MIT6_092IAP10_lec07
NI sbRIO-9627单板RIO OEM设备技术规格说明说明书
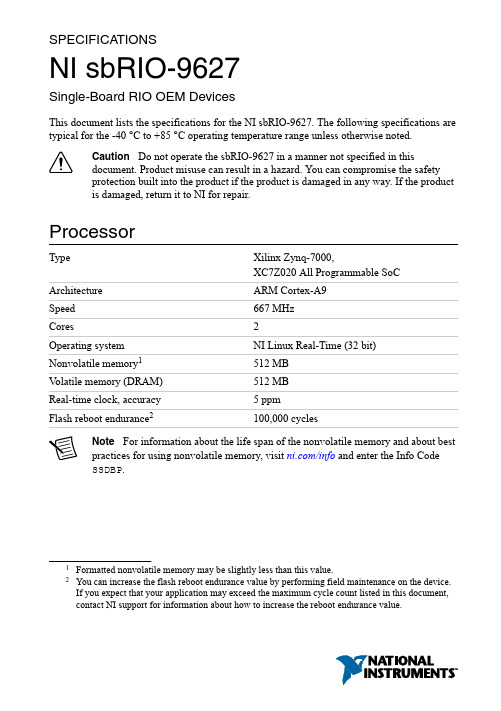
SPECIFICA TIONSNI sbRIO-9627Single-Board RIO OEM DevicesThis document lists the specifications for the NI sbRIO-9627. The following specifications are typical for the -40 °C to +85 °C operating temperature range unless otherwise noted.Caution Do not operate the sbRIO-9627 in a manner not specified in thisdocument. Product misuse can result in a hazard. You can compromise the safetyprotection built into the product if the product is damaged in any way. If the productis damaged, return it to NI for repair.ProcessorType Xilinx Zynq-7000,XC7Z020 All Programmable SoC Architecture ARM Cortex-A9Speed667 MHzCores2Operating system NI Linux Real-Time (32 bit)Nonvolatile memory1512 MBV olatile memory (DRAM)512 MBReal-time clock, accuracy 5 ppmFlash reboot endurance2100,000 cyclesNote For information about the life span of the nonvolatile memory and about bestpractices for using nonvolatile memory, visit /info and enter the Info CodeSSDBP.1Formatted nonvolatile memory may be slightly less than this value.2You can increase the flash reboot endurance value by performing field maintenance on the device.If you expect that your application may exceed the maximum cycle count listed in this document, contact NI support for information about how to increase the reboot endurance value.Operating SystemNote For minimum software support information, visit /info and enter theInfo Code swsupport.Supported operating system NI Linux Real-Time (32-bit)Minimum software requirementsApplication softwareLabVIEW LabVIEW 2015,LabVIEW 2015 Real-Time Module,LabVIEW 2015 FPGA ModuleEclipse Edition 2014C/C++ Development Tools forNI Linux Real-Time3Driver software NI CompactRIO Device Drivers August 2015 Reconfigurable FPGAType Xilinx Zynq-7000,XC7Z020 All Programmable SoCNumber of logic cells85,000Number of flip-flops106,400Number of 6-input LUTs53,200220Number of DSP slices(18 x 25 multipliers)Available block RAM560 KBNumber of DMA channels16Number of logical interrupts32Network/Ethernet PortNumber of interfacesFront Panel Ethernet 1 (Eth0)RMC Ethernet 1 (Eth1)3C/C++ Development Tools for NI Linux Real-Time is an optional interface for C/C++programming of the sbRIO-9627 processor. Visit /info and enter Info Code RIOCdev for more information about the C/C++ Development Tools for NI Linux Real-Time.2| | NI sbRIO-9627 SpecificationsNetwork interface10Base-T, 100Base-TX, and1000Base-T Ethernet4Compatibility IEEE 802.3Communication rates10 Mbps, 100 Mbps,1000 Mbps auto-negotiated, half-/full-duplex Maximum cabling distance100 m/segmentRS-232 (DTE) Serial PortNumber of interfacesOnboard RS-232 2 (Serial1, Serial2)RMC RS-232 via FPGA 3.3 V DIO 4 (Serial4, Serial5, Serial6, Serial7)Baud rate support ArbitraryMaximum baud rate230,400 bpsData bits5, 6, 7, 8Stop bits1, 2Parity Odd, Even, Mark, SpaceFlow control RTS/CTS, XON/XOFF, DTR/DSR, NoneRS-485 Serial PortNumber of interfacesOnboard RS-485 1 (Serial3)RMC RS-485 via FPGA 3.3 V DIO 2 (Serial8, Serial9)Maximum baud rate460,800 bpsData bits5, 6, 7, 8Stop bits1, 1.5, 2Parity Odd, Even, Mark, SpaceFlow control XON/XOFF4For revision D and earlier, 1000Base-T Ethernet link and communication is not guaranteed forprimary or secondary Ethernet ports below -20 °C. If you expect ambient temperatures below-20 °C, NI recommends using a 10/100 network infrastructure or assigning 10/100Mbpscommunication speeds to the Ethernet Adapter in NI Measurement & Automation Explorer(MAX).NI sbRIO-9627 Specifications| © National Instruments| 3Wire mode4-wire, 2-wire, 2-wire auto Isolation voltage, port to earth ground NoneEmbedded CANNumber of interfacesOnboard CAN 1 (CAN0)RMC CAN via FPGA 3.3 V DIO 1 (CAN1)Onboard CAN transceiver NXP PCA82C251T Maximum baud rate 1 MbpsMinimum baud rate10 kbpsUSB PortNumber of interfacesFront Panel USB Host 1 (USB0)RMC USB Host/Device 1 (USB1) Compatibility USB 2.0, Hi-Speed Maximum data rate480 Mb/sMaximum front panel USB current900 mASD Card SlotNumber of interfacesFront Panel SD 1 (SDIO0)RMC SD via FPGA 3.3 V DIO 1 (SDIO1)Supported Standards SD, SDHC5Front Panel SD ThroughputRead12.0 MB/s maximumWrite9.0 MB/s maximum5Both standard SD and microSD interfaces are supported.4| | NI sbRIO-9627 SpecificationsRMC SD via FPGA DIO ThroughputRead8.0 MB/s maximumWrite 6.5 MB/s maximumNote RMC SD has slower throughputs as the Xilinx Zynq-7000 requires SDinterfaces through the FPGA to operate at standard speed rather than at high speed.3.3 V Digital I/O on RMC ConnectorNumber of DIO channels96Maximum tested current per channel±3 mANote The performance of the RMC DIO pins is bounded by the FPGA, signalintegrity, the application timing requirements, and the RMC design. A general SPIapplication will typically be able to meet these requirements and achieve frequenciesof up to 10 MHz. For more information on using DIO to connect to RMCs, visit/info and enter the Info Code RMCDIO.Input logic levelsInput low voltage, V IL-0.3 V minimum; 0.8 V maximumInput high voltage, V IH 2.0 V minimum; 3.45 V maximumOutput logic levels2.4 V minimum;3.45 V maximumOutput high voltage, V OHwhen sourcing 3 mA0.0 V minimum; 0.4 V maximumOutput low voltage, V OLwhen sinking 3 mA3.3 V Digital I/O on 50-Pin IDC ConnectorNumber of DIO channels4Maximum tested current per channel±3 mAInput logic levelsInput low voltage, V IL-0.3 V minimum; 0.8 V maximumInput high voltage, V IH 2.0 V minimum; 5.25 V maximumNI sbRIO-9627 Specifications| © National Instruments| 5Output logic levelsOutput high voltage, V OH2.4 V minimum;3.45 V maximumwhen sourcing 3 mA0.0 V minimum; 0.4 V maximumOutput low voltage, V OLwhen sinking 3 mAAnalog Input CharacteristicsNumber of channels16 single-ended or 8 differential ADC resolution16 bitsMaximum aggregate sampling rate200 kS/sInput range±10 V, ±5 V, ±2 V, ±1 V Maximum working voltage (signal + common mode)10 V range±11 V5 V range±10.5 V2 V range±9 V1 V range±8.5 VInput impedancePowered on> 1 GΩ in parallel with 100 pFPowered off/overload 2.3 kΩ minimumOvervoltage protectionPowered on±25 V, for up to 2 AI pinsPowered off±15VAI accuracy6| | NI sbRIO-9627 SpecificationsGain drift 12 ppm of reading/°C Offset drift 4 ppm of range/°C AI noise10 V range 200 μVrms 5 V range 105 μVrms 2 V range 45 μVrms 1 V range 30 μVrmsINL ±64 ppm of range, maximum DNLNo missing codes guaranteed CMRR, DC to 60 Hz -80 dB Input bandwidth (-3 dB)540 kHz, typical Settling error (multichannel scanning)±60 ppm step size, typical Crosstalk (10 kHz)-70 dBTypical performanceFigure 1. Common Mode Rejection Ratio versus FrequencyC M R R (d B )Frequency (Hz)NI sbRIO-9627 Specifications | © National Instruments | 7Figure 2. Normalized Signal Amplitude versus FrequencyN o r m a l i z e d S i g n a l A m p l i t u d e (d B )Frequency (Hz)Figure 3. Settling Error versus Source ImpedanceE r r o r (p p m o f S t e p S i z e )Source Impedance (Ω)10010001000010000010000010000100010010Analog Output CharacteristicsNumber of channels 4DAC resolution16 bits8 | | NI sbRIO-9627 SpecificationsMaximum update rate6336 kS/sRange±10 VOverrange operating voltageMinimum10.3 VTypical10.6 VMaximum10.9 VOutput impedance0.4 Ω typicalCurrent drive±3 mA/channel maximumProtection Short-circuit to groundPower-on state70 VAO accuracyGain drift23 ppm of reading/°COffset drift 5.4 ppm of range/°CINL±194 ppm of range, maximumDNL±16 ppm of range, maximumCapacitive drive 1.5 nF, typicalSlew rate 3.7 V / μsec, typicalSettling time (100 pF load to 320 μV)FS step50 μs2 V step12 μs0.2 V step9 μs6This is the maximum update rate when running one AO channel in a loop with the FPGA top-level clock set to 40 MHz.7When the analog output initializes, a voltage glitch occurs for about 20 μs, peaking at 1.3 V,typical.8Range is 5 V.NI sbRIO-9627 Specifications| © National Instruments| 9CMOS BatteryNote The battery is user-replaceable. The NI sbRIO device ships with a BR1225coin cell battery from RAYOV AC, which is industrial-rated. Ensure that powerremains connected to the NI sbRIO device while you replace the battery so thattime-keeping is not disrupted. Refer to the Battery Replacement and Disposalsection for information about replacing the battery.10 yearsTypical battery life with power applied topower connectorTypical battery life in storage at 55 °C 2.5 years9Power Outputs on RMCCaution Exceeding the power limits may cause unpredictable device behavior.+5 V power outputOutput voltage 5 V ±5%Maximum current 1.5 AMaximum ripple and noise50 mV+3.3 V_AUX power outputOutput voltage 3.3 V ±5%Maximum current0.33 AMaximum ripple and noise50 mVFPGA_VIO power outputOutput voltage 3.3 V ±5%Maximum current0.33 AMaximum ripple and noise50 mVPower RequirementsThe NI sbRIO device requires a power supply connected either to the power connector or through the VIN_filtered pins through the RMC. Refer to the Powering On the NI sbRIO Device section in the NI sbRIO-9627 Getting Started Guide on /manuals for information about connecting the power supply. Refer to the NI sbRIO-9607/9627 RMC9Battery life may drop dramatically in extreme temperatures.10| | NI sbRIO-9627 SpecificationsDesign Guide on /manuals for more information about how to power the NI sbRIO device through the RMC.Caution Exceeding the power limits may cause unpredictable device behavior.Recommended power supply55 W, 30 VDC maximumPower supply voltage range9 VDC to 30 VDCReversed-voltage protection30 VDCPower consumption with RMC29 W maximumEnvironmentalCaution Clean the sbRIO-9627 with a soft, nonmetallic brush. Make sure that thedevice is completely dry and free from contaminants before returning it to service.-40 °C to 85 °C10Local ambient operating temperature neardevice (IEC 60068-2-1, IEC 60068-2-2)Maximum reported onboard sensor temperatureCPU/FPGA temperature98 °CPrimary System temperature85 °CSecondary System temperature85 °CTable 1. Component Maximum Case TemperatureThe sbRIO-9627 includes three onboard temperature monitoring sensors to simplify validation of a thermal solution by indicating thermal performance during validation and deployment.10If you expect ambient temperatures below -20 °C, NI recommends using a 10/100 network infrastructure or assigning 10/100Mbps communication speeds to the Ethernet Adapter in NI MAX.Refer to the Network/Ethernet Port section of this document for more information.11Use digital approach to ensure the on-chip temperature reading is below 98°C.NI sbRIO-9627 Specifications| © National Instruments| 11The sensors measure the CPU/FPGA junction temperature and printed circuit board temperatures that can be used to approximate the primary and secondary side local ambient temperatures. This approach is called digital validation. Alternatively, the traditional analog approach using thermocouples can be used to validate thermal performance. The digital approach is more accurate for determining the performance of the CPU/FPGA but is more conservative for determining the local ambient temperatures. NI recommends using digital validation.For digital validation, ensure that the reported CPU/FPGA, reported Primary System, and reported Secondary System temperatures do not exceed any of the maximum temperatures listed in this document. Thermal validation is complete if the reported temperatures are within specifications. For more information about how to access the onboard sensors, visit / info and enter the Info Code sbriosensors. If the reported Primary System temperature or reported Secondary System temperature exceed the maximum temperatures listed in this document then analog validation may be used for further verification.For analog validation, measure the local ambient temperature by placing thermocouples on both sides of the PCB, 5 mm (0.2 in.) from the board surface. Avoid placing thermocouples next to hot components such as the CPU/FPGA or near board edges, which can cause inaccurate temperature measurements. In addition to the local ambient temperature, the case temperature of the components should not exceed the recommended maximum case temperature.Note Some systems may require a heat sink or air flow to remain within themaximum allowed temperature ranges. You can mount the Thermal Kit forNI sbRIO-9607/9627/9637 (153901-02) heat spreader on the NI sbRIO device.Note The NI sbRIO device thermal performance is greatly influenced by severalfactors, including resource utilization, mounting, and adjacent power dissipation.These factors can substantially affect the achievable external ambient temperature atwhich the maximum local and reported temperatures are reached. NI recommendsadditional thermal design to remain within the maximum allowed temperatureranges. For information about and examples of environmental and design factors thatcan affect the thermal performance of NI sbRIO systems, visit /info and enterthe Info Code sbriocooling. For device-specific guidelines about enablingproper thermal design, refer to the NI sbRIO-9627 User Manual on /manuals.-40 °C to 85 °CStorage temperature(IEC 60068-2-1, IEC 60068-2-2)Operating humidity (IEC 60068-2-78)10% RH to 90% RH, noncondensing Storage humidity (IEC 60068-2-78)5% RH to 95% RH, noncondensing Maximum altitude5,000 mPollution Degree (IEC 60664)2The NI sbRIO device is intended for indoor use only.12| | NI sbRIO-9627 SpecificationsPhysical CharacteristicsWeight131.3 g (4.631 oz)Safety VoltagesConnect only voltages that are below these limits.V terminal to C terminal30 VDC maximum, Measurement Category I Measurement Category I is for measurements performed on circuits not directly connected to the electrical distribution system referred to as MAINS voltage. MAINS is a hazardous live electrical supply system that powers equipment. This category is for measurements of voltages from specially protected secondary circuits. Such voltage measurements include signal levels, special equipment, limited-energy parts of equipment, circuits powered by regulated low-voltage sources, and electronics.Caution Do not connect the sbRIO-9627 to signals or use for measurements withinMeasurement Categories II, III, or IV.Environmental ManagementNI is committed to designing and manufacturing products in an environmentally responsible manner. NI recognizes that eliminating certain hazardous substances from our products is beneficial to the environment and to NI customers.For additional environmental information, refer to the Minimize Our Environmental Impact web page at /environment. This page contains the environmental regulations and directives with which NI complies, as well as other environmental information not included in this document.Waste Electrical and Electronic Equipment (WEEE)EU Customers At the end of the product life cycle, all NI products must bedisposed of according to local laws and regulations. For more information abouthow to recycle NI products in your region, visit /environment/weee.Battery Replacement and DisposalBattery Directive This device contains a long-life coin cell battery. If you need toreplace it, use the Return Material Authorization (RMA) process or contact anNI sbRIO-9627 Specifications| © National Instruments| 13authorized National Instruments service representative. For more information aboutcompliance with the EU Battery Directive 2006/66/EC about Batteries andAccumulators and Waste Batteries and Accumulators, visit /environment/batterydirective.电子信息产品污染控制管理办法(中国RoHS)中国客户National Instruments符合中国电子信息产品中限制使用某些有害物质指令(RoHS)。
SignalTEK 10G 10G Ethernet Troubleshooter and Band

Why do I need a10G Ethernet T ester?ProblemLAN networks are at risk Solution SignalTEK 10G willAvoid network downtimeTroubleshoot Ethernet connectivity issues faster using diagnostic tools.Pinpoint bottlenecks fasterDiscover which part of your network is causing the bottleneck.Validate network upgradesVerify Multi-Gigabit switch upgrades to 1/2.5/5 and 10Gb/s speeds.Prove the maximum bandwidthProvide “proof of performance” PDF reports to the client.The new SignalTEK 10G measures the maximum bandwidth of the network cabling up to 10 Gigabits per second. Bysimulating actual network traffic users can test, troubleshoot and document network and data cable performance up to 10 Gigabit Ethernet standards.SignalTEK 10G has built-in Wi-Fi connectivity to connect seamlessly to the free AnyWARE Cloud test management system. AnyWARE Cloud offers pre-configuration to eliminate errors on-site, label printer connectivity to save time and “proof of performance” PDF reports for the clients.SignalTEK 10G10G Ethernet Troubleshooter and Bandwidth TesterIncrease your network speedfrom 1Gb/s to 10Gb/sProblemThere are 111 billion metres of Cat5e/Cat6 cabling installed globally that is limited to 1Gb/s bandwidth speeds due to the current switches deployed. Upgrading to Multi-Gigabit switches could increase speed but it is unclear what bandwidth the existing cabling will support.SolutionUse SignalTEK 10G to verify what the data cabling will support (up to 10Gb/s) before spending moneyon new Multi-Gigabit switches delivering2.5/5/10Gb/s speeds. Use the SignalTEK 10G again following the upgrade to prove performance to the client with the “proof of performance” PDF reports.As simple as 1-2-3Easy to understand traffic light status - The simple traffic lightindicator displays Good, Marginal or Poor power level based onIEEE 802.3 1G/10G limits.Max throughput test - The SignalTEK 10G will prove the maximumavailable bandwidth over the fibre link up to 10Gb/s.Discover a faulty SFP – The SFP temperature is measured to helpunderstand if it has become faulty.Will my existing cablinginfrastructure supportMulti-Gigabit technology?10G/Multi-Gigabit Performance90W PoE for AV and Digital SignageTest copper and fibrevertical cablingVoIP testing and troubleshootingMeets your network needs today and tomorrow.The SignalTEK 10G will help to increase network bandwidth without replacing expensive cableinfrastructure, troubleshoot PoE and Ethernet issues and prove the maximum bandwidth up to 10 Gigabits per second.6Testing through Network testing andConduct preventative maintenance testing, audit network capabilities and Prove performance of new cableinstallations up to 10GNetwork T estingThe SignalTEK 10G is also a network tester for troubleshooting and maintenance of active and passive copper and fibre networks.Port & network summary info Press the Autotest button to display summary information and allow for detailed inspection of networkparameters.VLAN detection & operationAutomatic detection of VLAN IDsallows the user to configure SignalTEK10G for operation on a VLAN.Custom WiremapUse a list of wiremap templates forcommon Ethernet cable types aswell as non-Ethernet cables, such asProfinet and ISDN.CDP/LLDP/EDP port informationShow port information using Cisco Discovery Protocol (CPD). Link Layer Discovery Protocol (LLDP) and Extreme Discovery Protocol (EDP).NetscanDisplay list of IP and MAC addressesof every device connected tothe network.72-hour event logFind rogue devices and intermittentissues using the 72-hour event log.SignalTEK 10G logs all network eventsover a 72-hour period to help diagnose connectivity issues faster, reducing hours onsite and reducing trips to the site. Leave the tester onsite, connect remotely tomonitor network activity, view the event log and control all functions of the tester from the office.The SignalTEK 10G will log all network eventsover a 72-hour period to help diagnose connectivity issues faster, reducing hoursonsite and reducing trips to site.72-hour event log captures network events down to the second eliminatingguessworkNo more trial and errorAccurately measure the maximum power available Supports PoE up to 90W (PoE++)Test all PoE Classes (0-8) and Types (af/at/bt)Identifies the powered pairsDetermine whether power is from a switch or mid-span injectorVerify the PoE installationPass / Fail indication to IEEE standards Extended power testSome switches may provide power exceeding their IEEE Class rating. Measure the maximum available power up to 90 watts.PoE T esting.Eliminate GuessworkThe SignalTEK 10Geliminates guesswork when installing, maintaining and troubleshooting wherePoE is deployed up to 90W (PoE++).10Adoption of Power over Ethernet (PoE)In just a few short years we have seen many different applications increasing adopt PoE, such as monitors, digital signage, phones, security cameras, lighting and access control.Previously technicians had to understand all the various standards, device power outputs and cable lengths to be sure a device will operate successfully.The SignalTEK 10G identifies the Class of the PoEsource and power available up to 90W to a PoE device regardless of cable length, cable quality or other factors. A clear pass/fail is provided to IEEE 802.3af/at/bt standards.The SignalTEK 10G identifies the Class of the PoE source and power available up to 90W to a PoE deviceregardless of cable length, cablequality or other factors.11Proof of PerformanceCloud software• Operates anywhere with a web browser – AnyWARE Cloud operates on a PC, Mac and tablet devices (Android and iOS)• Free storage – No need for separate servers or backup systems.• Easy to find project files – Attach all project filesincluding cable layout drawings, videos, and photos into the AnyWARE Cloud. Everything you need in one place. • Share reports easier – Use AnyWARE Cloud to share links to the test reports eliminating the need to manually email large attachments.• Reduce training time with WalkMe – AnyWARE Cloud is embedded with the WalkMe digital adoption platform providing proactive, step-by-step guidance on all key tasks.Fleet management• Easily manage the certifier fleet – Fleet manager allows you to see who has the SignalTEK 10G when the software was last updated and when the results were last synced. Allowing you to manage tester downtime and ensuring results are transferred back to the office and not lost or deleted.Professional PDF reporting• Customer profiles – Create a profile for each of thecustomers with their company logo, address and contact details. This information is automatically pulled through to the reports, saving time.Report formats• Summary report – This is a report showing multiple tests per page.• Detailed report – This is a comprehensive report with all the measurement results with one page per test. Reports can be generated on the SignalTEK 10G or on the free IDEAL AnyWARE Cloud.The AnyWARE Cloudmanagement system allows real time collaboration between Project Managers and Field Technicians. There is no need for Field Technicians to setup the SignalTEK 10G, Project Managers pre-configure thejobs and tests in the AnyWARE Cloud, eliminating potential mistakes and compressing the time taken to prepare reports for customers.Test Management SoftwareIDEAL AnyWARE Cloud Jobs screenIDEAL AnyWARE Cloud Test Result report12ax throughput test up to 10GComplete ConnectivityWi-Fi connectivity to the AnyWARE Cloud management system. USB connection for transferring test dataBuilt-in PDF ReportingReports can be generated directly from the SignalTEK 10G as well as the CloudPartner FinderProvides audible tone and visible indicator when connected tothe remote unitTouchscreenHigh resolution impact resistant touchscreenfor ease of useInternal LoadspeakerAudible tones assist theuser when testingIntuitive UserInterfaceSimplified user interfacefor easy setup andoperationRugged DesignRubberised housing, protected screenand protected measurement portLabel Printer ConnectivityEasily send label IDs to printers for fast and accurate labellingSignalTEK 10GPart NoDescriptionUPGRADE10GFIB UPGRADE SignalTEK 10G - Fibre testing option UPGRADE10GNETUPGRADE SignalTEK 10G - Network testing optionSignalTEK 10G is a future-proof investment as additional features can be unlocked with a simple license key when required. There are two upgrade options to choose from: fibre testing and advanced network testing.Future-proof the investment14Who is SignalTEK 10G designed for?SolutionSignalTEK 10GCT R157000SignalTEK 10GFT R157001SignalTEK 10GNT R157002SignalTEK 10GPRO R157003CategoryDisplays voltage and which pairs have PoEPass / Fail to PoE IEEE standardsMax power available (up to 90 watts)Type (af/at/bt) and Class (1 to 8)P o EF i b r eo p t i o n a lC o p p e rUptime efficiency and 72 hour event log Switch Speed - 100M, 1G, 2.5G, 5G, 10G Testing with packet loss, jitter and delay VLAN, PING, TraceRoute, Hub blink, NetScanProve network performance up to 10GCDP/LLDP/EDP port information N e t w o r ko p t i o n a lPass / Fail to fibre IEEE standards Wiremap, distance to fault, length Optical Tx/Rx power indication Max bandwidth test up to 10Gb/s SFP temperature, vendor and model Cable tracing (with compatible probe)Max bandwidth test up to 10Gb/sData transmission test 1/2.5/5/10GbSupports SFP/SFP+ (MM&SM)Pass / Fail to copper IEEE standardsData transmission test 1/10Gb NbaseT/Multi-Gigabit test 1/2.5/5/10Gb 15Proof of PerformanceIDEAL NETWORKS, SignalTEK and the IDEAL AnyWARE logos are trademarks or registered trademarks of IDEAL INDUSTRIES NETWORKS LIMITED.IDEAL INDUSTRIES NETWORKS LIMITEDStokenchurch House, Oxford Road, Stokenchurch, High Wycombe, Buckinghamshire, HP14 3SX, UK.Tel. +44 (0)1925 428 380 | Fax. +44 (0)1925 428 381********************Specification subject to change without notice. E&OE© IDEAL INDUSTRIES NETWORKS LIMITED 2020Publication no.: 157805 Rev.1SignalTEK 10G10G Ethernet Troubleshooterand Bandwidth TesterOrdering informationOptional Accessories。
IS104GPS-2F 6-port Gigabit managed PoE switch User

User ManualIS104GPS-2F6-port Gigabit managed PoE switchInstallation Manual Introduction<User Manual>mainly introduces the hardware features, installation methods,and precautions during the installation of IS104GPS-2F.This manual includes the following sections:Chapter1:Product introduction.Briefly describe the basic functions and features of the switch,detailed hardware and software specifications and appearance information.Chapter2:Hardware Connections.Guide the connection of switch with other devices and precautions.Chapter3:Product Installation.Guide the hardware installation method and precautions.Chapter4:Product Packaging and Use Recommendations.Chapter1Product Introduction1.1Product introductionThe IS104GPS-2F is a6-port Gigabit-managed industrial PoE switch that provides4Gigabit ports and2Gigabit SFP ports.Each PoE port can provide up to46W for IEEE802.3af/at compatible powered devices(PDs).It is especially suitable for applications where AC power is not easily available or high wiring costs.It support EMC industrial grade4protection;corrugated high-strength aluminum profile housing,IP40grade,low power design,seismic rail mounting,-40°C-75°C operating temperature, can work in harsh environments;IS104GPS-2F also supports Apollo cloud one-stop management platform for status checking and management monitoring,to make it become a reliable solution for Intelligent transportation,video surveillance and other harsh industrial environments.21.2FeaturesFull Gigabit Ethernet port4full Gigabit RJ45PoE network port,and2Gigabit SFP ports, breaking the traditional100M limitation,data transmission will not stuckBroadcom high performance industrial grade chip for more stable performanceBroadcom high-performance industrial-grade chips that dramatically increase network data processing ratesPowerful working environmentEMC industrial grade4protection;corrugated high-strength aluminum profile housing,IP40grade,low power design,seismic rail mounting,-40°C-75°C operating temperature,can work in harsh environments3Support Apollo cloud platform one-stop management Support cloud platform to visualize management of switches and attached power devices,making operation and maintenance management easier1.3Software and hardware specificationsHardware specificationChipBroadcom high performance chipFlash16MBRAM64MBDDRPort410/100/1000M RJ45Port21000M SFP PortPoE Power supply 410/100/1000MbpsRJ45Port support 802.3af/atPoE power supplyThe maximum power per port is46W4Indicator 6Link/Act indicator4POEindicatorALM Alarm indicatorP1、P2Power Indicator1SYS indicatorPerformance Forward mode:store and forward Backplane bandwidth:12Gbps Packet forwarding rate:8.9Mpps Support8K MAC address table depthStandard protocol IIEEE802.3:Ethernet Media Access Control (MAC)ProtocolIEEE802.3i:10BASE-T EthernetIEEE802.3u:100BASE-TX Fast EthernetIEEE802.3ab:1000BASE-T Gigabit Ethernet IEEE802.3z:1000BASE-X Gigabit Ethernet (optical fiber)5IEEE802.3ad:Standard method for performing link aggregationIEEE802.3x:Flow ControlIEEE802.1p:LAN Layer2Qos/Cos protocol for traffic prioritization(multicast filtering)IEEE802.1q:VLAN Bridge OperationIEEE802.1d:STP spanning treeIEEE802.1s:MSTP Spanning TreeIEEE802.1w:RSTP Spanning TreeIEEE802.3afIEEE802.3atIndustry Standard EMI:FCCCFR47Part15,EN55022/CISPR22, Class AEMS:IEC61000-4-2(ESD):±8kV(contact),±15kV6(air)IEC61000-4-3(RS):10V/m(80MHz-2GHz)IEC61000-4-4(EFT):Power Port:±4kV;Data Port:±2kVIEC61000-4-5(Surge):Power Port:±2kV/DM,±4kV/CM;Data Port:±6kVIEC61000-4-6(CS):3V(10kHz-150kHz);10V (150kHz-80MHz)IEC60068-2-6(Vibration)IEC60068-2-27(Shock)IEC60068-2-32(Free Fall)Operation environment Working temperature:-40~75°CStorage temperature:-40to75°CRelative humidity:5%to95%(no condensation)7Certification CE,FCC,RoHSMean timebetweenfailures(MTBF)100,000hrsWarranty3yearsLightningprotectionNetwork port:±6KV power port:±4KV ESD Contact:±8KV Air:±15KVPhysical specification Input:48-56VDCHousing:IP40grade protection,corrugated high strength metal housingInstallation:DIN rail mountingSize:163mm×46.5mm×110mm,Weight:1kg8Software specification101112131.4AppearanceIndicator StatusDescriptionP1、P2On The corresponding power supply working normally.Off The corresponding power supply is not connected or working abnormal.SYS Blink System is running normally14ingOff/ alwa ys brig ht System operation is abnormal/start unsuccessfulALM On Alarm start upOff Alarm not triggeredLink/ACT F1-F4BlinkingSFP port is working normalOff SFP port is working abnormally/port is not connected1516Chapter 2.Hardware Connection2.1Connect to RJ45portUse the network cable to connect the switch to the RJ45port of network device.Normally,the switch's downlink port has POE power supply enabled by default.It can support POE power supply to AP ,bridge,network camera and other PDs which comply with IEEE802.3af and IEEE802.3atstandards.2.2Connect to the SFP portThe SFP port of the IS104GPS-2F supports only Gigabit fiber modules.It is recommended to use standard SFP module products. The process of installing a fiber module on a switch is as follows:1.Grasp the fiber module from the side and insert it smoothly along the SFP port slot of the switch until the fiber module is in close contact with the switch;2.Confirm the Rx and Tx ports of the fiber module when connecting.Insert one end of the fiber into the Rx and Tx ports to ensure that the Tx and Rx ends of the interface are correctly connected,and the other end of the fiber is connected to another device.3.After power-on,check the status of the corresponding indicator.If the indicator is on,the link is up.If not,please check the line and confirm that the peer device is enabled.1718Attention:It is not allowed to excessively bend the fiber,and its radius of curvature should be no less than 10cm;Ensure the cleanliness of the fiber end face;Please do not look directly into the fiber optic connector with your eyes,as this may cause eye damage.2.3Check before power-onCheck that the power supply of the power outlet meets the switch specifications.Check that the power supply,switch,and rack are properly grounded.Check whether the switch is connected to other network devices.2.4Device initializationThe switch will automatically initialize after the power is turnedonand the power switch is turned on.The indicator light will appear as follows:After the power is turned on,the power indicator remains steady, the SYS light enters the blinking state,and the system runs normally.The indicator of each port indicates the connection status of each port,indicating that the switch has started to work normally.Chapter3,Product InstallationBefore installation,confirm the operating environment of the equipment:power supply voltage,installation space,installation method,etc.Please carefully confirm the following installation requirements:-Check for cables and connectors required for19installation♦-Check whether the cable is in place(not more than100m)according to reasonable configuration requirements.♦-The product does not provide mounting components,the user must prepare the components of the selected installation type:screws,nuts and tools to ensure reliable installationPower requirements:12-56V DC(12-48V nonsupportPoE,support date exchange only)Environmental requirements:Working temperature:-40~75°CStorage temperature:-40to75°CRelative humidity:5%to95%(no condensation) Power input20215pin 5.08mmterminalInput range:12-56VDCP1&P2dual redundant power supply,Support reverse connection protectionGround protectionGroundprotectionConnect to groundRail mountingChapter4,Packing list and use recommendations 4.1Product packagingItem Quantity Description Switch1set\Phoenix terminal1*5,1*2eachper one unit Connect to power and alarm switchWarranty card1piece For after-sales maintenance User Manual1copy Used to guide users to installswitches4.2Recommendations1.For safety reasons,non-professionals should not open the product casing;2.Pay attention to the danger of strong electricity and safe protection when the product is powered on;223.Do not use the switch in a humid environment to prevent water from entering the fuselage through the casing,resulting in damage to the machine;4.In the state of power-on of the product,please do not plug and unplug the cable if non special case;5.Please do not place heavy objects on the switch to avoid accidents;6.It is recommended to use the switch indoors.It is recommended to add a waterproof box when using it outdoors. Note:The pictures in the manual are for reference only,whichever is subject to the actual product.23。
BF6912AX规格书 SOP28

BYD Microelectronics Co., Ltd.
Micro800 非隔离型热电偶功能性插件模块 产品目录号 2080-TC2 说明书

接线图Micro800™ 非隔离型热电偶功能性插件模块产品目录号2080-TC2/idc/groups/literature/documents/wd/208 0-wd006_-mu-p.pdfFR Cette publication est disponible en français sous forme électronique (fichier PDF).Pour la télécharger, rendez-vous sur la page Internet indiquée ci-dessus.IT Questa pubblicazione è disponibile in Italiano in formato PDF. Per scaricarla collegarsi al sito Web indicato sopra.DE Diese Publikation ist als PDF auf Deutsch verfügbar. Gehen Sie auf die oben genannte Web-Adresse, um nach der Publikation zu suchen und sie herunterzuladen.ES Esta publicación está disponible en español como PDF. Diríjase a la dirección web indicada arriba para buscar y descarga esta publicación.PT Esta publicação está disponível em portugués como PDF. Vá ao endereço web que aparece acima para encontrar e fazer download da publicação.ZHZC2 Micro800™ 非隔离型热电偶功能性插件模块出版物 2080-WD006A-ZH-P - 2010年9 月环境和机柜防止静电放电本设备适用于在污染等级 2 工业环境、过电压 II 类应用中使用 (如 IEC 60664-1 所定义),在海拔高达 2000 米 (6562 英尺) 时不降额。
CHP Max Headend Optics Platform CHP-OPTSWITCH-2-L

DATA SHEET CHP Max Headend Optics Platform CHP-OPTSWITCH-2-L Dual Optical A/B SwitchThe CHP Max optical switch provides operators with a reliable and rapid response to changing network conditions, enabling them to proactively identify and fix problems before they impact subscribers. Cable operators can expect a reliable and rapid response to changing network conditions with the CHP Max optical switch design that leverages the installed base of CHP Max5000®chassis, preserving deployed capital. Each channel of the Optical Switch Module accepts two optical signals (“A,” the primary path, and “B,” the backup path). The unit’s microcontroller continuously monitors each fiber’s optical signal power level and the adjustable optical trip threshold for each path. Operators can configure the optical switch in Automatic or Manual Switch Mode. When configured for Automatic Switch Mode, the optical switch will automatically switch to the backup fiber path if the primary path falls below the optical switch threshold that is set by the operator.When optical power is restored to the primary path, the switch willautomatically switch back to the primary path. When placed in ManualSwitch Mode, the optical switch will remain on the path selected by theoperator until the operator selects the other path or returns the unit toAutomatic Switch Mode. Operators can select Automatic and ManualSwitch Mode by using the unit’s front ‐panel pushbutton switch,through the SNMP, or via CORView EMS.•High density to reduce footprint with a dualdensity, single slot unit with 2 independentswitches•Improve network services and customer Qualityof Experience (QoE) with redundant rings androute diversity•Very low power with less than 1 Watt typicalconsumption•Automatic and manual switching using frontpanel pushbutton or remotely through theSNMP or CORView ™Element ManagementSystem (EMS) FEATURESNetwork DiagramOPERATIONAL REQUIREMENTSSMMSMM ‐2 only CMMNo CHP Craft SoftwareNo CHP CORView/CORView LiteV3.5 or later Auto Configuration Supported NoSPECIFICATIONSSpecificationPhysicalDimensions 11.25 in W x 3.4 in H x 18.5 in D (3.2 cm x 8.7 cm x 47.0 cm)Weight2.5 lb (1.3 kg)Optical Connector TypeLC/APC EnvironmentalOperating Temperature Range 20°to 50°C (32°to 122°F)Storage Temperature Range‐40°to 70°C (‐40°to 158°F)Humidity85% non ‐condensing (max)OpticalOperating Wavelength Range1260–1610 nm Input Optical Power Range‐20 to +20 dBm Insertion Loss< 2 dB Optical Crosstalk> 50 dB Optical Return Loss> 45 dB SwitchingSwitching Time< 20 ms Switch TypeLatching, Opto ‐Mechanical Optical Switching Threshold Ranges‐20 to +18 dBm Restore Time0 to 10 minutes in 1 second increments Power RequirementsPower Consumption1 W (Typical), <2 W (max)NOTES:1.Includes handles and connectors.2.Temperature measured at optical switch’s module’s air inlet.ORDERING INFORMATIONCHP‐OPTSWITCH‐2‐L CHP Dual Dense Optical Switch LC/APCRELATED PRODUCTSCHP Chassis Optical Patch CordsPower Supplies Optical PassivesControl Module Installation ServicesContact Customer Care for product information and sales:•United States: 866‐36‐ARRIS•International: +1‐678‐473‐5656Note: Specifications are subject to change without notice.Copyright Statement:©2022CommScope,Inc.All rights reserved.ARRIS,the ARRIS logo,CHP Max5000,and CORView are trademarks of CommScope,Inc.and/or its affiliates.All other trademarks are the property of their respective owners.No part of this content may be reproduced in any form or by any means or used to make any derivative work(such as translation,transformation,or adaptation)without written permission from CommScope, Inc and/or its affiliates(“CommScope”).CommScope reserves the right to revise or change this content from time to time without obligation on the part of CommScope to provide notification of such revision or change.1514620 _CHP Optical Switch_DS_RevA。
Nuvoton IoT 平台设备和解决方案说明书

NuMicro®IoT Platform 2023-02-20Please Contact************************URL: https:///iot_startupCompanion App Monitor/ControlClouds /ServersCloud Ready Nuvoton Provides One-Stop IoT SolutionDevice Platform Edge DevicesRouter /GatewayGateway Platform ConnectivityDriver Ready Platform RTOS Platform OS/RTOS Supported NetworkSupported Clouds Android & iOS AppNB-IoTEthernetAzure RTOSNuvoton IoT PlatformIoT Device IoT Gateway OOB Platform AI +CloudNuvoton PlatformNuMaker-IoT-M487NuMaker-IoT-M263ANuMaker-IoT-M2354NuStamp-ACK-M031LENuMaker-LoRaD-M252NuMaker-M031BTYENuMaker-M032BTAINuMaker-IoT-MA35D1-A1NuMaker-IIoT-NUC980NuMaker-RTU-NUC980NuMaker-IoT-M487NuMaker-IIoT-NUC980NuMaker-RTU-NUC980NuMaker-IoT-M487Arm PelionAmazon Web ServiceMicrosoft AzureAlibaba CloudAllxonConnectivity* Supports Ethernet /Wi-Fi / Bluetooth / 4G & LTE / NB-IoT / LoRa * Supports MQTT /CoAP/ HTTP / TLS /AWS / Web Server Storage AI + CloudIoT Gateway OOB Platform IoT DeviceNuvoton IoT PlatformIoT Platform ApplicationPlatformNuMaker Board DetailsIoT device platformIoT General PlatformNuMaker-IoT-M487For sensor fusion and machine learning device applications. SupportsArm CMSIS-NN for neural network function.NuMaker-IoT-M263A Supports a mini PCIe connector for external modules to realize3G/4G/NB-IoT connectivity functionsIoT Security TF-M Platform NuMaker-IoT-M2354The latest IoT secure platform based on Arm® Cortex®-M23 TrustZone®technology with secure keys management, and storage protected byphysical tampering shield.Amazon ACK Platform NuStamp-ACK-M031LE Amazon approved Alexa Connect Kit (ACK) platform. Easy to implementsmart home appliances with Alexa Echo speaker ecosystem.LoRa Device Platform NuMaker-LoRaD-M252LoRa device development platform is fully compliant with LoRaWANClass A/C standard and supports 868-915MHz (EU/US) or 433-470MHz(CN) Bands.BLE PlatformNuMaker-M031BTYE Microcontroller with BLE5.0 & 2.4GHz proprietary for IoT sensor node &home appliancesNuMaker-M032BTAI Microcontroller with BLE5.0 & 2.4GHz proprietary, USB and Arduinosupport for smart devicesIoT gateway platformIoT Gateway PlatformNuMaker-IoT-MA35D1-A1NuMaker-IIoT-NUC980NuMaker-RTU-NUC980IoT Gateway Platform by LinuxBasic IoT Gateway Platform NuMaker-IoT-M487Supports multiple cloud services, such as Arm Pelion, Amazon WebService, Alibaba Cloud and Microsoft Azure IoT.OOB Platform forserverOOB Platform NuMaker-IIoT-NUC980NuMaker-RTU-NUC980with Allxon Cloud serviceBasic OOB Platform NuMaker-IoT-M487Affordable OOB platform supports complete SSL and TLS library forsecure linkCustomer Attribute CapabilitiesNon-OS RTOS LinuxCore & OS 8051/ M0/ M23/ M4 MCUNo OS, use BSP onlyM4 / M23MCURTOS with lite network stack (lwIP)ARM9/ A35MPULinux with full network stack orRTOS with lite network stackNetwork No or simple non-IP networkLower data rateEthernet(exclude M2354),Wi-Fi (UART), 4G LTE (UART), NB-IoT(UART)Lower data rateEthernet,Wi-Fi (USB/SDIO),4G LTE(USB/UART), NB-IoT(USB/UART), …Higher data rateGUI No or segmented LCD with emWin or LVGL with QT,emWin, or LVGL R&D 1 or 2 3 to5> 10Applications Simple Smart Devices Home Appliances,Smart Devices…Industrial, Smart Grid,Smart Building,Smart City, …Nuvoton PlatformsNuMaker-IoT-M487NuMaker-IoT-M263ANuMaker-IoT-M2354NuStamp-ACK-M031LENuMaker-LoRaD-M252NuMaker-M031BTYENuMaker-M032BTAINuMaker-IIoT-NUC980NuMaker-RTU-NUC980NuMaker-IoT-M487NuMaker-IoT-M2354NuMaker-IoT-MA35D1-A1NuMaker-IIoT-NUC980NuMaker-RTU-NUC980NuMaker-HMI-N9H304G LTE / NB-IoT/EthernetLinux OSCustomers Device ControlNon-OSCustomers4G LTE / NB-IoT/EthernetRTOSCustomersNuvoton IoT Platform –All-in-OneNuvoton MCURF Vendor OS Vendor Cloud VendorOS & Libraries(Mbed OS / Amazon FreeRTOS / AliOS Things /Azure RTOS / RT-Thread / Linux)RF Driver (as below)RF Module(Wi-Fi / LTE / NB-IoT / LoRa / BT)Network Stacks(TCP / UDP)Application CodeCloud Client(AWS / Alibaba / Azure /Pelion / Allxon)HardwareSoftwareI/O Drivers Network Protocols(MQTT / CoAP / HTTPS)Nuvoton MCU(M0 / M23 / M4 / ARM9)•Integrate MCU/OS/Network Protocols/RF Driver/Application Demos •Multiple HW Platform•Integrate RF Driver•MQTT/CoAP Example•Cloud Certification •Customer can focus on application development.Nuvoton IoT Platform with TF-MNuvoton MCU RF Vendor RTOS Vendor Cloud VendorMbed OS 6MbedTLS & LibrariesRF Driver (as below)RF Module(Wi-Fi / LTE / NB-IoT / LoRa)Network Stacks(TCP / UDP)Application CodeCloud ClientHardwareSoftwareI/O DriversNetwork Protocols(MQTT / CoAP / HTTPS)Nuvoton MCU(M235x series with TBSA-M hardware)P S A D e v A P I sTF-M CoreSecure Boot P S A A P I sP r o t e c t e d S t o r a g e (P S )A R o T S e r v i c e sP S A A P I sI n t e r n a l T r u s t e d S t o r a g eC r y p t oI n i t i a l A t t e s t a t i o nP l a t f o r mHALApplication Root of Trust PSA Root of TrustTrusted Firmware-MIsolation BoundaryNon-Secure AreaSecure AreaSolution for your IIoT PlatformRTOS & MCU H/W Driver& RF DriverNetwork StacksSecure ProtocolsCloud Connection SDKApplication SpecifiedStart from ZeroUsing Nuvoton PlatformWith Experience RTOS / CLOUD Time ++(Month)Development Schedule123456Using Nuvoton PlatformWithout experienceConnectivity Ecosystems SupportNuMaker Board OS / RTOSIP Connectivity *3Non-IP Connectivity *3CloudsEthernetWi-FiNB-IoT Cat-M1LTELoRa (Device)BLE 52.4GArm Pelion Amazon AWS Alibaba Cloud Microsoft Azure Allxon *5青蓮雲TinyTEENuMaker-IoT-MA35D1-A1Linux ●●●●●●●RT-Thread ●●●NuMaker-IIoT-NUC980Linux ●●●●●●●FreeRTOS ●RT-Thread ●●●NuMaker-RTU-NUC980(Chili)Linux ●●●●●●●●FreeRTOS ●RT-Thread ●●●NuMaker-IoT-M487Mbed OS ●●●●●*6●●●●Amazon FreeRTOS ●●●●AliOS Things ●●●RT-Thread ●●●●Azure RTOS ●●NuMaker-IoT-M467Mbed OS ●●●●●*6●●RT-Thread ●●●●NuMaker-IoT-M2354Mbed OS *1●●●●●●●●●RT-Thread ●●●●FreeRTOS ●●NuMaker-IoT-M263A Mbed OS●●●●●●●●NuMaker-LoRaD-M252Mbed OS /Non-OS *2●NuMaker-M031BTYE Non-OS ●NuMaker-M032BTAI Non-OS ●NuStamp-ACK-M031LENon-OS●●*4*1 Support on Mbed Studio *4 Alexa Connect Kit (ACK)*2 Non-OS ver. is NuLoRaNode.*5 Software as a Service (SaaS) *3 Refer supported components for detail.*6 Require an external LoRa moduleIoT Device Platform•Arm® Cortex®-M23 core •Runs at 64 MHz•512 KB Flash Memory •96 KB SRAM •IoT NodeNuMaker-IoT-M263AP l a t f o r m s•Arm® Cortex®-M23 core •Runs at 96 MHz•1024 KB Flash Memory •256 KB SRAM•IoT Node •TrustZone •PSA CertifiedNuMaker-IoT-M2354IoT General PlatformIoT Security TF-M Platform•Arm® Cortex®-M4 core •Runs at 192 MHz •512 KB Flash Memory •160 KB SRAM •Ethernet Gateway •Machine Learning -License plate recognition,Keyword spotting, …NuMaker-IoT-M487•Arm® Cortex®-M4 core •Runs at 200 MHz•1024 KB Flash Memory •512 KB SRAM •GatewayCharging, Energy monitor Communication, ...•Machine LearningNuMaker-IoT-M467IoT Device Platform•Arm® Cortex®-M0 core •Runs at 48 MHz•128 KB Flash Memory •16 KB SRAM •IoT Node •BQB Certified NuMaker-M031BTYEP l a t f o r m s•Arm® Cortex®-M0 core •Runs at 72 MHz•512 KB Flash Memory •96 KB SRAM•IoT Node •BQB CertifiedNuMaker-M032BTAIAmazon ACK Platform•Arm® Cortex®-M0 core •Runs at 48 MHz•128 KB Flash Memory •16 KB SRAM •Alexa Sensor Node with Amazon Alexa Connect Kit (ACK)NuStamp-ACK-M031LE•Arm® Cortex®-M23 core •Runs at 48 MHz•256 KB Flash Memory •32 KB SRAM •LoRa Node •Helium Node NuMaker-LoRaD-M252LoRa Device Platform BLE PlatformAlexa Connect Kit (ACK) –Interactive with AlexaIoT Gateway PlatformP l a t f o r m s•Dual Arm® Cortex-A35•Runs at 800 MHz•128MB DDR (up to 512MB)• 1 Gb NAND Flash •Ethernet Gateway •Wireless Gateway •Edge Computing NuMaker-IoT-MA35D1-A1•Arm® ARM926 core •Runs at 300 MHz•64 MB DDR2 in LQFP64 •256 Mb SPI NOR Flash•CAN 2.0B/RS485 to ETH •Ethernet Gateway •Gateway in small size •Remote terminal unit“Chili Board ” NuMaker-RTU-NUC980•Arm® ARM926 core •Runs at 300 MHz•64 MB DDR (up to 128MB)• 1 Gb SPI-NAND Flash •Ethernet Gateway •Wireless Gateway •Edge ComputingNuMaker-IIoT-NUC980•Arm® Cortex®-M4 core •Runs at 192 MHz •512 KB Flash Memory •160 KB SRAM•Crypto accelerators •Ethernet Gateway •Machine Learning ComputingNuMaker-IoT-M487OOB Platform for Server•Arm® ARM926 core •Runs at 300 MHz•64 MB DDR (up to 128MB)• 1 Gb SPI-NAND Flash •Support Allxon •Ethernet•Support Linux 4.4•Support RT-Thread OOBNuMaker-IIoT-NUC980•Arm® Cortex®-M4 core •Runs at 192 MHz •512 KB Flash Memory •160 KB SRAM•Crypto accelerators •Support RT-Thread OOBNuMaker-IoT-M487•Arm® ARM926 core •Runs at 300 MHz•64 MB DDR2 in LQFP64 •256 Mb SPI NOR Flash•Support Allxon•CAN Bus/RS485 to ETH •Ethernet•Support Linux 4.4•Support RT-Thread OOBNuMaker-RTU-NUC980“Chili Board”P l a t f o r m sIoT gateway is a bridge to pass raw data through the network to reach a central server for further processing.NUC980(NuMaker-IIoT-NUC980)Ethernet(UART/SPI/I 2C …)(4G LTE/WiFi …)Industrial IoT GatewayApplication Key Requirements•Bridging traditional industrial networks to Internet by secure communication through multiple network connectivity •Remote configuration and web style managementNuMaker-IIoT-NUC980 Platform Features•Hardware。
Agilent L Series 多端口电romechanical 复用开关(L7104A B C和

L7106BAgilent L Series Multiport Electromechanical Coaxial SwitchesL7104A/B/C and L7106A/B/C TerminatedL7204A/B/C and L7206A/B/C Unterminated DC to 4 GHz, DC to 20 GHz, DC to 26.5 GHz TechnicalOverviewHigh-performance multiport switchesat an affordable priceGuaranteed 0.03 dB repeatability ensures accuracy and reduces calibration cycles for the entire 2 million cycle operating life.Operating life of 5 million cycles typical Unmatched isolation maximizes measurement accuracy and improves system dynamic range Economical price minimizes budgetary constraints••••In today’s competitive world, automated test systems demand higher accuracyand performance than ever before. The Agilent Technologies L Series L7104A/B/C and L7106A/B/C terminated and L7204A/B/C and L7206A/B/C untermi-nated, multiport switches offer the improvements in insertion loss repeatability and isolation necessary to achieve higher test system performance. Long life, repeatability, and reliability lower the cost of ownership by reducing calibration cycles and increasing test system uptime and are vital to ATS measurement system integrity over time.Description The L7104/L7204A,B,C SP4T and L7106/L7206A,B,C SP6T multiport switches provide the life and reliability required for automated test and measurement, signal monitoring, and routing applications. Innovative design and careful process control creates switches that meet the requirements for highly repeat-able switching elements in test instruments and switching interfaces. The exceptional 0.03 dB insertion loss repeatability is warranted for 2 million cycles at 25° C. This reduces sources of random errors in the measurement path and improves measurement uncertainty. Switch life is a critical consideration in production test systems, satellite and antenna monitoring systems, and test instrumentation. The longevity of these switches increases system uptime, and lowers the cost of ownership by reducing calibration cycles and switch maintenance.High-performance multiport switches for microwave and RF instrumentation and systems SP4T and SP6T confi gurationMagnetic latchingWarranted 0.03 dB insertion loss repeatability for 2 million cycles Excellent isolation, typically > 85 dB at 26.5 GHzOpto-electronic indicators and interruptsTerminated and unterminated portsTTL/5 V CMOS compatible (optional)Figure 1. Agilent L7104A/B/C and L7106A/B/C simplifi ed schematics•••••••Product OverviewFigure 2. Agilent L7204A/B/C and L7206A/B/C unterminated simplifi ed schematicsOperating up to 4 GHz (A models), 20 GHz (B models), and 26.5 GHz (C models), these switches exhibit the exceptional isolation performance required to maintain measurement integrity. Isolation between ports is typically > 90 dB to 12 GHz and > 85 dB to 26.5 GHz. This reduces the infl uence of signals from other channels, sustains the integrity of the measured signal, and reduces system measurement uncertainties. These switches also minimize measurement uncertainty with low insertion loss and refl ection, which make them ideal elements in large multitiered switching systems.All the L7104/L7204A,B,C and L7106/L7206A,B,C are designed to fall within most popular industry footprints. The 2¼ inch square fl ange provides mounting holes, while the rest of the 2½ inch long by 2¼ inch diameter body will easily fi t into most systems. Ribbon cable or optional solder terminal connections accommodate the need for secure and effi cient control cable attachmentOption 100 provides solder terminal connections in place of the 16-pin ribbon drive cable. Option 100 does not incorporate the “open all paths” feature.Opto-electronic interrupts and indicators improve reliability and extend thelife of the switch by eliminating DC circuit contact failures characteristic of conventional electromechanical switches. These switches have an interrupt circuit that provides logic to open all but the selected ports, it then closesthe selected ports cutting off the current to the solenoids of the ports. These switches also offer independent indicators that are controlled by optical inter-rupts in the switch. The indicators provide a closed path between the indicator common pin and the corresponding sense pin of the selected path.ApplicationsMultiport switches fi nd use in a large number of applications, increasing systemfl exibility and simplifying system design.Signal routingThe simplest signal routing scheme takes the form of single input to multipleoutputs. These matrixes are often used on the front of an analyzer to test sev-eral two-port devices sequentially or to test multiport devices. In surveillanceapplications, a multiport switch can be used to select the optimum antennafor intercepting a signal. Two methods can be used to accomplish the singleinput to multiple output arrangement. Traditionally where isolation greater than60 dB was required, a tree matrix composed of SPDT switches was used. Whilethis gave great isolation, it was at the cost of more switches (Figure 3). Theseswitches have port-to-port isolations typically greater than 85 dB at 26.5 GHz,eliminating the need to use a tree matrix in order to achieve high isolation(Figure 4). In addition to the reduced part count, the path lengths are shorter, soinsertion loss is less, and paths are of equal length, so phase shift is constant.Full access switchingFull access switching systems give the fl exibility to route multiple input signalsto multiple outputs simultaneously. Full access switching matrixes are used ingeneric test systems in order to provide fl exible routing of signals to and frommany different devices under test, and stimulus and analysis instrumentation.Cross-point matrixes, using single pole double throw and cross-point switches,have traditionally been used in order to maintain high channel-to-channelisolation (Figure 5). As with the tree matrixes, this is at the cost of hardwareand performance. Full access switching can also be achieved using multiportswitches (Figure 6).The advantage of the multiport matrix over the cross-point matrix is lowerinsertion loss and improved SWR performance due to consistent path lengthand fewer switches and connecting cables.Figure 3. Tree matrixFigure 5. Cross-point matrixDedicated switching There are a number of applications where switching is used, not for fl exibility, but to accomplish a particular function within an instrument. For example,switched fi lter banks for reducing harmonics in the output of sources or to the input of analyzers can use multiport switches in series to select the right fi lter for the band of interest. For larger switching systems, where many switches are used to provide complex signal routing, a switch driver such as the Agilent 11713B/C with L7104/6 or L7204/6 switches is recommended.Driving the switch Each RF path can be closed by applying ground (TTL “High” for Option T24) to the corresponding “drive” pin. In general, all other RF paths are simultaneously opened by internal logic.Standard drive See Figure 11 for drive connection diagrams.Connect pin 1 to supply (+20 VDC to +32 VDC)Connect pin 15 to ground (see Note 1).Select (close) desired RF path by applying ground to the corresponding “drive” pin; for example ground pin 3 to close RF path 1 (see Note 2).To select another RF path, ensure that all unwanted RF path “drive” pins are disconnected from ground (to prevent multiple RF path engagement). Ground the “drive” pin which corresponds to the desired RF path (see Note 3). To open all RF paths, ensure that all RF path “drive” pins are disconnected from ground. Then, connect pin 16 to ground. This feature is not available with Option 100.•••••TTL drive (Option T24) See Figure 15 and 16 for drive connection diagrams.Connect pin 1 to supply (+20 VDC to +32 VDC)Connect pin 15 to ground (see Notes 1, 4).Select (close) desired RF path by applying TTL “High” to the corresponding “drive” pin; for example apply TTL “High” to pin 3 to close RF path 1 (see Note 2).To select another path, ensure that all unwanted RF path “drive” pins are at TTL “Low” (to prevent multiple RF path engagement). Apply TTL “High” to the “drive” pin which corresponds to the desired RF path (see Note 3).To open all RF paths, ensure that all RF path “drive” pins are at TTL “Low.” Then, apply TTL “High” to pin 16. This feature is not available with Option 100.Notes:Pin 15 must always be connected to ground to enable the electronic position-indicating circuitry and drive logic circuitry.CAUTION: IF PIN 15 IS NOT CONNECTED TO POWER SUPPLY GROUND, CATASTROPHIC FAILURE WILL OCCUR.After the RF path is switched and latched, the drive current is interrupted by the electronic position-sensing circuitry. Pulsed control is not necessary, but if implemented, the pulse width must be 15 ms minimum to ensure that the switch is fully latched.The default operation of the switch is break-before-make. Make-before-break switching can be accomplished by simultaneously selecting the old RF path “drive” pin and the new RF path “drive” pin. This will simultaneously close the old RF path and the new RF path. Once the new RF path is closed (15 ms), de-select the old RF path “drive” pin while leaving the new RF path “drive” pin selected. The switch circuitry will automatically open the old RF path while leaving the new RF path engaged.In addition to the quiescent current supplying the electronic position-sensing circuitry, the drive current fl ows out of pin 15 (during switching) on TTL drive switches (Option T24).Electronic position indicatorsThe electronic position indicators consist of optically isolated, solid-state relays which are driven by photo-electric sensors coupled to the mechanical position of the RF path’s moving elements (Figure 7). The circuitry consists of a common which can be connected to an output corresponding to each RF path. If multiple RF paths are engaged, the position indicator corresponding to each closed RF path will be connected to common. The solid state relays are confi gured for AC and/or DC operation. (See indicator specifi cations on page8.) The electronic position indicators require that the supply (20 to 32 VDC) be connected to pin 1 and ground connected to pin 15.•••••1.2.3.4.Figure 7. Pin function diagramSpecifi cations describe the instrument’s warranted performance. Supplementaland typical characteristics are intended to provide information useful in applying the instrument by giving typical, but not warranted performance parameters. Maximum power rating:1 W average into 50 Ωinternal loads Switching:1 W CW for terminated2 W CW for unterminatedNon-switching: 50 W Pk (not to exceed 1 watt average)for terminated100 W Pk (not to exceed 2 watt average)for unterminated Life:2,000,000 cycles minimum Switching speed:15 ms maximum Reference conditions:Cold switching only (NO Hot switching)Ambient temperature of 75°C or lessSea level (0.88 derating at 15,000ft.)Load VSWR < 1.2 (see graph for derating above 1.2 VSWR)Power handling at 25°C is 100 W at 4 GHzFigure 8. Power rating for cold switching at 75 °C•••••Specifi cationsFigure 9. Power derating factor versus VSWR Indicator specifi cations:Maximum withstand voltage: 60 V Maximum current capacity: 150 mA Maximum “ON” resistance: 2.5 ΩMaximum “OFF” resistance:10 G Ω Figure 10. TTL control voltage states (Option T24)Switch drive specifi cations1. Closing one RF path requires 200 mA. Add 200 mA for each additional RF path closed or open. Using all RF paths open (selecting pin 16) requires 200 mA per RF path reset with Vcc=24 VDC.Figure 11. Agilent L Series multiport switch insertion loss versus frequencyFigure 12. Agilent L Series multiport switch isolation versus frequencyFigure 13. Agilent L Series multiport switch SWR versus frequencyEnvironmental specifi cationsOperating temperature:–25 to 75°CStorage temperature:–55 to 85°CTemperature cycling:–55 to 85°C, 10 cycles per MIL-STD-202F,Method 107D, Condition A (modified) Vibration:Operating: 7 g: 5 to 2000 Hz at 0.25 in p-pSurvival: 20 g: 20 to 2000 Hz at 0.06 in p-p,4 min/cycle, 4 cycles/axisRandom: 2.41 g (rms) 10 min/axis Shock:Half-sine: 500 g at 0.5 ms,3 drops/direction, 18 totalOperating:50 g at 6 ms, 6 directionsMoisture resistance:65°C, 95% RH, 10 days per MIL-STD-202F,Method 106EAltitude storage:50,000 feet (15,240 meters perMIL-STD-202F, Method 105C, Condition B) RFI:Radiated Emission per CISPR 11 Magnetic fi eld:< 5 gauss ¼ inch from surfaceFigure 14. Product dimensions for L7104/106 A,B,C and L7204/206 A,B,CFigure 15. Drive connection diagrams with Option 161* Path 1 and 4 not connected for the L7104/L7204 A, B, C** “Open all the paths” pin is not available Figure 16. Drive connection diagrams with Option 100TroubleshootingSymptom Probable cause 1. Will not switch • Not connected to supply• Supply < 20 V • Supply current too low • Not connected to ground • Select line not at ground (std)• TTL “Low” voltage too high (Option 72) • All-path-open line selected 2. Position indicators • Supply not connected do not work • Supply < 20 VDC• Pin 15 not connected to groundOrdering informationSwitchesL7104A DC to 4 GHz, SP4T TerminatedL7104B DC to 20 GHz, SP4T TerminatedL7104C DC to 26.5 GHz, SP4T TerminatedL7204A DC to 4 GHz, SP4T UnterminatedL7204B DC to 20 GHz, SP4T UnterminatedL7204C DC to 26.5 GHz, SP4T UnterminatedL7106A DC to 4 GHz, SP6T TerminatedL7106B DC to 20 GHz, SP6T TerminatedL7106C DC to 26.5 GHz, SP6T TerminatedL7206A DC to 4 GHz, SP6T UnterminatedL7206B DC to 20 GHz, SP6T UnterminatedL7206C DC to 26.5 GHz, SP6T UnterminatedOption 100Solder terminals to replace ribbon cableOption 16116 PIN DIP socket and connector with 24 inchribbon cableOption UK6Commercial calibration test data with certifi cateOption T24TTL/5 V CMOS compatible optionDrivers11713B/C Attenuator switch driverDrive up to 20 sections of switches or attenuators.CablesOption 201 Accessory cableViking connector to bare tinned wires (60 inches long). Use to connect11713B/C to L7104/204/106/206 with Option 100. One required withL7104/L7204 Option 100; two required with L7106/L7206 Option 100.Option 401 Accessory cableDual-viking connector to 16-pin DIP connector.Use to connect 11713B/C to L7106/206 default Option 161.Option 601 Accessory cableViking connector to 16-pin DIP connector.Use to connect 11713B/C to L7104/L7204 default Option 161.Confi guration guideSee publication 5989-7277EN./fi nd/emailupdatesGet the latest information on the products and applications you select.Agilent Email UpdatesRemove all doubtOur repair and calibration serviceswill get your equipment back to you, performing like new, when prom-ised. You will get full value out of your Agilent equipment through-out its lifetime. Your equipment will be serviced by Agilent-trained technicians using the latest factory calibration procedures, automated repair diagnostics and genuine parts. You will always have the utmost confi dence in your measurements. Agilent offers a wide range of ad-ditional expert test and measure-ment services for your equipment, including initial start-up assistance onsite education and training, as well as design, system integration, and project management.For more information on repair and calibration services, go to:/fi nd/removealldoubtFor more information on Agilent T echnologies’ products, applications or services, please contact your local Agilent office. The complete list is available at:/fi nd/contactusAmericasCanada (877) 894-4414 Latin America 305 269 7500United States (800) 829-4444Asia Pacifi c Australia 1 800 629 485China 800 810 0189Hong Kong 800 938 693India 1 800 112 929Japan 0120 (421) 345Korea 080 769 0800Malaysia 1 800 888 848Singapore 180****8100Taiwan 0800 047 866Thailand 1 800 226 008Europe & Middle EastAustria 01 36027 71571Belgium 32 (0) 2 404 93 40 Denmark 45 70 13 15 15Finland 358 (0) 10 855 2100F rance 0825 010 700**0.125 €/minute Germany 07031 464 6333****0.14 €/minuteIreland 1890 924 204Israel 972-3-9288-504/544Italy 39 02 92 60 8484Netherlands 31 (0) 20 547 2111Spain 34 (91) 631 3300Sweden 0200-88 22 55Switzerland 0800 80 53 53United Kingdom 44 (0) 118 9276201Other European Countries: /fi nd/contactusRevised: July 17, 2008Product specifi cations and descriptions in this document subject to change without notice.© Agilent Technologies, Inc. 2008Printed in USA, October 31, 20085989-6030ENL7106B。
- 1、下载文档前请自行甄别文档内容的完整性,平台不提供额外的编辑、内容补充、找答案等附加服务。
- 2、"仅部分预览"的文档,不可在线预览部分如存在完整性等问题,可反馈申请退款(可完整预览的文档不适用该条件!)。
- 3、如文档侵犯您的权益,请联系客服反馈,我们会尽快为您处理(人工客服工作时间:9:00-18:30)。
Inheritance?
• Now create a Wizard…
Don’t Act Now!
You don’t have to Copy & Paste!
Buy Inheritance!
• Wizard is a subclass of Dude
public class Wizard exteeption object – Includes some useful information – “throws” the Exception
• You can create and throw Exceptions too!
public class Exception
• Bouncer draws a Sprite that
– Moves around – Bounces in a box
• A Sprite is an interface
– You can draw anything
• Mover
– Keeps updating the coordinates of a Sprite
...
mp -= 10;
}
}
Inheriting from inherited classes
• What about a Grand Wizard?
public class GrandWizard extends Wizard { public void sayName() { System.out.println(“Grand wizard” + name) } } = “Flash”
sprite.draw(graphics, x, y);
x += xDirection;
y += yDirection;
} }
Inheritance
Exceptions
I/O
Inheritance
Very Very Basic Inheritance
• Making a Game
public class Dude public String public int hp public int mp {
– null.someMethod(); – (new int[1])[1] = 0; – int i = “string”;
Why use an Exception?
• To tell the code using your method that something went wrong
Exception in thread "main" ng.ArrayIndexOutOfBoundsException: 5 at RuntimeException.main(RuntimeException.java:8)
}
A Mover that doesn’t bounce
public class StraightMover { private int x, y, xDirection, yDirection; private Sprite sprite; public StraightMover(int startX, int startY, Sprite sprite) { x = startX; y = startY; this.sprite = sprite; } public void setMovementVector(int xIncrement, int yIncrement) { xDirection = xIncrement; yDirection = yIncrement; } public void draw(Graphics graphics) {
public interface ICar {
boolean isCar = true;
int getNumWheels();
}
BigRig
class BigRig implements ICar { int getNumWheels() { return 18; } }
That Homework!
• A has all the fields and methods that B has
• A can add it’s own fields and methods • A can only have 1 parent • A can replace a parent’s method by reimplementing it • If A doesn’t implement something Java searches ancestors
What’s going on?
Parent of
Wizard, Elf..
Dude
Subclass
of Dude
Wizard
Thief
Elf
Subclass of
Wizard
Grand Wizard
You can only inherit from one class
Dude
Thief
Exceptions
Exceptions
• NullPointerException • ArrayIndexOutOfBoundsException
• ClassCastException • RuntimeException
What is an “Exception”?
• Event that occurs when something “unexpected” happens
How does Java do that? pt2
• What Java does when it sees
((Dude)grandWizard1).sayName() 1. Cast to Dude tells Java to start looking in Dude 2. Look for sayName()in Dude class 3. Found it! Call sayName()
grandWizard1.sayName();
((Dude)grandWizard1).sayName();
How does Java do that?
• What Java does when it sees
1. 2. 3. 4. 5. 6. 7. grandWizard1.punchFace(dude1) Look for punchFace()in the GrandWizard class It’s not there! Does GrandWizard have a parent? Look for punchFace()in Wizard class It’s not there! Does Wizard have a parent? Look for punchFace()in Dude class Found it! Call punchFace() Deduct hp from dude1
dude1.punchface(wizard1);
*except for private fields and methods
Buy Inheritance!
• Now augment a Wizard
public class Wizard extends Dude { ArrayList<Spell> spells; public class cast(String spell) { // cool stuff here
An Oval Sprite
public class Oval implements Sprite { private int width, height; private Color color;
public Oval(int width, int height, Color color) { // set the fields ... } public void draw(Graphics surface, int x, int y) { surface.setColor(color); surface.fillOval(x, y, width, height); surface.drawOval(x, y, width, height); } ...
Accessed index 5, which isn’t in the array
The method that called it was main
• Debugging and understanding control flow
How do exceptions “happen”?
• Java doesn’t know what to do, so it
public class Wizard { // ugh, gotta copy and paste // Dude’s stuff }
Inheritance?
• Now create a Wizard…
But Wait!
A Wizard does and has everything a
Dude does and has!
Elf
Bad Elf
You can only inherit from one class
Dude
Thief
Elf
Bad Elf
You can only inherit from one class
Dude
What if Thief and Elf both implement
public void sneakUp()
If they implemented differently, which sneakUp()does BadElf call?