通用焊接工艺规程(普通碳钢、合金钢、不锈钢、铜管焊接)
通用焊接工艺

通用焊接工艺规程1 总则本规程适用于本公司产品所有组焊体的焊接加工,适用于碳钢、低合金钢的二氧化碳气体保护焊工艺。
凡图纸技术文件上无特殊技术要求的,均按本工艺规范执行。
1.2 引用标准GB/T 324-2008 焊缝符号表示法GB/T 985.1-2008 气焊、电弧电弧焊、气体保护焊和高能束焊的推荐坡口GB/T 2900.22-2005 电工名词术语电焊机GB/T 3375-1994 焊接术语GB/T 10045 碳钢药芯焊丝GB/T 8110-2008 气体保护电弧用碳钢、低合金钢焊丝GB/T 8118--2010 电弧焊机通用技术条件HG/T 2537-1993 焊接用二氧化碳2 技术要求2.1 材料2.1.1钢材材质应符合材料标准的规定,并按JB/T3375的规定进行入厂检验,合格后方可使用。
2.1.2二氧化碳气体保护焊常用焊丝为药芯焊丝YJ501-1(E501T-1,相当AWS A5.20 E71T-1C),焊丝应符合GB/T 10045-2001的规定。
焊丝按规定进行入厂检验,合格后方可使用。
2.1.3CO2气体纯度≥99.5%。
3 焊接3.1 焊前准备3.1.1焊接前应熟悉产品图纸和产品作业指导书在小电流焊接时,电弧电压过高,金属飞溅将增多;电弧电压太低,则焊丝容易伸人熔池,使电弧不稳。
在大电流焊接时,若电弧电压过大,则金属飞溅增多,容易产生气孔;电压太低,则电弧太短,使焊缝成形不良。
3.2.2气体流量二氧化碳气体流量与焊接电流、焊接速度、焊丝伸出长度及喷嘴直径等有关。
气体流量应随焊接电流的增大、焊接速度的增加和焊丝伸出长度的增加而加大。
一般二氧化碳气体流量的范围为8~25L/min。
如果二氧化碳气体流量太大,由于气体在高温下的氧化作用,会加剧合金元素的烧损,减弱硅、锰元素的脱氧还原作用,在焊缝表面出现较多的二氧化硅和氧化锰的渣层,使焊缝容易产生气孔等缺陷;如果二氧化碳气体流量太小,则气体流层挺度不强,对熔池和熔滴的保护效果不好,也容易使焊缝产生气孔等缺陷。
通用焊接工艺规程(普通碳钢、合金钢、不锈钢、铜管焊接)

通用焊接工艺规范1 碳素钢、合金钢及不锈钢的焊接1.1焊前准备1.1.1 焊缝的坡口形式和尺寸应符合设计文件的规定,当无规定时,符合本规范附录A.0.1的规定.1.1.2 焊件的坡口加工宜采用机械方法,也可采用等离子弧、氧乙炔焰等热加工方法,在采用热加工方法加工坡口后,必须除去坡口表面的氧化皮、熔渣及影响接头质量的表面层,并应将凹凸不平处打磨平整。
1.1.3 焊件组焊前应将坡口及其两侧表面不小于20 mm范围内的油、漆、垢、锈、毛刺及镀锌层等清除干净,不得有裂纹、夹层、加工损伤、毛刺及火焰切割熔渣等缺陷。
油污清理方法如下,首先用丙酮或四氯化碳等有机溶剂擦洗,然后用不锈钢丝刷清理至露出金属光泽,使用的钢丝刷应定期进行脱脂处理。
1.1.4 管子或管件、筒体对接焊缝组对时,内壁应齐平,内壁错边量不宜超过管壁厚度的10%,且不应大于2mm;1.1.5 焊缝的设臵应避开应力集中区,便于焊接和热处理,并应符合下列规定:(1)钢板卷筒或设备、容器的筒节与筒节、筒节与封头组对时,相邻两纵向焊缝间的距离应大于壁厚的3倍,且不应小于100 mm,同一筒节上两相邻纵缝间的距离不应小于200 mm;(2)除焊接及成型管件外的其他管子对接焊缝的中心到管子弯曲起点的距离不应小于管子外径,且不应小于l00 mm;管子对接焊缝与支、吊架边缘之间的距离不应小于50 mm。
同一直管段上两对接焊缝中心面间的距离:当公称直径大于或等于150mm时不应小于150mm;公称直径小于150mm时不应小于管子外径;(3)不宜在焊缝及其边缘上开孔。
(4)不锈钢焊件焊接部位两侧各l00 mm范围内,在施焊前应采取防止焊接飞溅物粘污焊件表面的措施:可将石棉置于焊接部位两侧等。
1.1.6 焊条、焊丝在使用前应按规定进行烘干、保温,并应在使用过程中保持干燥。
焊丝使用前应清除其表面的油污、锈蚀等。
常用焊材烘干温度及保持时间见表4。
表4 常用焊材烘干温度及保持时间接上表:1.2焊接工艺要求1.2.1 碳素钢及合金钢焊接材料的选用,应符合设计文件的规定,当无规定时,符合本规范附录B第 B.0.1条及第B.0.2条的规定。
不锈钢管焊接工艺规程
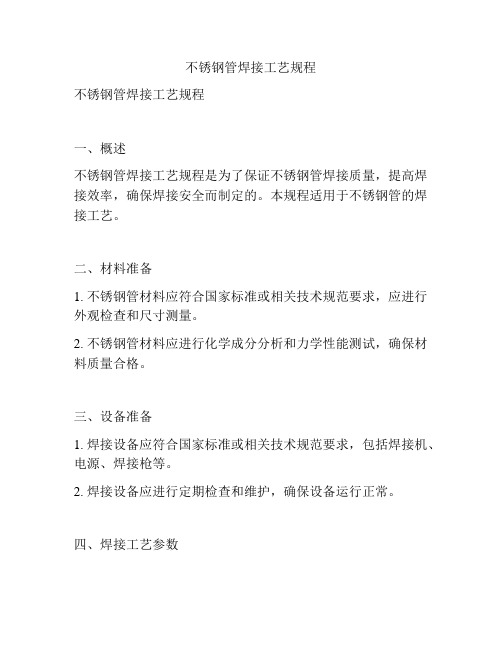
不锈钢管焊接工艺规程不锈钢管焊接工艺规程一、概述不锈钢管焊接工艺规程是为了保证不锈钢管焊接质量,提高焊接效率,确保焊接安全而制定的。
本规程适用于不锈钢管的焊接工艺。
二、材料准备1. 不锈钢管材料应符合国家标准或相关技术规范要求,应进行外观检查和尺寸测量。
2. 不锈钢管材料应进行化学成分分析和力学性能测试,确保材料质量合格。
三、设备准备1. 焊接设备应符合国家标准或相关技术规范要求,包括焊接机、电源、焊接枪等。
2. 焊接设备应进行定期检查和维护,确保设备运行正常。
四、焊接工艺参数1. 焊接电流和电压应根据不锈钢管的材料和壁厚确定,确保焊接质量。
2. 焊接速度应根据不锈钢管的材料和壁厚确定,确保焊缝的均匀性。
3. 焊接温度应控制在合适的范围内,避免过高或过低导致焊接缺陷。
五、焊接操作1. 焊工应熟悉不锈钢管的焊接工艺要求和操作规程,严格按照规程进行操作。
2. 焊工应佩戴防护设备,包括焊接面罩、手套等,确保个人安全。
3. 焊工应注意焊接过程中的熔渣和气孔等缺陷,及时进行修补或更换焊条。
六、焊后处理1. 焊接完成后,应对焊缝进行外观检查和尺寸测量,确保焊缝质量合格。
2. 焊缝表面应进行清理和抛光处理,使其达到要求的光洁度。
3. 焊缝应进行无损检测,确保焊接质量合格。
七、质量控制1. 焊接过程中应进行质量控制,包括焊缝外观、尺寸、化学成分等方面的检查。
2. 焊接过程中出现问题时,应及时进行调整和修正,确保焊接质量。
3. 焊接完成后应进行质量评定,确保焊接质量符合要求。
八、安全措施1. 在焊接过程中应注意防止火花飞溅和烟尘产生,保持工作环境清洁。
2. 焊接过程中应注意防止电击和火灾等事故的发生,确保人身安全。
3. 在操作不锈钢管时应注意防止划伤和损坏管材,确保材料完好。
九、总结不锈钢管焊接工艺规程是确保不锈钢管焊接质量的重要文件,通过严格执行规程要求,可以提高焊接效率,降低焊接风险,保证焊接安全。
各相关单位和人员应严格按照本规程要求进行操作,共同维护不锈钢管焊接质量。
不锈钢焊接工艺规程1
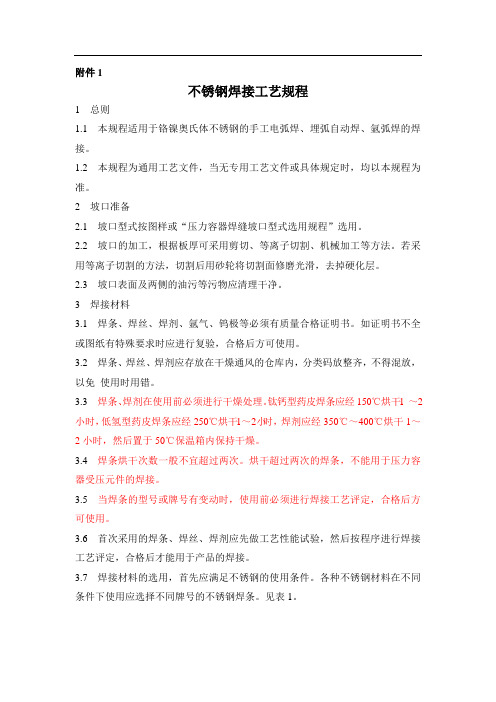
附件1不锈钢焊接工艺规程1 总则1.1 本规程适用于铬镍奥氏体不锈钢的手工电弧焊、埋弧自动焊、氩弧焊的焊接。
1.2 本规程为通用工艺文件,当无专用工艺文件或具体规定时,均以本规程为准。
2 坡口准备2.1 坡口型式按图样或“压力容器焊缝坡口型式选用规程”选用。
2.2 坡口的加工,根据板厚可采用剪切、等离子切割、机械加工等方法。
若采用等离子切割的方法,切割后用砂轮将切割面修磨光滑,去掉硬化层。
2.3 坡口表面及两侧的油污等污物应清理干净。
3 焊接材料3.1 焊条、焊丝、焊剂、氩气、钨极等必须有质量合格证明书。
如证明书不全或图纸有特殊要求时应进行复验,合格后方可使用。
3.2 焊条、焊丝、焊剂应存放在干燥通风的仓库内,分类码放整齐,不得混放,以免使用时用错。
3.3 焊条、焊剂在使用前必须进行干燥处理。
钛钙型药皮焊条应经150℃烘干1~ 2小时,低氢型药皮焊条应经250℃烘干1~ 2小时,焊剂应经350℃~400℃烘干1~2小时,然后置于50℃保温箱内保持干燥。
3.4 焊条烘干次数一般不宜超过两次。
烘干超过两次的焊条,不能用于压力容器受压元件的焊接。
3.5 当焊条的型号或牌号有变动时,使用前必须进行焊接工艺评定,合格后方可使用。
3.6 首次采用的焊条、焊丝、焊剂应先做工艺性能试验,然后按程序进行焊接工艺评定,合格后才能用于产品的焊接。
3.7 焊接材料的选用,首先应满足不锈钢的使用条件。
各种不锈钢材料在不同条件下使用应选择不同牌号的不锈钢焊条。
见表1。
表1 焊接奥氏体不锈钢选用焊条举例3.8 埋弧自动焊、氩弧焊用的焊丝,其成分与性能应与母材相近。
4 焊工4.1 凡参加铬镍奥氏体不锈钢焊接的焊工,应熟悉不锈钢焊接的要领,并经焊工考试合格。
焊工考试按国家劳动人事部颁发的《锅炉压力容器焊工考试规则》进行。
4.2 焊工所施焊的项目必须与焊工合格证的项目相符。
禁止无项操作。
4.3 压力容器主体焊缝、重要接管及人孔处的焊缝,焊工必须遵照焊接工艺卡的要求,焊后在所焊部位附近留有标记,并认真填写施焊记录。
焊接通用工艺规程

焊接通用工艺规程目录一:总则---------------------------------------------------3 二:焊工 ------------------------------------------------- 3 三焊接工艺评定 -----------------------------------------5 四:焊接材料-----------------------------------------------9 五:焊前准备----------------------------------------------11 六:焊接--------------------------------------------------146.1预热: --------------------------------------------146.2手工电弧焊焊接:-----------------------------------156.3 埋弧自动焊焊接:----------------------------------166.4不锈钢材料焊接:----------------------------------186.5手工钨极氩弧焊:-----------------------------------196.6换热器管束焊接:-----------------------------------216.7管一板自动焊焊接:---------------------------------236.8 CO2气体保护焊:-----------------------------------256.9复合钢的焊接 -------------------------------------29 七:焊工钢印打印位置规定----------------------------------43 八:焊缝外观质量检查标准--------------------------------- 45 九:焊缝返修规定----------------------------------------- 47 十:焊接材料选用原则--------------------------------------49一:总则1.1本规程适用于我厂碳素钢、低合金钢、珠光体耐热钢等金属材料手工电弧焊,钨极氩弧焊,换热管管束焊接,管板自动焊,复合钢的焊接,气体保护焊和埋弧自动焊。
焊接通用规程

一、气焊通用工艺规程1. 主题内容和适用范围本标准规定了气焊操作规程。
本标准适用于本公司金属结构件的气焊。
2. 引用标准YB/JQ10/15 《钢铁企业制造通用技术条件焊接结构件》。
3. 准备工作3.1 熟悉图纸和工艺要求,了解材质、规格、焊肉等工艺规程。
3.2 准备好氧、乙炔气。
3.2.1氧气含量不低于99.2%,水份不超过10ml/瓶;乙炔的杂质符合标准,磷化氢≤0.08%硫化物≤0.15,电石出气率≥235升/公斤。
3.2.2 使用临时乙炔发生器时。
发生器至少离火源10米,取暖设备1米,发生器内要保持足够的干净水,水封回火防止器要保持一定的水位。
3.2.3 发生器内用的电石按规定的一次加入量添加,块度为50—80mm,不得加电石粉末。
3.2.4氧气瓶严禁沾油,且装表前要放气吹去接下来头处的尘土杂物。
移动气瓶应避免撞击,禁止用起重机吊运。
3.3 检查焊炬、管带及氧气表、乙炔表是否正常,连接处是否紧密。
3.4 清理操作场地,检查焊件的装配质量。
焊缝间隙应均匀一致,符合要求,清除干净焊缝两侧10mm内的铁锈、油污,焊缝表面应进行打磨。
4. 气焊工艺4.1 根据工艺要求选用焊丝、焊剂,焊丝不允许有油污和铁锈。
对无要求的,可根据焊件的材质和板厚选用,焊丝直径可参考表1。
表1 焊丝直径与焊件厚度的关系4.2 根据焊件厚度选择焊咀型号工艺参数(表2,表3)4.3 根据焊件材质选择火焰类型。
4.3.1 碳化焰用于气焊高碳钢、高速钢、硬质合金、铝。
青铜及铸铁。
4.3.2 中性焰用于气焊低碳钢、低合金钢、高铬钢、不锈钢、紫铜、锡青铜、铝及铝合金、镁合金。
4.3.3 氧化焰用于气焊黄铜、锰钢。
镀锌铁皮等。
4.4 气焊时焊咀与工件之间要倾斜一定的角度,大小取决于板厚(表4)。
对于熔点高,导热性好的材料,角度要大些;始焊时为迅速加热焊件,应用80o—90o的角,然后再逐渐减小,收尾时应减小倾角,焊咀提高。
表4 焊咀倾角4.5 焊时先将金属加热到熔融状态,再填充焊丝,焊丝与焊件表面倾斜20 o—40o,且焊时焊咀和焊丝要交叉均匀摆动,以避免焊接缺陷。
通用焊接工艺规程(普通碳钢、合金钢、不锈钢、铜管焊接)

通用焊接工艺规范1 碳素钢、合金钢及不锈钢的焊接1.1焊前准备1.1.1 焊缝的坡口形式和尺寸应符合设计文件的规定,当无规定时,符合本规范附录A.0.1的规定.1.1.2 焊件的坡口加工宜采用机械方法,也可采用等离子弧、氧乙炔焰等热加工方法,在采用热加工方法加工坡口后,必须除去坡口表面的氧化皮、熔渣及影响接头质量的表面层,并应将凹凸不平处打磨平整。
1.1.3 焊件组焊前应将坡口及其两侧表面不小于20 mm范围内的油、漆、垢、锈、毛刺及镀锌层等清除干净,不得有裂纹、夹层、加工损伤、毛刺及火焰切割熔渣等缺陷。
油污清理方法如下,首先用丙酮或四氯化碳等有机溶剂擦洗,然后用不锈钢丝刷清理至露出金属光泽,使用的钢丝刷应定期进行脱脂处理。
1.1.4 管子或管件、筒体对接焊缝组对时,内壁应齐平,内壁错边量不宜超过管壁厚度的10%,且不应大于2mm;1.1.5 焊缝的设臵应避开应力集中区,便于焊接和热处理,并应符合下列规定:(1)钢板卷筒或设备、容器的筒节与筒节、筒节与封头组对时,相邻两纵向焊缝间的距离应大于壁厚的3倍,且不应小于100 mm,同一筒节上两相邻纵缝间的距离不应小于200 mm;(2)除焊接及成型管件外的其他管子对接焊缝的中心到管子弯曲起点的距离不应小于管子外径,且不应小于l00 mm;管子对接焊缝与支、吊架边缘之间的距离不应小于50 mm。
同一直管段上两对接焊缝中心面间的距离:当公称直径大于或等于150mm时不应小于150mm;公称直径小于150mm时不应小于管子外径;(3)不宜在焊缝及其边缘上开孔。
(4)不锈钢焊件焊接部位两侧各l00 mm范围内,在施焊前应采取防止焊接飞溅物粘污焊件表面的措施:可将石棉置于焊接部位两侧等。
1.1.6 焊条、焊丝在使用前应按规定进行烘干、保温,并应在使用过程中保持干燥。
焊丝使用前应清除其表面的油污、锈蚀等。
常用焊材烘干温度及保持时间见表4。
表4 常用焊材烘干温度及保持时间接上表:1.2焊接工艺要求1.2.1 碳素钢及合金钢焊接材料的选用,应符合设计文件的规定,当无规定时,符合本规范附录B第 B.0.1条及第B.0.2条的规定。
碳钢和不锈钢管子焊接工艺规范.doc

碳钢和不锈钢管子焊接工艺规范1 范围本规范规定了CO2气体保护焊和钨极氩弧焊用于管子焊接的焊接前准备、人员、工艺要求、工艺过程和检验。
本规范适用于管子与管子、管子与附件之间的对接和角接接头,焊接时,可采用药芯焊丝CO2气体保护焊,也可采用钨极氩弧焊。
焊接位置为管子水平转动位置和管子水平固定位置。
2 规范性引用文件《焊缝返修通用工艺》3 焊接前准备3.1 CO2半自动或自动焊焊丝选用,见表1。
表1 CO2半自动或自动焊焊丝选用3.2 钨极氩弧焊焊丝的选用,见表2。
表2 钨极氩弧焊焊丝的选用3.3 保护气体无论是药芯焊丝CO2气体保护焊所用的CO2,还是钨极氩弧焊所用的纯Ar气体,均应符合气体质量使用标准,其纯度达99.9 %。
3.4 焊接设备20mm范围内)作清理,并去除油、锈等污物。
3.6.2 对于碳钢管的锈蚀,应用钢刷打磨除锈。
不锈钢管应用丙酮进行清理。
3.6.3 坡口加工残留毛刺应除去,并应重新清理。
4 人员凡从事该工艺焊接的焊工,必须经过船级社资格认可考试,考试合格并经船级社认可后,方能参与相应等级项目的焊接。
5 工艺要求5.1 装配要求5.1.1 装配工在安装管子对接时,首先要检查管子接口同心度,防止安装错边。
5.1.2 管子对接定位可选用定位“马”固定,或在焊缝内作定位焊固定。
5.1.3 装配间隙,见表3。
表3 装配间隙5.2 对于要求单面焊双面成型的管子拼缝,焊前,有色金属管内应充氩气保护,并采用钨极氩弧焊(TIG焊)打底。
5.3 船上安装要求单面焊双面成型的管子拼缝,因无法进行充气保护,焊接中应仔细观察熔池,以确保背面焊缝质量。
对于不锈钢管,焊后,管内要作钝化处理。
5.4 焊接参数为确保管子的焊接质量,焊接时应参照表4的焊接参数进行。
表4 焊接参数6 工艺过程6.1 焊前充气焊前先用铝铂胶带对所焊管子接缝两端面及坡口面封住(对于较长管子可采用海绵、泡沫、可溶纸等工具做成堵板,设置于距焊缝150mm~200mm的两侧,造成一个气室),管子一端充氩气,管子另一端开一个约5mm的小孔排气,等管子内空气排尽并被氩气充满后,方可开始焊接。
- 1、下载文档前请自行甄别文档内容的完整性,平台不提供额外的编辑、内容补充、找答案等附加服务。
- 2、"仅部分预览"的文档,不可在线预览部分如存在完整性等问题,可反馈申请退款(可完整预览的文档不适用该条件!)。
- 3、如文档侵犯您的权益,请联系客服反馈,我们会尽快为您处理(人工客服工作时间:9:00-18:30)。
通用焊接工艺规范1 碳素钢、合金钢及不锈钢的焊接1.1焊前准备1.1.1 焊缝的坡口形式和尺寸应符合设计文件的规定,当无规定时,符合本规范附录A.0.1的规定.1.1.2 焊件的坡口加工宜采用机械方法,也可采用等离子弧、氧乙炔焰等热加工方法,在采用热加工方法加工坡口后,必须除去坡口表面的氧化皮、熔渣及影响接头质量的表面层,并应将凹凸不平处打磨平整。
1.1.3 焊件组焊前应将坡口及其两侧表面不小于20 mm范围内的油、漆、垢、锈、毛刺及镀锌层等清除干净,不得有裂纹、夹层、加工损伤、毛刺及火焰切割熔渣等缺陷。
油污清理方法如下,首先用丙酮或四氯化碳等有机溶剂擦洗,然后用不锈钢丝刷清理至露出金属光泽,使用的钢丝刷应定期进行脱脂处理。
1.1.4 管子或管件、筒体对接焊缝组对时,内壁应齐平,内壁错边量不宜超过管壁厚度的10%,且不应大于2mm;1.1.5 焊缝的设臵应避开应力集中区,便于焊接和热处理,并应符合下列规定:(1)钢板卷筒或设备、容器的筒节与筒节、筒节与封头组对时,相邻两纵向焊缝间的距离应大于壁厚的3倍,且不应小于100 mm,同一筒节上两相邻纵缝间的距离不应小于200 mm;(2)除焊接及成型管件外的其他管子对接焊缝的中心到管子弯曲起点的距离不应小于管子外径,且不应小于l00 mm;管子对接焊缝与支、吊架边缘之间的距离不应小于50 mm。
同一直管段上两对接焊缝中心面间的距离:当公称直径大于或等于150mm时不应小于150mm;公称直径小于150mm时不应小于管子外径;(3)不宜在焊缝及其边缘上开孔。
(4)不锈钢焊件焊接部位两侧各l00 mm范围内,在施焊前应采取防止焊接飞溅物粘污焊件表面的措施:可将石棉置于焊接部位两侧等。
1.1.6 焊条、焊丝在使用前应按规定进行烘干、保温,并应在使用过程中保持干燥。
焊丝使用前应清除其表面的油污、锈蚀等。
常用焊材烘干温度及保持时间见表4。
表4 常用焊材烘干温度及保持时间接上表:1.2焊接工艺要求1.2.1 碳素钢及合金钢焊接材料的选用,应符合设计文件的规定,当无规定时,符合本规范附录B第 B.0.1条及第B.0.2条的规定。
1.2.2 异种钢材焊接时的焊条选用。
(1) 当两侧母材均为非奥氏体钢或均为奥氏体钢时,可根据合金含量较低一侧母材或介于两者之间的选用焊材;(2) 当两侧母材之一为奥氏体钢时,应选用25Cr—13Ni型或含镍量更高的焊材。
1.2.3 定位焊缝应符合下列规定:(1)焊接定位焊缝时,应采用与根部焊道相同的焊接材料和焊接工艺。
(2)定位焊缝的长度、厚度和间距,应能保证焊缝在正式焊接过程中不致开裂。
(3)在焊接根部焊道前,应对定位焊缝进行检查,如发现有夹渣、气孔和裂纹等缺陷,应将缺陷部分除尽后方可施焊。
1.2.4 与母材焊接的工卡具其材质宜与母材相同或同一类别号,应在整个焊缝焊接及热处理完毕并经检验合格后方可拆除。
拆除工卡具时不应损伤母材,拆除后应将残留焊疤打磨修整至与母材表面齐平。
1.2.5 严禁在坡口之外的母材表面引弧和试验电流,并应防止电弧擦伤母材。
1.2.6 对含铬量大于或等于3%或合金元素总含量大于5%的焊件,氩弧焊打底焊接时,焊缝内侧应充氩气或其他保护气体,或采取其他防止内侧焊缝金属被氧化的措施。
1.2.7 焊接时应采取合理的施焊方法和施焊顺序。
1.2.8 施焊过程中应保证起弧和收弧处的质量,收弧时应将弧坑填满。
多层焊的层间接头应错开。
1.2.9 除工艺或检验要求需分次焊接外,每条焊缝宜一次连续焊完,当因故中断焊接,再次焊接前应检查焊层表面,确认无裂纹后,方可按原工艺要求继续施焊。
1.2.10 多层焊每层焊完后,应立即对层间进行清理,并进行外观检查,发现缺陷消除后方可进行下一层的焊接。
1.2.11 低温钢、奥氏体不锈钢、耐热耐蚀高合金钢以及奥氏体与非奥氏体异种钢接头焊接时应符合下列规定:在焊接作业指导书规定的范围内,在保证焊透和熔合良好的条件下,采用小电流、短电弧、快焊速和多层多道焊工艺,并应控制层间温度。
1.2.12 对抗腐蚀性能要求高的双面焊焊缝,与腐蚀介质接触的焊层应最后施焊。
1.2.13 焊接完毕后,应及时将焊缝表面的熔渣及表面飞溅物清理干净。
对奥氏体不锈钢焊缝及其附近表面进行酸洗、钝化处理。
2 铝及铝合金的焊接2.1 焊前准备2.1.1 焊缝的坡口形式和尺寸应符合设计文件的规定,当无规定时,符合本规范附录A.0.2的规定. 切割后的坡口表面应进行清理,并应达到平整光滑、无毛刺和飞边。
焊前清理应符合下列规定:2.1.1.1 施焊前应对焊件坡口、垫板及焊丝进行清理。
清理方法如下,首先用丙酮或四氯化碳等有机溶剂除去表面油污,两侧坡口的清理范围不应小于50 mm。
清除油污后,坡口及其附近的表面用不锈钢丝刷清理至露出金属光泽,使用的钢丝刷应定期进脱脂处理。
2.1.1.2 焊丝去除油污后,应采用化学方法去除氧化膜。
可用5%一10%的Na(OH)溶液,在温度为70℃下浸泡30~60 s,然后水洗,再用15%左右的HN03在常温下浸泡2min,然后用温水洗净,并使其干燥。
2.1.1.3 清理好的焊件和焊丝不得有水迹、碱迹,或被粘污。
2.2 焊接工艺要求2.2.1 手工钨极氩弧焊应采用交流电源,熔化极氩弧焊应采用直流电源,焊丝接正极。
2.2.2 焊接前焊件表面应保持干燥,无特殊要求时可不预热。
2.2.3 焊接前应在试板上试焊,当确认无气孔后再进行正式焊接。
2.2.4 宜采用大电流快速施焊法,焊丝的横向摆动不宜超过其直径的3倍。
2.2.5 引弧宜在引弧板上进行,纵向焊缝宜在熄弧板上熄弧。
引弧板和熄弧板的材料应与母材相同。
2.2.6 手工钨极氩弧焊的焊丝端部不应离开氩气保护区,焊丝与焊缝表面的夹角宜为15°,焊枪与焊缝表面的夹角宜为80°~90°。
2.2.7 多层焊时宜减少焊接层数,层间温度宜冷却至室温,且不应高于65℃。
层间的氧化铝等杂物应采用机械方法清理干净。
2.2.8 对厚度大于5mm的立向焊缝,宜采用两人双面同步氩弧焊工艺。
2.2.9 当钨极氩弧焊的钨极前端出现污染或形状不规则时,应进行修正或更换钨极。
当焊缝出现触钨现象时,应将钨极、焊丝、熔池处理干净后方可继续进行施焊。
2.2.10 当熔化极氩弧焊发生导电嘴、喷嘴熔入焊缝时,应将该部位焊缝全部铲除,更换导电嘴和喷嘴后方可继续施焊。
2.2.11 手工钨极氩弧焊和熔化极氩弧焊的焊接工艺参数宜符合表7.3.11-l、表7.3.11-2、表7.3.11-3的规定。
手工钨极氩弧焊工艺参数表7.3.11.-1半自动熔化极氩弧焊工艺参数表7.3.11-2自动熔化极氩弧焊工艺参数表7.3.11-32.2.12 焊件应采用下列防止变形措施:(1)焊接顺序应对称进行,当从中心向外进行焊接时,具有大收缩量的焊缝宜先施焊,整条焊道应连续焊完。
(2)焊件宜进行刚性固定或采取反变形方法,并应留有收缩余量。
3 焊后外观检查3.1 除设计文件有特殊要求的焊缝外,焊缝应在焊完后立即去除渣皮、飞溅物,清理干净焊缝表面,然后进行焊缝外观检查。
3.2 焊接表面应平滑,不应有裂纹、密集气孔、大弧坑、焊丝头、焊穿、深咬边、未熔合,未焊透等缺陷,焊瘤不高于1.5mm。
附录A 焊件的坡口形式和尺寸A.0.1 钢焊件坡口形式和尺寸应符合表A.0.1的规定。
钢焊件坡口形式和尺寸表A.0.1续表A.0.1A.0.2 铝及铝合金坡口形式和尺寸应符合表A.0.2的规定。
铝及铝合金被口形式和尺寸表A.0.2续表A.0.2附录B 焊接材料的选用B.0.1 同种钢焊接选用的焊接材料宜符合表D.0.1的规定。
同种钢焊接选用的焊接材料表D.0.1B.0.2 异种钢焊接选用的焊接材料宜符合表B.0.2的规定。
异种钢焊接选用的焊接材料表B.0.2B.0.3 铝及铝合金焊丝的选用宜符合表D.0.3的规定。
铝及铝合金焊丝的选用表B.0.3续表B.0.32、铜管加工和焊接工艺标准1、铜管加工工艺加工前的一般要求:1.1 密封冷媒系统要求管件内部表面清洁、无氧化、无水、无油等;1.2 不允许使用带有裂纹、不圆变形、扭曲、可见砂眼、喷墨(铜管厂检测有缺陷的标记)、发黑(氧化)等缺陷的铜管。
2、铜管加工要求总则2.1 管路的加工按设计图纸进行,形状、尺寸应符合设计要求;2.2 断口处直径改变应在铜管标准直径的2%以内,且断口不允许有飞边,毛刺;管件要脱油、去污、无铜屑,内外表面光洁,不许有油污、伤痕、氧化皮;焊接过程必须充氮保护,焊后用0.3~0.5MPa的干燥压缩空气吹净内部。
3、铜管下料、去毛刺使用工具:割管刀,有效直尺,铜管修边器3.1 铜管需定位固定后,再用割刀拆下,要保证割口平齐,不变形切割过程中,铜管均匀进给,以保证管口圆滑下料后必须用铜管修边器对端口去毛刺,去毛刺后,必须用0.3~0.5MPa的干燥压缩空气吹掉管内外的铜屑、杂物。
4、铜管弯曲使用工具:手工弯管机。
根据图纸和铜管的外形,选择合适的弯管机4.1 清除弯管机范围内一切可能影响弯管机运转的杂物,保证设备运行畅通无阻。
每次弯曲前需调整模具或参数,并进行空转试弯,确认设备正常后进行加工。
一般铜管的弯曲半径参照下表需弯管的铜管不能是硬质管,弯曲后的铜管不得有皱纹、破裂现象。
弯管后应把管子内部的油渍等异物清除掉。
5、喇叭口制作将已制作合格的铜管先套入对应的铜钠子,再放入铜管喇叭口扩口专用工具相对应的孔中,放入时铜管扩口端高出扩口器夹具面0.5~1mm,夹紧扩口器夹具,在扩口器顶尖上涂少许空调冷冻油,然后将手柄顺时针旋紧,再旋紧四分之三圈,退四分之一圈,如此反复进行,直到所扩口成90±2°扩成喇叭口后,喇叭口的接触面应光滑平整,且厚度均匀一致;不应有裂纹、损伤、麻点皱折等不足;喇叭口不应有偏斜不正等现象。
6、铜管焊接工艺铜管钎焊原理6.1 钎焊是利用液态钎料填满钎焊金属结合面的间隙面形成牢固接头的焊接方法,其工艺过程必须具备两个基本条件。
(1)液态钎料能润湿钎焊金属并能致密的填满全部间隙;(2)液态钎料与钎焊金属进行必要的物理、化学反应达到良好的金属间结合。
6.2 液态钎料的填缝原理:钎焊时,液态钎料是靠毛细作用在钎缝间流动的,这种液态钎料对母材金属的浸润和附着的能力称之为润湿性。
液态钎料对钎焊金属的润湿性越好,则毛细作用越强,因此填缝会更充分。
6.3 影响钎料润湿性的因素有以下方面:(1)钎料和焊件金属成分影响若钎料和钎焊金属在液态不互溶和固态不互溶,也不形成化合物,则它们之间的润湿性很差;若能液态互溶、固态互溶或形成化合物,则它们之间的润湿性很好。
(2)钎焊温度的影响温度的升高,可明显地改善润湿性。