IE工业工程标准工时测量
工业工程概念及标准工时测定(NEW)

如何分解作业要素(单元)?
测时纪录表
时间: 代号: 第 页
NO. CY.NO. T 步骤/工序1 1 R T 步骤/工序2 2 R T 步骤/工序3 3 R T 步骤/工序4 4 R T 步骤/工序5 5 R T 工序20 20 R
1
2
3
4 5 6
7
8 9 10 20
注:“T”单元时值
“R”表面读数
作业点
工 具
零部件
动作分析目的:经济动作
利用动作经济原则为改善之工具,其重点不在于改变整个制 造程序的工作计划,工作说明书的内容,不良的机器,生 产进度跟催或耽搁等问题,而是在于以上条件不改变之下 使工人工作效率提高,并使工人本身确感身心舒适愉快。 目 的: 减轻作业者的疲劳 提高作业效率
上限位置
肢体使用原则
1、双手作业 2、双手动作对称反向 3、身体动作以最低级别 进行 4、连续圆滑的曲线动作 5、动作姿势稳定 6、减少动作注意力 7、利用物体惯性 8、动作有节奏
作业配置原则
1、材料3定 2、材料工装预置在小臂 范围内 3、材料工装的取放简单 4、物品的移动以水平为 佳 5、利用物品自重工序传 递 6、作业高度适度 7、满足作业照明要求
工 序 分 析
工 作 分 析
效 率 改 善
精益企业
时间分析基础---动作分析
類別 1 2 3 4 5 6 7 8 9 10 11 12 13 14 15 16 17 動素名稱 伸手 (Reach) 握取 (Grash) 移物 (Move) 裝配 (Assemble) 應用 (Use) 拆卸 (Disassemble) 放手 (Release) 檢驗 ( I ) 尋找 (Search) 選擇 (Select) 計劃 (Plan) 對準 (Position) 預對 (Preposition) 持住 (Hold) 休息 (Rest) 遲延 (Unavoidable Delay) 故延 (Avoidable Delay) 文字符號 RE G M A U DA RL I SH ST PN P PP H RT UD AD 形象符號 定 義 接近或離開目的物之動作 為保持目的物之動作 保持目的物由某位置移至另一位置之動作 為結合2個以上目的物之動作 籍器具或設備改變目的物之動作 為分解2個以上目的物之動作 放下目的之動作 將目的手與規定標準比較之動作 為確定目的物位置之動作 為選定欲抓起目的物之動作 為計劃作業方法而遲延之動作 為便利使用目的物而校正位置之動作 使用目的物後為避免[對準]動作而放置目的物之動作 保持目的物之狀態 不含有用的動作而以休養為目的之動作 不含有用的動作而作業者本身所不能控制者 不含有用的動作而作業者本身可以控制之遲延
ie标准工时
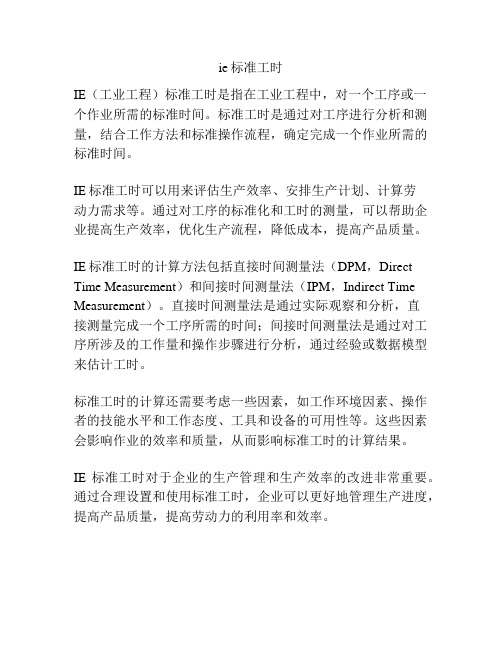
ie标准工时
IE(工业工程)标准工时是指在工业工程中,对一个工序或一个作业所需的标准时间。
标准工时是通过对工序进行分析和测量,结合工作方法和标准操作流程,确定完成一个作业所需的标准时间。
IE标准工时可以用来评估生产效率、安排生产计划、计算劳
动力需求等。
通过对工序的标准化和工时的测量,可以帮助企业提高生产效率,优化生产流程,降低成本,提高产品质量。
IE标准工时的计算方法包括直接时间测量法(DPM,Direct Time Measurement)和间接时间测量法(IPM,Indirect Time Measurement)。
直接时间测量法是通过实际观察和分析,直
接测量完成一个工序所需的时间;间接时间测量法是通过对工序所涉及的工作量和操作步骤进行分析,通过经验或数据模型来估计工时。
标准工时的计算还需要考虑一些因素,如工作环境因素、操作者的技能水平和工作态度、工具和设备的可用性等。
这些因素会影响作业的效率和质量,从而影响标准工时的计算结果。
IE标准工时对于企业的生产管理和生产效率的改进非常重要。
通过合理设置和使用标准工时,企业可以更好地管理生产进度,提高产品质量,提高劳动力的利用率和效率。
IE标准工时测量
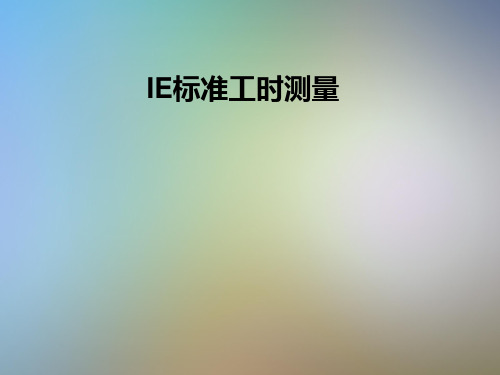
程序分析就是消除产品生产过程中的全部浪费和 不合理,从而提高效率!
1、加工 2、搬运 3、检查 4、停滞
(等待)
改善案例(各组讨论)
铁
铁
铁
架
架
架
30
米
塑
铁
料
铁
架
管
架
材
60米
主管
铁
架
料帐
工 具 架
铁 架
查阅领料单 走到塑料管材铁架处(50) 选择比实际长度稍长且必须稍长的管子 带料回柜台(50) 校对长度,用大拇子按住锯切点 带管子到工具铁架处(7) 从箱子里面取出手锯 带手锯及管子会柜台(7) 锯切 比对长度 发管子给领料人 在领料单上签字 放领料单在抽屉,并夹住。 带锯剩的管子回塑料管材铁架(50) 放回管子在铁加上 走回柜台(50)
七大浪费MUDA
等待浪费
库存 过多
不良改正
加工 过剩
制造过多
标准时间ST的制订方法与应用
1、认识标准时间
时间研究的定义:“时间研究是一种作业测定技术,旨在 决定一位合格、适当、训练有素的操作者,在标准状态下 ,对一特定的工作以正常速度操作所需要的时间。”
定义中有: 1、合格、适当、训练有素的操作者; 2、在标准状态下。
也就是说,必须测时22次才是合理次数。已 经 做了8次,还要测时14次。
General Electric观测次数
周期时间 40分钟以上 20-40分钟 10-20分钟 5-10分钟 2-5分钟 1-2分钟 0.75-1.0分钟 0.50-0.75分钟 0.25-0.50分钟 0.10-0.25分钟 0.10分钟以下
IE工业工程标准工时
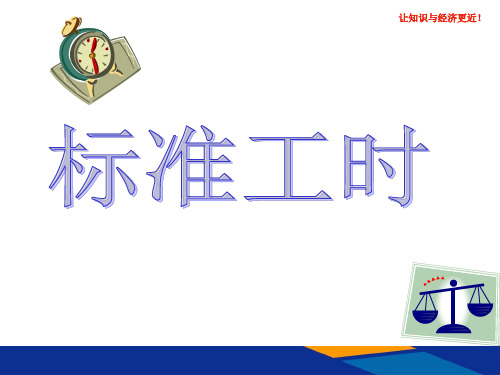
2 28.64 29.61 30.24 27.68 29.46 30.24 27.68 14.56
11
HI-11
Insert L101.IC502.L1.R915
2 28.64 30.47 28.16 29.17 30.46 30.47 28.16 14.69
12
HI-12
Insert IC901.IC502.L1.R915
2 24.13 26.14 25.34 30.68 24.38 30.68 24.13 13.07
22
HI-22
Cut PWB
2 29.12 24.36 28.34 26.87 24.35 29.12 24.35 13.30
23
TU-01
Front and back inspection#1
1 12.38 15.88 14.37 15.33 14.25 15.88 12.38 14.44
让知识与经济更近!
标准时间是由“正常时间”和“宽裕时间”两部分组成,其中"正常时间"为 观测时间和评比因素和;宽裕时间为生理宽放、疲劳宽放、作业宽放、管理宽放.
宽放种类及宽放率
作业宽放 3%~5%(普通3%) 不 可 疲劳宽放: 避 特种作业:30%以上; 免 重作业:20%~30%; 的 中作业:10%~20%; 宽 轻作业:5%~10%; 放 特轻作业:0%~5%
PAGE:___1___/___4___ PRE.
SIGN DATE 12-Sep
ADJUSTMENT
1
HI-01
Take carrier ,Insert CY3&CY4
2 23.16 28.46 26.47 15.34 28.49 28.49 15.34 12.19
ie标准工时计算
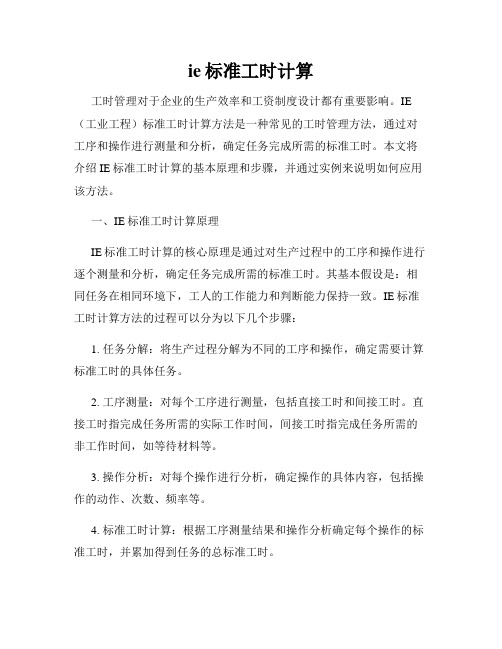
ie标准工时计算工时管理对于企业的生产效率和工资制度设计都有重要影响。
IE (工业工程)标准工时计算方法是一种常见的工时管理方法,通过对工序和操作进行测量和分析,确定任务完成所需的标准工时。
本文将介绍IE标准工时计算的基本原理和步骤,并通过实例来说明如何应用该方法。
一、IE标准工时计算原理IE标准工时计算的核心原理是通过对生产过程中的工序和操作进行逐个测量和分析,确定任务完成所需的标准工时。
其基本假设是:相同任务在相同环境下,工人的工作能力和判断能力保持一致。
IE标准工时计算方法的过程可以分为以下几个步骤:1. 任务分解:将生产过程分解为不同的工序和操作,确定需要计算标准工时的具体任务。
2. 工序测量:对每个工序进行测量,包括直接工时和间接工时。
直接工时指完成任务所需的实际工作时间,间接工时指完成任务所需的非工作时间,如等待材料等。
3. 操作分析:对每个操作进行分析,确定操作的具体内容,包括操作的动作、次数、频率等。
4. 标准工时计算:根据工序测量结果和操作分析确定每个操作的标准工时,并累加得到任务的总标准工时。
二、IE标准工时计算步骤下面以一家制造企业的生产线上的装配工序为例,介绍IE标准工时计算的具体步骤:1. 任务分解:将装配工序分解为多个具体操作,如零件装配、调试、清洁等。
2. 工序测量:对每个工序进行测量,记录实际完成该工序所需的工作时间。
例如,在零件装配工序中,测量实际装配一件零件所需时间为10分钟。
3. 操作分析:对每个操作进行分析,记录操作的具体内容和频率。
例如,在零件装配工序中,操作包括拆卸、安装、固定等,其中拆卸操作的频率为10次/小时,安装操作的频率为20次/小时。
4. 标准工时计算:根据工序测量结果和操作分析确定每个操作的标准工时。
例如,拆卸操作的标准工时为实际拆卸一次所需时间乘以频率,即10分钟/次×10次/小时=100分钟/小时。
三、IE标准工时计算实例假设某企业的装配工序共有5个具体操作,它们的实际工时和频率如下表所示:操作名称实际工时(分钟)频率(次/小时)零件装配 10 20调试 15 15清洁 5 30固定 8 25质检 12 10根据上述数据,可以计算每个操作的标准工时,然后累加得到任务的总标准工时。
ie标准工时
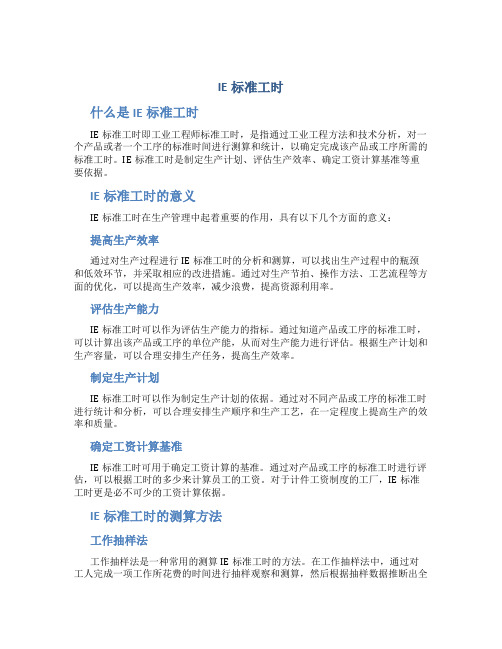
IE标准工时什么是IE标准工时IE标准工时即工业工程师标准工时,是指通过工业工程方法和技术分析,对一个产品或者一个工序的标准时间进行测算和统计,以确定完成该产品或工序所需的标准工时。
IE标准工时是制定生产计划、评估生产效率、确定工资计算基准等重要依据。
IE标准工时的意义IE标准工时在生产管理中起着重要的作用,具有以下几个方面的意义:提高生产效率通过对生产过程进行IE标准工时的分析和测算,可以找出生产过程中的瓶颈和低效环节,并采取相应的改进措施。
通过对生产节拍、操作方法、工艺流程等方面的优化,可以提高生产效率,减少浪费,提高资源利用率。
评估生产能力IE标准工时可以作为评估生产能力的指标。
通过知道产品或工序的标准工时,可以计算出该产品或工序的单位产能,从而对生产能力进行评估。
根据生产计划和生产容量,可以合理安排生产任务,提高生产效率。
制定生产计划IE标准工时可以作为制定生产计划的依据。
通过对不同产品或工序的标准工时进行统计和分析,可以合理安排生产顺序和生产工艺,在一定程度上提高生产的效率和质量。
确定工资计算基准IE标准工时可用于确定工资计算的基准。
通过对产品或工序的标准工时进行评估,可以根据工时的多少来计算员工的工资。
对于计件工资制度的工厂,IE标准工时更是必不可少的工资计算依据。
IE标准工时的测算方法工作抽样法工作抽样法是一种常用的测算IE标准工时的方法。
在工作抽样法中,通过对工人完成一项工作所花费的时间进行抽样观察和测算,然后根据抽样数据推断出全体工人完成该项工作所需的标准工时。
这种方法通常适用于每个工序都比较固定且重复性高的情况。
预定时间法预定时间法是另一种常用的测算IE标准工时的方法。
预定时间法通过将一个工序分解成为多个最小动作单位,并对每个动作单位的时间进行测算,然后根据动作单位的时间累加得出该工序的标准工时。
这种方法适用于工序比较繁杂且包含多个动作单位的情况。
标准数据法标准数据法则是以已确定的标准化数据标准和国内外行业标准作为IE标准工时的测算依据,从而快速准确地测算出工序的标准工时。
IE工时测量方法标准指引

IE工时测量方法标准指引咱先来说说啥是 IE 工时测量。
其实啊,这就好比你要算清楚做一顿饭得花多长时间。
比如说,你从洗菜、切菜到炒菜,每一个步骤所花费的时间都得算得明明白白的。
IE 工时测量呢,就是要给工作的每一个环节都精确地算好时间。
这可不是随便估摸一下就行的,得有一套标准的方法。
就拿咱们常见的生产线上组装一个小零件来说吧。
你得先选好要测量的那个工作任务,就像挑出要做的那道菜一样。
然后呢,得确定好从哪儿开始计时,到哪儿结束计时,这可不能马虎。
有一次,我去一个工厂观察,就发现了个有趣的事儿。
有个工人师傅在组装一个小部件,我就在旁边悄悄记录他的时间。
刚开始,他动作挺快的,可过了一会儿,可能是累了,速度就慢了下来。
这时候,如果我不仔细观察,不把这些变化都考虑进去,那测出来的工时可就不准确啦。
测量的时候,还得把那些会影响工作时间的因素都考虑到。
比如说,工作环境是不是舒服,工具好不好用。
就好比做饭的时候,要是厨房又热又挤,锅铲还不顺手,那做饭的速度肯定受影响。
还有啊,测量的次数也不能少。
不能只测一次就觉得准了,得多测几次,取个平均值,这样才能更靠谱。
就像你做一道新菜,第一次可能没掌握好火候,多做几次才能找到最合适的时间和方法。
另外,测量的人也得专业,不能一会儿看看手机,一会儿跟别人聊天,得全神贯注。
而且,还得和工人师傅提前沟通好,别让人家紧张,不然也会影响测量结果。
总之啊,IE 工时测量是个细致活儿,得有耐心,有方法,才能测准了,为提高工作效率提供有用的依据。
就像你只有把做饭的时间算准了,才能合理安排一天的生活,对吧?希望大家都能掌握好这个标准指引,让工作变得更高效,更有条理!。
IE工时测量方法标准指引
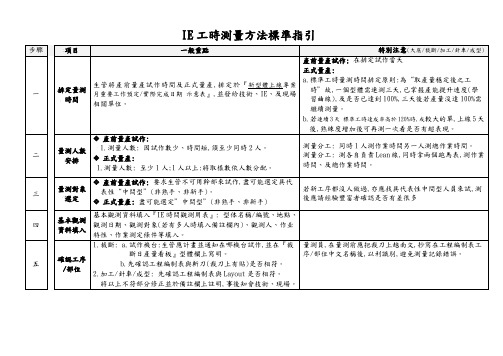
步驟
項目
一般重點
特別注意(大底/裁斷/加工/針車/成型)
一
排定量測時間
生管將產前量產試作時間及正式量產,排定於『新型體上線專案月重要工作預定/實際完成日期示意表』,並發給技術、IE、及現場相關單位。
產前量產試作:在排定試作當天
正式量產:
a.標準工時量測時間排定原則:為“取產量穩定後之工時”故,一個型體需連測三天,已掌握產能提升速度(學習曲線),及是否已達到100%,三天後若產量沒達100%需繼續測量。
註.寬放值:目前暫訂5%,之後漸調至零
4.量測完後應請現場幹部確認工序名稱並簽名。
註.名詞解釋:
a.作業時間:即有價作業時間,不含附帶時間。
b.總作業時間=有價作業時間+無價時間(有價作業時間之外如拿、放及調機等時間)
裁、加、針、成型之作業時間及總作業時間測量法
工時
工程
作業時間
總作業時間
停錶量測法
(不含附帶時間,至少需反覆量測5個數據求平均)
(不停錶量測法)
(含附帶時間,至少需反覆量測5個數據求平均)
裁斷
停錶量測法,從斬刀放下斬刀台,到斬完拿起瞬間的時間為一個數據
主料:不停錶量測法,從捲皮至該件皮料完成之時間為一個數據。
副料:不停錶量測法,從裁斷至下一次裁斷之時間,含裁斷、撿料、整理,為一個數據。(若同時裁多層多雙,應除以雙數才是單雙時間)
b.记录特殊状况有利改善:如观测数据有很大的不同时,必须注意是作业人员的原因,还是周边环境的影响,或是因没有确立标准作业等的原因等,对以後讨论改善方案很有用。
3.觀測技巧:a.尊重:先跟現場主管打過招呼,另除非量測對象是坐下作業時,量測員不能坐下休息以示尊重。
- 1、下载文档前请自行甄别文档内容的完整性,平台不提供额外的编辑、内容补充、找答案等附加服务。
- 2、"仅部分预览"的文档,不可在线预览部分如存在完整性等问题,可反馈申请退款(可完整预览的文档不适用该条件!)。
- 3、如文档侵犯您的权益,请联系客服反馈,我们会尽快为您处理(人工客服工作时间:9:00-18:30)。
下限位置
适合作业区域 最适合作业区域
人体各部分的尺寸、体重、体表面积、比重、重心以及人体各 部分在活动时相互关系和可及范围等人体结构特征参数提供人体 各部分的发力范围、活动范围、动作速度、频率、重心变化以及 动作时惯性等动态参数分析人的视觉、听觉、触觉、嗅觉以及肢 体感觉器官的肌能特征。
时间观测的步骤
步 骤 工 作 内 容
1
2 3 4 5 6 7 8 9 10
仔细观察作业对象
观察作业人员N个作业循环 分解观测作业对象,分解成机构作业要素 按照作业顺序,在观测记录表上记录作业要素 在观测记录表上记录必要外来事项 按动秒表 迅速纪录作业要素时间 依次观测全部作业要素 根据作业周期,决定观测M次数 整理观测时间,计算出个作业要数的 所需时间。
经典IE研究
Taylor 搬运实验与 劳动定额
Gilbreth 砌墙实验与 经典的工作研究 动作经济性原则
时间研究
动作研究
IE的使命
专门的
人员 物料 设备 时间 信息
观 察
综 合 体 系 通过
学 习 思 考
利用
数 学 物理学 社会科学
知识 技术
工学的 分析 设计 原理 方法
期待的成果
P Q C D S M
2、制订标准时间的基础
1、在正常的作业环境下; 2、确定而且最好是迄今为止最佳的工作方法; 3、胜任合适的作业者; 4、以一定正常的速度进行作业; 方法、条件、熟练度、劳动强度与速度、没 有在肉体上、精神上不利的影响、品质要求
动作分析与标准时间ST的关系
动 作 分 析 作 业 分 析 布 局 与 能 力 分 析
1)秒表法制订ST的方法和步骤
1、连续累积法
选择作业员并接近 收集记录有关资料 划分单元 初步决定观测次数 评时评分 观测次数是否足够 去除异常值 决定宽放数 N O
2、归零法
计算及预定标准时间
标准工时结构
在一定的工作方法、条件,任何正常人以正常速 度能完成某项作业的时间。
原始数据:测量时间 正常时间=测量时间(1+评定系数)
1 2 3 4 5
项 目
工序1
工序2
工序3
工序4
工序5
125件/H
能 力
100件/H
75件/H
110件/H
80件/H
生产线平衡率的计算
各工序时间总和
生产线平衡率= ---------------------------------- X 100%
人数 X CT CT----作业周期
生产线平衡率= ---------------- X 100%= 82%
机械设计原则
1、用夹具固定产品及 工具 2、使用专用的工具 3、合并两种工装为一 个 4、提高工装的便利 5、机械操作问题,程 序流程化 6、操控程序与作业程 序配合
三角形原理的定义:
在作业的过程中,有作业点、工具、零部件三个位置。 这三个位置构成了一个三角形关系。这个三角形越小,作业效率就越高。这就是“三 角形原理”。
作业点
工 具
零部件
动作分析目的:经济动作
利用动作经济原则为改善之工具,其重点不在于改变整个制 造程序的工作计划,工作说明书的内容,不良的机器,生 产进度跟催或耽搁等问题,而是在于以上条件不改变之下 使工人工作效率提高,并使工人本身确感身心舒适愉快。 目 的: 减轻作业者的疲劳 提高作业效率
上限位置
肢体使用原则
1、双手作业 2、双手动作对称反向 3、身体动作以最低级别 进行 4、连续圆滑的曲线动作 5、动作姿势稳定 6、减少动作注意力 7、利用物体惯性 8、动作有节奏
作业配置原则
1、材料3定 2、材料工装预置在小臂 范围内 3、材料工装的取放简单 4、物品的移动以水平为 佳 5、利用物品自重工序传 递 6、作业高度适度 7、满足作业照明要求
1、制订经济、有效、轻松的标准工时。 2、评估产能,生产排期的作用 3、发现现状问题,改善作业 4、研究各种方法的优劣评估 5、绩效评估管理(毛效率、净效率) 6、成本核算 7、生产线平衡率的改善和调整 8、新标准时间的制订
标准时间的几个概念
直接标准工时 = 生产线的标准工时X产量 直接标准工时 + 额外工时 + Downtime ≌ 实际直接工时 间接标准工时 = 直接标准工时 X (间接工人数 / 直接工人 数) 标准工时 = 直接标准工时+间接标准工时 标准工时 + 额外工时 + Downtime ≌ 实际工时 实际工时 = 实际直接工时+实际间接工时= 付钱的工时
七大浪费MUDA
标准时间ST的制订方法与应用
1、认识标准时间
时间研究的定义:“时间研究是一种作业测定技术,旨 在决定一位合格、适当、训练有素的操作者,在标准状态 下,对一特定的工作以正常速度操作所需要的时间。” 定义中有:
1、合格、适当、训练有素的操作者;
2、在标准状态下。
研究标准时间的意义与目的
现行方法: 操作:6 检查:4 搬运:6 16(214m)
局部调整与结构性改善对ST的关系
动作分析、作业改善、程序分析都是建立 高效率的基础,但从改善的全局看,我们 称之为局部性调整。 从产品工艺的结构特点,统筹规划企业的 产能和物流状况,从系统性、全面性实施 决策,我们称之为结构性改善。
结构改善
发现动作的浪费
如何发现动作的浪费? 动作浪费是指在制造物品的基础上,不能产生附加价值 的人的活动(包括设备的空转)。
因组装过快导致的收藏浪费 勉强作业 为作业而做的准备工作
关注员工的动作:
有无存放动作? 有无人员频繁走动而不作业? 有无人员在焦急的寻找? 有无人员在等待? 有无人员1小时都不抬头? 有无多余的空手等待? 有无单手作业?
标准时间=正常时间+放宽时间=正常时间(1+放宽系数)
秒表测时法制定标准工时
由泰勒创造,是目前全世界运用最古老、最普遍, 也不可能被其他方法替代的基本方法。 深入企业作现场测时,测时工程师必须充分了解 被测对象: 1、工作件的制程与作业。 2、作业的工作方法与作业标准。 3、进行该作业的人或机器。
经过计算:N=22(次) 也就是说,必须测时22次才是合理次数。已 经 做了8次,还要测时14次。
General Electric观测次数
周 期 时 间 40分钟以上 20-40分钟 10-20分钟 5-10分钟 2-5分钟 1-2分钟 0.75-1.0分钟 0.50-0.75分钟 0.25-0.50分钟 0.10-0.25分钟 0.10分钟以下 观 测 次 数 3 5 8 10 15 20 30 40 60 100 200
外来单元纪录
作业:#2748 工作件:产品A,工序#2 观测表NO.: 0289 观测人员:张 三 外来单元明细(归零法):
顺序
1 2 3
发生时分
09:21 10:09 11:53
外来单元
喝茶 尘沙入烟,揉眼 疲劳休息
时间(分) 备注
4 2 15 停工
抽样选择的次数
根据统计学,其基本条 件为信赖区间在2个标准查 范围内,即95%范围,误差 界限为±5%: 2
如何剔除异常值
由于各种原因,在测时数据中难免有 些异常值,如以下数据:
产品名称: 1 2 3 4 5 6 工序编号: 7 8 9 10 11 12
15 12 12 14 28
13
12
4
15
16
14
12
剔除原则
正常数据:介于平均数高30%与平均数 低25%之间的数据。
X=14 X上值=14(1+30%)=18.2 X下值=14(1-25%)=10.5
如何分解作业要素(单元)?
测时纪录表
时间: 代号: 第 页
NO. CY.NO. T 步骤/工序1 1 R T 步骤/工序2 2 R T 步骤/工序3 3 R T 步骤/工序4 4 R T 步骤/工序5 5 R T 工序20 20 R
1
2
3
4 5 6
7
8 9 10
20
注:“T”单元时值
“R”表面读数
60米
工 具 架
铁 架
查阅领料单 走到塑料管材铁架处(50) 选择比实际长度稍长且必须稍长的管子 带料回柜台(50) 校对长度,用大拇子按住锯切点 带管子到工具铁架处(7) 从箱子里面取出手锯 带手锯及管子会柜台(7) 锯切 比对长度 发管子给领料人 在领料单上签字 放领料单在抽屉,并夹住。 带锯剩的管子回塑料管材铁架(50) 放回管子在铁加上 走回柜台(50)
5 X 29
118
平衡损失率=1 - 平衡率=1-82%=18%
问 题
0.1分钟 0.7分钟 1.0分钟 0.8分钟 0.5分钟 0.4分钟 0.2分钟 0.6分钟
1、假设每天运转8小时(480分钟),请问这流水线的产 量范围? 2、假如每天计划生产480个产品,那么需要设定多少工 序呢?
制订标准时间的方法种类
IE 的基本概念和标准工时的测量
工艺
Tony Zhao
什么是IE?
—— 明其理,方学其道!
工业工程(Industrial Engineering)
工业工程是一门综合应用技术科学、社会科学、 管理科学、人文科学提高生产率、降低成本、提 高效益的管理技术。 IE是在泰勒(Taylor)所创建的科学管理的基础上, 不断吸收近代科学技术新近展发展起来的关于 “人员、机器、原料、时间与信息”的效率化的 应用技术方法,是关于“人的工作系统的设计的 学问”。