Characteristics of silver–glass composite powders as the silver electrode for Si solar cells
Novel fabrication of silver-coated glass capillaries for ready SERS-based detection of dissolved

ORIGINAL PAPERNovel fabrication of silver-coated glass capillaries for ready SERS-based detection of dissolved chemical speciesJi Won Lee &Hyang Bong Lee &Kwan Kim &Kuan Soo ShinReceived:29September 2009/Revised:6November 2009/Accepted:26November 2009/Published online:22December 2009#Springer-Verlag 2009Abstract A novel method to deposit a highly surface-enhanced Raman scattering (SERS)active silver film onto the inside surface of a glass capillary is developed.Firstly,Ag sol was synthesized by the reaction of AgNO 3with poly-(ethylenimine)(PEI),and then toluene and benzenethiol (BT)were added into the sol.The mixture was flowed through the glass capillary to obtain the SERS-active Ag film-coated glass capillary.The SERS activity of the Ag-coated capillary was dependent on the amount of PEI and BT used.In addition,BT could be easily desorbed from the Ag surface by treating it with a borohydride solution,maintaining the initial SERS activity.The SERS enhancement factor at 632.8-nm excitation was estimated to be on the order of 106.The detection limits of adenine and dipicolinic acid were then as low as 1.0×10−8and 1.0×10−7M,respectively,based on an S/N ratio of 3.This clearly suggests that the Ag-coated capillary is an invaluable device for the analysis of effluent chemicals by SERS.Keywords Adenine .Dipicolinic acid .Poly(ethylenimine).Silver nanoparticle .Surface-enhanced Raman scatteringIntroductionFor several decades,the electroless deposition of metal films has been a continuous research topic in the scientificcommunity because of its immense application prospects [1].It is especially challenging to coat thin metal films in a controlled way onto the inner surfaces of glass and plastic capillaries and microchannels [2–4].Gold-and silver-coated capillaries,for instance,can be incorporated into microchip analyzers,running on the basis of surface-enhanced Raman scattering (SERS)spectroscopy [5–8].On the other hand,the energy losses of hollow-glass waveguides,which are used for the delivery of high-power laser pulses and optical pulse compression,can be reduced significantly by coating the inside surface of the hollow waveguide with a highly reflective metallic layer [9,10].In principle,the metal film can be deposited inside the capillary,as well as the hollow silica waveguide,by a liquid-phase deposition process in which the thickness of the metal film may be controlled by varying the reaction time,the flow rate,the temperature,and the concentration of the reacting solutions [11].For the case of silver deposition,a photosensitive alkaline silver amine solution is usually mixed with a reducer solution composed of dextrose and a sodium salt of ethylenediaminetetracetic acid,and then the resultant solution is pumped into capillaries.The two primary solutions react to yield a film of metallic silver on the inner surface of the capillary [10].Otherwise,Ag films can also be formed by attaching silver particles from a colloidal suspension to glass or quartz slides derivatized with HS-terminated silanes [12,13].We have also demonstrated recently that silver can be deposited onto the inside surface of a glass capillary using only an ethanolic solution of AgNO 3and butylamine [14].We found recently that poly(ethylenimine)(PEI)-capped Au nanoparticles prepared in aqueous phase could be assembled into 2D arrays not only at the aqueous/toluene interface but also at the inner surface of the sampling bottle simply by the addition of benzenethiol (BT)[15].Au nanoparticle film could also be formed,through brief contactJ.W.Lee :H.B.Lee :K.Kim (*)Department of Chemistry,Seoul National University,Seoul 151-742,South Korea e-mail:kwankim@snu.ac.krK.S.Shin (*)Department of Chemistry,Soongsil University,Seoul 156-743,South Korea e-mail:kshin@ssu.ac.krAnal Bioanal Chem (2010)397:557–562DOI 10.1007/s00216-009-3365-9with the mixture,on the inner walls of capillary tubes[16]. Similar to gold,PEI-stabilized Ag nanoparticles can be prepared in aqueous solution in one step,and further,these particles can also be deposited as a film not only onto planar and curved surfaces of glasses but also onto silica beads and cotton fabrics.The Ag/PEI-coated capillaries would then be very useful in the development of SERS-coupled electro-phoresis,particularly so because silver,on the one hand,has higher SERS activity,and PEI,on the other hand,bears positive charges over a wide pH range to attract proteins and peptides[6,17].The purpose of this work is to assess the application capability of our Ag-coated capillary as a SERS-based chemical analysis system on a microchip.We firstly con-firmed that the as-prepared Ag-coated capillary is highly SERS active to show intense SERS peaks of BT and secondly that the BT molecules present initially on Ag surfaces can be easily desorbed by borohydride,but maintaining the initial SERS activity.The Ag-coated capillary could then be used for the detection of minute chemical species in flowing phase by SERS.Most importantly,we were able to observe the Raman peaks even when a solution containing a weakly chemisorbing biological molecule such as adenine,riboflavin,and dipico-linic acid was allowed to flow through the Ag-coated glass capillary.We are sure that this work will contribute to the development of SERS-based microchips and chemical ana-lyzers since Ag deposition is possible not only on glasses but also on plastic microchannels.ExperimentalSilver nitrate(AgNO3,99.8%),benzenethiol(BT,99+%), sodium borohydride(NaBH4,99%),adenine(99%), (−)-riboflavin(98%),dipicolinic acid(99%),and branched PEI(MW∼25kDa)were purchased from Aldrich and used as received.Other chemicals,unless specified,were of reagent grade,and highly purified water,with a resistivity greater than18.0MΩcm(Millipore Milli-Q System),was used in preparing aqueous solutions.The PEI-stabilized Ag nanoparticles were prepared by heating a mixture of100mL of10mM AgNO3and0.5–3mL of2%(w/w)PEI for15min.The size of the Ag nanoparticles was controlled by the amount of PEI added into the reaction mixture.The reacted mixture was ultra-centrifuged and filtered,and the precipitate was washed with copious amounts of deionized water.The PEI-stabilized Ag nanoparticles were re-dispersed in water, and toluene was subsequently poured over the aqueous Ag sol.A fairly homogeneous film was formed at the toluene–water interface by adding BT into the toluene phase.A large area of2D film was also able to form on a separate glass substrate immersed in the mixture.When depositing Ag onto the inside walls of a capillary,the mixture was injected using a syringe through the capillary tube:The glass capillary was of dimensions1.1mm in inner diameter by0.2mm in thickness and75mm in length.The flow of solutions through the capillary tube was controlled using a Sage Instruments Model341syringe pump.UV–vis spectra were obtained with a SINCO S-4100 UV–vis absorption spectrometer.Transmission electron microscope(TEM)images were taken on a JEM-200CX transmission electron microscope at200kV.Field emission scanning electron microscope(FE-SEM)images were obtained with a JSM-6700F FE-SEM operated at5.0kV. Raman spectra were obtained using a Renishaw Raman system Model2000spectrometer.The632.8-nm line from a 17-mW He/Ne laser(Spectra Physics Model127)was used as the excitation source.Raman scattering was detected over180°with a Peltier cooled(−70°C)charge-coupled device camera(400×600pixels).The data acquisition time was usually30s,and the measured intensity was normalized with respect to that of a silicon wafer at520cm−1.Results and discussionThe PEI-stabilized Ag nanoparticles were readily produced when a mixture of PEI and AgNO3solutions was heated. The size of the Ag nanoparticles was largely dependent on the molar ratio of the PEI and AgNO3.By increasing the molar ratio of PEI,smaller metal particles were produced, and vice versa.In this study,approximately5–30-nm-sized Ag nanoparticles were prepared,as demonstrated in the TEM images in the upper panels of Fig.1.The particles are spherical;the average sizes are5±4,14±6,or30±10nm. Clearly,when the concentration of PEI is low,larger particles are formed.In the UV–vis absorption spectra shown in the lower panel of Fig.1,the surface plasmon resonance(SPR)bands of Ag nanoparticles are observed at 390–408nm,depending on the ratio of PEI added into the reaction mixture.Specifically,the maximum of the SPR bands appears at390,398,and408nm,respectively,for the Ag sols corresponding to the TEM images.The distinct appearance of the SPR bands indicates that the PEI-stabilized Ag nanoparticles are present in a well-dispersed state.The gradual red-shift reflects the production of larger-sized nano-particles at lower PEI concentrations.The assembly of nanoparticles into homogeneous2D arrays is usually difficult to achieve due to their uncontrolled coagulation[18,19].We discovered that a fairly homoge-neous Ag film is formed at the water–toluene interface by heating the mixture of toluene and PEI-stabilized Ag sol to the boil.A more homogeneous Ag film is formed,this time at room temperature,when BT is added into the toluene phase.A yellowish Ag solution turns into a purple-colored558J.W.Lee et al.film at the toluene –water interface,as well as on the bottle wall.The fact that the filmed layer crept up the glass walls of the vial indicates that the force driving the formation of an interfacial monolayer is very strong.A 2D Ag film formed at the water –toluene interface can be transferred onto a separate glass substrate immersed in the mixture or onto the inner wall of a glass capillary as shown in the inset of Fig.2.The Ag film formed on a mica substrate by adding BT showed an UV –vis absorption band at ∼650nm as shown in Fig.2a.Its absorbance also increased upon increasing the amount of BT up to 1.0mL.The red-shift of the SPR band as much as ∼250nm from that in aqueous solution and the increase in its absorbance are indicative of the close-packing of Ag nano-particles in the film state [20].Much the same Ag film can be fabricated immediately onto the inside surface of a glass capillary by injecting a mixture comprised of BT,toluene,and PEI-stabilized Ag colloid through the capillary tube.As one expects from the intense SPR band at ∼650nm in the UV –vis spectra,strong Raman peaks of BT are observed,using a He/Ne laser at 632.8nm,from the Ag film assembled on glasses.It must be a SERS spectrum of BT.A fairly intense SERS spectrum of BT is also measured by focusing the laser light axially through the capillarywall,as shown in Fig.3a.The bands at 998,1,021,1,072,and 1,573cm −1in Fig.3a can be assigned to the in-plane ring-breathing mode,the in-plane C –H bending mode,the in-plane ring-breathing mode coupled with the C –S stretching mode,and the C –C stretching mode,respectively [21].When Ag film is formed by the addition of BT,its thickness is subtly dependent on the amount of BT added to the toluene phase.This can be seen in the UV –vis spectra of Ag films deposited on glass slides (data not shown),in which the absorbance clearly increases upon increasing the amount of BT from 0.1to 1.0mL,while the position of the SPR band gradually red-shifts from 530to 650nm.TheFig.2(a )UV –vis spectrum of the PEI-stabilized Ag film on a mica substrate formed by adding BT to the toluene phase.For comparison,the UV –vis spectrum of Ag nanoparticles corresponding to Fig.1is also shown in (b ).The inset shows the photograph of the Ag films transferred onto a separate glass substrate or onto the inner wall of glasscapillaryFig.1(Upper panel )TEM images and (lower panel )UV –vis spectra of Ag nanoparticles prepared by heating 100mL of 10mM aqueous AgNO 3with (a )3,(b )1,and (c )0.5mL of a 2%(w /w )aqueous PEI solution for 15minFig.3SERS spectra of BT adsorbed on PEI-stabilized Ag film on a glass substrate measured (a )as-prepared and (b )after treating with 0.1M borohydride for 30min,and then (c )after readsorption of BT (treating with 1mM BT for 1h)A novel fabrication of silver-coated glass capillaries 559optical property of the2D film is also affected by the initial size of the Ag nanoparticles.In this study,the most intense SERS peaks of BT are observed from an Ag-coated capillary fabricated using a mixture of1.0mL of BT,2mL of toluene, and5mL of Ag sol comprised of30-nm-sized Ag nano-particles.Subsequent experiments have thus been conducted using those capillaries.In order to use those capillaries in probing the adsorption characteristics of other adsorbates,BT should not interfere with these molecules,however.BT can be desorbed from the PEI-stabilized Ag nano-particles without disturbing the SERS activity of the Ag film.This is possible due to the potential dependent adsorption strength of thiol molecules onto Ag.When a cathodic scan is applied to a thiol-adsorbed Ag electrode, thiol molecules are gradually desorbed from the electrode [22].In this work,we pursued an alternative method, treating the thiol-adsorbed Ag substrates with an ethanolic solution of borohydride.Recently,Yan et al.reported that self-assembled monolayers(SAMs)of thiols on gold can be removed efficiently by immersing the SAMs in NaBH4 solution[23].This method also works well,using Ag nanoparticle-coated glass capillary.Figure4a shows a series of SERS spectra taken under the flow of0.1M ethanolic borohydride through a capillary tube.The SERS peaks of BT gradually diminished with the borohydride treatment. This is seen more clearly from the band area of the BT peak at1,573cm−1drawn versus the contact time with borohydride,as shown in Fig.4b.More than80%of BT is desorbed from the Ag within5min.It is remarkable that the SERS activity of the PEI-stabilized Ag is maintained even after the treatment with borohydride.When BT is readsorbed onto the Ag substrate,the SERS spectrum is restored,as shown in Fig.3b,c.We have taken SERS spectra of a few compounds of biological significance,i.e.,aqueous solutions of adenine (DNA base)and riboflavin(biosynthetic cofactor)as shown in Fig.5.The observed SERS spectral patterns of adenine and riboflavin are very similar to the reported data[24,25]. The ready acquisition of Raman spectra for small amounts of substances of biological importance is very promising. Therefore,it is worth examining the detection limit of the present methodology for biological compounds.In this light,we have taken a series of Raman spectra by flowing an adenine solution at various concentrations ranging from 10−4to10−8M through the Ag-coated capillary.In all cases,the Raman peak intensities reached a maximum value within10min:The time reaching to equilibrium may be reduced by adjusting factors such as the length of capillary and the flow rate of solution for the real-world applications.Figure6a shows the SERS spectra thus obtained after10min of flow of adenine at various concentrations.In agreement with the previous reports,one distinct band is observed at734cm−1,along with a series of weak bands in the region1,200−1,500cm−1;all these bands were assigned previously to the skeletal vibration modes[24].Figure6b shows the intensity of the adenine peak at734cm−1drawn versus the concentration of adenine solution.It is seen that the SERS signal attains a plateau value when the adenine concentration is above5×10−6M,probably due to the full coverage of adenine molecules onto silver.When the adenine concentration is lower than10−6M,the number of adsorbed adenine molecules decreases,resulting in weaker SERS signals.Nonetheless,we are able to detect as low as2.0×10−8M of adenine with an S/N ratio of4.5±1.0;the detection limit would then be1.0×10−8M based on an S/N ratio of3. Based on these promising results,we have subsequently attempted to detect dipicolinic acid,a signature molecule for bacterial spores.Dipicolinic acid is an excellent marker molecule for bacterial spores,including those of Bacillus anthracis (anthrax)[26].Other relatively harmless bacteria of the same genus also produce dipicolinic acid-containing spores, so the detection of dipicolinic acid alone maynot Fig.4(a)SERS spectra taken during the flow of a0.1M ethanolic solution of borohydride through a capillary coated earlier with BT-adsorbed,PEI-stabilized Ag nanoparticles:The flow rate of borohy-dride was0.19mL/min.(b)Band area of the BT peak at1,573cm−1 versus the contact time with borohydride in(a)560J.W.Lee et al.necessarily be indicative of the presence of a biohazard.However,the detection of bacterial spores of any type in an unexpected setting is sufficient to call attention to the need of further investigation [27].The sensitivity of SERS,combined with its molecular specificity,suggests that SERS would be well suited for the detection of spores through identification of dipicolinic acid [28].However,the affinity of dipicolinic acid for Ag or Au surfaces is known to be lower than that of even pyridine [29].Our silver-coated glass capillary can nonetheless be used to detect dipicolinic acid down to a sub-micromolar regime.Similar to adenine,we have taken a series of Raman spectra by flowing a dipicolinic acid solution at 10−3–10−7M through an Ag-coated capillary.The most distinct band was identified,immediately after the flow of the solution,at 1,010cm −1that could be assigned to the ring-breathing vibration of the pyridine ring,and about 10min was required to reach a steady state.Figure 7ashowsFig.6(a )Collection of SERS spectra of adenine measured after the attainment of steady state during the flow of its solution at 10−4−10−8M through an Ag-coated capillary.(b )The peak intensity of the ring-breathing band of adenine at 734cm −1in (a ),normalized with respect to that of a silicon wafer at 520cm −1versus the concentration ofadenineFig.5SERS spectra of (a )adenine and (b )riboflavin adsorbed on Ag nanoparticle-coated glass capillary in 1mM ethanolicsolutionFig.7(a )Collection of SERS spectra of dipicolinic acid measured after the attainment of steady state during the flow of its solution at 10−3−10−7M through an Ag-coated capillary.(b )The peak intensity of the ring-breathing band of dipicolinic acid at 1,010cm −1in (a ),normalized with respect to that of a silicon wafer at 520cm −1versus the concentration of dipicolinic acidA novel fabrication of silver-coated glass capillaries 561the collection of SERS spectra measured after the attainment of steady state at various concentration of dipicolinic acid. Figure7b shows the intensity of the ring-breathing band at 1,010cm−1drawn versus the concentration of dipicolinic acid solution.Based on an S/N ratio of3,the detection limit is estimated to be1.0×10−7M.This clearly suggests that our Ag-coated capillary is an invaluable device for the analysis of effluent chemicals by SERS.ConclusionsWe have succeeded in depositing Ag nanoparticles onto the inner surface of a glass capillary simply by injecting a mixture, composed of BT,toluene,and PEI-stabilized Ag sol produced by heating a PEI-containing AgNO3solution,through the capillary.The Ag-coated capillary was a very efficient SERS-active substrate to be usable in the microanalysis of effluent chemicals.The detection limits of adenine and dipicolinic acid were,for instance,as low as1.0×10−8and 1.0×10−7M,respectively,based on an S/N ratio of3.Since the present method is cost effective and is suitable for the mass production of Ag-coated capillaries,its application prospects are expected to be very high in many areas of science and technology including microchemical analysis, especially for in situ,real-time detection and monitoring of dissolved species by SERS in microfluidic devices. Acknowledgments This work was supported by the Korea Science and Engineering Foundation(grant no.R11-2007-012-02002-0and M10703001067-08M0300-06711-Nano2007-02943)and the Korea Research Foundation(grant KRF-2008-313-C00390,KRF-2008-313-C00411,and2009-0072467).References1.Mallory GO,Hajdu JB(eds)(1990)Electroless plating:fundamentalsand applications.American electroplaters and surface finishers society,Orlando2.Niidome Y,Takahashi H,Kawasawa T,Hori A,Yamada S(2003)Jpn J Appl Phys42:7640–76413.Goluch ED,Shaikh KA,Ryu K,Chen J,Engel J,Liu C(2004)Appl Phys Lett85:3629–36314.Xia Y,Venkateswaran N,Qin D,Tien J,Whitesides GM(1998)Langmuir14:363–3715.Kennedy BJ,Milofsky R,Carron KT(1997)Anal Chem69:4708–47156.He L,Natan MJ,Keating CD(2000)Anal Chem72:5348–53557.Mulvaney SP,Keating CD(2000)Anal Chem72:145–1588.Pumera M,Wang J,Grushka E,Polsky R(2001)Anal Chem73:5625–56289.Marcatili EAJ,Schmeltzer RA(1964)Bell Syst Tech J43:1783–180910.Mohebbi M,Fedosejevs R,Gopal V,Harrington JA(2002)ApplOpt41:7031–703511.Rabii CD,Gibson DJ,Harrington JA(1999)Appl Opt38:4486–449312.Park SH,Im JH,Im JW,Chun BH,Kim JH(1999)Microchem J63:71–9113.Yang L,Guihen E,Glennon JD(2005)J Sep Sci28:757–76614.Park HK,Yoon JK,Kim K(2006)Langmuir22:1626–162915.Kim K,Lee HB,Lee JW,Park HK,Shin KS(2008)Langmuir24:7178–718316.Kim K,Lee JW,Lee HB,Shin KS(2009)Langmuir25:9697–970217.Nutku MS,Erim FB(1999)J Microcolumn Sep11:541–54318.Chi LF,Rakers S,Hartig M,Fuchs H,Schmid G(1998)ThinSolid Films327:520–52319.Brown JJ,Porter JA,Daghlian CP,Gibson UJ(2001)Langmuir17:7966–796920.Grabar KC,Freeman RG,Hommer MB,Natan MJ(1995)AnalChem67:735–74321.Joo TH,Kim MS,Kim K(1987)J Raman Spectrosc18:57–6022.Widrig CA,Chung C,Porter MD(1991)J Electroanal Chem310:335–35923.Yan M,Zhan S,Zhou X,Liu Y,Feng L,Lin Y,Zhang Z,Hu J(2008)Langmuir24:8707–871024.Maxwell DJ,Emory SR,Nie S(2001)Chem Mater13:1082–108825.Nirode WF,Devault GL,Sepaniak MJ(2000)Anal Chem72:1866–187126.Murrell WG(1969)In:Goul GW,Hurst A(eds)The bacteriaspore.Academic Press,London,ch.727.Bell SEJ,Mackle JN,Sirimuthu NMS(2005)Analyst130:545–54928.Zhang X,Young MA,Lyandre O,Van Duyne RP(2005)J AmChem Soc127:4484–448929.Bell SEJ,Sirimuthu NMS(2008)Chem Soc Rev37:1012–1024562J.W.Lee et al.。
The Properties of Amorphous and Glassy Materials

The Properties of Amorphous and GlassyMaterialsAmorphous and glassy materials are two important types of solids with unique properties that distinguish them from crystalline solids. Unlike crystalline solids, amorphous and glassy materials lack long-range periodicity in their atomic arrangements. This leads to several interesting properties that are advantageous for various applications.One of the most important properties of amorphous and glassy materials is their mechanical strength. They typically exhibit high hardness and high fracture toughness, making them ideal for use in applications that require durable materials. For example, glasses are often used in the construction of windows and mirrors because they are highly resistant to shattering upon impact.Another important property of amorphous and glassy materials is their optical transparency. Because their atomic arrangements lack long-range order, they do not have a characteristic X-ray diffraction pattern. This causes them to scatter light differently compared to crystalline materials, resulting in unique optical properties. For example, amorphous materials can be made transparent or opaque depending on their composition and processing conditions. This property has been exploited to create a range of materials with applications in electronics, optics, and photonics.Amorphous and glassy materials also exhibit interesting electrical properties. They can be optimized for high resistance or high conductivity depending on their composition and processing conditions. For example, glasses have been developed with high electrical resistivity, making them ideal for use in insulating materials. Moreover, amorphous semiconductors have been developed with unique electronic properties, making them ideal for use in electronic devices.Another important property of amorphous and glassy materials is their thermal stability. Because they lack long-range atomic order, they do not have any preferred directions for thermal expansion. This makes them highly stable over a wide temperaturerange, making them ideal for use in high-temperature applications. For example, glasses have been developed for use in high-temperature furnaces and in aerospace applications where materials must be able to withstand extreme thermal conditions.Finally, the amorphous and glassy states are highly important for the study of fundamental physics and materials science. For example, they can be studied to better understand the underlying mechanisms that lead to the glass transition, which is a fundamental phenomenon in condensed matter physics. Moreover, the development of new glass and amorphous materials has led to the discovery of entirely new material properties and has opened up new areas of research in materials science.In conclusion, amorphous and glassy materials are unique types of solids that exhibit several important properties, including mechanical strength, optical transparency, electrical properties, thermal stability, and the ability to be studied for fundamental physics and materials science. These properties make them ideal for a range of applications in electronics, optics, aerospace, and other fields, as well as important for advancing our understanding of the underlying principles governing the behavior of solids.。
材料概论单词表

Chapter 1alloy 合金atomic-scale architecture 原子尺度结构(构造)brittle 脆性的ceramic 陶瓷composite 复合材料concrete 混凝土conductor 导体crystalline 晶态的devitrified 反玻璃化的(晶化的)ductility (可)延(展)性,可锻性electronic and magnetic material? 电子和磁性材料element 元素fiberglass 玻璃钢glass 玻璃glass-ceramic 玻璃陶瓷/微晶玻璃insulator 绝缘体materials science and engineering 材料科学与工程materials selection 材料选择metallic 金属的microcircuitry 微电路microscopic-scale architecture 微观尺度结构(构造)noncrystalline 非晶态的nonmetallic 非金属的oxide 氧化物periodic table 周期表plastic 塑性的、塑料polyethylene 聚乙烯polymer 聚合物property 性能(质)refractory 耐火材料、耐火的semiconductor 半导体silica 石英、二氧化硅silicate 硅酸盐silicon 硅steel 钢structural material 结构材料wood 木材Chapter 7aluminum alloy 铝合金gray iron 灰口铁amorphous metal 无定形金属high-alloy steel 高合金钢austenitic stainless steel 奥氏体不锈钢high-strength low-alloy steel 高强度低合金钢Brinell hardness number 布氏硬度值Hooke’s law 胡克定律carbon steel 碳钢impact energy 冲击能cast iron 铸铁lead alloy 铅合金Charpy test Charpy试验low-alloy steel 低合金钢cold working 冷作加工lower yield point 屈服点下限copper alloy 铜合金magnesium alloy 镁合金creep curve 蠕变曲线malleable iron 可锻铸铁primary stage 第一(初期)阶段martensitic stainless steel 马氏体不锈钢secondary stage 第二阶段modulus of elasticity 弹性模量tertiary(final)? stage 第三(最后)阶段modulus of rigidity 刚性模量dislocation climb 位错攀(爬)移nickel alloy 镍合金ductile iron 球墨铸铁nickel-aluminum superalloy 镍铝超合金ductile-to-brittle transition temperature 韧性-脆性转变温度nonferrous alloy 非铁合金ductility (可)延(展)性,可锻性plastic deformation 塑性变形elastic deformation 弹性变形Poission’s ratio 泊松比engineering strain 工程应变precious metal 贵金属engineering stress 工程应力precipitation-hardened stainless steel 沉淀(脱溶)硬化不锈钢fatigue curve 疲劳曲线rapidly solidified alloy 速凝合金/快速固化合金fatigue strength (endurance limit) 疲劳强度(耐久极限)refractory? metal 耐火(高温)金属ferritic stainless steel 铁素体不锈钢Rockwell hardness 洛氏硬度ferrous alloy 铁基合金shear modulus 剪(切)模量fracture mechanics 断裂机制shear strain 剪(切)应变fracture toughness 断裂韧性shear stress 剪(切)应力gage length 标距(长度),计量长度,有效长度solution hardening 固溶强化galvanization 电镀,镀锌steel 钢strain hardening 应变强化white iron 白铁,白口铁superalloy 超合金wrought alloy 可锻(锻造、轧制)合金tensile strength 拉伸强度yield point 屈服点titanium alloy 钛合金yield strength 屈服强度tool steel 工具钢Young’s modulus 杨氏模量toughness 韧性zinc alloy 锌合金upper yield point 屈服点上限Chapter 8annealing point 退火点linear coefficient of thermal expansion线性热膨胀系数refractory 耐火材料borosilicate glass 硼硅酸盐玻璃expansion 膨胀silicate 硅酸盐brittle fracture 脆性断裂magnetic ceramic 磁性陶瓷silicate glass 硅酸盐玻璃clay 粘土melting range 熔化(温度)范围soda-lime silica glass 钠钙硅酸盐玻璃color 颜色modulus of rupture 断裂模量softening point 软化点cosine law 余弦定律network former 网络形成体specular reflection 镜面反射creep 蠕变netwrok modifier 网络修饰体/网络外体static fatigue 静态疲劳crystalline ceramic 晶态陶瓷nonoxide ceramic 非氧化物陶瓷structural clay product 粘土类结构制品diffuse reflection 漫反射nonsilicate glass 非硅酸盐玻璃surface gloss 表面光泽E-glass 电子玻璃(E玻璃)nonsilicate oxide ceramic 非硅酸盐氧化物陶瓷tempered glass 钢化玻璃electronic ceramic 电子陶瓷nuclear ceramic 核用陶瓷thermal conductivity 热传导率enamel 搪瓷nucleate 成(形)核thermal shock 热震Fourier’s law 傅立叶定律Opacity 乳浊transformation toughening 相变增韧fracture toughness 断裂韧性optical property 光学性质translucency 半透明Fresnel’s formula Fresnel公式partially stabilized zirconia ??部分稳定氧化锆transparency 透明glass 玻璃polar diagram 极坐标图viscosity 粘度glass-ceramic 玻璃陶瓷/微晶玻璃pottery 陶器(制造术)viscous deformation 粘性变形glass transition temperature 玻璃转变温度pure oxide 纯氧化物vitreous silica 无定形二氧化硅/石英玻璃glaze 釉reflectance 反射(率)whiteware 白瓷Griffith crack model Griffith裂纹模型refractive index 折射率working range 工作(温度)范围intermediate 中间体/中间的Chapter 9Chapter 10admixture 外加剂fiberglass 玻璃钢metal-matrix composite 金属基复合材料aggregate 聚集体fiber-reinforced composite 纤维增强复合材料particulate composite 颗粒复合材料aggregate composite 聚集体复合材料hardwood 硬质木材polymer-matrix composite 聚合物基复合材料anisotropic 各向异性hemicellulose 半纤维素portland cement 波特兰水泥cement 水泥interfacial strength 界面结合强度property averaging 性能平均ceramic-matrix composite 陶瓷基复合材料isostrain 等应变radial cell 径向细胞concrete 混凝土isotress 等应力softwood 软质木材continuous fiber 连续纤维isotropic 各向同性specific strength 比强度discrete (chopped) fiber 不连续(短切)纤维laminate 层状的strength-to-weight ratio 强度质量比率dispersion-strengthened metal 弥散强化金属lignin 木质素whisker 晶须longitudinal cell 经向(纵向)纤维wood 木材woven fabric 纺织构造E-glass 电子玻璃matrix 基质(体)philosophy 基本原理cross over 交叉,穿过,跨越restriction 限制(定)configuration 构造(形式),结构align 使成一直线(一行)elongate 拉长(的)/延伸(的)aggregate 集料,粒料,骨料chop 切utility 效用,实用,功用in regard for 考虑到cite 引用(证、述),援引,列举,举出(例),提到,谈到embed 埋置,把? 嵌入(或插入)dielectric 电介质implication 含意(义)epoxy 环氧树脂polyester 聚酯polyetheretherketone (PEEK) 聚醚酮醚polyphenylene sulfide (PPS) 聚苯亚砜entrant 新到者requisite 必需的imitate 仿deciduous 每年落叶的,非永久的commonality 共性,共同特点dramatic 生动的vertically 竖直地,直立地longitudinal 经度的,纵向的sap 树液cellulose 纤维素alignment 直线排列phenol-propane 苯酚-丙烷manifest 显示,出现,显露dimension 尺寸specify 详细说明staggering 令人惊愕的igneous 火成的inspection 检查,视察interstice 空隙,裂缝enclose 包围,封闭entrain 混(气泡)于混凝土中entrap 截留的,夹杂的thaw 融化(解),解冻identify 认识,鉴定,确定generality 一般(性),一般原则,普遍(性),通则consistent with 与? 一致emphasis 强调,重点,重要性axially 轴向weighted average 加权平均elementary 基本的reverse 相反的rigorous 严格的,严密的,精确的bound 限度take for granted 被忽略(视)communicate 传达,传递deflect 偏转unless otherwise state 除非另外说明appreciation 正确评价,鉴别substantial 多的,大的,大量的offset 弥补,抵消,偏移assembly 装配,组装,总成Chapter 11capacitor 电容器electron-hole pair 电子-空穴对piezoelectric coupling coefficient 压电耦合系数ceramic 陶瓷electronic conduction 电子传导piezoelectric effect 压电效应charge carrier 载流子energy band 能带polymer 聚合物charge density 电荷密度energy band gap 能隙positive charge carrier 正载流子coercive field 矫顽(电)场energy level 能级PZT 锆钛酸铅conduction band 导带extrinsic semiconductor 非本征半导体remanent polarization 剩余极化conductivity 传导率Fermi function 费米函数resistivity 电阻率conductor 导体Fermi level 费米能级resistance 电阻current 电流ferroelectric 铁电性reverse piezoelectric effect逆压电效应dielectric 介电性,介电体free electron 自由电子saturization polarization 饱和极化dielectric constant 介电常数glass 玻璃Seebeck potential 赛贝克(电)势dielectric strength 介电强度hysteresis loop (电)滞回线semiconductor 半导体domain (电)畴insulator 绝缘体spontaneous polarization 自发极化drift velocity 漂移速率intrinsic semiconductor 本征半导体superconductor 超导体electric permittivity 电容率,介电常数metal 金属temperature coefficient of resistivity 电阻率温度系数electrical conduction 电导negative charge carrier 负载流子electrical field strength 电场强度Ohm’s law 欧姆定律thermocouple 热(电)偶electrically poled 电极化的orbital 轨道transducer 变(转)换器/换能器electron 电子paraelectric 顺电性的valence band 价带electron hole 电子空穴Pauli exclusion principle 泡利不相容原理voltage 电压commonality (特点等的)共有,共同特点,共性in light of 按照,根据manifestation 显示,表明,表现,表现形式,现象give way to 让路(步),退让,让位,屈服spacing 间隔(距)abstract 抽象reciprocal 倒数的mobility 迁移率drift 漂移precisely 正好地hypothetical 假(设)定的delocalize 使离开原位extension 扩展(充)pseudocontinuous 准连续的nature 自然状态conductive to 有助(益)的on the order of (数值)相当于,大约,数量级为,跟相似的accessibility 能进入(的),可得到(的)inability 无能(力)attribute to 归结于agitation 扰动wave packet 波包(群)irregularity 不规则,无规律reminiscent 回忆往事的,提醒的,暗示的ultimately 最后(终)于trace 追溯,上溯ambient 周围的(环境)tabulate 把......制成表格,列表finite 有限的empirical 经验的ironically 冷嘲的,具有讽刺意味的,用反语的,挖苦的,令人啼笑皆非的synchronization 同时发生,同步cooperative 配合account for 解释,占多少比例speculation 思索cryogenic 低温学的appreciable 可评估的,可感知的breakdown 崩溃,击穿subsection 细分asymmetrical 不对称的dipole 偶极子polarization 极化crystallographic 晶体的,晶体学的at the expense of 以…..为代价symmetrical 对称的exaggerate 夸张(大)extrapolate 推断(知),外推induce 诱导prefix 前缀intriguing 引起? 的兴趣(或好奇心)stem from 由…引起的,产生(起源、归因于),出身于constrain 强迫,抑制,约束straightforward 简单,易懂的ensuring 确保,保证pseudo-single crystal 准单晶consolidate 加固,使合成一体transmitter 变送器,发射机oscillation 振动megahertz MHzChapter 12acceptor level 受主能级device 元件impurity 杂质amorphous semiconductor 无定形半导体diode 二极管intrinsic semiconductor 本征半导体amplifier 放大器donor level 施主能级microcircuit 微电路Arrhenius behavior ???Arrhenius行为dopant 掺杂剂n-type semiconductor ??n型半导体base 基极drain 漏极p-n junction? ??p-n结carrier mobility 载流子迁移(率)electron hole 电子空穴p-type semiconductor? p型半导体chalcogenide 硫族(属)化物emitter 发射极rectifier 整流器charge 电荷energy band gap 能隙reverse bias ?反向偏置charge carrier ??载流子exhaustion range 耗尽区saturation range 饱和区charge density 电荷密度extrinsic semiconductor 非本征半导体source 源极chip (基)片Fermi function 费米函数thermal activation 热激活collector 集电极Fermi level 费米能级III-V compound III-V化合物compound semiconductor 化合物半导体field-effect transistor (FET) 场效应晶体管II-VI compound II-VI化合物conduction band 导带forward bias 正向偏置transistor 晶体管conduction electron 传导电子gate 栅极valence band 价带conductivity 传导率Hall effect 霍尔效应clustered 丛生,成群overlap 交迭activation 活化,激活occurrence 发生,出现,事件,发生的事情dominate 支配,占优势semilog 半对数的ambient 周围(环境)的phosphorus 磷plateau 平原/平台compensation 补(赔)偿intimate 亲密at right angle 成直角sideways 侧(横)向in order 整齐,状态良好,适应on the average 平均,按平均数计算,一般地说zinc blende 闪锌矿counterpart 配对物threshold 开始(端),极限photovoltaic 光电nondepletable 耗不尽的silane 硅烷xerography 静电复印术photoconductive 光敏polarization 极化herald 先驱,先兆excess 过量的,额外的,附加的overshoot 过冲distort 畸变,使失真Chapter 13antiparallel spin pairing 反平行(电子)对domain (bloch) wall 畴壁flux density 通量(磁力线)密度eddy current 涡流garnet 石榴子石Bohr magneton 玻尔磁子electron spin 电子自旋hard magnet 硬(永)磁铁(体)ceramic magnet 陶瓷磁铁(体)energy loss 能(量)损(失)hysteresis loop (磁)滞回线coercive field 矫顽(磁)场exchange interaction 交互作用induction 感应(诱导)coercive force矫顽(磁)力ferrimagnetism 铁氧体磁性,(亚)铁磁性inverse spinel 反尖晶石diamagnetism 抗(反)磁性ferrite 铁氧体,铁素体Joule heating 焦耳热domain structure 畴结构ferromagnetism 铁磁性magnetic dipole 磁偶极子magnetic field 磁场metallic magnet 金属磁体soft magnet 软(暂时)磁体(铁)magnetic field strength 磁场强度paramagnetism 顺磁性spinel 尖晶石magnetic flux line 磁通量(力)线permanent magnet 永(久)磁体superconducting magnet 超导磁体magnetic moment 磁矩permeability 导磁性(率)textured micostructure 织构magnetism 磁性preferred orientation 择优取向transition metal 过渡金属magnetite 磁铁矿(石)relative permeability 相对(磁)导率transition metal ion 过渡金属离子magnetization 磁化remanent induction 剩余感应YIG 钇铁石榴子石Magnetoplumbite 磁铅石,磁铁铅矿saturation induction 饱和感应nomenclature 命名routinely 常规,惯例counterpart 对手modest 小的reversible 可逆的traced out 探寻踪(轨)迹primitive 原始的,早期的,开始的,基本的,简单的visualize 目测,观察,设想relativistic 相对论的aligned 排列好的distinction (差)区别,特性tetrahedrally 四面体的octahedrally 八面体的inventory 清单,目录cancellation 抵(取)消traverse 在?? 上来回移动,沿? 来回移动flunctuate 波动,涨落,起伏,动摇不定ingot 铸模,铸块,锭fidelity 保真Samarium 钐Alnico 磁钢simultaneously 同时发生的product? (乘)积solenoid 螺线管deflection 偏转interchangeably 可交(互)换的,可代替的gem 宝石dodecahedral 十二面体的waveguide 波导hexagonal 六方晶系的strontium 锶fortuitous 偶然的,幸运的perovskite 钙钛矿availability 利用(或获得)的可能性levitation 悬浮Chapter 11. In the term “Materials Science and engineering”, the word materials include andmaterials, “science” relates to the of materials, “engineering” is about .?2. To understand the properties of a material, one needs to examine of the material at either microscopic or submicroscopic scale (atomic and/or microscopic).Composition----technology----structure----properties----application is the line in materials scienceand engineering.3. structural materials include ,? , , .4. semiconductors are a type of electronic materials with its unique, electrical conductivity.5. What are the levels (or steps) in the selection of materials for a given design?1.16. What are the general characteristics of metals? (or what are the characteristics that a material is considered to be metallic?)7. Where are the metal elements located in the periodic table?8. V arious aluminum parts can be fabricated by . The unusually high degree of for the these alloys is possible with a carefully controlled, microstructure.9. Compare the properties of aluminum and aluminum oxide (advantages and disadvantages)10. What are the developments in ceramic technology?11. SiO2 is the basis of a large and complex family of , which include clays and claylike materials.12. The composition characteristics of ceramics.13. Explain the concept “ crystalline” and “ noncrystalline”.14. Constituents in window glasses.15. What are steps for getting glass-ceramics?16. Structure and property characteristics of glass-ceramics.17. Characteristics of lithium aluminosicliate compounds.18.What is the alternative name for polymers? What do plastics imply?19. Polymer consists of “poly” and “mer”. What is “mer”?20. What are the elements for the polymers?21.What is the property that plastics share with metals?22. What are characteristics of polymers (advantages and disadvantages)?23. What are the progress of “engineering polymers”?24. What are composites?25. Take fiberglass as an example to explain the property of good composites.26. Give examples of composites and their constituents.27. What is semiconduction?28. Where are the semiconducting elements located in the periodic table? Give the names of examples.29. Give examples of compound semiconductors and their applications.1.230. Why aluminum alloys are more ductile than magnesium alloys?31. Why commercial ceramics are normally not transparent?32. How to get transparent ceramics?33. What is the relationship between porosity and transparency of ceramics?34. What is the application of transparent alumina ceramics?1.335. The importance of materials selection?36. Compare the characteristics of four structural materials.37. What are the factors considered in selection a substitute material?Chapter 7 Metals7.1 Ferrous alloysWhat are the two main categories of ferrous alloys? What is difference between them?What are the types of steels? How are they classified?The properties and other characteristics of carbon and low-alloy steels. Examples of their applications.What are HDLA steels? What are important to obtain these steels?What are the types of high-alloy steels? What are their main characteristics?Why stainless steels are resistant to rusting and staining?What are the types of stainless steels? How do they differentiate from each other?What are applications of tool steels?Can plain-carbon steels also be used as tool steels??What are the elements in normal cast irons?What are the characteristics of cast irons?How cast irons are shaped?What are the differences between cast irons and related wrought alloys?What are the types of cast irons? What are their differences?How to get amorphous alloys? What is feature of their microstructure? How about the superior properties of amorphous alloys?Why amorphous alloys are attractive for soft-magnet transformer cores?What are rapidly solidified alloys? What are the differences and common features of amorphous alloys and rapidly solidified alloys?7.2 Non Ferrous alloysCharacteristics of aluminum alloys.Characteristics of Al-Li alloys. Where are the alloys used?What are differences between aluminum and magnesium alloys?What is passivation? How does it contribute to the properties of titanium?What are types of structures of titanium alloys?Characteristics of copper alloys and their application examples.Characteristics of nickel alloys.What is galavanization and its application?What are the application of lead alloys? What is the problem with applications of lead?what are refractory and precious alloys?7.3 Major mechanic propertiesa stress versus strainWhat is the direct result of a pull-test?How to get the stress versus strain curve?What are the two parts in the stress versus strain curve? What are the differences?How to get the yield strength form stress versus strain curve?What are mechanisms of elastic deformation and plastic deformation?What does modulus elasticity (E) represent? How to get E from the stress versus strain curve? What are the indexes or parameters obtained from the stress versus strain curve?What is special for the stress versus strain curve of the low-carbon steel?What is Poission ratio? How to get it?Elastic deformation under shear loadings and shear modulus?b hardnessHow to do a hardness test?What are the different ways to express hardness?What is relationship between hardness and strength?c impact energyHow to measure impact energy?What is relationship between impact energy and toughness?What is the influence of the notch on the result from the Charpy test?What is the influence of test temperature on the result from the Charpy test?What is ductile-to-brittle transition of low-carbon steels? What the result of such a transition? Examples?Microstructural features of brittle and ductile failures.d fracture toughnessThe term fracture mechanics means the general analysis of of materials with preexisting .Fracture toughness is represented by the symbol KIC and is the critical value of at a necessary to produce catastrophic failure.Compare the fracture toughness of brittle and ductile materials.e fatigueGive explanation for the concept of fatigue.Draw a typical fatigue curve.What is mechanism of fatigue phenomenon?What the characteristics of a fracture surface in the case of fatigue?What is fatigue strength (endurance limit)?f creepThe definition of creep.What are the three stages of creep curve and the mechanism behind?How the Arrhenius plot is used in the creep phenomenon?The simple way to characterize the creep behavior.Chapter 88.1Why SiO2-based silicate materails are abundant?List examples of traditional ceramics. What are their applications?The composition system of Portland cement.What are refractories? Where can they be used?Give examples of advanced ceramics. What are differences between the advanced and traditional ceramics?Give examples of non-oxide ceramics and their applications.8.27. In point view of raw materials, what is similarity between silicate glasses and ceramics?8. What are oxides named in the glass composition? What are their roles in glasses?9. What is vitreous silica and its application?10. What is borosilicate glass? What are the oxides are used to make it? What are their applications?11. The general composition and applications of soda-lime-silica glasses.12. What are glazes and enamels? What are the similarity and difference?13. Examples of nonsilicate glasses.8.314. Why do glass-ceramics begin as ordinary glasses? What heat treatment is needed?15. What are characteristics of the omicrstructure of glass-ceramics?16. What are the advantages of glass-ceramics?17. Illustrate the crystallization of ordinary glass and glass after carefully controlled heat treatment.18. What are important to obtain glass-ceramics with fine (small) crystallites?19. The thermal properties of Li2O-Al2O3-SiO2 glass ceramics.8.420. What is brittle fracture?21. What is relationship between the tensile and compression strength of ceramics? Why?22. What is modulus of rupture? Form which test is it obtained?23. What is Graffith crack model? (Why ceramics and glass are brittle?)24. What is transformation toughening? Illustrate the mechanism.25. How microcracks raise fracture toughness?26. What is static fatigue? What are the conditions for static fatigue?27. Why creep is mor important in ceramics?28. What factors play important roles in the creep of ceramics?29. What is thermal shock?30. What is relationship between thermal shock and coefficient of thermal expansion, thermal conductivity? ?(How does thermal shock follow the properties of thermal expansion and thermal conductivity?)31. What are the factors influencing the thermal shock?32. What are the unique response when measuring the thermal expansion of a glass?33. What is Tg? What is the difference of a glass below and above its Tg?34. Draw a thermal expansion curve and a specific volume versus temperature curve of a glass?35. What are the ranges in the viscosity curve of a soda-lime-silica glass?36. Compare the words: Viscous behavior, viscosity, diffusivity, fluidity37. How viscous deformation is used in tempered glass?8.538. What is refractive index?39. What are the typical values of the refractive index for ceramics and glasses? What do these values mean?40. If a glass has a high refractive index, what will happen? What is the application of such a glass?41. What is reflectance? What is relationship between reflectance and refractive index?42.What is the difference between specular and diffuse reflection?43. Why do glasses and glassy coatings have high surface gloss?44. What do transparency, translucency and opacity mean?45. The microscopic mechanism of scattering?46. How color is formed in ceramics and glasses?47. The reasons for the opacity of ceramics and metals.COPYRIGHT©材料学院。
静电纺丝

Carbohydrate Polymers 92 (2013) 1012–1017Contents lists available at SciVerse ScienceDirectCarbohydratePolymersj o u r n a l h o m e p a g e :w w w.e l s e v i e r.c o m /l o c a t e /c a r b p olAntimicrobial activity of carboxymethyl chitosan/polyethylene oxide nanofibers embedded silver nanoparticlesMoustafa M.G.Fouda a ,b ,∗,M.R.El-Aassar c ,Salem S.Al-Deyab aaPetrochemical Research Chair,Chemistry Department,College of Science,King Saud University,P.O.Box 2455,Riyadh 11451,Saudi Arabia bTextile Research Division,National Research Center,Dokki,Cairo,P.O.Box 12622,Giza 12522,Egypt cPolymer Materials Research Department,Institute of Advanced Technology and New Material,City of Scientific Research and Technology Applications,New Borg El-Arab City 21934,Alexandria,Egypta r t i c l ei n f oArticle history:Received 22September 2012Received in revised form 10October 2012Accepted 19October 2012Available online 26 October 2012Keywords:ChitosanPolyethylene oxide Silver nanoparticles Electrospinning Antimicrobiala b s t r a c tA facile method to synthesize silver nanoparticles (AgNPs)using carboxymethyl chitosan (CMCTS),which act as reducing agent for silver ions as well as protecting agent for the formed AgNPs,is reported.CMCTS embedded AgNPs are mixed with polyethylene oxide (PEO).The blend polymers containing AgNPs are electrospun resulting in blend nano-fiber mats.The formation of AgNPs has been confirmed using UV–vis and TEM.The diameter range of 12–18nm of well-dispersed AgNPs with a concentration of 100ppm was obtained.The electrospun mats are characterized using SEM,EDX as well as TGA.Antimicrobial activity against different species of pathogenic/nonpathogenic;Staphylococcus aureus ATCC 25923,Pseudomonas aeruginosa ATCC 27853and Escherichia coli ATCC 25922in addition to the fungus Candida albicans ATCC 10231was studied.The results show excellent antimicrobial activity compared with nanofibers without AgNPs and AgNPs alone.© 2012 Elsevier Ltd. All rights reserved.1.IntroductionIn electrospinning,the simplest and most cost-effective method of fabricating polymer nanofibres,various polymers have been electrospun into ultrafine fibers with diameters range of 20–400nm (Huang,Zhang,&Kotaki,2003).In electrospinning,the polymer solution is placed into syringe with millimeter size nozzle.Strong electric field is applied on a droplet of polymer solution held by its surface tension at the tip of a syringe’s needle.As a result,the pendent drop becomes highly electrified and the induced charges are distributed over its surface.Increasing the intensity of electric field,the surface of the liquid drop will be distorted to a conical shape known as the Taylor cone (Taylor,1969).Once the electric field strength exceeds a threshold value,the repulsive electric force dominates the surface tension of the liquid and a stable jet emerges from the cone tip.The charged jet is then accelerated toward the target and rapidly thins and dries as a result of elongation and sol-vent evaporation.As the jet diameter decreases,the surface charge density increases and the resulting high repulsive forces split the jet to smaller jets.Ultimately,solidification occurs and fibers are deposited on the surface of the collector as randomly oriented∗Corresponding author at:Petrochemical Research Chair,Chemistry Department,College of Science,King Saud University,P.O.Box 2455,Riyadh 11451,Saudi Arabia.E-mail addresses:m gaballa@ ,mmfoudah@.sa (M.M.G.Fouda).nonwoven mats (Derch,Greiner,&Wendorff,2004).Besides charge density and applied voltage other parameters also influence the final nanofibrous structure and its properties,for example:polymer types and concentration,type of solvent,presence of electrolyte,type and concentration of electrolyte,viscosity,surface tension,tip-to-collector distance,flow rate of the polymer solution,inner diameter of the tip,material of the tip,etc.The field of nanoparticle research has witnessed tremendous growth due to the unique chemical and physical properties from the bulk.Silver nanoparticles have gained considerable attention today due to their potential applications in medical field,since it has been widely used in the production of biodegradable surgical sutures.Recently,electrospun nanofibers embedded AgNPs have a great antimicrobial potential.Different methods have been used to prepare AgNPs,where one of these is chemical reduction method in which the polymer can be used as both reducing and stabilizing agents for the formed AgNPs (Abou-Okeil,2012;Abou-Okeil,Amr,&Abdel-Mohdy,2012;El-Rafie et al.,2011;Hebeish,El-Naggar,et al.,2011;Textor,Fouda,&Mahltig,2010).Chitosan is one of the most important biopolymers,obtained from chitin,the second most abundant natural polysaccharide present on the earth next to cellulose (El-Shafei,Fouda,Knittel,&Schollmeyer,2008;Hebeish,Abdel-Mohdy,et al.,2011).The poor solubility of chitosan in water,due to its rigid crystalline structure,limits its effective utilization in electrospinning process.To overcome this drawback,it is necessary to convert chitosan to water-soluble derivative (El-Shafei et al.,2008).Chemical0144-8617/$–see front matter © 2012 Elsevier Ltd. All rights reserved./10.1016/j.carbpol.2012.10.047M.M.G.Fouda et al./Carbohydrate Polymers92 (2013) 1012–10171013Fig.1.Schematic diagram of the typical electrospinning setup.modification is anticipated to be quite promising.Carboxymethy-lation is one of the chemical methods to prepare water-soluble chi-tosan.This reaction takes place preferentially either at C-6hydroxyl groups or at the NH2-group resulting in N/O–carboxymethyl chi-tosan(CMCTS).Both products are water-soluble and contain an amino group either as the primary(NH2)or as secondary amine (NH CH2COOH).Polyethylene oxide(PEO)is one of the few biodegradable syn-thetic polymers approved for internal use in food,cosmetics, personal care products,and pharmaceutical.PEO is an effective ion conductive polymer(Morgado et al.,1999).Therefore,it is added in order to enhance the spinnability of the modified natural polymer.The objective of this research work is to synthesize well-stabilized AgNPs using CMCTS followed by electrospinning of CMCTS–AgNPs/PEO solution.The structure,morphology and the antimicrobial activity of the resulted nanofiber mats are character-ized.2.Experimental2.1.MaterialsPolyethylene oxide(PEO)(≥95%,average Mw124–186kg/mol) was obtained from Scientific Polymer Products,Inc.Silver nitrate (AgNO3)(99.998%)was purchased from Aldrich,Germany.Chi-tosan,DDA95%was obtained from Aldrich Chemical Co.,Germany. All other solvents and reagents were used as received without any further purification.2.2.Synthesis of carboxymethyl chitosan(CMCTS)The experimental technique adopted for carboxymethylation of chitosan was as follows:certain volume of sodium hydroxide solution(30%,w/v)was added to16g chitosan suspended in iso-propyl alcohol.The mixture was left under stirring for30min at room temperature.To this mixture34g of monochloroacetic acid was added and the content of theflask was subjected to continuous stirring for3h.At the end,the excess alkali was neutralized using glacial acetic acid and chitosan was precipitated by adding acetone. Finally,modified chitosan wasfiltered and washed with isopropyl alcohol/water(70:30)several times and dried at60◦C(El-Shafei et al.,2008).Thefinal product was soluble in water.2.3.Synthesis of silver nanoparticles(AgNPs)Silver nanoparticles(AgNPs)were prepared according to the procedure described by El-Rafie et al.(2011)and can be summa-rized as follows:0.5g of CMCTS is dissolved in100ml of distilled water,the temperature of the reaction is raised to60◦C and the pH is adjusted to11.5by using10M NaOH.1ml of AgNO3(1.7M) is added dropwise to the previous solution under continuous stir-ring for almost1h.The formation of silver nanoparticles solution was observed by monitoring the color change(visually,when the color of the solution started to change from its original color to the different degrees of the yellow color,then the reduction reac-tion started to work and silver nanoparticles started to seed).The AgNPs formed are characterized by(UV–vis),transmission electron microscope(TEM).2.4.Electrospinning of CMCTS–AgNPs/PEO solution2g of CMCTS is added to CMCTS solution containing sil-ver nanoparticles(0.5wt%)while stirring.To this solution,PEO (5wt%)is added slowly under continuous stirring till homogeneity occurs.Electrospinning of the prepared blend polymers solution containing AgNPs was carried out using two different methods; typical electrospinning technique and Nanospider technology as a modified electrospinning technique.A schematic diagram of the complete electrospinning apparatus is shown in Fig.1.It consisted of a syringe and stainless needle,a grounded electrode,an iron plate covered by aluminum foil as a collector,and an adjustable high voltage supply.2.5.Testing and analysisUV–vis spectrum was used to prove the formation of AgNPs (Hebeish,El-Naggar,et al.,2011).Particle shapes and sizes of AgNPs were obtained by transmission electron microscope(TEM); JEOL-JEM-1230.Scanning electron microscope(SEM)(JEOL GSM-6610LV)and(JEOL GSM-7600F)field emission scanning electron microscope were used to study the surface characteristics of elec-trospun nanofibers.Specimen in the form offilms was mounted on the specimen stabs and coated with thinfilm of gold by the sputtering method.The micrograph was taken at magnifica-tion of1000×using(KV)accelerating voltage.FT-IR spectra were obtained using FT-IR spectrometer,Bruker,TENSOR Series FT-IR1014M.M.G.Fouda et al./Carbohydrate Polymers 92 (2013) 1012–1017Fig.2.Solid state 13C NMR spectrum typical for O -carboxymethyl chitosan.Spectrometer,Germany,connected to a PC,and the data were analyzed by IR Solution software,where analytical methods are standard in OPUS TM software.2.6.Antimicrobial evaluation of electrospun nanofibersIn order to evaluate the antimicrobial properties of electrospun nanofiber mats with/without AgNPs against microbial pathogens and to compare this effect with the commonly used antibiotics in addition to AgNPs alone as +ve control,the zone of inhibition test was performed against the gram positive bacterium Staphylococ-cus aureus ATCC 25923,the gram negative bacteria Pseudomonas aeruginosa ATCC 27853and Escherichia coli ATCC 25922in addi-tion to the fungus Candida albicans ATCC 10231.To perform the test,several colonies of each strain,obtained from a fresh cul-ture in blood agar plate,were suspended in 5ml of Mueller-Hinton broth to achieve turbidity equal to the 0.5Mac-Farland standards.The suspensions were inoculated with sterile swabs onto 150mm diameter Mueller-Hinton agar plates and after the agar surfaces were allowed to dry,tested disks were applied on each plate.Plates were incubated at 37◦C for 24h and the zones of inhibition (IZ)were measured.Same was performed for the Candida except that it was inoculated in Sabouraud dextrose agar medium and incu-bated for 2–3days at 37◦C.The antimicrobial agents tested in this study were CMCTS–PEO nano-fiber incorporated with silver nano-particles (CMCTS–AgNPs/PEO),the antibiotic Amikacin (AK),ampicillin/clavulinic acid (AMC),100ppm AgNPs solution (10L per disk)as a positive control,in addition to negative controls as empty disks of CMCTS–PEO nano-fibers.3.Results and discussion3.1.Characterization of (CMCTS)by solid state 13C NMRCarboxymethylation of chitosan (CTS)is achieved with monochloroacetic acid and sodium hydroxide.According to El-Shafei et al.(2008)this reaction takes place preferentially either at C-6hydroxyl groups or at the NH 2-group resulting in N/O–carboxymethyl chitosan (CMCTS).The solid state 13C NMR spectrum for a typical N-carboxymethyl chitosan shows sig-nals attributed to the N-carboxymethyl substituent,at 47.7and 168.7ppm,for N CH 2and COOH,respectively (El-Shafei et al.,2008).But in case of our results,the solid state 13C NMR described in Fig.2shows signals at 73and 175ppm which attributed to O CH 2and COOH respectively.This downfield shift of thecarbon indicates the formation of O -carboxymethyl chitosan.The formation of this product agrees with the higher reactivity of hydroxyl group of C 6in this heterogeneous reaction.The N -carboxymethyl substituent is not present because of the absence of peaks at 47and 168ppm for N CH 2and COOH respectively.3.2.Characterization of the synthesized silver nanoparticles (AgNPs)In this research work,CMCTS was used as reducing and as stabi-lizing agent too.The formation of AgNPs could be visualized from changes in the color of the solutions from colorless to light yellow.The reduction of Ag +could occur via the reduction effect of CMCTS at 60◦C and pH 11.5for 30min.Fig.3shows the UV–visible absorp-tion spectra of AgNPs.The surface plasmon absorption bands are centered around 409nm (El-Rafie et al.,2011).The absorption band at 405nm becomes stronger and narrower which means higher conversion of Ag +to Ag 0with smaller nanoparticles size.Fig.4a and b shows the TEM image and the histogram of the size and size distribution of the AgNPs.Results revealed that the size range of prepared AgNPs was between 12and 18nm.3.3.Morphology of the CMCTS–AgNPs/PEO-electrospun nanofibersThe performance and morphology of the electrospun fiber were affected by the electrospinning process parameters.In the present study,two different electrospinning setups were used.In the first setup,a typical electrospinning setup was used (Fig.1)alongwithFig.3.UV–vis spectra of silver nanoparticles embedded in CMCTS.M.M.G.Fouda et al./Carbohydrate Polymers92 (2013) 1012–10171015Fig.4.(a and b)TEM image and the histogram of the size and size distribution of the AgNPs.Nanospider technology.Both electrospinning setup and Nanospi-der are used in order to prepare nanofiber mats,but,Nanospider is used in large scale/sample production of the selected and best nanofiber mats from the results obtained,in addition,no differ-ence in morphology of the resulted mats for both techniques is observed.Generally,the electrospun mat is opaque due to light scattering from thefibrous structure.The obtainedfibers(Fig.5a and b)had cylindrical morphology and nofiber bundles,indicat-ing that applied parameters were adequate for the formation of fibers and proper evaporation of the solvent.On the other hand, the presence of AgNPs in CMCTS has little effect on the electrospun fiber morphology.Thefiber diameter ranged from50to300nm. In addition,after the encapsulation of AgNPs into CMCTS–PEO nanofiber,thefiber diameter decreases compared tofibers consist-ing of CMCTS–PEO without AgNPs,due to the high conductivity, which plays a key role in decreasing of thefiber diameter during electrospinning(Sheikh et al.,2010).The presence of AgNPs results in high electric charge and subsequently high conductivity of the polymer solution which leads to high charge values during elec-trospinning process and possibly forming thinnerfiber diameter (Nirmala et al.,2010;Nirmala,Navamathavan,Kang,El-Newehy, &Kim,2011;Nirmala,Park,et al.,2011).At the same timethe Fig.5.SEM images of electrospun nanofibers containing AgNPs;(a)CMCTS;(b)CMCTS–Ag,(c)CMCTS/PEO–Ag and(d)CMCTS/PEO–Ag(EDX).1016M.M.G.Fouda et al./Carbohydrate Polymers 92 (2013) 1012–1017Fig.6.FT-IR spectra of electrospun nanofibers;(a)PEO and (b)PEO–AgNPs.fibrous structure assures much more loading of AgNPs into the fibers.EDX was used to analyze the elemental constitution of solid samples.Elementary analysis of CMCTS–PEO/silver nanocompos-ite was carried out by using SEM–EDX.Fig.5c displays a spectrum of CMCTS–PEO/silver nanocomposite obtained by elemental micro-probe analysis of EDX.The results show that carbon,oxygen,and Ag were the principal element of CMCTS–PEO/silver nanocomposite.EDX analysis,as a result,provides direct evidence that AgNPs are embedded in the CMCTS–PEO composite.The quantitative analysis of CMCTS–PEO/silver nanocomposite is presented in Table 1.At the same time,Fig.5a and b shows SEM images of CMCTS–PEO/AgNPs nanofibers,which revealed that the AgNPs were evenly distributed in the CMCTS–PEO ultrafine fibers with an average size less than 12–18nm.This suggested that the AgNPs were well stabilized by CMCTS during the preparation of AgNPs.Table 1Stoichiometric ratio of CMCTS–AgNPs.ElementWeight%Atomic%(PEO)/Ag C K 83.9088.17O K 14.8111.68Ag L1.290.15Total100.003.4.FT-IR spectra of electrospun nanofibersFT-IR spectra of electrospun CMCTS–PEO and CMCTS–AgNPs/PEO are shown in Fig.6.The frequencies and assignments for the pristine PEO are indicated asfollows:Fig.7.Diameter inhibition zone (cm)of electrospun nanofibers against Staphylococcus aureus (Sa),Pseudomonas aeruginosa (ps)and Escherichia coli (Ec).M.M.G.Fouda et al./Carbohydrate Polymers92 (2013) 1012–101710172882cm−1due to the CH2group stretching vibration,1097cm−1 and841cm−1due to the C O C asymmetric stretch and bending vibrations.On the other hand,for the electrospun CMCTS–AgNPs nanofiber shows the same characteristic bands,in which the intensity of the bands at2882cm−1and at841cm−1was increased due to the CH2and C O C stretching vibration upon the presence of AgNPs.3.5.Antimicrobial of electrospun nanofibersFig.7shows chart of inhibition zone of the tested antimicrobial samples and the corresponding plates(a,b,c).Results illustrated that S.aureus was the most sensitive microbe against antimicro-bial disk(AMC),CMCTS–PEO–AgNPs nanofiber,and AgNPs solution with inhibition zone30,22and15millimeters(mm)respectively.C.albicans was the least sensitive against all tested antimicrobial agents with IZ of0mm,except for CMCTS–PEO–AgNPs that showed IZ of12mm.It was found that the CMCTS–PEO–AgNPs nanofibers were the most effective silver containing material with IZs of20, 18,15and12against S.aureus,P.aeruginosa,E.coli and C.albicans, respectively.In contrast,the AgNPs showed the least antimicro-bial activity among silver containing nanofibers with IZ of13,7, 6and0mm against S.aureus,P.aeruginosa,E.coli and C.albicans, respectively.It was observed that CMCTS–PEO–AgNPs nanofibers are the most effective silver containing material against all tested microbes.Also,it was found that CMCTS–PEO–AgNPs nanofiber was more than twofold strength of the positive control(AgNPs).How-ever,its efficacy was less than any of the tested antibiotics,but this can be compensated with the less hazardous effect of antibi-otics and the less chance of resistance development compared with silver nanoparticles.4.ConclusionSilver nanoparticles(AgNPs)have been successfully prepared using carboxymethyl chitosan(CMCTS)which acts as both reduc-ing and stabilizing agent for the formed AgNPs.CMCTS–AgNPs with polyethylene oxide(PEO)are well mixed together and subjected to electrospinning process.The resulted nanofiber mats’embedded AgNPs are characterized using different analytical tools.The pres-ence of silver ions in the polymer structure was found to be strongly affecting the electrospun nanofibers diameters due to enhance-ment of electrical conductivity of the nanofibers.The obtained results indicated that the number of Ag+ions that were converted into Ag0increased with increasing the aging time.Antimicrobial activity of the prepared sample was evaluated against different types of microorganisms.It was observed that CMCTS–PEO–AgNPs nanofibers are the most effective silver containing material against all tested microbes.Also,it was found that CMCTS–PEO–AgNPs nanofiber was more than twofold strength of the positive con-trol(AgNPs).Finally,the prepared CMCTS–AgNPs/PEO nanofibers matrix could be properly employed as recommended candidate for many biological applications such as prolonged antimicrobial wound dressing materials.AcknowledgementThe authors extend their appreciation to the Deanship of Scien-tific Research at King Saud University for funding this work through research group no.RGP-VPP-201.ReferencesAbou-Okeil,A.(2012).Ag nanoparticles growing onto cotton fabric using chitosan as a template.Journal of Natural Fibers,9,61–72.Abou-Okeil,A.,Amr,A.,&Abdel-Mohdy,F.A.(2012).Investigation of silver nanopar-ticles synthesis using aminated-beta-cyclodextrin.Carbohydrate Polymers,89, 1–6.Derch,R.,Greiner,A.,&Wendorff,J.H.(Eds.).(2004).Polymer nanofibers prepared by electrospinning.Dekker encyclopedia of nanoscience and nanotechnology.New York:CRC.El-Rafie,M.H.,El-Naggar,M.E.,Ramadan,M.A.,Fouda,M.M.G.,Al-Deyab,S.S., &Hebeish,A.(2011).Environmental synthesis of silver nanoparticles using hydroxypropyl starch and their characterization.Carbohydrate Polymers,86(2), 630–635.El-Shafei,A.M.,Fouda,M.M.G.,Knittel,D.,&Schollmeyer,E.(2008).Antibacte-rial activity of cationically modified cotton fabric with carboxymethyl chitosan.Journal of Applied Polymer Science,110(3),1289–1296.Hebeish,A.,Abdel-Mohdy,F.A.,Fouda,M.M.G.,Elsaid,Z.,Essam,S.,Tammam,G.H.,et al.(2011).Green synthesis of easy care and antimicrobial cotton fabrics.Carbohydrate Polymers,86(4),1684–1691.Hebeish,A.,El-Naggar,M.E.,Fouda,M.M.G.,Ramadan,M.A.,Al-Deyab,S.S.,& El-Rafie,M.H.(2011).Highly effective antibacterial textiles containing green synthesized silver nanoparticles.Carbohydrate Polymers,86(2),936–940. Huang,Z.M.,Zhang,Y.Z.,&Kotaki,M.(2003).A review on polymer nanofibers by electrospinning and their applications in posites Science and Technology,63(15),2223–2253.Morgado,J.,Friend,R.H.,Cacialli,F.,Chuah,B.S.,Moratti,S.C.,&Holmes,A.B.(1999).Journal of Applied Physics,86,6392.Nirmala,R.,Nam,K.T.,Park,S.J.,Shin,Y.S.,Navamathavan,R.,&Kim,H.Y.(2010).Formation of high aspect ratio polyamide-6nanofibers via electrically induced double layer during electrospinning.Applied Surface Science,256,6318–6323. Nirmala,R.,Navamathavan,R.,Kang,H.-S.,El-Newehy,M.H.,&Kim,H.Y.(2011).Preparation of polyamide-6/chitosan composite nanofibers by a single solvent system via electrospinning for biomedical applications.Colloids and Surfaces B: Biointerfaces,83,173–178.Nirmala,R.,Park,H.-M.,Navamathavan,R.,Kang,H.-S.,El-Newehy,M.H.,&Kim,H.Y.(2011).Lecithin blended polyamide-6high aspect ratio nanofibers scaf-folds via electrospinning for human osteoblast cell culture.Materials Science and Engineering C,31,486–493.Sheikh, F. A.,Barakat,N. A.M.,Kanjwal,M. A.,Jeon,S.H.,Kang,H.S.,& Kim,H.Y.(2010).Self synthesize of silver nanoparticles in/on polyurethane nanofibers:Nano-biotechnological approach.Journal of Applied Polymer Science, 115,3189–3198.Taylor,G.I.(1969).Proceedings of the Royal Society of London,313,453.Textor,T.,Fouda,M.M.G.,&Mahltig,B.(2010).Deposition of durable thin silver layers onto polyamides employing a heterogeneous Tollens’reaction.Applied Surface Science,256(8),2337–2342.。
第6课玻璃容器

Press-and-blow used to make wide-mouthed jars and for increasingly smaller necked containers. Better control of glass distribution.
The problems of different formulations include soda-lime and regular container glass are mixed when recycling.
一. Glass Types and General Properties
Advantages as a packaging material: inert to most chemicals perfect foods container. impermeability clarity perceived image rigidity stable at high temperatures Disadvantages :
Typical production rates range from 60 to 300 bottles per minute, depending on the number of sections in a machine, the number of gobs being extruded, and the size of the container.
二. Bottle Manufacture
Figure 6.2 Blow-and-blow bottle manufacture
英语介绍金银玉器PPT课件
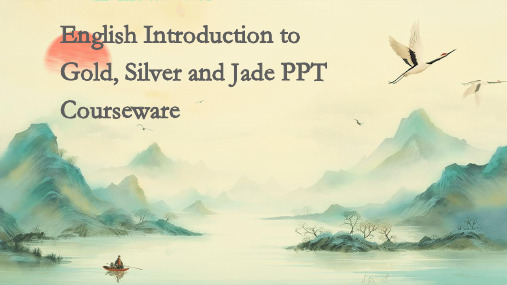
Environmental impact: Extraction of these materials can lead to environmental degradation and ecological damage.
Risks
However, the market for precious metals and jade is volatile, and prices can be affected by global economic conditions, political instability, and other external factors.
Over time, these materials have been used in jewelry, art, and other cultural objects.
The Status and Significance of Gold, Silver, and
Jade Articles in Chinese and Western Cultures
jewelry and other decorative objects.
Silver has also been highly valued in Western culture for its beauty and durability.
Silver has a similar status to gold in Chinese culture, often used in similar ways.
浮法玻璃float glass

From Wikipedia, the free encyclopediaFloat GlassFloat glass is a sheet of glass made by floating molten glass on a bed of molten metal, typically tin, although lead and various low melting point alloys were used in the past. This method gives the sheet uniform thickness and very flat surfaces. Modern windows are made from float glass. Most float glass is soda-lime glass, but relatively minor quantities of specialty borosilicate[1] and flat panel display glass are also produced using the float glass process.[2] The float glass process is also known as the Pilkington process, named after the British glass manufacturer Pilkington, which pioneered the technique (invented by Sir Alastair Pilkington) in the 1950s./**/History Until the 16th century, window glass or flat glass was generally cut from large discs (or rondels) of crown glass(冕牌玻璃). Larger sheets of glass were made by blowing large cylinders which were cut open and flattened, then cut into panes. Most window glass in the early 19th century was made using the cylinder method(柱状法). The 'cylinders' were 6 to 8 feet (1.8 to 2.4 m) long and 10 to 14 inches (250 to 360 mm) in diameter, limiting the width that panes of glass could be cut, and resulting in windows divided by transoms(横梁) into rectangular panels(矩形面板).The first advances in automating glass manufacturing were patented in1848 by Henry Bessemer, an English engineer. His system produced a continuous ribbon(带) of flat glass by forming the ribbon between rollers. This was an expensive process, as the surfaces of the glass needed polishing. If the glass could be set on a perfectly smooth body this would reduce costs considerably. Attempts were made to form flat glass on a molten tin bath, notably in the US. Several patents were granted, but this process was unworkable.Before the development of float glass, larger sheets of plate glass were made by casting a large puddle of glass on an iron surface, and then polishing both sides, a costly process. From the early 1920s, a continuous ribbon of plate glass was passed through a lengthy series of inline grinders(联机磨床) and polishers, reducing glass losses and cost.Glass of lower quality, sheet glass, was made by drawing upwards from a pool of molten glass a thin sheet, held at the edges by rollers. As it cooled the rising sheet stiffened and could then be cut. The two surfaces were not as smooth or uniform, and of lower quality than those of float glass. This process continued in use for many years after the development of float glass.Between 1953 and 1957, Sir Alastair Pilkington and Kenneth Bickerstaff of the UK's Pilkington Brothers developed the first successful commercial application for forming a continuous ribbon of glass using a molten tin bath on which the molten glass flows unhindered under theinfluence of gravity.[3]The success of this process lay in the careful balance of the volume of glass fed onto the bath, where it was flattened by its own weight.[4]Full scale profitable sales of float glass were first achieved in 1960.Manufacture Float glass uses common glass-making raw materials, typically consisting of sand, soda ash (sodium carbonate), dolomite, limestone, and salt cake (sodium sulfate) etc. Other materials may be used as colourants, refining agents(澄清剂) or to adjust the physical and chemical properties of the glass. The raw materials are 【A】mixed in a batch mixing process, then fed together with suitable cullet (waste glass), in a controlled ratio, 【B】into a furnace where it is heated to approximately 1500°C. Common flat glass furnaces are 9 m wide, 45 m long, and contain more than 1200 tons of glass. Once molten, the temperature of the glass is stabilised to approximately 1200°C to ensure a homogeneous specific gravity.【C】The molten glass is fed into a "tin bath", a bath of molten tin (about 3–4 m wide, 50 m long, 6 cm deep), from a delivery canal and is poured into the tin bath by a ceramic lip known as the spout lip(喷口).[5] The amount of glass allowed to pour onto the molten tin is controlled by a gate called a Tweel(流道控制闸门).Tin is suitable for the float glass process because【1】it has a high specific gravity, 【2】is cohesive, and 【3】immiscible(不相溶的)into the molten glass. Tin, however, oxidises in a natural atmosphere to form Tin dioxide (SnO2). Known in the production process as dross(结瘤), the tin dioxide adheres to the glass. To prevent oxidation, the tin bath is provided with a positive pressure protective atmosphere consisting of a mixture of nitrogen and hydrogen.The glass flows onto the tin surface forming a floating ribbon with perfectly smooth surfaces on both sides and an even thickness. As the glass flows along the tin bath, the temperature is gradually reduced from 1100°C until【D】the sheet can be lifted from the tin onto rollers (辊筒)at approximately 600°C. The glass ribbon is pulled off the bath by rollers at a controlled speed. Variation in the flow speed and roller speed enables glass sheets of varying thickness to be formed. Top rollers positioned above the molten tin may be used to control both the thickness and the width of the glass ribbon.Once off the bath, 【E】the glass sheet passes through a lehr kiln(退火炉)for approximately 100 m, where it is further cooled gradually so that it anneals without strain and does not crack from the change in temperature. On exiting the "cold end" of the kiln, 【F】the glass is cut by machines.Market As of 2009, the world float glass market, not including China and Russia, is dominated by the four companies: Asahi Glass(旭硝子,日本), NSG(核供应国)/Pilkington, Saint-Gobain(神戈班), and GuardianIndustries(守护者). Other companies include Sise Cam AS, PPG, Central Glass, Hankuk, Zeledyne, and Cardinal Glass Industries.[6]Glass batch calculationGlass batch calculation(玻璃配料计算) or glass batching is used to determine the correct mix of raw materials (batch) for a glass melt. Principle The raw materials mixture for glass melting is termed "batch". The batch must be measured properly to achieve a given, desired glass formulation. This batch calculation is based on the common linear regression equation:with N B and N G being the molarities 1-column matrices(摩尔分数单列矩阵)of the batch and glass components respectively, and B being the batching matrix.[1][2][3] The symbol "T" stands for the matrix transpose operation, "-1" indicates matrix inversion, and the sign "·" means the scalar product(数积). From the molarities matrices N, percentages by weight (wt%) can easily be derived using the appropriate molar masses.Example calculation An example batch calculation may be demonstrated here. The desired glass composition in wt% is: 67 SiO2, 12 Na2O, 10 CaO, 5 Al2O3, 1 K2O, 2 MgO, 3 B2O3, and as raw materials are used sand, trona(天然碱), lime, albite(钠长石), orthoclase(正长石),dolomite(白云石), and borax. The formulas and molar masses of the glass and batch components are listed in the following table:The batching matrix B indicates the relation of the molarity in the batch (columns,列) and in the glass (rows,行). For example, the batch component SiO2 adds 1 mol SiO2 to the glass, therefore, the intersection of the first column and row shows "1". Trona adds 1.5 mol Na2O to the glass; albite adds 6 mol SiO2, 1 mol Na2O, and 1 mol Al2O3, and so on. For the example given above, the complete batching matrix is listed below. The molarity matrix N G of the glass is simply determined by dividing the desired wt% concentrations by the appropriate molar masses, e.g., for SiO2 67/60.0843 = 1.1151.The resulting molarity matrix of the batch, N B, is given here. After multiplication(乘法)with the appropriate molar masses of the batch ingredients one obtains the batch mass fraction matrix M B:orThe matrix M B, normalized(归一化)to sum up to 100% as seen above, contains the final batch composition in wt%: 39.216 sand, 16.012 trona, 10.242 lime, 16.022 albite, 4.699 orthoclase, 7.276 dolomite, 6.533 borax. If this batch is melted to a glass, the desired composition given above is obtained.[4] During glass melting, carbon dioxide (from trona, lime, dolomite) and water (from trona, borax) evaporate.Another simple glass batch calculation can be found at the website of the University of Washington.[5]Advanced batch calculation by optimization If the number of glass and batch components is not equal, if it is impossible to exactly obtain the desired glass composition using the selected batch ingredients, or if the matrix equation is not soluble for other reasons (e.g., correlation), the batch composition must be determined by optimization techniques.Calculation of glass propertiesThe calculation of glass properties allows "fine-tuning"(微调)of desired material characteristics, e.g., the refractive index.[1]The calculation of glass properties (glass modeling) is used to predict glass properties of interest or glass behavior under certain conditions (e.g., during production) without experimental investigation, based on past data and experience, with the intention to save time, material, financial, and environmental resources, or to gain scientific insight. It was first practised at the end of the 19th century by A. Winkelmann and O. Schott. The combination of several glass models together with other relevant functions can be used for optimization and six sigma procedures. In the form of statistical analysis(统计分析)glass modeling can aid withaccreditation(鉴定)of new data, experimental procedures, and measurement institutions (glass laboratories).History Historically, the calculation of glass properties is directly related to the founding of glass science. At the end of the 19th century the physicist Ernst Abbe developed equations that allow calculating the design of optimized optical microscopes in Jena, Germany, stimulated by co-operation with the optical workshop of Carl Zeiss. Before ErnstAbbe's time the building of microscopes was mainly a work of art and experienced craftsmanship, resulting in very expensive optical microscopes with variable quality. Now Ernst Abbe knew exactly how to construct an excellent microscope, but unfortunately, the required lenses (透镜)and prisms(棱镜)with specific ratios of refractive index and dispersion(色散)did not exist. Ernst Abbe was not able to find answers to his needs from glass artists and engineers; glass making was not based on science at this time.[2]In 1879 the young glass engineer Otto Schott sent Abbe glass samples with a special composition (lithium silicate glass) that he had prepared himself and that he hoped to show special optical properties. Following measurements by Ernst Abbe, Schott's glass samples did not have the desired properties, and they were also not as homogeneous as desired. Nevertheless, Ernst Abbe invited Otto Schott to work on the problemfurther and to evaluate all possible glass components systematically. Finally, Schott succeeded in producing homogeneous glass samples, and he invented borosilicate glass with the optical properties Abbe needed.[2] These inventions gave rise to the well-known companies Zeiss and Schott Glass (see also Timeline of microscope technology).Systematic glass research was born. In 1908, Eugene Sullivan founded glass research also in the United States (Corning, New York).[3]At the beginning of glass research it was most important to know the relation between the glass composition and its properties. For this purpose Otto Schott introduced the additivity principle in several publications for calculation of glass properties.[4][5][6] This principle implies that the relation between the glass composition and a specific property is linear to all glass component concentrations, assuming an ideal mixture, with C i and b i representing specific glass component concentrations and related coefficients respectively in the equation below. 【#1】The additivity principle is a simplification and only valid (有效的)within narrow composition ranges as seen in the displayed diagrams for the refractive index and the viscosity. Nevertheless, the application of the additivity principle lead the way to many of Schott’s inventions, including optical glasses, glasses with low thermal expansion for cooking and laboratory ware (Duran), and glasses with reduced freezing point depression for mercury thermometers. Subsequently,English[7] and Gehlhoff et al.[8] published similar additive glass property calculation models.【#2】Schott’s additivity principle is still widely in use today in glass research and technology.[9][10]Additivity Principle(加和原理):Global modelsThe mixed-alkali effect(混合碱效应): If a glass contains more than one alkali oxide, some properties show non-additive behavior. The image shows, that the viscosity of a glass is significantly decreased.[11]Decreasing accuracy (精度)of modern glass literature data for the density at 20 °C in the binary system SiO2-Na2O.[12]Schott and many scientists and engineers afterwards applied the additivity principle to experimental data measured in their own laboratory within sufficiently narrow composition ranges (local glass models). This is most convenient because disagreements between laboratories andnon-linear glass component interactions do not need to be considered. In the course of several decades of systematic glass research thousands of glass compositions were studied, resulting in millions of published glass properties, collected in glass databases. This huge pool of experimental data was not investigated as a whole, until Bottinga,[13], Kucuk[14], Priven[15], Choudhary[16], Mazurin[17], and Fluegel[18][19] published their global glass models, using various approaches.【#3】In contrast to themodels by Schott the global models consider many independent datasources, making the model estimates more reliable. In addition,【#4】global models can reveal and quantify non-additive influences of certain glass component combinations on the properties, such as the mixed-alkali effect as seen in the diagram above, or the boron anomaly. 【#5】Global models also reflect interesting developments of glass property measurement accuracy, e.g., a decreasing accuracy of experimental data in modern scientific literature for some glass properties, shown in the diagram. They can be used for accreditation of new data, experimental procedures, and measurement institutions (glass laboratories). In the following sections (except melting enthalpy) empirical modeling techniques are presented, which seem to be a successful way for handling huge amounts of experimental data. The resulting models are applied in contemporary engineering and research for the calculation of glass properties.Non-empirical (deductive) glass models exist.[20] They are often not created to obtain reliable glass property predictions in the first place (except melting enthalpy), but to establish relations among several properties (e.g. atomic radius, atomic mass, chemical bond strength and angles, chemical valency, heat capacity) to gain scientific insight. In future, the investigation of property relations in deductive(演绎)models may ultimately lead to reliable predictions for all desired properties,provided the property relations are well understood and all required experimental data are available.Methods Glass properties and glass behavior during production can be calculated through statistical analysis of glass databases such asGE-SYSTEM[21] SciGlass[22] and Interglad,[23] sometimes combined with the finite element method. For estimating the melting enthalpy thermodynamic databases are used.Linear regression(线性回归)Refractive index in the system SiO2-Na2O. Dummy variables(虚变数)can be used to quantify systematic differences of whole dataseries from one investigator.[12]If the desired glass property is not related to crystallization (e.g., liquidus (液相线)temperature) or phase separation(相分离), linear regression canbe applied using common polynomial functions(多项式函数)up to the third degree. Below is an example equation of the second degree. TheC-values are the glass component concentrations like Na2O or CaO in percent or other fractions, the b-values are coefficients, and n is the total number of glass components. The glass main component silica (SiO2) is excluded in the equation below because of over-parametrization due to the constraint that all components sum up to 100%. Many terms in the equation below can be neglected based on correlation and significance analysis. Systematic errors such as seen in the picture are quantified by dummy variables(虚变数). Further details and examples are available in an online tutorial by Fluegel.[24]Non-linear regressionLiquidus surface in the system SiO2-Na2O-CaO using disconnected peak functions based on 237 experimental data from 28 investigators. Error = 15 °C.[25]The liquidus temperature has been modeled by non-linear regression using neural networks[26](神经网络)and disconnected peak functions.[25]The disconnected peak functions approach(离散峰函数法)is based on the observation that within one primary crystalline phase field linear regression can be applied[27] and at eutectic points(低共熔点)sudden changes occur.Glass melting enthalpy(玻璃熔融焓)The glass melting enthalpy reflects the amount of energy needed to convert the mix of raw materials (batch) to a melt glass. It depends on the batch and glass compositions, on the efficiency of the furnace and heat regeneration systems, the average residence time of the glass in the furnace, and many other factors. A pioneering article about the subject was written by Carl Kröger in 1953.[28]Finite element method(有限元法)For modeling of the glass flow in a glass melting furnace the finite element method is applied commercially,[29][30] based on data or models for viscosity, density, thermal conductivity, heat capacity, absorption spectra, and other relevantproperties of the glass melt. The finite element method may also be applied to glass forming processes.Optimization It is often required to optimize several glass properties simultaneously, including production costs. GE-SYSTEM[21][31] This can be performed, e.g., by simplex search(单一研究), or in a spreadsheet(试算表) as follows:1.Listing of the desired properties;2.Entering of models for the reliable calculation of properties basedon the glass composition, including a formula for estimating theproduction costs;3.Calculation of the squares of the differences (errors) betweendesired and calculated properties;4.Reduction of the sum of square errors using the Solver option[32] inMicrosoft Excel with the glass components as variables. Othersoftware (e.g. Microcal Origin) can also be used to perform these optimizations.It is possible to weight the desired properties differently. Basic information about the principle can be found in an article by Huff et al.[33] The combination of several glass models together with further relevant technological and financial functions can be used in six sigma optimization(六标准差优化).。
古罗马玻璃器英语介绍
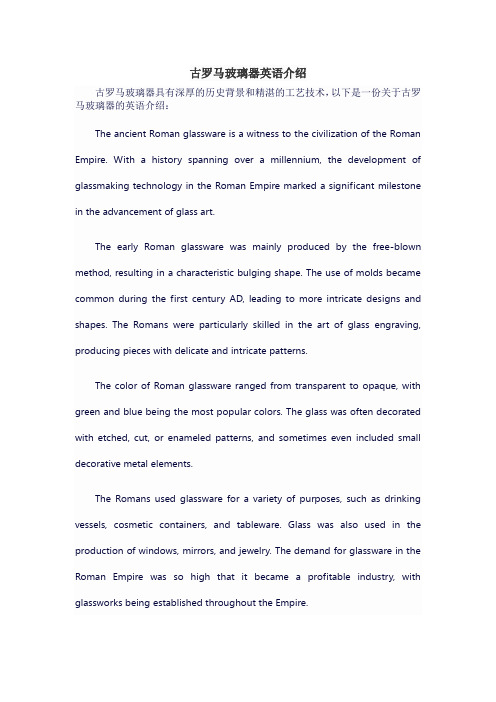
古罗马玻璃器英语介绍古罗马玻璃器具有深厚的历史背景和精湛的工艺技术,以下是一份关于古罗马玻璃器的英语介绍:The ancient Roman glassware is a witness to the civilization of the Roman Empire. With a history spanning over a millennium, the development of glassmaking technology in the Roman Empire marked a significant milestone in the advancement of glass art.The early Roman glassware was mainly produced by the free-blown method, resulting in a characteristic bulging shape. The use of molds became common during the first century AD, leading to more intricate designs and shapes. The Romans were particularly skilled in the art of glass engraving, producing pieces with delicate and intricate patterns.The color of Roman glassware ranged from transparent to opaque, with green and blue being the most popular colors. The glass was often decorated with etched, cut, or enameled patterns, and sometimes even included small decorative metal elements.The Romans used glassware for a variety of purposes, such as drinking vessels, cosmetic containers, and tableware. Glass was also used in the production of windows, mirrors, and jewelry. The demand for glassware in the Roman Empire was so high that it became a profitable industry, with glassworks being established throughout the Empire.The influence of Roman glassware can be seen in different cultures across Europe and the Middle East, as trade routes expanded to carry glassware beyond the borders of the Roman Empire. The legacy of Roman glassware continues to inspire artists and craftsmen even today, with its timeless elegance and technical brilliance.希望以上内容对你有帮助,建议查阅更多关于古罗马玻璃器的文献,获取更全面和准确的信息。
- 1、下载文档前请自行甄别文档内容的完整性,平台不提供额外的编辑、内容补充、找答案等附加服务。
- 2、"仅部分预览"的文档,不可在线预览部分如存在完整性等问题,可反馈申请退款(可完整预览的文档不适用该条件!)。
- 3、如文档侵犯您的权益,请联系客服反馈,我们会尽快为您处理(人工客服工作时间:9:00-18:30)。
Journal of Alloys and Compounds 491 (2010) 584–588Contents lists available at ScienceDirectJournal of Alloys andCompoundsj o u r n a l h o m e p a g e :w w w.e l s e v i e r.c o m /l o c a t e /j a l l c omCharacteristics of silver–glass composite powders as the silver electrode for Si solar cellsYou Na Ko,Hye Young Koo,Jung Hyun Kim,Yun Chan Kang ∗Department of Chemical Engineering,Konkuk University,1Hwayang-dong,Gwangjin-gu,Seoul 143-701,Republic of Koreaa r t i c l e i n f o Article history:Received 28August 2009Received in revised form 31October 2009Accepted 2November 2009Available online 10 November 2009Keywords:Chemical synthesis Gas–solid reactiona b s t r a c tSilver–glass composite powders as the electrode material for application in Si solar cells,were directly prepared by spray pyrolysis.The Pb-based glass composition appropriate to the Si solar cell applications was applied.The composite powders prepared at temperatures between 1000and 1200◦C had spherical shapes and pure silver crystal structures.The mean crystallite sizes of the composite powders prepared at temperatures of 900,1000,1100,and 1200◦C were 37,40,52,and 55nm.The silver conducting films had dense structures irrespective of the preparation temperatures of the composite powders.The sheet resis-tances of the silver conducting films were changed from 2.9to 5.3m /sq according to the preparation temperature of the silver–glass composite powders at a firing temperature of 700◦C.© 2009 Elsevier B.V. All rights reserved.1.IntroductionDuring the preparation of single-crystalline or polycrystalline Si solar cells,a silver electrode is formed on the side with an anti-reflecting preventing film.The silver electrode is generally fab-ricated by the firing of a printed layer formed by a screen printing method using silver paste containing a silver powder,a glass frit,and a resin binder [1–3].In order to improve the power genera-tion characteristics of Si solar cells,it is important to examine the characteristics of the silver electrode.Silver powders with large crystallite sizes and spherical mor-phology are preferred for use in the electrode material in Si solar cells.Therefore,silver powders prepared by gas phase reaction and liquid solution methods under carefully controlled prepara-tion conditions are used.A micron-sized glass frit with irregular morphology prepared by a conventional melting process is mainly used as a sintering agent in silver paste [4–7].The characteristics of silver conducting films are affected by the composition of glass frits [8–10].Glass frit with a softening point of 450–550◦C is generally used as the inorganic binder.Silver paste with glass frit having an appropriate softening point can be sintered at 600–800◦C,wetted appropriately,and bonded appropriately to a silicon substrate.The characteristics of fired Ag conducting films formed from the silver paste containing silver powders and glass frit are strongly affected by the mixing degree of silver and glass components.In this study,silver–glass composite powders as the electrode material for application in Si solar cells,was directly prepared by∗Corresponding author.Tel.:+82220496010;fax:+8224583504.E-mail address:yckang@konkuk.ac.kr (Y.C.Kang).spray pyrolysis.The Pb-based glass composition appropriate to the Si solar cell applications was applied.The morphological and elec-trical properties of silver electrodes formed from the silver–glass composite were investigated.2.Experimental proceduresThe silver–glass composite powders were prepared by spray pyrolysis from the spray solutions containing silver and glass components.The spray pyroly-sis equipment used consisted of six ultrasonic spray generators that operated at 1.7MHz,a 1000-mm-long tubular alumina reactor of 50-mm ID,and a bag filter.The PbO–SiO 2–B 2O 3–Al 2O 3–TiO 2glass system with glass transition temperature of 504.5◦C was applied.Spray solutions were prepared by adding Ag(NO 3)(LS-Nikko copper,99.99%),Pb(NO 3)2(Kanto,99%),tetraethyl orthosilicate (TEOS,Aldrich,98%),H 3BO 3(Kanto,99.5%),Al(NO 3)3·9H 2O (Junsei,98%),and titanium tetraisopropoxide (Junsei,98%)to distilled water with appropriate amount of nitric acid.The overall concentration of silver and glass components was fixed at 0.5M.The glass content was fixed at 3%of silver component.The preparation temperature of glass powders ranged from 900to 1200◦C.The flow rate of the carrier gas was fixed to 20L/min.Crystal structures of the prepared silver–glass composite powders were inves-tigated by X-ray diffraction (XRD,Rigaku,D/MAX-RB)with Cu K ␣radiation ( =1.5418Å).Morphological characteristics of the prepared silver–glass composite powders and fired electrodes were investigated by scanning electron microscopy (SEM,JEOL,JSM-6060).Sheet resistances of the silver electrodes were measured by a four-point prove method (CMT-SR 1000N,Advanced Instrument Technology).3.Results and discussionMorphologies of the silver–glass composite powders prepared at various temperatures are shown in Fig.1.The composite pow-ders had bimodal size distributions with submicron and nanometer sizes.Evaporation of some silver and glass compositions occurred inside the hot wall reactor maintained at temperatures between 900and 1200◦C.Therefore,nanometer-sized composite powders were prepared from evaporated vapors by nucleation and growth0925-8388/$–see front matter © 2009 Elsevier B.V. All rights reserved.doi:10.1016/j.jallcom.2009.11.008Y.N.Ko et al./Journal of Alloys and Compounds491 (2010) 584–588585Fig.1.SEM images of silver–glass composite powders prepared at various temperatures.(a)900◦C,(b)1000◦C,(c)1100◦C and(d)1200◦C.Fig.2.Size distribution of silver–glass composite powders.Fig.4.XRD patterns of silver–glass composite powders prepared at various tem-peratures.Fig.3.TEM images of silver–glass composite powders.(a)Low resolution and(b)high resolution.586Y.N.Ko et al./Journal of Alloys and Compounds491 (2010) 584–588Fig.5.SEM images of surfaces of silver conductingfilmsfired at700◦C.(a)900◦C,(b)1000◦C,(c)1100◦C and(d)1200◦C.Fig.6.SEM images of cross-sections of silver conductingfilmsfired at700◦C.(a)900◦C,(b)1000◦C,(c)1100◦C and(d)1200◦C.Y.N.Ko et al./Journal of Alloys and Compounds491 (2010) 584–588587Fig.7.AFM images of surfaces of silver conductingfilmsfired at700◦C.(a)900◦C,(b)1000◦C,(c)1100◦C and(d)1200◦C.processes.Fig.2shows the size distribution of the composite pow-ders prepared at a temperature of1100◦C.The powders with nanometer sizes were not counted.The mean size of the composite powders was0.62m.However,the mean size of the compos-ite powders prepared at temperatures of1000◦C was0.71m. Fig.3shows the TEM images of the silver–glass composite powders prepared at a temperature of1100◦C.The powders with submi-cron and nanometer sizes had spherical shapes and core–shell structures.Glass phase with amorphous structure covered the crys-talline silver powders as shown by high resolution TEM image.Fig.4shows the XRD patterns of the composite powders pre-pared by spray pyrolysis at various temperatures.The composite powders prepared at temperatures between1000and1200◦C had pure silver crystal structures.On the other hand,the composite powders prepared at a temperature of900◦C had small impurity peak of cubic Ag2O phase.AgO phase wasfirstly formed inside the hot wall reactor by decomposition of Ag(NO3)in the prepa-ration of Ag powders by spray pyrolysis in air atmosphere.The transformation of AgO to Ag2O occurred with continuous heating. Decomposition of Ag2O intermediate to Ag metal occurred at high preparation plete thermal decomposition of the Ag2O intermediate to Ag could be occurred at a low temperature of 473◦C.However,in this study,the residence time of the powders inside the hot wall reactor was short as0.48s at a preparation tem-perature of900◦C.Therefore,complete thermal decomposition of the Ag2O intermediate to Ag did not occur at a preparation tem-perature of900◦C.The mean crystallite sizes of the Ag powders prepared at temperatures of900,1000,1100,and1200◦C were37, 40,52,and55nm.Silver electrodes were fabricated byfiring of a printed layer formed by a screen printing method using silver paste containing a silver–glass composite powder and a resin binder.The silver–glass composite powders prepared by spray pyrolysis at various tem-peratures were mixed with an organic vehicle that consisted of ethyl cellulose,␣-terpineol,and butyl carbitol acetate(BCA).Sil-ver paste was screen printed onto a Si wafer substrate.The printed Si wafer substrate was dried at120◦C for30min.The printed Si wafer wasfired by2steps,atfirst temperature of400◦C for 30min at a heating rate of5◦C/min and in the second tempera-ture of700◦C for10min at a heating rate of5◦C/min.Figs.5and6 show the SEM images of the surfaces and cross-sections of the sil-ver conductingfilms.The conductingfilms had dense structures irrespective of the preparation conditions of the silver–glass com-posite powders.However,the smoothness of the surfaces of the silver conductingfilm was affected by the preparation tempera-tures of the silver–glass composite powders.Fig.7shows the AFM images of the surfaces of the silver conductingfilms.The conduct-ingfilms formed from the composite powders prepared at900and 1200◦C had rough surfaces.On the other hand,the conducting films formed from the composite powders prepared at1000and 1100◦C had smooth surfaces.The composite powders prepared at900and1200◦C had a number of nano-sized powders formed by nucleation and growth mechanism.The different size distribu-tions of the composite powders affected the morphologies of the588Y.N.Ko et al./Journal of Alloys and Compounds491 (2010) 584–588Fig.8.Sheet resistances of silver conductingfilmsfired at700◦C.silver conductingfilms.Glass materials were segregated between micron-sized silver grains at a highfiring temperature of700◦C as shown by arrows in Fig.5.However,the glass materials are well distributed in the silver conductingfilms.The thicknesses of the conductingfilms formed from the composite powders prepared at 900,1000,1100and1200◦C were5.8,4.8,5.0and4.5m,respec-tively.Fig.8shows the sheet resistances of the silver conductingfilms formed from the silver–glass composite powders prepared at var-ious temperatures.The sheet resistances of the silver conducting films are changed from2.9to5.3m /sq according to the prepa-ration temperatures of the silver–glass composite powders.The silver conductingfilms formed from the silver–glass composite powders had low sheet resistances because of high density of thefilms.4.ConclusionsThe characteristics of silver conductingfilms formed from the silver–glass composite powders prepared by spray pyrolysis at var-ious temperatures were investigated.The silver conductingfilms formed from the composite powders had dense structures and low sheet resistances because of high mixing degree of silver and glass materials.The glass frits prepared by conventional melting process are not necessary to the formation of silver conductingfilms from the silver–glass composite powders.Therefore,silver conducting films with good characteristics for Si solar cell applications could be formed from the silver–glass composite powders prepared by simple preparation process.AcknowledgementThis study was supported by a grant(M2009010025)from the Fundamental R&D Program for Core Technology of Materials funded by the Ministry of Knowledge Economy(MKE),Republic of Korea.References[1]S.B.Rane,P.K.Khanna,T.Seth,G.J.Phatak,D.P.Amalnerkar,B.K.Das,Mater.Chem.Phys.82(2003)237.[2]Y.Zhang,Y.Yang,J.Zheng,W.Hua,G.Chen,Mater.Chem.Phys.114(2009)319.[3]M.M.Hilali,S.Sridharan,C.Khadilkar,A.Shaikh,A.Rohatig,S.Kim,J.Electron.Mater.35(11)(2006)2041.[4]K.J.Park,D.S.Seo,J.K.Lee,Colloids Surf.A:Physicochem.Eng.Asp.313–314(2008)351.[5]S.H.Park,D.S.Seo,J.K.Lee,Colloids Surf.A:Physicochem.Eng.Asp.313–314(2008)197.[6]P.F.Becher,W.L.Newell,J.Mater.Sci.12(1977)90.[7]T.T.Hitch,J.Electron.Mater.3(1974)553.[8]K.K.Hong,S.B.Cho,J.Y.Huh,H.J.Park,J.W.Jeong,Met.Mater.Int.15(2)(2009)307.[9]Z.Liu,D.D.L.Chung,J.Electron.Mater.33(3)(2004)194.[10]S.A.Ketkar,G.G.Umarji,G.J.Phatak,T.Seth,U.P.Mulik,D.P.Amalnerkar,Mater.Sci.Eng.B132(2006)197.。