空分主冷事故
主冷发生爆炸的事故较多是什么原因,应采取什么防患措施

专业的论文在线写作平台
主冷发生爆炸的事故较多是什么原因,应采取什么防
患措施
空分设备爆炸事故中,以主冷爆炸居多。
产生化学性爆炸的因素是:
1)可燃物质;
2)助燃物质;
3)引爆源。
在主冷中有充分的助燃物质--氧,为碳氢化合物的氧化、燃烧、爆炸提供了必要条件。
爆炸严重的会造成整个设备破坏,甚至人员伤亡;轻微的爆炸在局部位置产生,使氧产品纯度降低,无法维持正常生产。
爆炸都与易燃物质--碳氢化合物在液氧中积聚有关。
引爆源主要有:
1)爆炸性杂质固体微粒相互摩擦或与器壁摩擦;
2)静电放电。
液氧中有少量冰粒、固体二氧化碳时,会产生静电荷。
当二氧化碳的含量为2×10-4~3×10-4时,所产生的静电位可达3000V;
3)气波冲击。
产生摩擦或局部压力升高;
4)存在化学活性特别强的物质(臭氧、氮氧化物等),使爆炸的敏感性增大。
主冷中有害杂质有乙炔、碳氢化合物和固态二氧化碳等。
它们随时都可以随气流进入主冷。
为了安全,预先在净化装置中,例如分子筛吸附器中,其杂质予以清除。
但是对切换式换热器自清除流程就做不到这一点。
为此,在流程设计和操作中采取以下。
浅谈空分主冷凝蒸发器爆炸机理及防范措施

浅谈空分主冷凝蒸发器爆炸机理及防范措施摘要:空分装置是以空气为原料经过压缩、低温膨胀做功和塔内低温精馏,从而获得所需要的各气体和低温液体产品,是冶金、化工等行业的核心设备之一。
近年来,因空分设备制造缺陷和操作管理不善等原因,已发生多起空分设备爆炸事故,特别是空分主冷凝蒸发器中烃类物质超标引起的爆炸是近年来事故频发的主要原因。
本文以空分装置主冷凝蒸发器发器为例,对空分装置爆炸原因及防范措施加以分析。
关键词:空分设备、主冷凝蒸发器、爆炸。
一、空分装置主冷凝蒸发器爆炸的机理空分主冷凝蒸发器的爆炸种类可分为物理性爆炸和化学性爆炸。
从爆炸的实例分析来看,化学性爆炸占主要部分。
众所周知形成化学性爆炸的必要条件是:可燃物、助燃物和引爆源。
在空分设备主冷凝蒸发器器中,引爆源主要有:(1)爆炸性杂质固体微粒相互摩擦或与器壁摩擦发热;(2)静电放电。
当液氧中含有少量冰粒、固体二氧化碳时,会产生静电荷。
有关数据显示:二氧化碳的含量提高到200-300ppm时,所产生的静电位可达到3000V;(3)气波冲击、流体冲击或汽蚀现象引起的压力脉冲,造成局部压力高而使温度升高;(4)化学活性特别强的物质(臭氧、氮氧化合物等)存在,使液氧中可燃物质混合物的爆炸敏感性增大。
助燃物为气氧和液氧;可燃物主要是碳氢化合物、乙炔或油分等高烃类杂质。
乙炔为不饱,其分子结构很不稳定,是极易燃烧爆炸的物质,乙炔在塔中,以分子形式溶解在液空中,但溶解度是一定的,当超过溶解度时,乙炔则以固体微颗粒形式出现。
乙炔在液空中的溶解度约为20ppm;在液氧中(-180℃左右)约为6.5ppm。
乙炔在被氧中的溶解度较小,过剩的乙炔以固体微颗粒悬浮在液氧中或附于管壁与通道内壁上。
在冷凝蒸发器中,液氧的平均温度为-180℃,气中能带走的乙炔量不到总量的5%,所以随着液氧的不断蒸发,液氧中的乙炔越聚越多,当超过其溶解度时就以固体形式析出,固体乙炔具有极不稳定的化学特性,当形成“死端沸腾”、“干蒸发”时就形成了爆炸的内因,一旦受到来自机械、物理、化学方面的冲击,即刻诱发爆炸。
浅谈空分装置主冷爆炸的原因及其预防措施

浅谈空分装置主冷爆炸的原因及其预防措施作者:刘巍来源:《硅谷》2009年第21期[摘要]介绍空分装置主冷爆炸对生产的影响,乙炔等危险杂质的来源及其爆炸危险性,采取多种净化方法相结合的方式清除乙炔等危险杂质,定期化验液氧中的碳氢化合物含量,并排放主冷中的液氧。
[关键词]乙炔主冷爆炸清除中图分类号:TU2文献标识码:A文章编号:1671-7597(2009)1110115-01近年来,随着我国钢铁工业的发展,钢产量不断提高,对生产过程中的氧气需求量迅速增加。
各钢铁企业的空分装置也不断增加,其安全运行对企业的安全生产和产量有着重要影响。
一、空分装置主冷爆炸的影响空分装置主冷爆炸按其产生的后果严重程度可分为严重爆炸和微爆。
主冷发生严重爆炸可使空分装置的保冷箱被炸开,整体发生倾斜倒塌,砸向厂房方向还可造成厂房损坏和厂房内人员的伤亡。
如,江西某钢铁公司的空分设备大爆炸,空分塔倾倒,造成厂房破坏。
主冷内部微爆虽不产生严重的后果,但其微爆可破坏空分装置的工况平衡,造成氧气纯度下降,氧气产量下降,影响生产的正常运行。
二、危险杂质来源及其爆炸危险性(一)碳氢化合物来源。
引起主冷爆炸的主要原因是危险杂质乙炔及其它碳氢化合物在主冷中浓缩及析出所致。
乙炔等危险杂质主要是随原料空气而带入。
此外,如果空气压缩过程中气体带油而裂解也会增加原料空气中的乙炔及碳氢化合物的含量。
大气中碳氢化合物的含量见表1。
这些微量的碳氢化合物随原料空气进入空分装置,在主换热器能够析出的有丁烯、丁烷。
其它将进入下塔溶解液空中。
(二)爆炸危险性。
随原料空气进入主冷中的乙炔等危险杂质尽管它们的含量甚微,但由于不饱和碳氢化合物可分解,产生大量的热及氢气而产生危险;或者因与氧发生氧化反应,放热且反应速度极快而造成爆炸。
碳氢化合物的爆炸下限在一定程度上可以反映其化学稳定性及危险性。
通常,碳原子数相等的碳氢化合物,随未饱和度增加相对危险增加,即炔>烯>烷;不同碳原子数的碳氢化合物相对危险性随碳原子数增多而增大。
空分车间事故分析
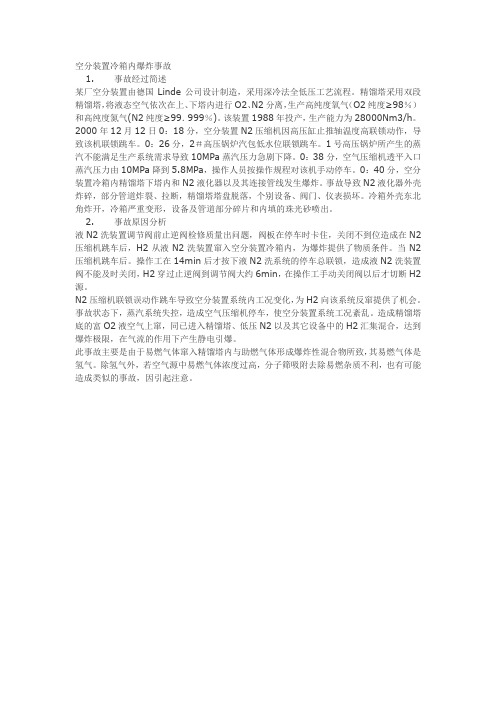
空分装置冷箱内爆炸事故1. 事故经过简述某厂空分装置由德国Linde公司设计制造,采用深冷法全低压工艺流程。
精馏塔采用双段精馏塔,将液态空气依次在上、下塔内进行O2、N2分离,生产高纯度氧气(O2纯度≥98%)和高纯度氮气(N2纯度≥99.999%)。
该装置1988年投产,生产能力为28000Nm3/h。
2000年12月12日0:18分,空分装置N2压缩机因高压缸止推轴温度高联锁动作,导致该机联锁跳车。
0:26分,2#高压锅炉汽包低水位联锁跳车。
1号高压锅炉所产生的蒸汽不能满足生产系统需求导致10MPa蒸汽压力急剧下降。
0:38分,空气压缩机透平入口蒸汽压力由10MPa降到5.8MPa,操作人员按操作规程对该机手动停车。
0:40分,空分装置冷箱内精馏塔下塔内和N2液化器以及其连接管线发生爆炸。
事故导致N2液化器外壳炸碎,部分管道炸裂、拉断,精馏塔塔盘脱落,个别设备、阀门、仪表损坏。
冷箱外壳东北角炸开,冷箱严重变形,设备及管道部分碎片和内填的珠光砂喷出。
2. 事故原因分析液N2洗装置调节阀前止逆阀检修质量出问题,阀板在停车时卡住,关闭不到位造成在N2压缩机跳车后,H2从液N2洗装置窜入空分装置冷箱内,为爆炸提供了物质条件。
当N2压缩机跳车后。
操作工在14min后才按下液N2洗系统的停车总联锁,造成液N2洗装置阀不能及时关闭,H2穿过止逆阀到调节阀大约6min,在操作工手动关闭阀以后才切断H2源。
N2压缩机联锁误动作跳车导致空分装置系统内工况变化,为H2向该系统反窜提供了机会。
事故状态下,蒸汽系统失控,造成空气压缩机停车,使空分装置系统工况紊乱。
造成精馏塔底的富O2液空气上窜,同已进入精馏塔、低压N2以及其它设备中的H2汇集混合,达到爆炸极限,在气流的作用下产生静电引爆。
此事故主要是由于易燃气体窜入精馏塔内与助燃气体形成爆炸性混合物所致,其易燃气体是氢气。
除氢气外,若空气源中易燃气体浓度过高,分子筛吸附去除易燃杂质不利,也有可能造成类似的事故,因引起注意。
空分事故案例分析 (1)
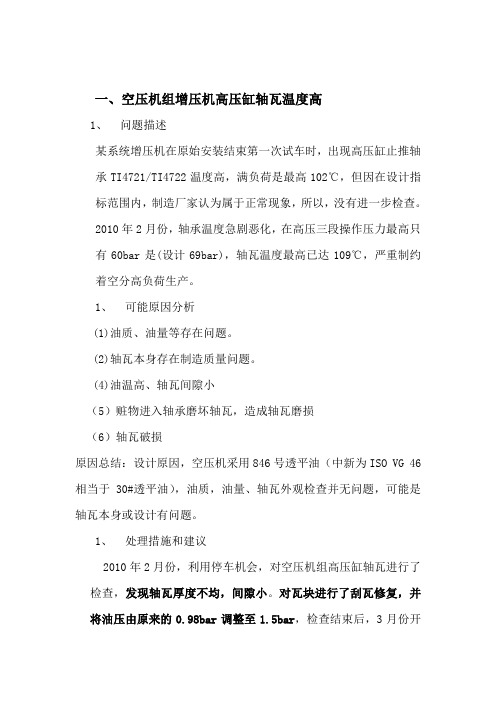
一、空压机组增压机高压缸轴瓦温度高1、问题描述某系统增压机在原始安装结束第一次试车时,出现高压缸止推轴承TI4721/TI4722温度高,满负荷是最高102℃,但因在设计指标范围内,制造厂家认为属于正常现象,所以,没有进一步检查。
2010年2月份,轴承温度急剧恶化,在高压三段操作压力最高只有60bar是(设计69bar),轴瓦温度最高已达109℃,严重制约着空分高负荷生产。
1、可能原因分析(1)油质、油量等存在问题。
(2)轴瓦本身存在制造质量问题。
(4)油温高、轴瓦间隙小(5)赃物进入轴承磨坏轴瓦,造成轴瓦磨损(6)轴瓦破损原因总结:设计原因,空压机采用846号透平油(中新为ISO VG 46相当于30#透平油),油质,油量、轴瓦外观检查并无问题,可能是轴瓦本身或设计有问题。
1、处理措施和建议2010年2月份,利用停车机会,对空压机组高压缸轴瓦进行了检查,发现轴瓦厚度不均,间隙小。
对瓦块进行了刮瓦修复,并将油压由原来的0.98bar调整至1.5bar,检查结束后,3月份开车,在90%生产负荷下,轴瓦温度最高76℃,取得了不错的效果。
沈鼓制造的压缩机普通存在轴瓦温度有一个偏高,建议对机组油质,油压,轴瓦进行检查,若以上没有问题,联系厂家解决。
二、分子筛蒸汽加热器泄漏1、问题描述2009年1月31号上午,某系统操作人员发现在分子筛蒸汽加热器E4201的底部水侧管子与壳体的间隙有水流出,为进一步确认,将蒸汽加热器底部保温全部拆除,打开蒸汽加热器底部壳侧盲法兰处有大量空气排出,而且还随着所加工空气的流量变化而变化,由此判断,蒸汽加热器管侧有漏点。
2、可能原因分析(1)分子筛蒸汽系统超压,超出材料承受范围。
(2)运行中,蒸汽加热器管壳侧温差过大,产生应力。
(3)蒸汽加热器后汽水分离器无液位,产生水击。
(4)冬季停车期间,防冻不彻底,冻坏设备。
最终原因:在装置运行期间,严格控制蒸汽加热器的操作压力和温度,分离器液位控制在250mm以上,没有发生过水击现象。
发生空分设备事故原因分析与管控措施
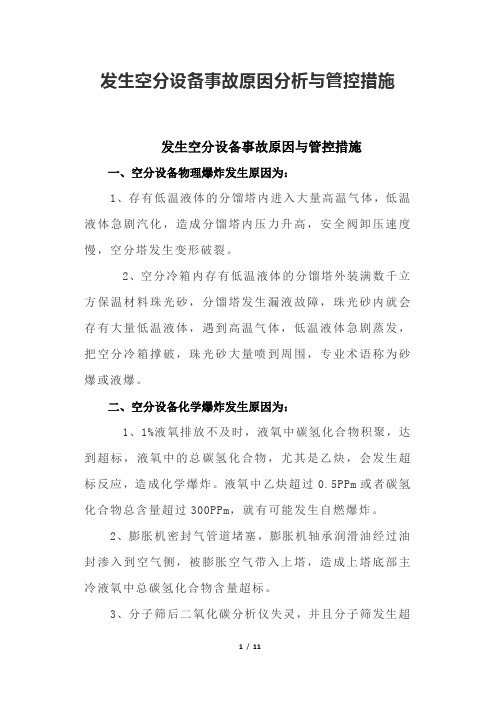
发生空分设备事故原因分析与管控措施发生空分设备事故原因与管控措施一、空分设备物理爆炸发生原因为:1、存有低温液体的分馏塔内进入大量高温气体,低温液体急剧汽化,造成分馏塔内压力升高,安全阀卸压速度慢,空分塔发生变形破裂。
2、空分冷箱内存有低温液体的分馏塔外装满数千立方保温材料珠光砂,分馏塔发生漏液故障,珠光砂内就会存有大量低温液体,遇到高温气体,低温液体急剧蒸发,把空分冷箱撑破,珠光砂大量喷到周围,专业术语称为砂爆或液爆。
二、空分设备化学爆炸发生原因为:1、1%液氧排放不及时,液氧中碳氢化合物积聚,达到超标,液氧中的总碳氢化合物,尤其是乙炔,会发生超标反应,造成化学爆炸。
液氧中乙炔超过0.5PPm或者碳氢化合物总含量超过300PPm,就有可能发生自燃爆炸。
2、膨胀机密封气管道堵塞,膨胀机轴承润滑油经过油封渗入到空气侧,被膨胀空气带入上塔,造成上塔底部主冷液氧中总碳氢化合物含量超标。
3、分子筛后二氧化碳分析仪失灵,并且分子筛发生超期使用,超温使用,再生不足,进入游离水,进油中毒等原因,不能完全吸附二氧化碳、总碳氢化合物等,碳氢化合物穿过分子筛进入分馏塔内,造成下塔底部液空和上塔底部主冷液氧总碳氢化合物含量超标。
4、对于自由端轴承在吸风管内的空压机来说,自由端轴承密封气管断开或堵塞,吸风管内产生的负压会把轴承内的、润滑油吸入空气中,造成分子筛中毒,空气中的总碳氢化合物会穿过分子筛,进入分馏塔内,造成下塔底部液空和上塔底部主冷液氧总碳氢化合物含量超标。
5、由于化工厂或化工车辆放散口在空压机吸风口附近放散杂环烃1#、杂环烃2#、粗酚、轻粗苯、硫磺、硫酸铵等化产气体,空气含有大量的总碳氢化合物。
空压机吸入总碳氢化合物含量高的空气,会造成总碳氢化合物会穿过分子筛,进入分馏塔内,造成下塔底部液空和上塔底部主冷液氧总碳氢化合物含量超标。
三、针对以上各种危险因素,制氧应制定相应的管控措施:1、操作空分塔进塔阀门必须缓慢,热空气进塔速度根据压力变化逐步调整。
爆炸事故案例

哈气化1 万m3 空分主冷爆炸事故的分析一、事故经过1996 年 7 月 18 日,哈尔滨气化厂空分分厂当班人员听到一声闷响,接着主冷凝器(以下简称“主冷”)液位全无、下塔液位上升,氧、氮不合格,现场有少量珠光砂从冷箱里泄了出来。
断定为主冷爆炸。
后经主冷生产厂家切开主冷发现上塔塔板全部变形,主冷四个单元中有一个单元局部烧熔,爆炸切口有碳黑,另一个单元发生轻微爆炸,下塔有一块塔板变形。
二、有关情况该套空分设备1993年投入生产,产量和纯度都达到要求。
该套设备是采用全低压板式换热器净化流程,没液空、液氧吸附器。
爆炸前工艺指标未发现异常,主冷液位控制在2500~2900mm,主冷处于全浸操作,当时气相色谱分析仪带病运行,每周分析1次。
造气、净化、甲醇三个分厂距离空分较近,化验分析碳氢化合物超标 3 倍多,有乙炔出现。
三、事故分析1.空气污染空气分厂与造气、甲醇、净化分厂较近,这三个分厂不正常排放对空分生产造成了威胁。
主冷液氧中碳氢化合物超标时有发生。
在爆炸前几天风向和气压都对空分生产不利,造成原料空气碳氢化合物含量上升。
2.碳氢化合物在主冷中积累碳氢化合物经过液空吸附器和液氧吸附器吸附后,部分被排除,另一部分在液氧中积聚,使其在液氧中浓度升高。
乙炔在液氧中局部浓缩而析出危险的固体乙炔,吸附器倒换周期长,液氧泵时开时停,导致碳氢化合物不能被及时排出,又未采取大量排液手段,导致超标。
3.操作不当在吸附器操作过程中,不按规程精心操作导致硅胶破碎,致使硅胶粉末进入主冷。
4.液氧中硅胶和二氧化碳颗粒随液体运动产生静电,是乙炔起爆的点火源。
四、教训和建议1.空分设备吸风口应该远离碳氢化合物杂质散发源,加强对空气监测。
2.防止硅胶和二氧化碳进入分馏塔,加强操作管理,缩短吸附器倒换周期,液氧泵 24 小时运行,增大膨胀量集中排放大量液氧。
3.空分设备运行 12 个月,停车全面加温,彻底清除碳氢化合物和油脂。
4.对设备进行及时维护修理,防止带病运行。
空分行业典型事故
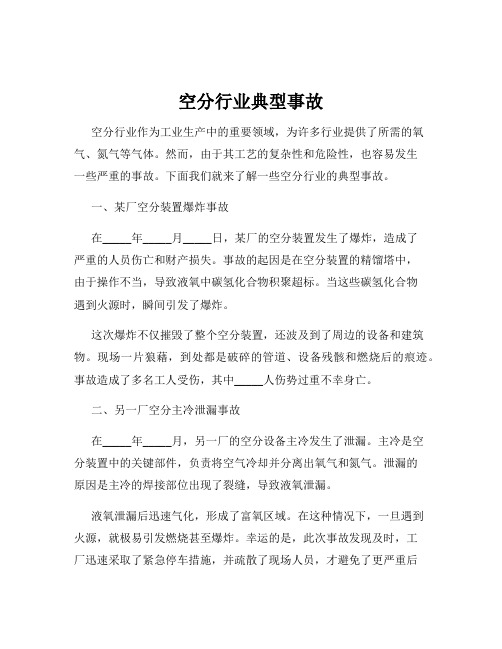
空分行业典型事故空分行业作为工业生产中的重要领域,为许多行业提供了所需的氧气、氮气等气体。
然而,由于其工艺的复杂性和危险性,也容易发生一些严重的事故。
下面我们就来了解一些空分行业的典型事故。
一、某厂空分装置爆炸事故在_____年_____月_____日,某厂的空分装置发生了爆炸,造成了严重的人员伤亡和财产损失。
事故的起因是在空分装置的精馏塔中,由于操作不当,导致液氧中碳氢化合物积聚超标。
当这些碳氢化合物遇到火源时,瞬间引发了爆炸。
这次爆炸不仅摧毁了整个空分装置,还波及到了周边的设备和建筑物。
现场一片狼藉,到处都是破碎的管道、设备残骸和燃烧后的痕迹。
事故造成了多名工人受伤,其中_____人伤势过重不幸身亡。
二、另一厂空分主冷泄漏事故在_____年_____月,另一厂的空分设备主冷发生了泄漏。
主冷是空分装置中的关键部件,负责将空气冷却并分离出氧气和氮气。
泄漏的原因是主冷的焊接部位出现了裂缝,导致液氧泄漏。
液氧泄漏后迅速气化,形成了富氧区域。
在这种情况下,一旦遇到火源,就极易引发燃烧甚至爆炸。
幸运的是,此次事故发现及时,工厂迅速采取了紧急停车措施,并疏散了现场人员,才避免了更严重后果的发生。
但这次泄漏事故仍然给工厂带来了不小的经济损失,同时也影响了正常的生产秩序。
三、某大型空分装置氧压机着火事故在_____年_____月_____日,某大型空分装置的氧压机突然着火。
经调查,事故的原因是氧压机的密封部件失效,导致氧气泄漏。
泄漏的氧气与周围的油污等可燃物接触,引发了火灾。
火灾发生后,现场的工作人员迅速启动了应急预案,使用灭火器和消防水进行灭火。
同时,及时通知了消防部门。
消防人员赶到后,经过一番努力,最终成功扑灭了大火。
但氧压机已经严重损坏,需要进行长时间的维修和更换,给企业的生产造成了较大的影响。
四、空分装置分子筛进水事故在_____年_____月,某厂的空分装置分子筛系统发生了进水事故。
原因是在操作过程中,误将大量的水引入了分子筛吸附器中。
- 1、下载文档前请自行甄别文档内容的完整性,平台不提供额外的编辑、内容补充、找答案等附加服务。
- 2、"仅部分预览"的文档,不可在线预览部分如存在完整性等问题,可反馈申请退款(可完整预览的文档不适用该条件!)。
- 3、如文档侵犯您的权益,请联系客服反馈,我们会尽快为您处理(人工客服工作时间:9:00-18:30)。
空分膨胀机工作原理?空分的一些事故分析及操作注意2009年12月06日:先容10000m3/h空分设备按计划进行检修,在打开底部两个人孔排珠光砂时发生了喷砂事故,造成1人死亡、1人受伤。
阐发了事故发生的原因,并提出了防范办法。
:1事故经过及征象四川威远钢铁有限公司动力厂制氧车间按照川威集团中修计划,在2007年1月24日15∶15召开了10000m3/h空分设备冷箱扒珠光砂的筹办会。
随落伍行了扒砂前的筹办事情:拆掉喷射蒸发器到排液总管之间的管道(便于扒砂);顶部人孔全数大开;15m平台的人孔紧固好并关闭珠1、事故经过1996年7月18日,哈尔滨气化厂空分分厂当班人员听见一声闷响,接着主冷凝器(以下略称"主冷")液位全无、下塔液位上涨,氧、氮不及格,现场有少量珠光砂从冷箱里泄了出来。
断定为主冷爆炸。
后经主冷出产厂家切开主冷发明上塔塔板全数变型,主冷四个单位中有1个单位局部烧熔,爆炸切口有煤黑,另外1个单位发生轻细爆炸,下塔有一块塔板变型。
二、有关情况该套空分设备1993年投入出产,产量和纯度都达到要求。
该套设备是接纳全低压板式换热器净化流程,没液空、液氧吸附器。
爆炸前工艺指标未发明异常,主冷液位控制在2500~2900mm,主冷处于全浸操作,当时气相色谱阐发仪带病运行,每周阐发1次。
造气、净化、甲醇三个分厂距离空分较近,化验阐发碳氢化物超过标准3倍多,有电石气出现。
3、事故阐发1.空气污染空气分厂与造气、甲醇、净化分厂较近,这三个分厂不没事了排放对空分出产造成为了威吓。
主冷液氧中碳氢化物超过标准时有发生。
在爆炸前几天风向和气压都对空分出产不利,造成原料空气碳氢化物含量上涨。
2.碳氢化物在主冷中积累碳氢化物经过液空吸附器和液氧吸附器吸附后,部门被排除,另外一部门在液氧中积聚,使其在液氧中液体浓度升高。
电石气在液氧中局部浓缩而析出危险的固体电石气,吸附器倒换周期长,液氧泵时开时停,导致碳氢化物不能被实时排出,又未采纳大量排液手眼,导致超过标准。
3.操作不当在吸附器操作历程中,不按规程精心操作导致硅胶破碎,致使硅胶粉末步入主冷。
4.液氧中硅胶和二氧化碳颗粒随液体运动孕育发生静电,是电石气起爆的焚烧源。
四、教训和提议1.空分设备吸风口应该阔别碳氢化物杂质散起源,加强对空气监测。
2.防止硅胶和二氧化碳步入分馏塔,加强操作办理,缩短吸附器倒换周期,液氧泵24小时运行,增大膨胀量集中排放大量液氧。
3.空分设备运行1二个月,停车全面加温,彻底断根碳氢化物和油脂。
4.对设备进行实时维护修理,防止带病运行。
5.加强阐发办理,严酷控制碳氢化物不超过标准。
上塔液悬明显的意味是液氧液面颠簸很厉害,并且是没有办法控制的。
液悬开始的一段时间氧液面大幅度地降落后又迅速上涨。
氧气纯度没有办法调解,也是跟着氧液面的颠簸而大幅度的颠簸。
氧液面降落时,氧纯度明显升高;氧液面突然上涨时,氧纯度很快降落。
这类反复的历程按照液悬的差别程度而呈周期性地变化。
小规模设备的上塔孕育发生液悬时,热互换器后的高压空气温度会出现不用人的劳力降落的征象,高压、中压压力也随之降落。
此时,下塔液空纯度没有办法调解至标准,液氮的纯度可以达到标准。
如果想采纳开大液氮节流阀的办法来提高液空纯度,其成果只能使液氮的纯度变坏。
若关小液空节流阀,只能导致液空液面的上涨。
低压加温阀会出现结霜的征象。
大型空分设备液悬时,明显地反应在上塔中部的阻力上。
液氧液面跟着阻力的上涨而降落,上塔压力跟着阻力的上涨而升高。
下塔的压力跟着氧液面的降落而上涨,进塔的空宇量随下塔压力的升高而减少。
氧纯度跟着氧液面的降落而升高,氮纯度跟着氧纯度的升高而减低。
膨胀后的压力随上塔压力的上涨而升高。
此时,打开不用人的劳力阀箱吹除阀(走污氮时)会吹出液体。
当上塔的中部阻力突然降落时,液氧液面激升,上、下塔压力开始降落,进塔空气流量增大,氧纯度降落。
距离一段时间又重复上述征象。
总之,上塔液悬时,上塔的阻力,蓄冷器冷端温度,氧、氮纯度和上、下塔压力显患上极不不变,切换器恢复迟缓。
当下塔孕育发生液悬时,最有使心服力的意味是液氮纯度没有办法调解至标准值,有时候甚或高于液空中含氧量。
采纳关小液氮节流阀来提高液氮纯度的办法是失效的,只能导致中压压力升高,增长下塔压力和液空液面的颠簸幅度。
此时,打开氖氦吹除阀会出现液体,小规模制氧机的中压加温阀会有结霜征象。
液空纯度很不不变,颠簸很大,有时候高于标准;有时候甚或低于空气中的含氧量。
液空液面颠簸也很大。
大型设备的下塔装有阻力计。
当下塔发生液悬时,首先下塔阻力明显地增长,液空液面逐渐降落到零。
当阻力增大到必然的程度时,突然降落,此时液空液面激增。
随即,下塔阻力开始上涨,又重复上述历程。
与此同时,下塔的压力和进塔空气流量颠簸也很大。
下塔液悬时,氧气纯度有可能提高至标准值,但产量加不大。
氮气的纯度始末没有办法提高至标准值,液氧液面和低压压力显患上不不变。
当大型空分塔孕育发生液悬时,除了接纳遏制膨胀机、堵截气源静置的方法消除外,有没有其它不影响没事了出产的办法?2007-12-0318:33答:接纳遏制膨胀机、堵截气源静置的方法消除液悬,必将造成氧压机、氮压机停运,对没事了出产带来损掉。
为此,可接纳适当排放液氮的方法来消除液悬,较为简单行患上通,不影响没事了出产。
如果在排液氮的同时,加大膨胀量则效果更佳。
具体操作方法如下:在将氧气流量关至比没事了时稍小些、其它各阀开度不变的情况下,只要将液氮排放阀适当打开,加大膨胀量后(一台膨胀机的最大膨胀量),从污氮气经过冷器后的温度显示可看到,2~3min就达到没事了值,即-173℃左右。
接着阻力压差开始降落,主冷液面开始上涨。
同时,从氧阐发仪可以看到氧纯度的变化,开始略有降落,10min后就慢慢上涨。
待阻力基本达到没事了值后,逐渐关小液氮排放阀,直至完全关闭。
用这类方法处理液悬,也可能一次不行,还需进行第二次处理的情况。
这首要是需要按照工况恶化的程度决议液氮排放量。
在操作时要注重将进塔空宇量控制不变;调治某项参数时,阀门的开闭要迟缓。
该操作方法的原理是:在进装配空宇量不变不变、氧气流量比没事了值稍小的情况下,排放液氮会使步入下塔的空宇量增长。
可是,增长膨胀量除为了补充排液的冷损外,因为膨胀空气进上塔,现实步入下塔的空宇量反而是减少的。
这样,下塔压力会有所减低,使主冷的传热温差减小,同时热负荷也减少(因入下塔空宇量减少),致使主冷中液氧蒸发量减少,从而使上塔的上涨气速降落,压差减小,液悬不懂的题目患上到处理完成。
临时停车时,液空液面和液氧液面为啥子会上涨?2007-11-2521:43答:在没事了运转时,上涨蒸气穿行小孔时具备必然的速率,能将分馏塔塔板上的液体托住,阻止液体从小孔漏下,而只能沿塔板流动,再路程经过过程溢流斗流至下块塔板。
停车后,因为上涨蒸气间断,塔板上的液体掉去上涨蒸气的托力,便由各块塔板的筛孔顺次流至底部,积存于冷凝蒸发器和液釜中。
是以,临时停车时,液氧、液空液面均会上涨,甚或跨越膨胀空气、氧气引出管口的位置,在再启动时易造成膨胀机带液或切换式换热器冷端带液的事故。
是以,在临时停车时应注重液面位置,须要时可排放掉部门液体。
加工空宇量不足对精馏工况有啥子影响?2007-11-2521:39答:当空宇量减少刻,塔内的上涨蒸宇量及回流液量均减小,但回流比仍可连结不变。
在没事了情况下,它对氧、氮产物纯度影响不大。
按照物料均衡,加工空宇量减小时,氧、氮产量城市相应地减少。
当宇量减小时,蒸气流速减低,塔板上的液量也减少,液层减薄,是以塔板阻力有所减低。
同时,因为主冷热负荷减小,传热面积有敷裕,传热温差也可减小。
这些影响将有帮助于减低上塔和下塔的压力。
当宇量减少过很长时间,可能出现因为气速过小而托不住筛孔上的液体,液体将从筛孔中直接漏下,孕育发生漏液征象。
下漏的液体没有与蒸气充实接触,部门蒸发不充实,氮液体浓度较高。
这将使精馏效果大大降落,影响到产物氧、氮的纯度,严重时甚或没有办法维持没事了出产。
是以,对精馏塔均规定有许可的最低负荷值,这与塔板的结构型式及预设时参数的选择有关。
答:影响氧气产量首要有下面所开列因素:1)加工空宇量不足。
空宇量不足的原因有:①环境温渡太高;②大气压力过低;③空气吸入过淋器被堵塞;④电压过低或电网频率减低,造成转速减低;⑤中间冷却器冷却效果欠好;⑥级间有内走漏;⑦阀门、管道漏气,不用人的劳力阀或切换阀走漏;⑧对分子筛纯化流程来讲,可能是切换蝶阀漏气。
2)氮均等纯渡过低。
原因有:①精馏塔板效率减低;②冷损过大造成膨胀空宇量过大;⑧液氮纯度过低,液氮量太大;④液氮量过小;⑤液空或液氮过冷器走漏;⑧污氮(或馏分)取出量过大;⑦液空、液氮调治阀开度不当,下塔工况未调好。
3)主冷换热不良。
主冷换热面不足,或氮侧有较多不固结气体,影响主冷的传热,使液氧的蒸发量减少。
4)设备阻力增长。
因为塔板、液空吸附器或过冷器堵塞,液空、液氮节流阀开渡过小或被堵塞,将造成下塔压力升高,进塔空宇量减少。
当切换式换热器冻结时,也将造成系统的阻力增长,进塔空宇量不用人的劳力减少。
5)氧气嗓道、器皿存在走漏。