蜡油加氢裂化装置
400万吨年蜡油加氢裂化装置动态仿真

Simulationꎬ OTS) 的在员工培训、 装置操作分析和控制系统的
研究起到了重要的作用 [1] ꎮ OTS 仿真模拟技术包括 DCS 操作
过程、 控制逻辑、 联锁逻辑的动态过程模拟ꎬ 它基于精确的热
动力学方程和传质动力学模型ꎬ 可逼真地模拟工厂的开车、 停
分离出来ꎬ 生成油在分馏塔内进行气液两相充分接触进行热交
换和质量的交换ꎬ 侧线产品有重石脑油、 航煤、 柴油ꎮ 脱丁烷
塔分离出 C4 及 C4 以下组分ꎬ 石脑油分馏塔对轻、 重石脑油进
行有效分离ꎬ 脱异戊烷塔脱除轻石脑油中异戊烷组分ꎬ 为下游
乙烯裂解装置提高优质原料ꎮ 装置流程示意如图 1 所示ꎮ
浙江石油化工有限公司 400 万吨 / 年蜡油加氢裂化装置由
反应部分、 分馏部分、 低分气脱硫部分、 脱异戊烷部分和公用
工程部分组成ꎬ 采用双剂串联一次通过加氢裂化工艺 [4] ꎬ 是我
国目前规模最大的单段串联一次通过工艺流程装置ꎮ 在反应部
分原料蜡油和氢气混合后经加热后达到反应温度ꎬ 在反应器内
催化剂上进行加氢精制和加氢裂化反应ꎬ 完成蜡油裂化成轻质
and practical operation experience of operators The simulation system has three operation interfaces: instructor machineꎬ
field station and DCS trainee station It has four training functions: start - upꎬ shutdownꎬ accident handling and SIS
4.0Mta蜡油加氢裂化装置的运行优化
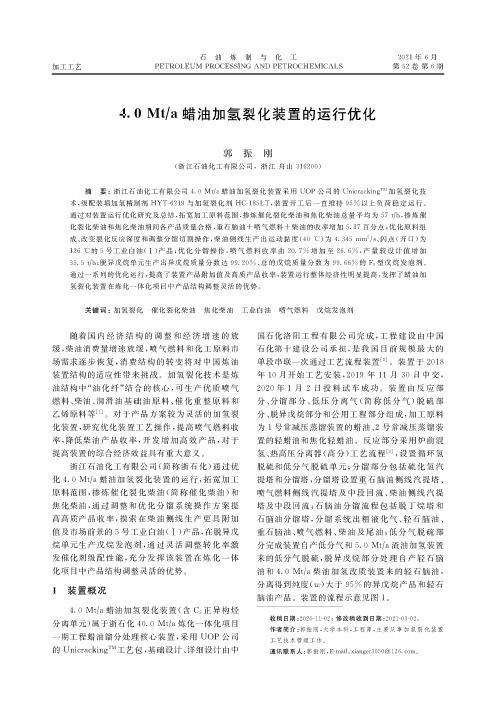
石油炼制与化工PETROLEUM PROCESSING AND PETROCHEMICALS2021年6月第52卷第6期加工工艺40Mt/a蜡油加氢裂化装置的运行优化郭振刚(浙江石油化工有限公司,浙江舟山316200/摘要:浙江石油化工有限公司4.0Mt/a蜡油加氢裂化装置采用UOP公司的Unicracking TM加氢裂化技术,级配装填加氢精制剂HYT6219与加氢裂化剂HC-185LT,装置开工后一直维持95%以上负荷稳定运行。
通过对装置运行优化研究及总结,拓宽加工原料范围,掺炼催化裂化柴油和焦化柴油总量平均为57t/h,掺炼催化裂化柴油和焦化柴油期间各产品质量合格,重石脑油+喷气燃料+柴油的收率增加5.17百分点;优化原料组成、改变裂化反应深度和调整分馏切割操作,柴油侧线生产出运动黏度(0O为4.345mm2/s、闪点(开口)为126c的5号工业白油(I)产品;优化分馏操作,喷气燃料收率由20.7%增加至26.6%,产量较设计值增加35.5t/h;脱异戊烷单元生产出异戊烷质量分数达99.20%、总的戊烷质量分数为99.66%的F。
型戊烷发泡剂。
通过一系列的优化运行,提高了装置产品附加值及高质产品收率,装置运行整体经济性明显提高,发挥了蜡油加氢裂化装置在炼化一体化项目中产品结构调整灵活的优势。
关键词:加氢裂化催化裂化柴油焦化柴油工业白油喷气燃料戊烷发泡剂随着国内经济结构的调整和经济增速的放缓,柴油消费量增速放缓,喷气燃料和化工原料市场需求逐步恢复,消费结构的转变将对中国炼油装置结构的适应性带来挑战。
加氢裂化技术是炼油结构中“油化纤”结合的核心,可生产优质喷气燃料、柴油、润滑油基础油原料、催化重整原料和乙烯原料等[1]。
对于产品方案较为灵活的加氢裂化装置,研究优化装置工艺操作,提高喷气燃料收率,降低柴油产品收率,开发增加高效产品,对于提高装置的综合经济效益具有重大意义。
浙江石油化工有限公司(简称浙石化)通过优化4.0Mt/a蜡油加氢裂化装置的运行,拓宽加工原料范围,掺炼催化裂化柴油(简称催化柴油)和焦化柴油,通过调整和优化分馏系统操作方案提高高质产品收率,摸索在柴油侧线生产更具附加值及市场前景的5号工业白油(I)产品,在脱异戊烷单元生产戊烷发泡剂,通过灵活调整转化率激发催化剂级配性能,充分发挥该装置在炼化一体化项目中产品结构调整灵活的优势。
加氢裂化装置加工焦化蜡油操作优化

加氢裂化装置加工焦化蜡油操作优化为了提高经济效益,降低成本,加大对石油资源的应用效率,在加氢裂化装置中掺入焦化蜡油成为很多工厂的选择,但是焦化蜡油本身存在很大缺陷,硫、氮元素含量很高,会影响加氢裂化装置使用周期,本文根据焦化蜡油特点,借助计算机软件深入分析了对其对加氢裂化装置的影响,并对反应系统进行优化,对产品质量进行跟踪对比总结,为系统降压提出合理的建议及有效的措施。
标签:焦化蜡油;加氢裂化;反应焦化蜡油是指在焦化装置收率最多的中间馏分,一般占焦化产品的20%-30%,是液体产物中收率最大的组分之一,为了科学合理利用焦化蜡油,提高其经济价值,一般作为催化裂化装置原料掺入加氢裂化装置中,但是由于焦化蜡油本身密度大,硫、氮元素含量高,特别是碱性氮含量高,还有较多的稠环芳烃、烯烃以及少量胶质,所以在掺入中要特别注意控制分量,掺入比例不能过高,以免影响催化裂化产品的质量。
本文借助了国外软件,通过计算机模拟测算,结合当前工艺水平,在实际的生产过程中对操作进行优化。
这对节约能源,减少对环境的污染具有十分重大的意义。
1 掺炼焦化蜡油对加氢裂化装置的影响经过实际检测后发现,掺入焦化蜡油后加氢裂化装置处理的原料性质变差,导致了加氢裂化尾油性质波动,BMCI指数较大,并对装置的运行周期产生了严重的影响,根据数据记录分析,在加氢裂化装置中加入焦化蜡油后,装置运行周期与BMIC之间关系变化,如表1:从表1中分析出,在加氢裂化装置掺炼焦化蜡油后,BMIC数值不断升高,最高达到了17.2,远远高于标准数据,同时,尾油终馏点指数也略有增加,达到512度,运行周期降低到了13天,从数据变化中得知,裂解炉的运行时间和加氢裂化装置中的原料性质有关,因此必须对加氢裂化装置进行优化,改善原料质量,才能有效提高加氢裂化装置的使用效率,提升工厂经济效益。
2 模拟测算分析借助软件测算加氢裂化装置原料性质、操作数据等。
2.1 原料性质分析根据软件模拟测算,发现在不同进料下,焦化蜡油的氮含量大于罐区蜡油,进而导致混合进料密度大、氮含量超标、残碳含量也比较高,在设计进料量为175 t/h的情况下,焦化蜡油的掺炼量应为11 t/h,但实际上焦化蜡油的掺炼量最高达到30 t/h。
蜡油加氢裂化装置柴油转化、减油增化方向研究

蜡油加氢裂化装置柴油转化、减油增化方向研究摘要:本文先是对蜡油加氢裂化装置概况及现状进行分析,其次蜡油加氢裂化装置柴油转化、减油增化的影响因素,最后提出蜡油加氢裂化装置柴油转化、减油增化的对策,促进企业可持续发展。
关键词:蜡油加氢;裂化装置;柴油转化;减油增化当前,为了促进企业可持续发展,很有必要探讨蜡油加氢裂化装置柴油转化、减油增化的措施,降低成本,提高企业发展效益。
1蜡油加氢裂化装置概况及现状某石化千万吨炼油项目的主体装置为蜡油加氢裂化装置,其将美国UOP企业的加氢裂化专利技术与工艺包引进。
通过分析,加氢裂化设计规模为每年210万吨,一年操作时间为8400h,装置操作弹性为60%~110%。
这一装置的主要反应部分在于合理利用炉前婚氢、单段全循环、热高分工艺流程,且还设置了循环氢脱硫塔,分馏系统主要使用的是四塔分离流程出柴油方案,即分馏塔、硫化氢脱硫塔、柴油汽提塔、航煤汽提塔[1]。
该装置使用的操作方法为单段全循环方法,最大程度地完成中间馏分忧的生产,将其当做整个企业的调和组分,将少量加氢裂化还未转化的油去重油催化裂化当做主要的原料,冷低分气脱硫之后可以去PSA装置完成氢气提纯,含硫干气到轻烃回收装置中。
当前,企业原始设计方案采用低硫原油为主要原料,完成最大量生产中间馏分柴油方案。
2016年企业为了降低生产加工总成本,将其换成加工高硫原料油,生产的是高效的石脑油,让装置柴汽比方案明显降低。
2018年之前,基本维持装置重石脑油在0.5~1.2ppm。
从2018年开始,维持硫含量在2.0~4.0ppm之间。
为了给下游重整更优的原料,被迫将加裂装置的石脑油通过石脑油加氢装置脱硫之后将其送到重整装置,最终导致企业加工总成本明显提高。
2蜡油加氢裂化装置柴油转化、减油增化的影响因素2.1反应器后精制剂超负荷运行最初的蜡油加氢裂化装置设计原材料为轻蜡油,反应器之内的催化剂装填级配更多以原始方案为基础,主要设计在于生产中间馏分油。
加氢裂化装置简介
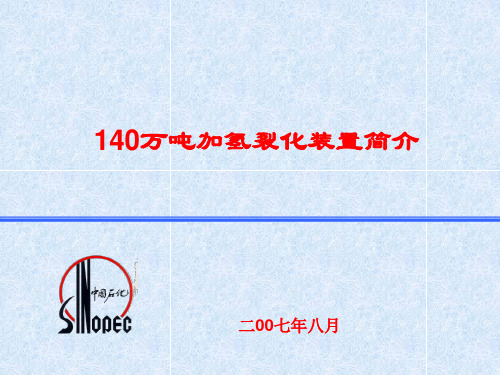
加氢裂化装置催化剂装填数据
• 反应器R401共计装入抚顺研究院产的精制催化剂 3936 167.55吨,保护剂CEN-2 4.675吨,保护剂 FZC-16 7.8吨。3936设计装填密度0.8 t/m3,实 际装填密度0.78 t/m3,FZC-16装填密度0.69 t/m3, CEN-02装填密度0.42 t/m3。具体装填数据见附 表。 • 反应器R402共计装入齐鲁第一化肥厂生产的抚顺 研究院研制的裂化催化剂ZHC-01 162.96吨,后 精制催化剂ZTS-03 12.99吨。ZHC-01设计装填 密度0.88 t/m3,实际装填密度0.89 t/m3,ZTS03设计装填密度0.82 t/m3,实际装填密度0.88 t/m3。
140万吨加氢裂化装置简介
二00七年八月
加氢裂化装置概述
140万t/a加氢裂化装置,是齐鲁石化公司加工 进口原油改扩建工程的重点项目,本装置与60万t/a 连续重整装置联合布局,由抚顺石油化工科学研究 院提供工艺试验中试报告,由中国石化北京设计院 设计,齐鲁胜利炼油设计院负责系统配套,大部分 设备由国内制造,中石化集团公司第十建设工程公 司负责施工安装。装置于1998年3月31日开工建设, 2000年11月23日实现中间交接,2001年3月5日产 品合格,实现装置一次开汽成功。
加氢裂化主催化剂性质
物化性质 孔容/mL/g 表面积/m2/g 堆密度/ g/100ml 压碎强度/ N/mm 烧减,mt% 磨耗,mt% 形状 条长/mm 直径/mm
(完整ppt)290万加氢裂化装置简介

初期 0.7973
172/187 194/201 209/222
237 <5 <1 55 -54 27
末期 0.7992
国标
172/188 194/201 209/222
237 <5 <1 55 -54 25
不大于2000
不低于38 不高于-47 不小于25
保证值
2000 max 38 min -47 max 25 min
290万吨/年加氢裂 化装置简介
中国石油华北石化公司
目录
• 一、装置概述 • 二、原料及主要产品性质 • 三、工艺技术方案 • 四、关键设备选型 • 五、仪表控制
中国石油华北石化公司
目录
• 六、能耗及物料平衡 • 七、平面布置 • 八、工艺流程简图 • 九、设备图片
中国石油华北石化公司
一、装置概述
中国石油华北石化公司
工艺技术方案
• 紧急泄放系统方案 为确保催化剂、高压设备及操作人员的安 全,设置2.1MPa/min和0.7MPa/min两个 紧急泄压系统
中国石油华北石化公司
工艺技术方案
• 反应部分共设置了两个循环氢加热炉和两 个加氢裂化反应器(并联使用),原料油 自高压进料泵出口分为两路,经换热后分 别与从两个循环氢加热炉出口来的循环氢 气混合,进入加氢裂化反应器,反应器生 成物经换热后合并进入热高压分离器进行 气液分离。
轻石脑油主要技术指标
产品 密度(20℃),g/cm3
初期 0.6413
末期 0.6418
硫,μg/g 氮,μg/g
<0.5
<0.5
<0.5
<0.5
保证值 10 Max
中国石油华北石化公司
蜡油加氢裂化装置低负荷生产及优化措施
蜡油加氢裂化装置低负荷生产及优化措施摘要:对炼厂而言,蜡油加氢裂化装置需要消耗较多的能耗,且其操作能力直接影响整个企业的能耗,因此还必须结合当前企业这一装置高能耗的现状,分析其原因,提出相应的改进措施。
结合实际工作可知,蜡油加氢裂化装置低负荷生产原因较多,比较常见的有单位能耗较大、尾油收率增加。
为此,本文从提高加热炉效率、控制氢油比、降低尾油收率等方面提出优化蜡油加氢裂化装置低负荷低负荷生产的建议,希望可以为企业高质量生产提供借鉴,提升企业的经济效益。
关键词:蜡油加氢裂化装置低;负荷生产;优化措施为适应市场需求,各地石化炼厂都调整了产品结构,所以当前阶段石化原料配额改变比较明显。
蜡油加氢裂化装置运行期间低负荷问题比较显著,同时能耗增大,尾油回收率增加。
这一问题的出现导致企业生成总成本明显增加,还会对企业的发展造成不良影响。
这就要求企业探索优化成本的方法,节约资源,提高自身经济效益,促进自身可持续发展。
1蜡油加氢裂化装置低负荷生产原因1.1单位能耗较大电耗与燃料气消耗是蜡油加氢裂化装置的主要能源消耗,其两项能耗占总能耗消耗的三成到四成左右。
生产制造工作开展期间因加工负荷不同,其能源消耗水平也不同。
但可以明确,低负荷生产其间加热炉的热效率要比高负荷运行其间热效率更低,燃料气消耗更高。
同时,随着时间增加,这就意味着能耗更高[1]。
若在低负荷情况下运行,除了燃料气消耗与电耗之外还会对安全生产产生不利影响,低负荷生产的过程中反应进料热处理加热炉负荷消耗主要有几大关键因素:一是冷蜡油与热蜡油配比进料量变化,导致混合原料油的进料温度降低。
二是若温度不变的情况下,低负荷运行期间反应热降低,反应馏出物换热器与原料油换热传热效果变差,降低了反应加热炉进料的温度。
1.2尾油收率增加为了实现节能减排的目标,可以通过该装置让尾油全循环回流给原料传热得以改善[2]。
提取了分馏塔底部的高温尾油之后其是轻柴油侧汽提塔底部再沸器的热量,必须确保轻柴油的闪点与初馏点合格,确保一定的总尾油量可以对轻柴油汽提塔底部温度进行维持,确保轻柴油的初沸点在135℃以内,闭口闪点在40℃以上。
蜡油加氢裂化装置
180万吨/年蜡油加氢裂化装置一、工艺流程选择1、反应部分流程选择A. 反应部分采用单段双剂串联全循环的加氢裂化工艺。
B. 反应部分流程选择:本装置采用部分炉前混氢的方案,即部分混合氢和原料油混合进入高压换热器后进入反应进料加热炉,另一部分混合氢和反应产物换热后与加热炉出口的混氢油一起进入反应器。
C. 本装置采用热高分流程,低分气送至渣油加氢脱硫后进PSA部分,回收此部分溶解氢。
同时采用热高分油液力透平回收能量。
因本装置处理的原料油流含量很高,氮含量较高,故设循环氢脱硫设施。
2、分馏部分流程选择A. 本项目分馏部分采用脱硫化氢塔-吸收稳定-常压塔出航煤和柴油的流程,分馏塔进料加热炉,优化分流部分换热流程。
采用的流程比传统的流程具有燃料消耗低、投资省、能耗低等特点。
B. 液化气的回收流程选用石脑油吸收,此法是借鉴催化裂化装置中吸收稳定的经验,吸收方法正确可靠,回收率搞。
具有投资少、能耗低、回收率可达95%以上等特点。
3、催化剂的硫化、钝化和再生A、本项目催化剂硫化拟采用干法硫化B、催化剂的钝化方案采用低氮油注氨的钝化方案C、催化剂的再生采用器外再生。
二、工艺流程简介1、反应部分原料油从原料预处理装置和渣油加氢裂化装置进入混合器混合后进入原料缓冲罐(D-101),经升压泵(P-101)升压后,再经过过滤(SR-101),进入滤后原料油缓冲罐(D-102)。
原料油经反应进料泵(P-102)升压后与部分混合氢混合,混氢原料油与反应产物换热(E-101),然后进入反应进料加热炉(F-101)加热,加热炉出口混氢原料和另一部分经换热后的混合氢混合,达到反应温度后进入加氢精制反应器(R-101),然后进入加氢裂化反应器(R-102),在催化剂的作用下,进行加氢反应。
催化剂床层间设有控制反应温度的急冷氢。
反应产物先与部分混合氢换热后再与混氢原料油换热后,进入热高压分离器(D-103)。
装置外来的补充氢由新氢压缩机(K-101)升压后与循环氢混合。
蜡油加氢裂化装置掺炼柴油技术应用
蜡油加氢裂化装置掺炼柴油技术应用作者:胡义来源:《中国化工贸易·上旬刊》2019年第12期摘要:在当前柴油价格持续低迷的大背景下,采用掺炼柴油技术可以有效增加柴油中一些高附加值产品的裂化,从而提高炼厂的经济效益。
本文通过分析蜡油加氢裂化装置在掺炼柴油技术中的应用,发现将蜡油加氢裂化装置应用于柴油的掺炼中,确实可以有效增加柴油的转化率。
关键词:加氢裂化装置;掺炼柴油;产品质量;经济效益近年我国投资建设多家大型炼厂,柴油年产量大幅度提升,但是新能源加快增长,柴油需求量逐年下降,及炼厂环保投入增多,竞争加剧,效益降低。
为提高柴油经济效益,将蜡油加氢裂化装置应用于柴油的掺炼技术中,可增加航煤、液化气等高附加值产品的产出。
1 蜡油加氢裂化装置简介蜡油是指在焦化装置收率最多的中间馏分,一般占焦化产品20%-30%,是液体产物中收率最大的组分之一,为科学利用蜡油,一般作为催化裂化装置原料掺入加氢裂化装置中,但因其密度大,硫、氮含量高。
加氢裂化装置可优化加氢裂化生产运行条件,实现产品品质的提升。
为更好满足生产要求,部分炼化企业开创性地将蜡油加氢裂化与加氢裂化工艺组合。
在原有串联的生产工艺体系,新增一台加氢裂化反应装置,实现蜡油加氢裂化装置技改后管线回炼焦化汽柴油能力的升级。
同时,相关技改评测显示,这一组合策略对重质化、劣质化原油液有较好处理能力。
根据原料性质不同,对应采用相应催化剂体系,实现产品结构的调整和优化。
2 蜡油加氢裂化装置在柴油掺炼技术中的应用2.1 目标产品的总体裂化效果一般情况下,蜡油加氢裂化装置工作能力大致为35t/h,在掺炼柴油时总量一定要控制在装置正常工作范围。
为方便对比蜡油加氢裂化装置在柴油掺炼技术中的裂化效果,对比掺炼减一级柴油与掺炼加氢焦化柴油与掺炼前,统计结果见表1,掺炼加氢焦化柴油的总体转化率达到91.39%,转化率较高,说明蜡油加氢裂化装置对加氢焦化柴油裂化效果更好,获取目标产品转化率可达到最高。
4.0 Mta蜡油加氢裂化装置开工标定
4.0Mt/a蜡油加氢裂化装置开工标定郭振刚(浙江石油化工有限公司,浙江省舟山市316200)摘要:浙江石油化工有限公司4.0Mt/a的蜡油加氢裂化装置(含C5正异构分离单元),采用UOPUnicrackingTM加氢裂化技术,装填加氢精制催化剂HYT 6219 1.3T,HYT 6219 1.3Q与加氢裂化催化剂HC 185LT,是国内目前规模最大的单段串联一次通过工艺流程装置。
装置开工后一直维持95%以上负荷稳定运行,重石脑油收率27.67%,芳烃潜含量58.3%,分馏增产3号喷气燃料收率达到23.74%。
催化剂在低反应温度下活性和选择性较好,单程转化率83.35%,C+5收率达到94.42%,综合能耗1652.41MJ/t,产品分布合理,质量达到设计要求。
关键词:蜡油加氢裂化装置 重石脑油 开工 标定 能耗1 装置概况浙江石油化工有限公司4.0Mt/a蜡油加氢裂化装置(含C5正异构分离单元)为40Mt/a炼化一体化项目一期工程蜡油馏分处理的核心装置,采用单段串联一次通过工艺流程[1],由反应部分、分馏部分、低分气脱硫部分、脱异戊烷部分和公用工程部分组成。
采用UOP工艺包,由中石化洛阳工程有限公司设计,中石化第十建设有限公司承建。
加工原料来自1号常减压重蜡油、2号常减压轻蜡油、焦化轻蜡油。
反应部分采用炉前混氢、热高压分离(高分)工艺流程[2],设置循环氢脱硫和低分气脱硫。
装置流程示意见图1。
图1 蜡油加氢裂化装置流程示意Fig.1 ProcessflowofVGOhydrocrackingunit2 装置开工过程2019年9月27日引生产水进行管线冲洗,10月18日高压蒸汽打靶合格,11月14日建立石脑油系统水联运,11月17日建立分馏系统水联运,11月30日加热炉烘炉和反应系统热态考核结束,12月12日催化剂装填完成,12月22日氢气全压气密完成,12月31日催化剂硫化钝化完成,逐步切换新鲜蜡油进料。
- 1、下载文档前请自行甄别文档内容的完整性,平台不提供额外的编辑、内容补充、找答案等附加服务。
- 2、"仅部分预览"的文档,不可在线预览部分如存在完整性等问题,可反馈申请退款(可完整预览的文档不适用该条件!)。
- 3、如文档侵犯您的权益,请联系客服反馈,我们会尽快为您处理(人工客服工作时间:9:00-18:30)。
180万吨/年蜡油加氢裂化装置
一、工艺流程选择
1、反应部分流程选择
A.反应部分采用单段双剂串联全循环的加氢裂化工艺。
B.反应部分流程选择:本装置采用部分炉前混氢的方案,即部分混合氢和原料油混合进入高压换热器后进入反应进料加热炉,另一部分混合氢和反应产物换热后与加热炉出口的混氢油一起进入反应器。
C.本装置采用热高分流程,低分气送至渣油加氢脱硫后进PSA部分,回收此部分溶解氢。
同时采用热高分油液力透平回收能量。
因本装置处理的原料油流含量很高,氮含量较高,故设循环氢脱硫设施。
2、分馏部分流程选择
A.本项目分馏部分采用脱硫化氢塔-吸收稳定-常压塔出航煤和柴油的流程,分馏塔进料加热炉,优化分流部分换热流程。
采用的流程比传统的流程具有燃料消耗低、投资省、能耗低等特点。
B.液化气的回收流程选用石脑油吸收,此法是借鉴催化裂化装置中吸收稳定的经验,吸收方法正确可靠,回收率搞。
具有投资少、能耗低、回收率可达95%以上等特点。
3、催化剂的硫化、钝化和再生
A、本项目催化剂硫化拟采用干法硫化
B、催化剂的钝化方案采用低氮油注氨的钝化方案
C、催化剂的再生采用器外再生。
二、工艺流程简介
1、反应部分
原料油从原料预处理装置和渣油加氢裂化装置进入混合器混合后进入原料缓冲罐(D-101),经升压泵(P-101)升压后,再经过过滤(SR-101),进入滤后原料油缓冲罐(D-102)。
原料油经反应进料泵(P-102)升压后与部分混合氢混合,混氢原料油与反应产物换热(E-101),然后进入反应进料加热炉(F-101)加热,加热炉出口混氢原料和另一部分经换热后的混合氢混合,达到反应温度后进入加氢精制反应器(R-101),然后进入加氢裂化反应器(R-102),在催化剂的作用下,进行加氢反应。
催化剂床层间设有控制反应温度的急冷氢。
反应产物先与部分混合氢换热后再与混氢原料油换热后,进入热高压分离器(D-103)。
装置外来的补充氢由新氢压缩机(K-101)升压后与循环氢混合。
混合氢先与热高分气进行换热,一部分和原料油混合,另一部分直接和反应产物换热后直接送至加氢精制反应器入口。
从热高压分离器出的液体(热高分油)经液力透平(HT-101)降压回收能量,或经调节阀降压,减压后进入热低压分离器进一步在低压将其溶解的气体闪蒸出来。
气体(热高分气)与冷低分油和混合氢换热,最后由热高分气空冷器(A-101)冷却至55℃左右进入冷高压分离器,进行气、油、水三相分离。
为防止热高分气中NH3和H2S在低温下生成铵盐结晶析出,赌赛空冷器,在反应产物进入空冷器前注入除盐水。
从冷高压分离器分理出的气体(循环氢),经循环氢脱硫后进入循环氢压缩机分液罐(D-108),有循环氢压缩机(K-102)升压后,返回反应部分同补充氢混合。
自循环氢脱硫塔底出来的富胺液闪蒸罐闪蒸。
从冷高压分离器分离出来的液体(冷高分油)减压后进入冷低压分离器,继续进行气、液、水三相分离。
冷高分底部的含硫污水减压后进入酸性水脱气罐(D-109)进行气液分离,含硫污水送出装置至污水汽提装置处理。
从冷低压分离器分离出的气体(低分气)至渣油加氢装置低压脱硫部分:液体(冷低分油)经与热高分气换热后进入脱硫化氢塔。
从热低压分离器分离出的气体(热低分气)经过水冷冷却后至冷低压分离器,液体(热低分油)直接进入脱硫化氢塔。
2、分馏和吸收稳定部分
自反应部分来的生成油进入脱硫化氢塔(C-201),他弟用重沸炉(F-201)加热。
脱硫化氢塔顶油气经空冷、水冷后进入脱硫化氢塔顶回流罐(D-201)。
回流罐顶气体送至吸收脱吸塔(C-205);液相则大部分经脱硫化氢塔顶回流泵送回脱硫化氢塔顶作为回流,小部分送至吸收脱吸塔二中段回流入口;含硫污水送至装置外污水汽提装置处理。
脱硫化氢塔滴油进入分馏塔进料加热炉(F-202)加热至分流所需要的温度进入分馏塔(C-202)。
分馏塔底吹入过热蒸汽。
分馏塔塔顶气相经分馏塔定空冷器冷凝冷却后进入分馏塔回流罐(D-202)。
液体部分作为塔顶回流经分馏塔顶回流泵打到分馏塔塔顶,部分至石脑油分馏塔(C-204)分出轻重石脑油,轻石脑油出装置,重石脑油冷却后一部分去吸收脱吸塔,一部分出装置。
冷凝水经分馏塔顶冷凝水泵送至注水罐回收利用。
分馏塔设一个侧线抽出,从柴油汽提塔出来的柴油与石脑油分馏塔底重沸器换热后依次经过脱吸塔底重沸器与稳定塔进料换热器,然后依原流程冷却后出装置;从分馏塔底抽出的油品为循环油,由分馏塔底泵抽出依次经柴油侧线塔底重沸器和稳定塔底重沸器以及尾油蒸汽发生器,循环回原料缓冲罐。
分馏塔设有两个中段回流,分别发生1.0MPa(G)和0.5MPa(G)蒸汽后返回塔内。
脱硫化氢塔顶气在吸收脱吸塔内,经吸收液化气组分后,干气送至装置外干气脱硫部分脱硫。
塔底油与柴油换热器换热后进入石脑油稳定塔(C-206)。
吸收脱吸塔错需要的热量由塔底重沸器提供。
吸收脱吸塔还设有两个中段回流经中段回流泵抽出,有中段回流冷却器取走热量。
石脑油稳定塔顶油气经冷却后进入塔顶回流罐。
液相大部分作为回流打回稳定塔顶,小部分作为液化气送出装置脱硫。
石脑油稳定塔底油为混合石脑油,返回石脑油分馏塔。