通用焊接工艺
完整版通用焊接工艺操作流程
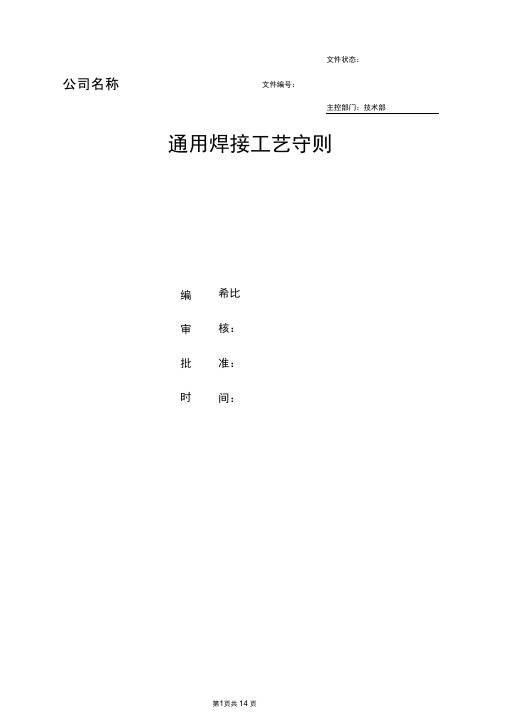
5、关于定位焊:
(1)点焊之前应检查装配质量,对装配不合格的部件不要点焊;
(2)不焊接的地方不能点焊;
(3) 定位焊位置:应避开焊缝拐弯处,且离焊缝端部20mm以上;
(4)焊点长度及间距:10〜20mm间距150〜300mm(可根据具体接头灵活掌握)
(5) 如果点焊是立焊,则焊接方向必须是由下往上焊。
图5不合格的角焊缝
(5)对接焊缝余高的规定见表7(单位:mm):
表7对接焊缝余高的要求
被焊件厚度(较薄件)
焊缝余高R
t<12.7
0WRW2.4
12.7VtW25
0WRW3.2
t>25
0WRW4.0
基本符号1基本符号标在基准线的实线侧时焊缝在接头的箭头侧2基本符号标在基准线的虚线侧时焊缝在接头的非箭头侧3对称焊缝或双面焊缝时可不画虚线基本符号标在基准线的两侧焊缝形状尺寸1焊缝截面尺寸标在基本符号的左侧2焊缝长度尺寸标在基本符号的右侧3坡口角度根部间隙等标在基本符号的上侧或下侧其它相冋焊缝数量符号焊接方法代号及其它要求标在尾部右侧3焊缝尺寸符号4焊缝图形的辅助符号和补充符号口焊接图形号辅助符号1平面符号符号说明焊缝表面要齐平通过打磨或加工焊缝表面凹陷2凹面符号3凸面符号焊缝表面凸起周围焊缝符号表示环绕工件焊一圈三面焊缝符号表示三面有焊缝现场焊接符号表示在装配现场进行焊接注
用于自动焊
手工电弧焊
交流焊机
BX3-500 ZX7-500
:各种钢的焊接
氩弧焊
氩弧焊机
YM-350GE2
:铝合金、不锈钢
直流反接
四、焊前准备:
1、气保焊机:应根据焊丝类别(实芯/药芯)和规格(①1.0、①1.2、①1.6)
通用焊接工艺规程(普通碳钢、合金钢、不锈钢、铜管焊接)

通用焊接工艺规范1 碳素钢、合金钢及不锈钢的焊接1.1焊前准备1.1.1 焊缝的坡口形式和尺寸应符合设计文件的规定,当无规定时,符合本规范附录A.0.1的规定.1.1.2 焊件的坡口加工宜采用机械方法,也可采用等离子弧、氧乙炔焰等热加工方法,在采用热加工方法加工坡口后,必须除去坡口表面的氧化皮、熔渣及影响接头质量的表面层,并应将凹凸不平处打磨平整。
1.1.3 焊件组焊前应将坡口及其两侧表面不小于20 mm范围内的油、漆、垢、锈、毛刺及镀锌层等清除干净,不得有裂纹、夹层、加工损伤、毛刺及火焰切割熔渣等缺陷。
油污清理方法如下,首先用丙酮或四氯化碳等有机溶剂擦洗,然后用不锈钢丝刷清理至露出金属光泽,使用的钢丝刷应定期进行脱脂处理。
1.1.4 管子或管件、筒体对接焊缝组对时,内壁应齐平,内壁错边量不宜超过管壁厚度的10%,且不应大于2mm;1.1.5 焊缝的设臵应避开应力集中区,便于焊接和热处理,并应符合下列规定:(1)钢板卷筒或设备、容器的筒节与筒节、筒节与封头组对时,相邻两纵向焊缝间的距离应大于壁厚的3倍,且不应小于100 mm,同一筒节上两相邻纵缝间的距离不应小于200 mm;(2)除焊接及成型管件外的其他管子对接焊缝的中心到管子弯曲起点的距离不应小于管子外径,且不应小于l00 mm;管子对接焊缝与支、吊架边缘之间的距离不应小于50 mm。
同一直管段上两对接焊缝中心面间的距离:当公称直径大于或等于150mm时不应小于150mm;公称直径小于150mm时不应小于管子外径;(3)不宜在焊缝及其边缘上开孔。
(4)不锈钢焊件焊接部位两侧各l00 mm范围内,在施焊前应采取防止焊接飞溅物粘污焊件表面的措施:可将石棉置于焊接部位两侧等。
1.1.6 焊条、焊丝在使用前应按规定进行烘干、保温,并应在使用过程中保持干燥。
焊丝使用前应清除其表面的油污、锈蚀等。
常用焊材烘干温度及保持时间见表4。
表4 常用焊材烘干温度及保持时间接上表:1.2焊接工艺要求1.2.1 碳素钢及合金钢焊接材料的选用,应符合设计文件的规定,当无规定时,符合本规范附录B第 B.0.1条及第B.0.2条的规定。
起重机通用焊接工艺规程
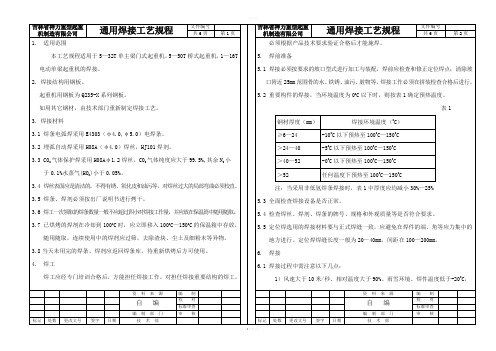
角焊缝质量应符合JB/ZQ\4000. 3中的BK级的规定。
7.2内在质量检查
对重要构件的受拉盖板及腹板受拉部位必须进行射线照相或超声波探伤检验焊缝的内部缺陷。
吉林省神力重型起重机制造有限公司
通用焊接工艺规程
文件编号
吉林省神力重型起重机制造有限公司
通用焊接工艺规程
文件编号
共6页
第1页
共6页
第2页
1.适用范围
本工艺规程适用于5—32T单主梁门式起重机,5—50T桥式起重机,1—16T电动单梁起重机的焊接。
2.焊接结构用钢板。
起重机用钢板为Q235-X系列钢板。
160—180
22—24
150—170
J422φ5.0
直流反接
200—220
24—26
130—140
资料来源
编制
资料来源
编制
自编
校对
自编
校对
标准审查
标准审查
编制部门
审核
编制部门
审核
标记
处数
更改文号
签字
日期
技术部
标记
处数
更改文号
签字
日期
技术部
吉林省神力重型起重机制造有限公司
通用焊接工艺规程
文件编号
吉林省神力重型起重机制造有限公司
3.8当天未用完的焊条、焊剂应返回焊条库,待重新烘烤后方可使用。
4.焊工
焊工应经专门培训合格后,方能担任焊接工作。对担任焊接重要结构的焊工,
必须根据产品技术要求验证合格后才能施焊。
5.焊前准备
5.1焊接必须按要求的坡口型式进行加工与装配,焊前应检查和修正定位焊点;清除坡口附近25mm范围骨的水、铁锈、油污、脏物等,焊接工作必须在拼装检查合格后进行。
焊接通用工艺守则
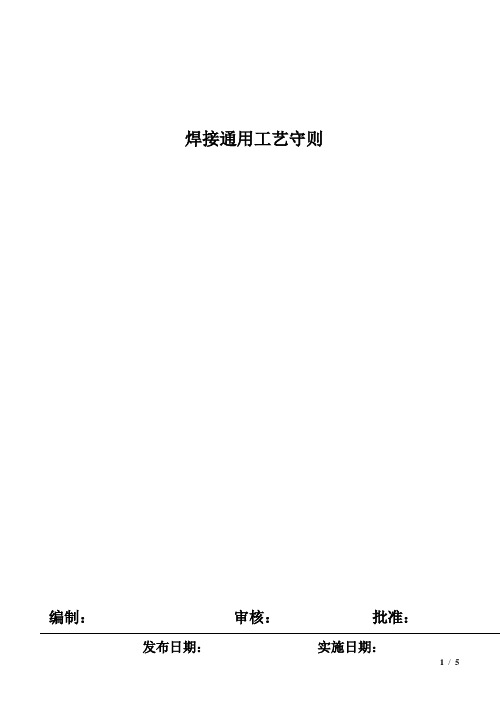
焊接通用工艺守则编制:审核:批准:发布日期:实施日期:焊接通用工艺守则1、工作前,焊(割)工必须穿戴好工作服、劳保鞋、防护眼镜等各种必须的劳动防护用品以防烫伤,伤目等事故。
未持有焊工操作证者不准操作。
学徒工应有师傅带领导。
2、施焊前应检查工作场地10m周围是否有易然易爆物品及影响安全生产的物品,并加以清除,检查焊(割)炬、皮管、接头及气瓶附件等是否良好,必须检查所用设备是否完好后送电。
3、设备应定期保养与维护,(每月保养一次)保证设备运行的准确性、可靠性及安全性。
4、焊前要认清施焊的材质,选用相同或相近牌号的焊条或焊丝进行焊接。
5、16Mn(Q345)板焊接时不允许选用酸性焊条(J422),应选用碱性焊条(J506)或采用二氧化碳气体保护焊。
6、不允许使用锈蚀的焊丝、脱皮和受潮的焊条:使用的焊丝有锈蚀应及时清理锈蚀后方可使用。
7、焊条打开包装后应尽量在一天内用完,中午及用不完的要采取防潮措施进行保存。
如已受潮应进行烘干后方可使用。
酸性焊条烘干温度为200-250度,碱性焊条烘干温度为300-350度。
8、调节电流电压时要在试弧板进行调节,不允许在工件上起弧,焊接前要用钢丝刷、抹布清理好焊缝左右30mm内的铁锈油污等,并喷洒防飞溅液,焊后要注意观察焊缝,发现有焊接缺陷应修补、漏焊的地方应及补焊,要用手砂轮机、铲刀打磨清理好余高、飞溅、焊渣等。
9、在重要结构件焊接时,要使用引弧板起弧,收弧板收弧。
10、焊缝表面不允许有焊接缺陷(气孔、夹渣、裂纹、未溶合、未焊透、咬边、焊偏)等存在。
11、立焊或仰焊焊接时电流为平焊电流的85%。
12、在风速超过2m/s的工作场所(含室内焊接时使用电风扇),使用气体保护焊作业时要使用挡板挡风,以确保焊接工位的风速不超过2m/s的要求,此时在工件上施焊时,焊枪的走向应采用同一方向进行。
13、焊接场所的湿度不应超过90%,下雨时不允许露天焊接作业。
14、在没有标注焊缝大小或焊接方式时,其焊接尺寸取两板中较薄板厚值的0.8倍,焊缝为连续焊缝。
通用焊接工艺

通用焊接工艺(一)1 总则本通用工艺适用于我公司采用手工电弧焊、埋弧自动焊,钨极氩弧焊及熔化极CO2气体保护焊工艺的各类钢制压力容器的焊接。
2 焊工2.1 焊工必须按《锅炉压力容器焊工考试规则》进行考试,并取得焊工合格证,方能在有效期内从事合格项目的焊接工作。
2.2 焊接前焊工必须了解所焊焊件的钢种、焊接材料、焊接工艺要点。
3 焊接方法3.1 下列焊缝一般采用埋弧焊3.1.1 10≤δ≤60的拼接焊缝;3.1.2 直径φ≥1000mm且δ≥10mm的A、B缝内、外口;600mm≤直径φ<1000mm的A、B缝外口。
3.2 下列焊缝一般采用手工焊:3.2.1 直径φ≥1000mm且δ<10mm的A、B缝内、外口;3.2.2 600mm≤直径φ<1000mm的A、B缝内口3.2.3 直径φ≥89mm接管与法兰B类缝外口;3.2.4 C、D 类焊缝。
3.3 下列焊缝一般采用钨极氩弧焊:3.3.1 直径φ≥1000mm 且δ≤8mm的A、B类缝打底焊;3.3.2 600mm≤直径φ<1000mm的A、B类缝打底焊;3.3.3 直径φ≥89mm接管与法兰B类缝打底焊;3.3.4 φ<89mm的接管与法兰B缝焊接;3.3.5 图样要求采用氩弧焊的C、D类焊缝焊接。
3.4 下列焊缝一般采用熔化极CO2气体保护焊:3.4.1 塔器的裙座和底座环的焊接;3.4.2 容器和换热器等设备的鞍座和支座的焊接。
4 焊接材料4.1 根据产品图纸或JB/T4709《钢制压力容器焊接规程》的规定选用相应的焊接材料。
4.2 焊条、焊丝、焊剂必须具有产品质量证明书,并符合相应的标准规定,经验收或复验合格后方可使用。
4.3 焊条存放处必须干燥,焊条应堆放整齐,分类、分牌号存放,避免混乱。
4.4 焊条、焊剂使用前应按说明书规定进行烘烤,焊条领用时须用焊条筒存放,随取随用。
连续使用的焊剂应过筛,除去其中的尘土和粉末。
4.5 焊丝表面应无铁锈、氧化皮、油污等污物。
碳钢管道焊接通用工艺

1.适用范围
本工艺适用于中低碳钢管道采用氩弧焊、手工电弧焊的焊接施工。
2.施工准备
2.1材料要求
2.1.1施工现场应配有符合要求的固定焊条库或流动焊条库。
2.1.2焊材必须具有质量证明书或材质合格证,焊材的保管、烘干、发放、回收严格按《压力管道安装质量保证手册》中有关规定执行,焊条的烘干工艺按生产厂家说明书提供的参数进行,否则应按以下参数进行烘干:
3)承插或角焊缝采用手工电弧焊进行焊接;
3.4点焊
点焊方式为过桥方式,其工艺和焊材于正式焊接工艺相同,点焊数为2-5点,焊点厚度为70%壁厚且不大于6mm。焊前需预热的,点焊前需预热,预热一切同正式焊接相同。
3.5预热
对有焊前预热要求的管道在焊口组对并检验合格后,应进行预热,预热方法采用电加热,预热范围为坡口两侧各不少于100mm。测温方式可采用测温笔或表面测温仪。
A)风速:手弧焊小于8m/s;氩弧焊小于2m/s;
B)相对湿度:相对湿度小于90%;
C)环境温度:当环境温度小于0℃时,对不预热的管道焊接前应在始焊处预热15℃以上;对焊接工艺要求预热的管道焊接前按要求进行预热,当环境温度低于-20℃时,必须采取保暖缓冷措施。
3.焊接
3.1焊接施工程序,见图1。
*当有要求时
2.2.2预热及热处理的设备完好,性能可靠,检测仪表在校准周期内,且符合《压力管道质保手册》中的计量要求。
2.2.3焊工所用的焊条保温筒,刨锤、钢丝刷等工具齐全。
2.3作业条件
2.3.1人员资格
焊工必须持有《焊工合格证》,且施焊项目应在其合格项目范围之内。
2.3.2环境条件
施焊前应确认环境符合下列要求
3.6焊接工艺
焊接技师培训教材(焊接通用工艺)
38
角焊缝的熔深(切片)
39
(6)焊缝厚度
焊缝截面中,从焊缝正面到焊缝背面的距离叫焊缝厚度。
焊缝厚度H
焊缝厚度H
40
(7)焊角与焊脚尺寸
角焊缝的横截面中,从一个直角面上的焊趾到另一个直角 表面的最小距离,叫焊角。 角焊缝横截面中画出的最大等腰直角三角形中直角边的 长度,叫焊角尺寸。
41
焊缝计算厚度 凸度
69
点状加热(2)
70
2)条状加热
火焰沿直线方向移动,连续加热金属表面,形成一条加 热线即条状加热。 薄板校平不作横向摆动加热,需扩大面积 时,从中间向两侧 平行的增加加热线,线距视变形程度而定,变形量大宜密 些。
71
3)带状加热
火焰移动过程中横向摆动,就形成带状加热。 带状加热的横向收缩大于纵向收缩量,带状加热多 用于校正厚板、变形量较大或刚性较大的构件。
焊接技师培训教材
(焊接通用工艺)
张明录
1
目录
一.焊缝符号和焊接方法代号 二.焊缝形状和尺寸 三.焊接应力与变形 四.焊接缺陷 五.焊接质量检验
2
一.焊缝符号和焊接方法代号
GB/T324—2008《焊缝符号表示方法》 GB/T5185—2005《金属焊接及钎焊方法在图样上的表示 代号》组成。
通过焊缝符号和焊接方法代号配套使用就能简单明了 的在图样上表示焊接方法,焊缝形式、焊缝尺寸、焊缝 表面状态、焊缝位置等。
2.用水急冷的目的是限制膨胀范围,增加对加热区的挤 压作用, 不必等待, 可立即看到效果。
浇水冷却要在颜色冷却到失去红色时才可浇水。
75
3. 矫正前应仔细观察和分析变形情况,弄清变形原 因, 确定加热位置。如T形梁焊后可能产生一般 的角变形和整梁的弯曲变形。 合理的矫正顺序应是:先矫正角变形,再矫正旁 弯, 最后再矫正上拱或下拱的变形。
焊接通用工艺标准——引熄弧板2016.5.30v1》
1 编制目的为了规范车间焊接用引弧板、熄弧板的设置,提高焊接质量,特制定本标准。
2 适用范围本标准规定了在焊接前引弧板、熄弧板设置的工艺要求,包括钢构件制作的CO2气体保护焊和埋弧自动焊。
当工艺文件无特殊规定时,均应按本标准的各项规定执行。
3 引用标准(1)《钢结构工程施工规范》GB50755-2012(2)《钢结构焊接规范》GB50661-20114 引弧板、引出板的设置4.1 引弧板、熄弧板的作用及设置目的焊接前在焊道两端正确设置引弧板、熄弧板是保证焊接质量重要工艺措施。
焊接起弧时接头能量不足,电流电压不稳定,易引起夹渣、未熔合、焊不透等缺陷,熄弧时熔池能量较大,焊接区温度较高,填充金属不足易引起弧坑导致焊缝收弧处出现冷热裂纹,故在焊接起熄弧处设置引弧板、熄弧板,可将端部的焊接缺陷引到主焊缝之外的引熄弧板上。
引弧板、熄弧板的运用可以提高构件主焊缝的焊接质量。
采用埋弧自动焊接时焊缝端部与引弧板相接处往往是无损检测的重点区域,使用不规范的引、熄弧板,在无损检测时,会因为焊缝缺陷而返工。
4.2 引弧板、熄弧板的工艺要求T形接头、十字形接头、角接接头和对接接头主焊缝两端,必须配置引弧板、熄弧板,其强度不应大于被焊钢材强度,且应具有与被焊钢材相近的焊接性。
焊条电弧焊和气体保护焊焊缝引出长度应大于25mm;埋弧焊焊缝引出长度应大于80mm。
超厚板有特殊要求的按焊接工艺评定要求长度操作。
焊接完成并完全冷却后,可采用火焰切割、碳弧气刨或机械等方法除去引弧板、引出板,并修磨平整,严禁用锤击落。
1页码 第2页,共5页引弧板、熄弧板的固定焊缝应按下图进行点固焊接:引弧板、熄弧板的固定焊缝位置示意 点焊厚度大于4mm ,点焊要牢固,避免弧坑4.3 引弧板、熄弧板的下料与使用引弧板、熄弧板的下料按正式零件加工,由工艺部下发手工号料单,由配件车间下料,配送至各使用车间。
号料、下料、配送定额由成本部进行测算后与车间共同确定。
焊接通用工艺守则
焊接工艺守则GY—CT—G22编制:审核:批准:XXXXXXXXXX有限公司1.主题内容和适用范围本守则规定了焊接件的焊前准备、组装和各种焊接方法技术规范本守则适用于公司消防车系列产品结构件焊接,凡产品图纸或技术文件中无特殊要求时,手工电弧焊、半自动电弧焊、电阻焊、气焊均按本守则执行。
2.引用标准JB/T5943-91 工程机械焊接件通用技术条件JB/T50077—96 气体保护电弧焊用碳钢、低合金钢焊丝产品质量分等GB985—88 气焊、手工电弧焊及气体保护焊焊缝坡口的基本形式和尺寸GB324—88 焊缝符号表示法3.一般规定3。
1 焊工考核焊工必须持证上岗并经人事部及有关部门考查合格后才能焊接产品,并定期考查。
3.1。
1 焊工应有较强的识图能力,能准确地找出图样上的焊接部位.焊接符号识别见附录Ⅰ;3.1。
2焊工应具有一定的电工知识、金属材料知识、焊接结构的装配知识。
3.1。
3焊工应具有各种位置焊接的熟练操作技能。
并能识别各种焊接缺陷,找出原因,采取相应纠正措施.3.1.4焊工应有一定的安全意识,特别是进行气焊、气割时,必须正确使用设备.3.2 材料公司常用被焊材料有普通炭素钢、优质碳素钢(只限45钢以下)、低合金结构钢(16Mn 15MnVN等)、不锈钢(1Cr18Ni9Ti Sus304N1 1Cr13)、铝合金钢板、铜管.3。
2.1进厂原材料(板材、型材、焊接材料)的钢号、规格、尺寸应符合有关国家标准、图样和工艺要求,不符合要求的,应按制度办理代用手续.3。
2。
2 进厂原材料必须经质检部门检查合格后,方可投入生产。
3。
2。
3焊接材料选用原则:碳钢和低合金钢按等强度原则选用,不锈钢和有色金属按等成分原则选用。
3。
2.4新研制或公司从末使用过的材料(含焊接材料),需经技术部门进行焊接工艺评定,经主管领导或主管设计认可后,方能投入生产。
3.2。
5 用于钢结构焊接的焊条,购买、保管、贮存、使用均应按JB3223《焊条质量管理规程》的规定执行,3.2。
焊接通用工艺及检验
焊接通用工艺与检验一、根底知识1、什么叫焊接?焊接是指通过加热、加压或两者并用,使两个别离的工件到达原子间的结合的一种方法。
2、焊接接头的分类:焊接接头是指用焊接的方法连接的接头称为焊接接头〔简称接头〕,焊接接头包括焊缝、熔合区和热影响区。
焊接接头可分为对接接头〔a〕、T型接头〔b〕、角接接头〔c〕和搭接接头〔d〕四种如以下图:3、坡口:所谓坡口就是根据设计或工艺需要,为了保证焊透,保证接头质量,在焊件的待焊部位加工的一定几何形状的沟槽。
由于我们焊接位置和结构的原因,大局部都要开坡口,其坡口为“V〞型,如图:α为破口张开角度通常为60?b为坡口间预留间隙通常为1-2mmp为坡口预留钝边通常为0-2mm4、手工电弧焊的特点是什么?其主要特点是:〔1〕工艺灵活,适应性强,适用于各种钢材厚度、结构形状及各种位置的焊接;〔2〕质量好,与气焊相比,金相组织细,热影响区小,接头性能好;〔3〕易于通过工艺调整〔如对称焊〕来控制变形和改善应力;〔4〕设备简单,操作和维修方便。
5、氩弧焊的特点及适应范围:氩弧焊是以氩气作为保护介质,以可熔化的焊丝或不熔化的钨棒作电极进行焊接的一种工艺方法。
由于焊接电流受到钨棒的限制,电弧功率较小,只适用于薄工件的焊接。
、焊接工艺标准包括哪些?选择工艺标准应考虑些什么?焊接工艺标准参数主要有:焊接电流、电弧电压、焊接速度和焊丝〔或焊条〕直径等。
选择焊接标准参数的原那么是:保证电弧稳定,焊缝形状尺寸符合要求,焊缝外表成形光洁整齐,无气孔、裂纹、夹渣、未焊透等缺陷,生产效率高,本钱低。
7、焊接电流过大或过小对焊接接头有哪些影响?为什么?随着焊接电流的增大,熔深和焊缝余高,都有显著的增加,而焊缝宽度变化不大,这是由于焊接电流的增大时,电弧产生的热量增多,传给工件的热量也增加,电弧对液体金属的作用力也相应增强,焊丝的熔化也相应增加,故使熔深和焊缝余高显著增加。
并容易产生咬边、烧穿、焊瘤和引起飞溅过大等焊接缺陷。
- 1、下载文档前请自行甄别文档内容的完整性,平台不提供额外的编辑、内容补充、找答案等附加服务。
- 2、"仅部分预览"的文档,不可在线预览部分如存在完整性等问题,可反馈申请退款(可完整预览的文档不适用该条件!)。
- 3、如文档侵犯您的权益,请联系客服反馈,我们会尽快为您处理(人工客服工作时间:9:00-18:30)。
通用焊接工艺规程
1 总则
本规程适用于本公司产品所有组焊体的焊接加工,适用于碳钢、低合金钢的二氧化碳气体保护焊工艺。
凡图纸技术文件上无特殊技术要求的,均按本工艺规范执行。
1.2 引用标准
GB/T 324-2008 焊缝符号表示法
GB/T 985.1-2008 气焊、电弧电弧焊、气体保护焊和高能束焊的推荐坡口GB/T 2900.22-2005 电工名词术语电焊机
GB/T 3375-1994 焊接术语
GB/T 10045 碳钢药芯焊丝
GB/T 8110-2008 气体保护电弧用碳钢、低合金钢焊丝
GB/T 8118--2010 电弧焊机通用技术条件
HG/T 2537-1993 焊接用二氧化碳
2 技术要求
2.1 材料
2.1.1钢材材质应符合材料标准的规定,并按JB/T3375的规定进行入厂检验,合格后方可使用。
2.1.2二氧化碳气体保护焊常用焊丝为药芯焊丝YJ501-1(E501T-1,相当AWS A5.20 E71T-1C),焊丝应符合GB/T 10045-2001的规定。
焊丝按规定进行入厂检验,合格后方可使用。
2.1.3CO2气体纯度≥99.5%。
3 焊接
3.1 焊前准备
3.1.1焊接前应熟悉产品图纸和产品作业指导书
在小电流焊接时,电弧电压过高,金属飞溅将增多;电弧电压太低,则焊丝容
易伸人熔池,使电弧不稳。
在大电流焊接时,若电弧电压过大,则金属飞溅增多,容易产生气孔;电压太低,则电弧太短,使焊缝成形不良。
3.2.2气体流量
二氧化碳气体流量与焊接电流、焊接速度、焊丝伸出长度及喷嘴直径等有关。
气体流量应随焊接电流的增大、焊接速度的增加和焊丝伸出长度的增加而加大。
一般二氧化碳气体流量的范围为8~25L/min。
如果二氧化碳气体流量太大,由于
气体在高温下的氧化作用,会加剧合金元素的烧损,减弱硅、锰元素的脱氧还
原作用,在焊缝表面出现较多的二氧化硅和氧化锰的渣层,使焊缝容易产生气
孔等缺陷;如果二氧化碳气体流量太小,则气体流层挺度不强,对熔池和熔滴
的保护效果不好,也容易使焊缝产生气孔等缺陷。
3.3 施焊
3.3.1焊接顺序按焊接工艺卡执行,无焊接工艺时应根据具体结构条件合理确定:
✧对具有中心线且左右对称的构件,应该左右对称地进行焊接,最好是双数
焊工同时进行,避免构件中心线产生移位。
✧构件中如同时存在对接缝和角接缝时,则应先焊对接缝,后焊角接缝。
如
同时存在立焊缝和平焊缝(如果允许翻转,尽量采用船型焊),则应先焊
立焊缝,后焊平焊缝。
所有焊缝应采取由中向左右,由下往上的焊接次序。
✧长度≤1000毫米可采用连续直通焊,≥1000毫米时采用分中逐步退焊法或
分段逐步退焊法等方法。
✧在结构中同时存在厚板与薄板构件时,先焊收缩量大的厚板多层焊,后焊
薄板单层焊缝。
多层焊时,各层的焊接方向最好要相反,各层焊缝的接头
应相互错开,或采用分段焊法,焊缝的接头不应处在纵横焊缝的交叉点。
图1:多层焊的分段退焊法
✧刚性较大的接缝,如立体分段的对接接缝(大接头),焊接过程不应间断,
应力求迅速连续完成。
3.3.2 定位焊
定位焊缝应有足够的强度,如发现定位焊缝有夹渣、气孔和裂纹等缺陷,应将缺陷部位除尽后再补焊。
定位焊缝的长度在20~50mm或采用点焊,定位焊缝间距在200~500mm。
3.3.3根部焊
中厚板根部焊道焊接时采用较大的焊接电流,焊枪指向距根部1~2mm处。
为保证焊缝熔合良好,焊枪与立板成35~45°夹角,如图2所示。
焊接时,采用左向焊法,焊枪做小幅度横向摆动,以获得合适的焊脚尺寸。
切不可过份追求获得太大焊脚。
否则,会造成铁水下淌,立板出现咬边,底板产生焊瘤,焊缝成形不良等缺陷。
图2
3.3.4盖面焊
根部焊道焊完后,将焊道上的熔渣、飞溅清理干净。
先焊焊道2,焊枪指向根部焊道与底板的焊趾处,可采用直线焊接或小幅摆动焊接法。
要注意底板一侧达到所要求的焊脚尺寸,同时焊趾整齐美观。
焊枪角度如图3所示。
图3 图4
第3道焊接时,焊接电流要比第1、2道小些,焊接速度要快些,以保证焊缝成形,不产生咬边缺陷。
焊枪角度如图4所示。
4. 注意事项
焊接过程中,导电嘴到母材之间的距离一般为焊丝直径的10~15倍。
保护气体应有足够的流量并保持层流(保护气体在喷嘴内和喷嘴外的一定距离作有规则的层状流动),及时清除附在导电嘴和喷嘴上的飞溅物,确保良好的保护效果。
焊接区域的风速应限制在1.0m/s以下,否则应采用挡风装置。
应经常清理送丝软管内的污物,送丝软管的曲率半径不得小于150mm。