材料力学性能第五章
材料力学性能第五章_金属的疲劳
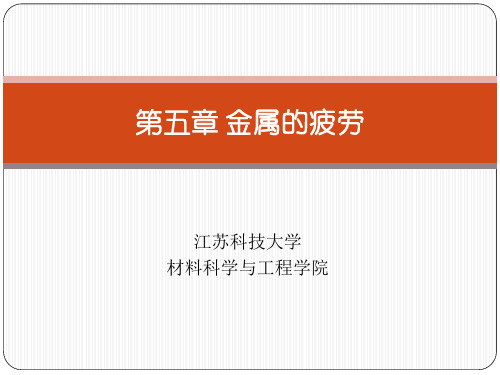
飞机舷窗
高速列车
5.1.3 疲劳宏观断口特征
疲劳断口保留了整个断裂过程的所有痕迹,记载着很多 断裂信息,具有明显的形貌特征,而这些特征又受材料 性质、应力状态、应力大小及环境因素的影响,因此对 疲劳断口的分析是研究疲劳过程、分析疲劳失效原因的 一种重要方法。 疲劳断裂经历了裂纹萌生和扩展过程。由于应力水平较 低,因此具有较明显的裂纹萌生和稳态扩展阶段,相应
疲劳破坏属低应力循环延时断裂,对于疲劳寿命 的预测就显得十分重要和必要。
对缺口、裂纹及组织等缺陷十分敏感,即对缺陷 具有高度的选择性。因为缺口或裂纹会引起应力 集中,加大对材料的损伤作用;组织缺陷(夹杂、 疏松、白点、脱碳等),将降低材料的局部强度, 二者综合更加速疲劳破坏的起始与发展。
18
应力σmax/10MPa
40
20
灰铸铁
0 103 104
105
106
107
循环周次/次
108
109
41
图 几种材料的疲劳曲线
疲劳极限
有水平段(碳钢、合金结构钢、球铁等) 经过无限次应力循环也不发生疲劳断裂,将对应
的应力称为疲劳极限,记为σ-1(对称循环)
无水平段(铝合金、不锈钢、高强度钢等) 只是随应力降低,循环周次不断增大。此时,根 据材料的使用要求规定某一循环周次下不发生断 裂的应力作为条件疲劳极限。 例:高强度钢、铝合金和不锈钢:N=108周次 钛合金:N=107周次
大小:瞬断区大小与机件承受名义应力及材料性质 有关,高名义应力或低韧性材科,瞬断区大;反之。 瞬断区则小。
材料力学性能 第五章 缺口试样的力学性能.
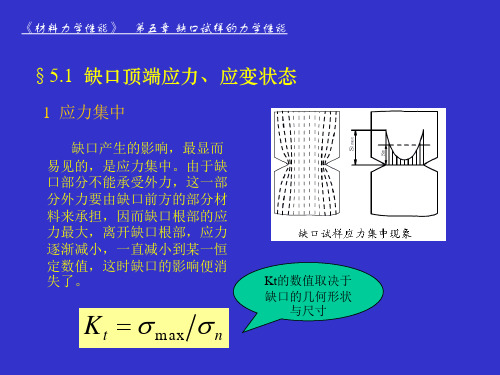
设想有一单位厚度的无限宽形板,对其施 加一拉应力后,与外界隔绝能源。在板内 制造一穿透裂纹,裂纹的扩张来自与系统 内部的弹性能释放。当裂纹扩张时,其表 面能增加了。
u uE us
系弹 统性 总应 能变
表 面 能
能
《材料力学性能》 第六章 断裂韧性基础
冷脆:材料因温度的降低 导致冲击韧性的急剧下降 并引起脆性破坏的现象
《材料力学性能》 第五章 缺口试样的力学性能
5.4.1 系列温度冲击试验
试验表明:随着温度降 低,冲击功由高阶能转 变为低阶能,材料由韧 性断裂过渡到脆性断裂, 断口形式也由纤维状断 口经过混合断口过渡为 结晶状断口,断裂性质 由微孔聚集型断裂过渡 为解理断裂。
定义: G u ( 2a2 ) 2a (2a) (2a) E E
G是弹性应变能的释放率或者裂纹扩展力。
《材料力学性能》 第六章 断裂韧性基础
恒位移条件: 裂纹扩展释 放出的弹性 能是三角形 OAC的面积。
恒载荷条件: 外力做的功一 半用于弹性能 的增加,一半 用于裂纹扩展 裂纹扩展释所 需的弹性能是 三角形OAC的 面积。
以 a 代替 2E a
1
1
2
2
1,
E
2
a
Griffith 公式
《材料力学性能》 第六章 断裂韧性基础
6.1.3 奥罗万(Orowan)的修正
Griffith研究的对象主要是玻璃这类很脆的材料,对于大多数金属材料, 虽然裂纹尖端由于应力集中作用,局部应力很高,但是一旦超过材料的屈 服强度,就会发生塑性变形。在裂纹尖端有一塑性区,材料的塑性越好强 度越低,产生的塑性区尺寸就越大。裂纹扩展必须首先通过塑性区,裂纹 扩展功主要耗费在塑性变形上,金属材料和陶瓷的断裂过程不同,主要区 别也在这里。由此,奥罗万修正了格里菲斯的断裂公式,得出:
第五章-塑料力学性能测试

成型、压延成型或吹膜成型等; 不同方法制样的试验结果不具备可比性; 同一种制样方法,要求工艺参数和工艺过程也要相同; 试样制备好后,要按GB/T 2918-1998标准,在恒温
恒湿条件下放置处理。
(2)材料试验机
影响因素主要有:测力传感器精度、速度控制精度、 夹具、同轴度和数据采集频率等。
第五章 力学性能测试
第一节 拉伸性能
一、概念及测试原理
1.基本概念
应变:当材料受外力作用,而所处的条件使它不能产生惯 性移动时,它的几何形状和尺寸将发生变化,这种变化就 称为应变。
应力:在任何给定时刻,在试样标距长度内,每单位原始 横截面积上所受的拉伸负荷。
拉伸强度:是在拉伸试验过程中,试样承受的最大拉伸应 力。
L0 100
L0
L
100
L
X
(3)标准偏差值按下式(5-4)计算
S
(Xi X)2
n 1
式中:S,标准偏差值;X
,单个测定值;X
i
,组
测定值的算术平均值;n,测定个数。
计算结果以算术平均值表示,σt取三位有效数字,
εt、S取二位有效数字。
3.影响因素
(1)试样的制备与处理 拉伸试验要求做成哑铃形试样; 制样方式有两种:一是用原材料制样;另一种是从制
精密度更高的平均值,试样数量可多于5个。
推荐试验速度
速度
允许偏差 速度
允许偏差
(mm/min) (%) (mm/min) (%)
1
±20
50
±10
2
±20
100 ±10
5
±20
200 ±10
工程力学--第五章 材料的力学性能

材料名称
牌号
许用应力 /MPa 轴向拉伸 轴向压缩 170 230 160-200 7 10.3 10
低碳钢 低合金钢 灰口铸铁 混凝土 混凝土 红松(顺纹)
Q235 16Mn C20 C30
170 230 34-54 0.44 0.6 6.4
Ⅲ. 关于安全因数的考虑
(1) 考虑强度条件中一些量的变异。如极限应力(s,
3. 求三角架的许可荷载
先按每根杆的许可轴力求各自相应的许可荷载:
[ FN1 ] 369 .24 kN [ F1 ] 184 .6 kN 2 2
[ FN2 ] 486.20 kN [ F2 ] 280.7 kN 1.732 1.732
该三角架的许可荷载应是[F1] 和 [F2]中的小者,所以
mm 80 mm7 mm等边角钢组成,杆AB由两根10号工字钢 组成。两种型钢的材料均为Q235钢,[]=170 MPa。试求许 可荷载[F]。
解 : 1. 根据结点 A 的受力图(图b),得平衡方程:
Fx 0
解得
FN2 FN1 cos30 0 FN1 sin 30 F 0
A A1 100% A
A1——断口处最小横截面面积。 延性材料: >5%, 脆性材料:
Q235钢:≈60%
如低碳钢、低合金钢、青铜等
<5%, 如铸铁、硬质合金、石料等。
注意: 1. 低碳钢的s,b都还是以相应的抗力除以试样横截 面的原面积所得,实际上此时试样直径已显著缩小,因而 它们是名义应力。 2. 低碳钢的强度极限b是试样拉伸时最大的名义应力,
哪一个大?
Ⅲ. 其他金属材料在拉伸时的力学性能
由-e曲线可见:
材料 弹性阶段 屈服阶段 强化阶段 局部变形 阶段 锰钢 √ × √ ×
材料力学性能-第五章-金属的疲劳(2)

2021年10月21日 星期四
材料 qf
第五章 金属的疲劳
表5-3 部分材料的qf值
结构钢
粗晶钢 球墨铸铁
0.6~0.8
0.1~0.2 0.11~0.25
灰铸铁 qf<0.05
钢经热处理后强度增加, qf增加。 高周疲劳时,大多数金属对缺口都十分敏
感,在低周疲劳时,对缺口的敏感性较小,主要 是因为低周疲劳时缺口根部已处于塑性区内,产 生了应力松弛,降低了应力集中。
2021年10月21日 星期四
第五章 金属的疲劳
过载持久值
金属材料在高于疲劳极限的
应力下运行时,发生疲劳断裂的
循环周次称为材料的过载持久值,R
也称有限疲劳寿命,它表征了材 料对过载的抗力。
N
图5-12 过载持久值
曲线越陡,过载持久值越高,说明材料在相同 的过载荷下能承受的应力循环周次越多,材料的抗 过载能力越强。
AB曲线上任一点: tan max 2 m 1 r
因此只要知道了r,求得,从O作相应连线 OH,H点的纵坐标即为所求的疲劳极限。
H
A
B
O
m
45
C
min max(min)—m图
AB曲线是不同r下的max,AC曲线是不同r下 的min。此图是脆性材料的疲劳图,对于塑性材料, 应该用屈服强度0.2进行修正。
此题中,m=13,n=4,
故R=1/13× (2×546+5×519+5×492+1×464)=508MPa
2021年10月21日 星期四
第五章 金属的疲劳
测定时注意两个问题:
第一级应力水平要略高于预计的疲劳极限。对于钢
材,R≈0.45b~ 0.5b,建议取1=0.5b。应力增量 一般为预计疲劳极限的3%~5%,钢材取
材料力学性能第五章

将不同应力比r下的疲劳 极限,分别以σmax(σmin) 和σm表示于坐标系中, 就形成疲劳图。 AHB就是在不同r下的疲 劳极限σmax。 疲劳极限随平均应力或 应力比的增加而增加, 但应力幅度a减小。
4/17/2014 安徽工业大学 材料科学与工程学院
29
B点:σm=0,r=-1,σa=σ-1, 疲劳极限σmax=σ-1 A点:σm=σb,r=1,σa=0,疲劳极限σmax=σb AB之间的各点即表示相应r(-1<r<1)下的疲劳极限
4/17/2014
安徽工业大学 材料科学与工程学院
24
屈强比σs/σb对光滑试样的疲劳极限也有一定影响,可用经验公 式计算对称循环下的疲劳极限:
-1 p 0.23( s b )
结构钢:
-1 0.27( s b )
-1 p 0.4 b -1 0.45 b
安徽工业大学 材料科学与工程学院
4/17/2014
27
OB: σr与r的几何关系: 所以只要知道应力比r,代入上式就可求出 ,在图上作角度 的直 线,与AC交于点B,即可求出相应r的疲劳极限
4/17/2014
安徽工业大学 材料科学与工程学院
28
2. σmax(σmin)-σm疲劳图
4/17/2014
安徽工业大学 材料科学与工程学院
13
4/17/2014
安徽工业大学 材料科学与工程学院
14
(3)瞬断区
是裂纹最后失稳快速扩展所形成的断口区域 在疲劳裂纹亚稳扩展阶段,随着应力不断循环,裂纹 尺寸不断长大, 当裂纹长大到临界尺寸ac时,因裂纹尖端的应力场强 度KI达到材料的断裂韧度KIC(KC),则裂纹失稳快 速扩展,导致机件最后瞬时断裂。 宏观特征:断口比疲劳区粗糙,同静载的裂纹件的断 口一样,随材料的性质而变: 脆性材料为结晶状断口, 韧性材料在中间平面应变区为放射状或人字纹断口, 在边缘平面应力区为剪切唇。
材料力学性能-第五章-其它疲劳类型(3)
不利的拉应力,易出现发状裂纹和氢脆。其它的表
面保护如涂漆、涂油或用塑料、陶瓷形成保护层等,
对减少腐蚀疲劳都是有益的。
六、腐蚀疲劳
工业上的很多零部件是在腐蚀介质中承受
交变载荷作用的,如船舶的推进器、压缩机和
燃气轮机的叶片等。它们的破坏是在疲劳和腐
蚀联合作用下发生的,称之为腐蚀疲劳。腐蚀
疲劳过程也包括裂纹的萌生和扩展过程,只不
过在腐蚀介质的参与下其裂纹萌生要比在惰性
介质中容易得多,所以裂纹扩展特性在整个腐
蚀疲劳过程中占有更重要的地位。
2021年10月24日 星期日
第五章 金属的疲劳
腐蚀疲劳的特点:
腐蚀环境不是特定的。只要环境介 质对材料有腐蚀作用,再加上交变应 力的作用,都可产生腐蚀疲劳,这一 点和应力腐蚀有很大不同,腐蚀疲劳 不需要金属-环境介质的特点组合, 因此,腐蚀疲劳更具有普遍性。
2021年10月24日 星期日
第五章 金属的疲劳
反向加载时沿滑移线形成BC`B`裂纹;
C`
B
B`
B`
图5-65 点腐蚀产生疲劳裂纹
2021年10月24日 星期日
第五章 金属的疲劳
保护膜破裂形成裂纹模型:
保护膜
该理论认为,在发生应力腐蚀破坏时,
首先表现为钝化膜的破坏,破坏处的金属
表面暴露在腐蚀介质中会成为阳极,而其
余具有钝化膜的表面便成为阴极,从而形
2021年10月24日 星期日
第五章 金属的疲劳
热疲劳裂纹是沿表 面热应变量最大的区域 形成的,裂纹源一般有 几个,在循环过程中微 裂纹相互连接形成主裂 纹。裂纹扩展方向垂直 于表面,并向纵深扩展 导致断裂。
图5-62 锅炉套管的热疲劳裂纹
材料力学性能-第五章-其它疲劳类型(1)
第五章 金属的疲劳
不论是循环硬化材料还是循环软化
材料,应力-应变回线只有在循环周次
达到一定值后才是闭合的—达到稳定状
态。对于每一个固定的应变幅,都能得
到相应的稳定的滞后回线,将不同应变
幅的稳定滞后回线的顶点连接起来,就
得到图5-47所示的循环应力-应变曲线。
2021年10月21日 星期四
第五章 金属的疲劳
时控制材料疲劳行为的已不是名义应力,而是塑
性变形区的循环塑性应变,所以,低周疲劳实质
上是循环塑性应变控制下的疲劳。
2021年10月21日 星期四
第五章 金属的疲劳
由于塑性变形的存在,应力
B
应变之间不再呈直线关系,
A
循环稳定后形成如图5-44所 示的封闭回线。
E
C
O
开始加载:O A B;
卸载:B C; 反向加载:C D; 反向卸载:D E; 再次拉伸:E B;
从而产生循环硬化。在冷加工后的金属中,充
满位错缠结和障碍,这些障碍在循环加载中被
破坏,或在一些沉淀强化不稳定的合金中,由
于沉淀结构在循环加载中被破坏均可导致循环
软化。
2021年10月21日 星期四
第五章 金属的疲劳
二、低周疲劳的应变-寿命(-N)曲线
低周疲劳时总应变幅t包括弹性应变幅e和
塑性应变幅p,即t=e+p。Manson和Coffin
2021年10月21日 星期四
第五章 金属的疲劳
在双对数坐标图上,上式等号右端两项是两条
直线,分别代表弹性应变幅-寿命线和塑性应变幅
寿命线,两条直线叠加成总应变幅-寿命线,如图5-
48所示。
直线交点对应的寿命称为过渡寿 命。交点左侧塑性应变幅起主导作 用,材料疲劳寿命由塑性控制;交 点右侧弹性应变幅起主导作用,材 料疲劳寿命由强度决定。因此,在 选择材料和确定工艺时,要弄清机 件承受哪一类疲劳。
材料科学第5章轴向拉压
§5–1 轴向拉压的概念及实例§5–2 轴向拉压横截面上的内力§5–3 轴向拉压横截面上的应力§5–4 材料在轴向拉压时的力学性能§5–5 轴向拉压时的强度计算§5–6轴向拉压时的变形分析第五章轴向拉伸和压缩§5–1 轴向拉压的概念及实例工程实例程实例程实例由二力杆组成的桥梁桁架工程实例工程实例由二力杆组成的桁架结构内燃机的连杆工程实例程实例受力特点:外力的合力作用线与杆件的轴线重合。
受力特点:外力的合力作用线与杆件的轴线重合。
变形特点拉伸变形轴线方向伸长,横向尺寸缩短。
变形特点压缩变形轴线方向缩短,横向尺寸增大;F F拉伸F F压缩拉压变形简图以拉压变形为主的杆件——杆偏心压缩讨论12、“等直杆的两端作用一对等值、反向、共线的集中力时,杆将产生轴向拉伸或压缩变形。
”PP3、情况下,构件会发生轴向拉压?F N -F=0F N =F轴力;FF F N FF N N F 的作用线与轴线重合单位:牛顿(N )F §5–2 轴向拉压时横截面上的内力一、内力轴力概念无论取左段还是右段,两段轴力大小相等,方向相反同一位置左、右侧截面内力分量必须具有相同的正负号。
轴力正负号规定轴力以拉为正,以压为负。
二、轴力图形象表示轴力随截面的变化情况,发现危险面;FF2F2F112233F N1=FFF N1F2FFF N 2F N2FFF N 3F N3例题作杆件的内力图,确定危险截面轴力图xNF FF2F2FFFF例题:已知F1=10kN;F2=20kN;F3=35kN;F4=25kN;试画出图示杆件的轴力图。
CF1F3F2F 4A B DkN 1011 F F N F N1F 1F 1F 3F 2F 4AB C DkN10F 2N 2233F N3F 4F N2F 1F 2F F F 122N kN2543 F F N 2、绘制轴力图。
《材料性能学》课件——第五章 材料的疲劳性能
前言
材料的疲劳问题研究从近150多年开始一直受到人们的关注,原因 之一就是工程中的零件或构件的破坏80%以上是由于疲劳引起。
图5-5 疲劳微裂纹的3种形式
晶界或亚晶 界处开裂
1、疲劳裂纹的萌生 在循环载荷的作用下,会在试件表面形成循环滑
移带。循环滑移带在表面加宽过程中,还会出现挤出 脊和侵入沟,随着挤出脊高度与侵入沟深度的不断增 加。侵入沟就像很尖锐的微观缺口,应力集中严重, 疲劳微裂纹也就易在此处萌生。
图5-6 金属表面“挤出”与“侵入”并形
三、疲劳断口的宏观特征
机件疲劳破坏的疲劳源可以是一个,也可以是 多个,它与机件的应力状态及过载程度有关。如单 向弯曲疲劳仅产生一个源区,双向反复弯曲可出现 两个疲劳源。过载程度愈高,名义应力越大,出现 疲劳源的数目就越多。若断口中同时存在几个疲劳 源,可根据每个疲劳区大小、源区的光亮程度确定 各疲劳源产生的先后,源区越光亮,相连的疲劳区 越大,就越先产生;反之,产生的就晚。
3、复合材料的疲劳破坏机理
疲劳破坏特点: (1)有多种疲劳损伤形式:如界面脱粘,分层、 纤维断裂、空隙增长等。实际上,每种损伤模 型都是由多种微观裂纹(或微观破坏)构成的。 损伤沿着最佳方位起始和扩展,可以一种或多 种形式出现。
3、复合材料的疲劳破坏机理
⑵复合材料不会发生瞬时的疲劳破坏,常常难以确 认破坏与否,故不能沿用金属材料的判断准则。常 以疲劳过程中材料弹性模量下降的百分数(如下降l %~2%)、共振频率变化(如1~2Hz)作为破坏依据。
- 1、下载文档前请自行甄别文档内容的完整性,平台不提供额外的编辑、内容补充、找答案等附加服务。
- 2、"仅部分预览"的文档,不可在线预览部分如存在完整性等问题,可反馈申请退款(可完整预览的文档不适用该条件!)。
- 3、如文档侵犯您的权益,请联系客服反馈,我们会尽快为您处理(人工客服工作时间:9:00-18:30)。
§5.2 疲劳S-N曲线及疲劳极限
升降法→测条件疲劳极限σ-1(低应力)
试验方法
数据整理,拟 合成疲劳曲线
成组试验法→测定高应力部分
① 成组试验法测高应力段
取3~4级较高应力水平,每级水平下,测5根左右试样计 算中值疲劳寿命
0.35 ~ 0.7 b
逐 步 减 小
1 0.7 b , N f )1
B点: σm =0 (r=-1), σa = σ-1 , 疲劳极限σrmax = σ-1 A点: σm = σb (r=1), σa = 0, 疲劳极限σrmax = σb 在A点时,静载已使材料断裂,故不允许再有 动载σa 。
GOODMAN 图
§5.2 疲劳S-N曲线及疲劳极限
四、疲劳断口分析
1、疲劳断口
失稳扩展裂纹长度为ac,则a0<ac, a0→ac的扩展是裂纹的亚稳扩展。
§5.3 疲劳裂纹扩展速率 a-N曲线测定试验一般采用三点弯曲单边 缺口试样,在固定r和Δσ下循环加载,记 录a随N的增长情况。由(Ni,ai)作曲线 用“七点递增多项式”来确定在每 个点下的da/dN,对a-N曲线上任意 数据点i,取其前后相邻的三点,加 上i点本身共七点,采用最小二乘法 进行局部拟合(抛物线): a a AN BN
§5.2 疲劳S-N曲线及疲劳极限
疲劳区:疲劳裂纹亚稳扩展 该区是判断疲劳断裂的重要特征证据。 疲劳区的宏观特征:断口比较光滑并分布有 贝纹线(或海滩花样)。 贝纹线:疲劳区的最大特征, 呈弧状台阶痕 迹。 原因: 载荷变动,eg.机器运转时的开动和 停歇,偶然过载引起的载荷变动。 贝纹特征常出现在实际机件的疲劳断口中, 而在实验室试样疲劳断口中很难看到(变动载 荷平稳)。 脆性材料(eg.铸铁、高强度钢)的疲劳断口 上也看不到贝纹线 循环应力低,材料韧性好,疲劳区大,贝纹 线细、明显。
ABC曲线上任一点B和原点 O连线,其几何关系:
A点:σm=0, r = -1, σa=σ-1 C点:σm=σb, r = 1, σa=0
应力比r→tan α和α →定位在ABC曲线上→其纵、横坐标之和,即为相应r的
疲劳极限σr
§5.2 疲劳S-N曲线及疲劳极限
2. 定量:绘制疲劳图(σmax(σmin)- σm)
。。。 。。。
n 0.35 b , N f )n
§5.2 疲劳S-N曲线及疲劳极限
② 升降法测疲劳极限σ-1 有效试样13根以上;一般取3~5级应力水平,每级应力增量一般为3%~5% 第一根σ应略高于σ-1估计值 若无法预计,则一般材料取(0.45~0.50) σb, 高强度钢取(0.30~0.40) σb。根据上一根试样结果,确定下一根试样的应 力水平,直至完成全部试验。 破坏(107周次循环断裂)→降低应力,通过→升高应力 σ1,107未断→ σ1 < σ-1 ; σ2(> σ1),107断; 内插 σ1 <σ3< σ2 , 107未断, | σ2-σ3|<10MPa
☼ 材料本身的影响: 材料性能主要影响疲劳辉纹,脆性越大,疲劳辉纹越不明显。 脆性辉纹可能是不连续的。 有疲劳灰纹为疲劳断裂,无疲劳灰纹不一定不为疲劳断裂
§5.2 疲劳S-N曲线及疲劳极限
☼ 加载历史的影响:
t
疲劳辉纹由密→疏→密 ☼ 缺口敏感性:
表面裂纹扩 展慢,心部 裂纹扩展快, 向下凸 缺口不敏感
青铜: σ-1=0.21σb
不同材料σ-1/σb=w (耐久比) 钢 σb≤1400MPa,w=0.5, σb >1400MPa,w<0.5 铸铁w=0.4~0.48 铜合金w=0.35~0.4
§5.2 疲劳S-N曲线及疲劳极限
四、σm对σ-1的影响
1. 定性
0
m
a
是纯动载荷,无静载荷(对 材料造成损伤的只是动载荷)
火车车轴受力 r 1, 0
m
若 > ,疲劳“过载持久值” 。
工作 -1
1
a
1
b
N
b
log N
§5.2 疲劳S-N曲线及疲劳极限
二、S-N曲线的测试方法
1、试样:圆截面,直径为10mm 2、方法:测试方法:四点弯曲试验 测试设备:旋转弯曲疲劳试验机 同一批试样试验速度要相同 平稳而无冲击的将力加载到规定值 试验一直进行到试样失效或达规定循环次数时终止 失效:试样出现肉眼可见疲劳裂纹或完全断裂。
§5.1 疲劳特点
弯曲疲劳 扭转疲劳 应力状态: 拉压疲劳 复合疲劳 环境:
大气疲劳 腐蚀疲劳 高温疲劳 热疲劳 接触疲劳
§5.1 疲劳特点
二、特点
疲劳是低应力循环延时断裂,即具有寿命的断裂. 应力↓寿 命↑. 断裂应力水平往往低于材料抗拉强度,甚至屈服强度。 在名义应力不高的情况下,由缺陷处局部应力集中而形成裂 纹,随着加载循环的增长,裂纹不断扩展,直至剩余截面不 能再承担负荷而突然断裂。实际构件的疲劳破坏过程总可以 分裂纹萌生、裂纹扩展和最终断裂三个组成部分。 疲劳是脆性断裂,在静载下无论显示脆性与否,在疲劳断 裂时都不会产生明显的塑性变形,而断裂却常常是突发性的, 没有预兆。是在长期累积损伤过程中,经裂纹的萌生和缓慢 亚稳扩展到临界尺寸时才突然发生的,因此,疲劳是一种潜 在的突发性脆性断裂 疲劳对缺陷(缺口、裂纹及组织缺陷)十分敏感 增大对材 料的损伤,降低材料的局部强度
逐点描绘法
§5.2 疲劳S-N曲线及疲劳极限
疲劳试验结果的统计处理及P-S-N曲线
对于应力在疲劳极限以下工作的构件,采用升降法测定的条件疲劳极 限,就可以满足设计要求。 对有限寿命设计,仅按上述常规成组法测定存活率50%的中值S-N曲线, 作为设计依据,往往偏于危险,因为这意味着有一半产品在达到预定 寿命之前出现早期破坏。 需要测得具有更高存活率的S-N曲线。如存活率为99.9%的S-N曲线, 该曲线给出的寿命N对1 000个产品,只有一个可能造成早期断裂。这 种S—N曲线给出的数据具有较大的可靠性。
a
>0
m
>0
m
既承受动载荷σa又承受静载荷 σm 损伤容量相同,若静载荷σm越大, 所能承受的动载荷σa越小。
0
m
§5.2 疲劳S-N曲线及疲劳极限
2. 定量:绘制疲劳图(σa- σm)
疲劳图:各种循环疲劳极限的集合 图,是疲劳曲线的另一种表达形式 纵坐标以应力幅σa 表示 横坐标以平均应力σm表示 在不同应力比r条件下,将σmax表示的 疲劳极限σr分解为σa和 σm ,并在该坐 标系中作ABC曲线,即为σa-σm疲劳图, σr =σa+σm。
a Y
min
a Y a
§5.3 疲劳裂纹扩展速率 3、
da K曲线 (由△K起控制作用) dN △Kth:疲劳裂纹扩展门槛值, 表示材料阻止疲劳裂纹开始扩 展的能力。
缺口敏感
表面裂纹扩 展快,心部 裂纹扩展慢, 向上凸
§5.3 疲劳裂纹扩展速率
§5.3 疲劳裂纹扩展速率
一、基本规律
da 1、疲劳裂纹扩展速率 dN
Ni-疲劳裂纹萌生寿命、 Nf-疲劳裂纹扩展
N N N
f i
p
N 5% ~ 10%N
i
f
疲劳总寿命=疲劳裂纹萌生寿命+疲劳裂纹扩展寿命
原始裂纹长度为a0,
2 0
脉冲加载
da / dN A 2BN
da f a , dN
2、△K(应力强度因子范围) 如认为疲劳裂纹扩展的每一微小过程类似是裂纹体小区域的断裂过程,ΔK 就是裂纹尖端控制疲劳裂纹扩展的复合力学参量。
K Y a
K K
Im a x
K
Im i n
Y
max
§5.2 疲劳S-N曲线及疲劳极限
瞬断区:裂纹失稳快速扩展 疲劳裂纹亚稳扩展时,随应力不断循 环,裂纹尺寸a↑, 当a≥ac(临界裂纹尺寸) 时,KI≥KIC,裂纹失稳快速扩展,机件 瞬时断裂。
其断口比疲劳区粗糙,宏观特征与静 载裂纹件断口一样,随材料性质而变: 脆性材料为结晶状断口;韧性材料的中 间平面应变区为放射状或人字纹断口, 边缘平面应力区为剪切唇。 位置:一般在疲劳源的对侧。 瞬断区的大小和机件名义应力及材料 性质有关:若名义应力较高或材料韧性 较差,则瞬断区就较大,反之,瞬断区 较小。
σmax= σm+σa σmin= σm-σa
对称交变应力
脉动应力
波动应力
不对称交变应力
§5.1 疲劳特点
常见的循环应力: ⑴ 对称交变应力 σm=0, r =-1(σmin=-σmax) (图a), 大多旋转轴类零件的
循环应力, 如火车轴的弯曲对称交变应力、曲轴的扭转交变应力
静载σm=0,动载σa= σmax ,是交变载荷中的最危险情况 ⑵ 脉动应力 σm= σa>0, r=0 (图b) , 齿轮齿根的循环弯曲应力;轴承 的循环脉动压应力,σm= -σa<0, r=-∞ (图c) ⑶ 波动应力 σm>σa, 0<r<1 (图d) , 如发动机缸盖螺栓的循环应力 ⑷ 不对称交变应力 r<0 , r≠-1 (图e), 如发动机连杆的循环应力
典型的疲劳断口具有三个形貌不同的 区域——疲劳源、疲劳区及瞬断区。 疲劳源:疲劳裂纹萌生的策源地 疲劳源一般在机件表面,常和缺口、裂纹、刀痕、蚀坑等缺陷相连(应力 集中)。材料内部也可能产生疲劳源:当材料内部存在严重冶金缺陷(夹杂、 缩孔、偏析、白点等)或内裂纹时(局部强度降低)。 随应力状态及其大小的不同,疲劳源可以有一个或几个。可根据源区的光 亮度、相邻疲劳区的大小和贝纹线的密度确定各疲劳源的产生顺序。 断口形貌:疲劳区光亮度最大 原因:①裂纹亚稳扩展过程中,应力交变引起的断面不断摩擦挤压而光亮; ②加工硬化使表面硬度提高。