反渗透膜处理镀镍废水工艺设计
电镀废水处理工艺设计技术设计方案
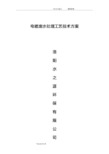
电镀废水处理工艺技术方案洛阳水之源环保有限公司2012-9-30项目提出甲方意将已处理后的电镀废水做深度处理,深度处理后的废水再利用,处理后的浓缩水回流到源水池再度提取水中的稀有金属。
由于原水水源中部分指标超标,不能达到饮用水标准,需进行处理,经调研特提出利用洛阳水之源环保有限公司提供的工艺技术和设备以求达到用水标准。
工艺技术方案一、设计思路在本着充分利用客户方原有设施和最大程度的节省投资,本着对客户负责、对我们自己负责的前提下,同时根据甲方提供水质报告、工艺技术及实际情况和要求特提出以下设计方案。
二、工艺方案及工艺流程由于原水水质中铁,硫酸盐,氯化物,镍等多项指标超标.工艺选择采用预处理加双膜工艺。
由于原水水质报告中铁,超标,这会对工艺中反渗透膜造成极大的不利,使得反渗透膜快速衰减,造成水通量下降和降低出水品质。
为防止此类问题的发生,我们预处理中增加了錳沙过滤装置及超滤装置,同时又有活性炭吸附装置。
超滤膜用于反渗透预处理时,运行压力0.1—0.2MPa,可以使出水浊度小于0.2NTU,SDI小于3;可以100%的去除水中残留滋生的细菌和近于100%胶体,尤其是胶体硅,在SDI小于1时超滤能去除水中所有的Fe、Al氧化物;能耗可减少30%以上。
最大程度上减少了对反渗透膜的危害,它还可以减少反渗透膜的清洗次数,降低维护费用,延长反渗透膜组件的使用寿命。
极大地降低了客户方的运行成本。
工艺方案技术参数:1、原水:已处理后的工业废水2、出水水质:GB5749-2006生活饮用水卫生标准3、产水量:10t/h一套。
工艺流程【已处理的工业废水】→【废水收集池】→【提升泵】→【多介质过滤(反冲)】→【碳滤装置】→【微滤过滤】→【精密过滤】→【超滤】→【投加阻垢剂及杀菌剂】→【中间水箱】→【保安过滤】→【高压泵】→【反渗透】→【净水池】→【用户】工艺配置序号名称规格型号数量材质备注1 废水收集池50-200m31套自备2 提升泵ZW80-22-30,Q=22m3/h,H=35m配备:电气控制、压力表、阀门等1台钢制3机械过滤器¢1000;Q=9.36m3/h;流速=10米/秒2套玻璃钢含滤料4 反冲机头F56 2套5 碳滤器¢1000;Q=9.36m3/h;流速=10米/秒2套玻璃钢含滤料6 反冲机头F56 2套7 微滤、精滤过滤器MF40-20;Q=20m3/h;过滤精度:5μ;1μ;配备:压力表、阀门等各1套不锈钢外壳含滤芯8 不锈超滤装置UF-3640-24;Q=20m3/h;配备机架、压力表、阀门和连接管;1套钢机架9 高压泵0GDL32-80;Q=20m3/h;H=130m;配备:电气控制、压力表、阀门和连接管1台不锈钢10 保安过滤器MF40-20;Q=20m3/h;过滤精度:1μ;配备:压力表、阀门和连接管1台不锈钢11RO装置RO-8040-10;Q=10m3/h配备:RO膜、压力管、压力表、流量计、机架、压力保护器、电气控制、阀门和连接管等;3节。
某某电镀厂0000md 电镀废水处理系统设计方案
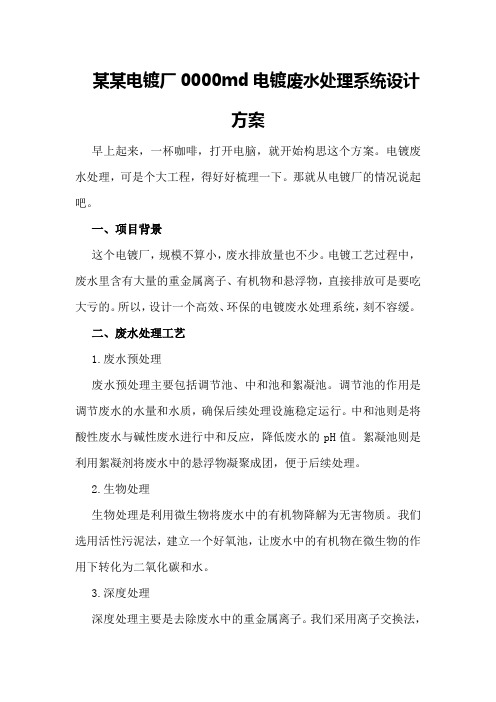
某某电镀厂0000md电镀废水处理系统设计方案早上起来,一杯咖啡,打开电脑,就开始构思这个方案。
电镀废水处理,可是个大工程,得好好梳理一下。
那就从电镀厂的情况说起吧。
一、项目背景这个电镀厂,规模不算小,废水排放量也不少。
电镀工艺过程中,废水里含有大量的重金属离子、有机物和悬浮物,直接排放可是要吃大亏的。
所以,设计一个高效、环保的电镀废水处理系统,刻不容缓。
二、废水处理工艺1.废水预处理废水预处理主要包括调节池、中和池和絮凝池。
调节池的作用是调节废水的水量和水质,确保后续处理设施稳定运行。
中和池则是将酸性废水与碱性废水进行中和反应,降低废水的pH值。
絮凝池则是利用絮凝剂将废水中的悬浮物凝聚成团,便于后续处理。
2.生物处理生物处理是利用微生物将废水中的有机物降解为无害物质。
我们选用活性污泥法,建立一个好氧池,让废水中的有机物在微生物的作用下转化为二氧化碳和水。
3.深度处理深度处理主要是去除废水中的重金属离子。
我们采用离子交换法,将废水中的重金属离子与离子交换树脂进行交换,从而实现重金属离子的去除。
4.废水回用废水经过处理后,水质得到了极大的改善。
我们可以将这部分水回用于电镀工艺中的清洗环节,实现废水资源的循环利用。
三、设备选型1.调节池选用不锈钢材质的调节池,有效容积为100立方米,配备自动控制系统,实现废水水量的实时调节。
2.中和池选用瓷砖衬里的中和池,有效容积为50立方米,配备pH自动检测仪和中和剂计量泵,确保废水pH值稳定。
3.絮凝池选用瓷砖衬里的絮凝池,有效容积为30立方米,配备絮凝剂计量泵和混合搅拌器,确保絮凝效果。
4.活性污泥池选用不锈钢材质的活性污泥池,有效容积为200立方米,配备曝气系统、回流泵和污泥浓缩池。
5.离子交换设备选用离子交换树脂填充的离子交换设备,处理能力为10吨/小时,配备自动控制系统,实现重金属离子的在线监测和去除。
6.废水回用设备选用反渗透膜组件的废水回用设备,处理能力为10吨/小时,配备自动控制系统,实现废水的高效回用。
电镀废水处理工艺设计
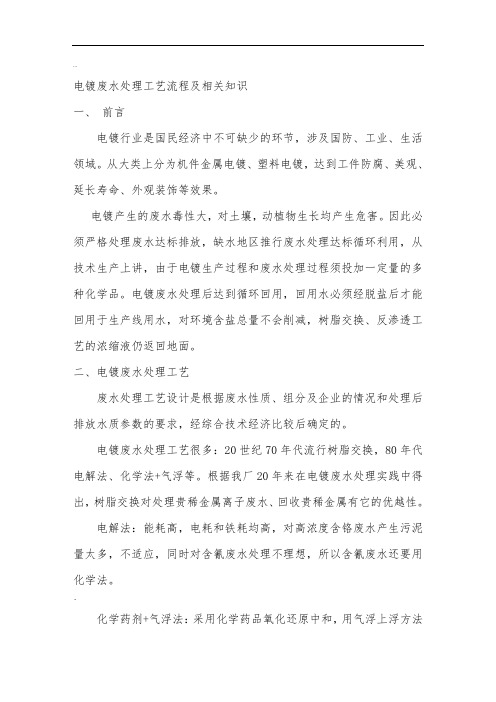
…电镀废水处理工艺流程及相关知识一、前言电镀行业是国民经济中不可缺少的环节,涉及国防、工业、生活领域。
从大类上分为机件金属电镀、塑料电镀,达到工件防腐、美观、延长寿命、外观装饰等效果。
电镀产生的废水毒性大,对土壤,动植物生长均产生危害。
因此必须严格处理废水达标排放,缺水地区推行废水处理达标循环利用,从技术生产上讲,由于电镀生产过程和废水处理过程须投加一定量的多种化学品。
电镀废水处理后达到循环回用,回用水必须经脱盐后才能回用于生产线用水,对环境含盐总量不会削减,树脂交换、反渗透工艺的浓缩液仍返回地面。
二、电镀废水处理工艺废水处理工艺设计是根据废水性质、组分及企业的情况和处理后排放水质参数的要求,经综合技术经济比较后确定的。
电镀废水处理工艺很多:20世纪70年代流行树脂交换,80年代电解法、化学法+气浮等。
根据我厂20年来在电镀废水处理实践中得出,树脂交换对处理贵稀金属离子废水、回收贵稀金属有它的优越性。
电解法:能耗高,电耗和铁耗均高,对高浓度含铬废水产生污泥量太多,不适应,同时对含氰废水处理不理想,所以含氰废水还要用化学法。
·化学药剂+气浮法:采用化学药品氧化还原中和,用气浮上浮方法进行泥水分离,因电镀污泥比重大,并且废水中含有多种有机添加剂,实际使用时气浮分离不彻底,并且运行管理不便,到90年代末,气浮法应用越来越少。
化学药剂+沉淀:该方法是最早应用的方法,经过30多年不同处理工艺实际使用比较后。
目前又回到了最早,也是最有效的处理工艺上来,国外在电镀处理上也大多采用该方法,但实际固液分离运行时间长后,沉淀池会有污泥翻上来,出水难以保证稳定达标。
近年开发的生物处理工艺:小水量单一镀种运行效果高,许多大工程使用很不稳定,因水质水量难以恒定,微生物对水温,品种,重金属离子的浓度,PH值的变化难稳定适应,出现瞬间大批微生物死亡,出现环境污染事故,而且培菌不易。
本工艺是针对不同性质的废水加入不同的药品进行氧化还原中和后,采用直接压滤分离方法分离污泥,投资省、运行操作管理方便,稳定可靠、能耗低。
镀镍废水膜法浓缩回用工艺
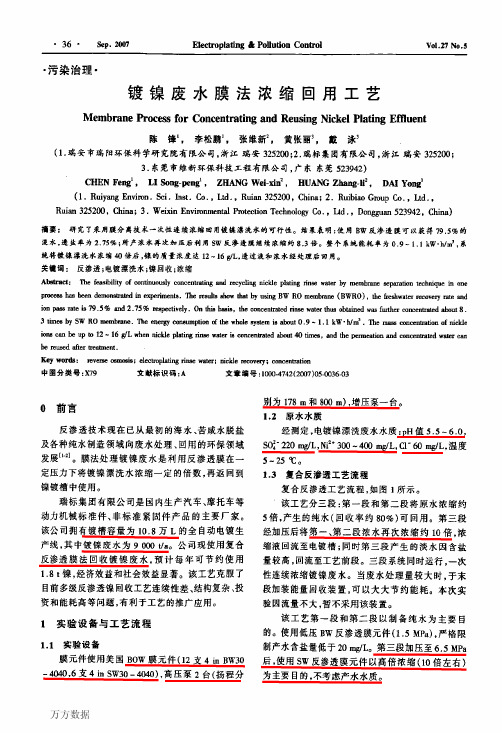
地址:上海市沫亭南路888舜129号
邮编:201615
联系人:罗耀宗
Tel/Fax:02I一67620787 13817104276
E-mall:Ivz~yrd@hotmail。toni
万方数据
3.东莞市维新环保科技5-程有限公司,广东东莞523942) CHEN FeltgI。 u Song-pengt。鄹iIANG W西一试f, EUtJANG Zhang一酽,DAI Yon93 (1.Ruiyang Endmn.sci.Inst.Co.,Ltd.,Ruian 325200,China;2.Ruibiao Group Co.,Ltd.。 Ruian 325200.China;3.Weixin Environmental Protection Technology Co.,Ltd.,Dongguan 523942,China)
虽然膜元件数量增加可以提高极限回收率,但 透盐率也由于第一段和第二段工艺以回收纯水为主 要目的。因此,适当减少膜元件数量?不仅可以提高 产水水质,而且降低了设备成本,缩短和简化了工艺
流程。由于系统流程缩短,第一、第二段工艺对于工 作压力和给水流量变化的响应更加敏感,使系统容 易调节以获得最佳运行效果。 2.2第三段高压反渗透运行结果
复合反渗透工艺流程,如图1所示。 该工艺分三段:第一段和第二段将原水浓缩约 5倍,产生的纯水(回收率约80%)可回用。第三段 经加压后将第一、第二段浓水再次浓缩约lO倍,浓 缩液回流至电镀槽;同时第三段产生的淡水因含盐 量较高,回流至工艺前段。三段系统同时运行,一次 性连续浓缩镀镍废水。当废水处理量较大时,于末 段加装能量回收装置,可以大大节约能耗。本次实 验因流量不大,暂不采用该装置。 该工艺第一段和第二段以制备纯水为主要目 的。使用低压BW反渗透膜元件(1.5 MPa),严格限 制产水含盐量低于20 mg/L。第三段加压至6.5 MPa 后,使用SW反渗透膜元件以高倍浓缩(10倍左右) 为主要目的,不考虑产水水质。
电镀含镍污水处理工艺及方案

电镀含镍污水处理工艺及方案(苏州湛清环保科技有限公司苏州215300)常见含镍废水有电镀镍废水、化学镀镍废水、线路板含镍废水、不锈钢酸洗含镍废水等,这几类废水根据镍离子在水中的不同形态可分为两种,一是较为单一的离子态,二是较为复杂的络合态,不同形态下的处理方法并不相同。
离子态的含镍废水处理起来较为容易,例如电镀镍,通过电化学作用,使溶液中的镍离子沉积在镀件表面,废水中的镍离子可与水形成水合离子,遇到部分氢氧化物即可反应生成沉淀,电镀镍中含镍主盐通常选用氯化镍和硫酸镍,其溶于水的镍离子在碱性条件下即生成氢氧化镍沉淀,这便是含镍工业废水最常见的碱法处理。
络合态的含镍废水处理起来比较困难,首先,常用碱法对含络合态镍离子的废水处理效果微乎其微,这是由于水中镍离子被有机络合物牢牢吸附成络合基团,使OH-无法与镍离子接触发生反应,于是,针对这样的情况,不少人开始尝试将镍离子与络合物分开,使镍离子能够暴露在OH-面前进而生成沉淀,这一过程称之为破络。
破络可通过氧化法实现,常规氧化法有芬顿法、次氯酸钠法、光化学氧化、臭氧氧化等,在几类氧化法中,成本较低的芬顿法、次钠法破络效果较差,含镍废水很难处理达标,而光化学氧化法、臭氧氧化法等破络效果较好,但投资成本及运行成本均较高,无法广泛应用在大多数含镍废水的处理中。
经过对这类废水的继续研究,湛清环保打破了传统的思维,另辟蹊径,不再执着于破络过程,而是从全新的角度出发,利用湛清自主研发的高效除镍剂HMC-M2直接与络合物争夺镍离子,组成全新的螯合基团,在混凝剂的作用下形成更大的絮凝体,进而沉淀去除。
这一方法依靠的是HMC-M2比有机络合物更强的络合力,从而节省掉氧化破络的过程,使该类含镍废水的处理更加方便快捷、简单有效,经长期实践,使用该法处理络合态含镍废水可稳定达到镍离子排放最高标准0.1mg/L以下。
膜法处理电镀清洗废水的零排放工艺设计与研究

1 膜 法 电镀 清 洗 废 水 处 理 零 排 放 工 处理废水、 电镀清洗废水 、 后处理废水以及电镀废 艺 设计
液. 其中, 镀件清洗废水是电镀废水 中的主要来源 之一, 几乎要占废水排放总量的 8%以上. 0 再加上 当前 电镀 生产主要 采用的是漂洗长流清洗工艺, 由于 电镀清洗废水 中的主要污染物是重金属 离子, 不含太多的有机物、悬浮物及杂质等, 适合
第4 期
胡国强: 膜法处理 电镀清洗废水的零排放工艺设计与研 究
9 3
达标 排放或 回用于镀件初级 的漂洗要求. 而在精 密电镀生产中, 对水的纯度要求非常高, 纳滤透过
水 直 接 用作 精 密 电镀 清 洗 则 达 不 到 纯 度 要 求 .陈 锋 等人 则 直 接使 用三 段 式 反 渗透 膜 工 艺 对 电镀 含
了纳滤膜具有操作压力低、水通量大 、对电镀含
N j废水有去除率高等优点, 但透过水的水质仅能
收 稿 E期 :2 1.52 . l 000 —4 宁 波大学 学报 ( 理工版 )网址 :t :3b b . uc ht/ x . u d. p/ n e a 基 金项 目: 宁波 大学 实验技术 研究 资助项 目 ( y .0 60 ). Sj 200 1 s 作 者简介 : 国强 ( 9 5 ) 胡 15 一 ,男, 江宁波 人,副教授 , 要研究 方向 : 分离技术 . - i hg oi g b . uc 浙 主 膜 Ema:u uqa @n u d - l n e n
极大地促进 了电镀废水有效利用和零排放处理的
生产实 际应用 p J √.
混合后再处理【 这种电镀混合废水治理达标排放 l j . 的传统方法虽经有效治理能达标排放, 但仍有大
电镀综合废水处理工程设计方案

电镀综合废水处理工程设计方案一、废水概况电镀行业是一种重要的金属表面处理工艺,其废水含有多种有毒有害物质,如重金属、酸碱、氰化物等。
为了保护环境和人类健康,电镀废水必须进行综合处理。
本设计方案旨在设计一套高效的电镀综合废水处理工程,以减少对环境的污染,并达到国家废水排放标准。
废水处理工程设计包括预处理、主处理、深度处理和后处理四个部分。
二、预处理预处理主要是通过物理化学方法将废水中的可溶性有机物、悬浮物和油污等进行去除,以减轻后续处理工艺的负担。
预处理过程包括网站排除、沉淀池、中和调节池和气浮池等单元。
其中,网站排除主要是通过过滤网将废水中的大颗粒悬浮物和固体杂质去除;沉淀池主要是利用重力沉降原理将废水中的悬浮物和沉积物去除;中和调节池主要是通过加入酸碱等试剂对废水进行中和调节,以提供后续处理工艺的最佳条件;气浮池主要是利用气浮原理将废水中的悬浮物和浮油等去除。
三、主处理主处理是将经过预处理后的废水进行进一步处理,主要是通过化学物理方法将废水中的重金属、有机物等进行去除。
主处理过程包括重金属沉淀、氧化沉淀、气体吸收和活性炭吸附等单元。
其中,重金属沉淀主要是利用添加沉淀剂将废水中的重金属离子转化成不溶性盐类,然后通过沉淀过程将其去除;氧化沉淀主要是通过添加氧化剂使废水中的有机物氧化,然后通过沉淀过程将氧化产物去除;气体吸收主要是通过将废水中的挥发性有机物吸附到吸附剂上,然后将吸附剂进行再生;活性炭吸附主要是利用活性炭对废水中的有机物进行吸附。
四、深度处理深度处理是为了进一步提高废水的水质,达到国家排放标准。
深度处理过程主要包括等温脱盐和高级氧化等单元。
其中,等温脱盐主要是利用逆渗透膜技术将废水中的溶解物质去除,以降低水中的总溶解固体含量;高级氧化主要是利用高级氧化剂对废水中的有机物进行降解,进一步减少有机物含量。
五、后处理后处理是为了进一步提高废水处理系统的可靠性和稳定性,以及回收部分资源。
后处理过程主要包括沉淀格栅、混合沉淀池和消毒等单元。
反渗透膜技术处理含镍废水

800 260 760 235 755 225
200 160 190 156 180 150
113 207 125 245 131 253
1.10 2.00 1.20 2.20 1.45 2.45
2005-4-10 2005-4-10 2006-4-10 2006-4-10 2007-4-10 2007-4-10
1
工艺流程
该系统由两部分组成,即原水预处理部分和反 渗透部分。
Á Á
24mÁ /d
Á
24mÁ /d
Á
24mÁ /d
Á
23.52mÁ /d
Á
ÁÁFra bibliotek!"#$
0.48mÁ /d
图1
工艺流程
Fig.1 Chart of technological process
1.1
胡齐福等, 反渗透膜技术处理含镍废水 的 PP 滤芯, 对预处理起到最后保安作用, 防止管路 中微粒进入 RO 泵, 以免损坏 RO 泵和膜组件。 所有 预处理工序都是为最大限度地防止和延缓污染物在 RO 膜面上的沉积,防止胶体物质及固体悬浮微粒 的赌赛以及有机物、 微生物、 氧化性物质等对膜的破 坏, 以延缓 RO 膜的水解过程, 从而使 RO 系统在良 好状态下工作。 1.2
测量时间 (年- 月- 日) 2005-4-10 2005-10-13 2006-4-10 2007-4-10
浓缩 50 倍后的浓缩液直接回用到电镀槽,作为生产 工艺的补充用水。 本方案处理工艺简单, 维护简单, 无 二次污染, 较彻底地实现了镀镍废水的零排放。
3
RO 膜的清洗与维护
在正常操作过程中, RO 元件内的膜面会受到 无机盐垢、 微生物、 胶体颗粒和不溶性有机物质的污 染, 从而引起膜通量下降, 从而导致设备成本上升, 产品质量下降等一系列问题。尽管本工艺的预处理 系统比较完善, 但经过较长时间运行, RO 膜面仍不 可避免地出现污染问题,这是膜分离技术在实际工 程中普遍存在的问题。因此, 在实际工程中, 要特别 注重对膜的维护- 膜污染的控制与清洗。 2005 年 10 月份, 膜污染较为严重, 通量下降约 20%, 采用加酸 和碱的方法进行化学清洗,膜通量恢复率基本能达 到设计值的 95%左右。
- 1、下载文档前请自行甄别文档内容的完整性,平台不提供额外的编辑、内容补充、找答案等附加服务。
- 2、"仅部分预览"的文档,不可在线预览部分如存在完整性等问题,可反馈申请退款(可完整预览的文档不适用该条件!)。
- 3、如文档侵犯您的权益,请联系客服反馈,我们会尽快为您处理(人工客服工作时间:9:00-18:30)。
反渗透膜技术处理含镍废水摘要:建立24m'/d电镀镶漂洗水膜法闭路循环回收系统,采用两级反渗透(RO)膜分离技术对电镀废水浓缩50倍以上,23.6m'/d透过液回用到电镀生产线作为漂洗用水,浓缩液再用蒸发器进一步浓缩后直接回到镀槽,废水处理实现闭路循环。
从2005年4月到2007年4月,共运行了2年,整个系统运行良好。
通过回用水和回收镍等资源,产生较显著的经济、社会和环境效益,实现清洁生产,基本上实现了电镀含镍废水的零排放。
关健询:电镀含镶废水;反渗透膜分离技术;回用水;回收镍一.电镀电镀是利用化学或电化学的方法对金属和非目前,电镀废水的治理把握住无害化的原则,金属表面进行装饰、防护及获取某些新性能的一种但是如何更好地实现电镀废水的资源化,回收利用工艺过程,在工业上通用性强,使用面广,几乎所有有用资源,国内外学者进行了广泛深入的研究。
本的工业部门( 如机械、机电、交通、电子、仪表、纺织、文重点对各种处理技术进行较为详细的分析,对螯轻工等) 都有电镀厂( 车间) 。
但由于电镀厂分散而合沉淀法和NMSTA 天然矿物污水处理剂在电镀废面广,镀件功能要求各异,镀种、镀液组分、操作方水治理中的应用进行了简单介绍,并结合新的排放式及工艺条件等种类繁多,相应带入电镀废水中的标准,对电镀废水处理技术的发展趋向进行展望。
二. 电镀废水来源及特点电镀废水水质成分不易控制,常见的铬、铜、镍、锌、锡、铅、镉及铁等各种重金属离子危害性更大,因此被列为当今全球三大污一般的电镀生产工艺由前处理、电镀和后处理工艺三部分组成,每个工艺一定程度上都有废水产生,其中,电镀生产过程中的镀件漂洗废水是电镀废水的主要来源之一,约占车间废水排放量的80%以上,废水中大部分的污染物质是由镀件表面的附着液在漂洗时带入的; 镀液过滤废水是指在镀液过滤过程中,滴漏的镀液以及在过滤前后冲洗过滤机、过滤介质或镀槽等的排放水; 废镀液包括清理镀槽时排出的残液、老化报废的镀液、退镀液和受污染严重的废弃槽液等。
这部分废液的浓度很高,如果直接排放,则环境污染更为严重。
因管理不善产生电镀车间“跑、冒、滴、漏”废水一般与冲刷设备、地坪等冲洗废水一并考虑处理; 另外,化验用水主要包括电镀工艺分析和废水、废气检测等化验分析用水,其水量不大,但成分较复杂,一般排入电镀混合废水系统进行统一处理后排析放[1]。
电镀废水成分复杂,除含氰废水和酸碱废水外,还含有铬、镍、镉等多种重金属,同时,废水中还含有相当数量的添加剂、光亮剂等有机化合物,例如各型表面活性剂、EDTA、柠檬酸、酒石酸、乙醇胺、乙二醇、硫脲、苯磺酸、香豆素及丁炔二醇等。
这些物质进入环境,必定会对人类健康及生态环境产生严重的危害[2]。
三. 电镀废水的危害电镀废水中的污染物较为复杂,水质成分不易控制,但总的来讲,可分为重金属离子废水、酸碱废水及含油脂类废水等,表现的成分却常常是同时含有多种污染物。
其中有毒有害的物质有镉、铅、铬、镍、锡、锌、酸、碱、悬浮物、石油类物质、含氮化合物、表而活性剂及磷酸盐等[3]。
另外目前采用氰化电镀工艺的厂家,其电镀废水中含有大量的氰化物。
电镀废水未经处理排放,会污染饮用水和工业用水,对生态环境产生危害; 酸碱废水会破坏水中微生物的生存环境,影响正常水源的酸碱度; 含氰废水毒性很大,微量就能致人死亡; 重金属离子属于致癌、致畸或致突变的剧毒物质,如果大量含有重金属离子的电镀废水不经处理直接排放,会通过食物链,在人体内富集而导致严重的健康问题,其中铬、镉和铜可导致肺癌; Cr( Ⅳ) 的毒性较镉次之,但人体若大量摄入能够引起急性中毒,长期摄入也能引起慢性中毒; 镍和铅在人体内有蓄积作用,长期摄入会引起慢性中毒。
镉、铬、铅及铝四种物质均为国家一类有害物质,铜、锌毒性相对较小,是国家二类有害物质。
日本震惊世界的水俣病和骨痛病就分别由重金属汞和镉引起的[4]; 有机物( 氨氮、磷酸盐等) 进入水体会引起富营养化,导致水中生物大量死亡。
氰化物是剧毒物质,最高允许排放质量浓度为0.3mg /L[5],氰化物中毒治愈后,还可能发生神经系统后遗症。
四. 电镀废水处理现状1.化学法化学法是借氧化还原反应或中和沉淀反应将 有毒有害的物质分解为无毒、无害的物质或将重金 属经沉淀和上浮法从废水中除去。
化学法处理电 镀废水,是目前国内外应用最广泛的电镀废水处理 方法,技术上较为成熟。
化学法包括化学还原法,氧化破氰法,沉淀法 等,是一种传统和应用广泛的处理电镀废水方法, 具有投资少、处理成本低、操作容易掌握等特点,能承受大水量和高浓度负荷冲击,可适用各类电镀废水治理[6]。
电镀废水的治理在国内外普遍受到重视 ,对电镀废水治理方法和工艺的研究也很多。
我国家目前法、蒸发浓缩法、电解法、离子交换法、吸附法、膜分法等。
从近几十年的国内外电镀废水处理技术发展趋势来看 , 电镀废水有 80 %采用化学法处理, 化学法处理电镀废水, 是目前国内外应用最广泛的电镀废水处理技术 , 技术上较为成熟。
化学法包括沉淀法、氧化还原法、铁氧体法等, 是一种传统和应用广泛的处理电镀废水方法[7]。
2.含氰废水的处理氯系处理法分为 2 个阶段 :第 1 阶段是将氰化,毒性小得多;第 2 阶段是将氰酸盐进 —步氧化分解成二氧化碳和氮气。
氯系处理含氰废水的氧化剂为液氯、次氯酸钠、二氧化氯等。
在去除氰的同时利用氧化还原原理, 还可除去水中的部分阴离子, 如-2S 丶32-SO 丶-3NO 和部分阳离子 , 如+2e F 丶+2n M 丶+2i N 。
一级将氰氧化 CNO - , 第二级再将 CNO - 氧化为,CO2 和 N2 。
由于第二阶段反应慢 , 需要加入亚铜离子作为催化剂。
臭氧处理含氰废水, 处理水质好 , 不存在氯氧化法的余氯问题 , 污泥少 , 但电耗大 , 设备投资高 , 工程实际应用较少[8]。
3.含铬废水处理含铬废水的处理方法有铁氧体法、亚硫酸盐还 原法、硫酸亚铁-石灰法等。
1)铁氧体法 铁氧体法处理含铬废水是向废水中投加硫酸亚铁, 使废水中的六价铬还原成三价铬, 然后投碱调整 废水 pH 值 , 使废水中的三价铬以及其他重金属离子(以 M n+表示)发生共沉淀现象。
在共沉淀时, 溶解于水中的重金属离子进入铁氧体晶体中, 生成复合的铁氧体。
采用铁氧体法一般侧重于处理六价铬、镍、铜、锌等重金属离子废水。
铁氧体法处理含铬废水的特点是 :硫酸亚铁来源广、价格低、处理设备简单、污泥不会引起二次污染, 但试剂投加量大, 产生的污泥量大, 污泥制作铁氧体时技术条件难控制, 能耗高, 处理成本高[9]。
2)亚硫酸盐还原法用亚硫酸盐处理含铬废水 , 主要是在酸性条件下, 使废水中的六价铬还原成三价铬 , 然后调整 pH 值, 使其形成氢氧化铬沉淀而除去, 废水得到净化。
常用的亚硫酸盐有亚硫酸氢钠、亚硫酸钠、焦亚硫酸钠。
该方法的特点是 :处理后水能达到排放标准, 并能回收利用氢氧化铬 , 设备和操作较简单。
化学法具有技术成熟、投资小、费用低、适应性强、自动化程度高等诸多优点 , 适用于各类电镀金属废水处理。
然而 , 化学法处理电镀废水虽然有效, 但其缺点也是显而易见的:首先 , 化学法会产生大量的污泥难以处理;另外 , 由于化学法要向水中加入大量化学药剂 , 使出水的含盐量高 , 难以回用, 如果出水外排不仅有可能造成二次污染 , 还浪费了宝贵的水资源。
如果采取化学精处理技术 , 提高出水品质 , 这部分水就有可能重复使用。
所谓化学精处理是在普通化学法基础上优化处理过程, 使废水达到比环保标准更高的质量, 以利于回收利用。
通过化学精处理回收废水的技术要点为:a.选择合理的工艺流程 , 避免重复加药, 降低废水含盐量 ;b.采用 pH/ORP 自控技术 , 准确投药 , 避免药剂过量 ;c.不同性质废水合理分道, 确保废水处理后达标;d.强化后处理过程 , 在达标基础上增加末端的 pH 精调、精密过滤, 必要时增加活性炭过滤 ;e.必要时将成分简单易于处理的废水与复杂的废水(如有机物含量高、色度高、沉淀困难等)分开处理, 仅对前者进行强化的后处理, 以保证回用水的水质和控制成本[10]。
五.工艺流程该系统由两部分组成,即原水预处理部分和反渗透部分。
漂洗废水→集水池→电镀槽→提升装置→预处理装置↓回用漂洗 ←透过液膜分离装置(两级)↓ 电镀槽←蒸发系统 浓缩液水箱1.预处理系统 由原水池、提升泵、袋式滤器、除油过滤器及保安滤器组成。
废水由原水池经过提升泵进入袋式滤器,可以去除大部分固体悬浮物、大分子胶体等。
然后废水经过除油过滤器。
然后废水经过除油过滤器也能去除水中的臭味、色度等。
最后废水进入保安滤的PP 滤芯,对预处理起到最后保安作用,防止管有预处理工序都是为最大限度地防止和延缓污染物在RO 膜面上的沉积,防止胶体物质及固体悬浮微的堵赛以及有机物、微生物、氧化性物质等对膜的破坏,以延缓RO 膜的水解过程,从而使RO 系统在良 好状态下工作。
2.二级RO 系统废水经过预处理后,一级RO 系统的浓缩液由二级输送泵进入二级RO 装置进行循环浓缩。
经过该系统的处理,二级浓缩液再浓缩了10倍以上,并送至蒸发系统,两极 RO 产水均进入RO 产水箱回用到生产线上,形成良性的清洁化生产的循环用水系统。
浓缩液经蒸发后直接回到电镀槽使用。
3.稳定运行反渗透膜系统处理后的出水主要回用于镀镍漂 洗水,由于镀镍液的工作温度为55-60'C ,在电镀 过程中有大量水分蒸发,故在RO 装置浓液排出的 稀镀镍液(量少时)可顺利加入镀镍槽中回用。
4.RO 膜的清洗与维护在正常操作过程中,RO 元件内的膜面会受到无机盐垢、微生物、胶体颗粒和不溶性有机物质的污染,从而引起膜通量下降,从而导致设备成本上升,产品质量下降等一系列问题。
尽管本工艺的预处理系统比较完善,但经过较长时间运行,RO 膜面仍不避免地出现污染问题,这是膜分离技术在实际工程中普遍存在的问题。
因此,在实际工程中,要特别注重对膜的维护一膜污染的控制与清洗。
5. 该法的的工艺改进预处理过程对于酸碱性物质,重金属,-CN ,+6r C 的去除不够完善,需要增加这些污染物的去处工艺,经电镀槽流出的污水,按照不同组分,可利用膜分离技术,使污染物从水中脱去的方法进行处理,具体过程如下:1) 含酸碱物质污水→膜()()回用清水排放沉淀池中和浓水→→→→→%80%20 2) 含+6r C 污水→膜()()回佣清水排放沉淀池加入还原剂还原成浓水→→→→+→%80%203Cr 3) 含-CN 污水→膜()()回用清水排放沉淀池氧化剂浓水→→→→→%80%206. 改进后工艺的特点改进后的工艺对污水处理效果或更好,可以出去污水中大量存在的镉,酸碱性物质,重金属,以及氰等污染物质,大幅减轻对环境的危害,减少对人体的危害,各物质在没有混合之前经过膜处理,不会有膜中毒现象,膜使用寿命延长。