淬火介质的冷却特性曲线究竟说明了什么
1淬火介质冷却曲线的判读和评价
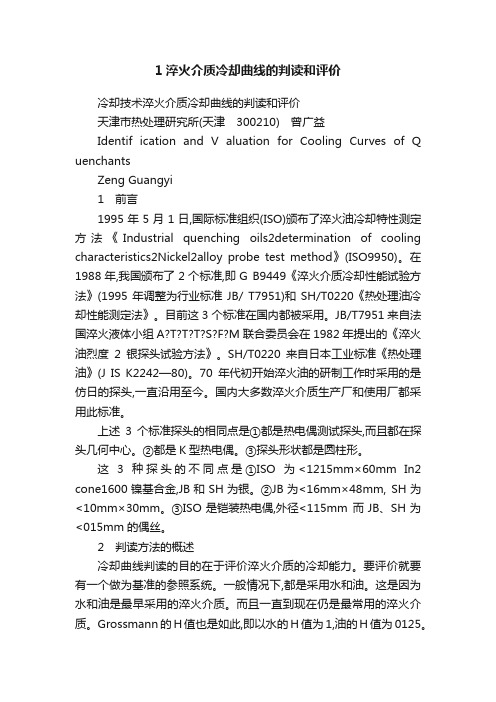
1淬火介质冷却曲线的判读和评价冷却技术淬火介质冷却曲线的判读和评价天津市热处理研究所(天津300210) 曾广益Identif ication and V aluation for Cooling Curves of Q uenchantsZeng Guangyi1 前言1995年5月1日,国际标准组织(ISO)颁布了淬火油冷却特性测定方法《Industrial quenching oils2determination of cooling characteristics2Nickel2alloy probe test method》(ISO9950)。
在1988年,我国颁布了2个标准,即G B9449《淬火介质冷却性能试验方法》(1995年调整为行业标准JB/ T7951)和SH/T0220《热处理油冷却性能测定法》。
目前这3个标准在国内都被采用。
JB/T7951来自法国淬火液体小组A?T?T?T?S?F?M联合委员会在1982年提出的《淬火油烈度2银探头试验方法》。
SH/T0220来自日本工业标准《热处理油》(J IS K2242—80)。
70年代初开始淬火油的研制工作时采用的是仿日的探头,一直沿用至今。
国内大多数淬火介质生产厂和使用厂都采用此标准。
上述3个标准探头的相同点是①都是热电偶测试探头,而且都在探头几何中心。
②都是K型热电偶。
③探头形状都是圆柱形。
这3种探头的不同点是①ISO为<1215mm×60mm In2 cone1600镍基合金,JB和SH为银。
②JB为<16mm×48mm, SH为<10mm×30mm。
③ISO是铠装热电偶,外径<115mm 而JB、SH为<015mm的偶丝。
2 判读方法的概述冷却曲线判读的目的在于评价淬火介质的冷却能力。
要评价就要有一个做为基准的参照系统。
一般情况下,都是采用水和油。
这是因为水和油是最早采用的淬火介质。
冷却特性曲线
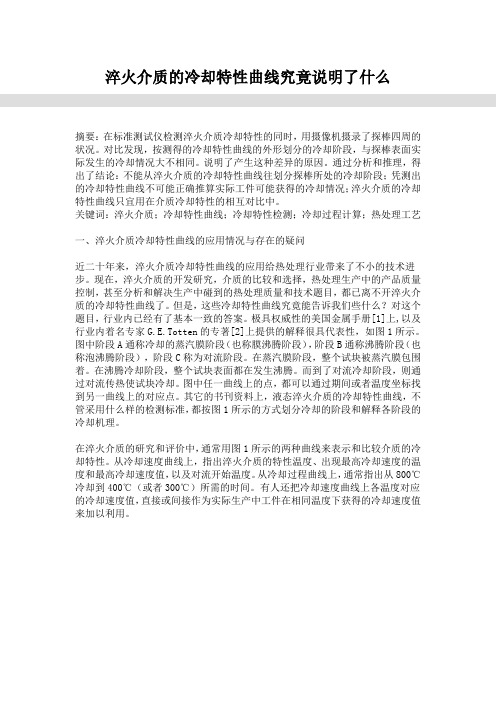
淬火介质的冷却特性曲线究竟说明了什么摘要:在标准测试仪检测淬火介质冷却特性的同时,用摄像机摄录了探棒四周的状况。
对比发现,按测得的冷却特性曲线的外形划分的冷却阶段,与探棒表面实际发生的冷却情况大不相同。
说明了产生这种差异的原因。
通过分析和推理,得出了结论:不能从淬火介质的冷却特性曲线往划分探棒所处的冷却阶段;凭测出的冷却特性曲线不可能正确推算实际工件可能获得的冷却情况;淬火介质的冷却特性曲线只宜用在介质冷却特性的相互对比中。
关键词:淬火介质;冷却特性曲线;冷却特性检测;冷却过程计算;热处理工艺一、淬火介质冷却特性曲线的应用情况与存在的疑问近二十年来,淬火介质冷却特性曲线的应用给热处理行业带来了不小的技术进步。
现在,淬火介质的开发研究,介质的比较和选择,热处理生产中的产品质量控制,甚至分析和解决生产中碰到的热处理质量和技术题目,都已离不开淬火介质的冷却特性曲线了。
但是,这些冷却特性曲线究竟能告诉我们些什么?对这个题目,行业内已经有了基本一致的答案。
极具权威性的美国金属手册[1]上,以及行业内着名专家G.E.Totten的专著[2]上提供的解释很具代表性,如图1所示。
图中阶段A通称冷却的蒸汽膜阶段(也称膜沸腾阶段),阶段B通称沸腾阶段(也称泡沸腾阶段),阶段C称为对流阶段。
在蒸汽膜阶段,整个试块被蒸汽膜包围着。
在沸腾冷却阶段,整个试块表面都在发生沸腾。
而到了对流冷却阶段,则通过对流传热使试块冷却。
图中任一曲线上的点,都可以通过期间或者温度坐标找到另一曲线上的对应点。
其它的书刊资料上,液态淬火介质的冷却特性曲线,不管采用什么样的检测标准,都按图1所示的方式划分冷却的阶段和解释各阶段的冷却机理。
在淬火介质的研究和评价中,通常用图1所示的两种曲线来表示和比较介质的冷却特性。
从冷却速度曲线上,指出淬火介质的特性温度、出现最高冷却速度的温度和最高冷却速度值,以及对流开始温度。
从冷却过程曲线上,通常指出从800℃冷却到400℃(或者300℃)所需的时间。
共析钢的c曲线和冷却过程指出各点处的组织

共析钢的c曲线和冷却过程指出各点处的组织钢的C曲线是描述钢在冷却过程中的硬度变化曲线,也是评价钢的淬透性能的重要指标之一。
冷却过程是指将高温钢材迅速冷却至室温的过程,这个过程会导致钢材的微观组织发生明显的变化。
下面我们将分别讨论钢的C曲线和冷却过程的各个阶段以及各点处的组织。
钢的C曲线是通过在冷却过程中对不同硬度的试样进行淬透试验,得到试样的硬度与淬透时间的关系曲线。
C曲线通常呈现出一个类似S形的曲线,如下图所示:[图片]在C曲线的最左侧,即淬火刚过程中,试样的硬度较低,这是因为冷却速度非常快,导致组织中的碳元素没有足够的时间扩散,形成了细小而分散的马氏体结构,马氏体的硬度较低。
此时的硬度主要由马氏体的体积分数决定,而马氏体的体积分数与碳的含量有关。
接下来是C曲线的陡峭部分,即最大淬透硬度,此时试样的硬度最高。
这是因为随着冷却时间的延长,马氏体逐渐增多,并出现了更多的残余奥氏体。
而奥氏体的硬度较低,所以整个试样的硬度会下降。
此时的硬度是由马氏体和残余奥氏体的体积分数共同决定的。
在C曲线的右侧,即逆硬度过程中,试样的硬度会再次上升。
这是因为冷却时间更长,奥氏体开始分解,转变为更硬的贝氏体和余量奥氏体。
贝氏体的形成速度较慢,而冷却时间增长正好有利于贝氏体的形成。
在逆硬度过程中,试样中贝氏体和余量奥氏体的体积分数会不断增加,从而提高试样的硬度。
在冷却过程中,钢的组织也会发生明显的变化。
在淬火刚过程中,钢材的组织主要由马氏体组成,因为冷却速度很快,没有足够的时间让碳元素扩散,导致马氏体形成。
马氏体的形态取决于钢的成分和冷却速度,常见的有板状马氏体、针状马氏体和高碳马氏体等。
随着冷却时间的延长,奥氏体逐渐出现并与马氏体共存。
奥氏体的形态也受到冷却速度的影响,常见的有等轴奥氏体、层状奥氏体和颗粒状奥氏体等。
奥氏体是面心立方结构,硬度较低,常常被认为是“软”组织。
然而,奥氏体的稳定性较好,能够长时间保持其形态而不发生相变。
液态介质中淬火冷却的四阶段理论

工件在水性介质中淬火,有时会听到爆炸声响。
本项研究工作是从探讨这种声响的产生原因开始的。
通过试验和研究,对爆炸声响的产生提出了一种解释。
试验中发现了几种用当前通行的液体介质中冷却的三阶段(蒸汽膜阶段、沸腾阶段和对流阶段)理论[1]无法解释的现象。
为解释这些现象,本文提出了液体淬火介质中淬火冷却的四阶段理论。
一对爆炸声响产生原因的初期分析经过分析,把此项研究观测的内容归结成两个:一个是完整蒸汽膜保持稳定的条件;另一个是蒸汽膜阶段的结束过程。
对这两个内容做了如下分析:1、在完整蒸汽膜阶段,是工件表面向外散失的热量使周围的液态介质变成了蒸汽,且形成的蒸汽足以使蒸汽膜保持完整。
是蒸汽膜把液态介质和工件表面分隔开,如图1a)。
因此,粗略地说,能使蒸汽膜保持稳定的条件是:从工件侧进入气液界面的热量Q1,多于、等于从气液界面向液相侧散失的热量Q2,如图1b)。
进而可以得出这样的关系:当Q1=Q2时,蒸汽膜厚度保持不变。
当Q1 > Q2时,蒸汽膜厚度会增大。
当Q1 < Q2时,蒸汽膜厚度会减小。
a)蒸汽膜把球体和液态介质分隔开b)气液界面的热量收支Q1和Q2图1 完整蒸汽膜的稳定性分析影响这种关系的重要因素有:工件表面温度高低、介质的沸点高低和饱和蒸汽压大小、气液界面液态侧的温度梯度大小,以及气液界面能(或者表面张力)高低等。
其中,气液界面能大小不太引人注意。
但是,众所周知,要费一点力气才能把肥皂泡吹大。
但停止吹气后,如果不堵着吹气口,肥皂泡就会把里面的空气压出来。
这是肥皂泡膜的表面张力引起的附加压力使泡内的气压高于外面气压的缘故。
由于气液界面的表面张力,蒸汽膜内的气压高于膜外的液压。
气液界面张力越大,内部气压也就越高。
只有更高的表面温度,才能烤出更多的蒸汽来形成更厚的蒸汽膜。
因此,在其它条件相同时,气液界面张力越大,蒸汽膜就越薄;相反,气液界面张力越小,蒸汽膜就越厚。
为了排除工件形状因素的影响,本文选定均匀球体为研究对象。
淬火介质的冷却曲线、冷却性能及选用
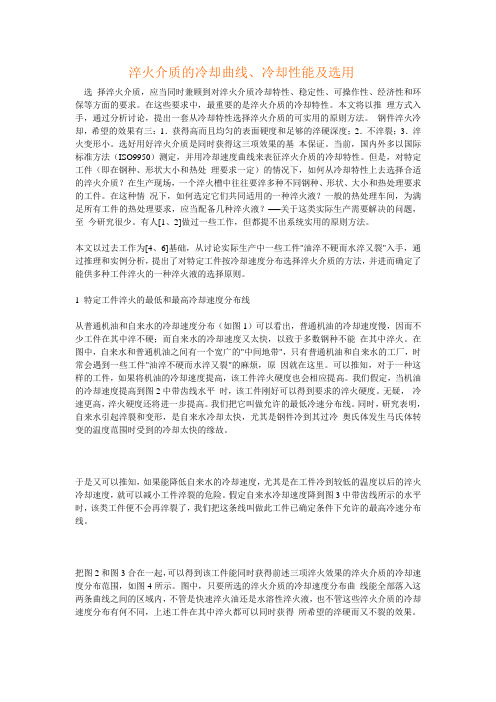
淬火介质的冷却曲线、冷却性能及选用选择淬火介质,应当同时兼顾到对淬火介质冷却特性、稳定性、可操作性、经济性和环保等方面的要求。
在这些要求中,最重要的是淬火介质的冷却特性。
本文将以推理方式入手,通过分析讨论,提出一套从冷却特性选择淬火介质的可实用的原则方法。
钢件淬火冷却,希望的效果有三:1.获得高而且均匀的表面硬度和足够的淬硬深度;2.不淬裂;3.淬火变形小。
选好用好淬火介质是同时获得这三项效果的基本保证。
当前,国内外多以国际标准方法(ISO9950)测定,并用冷却速度曲线来表征淬火介质的冷却特性。
但是,对特定工件(即在钢种、形状大小和热处理要求一定)的情况下,如何从冷却特性上去选择合适的淬火介质?在生产现场,一个淬火槽中往往要淬多种不同钢种、形状、大小和热处理要求的工件。
在这种情况下,如何选定它们共同适用的一种淬火液?一般的热处理车间,为满足所有工件的热处理要求,应当配备几种淬火液?──关于这类实际生产需要解决的问题,至今研究很少。
有人[1、2]做过一些工作,但都提不出系统实用的原则方法。
本文以过去工作为[4、6]基础,从讨论实际生产中一些工件"油淬不硬而水淬又裂"入手,通过推理和实例分析,提出了对特定工件按冷却速度分布选择淬火介质的方法,并进而确定了能供多种工件淬火的一种淬火液的选择原则。
1 特定工件淬火的最低和最高冷却速度分布线从普通机油和自来水的冷却速度分布(如图1)可以看出,普通机油的冷却速度慢,因而不少工件在其中淬不硬;而自来水的冷却速度又太快,以致于多数钢种不能在其中淬火。
在图中,自来水和普通机油之间有一个宽广的"中间地带",只有普通机油和自来水的工厂,时常会遇到一些工件"油淬不硬而水淬又裂"的麻烦,原因就在这里。
可以推知,对于一种这样的工件,如果将机油的冷却速度提高,该工件淬火硬度也会相应提高。
我们假定,当机油的冷却速度提高到图2中带齿线水平时,该工件刚好可以得到要求的淬火硬度。
淬火冷却介质的特性曲线及应用

冷却特性曲线的说明淬火介质的冷却过程分三个阶段:蒸汽膜阶段、沸腾冷却阶段、对流冷却阶段(见下图所示)。
用符合ISO9950标准的ivf冷却特性测试仪测出的冷却特性曲线(如下图)有几个特征值对淬火油的淬硬能力有重要影响。
第一个是油蒸汽膜冷却阶段向沸腾冷却阶段转变的温度,即图中A点对应的温度,叫做(上)特征温度;第二个是出现最高冷却速度的温度,即图中B点对应的温度;第三个是最高冷却速度值,即B点对应的冷却速度值;第四个是对流开始温度,即C点对应的温度。
如何从冷却特性选用淬火介质热处理淬火介质,用的首先是它的冷却性能。
因此,在确定介质的类别后,我们主张按介质的冷却特性来选择介质的品种。
比如,当我们确定应当选用快速淬火油后,具体的品种就应当根据工件特点和热处理要求从油的冷却速度分布上去选。
不管选用何种淬火介质,大致都可以按以下五条原则进行选择。
一看钢的含碳量多少── 含碳量低的钢有可能在冷却的高温阶段析出先共析铁素体,其过冷奥氏体最易发生珠光体转变的温度(即所谓"鼻尖"位置的温度)较高,马氏体起点(Ms)也较高。
因此,为了使这类钢制的工件充分淬硬,所用的淬火介质应当有较短的蒸汽膜阶段,且其出现最高冷却速度的温度应当较高。
相反,对含碳量较高的钢,淬火介质的蒸汽膜阶段可以更长些,出现最高冷却速度的温度也应当低些。
二看钢的淬透性高低——淬透性差的钢要求用冷却速度快的淬火介质,淬透性好的钢则可以用冷却速度慢一些的介质。
通常,随着钢的淬透性提高,过冷奥氏体分解转变的“C”曲线会向右下方移动。
所以,对淬透性差的钢,选用的淬火介质出现最高冷却速度的温度应当高些;而淬透性好的钢则低些。
有些淬透性好的钢过冷奥氏体容易发生贝氏体转变,要避开其贝氏体转变,也要求有足够快的低温冷却速度。
三看工件的有效厚度大小——如果工件的表面一冷到Ms点,就立即大大减慢介质的冷却速度,则工件内部的热量向淬火介质散失的速度也就立即放慢,这必然使工件表面一定深度以内的过冷奥氏体冷不到Ms点就发生非马氏体转变,其结果,淬火后工件只有很薄的马氏体层。
淬火介质的冷却特性曲线
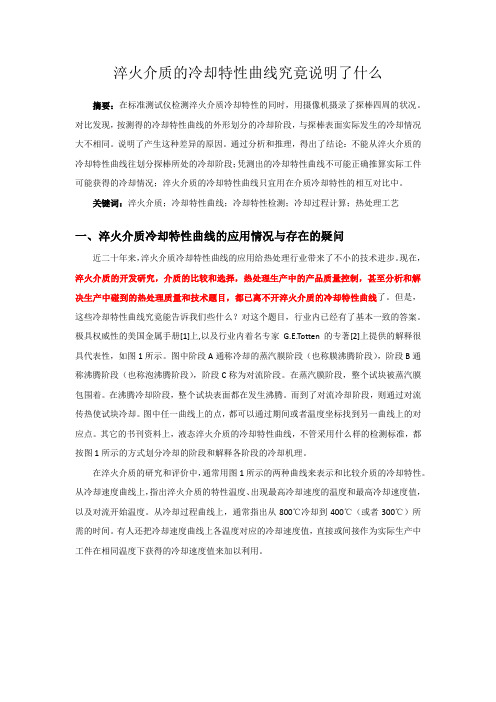
淬火介质的冷却特性曲线究竟说明了什么摘要:在标准测试仪检测淬火介质冷却特性的同时,用摄像机摄录了探棒四周的状况。
对比发现,按测得的冷却特性曲线的外形划分的冷却阶段,与探棒表面实际发生的冷却情况大不相同。
说明了产生这种差异的原因。
通过分析和推理,得出了结论:不能从淬火介质的冷却特性曲线往划分探棒所处的冷却阶段;凭测出的冷却特性曲线不可能正确推算实际工件可能获得的冷却情况;淬火介质的冷却特性曲线只宜用在介质冷却特性的相互对比中。
关键词:淬火介质;冷却特性曲线;冷却特性检测;冷却过程计算;热处理工艺一、淬火介质冷却特性曲线的应用情况与存在的疑问近二十年来,淬火介质冷却特性曲线的应用给热处理行业带来了不小的技术进步。
现在,淬火介质的开发研究,介质的比较和选择,热处理生产中的产品质量控制,甚至分析和解决生产中碰到的热处理质量和技术题目,都已离不开淬火介质的冷却特性曲线了。
但是,这些冷却特性曲线究竟能告诉我们些什么?对这个题目,行业内已经有了基本一致的答案。
极具权威性的美国金属手册[1]上,以及行业内着名专家G.E.Totten的专著[2]上提供的解释很具代表性,如图1所示。
图中阶段A通称冷却的蒸汽膜阶段(也称膜沸腾阶段),阶段B通称沸腾阶段(也称泡沸腾阶段),阶段C称为对流阶段。
在蒸汽膜阶段,整个试块被蒸汽膜包围着。
在沸腾冷却阶段,整个试块表面都在发生沸腾。
而到了对流冷却阶段,则通过对流传热使试块冷却。
图中任一曲线上的点,都可以通过期间或者温度坐标找到另一曲线上的对应点。
其它的书刊资料上,液态淬火介质的冷却特性曲线,不管采用什么样的检测标准,都按图1所示的方式划分冷却的阶段和解释各阶段的冷却机理。
在淬火介质的研究和评价中,通常用图1所示的两种曲线来表示和比较介质的冷却特性。
从冷却速度曲线上,指出淬火介质的特性温度、出现最高冷却速度的温度和最高冷却速度值,以及对流开始温度。
从冷却过程曲线上,通常指出从800℃冷却到400℃(或者300℃)所需的时间。
冷却特性曲线

冷却特性曲线淬火介质的冷却特性曲线究竟说明了什么摘要:在标准测试仪检测淬火介质冷却特性的同时,用摄像机摄录了探棒四周的状况。
对比发现,按测得的冷却特性曲线的外形划分的冷却阶段,与探棒表面实际发生的冷却情况大不相同。
说明了产生这种差异的原因。
通过分析和推理,得出了结论:不能从淬火介质的冷却特性曲线往划分探棒所处的冷却阶段;凭测出的冷却特性曲线不可能正确推算实际工件可能获得的冷却情况;淬火介质的冷却特性曲线只宜用在介质冷却特性的相互对比中。
关键词:淬火介质;冷却特性曲线;冷却特性检测;冷却过程计算;热处理工艺一、淬火介质冷却特性曲线的应用情况与存在的疑问近二十年来,淬火介质冷却特性曲线的应用给热处理行业带来了不小的技术进步。
现在,淬火介质的开发研究,介质的比较和选择,热处理生产中的产品质量控制,甚至分析和解决生产中碰到的热处理质量和技术题目,都已离不开淬火介质的冷却特性曲线了。
但是,这些冷却特性曲线究竟能告诉我们些什么?对这个题目,行业内已经有了基本一致的答案。
极具权威性的美国金属手册[1]上,以及行业内着名专家G.E.Totten的专著[2]上提供的解释很具代表性,如图1所示。
图中阶段A通称冷却的蒸汽膜阶段(也称膜沸腾阶段),阶段B通称沸腾阶段(也称泡沸腾阶段),阶段C称为对流阶段。
在蒸汽膜阶段,整个试块被蒸汽膜包围着。
在沸腾冷却阶段,整个试块表面都在发生沸腾。
而到了对流冷却阶段,则通过对流传热使试块冷却。
图中任一曲线上的点,都可以通过期间或者温度坐标找到另一曲线上的对应点。
其它的书刊资料上,液态淬火介质的冷却特性曲线,不管采用什么样的检测标准,都按图1所示的方式划分冷却的阶段和解释各阶段的冷却机理。
在淬火介质的研究和评价中,通常用图1所示的两种曲线来表示和比较介质的冷却特性。
从冷却速度曲线上,指出淬火介质的特性温度、出现最高冷却速度的温度和最高冷却速度值,以及对流开始温度。
从冷却过程曲线上,通常指出从800℃冷却到400℃(或者300℃)所需的时间。
- 1、下载文档前请自行甄别文档内容的完整性,平台不提供额外的编辑、内容补充、找答案等附加服务。
- 2、"仅部分预览"的文档,不可在线预览部分如存在完整性等问题,可反馈申请退款(可完整预览的文档不适用该条件!)。
- 3、如文档侵犯您的权益,请联系客服反馈,我们会尽快为您处理(人工客服工作时间:9:00-18:30)。
第28卷第2期2007年4月热处理技术与装备RECHUL I J I SHU Y U ZHUANG BE I Vol .28,No .2Ap r,2007收稿日期:2006-11-28作者简介:张克俭(1945-),男,工学博士,主要从事淬火介质产品开发及其应用技术的研究工作・试验研究・淬火介质的冷却特性曲线究竟说明了什么张克俭(北京华立精细化工公司 北京 102200)摘 要:在用标准测试仪检测淬火介质冷却特性的同时,用摄像机摄录了探棒周围的状况。
对比发现,按测得的冷却特性曲线的形状划分的冷却阶段,与探棒表面实际发生的冷却情况大不相同。
说明了产生这种差异的原因。
通过分析和推理,得出了结论:不能从淬火介质的冷却特性曲线去划分探棒所处的冷却阶段;凭测出的冷却特性曲线不可能准确推算实际工件可能获得的冷却情况;淬火介质的冷却特性曲线只宜用在介质冷却特性的相互对比中。
关键词:淬火介质;冷却特性曲线;冷却特性检测;冷却过程计算;热处理工艺中图分类号: TG154.4 文献标识码: B 文章编号: 1673-4971(2007)02-0025-04W ha t Cooli n g Ra te Curve of Quench i n g M ed i a I m pli esZhang Ke 2jian(Beijing Huali Fine Che m ical Company L td .Beijing 102200,China )Abstract:The visual phenomena occurred ar ound the quench p r obe were recorded with digital video ca 2mera during standard test of quenching media .It was found that partiti on of cooling p r ocess according t o the measured cooling rate curve is not t otally corres ponding t o what were visually observed .The reas ons of this discrepancy are discussed .It is concluded the cooling p r ocess of actual quenched parts can not be ac 2curately p redicted by merely using the measured cooling rate curves of quenching media,which are only app licable f or comparis on of characteristics of different quenching media .Key words:quenchant;cooling curve;cooling curve test;si m ulati on of quenching p r ocess;heat treat m ent technol ogy1 淬火介质冷却特性曲线的应用情况与存在的疑问近二十年来,淬火介质冷却特性曲线的应用给热处理行业带来了不小的技术进步。
现在,淬火介质的开发研究,介质的比较和选择,热处理生产中的产品质量控制,甚至分析和解决生产中遇到的热处理质量和技术问题,都已离不开淬火介质的冷却特性曲线了。
但是,这些冷却特性曲线究竟能告诉我们些什么?对这个问题,行业内已经有了基本一致的答案。
极具权威性的美国金属手册[1]上,以及行业内知名专家G .E .T otten 的专著[2]上提供的解释很具代表性,如图1所示。
图中阶段A 通称冷却的蒸汽膜阶段(也称膜沸腾阶段),阶段B 通称沸腾阶段(也称泡沸腾阶段),阶段C 称为对流阶段。
在蒸汽膜阶段,整个试块被蒸汽膜包围着。
图中,在沸腾冷却阶段,整个试块表面都在发生沸腾。
而到了对流冷却阶段,则通过对流传热使试块冷却。
曲线上的点,都可以通过时间或者温度坐标找到另一曲线上的对应点。
一般的书刊资料上,液态淬火介质的冷却特性曲线,不管采用什么样的检测标准,都按图1所示的方式划分冷却的阶段和解释各阶段的冷却机理。
在淬火介质的研究和评价中,通常用图1所示的热处理技术与装备第28卷图1 液态介质中淬火冷却的阶段划分和各阶段的散热机理两种曲线来表示和比较介质的冷却特性。
从冷却速度曲线上,通常指出淬火介质的特性温度、出现最高冷却速度的温度和最高冷却速度值,以及对流开始温度。
从冷却过程曲线上,通常指出从800℃冷却到400℃(或者300℃)所需的时间。
有人还把冷却速度曲线上各温度对应的冷却速度值,直接作为实际生产中工件在相同温度下获得的冷却速度值来加以利用。
众所周知,在同样冷却条件下小工件冷得快,大工件冷得慢。
根据这一常理,人们会理所当然地把它与淬火介质的冷却速度曲线联系起来。
由此便产生了这样的认识:在相同冷却条件下,工件上具有相同有效厚度的部分,都应当获得相同的冷却进程和冷却效果;并且,都可以在淬火介质的冷却特性曲线上找到它们的温度、冷却速度和冷却时间的对应关系。
考虑到测温的热电偶热端在探棒的几何中心,以及探棒材质和形状因素的影响,对上述认识和做法的准确性,我们一直持有一些怀疑。
为了澄清这方面的诸多疑团,在完成“液态淬火介质中冷却的四阶段理论”的研究后,通过试验和观测,研究了本课题。
研究的目的有三个:1)审查现行认识和用途的合理性;2)如果有问题,就找出产生问题的原因;3)确定淬火介质冷却特性曲线的合理应用场合和合理应用限度。
2 试验方法和试验结果2.1 试验方法和仪器在检测淬火介质之冷却特性的过程中,用摄像机同步观测记录探棒表面发生的现象。
为了获得更清晰的图像,采用的是无色或者颜色很浅、而且透明的淬火介质品种。
比如清水、盐水、精炼程度很高的基础油、快速淬火油和P AG淬火液等介质。
检测淬火介质冷却特性用的是ivf仪。
摄像用的是松下NV2GS11型摄像机。
采用1/1较快的快门速度,每秒拍摄25张图片。
试验中通常采用850℃的加热温度。
水性介质的液温在10~70℃内选取;油性介质的液温在30~100℃内选取。
2.2 试验结果试验获得了通常所见的淬火介质的冷却特性曲线,又获得了探棒冷却过程中表面附近冷却情况的摄像资料。
下面以清水、基础油和快速淬火油为代表,介绍本文的试验结果。
其中,把冷却速度曲线上一些选定点所对应的摄像观测结果以示意图形式画在同一张图上。
基础油的冷却特性曲线与多个选定点的冷却状况如图2所示。
快速淬火油的冷却特性曲线与多个选定点的冷却状况如图3所示。
60℃清水的冷却特性曲线与多个选定点的冷却状况如图4所示。
3 试验结果分析研究分析的重点放在两个方面:一是介质的冷却特性曲线与摄像观测到的冷却情况之间的关系。
二是不同淬火介质的冷却特性和摄像结果之间的共性规律。
3.1 冷却特性曲线与冷却介质散热阶段的关系稍加注意就会发现:冷却特性曲线上选定点所处的冷却阶段,和同一时刻探棒上实际发生的冷却阶段大不相同。
主要表现在:图2 50℃基础油的试验和观测结果对照图・62・第2期张克俭:淬火介质的冷却特性曲线究竟说明了什么图3 50℃快速淬火油的试验和观测结果对照图图4 60℃清水的试验和观测结果对照图 a )除了蒸汽膜阶段之初,如图2中第1点以外,在所有其它的选定点上,实际发生的冷却状况都与介质冷却特性曲线上所指的阶段构成不同。
b )在介质的冷却特性曲线上,除冷却阶段的分界点外,一定的探棒温度都对应着一种单一的冷却阶段。
但是,摄像结果表明,在大部分冷却过程中,探棒上不同部位都存在二、三个冷却阶段。
比如,即便在特别令人关注的特性温度点上,在基础油中试验时,探棒的上下两端都早已进入了沸腾冷却阶段。
这说明当时探棒表面同时存在两个冷却阶段。
在快速淬火油和60℃清水的特性温度点,探棒上同时存在着三种冷却阶段。
在出现最高冷却速度的时刻,三种介质中探棒上都同时存在三个冷却阶段;但是不同介质中各阶段所占的比例却不相同。
冷却特性曲线的对流开始温度上,在基础油和快速淬火油中也还存在三个冷却阶段。
清水中试验时,在冷却特性曲线的对流开始点,探棒上下部分处在对流阶段的同时,中上段还有少部分沸腾冷却区。
c )对不同介质品种,比较了冷却特性曲线上的特性温度、出现最高冷却速度的温度,以及对流开始温度时,摄像图片上的冷却阶段数和各阶段所占的比例。
结果证明,不同介质之间不存在共同之处。
d )所有这些结果都说明:现行的淬火介质冷却特性曲线与摄像观测到的冷却阶段之间,没有简单的对应关系。
因此,不能从淬火介质的冷却特性曲线去划分探棒所处的冷却阶段。
3.2 淬火介质的冷却特性曲线是如何形成的凭淬火介质中冷却的三阶段理论(如图1所示的划分法),以及有效厚度就能决定冷却进程的认识,无法解释图1所示冷却特性曲线的形成原因。
比如,按图1所示的阶段划分,一冷到所谓的特性温度点,整个探棒就会进入沸腾冷却阶段。
由于当时探棒的温度很高,相应的冷却速度曲线上应当出现整个冷却过程的最高冷却速度值。
但图线中最高冷却速度值却出现在更低的温度上。
事实上,这里涉及到两个问题:一是测量温度的热电偶热端位于探棒的几何中心。
它所测出的是内部点的温度变化。
二是决定探棒某点冷却特性的因素,除了探棒本身的传热学特性外,冷却介质在不同温度的散热机理(阶段)又起着非常重要的作用。
最新提出的“液态淬火介质中冷却的四阶段理论”则容易解释这一问题。
四阶段理论认为,在液态淬火介质中冷却的机理,可按工件温度高低划分成:蒸汽膜阶段、中间阶段、沸腾阶段和对流阶段。
中间阶段有其特定的成因和独有的特性[3]。
详细内容请查看原文。
下面只分析内部点的温度变化,用以说明图2~4对应的观测结果上常常存在2,3个冷却阶段的原因。
淬火冷却过程中,内部某点P 的温度降低是通过向更外部分散热来实现的,如图5所示。
产生这种散热的最终原因是液体介质对工件表面的冷却作用。
远近不同的表面部分被冷却,再通过热传导使P 点冷却下来。
不管参与冷却的表面处于蒸汽膜阶段、沸腾阶段、还是对流阶段,离P 点越近,其降温情况对P 点产生影响就越早;离P 点越远,其降温情况对P 点产生影响就越迟。
因此,任何时刻P 点实际的冷却情况是在该时刻之前一定时间范围内,远近不同的表面所受冷却情况的综合影响的结果。
内部点的冷却特性曲线,表述的就是这种影响随时间的・72・热处理技术与装备第28卷变化和随P 点温度的变化情况。
通常用来描述淬火介质冷却特性的图线,也正是这类曲线。