试模报告
注塑模具试模报告(最完美)

注塑模具试模报告引言注塑模具试模是一个关键的过程,它对产品的质量和生产效率具有重要影响。
本报告旨在详细介绍注塑模具试模过程中的各个环节,为了实现最完美的结果,我们将从模具设计、材料选择、工艺参数设置、试模测试以及优化改进等方面进行阐述。
概述注塑模具试模是在注塑机上进行的模具性能测试过程,通过对模具进行试模可以评估其性能和功能的可靠性,以确保产品能够满足设计要求。
试模过程中需要考虑模具的定位精度、注塑过程的稳定性、产品的成型质量等因素。
正文内容一、模具设计1. 模具结构设计:模具的结构设计应考虑产品的设计要求和注塑工艺的特点,确保模具能够精确定位并顺利进行注塑过程。
2. 模具材料选择:模具的材料选择应考虑产品的成型要求、生产批量和模具寿命等因素,常用的模具材料有硬质合金、工具钢、不锈钢等。
二、材料选择1. 塑料材料选择:根据产品的用途和要求选择合适的塑料材料,考虑其热稳定性、机械性能、耐化学腐蚀性等。
2. 材料预处理:塑料材料在注塑前需要进行干燥处理,以确保材料的质量和注塑过程的稳定性。
三、工艺参数设置1. 注射压力与速度设置:注射压力和速度的设置应根据产品形状、尺寸和壁厚等因素进行合理调整,以防止产生缺陷,如短射、热裂纹等。
2. 注射温度控制:注射温度的控制对于保证产品的成型质量至关重要,应根据塑料材料的熔融温度进行合理设定。
3. 模具温度控制:模具温度的控制能够影响产品的收缩和表面质量,应根据塑料材料的热性能设定合适的温度。
四、试模测试1. 注塑工艺试模:在试模过程中,通过调整工艺参数进行试模测试,如调整注射速度、温度等,评估产品的造型效果和成型质量。
2. 模具寿命测试:通过连续进行多次试模测试,以评估模具的寿命和性能稳定性,确定模具是否需进行改进或调整。
五、优化改进1. 问题分析和解决:根据试模测试的结果,分析产生的缺陷及其原因,并提出相应的解决方案,如调整工艺参数、优化模具结构等。
2. 模具维护与保养:及时进行模具的维护和保养工作,延长模具的使用寿命,提高生产效率和产品质量。
注塑机试模报告范文

注塑机试模报告范文一、实验目的1.熟悉注塑机的结构和工作原理;2.学会注塑机调试;3.掌握塑料试模的方法与步骤。
二、实验器材1.注塑机;2.模具;3.塑料颗粒;4.计时器;5.料筒;6.注射嘴。
三、实验步骤1.检查机器和模具是否完好,无损坏和杂质的情况;2.准备好塑料颗粒,并保证其质量和干燥度;3.将模具安装在注塑机上,并确保其稳定;4.打开注塑机的电源,进行设定温度和时间;5.将塑料颗粒放入料筒中,并控制好注射嘴的位置;6.启动注塑机,并观察塑料的注射情况;7.计时器记录注塑机的工作时间;8.完成注塑后,关闭注塑机电源,并取出注塑好的塑料制品;9.清理注塑机和模具的残留物和杂质。
四、实验结果与分析经过实验,我们成功地进行了注塑试模。
注塑机的结构和工作原理使得塑料颗粒通过加热和压力作用下,变为流动性良好的熔融态,然后通过注射嘴注入到模具中,最终形成我们想要的塑料制品。
在进行试模的过程中,我们需要注意模具的安装和稳定性,确保塑料颗粒可以均匀、连续地注入到模具中。
此外,对注射嘴的位置和长度的控制也很重要,如果注射嘴的位置不正确或长度过长,会影响塑料的注射质量。
实验中还需要设定好注塑机的温度和时间,这是根据所用塑料的熔点和流动性来决定的。
温度过高或时间过长会导致塑料过热或熔化不均匀,从而影响制品质量。
在实验中,我们通过记录注塑机的工作时间,可以对注塑的效率和生产能力进行评估和改进。
如果工作时间太长,可能需要适当调整注射速度或温度,以提高生产效率。
五、实验总结通过本次试验,我们掌握了注塑机的调试方法和塑料试模的步骤。
注塑机的结构和工作原理对于塑料制品的生产起着至关重要的作用。
同时,在试模的过程中,我们还需要注意模具的安装和稳定性、注射嘴的位置和长度、注塑机的温度和时间的调整。
这些因素直接影响着塑料的注射和成型效果。
通过实验的过程,我们对注塑机的工作原理和调试方法有了更深入的了解,并掌握了塑料试模的步骤。
压铸试模总结报告范文(3篇)

第1篇一、项目背景随着我国汽车、电子、电器等行业的发展,对精密金属制品的需求日益增加。
压铸作为一种高效、节能、环保的金属成型工艺,广泛应用于各类产品的制造中。
为了确保压铸件的质量和性能,试模环节至关重要。
本报告针对某型号压铸件进行试模,总结试模过程中的经验与教训,为后续生产提供参考。
二、试模目的1. 确保压铸件尺寸精度和表面质量;2. 优化模具结构,降低生产成本;3. 提高生产效率,缩短生产周期;4. 评估压铸工艺参数,为生产提供依据。
三、试模过程1. 模具设计:根据产品图纸,设计压铸模具,包括型腔、浇注系统、冷却系统等。
2. 模具加工:按照模具设计图纸,进行模具加工,确保模具精度和表面质量。
3. 模具装配:将加工好的模具零件进行装配,确保模具的刚性和密封性。
4. 工艺参数确定:通过实验,确定压铸工艺参数,如熔体温度、压射速度、保压压力、冷却时间等。
5. 压铸实验:在确定的工艺参数下,进行压铸实验,观察压铸件的尺寸精度、表面质量、内部缺陷等。
6. 数据分析:对实验数据进行整理和分析,评估压铸件的质量和性能。
四、试模结果1. 尺寸精度:压铸件尺寸精度达到产品图纸要求,无明显的尺寸偏差。
2. 表面质量:压铸件表面光滑,无明显的缺陷,如气孔、夹杂等。
3. 内部缺陷:压铸件内部无明显的缩松、冷隔等缺陷。
4. 生产成本:通过优化模具结构和工艺参数,降低了生产成本。
5. 生产效率:压铸实验证明,压铸件生产周期可缩短20%。
五、总结与建议1. 优化模具设计:在保证模具刚性和密封性的前提下,简化模具结构,降低生产成本。
2. 严格控制工艺参数:根据实验结果,确定合理的熔体温度、压射速度、保压压力、冷却时间等工艺参数。
3. 加强过程控制:在生产过程中,严格控制熔体温度、压射速度、保压压力等关键参数,确保压铸件质量。
4. 优化生产线:提高生产线自动化程度,降低人工成本,提高生产效率。
5. 持续改进:针对试模过程中发现的问题,持续改进模具设计、工艺参数和生产工艺,提高产品质量。
注塑试模产品报告模板

注塑试模产品报告模板一、试模背景及目的本次试模的背景是为了测试某个注塑产品的生产工艺及模具可行性,并验证产品的质量符合要求。
试模的目的是通过实际注塑生产出的产品,评估其尺寸精度、表面质量以及材料流动性等性能。
二、试模过程及参数设置1. 模具选择:XXX型号模具;2. 原料选择:XXX材料;3. 注塑设备:XXX注塑机;4. 注塑参数设置:- 射出压力:XXX MPa;- 射速:XXX mm/s;- 射胶量:XXX g;- 螺杆转速:XXX rpm;- 模具温控温度:XXX ;- 冷却时间:XXX s。
三、试模结果分析1. 尺寸精度测量了注塑产品的尺寸,并与设计要求进行对比分析。
结果显示,产品的尺寸精度符合要求,各个关键尺寸的偏差在允许范围内。
2. 表面质量观察了注塑产品的表面质量,除了小部分产品存在一些细微的表面瑕疵外,整体表面质量良好,没有明显的气泡、划痕或色差。
3. 材料流动性通过观察产品的浇口、水口及排气情况,评估了材料在注塑过程中的流动性。
结果显示,材料流动性良好,浇口和水口处没有明显挤出现象,且排气通畅。
四、问题分析及解决方案根据试模结果,发现了一些问题,如单个产品出现略微尺寸偏差等。
经过分析,可能是以下原因导致:1. 模具加工精度不够,导致产品尺寸偏差;2. 注塑参数设置不合理,影响了产品的质量。
为了解决以上问题,采取了以下措施:1. 优化模具的制造工艺,提高精度,确保产品尺寸稳定;2. 调整注塑参数,如调整射胶量及温控温度等,以改善产品的质量。
五、本次试模总结本次试模结果显示,注塑产品在尺寸精度、表面质量和材料流动性等方面均符合要求。
通过问题分析和解决方案,确定了进一步优化模具和注塑参数的方向,以提高产品质量和生产效率。
未来将根据试模结果的反馈,继续进行改进和优化,以提高生产工艺的稳定性和产品的竞争力。
以上是本次注塑试模产品的报告模板,希望对您的工作有所帮助。
如有需要,请根据具体情况进行修改和补充。
模具试模报告(二)2024
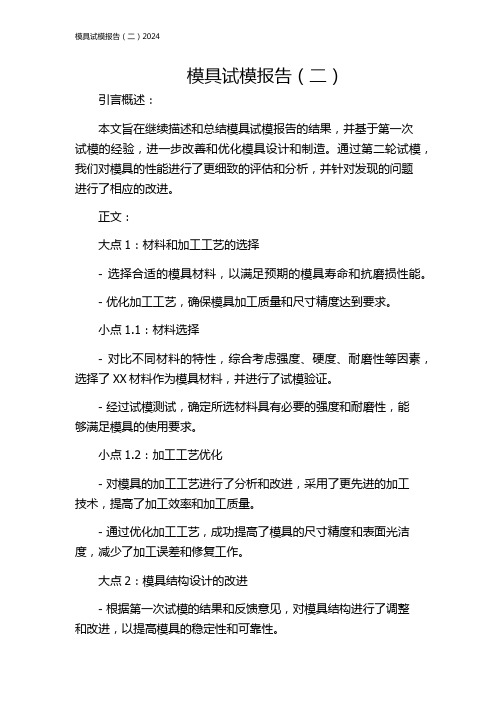
模具试模报告(二)引言概述:本文旨在继续描述和总结模具试模报告的结果,并基于第一次试模的经验,进一步改善和优化模具设计和制造。
通过第二轮试模,我们对模具的性能进行了更细致的评估和分析,并针对发现的问题进行了相应的改进。
正文:大点1:材料和加工工艺的选择- 选择合适的模具材料,以满足预期的模具寿命和抗磨损性能。
- 优化加工工艺,确保模具加工质量和尺寸精度达到要求。
小点1.1:材料选择- 对比不同材料的特性,综合考虑强度、硬度、耐磨性等因素,选择了XX材料作为模具材料,并进行了试模验证。
- 经过试模测试,确定所选材料具有必要的强度和耐磨性,能够满足模具的使用要求。
小点1.2:加工工艺优化- 对模具的加工工艺进行了分析和改进,采用了更先进的加工技术,提高了加工效率和加工质量。
- 通过优化加工工艺,成功提高了模具的尺寸精度和表面光洁度,减少了加工误差和修复工作。
大点2:模具结构设计的改进- 根据第一次试模的结果和反馈意见,对模具结构进行了调整和改进,以提高模具的稳定性和可靠性。
- 优化模具的流道设计,增加冷却系统,提高产品成型的效率和质量。
小点2.1:模具结构调整- 针对第一次试模中出现的问题,对模具的结构进行了调整,增加了支撑和固定部位,提高了模具的稳定性。
- 通过数值模拟和分析,确定了最佳的模具结构参数,确保产品能够顺利成型并达到设计要求。
小点2.2:流道设计优化- 在模具的流道设计中引入了新的改进措施,包括增加冷却系统和优化流道形状,以提高产品的冷却效果和塑料注射流畅性。
- 经过试模验证,流道设计的改进有效地减少了产品的缺陷和收缩问题,并提高了产品的外观质量和尺寸稳定性。
大点3:模具调试和参数优化- 对模具进行了调试和参数优化工作,以确保模具能够正常运行并达到预期的模具寿命和性能要求。
- 通过调整注射速度、温度等参数,改善了产品的填充性能和表面质量。
小点3.1:模具调试- 在试模过程中,及时发现和解决模具使用中的问题,对模具的运行状态进行调试和优化。
模具试模情况报告单

模具试模情况报告单一.试模前准备工作1.检查模具设计图纸是否准确无误;2.确保所有材料和工具准备齐全;3.清洁模具,并检查是否有损坏或磨损的部分。
二.试模过程1.试模前的安全操作:a.确保机器正常运作,并进行预热;b.穿戴好安全装备,如手套、护目镜和防护服;c.防止模具和工件过热或碰撞。
2.根据实际情况调整注塑机参数:a.确定模具温度和压力控制设定值;b.优化注塑速度和压力曲线。
3.注塑成型参数调整:a.根据模具结构和工件要求,确定注塑射速、射压和保压时间;b.进行试模操作,观察工件质量和模具状况。
4.重复试模操作,直到满足产品要求:a.调整注塑机参数,如温度、压力、速度等;b.检查成型品的尺寸、外观质量和性能。
5.记录试模过程和结果:a.记录每次试模的参数和成型品情况;b.分析并总结试模结果,找出问题所在并解决。
三.试模结果与评估1.注塑品外观质量:a.检查注塑品的表面光洁度、色泽、划伤和气泡等缺陷;b.判断注塑品的大小、形状、重量和尺寸是否达到设计要求。
2.注塑品功能性评估:a.进行注塑品的装配和功能测试;b.检查注塑品的强度、刚性和耐磨性等性能。
3.模具质量评估:a.检查模具表面是否光滑、无划痕或磨损;b.检查模具的寿命和稳定性。
四.试模总结和改进措施1.分析试模结果:a.根据试模过程和试模结果,找出存在的问题;b.分析问题的原因,如模具设计、注塑工艺参数等。
2.提出改进措施:a.针对问题提出相应的改进方案;b.改进模具设计、注塑工艺参数等,并进行试模验证。
3.试模总结:a.总结试模过程和结果,记录问题和解决方案;b.提出改进建议,如模具维护保养、工艺改进等。
五.建议和结论1.根据试模结果,对模具设计、注塑工艺等提出建议;2.根据试模结果,判断是否能够满足产品要求;3.总结试模的经验教训,以便今后的生产中能够更好地应对类似情况。
六.附件1.试模记录表;2.问题和改进建议列表;3.试模过程中的照片或视频等。
试模报告名词解释
试模报告名词解释1)机台规格: 用机台的最大锁模力来表征(例.450T)2)模具穴数: 为1表示一模出一个产品.3)进胶方式:指浇口(gate)类型和布局方式。
浇口常见形式为直接浇口、普通浇口(浇道)针点浇口、潜浇口、阀浇口。
一般注射成型采用多个浇点, 浇点位置选择比较关键。
4)顶出方式:将塑件由模具型腔或者型芯上脱出的机构为顶出机构。
顶出方式按照顶出机构驱动方式的不同或者模具结构的不同进行划分,按照前者可以分为手动、机动、液压等方式;按照后者可划分为简单顶出,两级顶出等。
正常顶出为一次顶出.5)原料干燥:原料干燥的目的是为了去除原料中的大部分水分,在成型前进行如果不干燥塑件表面可能出现银丝,气泡等缺陷。
吸水性强的材料必须进行干燥,不易吸水的材料可以不用干燥。
温度:烘干温度必须低于原料热变形温度。
时间:不同的原料烘干时间不一致,一般为2-4h。
例:对于PC+ABS料必须干燥(85度*4H).干燥效果的好坏主要由温度和时间控,温度不能过低,过低会延长干燥时间,也不可过高,超过材料的软化温度会使材料结块.6)每模重量(g)净重:一副模具中一次注射成型所得塑料成品的净重量(=单个成品重量+料头重量/穴数)。
毛重:上述净重加上浇头料的重量。
即脱模后,去除浇头前,塑料制品总重(=成品重量+料头重量)。
7)最大开模位置:公母模能够分离的极限距离(公母模分模面间的距离),一般分模时开模距离都小于最大开模位置。
(参见示意图)8)低压保护位置:合模时,为了避免公母模之间有异物阻隔,保护模具不碰损,注塑机配有低压保护装置。
低压保护位置是指启动低压保护时公母模分模面间的距离,低压保护持续到公母模刚合拢那一刻。
低压保护位置一般根据导柱或斜导柱与相应孔位对准时的位置来确定。
常用小布片等薄片物体来检验低压保护装置是否正常。
(参见示意图)9)高压启动位置:公母模合拢后,施加高压以便锁紧模具系统。
高压启动位置指的便是锁紧过程,铰链压缩的行程。
注塑车间试模报告
压力
储料终止 射退 备注
中 子 压力 中子进
中子退
试模人员:
速度 速度 速度
时 间 起始位置
时 间 起始位置 时 间 起始位置
车间主管:
开关模 关模一段 关模二段
压力 速度
低压模保 高压锁模
开模一慢 开模快一 开模快二
开模二慢 开模终止
备注 托模 托模进
压力 速度
托模退 托模方式
定价
项目负责人:
起始位置 延迟
夹水纹 缩水 烧焦
断水口 碰穿位披
锋 软胶脱胶
夹口线不平 走胶不齐
粘骨位
骨位发白
胶件变形
气纹严重
柱位披锋
顶白
困气
分型面披锋
气泡
气花 蛇仔纹
顶针披锋 行位披锋
混色 碰穿位不
穿 试模运作条件
喷嘴 一 段 温度
二段
三段
四段 冷却
Байду номын сангаас
全程
班产量
射出保压 射出一段 射出二段
压力
射出终止 保压一段
保压二段 备注 储料 储料一段 储料二段
注塑车间试模报告
产品型 产号品:名 注称塑:机 塑类料:批 试号模:原 因:
( 改模
产品名称:
模具制造商 余姚晨航模具
塑料名称:
颜 色:
)吨
总 周 期: (
)秒
次 数:
色粉编号:
新模
试料
修模
模 具 实 况(如有以下现象打“√”)
开模困难
断顶针
走胶困难
合模不紧贴
顶针不顺
顶针板变形
波浪纹
擦穿位披锋
粘前模 粘后模 粘水口
试模总结报告范文(3篇)
第1篇一、引言为了验证产品设计的合理性和可行性,提高产品质量,降低生产成本,我司在产品研发阶段进行了试模工作。
本次试模工作于XX年XX月XX日开始,至XX年XX月XX日结束。
现将试模过程及结果进行总结报告,以期为后续生产提供参考。
二、试模目的1. 验证产品设计的合理性和可行性;2. 优化模具设计,提高模具精度;3. 检验材料性能,确保产品质量;4. 评估生产成本,为生产决策提供依据。
三、试模过程1. 模具设计在试模前,我们根据产品图纸和技术要求,对模具进行了详细的设计。
设计过程中,充分考虑了产品的尺寸精度、形状、材料性能等因素。
2. 模具制造模具制造采用先进的技术和设备,确保了模具的精度和稳定性。
在制造过程中,对模具各部分进行了严格的检验,确保模具质量。
3. 试模材料本次试模采用的材料为XX材料,该材料具有良好的加工性能和力学性能,适用于本产品的生产。
4. 试模设备试模设备选用XX设备,该设备具有高精度、高效率的特点,能够满足试模要求。
5. 试模过程(1)试模前准备:检查模具、设备、材料等是否齐全,确保试模顺利进行。
(2)试模操作:按照操作规程进行试模,记录试模过程中的各项数据。
(3)试模结果分析:对试模结果进行分析,评估产品性能和模具质量。
四、试模结果及分析1. 产品性能(1)尺寸精度:产品尺寸精度达到设计要求,符合国家标准。
(2)形状:产品形状符合设计图纸,无明显变形。
(3)表面质量:产品表面光滑,无明显划痕、气泡等缺陷。
2. 模具质量(1)模具精度:模具精度达到设计要求,无明显磨损。
(2)模具稳定性:模具在试模过程中运行稳定,无异常现象。
3. 材料性能(1)力学性能:材料力学性能符合设计要求,具有较好的强度和韧性。
(2)加工性能:材料加工性能良好,易于加工。
4. 生产成本(1)模具成本:模具成本合理,符合预算。
(2)材料成本:材料成本合理,符合预算。
五、结论1. 产品设计合理,可行性高。
2. 模具设计精度高,稳定性好。
试模总结报告模板
试模总结报告模板
模板:
[报告标题]
1. 概述
介绍研究项目的目的、重要性和背景。
2. 目标与方法
详细描述研究的目标,并列出所采用的方法和工具。
3. 实施过程
说明研究项目的实施过程,包括数据收集、分析和解释的方法。
4. 结果与分析
列出研究项目的主要结果,并对其进行详细分析和解释。
5. 讨论与建议
根据研究结果,提出相关问题的讨论和建议。
6. 结论
总结研究项目的主要发现和结论。
7. 展望
探讨未来研究的可能性和发展方向。
8. 参考文献
列出研究过程中引用的所有参考文献。
[附录/附属材料]
在需要的情况下,将相关数据、表格、图表等附在报告后。
注:
1. 根据实际情况对各部分的标题进行调整和修改。
2. 报告内容应以客观、准确、简洁的方式呈现。
3. 报告格式应符合学术要求,包括页眉、页脚、段落等格式要求。
4. 根据具体要求,可以增加或删除报告中的部分内容。
- 1、下载文档前请自行甄别文档内容的完整性,平台不提供额外的编辑、内容补充、找答案等附加服务。
- 2、"仅部分预览"的文档,不可在线预览部分如存在完整性等问题,可反馈申请退款(可完整预览的文档不适用该条件!)。
- 3、如文档侵犯您的权益,请联系客服反馈,我们会尽快为您处理(人工客服工作时间:9:00-18:30)。
脱模退/Return 冷却方式/ Cooling method 冻水/Chiller( ) 普水/Tower( ) 模温机/Thermolator(√ ) 冻水/Chiller( ) ller( ) 普水/Tower( ) 模温机/Thermolator( ) 冻水/Chiller( ) 普水/Tower( ) 模温机/Thermolator( )
一段/1st Stg 储料 Material Suck- 二段/2nd Stg back 三段/3th Stg 四段/4th Stg 脱模方式/Method 脱模 Ejection Stage 脱模次数/Times 脱模一进/1st Ejt 脱模二进/2nd Ejt 实际模温/Mold Temp
冷却时间 /Cooling Time (s)
试模工艺表 Process Parameter Sheet
零件名称 /Part Name 机台型号 /Machine Model 毛量/Gross Weight(g) 水口类型 Gate Type 烘料温度 /Material Dry Temp: 零件编号 /Part Number 原料 /Raw Material 水口重 /Gate Weight(g) 大水口/Direct Gate( ) 细水口/Point Gate ( ) 潜水口/Sub-Gate( ) 热嘴/Hot nozzle ( ) 模具编号 (Mold NO.) 颜色 /Color 净重 /Net Weight(g) 试模阶段 Shoot Stage 成型总周期 /Total Cycle Time 烘料时间 /Material Dry Time: 模具尺寸 Mold Dimension 出模数 Cavity Quantity
issues
模具问题点 mold issues 单次试模原料 合计重量: 单次调机使用 原料净重: 试模员: 单次试模成品 数量: 单次试模废品 数量: 项目工程师: 废品率: 吨位是否符合 工艺设定: ETI模具工程师: 周期是否符合 工艺设定: 废品率产生原因分析:
数据统计
试模日期:
成型工艺参数/Process Parameter
料桶温度 /Barrel Temp.(°C) 喷嘴/Nozzle 压力/Pressure 一段/1st Stg 二段/2nd Stg 注 射 Injection Stage 三段/3th Stg 四段/4th Stg 五段/5th Stg 保压 Holding Pressure Stage 中子抽芯 Cylinder SLD 行程开关 Position Switch 产品问题点product 一段/1st Stg 二段/2nd Stg 三段/3th Stg 四段/4th Stg 单中子/One( ) 双中子/Two( ) 三中子/Three( ) 强制复位 (√ ) 顶针行程开关/For Ejector Pin ( ) 中子抽芯行程开关/For Cylinder ( ) 前模/Cavity 后模/Core 前模行位/Cavity SLD 后模行位/Core SLD 一段 /1st Stg 速度 /Speed 二段/2nd Stg 位置/Position 三段/3th Stg 时间/Time 四段 /4th Stg 五段/5th Stg 热流道温度 /Hot Runner Temp 压力/Pressure 一段/1st Stg 速度/Speed 二段/2nd Stg 位置/Position