基于参数化设计的驱动桥壳有限元分析系统设计(精)
基于设计FMEA的矿用车桥壳有限元分析

基于设计FMEA的矿用车桥壳有限元分析摘要:为了提高矿用车桥壳的可靠性和安全性,本文基于设计FMEA方法,结合有限元分析技术,对矿用车桥壳进行分析。
首先对矿用车桥壳的功能和使用条件进行了分析,并通过FMEA方法识别了可能存在的设计缺陷。
然后采用有限元分析对矿用车桥壳进行了模拟计算,得到了其受力状态和应力分布情况。
最后,根据分析结果提出了相应的改进措施,以提高矿用车桥壳的可靠性和安全性。
关键词:设计FMEA、矿用车桥壳、有限元分析、可靠性、安全性正文:一、引言矿用车桥壳是矿用车的主要部件之一,其可靠性和安全性对于整个矿用车的运行都具有重要的影响。
为了确保矿用车的安全运行,需要对矿用车桥壳进行可靠性和安全性分析,寻找可能存在的设计缺陷,并提出相应的改进措施。
二、设计FMEA方法FMEA(故障模式及影响分析)是一种通过对系统或组件的功能和使用条件进行分析,识别可能存在的设计缺陷,并采取相应的措施预防故障的方法。
在矿用车桥壳的分析中,FMEA方法可以帮助分析人员识别可能存在的设计缺陷,从而提出相应的改进措施。
具体步骤如下:(1)明确矿用车桥壳的功能和使用条件。
(2)识别可能存在的故障模式及其严重程度。
(3)分析故障模式的根本原因。
(4)提出相应的改进措施,加以实施和验证。
三、有限元分析技术有限元分析是一种通过数值方法解决实际工程问题的方法。
在矿用车桥壳的分析中,有限元分析可以对其受力状态和应力分布情况进行模拟计算,为确定故障原因和提出改进措施提供支持。
具体步骤如下:(1)建立矿用车桥壳的有限元模型,并进行网格划分。
(2)参考矿用车的使用条件,施加相应的荷载、边界条件等。
(3)进行有限元分析计算,得出矿用车桥壳的受力状态和应力分布情况。
四、案例分析以某矿用车桥壳为例,采用设计FMEA方法和有限元分析技术进行分析。
首先,明确矿用车桥壳的主要功能是承受载重和传递动力,在恶劣的工作环境下保持稳定运行。
其次,通过FMEA方法识别了可能存在的设计缺陷,如连接结构强度不足、材料性能不合格等。
汽车驱动桥壳的有限元分析和设计方法综述
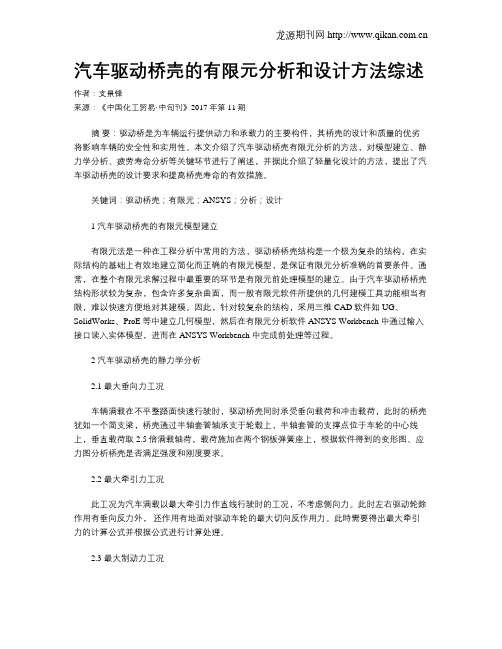
汽车驱动桥壳的有限元分析和设计方法综述作者:支景锋来源:《中国化工贸易·中旬刊》2017年第11期摘要:驱动桥是为车辆运行提供动力和承载力的主要构件,其桥壳的设计和质量的优劣将影响车辆的安全性和实用性。
本文介绍了汽车驱动桥壳有限元分析的方法,对模型建立、静力学分析、疲劳寿命分析等关键环节进行了阐述,并据此介绍了轻量化设计的方法,提出了汽车驱动桥壳的设计要求和提高桥壳寿命的有效措施。
关键词:驱动桥壳;有限元;ANSYS;分析;设计1 汽车驱动桥壳的有限元模型建立有限元法是一种在工程分析中常用的方法,驱动桥桥壳结构是一个极为复杂的结构,在实际结构的基础上有效地建立简化而正确的有限元模型,是保证有限元分析准确的首要条件。
通常,在整个有限元求解过程中最重要的环节是有限元前处理模型的建立。
由于汽车驱动桥桥壳结构形状较为复杂,包含许多复杂曲面,而一般有限元软件所提供的几何建模工具功能相当有限,难以快速方便地对其建模。
因此,针对较复杂的结构,采用三维CAD软件如UG、SolidWorks、ProE等中建立几何模型,然后在有限元分析软件ANSYS Workbench 中通过输入接口读入实体模型,进而在ANSYS Workbench 中完成前处理等过程。
2 汽车驱动桥壳的静力学分析2.1 最大垂向力工况车辆满载在不平整路面快速行驶时,驱动桥壳同时承受垂向载荷和冲击载荷,此时的桥壳犹如一个简支梁,桥壳通过半轴套管轴承支于轮毂上,半轴套管的支撑点位于车轮的中心线上,垂直载荷取2.5倍满载轴荷,载荷施加在两个钢板弹簧座上,根据软件得到的变形图、应力图分析桥壳是否满足强度和刚度要求。
2.2 最大牵引力工况此工况为汽车满载以最大牵引力作直线行驶时的工况,不考虑侧向力。
此时左右驱动轮除作用有垂向反力外,还作用有地面对驱动车轮的最大切向反作用力。
此時需要得出最大牵引力的计算公式并根据公式进行计算处理。
2.3 最大制动力工况驱动桥壳承受垂向力、制动力和制动力在两板簧座位置引起的转矩。
汽车驱动桥壳的有限元建模与分析_第一章绪论_8_14
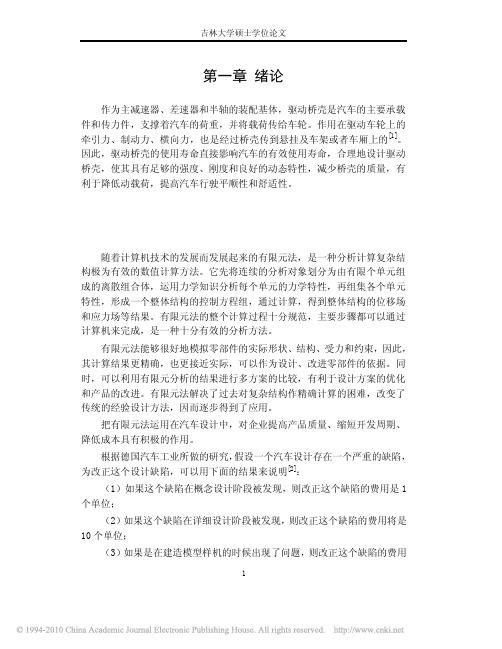
第一章 绪论 作为主减速器、差速器和半轴的装配基体,驱动桥壳是汽车的主要承载件和传力件,支撑着汽车的荷重,并将载荷传给车轮。
作用在驱动车轮上的牵引力、制动力、横向力,也是经过桥壳传到悬挂及车架或者车厢上的[1]。
因此,驱动桥壳的使用寿命直接影响汽车的有效使用寿命,合理地设计驱动桥壳,使其具有足够的强度、刚度和良好的动态特性,减少桥壳的质量,有利于降低动载荷,提高汽车行驶平顺性和舒适性。
1.1 汽车设计中应用的有限元法 1.1.1 有限元法在汽车设计中应用的意义 随着计算机技术的发展而发展起来的有限元法,是一种分析计算复杂结构极为有效的数值计算方法。
它先将连续的分析对象划分为由有限个单元组成的离散组合体,运用力学知识分析每个单元的力学特性,再组集各个单元特性,形成一个整体结构的控制方程组,通过计算,得到整体结构的位移场和应力场等结果。
有限元法的整个计算过程十分规范,主要步骤都可以通过计算机来完成,是一种十分有效的分析方法。
有限元法能够很好地模拟零部件的实际形状、结构、受力和约束,因此,其计算结果更精确,也更接近实际,可以作为设计、改进零部件的依据。
同时,可以利用有限元分析的结果进行多方案的比较,有利于设计方案的优化和产品的改进。
有限元法解决了过去对复杂结构作精确计算的困难,改变了传统的经验设计方法,因而逐步得到了应用。
把有限元法运用在汽车设计中,对企业提高产品质量、缩短开发周期、降低成本具有积极的作用。
根据德国汽车工业所做的研究,假设一个汽车设计存在一个严重的缺陷,为改正这个设计缺陷,可以用下面的结果来说明[2]:(1)如果这个缺陷在概念设计阶段被发现,则改正这个缺陷的费用是1个单位;(2)如果这个缺陷在详细设计阶段被发现,则改正这个缺陷的费用将是10个单位;(3)如果是在建造模型样机的时候出现了问题,则改正这个缺陷的费用1将是100个单位;(4)如果缺陷是在生产过程中被发现,则改正这个缺陷的费用将提高到1000个单位。
毕业设计(论文)汽车驱动桥壳UG建模及有限元分析

毕业设计(论文)汽车驱动桥壳UG建模及有限元分析毕业设计(论文)汽车驱动桥壳UG建模及有限元分析JIU JIANG UNIVERSITY毕业论文题目汽车驱动桥壳UG建模及有限元分析英文题目 Modeling by UG and Finite Element Analyzing of Automobile Drive Axle Housing 院系机械与材料工程学院专业车辆工程姓名班级指导教师摘要本篇毕业设计(论文)题目是《汽车驱动桥壳建模UG及有限元分析》。
作为汽车的主要承载件和传力件,驱动桥壳承受了载货汽车满载时的大部分载荷,而且还承受由驱动车轮传递过来的驱动力、制动力、侧向力等,并经过悬架系统传递给车架和车身。
因此,驱动桥壳的研究对于整车性能的控制是很重要的。
本课题以重型货车驱动桥壳为对象,详细论述了从UG软件中的参数化建模,到ANSYS中有限元模型的建立、边界条件的施加等研究。
并且通过对桥壳在不同工况下的静力分析和模态分析,直观地得到了驱动桥壳在各对应工况的应力分布及变形情况。
从而在保证驱动桥壳强度、刚度与动态性能要求的前提下,为桥壳设计提出可行的措施和建议。
【关键词】有限元法,UG,ANSYS ,驱动桥壳,静力分析,模态分析AbstractThis graduation project entitled “Modeling and Finite Element Analyzing of Automobile Drive Axle Housing”. As the mainly carrying and passing components of the vehicle, the automobile drive axle housing supports the weight of vehicle, and transfer the weight to the wheel. Through the drive axle housing, the driving force, braking force and lateral force act on the wheel transfer to the suspension system, frame and carriage.The article studies based on heavy truck driver axle ,discusses in detail from the UG software parametric modeling, establish of ANSYS FEM model, and the boundary conditions imposed, etc. And through drive axle housing of the different main conditions of static analysis and modal analysis, it can access the stress distribution and deformation in the corresponding status of drive axle directly. Thus, under the premise of ensuring the strength of drive axle housing, stiffness and dynamic performance requirements, the analysis can raise feasible measures and recommendations in drive axle housing design.Plans to establish thet hree---dimensional model by UG, to make all kinds of emulation analysis by Ansys.【Key words】 Finite element method,UG,ANSYS,Drive axlehousing,Static analysis,Modal analysis目录前言 1第一章绪论 21.1 汽车桥壳的分类 21.2 国内外研究现状 31.3 有限元法及其理论 51.4 ansys软件介绍 71.5 研究意义及主要内容 91.6 本章小结 10第二章驱动桥壳几何模型的建立 11 2.1 UG软件介绍 112.2 桥壳几何建模时的简化处理 11 2.3 桥壳几何建模过程 122.4 本章小结 24第三章驱动桥壳静力分析 25 3.1 静力分析概述 253.2 静力分析典型工况 253.3 驱动桥壳有限元模型的建立 27 3.3.1 几何模型导入 273.3.2 材料属性及网格划分 283.4 驱动桥壳各工况静力分析 293.4.1 冲击载荷工况 293.4.2 最大驱动力工况 323.4.3 最大侧向力工况 343.5 本章小结 37第四章驱动桥壳模态分析 384.1 模态分析概述 384.2 模态分析理论 384.3 驱动桥壳模态分析有限元模型的建立 40 4.4 驱动桥壳模态分析求解及结果 41 4.5 驱动桥壳模态分析总结 474.6 本章小结 47结论 48参考文献 50致谢 52前言在桥壳的传统设计中,往往采用类比方法,对已有产品加以改进,然后进行试验、试生产。
汽车桥壳的有限元分析毕业设计
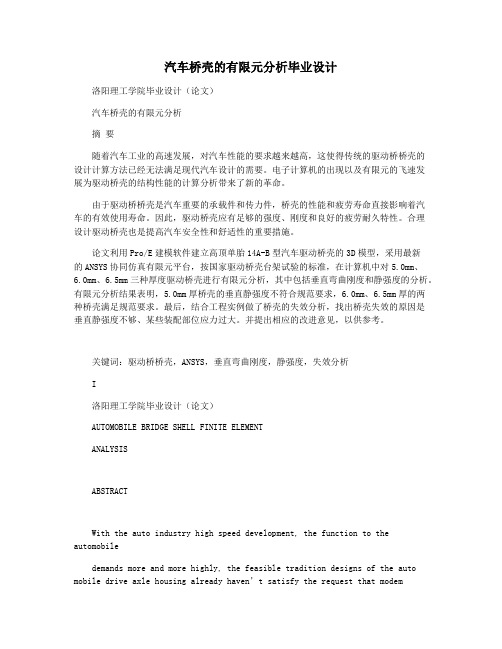
汽车桥壳的有限元分析毕业设计洛阳理工学院毕业设计(论文)汽车桥壳的有限元分析摘要随着汽车工业的高速发展,对汽车性能的要求越来越高,这使得传统的驱动桥桥壳的设计计算方法已经无法满足现代汽车设计的需要。
电子计算机的出现以及有限元的飞速发展为驱动桥壳的结构性能的计算分析带来了新的革命。
由于驱动桥桥壳是汽车重要的承载件和传力件,桥壳的性能和疲劳寿命直接影响着汽车的有效使用寿命。
因此,驱动桥壳应有足够的强度、刚度和良好的疲劳耐久特性。
合理设计驱动桥壳也是提高汽车安全性和舒适性的重要措施。
论文利用Pro/E建模软件建立高顶单胎14A-B型汽车驱动桥壳的3D模型,采用最新的ANSYS协同仿真有限元平台,按国家驱动桥壳台架试验的标准,在计算机中对5.0mm、6.0mm、6.5mm三种厚度驱动桥壳进行有限元分析,其中包括垂直弯曲刚度和静强度的分析。
有限元分析结果表明,5.0mm厚桥壳的垂直静强度不符合规范要求,6.0mm、6.5mm厚的两种桥壳满足规范要求。
最后,结合工程实例做了桥壳的失效分析,找出桥壳失效的原因是垂直静强度不够、某些装配部位应力过大。
并提出相应的改进意见,以供参考。
关键词:驱动桥桥壳,ANSYS,垂直弯曲刚度,静强度,失效分析I洛阳理工学院毕业设计(论文)AUTOMOBILE BRIDGE SHELL FINITE ELEMENTANALYSISABSTRACTWith the auto industry high speed development, the function to the automobiledemands more and more highly, the feasible tradition designs of the auto mobile drive axle housing already haven’t satisfy the request that modemdesigns. The calculation analysis that the electronic computer appearing develops at full speed for the structure designs as well as finite element method after has brought about new revolution.Since the axle housing is mainly carrying and passing components of thevehicle, the axle housing function and fatigue life have direct impact to effective automobile useful time, the axle housing should have sufficient intensity, stiffness and well durable fatigue property. Therefore, the axle housing designs are also to improve automobile safety and the comfortableness importance rationally methods.The thesis makes use of Pro/E software building the 3D models of 14A-Btype’s axle housing. Using ANSYS workbench FEA simulated platform, according to the national standard of drive axle housing tests, three types thickness drive axle housing has simulated by FEA on 5.0mm, 6.0mm, 6.5mm inthe computer has included vertical curves just degree and start intensity analysis. Static analysis of result indicates that the perpendicularityintensity and fatigue strength of the 5.0mm axle housing is unqualified, 6.0mm, 6.5mm two types’ axle housing come up to the national standard. End, wedge bonding engineering solid instance the lapse that made bridge housing analysis, finding out the reason of bridge housing lapse is perpendicular stat intensity not enough and some assembly part stress over big. And the submissions correspond of betterment opinion to provide a reference.KEY WORDS: Drive axle housing, ANSYS Workbench, The vertical curves just a degree, Quiet intensity, Failure analysisII洛阳理工学院毕业设计(论文)目录前言 ........................................................................... ....................... 1 第1章绪 (2)1.1汽车桥壳的分类和机构特征概述 (2)1.2.1 国外CAE的发展和现状论述 ..................................... 3 1.2.2国内CAE分析的发展和现状 ..................................... 4 1.3 本课题的工程背景和研究意义 ............................................. 4 1.4 本文的主要研究内容和技术路线 (5)1.4.1 本文的主要研究内容...................................................5 1.4.2 技术路线流程图........................................................... 5 1.5 小结 ........................................................................... ............. 6 第2章有限元基本方法和桥壳有限元模型. (7)2.1 有限元基本方法及其计算工具简介 (7)2.1.1 有限元方法及其理论...................................................7 2.1.2 ANSYS系列通用有限元软件 ...................................... 8 2.2 14A-B型汽车桥壳的实体模型和有限元模型 .. (10)2.2.1 桥壳实体模型 ............................................................ 10 2.2.2 有限元模型、网络划分和单元介绍 ......................... 11 2.2.3 驱动桥桥壳模型材料介绍......................................... 12 2.3 小结 ........................................................................... ........... 12 第3章驱动桥的受力特征及结构静力分析.. (14)3.1 汽车驱动桥桥台试验 (14)3.1.1 驱动桥桥壳垂直弯曲刚度和静强度试验简介 ......... 14 3.1.2 垂直弯曲刚度和静强度试验评估指标 ..................... 14 3.2 桥壳受力特征.. (15)3.2.1 约束情况 (15)3.2.2 载荷施加方式 ............................................................16 3.3 有限元分16III1.2 汽车桥壳CAE分析的研究和发展 (3)洛阳理工学院毕业设计(论文)3.4 小结 ........................................................................... ........... 18 第4章静力分析结果 (19)4.1 垂直弯曲刚度分析结果对比...............................................19 4.2 垂直弯曲静强度分析结果对比 ........................................... 22 4.3 小结 ........................................................................... ........... 25 第5章桥壳失效原因及改进意见 (27)5.1 分析失效原因的目的........................................................... 27 5.2 分析的一般步骤 (27)5.3 失效原因及改进意见........................................................... 27 5.4 小结 ........................................................................... ........... 28 结论 ........................................................................... ..................... 29 谢辞 ........................................................................... ....................... 30 参考文献 ........................................................................... ................. 31 附录 ........................................................................... (32)IV洛阳理工学院毕业设计(论文)前言汽车驱动桥是汽车主要的传力件和承载件,它不仅要把发动机输出的扭矩传递到车轮以驱动汽车行驶,还要承受汽车以及路面的各种力和扭矩,因此要有足够的强度、刚度和疲劳强度。
基于UG的装载机驱动桥壳有限元分析
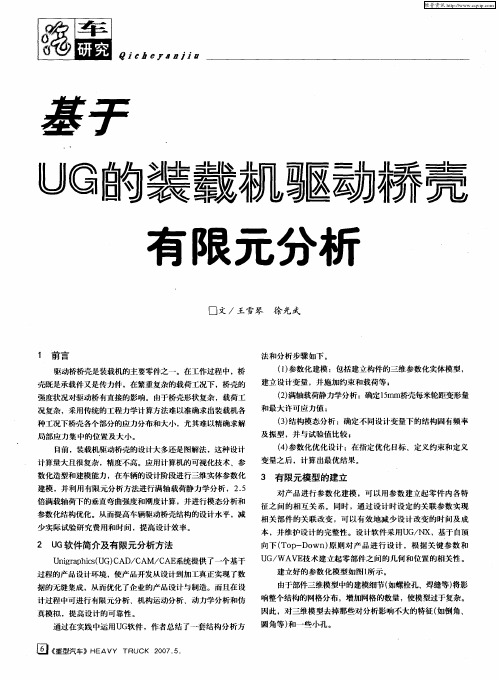
图 2 有限元模型
力【 s ol o
4 驱 动桥壳 有 限元分析
4 1 有限元分析方案 . 由于前驱动桥壳 是通 过螺栓 与车架刚性联 接 ,而载荷作
用的力 、弯 矩和扭矩 等是经过车轮及 轮边减速器 等传递到桥
壳 的 法 兰端 面 上 。因 此 ,在 桥 壳 有 限 元 分 析 中 ,法 兰 端 面 处
参 数化 结 构 优 化 。从 而 提 高 车辆 驱 动 桥壳 结 构 的 设 计 水平 ,减
() 4 参数化优化设计 :在指定优化 目标、定义 约束和定义
变量 之 后 ,计 算 出最 优 结 果 。
3 有 限 元模型 的建立
对产 品进 行参数化建模 ,可以用参数建立起 零件 内各特
征 之 间 的 相互 关 系。 同时 ,通 过 设 计 时 设 定 的关 联 参 数 实 现
相关部件 的关 联改变 ,可 以有效地减少设 计改变的时 间及成 本 ,并 维护设 计的完整性。设计软件采用U / G NX,基于 自顶
少实际试验研究费用和时间 ,提高设计效率 。
2 G u 软件简介及有限元分析方法
U irp i ( .C ng a hc UG) AD/ AM/ AE系统提供了一个基于 s C C
为载荷作用位 置 ,而在变截 面箱形梁 与车架联接处 表面为 固 定约束 面 ,即在约 束面上 的所 有节点 为零位 移点 ,如 图3 所
松 比为0 3 . ,许用应 力为【 s 0 ~7 9 o] 0 8 M阳 。 =4
图 1 参数化模型
4 2 结构静力学分 析 . 4 2 1 满载运行 紧急制动工况 ..
从图4 、图5 可以看 出,桥壳在工况 I中受力变形 ,其最大 的位 移处于桥壳的法兰端 面,为1 1 2 .4 mm,最小的位 移是被 约束的变截 面箱形梁与车 架联接处表 面地 方。每米轮距 的变 形量 为 112 .4mm/ .9 m=0 8 1 13 1 .2mm/ m,远小于 国标规定的 15 .mm/ m。根据第四强度理论 ,最大Vo ss n mi 等效应力为 e 364 a 8 .MP ,出现在变截 面箱形梁 约束 处的附近 ,小 于许用应
轿车差速器的设计与桥壳有限元分析
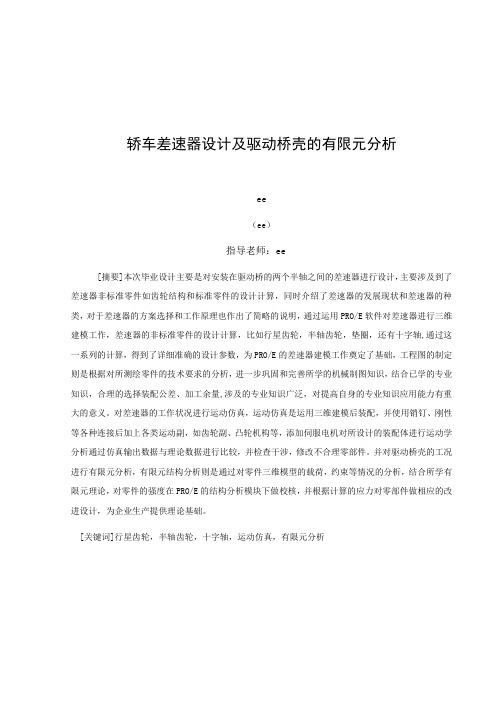
轿车差速器设计及驱动桥壳的有限元分析ee(ee)指导老师:ee[摘要]本次毕业设计主要是对安装在驱动桥的两个半轴之间的差速器进行设计,主要涉及到了差速器非标准零件如齿轮结构和标准零件的设计计算,同时介绍了差速器的发展现状和差速器的种类,对于差速器的方案选择和工作原理也作出了简略的说明,通过运用PRO/E软件对差速器进行三维建模工作,差速器的非标准零件的设计计算,比如行星齿轮,半轴齿轮,垫圈,还有十字轴,通过这一系列的计算,得到了详细准确的设计参数,为PRO/E的差速器建模工作奠定了基础,工程图的制定则是根据对所测绘零件的技术要求的分析,进一步巩固和完善所学的机械制图知识,结合已学的专业知识,合理的选择装配公差、加工余量,涉及的专业知识广泛,对提高自身的专业知识应用能力有重大的意义。
对差速器的工作状况进行运动仿真,运动仿真是运用三维建模后装配,并使用销钉、刚性等各种连接后加上各类运动副,如齿轮副、凸轮机构等,添加伺服电机对所设计的装配体进行运动学分析通过仿真输出数据与理论数据进行比较,并检查干涉,修改不合理零部件。
并对驱动桥壳的工况进行有限元分析,有限元结构分析则是通过对零件三维模型的载荷,约束等情况的分析,结合所学有限元理论,对零件的强度在PRO/E的结构分析模块下做校核,并根据计算的应力对零部件做相应的改进设计,为企业生产提供理论基础。
[关键词]行星齿轮,半轴齿轮,十字轴,运动仿真,有限元分析The Design of Vehicle’s Differential and the Finite Element Analysis about the Driving Axle Housingee(ee )Tutor: eeAbstract:The design of the main drivers on the installation of the bridge in between the two axle differential design, mainly related to the differential structure ofnon-standard parts such as gear parts and standards for design and calculation, but also introduced the development of differential status and the type of differential. For differential selection and the principle of the program have also made a brief note. Building the differential’s 3D modeling through the use of PROE sofeware , differential calculation in the design of non-standard parts, such as planetary gear, axle shaft gear, the gasket , and cross axis, through a series of calculation, get the accurate and detailed design parameters, for PRO/E differential modeling work laid a foundation , formulation is based on the engineering drawing for the parts of surveying and mapping analysis of the technical requirements of the further consolidate and improve the knowledge of mechanical drawing, combining has to learn professional knowledge , Reasonable selective assembly tolerance allowance involves extensive professional knowledge, to improve their professional knowledge application ability is of great significance. On the working conditions of differential motion simulation, motion simulation is to use 3 d modeling after assembly, and use the pin after connected rigid, etc and all kinds of motion pair, such as gear CAM mechanism, etc. Add by design of the servo motor assembly kinematic analysis by comparing the simulation output data with theoretical data, and check the interference, modify unreasonable parts. And carries on the finite element analysis on the operation condition of the drive axle housing, the finite element structure analysis is based on a load of parts 3 d model, the constraints such as case analysis, combined with the finite element theory, we learned about the strength of the parts under the structure analysis module of PRO/E to do checking. And according to the calculation of the stresses on the parts to do the corresponding improvement design .Provides the theoretical foundation for the enterprise productionKeywords:planetary gear , axle shaft gear, universal joint pin, exercise simulation, finite element analysis目录1绪论 (1)1.1汽车差速器研究的背景及意义 (1)1.2汽车差速器国内外研究现状 (1)1.2.1国外差速器生产企业的研究现状 (1)1.2.2我国差速器行业市场的发展以及研究现状 (2)1.3汽车差速器的功用及其分类 (3)1.4毕业设计初始数据的来源与依据 (4)2 差速器的设计 (5)2.1对称式行星齿轮的设计计算 (5)2.1.1对称式差速器齿轮参数的确定 (5)2.1.2差速器齿轮的几何计算图表 (11)2.1.3差速器齿轮的强度计算 (12)2.1.4差速器齿轮材料的选择 (13)2.1.5差速器齿轮的设计方案 (14)2.2差速器行星齿轮轴的设计计算 (14)2.2.1行星齿轮轴的分类及选用 (14)2.2.2行星齿轮轴的尺寸设计 (15)2.2.3行星齿轮轴材料的选择 (15)2.3差速器垫圈的设计计算 (15)2.3.1半轴齿轮平垫圈的尺寸设计 (16)2.3.2行星齿轮球面垫圈的尺寸设计 (16)3 差速器部分三维建模 (17)3.1 三维软件PRO/E的介绍 (17)3.2 各零部件实体模型的建立 (17)3.3 差速器部分总装图 (18)4 工程图的制作 (20)5 十字轴与行星齿轮加工工艺的制定 (21)5.1 十字轴 (21)5.1.1零件的材料及技术要求的确定: (21)5.1.2加工工艺流程的制定 (21)5.1.3各个工序定位基准的选择 (21)5.1.4工序及尺寸公差的确定 (22)5.1.5热处理 (24)5.1.6机加工设备的选择 (24)5.2 行星齿轮 (24)5.2.1零件的材料及技术要求的确定 (24)5.2.3各个工序定位基准的选择 (25)5.2.4工序及尺寸公差的确定 (25)5.2.5热处理 (26)5.2.6机加工设备的选择 (26)6 差速器运动仿真分析 (27)6.1 差速器原理 (27)6.2差速器运动的分解 (28)6.3 机构运动仿真 (29)6.4 获取仿真结果及分析 (29)7 驱动桥壳有限元结构分析 (31)7.1 桥壳有限元模型的建立 (31)7.2 桥壳有限元分析 (31)7.2.1满载运行紧急制动工况 (32)7.2.2通过不平路面最大垂直力工况 (33)8 结语 (35)8.1 主要内容及成果 (35)8.2 感受与展望 (35)参考文献 (37)附录1 (39)附录2 (47)1绪论1.1汽车差速器研究的背景及意义汽车行业发展初期,法国雷诺汽车公司的创始人雷诺发明了汽车差速器,汽车差速器作为汽车必不可少的部件之一曾被汽车专家誉为“小零件大功用”。
驱动桥壳有限元结构分析

第1章绪论驱动桥壳是汽车的主要零件之一,作为主减速器、差速器和半轴的装配基体,它是汽车的主要承载件和传力件,支撑着汽车的荷重,并将载荷传给车轮。
在实际行使中,作用在驱动车轮上的牵引力、制动力、横向力,也是经过桥壳传到悬挂及车架或者车厢上的。
同时,驱动桥壳的使用寿命直接影响汽车的有效使用寿命。
因此,合理地设计驱动桥壳,使其具有足够的强度、刚度和良好的动态特性,减少桥壳的质量,有利于降低动载荷,提高汽车行驶平顺性和舒适性。
1.1国内外研究现状过去工程师在对简单机械结构进行分析时,都要进行一系列的简化与假设,再采用材料力学、弹性力学或塑性力学的理论进行分析。
随着工业技术的迅速发展,有越来越多的复杂结构,包括复杂的几何形状、复杂的受力状态等问题需要去分析研究,而在工程实际中,这些复杂的问题往往不能求出它们的解析解。
[1]要解决这些问题通常有两种途径:一是试验法,通过提出一定假设,回避一些难点,对复杂问题进行简化,使之成为能够处理的问题[2]。
然而,由于太多的简化和假设,通常会导致极不准确甚至错误的解答。
因此,另一种行之有效的途径就是尽可能保留问题的实际状况,寻求近似的数值解。
而在众多的数值方法中,有限元分析法因其突出的优点而被广泛地应用。
经过半个多世纪的实践,有限元法已从弹性力学平面问题扩展到空间问题、板壳问题;从静力问题扩展到动力问题、稳定问题和波动问题;从线性问题扩展到非线性问题;从固体力学领域扩展到流体力学、传热学、电磁学等其他连续介质领域;从单一物理场计算扩展到多物理场的耦合计算[4]。
它经历了从低级到高级、从简单到复杂的发展过程,目前已成为工程计算最有效的方法之一。
2001年,重庆大学的褚志刚等学者对某后桥壳进行了静强度分析计算,结果表明该后桥壳静态分析的应力分布合理,在实际破坏区域内的静态应力很小,但分析结果与该车在实际道路试验中的破坏不相吻合。
通过模态分析发现,其前九阶频率与路面谱频率范围重合,模态振型尤以后背盖与上下壳体的焊接处、半轴套管内端直径渐变处、上壳体倒圆处的变形较大;当桥壳和弹簧系统在垂直激励作用下时,即通过动态响应分析法,找出桥壳上的动应力集中区,确认破坏的确切位置,与实际情况相吻合。
- 1、下载文档前请自行甄别文档内容的完整性,平台不提供额外的编辑、内容补充、找答案等附加服务。
- 2、"仅部分预览"的文档,不可在线预览部分如存在完整性等问题,可反馈申请退款(可完整预览的文档不适用该条件!)。
- 3、如文档侵犯您的权益,请联系客服反馈,我们会尽快为您处理(人工客服工作时间:9:00-18:30)。
基于参数化设计的驱动桥壳有限元分析系统设计
一、前言
驱动桥壳是安装主减速器、差速器、半轴、轮毂和悬架的基础件,主要作用是支承并保护主减速器、差速器和半轴等零部件。
它和从动桥一起承受汽车质量,使左、右驱动车轮的轴相对位置固定,汽车行驶时,承受驱动轮传来的各种反力、作用力和力矩,并通过悬架传给车架。
桥壳可被视为一空心横梁,两端经轮毂轴承支承于车轮上,在钢板弹簧座处桥壳承受汽车弹簧上的载荷,而沿左右轮胎的中心线,地面给轮胎以反力(双轮胎时则沿双胎中心),桥壳则承受此力与车轮重力之差值。
由于其形状复杂、应力计算困难,又要求具有足够的强度和刚度,传统设计方法不免有很多局限性。
本文以某系列整体式桥壳为例,利用软件的二次开发功能便捷实现桥壳在某特定工况下的设计与分析。
二、桥壳参数化的基本内容
1.设计目标
以冲击载荷工况为例,由于桥壳在承受最大铅垂力时,危险断面出现在钢板弹簧座附近,因此以桥壳的轮距(方断面长、圆断面长)和断面(高度、厚度)为参数化设计目标。
此时
的弯曲应力为
(1)
式中,G是汽车满载静止于水平路面时驱动桥给地面的载荷;B是驱动车轮轮距;s 是驱动桥壳上两钢板弹簧座中心间的距离;kd是动载荷系数,对载货汽车取2.5;Wv是桥壳在
危险断面处的垂向弯曲截面系数,如表所示。
表钢板弹簧座附近的断面形状及截面系数
2.参数化的基本方法
桥壳参数化采用的是建立零件的参数化数字模型,通过修改关键尺寸参数的方法实现新零件模型建立和设计。
首先在Pro/ENGINEER中建立驱动桥壳三维模型(如图1所示),提取钢板弹簧座附近方形断面和圆形断面的尺寸变量,利用Visual Basic语言将用户输入的界面信息传递给相应的变量,然后驱动再生进程,进行修改设计。
图2为Visual Basic
设计的桥壳参数化界面。
三、参数化的程序实现方法
1.软件支持和设计思想
Automation Gate way for Pro/ENGINEER Wildfire是基于Microsoft的
ActiveX技术开发而成的,它允许Pro/ ENGINEER直接集成任何支持ActiveX的应用软件。
Automation Gateway允许开发者使用多种编程语言进行开发工作。
设计思想:在Visual Basic中建立主窗体、桥壳窗体和桥壳类,桥壳窗体用来操作参数化界面,桥壳类用来修改界面传递的关键尺寸,主窗体用来联系桥壳与其他零件。
在Visual Basic中引用GWAX Rand Automation Gateway项,在桥壳类中声明对象Public
rgateway As New Gw ay AX,就可以通过对象Grate way操作Pro/ENGINEER变量。
考虑到可扩展性,因此为每个零件单独建类,方便数据管理,同时窗体和类一一对应,完
成窗体变量到类变量的实时数据传递。
2.参数化流程和方法
以图2 所示的设计界面中“修改圆形断面后的轮距”项为例,输入修改参数的数值为1870,点击“确定并关闭” 按钮后,程序将按照如图3所示的流程完成设计任务。
应用Model Retrieve () 和Session Set Current Model()函数调出需要修改的零件样本,提取该零件要修改尺寸对应的变量,Param Set Value()函数给这些变量赋值,关联参数调整计算结束后,通过Param Set Value()完成数据的更新,并通过ModelRegenerate()更新模型、再生零件,可完成新零件的设计。
修改后的桥壳需进行干涉检验,首先将桥壳自动装配到总成中,再检验装配体干涉情
况。
自动装配的实现参考代码为:
l Gw Err = rgateway 1 . ModelRetrieve("csban.asm")
l Gw Err = rgate way 1 . SessionSetCurrentModel("csban.asm")
l Gw Err = rgate way 1 .
ModelRetrieve("qiaoke.prt")
lGwE rr = rgateway 1 . A smA dd Cons tr aint ( lID ( 1 ) , A LGN , " qiaok e .
prt","FRO NT","csban.asm/dongban. prt","FRONT", 0)
lGwE rr = rgateway 1 . A smA dd
Cons tr aint ( lID ( 2 ) , A LGN , " qiaoke .
prt","TOP","csban.asm/dongban.prt",
"TOP", 0)
l Gw Err = rgate way 1 . AsmAddComponent(lID(4), "csban. asm", "qiaoke.prt")
调用AsmAddConstraint()函数给要装配的零件施加约束,再采用AsmAddComponent()组装,即可完成装配。
干涉检验:利用程序向Pro/ENGINEER 的
config.pro中写入宏操作代码并执行即可:
WriteToFile"config.pro","mapkey q @ MAPKEY_NAME全局
涉;~Select`main_dlg_cur` MenuBar1`1
`Analysis`;\", True
WriteToFile"config.pro","map
key(c ontinued)~S elec t`main_dlg_
cur``Analysis.cas_na_geometry`;\", True
SendKeys "{q}", True
执行以上代码,可检验修改后的桥壳是否与其他零件产生干涉,如干涉,则应根据干涉程度返回界面重新修改。
修改后的零件还需进行有限元分析,进一步验证零件修改的可靠性。
在已安装ANSYS的机器上设置ANSYS与Pr o/ENGINEE R的连接,执行Send Keys"{a}",True,系统便会自动执行类似干涉检验的一段代码,从而将零件自动导入
ANSYS,图4为进行有限元分析前的工况选择。
四、桥壳有限元分析
将三维模型导入到ANSYS后,选择10节点的92号单元,对其进行网格划分,得到15,149个单元,30,761个节点。
有限元模型如图5所示。
该载货汽车满载轴荷G为0.98x105N,修改后的轮距B 为1.87m,板簧间距为1.03m,桥壳材料为16MnL,弹性
模量为206GPa,泊松比为0.29。
施加在两个钢板弹簧座上,最大垂向力为:
(2)(3)
式中:Z L、Z R是分别施加在左右钢板弹簧上的载荷;a 是左边钢板弹簧座中点与桥壳中央点的距离;b 是右边钢板弹簧座中点与桥壳中央点的距离。
由式(2 )和式(3)可以求得。
冲击载荷下桥壳的边界条件:垂向力平均施加到弹簧座上的各个节点,将桥壳两端车
轮中心线处全部约束。
将以上信息编写为APDL命令流的方式:在文本文件*.txt中进行代码编写,通过Sendkeys()函数把"/input,...,txt"发送到GUI界面中的命令窗口,进行Pro/ENGINEER工作目录下APDL命令流文本的调用,完成零件主要接触面的应力、应变分析。
图6和图7为选择工况2后ANSYS从一系列对应不同工况的命令流文本中,选择调用*.txt冲击载荷命令流文本进行修改分析的结果。
(1)变形分析:垂向位移最大值为0.3614mm。
除去轮距得0.1933mm,此值小于每米
轮距最大变形1.5mm(QC/ T534-1999)的要求。
(2)应力分析:在冲击荷载作用下,其最大应力值为165.69M Pa,发生在钢板弹簧座附近。
大部分部位的应力值在36.821~73.641M Pa之间,应力集中部位的应力值大约在128.87MPa左右,此值小于桥壳材料16MnL的许用应力211~238MPa,因此所设计的桥
壳强度和变形均符合要求。
五、结论
通过对桥壳结构的设计可见,利用CAD软件的参数化设计,结合CAE软件的仿真分析计算,能够有效地提高设计效率、降低设计成本、获得有效分析数据。
其设计方法和设计思想不仅适用于汽车驱动桥零部件的设计开发,还为其他产品设计分析系统的开发提供
了参考。