悬架设计
汽车悬架发展简史

汽车悬架发展简史汽车悬架是汽车的重要组成部分,它直接影响着车辆的操控性、舒适性和安全性。
在汽车发展的历程中,悬架的设计和技术也经历了多次革新和改进。
本文将从人类视角出发,为你讲述汽车悬架的发展简史。
一、早期悬架设计最早的汽车悬架设计可以追溯到19世纪末。
当时的汽车悬架主要采用弹簧和减震器的组合,以提供车辆的平稳性和舒适性。
这种设计在当时被认为是先进的,但由于技术和材料的限制,悬架的效果并不理想。
二、悬架的革新随着科技的进步和工业化的发展,汽车悬架的设计逐渐得到改进。
在20世纪初,液压减震器的出现使得悬架的效果有了显著提升。
液压减震器可以根据路面状况自动调节阻尼力,使得车辆行驶更加稳定和舒适。
悬架材料的改进也为悬架的发展提供了支持。
钢材的广泛应用使得悬架的结构更加坚固和耐用,从而提高了车辆的安全性和稳定性。
三、空气悬架的出现20世纪50年代,空气悬架开始在汽车上应用。
空气悬架通过气压的调节来改变悬架的硬度和高度,从而提供更好的悬架性能。
空气悬架的出现使得车辆在不同路况下都能保持较好的悬架效果,进一步提升了车辆的舒适性和操控性。
四、电子悬架的引入随着电子技术的发展,电子悬架逐渐在高端汽车上引入。
电子悬架通过传感器和控制系统来实时监测和调节悬架的状态,以适应不同的行驶条件和驾驶方式。
电子悬架的出现使得车辆可以根据驾驶者的需求来调节悬架的硬度和高度,进一步提升了车辆的操控性和舒适性。
五、未来发展趋势随着汽车科技的不断进步,悬架的发展也将朝着更加智能化和高效化的方向发展。
未来的悬架可能会采用更先进的材料和技术,以提供更好的悬架性能和更高的安全性。
六、总结汽车悬架的发展经历了多次革新和改进,从最早的弹簧减震器到如今的电子悬架,每一次的改进都使得车辆的悬架性能得到提升。
随着科技的进步,我们有理由相信未来的悬架技术将会更加先进和智能化,为驾驶者提供更好的悬架体验。
作为车辆的重要组成部分,悬架的发展不仅仅是技术的进步,更是人类对于驾驶舒适性和安全性的追求。
第6章悬架设计

轴上的悬架横向刚度小,则容易造成转向轮发生 摆振现象。
5)悬架占用的空间尺寸 占用横向尺寸大的悬架影响发动机的布置和从
车上拆装发动机的困难程度; 占用高度空间小的悬架,则允许行李箱宽敞,
而且底部平整,布置油箱容易。
24
悬架
双横臂式
单横臂式 单纵臂式 单斜臂式 麦弗逊式 扭转梁随动臂式
结构简单、 结构简单,用于 紧凑,轿车 发动机前置前轮 上用得较多 驱动轿车后悬架
汽车设计
三、前、后悬架方案的选择 前轮和后轮均采用非独立悬架; 前轮采用独立悬架,后轮采用非独立悬架; 前轮与后轮均采用独立悬架。
26
汽车设计
1 前轮和后轮均采用非独立悬架
轴转向效应
27
汽车设计
对前轴,这种偏转使汽车不足转向趋势增加 对后桥,则增加了汽车过多转向趋势
45
汽车设计
五、悬架侧倾角刚度及其在前、后轴的分配 悬架侧倾角刚度:指簧上质量产生单位侧倾角时, 悬架给车身的弹性恢复力矩。 要求在侧向惯性力等于0.4倍车重时,乘用车车身 侧倾角2.5°~ 4°,货车车身侧倾角不超过6°~ 7°。 应使前悬架具有的侧倾角刚度略大于后悬架的侧 倾角刚度。对乘用车,前、后悬架侧倾角刚度的比 值一般为1.4~2.6。
46
汽车设计
§6-4 弹性元件的计算
38
汽车设计
三、悬架弹性特性 1、定义
悬架受到垂直外力F与由此所引起的车轮中心 相对于车身位移f(即悬架的变形)的关系曲线 。 2、分类
线性弹性特性、非线性弹性特性 1)线性弹性特性 定义: 悬架变形f与所受垂直外力F之间成固定比例 变化,弹性特性为一直线,悬架刚度为常数 。
《悬架设计》课件2

THANKS
复合材料
利用碳纤维、玻璃纤维等复合材料,提高悬架刚 度和强度,同时减轻重量。
智能材料
运用压电陶瓷、形状记忆合金等智能材料,实现 悬架的自适应调节和主动控制。
智能化技术在悬架设计中的应用
传感器技术
辅助驾驶系统
利用传感器实时监测车辆行驶状态和 路面状况,为悬架系统提供精确的数 据支持。
结合雷达、激光雷达、摄像头等技术 ,实现悬架的主动调节,提升驾驶安 全性和舒适性。
性能特点
该货车悬架系统具有较大 的承载能力和刚度,确保 车辆在重载情况下仍具有 良好的行驶稳定性。
设计优化
通过合理设计钢板弹簧的 形状和刚度,降低车辆自 重和提高燃油经济性,同 时保证货车的承载能力。
06
未来悬架设计展望
新材料在悬架设计中的应用
轻量化材料
采用高强度钢、铝合金等轻量化材料,降低悬架 重量,提高车辆燃油经济性和操控性能。
悬架的性能要求
刚度与阻尼
悬架需具备合适的刚度与阻尼,以 实现良好的缓冲减震效果。刚度决 定了悬架的支撑强度,而阻尼则影
响减震性能。
侧倾刚度
为了维持车身姿态稳定,悬架还需 具备足够的侧倾刚度,以抵抗车身
侧倾。
纵向刚度与横向刚度
纵向刚度影响车辆纵向稳定性,横 向刚度则影响车辆操控稳定性。
适应性与可靠性
悬架的定义与功能
缓冲减震
吸收和缓冲来自路面的冲击,提高乘坐 舒适性。
传递力矩
将地面施加在车轮上的力和力矩传递到 车身,同时将驾驶控制信号传递给车轮 。
维持车身姿态
保持车身姿态稳定,防止过大的颠簸和 摇摆。
适应路面变化
通过调节减震器和弹簧等元件的参数, 适应不同路面状况和驾驶需求。
独立悬架课程设计方案模板
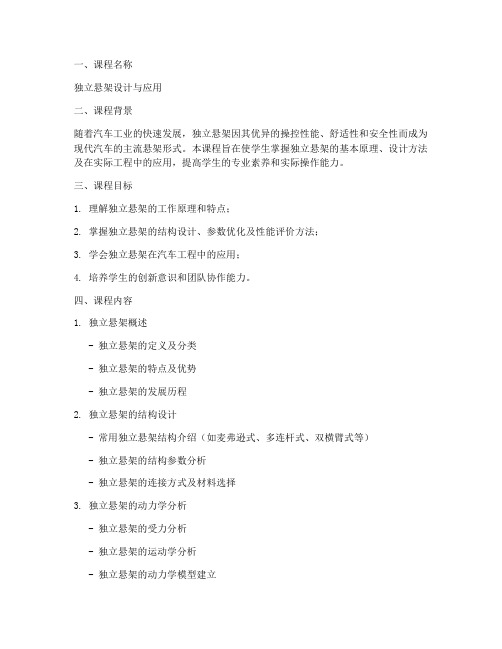
一、课程名称独立悬架设计与应用二、课程背景随着汽车工业的快速发展,独立悬架因其优异的操控性能、舒适性和安全性而成为现代汽车的主流悬架形式。
本课程旨在使学生掌握独立悬架的基本原理、设计方法及在实际工程中的应用,提高学生的专业素养和实际操作能力。
三、课程目标1. 理解独立悬架的工作原理和特点;2. 掌握独立悬架的结构设计、参数优化及性能评价方法;3. 学会独立悬架在汽车工程中的应用;4. 培养学生的创新意识和团队协作能力。
四、课程内容1. 独立悬架概述- 独立悬架的定义及分类- 独立悬架的特点及优势- 独立悬架的发展历程2. 独立悬架的结构设计- 常用独立悬架结构介绍(如麦弗逊式、多连杆式、双横臂式等)- 独立悬架的结构参数分析- 独立悬架的连接方式及材料选择3. 独立悬架的动力学分析- 独立悬架的受力分析- 独立悬架的运动学分析- 独立悬架的动力学模型建立4. 独立悬架的参数优化- 独立悬架性能评价指标- 参数优化方法(如遗传算法、粒子群算法等)- 优化结果分析与验证5. 独立悬架在汽车工程中的应用- 独立悬架在轿车、SUV、MPV等车型中的应用- 独立悬架在新能源汽车中的应用- 独立悬架在赛车、特种车辆中的应用6. 独立悬架的试验与验证- 独立悬架试验台搭建- 独立悬架性能试验方法- 试验结果分析与总结五、教学方法1. 讲授法:系统讲解独立悬架的基本原理、设计方法及实际应用;2. 案例分析法:通过分析典型独立悬架案例,提高学生的实践能力;3. 讨论法:引导学生对独立悬架设计中的问题进行讨论,培养学生的创新思维;4. 实践操作法:组织学生进行独立悬架设计、建模及仿真实验,提高学生的实际操作能力。
六、课程评价1. 平时成绩:课堂参与度、作业完成情况等(40%);2. 实践成绩:独立悬架设计、建模及仿真实验成绩(30%);3. 期末考试:独立悬架基本原理、设计方法及应用的笔试成绩(30%)。
七、课程资源1. 教材:《汽车悬架设计与应用》;2. 网络资源:相关学术网站、汽车设计软件等;3. 实验设备:独立悬架试验台、计算机等。
悬架设计

B:前悬架用宽的弹簧片,会影响转向轮的最大转角。
C:片宽选取过窄,又得增加片数,从而增加片间的摩
擦和弹簧的总厚
大家好
next 50
汽车设计
大家好
back
51
汽车设计2).钢板弹簧片厚h的选择(影响)
➢增加片厚h,可以减少片数n
➢钢板弹簧各片厚度可能有相同和不同两种情况,
希望尽可能采用前者
选 择
➢但因为主片工作条件恶劣,为了加强主片及卷 耳,也常将主片加厚,其余各片厚度稍薄。此时,
汽车设计
1.满载弧高fa
➢满载弧高fa是指钢板弹簧装到车轴(桥)上, 汽车满载时钢板弹簧主片上表面与两端(不包 括卷耳半径)连线间的最大高度差
➢fa用来保证汽车具有给定的高度
➢当fa=0时,钢板弹簧在对称位置上工作 ,为 了在车架高度已限定时能得到足够的支挠度值, 常fa=10~20mm。
大家好
45
40 40
汽车设计
Fk Fc F0
ca/cm 1
大家好
41
汽车设计
四、悬架侧倾角刚度及其在前、后轴的分配
1.侧倾角刚度
侧向惯性力为0.4G时:
乘用车侧倾角:2.5-4.0度
货车侧倾角:6-7度
2.前、后轴侧倾角刚度的匹配
乘用车:前、后悬架侧倾角刚度比值:
1.4~2.6
大家好
42
汽车设计
第四节 弹性元件的计算
➢各片的承受的弯矩正比于其惯性矩
➢同时该截面上各片的弯矩和等于外力 所引起的弯矩
n
c6aE/
ak31(Yk
Yk1)
k1
k
ak1(l1lk1)
Yk 1/ Ji i1
课程设计悬架系统

课程设计悬架系统一、教学目标本课程的学习目标包括知识目标、技能目标和情感态度价值观目标。
知识目标要求学生掌握悬架系统的结构、原理和功能,了解不同类型的悬架系统及其优缺点。
技能目标要求学生能够分析悬架系统的性能,进行简单的悬架系统设计和优化。
情感态度价值观目标则是培养学生的创新意识、团队合作精神和对汽车工程领域的兴趣。
通过本课程的学习,学生将能够:1.描述悬架系统的组成、原理和功能。
2.分析不同类型的悬架系统及其适用场景。
3.评价悬架系统的性能指标。
4.设计简单的悬架系统并进行优化。
5.展现创新意识、团队合作精神和对汽车工程领域的兴趣。
二、教学内容根据课程目标,本课程的教学内容主要包括悬架系统的结构、原理、功能及性能评价。
具体安排如下:1.第一课时:介绍悬架系统的组成和分类,分析各类悬架系统的结构特点和适用场景。
2.第二课时:讲解悬架系统的原理和功能,通过实例展示悬架系统在车辆行驶中的作用。
3.第三课时:讲解悬架系统的性能评价指标,如刚度、阻尼、稳定性等,分析不同悬架系统性能的优缺点。
4.第四课时:教授如何设计简单的悬架系统并进行优化,培养学生解决实际问题的能力。
三、教学方法为激发学生的学习兴趣和主动性,本课程将采用多种教学方法,如讲授法、讨论法、案例分析法和实验法等。
1.讲授法:用于讲解悬架系统的基本概念、原理和性能评价。
2.讨论法:学生探讨不同悬架系统的优缺点及其适用场景。
3.案例分析法:分析实际案例,让学生了解悬架系统在车辆行驶中的作用。
4.实验法:让学生动手进行悬架系统的设计和优化,提高实际操作能力。
四、教学资源本课程所需教学资源包括教材、参考书、多媒体资料和实验设备。
1.教材:选用权威、实用的教材,为学生提供系统、全面的学习资料。
2.参考书:推荐学生阅读相关领域的参考书籍,丰富知识体系。
3.多媒体资料:制作精美的PPT、动画等多媒体资料,帮助学生形象地理解悬架系统的原理和功能。
4.实验设备:准备相应的实验设备,让学生进行悬架系统的设计和优化实验,提高实际操作能力。
悬架设计
悬架设计三、设计要求:1)良好的行驶平顺性:簧上质量 + 弹性元件的固有频率低;前、后悬架固有频率匹配:乘:前悬架固有频率要低于后悬架尽量避免悬架撞击车架;簧上质量变化时,车身高度变化小。
2)减振性好:衰减振动、抑制共振、减小振幅。
3)操纵稳定性好:车轮跳动时,主销定位参数变化不大;前轮不摆振;稍有不足转向(δ1>δ2)4)制动不点头,加速不后仰,转弯时侧倾角合适5)隔声好6)空间尺寸小。
7)传力可靠、质量小、强度和寿命足够。
§6-2 悬架结构形式分析:一、非独立悬架和独立悬架:二、独立悬架结构形式分析:1、评价指标:1)侧倾中心高度:A、侧倾中心:车身在通过左、右车轮中心的横向垂直平面内发生侧倾时,相对于地面的瞬时转动中心,叫侧倾中心。
B、侧倾中心高度:侧倾中心到地面的距离。
C、侧倾中心位置影响:位置高:侧倾中心到质心的距离缩短,侧向力臂和侧倾力矩↓,车身侧倾角↓;过高:车身倾斜时轮距变化大,加速轮胎车轮外倾角α磨损。
2)车轮定位参数:车轮外倾角α,主销内倾角β,主销后倾角γ,车轮前束等会发生变化。
主销后倾角γ变化大→转向轮摆振车轮外倾角α化大→直线行驶稳定性;轮距变化,轮胎磨损3)悬架侧倾角刚度A、车厢侧倾角:车厢绕侧倾轴线转动的角度B、影响:车厢侧倾角与侧倾力矩和悬架总的侧倾角刚度有关,影响操纵稳定性和平顺性4)横向刚度:影响操纵稳定性转向轴上悬架横向刚度小,转向轮易摆振, 5)空间尺寸:占用横向尺寸→影响发动机布置和拆装;占用高度尺寸→影响行李箱大小和油箱布置。
2、不同形式悬架比较(表6-1)问:A、车轮跳动时,为什么α、β、γ如此变化?B、轮距为什么如此变化?C、应用?1)双横臂式:A、α、β均变,∵非平移,选择四杆结构,可小;B、四杆;C、应用:中高轿前悬,不用于微轿(空间)。
2)单横臂:A、α、β变化大,∵绕一点横向转动;B、绕一点横向转动;C、应用:后悬,少用于前悬。
悬架系统设计计算报告
悬架系统设计计算报告一、引言悬架系统作为汽车底盘的重要组成部分,对车辆的行驶稳定性、乘坐舒适性和操控性能等方面有着重要影响。
因此,在汽车设计和制造过程中,悬架系统的设计十分关键。
本报告将介绍悬架系统设计过程中的计算方法和依据,并对其进行详细说明。
二、悬架系统设计计算方法1.载荷计算:首先需要计算车辆在不同行驶条件下的载荷。
通过分析车辆的使用环境和客户需求,确定悬架系统的额定载荷。
然后,根据车辆自重、乘员重量、行李重量、荷载等因素,计算出车辆的总载荷。
2.载荷分配计算:在计算悬架系统的载荷分配时,需要考虑车辆的静态和动态载荷。
静载荷主要指车辆停靠时的重力,而动载荷主要指车辆行驶过程中因加速度、制动力和路面不平均性等引起的载荷。
通过对车辆不同部位的载荷进行测量和分析,确定每个车轮的载荷。
3.悬架系统刚度计算:悬架系统的刚度对车辆的操控性和乘坐舒适性有着直接影响。
悬架系统的刚度可以分为纵向刚度、横向刚度和垂向刚度等。
在设计悬架系统的过程中,需要根据车辆的使用环境和性能需求,计算悬架系统的刚度。
4.悬架系统减振器计算:悬架系统的减振器的设计和选型是悬架系统设计的重要环节。
减振器可以减少车辆在行驶过程中的震动,提高乘坐舒适性和行驶稳定性。
根据悬架系统的刚度和载荷等因素,计算减振器的选择和设计参数。
5.悬架系统运动学计算:悬架系统的运动学计算是为了确定悬架系统在不同行驶状态下的主要参数,以便进行悬架系统的设计和调整。
通过对车辆的几何尺寸、运动学参数和悬架结构的分析和计算,确定悬架系统的工作范围和参数。
三、计算依据在悬架系统设计计算中,需要依据以下相关标准和原则进行设计:2.汽车悬架系统设计手册:根据汽车制造商提供的相关手册和技术资料,对悬架系统设计进行指导和计算。
3.数学和工程力学原理:在悬架系统设计计算过程中,需要运用数学和工程力学的相关原理和方法,如力学平衡、弹性力学、振动理论等,进行悬架系统的计算。
4.仿真和试验数据:通过对悬架系统的仿真分析和试验测试,获取悬架系统的相关参数和性能数据,为悬架系统的设计计算提供依据。
汽车设计悬架设计
汽车设计悬架设计汽车悬架是汽车的重要组成部分之一,它负责支撑和连接车身和车轮,使汽车具备稳定驾驶性能、良好的操控性和舒适的行驶感受。
悬架设计的好坏直接关系到车辆的行驶稳定性、车身姿态控制以及车辆舒适性。
本文将从悬架的基本原理、结构形式、悬架参数优化以及新技术应用等方面,对汽车悬架的设计进行详细阐述。
汽车悬架的基本原理是通过弹簧和减振器来吸收和分散来自不平路面的冲击力,并提供车身的载荷支撑。
弹簧可以是螺旋弹簧、气囊弹簧或扭力杆弹簧,而减振器则是通过内部的液压阻尼器将冲击力转化为热能。
汽车悬架的结构形式多种多样,常见的有独立悬架、非独立悬架和半独立悬架等。
其中独立悬架可以使轮胎保持垂直于地面,确保每个车轮都能独立地跟随路面变化,提高车辆的操控性和舒适性。
在悬架设计中,悬架参数的优化是至关重要的一步。
悬架参数包括弹簧刚度、减振器阻尼、悬挂点位置等。
弹簧刚度的选择直接关系到车辆的悬架活动范围和弹性特性,太硬的弹簧会使车辆过于坚硬,太软的弹簧则会使车辆过于柔软。
减振器阻尼的调节可以影响车辆的悬挂变形和减振效果,适当的阻尼可以提高悬架的响应速度和抗冲击能力。
悬挂点位置的选择与车辆的悬挂角度和车轮跳跃力有关,较高的悬挂角度可以提高车辆的通过性和减震效果,而较低的车轮跳跃力可以提高车辆的稳定性和操控性。
近年来,随着科技的进步,汽车悬架的设计也有了许多新的技术应用。
例如,电子悬架系统可以通过电磁感应和控制阀来调节悬架的硬度和高度,实现动态悬架调节;主动减振器系统则可以根据路面状况和驾驶环境主动调节减振器的阻尼,提供更好的悬架效果。
此外,气动悬架系统可以通过空气弹簧和电动泵进行主动调节,提供更好的减震效果和稳定性。
这些新技术的应用使汽车悬架能够更好地适应不同行驶条件和驾驶需求,提供更好的驾驶体验。
综上所述,汽车悬架设计对车辆的行驶稳定性、操控性和舒适性具有巨大影响。
悬架设计应该根据车辆的使用环境和驾驶需求合理选择悬架形式、优化悬架参数,并结合新技术的应用来提供更好的行驶性能。
悬架设计指南范文
悬架设计指南范文悬架设计是车辆工程中的一个重要部分,它直接关系到车辆的操控性、舒适性以及安全性。
本文将从悬架的基本原理、悬架系统的组成部分、悬架设计的要素以及常见的悬架类型等方面进行详细介绍。
1.悬架的基本原理悬架是连接车体和车轮的一组系统,它的主要功能是减震、支撑和保持车轮接触路面的稳定性。
悬架系统通过减震器、弹簧、阻尼器和托架等部件来实现对车体和车轮的衔接和控制。
在车辆行驶过程中,悬架系统将路面的不平度转化为车体的垂直运动,并通过减震器来吸收和控制车体的能量。
2.悬架系统的组成部分悬架系统主要由减震器、弹簧、阻尼器、控制臂、托架和稳定杆等组成。
其中,减震器和弹簧是悬架系统中最重要的两个部件。
减震器主要用于吸收和控制车体的能量,而弹簧则主要用于支撑车体的重量,并提供适当的车身高度。
3.悬架设计的要素悬架设计的要素包括载荷分配、悬架行程、悬架刚度和减震器调校等。
载荷分配是指在不同驾驶状态下车轮承受的重量比例,合理的载荷分配能够提高车辆的操控性和稳定性。
悬架行程是指车轮在垂直方向上的运动范围,合理的行程能够提供足够的减震和保持车轮接触路面。
悬架刚度是指弹簧对垂直位移的阻力,适当的刚度能够提高车辆的操控性和舒适性。
减震器调校是指根据车辆的驾驶状态和行驶环境调整减震器的工作效果,合理的调校能够提供更好的悬架控制和舒适性。
4.常见的悬架类型常见的悬架类型包括独立悬架、刚性悬架和半独立悬架等。
独立悬架是指每个车轮都配备有独立的悬架系统,它能够提供更好的悬架控制和车轮独立运动。
刚性悬架是指车轮之间通过刚性连接,它简单、结构稳定,但无法独立运动。
半独立悬架是介于独立悬架和刚性悬架之间的一种类型,它主要用于低成本和简化设计的车辆。
在悬架设计的过程中,需要综合考虑车辆的操控性、舒适性和安全性等因素。
通过合理的悬架设计能够提高车辆行驶的稳定性和舒适性,并降低车辆行驶时的振动和疲劳程度。
同时,与其他车辆系统的协调和优化也是悬架设计的重要内容,例如制动系统、转向系统和底盘结构等。
- 1、下载文档前请自行甄别文档内容的完整性,平台不提供额外的编辑、内容补充、找答案等附加服务。
- 2、"仅部分预览"的文档,不可在线预览部分如存在完整性等问题,可反馈申请退款(可完整预览的文档不适用该条件!)。
- 3、如文档侵犯您的权益,请联系客服反馈,我们会尽快为您处理(人工客服工作时间:9:00-18:30)。
一、悬架的静挠度悬架的静扰度 是指汽车满载静止时悬架上的载荷Fw 与此时悬架刚度c 之比,即c F f w c /=货车的悬架与其簧上质量组成的振动系统的固有频率,是影响汽车行驶平顺性的主要参数之一。
因汽车的质量分配系数近似等于1,因此货车车轴上方车身两点的振动不存在联系。
货车的车身的固有频率n,可用下式来表示: n=π2//m c 式中,c 为悬架的刚度(N/m ),m 为悬架的簧上质量(kg ) 又静挠度可表示为:c mg f c /=g :重力加速度(2/9810s mm g =),代入上式得到: n=15.77/c f n: Hzc f : mm分析上式可知:悬架的静挠度直接影响车身的振动频率,因此欲保证汽车有良好的行驶平顺性,就必须正确选择悬架的静挠度。
又因为不同的汽车对平顺性的要求不相同,货车的前悬架偏频要求在1.50~2.10Hz 之间,因为货车主要以载货为主,所以选取频率为:1.8Hz. 由 n=15.77/c f 得, c f =76.7mm ,取c f =77mm二、 悬架的动挠度悬架的动挠度是指从满载静平衡位置开始悬架压缩到结构容许的最大变形时,车轮中心相对车架的垂直位移。
通常货车的动挠度的选择范围在6~9cm.。
本设计选择:d f =80mm三、 悬架的弹性特性悬架的弹性特性有线性弹性特性和非线性弹性特性两种。
由于货车在空载和满载时簧上质量变化大,为了减少振动频率和车身高度的变化,因此选用刚度可变的非线性悬架。
已知满载静止时负荷kg G 93401=。
簧下部分荷重kg G u 12201=,由此可计算出单个钢板弹簧的载荷:N g G G F u w 397882/8.9*)12209340(2/)(222=-=-=因为2/)(222g G G F u w -=,c F f w c /=,c mg f c /=mm f c 77=代入公式,可得C=516.7N/mm4.2.1满载弧高 :满载弧高a f 是指钢板弹簧装到车轴上,汽车满载时钢板弹簧主片上表面与两端连线间的高度差。
常取a f =10~20mm.在此取:mm f a 15=4.2.2钢板弹簧长度L 的确定:(1) 选择原则:钢板弹簧长度是弹簧伸直后两卷耳中心之间的距离。
货车前悬架:L=(0.26~0.35)轴距,后悬架:L=(0.35~0.45)轴距。
(2) 钢板弹簧长度的初步选定:根据经验L=0.35X 轴距=0.35X5300=1855mm ,并结合国内外货车资料,初步选定主簧主片的长度为1855mm =m L 。
4.2.3钢板弹簧断面尺寸的确定:(1) 钢板弹簧断面宽度b 的确定:有关钢板弹簧的刚度,强度可按等截面的简支梁计算,引入挠度增大系数δ加以修正。
因此,可根据修正后的简支梁公式计算钢板弹簧所需的总惯性距0J 。
对于对称式钢板弹簧[]E c kS L J 48/)(30δ-= 式中: S ——U 形螺栓中心距(mm )k ——U 形螺栓夹紧(刚性夹紧,k 取0.5);c ——钢板弹簧垂直刚度(N/mm ),c=c W f F /;δ——为挠度增大系数。
挠度增大系数δ的确定:先确定与主片等长的重叠片数1n ,再估计一个总片数0n ,求得01/n n =η,然后δ=1.5/[])5.01(04.1η+,初定δ。
对于弹簧:L=1855mmk=0.5S=200mm1n =30n =10103=ηδ=1.5/[])5.01(04.1η+=1.5/⎥⎦⎤⎢⎣⎡⨯+⨯)1035.01(04.1=1.25E=2.1510⨯N/4m m计算主簧总截面系数0W :0W [][]W W kS L F σ4/)(-≥式中[]w σ为许用弯曲应力。
[]w σ的选取:前弹簧和平衡悬架弹簧为350~450MPa 。
后主簧为450~550N/2m m ,后副簧为220~250 N/2m m 。
w F =m F =39788NL=1855mmk=0.5S=200mm[]w σ=450 N/2m m .再计算主簧平均厚度:[]cw p Ef kS L W J h 6)(/2200σδ-== =17.85mm 有了以p h 后,再选钢板弹簧的片宽b 。
推荐片宽和片厚的比值在b/hp 在6~10范围内选取。
mm h b p 95.12485.17*77=== ,取整为125mm 。
通过查手册可得钢板截面尺寸b 和h 符合国产型材规格尺寸。
(3)钢板断截面形状的选择:本设计选取矩形截面。
(4) 钢板弹簧片数的选择:片数n 少些有利于制造和装配,并可以降低片与片之间的干摩擦,改善汽车的行驶平顺性。
但片数少了将使钢板弹簧与等强度梁的差别增大,材料的利用率变坏。
多片钢板弹簧一般片数在6~14片之间选取,重型货车可达20片。
用变截面少片弹簧时,片数在1~4选取。
根据货车的载荷并结合国内外资料初步选取本货车弹簧的片数为10片,4.2.4 钢板弹簧各片长度的确定先将各片的厚度i h 的立方值3i h 按同一比例尺沿纵坐标绘制在图上,再沿横坐标量出主片长度的一半L/2和U 型螺栓中心距的一半s/2,得到A,B 两点,连接A ,B 两点就得到三角形的钢板弹簧展开图。
AB 线与各片上侧边的交点即为各片的长度。
如果存在与主片等长的重叠片,就从B 点到最后一个重叠片的上侧边断点连一直线,此直线与各片上侧边的交点即为各片长度。
各片实,际长度尺寸需经圆整后确定。
各片厚度相等,用计算法计算:因为弹簧主片长2120mm ,第1、2、3片等长,共10片,各片等厚,U 型螺栓夹紧距S=200mm ,所以按比例计算出其余各片长度。
第1、2、3等长,mm L L L 2120321===第4片长:mmS S L L 16482008/7)2001855(8/7)(4=+-=+-= 同理mmS S L L 14412008/6)2001855(8/6)(5=+-=+-=mmS S L L 12342008/5)2001855(8/5)(6=+-=+-=mmS S L L 10272008/4)2001855(8/4)(7=+-=+-=mmS S L L 8212008/3)2001855(8/3)(8=+-=+-=mmS S L L 6142008/2)2001855(8/2)(9=+-=+-=第10片长:mmS S L L 4072008/1)2001855(8/1)(10=+-=+-=4.4 钢板弹簧总成在自由状态下的弧高及曲率半径计算(1)钢板弹簧总成在自由状态下的弧高0H钢板弹簧总成在自由状态下的弧高0H ,用下式计算:)(0f f f H a c ∆++= 式中,c f 为静挠度;a f 为满载弧高;f ∆为钢板弹簧总成用U 型螺栓夹紧后引起的弧高变化,22))(3(L f f S L S f c a +-=∆;S 为U 型螺栓的中心距。
L 为钢板弹簧主片长度。
mm L f f S L S f c a 34.141855*2)7715(*)2001855*3(*2002))(3(22=+-=+-=∆ 则mm f f f H a c 34.10634.141577)(0=++=∆++=(2)钢板弹簧总成在自由状态下的曲率半径的确定:钢板弹簧总成在自由状态下的曲率半径:mm H L R 302061.104*8/15908/2020≈==3)钢板弹簧各片自由状态下曲率半径的确定矩形断面钢板弹簧装配前各片曲率半径由下式确定[]i i i Eh R R R /)2(1/000σ+=式中,i R 为第i 片弹簧自由状态下的曲率半径(mm ),为钢板弹簧总成0R 在自由状态下的曲率半径(mm )为各片钢板弹簧预应力i 0σ(N/2m m );E 为材料的弹性模量N/2m m ,取E 为5101.2⨯ N/2m m ;为第i h i 片的弹簧厚度(mm )。
在已知的条件下,可以用式和各片弹簧的预应力i R 00σ[]i i i Eh R R R /)2(1/000σ+=计算出各片钢板弹簧自由状态下的曲率半径R i 。
对于片厚相同的钢板弹簧,各片弹簧的预应力值应不宜选取过大;推荐主片在根部的工作应力与预应力叠和后的合成应力应在300~350N/2m m 内选取。
1~4片长片叠加负的预应力,短片叠加正的预应力。
预应力从长片由负值逐渐递增为正值。
在确定各片预应力时,理论上应满足各片弹簧在根部处的预应力所造成的弯矩之代数和等于零,即i M :01=∑=ni i M或 010=∑=i ni i W σ下面计算各片在自由状态下曲率半径的:各片的预应力及其他参数如下: i 1 2 3 4 5 6 7 8 9 10 i 0σ-2.3 -1.8 -1.3 -0.8 0 0.5 1 1.5 2.0 2.5 mm R 30200= E=5101.2⨯ N/2m m i h =12mm 然后用上述公式计算各片在自由状态下曲率半径,结果见下表:i1 2 3 4 5 6 7 8 9 10 3038 3032 3029 3026 3020 3016 3012 3009 3006 3001(4)钢板弹簧总成各片在自由状态下弧高的计算:如果第i 片的片长为i L ,则第i 片弹簧的弧高为: i i i R L H 8/2= 则将各片长度和曲率半径代入上式,得弹簧总成各片在自由状态下弧高: i 1 2 3 4 5 6 7 8 9 10)(mm H i104.0 104.2 104.382.1 62.6 45.7 31.4 19.8 10.84.5 4.5、 钢板弹簧总成弧高的核算根据最小势能原理,钢板弹簧总成的稳定平衡状态是各片势能总和最小状态,由此可求得等厚叶片弹簧的为:0R1/0R =∑∑==ni i i n i i L R L 11/)/(式中,为钢板弹簧i L 第i 片长度。
钢板弹簧的总成弧高为H 028/R L ≈上式计算的结果应与)(0f f f H a c ∆++=计算的设计结果相近。
如果相差太多,可重新选择各片预应力再行核算。
将弹簧各片的长度和曲率半径代入上述公式可得:3025mm =0R然后再代入H 028/R L ≈ =104.47mm原设计值为H 0=104.61mm ,相差不大,符合要求。
五、钢板弹簧强度验算当货车紧急制动时,货车的前钢板弹簧承受的载荷最大,在它的后半段出现的最大应力max σ用下式计算max σ=[][]02112'11)(/)(w l l c l l m G ++ϕ式中,1G 为作用在前轮上的垂直静载荷,'1m 为制动时前轴负荷转移系数;货车:'1m =1.40~1.60,取1.5;ϕ为道路附着系数,取0.8,1l 、2l 为钢板弹簧前后段长度;w0为钢板弹簧总截面系数;C 为弹簧固定点到路面的距离。