QC成果(降低布料小车故障停机时间)
qc工程成果案例

qc工程成果案例QC工程成果案例:1. 提高产品质量:某电子产品公司在QC工程的指导下,对产品的生产流程进行了全面优化和改进,通过减少生产环节、优化工艺流程、提高生产设备的稳定性等措施,使产品的不良率下降了30%,大大提高了产品的质量水平。
2. 降低生产成本:一家制造业公司在QC工程的帮助下,通过精细化管理和优化生产过程,成功降低了生产成本。
他们通过优化供应链管理,减少了物料的浪费和库存,优化生产计划,减少了人力资源的浪费,使得公司的生产成本降低了20%,提高了企业的竞争力。
3. 缩短交付周期:一家制造业公司在QC工程的引导下,对产品的生产流程进行了优化,通过减少非价值增加的工序,优化工艺流程,提高设备的利用率,成功将产品的交付周期缩短了50%,大大提高了客户的满意度。
4. 改善员工满意度:一家公司在QC工程的指导下,对员工的工作环境和工作条件进行了改善,增加了员工的参与度和自主性。
通过员工培训和技能提升,使得员工的工作效率和满意度大幅提高,减少了员工的离职率,提高了公司的稳定性和持续发展能力。
5. 提高供应商质量:一家公司在QC工程的指导下,对供应商进行了全面的评估和管理,建立了供应商质量管理体系,通过定期的供应商考核和反馈机制,使得供应商的质量水平得到了明显提升,减少了因供应商质量问题带来的产品返工和退货,提高了公司的供应链的稳定性和可靠性。
6. 安全生产提升:一家制造业公司在QC工程的引导下,对生产现场的安全管理进行了全面的改进和优化。
通过加强安全培训和意识教育,制定并执行安全操作规程,改善现场的安全设施和环境,成功降低了事故发生率,提高了员工的安全意识和安全行为,保障了生产过程的安全稳定。
7. 产品创新改进:一家公司在QC工程的指导下,对产品进行了全面的市场调研和用户需求分析,通过优化产品设计和工艺流程,提高了产品的性能和品质。
通过不断的创新和改进,使得公司的产品在市场上获得了更高的竞争力,提高了公司的盈利能力和市场份额。
降低车辆维修成本QC课题成果报告
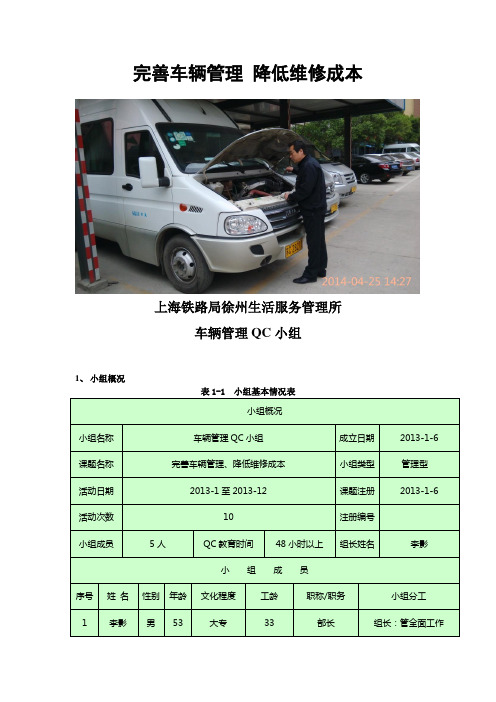
完善车辆管理降低维修成本上海铁路局徐州生活服务管理所车辆管理QC小组1、小组概况表1-1 小组基本情况表制表:乔文举校核:李影制表时间:2013年1月7日2、选择课题2.2活动计划表2-1 小组活动计划表制表:乔文举校核:李影制表时间:2013年1月10日3、现状调查:制表:乔文举校核:李影时间:2013年1月25日3.3 对车辆维修流程进行调查图3-1 车辆维修流程图:制图:乔文举校核:李影时间:2013年1月25日制表:乔文举 校核:李影时间:2013年2月10日制表:乔文举 校核:李影 时间:2013年2月12日 调查结果:我所现有12辆正常使用的车辆,因维修过程控制不严和修理厂原因造成车辆维修成本偏高。
4、设定目标4.1 2013年车辆维修费比上年度同期下降10%:图4-14.2 目标设定依据:根据现状调查,通过分析对比,从车辆维修方面及车辆使用可以设定目标:2013年车辆修理费比2012年下降10%。
制表:乔文举校核:李影日期:2013年2月18日5、分析原因5.1 分析原因:目标设定后,小组成员充分发挥大家的经验及所想,开阔思路,集思广益,对造成“车辆维修费高”的的原因进行分析和归纳,并用关联图对有关原因进行了整理:5.2确定主要原因:表5-1 确定主要原因序号因素名称确定方法确认情况是否要因参加人员1 没有进行必要教育培训调查分析1、每周和每月都进行安全例会和案例分析,对司机进行思想教育和安全、枝术、行车经验上进行交流;2、不定期进行业务技能培训;3、每年都进行有关驾驶枝能考核和绩效考核;4、公司设置安全专职实行技术指导和监督;5、不定期到车间对车辆进行安检和对司机进行行车指导。
否小组全体人员2 车辆保养制度不健全调查分析1、公司已有健全的车辆保养制度;2、车辆严格按车辆保养制度进行保养。
否小组全体人员3 车辆设计存在缺陷讨论分析厂家原有设计问题,客观存在,QC小组无法改变,目前还没有发现因设计原因而需进行维修的项目。
电力行业优秀QC成果-减少一体化远动系统故障次数

02
提高了电力企业的生产效率和经济效益,减少了维护成本和人力成本。
1
2
3
在实施过程中,通过优化远动系统的硬件和软件配置,提高了系统的稳定性和可靠性,减少了故障次数。
通过加强设备的日常维护和保养,提高了设备的运行效率和寿命,减少了维修成本和人力成本。
通过改进系统的监控和报警机制,及时发现和解决故障,缩短了故障处理时间,提高了系统的运行效率。
实地指导
派遣专家团队到有需求的企业进行实地指导,帮助企业快速掌握该成果的应用技巧。
网络推广
利用电力行业网站、论坛等平台,发布相关信息,吸引更多企业关注和应用。
组织培训
通过组织培训班、研讨会等形式,向全国各地的电力企业和相关单位推广该成果。
提高系统稳定性
通过推广该成果,可以有效提高一体化远动系统的稳定性,减少故障次数,保障电力系统的正常运行。
QC小组成立
在实施过程中,QC小组采用了多种方法,如头脑风暴法、因果分析法、对策表等,对一体化远动系统故障进行了全面分析,并针对性地提出了改进措施。
实施过程
经过实施,一体化远动系统故障次数得到了有效减少,提高了电网运行的稳定性和可靠性,为电力公司带来了显著的经济效益和社会效益。
成果效益
持续改进:虽然QC小组已经取得了一定的成果,但随着电力行业的不断发展,一体化远动系统可能面临新的挑战和问题。因此,需要持续关注系统的运行状况,及时发现和解决潜在问题,以实现持续改进。
QC成果总结与展望
CATALOGUE
04
随着电力行业的快速发展,远动系统在保障电网安全稳定运行中发挥着越来越重要的作用。然而,由于各种原因,一体化远动系统在实际运行中频繁出现故障,给电网安全带来严重威胁。
发电企业qc成果报告范文

发电企业qc成果报告范文1. 简介本报告旨在总结我公司在过去一年中实施的质量控制(QC)项目的成果和效益。
发电企业作为一个关键的基础设施提供者,质量控制的重要性不言而喻。
通过实施QC项目,我公司取得了显著的进展和成果。
2. QC项目概述2.1 目标主要目标是提高发电设备和服务的质量,降低生产过程中的不良率,减少停机时间,并增强客户满意度。
同时,通过优化运营流程和管理体系,提高效率和竞争力。
2.2 实施步骤- 队伍培训:对公司员工进行质量控制知识和技能的培训,提高其对质量的认识和意识。
- 流程优化:分析现有的生产流程和供应链,识别问题和瓶颈,并提出改进方案。
- 标准制定:制定一系列标准和规范,包括产品质量标准、工艺标准、检验标准等。
- 设备升级:对关键设备进行升级和维护,确保其正常运行和高效性。
- 数据分析:收集、整理和分析大量的生产数据,识别潜在问题,并制定改进措施。
- 团队合作:建立跨部门的合作机制,共同解决生产中的问题和挑战。
3. QC成果报告3.1 质量改进通过QC项目的实施,我们取得了显著的质量改进。
产品质量不良率降低了30%,从而降低了维修成本和客户投诉的数量。
我们成功根除了一些生产过程中的常见问题,包括设备故障、材料质量问题等。
3.2 生产效率提升优化生产流程和供应链管理,我们实现了生产效率的提升。
生产周期缩短了15%,减少了库存积压,提高了生产排程的准确性。
通过流程改进,我们降低了生产成本,并能更好地满足客户需求。
3.3 团队协作和沟通QC项目促进了跨部门的合作和沟通。
通过建立日常沟通机制和共享信息平台,我们解决了不同部门之间的信息孤立问题,提高了团队协作的效率和质量。
团队成员之间的沟通更加顺畅,解决问题的速度也大大加快。
3.4 客户满意度质量的提升和生产效率的提高,给客户带来了更好的体验和服务。
我们的客户满意度得到了显著提高,客户投诉率大幅下降。
我们获得了一些重要客户的长期合作,并开拓了新的市场。
QC成果减少生产影响时间
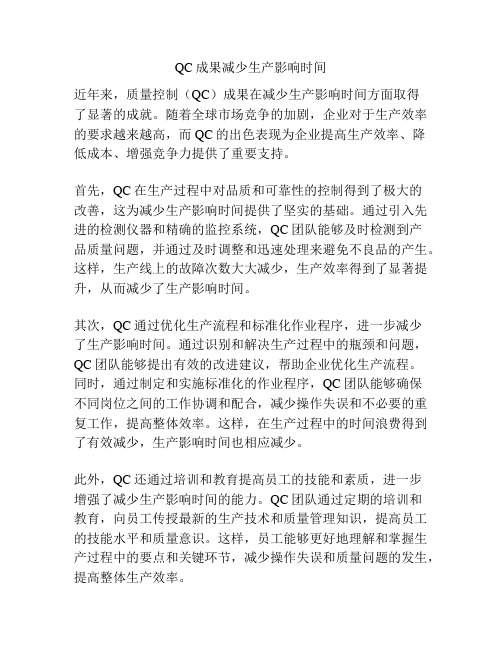
QC成果减少生产影响时间近年来,质量控制(QC)成果在减少生产影响时间方面取得了显著的成就。
随着全球市场竞争的加剧,企业对于生产效率的要求越来越高,而QC的出色表现为企业提高生产效率、降低成本、增强竞争力提供了重要支持。
首先,QC在生产过程中对品质和可靠性的控制得到了极大的改善,这为减少生产影响时间提供了坚实的基础。
通过引入先进的检测仪器和精确的监控系统,QC团队能够及时检测到产品质量问题,并通过及时调整和迅速处理来避免不良品的产生。
这样,生产线上的故障次数大大减少,生产效率得到了显著提升,从而减少了生产影响时间。
其次,QC通过优化生产流程和标准化作业程序,进一步减少了生产影响时间。
通过识别和解决生产过程中的瓶颈和问题,QC团队能够提出有效的改进建议,帮助企业优化生产流程。
同时,通过制定和实施标准化的作业程序,QC团队能够确保不同岗位之间的工作协调和配合,减少操作失误和不必要的重复工作,提高整体效率。
这样,在生产过程中的时间浪费得到了有效减少,生产影响时间也相应减少。
此外,QC还通过培训和教育提高员工的技能和素质,进一步增强了减少生产影响时间的能力。
QC团队通过定期的培训和教育,向员工传授最新的生产技术和质量管理知识,提高员工的技能水平和质量意识。
这样,员工能够更好地理解和掌握生产过程中的要点和关键环节,减少操作失误和质量问题的发生,提高整体生产效率。
综上所述,QC成果在减少生产影响时间方面取得了显著的成就。
通过强化品质和可靠性的控制、优化生产流程和标准化作业程序,以及提高员工技能和素质,QC团队有效地减少了生产过程中的时间浪费,提高了生产效率。
这为企业降低成本、提高竞争力提供了有力支持。
未来,随着QC技术的不断创新和发展,相信其在减少生产影响时间方面的作用将进一步增强。
在过去的几年中,质量控制(QC)成果在减少生产影响时间方面取得了显著的成就。
在现代化的生产环境下,企业面临着不断增长的需求和更加激烈的竞争压力。
qc降低设备故障率浅谈如何降低设备故障率减少维修成本
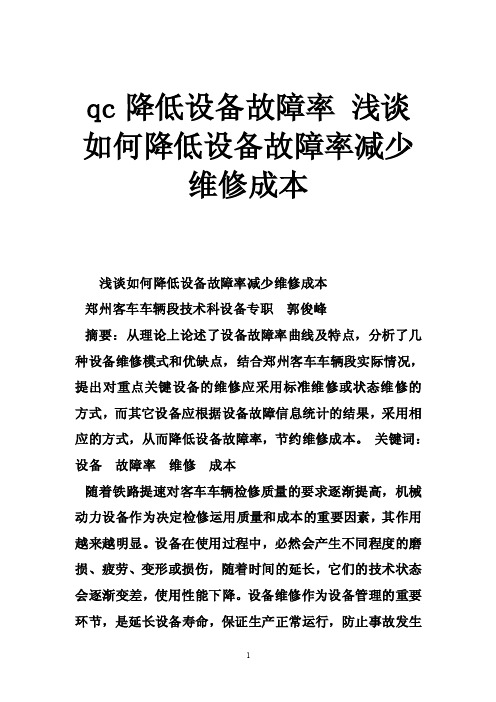
qc降低设备故障率浅谈如何降低设备故障率减少维修成本浅谈如何降低设备故障率减少维修成本郑州客车车辆段技术科设备专职郭俊峰摘要:从理论上论述了设备故障率曲线及特点,分析了几种设备维修模式和优缺点,结合郑州客车车辆段实际情况,提出对重点关键设备的维修应采用标准维修或状态维修的方式,而其它设备应根据设备故障信息统计的结果,采用相应的方式,从而降低设备故障率,节约维修成本。
关键词:设备故障率维修成本随着铁路提速对客车车辆检修质量的要求逐渐提高,机械动力设备作为决定检修运用质量和成本的重要因素,其作用越来越明显。
设备在使用过程中,必然会产生不同程度的磨损、疲劳、变形或损伤,随着时间的延长,它们的技术状态会逐渐变差,使用性能下降。
设备维修作为设备管理的重要环节,是延长设备寿命,保证生产正常运行,防止事故发生的重要保证。
1 设备的故障率曲线1.1 设备故障率浴盆曲线及特点根据设备故障率统计,发现大部分机械设备故障率曲线如图1所示。
这种故障曲线常被叫做浴盆曲线。
按照这种故障曲线,设备故障率随时间的变化大致分早期故障期、偶发故障期和耗损故障期。
早期故障期对于设备来说又叫磨合期。
在此期间,开始的故障率很高,但随时间的推移,故障率迅速下降。
此期间发生的故障主要是设计、制造上的缺陷所致,或使用不当所造成的。
例如我段动车所在2007年底引进的德国U2000-400型不落轮车床设备及德国HAT-MO2型空心轴探伤设备在使用初期的3个月内故障较为频繁,原因主要是国内厂家引进技术,在消化吸收国外技术方面不太完善,造成设备故障频发。
这些设备经过改进后,设备故障率大致处于稳定状态。
在此期间,故障率比较低,这是设备的正常工作期或最佳状态期。
在此期间发生的故障多为使用不当及维修不力产生的,可以通过改进管理和维护保养使故障率降到最低。
在设备使用后期,由于设备零部件的磨损、疲劳、老化、腐蚀等,故障率不断上升。
根据以上理论,可以明显得出结论:在理论上,如果在耗损故障期开始时进行大、中修,可经济而有效地降低故障率。
供电局QC成果-缩短故障电缆处理时间
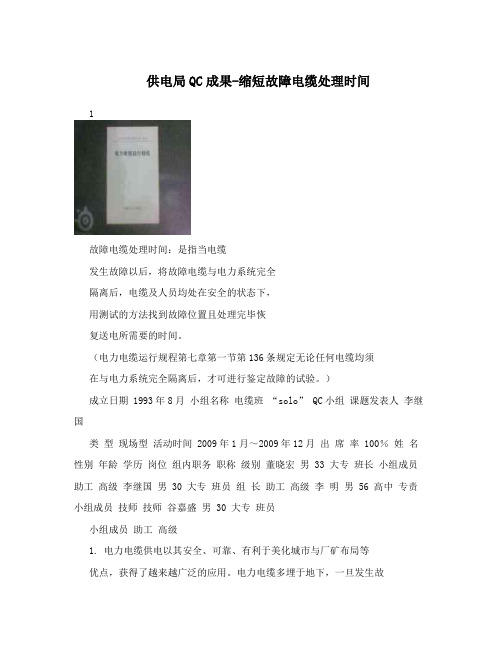
供电局QC成果-缩短故障电缆处理时间1故障电缆处理时间:是指当电缆发生故障以后,将故障电缆与电力系统完全隔离后,电缆及人员均处在安全的状态下,用测试的方法找到故障位置且处理完毕恢复送电所需要的时间。
(电力电缆运行规程第七章第一节第136条规定无论任何电缆均须在与电力系统完全隔离后,才可进行鉴定故障的试验。
)成立日期 1993年8月小组名称电缆班“solo” QC小组课题发表人李继国类型现场型活动时间 2009年1月~2009年12月出席率 100%姓名性别年龄学历岗位组内职务职称级别董晓宏男 33 大专班长小组成员助工高级李继国男 30 大专班员组长助工高级李明男 56 高中专责小组成员技师技师谷嘉盛男 30 大专班员小组成员助工高级1. 电力电缆供电以其安全、可靠、有利于美化城市与厂矿布局等优点,获得了越来越广泛的应用。
电力电缆多埋于地下,一旦发生故障,寻找起来十分困难,往往要花费数小时,甚至几天的时间,不仅浪费了大量的人力、物力,而且会造成难以估量的停电损失。
22. 随着电力电缆在城市电网中的应用日益广泛,运行时间越久,故障会越来越频繁,如何及时有效地处理故障,保证城市供电和电网的正常运行,就要看是否能够快速准确地判定故障性质和地点。
电网供电要求:设备停运时间越短越好。
根具东河分局07年至08年因故障设备造成停电,所需处理的时间统计如下表:8%故障设备处理用时所占比例 13%电力电缆电力电缆 8067分钟 79%架空线路架空线路 1384分钟 13%其他设备 875分钟 8% 其他设备79%表2-1故障设备处理用时表图2-1故障设备处理用时饼状图根据统计表和饼分图可以看出处理电缆故障用时最多,占79%。
所以缩短故障电缆的处理时间是降低设备停运时间的一个有效方法。
3. 在10kV配电网中电力电缆供电比例越来越大,但是在地下直埋电缆系统中探测故障是一件非常费时的事,并且会对用户引起十分不便的停电,某些技术还可能会损坏电缆。
QC成果报告实例
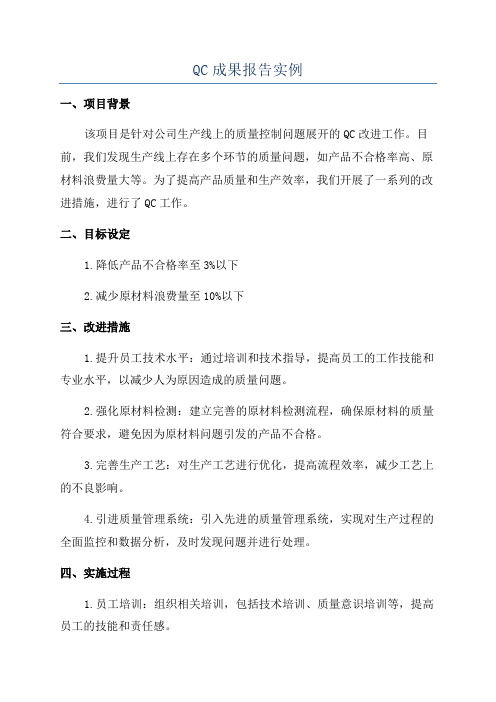
QC成果报告实例一、项目背景该项目是针对公司生产线上的质量控制问题展开的QC改进工作。
目前,我们发现生产线上存在多个环节的质量问题,如产品不合格率高、原材料浪费量大等。
为了提高产品质量和生产效率,我们开展了一系列的改进措施,进行了QC工作。
二、目标设定1.降低产品不合格率至3%以下2.减少原材料浪费量至10%以下三、改进措施1.提升员工技术水平:通过培训和技术指导,提高员工的工作技能和专业水平,以减少人为原因造成的质量问题。
2.强化原材料检测:建立完善的原材料检测流程,确保原材料的质量符合要求,避免因为原材料问题引发的产品不合格。
3.完善生产工艺:对生产工艺进行优化,提高流程效率,减少工艺上的不良影响。
4.引进质量管理系统:引入先进的质量管理系统,实现对生产过程的全面监控和数据分析,及时发现问题并进行处理。
四、实施过程1.员工培训:组织相关培训,包括技术培训、质量意识培训等,提高员工的技能和责任感。
2.建立原材料检测流程:与供应商合作,建立原材料检测标准和流程,并对原材料进行严格检验。
3.工艺优化:与工艺工程师合作,对生产工艺进行评估和改进,消除不良因素。
4.质量管理系统的引入:与IT部门合作,引进质量管理系统,对生产过程进行实时监控和数据分析。
五、改进效果1.产品不合格率下降:经过一段时间的改进措施的实施,产品不合格率从原来的10%下降到当前的2%。
2.原材料浪费减少:通过原材料检测流程的建立和严格执行,原材料浪费量减少了30%。
3.生产效率提升:工艺优化和质量管理系统的引入,使得生产效率提高了20%,生产线的运行更加稳定。
六、总结通过以上的改进措施,我们成功地降低了产品不合格率和原材料浪费量,提高了生产效率。
QC工作的实施有助于找出生产过程中的问题,并采取有效的措施进行改进。
然而,我们也意识到QC工作是一个持续不断的过程,需要不断地进行监控和改进,以保持产品质量和生产效率的提高。
七、改进建议1.继续加强员工培训,提高其技能和责任感。
- 1、下载文档前请自行甄别文档内容的完整性,平台不提供额外的编辑、内容补充、找答案等附加服务。
- 2、"仅部分预览"的文档,不可在线预览部分如存在完整性等问题,可反馈申请退款(可完整预览的文档不适用该条件!)。
- 3、如文档侵犯您的权益,请联系客服反馈,我们会尽快为您处理(人工客服工作时间:9:00-18:30)。
综上所述达到目标值是可行的
四、分析原因
小组全体成员对造成“非计划停机换带”,“非定修更换行走轮” 的;两个症结,运用头脑风暴法分析,绘制关联图如下:
主动轮处纠偏轮使用周期短 F 主动轮纠偏轮磨损
头轮处纠偏轮磨损 E
皮带托辊轴承抱死 D 头轮辊面焊痕磨损 C
回收再利用的运输带尺寸不符合标准 G 皮带接口挂扯
确认六 :主动轮处纠偏轮 使用周期短
调查人
确认时间
冯翠岩
2013.6.10
6月1日----6月9日小组成员冯翠岩对布料小车主动轮处纠偏轮使用周期进 行了调查,统计如下表 :
制表人:张强 制表时间:2013.6.10
首钢长治钢铁公司
主动轮处纠偏轮实物图
断裂纠偏轮实物图
纠偏轮更换过程实物图
确认标准
ZY.15.024-2013《设备点检标准》第10.06条款规定布料小车 主动轮处纠偏轮使用周期必须 > 9天/个 6月1日——6月9日经小组成员调查,1#、2#布料小车主动轮 处纠偏轮分别使用:7、5、4、8天/个均 < 9天/个的使用标准, 不符合要求。 要因 制表人:冯翠岩 制表时间 2013.6.10
磨损纠偏轮实物图
确认标准 确认分析 确认结果
ZY.15.024-2013《设备点检标准》第10.07条款中规定,布 料小车头轮处纠偏轮磨损厚度< 35mm。 6月12日—6月20日经小组成员现场调查可知:布料小车头 轮处纠偏轮磨损厚度最大为32mm < 35mm符合标准。 非要因
制表人:武乐 制表时间 2013.6.21
床上往复运动的皮带运输机,简称布料小车。它在炉内没
有轨道为悬臂结构。布料小车皮带传动装置固定在车架上, 随车体一起移动,布料时易产生偏析。当车体前进或后退 时,送到布料小车上的生球量是变化的,车体越往后,皮 带上的生球量就越多,布到炉内干燥床上的料面不是水平 的而是倾斜的。 为消除偏析,在控制布料小车布到干燥床上生 球量均匀时,必须在料层薄的区域多做几次小范围 的往复运动,造成了布料小车故障停机时间的增加, 且换向频繁,对小车轨道及行走轮形成磨损 。
确认标准
ZY.15.024-2013《设备点检标准》第10.14条款规定布料小车订 制回收再利用运 输带尺寸参数标准 为: m, m。
确认分析 确认结果
5月15日——5月16日经小组成员调查,1#、2#布料小车使用的 回收再利用运输带订制的小车带尺寸参数均在使用标准范围内, 符合标准。
回收再利用的运输带尺寸不符合标准 布料车皮带降温装置不完善
干燥床局部温度高 行走轮轴焊接处开焊
首钢长治钢铁公司
五、确定主要原因 小组针对十条末端因素,逐条进行验证,以确定是否是主要原因, 确认情况如下:
确认一 :5#、8#带机头清 扫器清扫效果差
调查人 张强
确认时间 2013.6.2
小组成员张强对 5#、8#带机头清扫器清扫效果进行调查,针对2013 年5月21日—5月30日5#、8#带机头清扫器位置进行调查小组成员在其中 随机抽样做统计表如下 :
确认分析 确认结果
确认七 :回收再利用的运 输带尺寸不符合标准
调查人
确认时间
侯方平
2013.6.11
5月15日----5月16日小组成员侯方平对布料小车所使用的回收再利 用的运输带尺寸参数进行调查,统计如下表 :
制表人:武乐 制表时间:2013.5.17
首钢长治钢铁公司
回收再利用小车带实物图
更换下旧头轮焊痕厚度测量过程
确认三 :头轮辊面焊痕磨损
调查人 王庆国
确认时间 2013.6.6
5月20日----5月28日小组成员王庆国对布料小车头轮焊痕的磨损情况进 行了调查,统计如下表 :
制表人:王庆焊痕实物图
更换下旧头轮焊痕厚度测量过程
确认标准
ZY.15.024-2013《设备点检标准》第3.21条款规定布料 小车头轮焊痕厚度必须 > 20mm。 5月20日——5月28日经小组成员调查,1#、2#布料小 车更换的旧头轮辊面焊痕厚度分别为35mm、38mm均 > 20mm,符合标准。 非要因 制表人:王庆国 制表时间 2013.6.6
确认标准
ZY.15.024-2013《设备点检标准》第11.09条款规定布 料小车所用的托辊轴承抱死数量为“0”。
6月4日——6月12日经小组成员对1#、2#布料小车使 用的托辊轴承抱死数量进行调查,皮带托辊轴承抱死数 量为“0”符合标准。 非要因 制表人:韩中华 制表时间 2013.6.13
确认分析 确认结果
我们是首钢长治钢铁公司烧结厂“一缕阳光QC小组”。小组至1997年 组建,三年来追求卓越,不断创新。2011年本小组以“节能减排、降本增效, 节约生产成本”为宗旨,立足现场,解决难题,为公司创造了良好的经济效 益。
热轧带肋钢筋
热轧高速盘条
矿渣水泥
首钢长治钢铁公司
一、概述
布料小车是球团矿生产过程中,将生球送往炉内干燥
制表人:张强 制表时间2013 .5.31
首钢长治钢铁公司
确认标准 确认分析 确认结果
ZY.15.024-2013《设备点检标准》第4.16条款规定:布料小车 道轨上物料洒溅量为“0”。 5月21日——5月30日,小组成员对布料小车道轨上洒溅的物料 进行调查,料量平均为:3.89kg、3.44kg不符合标准。 5#、 8#带机头清扫器清扫效果差。 要因
发表人:冯翠岩 陈慧敏 发表人:冯翠岩陈慧敏
一缕阳光QC小组
首钢长治钢铁公司 首钢长治钢铁公司
首钢长治钢铁公司
首钢长治钢铁公司,前身是长治钢铁有限公司(简称长 钢)创建于1947年, 是中国共产党在太行山革命根据地建设 的第一个钢铁企业。经过63年的发展,公司集采矿、采煤、 炼焦、炼铁、炼钢、轧材、水泥制造、工程建设、锻压机械 制造、房地产开发于一体,生产棒材、线材、热轧带肋钢筋、 无缝钢管、矿渣水泥、环保墙体制品、螺钉和PP-R管等八大 系列产品的大型国有企业。长钢的建筑用钢材钢质纯净、成 份稳定,名冠三晋,享誉省内外。主导产品“上党”牌钢筋 混凝土用热轧带肋钢筋1999年通过了国家冶金产品质量认证, 同年荣获国家冶金产品实物质量“金杯奖”奖牌。
制表人:张强 制表时间2013.6.2.
确认二 :弹簧管破裂
调查人 孟云平
确认时间
2013.6.5
5月14日----5月22日小组成员孟云平对布料小车弹簧管的破损情况 进行了调查,统计如下表 :
制表人:孟云平 制表时间:2013.5.23
首钢长治钢铁公司
弹簧管破裂漏水实物图
破裂弹簧管绑缚过程
确认标准
课题名称: 降低布料小车 故障停机时间
注册日期 2013.3.12
课题类型 现场型
组长 韩中华
小组名称 一缕阳光 QC小组
首钢长治钢铁公司
二、选题理由 烧结厂降本目标要求 车 间 要 求 三车间故障停机时间为300分/月 布料小车故障停机时间为100分/月
生 产
现
状
图3
由排列图可知:布料小车故障停机时间位于三车间故障停机时间的首位 ;占三车间故障停机时间的41.61%。
布料小车在竖炉工艺中的位置:
5#、8#带机头 竖炉
齿轮悬臂式布 料小车
布料小车在竖炉工艺中的作用: 齿轮悬臂式布料小车的作
用:将一定量的生球均匀
的散布在干燥床上。
首钢长治钢铁公司
齿轮悬臂式布料小车的结构:
首钢长治钢铁公司
小组简介
小组成立 日期1997.2 活动次数 22次 出勤率 97
课题编号 15001016-2013
降低布料小车故障停机时间
三、设定目标
图4 布料小车故障停机时间柱状图 139.25 150 100 50 0 现状 目标
制图人:冯翠岩 制图时间2013.4.2.
100
首钢长治钢铁公司
目标可行性分析 1、掌握现状 小组成员查阅布料小车运行记录,2012年7月—2013年2月统计布料小 车故障停机时间数据见表2。
由表2可知:2012年7月至2013年2月,布料小车故障停机时间平 均为: X=139.25分/月。
首钢长治钢铁公司
2、分层调查
对布料小车各种故障停机时间因素调查小组对2012年7月——2013年2月布 料小车故障停机时间按故障因素从15方面进行分类整理,以便找出小组改进方向。 统计如下: 布料小车各种故障停机时间统计表
首钢长治钢铁公司
生 产 现 状
200 150 100 50 0 7月 单位:分 8月 9月 98 132 141
185
173 122 94
169 139.25
10月
11月
12月
1月
2月
2012年 月份 布料车故障时间 平均值
2013年
选定 课题
从2012年7月至2013年2月份布料小车故障停机时间 折线图可以看出:布料小车故障停机时间平均为139.25 分/月,与车间要求布料小车故障停机时间100分/月,还 有一定的差距。
确认五 :头轮处纠偏轮磨损
调查人
确认时间
武乐
2013.6.21
6月12日----6月20日小组成员武乐对布料小车头轮处的纠偏轮磨损情况 进行了调查,统计如下表 :
制表人:冯翠岩
制表时间:2013.6.21
首钢长治钢铁公司
制图人:王庆国 制图时间:2013.6.21
首钢长治钢铁公司
布料小车头轮处纠偏轮位置
②布料小车故障停机时间可下降空间测算:
图6 布料小车故障停机时间 400 353 232 71 1#布料车 2#布料车 1#布料车
单 位 : 分
300 200 100 0
40 2#布料车
非计划停机换带