PCA-过程能力(CPK)分析
SPC中有关过程能力的分析机理

说明
1 水平的合格品率为68% 2 水平的合格品率为95.4% 3 水平的合格品率为99.73% 4 水平的合格品率为99.994% 5 水平的合格品率为99.9999% 6 水平的合格品率为100%
值 0.33 0.67 1.0 1.33 1.67 2.0
0.33 0.68 1
1.33
1.67
2.00
短期过程能力:仅由偶 因引起的变异所形成的 过程能力,既是指过程 处于稳定的过程能力, 反映短期变异。此变异 可由控制图的有关参数 估计:
长期过程能力:是指由偶因和异因之和引起的总变 异所形成的过程能力,反映长期变异,也称实绩变 异S。此变异可由控制图的有关参数估计:
1 概念:过程能力指数是衡量过程能力对产品规格
•一般机械能力 •调查的替换
抽样批次
1 2 3 4 5 6 7 8
, •从而K=0,则
,这是“无偏”的情况,即理想状态
。 •当 •恰好位于公差上限或下限时
•从而,K = 1
;
•当 位于公差界限之外时,
。
•此时, ,则
。此时的 Cpk 为“ 0 ”
•即:
•当
时,工序加工过程中的不合格品率
大于或等于50%。对不合格品率这样大的工序,已远
远不能满足加工的质量要求,故认为此时的工序能
0.36 18.92 13.18 9.16 6.28 4.21 2.75 1.40 1.06 0.63 0.36 0.20 0.11 0.06 0.03 0.01 0.01 0.00
0.40 20.19 14.59 10.55 7.53 5.27 3.59 2.39 1.54 0.96 0.59 0.35 0.20 0.11 0.06 0.03 0.02 0.01 0.00
CPK过程能力分析
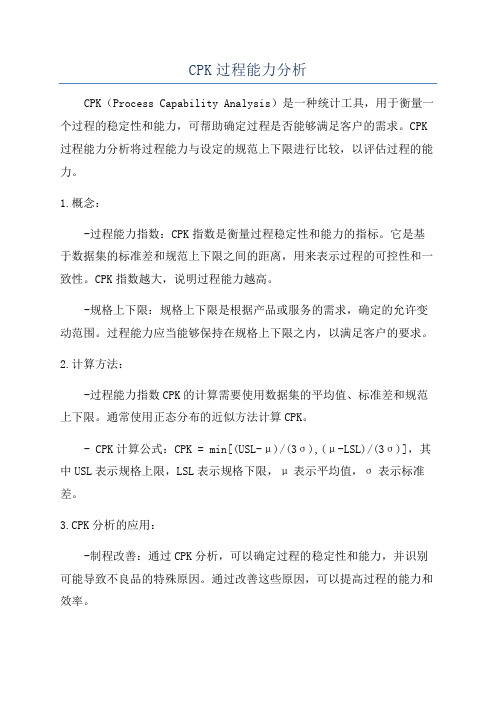
CPK过程能力分析CPK(Process Capability Analysis)是一种统计工具,用于衡量一个过程的稳定性和能力,可帮助确定过程是否能够满足客户的需求。
CPK 过程能力分析将过程能力与设定的规范上下限进行比较,以评估过程的能力。
1.概念:-过程能力指数:CPK指数是衡量过程稳定性和能力的指标。
它是基于数据集的标准差和规范上下限之间的距离,用来表示过程的可控性和一致性。
CPK指数越大,说明过程能力越高。
-规格上下限:规格上下限是根据产品或服务的需求,确定的允许变动范围。
过程能力应当能够保持在规格上下限之内,以满足客户的要求。
2.计算方法:-过程能力指数CPK的计算需要使用数据集的平均值、标准差和规范上下限。
通常使用正态分布的近似方法计算CPK。
- CPK计算公式:CPK = min[(USL-μ)/(3σ),(μ-LSL)/(3σ)],其中USL表示规格上限,LSL表示规格下限,μ表示平均值,σ表示标准差。
3.CPK分析的应用:-制程改善:通过CPK分析,可以确定过程的稳定性和能力,并识别可能导致不良品的特殊原因。
通过改善这些原因,可以提高过程的能力和效率。
-过程控制:CPK过程能力分析可以帮助制定过程控制界限,确保过程稳定,符合规格要求。
通过及时监控过程变异性,并采取控制措施,可以提高过程品质。
-供应商评估:CPK过程能力分析可用于对供应商的能力进行评估。
通过比较供应商的CPK值,可以确定哪些供应商能够满足规格要求,并为采购决策提供依据。
4.CPK分析的局限性:-基于数据的稳定性:CPK分析需要基于大量的数据,来评估过程的稳定性和能力。
如果数据量不足或者不具有代表性,可能会导致CPK值的偏差。
-规格上下限的确定:规格上下限的确定需要考虑产品或服务的需求以及客户的期望。
如果规格上下限不准确或过于宽松,可能会导致对过程能力的误判。
综上所述,CPK过程能力分析是一种重要的统计工具,可以帮助组织评估和改进其过程的稳定性和能力。
CPK(过程能力分析报告方法)
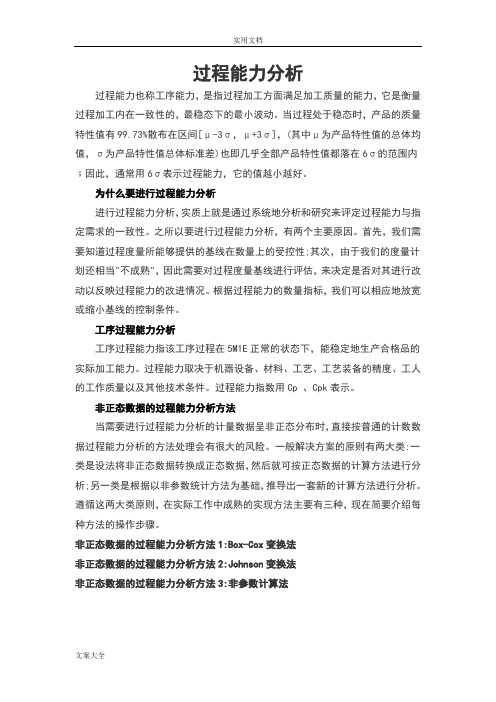
过程能力分析过程能力也称工序能力,是指过程加工方面满足加工质量的能力,它是衡量过程加工内在一致性的,最稳态下的最小波动。
当过程处于稳态时,产品的质量特性值有99.73%散布在区间[μ-3σ,μ+3σ],(其中μ为产品特性值的总体均值,σ为产品特性值总体标准差)也即几乎全部产品特性值都落在6σ的范围内﹔因此,通常用6σ表示过程能力,它的值越小越好。
为什么要进行过程能力分析进行过程能力分析,实质上就是通过系统地分析和研究来评定过程能力与指定需求的一致性。
之所以要进行过程能力分析,有两个主要原因。
首先,我们需要知道过程度量所能够提供的基线在数量上的受控性;其次,由于我们的度量计划还相当"不成熟",因此需要对过程度量基线进行评估,来决定是否对其进行改动以反映过程能力的改进情况。
根据过程能力的数量指标,我们可以相应地放宽或缩小基线的控制条件。
工序过程能力分析工序过程能力指该工序过程在5M1E正常的状态下,能稳定地生产合格品的实际加工能力。
过程能力取决于机器设备、材料、工艺、工艺装备的精度、工人的工作质量以及其他技术条件。
过程能力指数用Cp 、Cpk表示。
非正态数据的过程能力分析方法当需要进行过程能力分析的计量数据呈非正态分布时,直接按普通的计数数据过程能力分析的方法处理会有很大的风险。
一般解决方案的原则有两大类:一类是设法将非正态数据转换成正态数据,然后就可按正态数据的计算方法进行分析;另一类是根据以非参数统计方法为基础,推导出一套新的计算方法进行分析。
遵循这两大类原则,在实际工作中成熟的实现方法主要有三种,现在简要介绍每种方法的操作步骤。
非正态数据的过程能力分析方法1:Box-Cox变换法非正态数据的过程能力分析方法2:Johnson变换法非正态数据的过程能力分析方法3:非参数计算法当第一种、第二种方法无法适用,即均无法找到合适的转换方法时,还有第三种方法可供尝试,即以非参数方法为基数,不需对原始数据做任何转换,直接按以下数学公式就可进行过程能力指数CP和CPK的计算和分析。
过程能力分析CPK
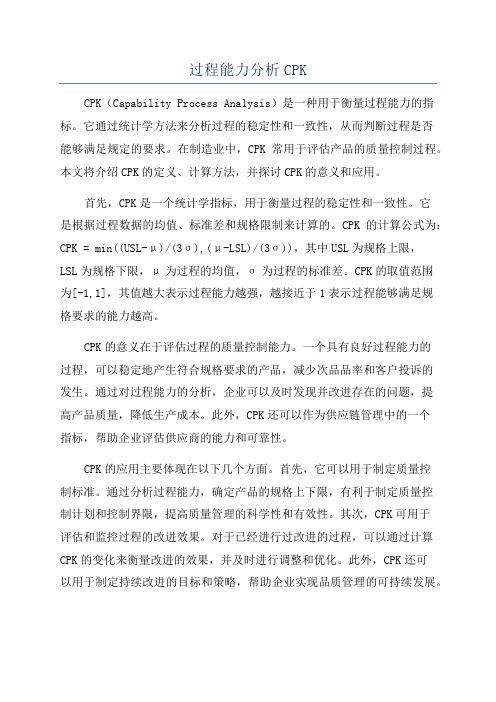
过程能力分析CPKCPK(Capability Process Analysis)是一种用于衡量过程能力的指标。
它通过统计学方法来分析过程的稳定性和一致性,从而判断过程是否能够满足规定的要求。
在制造业中,CPK常用于评估产品的质量控制过程。
本文将介绍CPK的定义、计算方法,并探讨CPK的意义和应用。
首先,CPK是一个统计学指标,用于衡量过程的稳定性和一致性。
它是根据过程数据的均值、标准差和规格限制来计算的。
CPK的计算公式为:CPK = min((USL-μ)/(3σ),(μ-LSL)/(3σ)),其中USL为规格上限,LSL为规格下限,μ为过程的均值,σ为过程的标准差。
CPK的取值范围为[-1,1],其值越大表示过程能力越强,越接近于1表示过程能够满足规格要求的能力越高。
CPK的意义在于评估过程的质量控制能力。
一个具有良好过程能力的过程,可以稳定地产生符合规格要求的产品,减少次品品率和客户投诉的发生。
通过对过程能力的分析,企业可以及时发现并改进存在的问题,提高产品质量,降低生产成本。
此外,CPK还可以作为供应链管理中的一个指标,帮助企业评估供应商的能力和可靠性。
CPK的应用主要体现在以下几个方面。
首先,它可以用于制定质量控制标准。
通过分析过程能力,确定产品的规格上下限,有利于制定质量控制计划和控制界限,提高质量管理的科学性和有效性。
其次,CPK可用于评估和监控过程的改进效果。
对于已经进行过改进的过程,可以通过计算CPK的变化来衡量改进的效果,并及时进行调整和优化。
此外,CPK还可以用于制定持续改进的目标和策略,帮助企业实现品质管理的可持续发展。
在实际应用中,CPK的计算需要大量的数据支撑。
必须收集足够的过程数据,包括过程的样本数据和规格限制,才能准确计算CPK值。
此外,CPK的计算还要求过程数据服从正态分布。
如果过程数据不符合正态分布,可能会导致CPK值的计算误差。
因此,在使用CPK进行过程分析时,需要确保数据收集准确可靠,并对数据是否符合正态分布进行检验。
「cpk」过程能力指数附案例分析和改善措施

「cpk」过程能力指数附案例分析和改善措施第一篇:「cpk」过程能力指数附案例分析和改善措施「CPK」过程能力指数,附案例分析和改善措施过程能力指数(Process capability index,CP或CPK),也译为工序能力指数、工艺能力指数、制程能力指数一、什么是过程能力指数过程能力指数也称工序能力指数,是指工序在一定时间里,处于控制状态(稳定状态)下的实际加工能力。
它是工序固有的能力,或者说它是工序保证质量的能力。
这里所指的工序,是指操作者、机器、原材料、工艺方法和生产环境等五个基本质量因素综合作用的过程,也就是产品质量的生产过程。
产品质量就是工序中的各个质量因素所起作用的综合表现。
对于任何生产过程,产品质量总是分散地存在着。
若工序能力越高,则产品质量特性值的分散就会越小;若工序能力越低,则产品质量特性值的分散就会越大。
那么,应当用一个什么样的量,来描述生产过程所造成的总分散呢?通常,都用6σ(即μ+3σ)来表示工序能力:工序能力是表示生产过程客观存在着分散的一个参数。
但是这个参数能否满足产品的技术要求,仅从它本身还难以看出。
因此,还需要另一个参数来反映工序能力满足产品技术要求(公差、规格等质量标准)的程度。
这个参数就叫做工序能力指数。
它是技术要求和工序能力的比值,即当分布中心与公差中心重合时,工序能力指数记为Cp。
当分布中心与公差中心有偏离时,工序能力指数记为Cpk。
运用工序能力指数,可以帮助我们掌握生产过程的质量水平。
二、过程能力指数的意义制程能力是过程性能的允许最大变化范围与过程的正常偏差的比值。
制程能力研究在於确认这些特性符合规格的程度,以保证制程成品不符规格的不良率在要求的水准之上,作为制程持续改善的依据。
当我们的产品通过了GageR&R的测试之后,我们即可开始Cpk值的测试。
CPK值越大表示品质越佳。
CPK=min ((X-LSL/3s),(USL-X/3s))三、过程能力指数的计算公式CPK= Min[(USL-Mu)/3s,(Mu|Ca|)Cpk是Ca及Cp两者的中和反应,Ca反应的是位置关系(集中趋势),Cp反应的是散布关系(离散趋势)八、过程能力指数的应用1 当选择制程站别Cpk来作管控时,应以成本做考量的首要因素,还有是其品质特性对后制程的影响度。
CPK过程能力分析
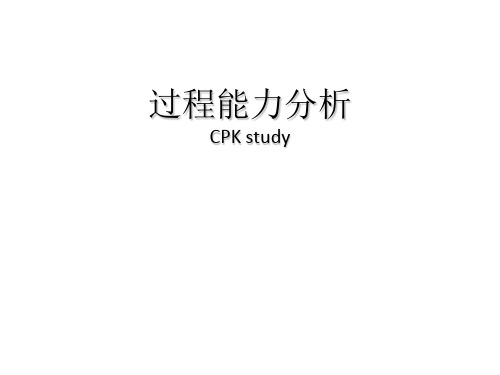
- 名称不同:Cpk是过程能力指数,Ppk是过程性能指数.
- 实施时机不同:Cpk一般是量产时实施,Ppk一般试生产时实施. 我们默认为稳定状态下连续抽样表征了量产的状况,所以新飞通目前 采取了在试产阶段控制Cpk的方式
12
600.4 599.6 600.0 600.8 600.4
13
599.4 599.0 598.4 599.0 599.6
14
598.8 599.2 599.6 598.6 599.8
5
6
598.8 598.8 599.8 599.2 599.4
600.0 600.2 600.2 599.6 599.0
案例-步骤4
用 ppm表示实际DATA脱离规格的程度。
案例-步骤4
只考虑工程的群内变动显示正态分布时,数据表现为 脱离规格的预想 ppm
案例-步骤4
对所有DATA的变动值来显示正态分布时, DATA表现脱离规格的预测 ppm
提高过程能力的思路
常犯的错误或常见问题
✓ 工艺过程不处于稳定状态,有异常发生时进行过程 性能分析
✓ 样本数量太少 ,不具备代表意义
✓ 有明显因为各种特殊原因导致的明显有问题的数 据,没做剔除而保留下来,影响了整体分析的结果
✓ 对计算结果的意义不了解,没有制定很好的改善 措施
回顾与讨论
过程能力分析的前提条件是什么? CP与CPK,PP与PPK之间的区别是什么? CPK与PPK之间的区别是什么? CP>1.67而 CPK<1.0的时候,应该如何处理? CP<1.0的时候,又该如何处理
CPK过程能力分析报告
CPK过程能力分析报告CPK(Process Capability Analysis)是一种常用的质量管理工具,用于评估一个过程的稳定性和能力。
它可以帮助我们确定过程是否能够生产出具有一致性和可接受性的产品。
本报告将通过对一个CPK过程进行分析,来评估其稳定性和能力。
在进行CPK分析之前,首先需要收集样本数据。
在本次分析中,我们选择了一个汽车零部件生产过程作为研究对象。
我们收集了该过程连续一周的生产数据,每天取20个样本,即总共取得了140个样本。
每个样本中包含了产品的关键尺寸数据,例如长度、宽度和高度。
第一步是计算样本数据的平均值(X)和标准偏差(S)。
通过计算这些统计指标,我们可以得到该过程的中心线和过程稳定性的度量。
接下来,我们计算过程能力指数CPK。
CPK指数是评估一个过程的能力是否足够稳定以满足特定设计规格要求的重要指标。
CPK的计算需要使用过程的公差范围(TS),它是由设计规格确定的,以指导产品的尺寸范围。
CPK的计算公式如下:CPK = min((USL – X) / 3S, (X – LSL) / 3S)其中,USL是上限规格限制(Upper Specification Limit),LSL是下限规格限制(Lower Specification Limit),X是样本数据的平均值,S是样本数据的标准偏差。
通过计算CPK,我们可以得到我们的样本数据是否能够满足设计规格要求。
在本次分析中,我们假设该零部件的设计规格要求为长度在100到120之间。
经过对数据的分析,我们得到了以下结果:平均值X=110.45标准偏差S=2.62USL=120LSL=100将这些数据代入CPK的计算公式中,我们可以计算出CPK的值。
CPK = min((120 – 110.45) / (3 * 2.62), (110.45 – 100) / (3 * 2.62))= min(3.63, 3.64)=3.63结果显示,该过程的CPK指数为3.63,远远超过了1.33(通常认为CPK大于1.33表示过程能力足够稳定)。
过程能力指数(Cpk)在质量管理中的应用与评估
过程能力指数(Cpk)在质量管理中的应用与评估过程能力指数(Cpk)在质量管理中的应用与评估质量管理是一个企业始终追求的目标,而过程能力指数(Cpk)是一种常用于评估过程稳定性和性能的指标。
在质量管理中,Cpk可以用于检测和控制产品或服务的质量,帮助企业实现高品质的生产和服务目标。
本文将介绍Cpk的概念、计算方法以及其在质量管理中的应用和评估。
首先,让我们了解一下Cpk的概念。
Cpk是一种统计指标,用于评估过程的能力和稳定性。
它基于过程的数据,反映了过程中产品或服务产生的偏差程度。
Cpk的计算基于过程的平均值、标准差和规范上下限。
在质量管理中,Cpk用于衡量过程的能力,即过程是否能够满足规定的质量要求。
Cpk的计算方法如下:Cpk = min[(USL –μ) / 3σ, (μ –LSL) / 3σ]其中,USL表示规范的上限,LSL表示规范的下限,μ表示过程的平均值,σ表示过程的标准差。
Cpk值越大,表示过程的能力越高;Cpk值越小,表示过程的能力越低。
Cpk在质量管理中的应用主要包括以下几个方面:1. 过程能力评估:Cpk可以用于评估过程的能力和稳定性。
通过计算Cpk值,企业可以了解到过程是否能够满足规定的质量要求。
如果Cpk值较低,说明过程存在偏差较大的情况,需要进行改进和控制;如果Cpk值较高,说明过程的能力较强,可以继续保持稳定状态。
2. 品质控制:Cpk可以用于控制产品或服务的质量。
通过设定Cpk值的目标或下限,企业可以监测产品或服务的质量水平。
当Cpk值低于目标或下限时,说明产品或服务存在质量问题,需要及时采取措施进行改进和控制。
3. 过程改进:Cpk可以用于指导过程改进。
通过持续监测和分析Cpk值,企业可以找出过程中存在的问题,并采取相应的改进措施。
比如,当Cpk值较低时,可能是因为过程中存在一些不稳定的因素,需要进行变量的控制和调整;或者是因为过程中存在一些特殊因素,需要进行剔除或调整。
CPK(过程能力指数) 基本知识
限)
整理课件
Cpk等级评定及处理原则
等级 A+ A B C D
Cpk值
处理原则
≧1.67
无缺点、考虑降低成本
1.33 ≦ Cpk < 1.67 状态良好维持现状
1.00 ≦ Cpk < 1.33 改进为 A 级
0.67 ≦ Cpk < 1.00 制程不良较多,必须提升其能力
Cpk < 0.67 制程能力太差,应考虑重新整改设计制程
整理课件
Cpk和过程良率換算
Cpk
每一百件之不良 Defects per 100 parts
每一百万件之不良(Dppm) Defects per million parts
合格率%
0.33
31.7
0.67
4.5
1
0.27
1.33
0.0063
9.995 10.014
9.928 9.983 9.972 10.016 9.992 9.987 10.025 9.972
9.981 9.971 9.914 9.976 10.054 10.003 10.027 9.995 10.021 9.975
9.963 10.095 10.017
9.968 10.159
1.67
0.000057
2
0.0000002
317310 45500 2700
63 0.57 0.002
68.3 95.5 99.73 99.9937 100 ≒100
整理课件
推理题2
用一个3升的杯子和一 个5升的杯子,量出4升 水,不用其他的辅助工 具。 (杯子无刻度)
整理课件
PCA过程能力分析
PCA过程能力分析PCA,即过程能力分析(Process Capability Analysis),是一种用来评估和监控一个过程的能力的统计技术。
它通过对数据的分析,衡量过程在特定规格限制下的稳定性和能力,从而帮助组织提高产品和服务的质量。
PCA的过程可以分为以下几个步骤:1.数据收集:首先,需要收集与所分析过程相关的数据,通常是通过随机抽样或持续采集的方式获取。
收集到的数据可以包括供应商提供的过程输入数据和通过测量和检验获得的过程输出数据。
2.数据清洗和整理:在进行PCA之前,需要对收集到的数据进行清洗和整理。
这意味着排除异常值、缺失数据和其他干扰因素,确保数据的准确性和完整性。
3.基本统计分析:在进行PCA之前,可以通过基本的统计分析来了解数据的分布、特征和变化趋势。
这包括计算数据的均值、方差、标准偏差、范围和分布形状等统计量。
4.过程稳定性分析:PCA的第一步是评估过程的稳定性。
稳定的过程是指在相同条件下,过程输出的变异性是可预测和一致的。
常用的稳定性指标包括平均移动范围(AMR),平均移动极差(AMRA),与过程的稳定性指标(如过程的标准偏差和过程的变异系数)。
5. 规格限制分析:PCA的下一步是评估过程能否满足规格限制。
规格限制是根据产品或服务的要求和客户的期望设定的,它描述了过程输出的允许范围。
常用的规格限制指标包括能力指标(如过程的Cp、Cpk和Ppk)和性能指标(如过程的DPMO和PPM)。
6. 判定能力分析:通过将稳定性指标和规格限制指标进行对比,可以评估过程的能力。
Cp指标衡量了过程输出相对于规格宽度的分散程度,而Cpk指标则考虑了过程中心与规格中心之间的差异。
一般来说,Cp和Cpk值越大,说明过程的能力越高。
7.改进和控制:如果过程的能力不足,需要采取相关的改进措施来提高过程能力。
改进措施可以包括改变过程的设计、调整输入参数、改变材料或操作方式等。
此外,还可以制定和实施控制措施,以确保过程能力的持续改进和稳定。
- 1、下载文档前请自行甄别文档内容的完整性,平台不提供额外的编辑、内容补充、找答案等附加服务。
- 2、"仅部分预览"的文档,不可在线预览部分如存在完整性等问题,可反馈申请退款(可完整预览的文档不适用该条件!)。
- 3、如文档侵犯您的权益,请联系客服反馈,我们会尽快为您处理(人工客服工作时间:9:00-18:30)。
目录
▪ 过程能力分析的目的和步骤 ▪ 如何进行合理抽样 ▪ 过程稳定性分析 ▪ 过程数据正态性分析 ▪ CP/CPK的计算方法和应用方法 ▪ 属性型数据质量统计指标
过程稳定性分析
过程稳定的意义
一个稳定的过程仅存在随机性变异 通过稳定性可以检验是否存在系统性变异,如果存 在系统性变异,在进行PCA之前应剔除
过程能力的应用
▪ 过程能力指数代表了过程能力的高低,过程能力指数越大表明 对应的过程能力越高。一般说来对过程能力的评价标准为:
Cpk的取值范围
级别
过程能力的评价
Cpk≥1.67 1.67> Cpk≥1.33 1.33> Cpk≥1.0 1.0>Cpk≥0.67 0.67>Cpk
Ⅰ
过程能力较高
Ⅱ
过程能力充分
过程能力分析的步骤
否 定义缺陷和缺陷机会
确定过程质量特征值
计量值数据?
是 定义变异来源
抽样
过程是否稳定? 是
计算 DPU 计算 DPMO
否
计算Cp(q),Cpk(q)
否 剔除根本影响因素
测量系统分析
否 能力是否充足?
是 制定抽样计划
剔除系统性原因
否
过程是否稳定?
是
是否能转换? 是
否
数据服从正态分 布?
First-time yield=(良品数/生产数)×100% Final Yield:是指单位产品在最后工序生产合格的概率,其计 算公式为:
Final yield=(1- 最后工序的不良品数 )×100%
产品数
综合直通率=工序1直通率×工序2直通率×工序3直 通率×工序4直通率×工序5直通率…
以上两个统计指标都是基于结果(良品和不良品)的统计指标,关注的是“efficiency”
18.29
多变异分析(MVA)
• 变异按来源可分为
—产品内变异 —产品间变异 —时间变异
• MVA的目的-确定过程的主要变异来源从而进行 合理的抽样
多变异分析(MVA)
diameter
1 2 3 1 2 3 1 2 3
多变异分析图
Multi-Vari Chart for diameter by position - time
DPMO=(缺陷数/缺陷机会数)×1000000 DPU(defects per unit):是指单位产品所包含的缺陷数量。其计算公式为:
DPU=缺陷数/产品数 DPHU(defects per hundred units: 是指每百产品中所包含的缺陷数量. 其计算公式为:
DPHU=(缺陷数/产品数)×100
以上四个统计指标都是基于缺陷的统计指标,关注的是“effectiveness”,其中DPMO /DPO还综合考虑了产品的复杂度(即是缺陷机会数)
TY/RTY/NY
Throughput Yield:是指在某一特定工序所产生的所有缺陷机会都符合相 关质量标准要求的概率。换句话讲,就是在给定工序点中“将所有事情做 对”的可能性。计算公式为:
DPMO/DPU/DPHU/DPO
DPO(defects per opportunity):是指单位缺陷机会数中产生的缺陷 数量。其计算公式为:
DPO=缺陷数/缺陷机会数 DPMO(defects per million opportunities): 是指每百万缺陷机会数中 产生的缺陷数量。其计算公式为:
合理抽样
合理抽样是指 • 它能捕捉过程的随机性变异 • 它不包含系统性变异
合理抽样的目的是使抽取的样本具有代表性,能代表过 程变化
抽样时重点注意以下几点: • 谁测量的数据? • 测量仪器是否被校准? • 搜集数据之后过程是否发生变化? • 对影响过程输出的关键影响因素所发生的变化是否做了 记录? • 数据搜集的时间、过程、目的和抽样方式
Cp 和 Cpk
定义
LSL
USL - LSL USL - LSL
CP 3 3s
USL
-3 -2 -1 µ + +2 +3
B= ±3
仅有上公差限: CPU
C PU
USL - 3
USL - X 3s
USL
µ
仅有下公差限: CPl
C PL
- LSL
3
X - LSL 3s
LSL
µ
计算 C PK
shaft
18.6 18.5
position
left middle right
18.4
18.3
18.2
18.1
12am
8am
time
10am
根据 MVA确定合理的抽样方案
▪ 产品内的测量点的个数(n):如果产品内部存在变异,那么 至少应选择两个位置。如果产品内的变异很大,应增加产品内 位置选择的个数。当不知道产品内是否存在变异时,通常选取 3-5 个点。 ▪ 一次抽取的产品个数(b):至少 3个;如果产品间变异很大, 就增加个数。通常选5-10 个。 ▪ 时间点的数量(a): 至少 3个; 如果时间变异很大,应增加时间 点选取的个数。
Ⅲ
过程能力尚可,但接近
Ⅳ
1.0时要注意
Ⅴ
过程能力不足,需采取措
施
过程能力严重不足
过程能力的应用
▪ 过程能力指数与合格品率的关系
CP CPK
0.33 0.67
1 1.33 1.67
2
0.33
0.67
1.0
68.268% 84.000% 84.134%
/
95.450% 97.722%
/
/
99.730%
满足规范的要求,此时不需要进行过程调整,只需要维持现状即可。
目录
▪ 过程能力分析的目的和步骤 ▪ 如何进行合理抽样 ▪ 过程稳定性分析 ▪ 过程数据正态性分析 ▪ CP/CPK的计算方法和应用方法 ▪ 属性型数据质量统计指标
FTY/FPY/FY
First-time Yield/First-pass Yield:是指产品经过某一特定工序 合格的概率,其计算公式为:
1.仅有 USL: 2.仅有 LSL:
CPK = CPU CPK = CPL
3. USL 和 LSL都存在:
{ } (1) CPK = Min CPU ,CPL
(2)
CPK
=
USL
- LSL
±3
-
2
=
USL
- LSL ±3s
-
2
= - USL + LSL
2
(3) CPK = CP (1- k)
k = 2 USL - LSL
多变异分析(MVA)
多变异分析案例
为了分析轴的直径变异并确定变异来源, 质量工程师 选择了3个时间点, 8:00 AM、10:00 AM、12:00 AM, 在每个时间点上选取3根轴,每根轴选取3个位置进行测 量
时间
单位 位置
左 中 右 均值 组均值
8AM 123
10AM 123
12AM 123
18.5 18.2 18.4 18.3 18.4 18.2 18.2
= USL + LSL 2
练 习:
计算 Cp 和Cpk
公差.
过程
1 2 3
目标值 15 10 8
容差
±±±000...00223
均值 14.990
9.98 8.05
标准差 0.005 0.01 0.04
C P C PK
过程能力分析要点
抽样是合理的 样本量尽量大,通常大于100 过程稳定 数据相互独立 检查是否有异常值 检验数据正态性,必要时化为正态 用单值而不是数据均值
非正态数据的特征: -有异常数据 -分布非正态
数据转换
如果过程稳定却非正态,可以数据转换为正态.但如果非正 态是由系统性原因引起的,那么在进行过程能力分析之前应 剔除这些系统性变异. 若 X非正态,可通过以下方式转化为正态 :
1,
X, 3 X logX,ln X
X
目录
▪ 过程能力分析的目的和步骤 ▪ 如何进行合理抽样 ▪ 过程稳定性分析 ▪ 过程数据正态性分析 ▪ CP/CPK的计算方法和应用方法 ▪ 属性型数据质量统计指标
PCA
目录
▪ 过程能力分析的目的和步骤 ▪ 如何进行合理抽样 ▪ 过程稳定性分析 ▪ 过程数据正态性分析 ▪ CP/CPK的计算方法和应用方法 ▪ 属性型数据质量统计指标
课程目标
▪ 理解过程能力分析的目的 ▪ 掌握过程能力分析的步骤 ▪ 会计算 Cp 和 Cpk ▪ 会计算DPU 和 DPMO ▪ 能够将 DPMO转化为 Sigma水平
不要对不稳定的过程计算Cp 和 Cpk
用控制图来分析稳定性*
通过控制图可以确定过程是否稳定. 常用的控制 图有: -均值(Xbar) -极差(R)控制图 -均值(Xbar) - 标准差(S)控制图 -单值- 移动极差控制图
*控制图将在今后的课程中进行详细的讨论
用控制图来分析稳定性
MINITA: Stat/Control Charts/
99.999999 8%
过程能力的应用
过程能力指数Cp和Cpk的联合运用
Cp表示了过程固有的均匀性、一致性,Cp越大,则过程特性值的分布越集中,过 程能力越强。Cpk表示了实际过程特性值与规范的符合程度,既要考虑特性值分布的集 中程度,也要考虑实际分布中心与公差中心的偏离程度,是二者的综合体现。从数学上 看Cpk与Cp的关系是:Cpk≤Cp,在实际运用过程中会遇到如下四种情况: a. 如Cp足够大但是Cpk不足(例如Cp>2、Cpk<1.5,表明过程特性值分布中心
是
正态性转换
计算 Cp , Cpk
改进测量系统
评价过程能力,确定瓶颈过程