大型连铸坯质量控制
提高连铸坯内部质量的方法
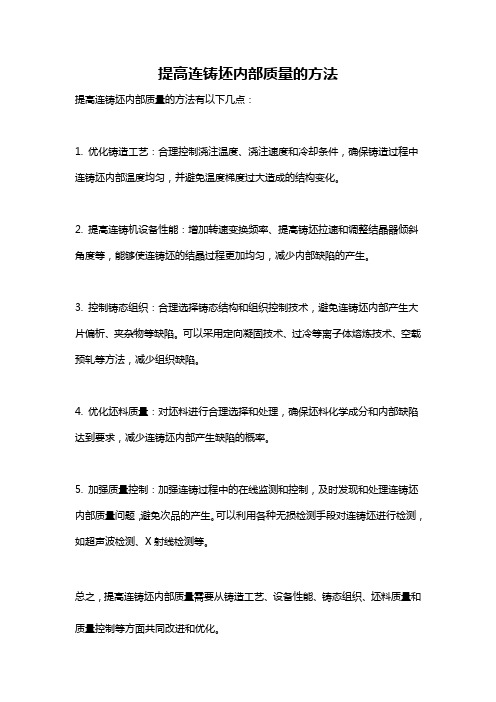
提高连铸坯内部质量的方法
提高连铸坯内部质量的方法有以下几点:
1. 优化铸造工艺:合理控制浇注温度、浇注速度和冷却条件,确保铸造过程中连铸坯内部温度均匀,并避免温度梯度过大造成的结构变化。
2. 提高连铸机设备性能:增加转速变换频率、提高铸坯拉速和调整结晶器倾斜角度等,能够使连铸坯的结晶过程更加均匀,减少内部缺陷的产生。
3. 控制铸态组织:合理选择铸态结构和组织控制技术,避免连铸坯内部产生大片偏析、夹杂物等缺陷。
可以采用定向凝固技术、过冷等离子体熔炼技术、空载预轧等方法,减少组织缺陷。
4. 优化坯料质量:对坯料进行合理选择和处理,确保坯料化学成分和内部缺陷达到要求,减少连铸坯内部产生缺陷的概率。
5. 加强质量控制:加强连铸过程中的在线监测和控制,及时发现和处理连铸坯内部质量问题,避免次品的产生。
可以利用各种无损检测手段对连铸坯进行检测,如超声波检测、X射线检测等。
总之,提高连铸坯内部质量需要从铸造工艺、设备性能、铸态组织、坯料质量和质量控制等方面共同改进和优化。
连铸坯的缺陷及控制

二冷段和末端区的电磁搅拌可有效抑制枝晶搭桥形成封闭 的液窝。
连铸主要工艺参数
① 拉坯速度及其控制 ② 铸坯的冷却(结晶器冷却、二次冷却)
连铸坯的内部凝固是在出结晶器后进行的,后继的二次水冷、 弯曲矫直等直接影响内部质量。
连铸坯的缺陷及控制
提高连铸坯内部质量的工艺措施:
① 控制二冷段的传热,使铸坯均匀凝固,提高等轴晶率; 偏析、缩孔、缩松
② 降低浇钢的过热度; ③ 使用性能好的保护渣,防止钢水二次氧化和污染; ④ 控制拉速,保证连铸机正常运行; ⑤ 电磁搅拌(二冷段和末端区)。 偏析、缩孔、缩松
连铸坯的缺陷及控制
提高连铸坯表面质量的工艺措施:
① 控制结晶器的传热,使初凝固壳均匀; 裂纹、凹陷
② 控制结晶器的振动;
振痕、横裂纹
③ 使用性能好的保护渣;
气孔、夹杂
④ 优化结晶器结构;
倒锥角度,弧形壁
⑤ 电磁搅拌;
气孔、夹杂
⑥ 软接触电磁连铸。
振痕、裂纹
电磁搅拌的部位:
结晶器电磁搅拌:
(1)借助旋转电磁场使连铸 机结晶器内的金属液产生平 面旋转,去除杂质、气体。
结晶器电磁搅拌:
(2)扩大等轴晶区改善宏观 偏析,减少粗大柱状晶区 。
软接触电磁连铸:
软接触电磁连铸:
(1)减轻结晶器振动对弯月 面的影响,液态渣膜连续均 匀。
软接触电磁连铸:
(2)减小初凝壳对结晶器的 连铸坯的内部缺陷
裂纹 气孔 夹杂 缩孔、缩松 成分偏析
连铸坯的缺陷及控制
连铸坯的缺陷及控制
1. 连铸坯的表面缺陷
裂纹 气孔 夹杂 振痕、凹陷 成分偏析
连铸坯的缺陷及控制
1. 连铸坯的表面缺陷
连铸圆坯质量控制

连铸坯质量检验及控制一、连铸坯的内部结构(凝固组织)的一般特征及检验。
连铸坯的检验方法连铸坯的内部结构:经过酸浸(酸洗)或硫印的方法在连铸坯横断面或纵断面上用肉眼或低倍放大镜看到内部组织结果。
硫印硫印是用感光相纸显示试样上硫偏析(合金中各组成元素在结晶时分布不均匀的现象称为偏析)的方法,主要用于钢铁行业铸坯质量的检验。
从铸坯上取纵向或横向试样,试验面加工的光洁度不应低于6。
使用反差大的溴化银表面相纸,把与试样大小相同的相纸放入稀硫酸中浸泡1-2分钟后取出,将相纸对准检查面轻轻覆盖好,将试样与相纸间气泡赶净,待接触2-5分钟后取下,将相纸在流水中冲洗,然后定影烘干,即完成一张硫印。
印基本原理:硫酸与试样上的硫化物(FeS、MnS)发生反应,生成硫化氢气体,硫化氢气体再与感光相纸上的溴化银作用,生成硫化银沉淀在相纸相应的位置上,形成黑色或褐色斑点。
用硫印试验,可显示钢锭、连铸坯中心裂纹、偏析线、低倍结构和夹杂分布等。
酸洗用酸液洗去基体表面锈蚀物和轧皮的过程。
用酸浸或硫印法所显示的组织结构属于宏观结构,是连铸坯和金属材料检验中最为常见的检验技术。
连铸坯的内部结构连铸坯自表面至中心都是由边缘等轴晶区(激冷区)、柱状晶区和中心等轴晶,区三部分组成。
温度梯度较大时,固液两相区(图1)小,有利于柱状晶的生长,而凝固速度较快,则易于生成枝晶间距小的铸造组织,所以连铸坯具有较发达的柱状晶组织,并具有较小的枝晶间距。
(图1)枝晶间距是指相邻同次枝晶间的垂直距离,它是树枝晶组织细化程度的表征。
枝晶间距越小,组织就越细密,分布于其间的元素偏析范围也就越小,故越容易通过热处理而均匀化。
通常采用的有一次枝晶(柱状晶主干)间距d1,和二次分枝间距d2两种。
连铸坯宏观组织的好坏可以用等轴晶所占的比例多少来衡量,轴晶结构致密,加工性能能好。
柱状晶具有明显的方向性,加工性能差,容易导致中心偏析,中心疏松和中心裂纹等缺陷。
二、连铸坯内部凝固结构的控制连铸坯凝固过程的一般特征:从连铸坯的侧面优先凝固,其温度梯度高,凝固速度快,连铸坯内部结晶体成长是不规则的,局部优先生长使内部晶体生长使内部晶体产生“搭桥”等现象,造成因钢水补充不足而出现中心缩孔等缺陷。
连铸坯质量的控制

连铸坯的质量控制系统专业:班级:姓名:XXX目录1连铸坯纯净度与产品质量 (1)1.1纯净度与质量的关系 (1)1。
2提高纯净度的措施 (2)2连铸坯质量............................................................ 错误!未定义书签。
2.1 连铸坯的几何形状质量 (3)2。
1.1 铸坯形状缺陷类型 (4)2。
1。
2 铸坯形状缺陷产生原因及防止措施 (4)2.1.3 铸坯鼓肚 (4)2.1.4 铸坯菱变 (4)2。
1。
5 铸坯变成梯形坯 (5)2.2 连铸坯表面质量 (5)2。
2。
1 连铸坯表面振痕 (5)2。
2。
2 振痕形成机理 (5)2。
2.3 振痕对铸坯质量的影响 (6)2。
2。
4 影响振痕深度的因素 (6)2.2.5 减少振痕深度的措施 (7)2。
2.6 铸坯表面裂纹 (7)2。
2。
7 表面纵裂纹 (8)2。
2.8 铸坯角部纵裂纹 (11)2。
2。
9 表面横裂纹 (12)2。
2.10 角部横裂纹 (14)2.2。
11 铸坯表面星状和网状裂纹 (15)2。
2.12 铸坯表面夹渣(杂) (16)2.2。
13 铸坯气孔和气泡 (17)2。
2.14 铸坯表面凹陷 (17)2。
2.15 铸坯表面增碳和偏析 (18)2。
2.16 重皮和重结及结疤 (19)2.3 连铸坯内部质量 (19)2。
3。
1 铸坯内部裂纹 (19)2。
3.2 皮下裂纹 (20)2.3.3 中间裂纹 (20)2.3.4 矫直裂纹 (21)2。
3。
5 压下裂纹 (22)2.3。
6 断面裂纹-——-中心线裂纹 (22)2。
3。
7三角区裂纹 (24)2。
3.8角部附近的裂纹 (25)2.3。
9白点及发纹 (25)2。
3。
10铸坯中心偏析、疏松和缩孔 (25)2.3。
11铸坯内部夹渣(杂) (26)3连铸坯星状缺陷 (27)3.1 鼓肚变形 (27)3。
2 菱形变形 (28)3.3 圆铸坯变形 (28)致谢 (29)摘要连铸坯质量决定着最终产品的质量。
连铸坯质量控制
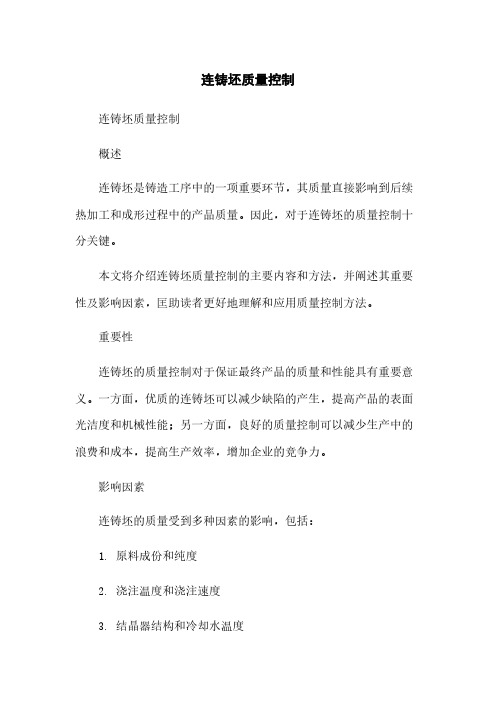
连铸坯质量控制连铸坯质量控制概述连铸坯是铸造工序中的一项重要环节,其质量直接影响到后续热加工和成形过程中的产品质量。
因此,对于连铸坯的质量控制十分关键。
本文将介绍连铸坯质量控制的主要内容和方法,并阐述其重要性及影响因素,匡助读者更好地理解和应用质量控制方法。
重要性连铸坯的质量控制对于保证最终产品的质量和性能具有重要意义。
一方面,优质的连铸坯可以减少缺陷的产生,提高产品的表面光洁度和机械性能;另一方面,良好的质量控制可以减少生产中的浪费和成本,提高生产效率,增加企业的竞争力。
影响因素连铸坯的质量受到多种因素的影响,包括:1. 原料成份和纯度2. 浇注温度和浇注速度3. 结晶器结构和冷却水温度4. 结晶器护盖的材质和形状5. 连铸速度和拉速6. 过度超熔度和段距这些因素的合理控制和调整,可以有效地提高连铸坯的质量。
质量控制方法质量控制步骤连铸坯质量控制主要包括以下几个步骤:1. 原料质量检验:对原料的成份、纯度及其它关键指标进行检验,确保原料的质量符合要求。
2. 浇注质量控制:合理控制浇注温度和速度,以避免过热或者过冷引起的坯体缺陷。
3. 结晶器质量控制:结晶器的结构和冷却水温度对坯体的结晶质量有直接影响,因此需加强结晶器的质量控制。
4. 连铸速度和拉速控制:坯体的连铸速度和拉速会影响坯体的晶粒细化程度和坯体的机械性能,需要进行合理的控制。
5. 坯体表面质量控制:通过加强护盖材料和形状的选取,合理调整过度超熔度和段距,以提高坯体表面的光洁度。
质量控制指标连铸坯的质量控制需要依据具体产品的要求和标准来制定相应的指标。
普通来说,常见的质量控制指标包括:1. 外观质量:包括表面光洁度、无裂纹、无疤痕等;2. 坯体几何尺寸:包括宽度、厚度、长度等;3. 结晶质量:包括坯体的晶粒细化程度、晶界清晰度等;4. 坯体力学性能:包括抗拉强度、屈服强度、延伸率等;以上指标应根据产品要求,通过实验和测试方法进行监控和评估。
连铸坯质量的控制

连铸坯质量的控制
一、引言
连铸是钢铁生产过程中的重要环节,其连铸坯的质量影响着钢质的稳定性、物
理性能和化学成分等方面。
因此,连铸坯质量控制一直是钢铁生产中的关键技术之一。
二、连铸坯质量的影响因素
1.原料质量:包括钢水、氧化渣等的质量;
2.坯型结构和尺寸:坯型结构和尺寸的设计直接影响坯料的冷却效果和
内部应力状态;
3.坯料表面状态:表面缺陷会在浇铸过程中暴露出来,影响坯料的质量;
4.坯料内部缺陷:坯料内部缺陷会影响钢材的使用寿命和物理性能;
5.连铸工艺参数:包括浇注速度、结晶器温度和冷却水流量等。
三、连铸坯质量控制的措施
为了控制连铸坯质量,需要在生产过程中采取以下措施:
1.加强原料质量控制:保证钢水、氧化渣等原料的质量,避免对坯料质
量的不利影响;
2.优化坯型设计:通过设计合理的坯型结构和尺寸,使坯料均匀冷却、
内部应力均匀分布;
3.改进坯料清理技术:减少表面缺陷的产生;
4.加强坯料表面处理:处理坯料表面缺陷,消除缺陷部位;
5.控制连铸工艺参数:调整浇注速度和结晶器温度等工艺参数控制坯料
成分,改善坯料品质。
四、
通过加强原料质量控制、优化坯型设计、改进坯料清理技术、加强坯料表面处
理和控制连铸工艺参数等措施,可以有效地控制连铸坯质量。
同时,连铸坯质量控制也是钢铁生产中不可或缺的环节,对于提高钢材质量和降低成本都具有非常重要的意义。
连铸坯质量控制技术
连铸坯质量控制技术引言连铸是一种重要的铸造工艺,用于生产大批量的金属坯料。
连铸坯的质量直接影响到后续工艺的效果和产品的质量。
因此,连铸坯质量控制技术是提高产品质量和降低生产成本的关键。
本文将介绍连铸坯质量控制技术的重要性,并详细探讨了影响连铸坯质量的因素和常用的质量控制方法。
连铸坯质量的重要性连铸坯是下一步金属加工的原料,其质量直接影响到成品的质量。
良好的连铸坯质量可以保证产品的力学性能、表面质量和尺寸精度。
同时,优质的连铸坯还可以减少加工过程中的金属损耗和工时,提高生产效率和经济效益。
此外,连铸坯质量控制也是减少缺陷和事故的重要环节。
通过合理的质量控制措施,可以有效预防坯料的开裂、缺口、气孔等缺陷,避免金属材料的浪费和安全事故的发生。
综上所述,连铸坯质量控制技术对于提高产品质量和生产效率具有重要意义。
影响连铸坯质量的因素连铸坯质量受到多个因素的影响。
以下是一些常见的影响因素:1. 喷水冷却水质量连铸过程中的喷水冷却是保证连铸坯结晶过程良好进行的重要环节。
冷却水的质量对连铸坯表面质量和内部组织均匀性有很大影响。
如果冷却水中含有过多的杂质和氯离子,容易导致坯料表面起泡、气孔等缺陷。
2. 浇注温度和速度浇注温度和速度是影响连铸坯结晶行为的关键参数。
过高的温度和过快的浇注速度会导致坯料表面凝固不均匀,产生质量缺陷。
而过低的温度和过慢的浇注速度则会引起结晶过程延长,出现细晶区、大晶区等组织缺陷。
3. 结晶器结构和材料结晶器是连铸过程中实现坯料结晶的关键部件。
结晶器的结构和材料选择直接影响到连铸坯的结晶行为和组织性能。
不合理的结构设计和材料选择可能导致结晶器磨损、结晶不良等问题。
4. 冷却方式和参数连铸坯的冷却方式和参数选择对坯料的宏观和微观组织均有影响。
合理的冷却方式和参数可以保证连铸坯结晶行为的均匀性和完整性,防止产生缺陷和组织不良现象。
常用的质量控制方法为了确保连铸坯质量的稳定和一致性,可以采用以下几种常用的质量控制方法:1. 自动化控制系统自动化控制系统可以通过实时监测和控制连铸过程的关键参数,如浇注温度、浇注速度和冷却水流量等,来确保连铸坯的质量符合要求。
连铸坯质量控制
连铸坯质量控制摘要:连铸坯得表面质量,主要就是指连铸坯表面就是否存在裂纹、夹渣及皮下气泡等缺陷。
连铸坯这些表面缺陷主要就是钢液在结晶器内坯壳形成生长过程中产生得,与浇注温度、拉坯速度、保护渣性能、浸入式水口得设计,结晶式得内腔形状、水缝均匀情况,结晶器振动以及结晶器液面得稳定因素有关。
连铸坯得内部质量,就是指连铸坯就是否具有正确得凝固结构,以及裂纹、偏析、疏松等缺陷程度。
二冷区冷却水得合理分配、支撑系统得严格对中就是保证铸坯质量得关键。
关键词:连铸坯、质量、控制正文:(一)连铸坯纯净度度与产品质量1、纯净度与质量得关系纯净度就是指钢中非金属夹杂物得数量、形态与分布。
与模铸相比,连铸得工序环节多,浇注时间长,因而夹杂物得来源范围广,组成也较为复杂;夹杂物从结晶器液相穴内上浮比较困难,尤其就是高拉速得小方坯夹杂物更难于排除。
夹杂物得存在破坏了钢基体得连续性与致密性。
大于50μm得大型夹杂物往往伴有裂纹出现,造成连铸坯低倍结构不合格,板材分层,并损坏冷轧钢板得表面等,对钢危害很大。
夹杂物得大小、形态与分布对钢质量得影响也不同,如果夹杂物细小,呈球形,弥散分布,对钢质量得影响比集中存在要小些;当夹杂物大,呈偶然性分布,数量虽少对钢质量得危害也较大。
例如:从深冲钢板冲裂废品得检验中发现,裂纹处存在着100~300μm不规则得CaO-Al2O3与Al2O3得大型夹杂物。
再如,由于连铸坯皮下有Al2O3夹杂物得存在,轧成得汽车薄板表面出现黑线缺陷,导致薄板表面涂层不良。
还有用于包装得镀锡板,除要求高得冷成型性能外,对夹杂物得尺寸与数量也有相应要求。
国外生产厂家指出,对于厚度为0、3mm得薄钢板,在1m2面积内,粒径小于50μm得夹杂物应少于5个,才能达到废品率在0、05%以下,即深冲2000个DI罐,平不到1个废品。
可见减少连铸坯夹杂物数量对提高深冲薄板钢质量得重要性。
对于极细得钢丝(如直径为0、01~0、25mm得轮胎钢丝)与极薄钢板(如厚度为0、025mm得镀锡板)中,其所含夹杂物尺寸得要求就可想而知了。
连铸坯质量控制
连铸坯质量控制连铸坯质量控制引言连铸坯质量是决定钢铁产品质量的重要因素之一。
在连铸过程中,通过控制连铸坯的凝固结晶形貌、尺寸尺寸以及内部缺陷等,可以保证最终钢铁产品的质量稳定性。
本文将介绍连铸坯质量控制的基本原则和常用技术手段。
1. 连铸坯凝固结晶形貌控制1.1 凝固路径设计连铸坯的凝固路径设计是影响凝固结晶形貌的关键因素。
凝固路径包括主要凝固温度区间、凝固速度以及凝固过程中应有的温度梯度等要点。
通过科学合理地设计凝固路径,可以控制连铸坯的凝固结晶形貌,提高产品的均匀性和致密性。
1.2 凝固浸没深度控制凝固浸没深度是指连铸坯在铸机中浸没的深度。
凝固浸没深度的调整可以通过调整浇注速度、浇注高度和结晶器深度等因素来实现。
恰当地控制凝固浸没深度可以优化凝固结构,减少坯壳厚度和缩孔等缺陷的发生。
2. 连铸坯尺寸控制2.1 坯型设计连铸坯的尺寸控制需要科学合理地设计坯型。
坯型设计要考虑连铸机的性能和工艺条件,以及产品需要达到的尺寸要求。
有效的坯型设计可以保证连铸坯尺寸的精确控制,减少修磨损失并提高铸坯产量。
2.2 坯型换边控制连铸坯在连铸过程中,由于挤压力和引拉力的作用,容易发生坯型换边的情况。
坯型换边会导致铸轧过程中尺寸控制困难,甚至导致产品尺寸不合格。
通过控制连铸机的工艺参数和优化设备结构,可以有效地控制坯型换边,提高铸坯质量。
3. 连铸坯内部缺陷控制3.1 结晶器设计结晶器是连铸过程中控制坯内部缺陷的关键设备。
结晶器的设计应考虑到坯内部的流动状态,并通过合理的传热和传质方式,控制连铸坯内的气体和夹杂物等缺陷。
合理的结晶器设计可以有效减少坯内部夹杂物和气体等缺陷的产生。
3.2 液相线保护措施液相线是连铸过程中凝固结构变化的关键位置。
液相线的形成过早或过晚都会导致内部缺陷的产生。
通过合理的冷却水设定和轧制工艺,可以保证液相线的稳定形成,有效控制坯内部缺陷。
结论连铸坯质量控制是保证钢铁产品质量稳定的关键环节。
连铸坯质量控制
连铸坯质量控制连铸坯质量控制1. 引言2. 连铸坯质量特点连铸坯的质量特点主要包括以下几个方面:2.1 凝固结构连铸坯是通过冷却凝固过程形成的,其凝固过程直接影响到坯体的凝固结构。
凝固结构的好坏会对后续的加工以及材料性能产生重要影响。
2.2 化学成分均匀性连铸坯的化学成分均匀性是其质量的重要指标之一。
成分不均匀容易导致后续钢材性能不稳定,从而影响到产品的质量。
2.3 表面缺陷由于连铸坯制造过程中的一些不可避免的因素,气体夹杂、氧化皮等,会在坯体表面形成一些缺陷。
这些表面缺陷会对后续产品的外观质量产生负面影响。
2.4 尺寸偏差连铸坯的尺寸偏差是指坯体的实际尺寸与标准尺寸之间的差异。
尺寸偏差会影响到钢材的加工工艺和成形质量。
3. 连铸坯质量控制因素及措施连铸坯质量的影响因素众多,包括原料质量、连铸工艺参数、设备状况等。
针对这些影响因素,可以采取以下控制措施来提高连铸坯的质量:3.1 原料质量控制通过严格控制原料的化学成分和物理性能,确保连铸坯的化学成分均匀性和机械性能达到要求。
3.2 连铸工艺参数控制连铸工艺参数的合理设置对坯体的凝固结构和表面质量具有决定性影响。
需要通过优化连铸工艺参数,如冷却水流量、浇注速度等,来控制连铸坯的质量。
3.3 设备维护与改进连铸设备的状态对连铸坯质量也有重要影响。
定期进行设备维护和检修,及时处理设备故障,可以保证设备处于良好状态,进而提高连铸坯的质量。
3.4 检测手段与技术利用先进的检测手段和技术,如超声波检测、磁力检测等,可以对连铸坯进行质量检测,及时发现问题并采取相应措施。
4.连铸坯质量控制是钢铁生产中至关重要的环节。
通过对连铸坯质量特点的分析和影响因素的控制,可以采取相应的措施来提高连铸坯的质量。
这不仅对于保证下游产品质量,还对于提高工业生产效益和降低资源消耗具有重要意义。
开展连铸坯质量控制工作是必不可少的。
- 1、下载文档前请自行甄别文档内容的完整性,平台不提供额外的编辑、内容补充、找答案等附加服务。
- 2、"仅部分预览"的文档,不可在线预览部分如存在完整性等问题,可反馈申请退款(可完整预览的文档不适用该条件!)。
- 3、如文档侵犯您的权益,请联系客服反馈,我们会尽快为您处理(人工客服工作时间:9:00-18:30)。
GCr15连铸坯组织及缺陷的超声波检测赵荒培(中冶京诚(营口)装备技术有限公司营口115004)本文采用UT评估大型轴承钢连铸坯的质量。
提出组织衰减、表征缩孔及指示性缺陷的数字表述等三项指标。
可作为评判连铸坯质量的判据。
关键词:UT, 连铸坯,轴承钢,质量随着国内工业的发展,轴承钢需求量日益增加。
轴承钢连铸坯(≥Ф600mm)的组织与缺陷对最终产品质量有相关影响。
因此,提高轴承钢的质量的研究对于企业的发展,满足市场需求起着重要的作用[1-4]。
常规的连铸坯的宏观检查虽然能直观地观察到偏析,疏松、缩孔等缺陷;但其单一横截面的检测不易对整体质量进行准确的评估。
相对于装备制造行业而言,对连铸坯进行检查,以便较早除去对后面工序无价值的不合格品,可以改善制造方法和作业方法以及提高效率。
本文采用检测连铸坯的超声波组织衰减及其孔洞式缺陷。
并试图制定一个适用于对生产具有参考意义的方法。
1 大型连铸坯检测依据1.1 GCr15低倍组织的特点GCr15轴承钢是一种典型的高碳特殊钢。
其低倍组织有两个显著地特点:(1)凝固组织与宏观碳偏析关系颇为复杂;(2)由于其高碳、铬所导致的凝固温度区较宽,其低倍组织缩孔出现的概率较大。
连铸坯由外至内,柱状晶、树枝晶、和等轴晶组成。
外层的超声波穿透性好于内部等轴晶。
钢锭的结晶由外至内,激冷层-柱状晶(树枝晶)-等轴晶(自由晶)。
柱状晶的超声波的穿透性比等轴晶好。
金属的显微组织的差异对超声波衰减有显著影响。
衰减小的具有较细的晶粒而致密。
其底波和伤波下降较小。
1.2 UT检测的目的UT是用于非破坏性方法把材料中的缺陷作为超声波能量的变化检测出来简洁方法[5-10]。
可以直接而客观地估计:是否存在缺陷,其位置、分布与形状等。
这些推断必须加上材料的性质、制造的方法等冶金学的统计经验和知识,而且有时还需要与其它的方法结合使用。
连铸坯UT分选--------(1)标准以上后工序→UT→选别(2)标准以下→低倍试验(异常组织偏析,或孔洞式缺陷)→合格(或不合格)→补救(或判废)。
1.3 UT检测难点现场连铸坯的UT检测,常采用黑皮探伤。
不但其探头与钢锭表面的接触状况不稳定是无法定量检测的原因之一,而且其内部缺陷反射波,波高与缺陷的对应关系不确定,因此其缺陷等级无法准确判定。
如侧面探测大铸坯的缩孔型缺陷时相当于圆柱性缺陷。
而气泡或夹杂(渣)等缺陷相当于球状缺陷。
圆板形缺陷与其面积成正比,球状缺陷的反射与其直径成正比,而圆柱形的反射与其直径的平方根成正比。
其次,缺陷的倾斜和粗糙度,铸态材料的内部缺陷表面往往不光滑(缩孔表面粗糙尤甚)。
其实际缺陷的反射比之人工缺陷的反射小的多。
常导致过小评价缺陷等级的错误。
缺陷波的指向性。
对于声波垂直入射的任一情况下,缺陷的反射特性因其形状、大小而有很大的不同。
再次,缺陷的性质。
当缺陷与基体的声阻抗之比非常大时,声波将在该缺陷表面几乎完全反射,如钢材中的裂纹、气泡等反射。
然而非金属夹杂物密集区产生的缺陷反射波较之裂纹等小的多。
对于呈立体分布的非金属夹杂物,其反射波高与其面积和密集度有关。
此外,小信号叠加反射。
一定范围,虽然单个缺陷的尺寸小于规定的判伤界限,但临近诸多小缺陷群体信号的叠加则使群体缺陷的检测成为可能。
如:组织反射。
钢的化学成分偏析及组织不均匀可引起超声波的反射。
总之,超声波检测钢锭、连铸坯,其内部缺陷性质,大小难于判定。
但可以对其组织的声波衰减,大的孔洞式缺陷给出孰优孰劣的推论。
这也是本文的目的。
1.4 UT的质量级别1.4.1考虑试样衰减大的分类缺陷反射波,只用大小进行分类,没有考虑材料的衰减。
如果考虑材料的衰减,需要先制定出被检材料的底波多次反射的标准次数,然后按比其多或少的材料的多次反射次数。
来规定反射波高度的分类范围。
被检才材料的底波反射次数比标准次数少的是相对衰减大的材料。
在显示屏上就会出现过小的缺陷波。
反之,比标准多的材料,衰减小,反射波就过大。
需要注意的是底波反射次数少,也可能是存在大的缺陷。
该法是检测件整体进行质量评价。
对被检查件进行全面扫查。
以A型显示图形的缺陷反射波高度为横轴,以产生这一高度反射波的数目为横轴,进行质量评价[11]。
表1。
表中n为标准底面多次反射次数,被认为是无缺陷干扰标准底面多次反射次数。
a、b、c、x、y、z为适当定出的反射波高。
由表1可知,需先检测被检连铸坯的底面反射次数的标准次数,然后按比它多、或少的底波反射次数,来确定其反射波高度的分类范围。
底波反射次数低于标准次数是衰减大的材料,在显示屏上就会出现过小的缺陷反射波;反之,比标准多的被测连铸坯,衰减小,缺陷反射波就会过大。
需注意的是:连铸坯反射次数少,多数存在大的缺陷。
相对于我公司生产的GCr15连铸坯而言,不进行UT定量检测其不连续缺陷。
其底波反射数与级别(简称D级别)的对应关系定义如表2。
如果考虑缺陷波的影响,则需考虑底波与缺陷波的相对值。
其缺陷反射波的高度的分类(简称Q级别)。
该法优点是反射波的数值不受探头接触的影响。
有时用衰减器以分贝值读出着两个反射波高度比,还可以防止仪器差引起的影响。
见表3。
1.4.2 铸件的体积亏损缺陷定义连铸坯的体积亏损(孔洞式缺陷),均表征为缩孔。
简称S型缺陷。
设定缺陷(缩孔)的分类。
见表2.1.4.3 横截面探伤指示性缺陷的数字分类当连铸坯的横截面为冷切面时,当其连铸坯的长度小于7米时,可采用0.5MHz 直探头检测其连铸坯的横截面。
对于Ф650连铸坯而言,其截面的中心区域无底波反射。
可采用移动探头圆周移动探测,可绘出无底波区域的轮廓。
裂纹,缩孔,白点等缺陷,当其缺陷的形状相同时,其探伤的图形也是相同的。
为了避免根据探伤图形定缺陷性质的困惑。
本文借用日本的3位数字表述分类。
简称H3分类。
见表3。
2 试验2.1试样GCr15,Ф600mm 连铸坯.径向与纵向探伤。
A型脉冲探伤仪,型号为HS511。
80dB以下的连续可调衰减器误差≤1%,垂直线性误差≤5%;检测频率,1MHz;晶片直径,¢24mm。
宏观低倍检测:采用GB/T226中的电解腐蚀法。
2.2 检测结果径向探伤,缺陷波很强,底波消失。
估计为大面积缺陷,如裂纹,夹层等。
其取了两片试片用于低倍试验。
距字端110mm处取第一编号低倍试片,距字端1090mm处取第二个片。
1#片的UT波形与低倍组织对应详见图1.GCr15CMn连铸坯(编号不详)径向探伤,发现缺陷波与底波共存。
取两片(4#,5#)做低倍。
详见图1与图2。
4#试片缺陷波高80%,底波25%。
中心为缩孔。
图1轴承钢连铸坯4#的UT波形(左)与其低倍组织(右)5#UT波型图为,缺陷波高80%,底波高40%。
图2 5#连铸坯UT波形(左)与其低倍组织(右)评级:D型衰减组织5级(底波多次反射次数法)Q型衰减组织:1# A-a级;2#A-a(反射波高度的分类)S型表征缺陷(表征缩孔):1#,3.5级,2#,3级(表征缩孔级别)详见表4.3 讨论轴承钢连铸坯的最大问题是连铸坯的中心部分的质量,铸坯断面越大,中心的碳偏,缩孔越严重。
采用强冷工艺可以获得发达的柱状晶组织,但由于选分结晶而导致严重的中心碳偏析,加宽了钢液的凝固温度范围,形成缩松等缺陷。
即形成所谓的中心晶间裂纹。
而采用弱的冷却速度形成粗大等轴晶和严重的缩孔。
同样导致严重的碳偏析。
只有首先获得合理的凝固组织,才能得到较轻的宏观偏析。
连铸坯的边缘部分(柱状晶区)致密度和均匀性都好于中心部位(等轴晶区),文献报道轴承钢连铸坯边部致密度达到0.8~0.85。
中心达到0.5~0.7。
即相应的柱状晶区致密度高于等轴晶区。
其致密的柱状晶区的超声波穿透性比等轴晶区的穿透性要好。
因此测定中心区域的组织衰减,比较不同工艺制度生产的连铸坯,或检查不同连铸坯的组织衰减的差别,显然具有质量评价的意义。
图1与图2两只试片的低倍组织近乎相同,但其UT检测却有差别。
二试样的缺陷波几近相同,但其底波反射却存在差别。
超声波的波长与晶粒直径D有一定的对应关系,当其比值小于70时,随着值的减小,超声波的衰减急剧增大。
显然其底波较低的试片的组织衰减较为严重。
采用UT检测连铸坯所获得的信息对于了解缺陷是相当定性的。
UT结果的本身的等级分类,即探伤结果的评价基准不一定是缺陷本身的分级;也不是材料可否使用的基准,而是缺陷的有害性的评价基准。
今后,随着UT信息量的增加,以加深对轴承钢连铸坯缺陷性质的认识,应力求UT结果的分级与缺陷的分级由表征与实际统一起来。
在此基础上定出有害性的评价标准,进而制定出检测件是否合格的评判标准。
参考文献1沈峰等轴承钢连铸大方坯偏析和致密度的分析材料研究,2009年增刊.p538-5412 祝宜明张文基等轴承钢连铸中心碳偏析的探讨连铸,2001.1 p34-363 刘兴洪缪新德等兴澄特钢炼钢连铸GCr15钢生产过程质量控制 2008年特钢年会论文集4刘宪民成国光郝增林 GCr15轴承钢小方坯连铸低倍缺陷分析与控制2006,1(151). P39-40.5 ASTM A 609 Standard Practice for Casting, Carbon, Low-Alloy and Martensitic Stainless Steel, Ultrasonic Examination Thereof6 ASTM A217 Specification for Steel Castings, Martensitic Stainless and Alloy, for Pressure-containing Parts, Suitable for High-Temperature Service7 ASTM E317 Practice for Evaluating Performance Characteristics Systems Without the Use of Electronic Measurement Instruments8 GB/T7233-1987 铸件超声探伤标准9GB/T 1503-2008 铸钢轧辊10 GB/T 7233.1-2009(部分替代GB/T 7233-1987)超声检测第一部分:一般用途铸钢件11李靖等校译.超声探伤法,广东科技出版社,1981.12 吴楠基于小波变换的低碳钢连铸坯超声探伤声学技术 2006 25(4) p299-303。