七大浪费问题点原因及对策)
7大浪费的产生原因和消除方法

7大浪费的产生原因和消除方法丰田的7种浪费丰田生产方式认为,不产生附加价值的一切作业都是浪费,它把浪费分为以下7种。
1、生产过剩的浪费:一心想要多销售而大量生产,结果在人员、设备、原材料方面都产生浪费。
在没有需求的时候提前生产而产生浪费。
2、不合格产品的浪费:在生产过程中出现废品、次品,会在原材料、零部件、返修所需工时数、生产这些不合格产品所消耗的资源方面产生浪费。
3、待工的浪费:在进行机械加工时,机器发生故障不能正常作业,或因缺乏零部件而停工等活等,在这样的状态下所产生的浪费都是停工等活的浪费。
4、动作上的浪费:不产生附加价值的动作、不合理的操作、效率不高的姿势和动作都是浪费。
5、搬运的浪费:除去准时化生产所必需的搬运,其他任何搬运都是一种浪费。
比如在不同仓库间移动、转运、长距离运输、运输次数过多等。
6、加工本身的浪费:把与工程的进展状况和产品质量没有任何关系的加工当做是必要的加工而进行操作,此种状况下所产生的浪费。
7、库存的浪费:因为原材料、零部件、各道工序的半成品过多而产生的浪费。
这些东西过度积压还会引起库存管理费用的增加。
消除7种浪费的步骤从哪里开始消除这7种浪费为好呢?在像丰田一样积累了50年以上的改善经验和没有这些改善经验的企业中,在生产体制上存在着很大差异。
在此让我们以问题比较多的企业为对象,来思考一下处理7种浪费的基本顺序。
步骤①:在需要的时候适时生产需要的产品可以排除生产过剩的浪费,这需要具备严格管理的思想。
步骤②:如果经常产生不合格产品,抑制生产过剩是很困难的。
我们要消除不合格产品,消除制造不合格产品的浪费。
步骤③:对于停工等活,只要明白其要点就很容易改善。
消除停工等活的浪费,有效利用人力资源。
步骤④~⑥可以根据消除浪费的着眼点从可以实施的部分开始实施。
步骤④:对于动作的浪费,如果减少工时数(人数×时间)将会对消除浪费产生很大影响。
但是,即使是进行动作分析,清除了一些细小的浪费,也会被其他的问题所掩盖,所以必须注意。
生产7大浪费及解决方案

生产7大浪费及解决方案大家好,今天我们聊聊生产过程中的那些浪费问题,嗯,是的,你没听错,就是浪费。
听到这个词,大家脑海里可能会浮现出各种奇怪的场景。
不过,别急着走神,我们要聊的是制造业中的浪费问题,这些浪费可是让企业流血的罪魁祸首哦。
咱们一块儿来看下去,如何搞定这些浪费,提升生产效率!1. 过多的库存1.1 库存的烦恼哎,说到库存,大家可能会觉得,哇,库存多点不是好事吗?其实不然。
库存积压就像是家里的旧物堆积,既占地方又浪费资源。
库存多了,产品可能过时,生产线也被拖慢,哎,这可真是让人头疼的事儿。
1.2 解决办法那咋办呢?第一步,咱们得搞清楚需求,精准预测,别买一堆又用不上的原材料。
还有,利用“刚性生产”这种方法,按需生产,减少库存积压,真的是“下手快,省得多”。
2. 生产过剩2.1 过剩的烦恼生产过剩嘛,就像是做饭时多煮了一大锅菜,结果吃不完,全都浪费了。
生产线上的东西做得太多,不但没卖出去,库存也得增加,造成不必要的浪费。
2.2 解决办法要解决这个问题,得合理规划生产计划。
可以采用“拉动式生产”,根据实际需求来调整生产节奏,不盲目追求产量,做到“生产有节奏,库存不超标”。
3. 过多的等待时间3.1 等待的煎熬生产过程中,机器闲置、员工等活儿等得不耐烦,这都是浪费时间的表现。
就像是排队等餐,一等就等个天荒地老,效率低得让人心烦。
3.2 解决办法要减少等待时间,就得提高生产线的流畅度。
可以引入“持续改进”的理念,优化生产流程,减少不必要的等待,让生产线像高速公路一样通畅无阻。
4. 不必要的搬运4.1 搬运的麻烦如果生产线上的东西被搬来搬去,就像是玩具被小孩乱丢乱放,费劲不说,还容易出错。
搬运不仅费时费力,还增加了损耗的风险。
4.2 解决办法减少搬运的办法就是优化工作环境,尽量把需要的工具和原材料都放在离工作位置较近的地方。
这样,就能减少不必要的搬运,真是“近水楼台先得月”了。
5. 过多的加工5.1 加工的困扰有些生产流程中,产品被多次加工,就像是在一块木板上反复雕刻,最后不仅时间耗费大,结果也未必好。
产品工作过程中的七大浪费及其解决方案

产品工作过程中的七大浪费及其解决方案在产品开发过程中,存在着七大浪费,也称为“七大Muda”,这些浪费会导致时间、资源和成本的浪费。
了解这些浪费并采取相应的解决方案,可以帮助产品团队提高效率和质量。
1.过度生产过度生产指的是在没有需求的情况下,过早或生产过多的产品。
这会造成库存积压、资金占用和产品过期等问题。
解决方案是通过使用“精益生产”原则,只在有需求的情况下生产所需数量的产品。
2.运输浪费运输浪费包括不必要的物料运输和产品运输。
这会增加成本、延长交货时间,并增加货物损坏的风险。
解决方案是优化物料和产品运输的路径,减少运输距离和次数,并避免不必要的中间仓储。
3.等待浪费等待浪费指的是因为制造过程中的等待而导致的时间浪费。
这可能是由于缺乏前置物料、技术故障或生产线停机等原因引起的。
解决方案是通过优化供应链管理和生产计划来减少等待时间,并确保所需的物料和资源都及时准备就绪。
4.过度加工过度加工是指在产品制造过程中超出需求的额外工作量。
这可能是因为不明确的设计要求、复杂的工艺流程或繁琐的审批程序等原因。
解决方案是通过简化产品设计、优化工艺流程和减少不必要的审批程序来减少过度加工。
5.库存浪费库存浪费是指因过量的库存而造成的资金占用、过期、变质等问题。
这可能是由于过度生产、缺乏库存管理和控制、或供应链延迟等原因导致的。
解决方案是通过精细的库存管理和控制,采取准时交付和供应链协同等方法来减少库存浪费。
6.动作浪费动作浪费指的是在制造过程中没有价值的额外运动和步骤。
如多余的物料搬运、操作过程不流畅、等待签字批准等。
解决方案是通过优化工作站布局,提供合适的工具和设备,并对操作过程进行持续改进来减少动作浪费。
7.缺陷浪费缺陷浪费是指由于制造过程中的缺陷导致的废品、返工、售后客户投诉等问题。
这可能是由于原材料质量问题、工艺流程不稳定或操作不当等原因引起的。
解决方案是通过质量控制和过程改进来减少缺陷,并提高产品质量和客户满意度。
精益管理:7大浪费的产生原因和消除方法

精益管理:7大浪费的产生原因和消除方法今天和大家一起聊聊丰田所说的7种浪费以及消除浪费的步骤和对策,值得制造业同仁学习。
跟你的供应商一起阅读,让大家尊重自然资源,消除浪费,提升利润率。
丰田的七种浪费1.生产过剩的浪费一心想要多销售而大量生产,结果在人员、设备、原材料方面都产生浪费。
在没有需求的时候提前生产而产生浪费。
2.不合格产品的浪费在生产过程中出现废品、次品,会在原材料、零部件、返修所需工时数、生产这些不合格产品所消耗的资源方面产生浪费。
3.待工的浪费在进行机械加工时,机器发生故障不能正常作业,或因缺乏零部件而停工等活等,在这样的状态下所产生的浪费都是停工等活的浪费。
4.动作上的浪费不产生附加价值的动作、不合理的操作、效率不高的姿势和动作都是浪费。
5.搬运的浪费除去准时化生产所必需的搬运,其他任何搬运都是一种浪费。
比如在不同仓库间移动、转运、长距离运输、运输次数过多等。
6.加工本身的浪费把与工程的进展状况和产品质量没有任何关系的加工当做是必要的加工而进行操作,此种状况下所产生的浪费。
7.库存的浪费因为原材料、零部件、各道工序的半成品过多而产生的浪费。
这些东西过度积压还会引起库存管理费用的增加。
消除七种浪费的步骤步骤①:在需要的时候适时生产需要的产品可以排除生产过剩的浪费,这需要具备严格管理的思想。
步骤②:如果经常产生不合格产品,抑制生产过剩是很困难的。
我们要消除不合格产品,消除制造不合格产品的浪费。
步骤③:对于停工等活,只要明白其要点就很容易改善。
消除停工等活的浪费,有效利用人力资源。
步骤④~⑥可以根据消除浪费的着眼点从可以实施的部分开始实施。
步骤④:对于动作的浪费,如果减少工时数(人数×时间)将会对消除浪费产生很大影响。
但是,即使是进行动作分析,清除了一些细小的浪费,也会被其他的问题所掩盖,所以必须注意。
步骤⑤:要消除搬运的浪费,就要在搬运距离和搬运次数等方面加以改进。
步骤⑥:对于加工过程中本身的浪费,要认识到不产生附加价值的一切东西都是浪费。
七大浪费及改善八大步骤
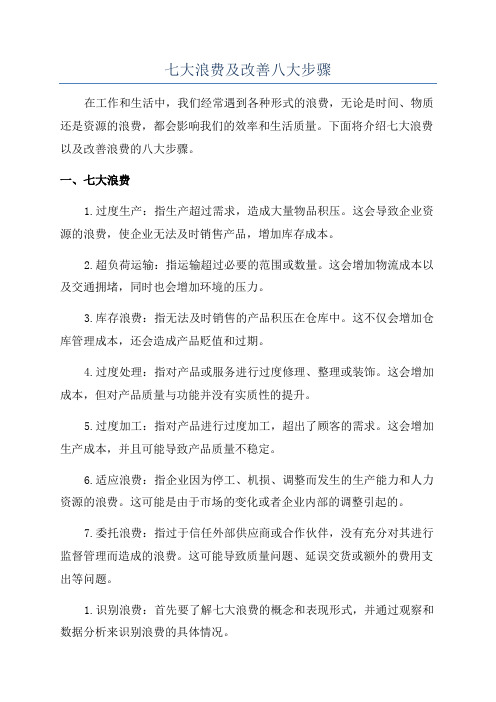
七大浪费及改善八大步骤在工作和生活中,我们经常遇到各种形式的浪费,无论是时间、物质还是资源的浪费,都会影响我们的效率和生活质量。
下面将介绍七大浪费以及改善浪费的八大步骤。
一、七大浪费1.过度生产:指生产超过需求,造成大量物品积压。
这会导致企业资源的浪费,使企业无法及时销售产品,增加库存成本。
2.超负荷运输:指运输超过必要的范围或数量。
这会增加物流成本以及交通拥堵,同时也会增加环境的压力。
3.库存浪费:指无法及时销售的产品积压在仓库中。
这不仅会增加仓库管理成本,还会造成产品贬值和过期。
4.过度处理:指对产品或服务进行过度修理、整理或装饰。
这会增加成本,但对产品质量与功能并没有实质性的提升。
5.过度加工:指对产品进行过度加工,超出了顾客的需求。
这会增加生产成本,并且可能导致产品质量不稳定。
6.适应浪费:指企业因为停工、机损、调整而发生的生产能力和人力资源的浪费。
这可能是由于市场的变化或者企业内部的调整引起的。
7.委托浪费:指过于信任外部供应商或合作伙伴,没有充分对其进行监督管理而造成的浪费。
这可能导致质量问题、延误交货或额外的费用支出等问题。
1.识别浪费:首先要了解七大浪费的概念和表现形式,并通过观察和数据分析来识别浪费的具体情况。
2.制定改善目标:根据识别出的浪费情况,制定明确的改善目标,包括减少过剩生产、降低物流成本、控制库存等方面。
3.分析原因:深入分析每个浪费现象背后的原因,找出造成浪费的根本问题。
4.寻找解决方案:根据分析结果,寻找符合实际情况的解决方案。
可以进行团队讨论和跨部门合作,以找到最佳的解决方案。
5.实施改善措施:在制定改善方案的基础上,通过有效的实施措施来减少浪费。
这涉及到管理的改进、流程的调整、员工的培训等多个方面。
6.持续改进:改善工作不是一次性的,而是需要持续不断的努力。
建立一个持续改进的机制,定期评估改善效果并进行调整。
7.培训与教育:通过培训和教育,提高员工对浪费的认识和改善意识。
精益生产之七大浪费
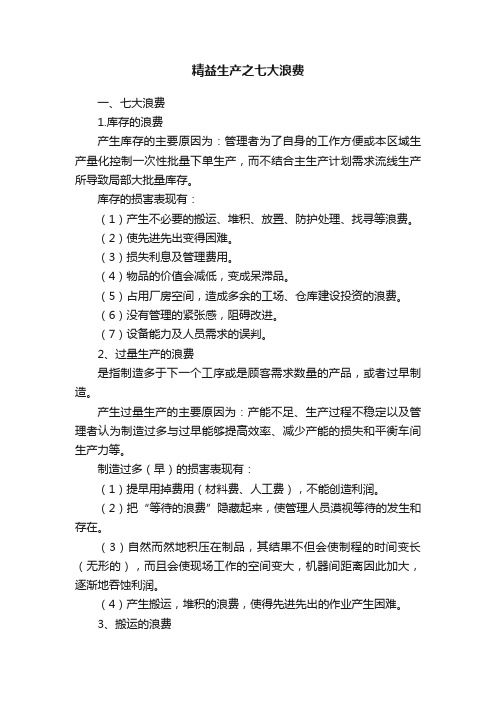
精益生产之七大浪费一、七大浪费1.库存的浪费产生库存的主要原因为:管理者为了自身的工作方便或本区域生产量化控制一次性批量下单生产,而不结合主生产计划需求流线生产所导致局部大批量库存。
库存的损害表现有:(1)产生不必要的搬运、堆积、放置、防护处理、找寻等浪费。
(2)使先进先出变得困难。
(3)损失利息及管理费用。
(4)物品的价值会减低,变成呆滞品。
(5)占用厂房空间,造成多余的工场、仓库建设投资的浪费。
(6)没有管理的紧张感,阻碍改进。
(7)设备能力及人员需求的误判。
2、过量生产的浪费是指制造多于下一个工序或是顾客需求数量的产品,或者过早制造。
产生过量生产的主要原因为:产能不足、生产过程不稳定以及管理者认为制造过多与过早能够提高效率、减少产能的损失和平衡车间生产力等。
制造过多(早)的损害表现有:(1)提早用掉费用(材料费、人工费),不能创造利润。
(2)把“等待的浪费”隐藏起来,使管理人员漠视等待的发生和存在。
(3)自然而然地积压在制品,其结果不但会使制程的时间变长(无形的),而且会使现场工作的空间变大,机器间距离因此加大,逐渐地吞蚀利润。
(4)产生搬运,堆积的浪费,使得先进先出的作业产生困难。
3、搬运的浪费不必要的搬运零件和产品,例如两个连续的生产工序,将产品在完成一个工序后,先运到仓库,然后再运到下一个工序。
较理想的情况是让两个工序的位置相邻,以便使产品能够从一个工序立即转到下一个工序。
产生搬运的主要原因为:车间布置采用批量生产,依工作站为区别的集中的水平式布置(也就是分工艺流程批量生产),无连续流生产的观念。
4、等待的浪费在生产过程中,操作员或者设备空闲。
产生等待的主要原因为:作业不平衡,安排作业不当、待料、品质不良等。
5、多余动作的浪费操作员所作的没有增值的动作,例如找零件,找工具、文件等。
产生多余动作的主要原因为:生产场地规划不好,生产模式设计不周全,生产动作不规范统一。
6、缺陷的浪费不良品和废品。
七大浪费与改善对策
七大浪费与改善对策浪费是在资源利用过程中产生的不必要的浪费或损失。
在社会发展的过程中,浪费问题成为越来越突出的挑战。
以下是七大浪费及其改善对策。
1.物质浪费:物质浪费是指在生产、加工、运输和消费过程中,由于不合理的生产方式和自我约束不足而产生的资源浪费。
改善对策包括:-加强生产计划和管理,合理规划生产量,避免生产过剩。
-推广可持续发展的生产方式,提高资源利用效率。
-加强生产过程监控,减少废弃物的产生。
-发展循环经济模式,推广物品再利用和回收利用。
2.能源浪费:能源浪费是指在能源生产、传输、储存和利用过程中浪费能源资源的现象。
改善对策包括:-推广能源高效利用技术和设备,降低能源消耗。
-加强能源行业监管,提高能源利用效率,避免能源浪费。
-鼓励使用清洁能源,减少对化石能源的依赖。
-提高能源意识,倡导低碳生活方式。
3.时间浪费:时间浪费是指在日常生活和工作中,由于不合理的时间安排和自我管理不善而导致的时间浪费。
改善对策包括:-制定合理的时间计划,合理安排工作和休息时间。
-提高时间管理能力,学会设定优先级,避免优先级低的任务占用过多时间。
-减少社交媒体和电子设备的使用时间,避免分散注意力和产生干扰。
-培养良好的时间观念,珍惜时间,合理利用每一分每一秒。
4.知识浪费:知识浪费是指在学习、研究和传播知识的过程中,由于不进行有效利用和传承而产生的知识资源浪费。
改善对策包括:-建立知识共享平台,促进知识的交流和共享。
-加强知识产权保护,保护创新成果。
-发展教育和培训机构,提高人才培养质量。
-培养创新意识和实践能力,将知识转化为创造性的成果。
5.人力资源浪费:人力资源浪费是指在人力资源管理和运用过程中,由于不合理的组织结构和人员配置而造成的人力资源的浪费。
改善对策包括:-优化组织结构,合理配置人力资源。
-实行科学的人才选拔机制,提高人员素质和能力。
-加强人力资源培训和发展,提高人员的工作适应能力和综合素质。
-建立激励机制,激发人力资源的积极性和创造性。
7大浪费的产生原因和消除方法
7大浪费的产生原因和消除方法丰田的7种浪费丰田生产方式认为,不产生附加价值的一切作业都是浪费,它把浪费分为以下7种。
1、生产过剩的浪费:一心想要多销售而大量生产,结果在人员、设备、原材料方面都产生浪费。
在没有需求的时候提前生产而产生浪费。
2、不合格产品的浪费:在生产过程中出现废品、次品,会在原材料、零部件、返修所需工时数、生产这些不合格产品所消耗的资源方面产生浪费。
3、待工的浪费:在进行机械加工时,机器发生故障不能正常作业,或因缺乏零部件而停工等活等,在这样的状态下所产生的浪费都是停工等活的浪费。
4、动作上的浪费:不产生附加价值的动作、不合理的操作、效率不高的姿势和动作都是浪费。
5、搬运的浪费:除去准时化生产所必需的搬运,其他任何搬运都是一种浪费。
比如在不同仓库间移动、转运、长距离运输、运输次数过多等。
6、加工本身的浪费:把与工程的进展状况和产品质量没有任何关系的加工当做是必要的加工而进行操作,此种状况下所产生的浪费。
7、库存的浪费:因为原材料、零部件、各道工序的半成品过多而产生的浪费。
这些东西过度积压还会引起库存管理费用的增加。
消除7种浪费的步骤从哪里开始消除这7种浪费为好呢?在像丰田一样积累了50年以上的改善经验和没有这些改善经验的企业中,在生产体制上存在着很大差异。
在此让我们以问题比较多的企业为对象,来思考一下处理7种浪费的基本顺序。
步骤①:在需要的时候适时生产需要的产品可以排除生产过剩的浪费,这需要具备严格管理的思想。
步骤②:如果经常产生不合格产品,抑制生产过剩是很困难的。
我们要消除不合格产品,消除制造不合格产品的浪费。
步骤③:对于停工等活,只要明白其要点就很容易改善。
消除停工等活的浪费,有效利用人力资源。
步骤④~⑥可以根据消除浪费的着眼点从可以实施的部分开始实施。
步骤④:对于动作的浪费,如果减少工时数(人数×时间)将会对消除浪费产生很大影响。
但是,即使是进行动作分析,清除了一些细小的浪费,也会被其他的问题所掩盖,所以必须注意。
管理工作中的七种浪费
管理工作中的七种浪费在管理工作中,浪费是一个常见但十分不可忽视的问题。
浪费不仅会影响工作效率,还会浪费时间和资源,对组织的整体运营产生负面影响。
本文将介绍管理工作中的七种常见浪费,并提供解决方案以提高工作效率。
一、等待浪费等待是管理工作中最常见的浪费之一。
员工经常在等待他人提供必要信息、审批文件或决策。
这种等待会导致工作停滞、项目延迟和效率低下。
解决方案:- 沟通:及时与相关人员沟通,明确工作需求和时间要求。
- 自我管理:提前预估可能遇到的等待情况,提前准备工作以最大程度地减少等待时间。
二、错误与修复浪费错误与修复浪费指在工作中因为疏忽或不正确的操作而导致出现错误,并需要额外的时间和资源来修复。
这种浪费会导致工作进度延迟和效率下降。
解决方案:- 审查工作:在提交工作前仔细审查,确保没有明显的错误。
- 持续学习:通过学习和培训提高专业素养,减少因为不正确的操作而产生的错误。
三、不必要的运动浪费不必要的运动浪费是指在工作中花费过多的时间在不必要的行动和移动上,而不是专注于核心任务。
这种浪费会造成时间和体力的浪费,并可能导致其他工作的延迟。
解决方案:- 计划并组织工作:合理安排工作流程,避免来回奔波或过多的行动。
- 利用科技:使用现代化的办公设备和工具,例如视频会议和远程办公,减少不必要的跑动。
四、过度处理浪费过度处理浪费指在工作中花费过多的时间、精力和资源来完成一个任务,超过了任务本身所需的程度。
这种浪费会导致资源低效利用和工作过程的不必要复杂化。
解决方案:- 设定优先级:根据任务的重要性和紧急性确定工作的优先级,合理分配资源。
- 简化流程:评估工作流程,简化步骤和流程,以提高效率。
五、库存浪费库存浪费是指过量存储和积压的物品或材料,这些库存会占用空间和资源,增加了管理成本。
库存浪费还可能导致过期或损坏的物品,造成更大的损失。
解决方案:- 精确预测需求:通过分析数据和趋势预测需求,避免过量的库存。
- 定期清理:定期检查和清理库存,保持库存的合理水平。
七大浪费的改善与对策
七大浪费的改善与对策1.生产浪费生产浪费指生产过程中的一些非必要的使用和消耗。
这包括工人的浪费时间、废弃物和废弃物处理成本、以及不必要的设备维护和更新。
为了减少这种浪费,应采取以下措施:-优化生产流程,减少非必要的等待时间和操作。
-设立回收和再生材料处理系统,以减少废品和废水的处理成本。
-定期进行设备维护和更新,以提高效率和减少停机时间。
2.运输浪费运输浪费包括多余运输、不必要的库存、过度包装和物流瓶颈。
以下是减少运输浪费的方法:-采用合理的物流系统,减少运输次数。
-采用精确和及时的库存管理,避免过度库存。
-减少包装物和使用可再利用材料。
3.智力浪费智力浪费是指在设计、开发和管理过程中的浪费。
这包括低效的流程、资源浪费和不合理的管理决策。
以下是减少智力浪费的方法:-采用有效的项目管理和流程优化,以提高效率。
-对资源进行严格的监控和规划。
-制定有效的管理决策。
4.人员浪费人员浪费包括低效的时间管理、人员缺乏培训和绩效评估、以及过多的会议和文档。
以下是减少人员浪费的方法:-建立有效的绩效管理和员工培训计划。
-采用自动化和数字化工具,减少文档和会议的数量。
-优化日常规划和时间管理。
5.能源浪费能源浪费包括不必要的照明和加热,以及能源资源的不合理使用。
以下是减少能源浪费的方法:-优化建筑设计和能源系统,减少不必要的照明和加热。
-采用节能技术和设备。
-定期进行设备维护和更新,以提高效率。
6.物料浪费物料浪费包括不必要的消耗、过度库存和不必要的废弃物。
以下是减少物料浪费的方法:-采用有效的物料管理和库存规划。
-控制消耗的数量,减少浪费和废弃物。
-实行回收和再生计划。
7.外部浪费外部浪费是指生态和社会影响的损失,包括污染、环境破坏和资源不合理使用。
以下是减少外部浪费的方法:-采用可持续和环保技术和方法。
-实现严格的环境管理和监控。
-加强社会责任感,推动可持续发展。
- 1、下载文档前请自行甄别文档内容的完整性,平台不提供额外的编辑、内容补充、找答案等附加服务。
- 2、"仅部分预览"的文档,不可在线预览部分如存在完整性等问题,可反馈申请退款(可完整预览的文档不适用该条件!)。
- 3、如文档侵犯您的权益,请联系客服反馈,我们会尽快为您处理(人工客服工作时间:9:00-18:30)。
① 浪费 1:过量生产的浪费
问题点
◇ 过量、先行生产 ◇ 库存 · 在制品增加 ◇ 材料 · 部品的先行使用 ◇ 资金周转率低下 ◇ 计划的柔性低下 ◇ 不良发生的所在
原因
○ 过剩人员 / 设备 ○ 大批量生产 ○ 高性能的大型设备 ○ 只能不断生产的结构
解决方案
★ 少人化 ★ 流1个 ★ 缩短准备交替时间 ★ 生产的均衡化 ★ 彻底的看板使用
特征
ⓐ 把搬运也当作作业的认识 ⓑ 一时的积载
ⓒ 保管作业 ⓓ 搬移堆积 ⓔ 非合理的 Layout
ⓕ 作业标准的阻碍(由作业者搬运)
ⓖ 依次搬运太多(数量确认) 非合理的Layout
行动为本的超一流经营公司
3 / 152
K&CPEC 韩中产业教育中心
Korea & China Productivity Education Center
问题点
◇ 发生不必要的工程
原因
○ 对工程顺序的分析不足
解决方案
★ 工程设计的合理化
◇ 发生不必要的作业 ◇ 人员、作业工时的增加
◇ 作业性的低下 ◇ 不良的增加
○ 对工程内容的分析不足 ○ 使用不合理的治具
○ 标准化ห้องสมุดไป่ตู้不完备 ○ 对材料的未检讨
★ 作业内容的再评价/修正 ★ 治具改善和自动化
★ 标准作业 ★ VE 推进
⑤ 浪费 5:等待的浪费
问题点
◇ 人、作业、时间、
原因
○ 工程异常
解决方案
★ 生产的均衡化
○ 不合理的设备布置 机械的浪费
◇ 在制品及库存增加 ○ 前工程发生问题 ○ 能力不均衡 ○ 大批量生产
★ U字型的布置
★ 自动化 ★ Cycle内的准备交替 ★ Fool-Proof
特征
ⓐ 机械在加工时观望 ⓑ 机械在转动,因此不能伸手 (作业编成) ⓒ 从前工程的材料或半成品的缺品 ⓓ 从前工程没有流过来
1. TPS中的7大浪费
过量生产的浪费
不良/再作业的浪费
5 %
附加值
搬运的浪费
动作的浪费
浪费 / 非附加值
库存的浪费
等待的浪费
加工其本身的浪费
最坏的浪费就是成为所有浪费根源的过量生产的浪费!
行动为本的超一流经营公司
1 / 152
K&CPEC 韩中产业教育中心
Korea & China Productivity Education Center
③ 浪费 3:库存的浪费
问题点
◇ 阻碍流动 ◇ 不良发生 ◇ 资金周转率低下 ◇ 生产周期增加 ◇ 管理资金增加(仓库/人员) ◇ 计划的柔性低下
原因
○ 过剩人员 / 设备 ○ 大批量生产 ○ 先行生产、生产计划变更
解决方案
★ 对于库存的意识革命 ★ U字设备布置 ★ 均衡化生产 ★ 流水生产(流1个) ★ 看板的有效利用 ★ 缩短准备交替
K&CPEC 韩中产业教育中心
Korea & China Productivity Education Center
解决方案
★ 自动化、标准作业化 ★ Fool-Proof的设置 ★ 在工程中确保品质 ★ 品质保证制度的确立 ★ 全数检查
特征
ⓐ 出现不良也放任 ⓑ 出现不良也不树立对策 ⓒ 工程的编成无法保证品质 ⓓ 在标准作业中没有把检查编制进去 ⓔ 作业者的意识和训练不充分
行动为本的超一流经营公司
8 / 152
特征
ⓐ 机械加工的过程中用手支撑 作业物品
ⓑ 主作业之前的准备作业 (在里面打孔的作业) ⓒ 如果治具不完备或状态不好,
那么加工时需要额外的时间
ⓓ 已发生设计变更,但现场依然以 以前的做法进行
行动为本的超一流经营公司
5 / 152
K&CPEC 韩中产业教育中心
Korea & China Productivity Education Center
ⓔ 自己工程发生问题
ⓕ 准备流到下一个工程的等待作业 数量多
行动为本的超一流经营公司
6 / 152
K&CPEC 韩中产业教育中心
Korea & China Productivity Education Center
⑥ 浪费 6:动作的浪费
问题点
◇ 人员 · 工时的增加 ◇ 功能的隐蔽 ◇ 作业的不稳定 ◇ 不必要的动作
○ 无计划的生产
○ 不合理的 Layout
特征
ⓐ 把库存视为当然的意识 ⓑ 工程发生异常 ⓒ 看板过多的情况 ⓓ 以设备为中心的工程编制
行动为本的超一流经营公司
4 / 152
K&CPEC 韩中产业教育中心
Korea & China Productivity Education Center
④ 浪费 4:加工其本身的浪费
7 / 152
K&CPEC 韩中产业教育中心
Korea & China Productivity Education Center
⑦ 浪费 7:不良的浪费
问题点
◇ 材料费增加 ◇ 生产性低下 ◇ 检查人员和工程的增加 ◇ 不良品和投诉的增加
原因
○ 工程中检查不足 ○ 检查方法/基准等不完备 ○ 过剩的品质 ○ 标准作业的遗漏
② 浪费 2:搬运的浪费
问题点
◇ 非效率的空间利用 ◇ 生产性的低下 ◇ 搬运工时的增加 ◇ 搬运设备的增设 ◇ 产品发生瑕疵和磕碰
原因
○ 不合理的 Layout ○ 单技能工 ○ 坐式作业 ○ 无计划的生产 ○ 搬运的活性低下
解决方案
★ U字设备布置 ★ 流水生产 ★ 多技能工化 ★ 立式作业 ★ 利用SUIT方式
原因
○ 工程间的移动时间过长 ○ 作业者根性的蔓延 ○ 不合理的 Layout ○ 教育 · 训练的不足
解决方案
★ 流水生产 ★ U字型设备布置 ★ 标准作业 ★ 动作经济的原则
特征
ⓐ 只用一只手作业 ⓑ 步行距离长 ⓒ 必要的治具和工具不在身边 ⓓ 拆解 · 安装需要时间 ⓔ 有反复的作业
行动为本的超一流经营公司
特征
ⓐ 在作业等待时间里进行下一个作业 ⓑ 作业或机械(设备)有空闲时间 ⓒ 只追求每小时的生产性
ⓓ 高价的机械,只考虑
时间开动率 → 折旧 ⓔ 如果在能够生产时不进行生产, 那么会感到不安
行动为本的超一流经营公司
2 / 152
K&CPEC 韩中产业教育中心
Korea & China Productivity Education Center