E3-ESwitching_chapter3
Native Instruments MASCHINE MK3 用户手册说明书
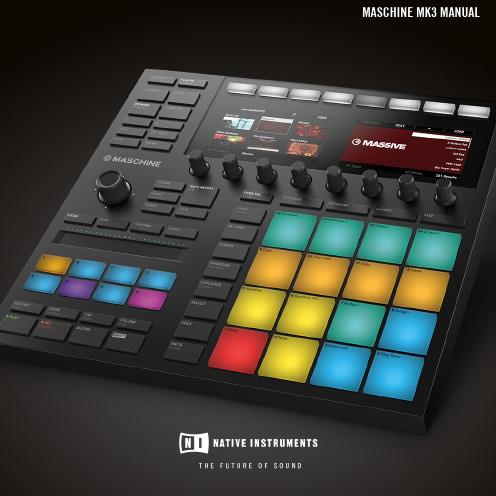
The information in this document is subject to change without notice and does not represent a commitment on the part of Native Instruments GmbH. The software described by this docu-ment is subject to a License Agreement and may not be copied to other media. No part of this publication may be copied, reproduced or otherwise transmitted or recorded, for any purpose, without prior written permission by Native Instruments GmbH, hereinafter referred to as Native Instruments.“Native Instruments”, “NI” and associated logos are (registered) trademarks of Native Instru-ments GmbH.ASIO, VST, HALion and Cubase are registered trademarks of Steinberg Media Technologies GmbH.All other product and company names are trademarks™ or registered® trademarks of their re-spective holders. Use of them does not imply any affiliation with or endorsement by them.Document authored by: David Gover and Nico Sidi.Software version: 2.8 (02/2019)Hardware version: MASCHINE MK3Special thanks to the Beta Test Team, who were invaluable not just in tracking down bugs, but in making this a better product.NATIVE INSTRUMENTS GmbH Schlesische Str. 29-30D-10997 Berlin Germanywww.native-instruments.de NATIVE INSTRUMENTS North America, Inc. 6725 Sunset Boulevard5th FloorLos Angeles, CA 90028USANATIVE INSTRUMENTS K.K.YO Building 3FJingumae 6-7-15, Shibuya-ku, Tokyo 150-0001Japanwww.native-instruments.co.jp NATIVE INSTRUMENTS UK Limited 18 Phipp StreetLondon EC2A 4NUUKNATIVE INSTRUMENTS FRANCE SARL 113 Rue Saint-Maur75011 ParisFrance SHENZHEN NATIVE INSTRUMENTS COMPANY Limited 5F, Shenzhen Zimao Center111 Taizi Road, Nanshan District, Shenzhen, GuangdongChina© NATIVE INSTRUMENTS GmbH, 2019. All rights reserved.Table of Contents1Welcome to MASCHINE (25)1.1MASCHINE Documentation (26)1.2Document Conventions (27)1.3New Features in MASCHINE 2.8 (29)1.4New Features in MASCHINE 2.7.10 (31)1.5New Features in MASCHINE 2.7.8 (31)1.6New Features in MASCHINE 2.7.7 (32)1.7New Features in MASCHINE 2.7.4 (33)1.8New Features in MASCHINE 2.7.3 (36)2Quick Reference (38)2.1Using Your Controller (38)2.1.1Controller Modes and Mode Pinning (38)2.1.2Controlling the Software Views from Your Controller (40)2.2MASCHINE Project Overview (43)2.2.1Sound Content (44)2.2.2Arrangement (45)2.3MASCHINE Hardware Overview (48)2.3.1MASCHINE Hardware Overview (48)2.3.1.1Control Section (50)2.3.1.2Edit Section (53)2.3.1.3Performance Section (54)2.3.1.4Group Section (56)2.3.1.5Transport Section (56)2.3.1.6Pad Section (58)2.3.1.7Rear Panel (63)2.4MASCHINE Software Overview (65)2.4.1Header (66)2.4.2Browser (68)2.4.3Arranger (70)2.4.4Control Area (73)2.4.5Pattern Editor (74)3Basic Concepts (76)3.1Important Names and Concepts (76)3.2Adjusting the MASCHINE User Interface (79)3.2.1Adjusting the Size of the Interface (79)3.2.2Switching between Ideas View and Song View (80)3.2.3Showing/Hiding the Browser (81)3.2.4Showing/Hiding the Control Lane (81)3.3Common Operations (82)3.3.1Using the 4-Directional Push Encoder (82)3.3.2Pinning a Mode on the Controller (83)3.3.3Adjusting Volume, Swing, and Tempo (84)3.3.4Undo/Redo (87)3.3.5List Overlay for Selectors (89)3.3.6Zoom and Scroll Overlays (90)3.3.7Focusing on a Group or a Sound (91)3.3.8Switching Between the Master, Group, and Sound Level (96)3.3.9Navigating Channel Properties, Plug-ins, and Parameter Pages in the Control Area.973.3.9.1Extended Navigate Mode on Your Controller (102)3.3.10Navigating the Software Using the Controller (105)3.3.11Using Two or More Hardware Controllers (106)3.3.12Touch Auto-Write Option (108)3.4Native Kontrol Standard (110)3.5Stand-Alone and Plug-in Mode (111)3.5.1Differences between Stand-Alone and Plug-in Mode (112)3.5.2Switching Instances (113)3.5.3Controlling Various Instances with Different Controllers (114)3.6Host Integration (114)3.6.1Setting up Host Integration (115)3.6.1.1Setting up Ableton Live (macOS) (115)3.6.1.2Setting up Ableton Live (Windows) (116)3.6.1.3Setting up Apple Logic Pro X (116)3.6.2Integration with Ableton Live (117)3.6.3Integration with Apple Logic Pro X (119)3.7Preferences (120)3.7.1Preferences – General Page (121)3.7.2Preferences – Audio Page (126)3.7.3Preferences – MIDI Page (130)3.7.4Preferences – Default Page (133)3.7.5Preferences – Library Page (137)3.7.6Preferences – Plug-ins Page (145)3.7.7Preferences – Hardware Page (150)3.7.8Preferences – Colors Page (154)3.8Integrating MASCHINE into a MIDI Setup (156)3.8.1Connecting External MIDI Equipment (156)3.8.2Sync to External MIDI Clock (157)3.8.3Send MIDI Clock (158)3.9Syncing MASCHINE using Ableton Link (159)3.9.1Connecting to a Network (159)3.9.2Joining and Leaving a Link Session (159)3.10Using a Pedal with the MASCHINE Controller (160)3.11File Management on the MASCHINE Controller (161)4Browser (163)4.1Browser Basics (163)4.1.1The MASCHINE Library (163)4.1.2Browsing the Library vs. Browsing Your Hard Disks (164)4.2Searching and Loading Files from the Library (165)4.2.1Overview of the Library Pane (165)4.2.2Selecting or Loading a Product and Selecting a Bank from the Browser (170)4.2.2.1[MK3] Browsing by Product Category Using the Controller (174)4.2.2.2[MK3] Browsing by Product Vendor Using the Controller (174)4.2.3Selecting a Product Category, a Product, a Bank, and a Sub-Bank (175)4.2.3.1Selecting a Product Category, a Product, a Bank, and a Sub-Bank on theController (179)4.2.4Selecting a File Type (180)4.2.5Choosing Between Factory and User Content (181)4.2.6Selecting Type and Character Tags (182)4.2.7List and Tag Overlays in the Browser (186)4.2.8Performing a Text Search (188)4.2.9Loading a File from the Result List (188)4.3Additional Browsing Tools (193)4.3.1Loading the Selected Files Automatically (193)4.3.2Auditioning Instrument Presets (195)4.3.3Auditioning Samples (196)4.3.4Loading Groups with Patterns (197)4.3.5Loading Groups with Routing (198)4.3.6Displaying File Information (198)4.4Using Favorites in the Browser (199)4.5Editing the Files’ Tags and Properties (203)4.5.1Attribute Editor Basics (203)4.5.2The Bank Page (205)4.5.3The Types and Characters Pages (205)4.5.4The Properties Page (208)4.6Loading and Importing Files from Your File System (209)4.6.1Overview of the FILES Pane (209)4.6.2Using Favorites (211)4.6.3Using the Location Bar (212)4.6.4Navigating to Recent Locations (213)4.6.5Using the Result List (214)4.6.6Importing Files to the MASCHINE Library (217)4.7Locating Missing Samples (219)4.8Using Quick Browse (221)5Managing Sounds, Groups, and Your Project (225)5.1Overview of the Sounds, Groups, and Master (225)5.1.1The Sound, Group, and Master Channels (226)5.1.2Similarities and Differences in Handling Sounds and Groups (227)5.1.3Selecting Multiple Sounds or Groups (228)5.2Managing Sounds (233)5.2.1Loading Sounds (235)5.2.2Pre-listening to Sounds (236)5.2.3Renaming Sound Slots (237)5.2.4Changing the Sound’s Color (237)5.2.5Saving Sounds (239)5.2.6Copying and Pasting Sounds (241)5.2.7Moving Sounds (244)5.2.8Resetting Sound Slots (245)5.3Managing Groups (247)5.3.1Creating Groups (248)5.3.2Loading Groups (249)5.3.3Renaming Groups (251)5.3.4Changing the Group’s Color (251)5.3.5Saving Groups (253)5.3.6Copying and Pasting Groups (255)5.3.7Reordering Groups (258)5.3.8Deleting Groups (259)5.4Exporting MASCHINE Objects and Audio (260)5.4.1Saving a Group with its Samples (261)5.4.2Saving a Project with its Samples (262)5.4.3Exporting Audio (264)5.5Importing Third-Party File Formats (270)5.5.1Loading REX Files into Sound Slots (270)5.5.2Importing MPC Programs to Groups (271)6Playing on the Controller (275)6.1Adjusting the Pads (275)6.1.1The Pad View in the Software (275)6.1.2Choosing a Pad Input Mode (277)6.1.3Adjusting the Base Key (280)6.1.4Using Choke Groups (282)6.1.5Using Link Groups (284)6.2Adjusting the Key, Choke, and Link Parameters for Multiple Sounds (286)6.3Playing Tools (287)6.3.1Mute and Solo (288)6.3.2Choke All Notes (292)6.3.3Groove (293)6.3.4Level, Tempo, Tune, and Groove Shortcuts on Your Controller (295)6.3.5Tap Tempo (299)6.4Performance Features (300)6.4.1Overview of the Perform Features (300)6.4.2Selecting a Scale and Creating Chords (303)6.4.3Scale and Chord Parameters (303)6.4.4Creating Arpeggios and Repeated Notes (316)6.4.5Swing on Note Repeat / Arp Output (321)6.5Using Lock Snapshots (322)6.5.1Creating a Lock Snapshot (322)6.5.2Using Extended Lock (323)6.5.3Updating a Lock Snapshot (323)6.5.4Recalling a Lock Snapshot (324)6.5.5Morphing Between Lock Snapshots (324)6.5.6Deleting a Lock Snapshot (325)6.5.7Triggering Lock Snapshots via MIDI (326)6.6Using the Smart Strip (327)6.6.1Pitch Mode (328)6.6.2Modulation Mode (328)6.6.3Perform Mode (328)6.6.4Notes Mode (329)7Working with Plug-ins (330)7.1Plug-in Overview (330)7.1.1Plug-in Basics (330)7.1.2First Plug-in Slot of Sounds: Choosing the Sound’s Role (334)7.1.3Loading, Removing, and Replacing a Plug-in (335)7.1.3.1Browser Plug-in Slot Selection (341)7.1.4Adjusting the Plug-in Parameters (344)7.1.5Bypassing Plug-in Slots (344)7.1.6Using Side-Chain (346)7.1.7Moving Plug-ins (346)7.1.8Alternative: the Plug-in Strip (348)7.1.9Saving and Recalling Plug-in Presets (348)7.1.9.1Saving Plug-in Presets (349)7.1.9.2Recalling Plug-in Presets (350)7.1.9.3Removing a Default Plug-in Preset (351)7.2The Sampler Plug-in (352)7.2.1Page 1: Voice Settings / Engine (354)7.2.2Page 2: Pitch / Envelope (356)7.2.3Page 3: FX / Filter (359)7.2.4Page 4: Modulation (361)7.2.5Page 5: LFO (363)7.2.6Page 6: Velocity / Modwheel (365)7.3Using Native Instruments and External Plug-ins (367)7.3.1Opening/Closing Plug-in Windows (367)7.3.2Using the VST/AU Plug-in Parameters (370)7.3.3Setting Up Your Own Parameter Pages (371)7.3.4Using VST/AU Plug-in Presets (376)7.3.5Multiple-Output Plug-ins and Multitimbral Plug-ins (378)8Using the Audio Plug-in (380)8.1Loading a Loop into the Audio Plug-in (384)8.2Editing Audio in the Audio Plug-in (385)8.3Using Loop Mode (386)8.4Using Gate Mode (388)9Using the Drumsynths (390)9.1Drumsynths – General Handling (391)9.1.1Engines: Many Different Drums per Drumsynth (391)9.1.2Common Parameter Organization (391)9.1.3Shared Parameters (394)9.1.4Various Velocity Responses (394)9.1.5Pitch Range, Tuning, and MIDI Notes (394)9.2The Kicks (395)9.2.1Kick – Sub (397)9.2.2Kick – Tronic (399)9.2.3Kick – Dusty (402)9.2.4Kick – Grit (403)9.2.5Kick – Rasper (406)9.2.6Kick – Snappy (407)9.2.7Kick – Bold (409)9.2.8Kick – Maple (411)9.2.9Kick – Push (412)9.3The Snares (414)9.3.1Snare – Volt (416)9.3.2Snare – Bit (418)9.3.3Snare – Pow (420)9.3.4Snare – Sharp (421)9.3.5Snare – Airy (423)9.3.6Snare – Vintage (425)9.3.7Snare – Chrome (427)9.3.8Snare – Iron (429)9.3.9Snare – Clap (431)9.3.10Snare – Breaker (433)9.4The Hi-hats (435)9.4.1Hi-hat – Silver (436)9.4.2Hi-hat – Circuit (438)9.4.3Hi-hat – Memory (440)9.4.4Hi-hat – Hybrid (442)9.4.5Creating a Pattern with Closed and Open Hi-hats (444)9.5The Toms (445)9.5.1Tom – Tronic (447)9.5.2Tom – Fractal (449)9.5.3Tom – Floor (453)9.5.4Tom – High (455)9.6The Percussions (456)9.6.1Percussion – Fractal (458)9.6.2Percussion – Kettle (461)9.6.3Percussion – Shaker (463)9.7The Cymbals (467)9.7.1Cymbal – Crash (469)9.7.2Cymbal – Ride (471)10Using the Bass Synth (474)10.1Bass Synth – General Handling (475)10.1.1Parameter Organization (475)10.1.2Bass Synth Parameters (477)11Working with Patterns (479)11.1Pattern Basics (479)11.1.1Pattern Editor Overview (480)11.1.2Navigating the Event Area (486)11.1.3Following the Playback Position in the Pattern (488)11.1.4Jumping to Another Playback Position in the Pattern (489)11.1.5Group View and Keyboard View (491)11.1.6Adjusting the Arrange Grid and the Pattern Length (493)11.1.7Adjusting the Step Grid and the Nudge Grid (497)11.2Recording Patterns in Real Time (501)11.2.1Recording Your Patterns Live (501)11.2.2The Record Prepare Mode (504)11.2.3Using the Metronome (505)11.2.4Recording with Count-in (506)11.2.5Quantizing while Recording (508)11.3Recording Patterns with the Step Sequencer (508)11.3.1Step Mode Basics (508)11.3.2Editing Events in Step Mode (511)11.3.3Recording Modulation in Step Mode (513)11.4Editing Events (514)11.4.1Editing Events with the Mouse: an Overview (514)11.4.2Creating Events/Notes (517)11.4.3Selecting Events/Notes (518)11.4.4Editing Selected Events/Notes (526)11.4.5Deleting Events/Notes (532)11.4.6Cut, Copy, and Paste Events/Notes (535)11.4.7Quantizing Events/Notes (538)11.4.8Quantization While Playing (540)11.4.9Doubling a Pattern (541)11.4.10Adding Variation to Patterns (541)11.5Recording and Editing Modulation (546)11.5.1Which Parameters Are Modulatable? (547)11.5.2Recording Modulation (548)11.5.3Creating and Editing Modulation in the Control Lane (550)11.6Creating MIDI Tracks from Scratch in MASCHINE (555)11.7Managing Patterns (557)11.7.1The Pattern Manager and Pattern Mode (558)11.7.2Selecting Patterns and Pattern Banks (560)11.7.3Creating Patterns (563)11.7.4Deleting Patterns (565)11.7.5Creating and Deleting Pattern Banks (566)11.7.6Naming Patterns (568)11.7.7Changing the Pattern’s Color (570)11.7.8Duplicating, Copying, and Pasting Patterns (571)11.7.9Moving Patterns (574)11.7.10Adjusting Pattern Length in Fine Increments (575)11.8Importing/Exporting Audio and MIDI to/from Patterns (576)11.8.1Exporting Audio from Patterns (576)11.8.2Exporting MIDI from Patterns (577)11.8.3Importing MIDI to Patterns (580)12Audio Routing, Remote Control, and Macro Controls (589)12.1Audio Routing in MASCHINE (590)12.1.1Sending External Audio to Sounds (591)12.1.2Configuring the Main Output of Sounds and Groups (596)12.1.3Setting Up Auxiliary Outputs for Sounds and Groups (601)12.1.4Configuring the Master and Cue Outputs of MASCHINE (605)12.1.5Mono Audio Inputs (610)12.1.5.1Configuring External Inputs for Sounds in Mix View (611)12.2Using MIDI Control and Host Automation (614)12.2.1Triggering Sounds via MIDI Notes (615)12.2.2Triggering Scenes via MIDI (622)12.2.3Controlling Parameters via MIDI and Host Automation (623)12.2.4Selecting VST/AU Plug-in Presets via MIDI Program Change (631)12.2.5Sending MIDI from Sounds (632)12.3Creating Custom Sets of Parameters with the Macro Controls (636)12.3.1Macro Control Overview (637)12.3.2Assigning Macro Controls Using the Software (638)12.3.3Assigning Macro Controls Using the Controller (644)13Controlling Your Mix (646)13.1Mix View Basics (646)13.1.1Switching between Arrange View and Mix View (646)13.1.2Mix View Elements (647)13.2The Mixer (649)13.2.1Displaying Groups vs. Displaying Sounds (650)13.2.2Adjusting the Mixer Layout (652)13.2.3Selecting Channel Strips (653)13.2.4Managing Your Channels in the Mixer (654)13.2.5Adjusting Settings in the Channel Strips (656)13.2.6Using the Cue Bus (660)13.3The Plug-in Chain (662)13.4The Plug-in Strip (663)13.4.1The Plug-in Header (665)13.4.2Panels for Drumsynths and Internal Effects (667)13.4.3Panel for the Sampler (668)13.4.4Custom Panels for Native Instruments Plug-ins (671)13.4.5Undocking a Plug-in Panel (Native Instruments and External Plug-ins Only) (675)13.5Controlling Your Mix from the Controller (677)13.5.1Navigating Your Channels in Mix Mode (678)13.5.2Adjusting the Level and Pan in Mix Mode (679)13.5.3Mute and Solo in Mix Mode (680)13.5.4Plug-in Icons in Mix Mode (680)14Using Effects (681)14.1Applying Effects to a Sound, a Group or the Master (681)14.1.1Adding an Effect (681)14.1.2Other Operations on Effects (690)14.1.3Using the Side-Chain Input (692)14.2Applying Effects to External Audio (695)14.2.1Step 1: Configure MASCHINE Audio Inputs (695)14.2.2Step 2: Set up a Sound to Receive the External Input (698)14.2.3Step 3: Load an Effect to Process an Input (700)14.3Creating a Send Effect (701)14.3.1Step 1: Set Up a Sound or Group as Send Effect (702)14.3.2Step 2: Route Audio to the Send Effect (706)14.3.3 A Few Notes on Send Effects (708)14.4Creating Multi-Effects (709)15Effect Reference (712)15.1Dynamics (713)15.1.1Compressor (713)15.1.2Gate (717)15.1.3Transient Master (721)15.1.4Limiter (723)15.1.5Maximizer (727)15.2Filtering Effects (730)15.2.1EQ (730)15.2.2Filter (733)15.2.3Cabinet (737)15.3Modulation Effects (738)15.3.1Chorus (738)15.3.2Flanger (740)15.3.3FM (742)15.3.4Freq Shifter (743)15.3.5Phaser (745)15.4Spatial and Reverb Effects (747)15.4.1Ice (747)15.4.2Metaverb (749)15.4.3Reflex (750)15.4.4Reverb (Legacy) (752)15.4.5Reverb (754)15.4.5.1Reverb Room (754)15.4.5.2Reverb Hall (757)15.4.5.3Plate Reverb (760)15.5Delays (762)15.5.1Beat Delay (762)15.5.2Grain Delay (765)15.5.3Grain Stretch (767)15.5.4Resochord (769)15.6Distortion Effects (771)15.6.1Distortion (771)15.6.2Lofi (774)15.6.3Saturator (775)15.7Perform FX (779)15.7.1Filter (780)15.7.2Flanger (782)15.7.3Burst Echo (785)15.7.4Reso Echo (787)15.7.5Ring (790)15.7.6Stutter (792)15.7.7Tremolo (795)15.7.8Scratcher (798)16Working with the Arranger (801)16.1Arranger Basics (801)16.1.1Navigating Song View (804)16.1.2Following the Playback Position in Your Project (806)16.1.3Performing with Scenes and Sections using the Pads (807)16.2Using Ideas View (811)16.2.1Scene Overview (811)16.2.2Creating Scenes (813)16.2.3Assigning and Removing Patterns (813)16.2.4Selecting Scenes (817)16.2.5Deleting Scenes (818)16.2.6Creating and Deleting Scene Banks (820)16.2.7Clearing Scenes (820)16.2.8Duplicating Scenes (821)16.2.9Reordering Scenes (822)16.2.10Making Scenes Unique (824)16.2.11Appending Scenes to Arrangement (825)16.2.12Naming Scenes (826)16.2.13Changing the Color of a Scene (827)16.3Using Song View (828)16.3.1Section Management Overview (828)16.3.2Creating Sections (833)16.3.3Assigning a Scene to a Section (834)16.3.4Selecting Sections and Section Banks (835)16.3.5Reorganizing Sections (839)16.3.6Adjusting the Length of a Section (840)16.3.6.1Adjusting the Length of a Section Using the Software (841)16.3.6.2Adjusting the Length of a Section Using the Controller (843)16.3.7Clearing a Pattern in Song View (843)16.3.8Duplicating Sections (844)16.3.8.1Making Sections Unique (845)16.3.9Removing Sections (846)16.3.10Renaming Scenes (848)16.3.11Clearing Sections (849)16.3.12Creating and Deleting Section Banks (850)16.3.13Working with Patterns in Song view (850)16.3.13.1Creating a Pattern in Song View (850)16.3.13.2Selecting a Pattern in Song View (850)16.3.13.3Clearing a Pattern in Song View (851)16.3.13.4Renaming a Pattern in Song View (851)16.3.13.5Coloring a Pattern in Song View (851)16.3.13.6Removing a Pattern in Song View (852)16.3.13.7Duplicating a Pattern in Song View (852)16.3.14Enabling Auto Length (852)16.3.15Looping (853)16.3.15.1Setting the Loop Range in the Software (854)16.4Playing with Sections (855)16.4.1Jumping to another Playback Position in Your Project (855)16.5Triggering Sections or Scenes via MIDI (856)16.6The Arrange Grid (858)16.7Quick Grid (860)17Sampling and Sample Mapping (862)17.1Opening the Sample Editor (862)17.2Recording Audio (863)17.2.1Opening the Record Page (863)17.2.2Selecting the Source and the Recording Mode (865)17.2.3Arming, Starting, and Stopping the Recording (868)17.2.5Using the Footswitch for Recording Audio (871)17.2.6Checking Your Recordings (872)17.2.7Location and Name of Your Recorded Samples (876)17.3Editing a Sample (876)17.3.1Using the Edit Page (877)17.3.2Audio Editing Functions (882)17.4Slicing a Sample (890)17.4.1Opening the Slice Page (891)17.4.2Adjusting the Slicing Settings (893)17.4.3Live Slicing (898)17.4.3.1Live Slicing Using the Controller (898)17.4.3.2Delete All Slices (899)17.4.4Manually Adjusting Your Slices (899)17.4.5Applying the Slicing (906)17.5Mapping Samples to Zones (912)17.5.1Opening the Zone Page (912)17.5.2Zone Page Overview (913)17.5.3Selecting and Managing Zones in the Zone List (915)17.5.4Selecting and Editing Zones in the Map View (920)17.5.5Editing Zones in the Sample View (924)17.5.6Adjusting the Zone Settings (927)17.5.7Adding Samples to the Sample Map (934)18Appendix: Tips for Playing Live (937)18.1Preparations (937)18.1.1Focus on the Hardware (937)18.1.2Customize the Pads of the Hardware (937)18.1.3Check Your CPU Power Before Playing (937)18.1.4Name and Color Your Groups, Patterns, Sounds and Scenes (938)18.1.5Consider Using a Limiter on Your Master (938)18.1.6Hook Up Your Other Gear and Sync It with MIDI Clock (938)18.1.7Improvise (938)18.2Basic Techniques (938)18.2.1Use Mute and Solo (938)18.2.2Use Scene Mode and Tweak the Loop Range (939)18.2.3Create Variations of Your Drum Patterns in the Step Sequencer (939)18.2.4Use Note Repeat (939)18.2.5Set Up Your Own Multi-effect Groups and Automate Them (939)18.3Special Tricks (940)18.3.1Changing Pattern Length for Variation (940)18.3.2Using Loops to Cycle Through Samples (940)18.3.3Using Loops to Cycle Through Samples (940)18.3.4Load Long Audio Files and Play with the Start Point (940)19Troubleshooting (941)19.1Knowledge Base (941)19.2Technical Support (941)19.3Registration Support (942)19.4User Forum (942)20Glossary (943)Index (951)1Welcome to MASCHINEThank you for buying MASCHINE!MASCHINE is a groove production studio that implements the familiar working style of classi-cal groove boxes along with the advantages of a computer based system. MASCHINE is ideal for making music live, as well as in the studio. It’s the hands-on aspect of a dedicated instru-ment, the MASCHINE hardware controller, united with the advanced editing features of the MASCHINE software.Creating beats is often not very intuitive with a computer, but using the MASCHINE hardware controller to do it makes it easy and fun. You can tap in freely with the pads or use Note Re-peat to jam along. Alternatively, build your beats using the step sequencer just as in classic drum machines.Patterns can be intuitively combined and rearranged on the fly to form larger ideas. You can try out several different versions of a song without ever having to stop the music.Since you can integrate it into any sequencer that supports VST, AU, or AAX plug-ins, you can reap the benefits in almost any software setup, or use it as a stand-alone application. You can sample your own material, slice loops and rearrange them easily.However, MASCHINE is a lot more than an ordinary groovebox or sampler: it comes with an inspiring 7-gigabyte library, and a sophisticated, yet easy to use tag-based Browser to give you instant access to the sounds you are looking for.What’s more, MASCHINE provides lots of options for manipulating your sounds via internal ef-fects and other sound-shaping possibilities. You can also control external MIDI hardware and 3rd-party software with the MASCHINE hardware controller, while customizing the functions of the pads, knobs and buttons according to your needs utilizing the included Controller Editor application. We hope you enjoy this fantastic instrument as much as we do. Now let’s get go-ing!—The MASCHINE team at Native Instruments.MASCHINE Documentation1.1MASCHINE DocumentationNative Instruments provide many information sources regarding MASCHINE. The main docu-ments should be read in the following sequence:1.MASCHINE Getting Started: This document provides a practical approach to MASCHINE viaa set of tutorials covering easy and more advanced tasks in order to help you familiarizeyourself with MASCHINE.2.MASCHINE Manual (this document): The MASCHINE Manual provides you with a compre-hensive description of all MASCHINE software and hardware features.Additional documentation sources provide you with details on more specific topics:▪Controller Editor Manual: Besides using your MASCHINE hardware controller together withits dedicated MASCHINE software, you can also use it as a powerful and highly versatileMIDI controller to pilot any other MIDI-capable application or device. This is made possibleby the Controller Editor software, an application that allows you to precisely define all MIDIassignments for your MASCHINE controller. The Controller Editor was installed during theMASCHINE installation procedure. For more information on this, please refer to the Con-troller Editor Manual available as a PDF file via the Help menu of Controller Editor.▪Online Support Videos: You can find a number of support videos on The Official Native In-struments Support Channel under the following URL: https:///NIsupport-EN. We recommend that you follow along with these instructions while the respective ap-plication is running on your computer.Other Online Resources:If you are experiencing problems related to your Native Instruments product that the supplied documentation does not cover, there are several ways of getting help:▪Knowledge Base▪User Forum▪Technical Support▪Registration SupportYou will find more information on these subjects in the chapter Troubleshooting.1.2Document ConventionsThis section introduces you to the signage and text highlighting used in this manual. This man-ual uses particular formatting to point out special facts and to warn you of potential issues. The icons introducing these notes let you see what kind of information is to be expected:This document uses particular formatting to point out special facts and to warn you of poten-tial issues. The icons introducing the following notes let you see what kind of information can be expected:Furthermore, the following formatting is used:▪Text appearing in (drop-down) menus (such as Open…, Save as… etc.) in the software and paths to locations on your hard disk or other storage devices is printed in italics.▪Text appearing elsewhere (labels of buttons, controls, text next to checkboxes etc.) in the software is printed in blue. Whenever you see this formatting applied, you will find the same text appearing somewhere on the screen.▪Text appearing on the displays of the controller is printed in light grey. Whenever you see this formatting applied, you will find the same text on a controller display.▪Text appearing on labels of the hardware controller is printed in orange. Whenever you see this formatting applied, you will find the same text on the controller.▪Important names and concepts are printed in bold.▪References to keys on your computer’s keyboard you’ll find put in square brackets (e.g.,“Press [Shift] + [Enter]”).►Single instructions are introduced by this play button type arrow.→Results of actions are introduced by this smaller arrow.Naming ConventionThroughout the documentation we will refer to MASCHINE controller (or just controller) as the hardware controller and MASCHINE software as the software installed on your computer.The term “effect” will sometimes be abbreviated as “FX” when referring to elements in the MA-SCHINE software and hardware. These terms have the same meaning.Button Combinations and Shortcuts on Your ControllerMost instructions will use the “+” sign to indicate buttons (or buttons and pads) that must be pressed simultaneously, starting with the button indicated first. E.g., an instruction such as:“Press SHIFT + PLAY”means:1.Press and hold SHIFT.2.While holding SHIFT, press PLAY and release it.3.Release SHIFT.Unlabeled Buttons on the ControllerThe buttons and knobs above and below the displays on your MASCHINE controller do not have labels.。
ABB 电流和电压监控继电器系列说明书
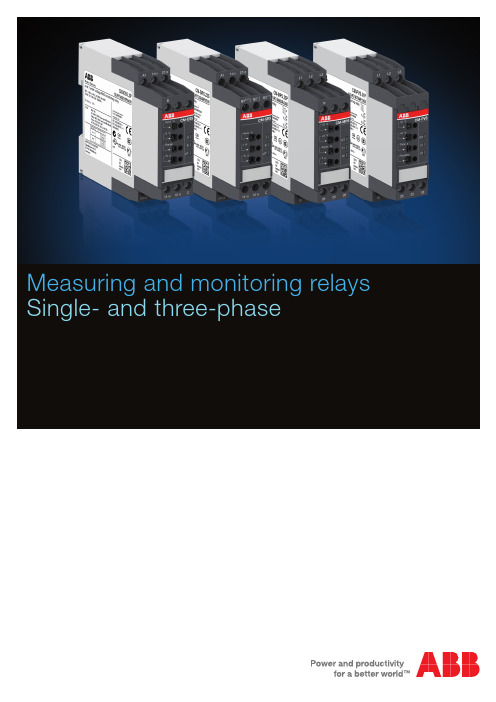
Measuring and monitoring relays Single- and three-phase2 2CDC112184B0201Current and voltage monitoring relays Monitoring the parameters of single-phase mainsCurrent monitoringThe ABB current monitoring relays CM-SRS.xx reliably monitor currents which exceed or fall below the selected threshold value. The functions overcurrent or undercurrent monitoring can be preselected. Single- and multifunction devices for monitoring of direct or alternating currents from 3 mA to 15 A are available.Applications of current and voltage monitoring relays in single-phase mainsCurrent window monitoring (I min , I max )The window monitoring relay CM-SFS.2x is the right solution if the application requires the simultaneous monitoring of over- and undercurrents.Voltage monitoringThe ABB voltage monitoring relays CM-ESS.xx are used to monitor direct and alternating voltages within a range of 3 to 600 V. Over- or undervoltage detection can be preselected.Voltage window monitoring (U min , U max )For the simultaneous detection of over- and undervoltages, the window monitoring relay CM-EFS.2 can be used.For the monitoring of currents and voltages in single-phase AC/DC systems, ABB’s CM range contains a wideselection of powerful and compact devices all in only 22.5 mm wide. This meauring range includes current and voltage monitoring relays for over- and undercurrent protection, over- and undervoltage protection and phase loss monitoring – from 3 mA to 15 A and from 3 V to 600 V. Incorporating ABB’s long-term experience the CM range provides highestsafety and reliability for your electric installation.2CDC112184B0201 3Three-phase monitoring relays Monitoring the parameters in three-phase mainsMonitoring for over- and undervoltageAll electric devices can be damaged when operated continuously at voltages over or under their rated values. An overvoltage could potentially cause heating within the device. If the temperature is unduly high, component parts and thus whole devices or installations may fail or may be destroyed. Undervoltages involve the risk that the switching elements reach an undefined state. In this case, parts of the installation still function, but not others. This misoperation can result in damage of the product or installation. In the worst case, wrong voltages may even cause harm to the operating personnel.Applications for three-phase monitoring relays in three-phase mainsPhase unbalance monitoringIf the supply by the three-phase system is unbalanced due to uneven distribution of the load, the motor will convert a part of the energy into reactive power. This energy gets lost unexploited; also the motor is exposed to higher thermal strain. Other thermal protection devices fail to detect continuing unbalances which can lead to damage or destruction of the motor. The CM range three-phase monitoring relays with phase unbalance monitoring can reliably detect this critical situation.Phase failure detectionIn case of a phase loss, undefined states of the installation are likely to occur. E.g. the startup process of motors is disturbed. All three-phase monitoring relays of the ABB CM range detect a phase loss as soon as the voltage of one phase drops below 60 % of its nominal value.Phase sequence monitoringA change of the phase sequence during operation or an incorrect phase sequence that is applied at start-up will cause a three-phase motor to run with reverse rotation. Certain motors when operated in the reverse direction will cause severe damage to connected loads such as pumps, screw compressors and fans. Especially for non-fixed or portable equipment, such as construction machinery, phase sequence detection prior to the start-up process is highly recommended. ABB offers three-phase monitoring relays with selectable phase sequence monitoring. This provides the capability of ignoring phase sequence conditions for applications, such as motors with forward and reverse rotation, where the phase sequence is Only reliable and continuous monitoring of three-phase networks guarantees trouble-free and economic operation of machines and installations. Thus, the three-phase monitoring relays of the CM range monitor the phase voltages, phase sequence, phase unbalance and phase loss.Interrupted neutralUnder normal conditions, individual phase voltages are equal and the load causes the individual phase currents to vary. Systems that have neutral conductors accommodate this variation by a compensating current flow through the neutralconductor. If the neutral conductor breaks, the compensating current can no longer flow. As a result, the voltage is divided asymmetrically on the individual phases. This means that over- and undervoltages are produced in the individual phases and these can damage or even destroy the connected consumers. ABB offers three-phase monitoring relays that monitor the neutral conductor for interrupted neutral. The interruption of the neutral is detected by means of phase balance monitoring. Automatic phase sequence correctionThe new generation of ABB three-phase monitoring relays offers devices with automatic phase sequence correction. If phase sequence monitoring and phase sequence correction are activated, and in conjunction with a reversing contactor combination, it is ensured that for any non-fixed or portable equipment, e.g. construction machinery, the correct phase sequence is applied to the input terminals of the load.Current and voltage monitoring relays for single-phase AC/DC currentsCurrent monitoring relaysVoltage monitoring relaysCharacteristics of current monitoring relays−Monitoring of DC and AC currents (3 mA to 15 A)−TRMS measuring principle−One device includes 3 measuring ranges−Over- and/or undercurrent monitoring configurable 1)−CM-SFS.2 and CM-SRS.M: Latching function configurable−Hysteresis adjustable (3-30 %) or fixed hysteresis (5 %) 1)−Precise adjustment by front-face operating controls−Screw connection technology orEasy Connect Technology available−Housing material for highest fire protection classificationUL 94 V-0−Tool-free mounting on DIN rail as well as demounting−22.5 mm (0.89 in) width− 3 LEDs for status indication1) depending on deviceCharacteristics of voltage monitoring relays−Monitoring of DC and AC voltages (3-600 V)−TRMS measuring principle−One device includes 4 measuring ranges−Over- and/or undervoltage monitoring configurable 1)−CM-ESS.M and CM-EFS.2: Latching function configurable−Hysteresis adjustable (3-30 %) or fixed hysteresis (5 %) 1)−Precise adjustment by front-face operating controls−Screw connection technology orEasy Connect Technology available−Housing material for highest fire protection classificationUL 94 V-0−Tool-free mounting on DIN rail as well as demounting−22.5 mm (0.89 in) width− 3 LEDs for status indication1) depending on deviceApprovals forcurrent and voltage monitoring relaysA UL 508, CAN/CSA C22.2 No.14C GL(pending)D GOSTK CB SchemeE CCCL RMRSSingle-phase voltage and current monitoring relays protect sensitive equipment and control systems against undervoltage (brownout) or undercurrent events or overvoltage or overcurrent events. Different units with adjustable or fixed threshold values (trip points) are available.All devices are available with two different terminal versions. You can choose between the proven screw connection technology (double-chamber cage connection terminals) and the completely tool-free Easy Connect Technology (push-in terminals).Marks forcurrent and voltage monitoring relaysa CEb C-Tick4 2CDC112184B0201Single- / multifunctional monitoring relays for monitoring of three-phase mainsSinglefunctionalMultifunctionalThe reliable and continuous monitoring of three-phase networks guarantees trouble-free and economic operation of machines and installations.The most multifunctional devices in the EPR assortment are the CM-MPS/N monitoring relays for rated voltage levels up to 820 V AC and 400 Hz. Additionally a variety of economic and cost-efficient three-phase monitoring relays are offered in this range with specialized functionality.Most devices are available with two different terminal versions. You can choose between the proven screw connection technology (double-chamber cage connection terminals) and the completely tool-free Easy Connect Technology (push-in terminals).Characteristics−Monitoring of three-phase mains for phase sequence (canbe switched off), phase failure, phase unbalance over- andundervoltage 1)−TRMS measuring principle−Threshold values are adjustable as absolute values 1)−Powered by the measuring circuit−Precise adjustment by front-face operating controls−Screw connection technology orEasy Connect Technology available−Housing material for highest fire protection classificationUL 94 V-0−Tool-free mounting on DIN rail as well as demounting−S-range: 22.5 mm (0.89 in) width−N-range : 45 mm (1.78 in) width− 3 LEDs for status indication1) depending on deviceApprovalsA UL 508, CAN/CSA C22.2 No.14(CM-PVS.81 pending,not for CM-MPN.72)C GL(pending)D GOSTK CB Scheme(pending)E CCC(CM-PVS.81 pending)Marksa CEb C-Tick(CM-PVS.81 pending)2CDC112184B0201 56 2CDC112184B0201TypeRated control supply voltage Connection technologyMeasuring rangesOrder codeCM-SRS.11P24-240 V AC/DCPush-in terminals3-30 mA, 10-100 mA, 0.1-1 A1SVR 740 840 R0200110-130 V AC 1SVR 740 841 R0200220-240 V AC 1SVR 740 841 R1200CM-SRS.11S24-240 V AC/DCScrew terminals3-30 mA, 10-100 mA, 0.1-1 A1SVR 730 840 R0200110-130 V AC 1SVR 730 841 R0200220-240 V AC 1SVR 730 841 R1200CM-SRS.12S24-240 V AC/DCScrew terminals0.3-1.5 A, 1-5 A, 3-15 A1SVR 730 840 R0300110-130 V AC 1SVR 730 841 R0300220-240 V AC 1SVR 730 841 R1300CM-SRS.21S24-240 V AC/DCScrew terminals3-30 mA, 10-100 mA, 0.1-1 A1SVR 730 840 R0400110-130 V AC 1SVR 730 841 R0400220-240 V AC 1SVR 730 841 R1400CM-SRS.21P24-240 V AC/DCPush-in terminals 1SVR 740 840 R0400110-130 V AC 1SVR 740 841 R0400220-240 V AC 1SVR 740 841 R1400CM-SRS.22S 24-240 V AC/DCScrew terminals0.3-1.5 A, 1-5 A, 3-15 A1SVR 730 840 R0500110-130 V AC 1SVR 730 841 R0500220-240 V AC1SVR 730 841 R1500CM-SRS.M1P 24-240 V AC/DC Push-in terminals 3-30 mA, 10-100 mA, 0.1-1 A 1SVR 740 840 R0600CM-SRS.M1S Screw terminals 1SVR 730 840 R0600CM-SRS.M2S 0.3-1.5 A, 1-5 A, 3-15 A 1SVR 730 840 R0700CM-SFS.21P 24-240 V AC/DC Push-in terminals 3-30 mA, 10-100 mA, 0.1-1 A 1SVR 740 760 R0400CM-SFS.21S Screw terminals1SVR 730 760 R0400CM-SFS.22S0.3-1.5 A, 1-5 A, 3-15A1SVR 730 760 R0500CM-ESS.1P24-240 V AC/DCPush-in terminals3-30 V , 6-60 V , 30-300 V , 60-600 V1SVR 740 830 R0300110-130 V AC 1SVR 740 831 R0300220-240 V AC 1SVR 740 831 R1300CM-ESS.1S24-240 V AC/DCScrew terminals3-30 V , 6-60 V , 30-300 V , 60-600 V1SVR 730 830 R0300110-130 V AC 1SVR 730 831 R0300220-240 V AC 1SVR 730 831 R1300CM-ESS.1P24-240 V AC/DCPush-in terminals3-30 V , 6-60 V , 30-300 V , 60-600 V1SVR 740 830 R0300110-130 V AC 1SVR 740 831 R0300220-240 V AC 1SVR 740 831 R1300CM-ESS.1S24-240 V AC/DCScrew type terminals3-30 V , 6-60 V , 30-300 V , 60-600 V1SVR 730 830 R0300110-130 V AC 1SVR 730 831 R0300220-240 V AC 1SVR 730 831 R1300CM-ESS.1P24-240 V AC/DCPush-in terminals3-30 V , 6-60 V , 30-300 V , 60-600 V1SVR 740 830 R0300110-130 V AC 1SVR 740 831 R0300220-240 V AC 1SVR 740 831 R1300CM-ESS.1S 24-240 V AC/DCScrew type terminals3-30 V , 6-60 V , 30-300 V , 60-600 V1SVR 730 830 R0300110-130 V AC 1SVR 730 831 R0300220-240 V AC 1SVR 730 831 R1300CM-ESS.MP 24-240 V AC/DC Push-in terminals 3-30 V , 6-60 V , 30-300 V , 60-600 V 1SVR 740 830 R0500CM-ESS.MS Screw type terminals 1SVR 730 830 R0500CM-ESS.MP 24-240 V AC/DC Push-in terminals 3-30 V , 6-60 V , 30-300 V , 60-600 V 1SVR 740 830 R0500CM-ESS.MS Screw type terminals 1SVR 730 830 R0500CM-EFS.2P 24-240 V AC/DC Push-in terminals 3-30 V , 6-60 V , 30-300 V , 60-600 V 1SVR 740 750 R0400CM-EFS.2S24-240 V AC/DCScrew type terminals3-30 V , 6-60 V , 30-300 V , 60-600 V1SVR 730 750 R0400Current and voltage monitoring relays Ordering dataThree-phase monitoring relays Ordering dataType Rated control supply voltage =measuring voltage Interrupted neutral monitoring ConnectiontechnologyOrder codeCM-MPS.11P 3 x 90-170 V AC yes Push-in terminals1SVR 740 885 R1300CM-MPS.11S yes Screw terminals1SVR 730 885 R1300CM-MPS.21P 3 x 180-280 V AC yes Push-in terminals1SVR 740 885 R3300CM-MPS.21S yes Screw terminals1SVR 730 885 R3300CM-MPS.31P 3 x 160-300 V AC no Push-in terminals1SVR 740 884 R1300CM-MPS.31S no Screw terminals1SVR 730 884 R1300CM-MPS.41P 3 x 300-500 V AC no Push-in terminals1SVR 740 884 R3300CM-MPS.41S no Screw terminals1SVR 730 884 R3300CM-MPS.23P 3 x 180-280 V AC yes Push-in terminals1SVR 740 885 R4300CM-MPS.23S yes Screw terminals1SVR 730 885 R4300CM-MPS.43P 3 x 300-500 V AC no Push-in terminals1SVR 740 884 R4300CM-MPS.43S no Screw terminals1SVR 730 884 R4300CM-MPS.52P 3 x 350-580 V AC no Push-in terminals1SVR 760 487 R8300CM-MPS.52S no Screw terminals1SVR 750 487 R8300CM-MPS.62P 3 x 450-720 V AC no Push-in terminals1SVR 760 488 R8300CM-MPS.62S no Screw terminals1SVR 750 488 R8300CM-MPS.72P 3 x 530-820 V AC no Push-in terminals1SVR 760 489 R8300CM-MPS.72S no Screw terminals1SVR 750 489 R8300CM-PSS.31P 3 x 380 V AC no Push-in terminals1SVR 740 784 R2300CM-PSS.31S no Screw terminals1SVR 730 784 R2300CM-PSS.41P 3 x 400 V AC no Push-in terminals1SVR 740 784 R3300CM-PSS.41S no Screw terminals1SVR 730 784 R3300CM-PVS.31P 3 x 160-300 V AC no Push-in terminals1SVR 740 794 R1300CM-PVS.31S no Screw terminals1SVR 730 794 R1300CM-PVS.41P 3 x 300-500 V AC no Push-in terminals1SVR 740 794 R3300CM-PVS.41S no Screw terminals1SVR 730 794 R3300CM-PVS.81P 3 x 200-400 V AC no Push-in terminals1SVR 740 794 R2300CM-PVS.81S no Screw terminals1SVR 730 794 R2300CM-PAS.31P 3 x 160-300 V AC no Push-in terminals1SVR 740 774 R1300CM-PAS.31S no Screw terminals1SVR 730 774 R1300CM-PAS.41P 3 x 300-500 V AC no Push-in terminals1SVR 740 774 R3300CM-PAS.41S no Screw terminals1SVR 730 774 R3300CM-PBE 3 x 380-440 V AC, 220-240 V AC yes Screw terminals1SVR 550 881 R9400CM-PBE 3 x 380-440 V AC no Screw terminals1SVR 550 882 R9500CM-PVE 3 x 320-460 V AC, 185-265 V AC yes Screw terminals1SVR 550 870 R9400CM-PVE 3 x 320-460 V AC no Screw terminals1SVR 550 871 R9500CM-PFS 3 x 200-500 V AC no Screw terminals1SVR 430 824 R93002CDC112184B0201 7D o c u m e n t n u m b e r 2C D C 112 184 B 0201 p r i n t e d i n G e r m a n y (04/12-Z V D )Contact usABB STOTZ-KONTAKT GmbH /lowvoltage-> Control Products -> Electronic Relays and Controls -> Three Phase Monitors -> Single Phase Monitors/contactsNote:We reserve the right to make technical changes or modify the contents of this document without prior notice. With regard to purchase orders, the agreed particulars shall prevail. ABB AG does not accept any responsibility whatsoever for potential errors or possible lack of information in this docu-ment.We reserve all rights to this document and the sub-ject matter and illustrations contained therein. Any reproduction, disclosure to third parties or utilisation of its contents – in whole or in part – is forbidden without prior written consent from ABB AG. Copyright© 2012 ABB All rights reserved。
PEL家族电力和能量日志器的阶段顺序指示灯说明书

PEL Phase Order Indicator Blinking Red How to Determine WHY indicator is blinking.The PEL family of Power and Energy Loggers have a “Phase Order” light on their front panel. This indicator lights up and blinks red when the PEL indicates a potential issue with the phase order. There may be times when the Phase Order indicator is blinking red but you are certain that all of your voltage and current inputs are connected to your electrical network correctly. Many users have recorded successful campaigns with this indicator blinking. The actual conditions of the network you are monitoring may be causing this and there is nothing you can do to remedy it. This document should help you understand the nature of the indicator and the reasoning behind it. This document will describe how to determine what is causing the Phase Order indicator to blink red. The PEL analyzes various angles between the current, voltage and power. The angles measured, and theirrelationship to each other, will trigger the indicator light. It may not be obvious why the Phase Order light is lit. Required Items:⏹ The Voltage (V1,V2,V3,N) and Current (I1,I2,I3) inputs are connected correctly to the electrical network ⏹ Connecting to the PEL via the DataView® Control Panel or through the Android App⏹ Viewing the Phasor Diagram using the Real-time view in the Control Panel/App⏹Knowing which Electrical Hook-up is programmed into the PEL (3-phase 4-wire Y, 3-phase 3-wire Delta, etc….)⏹ Annex tables (at the end of this document), extracted from the PEL user manual. Once you have the above information, then you are ready to determine the reason behind the indicator. Example Phasor Diagram with “Phase Order” indicator blinking red.In the real-time example below, the Phasor Diagram on a PEL where the red “Phase Order” indicator is blinking. Observing this view is needed to find the root cause of the indicator. Follow the steps outlined below.Open PEL Control Panel, select the PEL under “Pel Network”.1)Click on “Real-time data”2)Click on the Phasor Diagram icon to display the below screen.3)The angles that are triggering the Phase Order indicator will be displayed as either a Yellow ? or a Red X.Our example has a Yellow ? next to “Current Rotation”. This indicates that the reason lies within theCurrent Rotation angles associated with a 3-phase 4-wire Y electrical network.4)Looking at the current rotation angles, we see the following angles:These angles show the relative vector for each leg of current, and their relationship to each other.5)Refer to the Annex table “A.5.1 – Current Phase Order”. There are 3 charts showing the ElectricalHookup and the phase angles that are acceptable for proper Phase Order. Since Current Rotation is the cause of the indicator, we need the Current Phase Order chart.In this example, the Electrical Hookup is “3-phase 4-wire Y” and the acceptable angles are show below:6) If we look at the “3-Phase 4-Wire Y” row (highlighted yellow), we see that angles between (I1,I3), (I3,I2),and (I2,I1) all need to be at 120o ±30o (circled red). Therefore, the acceptable angles are 150o to 90o for the Current Phase Order to be considered good. When the angles are within these limits, then the Phase Order Indicator will not blink red.7)If we look back to our Phasor Diagram, we can see that the angle of (I1,I3) is at 72.2o (circled red).This angle of 72.2o is outside of the normal acceptable range of 120o ±30o (150o to 90o) as defined by the chart.8)The PEL then concludes that the Current Angle between I1 and I3 is outside of acceptable range and thiswill light up the Phase Order indicator by blinking red.9)There may be multiple areas and multiple angles that are causing the issue. Please analyze all anglesfrom the category that has a Yellow ? or a Red X.10)Repeat above process if the fault lies with Voltage Rotation/“Voltage Phase Order” (Annex A.5.2) or withPower Rotation/”Current vs Voltage Phase Order“ (Annex.5.3)There can be many valid reasons why these angles are outside of our defined limits. These varied reasons can be caused by the native behavior of the electrical network the PEL is monitoring.For example, the state of the current and whether it is Lagging, Leading or In-Phase with the voltage. If you have a strong Inductive load on your system, the current will lag behind your voltage. If you have a strong Capacitive load, the current will lead the voltage. If your load is purely Resistive, the current will be in-phase with your voltage. If the current leads or lags the voltage by a large margin, then the PEL may interpret this as a Phase Order error.Low levels of current that have a high harmonic content may also trigger the Phase Order indicator.I hope you found this useful in determining why your Phase Order indicator is blinking red.If you have any further questions, feel free to contact AEMC Technical Support at 1-800-343-1391 x351 or via email to ******************** .Thank you.ANNEXES。
IO-Link数字流量开关操作手册说明书

Before UseDigital Flow SwitchPF3A703H/PF3A706H/PF3A712H-LSafety InstructionsThese safety instructions are intended to prevent hazardous situations and/orequipment damage.These instructions indicate the level of potential hazard with the labels of"Caution", "Warning" or "Danger". They are all important notes for safety and mustbe followed in addition to International standards (ISO/IEC) and other safetyregulations.OperatorThank you for purchasing an SMC PF3A703H/PF3A706H/PF3A712H-L DigitalFlow Switch.Please read this manual carefully before operating the product and make sure youunderstand its capabilities and limitations. Please keep this manual handy forfuture reference.Safety Instructions1324DisplayBody(IN side)Connector pin numbers(on the product)Mounting•Never mount the product in a place that will be used as a mechanical support during piping.•Never mount the product upside down.•Attach the piping so that the fluid flows in the direction indicated by the arrow on the body.•The monitor with integrated display can be rotated.Rotating the display with excessive force will damage the end stop.•Visibility decreases if the display is viewed from the opposite side to the buttons.Check the settings and display from in front of the display.Mounting and InstallationRefer to the product catalogue or SMC website (URL https://) for moredetailed information.IN OUTArrowthe IN side of the product.When installing a regulator at the IN side of the product, make sure that hunting is not generated.•The piping on the IN side must have a straight section of piping whose length is 8 timesthe piping diameter or more.If a straight section of piping is not installed, the accuracy will vary by approximately 3%F.S.•Avoid sudden changes to the pipingsize on the IN side of the product.The accuracy may vary.•Do not release the OUT side pipingport of the product directly to theThe accuracy may vary.○Flow direction○Rotation of the display•Use the correct tightening torque for piping. (Refer to the table below for the requiredtorque values.)•If the tightening torque is exceeded, the product can be damaged.If the tightening torque is insufficient, the fittings may become loose.•Avoid any sealing tape getting inside the fluid passage.•Ensure there is no leakage after piping.•When mounting the fitting, a spanner should be used on the body (metal part) of thefitting only.Holding other parts of the product with a spanner may damage the product.Specifically, make sure that the spanner does not damage the M12 connector.■WiringConnection•Connections should only be made with the power supply turned off.•Use a separate route for the product wiring and any power or high voltage wiring. If wiresand cables are routed together with power or high voltage cables, malfunction may resultdue to noise.•If a commercially available switching power supply is used, be sure to ground the frameground (FG) terminal. If the product is connected to the commercially available switchingpower supply, switching noise will be superimposed and the product specifications will notbe satisfied. In that case, insert a noise filter such as a line noise filter/ ferrite between theswitching power supplies or change the switching power supply to the series power supply.Connecting/Disconnecting•Align the lead wire connector with the connector keygroove, and insert it straight in. Turn the knurled partclockwise. Connection is complete when the knurledpart is fully tightened. Check that the connection is notloose.•To remove the connector, loosen the knurled part andpull the connector straight out.Connector pin numbers (lead wire)Outline of SettingsPower is supplied.∗: If a button operation is not performed for 3 seconds during the setting, the display will flash. (This is toprevent the setting from remaining incomplete if, for instance, an operator were to leave during setting.)∗: 3 step setting mode, simple setting mode and function selection mode settings will reflect on each other.■3 step setting modeIn the3 step setting mode, the set value selected in the sub display and the hysteresiscan be changed in just 3 steps.Switch ONP_1Flow[L/min]H_1settingsWhen shipped, the default setting is as follows.When the flow exceeds the set value [P_1], the switch will be turned ON.When the flow falls below the set value by the amount of hysteresis [H_1] or more, theswitch will turn OFF.If the operation shown below is acceptable, then keep these settings.For more detailed settings, set each function in the function selection mode.(1) Press the S button once when the item to be changed is displayed on the subdisplay.The set value on the sub display (right) will start flashing.S<Operation>[Hysteresis mode]In the 3 step setting mode, the set value (P_1 or n_1) and hysteresis (H_1) can bechanged.Set the items on the sub display (set value and hysteresis) using the ▲ or ▼ buttons.When changing the set value, follow the operation below. The hysteresis setting can bechanged in the same way.(2) Press the ▲ or ▼ button to change the set value.The ▲ button is to increase and the ▼ button is to decrease the set value.●Press the ▲ button once to increase the value by one digit, press and hold tocontinuously increase.●When ▲ and ▼ buttons are pressed simultaneously for 1 second or more, the setvalue is displayed as [ - - - ], and the set value will be set to the same as thedisplayed value automatically. Afterwards, it is possible to adjust the value bypressing ▲ or ▼.●Press the ▼ button once to reduce the value by one digit, press and hold tocontinuously reduce.(3) Press the S button to complete the setting.To change setting, refer to the operation manual from SMC website(URL https://) or contact SMC.<Operation>[Hysteresis mode](1) Press the S button for 1 second or longer(but less than 3 seconds) in measurementmode. [SEt] is displayed on the main display.When the button is released while in the [SEt] display, the current flow value isdisplayed on the main display, [P_1] or [n_1] is displayed on the sub display (left)and the set value is displayed on the sub display (right).(2) Change the set value using the ▲ or ▼ button, and press the SET button to set thevalue. Then, the setting moves to hysteresis setting.(5) Press and hold the S button for 2 seconds or longer to complete the simple setting.(If the button is pressed for less than 2 seconds, the setting will be returned to P_1.)(3) Change the set value with the ▲ or ▼ button, and press the S button to set thevalue. Then, the setting moves to the setting of OUT2.∗1: Selected items of (1) to (4) become valid after pressing the S button.∗2: After enabling the setting by pressing the S button, it is possible to return to measurementmode by pressing the S button for 2 seconds or longer.∗3: When the output mode is set to accumulated pulse, error output or output OFF, the simplesetting mode cannot be used.(the setting returns to measurement mode by releasing the button when [SEt] is displayed.)■Simple setting modeIn the simple setting mode, the set value, hysteresis and delay time can be changed whilechecking the current flow value (main display).(4) Like the setting of OUT1, the setting returns to the setting of OUT2 by pressing theS button after setting the set value and hysteresis.∗: When [F 1] and [F 2] are set to accumulatedpulse output, error output or output OFF [---]will be displayed in the sub screen when[SEt] is displayed. It is not possible to moveto the Simple setting mode.Change the Function Settings∗1: Setting is only possible for models with the units selection function.∗2: [F 2] The OUT2 setting can be set on the product screen, but since there is no OUT2 switch outputfunction as an output specification, it is not possible to output the ON/OFF signal to an external device.∗3: When the 1 switch output type (output specification symbol is L) is used, [F5] is displayed as [---]and cannot be set.1 to 5 V or 0 to 10 V can be selected when the analogue voltage output type is used.Analogue output free range function can be selected.∗4: When Line name is selected, a suitable line name can be input.To change setting, refer to the operation manual from SMC website(URL https://) or contact SMC.■Function selection modeIn measurement mode, press theS button for 3 seconds or longer,to display [F 0].The [F] indicates the mode forchanging each Function Setting.Press the S button for 2 secondsor longer in function selectionmode to return to measurementmode.To change setting, refer to the operation manual from SMC website(URL https://) or contact SMC.○Reset operationThe Accumulated Flow, Peak Value and Bottom Value can be reset.To reset the accumulated value, press the ▼ and S button for 1 second or longer.○Snap shot functionThe current flow rate value can be stored to the switch output ON/OFF set point.When the items on the Sub display (left) are selected in either 3 step setting mode, Simplesetting mode or Setting of each function mode, by pressing the ▲ and ▼ buttonssimultaneously for 1 second or longer, the value of the sub display (right) will show "----",and the values corresponding to the current flow rate are automatically displayed.MaintenanceHow to reset the product after a power loss or when the power has beenunexpectedly removedThe settings for the product are retained in memory prior to the power loss or de-energizingof the product.The output condition is also recoverable to that prior to the power loss or de-energizing.However, this may change depending on the operating environment. Therefore, check thesafety of the whole installation before operating the product.If the installation is using accurate control, wait until the product has warmed up(approximately 10 to 15 minutes) before operation.Refer to the product catalogue or operation manual from SMC website(URL https://) for more information about the product specifications anddimensions.Specifications / Dimensions○Key-lock function(1) Press the S button for 5 seconds or longer in measurement mode. When [oPE] isdisplayed on the main display, release the button.The current setting "LoC" or "UnLoC" will be displayed on the sub display.(2) Select the key locking/un-locking using the ▲ or ▼ button, and press the S button toset.To use each of these functions, refer to the operation manual from SMC website(URL https://) or contact SMC.The IODD file can be downloaded from the SMC website (URL https://).Note: Specifications are subject to change without prior notice and any obligation on the part of the manufacturer.© 2020 SMC Corporation All Rights ReservedAkihabara UDX 15F, 4-14-1, Sotokanda, Chiyoda-ku, Tokyo 101-0021, JAPANPhone: +81 3-5207-8249 Fax: +81 3-5298-5362URL https://PF※※-OMX0003Troubleshootingdisplayed, please contact SMC.Refer to the operation manual from SMC website (URL https://) for moreinformation about troubleshooting.。
OSHA现场作业手册说明书
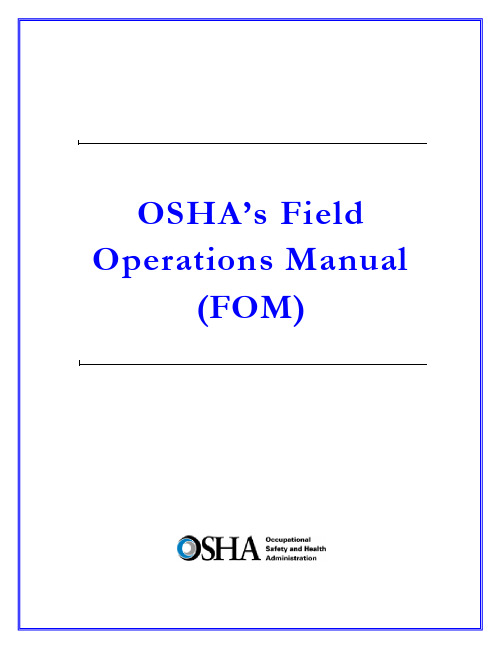
DIRECTIVE NUMBER: CPL 02-00-150 EFFECTIVE DATE: April 22, 2011 SUBJECT: Field Operations Manual (FOM)ABSTRACTPurpose: This instruction cancels and replaces OSHA Instruction CPL 02-00-148,Field Operations Manual (FOM), issued November 9, 2009, whichreplaced the September 26, 1994 Instruction that implemented the FieldInspection Reference Manual (FIRM). The FOM is a revision of OSHA’senforcement policies and procedures manual that provides the field officesa reference document for identifying the responsibilities associated withthe majority of their inspection duties. This Instruction also cancels OSHAInstruction FAP 01-00-003 Federal Agency Safety and Health Programs,May 17, 1996 and Chapter 13 of OSHA Instruction CPL 02-00-045,Revised Field Operations Manual, June 15, 1989.Scope: OSHA-wide.References: Title 29 Code of Federal Regulations §1903.6, Advance Notice ofInspections; 29 Code of Federal Regulations §1903.14, Policy RegardingEmployee Rescue Activities; 29 Code of Federal Regulations §1903.19,Abatement Verification; 29 Code of Federal Regulations §1904.39,Reporting Fatalities and Multiple Hospitalizations to OSHA; and Housingfor Agricultural Workers: Final Rule, Federal Register, March 4, 1980 (45FR 14180).Cancellations: OSHA Instruction CPL 02-00-148, Field Operations Manual, November9, 2009.OSHA Instruction FAP 01-00-003, Federal Agency Safety and HealthPrograms, May 17, 1996.Chapter 13 of OSHA Instruction CPL 02-00-045, Revised FieldOperations Manual, June 15, 1989.State Impact: Notice of Intent and Adoption required. See paragraph VI.Action Offices: National, Regional, and Area OfficesOriginating Office: Directorate of Enforcement Programs Contact: Directorate of Enforcement ProgramsOffice of General Industry Enforcement200 Constitution Avenue, NW, N3 119Washington, DC 20210202-693-1850By and Under the Authority ofDavid Michaels, PhD, MPHAssistant SecretaryExecutive SummaryThis instruction cancels and replaces OSHA Instruction CPL 02-00-148, Field Operations Manual (FOM), issued November 9, 2009. The one remaining part of the prior Field Operations Manual, the chapter on Disclosure, will be added at a later date. This Instruction also cancels OSHA Instruction FAP 01-00-003 Federal Agency Safety and Health Programs, May 17, 1996 and Chapter 13 of OSHA Instruction CPL 02-00-045, Revised Field Operations Manual, June 15, 1989. This Instruction constitutes OSHA’s general enforcement policies and procedures manual for use by the field offices in conducting inspections, issuing citations and proposing penalties.Significant Changes∙A new Table of Contents for the entire FOM is added.∙ A new References section for the entire FOM is added∙ A new Cancellations section for the entire FOM is added.∙Adds a Maritime Industry Sector to Section III of Chapter 10, Industry Sectors.∙Revises sections referring to the Enhanced Enforcement Program (EEP) replacing the information with the Severe Violator Enforcement Program (SVEP).∙Adds Chapter 13, Federal Agency Field Activities.∙Cancels OSHA Instruction FAP 01-00-003, Federal Agency Safety and Health Programs, May 17, 1996.DisclaimerThis manual is intended to provide instruction regarding some of the internal operations of the Occupational Safety and Health Administration (OSHA), and is solely for the benefit of the Government. No duties, rights, or benefits, substantive or procedural, are created or implied by this manual. The contents of this manual are not enforceable by any person or entity against the Department of Labor or the United States. Statements which reflect current Occupational Safety and Health Review Commission or court precedents do not necessarily indicate acquiescence with those precedents.Table of ContentsCHAPTER 1INTRODUCTIONI.PURPOSE. ........................................................................................................... 1-1 II.SCOPE. ................................................................................................................ 1-1 III.REFERENCES .................................................................................................... 1-1 IV.CANCELLATIONS............................................................................................. 1-8 V. ACTION INFORMATION ................................................................................. 1-8A.R ESPONSIBLE O FFICE.......................................................................................................................................... 1-8B.A CTION O FFICES. .................................................................................................................... 1-8C. I NFORMATION O FFICES............................................................................................................ 1-8 VI. STATE IMPACT. ................................................................................................ 1-8 VII.SIGNIFICANT CHANGES. ............................................................................... 1-9 VIII.BACKGROUND. ................................................................................................. 1-9 IX. DEFINITIONS AND TERMINOLOGY. ........................................................ 1-10A.T HE A CT................................................................................................................................................................. 1-10B. C OMPLIANCE S AFETY AND H EALTH O FFICER (CSHO). ...........................................................1-10B.H E/S HE AND H IS/H ERS ..................................................................................................................................... 1-10C.P ROFESSIONAL J UDGMENT............................................................................................................................... 1-10E. W ORKPLACE AND W ORKSITE ......................................................................................................................... 1-10CHAPTER 2PROGRAM PLANNINGI.INTRODUCTION ............................................................................................... 2-1 II.AREA OFFICE RESPONSIBILITIES. .............................................................. 2-1A.P ROVIDING A SSISTANCE TO S MALL E MPLOYERS. ...................................................................................... 2-1B.A REA O FFICE O UTREACH P ROGRAM. ............................................................................................................. 2-1C. R ESPONDING TO R EQUESTS FOR A SSISTANCE. ............................................................................................ 2-2 III. OSHA COOPERATIVE PROGRAMS OVERVIEW. ...................................... 2-2A.V OLUNTARY P ROTECTION P ROGRAM (VPP). ........................................................................... 2-2B.O NSITE C ONSULTATION P ROGRAM. ................................................................................................................ 2-2C.S TRATEGIC P ARTNERSHIPS................................................................................................................................. 2-3D.A LLIANCE P ROGRAM ........................................................................................................................................... 2-3 IV. ENFORCEMENT PROGRAM SCHEDULING. ................................................ 2-4A.G ENERAL ................................................................................................................................................................. 2-4B.I NSPECTION P RIORITY C RITERIA. ..................................................................................................................... 2-4C.E FFECT OF C ONTEST ............................................................................................................................................ 2-5D.E NFORCEMENT E XEMPTIONS AND L IMITATIONS. ....................................................................................... 2-6E.P REEMPTION BY A NOTHER F EDERAL A GENCY ........................................................................................... 2-6F.U NITED S TATES P OSTAL S ERVICE. .................................................................................................................. 2-7G.H OME-B ASED W ORKSITES. ................................................................................................................................ 2-8H.I NSPECTION/I NVESTIGATION T YPES. ............................................................................................................... 2-8 V.UNPROGRAMMED ACTIVITY – HAZARD EVALUATION AND INSPECTION SCHEDULING ............................................................................ 2-9 VI.PROGRAMMED INSPECTIONS. ................................................................... 2-10A.S ITE-S PECIFIC T ARGETING (SST) P ROGRAM. ............................................................................................. 2-10B.S CHEDULING FOR C ONSTRUCTION I NSPECTIONS. ..................................................................................... 2-10C.S CHEDULING FOR M ARITIME I NSPECTIONS. ............................................................................. 2-11D.S PECIAL E MPHASIS P ROGRAMS (SEP S). ................................................................................... 2-12E.N ATIONAL E MPHASIS P ROGRAMS (NEP S) ............................................................................... 2-13F.L OCAL E MPHASIS P ROGRAMS (LEP S) AND R EGIONAL E MPHASIS P ROGRAMS (REP S) ............ 2-13G.O THER S PECIAL P ROGRAMS. ............................................................................................................................ 2-13H.I NSPECTION S CHEDULING AND I NTERFACE WITH C OOPERATIVE P ROGRAM P ARTICIPANTS ....... 2-13CHAPTER 3INSPECTION PROCEDURESI.INSPECTION PREPARATION. .......................................................................... 3-1 II.INSPECTION PLANNING. .................................................................................. 3-1A.R EVIEW OF I NSPECTION H ISTORY .................................................................................................................... 3-1B.R EVIEW OF C OOPERATIVE P ROGRAM P ARTICIPATION .............................................................................. 3-1C.OSHA D ATA I NITIATIVE (ODI) D ATA R EVIEW .......................................................................................... 3-2D.S AFETY AND H EALTH I SSUES R ELATING TO CSHO S.................................................................. 3-2E.A DVANCE N OTICE. ................................................................................................................................................ 3-3F.P RE-I NSPECTION C OMPULSORY P ROCESS ...................................................................................................... 3-5G.P ERSONAL S ECURITY C LEARANCE. ................................................................................................................. 3-5H.E XPERT A SSISTANCE. ........................................................................................................................................... 3-5 III. INSPECTION SCOPE. ......................................................................................... 3-6A.C OMPREHENSIVE ................................................................................................................................................... 3-6B.P ARTIAL. ................................................................................................................................................................... 3-6 IV. CONDUCT OF INSPECTION .............................................................................. 3-6A.T IME OF I NSPECTION............................................................................................................................................. 3-6B.P RESENTING C REDENTIALS. ............................................................................................................................... 3-6C.R EFUSAL TO P ERMIT I NSPECTION AND I NTERFERENCE ............................................................................. 3-7D.E MPLOYEE P ARTICIPATION. ............................................................................................................................... 3-9E.R ELEASE FOR E NTRY ............................................................................................................................................ 3-9F.B ANKRUPT OR O UT OF B USINESS. .................................................................................................................... 3-9G.E MPLOYEE R ESPONSIBILITIES. ................................................................................................. 3-10H.S TRIKE OR L ABOR D ISPUTE ............................................................................................................................. 3-10I. V ARIANCES. .......................................................................................................................................................... 3-11 V. OPENING CONFERENCE. ................................................................................ 3-11A.G ENERAL ................................................................................................................................................................ 3-11B.R EVIEW OF A PPROPRIATION A CT E XEMPTIONS AND L IMITATION. ..................................................... 3-13C.R EVIEW S CREENING FOR P ROCESS S AFETY M ANAGEMENT (PSM) C OVERAGE............................. 3-13D.R EVIEW OF V OLUNTARY C OMPLIANCE P ROGRAMS. ................................................................................ 3-14E.D ISRUPTIVE C ONDUCT. ...................................................................................................................................... 3-15F.C LASSIFIED A REAS ............................................................................................................................................. 3-16VI. REVIEW OF RECORDS. ................................................................................... 3-16A.I NJURY AND I LLNESS R ECORDS...................................................................................................................... 3-16B.R ECORDING C RITERIA. ...................................................................................................................................... 3-18C. R ECORDKEEPING D EFICIENCIES. .................................................................................................................. 3-18 VII. WALKAROUND INSPECTION. ....................................................................... 3-19A.W ALKAROUND R EPRESENTATIVES ............................................................................................................... 3-19B.E VALUATION OF S AFETY AND H EALTH M ANAGEMENT S YSTEM. ....................................................... 3-20C.R ECORD A LL F ACTS P ERTINENT TO A V IOLATION. ................................................................................. 3-20D.T ESTIFYING IN H EARINGS ................................................................................................................................ 3-21E.T RADE S ECRETS. ................................................................................................................................................. 3-21F.C OLLECTING S AMPLES. ..................................................................................................................................... 3-22G.P HOTOGRAPHS AND V IDEOTAPES.................................................................................................................. 3-22H.V IOLATIONS OF O THER L AWS. ....................................................................................................................... 3-23I.I NTERVIEWS OF N ON-M ANAGERIAL E MPLOYEES .................................................................................... 3-23J.M ULTI-E MPLOYER W ORKSITES ..................................................................................................................... 3-27 K.A DMINISTRATIVE S UBPOENA.......................................................................................................................... 3-27 L.E MPLOYER A BATEMENT A SSISTANCE. ........................................................................................................ 3-27 VIII. CLOSING CONFERENCE. .............................................................................. 3-28A.P ARTICIPANTS. ..................................................................................................................................................... 3-28B.D ISCUSSION I TEMS. ............................................................................................................................................ 3-28C.A DVICE TO A TTENDEES .................................................................................................................................... 3-29D.P ENALTIES............................................................................................................................................................. 3-30E.F EASIBLE A DMINISTRATIVE, W ORK P RACTICE AND E NGINEERING C ONTROLS. ............................ 3-30F.R EDUCING E MPLOYEE E XPOSURE. ................................................................................................................ 3-32G.A BATEMENT V ERIFICATION. ........................................................................................................................... 3-32H.E MPLOYEE D ISCRIMINATION .......................................................................................................................... 3-33 IX. SPECIAL INSPECTION PROCEDURES. ...................................................... 3-33A.F OLLOW-UP AND M ONITORING I NSPECTIONS............................................................................................ 3-33B.C ONSTRUCTION I NSPECTIONS ......................................................................................................................... 3-34C. F EDERAL A GENCY I NSPECTIONS. ................................................................................................................. 3-35CHAPTER 4VIOLATIONSI. BASIS OF VIOLATIONS ..................................................................................... 4-1A.S TANDARDS AND R EGULATIONS. .................................................................................................................... 4-1B.E MPLOYEE E XPOSURE. ........................................................................................................................................ 4-3C.R EGULATORY R EQUIREMENTS. ........................................................................................................................ 4-6D.H AZARD C OMMUNICATION. .............................................................................................................................. 4-6E. E MPLOYER/E MPLOYEE R ESPONSIBILITIES ................................................................................................... 4-6 II. SERIOUS VIOLATIONS. .................................................................................... 4-8A.S ECTION 17(K). ......................................................................................................................... 4-8B.E STABLISHING S ERIOUS V IOLATIONS ............................................................................................................ 4-8C. F OUR S TEPS TO BE D OCUMENTED. ................................................................................................................... 4-8 III. GENERAL DUTY REQUIREMENTS ............................................................. 4-14A.E VALUATION OF G ENERAL D UTY R EQUIREMENTS ................................................................................. 4-14B.E LEMENTS OF A G ENERAL D UTY R EQUIREMENT V IOLATION.............................................................. 4-14C. U SE OF THE G ENERAL D UTY C LAUSE ........................................................................................................ 4-23D.L IMITATIONS OF U SE OF THE G ENERAL D UTY C LAUSE. ..............................................................E.C LASSIFICATION OF V IOLATIONS C ITED U NDER THE G ENERAL D UTY C LAUSE. ..................F. P ROCEDURES FOR I MPLEMENTATION OF S ECTION 5(A)(1) E NFORCEMENT ............................ 4-25 4-27 4-27IV.OTHER-THAN-SERIOUS VIOLATIONS ............................................... 4-28 V.WILLFUL VIOLATIONS. ......................................................................... 4-28A.I NTENTIONAL D ISREGARD V IOLATIONS. ..........................................................................................4-28B.P LAIN I NDIFFERENCE V IOLATIONS. ...................................................................................................4-29 VI. CRIMINAL/WILLFUL VIOLATIONS. ................................................... 4-30A.A REA D IRECTOR C OORDINATION ....................................................................................................... 4-31B.C RITERIA FOR I NVESTIGATING P OSSIBLE C RIMINAL/W ILLFUL V IOLATIONS ........................ 4-31C. W ILLFUL V IOLATIONS R ELATED TO A F ATALITY .......................................................................... 4-32 VII. REPEATED VIOLATIONS. ...................................................................... 4-32A.F EDERAL AND S TATE P LAN V IOLATIONS. ........................................................................................4-32B.I DENTICAL S TANDARDS. .......................................................................................................................4-32C.D IFFERENT S TANDARDS. .......................................................................................................................4-33D.O BTAINING I NSPECTION H ISTORY. .....................................................................................................4-33E.T IME L IMITATIONS..................................................................................................................................4-34F.R EPEATED V. F AILURE TO A BATE....................................................................................................... 4-34G. A REA D IRECTOR R ESPONSIBILITIES. .............................................................................. 4-35 VIII. DE MINIMIS CONDITIONS. ................................................................... 4-36A.C RITERIA ................................................................................................................................................... 4-36B.P ROFESSIONAL J UDGMENT. ..................................................................................................................4-37C. A REA D IRECTOR R ESPONSIBILITIES. .............................................................................. 4-37 IX. CITING IN THE ALTERNATIVE ............................................................ 4-37 X. COMBINING AND GROUPING VIOLATIONS. ................................... 4-37A.C OMBINING. ..............................................................................................................................................4-37B.G ROUPING. ................................................................................................................................................4-38C. W HEN N OT TO G ROUP OR C OMBINE. ................................................................................................4-38 XI. HEALTH STANDARD VIOLATIONS ....................................................... 4-39A.C ITATION OF V ENTILATION S TANDARDS ......................................................................................... 4-39B.V IOLATIONS OF THE N OISE S TANDARD. ...........................................................................................4-40 XII. VIOLATIONS OF THE RESPIRATORY PROTECTION STANDARD(§1910.134). ....................................................................................................... XIII. VIOLATIONS OF AIR CONTAMINANT STANDARDS (§1910.1000) ... 4-43 4-43A.R EQUIREMENTS UNDER THE STANDARD: .................................................................................................. 4-43B.C LASSIFICATION OF V IOLATIONS OF A IR C ONTAMINANT S TANDARDS. ......................................... 4-43 XIV. CITING IMPROPER PERSONAL HYGIENE PRACTICES. ................... 4-45A.I NGESTION H AZARDS. .................................................................................................................................... 4-45B.A BSORPTION H AZARDS. ................................................................................................................................ 4-46C.W IPE S AMPLING. ............................................................................................................................................. 4-46D.C ITATION P OLICY ............................................................................................................................................ 4-46 XV. BIOLOGICAL MONITORING. ...................................................................... 4-47CHAPTER 5CASE FILE PREPARATION AND DOCUMENTATIONI.INTRODUCTION ............................................................................................... 5-1 II.INSPECTION CONDUCTED, CITATIONS BEING ISSUED. .................... 5-1A.OSHA-1 ................................................................................................................................... 5-1B.OSHA-1A. ............................................................................................................................... 5-1C. OSHA-1B. ................................................................................................................................ 5-2 III.INSPECTION CONDUCTED BUT NO CITATIONS ISSUED .................... 5-5 IV.NO INSPECTION ............................................................................................... 5-5 V. HEALTH INSPECTIONS. ................................................................................. 5-6A.D OCUMENT P OTENTIAL E XPOSURE. ............................................................................................................... 5-6B.E MPLOYER’S O CCUPATIONAL S AFETY AND H EALTH S YSTEM. ............................................................. 5-6 VI. AFFIRMATIVE DEFENSES............................................................................. 5-8A.B URDEN OF P ROOF. .............................................................................................................................................. 5-8B.E XPLANATIONS. ..................................................................................................................................................... 5-8 VII. INTERVIEW STATEMENTS. ........................................................................ 5-10A.G ENERALLY. ......................................................................................................................................................... 5-10B.CSHO S SHALL OBTAIN WRITTEN STATEMENTS WHEN: .......................................................................... 5-10C.L ANGUAGE AND W ORDING OF S TATEMENT. ............................................................................................. 5-11D.R EFUSAL TO S IGN S TATEMENT ...................................................................................................................... 5-11E.V IDEO AND A UDIOTAPED S TATEMENTS. ..................................................................................................... 5-11F.A DMINISTRATIVE D EPOSITIONS. .............................................................................................5-11 VIII. PAPERWORK AND WRITTEN PROGRAM REQUIREMENTS. .......... 5-12 IX.GUIDELINES FOR CASE FILE DOCUMENTATION FOR USE WITH VIDEOTAPES AND AUDIOTAPES .............................................................. 5-12 X.CASE FILE ACTIVITY DIARY SHEET. ..................................................... 5-12 XI. CITATIONS. ..................................................................................................... 5-12A.S TATUTE OF L IMITATIONS. .............................................................................................................................. 5-13B.I SSUING C ITATIONS. ........................................................................................................................................... 5-13C.A MENDING/W ITHDRAWING C ITATIONS AND N OTIFICATION OF P ENALTIES. .................................. 5-13D.P ROCEDURES FOR A MENDING OR W ITHDRAWING C ITATIONS ............................................................ 5-14 XII. INSPECTION RECORDS. ............................................................................... 5-15A.G ENERALLY. ......................................................................................................................................................... 5-15B.R ELEASE OF I NSPECTION I NFORMATION ..................................................................................................... 5-15C. C LASSIFIED AND T RADE S ECRET I NFORMATION ...................................................................................... 5-16。
KNX电源说明书

Product and Applications DescriptionThe Switch-/Dimming Actuator is a KNX device for control-ling up to one group (channels) of lamps via theDC 0/1 -10 V control terminal of dimmable electronic ballasts(ECGs). In addition there is a switching contact for directswitching on/off of the connected lamps.The device is installed into or attached to a 4 x 4 inch junc-tion box. The bus is connected via a bus terminal block. Theactuator electronics are supplied via the bus voltage.The channel of the Switch-/Dimming Actuator can controlseveral dimmable electronic ballasts. Their number is limitedby the switching capacity and by the control power. If theon/off function is not used via the switching contact of theSwitch-/Dimming Actuator, the number of controllable ECGsis only dependent on the load of the DC 1-10 V control volt-age. This might allow controlling a larger number of ECGs(see Technical Specifications below).Various functions can be configured such as for switchingon/off lamps, dimming up / down or setting a particulardimming level.With the ETS (Engineering Tool Software) the applicationprogram is selected, its parameters and addresses are as-signed appropriately and downloaded into theSwitch-/Dimming Actuator.Amongst others, the application program includes an op-tional counter for switching cycles and operating hours withthreshold monitoring for each output and an integrated 8-bitscene control for incorporating the output into up to 8scenes.Each output of the actuator may be set to one of the follow-ing operating modes:- Normal operation- Timer operationBuilding sThe buildinswitching thswitches anbeen commApplicatiThe device n“07 B0 A1P.T.O.ng site functionuilding site function provided ex-factory enablesing the building site lighting on and off via bus walles and actuators, even if these devices have not yetommissioned with ETS.lication Programvice needs the application programA1Dimmer 983B01”.L1V30425161A - DS02instabus ®Technical ManualSwitch-/Dimming Actuator JB 527C235WG1 527-4CB23April 2017 / Page 2Location and Function of the Interface ElementsA4A5A6A7A1A2A7A3A3A7A8A9A11A10A1Type label (with space for physical address of the ac-tuator)A2Identification number of the device A3Protective lid over bus connectionA4Bus connection terminal block for single core conduc-tors with 0.6...0.8 mm ØA5LED for indicating normal operating mode (LED off) oraddressing mode (LED on); returns to normal operating mode automatically after receiving the physical address A6Learning button for switching between normal operat-ing mode and addressing mode and for receiving the physical address A71/2 inch screw nut A8Wire (red) Load A (AWG # 12)A9Wire (black) Line (Hot) (AWG # 12)A10Wire (grey) DIM Common (AWG # 18)A11Wire (purple) DIM A (AWG # 18)Dimension DiagramDimensions in mm (inch)(2.76)(2.76)(3.54)(1.76).B1B4B2B1B3B1B4B2B3B14” x 4” Junction Box B2DeviceB3Bus connection pins of the module for connection of the bus terminal block for single core conductors with 0.6…0.8 mm ØB41/2 inch screw nutMounting and Dismounting∂Mounting of a JB module:Option 1 (mounting inside a J-Box)- Insert the thread of the JB module (B2) into the 1/2 inch knockout between two adjacent J-Boxes (B1)- Fasten the JB module (B2) with the 1/2 inch thread nut (B4)- Remove the protective lid (B3) and connect the bus wire to the bus terminal block (A4)- Connect the wires from the device to the field wires using wire nuts (not provided in package)Option 2 (mounting outside of a J-Box)- Insert the thread of the JB module (B2) into the 1/2 inch knockout of the J-Box (B1)- Fasten the JB module (B2) with the 1/2 inch thread nut (B4)to the J-Box (B1)- Connect the bus wire to the bus terminal block under the protective cover (B3)- Connect the wires from the device to the field wires using wire nuts (not provided in package)∂Assignment of the Physical Address:- A short push (< 2 s) of learning button (A6) enables the ad-dressing mode, which is indicated when the LED is continu-ously on (A5). The device returns to normal operating mode (LED Off) automatically after receiving the physical address or if the learning button is pushed again.- A very long push (> 20 s) of the learning button resets the device to factory settings. This is indicated by constant flash-ing for 8 seconds.- A long push (> 5 s up to 20 s) of the learning button ena-bles the Connection Test for commissioning with Desigo.This mode can be disabled by a short push any time.- Install the protective lid (B3) and fasten with screws (pro-vided in package)∂Dismounting a JB module:- Disconnect power to the module- Remove the wire nuts and bus connection- Unfasten the 1/2 inch thread nut (B4) connecting the JB module (B2) to the J-Box (B1)- Remove the JB module (B2) from the J-Box (B1)D2.4WiringBus connectionSlipping off/on bus connection blocksThe bus connection block consists of two components (C2.1and C2.2) with four terminal contacts each. Take care not to damage the two test sockets (C2.3) by accidentally connect-ing them to the bus cable or with the screw driver (e.g.when attempting to unplug the bus connection block).Slipping off bus connection blocks- Carefully put the screw driver to the wire insertion slit of the bus connection block’s grey component (C2.2)and- pull the bus connection block (C2) from the module.NoteDon’t try to remove the bus connection block from the bot-tom side. There is a risk of shorting-out the device!Slipping on bus connection blocks- Slip the bus connection block (C2) onto the guide slot of the module and- press the bus connection block (C2) down to the stop.Connecting and Disconnecting bus cables Connecting bus cables- The bus connection block (D2) can be used with single core conductors Ø 0.6…0.8 mm.- Remove approx. 5 mm of insulation from the conductor (D1) and plug it into the bus connection block (D2)(red = +, grey = -)Disconnecting bus cables- Unplug the bus connection block (D2) and remove the bus cable conductor (D1) while simultaneously wiggling it.Connecting mains and load circuit:Connect wires-Connect wire leads using wire nuts.。
e英语教程3课后答案
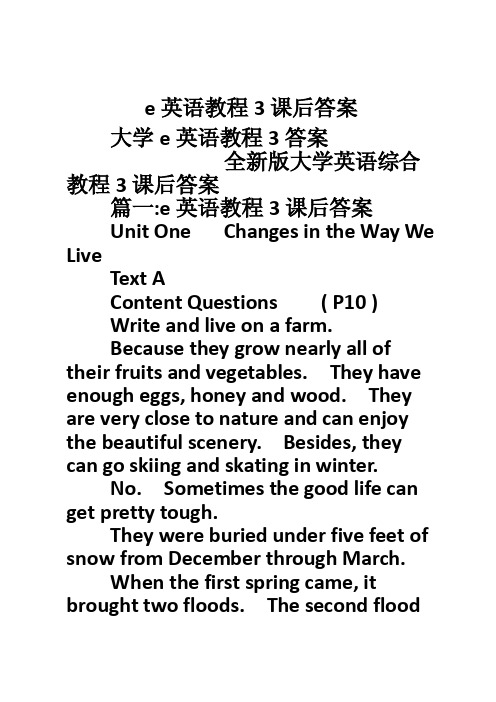
e英语教程3课后答案大学e英语教程3答案全新版大学英语综合教程3课后答案篇一:e英语教程3课后答案Unit One Changes in the Way We LiveText AContent Questions ( P10 )Write and live on a farm.Because they grow nearly all of their fruits and vegetables. They have enough eggs, honey and wood. They are very close to nature and can enjoy the beautiful scenery. Besides, they can go skiing and skating in winter.No. Sometimes the good life can get pretty tough.They were buried under five feet of snow from December through March.When the first spring came, it brought two floods. The second floodrefers to the good harvest in the growing season.He decided to quit his job and start to freelance.He has to crawl into black bear dens for “Sports Illustrated”, hitch up dogsled racing teams for “Smithsonian”magazine, check out the Lake Champlain “monster”for “Science Digest”, and canoe through the Boundary Waters Wilderness area of Minnesota for “Destinations”.As for insurance, they have only bought a poor man‟s major-medical policy and the policy on their two cars.They cut back their expenses without appreciably lowering their standard of living. For example, they patronize local restaurants instead of more expensive places in the city. They still attend the opera and ballet but only a few times a year. They eat less meat,drink cheaper wine and see fewer movies.A tolerance for solitude and lots of energy.They will leave with a feeling of sorrow but also with a sense of pride at what they have been able to accomplish.They chose to live in the country because they want to improve the quality of their lives. Yes, they have finally realized their dreams.Text Organization ( P11 )Part One (paragraphs 1—3) The writer views his life in the country as a self-reliant and satisfying one.Part Two (paragraphs 4—7 ) Life in the country is good yet sometimes very hard.Part Three (paragraphs 8—11) After quitting his job, the writer‟s income was reduced, but he and his family were able to manage to get by.Part Four (paragraphs 12—15 ) A tolerance for solitude and a lot of energy have made it possible for the family to enjoy their life in the country.Happy Moments and Events1) growing nearly all their fruits and vegetables2) canoeing, picnicking, long bicycle rides, etc.3) keeping warm inside the house in winter4) writing freelance articles5) earning enough money while maintaining a happy family life Hardships1) working hard both in winter and in summer2) harsh environment and weather condition3) anxious moments after the writer quit his job4) cutting back on dailyexpenses5) solitudeVocabulary1. Fill in the gaps with words or phrases given in the box. ( P15 )1) on balance2) resist 3) haul4) wicked5) illustrated 6) budget 7) lowering 8) boundary9) involved10)economic 11) blasting 12) just about2. Now use the verb in brackets to form an appropriate phrasal verb you have learned and complete the sentence with it. ( P16 )1) cut back / down2)pick up3)get by4) get through5)face up to6)turn in7)making up for8)think up3. Rewrite each sentence with the word or phrase in brackets, keeping the same meaning. (P17 )1) pursued his mathematical studies and taught himself astronomy.2) often generate misleading thoughts.3) attach great importance to combining theory with practice in our work.4) be suspected of doing everything for money.5) before he gets through life.4. Complete the sentences, using the words or phrases in brackets ( P17 )1. their indoor a profitto invest in2. device the improvement on a global scale3. stackedtemptationnever dined outConfusable Use ( P18 )househomehome familyhouseholddoubtsuspecteddoubtedsuspectedsuspectWord Formation ( P19 )1) rise 2) final3) regular 4) cash5) hows and whys6) upped 7) yellowed 8) bottled 9) lower10) searchCloze1. Text-related ( P20 )1) gets by2) temptation 3) get through4) improvement 5) aside from 6) suspect7) supplement 8) profit 9) stacking2. Theme-related ( P21 )1) replaced 2) consider 3) quit4) world 5) tough6) fuels7) provide 8) luxuries 9) balance10) idealTranslation1. Translate the sentences into English ( P21 )1) We have a problem with the computer system, but I think it isfairly minor.2) My father died when I was too young to live on my own. The people of my hometown took over responsibility for my upbringing at that point.3) the toys have to meet strict safety requirements before they can be sold to children.{e英语教程3课后答案}.4) Radio and television have supplemented rather than replaced the newspaper as carriers of new and opinion.5) When it comes to this magazine, it is a digest of articles from many newspapers and magazines around the world.2. Translate the passage into English ( P21 )A decade ago, Nancy did what so many Americans dream about. Shequit an executive position and opened a household device store in her neighborhood. People like Nancy made the decision primarily for the improvement in the quality of their lives.But, to run a business on a small scale is by no means an easy job. Without her steady income, Nancy had to cut back on her daily expenses. Sometimes she did not even have the money to pay the premiums for the various kinds of insurance she needed.Fortunately, through her own hard work, she has now got through the most difficult time. She is determined to continue pursuing her vision of a better life.Text B1. Choose the best answer for each of the following. ( P27 )1—6. a c d ba cTranslate into Chinese the underlined sentences in the essay ( P28 ) 什么?你说那听起来不像你府上的生活?其实,不仅仅是你一个人这么想。
三相电源监测传感器系列产品说明书
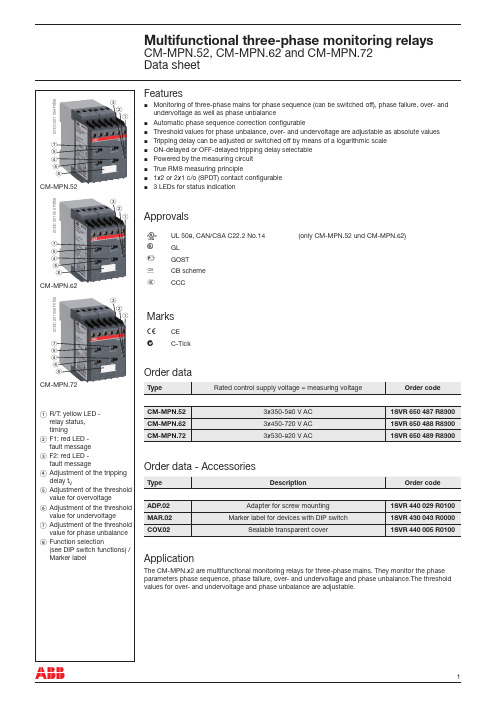
2C D C 251 054 F 0t 08ᕅ ᕄ ᕃᕉᕇᕆ ᕈ ᕊCM-MPN.522C D C 251055 F 0t 08ᕅ ᕄ ᕃᕉᕇᕆ ᕈ ᕊCM-MPN.622C D C 251 056 F 0t08ᕅ ᕄ ᕃᕉᕇᕆ ᕈ ᕊCM-MPN.72Multifunctional three-phase monitoring relaysCM-MPN.52, CM-MPN.62 and CM-MPN.72Data sheetApplicationThe CM-MPN.x2 are multifunctional monitoring relays for three-phase mains. They monitor the phase parameters phase sequence, phase failure, over- and undervoltage and phase unbalance.The threshold values for over- and undervoltage and phase unbalance are adjustable.Order dataOrder data - AccessoriesFeaturesMonitoring of three-phase mains for phase sequence (can be switched off), phase failure, over- andu ndervoltage as well as phase unbalance Automatic phase sequence correction configurableThreshold values for phase unbalance, over- and undervoltage are adjustable as absolute values Tripping delay can be adjusted or switched off by means of a logarithmic scale ON-delayed or OFF-delayed tripping delay selectable Powered by the measuring circuit True RMS measuring principle1x2 or 2x1 c/o (SPDT) contact configurable 3 LEDs for status indicationApprovalsA UL 508, CAN/CSA C22.2 No.14(only CM-MPN.52 und CM-MPN.62)C GLD GOST K CB scheme ECCCMarksa CE bC-TickR/T: yellow LED - relay status, timingF1: red LED - fault message F2: red LED - fault messageAdjustment of the trippingd elay t V Adjustment of the thresholdvalue for overvoltage6 Adjustment of the threshold value for undervoltage7 Adjustment of the threshold value for phase unbalance 8 Function selection(see DIP switch functions) / Marker labelOperating modeConfiguration of the devices is made by means of setting elements accessible on the front of the unit and signalling is made by means of front-face LEDs.Adjustment potentiometerThreshold valuesBy means of three separate potentiometers with direct reading scales, the threshold values for over- and undervoltage as well as for phase unbalance can be a djusted within the measuring range.Tripping delay t VThe tripping delay t V can be adjusted within a range of 0.1-30 s by means of a potentiometer with logaritmic scale. By turning to the left stop, the tripping delay can be switched off.DIP switches2C D C 252 041 F 0b 08LEDs1) Possible misadjustments of the front-face operating controls:Overlapping of the threshold values: An overlapping of the threshold values is given, if the threshold value foro vervoltage is set to a smaller value than the threshold value for u ndervoltage.DIP switch 3 = OFF and DIP switch 4 = ON: Automatic phase sequence c orrection is activated and selected operating mode is 1x2 c/o (SPDT) contactsDIP switch 2 and 4 = ON: Phase sequence detection is deactivated and the automatic phase sequence correction is activedFunction diagram legendG Control supply voltage not applied / Output contact open / LED off B Control supply voltage applied / Output contact closed / LED glowingPhase sequence and phase failure monitoringApplying control supply voltage begins the fixed start-up delay t S . When t S is complete and all phases are present with correct voltage, the output relays energize and the yellow LED R/T glows. Phase sequence monitoringIf phase sequence monitoring is activated, the output relays de- e nergize as soon as a phase sequence error occurs. The fault is displayed by alternated flashing of the LEDs F1 and F2. The output relays re- energize automatically as soon as the phase sequence is correct again. Phase failure monitoringThe output relays de-energize instantaneous if a phase failure o ccurs. The fault is indicated by lightning of LED F1 and flashing of LED F2. The output relays re-energize automatically as soon as the voltage returns to the tolerance range.25-2625-28L1, L2, L315-1615-182C D C 252 094 F 0207F1: red LED F2: red LED R/T: yellow LEDMeasuring valuet s = start-up delay fixed 200 msFunction descriptions/diagramsOver- and undervoltage monitoring 1x2 c/o (SPDT) contactsjApplying control supply voltage begins the fixed start-up delay t S . When t S is complete and all phases are present with correct voltage and with correct phase sequence, the output relays energize and the yellow LED R/T glows.Type of tripping delay = ON-delay AIf the voltage to be monitored exceeds or falls below the set threshold value, the output relays de-energize after the set tripping delay t V is complete. The LED R/T flashes during timing and turns off as soon as the output relays de-energize.The output relays re-energize automatically as soon as the voltage returns to the tolerance range, taking into account a fixed hysteresis of 5 %. The LED R/T glows.L1, L2, L315-1615-18> U > U - 5 %< U + 5 %< U25-2625-282C D C 252 090 F 0207F1: red LED F2: red LED R/T: yellow LEDMeasuring valuet s = start-up delay fixed 200 ms t v = adjustable tripping delayType of tripping delay = OFF-delay BIf the voltage to be monitored exceeds or falls below the set threshold value, the output relays de-energize instantaneously and the LED R/T turns off.As soon as the voltage returns to the t olerance range, taking into account a fixed hysteresis of 5 %, the output relays re-energize a utomatically after the set tripping delay t V is complete. The LED R/T flashes d uring timing and turns steady when timing is c omplete.25-2625-28L1, L2, L315-1615-18> U> U - 5 %< U + 5 %< U2C D C 252 091 F 0207F1: red LED F2: red LED R/T: yellow LEDMeasuring valuet s = start-up delay fixed 200 ms t v = adjustable tripping delayOver- and undervoltage monitoring 2x1 c/o (SPDT) contactiApplying control supply voltage begins the fixed start-up delay t S . When t S is complete and all phases are present with correct v oltage and with correct phase sequence, the output relays energize. The yellow LED R/T glows as long as at least one output relay is e nergized.Type of tripping delay = ON-delay AIf the voltage to be monitored exceeds or falls below the set threshold value, output relay R1 (overvoltage) or output relay R2 (undervoltage) de-energizes after the set tripping delay t V is c omplete. The LED R/T flashes during timing.The corresponding output relay re-energizes automatically as soon as the voltage returns to the tolerance range, taking into a ccount a fixed hysteresis of 5 %.L1, L2, L315-1615-1825-2625-28> U> U - 5 %< U + 5 %< U2C D C 252 006 F 0207F1: red LED F2: red LED R/T: yellow LEDMeasuring valuet s = start-up delay fixed 200 ms t v = adjustable tripping delayType of tripping delay = OFF-delay BIf the voltage to be monitored exceeds or falls below the set threshold value, output relay R1 (overvoltage) or output relay R2 (undervoltage) de-energizes instantaneously.As soon as the voltage returns to the tolerance range, taking into a ccount a fixed hysteresis of 5 %, the corresponding output relay re-energizes automatically after the set tripping delay t V is complete. The LED R/T flashes during timing.L1, L2, L315-1615-1825-2625-28> U > U - 5 %< U + 5 %< U2C D C 252 007 F 0207F1: red LED F2: red LED R/T: yellow LEDMeasuring valuet s = start-up delay fixed 200 ms t v = adjustable tripping delayPhase unbalance monitoringApplying control supply voltage begins the fixed start-up delay t S . When t S is complete and all phases are present with correct voltage and with correct phase sequence, the output relays energize and the yellow LED R/T glows.Type of tripping delay = ON-delay AIf the voltage to be monitored exceeds or falls below the set phase unbalance threshold value, the output relays de-energize after the set tripping delay t V is c omplete. The LED R/T flashes during timing and turns off as soon as the output relays de-energize.The output relays re-energize automatically as soon as the voltage r eturns to the tolerance range, taking into account a fixed hysteresis of 20 %. The LED R/T glows.L1, L2, L315-1615-1825-2625-282C D C 252 092 F 0207F1: red LED F2: red LED R/T: yellow LEDMeasuring valueUnbalanceUnbalance - HysteresisUnbalance + HysteresisUnbalancet s = start-up delay fixed 200 ms t v = adjustable tripping delayType of tripping delay = OFF-delay BIf the voltage to be monitored exceeds or falls below the set phase unbalance threshold value, the output relays de-energize i nstantaneously and the LED R/T turns off.As soon as the voltage r eturns to the t olerance range, taking into account a fixed hysteresis of 20 %, the output relays re-energize automatically a fter the set tripping delay t V is c omplete. The LED R/T flashes d uring timing and turns steady when timing is c omplete.25-2625-28L1, L2, L315-1615-182C D C 252 093 F 0207F1: red LED F2: red LED R/T: yellow LEDMeasuring valueUnbalanceUnbalance - HysteresisUnbalance + HysteresisUnbalancet s = start-up delay fixed 200 ms t v = adjustable tripping delayAutomatic phase sequence correctionThis function can be selected only if phase sequence monitoring is activated k (DIP switch 3 = ON) and operating mode 2x1 c/o (SPDT) contact j is selected (DIP switch 2 = OFF).Applying control supply voltage begins the fixed start-up delay t S1. When t S1 is complete and all phases are present with correct voltage, output relay R1 energizes. Output relay R2 energizes when the fixed start-up delay t S2 is complete and all phases are present with correct phase sequence. Output relay R2 remainsde-energized if the phase sequence is incorrect.If the voltage to be monitored exceeds or falls below the set threshold values for phase unbalance, over- or undervoltage or if a phase failure occurs, output relay R1 de-energizes and the LEDs F1 and F2 indicate the fault.Output relay R2 is responsive only to a false phase sequence. In conjunction with a reversing contactor combination, this enables an automatic correction of the rotation direction. See circuit diagrams.L1, L2, L315-1615-1825-2625-282C D C 252 085 F 0207F1: red LED F2: red LED R/T: yellow LEDMeasuring valuet S1 = start-up delay of R1 fixed 250 ms t S2 = start-up delay of R2 fixed 200 ms2C D C 252 086 F 0b 072C D C 252 087 F 0b 07Control circuit diagram (K1 = CM-MPN.x2)Power circuit diagramConnection diagramL1L228261525L3L3151618262825L2L116182C D C 252 038 F 0b 08L1, L2, L3 Control supply voltage = measuring voltage 15-16/18 Output contacts -25-26/28 closed-circuit principleCM-MPN.52, CM-MPN.62, CM-MPN.72Data at T a = 25 °C and rated values, unless otherwise indicatedData at T a = 25 °C and rated values, unless otherwise indicated1)Closed-circuit principle: Output relay(s) de-energize(s) if measured value exceeds or falls below the adjusted threshold value1112Technical diagramsLoad limit curvesAC load (resistive)2C D C 252 194 F 0205DC load (resistive)2C D C 252 193F 0205Derating factor Fat inductive AC load2C D C 252 192 F 0205Switching current [A]S w i t c h i n g c y c l e s2C D C 252 148 F 0206Dimensionsin mm2C D C 252 032 F 000313Further documentationYou can find the documentation online at /lowvoltage R Control Products R Electronic Relays and ControlsDimensions - Accessoriesin mm2C D C 252 009 F 00102C D C 252 010 F 0010ADP .02 - Adapter for screw mountingMAR.02 - Marker label2C D C 252 009 F 0010COV .02 - Sealable transparent coverABB STOTZ-KONTAKT GmbHP. O. Box 10 16 8069006 Heidelberg, Germany Phone: +49 (0) 6221 7 01-0Fax: +49 (0) 6221 7 01-13 25E-mail:*****************.comYou can find the address of your local sales organisation on theABB home page/contacts-> Low Voltage Products and Systems Contact usNote:We reserve the right to make technical changes or modify the contents of this document without prior notice. With regard to purchase orders, the agreed particulars shall prevail. ABB AG does not accept any responsibility whatsoever for potential errors or possible lack of information in this document.We reserve all rights in this document and in the subject matter and illustrations contained therein. Any reproduction, disclosure to third parties or utilization of its contents – in whole or in parts – is forbidden without prior written consent of ABB AG. Copyright© 2010 ABBAll rights reserved D o c u m e n t n u m b e r . 2 C D C 1 1 2 1 2 8 D 0 2 0 1 ( 0 7 / 1 0 )。
- 1、下载文档前请自行甄别文档内容的完整性,平台不提供额外的编辑、内容补充、找答案等附加服务。
- 2、"仅部分预览"的文档,不可在线预览部分如存在完整性等问题,可反馈申请退款(可完整预览的文档不适用该条件!)。
- 3、如文档侵犯您的权益,请联系客服反馈,我们会尽快为您处理(人工客服工作时间:9:00-18:30)。
在线代理|网页代理|代理网页|Exam View er - E Sw itching Chapter 3 - CCNA E xploration: LAN Sw itching and Wireless (Version 4.0)Below y ou will f ind the assessment items as presented on the exam as well as the scoring rules associated with the item.Cisco Networking A cademy content is copyrighted and the unauthorized posting, distribution or sharing of this exam content is prohibited. 1Which two statements describe the benef its of VLANs? (Choose two.)VLANs improv e network perf ormance by regulating f low control and window size.VLANs enable switches to route packets to remote networks via VLAN ID f iltering.VLANs reduce network cost by reducing the number of phy sical ports required on switches.VLANs improv e network security by isolating users that hav e access to sensitiv e data and applications.VLANs div ide a network into smaller logical networks, resulting in lower susceptibility to broadcast storms.2What are two characteristics of VLAN1 in a def ault switch conf iguration? (Choose two.)VLAN1 should renamed.VLAN 1 is the management VLAN.All switch ports are members of VLAN1.Only switch port 0/1 is assigned to VLAN1.Links between switches must be members of VLAN1.3Ref er to the exhibit. SW1 and SW2 are new switches being installed in the topology shown in the exhibit. Interf ace Fa0/1 on s witch SW1 has been conf igured with trunk mode “on”. Which statement is true ab out f orming a trunk link between the switches SW1 and SW2?Interf ace Fa0/2 on switch SW2 will negotiate to become a trunk link if it supports DTP.Interf ace Fa0/2 on switch SW2 can only become a trunk link if statically conf igured as a trunk.Interf ace Fa0/1 conv erts the neighboring link on the adjacent switch into a trunk link if the neighboring interf ace is conf ig ured in nonegotiate mode.Interf ace Fa0/1 conv erts the neighboring link on the adjacent switch into a trunk link automatically with no consideration of the conf iguration on the neighboring interf ace.4Ref er to the exhibit. Computer 1 sends a f rame to computer 4. On which links along the path between computer 1 and computer 4 will a VLAN ID tag be included with the f rame?AA, BA, B, D, GA, D, FC, EC, E, F5The network administrator wants to separate hosts in Building A into two VLANs numbered 20 and 30. Which two statements are true concerning VLAN conf iguration? (Choose two.)The VLANs may be named.VLAN inf ormation is sav ed in the startup conf iguration.Non-def ault VLANs created manually must use the extended range VLAN numbers.The network administrator may create the VLANs in either global conf iguration mode or VLAN database mode.Both VLANs may be named BUILDING_A to distinguish them f rom other VLANs in diff erent geographical locations.在线代理|网页代理|代理网页|6Ref er to the exhibit. Which two conclusions can be drawn regarding the switch that produced the output shown? (Choose two.)The network administrator conf igured VLANs 1002-1005.The VLANs are in the activ e state and are in the process of negotiating conf iguration parameters.A FDDI trunk has been conf igured on this switch.The command switchport access vlan 20 was entered in interf ace conf iguration mode f or Fast Ethernet interf ace 0/1. Dev ices attached to ports f a0/5 through f a0/8 cannot communicate with dev ices attached to ports f a0/9 through f a0/12 without the use of a Lay er 3 dev ice.7What happens to the member ports of a VLAN when the VLAN is deleted?The ports cannot communicate with other ports.The ports def ault back to the management VLAN.The ports automatically become a part of VLAN1.The ports remain a part of that VLAN until the switch is rebooted. They then become members of the management VLAN.8A network administrator is remov ing sev eral VLANs from a switch. When the administrator enters the no vlan 1 command, an error is receiv ed. Why did this command generate an error?VLAN 1 can nev er be deleted.VLAN 1 can only be deleted by deleting the vlan.dat f ile.VLAN 1 can not be deleted until all ports hav e been remov ed f rom it.VLAN 1 can not be deleted until another VLAN has been assigned its responsibilities.9What is the eff ect of the switchport mode dynamic desirable command?DTP cannot negotiate the trunk since the nativ e VLAN is not the def ault VLAN.The remote connected interf ace cannot negotiate a trunk unless it is also conf igured as dy namic desirable.The connected dev ices dy namically determine when data f or multiple VLANs must be transmitted across the link and bring thetrunk up as needed.A trunk link is f ormed if the remote connected dev ice is conf igured with t he switchport mode dynamic auto or switchportmode trunk commands.10在线代理|网页代理|代理网页|Ref er to the exhibit. The exhibited conf igurations do not allow the switches to f orm a trunk. What is the most likely cause of this problem?Cisco switches only support the ISL trunking protocol.The trunk cannot be negotiated with both ends set to auto.By def ault, Switch1 will only allow VLAN 5 across the link.A common nativ e VLAN should hav e been conf igured on the switches.11Switch port f a0/1 was manually conf igured as a trunk, but now it will be used to connect a host to the network. How should the network administrator reconf igure switch port Fa0/1?Disable DTP.Delete any VLANs currently being trunked through port Fa0/1.Administrativ ely shut down and re-enable the interf ace to return it to def ault.Enter the switchport mode access command in interf ace conf iguration mode.在线代理|网页代理|代理网页|在线代理|网页代理|代理网页|12Ref er to the exhibit. Computer B is unable to communicate with computer D. What is the most likely cause of this problem?The link between the switches is up but not trunked.VLAN 3 is not an allowed VLAN to enter the trunk between the switches.The router is not properly conf igured to route traff ic between the VLANs.Computer D does not hav e a proper address f or the VLAN 3 address space.13在线代理|网页代理|代理网页|Ref er to the exhibit. The network administrator has just added VLAN 50 to Switch1 and Switch2 and assigned hosts on the IP ad dresses of the VLAN in the 10.1.50.0/24 subnet range. Computer A can communicate with computer B, but not with c omputer C or computer D. What is the most likely cause of this problem?There is a nativ e VLAN mismatch.The link between Switch1 and Switch2 is up but not trunked.The router is not properly conf igured f or inter-VLAN routing.VLAN 50 is not allowed to entering the trunk between Switch1 and Switch2.14Ref er to the exhibit. Which statement is true concerning interf ace Fa0/5?The def ault nativ e VLAN is being used.The trunking mode is set to auto.Trunking can occur with non-Cisco switches.在线代理|网页代理|代理网页|VLAN inf ormation about the interf ace encapsulates the Ethernet f rames.15What statements describe how hosts on VLANs communicate?Hosts on diff erent VLANs use VTP to negotiate a trunk.Hosts on diff erent VLANs communicate through routers.Hosts on diff erent VLANs should be in the same IP network.Hosts on diff erent VLANs examine VLAN ID in the frame tagging to determine if the frame f or their network.16Ref er to the exhibit. How f ar is a broadcast f rame that is sent by computer A propagated in the LAN domain?none of the computers will receiv e the broadcast f ramecomputer A, computer B, computer Ccomputer A, computer D, computer Gcomputer B, computer Ccomputer D, computer Gcomputer A, computer B, computer C, computer D, computer E, computer F, computer G, computer H, computer I17What is a valid consideration f or planning VLAN traff ic across multiple switches?Conf iguring interswitch connections as trunks will cause all hosts on any VLAN to receiv e broadcasts f rom the other VLANs.A trunk connection is aff ected by broadcast storms on any particular VLAN that is carried by that trunk.Restricting trunk connections between switches to a single VLAN will improv e eff iciency of port usage.Carry ing all required VLANs on a single access port will ensure proper traff ic separation.18What statement about the 802.1q trunking protocol is true?802.1q is Cisco proprietary.802.1q f rames are mapped to VLANs by MAC address.802.1q does NOT require the FCS of the original f rame to be recalculated.802.1q will not perf orm operations on f rames that are forwarded out access ports.19What switch port modes will allow a switch to successf ully f orm a trunking link if the neighboring switch port is in "dy namic desirable"mode?dy namic desirable modeon or dy namic desirable modeon, auto, or dy namic desirable modeon, auto, dy namic desirable, or nonegotiate mode20在线代理|网页代理|代理网页|Ref er to the exhibit. Company HR is adding PC4, a specialized application workstation, to a new company off ice. The company will adda switch, S3, connected v ia a trunk link to S2, another switch. For security reasons the new PC will reside in the HR VLAN, V LAN 10.The new off ice will use the 172.17.11.0/24 subnet. Af ter installation, users on PC1 are unable to access shares on PC4. What is th e likely cause?The switch to switch connection must be conf igured as an access port to permit access to VLAN 10 on S3.The new PC is on a diff erent subnet so Fa0/2 on S3 must be conf igured as a trunk port.PC4 must use the same subnet as PC1.A single VLAN cannot span multiple switches.21What must the network administrator do to remov e Fast Ethernet port f a0/1 f rom VLAN 2 and assign it to VLAN 3?Enter the no vlan 2 and the vlan 3 commands in global conf iguration mode.Enter the switchport access vlan 3 command in interf ace conf iguration mode.Enter the switchport trunk native vlan 3 command in interf ace conf iguration mode.Enter the no shutdown in interf ace conf iguration mode to return it to the def ault conf iguration and then conf igure the port f orVLAN 3.在线代理|网页代理|代理网页|。