可靠性设计分析ReliabilityDesignandAnalysis
可靠性分析报告

可靠性分析报告品质是设计出来而不是制造出来,广义的品质除了外观、不良率外、还需兼长期使用下的可靠性,因此,在开发新产品前之可靠性预估及开发的实验推断相互印证是很重要的,本篇即针对可靠性分析的一般术语,如何事前预估,事后实验推断以及如何做加速试验及寿命试验做个说明.1. 概论:(1) 何谓可靠性(Reliability)?可靠性系指某种零件或成品在规定条件下,且于指定时间内,能依要求发挥功能的概率,即时间t 时的可靠性R(t)=(例) 假设开始时有100件物品参与试验,500小时后剩80件,则500小时后的可靠性R(t=500)为80/100=0.8简单地说,可靠性可看为残存率.(2) 何谓瞬间故障率(Hazard Rate ,Failure Rate),时间t 时每小时之故障数瞬间故障率h (t )=时间t 时之残存数上例中,若500小时后剩80件,若当时每小时故障数为两件,则第500小时之瞬间故障为2/80=2.5%换句话说,瞬间故障率系指时间t 时,尚未发生故障的物件,其单位时间内发生故障之概率.时间t 时残存数 开始时试验总数(3)浴缸曲线(Bath Tub Curve)瞬间故障率h(t)h(t)=常数=恒定故障率时期耗竭期Period periodA.早期故障期:a.设计上的失误(线路稳定度Marginal design)b.零件上的失误(Component selection & reliability)c.制造上的失误(Burn-in testing)d.使用上失误。
一般产品之Burn-in 即要消除早期故障(Infant Mortality)使客户接到手时已经是恒定故障率h(t)=B、恒定故障率期:此时故障为random,为真正有效使用此段时期越长越好。
C、耗竭故障期;零件已开始耗竭,故障率急剧增加,此时维护重置成本为高。
(4)平均故障间隔时间(Mean Time Between Failure,MTBF)当故障率几乎为恒定时(若0.002/小时),此时进行10000小时约有0.002/小时*10000小时=20个故障,即平均500小时会发生一次故障,故MTBF 为500小时,为0.002/小时的倒数,即MTBF=1/λ.λ可看成频率(Frequency),MTBF即代表周期(Period)(5)、可靠性R(t)之数学表示根据实验及统计推行,要恒定故障期,R(t=)随着时间的增加而呈指数递减(Exponentially decreasing)当t=0时,因尚无任何故障,故R(t=0)=1t=∞以数学表示,R(t)即R(t)=e-λt其中λ即为恒定故障期之瞬间故障率t (6)、恒定故障期时MTBF与R(t)的关系,由前,R(t)=e-λt λ=1/MTBF故R(t)=e-t/MFBF当t=MTBF时,R(t)=e-MTBF/MFBF=e-1 ≒0.37即在恒定故障期时,试验至t=MTBF时,其可靠性(即残存比率)为37%,即约有63%故障.2新产品(MTBF Time Between Failure)之事前预估(1) 系统可靠性与组件可靠性之关系一般系统可靠性之计算时有下列假设:A 、 每个组件有独立之λi ,即甲组件故障不影响乙组件。
可靠性分析Reliability Analysis
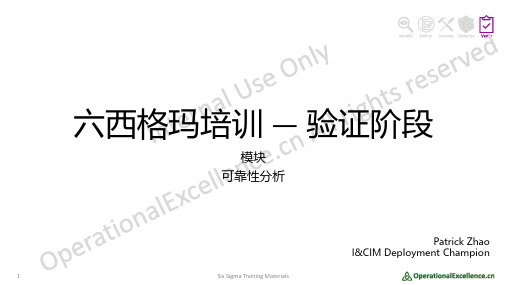
六西格玛培训—验证阶段模块可靠性分析Patrick ZhaoI&CIM Deployment Champion可靠性分析介绍执行可靠性分析可靠性分析介绍执行可靠性分析可靠性与质量•狭义的质量,一般指的是符合性质量,即是否满足标准或规范,通常是以产品出厂时的状态为准,此时传统的质量控制人员已经完成任务。
•可靠性更多关注在产品的全生命周期中的质量表现,即产品是否能够始终满足标准,始终满足客户的应用。
在如今全面质量管理的阶段,产品的可靠性也越来越需要企业投入更多的时间。
•企业中的可靠性分析可以分为产品和过程:•产品:分析产品在客户使用中是否满足可靠性目标。
•过程:一般指设备、工装、模具等在长期使用过程中,是否会出现问题。
可靠性工程的益处•在物质匮乏的年代,衣服可能是作为耐用品使用,而如今衣服已经越来越成为快速消费品。
曾经的手机等电子产品,更换周期也同样有越来越短的趋势。
甚至是汽车也开始加速迭代,不停缩短换车的时间。
•在这样的背景下,可靠性似乎成为了一个不是那么重要的关注点,可是为什么我们仍然在关注可靠性工程?•政府、法规的要求。
•不可靠的产品通常有安全或健康风险。
•产品变得复杂,零件变多,更容易发生故障。
•可靠性的优势可以成为销售和市场部门的宣传点。
•处于保护环境,节约资源的考虑。
可靠性分析的常用术语•浴缸曲线(Bathtub Curve)•MTTF: Mean Time To Failure(平均失效前时间)•MTTR: Mean Time To Repair(平均修复时间)•MTBF: Mean Time Between Failure(平均故障发生间隔时间)•威布尔分布(Weibull Distribution)•数据删失(Data Censoring)•HALT: Highly Accelerated Life Testing(高加速寿命试验)•HASS: Highly Accelerated Stress Screening(高加速应力筛选)•HASA: Highly Accelerated Stress Audit(高加速应力稽核/抽检)浴缸曲线•浴缸曲线(Bathtub Curve)在可靠性分析中是一种常用的概念,它把失效分为三个阶段。
复杂产品的六性指标分析与设计研究
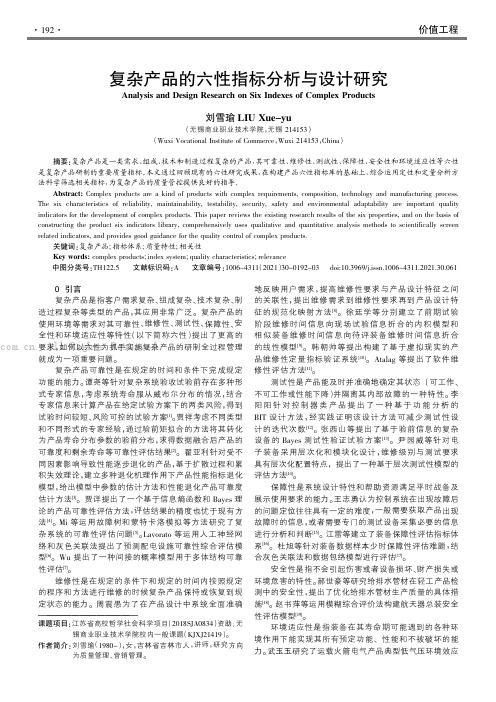
0引言复杂产品是指客户需求复杂、组成复杂、技术复杂、制造过程复杂等类型的产品,其应用非常广泛。
复杂产品的使用环境等需求对其可靠性、维修性、测试性、保障性、安全性和环境适应性等特性(以下简称六性)提出了更高的要求,如何以六性为抓手实施复杂产品的研制全过程管理就成为一项重要问题。
复杂产品可靠性是在规定的时间和条件下完成规定功能的能力。
谭尧等针对复杂系统验收试验前存在多种形式专家信息,考虑系统寿命服从威布尔分布的情况,结合专家信息来计算产品在给定试验方案下的两类风险,得到试验时间较短、风险可控的试验方案[1]。
贾祥考虑不同类型和不同形式的专家经验,通过验前矩拟合的方法将其转化为产品寿命分布参数的验前分布,求得数据融合后产品的可靠度和剩余寿命等可靠性评估结果[2]。
翟亚利针对受不同因素影响导致性能逐步退化的产品,基于扩散过程和累积失效理论,建立多种退化机理作用下产品性能指标退化模型,给出模型中参数的估计方法和性能退化产品可靠度估计方法[3]。
贾详提出了一个基于信息熵函数和Bayes 理论的产品可靠性评估方法,评估结果的精度也优于现有方法[4]。
Mi 等运用故障树和蒙特卡洛模拟等方法研究了复杂系统的可靠性评估问题[5]。
Lavorato 等运用人工神经网络和灰色关联法提出了预测配电设施可靠性综合评估模型[6]。
Wu 提出了一种间接的概率模型用于多体结构可靠性评估[7]。
维修性是在规定的条件下和规定的时间内按照规定的程序和方法进行维修的时候复杂产品保持或恢复到规定状态的能力。
周震愚为了在产品设计中系统全面准确地反映用户需求,提高维修性要求与产品设计特征之间的关联性,提出维修需求到维修性要求再到产品设计特征的规范化映射方法[8]。
徐廷学等分别建立了前期试验阶段维修时间信息向现场试验信息折合的内积模型和相似装备维修时间信息向待评装备维修时间信息折合的线性模型[9]。
韩朝帅等提出构建了基于虚拟现实的产品维修性定量指标验证系统[10]。
可靠性设计 百度百科-免费的
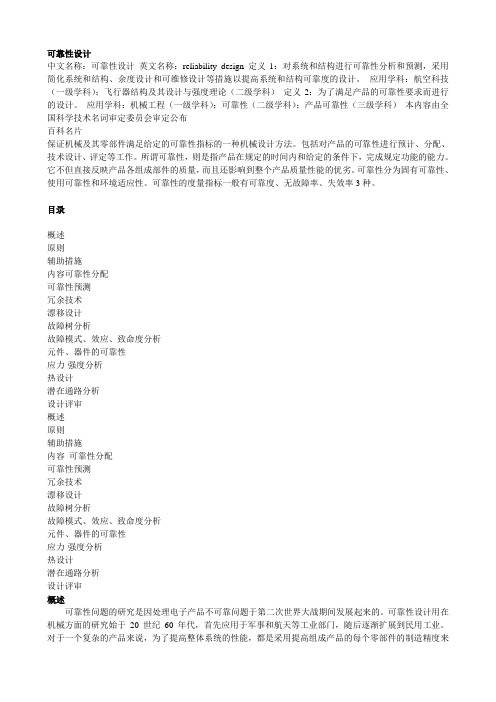
可靠性设计中文名称:可靠性设计英文名称:reliability design 定义1:对系统和结构进行可靠性分析和预测,采用简化系统和结构、余度设计和可维修设计等措施以提高系统和结构可靠度的设计。
应用学科:航空科技(一级学科);飞行器结构及其设计与强度理论(二级学科)定义2:为了满足产品的可靠性要求而进行的设计。
应用学科:机械工程(一级学科);可靠性(二级学科);产品可靠性(三级学科)本内容由全国科学技术名词审定委员会审定公布百科名片保证机械及其零部件满足给定的可靠性指标的一种机械设计方法。
包括对产品的可靠性进行预计、分配、技术设计、评定等工作。
所谓可靠性,则是指产品在规定的时间内和给定的条件下,完成规定功能的能力。
它不但直接反映产品各组成部件的质量,而且还影响到整个产品质量性能的优劣。
可靠性分为固有可靠性、使用可靠性和环境适应性。
可靠性的度量指标一般有可靠度、无故障率、失效率3种。
目录概述原则辅助措施内容可靠性分配可靠性预测冗余技术漂移设计故障树分析故障模式、效应、致命度分析元件、器件的可靠性应力-强度分析热设计潜在通路分析设计评审概述原则辅助措施内容可靠性分配可靠性预测冗余技术漂移设计故障树分析故障模式、效应、致命度分析元件、器件的可靠性应力-强度分析热设计潜在通路分析设计评审概述可靠性问题的研究是因处理电子产品不可靠问题于第二次世界大战期间发展起来的。
可靠性设计用在机械方面的研究始于20世纪60年代,首先应用于军事和航天等工业部门,随后逐渐扩展到民用工业。
对于一个复杂的产品来说,为了提高整体系统的性能,都是采用提高组成产品的每个零部件的制造精度来达到;这样就使得产品的造价昂贵,有时甚至难以实现(例如对于由几万甚至几十万个零部件组成的很复杂的产品)。
事实上可靠性设计所要解决的问题就是如何从设计中入手来解决产品的可靠性,以改善对各个零部件可靠度(表示可靠性的概率)的要求。
可靠度的分配是可靠性设计的核心。
常见可靠性分析方法

常见可靠性分析方法
常见可靠性分析方法包括:
1.故障模式和影响分析(Failure Mode and Effects Analysis,FMEA):通过识别系统的潜在故障模式、分析其对系统性能的影响和评估控制风险,以提高系统的可靠性。
2.故障树分析(Fault Tree Analysis,FTA):通过创建逻辑关系的树状结构,分析系统故障的可能原因、概率和严重性,并确定系统的可靠性。
3.可靠性块图分析(Reliability Block Diagram,RBD):通过将系统分解为可靠性块,分析各个块的可靠性,以评估系统的整体可靠性。
4.可靠性增长分析(Reliability Growth Analysis,RGA):通过分析故障发现、修复和测试周期的数据,预测系统在未来的使用中可能的可靠性增长。
5.可靠性试验分析(Reliability Testing Analysis,RTA):通过设计和执行可靠性试验,分析试验结果,评估系统的可靠性。
6.故障模式、效果和关联分析(Failure Mode, Effects, and Criticality Analysis,FMECA):对系统的故障模式进行有序的分析和评估,以确定故障的影响和严重性。
7.可靠性统计分析(Reliability Statistics Analysis):通过统计方法对系统故障数据进行分析,计算系统的可靠性指标,例如平均故障间隔时间(Mean Time Between Failures,MTBF)和平均修复时间(Mean Time To Repair,MTTR)。
注意:以上只是常见的可靠性分析方法,并不是所有可靠性问题都适用于这些方法,具体的分析方法应根据具体情况选择。
工程设计中的可靠性分析与优化

工程设计中的可靠性分析与优化随着信息化和智能化的快速发展,现代化社会对于工程的需求也越来越高。
作为工程的核心部分,设计对于工程的可靠性有着至关重要的影响。
在工程设计中,可靠性分析和优化是必不可少的环节,其目的是提高工程的可靠性,减少其故障率和维修成本,提高其生产效率和经济效益。
一、可靠性分析的基本概念可靠性分析是指对工程设计中可能存在的各种故障和失效情况进行分析和评估,以确定工程的可靠性和失效率。
其主要包括故障模式分析、失效模式和影响分析、可靠性试验等几个方面。
故障模式分析(FMEA)是指对于可能导致故障的因素进行分析和评估,以确定故障的可能性和影响范围。
失效模式和影响分析(FMECA)是针对故障模式的进一步分析,确定故障的影响程度和应对措施。
可靠性试验(Reliability Test)是通过测试的方式来检测工程设备的可靠性,确定故障率和失效率等参数,为后续的优化提供依据。
二、可靠性优化的基本方法可靠性优化是指通过对工程设计的改进,减少故障率和维修成本,提高生产效率和经济效益。
其主要包括设计改进、故障预测和预防、优化维护等几个方面。
设计改进是指通过改进设计、材料、结构和工艺等方面来提高工程的可靠性。
首先要考虑设计模式的合理性和精准性,通过模拟和优化分析,消除隐患和缺陷,提高工程的性能和安全性。
其次,要考虑材料和工艺的优化,选取合适的材料和工艺,提高工程的长期稳定性和可维护性,以降低故障率和维修成本。
故障预测和预防是指通过对故障模式进行分析和预测,预防故障的发生和扩散。
其主要包括故障预测、测试和检测、故障处理和故障分析等几个方面。
针对可能出现的故障情况进行预判和处理,选取合适的预防措施,以及尽早发现和处理故障现象,减少其影响范围和次生损失。
优化维护是指通过对维护方式进行优化和改进,提高维护效率和经济效益,减少维护成本和故障率。
其主要包括维护计划和策略、维修流程和方法、提高技术水平等几个方面。
采用有效的维护策略和技术手段,提高维修的准确率和效率,降低停机时间和维修成本,以保障工程的长期稳定运行。
可靠性工程师热设计指南英文
可靠性工程师热设计指南英文英文回答:Reliability engineering is a critical aspect of product development and design. As a reliability engineer, I am responsible for ensuring that the products we create are dependable and meet the expectations of our customers. In order to achieve this, there are several key guidelinesthat I follow.First and foremost, it is essential to understand the requirements and expectations of our customers. This involves conducting thorough market research and gathering feedback from customers to identify their needs. By understanding what our customers value the most, we can prioritize our design efforts and focus on the areas that are most critical for reliability.Next, I pay close attention to the design phase of the product development process. This is where the foundationfor reliability is laid. I work closely with the design team to identify potential failure modes and develop strategies to mitigate them. For example, if we are designing a mobile phone, we would consider factors such as the robustness of the hardware, the durability of the screen, and the reliability of the battery.Additionally, I utilize various reliability analysis techniques to assess the reliability of our products. This includes techniques such as failure mode and effects analysis (FMEA) and reliability block diagrams (RBD). These tools help me identify potential failure points in the system and prioritize areas for improvement. By conducting these analyses, we can proactively address potential reliability issues before they become a problem for our customers.Furthermore, I collaborate closely with other departments such as manufacturing and quality assurance to ensure that our products are manufactured and tested to meet the highest reliability standards. This involves conducting regular audits of our manufacturing processes,implementing rigorous quality control measures, and continuously monitoring the performance of our products in the field.In conclusion, as a reliability engineer, my role is to ensure that our products are reliable and meet the expectations of our customers. By understanding customer needs, focusing on design, utilizing reliability analysis techniques, and collaborating with other departments, wecan create products that are dependable and trusted by our customers.中文回答:可靠性工程是产品开发和设计的重要方面。
产品可靠性设计报告
产品可靠性设计报告1. 引言本报告旨在分析和评估产品的可靠性设计,并提出可靠性改进措施。
产品可靠性是指产品在特定使用条件下,保持满足要求功能和性能的能力。
高可靠性是现代产品设计中至关重要的一个特征,因为它关乎用户的安全和满意度。
通过对产品进行可靠性分析和改进,可以减少故障率、延长产品的使用寿命,提高产品的市场竞争力。
2. 可靠性分析为了评估产品的可靠性设计,我们采用了以下方法进行可靠性分析:2.1. 故障模式与影响分析(FMEA)故障模式与影响分析(Failure Mode and Effects Analysis,FMEA)是一种用于分析和评估系统、组件或过程中潜在故障模式及其影响的方法。
在本次可靠性分析中,我们对产品的不同部件和系统进行了FMEA分析。
2.2. 可靠性块图(Reliability Block Diagram,RBD)可靠性块图是一种图形化方法,用于分析系统中不同组件之间的可靠性关系。
通过构建可靠性块图,我们可以评估系统中关键组件的可靠性,并确定潜在的故障点。
2.3. 可靠性测试通过实际测试和模拟实验,我们对产品进行了可靠性测试。
测试包括环境适应性测试、振动测试、温度和湿度测试等。
通过测试,我们发现了产品在一些特定条件下的故障模式,并根据测试结果进行了相应的改进。
3. 可靠性改进措施基于可靠性分析的结果,我们提出了以下可靠性改进措施:3.1. 设计优化通过对产品设计的优化,可以减少故障发生的概率。
我们将加强对关键部件和系统的设计验证,并增加冗余机制,以提高产品的可靠性。
同时,我们还将采用更耐用和可靠的材料,以延长产品的使用寿命。
3.2. 生产过程控制在生产过程中,我们将加强对关键工艺参数的控制,并建立完善的质量控制和检测机制。
通过提高生产过程的可控性,能够有效降低产品的制造缺陷率,提高产品的可靠性。
3.3. 供应链管理供应链管理对于产品可靠性至关重要。
我们将与供应商建立长期稳定的合作关系,并加强对供应商的审核和监督。
微电子封装技术中的可靠性设计与分析
微电子封装技术中的可靠性设计与分析第一章:引言随着微电子技术的迅猛发展,封装技术作为微电子技术中至关重要的一环,对于保证芯片的可靠性和稳定性起着关键作用。
本文将对微电子封装技术中的可靠性设计与分析进行探讨和研究。
第二章:微电子封装技术概述微电子封装技术是将芯片与外部环境隔离,并提供保护和连接功能的一种技术。
该技术可以分为无源封装和有源封装两大类,其中无源封装主要用于电子元器件或被动元件,有源封装主要用于集成电路芯片等。
第三章:微电子封装技术中的可靠性设计在微电子封装技术中,可靠性是至关重要的设计指标。
可靠性设计需要从以下几个方面考虑:1. 热管理:合理设计散热结构,保证芯片工作温度的稳定和可控;采用热传导材料和散热装置,有效地降低芯片温度,提高其可靠性。
2. 电磁兼容性:合理设计封装结构,以减少电磁干扰对芯片性能的影响;采用电磁屏蔽措施,提高封装结构对电磁波的屏蔽能力。
3. 机械可靠性:针对不同的应用场景和环境,选择合适的封装材料和结构,以提高封装的机械强度和抗震性能。
4. 寿命预测:通过可靠性测试和模拟,对封装结构进行寿命预测和分析,以预测其在实际使用中的可靠性水平。
第四章:微电子封装技术中的可靠性分析方法对于微电子封装技术中的可靠性分析,可以采用以下几种方法:1. 应力分析:通过应力分析软件模拟封装结构在不同工作状态下的应力分布情况,以评估其结构的强度和稳定性。
2. 可靠性测试:采用加速寿命测试方法,对封装结构进行长时间高负荷的可靠性测试,以评估其在实际使用中的寿命和可靠性水平。
3. 故障分析:对实际使用中出现的封装结构失效进行系统的故障分析,找出导致失效的原因,并采取相应的改进措施。
第五章:案例研究通过对几个典型的微电子封装技术案例进行研究,分析其可靠性设计和分析方法的应用效果,以及相应的问题和改进措施。
第六章:总结与展望本文对微电子封装技术中的可靠性设计与分析进行了系统的探讨和研究。
通过合理的设计和分析方法,可以提高微电子封装技术的可靠性和稳定性,为微电子工程提供更可靠的基础。
机械工程中的可靠性分析与优化设计
机械工程中的可靠性分析与优化设计在机械工程中,可靠性是一个至关重要的概念。
机械设备的可靠性决定了它们是否能够在设计寿命内正常运行,而可靠性分析与优化设计则是确保机械设备具有高度可靠性的关键。
可靠性分析是通过对机械设备的各种故障形式和失效原因进行分析,以确定可能导致失效的主要因素。
这些因素可以包括材料质量、制造工艺、工作环境等等。
通过对这些因素的分析,可以找出引起故障的根本原因,并采取相应的措施来提高机械设备的可靠性。
一种常用的可靠性分析方法是故障模式和效应分析(Failure Mode and Effects Analysis,简称FMEA)。
FMEA的基本原理是通过分析潜在的失效模式和它们对系统性能的影响,来确定机械设备中的关键零部件和失效途径。
通过对失效途径的分析,可以找出引起故障的原因,并采取相应的措施来预防故障的发生。
而在可靠性优化设计方面,一种常用的方法是可靠性设计优化(Reliability-based Design Optimization,简称RBDO)。
RBDO是一种结合了可靠性分析和优化技术的方法,旨在通过将可靠性约束嵌入到设计优化过程中,以实现对机械设备的可靠性进行优化。
在RBDO中,首先需要对机械设备的可靠性进行分析,确定失效概率和可靠度等指标。
然后,在设计优化过程中,将这些可靠性指标作为约束条件,以保证设计方案具有足够的可靠性。
通过不断优化设计方案,可以得到一个在可靠性和性能方面都达到最优的机械设备。
除了这些传统的可靠性分析与优化方法外,近年来一些新兴的技术也被应用到机械工程中的可靠性分析与优化设计中。
例如,基于故障树分析(Fault Tree Analysis,简称FTA)的可靠性分析方法可以更加直观地描述故障的发生途径;而基于人工智能技术的优化算法如遗传算法、神经网络等能够更高效地搜索最优解。
需要注意的是,机械工程中的可靠性分析与优化设计应该考虑的因素众多。
除了上述提到的材料质量、制造工艺、工作环境等外,还包括设计参数的选择、零部件的可靠性要求、运输和安装过程中的影响等。
- 1、下载文档前请自行甄别文档内容的完整性,平台不提供额外的编辑、内容补充、找答案等附加服务。
- 2、"仅部分预览"的文档,不可在线预览部分如存在完整性等问题,可反馈申请退款(可完整预览的文档不适用该条件!)。
- 3、如文档侵犯您的权益,请联系客服反馈,我们会尽快为您处理(人工客服工作时间:9:00-18:30)。
详细设计准则
❖将产品的可靠性设计准则以“XX可靠性设计准则”条
款形式输出。
9
可靠性定性分析要求
❖ 定性分析要求
定性分析要求一般是在产品研制过程中要求采取 的可靠性分析工作,以保证与提高产品可靠性。
这些可靠性分析工作需要在产品研制的各个阶段 根据产品的实际情况和分析方法的特点,具体组 织实施。
10
可靠性定性分析要求
在定量化设计分析缺乏大量数据支持的情况下, 提出定性设计分析要求并加以实现则更为重要。
❖ 可靠性定性要求分类
定性设计要求 定性分析要求
4
可靠性定性设计要求
❖ 定性设计要求概念
定性设计要求一般是在产品研制过程中要求采取的 可靠性设计措施,以保证与提高产品可靠性。
这些要求都是概要性的设计措施,在具体实施时, 需要根据产品的实际情况而细化。
❖ 定性分析要求主要项目
功能危险分析(FHA) 故障模式和影响分析(FMEA) 故障树分析(FTA) 区域安全性分析(ZSA)
11
可靠性定量要求
❖ 可靠性定量要求概念
确定产品的可靠性参数、指标以及验证时机和验 证方法,以便在设计、生产、试验验证、使用过 程中用量化方法评价或验证装备的可靠性水平。
可靠性参数要反映战备完好性,任务成功性,维 修人力费用及保障资源费用等四个方面的要求。
16
❖ 在轨工卫作可星靠可度靠性参数举例
卫星在轨工作期间的成功概率。
❖ 在轨工作寿命
卫星在轨工作时间。也称为在轨服务寿命、 在轨任务时间。
❖ 返回型卫星返回可靠度
17
❖ 平均任卫务持星续可时靠间(性M参MD数)举例
综合反映卫星在轨工作可靠性和在轨工作寿 命的一个参数。
❖ 单点失效概率
卫星上单点失效项目在轨工作寿命终期的失 效概率。
❖ 主要的定性设计要求示例
制定和贯彻可靠性设计准则
简化设计
余度设计
5
可靠性设计准则
❖ 可靠性设计准则含义
在研制过程中尽可能充分挖掘研制单位已有的工程 经验,把设计人员多年积累的设计经验与教训加 以总结提高,形成可靠性设计标准和指令性文件。
指导工程设计人员如何把产品的可靠性设计到产 品中去。
用可靠性设计准则逐条审查设计的符合性,完成 设计准则符合性报告,供设计评审时使用。
❖ 贮存期限
即储存寿命,指产品在规定的条件下储存时,仍 能满足规定质量要求的时间长度。
15
卫星可靠性参数举例
❖ 任务可靠度
卫星从发射准备到在轨工作到规定时间或回收的 成功概率。发射准备指卫星进入发射阵地到运载 火箭点火前这段时间。
❖ 在轨测试交付可靠度
卫星发射入轨道或定点后,在交付使用之前对其 功能(例如通信或遥感能力等)进行在轨测试的 成功概率。
度量的可靠性要求,它更多的是从承制方的角度来评
价产品的可靠性水平。
19
MTBF、MTBCF
可靠性指标
❖ 可靠性指标含义
可靠性指标是可靠性参数要求的量值。如 MTBF=1000H即为可靠性指标。
与使用、合同参数相对应,可靠性指标分为可靠 性使用指标和可靠性合同指标。
20
可靠性定量要求特性
❖ 目成标熟期值目标 、值门限值、规定值、最低可接受值 成熟期门限值
常用可靠性参数举例
❖ 平均故障间隔时间MTBF
在规定的条件下和规定的时间内,产品的寿命单 位总数与故障总次数之比。
❖ 任务可靠度MR
产品在规定的任务剖面内完成规定功能的概率。
❖ 工作寿命
产品从开始工作到报废为止的全部工作时间。
14
常用可靠性参数举例
❖ 首次翻修期限
在规定条件下,产品从交付(或开始使用)到首 次经基地或工厂大修(或翻修)的工作时间和 (或)日历持续时间。
研制阶段 目标值
研制阶段 门限值
设计 定型
生产 定型
批生产
大量部署 和使用
21
论证阶段
可靠性参数值时序图
方案阶段
工程研制阶段
目的
❖说明编制可靠性设计准则的目的。
适用范围
❖应说明编制的可靠性设计准则适用于何产品或何系列 产品 。
8
可靠性设计准则
❖ 主要内容
依据
❖应说明编制可靠性设计准则的主要依据。
合同规定的可靠性定性、定量要求;
合同规定引用的有关规范、标准、手册等提出的可靠性设计 准则;
同类型产品的可靠性设计经验以及可供参考的通用可靠性设 计准则。
目录
❖ 可靠性要求概念 ❖ 可靠性定性要求 ❖ 可靠性定量要求 ❖ 可靠性定量要求制定 ❖ 可靠性定性要求制定
1
可靠性要求
❖ 可靠性要求
产品使用方向承制方(或生产方)从可靠性角度提出 的研制目标。
进行可靠性设计、分析、制造、试验和验收的依 据。
只有在透彻地了解这些要求后,才能将可靠性正 确地设计、生产到产品中去,并按要求有计划地 实施有关的组织、监督、控制及验证工作。
2
可靠性要求
❖ 可靠性要求分类
定性要求
❖用一种非量化的形式来设计、评价和保证产品的可靠 性。
定量要求
❖规定产品的可靠性参数、指标和相应的验证方法。 ❖用定量方法进行设计分析,进行可靠性验证,从而保
证产品的可靠性。
3
❖ 可靠性定性可要靠求性概念定性要求
用一种非量化的形式来设计、评价和保证产品的
12
可靠性定量要求
❖ 可靠性定量要求分类
基本可靠性要求
❖基本可靠性反映了产品对维修人力费用和后勤保障资 源的需求。
❖确定基本可靠性指标时应统计产品的所有寿命单位和 所有的故障。
任务可靠性要求
❖任务可靠性是产品在规定的任务剖面中完成规定功能 的能力。
❖确定任务可靠性指标时仅考虑在任务期间那些影响任13 务完成的故障(即致命性故障)。
❖ 贮存寿命 ❖ 贮存期测试周期 ❖ 贮存可靠性
18
可靠性定量要求参数类别
❖ 参数类别
使用参数
❖使用可靠性参数及指标反映了系统及其保障因素在计 划的使用和保障环境中的可靠性要求,它是从最终用 户的角度来评价产品的可靠性水平。
MFHBF、MCSP、MTBM
合同参数
❖合同可靠性参数及指标反映了合同中使用的易于考核
6
可靠性设计准则
❖ 可靠性设计准则作用
可靠性设计准则是进行可靠性定性设计的重要依 据。
贯彻可靠性设计准则可以提高产品的固有可靠性。 可靠性设计准则是把可靠性设计和性能设计有机
结合的有效方法。 可靠性设计准则是一个单位产品设计经验的总结
与升华。
7
可靠性设计准则
❖ 主要内容
概述
❖说明产品名称、型号、功能和配套关系;产品合同规 定的可靠性定性、定量要求等 。