加氢裂化装置用能分析及节能
加氢裂化装置的能耗分析及节能措施探讨

1 1 工 艺流 程布 置 .
根 据 催 化 剂 选择 、 料 和 目的 产 品 的 不 同 , 氢 裂 化 装 置 常 原 加 用 流 程 大 致 可 以 归 纳 为 三 类 , 单 段 一 次 通 过 流 程 ; 段 、 剂 即 两 双 全循环流程和双剂 串联 一次通 过或 全循 环流 程 ; 资料 报道 _ 单 2
o a e Ene g e s r s fS v r y M a u e
X U e — i n W i—x a g
( i h e oh m cl o p n ,P t C ia La n gP ni 2 0 2 hn ) La eP t c e i m a y er hn , i i aj 1 4 2 ,C ia o r aC o on n
着反应器 的操作 时间增长 , 催化剂活性 逐渐下 降 , 须提 高催 化 必 剂使用温度 , 以补偿 活性 的损失 , 时裂化 反应 相应 增加 , 应 此 反 热增大 , 有效 回收的热 量增 加 , 能耗 降低 ; 同时控 制催 化剂 床 但 层 温 度 的冷 氢 量 有 所 增 大 , 环 氢 压 缩 机 流 量 相 应 增 加 。 循
Absr c t a t:T a tr fe tn h n r y c n u to fh d o r c i g u i we e a ay e u h a r c s o l y hef co s afc i g t e e e g o s mp in o y r c a k n n t r n lz d s c sp o e sf w a — l o ta d c n iin o p r t n ec u n o d to fo e a i t .Al k n fs vng e e y me s r swe e a v n e o e u i n r o s mp i n i o l i dso a i n g a u e r d a c d f rr d cnge e g c n u to n- y c u i g u i g h ts p rt r a d i g d sg a e e e g q i me t o x mp e t e lq i u b n l d n sn o e a ao nd a d n e in s v n r e u p n s fr e a l h i u d t r i e,se e s c pa i y tpls a ct y r g l t n s se a d S n,i r e o f r ih r fr n e f rsmia kn v ru i. e u a i y t m n O o o n od rt u n s ee e c i lr ma ig o e n t o Ke y wor ds:e eg o s mp i n;s v n r a u e ;hy r c a ki g n r c n u to y a e e e g me s r s y d o rc n
140_10_4t_a加氢裂化装置节能增效分析

1前言高桥分公司加氢裂化装置于2004年10月22日投产,设计规模为140×104t/a ,采用双剂串联一次通过的加氢裂化工艺。
反应部分采用国内成熟的炉前混氢方案;分馏部分采用脱丁烷塔加常压塔出柴油方案;吸收稳定部分采用轻石脑油作吸收剂的方案;脱硫部分采用有机脱硫剂的方案。
该装置采用中油型生产方案,以最大限度的生产中间馏分油,产品柴油、航煤调合后出厂,重石脑油作为连续重整原料,轻石脑油作为化工原料出厂。
本装置原料来自3号蒸馏装置的减压蜡油和延迟焦化装置的焦化蜡油,氢气来自制氢装置,纯度为99.9%。
本装置使用抚顺石油化工研究院开发的FZC 系列保护剂、FF-26加氢裂化预精制催化剂和3976加氢裂化催化剂。
为了适应加工含硫原油的需要,该装置于2007年10月进行改造,增加循环氢脱硫设施,对部分管线材质升级,2008年5月30日开工正常。
目前装置生产稳定,处理原料硫含量在1.7%左右。
2节能增效分析加氢裂化装置的节能降耗主要体现在对电、蒸汽、燃料、氢气的节约上。
改进换热流程、优化操作、产品综合利用是加氢裂化装置节能的重点。
2.1氢耗加氢裂化装置是生产优质产品的重要炼油工艺,其进料范围宽,操作模式灵活,但需消耗大量氢气。
高桥分公司加氢裂化装置根据不同原料及转化深度,以及不同的产品方案,氢耗量在320~380m 3(标准)新氢/t 进料。
根据2008年10月的标定数据进行经济核算可知,当氢气价格为15000元/t 时,氢气成本约占装置生产总成本的8%。
故欲提高装置效益,关键之一是降低氢气成本,而对氢耗进行深入分析,有助于提出进一步降低氢耗的具体措施。
装置氢耗包括化学氢耗、溶解氢耗与泄漏氢耗。
2.1.1化学氢耗化学氢耗为化学反应所消耗氢气,约占总耗氢的85%左右,它与催化剂性质,催化剂使用时间、原料及产品方案有关,一般情况下,当催化剂品种一定时,随催化剂使用时间而增加,所以运行末期比初期要增加15%左右。
加氢裂化装置能耗分析

冷高分+单塔汽提, 公用工程
12.91
8.0
300
中石油广 西钦州
240
热高分+双塔汽提 +循环氢脱硫, 公 用工程
11.43
7.5
350
1
加氢精制装置设计能耗分析
各炼油厂加氢精制装置原料主要性质
国内加氢裂化装置原料性质对比表 混合原 料硫含 量 ppm
24200
国内新建或在建 加氢裂化装置
组成(万吨 组成(万吨/a) 焦化汽油 焦化柴 油
中石油大连石化
混合去石脑油加氢再加工分离液化气 、轻重石脑油。
去催化裂化
装置原料性质、 装置原料性质、产品分布及质量 对装置工艺技术条件及用能分析 由以上原料与产品分布及规格上的差异定性分析,导致 装置工艺设计技术参数上的不同,主要技术参数对比如下:
装置名称 氢耗 循环氢油比 反应器入口压 力 循环氢脱硫 t胺液 原料 胺液/t原料 胺液 油 反应器总液 时空速h-1 时空速
项目 压力能回收 回收低温热 回收低温热 回收低温热 能耗增加Kg标油/t原料 ( 泉州石化-大连石化) -0.66 1.63 12.32 2.22 备注 回收了高能级能量 用来加热热水或除盐水外送 发1.0MPa蒸汽 发0.4 MPa蒸汽
总结
• 从收集到的国内加氢裂化装置资料来看, 装置原料性质、目的产品及收率是影响装 置能耗的主要因素,以中馏分油及尾油为 产品方案的装置,其设计压力、氢耗明显 低于我司以重石脑油、柴油为目的产品的 加氢裂化装置,进而影响到油品、补充氢 升压电耗增加。
中化泉州石化
3.08
738/1348/843 R101HT/R101HC /R102HC 1500
17.093/16.607 R101HC/R102HC 15.50
浅谈石油化工加氢裂化装置的能耗分析及节能

浅谈石油化工加氢裂化装置的能耗分析及节能发布时间:2022-07-27T06:00:39.727Z 来源:《工程管理前沿》2022年第6期作者:邢振德[导读] 石化工业是推动国民经济发展的一个重要领域,同时也是人们日常生活中不可缺少的一部分。
邢振德中国石油化工股份有限公司天津分公司炼油部联合六车间?天津市300270摘要:石化工业是推动国民经济发展的一个重要领域,同时也是人们日常生活中不可缺少的一部分。
然而,在使用石油的过程中,不仅要耗费大量的能源,而且还会排放出一些有害的废气,对环境造成威胁。
在石化工业中,加氢裂化设备可以降低对石油的污染,实现能源节能和环保。
因此,我们必须对其能耗进行分析。
关键词:石油化工行业;加氢裂化装置;能耗分析及节能随着石化工业的迅速发展,我们国家的经济实力和人民的生活质量都得到了极大地提升。
我们每天都要用到石油,在使用的时候,会释放出大量的废气,污染环境。
而加氢裂化设备是石化工业中常用的一种设备,其在石化工业中的应用也起着举足轻重的作用。
因此,加氢裂化设备的能量消耗是一个非常重要的问题,必须要对其进行深入的分析,才能将其推广到整个石化行业,再加上如今是一个注重节能和环境保护的年代,加氢裂化设备的节能效果也非常的重要。
一、石油化工加氢裂化装置的能耗分析加氢裂化设备是目前石化工业中使用最多的设备,它能有效地提高原油精制过程中的转换效率,并能得到优质的轻油。
然而,目前的加氢裂化设备在能耗、节能等方面的配置相对较少,并没有达到最大限度地节能减排,因此,必须通过对加氢裂化设备的能耗进行分析,寻找节能的方法。
而且目前的设备能量消耗也分为三大部分,能量的转化、利用和回收,但是从回收利用的角度来看,设备的能量利用率并不高,只有58.1%的能量回收利用,剩余的能量全部被浪费掉了。
所以在能量分析的时候,必须要更加的严谨,更加的规范,这样我们就可以对设备进行进一步的改造,从而达到节能的目的。
加氢裂化装置降耗分析及节能措施
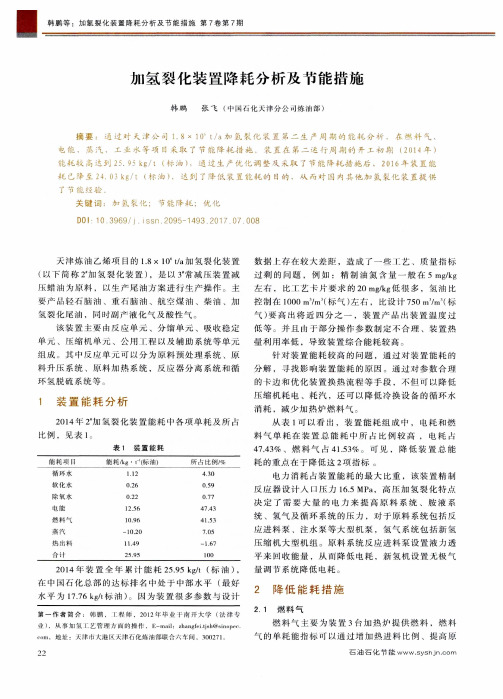
管理 ・ 实 跬 ,Ma n a g e me n t &P r a c t i c e
图1 2 加 氢 裂 化 装 置 反 应 部 分 换 热流 程
料 温 度 、提 高 原 料 换 热 终 温 ,优 化 加 热 炉 操 作 、 提 高加 热 炉热 效率 等措 施 来 降低 。
蜡 油 为 原 料 , 以 生 产 尾 油 方 案 进 行 生 产 操 作 。 主 氢裂化 尾 油 , 时 副 产 液 化 气 及酸 性 气 。 左 右 , 比工 艺 卡 片 要 求 的 2 0 m g / k g 低 很 多 ,氢 油 比
要 产 品轻 石脑 油 、重石 脑油 、航 窄煤 油 、柴油 、加 控 制 在 1 0 0 0 1 3 1 ' / m ( 标气 ) 左 有 ,比设 计 7 5 0 m / m ( 标 气) 要 高 出将 近 四 分 之一 ,装 置 产 晶 装 置温 度 过
韩 鹏 等 :加 氢 裂 化 装 置 降 耗 分 析 及 节 能 措 施 第 7 卷第 7 期
加 氢 裂 化 装 置 降 耗 分 析 及 节 能 措 施
下
韩 鹏
张飞 啦
叭 ( 中l i 化天津分公司炼油部 )
.
过对 天 津公 司
工业 水 等 项 目
2 5. 9 5 kg /t 【 3 kg /t ( 标 油
低 等 。并 且 F } = i 于 部 分 操 作 参 数 制 定 不 合 理 、 装 置 热 该 装 置 主 要 南 反 应 单 元 、分 馏 单 元 、 吸 收 稳 定
单 元 、压 缩机 单 元 、公 用 l 程 以及辅 助 系统 等单 元 量 利用 率低 ,导致 装 置综 合能 耗较 高 。 组成 。其 中反 应 单元 可 以 分 为原 料预 处 理 系统 、原
加氢裂化装置用能分析及节能措施

设计 1200000
769.9 173.1 878.2 0.0 30.5 6.7 19.7 619.3 111.2 -708.8 -13.0 1886.8
2008 年 860338
66
434.9 1025.1
0.04 35.4 15.7 13.9 740.0 60.7 -791.0 -11.4 1523.3
26/FC-26 一 段 串 联 全 循 环 加 氢 裂 化 工 艺 流 程 , 装 置 开 工 后 能 耗 一 直 处 于 较 高 水 平 。 通 过 对 能 耗 组 成 分 析 , 发 现 装 置 实 际 能 耗 中 电 耗 占 46%~49% , 燃 料 消 耗 占 23%~29% , 蒸 汽 消 耗 占 14%~16% , 与 设 计 值 差 距 较 大 。 通 过 对 装 置 高 压 贫 胺 液 泵 更 换 小 叶 轮 、 新 氢 压 缩 机 应 用 Hydro COM 气 量 调 节 系 统 , 采 取 原 料 热 进 料 , 提 高 新 氢 纯 度 等 节 能 改 造 , 以 及 维 持 适 宜 氢 油 体 积 比 ( 约 为 1000) , 降 低 热 高 压 分 离 器 和 分 馏 进 料 加 热 炉 温 度 , 降 低 主 汽 提 塔 压 力 , 提 高 装 置 负 荷 率 等 优 化 措 施 , 装 置 能 耗 从 2008 年 的 1523MJ/t 降 低 到 2010 年 的 1150MJ/t 。 同 时 指 出 , 加 氢 裂 化 装 置 下 一 步 可 以 通 过增加变频电机、实施低温热利用、采用旋流脱烃等措施进一步降低能耗。
加 氢 裂 化 装 置 2006 年 、2007 年 的 综 合 能 耗 较 高 ,分 别 为 1938.97MJ/t 和 1640.09MJ/t,与 国 内 同 类 装置相比,差距较大。 降低能耗是提高装置运行水 平的重要任务。 2.1 加氢裂化能耗组成
1400kt/a加氢裂化装置节能增效分析

高桥 分公 司 10 k/ 加 氢 裂 化装 置 于 2 0 4 0 ta 04 年 8月 1 0日建 成 中交 ,0 4年 1 20 0月 2 2日投产 。 加氢 裂化 装置 至 2 0 0 8年 9月 3 0日, 效作 业 天 有 数 为 3 1 6天 , 加工原料 油 1 7 5 8 , 中减 压 5. 共 0 3 4 t其 蜡油为 1 6 6 6 , 化 蜡 油 为 19 2 , 用 氢 气 0 1 1 t焦 13 t 耗
对 节约能 源的具体 途径进 行分析 。
2. 氢 耗 1
尤其是 随着炼 油厂 加 工原 油 的劣 质化 , 原料 蜡油 密 度变 重 , 氮 含 量 增加 , 得反 应 温 度 越 来越 硫 使 高 , 环氢 量 增加 , 料气 、 循 燃 中压蒸 汽 的消耗 也 随 之增 大。对加 氢裂化装 置能源 消耗情况 进行深 入 分析 , 找出节 约能源 消耗 的措施 , 合理利 用加氢 裂 化产 品 , 装置将 发挥更好 的经济 效益 , 同时对加 氢
油 化 工 集 团 公 司 抚 顺 石 油 化 工 科 学 研 究 院
装置 氢耗包 括 化学 氢 耗 、 溶解 氢 耗 与泄 漏氢 耗 。化学 氢耗 为化 学 反应 所 消耗 氢气 , 占总耗 约 氢的 8 %左 右 , 与 催 化剂 性 质 , 化 剂 使 用 时 5 它 催 间 、 料 及 产 品 方 案 有关 , 般 当催 化 剂 品 种一 原 一 定, 随催 化剂使 用时 间而增加 , 以运行 末期 比初 所
正常, 改造后 能 处理 高 硫原 料 。主要 反 应 部分 增
加循 环氢脱硫设 施 ; 分管线材 质升级 , 部 目前装 置
生产 正常 , 理原料硫 含量在 17 。 处 .%
加氢裂化装置节能优化分析

加氢裂化装置节能优化分析随着科技的不断发展和进步,各企业间的竞争日趋白热化,这就对提高企业效益提出了更高的要求,加氢裂化(Hydrocracking,HC)技术是现代炼油和石油化工企业油、化、纤结合的核心工艺之一,HC 装置的操作状况和用能水平对企业能耗及经济效益有着重要影响,其具有加工原料范围广、产品质量好、液体收率高、生产灵活性大等特点。
标签:加氢裂化;能耗;节能进入二十一世纪后,各国都将实施经济增长与保护环境并重的可持续发展战略,既重视经济效益也重视环境效益。
为保护生态环境,对油品的质量要求将越来越严,生产清洁油品已经是大势所趋。
此背景下,我国炼油工业也加快了加氢裂化技术开发的步伐,而科学合理的分析加氢裂化装置的能量平衡,可以有效地降低加氢裂化装置的能耗,对加氢裂化装置进行节能技术的研究仍是各加氢裂化装置的重要课题。
1 加氢装置能耗的状况分析1.1 能耗特点加氢裂化工艺过程主要包括催化加氢反应、油品分馏和氢气高压压缩等过程。
装置用能有如下特点:1.1.1 总输入能量多,升压用电在能耗中所占比例大。
加氢裂化装置进料和氢气的升温、升压均需要供入大量能量,循环氢压缩机用3~5MPa 蒸汽驱动,能耗较高。
加氢裂化装置反应压力高,進料和氢气需由电动的进料泵和补充氢压缩机进行升压,电耗较高。
1.1.2 化学耗氢量与反应苛刻度(或转化率)有关。
加氢裂化反应过程苛刻度高(转化率高),耗氢量大,所需补充氢压缩机功率大,压缩能耗也相应上升。
1.1.3 低温热多。
高能级的热量输入加氢裂化装置后,通过一系列的化学和物理过程,大部分转化成为低温热,即150摄氏度~200摄氏度以下油品的热量及排入大气的400摄氏度以下烟气热量等。
利用好这部分热量,也是降低装置能耗的一个重要方面。
1.2 影响能耗的因素1.2.1 工艺条件加氢裂化装置在催化剂确定后,影响加氢效果的主要工艺条件是反应压力、反应温度、空速和氢油比等,这些工艺条件与能耗有着直接的关系。
- 1、下载文档前请自行甄别文档内容的完整性,平台不提供额外的编辑、内容补充、找答案等附加服务。
- 2、"仅部分预览"的文档,不可在线预览部分如存在完整性等问题,可反馈申请退款(可完整预览的文档不适用该条件!)。
- 3、如文档侵犯您的权益,请联系客服反馈,我们会尽快为您处理(人工客服工作时间:9:00-18:30)。
1 前言
随着我国经济的快速增长 , 资源环境约束已成 为未来中国经济社会发展严峻挑战 。与此同时在国 际原油价格长期居高不下的情况下 , 石化企业面临 竞争和发展的压力日益增大 。 石油 、石化企业是耗 能大户 , 能耗费用占加工成本的比例最大 。 温家宝 总理 2006 年 3 月 5 日在十届全国人大四次会议上 的政府工作报告中提出 , “十一五”期间单位国内生 产总值能耗降低 20 %左右 , 2006 年单位国内生产总 值能耗降低 4 %左右 。 因此 , 节能降耗不仅 是石油 石化行业自身挖潜增效求发展的需要 , 也是完成国 家宏观发展目标的必然要求 。
第 25 2007
卷 年
, 总第 141 1 月,第1
期 期
《 节 能 技 术》 ENERGY CONSERVATION TECHNOLOGY
Vol .25 ,Sum .No .141 Jan .2007 , No .1
加氢裂化装置用能分析及节能
赵孟姣 , 陈保东 (辽宁石油化工大学 , 辽宁 113001)
(2)在现有的工艺条件和催化剂条件下 , 对本装 置能量转换环节中包含的加热炉 , 压缩机及泵做如 下改进 , 可减少总供入能量 。
(3)加热炉的节能 , 应控制好燃烧所使用的空气 量 , 空气过剩系数应控制在1 .05 ~ 1 .1ห้องสมุดไป่ตู้范围 , 满足完 全燃烧要求 , 从而减少了总供入能的量 。 适时对燃 料气的组成进行测定 , 确定合适供应空气量 , 满足燃
三台加热炉的燃料总量占总供入能的41 .29 %。 其中两台加热炉的热效率都达到了 80 %以上 , 三台 加热炉平均效率为大于 76 %, 比整个装置的能量转 化率低了 16 %, 而且是用能大户 , 可得出结论 , 提高 加热炉的热效率对提高整个装置的能量转换有很重 要的贡献 。
供入装置的电能占总供入能的13 .27 %。大部分 的电能都消耗在驱动设备上 。 在本装置的泵中 , 平 均效率 为24 .44 %, 最 高达 到 67 %, 而最 低 的只 有 7 .23 %。由此可知 , 泵的电机与泵绝大多数都是不相 配的 。 3 .2 能量利用环节
与传输 、工艺利用和能量回收三个环节 。依据 图 1 的用能原理图 , 进行加氢裂化装置的能量平衡测试 及用能分析 。 3 .1 转换环节
装置的总 供入能为79 087 .29 kW 。能量转换 环 节的能量效率为92 .47 %, 火用转换效率为75 .91 %, 说 明转换环节的能量和火用 效率很高 。 从能量平衡计 算结果看出 , 有5 954 .539 kW能量损失掉了 , 其中排 烟损失和无效动力损失都很大 , 它们都分别占热损 失的41 .82 %, 45 .13 %。从数 据上看 , 无效动力 损失 最大 。
Abstract :According to some refining industry practices , this paper analyses the hydrocracking equipment characteristics of energy balance .Based on it , this paper suggest saving energy ways and discuss its feasibility . Key words:hydrocracking ;energy balance ;saving energy
摘 要 :结合某石化企业加氢裂化装置的实际情况 , 通过装置的能量平衡测试 , 对加氢裂化装 置的用能特点进行量化分析 , 并以用能分析为依据 , 探讨加氢裂化装置的节能途径及其可行性 。
关键词 :加氢裂化 ;能量平衡 ;节能 中图分类号 :TE683 文献标识码 :A 文章编号 :1002 -6339 (2007)01 -0050 -03
装置的总 工艺用能为 111 566 .3 kW 。主要用 能 设备是两台反应器和分流塔系统的五个塔及相关系 统 。在工艺总用能中 , 有效能占31 .83 %, 被 换热器 回收的循环能占55 .72 %, 反应 热提供了6 .73 %。由 此看出 , 提高换热器的传热效果 , 增大物流循环能量 的换热回收可以减少用能设备的外界功能 , 已达到 节约能源的目的 。
(4)采用目前的新型高效节能技术 , 如某石化公 司加氢裂化装置的新氢压缩机采用奥地利贺尔碧格
技术 , 控制压缩机单向阀的延迟关闭时间来调节新 氢压缩 机流量 , 比改 造前 采用 回流调 流量 可节 电 48 %左右 。
(5)对于正在运转的加氢裂化装置 , 注抗垢剂是 一种简单易行的办法 , 如法国石油研究院在给国内 某厂加氢装置的基础设计文件中就要求在原料油换
(7)常减压 、焦化装置可以和加氢裂化装置联合 起来 , 蜡油出装置前不用冷却 , 直接进入加氢裂化装 置 , 既可以降低常减压装置风冷电机电耗 , 又可以减 少加氢裂化装置加热炉负荷 , 降低燃料消耗 , 加氢裂 化装置进料温度每降低 10 ℃, 可节能1 .1 kgEO/t 左 右。
本文结合某石化加氢裂化装置的实际情况 , 通 过装置的能量平衡测试研究 , 分析加氢裂化装置的 用能特点 , 并对加氢裂化装置节能降耗的途径进行 了初步探讨 。
收稿日期 2006 -11 -10 修订稿日期 2006 -11 -17 作者简介 :赵孟姣(1979~ ), 女 , 硕士 。
· 50 ·
能量的工艺利用环节中 , 可以发现通过优化用 能设备的操作条件 , 可以达到节能降耗的效果 。
(1)保持合理的氢油比 , 即低于 1000 :1 , 使循环 氢稳定在合理的水平 , 避免增加压缩机和加热炉的 负荷 , 也不要过低 , 过低则会降 低反应过程的 氢分 压 , 导致催化剂快速失活而不能长期运转 。
Analyses on Energy Balance and Energy Saving in Hydrocracking Equipment
ZHAO Meng -jiao , CHEN Bao -dong (Liaoning Petrochemical University , Liaoning 113001 , China)
· 52 ·
热器一侧加注抗垢剂 , 以保证换热器的传热效率 。 (6)加热炉的长期使用会使炉管结灰 , 会显著降
低炉管的传热系数 , 降低加热炉的效率 , 致使加热炉 燃料消耗增加 , 排烟温度升高 。 目前加热炉的除灰 设计多采用蒸汽除灰器 , 但实践证明 , 除灰器效果不 佳 , 而且容易损坏 。 而国内某企业在加热炉中投放 了除灰剂 , 使烟气入余热锅炉的温度由投放前的大 于 690 ℃降低至 620 ℃以下 。
分流塔系统的底部供热为2 .011 MW , 而另一方 面塔中段回流及冷却器带走0 .826 6 MW的热量 , 因 此要平衡好操作中供热与取热的关系 , 减少能源的 浪费 。 尾油产品从分馏塔带走的热量占整个塔热量 的46 .68 %, 比 例很大 。 这说明 减少尾 油带走 的能 量 , 对装置的节能非常有益 。 3 .3 能量回收环节
回收环节的能量回收率为40 .14 %, 火用回收率更 低 , 为29 .50 %。还处于低水平 , 表明有很大的改进潜 力 。在各种未回收的排弃能量中 , 冷却排气能占 59 .31 %。这说明由 空冷器和 水冷器带 走得热 量太 大 , 造成 很 大 的 浪 费 。 空 冷 器 A501 , A604 , A605 , A606 就可回 收47 667 .05 kW的能 量 。 其 中空 冷器 A501 的冷却负 荷最大41 283 kW , 占整个空 冷负荷 的86 .6 %。在装置余热资源中 , 还有一项是高分到低 分的液体压差达到了7 MPa , 可采用液力涡轮泵来回 收这部分能量 。
本环 节 的 能 量 效 率 为 81 .54 %, 火用 利 用 率 为
35 .73 %。能量利用率较高 , 它的损失仅为散热这一 项引起 。 而火用效率较低 , 客观地反映了能量在使用 环节降质的属性 。 从设备的火用能情况看 , 火用 损失主 要是过程火用损 。过程火用损中 , 各种塔的火用损最大 , 占总过程火用 损的65 .89 %, 反应器的火用 损占过程火用 损的34 .10 %。因此 , 我们应在保证产品生产的条件 下 , 注意减少反应器和塔的过程火用 损 , 特别是塔的 过程火用损 。
· 51 ·
烧的要求 , 提高炉子的效率 。 (4)本装置新氢压缩机的电机功率过大 , 应用小
型号的电机与之匹配 。 由于本装置有剩余的热量 , 可以考虑用作产生蒸汽的热源 , 采用蒸汽驱动的新 氢压缩机 。 上述改进措施 , 即可以提高压缩机的效 率 , 也能减少了对电能的需求 , 使总供入能也减少 。
3 加氢装置的“ 三环节”用能分析〔1 -3〕
进行生产的装置用能分析 , 常用以“三环节”分 析法 , 也就是把炼油过程的用能归纳为能量的转换
图 1 用 能原理图 EP -总 供入 能 ;EW -直 接损 失能 ;EB -直 接输 出 能 ; EU -有效供 能 ;ED -回 收驱 动 能 ;ER -回 收循 环 能 ; ET -热力学 能 耗 ;EO -待 回 收能 ;EE -回 收 输 出 能 ; EJ -排弃能
2 加氢裂化装置能量平衡测试及用能特点
2 .1 能量平衡测试与用能分析的依据 任何一个炼油生产过程用能都可以归纳为能量
的转换和输出 、工艺利用 、能量回收三个环节 , 因此 , 依据图 1 的用能原理图〔1〕 , 进行加氢裂化装置的能 量平衡测试及用能分析 。 2 .2 某石化加氢裂化装置概况
4 节能的途径
从以上分析看出 , 能量的回收环节是能量利用 的薄弱环节 , 能量的工艺利用环节是装置的核心 , 决 定着回收环节可供出回收能量的数量和需要由转换 环节的能量的数量 。因此节能措施首要从工艺总用 能着手 , 然后依次考虑能量回收环节和能量转换环 节。 4 .1 降低工艺总用能