轮胎成型工艺
汽车轮胎的制造工艺解析

汽车轮胎的制造工艺解析随着汽车产业的快速发展,汽车轮胎作为汽车的重要组成部分,对行车安全和舒适性起着至关重要的作用。
汽车轮胎的制造工艺直接关系到轮胎的质量和性能,本文将对汽车轮胎的制造工艺进行解析,以帮助读者更好地了解轮胎的制造过程。
1. 胎体制造汽车轮胎的胎体是由多层胶片和带状钢丝组成的,它们通过粘合剂和硫化剂进行固化。
首先,将胶片和钢丝分别经过预处理,然后在制胎机上进行胶片和钢丝的叠合。
胶片和钢丝的叠合过程需要严格控制叠合的张力和角度,以确保胎体的均匀性和稳定性。
接下来,将叠合好的胶片和钢丝放入模具中,加入粘合剂和硫化剂,然后进行压制和硫化,最终得到胎体。
2. 胎面制造胎面是汽车轮胎与地面接触的部分,它直接影响到轮胎的抓地力和操控性能。
胎面的制造过程主要包括胎面花纹设计、胶料混炼和成型。
胎面花纹设计是根据轮胎的使用环境和性能要求,通过计算机辅助设计软件进行设计,以确保胎面的排水性能、抓地力和噪音性能等。
胶料混炼是将橡胶和其他添加剂混合在一起,通过机械设备进行加热和搅拌,以获得具有特定性能的橡胶胶料。
成型是将混炼好的胶料放入模具中,经过加热和压制,使其成型成为胎面。
3. 布带制造布带是汽车轮胎的重要结构部分,它承受着轮胎的负荷和扭矩,并提供了轮胎的强度和刚性。
布带的制造过程主要包括布带材料的选择、布带的编织和涂胶。
布带材料通常采用尼龙或聚酯纤维,这些纤维具有高强度和耐磨性。
布带的编织是将布带材料通过编织机进行交叉编织,以形成坚固的网状结构。
涂胶是将编织好的布带放入涂胶机中,将胶料均匀涂覆在布带上,然后通过加热和压制使其固化。
4. 胎侧制造胎侧是连接胎体和胎面的部分,它起到支撑和保护轮胎的作用。
胎侧的制造过程主要包括胎侧胶料的混炼和成型。
胎侧胶料的混炼过程与胎面胶料的混炼类似,但需要根据胎侧的形状和尺寸进行调整。
成型是将混炼好的胎侧胶料放入模具中,经过加热和压制,使其成型成为胎侧。
5. 胎圈制造胎圈是连接轮胎和车轮的部分,它需要具备高强度和耐磨性。
轮胎的制造工艺流程
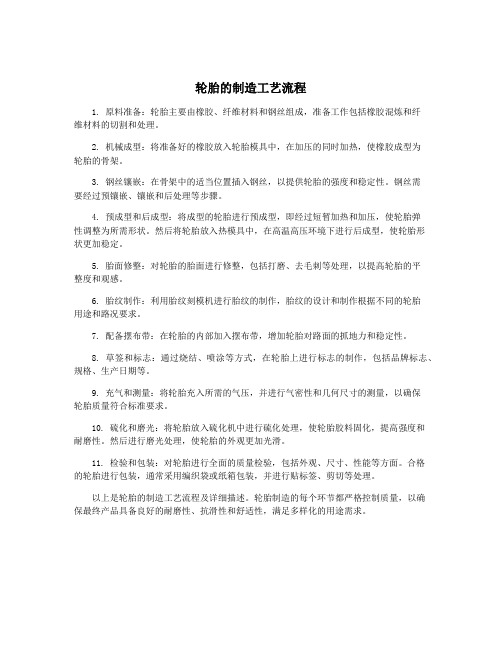
轮胎的制造工艺流程1. 原料准备:轮胎主要由橡胶、纤维材料和钢丝组成,准备工作包括橡胶混炼和纤维材料的切割和处理。
2. 机械成型:将准备好的橡胶放入轮胎模具中,在加压的同时加热,使橡胶成型为轮胎的骨架。
3. 钢丝镶嵌:在骨架中的适当位置插入钢丝,以提供轮胎的强度和稳定性。
钢丝需要经过预镶嵌、镶嵌和后处理等步骤。
4. 预成型和后成型:将成型的轮胎进行预成型,即经过短暂加热和加压,使轮胎弹性调整为所需形状。
然后将轮胎放入热模具中,在高温高压环境下进行后成型,使轮胎形状更加稳定。
5. 胎面修整:对轮胎的胎面进行修整,包括打磨、去毛刺等处理,以提高轮胎的平整度和观感。
6. 胎纹制作:利用胎纹刻模机进行胎纹的制作,胎纹的设计和制作根据不同的轮胎用途和路况要求。
7. 配备摆布带:在轮胎的内部加入摆布带,增加轮胎对路面的抓地力和稳定性。
8. 草签和标志:通过烧结、喷涂等方式,在轮胎上进行标志的制作,包括品牌标志、规格、生产日期等。
9. 充气和测量:将轮胎充入所需的气压,并进行气密性和几何尺寸的测量,以确保轮胎质量符合标准要求。
10. 硫化和磨光:将轮胎放入硫化机中进行硫化处理,使轮胎胶料固化,提高强度和耐磨性。
然后进行磨光处理,使轮胎的外观更加光滑。
11. 检验和包装:对轮胎进行全面的质量检验,包括外观、尺寸、性能等方面。
合格的轮胎进行包装,通常采用编织袋或纸箱包装,并进行贴标签、剪切等处理。
以上是轮胎的制造工艺流程及详细描述。
轮胎制造的每个环节都严格控制质量,以确保最终产品具备良好的耐磨性、抗滑性和舒适性,满足多样化的用途需求。
全钢丝子午线轮胎胎圈成型作业要点

全钢丝子午线轮胎胎圈成型作业要点一、胎圈成型工艺流程1.预成型预成型是指将钢丝制成所需形状的过程。
首先,将经过拉丝和整形的钢丝编织成带状结构,然后将带状结构卷绕成圆形,经过加热和冷却后形成预成型胎圈。
2.折边折边是将预成型胎圈的边缘向内折叠,使其与轮胎胎体更好地贴合,并增加胎圈的强度。
折边需要使用专用的机器在预成型胎圈的两个边缘同时进行。
3.焊接焊接是将折边后的预成型胎圈进行焊接,使其形成闭合的圆环。
焊接工艺包括电阻焊接和MIG/MAG焊接两种方法。
电阻焊接是通过电流通过两个电极产生热量,将焊接接口加热至熔点并形成焊接。
MIG/MAG焊接则是通过提供电弧和外部保护气体,将焊接接口加热至熔点并形成焊接。
4.定型焊接后的胎圈需要进行定型,以确保其形状和尺寸的精确性。
定型过程中会使用模具将胎圈暴露在高温和高压的环境中,使其获得稳定的形状。
二、胎圈成型工艺控制要点胎圈成型工艺的控制对于保证轮胎质量和性能至关重要。
以下是胎圈成型工艺的控制要点。
1.原材料控制胎圈的制作需要优质的钢丝作为原材料,因此需要对原材料进行严格的控制。
包括控制钢丝的拉伸性能、硬度和表面质量等。
2.温度控制在胎圈成型过程中,温度对于预成型、焊接和定型等环节都有重要影响。
需要严格控制每个环节的温度,确保系统温度稳定和过程可控。
3.加工精度控制胎圈成型工艺要求胎圈的形状和尺寸精确。
因此,在每一个环节都需要控制加工精度,包括拉丝和整形、卷绕、折边、焊接和定型等。
4.检测控制胎圈成型后需要进行质量检测,包括外观质量、尺寸和热处理等。
需要建立完善的检测控制体系,确保胎圈的质量达到要求。
三、胎圈成型工艺常见问题及解决方法在胎圈成型过程中,常常会遇到一些问题,需要及时解决。
以下是一些常见问题及其解决方法。
1.焊接接头质量不合格可能原因有电阻焊接/MIG/MAG焊接参数设置不合理、焊接接触面不整齐等。
可以通过调整焊接参数、整理焊接接触面等方法解决。
2.预成型胎圈尺寸不准确可能原因有预成型工艺参数不合理、设备磨损等。
轮胎的成型定型工艺

轮胎的成型定型工艺一、胎圈胶料准备胎圈胶料是轮胎成型的重要组成部分,在成型定型工艺中的使用起着关键性的作用。
在成型过程中,需要将胎圈胶料提前准备好,确保有足够的用量和质量。
一般情况下,根据预定的胎胚结构确定所需的胎圈胶料的类型、种类和比例。
二、胎胚装配轮胎成型定型的重要步骤之一是胎胚的装配。
胎胚一般是由胎圈布、骨架布和内层胶料等材料组成。
在装配过程中,首先将胎圈布放在成型定型机的模具上,然后按照预定的方式和比例依次加入骨架布和内层胶料。
三、成型定型在胎胚装配完成后,进入成型定型的工艺步骤。
首先,将胎胚放入成型模具内,并通过加热和加压的方式进行成型。
加热的温度和时间根据胎圈胶料的特性和成型模具的要求来确定。
经过一定的时间和温度的作用,胎胚会逐渐变形,并与模具表面保持一定的接触。
此时,通过加压,将胎胚与模具完整地贴合在一起,形成轮胎的基本形状。
四、冷却定型在成型定型的过程中,轮胎的形状已经初步定型,但其形态和结构还不够稳定。
因此,在完成成型后,需要对轮胎进行冷却定型,使其形态和结构更加稳定。
冷却定型是通过将成型定型的轮胎放置在冷却设备中进行冷却。
冷却的时间根据轮胎的尺寸和材料的特性来确定,一般约为数小时至数天不等。
在冷却过程中,轮胎的温度会逐渐降低,形态和结构也会逐渐固定。
五、去胶、修整在轮胎冷却定型后,会存在一定的胶料溢出和不平整的情况。
因此,需要对轮胎进行去胶和修整的工艺步骤。
去胶是指将轮胎表面附着的多余胶料除去,使轮胎外观更加整洁。
修整是指对轮胎的边缘和表面进行修整,使其尺寸和形状符合要求。
去胶和修整的方式可以通过切割、磨削和涂覆等方式进行。
最后,经过上述的成型定型工艺步骤,轮胎的形态和结构基本定型完成。
然后,可以进行后续的胎面花纹设计、胎壁结构加强和胎胚检查等工艺步骤,最终完成轮胎的制造。
这些工艺步骤的严格执行和精确控制,对于保证轮胎的质量和性能起到至关重要的作用。
六、胎面花纹设计胎面花纹是轮胎上面的纹路和凹槽,对轮胎的性能和使用效果有着直接的影响。
轮胎行业工艺流程

轮胎行业工艺流程
《轮胎行业工艺流程》
轮胎作为车辆的重要零部件,其制造工艺流程非常复杂。
以下是轮胎行业工艺流程的简要介绍:
1. 布胎:轮胎的制作是从内部开始的,首先是将胎体的骨架结构通过一定的工艺手段进行排布,形成布胎。
布胎的设计和制作需要考虑轮胎的尺寸、荷载和速度等因素。
2. 胶料制备:轮胎的胎体和胎面需要使用各种不同类型的橡胶,其中包括天然橡胶、合成橡胶等材料。
这些橡胶材料需要经过一系列的工艺流程,包括混炼、压片、硫化等步骤,制备成适合轮胎生产的胶料。
3. 成型:成型是轮胎制造的关键环节,通过在模具内注入胶料并施加压力和热力,使其在模具内形成具有特定轮胎花纹和轮胎轮廓的成品。
成型过程需要严格控制温度、压力和时间等参数。
4. 硫化:硫化是将成型后的轮胎在高温和压力条件下进行固化和交联的过程。
这一步骤是轮胎工艺流程中至关重要的环节,能够提高轮胎的耐磨性和耐老化性能。
5. 检测和质量控制:轮胎生产完成后,需要进行严格的检测和质量控制,确保轮胎符合相关的安全和性能标准。
这些检测包括轮胎的尺寸、硬度、韧性、耐磨性等各项指标。
以上是轮胎行业的工艺流程的主要环节,轮胎的制造需要精密的设备和严格的工艺管理,以确保轮胎的安全性和性能可靠性。
随着技术的不断发展,轮胎制造工艺也在不断创新和改进,以满足市场和消费者的需求。
轮胎制作工艺流程

轮胎制作工艺流程
轮胎制作工艺流程如下:
1. 原材料准备:准备好橡胶原料,包括天然橡胶、合成橡胶、碳黑、油类、硫磺、促进剂等材料,将它们混合在一起制成胶料。
所有的原材料在进入密炼机以前,必须进行测试,被放行以后方可使用。
2. 操作面板准备:准备一个操作面板及其相应的模具,将模具涂上分离剂,这样胶料不会黏在模具上。
3. 印刷码号:把轮胎的型号和其他信息通过印刷或标签贴在胶料上。
4. 预成型:通过加热和压缩处理,让胶料变得柔软、易于成型。
5. 成型:使用由钢丝和胶体组成的设备,将胶料填入模具中。
模具中设置了轮胎的亚部组件,例如带钢、编织钢丝帘子和胶层。
这使得轮胎在运行中更加结实耐用。
6. 硫化:将模具送入硫化炉中,在高温高压的环境下对轮胎进行硫化处理。
硫磺能让轮胎聚合,从而变得更加结实和耐用。
7. 完成:待轮胎从模具中取出并清理后,通过品检和测试等严格的质量控制流程,使得轮胎性能更为稳定,再包装、存储、销售。
如需更多轮胎制作工艺的信息,建议咨询轮胎制造行业资深业内人士或查阅相关论坛。
全钢子午线轮胎成型生产工艺流程

嗨,大家好!今天我要给大家介绍一下全钢子午线轮胎是怎么做出来的。
轮胎是汽车上的一个很重要的部件,它可以让汽车跑得更稳,开得更安全。
那么全钢子午线轮胎是怎么做出来的呢?
我们要准备一些东西,有橡胶、钢丝、合成橡胶、填料和胶料。
这些东西要通过混炼机搅拌在一起,搅拌好的橡胶要挤出来成长长的橡胶带。
接下来就是做成型的模子啦!这个模子好像是汽车轮胎的样子,特别大特别笨重。
制作这么大的模子一定要很小心,而且还要考虑到轮胎的外形和里面的花纹。
然后呢,就是把橡胶带放进去成型模子里,再加热一下,压一下,橡胶就会变成轮胎的形状啦!这个过程中需要控制好温度和压力,不然橡胶会乱跑。
成型好之后,要把轮胎放到硫化机里去硫化,这也是很重要的一步。
硫化是让轮胎变得有弹性和耐磨的,通过加热和加压就可以把橡胶做出来好像胶一样,让它变得更结实。
要检查轮胎的质量和外观。
看看大小对不对,硬不硬,拉拉看看,还要看有没有外面的瑕疵。
检查好之后再来外观处理,把轮胎上面的毛刺去掉,再来涂涂油,然后加上标志。
除了这些步骤以外,还有一些小秘诀,喔,是我不能说的!不过啦,
还有一个很厉害的,就是轮胎生产的机器可以自己调整参数,来适应
不同规格的轮胎。
这样就可以生产出更多不一样的轮胎啦。
全钢子午线轮胎成型生产工艺流程需要好多步骤啊!要控制好每一步,才能做出好的轮胎。
这些轮胎都是给汽车用的,所以一定要做得好,
才能让汽车开得更好!。
轮胎厂工艺流程
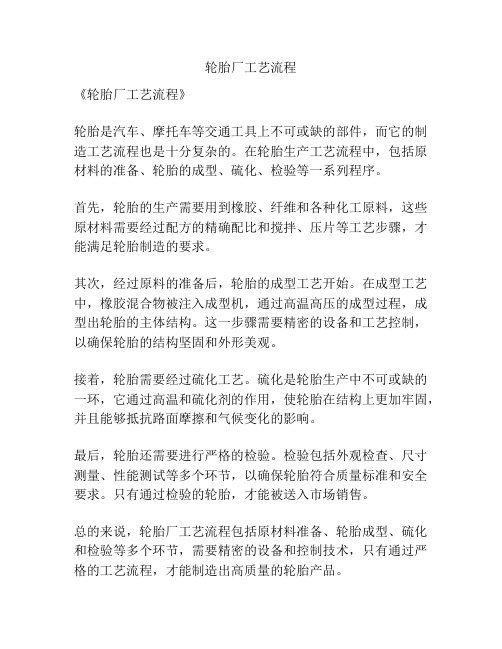
轮胎厂工艺流程
《轮胎厂工艺流程》
轮胎是汽车、摩托车等交通工具上不可或缺的部件,而它的制造工艺流程也是十分复杂的。
在轮胎生产工艺流程中,包括原材料的准备、轮胎的成型、硫化、检验等一系列程序。
首先,轮胎的生产需要用到橡胶、纤维和各种化工原料,这些原材料需要经过配方的精确配比和搅拌、压片等工艺步骤,才能满足轮胎制造的要求。
其次,经过原料的准备后,轮胎的成型工艺开始。
在成型工艺中,橡胶混合物被注入成型机,通过高温高压的成型过程,成型出轮胎的主体结构。
这一步骤需要精密的设备和工艺控制,以确保轮胎的结构坚固和外形美观。
接着,轮胎需要经过硫化工艺。
硫化是轮胎生产中不可或缺的一环,它通过高温和硫化剂的作用,使轮胎在结构上更加牢固,并且能够抵抗路面摩擦和气候变化的影响。
最后,轮胎还需要进行严格的检验。
检验包括外观检查、尺寸测量、性能测试等多个环节,以确保轮胎符合质量标准和安全要求。
只有通过检验的轮胎,才能被送入市场销售。
总的来说,轮胎厂工艺流程包括原材料准备、轮胎成型、硫化和检验等多个环节,需要精密的设备和控制技术,只有通过严格的工艺流程,才能制造出高质量的轮胎产品。
- 1、下载文档前请自行甄别文档内容的完整性,平台不提供额外的编辑、内容补充、找答案等附加服务。
- 2、"仅部分预览"的文档,不可在线预览部分如存在完整性等问题,可反馈申请退款(可完整预览的文档不适用该条件!)。
- 3、如文档侵犯您的权益,请联系客服反馈,我们会尽快为您处理(人工客服工作时间:9:00-18:30)。
口型板变形;热炼温度和压出温度掌握不正;压出速度不均匀或联 动装置配合不当;压出后冷却不足;热炼不充分。 焦烧 产生原因为:胶料配方设计不当,焦烧性能差;热炼和压出温度 过高;机头中有积胶、死角或冷却水不通;供胶中断;空车滞料。 断边烂边 产生原因为:热炼不足,胶料可塑性小;胶料焦烧;胎面口型 边部流胶口小或堵塞;机头、口型板温度低。
↓
压 片、冷 却、下 料
胶
↓ 料
热
炼
↓↓
↓
↓
↓
汽门嘴化学处理 过 滤 垫带压出 胎面压出 三角胶条压型 钢丝压出和成圈
↓
粘贴胶垫
↓
↓↓↓Fra bibliotek↓加硫磺 接 头 定长、切割 钢 圈 制 造 ←
↓
↓
↓
↓
气门嘴硫化
热 炼 垫带硫化 接 头
↓
帆布
↓
↓
↓
↓
↓
↓
内胎压出 ↓
外
胎
成
↓
↓
内胎接头成型
第二章 轮胎的成型工艺
(一)轮胎制造工艺流程和准备工艺 1、胎面压出 (2)胎面压出方法 ① 胎面压出按设备分为热喂料挤出法与
冷喂料挤出法 ② 按胎面压出方法分为整体压出法与分
层压出法
第二章 轮胎的成型工艺
(一)轮胎制造工艺流程和准备工艺 1、胎面压出 (3)胎面压出工艺条件 ① 胎面压出工艺流程 胎面压出工艺有热喂料压出和冷
第二章 轮胎的成型工艺
(一)轮胎制造工艺流程和准备 工艺
2、帘布压延 (1)压延设备 轮胎帘、帆布
挂胶常用四辊压延机和三辊 压延机,三辊压延机用于胶料 压片或帘,帆布擦胶和贴胶 四辊压延机用于帘、帆布贴 胶或胶片的贴合,常用的为L 型或T型、现代采用的Z型或S 型压延机;四辊压延机的几种 形式可见图3-6所示。
喂料压出两种。
热喂料压出工艺流程为:热炼→压出→贴合→秤量→冷 却→自动打印(规格,标记)→打磨→自动定长→裁断→ 检验→存放。除热炼工艺在热炼机上完成外,其它工 工序由挤出机联动装置流水作业完成。
冷喂料压出工艺采用复合压出,工艺流程为:割条→冷 喂料→复合压出→输送 (自然冷却)→收缩辊道→预秤 量、扫锚(各部位尺寸)→冷却→自动打印→自动定长 →裁断→称量→检验→存放。
胎面压出工艺条件
冷喂料复合压出机在胎面压出后,首先 自然冷却,再经收缩辊道定型,迸入冷 却水槽,其中喷淋冷却25m,浸泡冷却 1OOm。
第二章 轮胎的成型工艺
(一)轮胎制造工艺流程和准备工艺 1、胎面压出 (4)胎面压出常见的质量缺陷及产生原因 胎面内部有气孔 产生原因为:原材料中水分或挥发物多;热炼工艺不
第二章 轮胎的成型工艺
(一)轮胎制造工艺流程和准备工艺 2、帘布压延 (2)压延工艺要求 温度:供胶温度应保持均匀稳定,一般约90℃。压延机辊筒温
度,上辊、中辊为100±5℃,旁辊、下辊为95±5℃。帘布温 度保持在70℃左右 速度∶用V1、V2、V3,V4表示旁轴、上辊、中辊和下辊的速度, 辊筒速度之间的关系,贴胶时帘布通过的上辊、中辊速度必须 相等,旁辊与下辊速度相等,两面贴胶时,则彼此关系为 V2=V3≥V1=V4)即V1:V2:V3:V4为1:1.4:1.4:1 帘布张力:张力在1.5kN/根左右 帘布厚度:帘布上下层挂胶厚度分别为0.4~0.5mm 缓冲层上 下挂胶厚度为0.65~0.7Omm。压延后挂胶帘布在存放过程中, 因 收 缩 使 得 压 延 厚 度 增 加 , 增 厚 比 值 一 般 约 为 1.05 ~ 1 .l0
↓
↓ 外胎定型
↓
内胎硫化
↓
↓ 外胎硫化
↓
↓
内胎检验
垫带检验
外胎成品检验
↓
↓
配
套
↓
入
库
包
装
帘帆布干燥
↓↓ 帘帆布压延 ↓
裁断 ↓ 帘 布 筒 贴 合、
↓ 型
第二章 轮胎的成型工艺
(一)轮胎制造工艺流程和准备工艺
1、胎面压出 (1)胎面的结构形式
轮胎胎面的胎冠和 胎侧的作用不同,胶料 的性能要求不同。一般 有如下几种形式: ① 一方一块 ② 两方两块(a) ③ 两方三块(b) ④ 三方四块(c) ⑤ 四方五块
胎面压出工艺条件
热喂料压出法的胎面压出后,通常采用水槽或 喷淋等方法冷却半成品胎面。冷却过程中,为 防止压出胶料因骤冷而引起局部收缩及喷霜, 水槽宜用分段逐步冷却方法,水槽长度不应过 短,可高达1OOm以上,第一段冷却水温度稍 高,约为4O℃,第二段冷却水温度略低,第三 段冷却水温度最低,可降到2O℃左右,对半成 品胎面的存放有利。喷淋法冷却胎面效率较高, 但冷却水温度要求低于2O℃,以12~15℃为宜。
第二章 轮胎的成型工艺
(一)轮胎制造工艺流程和准备工艺 1、胎面压出 (3)胎面压出工艺条件
冷却 半成品胎面的冷却程度影响压出质 量。胎面胶压出离开口型时,胶温高达 120℃以上,极易产生热变形,加速其收缩 定型;影响规格尺寸的稳定性,同时在存 放过程中容易焦烧,因此,必须将胶温降至 40℃以下,才能获得充分冷却。
第二章 轮胎的成型工艺
(一)轮胎制造工艺流程和准备工艺 1、胎面压出 (3)胎面压出工艺条件
压出温度:胎面压出前,首先预热机头、 机身及口形板,供胶温度控制在80~90℃ 左右。一般挤出机机筒温度为40±5℃, 机头温度为80±5℃,口型板温度为 85±5℃,不应超过100℃,排胶温度应 小于120℃。
第二章 轮胎的成型工艺
(一)轮胎制造工艺流程和准备工艺 1、胎面压出 (3)胎面压出工艺条件
压出速度:挤出机压出速度直接影响胎面半成品的规格及致密 性,压出速度快,胎面半成品膨胀率及收缩率增大,表面粗 糙;压出速度慢,半成品表面光滑,保证胎面压出质量。
压出速度即单位时间内压出长度(m/min)。压出速度的 快 慢 取 决 于 挤 出 机 的 螺 杆 转 速 , 一 般 转 速 范 围 在 30 ~ 5Or/mjn时,压出速度为4~12m/min。压出速度的快慢根据 轮胎规格而定,大规格胎面压出速度应比小规格胎面压出 速度慢。压出速度还与生胶品种、胶料含胶率、可塑度、 压出温度等因素有关,天然橡胶胎面压出速度应比合成胶 胎面压出速度慢。
第二章 轮胎的成型工艺
张 馨 高分子材料实训中心
2008年3月
第二章 轮胎的成型工艺
(一)轮胎制造工艺流程和准备工艺 其中工序包括:胶料混塑炼、
胎体帘帆布压延、胎面压出、胶帘 帆布裁断、钢丝圈制造、贴合、成 型、硫化等
轮胎制造工艺流程见下图:
轮胎制造工艺流程图:
生胶及原材料加工、称量
↓ 密炼机塑、混炼