烧特性(1)循环流化床锅炉燃烧技术最大特点是通过物料循环系统在炉内循环反复燃烧和中温燃烧。
循环流化床燃烧时由于流化速度较快,绝大多数的固体颗粒被烟气带出炉膛,在炉膛出口处的分离器将固体颗粒分离下来并经过反料器送回炉床内再燃烧,如此反复循环,就形成了循环流化床。
由于循环燃烧使燃料颗粒在炉内的停留时间大大增加,直至燃尽,流态化的燃烧是以高扰动、固体粒子强烈混合以及没有固定床面和物料循环系统为其特征,被烟气携带床料经气固分离器后,返回床内继续燃烧。
循环流化床锅炉床温控制优化分析

循环流化床锅炉床温控制优化分析循环流化床锅炉是一种常用的燃煤锅炉,其具有结构紧凑、效率高、烟气污染少等优点。
而循环流化床锅炉床温的控制是循环流化床锅炉运行的关键之一,对于提高锅炉的热效率和节能减排具有重要作用。
因此,对循环流化床锅炉床温控制进行优化分析是非常必要的。
1.温度传感器的选择:选择合适的温度传感器对床温的测量至关重要。
常用的温度传感器有热电偶和热电阻,它们的测量精度和响应速度不同,需要根据实际情况选择合适的传感器。
2.建立床温模型:通过建立循环流化床锅炉的床温模型,可以对床温的变化进行预测和优化。
模型可以基于物理原理建立,也可以通过机器学习等方法进行建模。
床温模型的建立可以使用实际运行数据进行参数拟合,提高模型的准确性。
3.控制策略的选择:循环流化床锅炉床温的控制可采用PID控制、模糊控制、模型预测控制等多种控制策略。
不同的控制策略适用于不同的应用场景,需要根据实际情况选择合适的控制策略。
4.优化算法的应用:对于循环流化床锅炉床温控制,可以引入优化算法来实现最优化控制。
例如,可以使用遗传算法、粒子群优化算法等来寻找最优的控制参数,进一步提高床温的控制效果。
5.模拟仿真和实验验证:对于循环流化床锅炉床温控制的优化分析,可以通过模拟仿真和实验验证来评估不同的控制策略和优化算法的效果。
通过比较不同方案的性能指标,选择最优的控制策略和优化算法。
总结来说,循环流化床锅炉床温的控制优化分析是一个复杂的问题,需要综合考虑床温传感器的选择、床温模型的建立、控制策略的选择、优化算法的应用等多个因素。
通过优化分析,可以提高循环流化床锅炉的热效率和节能减排效果,实现可持续发展。
- 1、下载文档前请自行甄别文档内容的完整性,平台不提供额外的编辑、内容补充、找答案等附加服务。
- 2、"仅部分预览"的文档,不可在线预览部分如存在完整性等问题,可反馈申请退款(可完整预览的文档不适用该条件!)。
- 3、如文档侵犯您的权益,请联系客服反馈,我们会尽快为您处理(人工客服工作时间:9:00-18:30)。
文献综述高分子材料与工程流化床操作参数优化的研究进展1 引言在一个超微气流粉碎设备,将颗粒物料堆放好,当气体由设备下部通入床层,当气流速度加大到某种程度,固体颗粒在床层内就会产生沸腾状态,这种床层称为流化床。
流体向上流过一个微细颗粒的床层(塔体),当流速低的时候流体只是穿过静止的颗粒之间的空隙,此时的床体称为固定床;随着流速的增加,颗粒互相离开,并可在向上流动的气体或者液体中,此时的床层就是流化床起点。
简单的说固体颗粒在流体作用下表现出类似流体状态的现象称为流态化。
本实验是研究模拟流化床状态,考察流化状态的中影响因素看到少量的颗粒在一定的区间进行震动和游动,称为膨胀床;速度再升高达到使全部颗粒都刚好悬浮。
当流体(气体)通过床层的速度逐渐提高到某值时,颗粒出现松动,颗粒间空隙增大,床层体积出现膨胀。
如果再进一步提高流体速度,床层将不能维持固定状态。
此时,颗粒全部悬浮与流体中,显示出相当不规则的运动。
随着流速的提高,颗粒的运动愈加剧烈,床层的膨胀也随之增大,但是颗粒仍逗留在床层内而不被流体带出。
床层的这种状态和液体相似称为流化床。
在气固流态化过程中 ,气流量、压差、静床层高度、分布板参数的不同对反应装置内气固接触、传热、传质都有重要影响 ,并且直接关系到反应器的生产能力。
在过去的几十年中 ,气固流化床聚合技术取得了巨大的工业成功,而这种反应器存在着不容忽视的缺点—--传热能力差 ,使得反应器内部容易结块 ,从而严重制约了流化床反应器的稳定生产。
对于气固流化床 ,颗粒的粒度和密度以及气体的密度之差对流化特性有显著影响。
研究不同颗粒体系的流动模式和流化状况,对工业反应器的设计和优化优化工艺参数具有重要意义 ,也是流态化领域研究的重要课题。
目前,文献中提及的检测流化床流型的方法主要有压力脉动法、核磁共振(MRI)法、激光法和光纤法等,但这些方法也存在一定的局限,如压力脉动法存在准确度不高,对流场造成影响的缺点;MRI 法则不适用于工业上铁制的置,限制了其在实际生产中的应用;激光法由于需要向体系内掺入示踪荧光粒子,导致流化床内物料系统的变化,对生产造成影响,从而无法在工业流化床反应器上使用;而光纤法则需要将光纤探头插入流化床中,对床内的流动形态产生影响,也无法应用于工业生产。
完善流化床的操作参数研究,寻找一种快捷有效、能适用于工业环境并可实时在线检测流型及流化状况的方法对工业生产的优化和安全监控具有重要意义。
2 理想流化床与实际流化床理想流化床:在理想情况下,流体通过颗粒床层时,克服流体阻力产生的压降与空塔气速之间的关系如图(1-1) 所示,大致可分为以下几个阶段:图1-1 理想流化床Δp-u关系曲线a.固定床阶段:此时气速较低,床层静止不动,气体通过床层的空隙流动,随气速的增加,气体通过床层的摩擦阻力也相应增加。
如图1-1中AB段所示。
b.流化床阶段:当流速继续增大超过C点时,床层开始松动,颗粒重排,床层空隙率增大,逐渐地颗粒开始悬浮在流体中自由运动,床层的高度亦随气速的提高而增高,但整个床层的压力降仍保持不变,仍然等于单位面积的床层净重力。
流态化阶段的△p与u的关系如图1-1中CD段所示。
当降低流化床气速时,床层高度、空隙率也随之降低,△p -u关系曲线沿DCA’返回。
这是由于从流化床阶段进入固定床阶段时,床层由于曾被吹松,其空隙率比相同气速下未被吹松的固定床要大,因此,相应的压降会小一些。
与C点对应的流速称为临界流化速度umf,它是最小流化速度。
相应的床层空隙率称为临界空隙率emf。
流化阶段中床层的压力降,可根据颗粒与流体间的摩擦力恰与其净重力平衡的关系求出,即△p=L mf(1-εmf)(ρs-ρ)g式1式中Lmf――开始流化时床层的高度。
随着流速的增大,床层高度和空隙率e都增加,而Δp 维持不变,压降不随气速改变而变化是流化床的一个重要特征。
根据这一特点,可通过测定床层压降来判断流化质量优劣。
整个流化床阶段的压力降为△p=L(1-ε)(ρs-ρ)g式2在气固系统中,r与rs相比较小可以忽略。
c.气流输送阶段在此阶段,气流中颗粒浓度降低,由浓相变为稀相,使压力降变小,并呈现出复杂的流动情况。
实际流化床:实际流化床的情况比较复杂,其Δp-u关系曲线如图(1-2)所示。
它与理想流化床Δp-u曲线的主要区别是:图1-2气体实际流化床Δp-u关系曲线a.在固定床区域AB和流化床区域DB之间有一个“驼峰”BCD,这是因为固定床的颗粒间相互挤压,需要较大的推动力才能使床层松动,直至颗粒达到悬浮状态时,压降Δp便从“驼峰”段降到水平段DC′段,此后降基本不随气速而变,最初的床层愈紧密,“驼峰”段越陡峭。
b.由于流化床阶段Δp保持不变,压降线DE应为水平线,而实际流化床中DE线右端略微向上倾斜。
这是由于气体通过床层时的压强降除绝大部分用于平衡床层颗粒的重力外,还有很少一部分能量消耗于颗粒之间的碰撞及颗粒容器壁之间的摩擦。
c.在图1-2中还可见到DE线的上下各有一条虚线,这是气体流化床压力降的波动范围,而DE 线是这两条线的平均值。
在气泡运动、长大、破裂的过程中产生压力降的波动。
d.图1-2中EDC′(流化床阶段)C′A′(固定床)阶段的交点C′即为临界点,该点所对应的流速为临界流化速度umf,空隙率称为临界空隙率emf,其值比没有流化过的原始流化床的空隙率要稍大一些。
3 实际气-固流化床中的问题对于密度差较大的气-固流化系统,一般趋向于形成聚式流化。
在气-固系统的流化床中,超过流化所需最小气量的那部分气体以气泡形式通过颗粒层,上升至床层上界面时破裂,这些气泡内可能夹带有少量固体颗粒。
此时床层内分为两相,一相是空隙小而固体浓度大的气固均匀混合物构成的连续相,称为乳化相;另一相则是夹带有少量固体颗粒而以气泡形式通过床层的不连续相,称为气泡相。
由于气泡在床层中上升时逐渐长大、合并,至床层上界面处破裂,因此,床层极不稳定,上界面亦以某种频率上下波动,床层压降也随之相应波动。
而聚式流化床中,空穴相和乳化相的存在,将会导致气流的不均匀分布和气固相接触不良,对传热、传质和化学反应不利,并且可能引发床层的如下不正常现象。
腾涌现象:腾涌现象主要出现在气-固流化床中。
若床层高度与直径之比值过大,或气速过高,或气体分布不均时,会发生气泡合并现象。
当气泡直径长到与床层直径相等时,气泡将床层分为几段,形成相互间隔的气泡层与颗粒层。
颗粒层被气泡推着向上运动,到达上部后气泡突然破裂,颗粒则分散落下,这种现象称为腾涌现象。
出现腾涌时,Δp-u曲线上表现为Δp在理论值附近大幅度的波动。
这是因为气泡向上推动颗粒层时,颗粒与器壁的摩擦造成压降大于理论值,而气泡破裂时压降又低于理论值。
如图1-3所示。
图1-3 腾涌发生后Δp-u的关系流化床发生腾涌时,不仅使气-固接触不均,颗粒对器壁的磨损加剧,而且引起设备振动,甚至损坏设备。
沟流现象:沟流现象是指气体通过床层时形成短路,大部分气体穿过沟道上升,没有与固体颗粒很好地接触。
故在Δp-u图上表现为低于单位床层面积上的重力,如图1-4所示。
图1-4 沟流发生后Δp-u的关系沟流现象的出现主要与颗粒的特性和气体分布板的结构有关。
粒度过细、密度大、易于粘连的颗粒,以及气体在分布板处的初始分布不均,都容易引起沟流。
一旦发生沟流,部分床层就变成了死床,颗粒无法与气流接触,这将导致实际生产效率大大减小,同时造成大量原理的浪费。
4 小结为了在实际生产中减少和避免上述现象发生,模拟流化床越来越受到人们的重视。
在实际生产前,通过模拟流化床装置,得到优化后的操作参数,可以大大减少甚至避免上述现象的发生,从而减少生产成本,提高生产效率,为企业带来巨大效益。
参考文献[1] 沈志恒,陈巨辉等.高固体流率循环流化床内气体–颗粒团聚物流动特性[J]. 中国电机工程学报:2009;29(29):25-29.[2] 李海红, 王利红,申兰芹.磁铁矿生物流化床操作参数的优化[J].河北工程大学学报:2007;3(24):23-25.[3] 洪若瑜,李洪钟等.基于双流体模型的流化床模拟[J].化工学报,1995;3(46):349-356.[4] 邓俊,朱学军等.宽粒度分布颗粒临界流化特性研究[J].化学工程与装备,2008;4:5-7.[5] 刘道银, 陈晓平等.流化床密相区颗粒扩散系数的CFD 数值预测[J].化工学报, 2009; 60 ( 9 ) : 2183-2190.[6] 耿凡,袁竹林,王宏生.流化床中烟丝颗粒的流动特性[J].东南大学学报,2009; 5(39):1012-1017.[7] 杨建华,屈卫东,秦光耀.流型对循环流化床径向气体混合影响的试验研究[J].热能动力工程,2009;6(24):737-740.[8] 张卫东,陈锋,陈汉良.气、固二相流化床在线分析系统[J].化学反应工程与工艺, 1987:1(3):81-84.[9] 任聪静,王靖岱, 阳永荣.气固流化床中不同颗粒的流动模式及其转变[J].浙江大学学报, 2010:2(44):305-309.[10] 欧阳洁,李静海.确定性颗粒轨道模型在流化床模拟中的研究进展[J].化工学报, 2004, 10 (55) : 1581-1592.[11] 徐以泉,郭庆杰,司崇殿,曹长青.微小流化床流化特性分析.过程工程学报, 2009; 2(9) :209~215 .[12] ShuyanWang, Xiaoqi Li, Yanbo Wu, Xin Li, Qun Dong,and Chenghai Yao. Simulation of Flow Behavior of Particles in a Liquid Solid-Fluidized Bed[J]:Ind. Eng. Chem. Res. 2010, 49, 10116–10124.[13] J. R. GRACE.Fluidized Bed Reactor Modeling[J]:In Chemical Reactors;1981,10:3-18.。