蜡油加氢
蜡油加氢操作规程(3篇)

第1篇一、操作前的准备1. 确保设备完好,检查各阀门、管道、仪表等无泄漏、堵塞现象。
2. 确认原料蜡油质量符合要求,检查原料罐液位、温度、压力等参数。
3. 检查氢气供应系统,确保氢气纯度、压力符合要求。
4. 检查反应器、分离器、冷却器等设备,确保正常运行。
5. 检查现场安全设施,如消防器材、报警装置等。
6. 确认操作人员熟悉操作规程,了解设备性能和安全隐患。
二、操作步骤1. 启动氢气供应系统,调节氢气流量,确保氢气纯度和压力稳定。
2. 打开原料油罐阀门,启动原料油泵,将蜡油送入反应器。
3. 调节反应器温度,使其保持在设定范围内。
4. 检查反应器进出口温度、压力等参数,确保反应器正常运行。
5. 检查分离器、冷却器等设备,确保其正常运行。
6. 检查氢气、蜡油、反应产物等物料流量,确保流量稳定。
7. 定期检查设备,发现异常情况及时处理。
8. 检查设备安全联锁,确保其正常工作。
9. 操作过程中,密切关注设备运行状态,发现异常情况立即停车检查。
三、操作注意事项1. 操作人员应穿戴好劳动保护用品,如防护服、防护眼镜、手套等。
2. 严禁在设备运行过程中进行检修、清洁等操作。
3. 操作过程中,严禁触摸高温、高压设备。
4. 严禁操作人员携带易燃、易爆物品进入操作区域。
5. 操作过程中,注意观察设备运行状态,发现异常情况立即停车处理。
6. 严格执行设备安全联锁,确保设备安全运行。
7. 操作过程中,注意观察反应器、分离器、冷却器等设备温度、压力、液位等参数,确保其稳定。
8. 操作过程中,注意观察氢气、蜡油、反应产物等物料流量,确保其稳定。
9. 定期对设备进行维护保养,确保设备正常运行。
四、操作后的处理1. 停车前,确保设备稳定运行,关闭相关阀门。
2. 停车后,对设备进行检查,确认无异常情况。
3. 关闭氢气供应系统,释放设备内残余压力。
4. 清理操作区域,确保现场整洁。
5. 记录操作过程中的各项参数,如温度、压力、流量等。
蜡油的加氢裂化反应
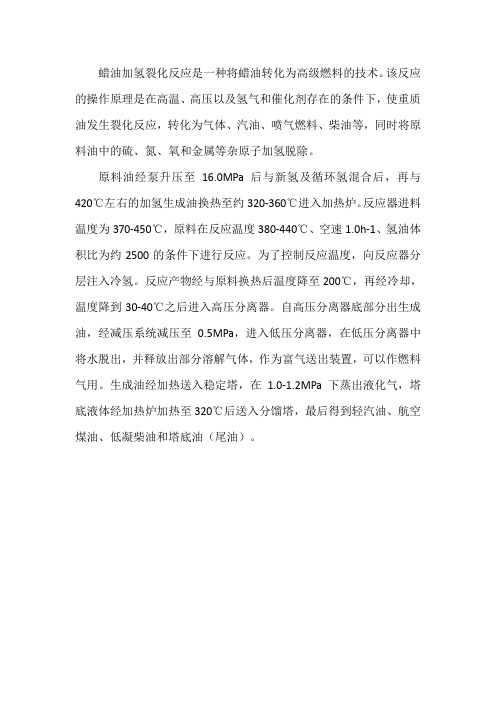
蜡油加氢裂化反应是一种将蜡油转化为高级燃料的技术。
该反应的操作原理是在高温、高压以及氢气和催化剂存在的条件下,使重质油发生裂化反应,转化为气体、汽油、喷气燃料、柴油等,同时将原料油中的硫、氮、氧和金属等杂原子加氢脱除。
原料油经泵升压至16.0MPa后与新氢及循环氢混合后,再与420℃左右的加氢生成油换热至约320-360℃进入加热炉。
反应器进料温度为370-450℃,原料在反应温度380-440℃、空速1.0h-1、氢油体积比为约2500的条件下进行反应。
为了控制反应温度,向反应器分层注入冷氢。
反应产物经与原料换热后温度降至200℃,再经冷却,温度降到30-40℃之后进入高压分离器。
自高压分离器底部分出生成油,经减压系统减压至0.5MPa,进入低压分离器,在低压分离器中将水脱出,并释放出部分溶解气体,作为富气送出装置,可以作燃料气用。
生成油经加热送入稳定塔,在1.0-1.2MPa下蒸出液化气,塔底液体经加热炉加热至320℃后送入分馏塔,最后得到轻汽油、航空煤油、低凝柴油和塔底油(尾油)。
蜡油的加氢处理工艺

8对蜡油进行加氢处理,目的是为了更好的发挥出蜡油加氢处理的作用与意义价值,并且能够更好地满足高硫或者是劣质的原油加工生产过程,从而更好的通过蜡油加氢处理提升原油加工深度,获取越来越多的轻质油品的收益,从而更好的适应与满足炼油厂的生产与工作技术发展要求。
因此本篇文章将重点对蜡油的加氢处理工艺进行分析与研究,并提出蜡油加氢处理重要性与具体蜡油加氢处理技术措施方法以及影响蜡油加氢处理效果的因素进行提出与分析,希望能够贡献微薄之力提供建设性意见,详见下文叙述。
1 蜡油加氢处理重要性蜡油加氢处理指的是将重质油变得轻质化的一种技术措施,其中主要利用将蜡油加氢裂化以及催化裂化等等作为主要技术措施,但是最终的目的都是为了更好的提高油品质量,从而提炼出的油品更好的满足市场的需求与要求、其中催化裂化技术主要是将原有进行二次加工处理,因此催化裂化是油品生产中最关键也是最重要的加速措施{2}。
有效通过蜡油加氢处理从而更好的实现环保的目标,提高油品质量,更好的为我国社会炼油化工厂获取经济效益与收益。
在当前蜡油加氢处理过程中,科学合理使用催化裂化工艺措施,不仅能够有效提高原油加工的深度,还能更好的生产出高质量的汽油以及柴油等等,提高经济效益的同时更好的跟上社会市场发展步伐从而更好的满足社会市场对油品的需求。
蜡油的质量好坏决定着成品油产品的质量优劣,因此为了能够更好的生产出高质量的油品,大部分的炼油化工厂选择蜡油加氢处理方法。
其中主要是把蜡油作为催化裂化技术实施当中的原料,加氢实施过程中的原料以及润滑油的原料等等,然后进一步对蜡油进行加氢处理,处理过程中减少蜡油中所包含的杂质,达到改进原料质量的目的,从而更好的提升蜡油加氢处理催化裂化的工作运营效率,达到降低催化裂化过程中硫化物的排放量的结果,这样一蜡油加氢处理过程非常有利于环境保护,且能够有效减少环境污染,由此可见蜡油加氢处理十分重要,且是当下炼油化工厂中实现安全运行运转的必然要求。
蜡油加氢裂化装置氢耗的影响因素分析及措施

蜡油加氢裂化装置氢耗的影响因素分析及措施摘要:在炼油企业降耗增效的大形势下,降低氢耗对于降低加工成本尤为重要。
蜡油加氢处理装置的氢耗在加工成本中占很大比例。
为了降低蜡油加氢处理装置的氢耗,有必要分析其影响因素并提出改进建议,为车间节能生产提供参考。
基于此,对蜡油加氢裂化装置氢耗的影响因素分析及措施进行研究,以供参考。
关键词:新氢;反应温度;原料组分;溶解损失;转化率引言加热炉的燃料气消耗在炼油装置能耗中占有相当大的比例,少则20%~30%,多则80%~90%,加热炉技术水平及操作性能极大地影响着炼油装置的能源消耗水平。
因此,提高加热炉热效率,降低燃料气消耗,对降低能耗具有十分重要的意义。
1氢耗的影响因素1.1溶解损失在氢气循环过程中,一部分氢气会溶解在热高压分离器(简称热高压分离器)和冷高压分离器(简称冷高压分离器)的液相中,称为溶解损失。
相关研究文献指出,180℃和240℃的高温是两个拐点。
在80℃左右,循环氢的体积分数最低。
当温度高于180℃时,循环氢的体积分数随着温度的升高而逐渐增加。
当温度超过240℃时,循环氢体积分数的增加趋势减缓。
考虑到循环氢浓度和设备的承受能力,装置的高温应为240℃~260℃。
对于高冷含量,降低操作温度有利于提高氢气纯度,但温度过低和高压空冷器、高压换热器负荷过重会导致能耗过高。
综合考虑,冷高分操作温度应控制在45℃~55℃。
1.2压力控制装置的压力控制采用循氢机入口的压力控制器控制新氢返回量和循氢机入口分液罐顶排放循环氢来控制,这样可以有效控制系统压力,又可以对临氢系统的氢分压进行调节,这种方式避免了循环氢连续排放造成的氢气浪费。
1.3浓度一般钢材在水溶液中,浓度越高,越容易产生硫化物应力腐蚀开裂。
有日本资料报导:当水溶液中的浓度低于50~60ppm时,应力腐蚀开裂的可能性很低。
对任何一种钢,都存在一个浓度的门限值,超过此门限值都可发生应力腐蚀开裂。
Troiano曾对16Mn钢试样进行研究,考察常温下浓度对裂纹扩展的影响,试验结果表明,常温条件下,钢材内部裂纹扩展非常缓慢。
蜡油加氢工艺技术

蜡油加氢工艺技术蜡油加氢是一种常用的加工技术,用于提高蜡油的质量和改善其性能。
在蜡油加氢工艺技术中,蜡油通过与氢气反应,使其分子中的不饱和键饱和化,提高其稳定性和耐高温性能。
蜡油加氢工艺技术的基本原理是利用催化剂催化剂对蜡油中的不饱和键进行加氢反应。
蜡油加氢反应一般在高温高压下进行,通常是在200-350℃,5-20MPa的条件下进行。
蜡油加氢一般分为两个步骤:预处理和催化加氢。
预处理的目的是去除蜡油中的杂质,如酸、水和硫等,以提高催化剂的活性和稳定性。
在预处理过程中,蜡油首先通过精炼和提纯的过程,去除其中的不溶物和溶解物。
然后,通过酸洗和碱洗的过程,去除其中的酸性和碱性杂质。
最后,通过加氢脱硫的过程,去除其中的硫化物。
催化加氢是蜡油加氢的核心步骤,通过与催化剂接触,使蜡油中的不饱和键加氢饱和,从而提高其质量和性能。
催化剂一般采用贵金属催化剂,如铂、钯和铑等。
在催化加氢过程中,蜡油分子中的双键会与氢气分子发生反应,形成单键,并释放出能量。
催化剂起到催化反应的作用,加快反应速度,提高反应效率。
蜡油加氢工艺技术主要有以下几个优点。
首先,加氢可以去除蜡油中的不饱和键,提高其稳定性,延长其使用寿命。
其次,加氢可以提高蜡油的熔点和燃点,使其更适合在高温环境下使用。
此外,加氢还可以降低蜡油的黏度和凝固点,改善其流动性。
最后,加氢还可以改善蜡油的抗氧化性能,防止其在使用过程中氧化变质。
总之,蜡油加氢工艺技术是一种常用的加工技术,用于提高蜡油的质量和改善其性能。
通过预处理和催化加氢的步骤,可以去除蜡油中的杂质和不饱和键,提高其稳定性和耐高温性能。
蜡油加氢工艺技术具有许多优点,可以使蜡油更适合在各种应用领域中使用。
蜡油加氢
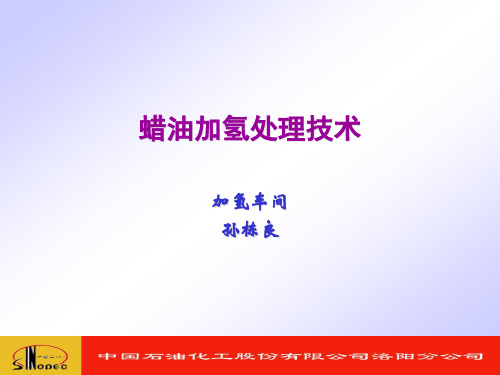
100
FCC汽油硫含量/( μ g/g)
90 80 70 60 50 40 30 20 10 1000 1500 2000 2500 3000 3500 4000
进料硫含量/(μg/g)
FCC汽油硫含量与原料硫含量的关系
100
FCC汽油硫含量/( μ g/g)
蜡油加氢处理的必要性
欧洲汽油规格变化 项 目 1993 年 欧洲Ⅰ号 0.1 5 无规定 无规定 2.5 13 1998 年 欧洲Ⅱ号 0.05 5 无规定 无规定 2.5 13 2000 年 欧洲Ⅲ号 0.015 1 42 18 2.7 5 2005 年 欧洲Ⅳ号 0.005 1 35 18 2.3 2009 年 欧洲Ⅴ号 0.001 1 35 18 2.3 汽车排放标准 硫含量/% 苯含量/% 芳烃含量/% 烯烃含量/% 氧含量/% 铅含量/mg/L
蜡油加氢处理的必要性
欧洲柴油规格变化 项目 汽车排放标准 十六烷值,≮ 十六烷指数,≮ 密度/kg/m3 多环芳烃含量 /%(v/v) ≯ T/℃ ≯ 硫含量/% ≯ 1993 年 欧洲Ⅰ号 49 46 820-860 无规定 370 0.2 1998 年 欧洲Ⅱ号 49 46 820-860 无规定 370 0.05 2000 年 欧洲Ⅲ号 51 46 820-845 11 360 0.035 820-825 11 340 0.005 820-825 11 340 0.001 2005 年 欧洲Ⅳ号 51 2009 年 欧洲Ⅴ号 51
蜡油加氢处理技术
加氢车间 孙栋良
世界炼油工业现状
2005年底,世界炼油能力42.52亿吨,其中 • 美国 8.56亿吨
• 中国 3.28亿吨
蜡油加氢装置简介

100万吨/年蜡油加氢装置装置简介中国石化股份有限公司上海高桥分公司炼油事业部2007年3月编制:何文全审核:严俊校对:周新娣目录第一章工艺简介一、概述中国石化股份有限公司上海高桥分公司炼油事业部是具有五十多年历史的加工低硫石蜡基中质原油的燃料——润滑油型炼油企业,根据中国石化股份有限公司原油油种变化和适应市场发展的需求,上海高桥分公司到2007年以后除了加工大庆原油、海洋原油等低硫原油外,将主要加工含硫2.0%左右的含硫含酸进口原油。
由于常减压生产的减压蜡油和延迟焦化装置生产的焦化蜡油中含有较多的不饱和烃及硫、氮等有害的非烃化合物,这些产品无法达到催化裂化装置的要求。
为了使二次加工的蜡油达到催化裂化装置的要求,必须对焦化蜡油和减压蜡油进行加氢精制,因此上海高桥分公司炼油事业部进行原油适应性改造时,将原100万吨/年柴油加氢精制装置改造为100万吨/年蜡油加氢装置。
本装置的建设主要是为了催化裂化装置降低原料的硫含量和酸度服务。
本装置由中国石化集团上海工程有限公司设计,基础设计于2005年6月份完成,2005年8月份进行了基础设计审查,工程建设总投资2638.73万元,其中工程费用2448.74万元。
2006年7月降蜡油含硫量由原设计2.44%提高至3.28%,工程建设总概算增加820.8万元。
二、装置概况及特点1.装置规模及组成蜡油加氢精制装置技术改造原料处理能力为100万吨/年,年开工时数8400小时。
本装置为连续生产过程。
主要产品为蜡油、柴油、汽油。
本装置由反应部分、循环氢脱硫部分、氢压机部分(包括新氢压缩机、循氢压缩机)、加热炉部分及公用工程部分等组成。
2.生产方案混合原料经过滤后进入缓冲罐,用泵升压,经换热、混氢,再经换热进入加热炉,加热至350℃后进反应器进行加氢,反应产物经换热后进热高分进行气液分离,气相进一步冷却,进冷高分进行气液分离,气相进新增的循环氢脱硫塔脱硫后作为循环氢与新氢混合,组成混合氢循环使用;液相减压后至热低分,热低分的液相至催化裂化装置。
蜡油加氢工艺流程原理

蜡油加氢工艺流程原理一、蜡油加氢工艺原理蜡油加氢工艺是通过在催化剂的作用下,加氢将蜡油中的长链或支链烷烃转化为液态产品。
加氢反应需要催化剂的参与,常用的催化剂有铼、钼、钯等金属催化剂。
这些催化剂能够促进长链或支链蜡状烃的断裂和饱和,从而使其转化为液态烃类产物。
加氢反应的化学方程式如下:CnH2n+2 + H2 → CnH2n+2在这个反应中,长链或支链烷烃通过加氢反应,断裂成较短的烷烃分子。
这些烷烃分子具有较高的液态性和流动性,因此将蜡油中的固态成分转化为液态产品。
从而提高了蜡油的加工利用价值。
二、蜡油加氢工艺流程蜡油加氢工艺通常分为预处理和加氢反应两个阶段。
预处理阶段主要是将蜡油中的杂质和硫化物去除,以保证加氢反应的高效进行。
而加氢反应阶段则是将蜡油中的长链或支链烷烃转化为液态产品的过程。
1. 预处理阶段蜡油经过深冷处理后,将其中的硫和杂质去除,以提高加氢反应的反应效率。
首先,蜡油通过加热和减压,将其中的轻质烃类物质蒸馏出来,以减少后续反应中的催化剂中毒和水蒸气形成的影响。
然后,蜡油进入硫化物的重整器中,其中,通过氢气和催化剂的作用,将蜡油中的硫化物还原为硫化氢和轻质气体,从而将硫化物去除。
2. 加氢反应阶段经过预处理后的蜡油进入加氢反应器中,经过加氢催化剂的作用,将其中的长链或支链烷烃转化为液态产品。
在反应器中,蜡油混合氢气在催化剂的作用下进行加氢反应,将蜡油中的长链或支链烷烃分子断裂和饱和,从而生成液态烃类产物。
加氢反应器通常采用固定床反应器或流化床反应器,以确保反应的均匀进行和热量平衡。
3. 分离和提纯加氢反应产物中将液态烃类产品通过分馏和提纯的手段,分离出可用的燃料油或化工原料。
对剩余的蜡油加氢反应产物进行再处理和利用,以提高资源的综合利用效率。
三、蜡油加氢工艺应用蜡油加氢工艺在炼油和化工领域具有重要的应用价值,主要具有如下几个方面的应用:1. 对蜡状重质烃进行加氢处理,提高了蜡油的装置效果和加工利用价值。
- 1、下载文档前请自行甄别文档内容的完整性,平台不提供额外的编辑、内容补充、找答案等附加服务。
- 2、"仅部分预览"的文档,不可在线预览部分如存在完整性等问题,可反馈申请退款(可完整预览的文档不适用该条件!)。
- 3、如文档侵犯您的权益,请联系客服反馈,我们会尽快为您处理(人工客服工作时间:9:00-18:30)。
原料油的性质
• CGO:减压渣油(VR)通过延迟焦化得
到的重馏分油,其特点是氮含量高,对 后续加工有较大影响。
• CGO:馏程较VGO轻,但与相同馏程 直馏VGO相比,其氮含量高4~10倍, 碱氮含量也高约4~10倍
原料油的性质
我国CGO的主要性质 原料油 20℃密度(g/cm ) 硫 /w % 氮(μg/g) 碱氮(μg/g) 残炭/w% 馏程(D-1160)/℃ 初馏点 10% 30% 50% 90% 95% 247 342 -374 -435 259 364 -396 428 444 254 389 -428 472 487 252 371 -403 456 477
中国炼油工业的现状
2005年中国原油生产与石油消费状况
项目 原油产量 原油加工能力 石油消费量 原油加工量 数量/亿吨 1.82 3.28 3.17 2.95 世界排名 5 2 2 2
中国炼油工业的现状
炼厂平均加工规模显著扩大 • 加工能力在700万吨以上规模的炼厂13个
• 已建成8个加工能力达到千万吨级的炼厂
镇海、茂名、金陵、高桥、金山、齐鲁、大连、兰州 (大连石化炼油能力2050万吨/年,国内最大) • 在建的千万吨级炼厂 青岛、福建、广州、独山子、惠州
主要国家部分炼油装置能力、所占比例
原油 亿吨/ 年 美国 日本 8.39 2.35 FCC 万吨/ 年 28766 4375 % 34.3 18.6 加氢裂化 万吨/ 年 7198 866 % 8.6 3.7 加氢精制 万吨/年 59545 20297 % 71.0 86.2
2 3
沙轻DAO 0.9509 2.89 1820 81.38 13 6 0.8 2.6
沙中DAO 0.9638 4.07 1885 116.5 28 7.1 4.0 10.0
原料油性质的影响
3
伊朗轻质VGO 伊朗重质VGO 0.9082 1.72 1700 391 34 0.24 0.9121 1.89 1600 425 27 0.36
沙特中质VGO 0.9235 3.10 898 212 31 0.23
伊朗VGO 0.9050 1.90 1800 368 38 0.1
沙特轻质VGO 0.9118 2.50 1100 213 35
蜡油加氢处理的必要性
欧洲汽油规格变化 项 目 1993 年 欧洲Ⅰ号 0.1 5 无规定 无规定 2.5 13 1998 年 欧洲Ⅱ号 0.05 5 无规定 无规定 2.5 13 2000 年 欧洲Ⅲ号 0.015 1 42 18 2.7 5 2005 年 欧洲Ⅳ号 0.005 1 35 18 2.3 2009 年 欧洲Ⅴ号 0.001 1 35 18 2.3 汽车排放标准 硫含量/% 苯含量/% 芳烃含量/% 烯烃含量/% 氧含量/% 铅含量/mg/L
重馏分油加氢处理技术
重馏分油:VGO、CGO、DAO 加氢处理的主要目的:优质的FCC原料
气体 石脑油 柴油 干气 液化气 催化汽油
氢气 VGO/CGO/DAO 加氢处理
分 馏 塔
催 化 裂 化
催化柴油
>350℃加氢尾油
重循环油
油浆
重馏分油加氢处理的作用
改善FCC原料质量,提高其可裂化性,减少生
3
管输CGO 0.8826 0.89 3825 1367 <0.01
大庆CGO 0.8732 0.17 3700 903 0.01
辽河CGO 0.9138 0.29 5200 2362 0.18
胜利CGO 0.9140 1.00 6200 2248 0.31
原料油的性质
DAO:密度、馏程、粘度、S、N、碱 氮、残炭、金属含量均比同一原油直 馏VGO要高。在达到相同的产品硫含 量时,加氢处理条件较为苛刻,其催 化剂运转周期也较短。
焦。
由FCC装置生产低(或超低)硫汽油和柴油。 减少FCC烟气中SOX,NOX排放。 当加氢处理有一定程度的轻质化时,可增加中 馏分油收率。
重馏分油加氢处理的作用之一
改善FCC原料质量,提高其可裂化性:
通过加氢处理,降低原料稠环芳烃含量(使
之变为较易裂化的环烷烃)、提高氢含量、降
低氮含量(特别是碱性氮化物) ,则可提高
80 60 40 20 0 0.00
C5 ~221℃
C5 ~204℃
C5 ~190℃
0.05
0.10
0.15
0.20
0.25
0.30
0.35
0.40
0.45
FCC原料油硫含量/m%
重馏分油加氢处理的作用之三
减少FCC烟气中SOX,NOX排放:
FCC装置的再生器是炼厂主要污染物排放点
之一。美国对于未设有SO2排放控制设施的装
蜡油加氢处理技术
加氢车间 孙栋良
世界炼油工业现状
2005年底,世界炼油能力42.52亿吨,其中 • 美国 8.56亿吨
• 中国 3.28亿吨
• 俄罗斯2 .67亿吨 • 日本 2.34亿吨
世界炼油工业现状
• 炼油能力略有增长,炼厂平均规模明显提 高
年份 2000 2003 2005 炼厂数 756 722 661 原油加工能力 (亿吨/年) 40.77 40.94 42.52 炼油厂平均规模 (万吨/年) 539 567 643
目前世界最大的炼油厂(≥2000万t/a)
序号 公 司 1 帕拉瓜纳炼制中心 2 SK(前油公公司) 3 LG-加德士公司 4 埃克森-美孚公司 5 印度信任石油公司 6 Hovensa股份有限公司 7 双龙精油株式会社 8 埃克森-美孚公司 9 埃克森-美孚公司 10 俄罗斯投资公司 11 英国石油公司 12 英国石油公司 13 壳牌东方石油公司 14 伊朗国家石油公司 15 沙特阿拉伯国家石油公司 地 点 原油加工量(万t/a) 委内瑞拉,胡迪瓦那 4700 韩国,蔚山 4085 韩国,仁川 3168 新加坡,亚辽查湾岛裕廊 2900 印度,贾姆纳格尔 2700 维尔京群岛,圣克罗依岛 2625 韩国,温山 2600 美国,得克萨斯洲贝汤 2540 美国,路易斯安那巴吞鲁日 2425 俄罗斯,安加尔斯克 2204 美国,德克萨斯洲德克萨斯城 2185 美国,印地安那洲怀廷 2050 新加坡,武公岛 2025 伊朗,阿巴丹 2000 沙特阿拉伯,拉比格 2000
• 催化裂化:1942年第一套流化催化裂化 装置运转以来,特别是20世纪60年代分 子筛催化剂的应用使此工艺迅速发展, 现已成为炼油厂的核心加工工艺,是最 重要的原油二次加工手段。
蜡油加氢处理的必要性
• 我国催化裂化汽油占汽油调和总量70% 以上,催化裂化柴油占柴油调和总量的 近三分之一。汽油和柴油中的硫主要来 源于催化裂化汽油和柴油 。 • 随着环保意识的增强及环保法规的日益 严格。世界范围内燃料规格不断提高。
由FCC装置生产低(或超低)硫汽柴油:
100
FCC汽油硫含量/( μ g/g)
90 80 70 60 50 40 30 20 10 1000 1500 2000 2500 3000 3500 汽油硫含量与原料硫含量的关系
100
FCC汽油硫含量/( μ g/g)
置,要求FCC进料硫含量<0.3%,预计国内炼
油厂的SOX排放限值也将逐步向国际先进水平 靠拢。
重馏分油加氢处理的作用之四
当加氢处理有一定程度的轻质化时,可增 加中馏分油收率:
采用HT/HC两种催化剂,控制单程转化>30%;
与FCC联合形成组合工艺,柴油收率最高,汽
柴油质量好。
化学原理
• 主要目的是降低原料油中的杂质含量,提高其质量和 可裂化性。 • 希望发生的化学反应主要有:脱金属(DM)、脱残 炭(DCCR,即减少导致生成积炭或生焦的化合物含 量)、脱硫、脱氮和芳烃饱和等 。 • 加氢处理中需要达到一定的轻质化率时,还会发生烃 类分子C-C键断裂的加氢裂化反应,包括烷烃加氢裂 化、烷基芳烃和环烷烃的加氢脱烷基、环烷烃开环。
蜡油加氢处理的必要性
欧洲柴油规格变化 项目 汽车排放标准 十六烷值,≮ 十六烷指数,≮ 密度/kg/m3 多环芳烃含量 /%(v/v) ≯ T/℃ ≯ 硫含量/% ≯ 1993 年 欧洲Ⅰ号 49 46 820-860 无规定 370 0.2 1998 年 欧洲Ⅱ号 49 46 820-860 无规定 370 0.05 2000 年 欧洲Ⅲ号 51 46 820-845 11 360 0.035 820-825 11 340 0.005 820-825 11 340 0.001 2005 年 欧洲Ⅳ号 51 2009 年 欧洲Ⅴ号 51
+
50
60
70
80
HD3 Aro/m%
原料油中碱性氮 与FCC转化率和汽油产率之间的关系
100 90 液化气 汽 油 重 油 转化率 80 70 60 50 40 30 20 10 0 0 250 500 750 1000 1250 1500
产品收率和转化率,%
碱性氮含量, ppm
重馏分油加氢处理的作用之二
世界炼油工业现状
出现一批大型和超大型炼油厂 在同等规模下,单套装置比双套装置投资减 少24%,装置能耗减少19%;比三套装置投 资减少55%,能耗减少29%。
大型炼厂规模以1000-2000万吨/年为宜。 产业集中度不断提高
2000万吨/年规模的炼厂 1998年,15座 2004年,18座 2005年,20座
德国
伊朗 中国 全球
1.16
0.74 3.04 41.92
1792
150 10232 78603
15.4
2.0 33.6 18.7
964
699 1502 24414
8.3
9.5 4.9 5.8
8961
999 7254 199622