Dynamic recrystallization of Mg and Mg–Y alloysCrystallographic textu
《机械工程材料》杂志防诈骗公告
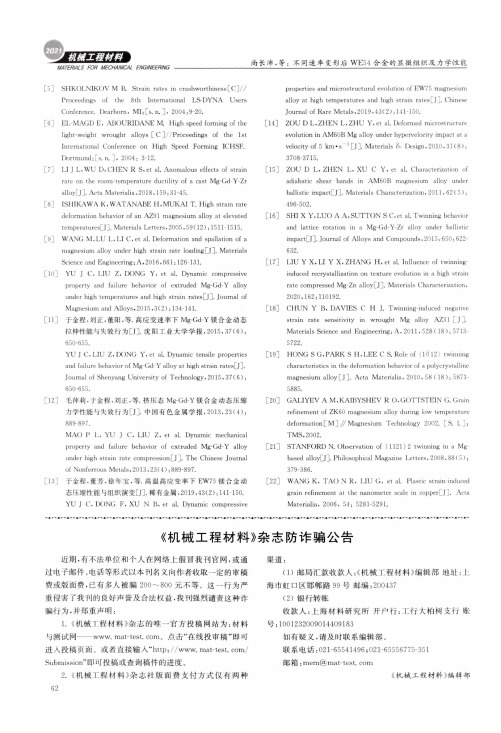
MATERIALS FO R M ECHANICAL ENGINEERING尚长沛,等:不同速率变形后WE 54合金的显微组织及力学性能[5] S H K O L N I K O V M B. Strain rates i n crashworthiness [C]//Proceedings of the 8th International L S -DYNA Users Conference. Dearborn. M I :[s . n.]» 2004:9-20.[6] E L -M A G D E, A B O U R I D A N E M. High speed forming of thelight-weight wrought alloys [ C ]//Proceedings of the 1s t International Conference on High Speed Forming ICHSF. Dortmund :[s . n .2004: 3-12.[7] LI J L »W U D ,C H E N R S,et a l . Anomalous effects of s trainrate on the room-temperature d u ctility of a cast Mg-Gd-Y-Zr alloy[J]. Acta Materialia»2018,159:31-45.[8] I S H I K A W A K ,W A T A N A B E H ’M U K A I T. High strain ratedeformation behavior of an AZ91 magnesium alloy a t elevated temperatures[J]. Materials Letters,2005,59(12) : 1511-1515.[9] W A N G M.L U L»LI C,et a l . Deformation and spallation of amagnesium alloy under high strain rate loading [J]. Materials Science and Engineering : A ,2016,661 : 126-131.[10] Y U J C» LIU Z» D O N G Y, e t a l . Dynamic compressiveproperty and f a i l u r e behavior of extruded Mg-Gd-Y alloy under high temperatures and high strain rates[J]. Journal of Magnesium and Alloys,2015»3(2) : 134-141.[11] 于金程,刘正,董阳,等.高应变速率下Mg-Gd-Y 镁合金动态拉伸性能与失效行为[J].沈阳工业大学学报,2015,37(6):650-655.Y U J C, LIU Z. EX)NG Y, e t a l . Dynamic tensile properties and f a i l u r e behavior of Mg-Gd-Y alloy a t high strain rates[J]. Journal of Shenyang University of Technology, 2015» 37(6): 650-655.[12] 毛萍莉,于金程,刘正,等.挤压态Mg-Gd-Y 镁合金动态压缩 力学性能与失效行为[J].中国有色金属学报,2013,23(4):889-897.M A O P L, Y U J C» LIU Z» e t a l . Dynamic mechanical property and f a i l u r e behavior of extruded Mg-Gd-Y alloy under high strain rate compression [J]. The Chinese Journal of Nonferrous Metals,2013»23(4):889-897.[13] 于金程•董芳,徐年宝,等.高温高应变率下E W 75镁合金动 态压缩性能与组织演变[J].稀有金属,2019,43(2): 14卜150.Y U J C» EX)NG F, X U N B, e t a l . Dynamic compressiveproperties and microstructural evolution of EW 75 magnesium alloy a t high temperatures and high strain rates[J]. Chinese Journal of Rare Metals ,2019,43(2): 141-150.[14] Z O U D L ,Z H E N L ,Z H U Y,et a l . Deformed microstructurcevolution i n A M 60B M g alloy under hypervelocity impact a t a velocity of 5 k m *s _1[J]. Materials Design, 2010,31 (8):3708-3715.[15] Z O U D L, Z H E N L, X U C Y, e t a l . Characterization ofadiabatic shear bands i n A M 60B magnesium alloy under b a l l i s t i c impact[J]. Materials Characterization, 2011,62(5): 496-502.[16] SHI X Y ,L U O A A ,S U T T O N S C-et a l . Twinning behaviorand l a t t i c e rotation i n a Mg-Gd-Y-Zr alloy under b a l l i s t i c impact[J]. Journal of Alloys and Compounds,2015,650:622 632.[17] LIU Y X,LI Y X, Z H A N G H,et a l . Influence of twinninginduced recrystallization on texture evolution i n a high s train rate compressed Mg-Zn alloy [J]. Materials Characterization. 2020,162:110192.[18] C H U N Y B, D A V I E S C H J . Twinning-induced negativestrain rate sensitivity i n wrought M g alloy AZ31 [ J ]. Materials Science and Engineering : A, 2011 ♦ 528 (18) : 5713^ 5722.[19] H O N G S G ,P A R K S H ,L E E C S . Role of {1012} twinningcharacteristics i n the deformation behavior of a polycrystalline magnesium alloy[J]. Acta Materialia ,2010, 58 ( 18): 5873- 5885.[20] G A L I Y E V A M ,K A I B Y S H E V R O ’G O T T S T E I N G. Grain refinement of ZK60 magnesium alloy during low temperature deformation [ M ]Magnesium Technology 2002. [S. 1.]:T M S ,2002.[21] S T A N F O R D N. Observation of {1121} 2 twinning i n a M gbased alloy[J]. Philosophical Magazine Letters* 2008,88(5): 379-386.[22] W A N G K, TAC) N R, LIU G, e t al . Plastic strain-induced grain refinement a t the nanometer scale i n copper[J]. Acta Materialia, 2006, 54: 5281-5291.《机械工程材料》杂志防诈骗公告近期,有不法单位和个人在网络上假冒我刊官网,或通 过电子邮件、电话等形式以本刊名义向作者收取一定的审稿 费或版面费,已有多人被骗200〜800元不等。
应变速率对AZ61镁合金动态再结晶行为的影响
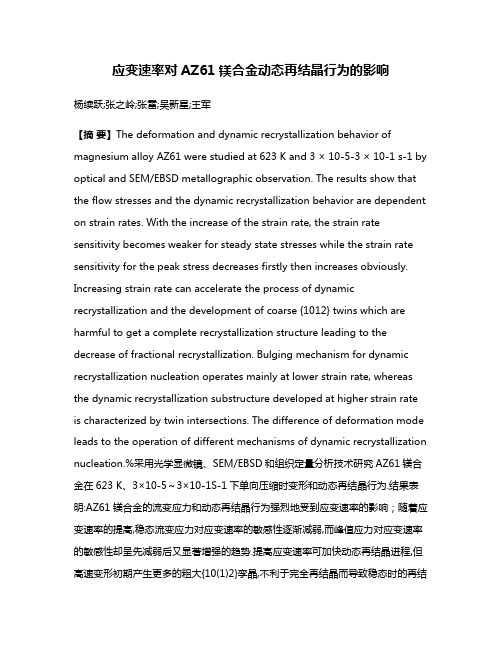
应变速率对AZ61镁合金动态再结晶行为的影响杨续跃;张之岭;张雷;吴新星;王军【摘要】The deformation and dynamic recrystallization behavior of magnesium alloy AZ61 were studied at 623 K and 3 × 10-5-3 × 10-1 s-1 by optical and SEM/EBSD metallographic observation. The results show that the flow stresses and the dynamic recrystallization behavior are dependent on strain rates. With the increase of the strain rate, the strain rate sensitivity becomes weaker for steady state stresses while the strain rate sensitivity for the peak stress decreases firstly then increases obviously. Increasing strain rate can accelerate the process of dynamic recrystallization and the development of coarse {1012} twins which are harmful to get a complete recrystallization structure leading to the decrease of fractional recrystallization. Bulging mechanism for dynamic recrystallization nucleation operates mainly at lower strain rate, whereas the dynamic recrystallization substructure developed at higher strain rate is characterized by twin intersections. The difference of deformation mode leads to the operation of different mechanisms of dynamic recrystallization nucleation.%采用光学显微镜、SEM/EBSD和组织定量分析技术研究AZ61镁合金在623 K、3×10-5~3×10-1S-1下单向压缩时变形和动态再结晶行为.结果表明:AZ61镁合金的流变应力和动态再结晶行为强烈地受到应变速率的影响;随着应变速率的提高,稳态流变应力对应变速率的敏感性逐渐减弱,而峰值应力对应变速率的敏感性却呈先减弱后又显著增强的趋势.提高应变速率可加快动态再结晶进程,但高速变形初期产生更多的粗大{10(1)2}孪晶,不利于完全再结晶而导致稳态时的再结晶体积分数反而较低;在中低应变速率下动态再结晶以晶界弓出形核为主,而在高应变速率下则主要通过孪晶分割来进行;由应变速率引起变形机制的变化是导致不同动态再结晶行为的原因.【期刊名称】《中国有色金属学报》【年(卷),期】2011(021)008【总页数】7页(P1801-1807)【关键词】AZ61镁合金;高温变形;应变速率;动态再结晶;孪晶【作者】杨续跃;张之岭;张雷;吴新星;王军【作者单位】中南大学材料科学与工程学院,长沙410083;中南大学有色金属材料科学与工程教育部重点实验室,长沙410083;中南大学材料科学与工程学院,长沙410083;中南大学材料科学与工程学院,长沙410083;中南大学材料科学与工程学院,长沙410083;中南大学材料科学与工程学院,长沙410083【正文语种】中文【中图分类】TG146.2HCP结构的镁合金滑移系较少,低温塑性差,其变形多在高温下进行。
应变速率对Mg-13Gd-4Y-2Zn-0.5Zr镁合金旋转反挤压的影响

2019 年 4 月
中国材料进展
MATERIALS CHINA
Vol ������ 38 No ������ 4 Apr������ 2019
应变速率对 Mg ̄13Gd ̄4Y ̄2Zn ̄0������ 5Zr 镁合金
旋转反挤压的影响
屈晓晓1ꎬ 张治民1ꎬ 于建民1ꎬ 房庆龄1ꎬ 刘 涛2
QU Xiaoxiao1ꎬ ZHANG Zhimin1ꎬ YU Jianmin1ꎬ FANG Qingling1ꎬ LIU Tao2
(1. School of Materials Science and Engineeringꎬ North University of Chinaꎬ Taiyuan 030000ꎬ China) (2. Taiyuan Military Representative Office of Armored Military Representative Bureauꎬ Taiyuan 030006ꎬ China)
(1. 中北大学材料科学与工程学院ꎬ 山西 太原 030000) (2. 装甲军代局驻太原地区军代室ꎬ 山西 太原 030006)
摘 要: 旋转反挤压是一种将旋转运动和正常反挤压运4Y ̄2Zn ̄0������ 5Zr 镁合
金的剧烈塑性变形ꎬ 改善其组织和性能ꎮ 以旋转挤压为工艺对象ꎬ 利用 Gleeble ̄3500 热模拟机研究了镁合金杯形件成形过程 中应变速率对材料组织和性能的影响规律ꎮ 结果表明: Mg ̄13Gd ̄4Y ̄2Zn ̄0������ 5Zr 镁合金杯形件旋转反挤压过程中ꎬ 显微硬度分 布较为均匀ꎬ 试样从外部到内部的晶粒逐渐细化ꎬ 沿旋转方向动态再结晶程度逐渐提高ꎬ 晶粒尺寸逐渐减小ꎮ 在周向应变速 率 ε̇ 周 从 0 增大到 0������ 05 s-1 的过程中ꎬ 动态再结晶晶粒的占比逐渐上升ꎬ 在 ε̇ 周 为 0������ 005 s-1 时ꎬ 片状 LPSO 相的破碎使此时材 料的硬度提高ꎬ 并抑制了动态再结晶晶粒的产生ꎮ ε̇ 周 的继续增加使位错密度增大ꎬ 促进了动态再结晶ꎮ 在旋转反挤压进行过 程中ꎬ 随时间的增加成形载荷波动上升ꎬ 且随着 ε̇ 周 的增加ꎬ 成形载荷逐渐下降ꎮ
变形参数对Mg
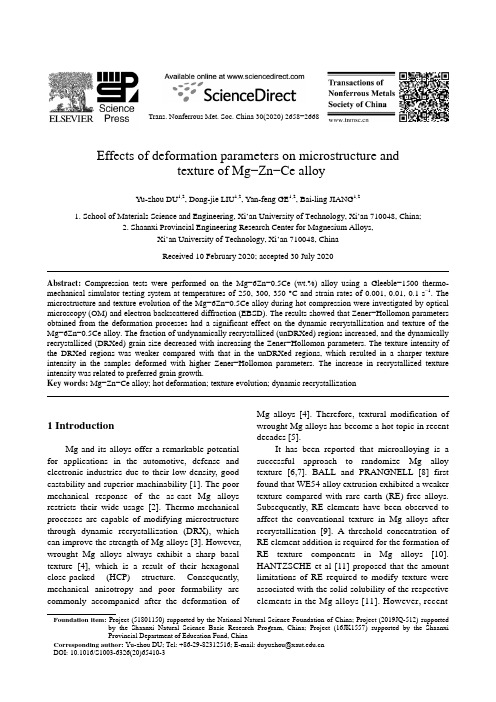
Trans. Nonferrous Met. Soc. China 30(2020) 2658−2668Effects of deformation parameters on microstructure andtexture of Mg−Zn−Ce alloyYu-zhou DU1,2, Dong-jie LIU1,2, Yan-feng GE1,2, Bai-ling JIANG1,21. School of Materials Science and Engineering, Xi’an University of Technology, Xi’an 710048, China;2. Shaanxi Provincial Engineering Research Center for Magnesium Alloys,Xi’an University of Technology, Xi’an 710048, ChinaReceived 10 February 2020; accepted 30 July 2020Abstract: Compression tests were performed on the Mg−6Zn−0.5Ce (wt.%) alloy using a Gleeble−1500 thermo- mechanical simulator testing system at temperatures of 250, 300, 350 °C and strain rates of 0.001, 0.01, 0.1 s−1. The microstructure and texture evolution of the Mg−6Zn−0.5Ce alloy during hot compression were investigated by optical microscopy (OM) and electron backscattered diffraction (EBSD). The results showed that Zener−Hollomon parameters obtained from the deformation processes had a significant effect on the dynamic recrystallization and texture of the Mg−6Zn−0.5Ce alloy. The fraction of undynamically recrystallized (unDRXed) regions increased, and the dynamically recrystallized (DRXed) grain size decreased with increasing the Zener−Hollomon parameters. The texture intensity of the DRXed regions was weaker compared with that in the unDRXed regions, which resulted in a sharper texture intensity in the samples deformed with higher Zener−Hollomon parameters. The increase in recrystallized texture intensity was related to preferred grain growth.Key words: Mg−Zn−Ce alloy; hot deformation; texture evolution; dynamic recrystallization1 IntroductionMg and its alloys offer a remarkable potentialfor applications in the automotive, defense andelectronic industries due to their low density, goodcastability and superior machinability [1]. The poormechanical response of the as-cast Mg alloysrestricts their wide usage [2]. Thermo-mechanicalprocesses are capable of modifying microstructurethrough dynamic recrystallization (DRX), whichcan improve the strength of Mg alloys [3]. However,wrought Mg alloys always exhibit a sharp basaltexture [4], which is a result of their hexagonalclose-packed (HCP) structure. Consequently,mechanical anisotropy and poor formability arecommonly accompanied after the deformation ofMg alloys [4]. Therefore, textural modification ofwrought Mg alloys has become a hot topic in recentdecades [5].It has been reported that microalloying is asuccessful approach to randomize Mg alloytexture [6,7]. BALL and PRANGNELL [8] firstfound that WE54 alloy extrusion exhibited a weakertexture compared with rare earth (RE)-free alloys.Subsequently, RE elements have been observed toaffect the conventional texture in Mg alloys afterrecrystallization [9]. A threshold concentration ofRE element addition is required for the formation ofRE texture components in Mg alloys [10].HANTZSCHE et al [11] proposed that the amountlimitations of RE required to modify texture wereassociated with the solid solubility of the respectiveelements in the Mg alloys [11]. However, recentFoundation item: Project (51801150) supported by the National Natural Science Foundation of China; Project (2019JQ-512) supported by the Shaanxi Natural Science Basic Research Program, China; Project (16JK1557) supported by the ShaanxiProvincial Department of Education Fund, ChinaCorresponding author:Yu-zhouDU;Tel:+86-29-82312516;E-mail:*****************.cnDOI:10.1016/S1003-6326(20)65410-3Yu-zhou DU, et al/Trans. Nonferrous Met. Soc. China 30(2020) 2658−2668 2659studies have reported that the resulting texture after dynamic recrystallization in RE containing Mg alloys has also been influenced by deformation parameters [12,13]. For example, ROBSON et al [13] found an unusual texture component in the Mg−6Y−7Gd−0.5Zr (wt.%) alloy when extruding with a high extrusion ratio [13]. The inhibition of shear bands deformed at high temperature resulted in the disappearance of the RE texture component in the Mg−Gd binary alloy [14], but the RE texture component in the Mg−Zn−Ce alloy was prohibited when extruding at low temperature (300 °C) due to the inhibition of the activation of the 〈c+a〉 slip system [15]. High strain rate also played an essential role in RE formationin Mg−0.23wt.%Ce alloy, because the high deformation speed provided great deformation- induced stored energy for the dynamic recrystallization process [16]. Therefore, the texture development during dynamic recrystallization is associated with chemical compositions and deformation parameters. However, there is still a lack of the effect of deformation parameters on the texture of RE containing Mg alloys.Unraveling the relationship between the processing conditions and the microstructure can provide guidelines to produce a desirable microstructure for Mg alloys. Mg−Zn based alloys are promising candidates for commercial applications. Ce is an important alloying element in Mg alloys [17]. Generally, a small addition of Ce is enough to reduce the texture intensity of wrought Mg alloys [18]. Therefore, 0.5 wt.% Ce was addedin the present study, and Mg−6Zn−0.5Ce (wt.%) alloys were deformed under various deformation parameters to identify the influence of deformation parameters on microstructural evolution and texture. The aim of the present study is to provide a way to fabricate high performance RE-containing Mg alloys with high strength and ductility.2 ExperimentalThe Mg−6Zn−0.5Ce (wt.%) alloys were fabricated by melting pure Mg, pure Zn and Mg−30%Ce master alloys at 750 °C with the protection of a mixed atmosphere of CO2 and SF6. The casting ingots were homogenized at 350 °C for 12 h. After that, cylindrical samples with diameters of 8 mm and heights of 12 mm were machined from the homogenized alloys and used in compression tests. The compression tests were carried out on a Gleeble−1500 thermo-mechanical simulator testing system. The specimens were uniaxially compressed to a height reduction of 60% (corresponding to a true strain of 0.9) at strain rates of 0.001−0.1 s−1 and temperatures of 250−350 °C. The compressed specimens were immediately quenched into water to preserve the deformed microstructure. For each condition of deformation, at least three samples were repeated to ensure reproducibility.Specimens for microstructural observation and texture were cut from the central part of the section parallel to the compression direction. The volume fraction of the deformed region was measured according to the area ratio of the extruded alloys using Image Pro 5.0 software. Electron backscattered diffraction (EBSD) tests were conducted on a scanning electron microscope (SEM) with an HKL-EBSD system under accelerating voltage of 20 kV. The acquired EBSD data with band contrast larger than 20 were used to calculate pole figures using the software of the MTEX toolbox [19]. The step sizes for the EBSD tests were 0.7−2 μm according to the DRXed grain size of the compressed samples.3 Results and discussion3.1 Compressive stress−strain curves anddeformation activation energyFigure 1 presents the SEM images of the as-cast and homogenized alloys. A large amount of semi-continuous second phases distributing along grain boundaries were observed in the as-cast alloy (Fig. 1(a)). The semi-continuous second phases became discrete for the homogenized alloy (Fig. 1(b)), indicating that the second phases were partially dissolved into the matrix. The EDS results of the second phase are shown in Fig. 1(c). It could be seen that the second phase contained about 43.73 at.% Zn, 7.92 at.% Ce, and 48.35 at.% Mg. A T phase with a composition of 7.7 at.% Ce, 19.3−43.6 at.% Zn in the Mg−Zn−Ce alloy was obtained at 350 °C[20]. The second phase in the rapidly solidified Mg−8Zn−MM alloy was determined to be Mg52.6Zn39.5MM7.9, which was also called a T phase [21]. The difference in chemical composition of the second phase between the previous investigation and the present study wasYu-zhou DU, et al/Trans. Nonferrous Met. Soc. China 30(2020) 2658−2668 2660Fig. 1SEM images of as-cast (a), homogenized (b) Mg−6Zn−0.5Ce (wt.%) alloy s and EDS results (c) of second phases arrowed in (a)because the EDS results were affected by the surrounding Mg matrix due to its relatively large area and depth for analysis. Hence, the second phase in the Mg−6Zn−0.5Ce (wt.%) alloy was inferred to be a T phase in the present study.Figure 2 shows the true stress−true strain curves of the homogenized alloys after compression. All curves showed similar flow deformation behavior, i.e., the flow stress first increased to a maximum and then decreased to a steady state, which was typical characteristic of the dynamicFig. 2True stress−true strain curves of samples compressed at different strain rates: (a) 0.1 s−1;(b) 0.01 s−1; (c) 0.001 s−1recrystallization [22]. At the beginning of the deformation, the hardening rate was higher than the softening rate, which resulted in a sharp rise of flow stress with increasing strain. With further deformation, the softening effect from dynamic recrystallization exceeded the hardening effect during deformation, which gave rise to a decrease in flow stress. When a dynamic balance between softening and hardening reached, flow stress showed a steady state. Additionally, it couldYu-zhou DU, et al/Trans. Nonferrous Met. Soc. China 30(2020) 2658−2668 2661be observed that the peak of flow stress and corresponding strain were reduced with increasing deformation temperature and decreasing strain rate. Higher temperature provided higher dislocation mobility and lower strain rate, which could provide longer time for activation energy accumulation and was beneficial to the softening process.Deformation activation energy is typically used to characterize the difficulty of the hot deformation process, which can be determined by the Arrhenius equations [23]:11exp[/()]n A Q RT εσ−& (1)2exp()exp[/()]A Q RT εβσ−& (2)[sinh()]exp[/()n A Q RT εασ−& (3)where Q is deformation activation energy (kJ/mol), ε& is the strain rate (s −1), σ is the flow stress (MPa), R is the mole gas constant (8.314 J/(mol·K)), T is the thermodynamic temperature (K), and A 1, A 2, A , n 1, n , β and α are material constants (α=β/n 1).From Eqs. (1)−(3), the material constants n 1 and β can be calculated as 1ln ln Tn εσ∂ = ∂ & (4)ln T εβσ∂ = ∂ & (5)Then, the values of n 1 and β were determinedby measuring the slopes of the ln ε&−ln σ and ln ε&−σ curves at each temperature, respectively. Figure 3shows the linear relationship of ln ε&−ln σ and ln ε&−σ at different temperatures obtained by linear fitting. The average values of n 1 and β were calculated to be 5.797 and 0.079. Then, the value of α of the alloy was determined as α=β/n 1=0.0136.The activation energy can be calculated by the hyperbolic sine law according to Eq. (6)ln ln[sin()]ln[sin()](1/)T Q R T εεασασ ∂∂= ∂∂ && (6)Figure 4 shows the linear relationships of ln ε&−ln[sinh(ασ)] and ln[sinh(ασ)]−1/T . Then, the average activation energy (Q ) for the Mg − 6Zn−0.5Ce (wt.%) alloy was determined to beFig. 3 Variation of ln ε&−ln σ (a) and ln ε&−σ (b) at different temperaturesFig. 4 Variation of ln ε&−ln[sinh(ασ)] at different temperatures (a) and ln[sinh(ασ)]−1/T at different strain rates (b)Yu-zhou DU, et al/Trans. Nonferrous Met. Soc. China 30(2020) 2658−26682662120.88 kJ/mol, which is close to the latticeself-diffusion activation energy of Mg (Q sd = 135 kJ/mol) [24]. The Q values were reported to be 123−164 kJ/mol for the AZ31 alloy [25−28],152 kJ/mol for the AZ61 alloy [29], 154 kJ/mol for the AZ80 alloy [30], 176 kJ/mol for the AZ91 alloy [31], and 160−175 kJ/mol for ZK60 alloy [32].The Q values of Mg alloys are related to themicrostructure. Fine precipitates could effectivelyinhibit dislocation movement during deformation,and fine grains providing more grain boundariescould act as barriers to lattice self-diffusion.Additionally, the addition of alloying elementshinders the movement of dislocation, whichleads to the increase in flow stress and activationenergy. For the Mg −6Zn −0.5Ce (wt.%) alloy in thepresent study, Ce mainly existed in the form of theMg −Zn −Ce (T ) phase, and only Zn existed in theform of solute in the Mg matrix. The diffusionvelocity would be expected to be similar for Mgand Zn atoms due to similar atomic radius.Therefore, the Q value of the Mg −Zn −Ce alloy was almost the same as the lattice self-diffusionactivation energy of Mg. This indicated that the DRX of the Mg −6Zn −0.5Ce (wt.%) alloy wascontrolled by lattice self-diffusion. The deformation activation energy could be used to derive the Zener −Hollomon (Z ) parameter, which combined the effects of deformationtemperature and strain rate on the deformation behavior and is given by the following equation:exp[/()]Z Q RT ε=& (7)The Zener −Hollomon parameters for thesamples in the present study are shown in Table 1.Table 1 Zener −Hollomon parameters corresponding todifferent deformation parametersSample No. T /°C ε&/s −1 ln Z 1 250 0.001 20.89 2 250 0.01 23.19 3 250 0.1 25.5 4 300 0.001 18.47 5 300 0.01 20.77 6 300 0.1 23.07 7 350 0.001 16.43 8 350 0.01 18.73 9 350 0.1 21.04 3.2 Microstructural evolution with Zener −Hollomon parameters Figure 5 shows the optical images of theFig. 5 Optical images of compressed samples with different Zener −Hollomon parameters: (a) ln Z =16.43; (b) ln Z = 18.47; (c) ln Z =18.73; (d) ln Z =20.77; (e) ln Z =20.89; (f) ln Z =21.04; (g) ln Z =23.07; (h) ln Z =23.19; (i) ln Z =25.5Yu-zhou DU, et al/Trans. Nonferrous Met. Soc. China 30(2020) 2658−2668 2663compressed alloys. It is clearly observed that thesamples deformed with high Z parameters show a heterogeneous microstructure containing fine DRXed grains and coarse unDRXed regions. The unDRXed region decreased and the DRXed region increased gradually with decreasing Z value. The samples with low Z values (ln Z <20) showed an almost fully recrystallized micro- structure (Figs. 5(a −c)).To further analyze the influence of Z parameters on dynamic recrystallization, the fraction of DRXed region was statistically analyzed using Image Pro software, as shown in Fig. 6. The fraction of DRXed region increased with decreasing ln Z value, which indicated that high temperature and low strain rate promoted the dynamic recrystallization process. High deformation temperature provided more thermal energy and low strain rate supplied more deformation time for dislocation movement, which gave rise to a high degree of dynamic recrystallization.Fig. 6 Variation of fraction of DRXed region with different Zener −Hollomon parameters Figure 7 shows the variation of DRXed grain size as a function of Z parameter for the specimens compressed to a strain of 60%. WATANABE et al [33] suggested that the DRXed grain size is closely related to the Z parameter, which could be expressed as follows:rec mZd A = (8)where d rec is the average DRXed grain size, m is thegrain size exponent and A is a constant. It is easy toderive the following relationship:ln d rec =ln A /m −ln Z /m (9)It could be seen from Fig. 7 that ln d rec and ln Z show a linear relationship, indicating that the factors affecting the DRXed grain size are similar in the present processing regimes [34].Fig. 7 Variation of DRXed grain size with Z parameter at different temperatures3.3 Relationship between texture and Zener −Hollomon parameterThe degree of dynamic recrystallization and DRXed grain size both increased with decreasing Z values, as mentioned in Section 3.2. To investigate the texture of the Mg −Zn −Ce alloy under different deformation conditions, samples with different Z parameters were analyzed using EBSD. Figure 8 shows the EBSD results of the specimens deformed with different Z parameters. Crystallographic orientations are represented by different colors, as defined in the inverse pole figure (IPF). The samples deformed with high Z parameters exhibiteda heterogeneous microstructure with fine DRXedgrains and coarse unDRXed region (Figs. 8(a) and (b)), which was consistent with the OM observations (Fig. 5). It should be noticed that theunDRXed region was almost red, signifying that the 〈0001〉 direction was oriented towards compression direction. However, the DRXed regions showed different colors, indicating that grain orientation was randomized after dynamic recrystallization. The (0001) pole figures are also presented in Fig. 8. Generally, the basal slip is preferentially activated during deformation and promotes grain rotation in a certain direction to form basal texture in Mg alloys [35]. In the present study, compression deformation can rotate the basal planes of the Mg −Zn −Ce alloy perpendicular to the compression direction (CD). Therefore, the as-compressedYu-zhou DU, et al/Trans. Nonferrous Met. Soc. China 30(2020) 2658−26682664Fig. 8 IPF images and their corresponding (0001) pole figures under different deformation conditions: (a) ln Z =25.5; (b) ln Z =20.77; (c) ln Z =16.43 (CD represents compression direction)samples exhibited a basal texture. Concurrently, the texture intensity was continuously weakened with decreasing Z parameters. Deformation parameters significantly affected texture evolution of RE- containing Mg alloys [14]. It has been reported that extrusion at low temperature (300 °C) inhibits the formation of the RE texture component in the Mg −Zn −Ce alloy [15] because of the hard activation of non-basal slip deformed at low extrusion temperature. However, RE texture was not detected in the Mg −Gd alloy deformed at high temperatures [14], which was considered to be the prohibition of shear bands at high temperatures. The difference of texture intensity in the Mg −Zn −Ce alloy of the present study should be related to the extent of dynamic recrystallization during hot deformation. The recrystallization region exhibited a weaker texture compared with the unDRXed region of the Mg alloys [36]. That texture intensity was gradually decreased with the decreasing unDRXed zone in the ZK series alloys [37]. XIA et al [38] believed that dynamic recrystallization was a main factor in weakening the texture intensity in Mg −6.8Gd −4.5Y −1.1Nd −0.5Zr (wt.%) alloy. This indicated that texture weakening in Mg alloysmight result from dynamic recrystallization. In the present study, the DRX regions increased with decreasing Z parameter, which led to a decrease of the overall texture intensity.To clarify the effects of deformation parameters on recrystallization texture in Mg −Zn −Ce alloys, the DRXed regions for the samples compressed with high Z parameters were separated and the corresponding (0001) pole figures are presented in Fig. 9. The DRXed grain size gradually increased with decreasing Z parameter. Nevertheless, basal texture intensity in the recrystallization regions showed a similar trend (4.80 (Fig. 9(a)) to 6.62 (Fig. 8(c)) in intensity).Texture weakening in RE-containing Mg alloys was proposed to be related to twinning inducing nucleation [11], shear band inducing nucleation [39] and solute segregation at grain boundaries or stacking faults [40]. Although the physical mechanism of texture weakening in Mg alloys is still controversial, it is generally accepted that the development of recrystallization texture is determined by the oriented nucleation theory and/or the oriented growth theory [41]. In the oriented nucleation theory, a specific grain orientationYu-zhou DU, et al/Trans. Nonferrous Met. Soc. China 30(2020) 2658−2668 2665Fig. 9 DRXed regions and their corresponding (0001) pole figures under different deformation conditions: (a) ln Z =25.5; (b) ln Z =20.77 (CD represents compression direction)formed and remained stable during subsequent grain growth. However, the oriented growth theory proposes that the orientation dependence of the grain boundary mobility is responsible for the recrystallization texture. In the present study, the sample (ln Z =25.5) with the finest DRXed grain size of about 3 μm exhibited a weaker texture intensity (Fig. 9(a)), while the intensity was strengthened with increasing DRXed grain size (Fig. 9(b)). It seems that the preferred grain growth led to an increase in texture intensity. Previous investigations have suggested that DXRed grain size is an important factor in forming RE texture component in RE-containing Mg alloys [42]. WU et al [43] detected that basal-oriented grains have grain growth advantage over other oriented grains in Mg alloys. The reduction in grain boundary energy is the driving force for grain growth. HOLM et al [44] suggested that texture development was associated with grain boundary anisotropy. The basal-oriented grains have low grain boundary energy compared with the non-basal grains, because of the close atomic arrangement in the basal planes. HUANG et al [45] showed that solute atoms were preferentially segregated to high-energy grain boundaries to reduce the grain boundary energy. Therefore, the solute atom Ce with a large atomicradius in the Mg −Zn −Ce alloy contrasts with the Mg atom and segregates to off-basal oriented grains. As a result, the grain boundary mobility of the off-basal oriented grains is reduced. In contrast, basal-oriented grains can grow more easily during grain growth, which contributes to the enhancement of the (0001) texture intensity with increasing of DRXed grains. Moreover, RIOS et al [46] indicated that the activation energy of high-angle grain boundary mobility is much smaller than that of low-angle grain boundary mobility. Therefore, high-angle grain boundaries would have high mobility compared to low-angle boundaries. Consequently, the basal oriented grains prefer to growing towards the off-basal grains during grain growth. Based on the above discussion, it is inferred that texture strengthening is related to the preferred grain growth.The present study revealed that the microstructure of the compressed Mg −Zn −Ce alloy differed significantly when deformed with different Zener −Hollomon parameters. A bimodal micro- structure was obtained when compressed with high Z parameters, in which the unDRXed region exhibited a stronger texture intensity and the DRXed region showed a weaker texture. This inhomogeneous microstructure and strong textureYu-zhou DU, et al/Trans. Nonferrous Met. Soc. China 30(2020) 2658−2668 2666intensity in the unDRXed regions deteriorated ductility. Nevertheless, the texture intensity increased with increasing the DRXed grain size. The microstructure characteristics provide a way to fabricate high performance Mg alloys with high strength and ductility, i.e. obtaining a complete DRXed microstructure with fine grains. Therefore, how to reduce the fraction of unDRXed regions and control the DRXed grain size is essential to achieve superior properties, which will be further investigated.4 Conclusions(1) The dynamic recrystallization and texture of the Mg−Zn−Ce alloy were affected significantly by deformation parameters.(2) Higher Zener−Hollomon parameter resulted in larger fraction of deformed regions and finer dynamically recrystallized (DRXed) grain sizes.(3) Texture intensity in the unDRXed regions was stronger compared to that in the DRXed regions, which contributed to a sharper texture intensity in the samples deformed with higher Zener−Hollomon parameter.(4) The recrystallized texture was intensified with increasing grain size, which was attributed to the preferred grain growth.References[1]CHENG Yuan-fen, DU Wen-bo, LIU Ke, FU Jun-jian,WANG Zhao-hui, LI Shu-bo, FU Jin-long. Mechanicalproperties and corrosion behaviors of Mg−4Zn−0.2Mn−0.2Ca alloy after long term in vitro degradation [J].Transactions of Nonferrous Metals Society of China, 2020,30: 363−372.[2]WANG X J, XU D K, WU R Z, CHEN X B, PENG Q M,JIN L, XIN Y C, ZHANG Z Q, LIU Y, CHEN X H, CHEN G,DENG K K, WANG H Y. What is going on in magnesiumalloys? [J]. Journal of Materials Science & Technology, 2018,34: 245−247.[3]ZHANG Yang, CHEN Xiao-yang, LU Ya-lin, LI Xiao-ping.Microstructure and mechanical properties of as-extrudedMg−Sn−Zn−Ca alloy with different extrusion ratios [J].Transactions of Nonferrous Metals Society of China, 2018,28: 2190−2198.[4]JIA Qing-gong, ZHANG Wei-xi, SUN Yi, XU Chun-xian,ZHANG Jin-shan, KUAN Jun. Microstructure andmechanical properties of as-cast and extruded biomedicalMg−Zn−Y−Zr−Ca alloy at different temperatures [J].Transactions of Nonferrous Metals Society of China, 2019,29: 515−525. [5]LIU Ke, LIU Jin-xue, LI Shu-bo, WANG Zhao-hui, DUWen-bo, QANG Qing-feng. Effects of secondary phases ontexture and mechanical properties of as-extruded Mg−Zn−Eralloys [J]. Transactions of Nonferrous Metals Society ofChina, 2018, 28: 890−895.[6]GIFFITHA D. Explaining texture weakening and improvedformability in magnesium rare earth alloys [J]. MaterialsScience and Technology, 2015, 31: 10−24.[7]ZHAO Hong-liang, HUA Yun-xiao, DONG Xiang-lei, XINGHui, LU Yan-li. Influence of trace Ca addition on texture andstretch formability of AM50 magnesium alloy sheet [J].Transactions of Nonferrous Metals Society of China, 2020,30: 647−656.[8]BALL E A, PRANGNELL P B. Tensile−compressive yieldasymmetries in high strength wrought magnesium alloys [J].Scripta Metallurgica et Materialia, 1994, 31: 111−116.[9]HIRSCH J, AL-SAMMAN T. Superior light metals bytexture engineering: Optimized aluminum and magnesiumalloys for automotive applications [J]. Acta Materialia, 2013,61: 818−843.[10]STANFORD N. Micro-alloying Mg with Y, Ce, Gd and Lafor texture modification—A comparative study [J]. MaterialsScience and Engineering A, 2010, 527: 2669−2677.[11]HANTZSCHE K, BOHLEN J, WENDT J, KAINER K U, YIS B, LETZIG D. Effect of rare earth additions on microstructure and texture development of magnesium alloysheets [J]. Scripta Materialia, 2010, 63: 725−730.[12]ZENGIN H, TUREN Y. Effect of La content and extrusiontemperature on microstructure, texture and mechanical properties of Mg−Zn−Zr magnesium alloy [J]. MaterialsChemistry and Physics, 2018, 214: 421−430.[13]ROBSON J D, TWIER A M, LORIMER G W, ROGERS P.Effect of extrusion conditions on microstructure, texture, andyield asymmetry in Mg–6Y–7Gd–0.5wt%Zr alloy [J].Materials Science and Engineering A, 2011, 528: 7247−7256.[14]STANFORD N, BARNETT M R. The origin of “rare earth”texture development in extruded Mg-based alloys and itseffect on tensile ductility [J]. Materials Science and Engineering A, 2008, 496: 399−408.[15]CHINO Y, HUANG X S, SUZUKI K, SASSA K,MABUCHI M. Texture and mechanical properties of Mg−Zn−Ce alloy extruded at different temperatures [J].Materials Transaction, 2011, 52: 1104−1107.[16]IMANDOUST A, BARRET C, OPPEDAL A, WHIT-TINGTON W, PAUDEL Y, KADIRI H. Nucleation andpreferential growth mechanism of recrystallization texture inhigh purity binary magnesium−rare earth alloys [J]. ActaMaterialia, 2017, 138(Supplement C): 27−41.[17]WU L B, LIU X H, WU R Z, CUI C L, ZHANG J H,ZHANG M L. Microstructure and tensile properties ofMg–Li–Al–Zn based alloys with Ce addition [J].Transactions of Nonferrous Metals Society of China, 2012,22: 779−785.[18]CHAI Yan-fu, HE Chao, JIANG Bin, FU Jie, JIANGZhong-tao, YANG Qing-shan, SHENG Hao-ran, HUANGGuang-sheng, ZHANG Ding-fei, PAN Fu-sheng. Influenceof minor Ce additions on the microstructure and mechanicalproperties of Mg−1.0Sn−0.6Ca alloy [J]. Journal of MaterialsScience and Technology, 2020, 37: 26−37.。
均匀化退火及挤压对Mg-Hg-Ga合金显微组织和耐腐蚀性能的影响

均匀化退火及挤压对Mg-Hg-Ga合金显微组织和耐腐蚀性能的影响刘莉;冯艳;王日初;彭超群;李晓庚【摘要】The microstructures of Mg-Hg-Ga alloy modified by homogenizing and hot extrusion were investigated by optical microscope,XRD and EBSD.The influence of homogenizing and hot extrusion on the corrosion behavior of Mg-Hg-Ga alloy was examined by hydrogen generation tests,potentiodynamic polarization,galvanostatic tests,impedance spectra (EIS) tests and current efficiency tests.The results show that the amount of second phase Mg2Hg significantly reduces after homogenizing.The hot extrusion promotes the dynamic recrystallization and refines the grains of Mg-Hg-Ga alloy,and the {0001} basal texture forms in the hot extruded alloy.The homogenizing promotes the corrosion resistance and anode efficiency of alloy and reduces the electrochemical activity of alloy.The hot extrusion improves the electrochemical activity,anode efficiency and reduces the corrosion resistance at the same time.The extruded alloy performs the most negative mean potential of-1.841 V(vs SCE),the largest hydrogen generation rate corrosion current density are 4.13 mL/(cm2·h) and 1.010 mA/cm2,respectively.The hydrogen generation rate and the corrosion current of the homogenized alloy are the smallest,which are 1.75 mL/(m2·h-1) and 0.241mA/cm2,respectively.The anode efficiency increases from 53.68% of as-cast alloy to 66.63% of extrusion alloy.%利用金相显微镜、X射线衍射、EBSD等检测方法分析铸态、均匀化退火态和挤压态Mg-Hg-Ga合金的显微组织,并采用析氢浸泡法、动电位极化扫描、恒电流放电、交流阻抗法、阳极效率测试,研究均匀化退火及挤压对Mg-Hg-Ga阳极材料腐蚀电化学性能的影响.结果表明:均匀化退火使铸态组织中第二相数量明显减少,挤压后合金发生动态再结晶,晶粒明显细化,并形成{0001}基面织构.均匀化退火提高合金的耐腐蚀性能和阳极电流效率,降低合金的电化学活性.热挤压降低合金的耐腐蚀性能,提高合金的电化学活性和阳极电流效率.挤压态合金表现出最负的平均放电电位-1.841 V(vs SCE),最大的析氢速率4.13 mL/(cm2·h)和腐蚀电流密度1.010mA/cm2.均匀化退火态合金的析氢速率和腐蚀电流密度下降到最小,分别为1.75 mL/(cm2·h)和0.241 mA/cm2,阳极电流效率由铸态的53.68%上升到挤压态的66.63%.【期刊名称】《中国有色金属学报》【年(卷),期】2017(027)001【总页数】8页(P32-39)【关键词】Mg-Hg-Ga合金;挤压;均匀化退火;显微组织;电化学性能【作者】刘莉;冯艳;王日初;彭超群;李晓庚【作者单位】中南大学材料科学与工程学院,长沙410083;中南大学材料科学与工程学院,长沙410083;中南大学材料科学与工程学院,长沙410083;中南大学材料科学与工程学院,长沙410083;中南大学材料科学与工程学院,长沙410083【正文语种】中文【中图分类】TG113;TG146.1+1海水激活电池作为一种重要的能源,广泛应用于水下设备,依靠阳极金属材料在海水中的腐蚀溶解提供阳极放电电流[1]。
镁合金动态再结晶的研究现状

近年来,随着能源供求的紧张、不可再生能源的大量消耗,能源危机逐渐凸显。
为节约能源,各国对新材料的需求更加迫切,尤其是轻合金材料,如镁及镁合金材料。
镁合金具有密度小、比强度高等优点,是目前工业应用中最轻的工程材料[1]。
然而,镁合金为密排六方结构,与其它合金相比结构对称性低,因此成形性较差,从而限制镁合金特别是变形镁合金在工业上的应用。
动态再结晶(DRX )是在热塑性变形过程中发生的再结晶[2],作为一种重要的软化和晶粒细化机制,动态再结晶对控制镁合金变形组织、改善塑性成形能力以及提高材料力学特性具有十分重要的意义。
镁合金动态再结晶随合金变形方式的不同存在一定的差异,因此,系统研究其动态再结晶形核与晶粒长大的规律,完善镁合金的塑性变形理论体系,并利用动态再结晶细化晶粒的原理有效控制镁合金的组织和性能,将在生产中具有极为重要的应用价值[3-6]。
简述了当今国内外现有的镁合金动态再结晶机制和变形温度、变形速率、变形程度以及稀土元素对镁合金动态再结晶的影响。
1影响因素通常镁合金塑性变形过程中变形温度、应变速率、应变量的改变和稀土元素的添加都会影响塑性变形机制,因此,会对动态再结晶的行为造成影响[7]。
1.1变形温度的影响变形温度是通过改变位错密度的累积速率影响DRX 形核和长大,随着温度的升高、原子的扩散、位错的交滑移和晶界的迁移得到加强,变形的临界切应力减小[8-9]。
合金中原子的热振荡加剧、扩散速率增大、位错的运动(滑移、攀移、交滑移)及位错缠结滑动比低温时更容易,使动态再结晶的形核率增大,晶界的迁移能力明显增强,因此,提高变形温度可以促进镁合金动态再结晶的发生[10]。
何运斌等[11]对热变形中的ZK60镁合金研究后发现,变形温度增加时,试样的平均动态再结晶体积分数增大,合金变形更加均匀。
S.M.Fatemi-Var ⁃zaneh ,A.Zarei-Hanzaki 等在对AZ31镁合金动态再结晶的研究中指出,在试验温度范围内,试样的组织随非连续动态再结晶的发生而改变,如动态再结晶晶粒的尺寸与动态再结晶晶粒的体积分数均随变形温度的上升而增大[12],如图1所示。
材料成型专业英语词汇
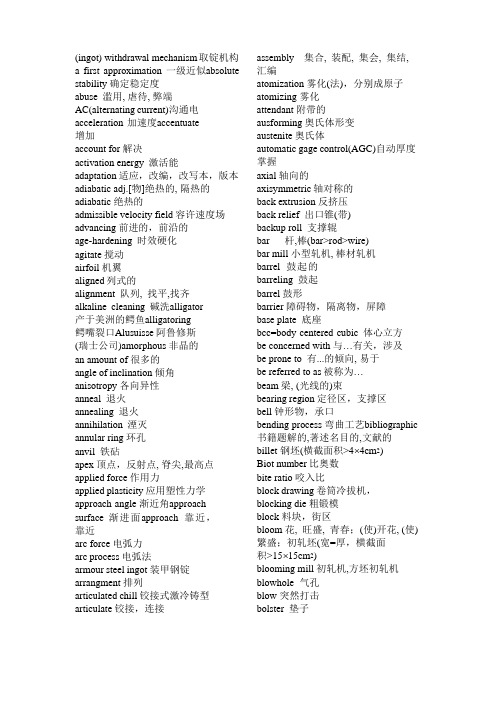
(ingot) withdrawal mechanism 取锭机构a first approximation 一级近似absolute stability 确定稳定度abuse 滥用, 虐待, 弊端AC(alternating current)沟通电acceleration 加速度accentuate增加account for 解决activation energy 激活能adaptation 适应,改编,改写本,版本adiabatic adj.[物]绝热的, 隔热的adiabatic 绝热的admissible velocity field 容许速度场advancing 前进的,前沿的age-hardening 时效硬化agitate 搅动airfoil 机翼aligned 列式的alignment 队列,找平,找齐alkaline cleaning 碱洗alligator产于美洲的鳄鱼alligatoring鳄嘴裂口Alusuisse 阿鲁修斯(瑞士公司) amorphous 非晶的an amount of 很多的angle of inclination 倾角anisotropy 各向异性anneal 退火annealing 退火annihilation 湮灭annular ring 环孔anvil 铁砧apex 顶点,反射点, 脊尖,最高点applied force 作用力applied plasticity 应用塑性力学approach angle 渐近角approach surface 渐进面approach 靠近,靠近arc force 电弧力arc process 电弧法armour steel ingot 装甲钢锭arrangment 排列articulated chill 铰接式激冷铸型articulate 铰接,连接assembly 集合, 装配,集会, 集结, 汇编atomization 雾化(法),分别成原子atomizing 雾化attendant 附带的ausforming 奥氏体形变austenite 奥氏体automatic gage control(AGC)自动厚度掌握axial 轴向的axisymmetric 轴对称的back extrusion 反挤压back relief 出口锥(带)backup roll 支撑辊bar 杆,棒(bar>rod>wire)bar mill 小型轧机, 棒材轧机barrel 鼓起的barreling 鼓起barrel 鼓形barrier 障碍物,隔离物,屏障base plate 底座bcc=body centered cubic 体心立方be concerned with 与…有关,涉及be prone to 有...的倾向, 易于be referred to as 被称为…beam 梁, (光线的)束bearing region 定径区,支撑区bell 钟形物,承口bending process 弯曲工艺bibliographic 书籍题解的,著述名目的,文献的billet 钢坯(横截面积>4⨯4cm2)Biot number 比奥数bite ratio 咬入比block drawing 卷筒冷拔机,blocking die 粗锻模block 料块,街区bloom 花,旺盛,青春;(使)开花, (使) 繁盛;初轧坯(宽=厚,横截面积>15⨯15cm2)blooming mill 初轧机,方坯初轧机blowhole 气孔blow 突然打击bolster 垫子bottom-pressure casting 加压下铸breakage 损坏breakdown 破环,打碎breakthrough 临界点bridle roll 活套张紧辊,拉紧辊broadside mill 宽展机buckle 带扣;扣住, 变弯曲;扣箍,纹buckle 弯曲buckling 纵向弯曲build up 增进,增大bulge 鼓起,突出bull block 卷取机,冷拔机卷筒buoyancy 浮力burning 过烧butt 粗大的一端, 残料calibration 标度, 刻度,校准call upon 要求,号召, 访问cam 凸轮camber 拱形;呈拱形;隆起,上拱度canning 包套capital investment 资金总额,资本投资carbon block 碳砖炉衬, 碳砖衬里casing 外套category类别,种类cell wall晶胞壁cellular growth 分格生长,胞状长大cellular 胞状的cellular 细胞的, 网状的,蜂窝状的,胞状的cemented carbide 硬质合金cementite 渗碳体centrifugal离心的ceramic 陶瓷的chain drive 链条传动channel 槽,沟charge炉料,坯料chevron cracking V 形裂纹,人形裂纹chevron 人字形chevron 人字形,V 字形chilling block 激冷块,激冷试块,冷铁chill 激冷铸型chill 激冷铸型chipping 刨削circular symmetry 圆对称civil engineer 土木工程师clamp 卡紧clearance 间隙, 空隙climb 攀移close control 周密掌握,准确检查closed-die forging 闭模锻造cluster mill 多辊式轧钢机coefficient of spread 宽展系数cogging mill 初轧机, 开坯机, 粗轧机cog 开坯coil up 盘绕,盘起coiler 卷取机cold finish 冷加工精整cold reduce 冷减径,冷轧cold reduction 冷压缩;冷减径collapsible 折叠式combined stress 综合应力,组合应力commercial alloy 工业合金compact shape 紧凑型competewith 与...竞争,比得上compete竞争competing process 竞争性工艺complexity 简单性compocasting 混成砂型铸造compressive stress 压应力concave 凹面的concentricity 同心concerned with 有关conductor grade 导电级conical 圆锥的, 圆锥形的constant-volume relationship 体积不变关系constitutional supercooling 组成过冷,组分过冷constraint factor 约束系数constraint 强制,约束constrain 约束consumable electrode remelting 自耗电极再熔contact-bend-stretch (CBS) rolling process 接触-弯曲-拉伸轧制过程(滚压法)container 挤压筒containerless 无模continuous casting 连(续浇)铸continuous hot-strip mill 连续式带材热轧机continuous mill 连续式轧机continuous rheocaster 连续流变铸造机contour 轮廓,周线, 等高线;外形,轮廓contour 轮廓,等高线,等值线convection 对流conventional strain 传统应变,名义应变=apparent strain=nominal strain convention 协定,惯例,习俗,规定conversion coating 可换涂层convex 外表弯曲如球的外侧, 凸起的copper rim 铜环cored structure 核状偏析组织correlation 相关creep deformation 蠕变变形creep failure 蠕变破坏creep test 蠕变试验critical打算性的cross rolling 横轧cross slip 交滑移crosshead 十字头,卡头crown 隆起crucible 坩埚crumble 裂开crystallographic texture 晶体学织构cumulative 累积的Cupping 杯突curling卷曲,卷边cylindrical圆柱体的DC(direct current)直流电dead soft 极软,完全软dead zone 死区decarbonization 脱碳,脱碳作用,除碳法deep drawing 深冲,深拉degreasing(碱洗)除油degree Celsius (degree Centigrade) 摄氏度delivery speed 轧出速度dendritic 枝晶dentrite 枝晶departure 偏离dependent variable 应变量,他变量development work 试制工作diamond 金刚石die block 模块,模具坯料die fill 模填充die half 半模die head 模头,冲垫die holder 凹模固定板;模座die stack 模具组合die throat 模孔dimensional tolerance 尺寸公差dimensional tolerance 尺寸公差direct-compression-type process 直承受压型工艺direct-drive pumping system 直接传动泵送系统direction extrusion 直接挤压,正挤压discard 丢弃, 抛弃;放弃discoloration 变色, 污点dislocation 位错dispersed 分散的dissipation 消散,分散, 铺张,消耗dissipation 耗散,逸散,能量耗散disturb 干扰,扰动diverse 不同的, 变化多的domed-shaped 圆顶形,半球形double diffusive 双集中draft allowance 倾斜角容许误差draft angle 倾斜角,脱模角drawbench 拉床,冷拔机drawhead 拉拔机机头,拉床机头drawing down 锻拉drawing out 拔长drawing 拉拔drive 驱使, 动力, 推动driven roll 从动辊driven roll 从动辊drop hammer 落锤drop tower 吊塔,下垂塔droplet 液滴ductile 易延展的ductility 延展性dummy block (在挤压活塞与热金属之间)挤压垫dynamic recovery 动态回复dynamic recovery 动态回复dynamic recrystallization 动态再结晶edging pass 立轧道次edging roll 立辊,轧边辊edging 边锻,侧锻effect 效应elastic constant 弹性常数elastic modulus 弹性模量electric discharge machining 电火花加工electrical cable 电缆electrode电焊条,电极electroplatedslab 电镀板electro-slagrefining 电渣精炼eliminate消退,排解ellipsoidal 椭球形embrittle 使变脆encase 嵌入engineering strain 工程应变enthalpy difference 焓差enthalpy(热)焓enthalpy 焓entropy 熵EP(extra-pure)超纯的evolved as heat 以热放出exaggerate 夸大, 夸大excessive 过分的expenditure消耗,支出, 花费exponential指数的extension 延长extensive 大规模的extraction 抽取,排出extrapolating 外延,外推fabrication 制造facilitate 使简洁Fahrenheit (degree)华氏度fall off 下降,削减fall within 属于fault层错,断层fcc=face centered cubic 面心立方feed roll 送料辊ferrite 铁素体fibrous 纤维的fillet 圆角fine detail 细节finishing die 精模,成品模finishing roll 精轧轧辊finishing stand 精轧机座,成品机座finishing temperature 终轧温度,最终温度finishing train 精轧机组finite element method methods 有限元法fir-tree cracking 杉树状裂纹fir-tree crystal 枝晶fissue 裂缝,龟裂flange 凸缘,法兰flash gutter 飞边槽flash 飞边,毛刺flat die 平模flat tool 平口刀具flat-faced die 平模flatness 平直度,平坦度, 平面flex 挠曲flexile roll 挠性轧辊floating bend roll 游动弯曲辊floating plug 游动芯头floating zone technique 浮动区域技术, 区域精炼技术flow resistance 流阻,抗流变性flux of matter 物质通量flux pool 掩盖剂熔池flying micrometer 快速测微仪, 飞测千分尺FM (Frequency Modulation) 调频foil 箔,薄金属片follower block 从动块,从动机构局部follower pad 挤压垫片forging hammer 锻锤forging press 锻压机four-high mill 四辊轧机(机座) fractional reduction 缩减分数fracture criteria 断裂判据(准则) fracture toughness 断裂韧度fracture 裂开,断裂framework 构架,框架frictional condition 摩擦条件frictional drag 摩擦拽力frictional resistance 摩擦阻力frictional restraint 摩擦阻力full hard 全硬化,淬透fullering 压槽锻fuller 压槽fundamentals根本原理funnel 漏斗,烟窗,烟道funnel 漏斗gage(=gauge) 标准度量,计量器,估量Geiringer velocity equation 盖林格速度方程general solution〔微分方程的〕通解glass pad 玻璃垫,玻璃衬垫glassy 玻璃状的graphite 石墨gravitational acceleration 重力加速度grid patter 网格状线,网格图形grinding 磨削grooved roll 有槽grooving 开槽guard against 提防, 预防gutter 槽,沟hammering锻锤headroom 净空, 头上空间, 净空高度heat supplied 供热heat transfer 换热,传热heavy scale (钢锭的)厚氧化皮Hencky equation 汉基方程hexagonal 六角形的HF(high frequency)高频Hodograph 速度图,矢端图,速端曲线homogeneous upset test 均匀墩粗试验homogeneous 均匀的horizontal DC casting 水平连铸hot shortness 热脆hot shortness 热脆hot tearing 热撕裂,形成热裂缝hot torsion test 高温扭转试验housing 机架hub 轮毂,磁盘套,套筒hydraulic accumulator system 液压储能系统hydraulic jack 液压千斤顶hydraulic mechanism 液压机构hydraulic press 液压机hypercooling 特定程度的过冷hypocooling 亚冷,次冷I beam 工字钢, 工字梁ideal work of deformation 抱负塑性(变形)功impact blow 冲击作用impact extrusion 冲挤,冷挤压impact 碰撞,冲击impact 撞击,冲击imperative 强制的, 紧急的, 必要的implementation 执行,实现impose 利用,施加影响的impression die 压模in term of 依据,凭借…in terms of 从…角度,依据…in terms 在谈判(协商)中,依据…incipient melting 初熔incline 倾斜, 斜坡, 斜面included angle=separation angle 夹角inclusion 夹杂物inclusion 夹杂物Incorporate into 合并,缩写成…increment 增量indentation 压痕indenter 受托代购商,压头indenting 压窝independent variable 独立变量,自由变量indirect extrusion 间接挤压,反挤压indirect-compression process 间承受压型工艺induction heating 感应加热inert 惰性initially 开头inlet nozzle 入口嘴innovative 创的in-process 在线installation 安装,装臵installation 装臵,设备instantaneous 瞬间的,即刻的interdependence 相互依靠intergranular 晶粒间的intermediate annealing 中间退火intermediate frequency(i-f)中频intermediate 中间的internal 在中心的Internal-combustion engine 内燃机interphase boundary 相间边界interpolate 窜改,添写进去, 插入语句intersperse 交替interval 区间,间隔intricate 简单的invariable 不变地,总是inverted extrusion 反挤压irrespective 不考虑isenthalpic 等焓的isothermal forging 等温锻造isotope 同位素isotropic 各向同性的isotropy 各向同性jaw 叉钳, 钳夹jaw 钳夹keep pace with 与..同步,与…齐步前进lamination 迭片构造;层压land width 通道宽度lap 重叠large scale plasticity 大比例塑性变形late stage 晚期的lead bath 铅淬火槽lead sheathing 包铅层lead 铅leveler (=leveller) 轧平机,矫直机likewise 同样地limit design 极限设计limited segregation 有限偏析limiting deformation 极限变形liner 衬垫linkage 连接,链接logarithm 对数longitudinal 纵向的loose 松动的,疏松的,不准确lubricant 润滑剂lying flat 平放lying on edge 侧立mandrel drawing 长芯棒管材拉拔mandrel 心轴;芯棒,顶杆mandrel 芯棒,顶杆mandrel 芯杆manifest 说明,呈现Marangoni effect 马兰各尼效应(界面张力梯度引起的流淌)marstraining 马氏体形变热处理martensite 马氏体mass feeding〔质量〕补缩mass flow rate 质量流量mast 桅杆,炉柱match 协作matrix method 矩阵法matrix 矩阵measure out 测量出mechanical equivalent of heat 热功当量mechanical press 机械压力机mechanics 力学,机构meet .. requirement 满足…要求melt drag 熔体拖拽法melt spinning 熔体旋压(纺丝,拉丝)工艺merchant mill 条钢轧机metal maching processing 切削加工metal pool 金属熔池metalworking process 金属加工工艺metastable 介稳的milestone 里程碑mill edge 轧制的(未经剪切的)边, 热轧边mill production 轧机生产力量mill product 轧制产品mill product 轧制成品mill spring 轧机弹跳mixer 搅拌器modelling 模型化,模拟monocrystal 单晶monograph=treatise 专论,专题论文morphological 形态的,构造的morphological 形态学的motor 电动机mould cavity 模腔multiple passes 多道次multiple 多样的, 多重的;成倍增加multipule –die machine 多模拉丝机mushy freezing zone 糊状凝固区music wire 琴弦,琴用钢丝natural and error 尝试法,试错法natural strain 自然应变necking 颈缩Newtonian suspension 牛顿悬浮液nib 尖端,尖头,楔尖劈nigh-current source 高电流源nomenclature 术语nonferrous metal 有色金属non-heat-treatable 不行热处理的novel condition 条件nucleated source 形核源nucleation 形核(现象)numerical controlled(N/C)machining 数控切割oblong 长方形,椭圆形offset 错排,偏移ohmic resistance 欧姆电阻on the basis of 依据onset 发端open-die forging 自由锻,开式模锻opening 通路order of complexity 简单程度orifice 孔, 口;喷嘴oval 卵形的, 椭圆的overlap 重叠oxalate 草酸(盐)oxidation 氧化oxide stringer 氧化皮细纹,氧化皮发纹oxygen lance 氧气喷枪packing 填料parallelland 平行带parting line 分型线,分隔线patenting 铅浴淬火payload 有效载荷pearlite 珠光体, 珍宝岩Pechiney 皮切尼(法国铝公司) pendulum mill 摆式轧机periphery 边缘,外围perlite 珍宝岩,珠光体perpendicularto 垂直于,与…正交pickle 酸洗,腌, 泡pickling 酸洗,浸洗pierce 刺穿, 穿透,钻孔,穿孔piercing 冲孔piercing 打孔pinch roll 夹送辊,夹紧辊,摩擦辊pinch 捏,撮pipe diffusion 管集中pipe 重皮(缺陷)piston 活塞,阳模pit 深坑, 深渊, 陷阱,凹陷planar 平面的plane front 平面波阵面,平面长大plane of shear=shear plane 剪切面plane-strain compression test 平面应变压缩试验plane-strain 平面应变planetary mill 行星式轧机planishing roll 平坦辊plasma torch 等离子喷枪,等离子焰炬plasma-arc melting 等离子熔炼plasma-arc 等离子弧plastic work 塑性功plastic-rigid solid 刚塑性体plastometer 塑性计platen 压盘platform 升降台,送料台plug drawing 定径拉拔plug 芯头point 弄尖polygon 多角形, 多边形porosity 孔隙positive正的,阳极的postpone 延迟,暂缓powder rolling 粉末轧制成型power hammer 动力锤predominate 占优势,统治,支配preferable 优先选择的prefered orientation 择优取向preform 预变形prescribe 规定,指示presentation 介绍,陈述,表达pressing 压制pressure plate 压力板,压板pressure vessel 压力容器prestrain 预应变primary roughing mill 初始开坯机principal stress 主应力prior coating 预涂层procedure 工序processing operation 工艺作业product mix 产品系列, 产品组合production run 生产性运行profile侧面profile 轮廓projection 突出局部,凸块propeller shaft 螺旋桨prototype 试验模型psi=pounds per square inch 磅/平方英寸pulling 拖,拽pullover 拔送器pull 拉力,张力pull 拉力,张力,拉,拔punching 冲孔,穿孔punch 冲孔,打孔,冲压机,冲床pyro-“火”,”热”,”焦”等含义pyrometallurgy 火法冶金学pyrometer 高温计quantitative 定性量的quenching 激冷,淬火radial coordinate 极坐标,径向坐标radial 径向的rail 钢轨,导轨,横杆, 围栏, 扶手ram 杆,推杆,挤压杆ram speed (压力机)滑块速度;冲击速度rationalize 合理化reaction 反响, 反作用,反动(力) reaction 反响,反作用力rear 后面, 后面的, 反面的;举起recalescence 金属潜热的释放,复辉,再炎热recalescence 再炎热recalescence 再辉,金属潜热的释放recast 重铸,重算,重做recess 凹进处reciprocate (使...)往复,互换recovery process 回复工艺,恢复过程rectifier 整流装臵reduction 削减,压下,缩减量,复原redundant work 附加功,关心作业redundant work 附加工,关心作业reeling 矫直refinish 再修整refractory material 难熔材料,耐高温材料refractory metal 耐高温金属refractory 难掌握的, 难熔的,耐火材料regime 状况,体制removal 切除reorientation 重取向repeater 转发器reposition重配臵reservoir 贮藏处,贮备retention 保持,保存reversible 可逆的reversing mill 可逆式轧机rheocasting 流变铸造rheological 流变的rheo-流变的rib 筋(jin),肋(lei)ridge 脊,隆起局部right angle 直角rigid block 刚性体rinse 漂洗,清洗rod 棒,杆roll 轧辊roll caster 滚动铸型铸造roll forming 滚轧成形,辊锻成形, 轧锻rolled sheet 辊轧板roller leveling 辊式矫直roller-leveler 辊式矫直机,钢板压平机roller-leveling machine 辊式矫直机rolling mill 轧钢厂rolling 滚压Rolls Royce 劳斯莱斯rotor 转子roughing stand 粗轧机座roughing train 粗轧机组rounded apex 圆形底流排出口rpm=revolutions per minuterunout table 输出辊道rupture裂开,折断,裂缝safetyvalve 安全阀scab 疤, 痂scale 鳞皮scalebreaker mill 破鳞机scalp 剥皮scratch 划伤screw 压下丝杠,螺丝seam 线,缝seam 缝,线,裂缝seating surface 支持面secondary dendrite arm spacing 二次枝晶臂间距secondary tensile stress 副拉应力sedimentation 沉淀segregated cell 偏析晶胞self-diffusion 自集中Sendzimir mill 森吉米尔式轧机, 二十辊冷轧机sensor 传感器servocontrol 伺服掌握severity 严峻,剧烈,.严峻强度sharp 锐利的, 锐利的, 明显的,猛烈的,刺耳的,急剧的,精明的,灵敏的shear plane 切变面, 剪切面shear strength 切变强度shearedplate 切边的中厚板shearingprocess 剪切工艺sheathing 掩盖物, 罩子,加护套sheet-metal金属薄板,金属片ShiroKobayashi 小林史郎shrinkage porosity 收缩疏松,缩松,松心shrunk shrink 的过去式和过去分词(使) 收缩,(使)缩小side view 侧视图simulate 模拟simulation 仿真,模拟sinking drawing 减径拉拔sinking 减径拔管sinter 烧结skin pass 外表冷轧,外表光轧skylab 太空试验室skylark 云雀,火箭slabanalysis 主应力法slabmethod 主应力法slabbing mill板坯初轧机slab扁锭(宽≥2⨯厚,横截面积>10⨯10cm2)slag 电渣sleeve 套slip-line field theory 滑移线场理论sliver 渣粒sliver 毛刺,渣粒slope 斜坡, 斜面, 倾斜; 使)顺斜slug 毛坯solidification front 凝固前沿solidification interval 凝固间隙solidus 固相线solidus 固相线soluble 可溶的solute partition 溶质分区solute profile 溶质分布solvus 固溶度曲线sound product 发声产品sounder casting 较好的铸件sounding rocket 探测火箭soundness 安定性,致密性specific heat 比热spheroidization 球化处理spiral constriction 螺旋收缩splat cooling 急冷,喷涂细片冷却法splat 椅背中间纵立长条木,薄片激冷金属spray method 喷射成型法spread law 宽展定律spread ratio 宽展比spread宽展spring temper 弹性回火spring wire 弹簧钢丝squeeze ratio 挤压比squirt 喷射stacking –fault energy 层错能stagnant 停滞的, 迟钝的stand 机架steel casing 钢外套stem 茎, 杆stepped cone multiple-pass wiredrawing 级轮多道次拉伸机stepped cone 级轮sticking friction 粘着摩擦stock 原料,坯料stool(模)底板straightener 矫直机strainhardening 应变硬化strain phase transformation 应变诱导相变strand stand 中间机架stretch forming 拉伸成形,拉伸造型stretcher strains 滑移线streteher leveling 拉伸矫直stringer 发纹stroke 行程subsequence 后继, 随后subsidiary 补充的,关心的substantially 充分地substantial 实质的,真正的substructure 亚构造succeeding 后续的sulfate 硫酸盐superalloy 高温合金superimpose 重叠,添加superimpose 添加, 双重, 迭叠,重叠superior surface finish 高级外表光滑度surface finishing 外表抛光,精整surface finish 外表抛光,外表精整surface melting 外表熔解suspending medium 悬浮介质swager 锻锤,锤锻机swagging 旋锻,环锻synchronize 同步tandem mill 连轧机,串列式轧机tandem 序列,串列的taper 渐渐变细Teflon=polytetrafluoroethylene 特氟隆(聚四氯乙烯) temper rolling 外表光轧,平坦temper 回火tenfold 十倍的,成十倍tension type process 张力型工艺terminal curve 末端曲线terminology 术语,词汇theory of plasticity 塑性理论thermal conductivity 热导率thermal shock 热冲击thermomechanical processing 形变热处理工艺thermomechanical treatment 形变热处理thermosolutal fluid 热熔流体thin skin 薄皮thixocasting 触变铸造thixotropic property 触变性质thixotropic slurry 触变浆料thixo-触变的thread rolling 滚丝, 搓丝throughput n.生产量, 生产力量, 吞吐量throughput 吞吐量tin 锡titanium 钛top view 上视图topological 拓扑的total system 综合系统toughness 刚度,韧性,toward this end 为此,因此tractable 易处理的transformer 变压器transverse 横的transverse 横向的trimmededge 铣过的底边trimming die 修整模,修边模trim 密封面,修整,装饰true strain 真应变tube drawing 拉管tube drawing 拉管tube winking 缩口拉拔,减径拉拔,空拉tubular 管状的tundish 漏斗tungsten 钨turbine blade 涡轮叶片turbine 涡轮turn to 求助于,转向,致力于turntable 转台,回转台two band caster 双带铸造机(Hazelett process 黑兹利特工艺)two-high mill 二辊轧机Ugine-Sejournel process 尤金-塞焦耐特热挤压工艺,玻璃润滑剂高速挤压法UHF(ultra-high frequency)超高频uncoiler 开卷机, 拆卷机undercool 过冷uniaxial compression 单向压缩uniaxial 单轴的uniform-deformation energy method 均匀变形能量法unilateral 单边的,单面的universal mill 万能轧机universal-mill plate 齐边钢板unpinning 脱钉upper- (lower-) bound solution 上(下)界解upper limit 上限upper-bound 上界upsetting 镦粗upset 倒转upward向上弯vacuum arc refining 真空电弧精炼valved nozzle 阀门嘴versatile 通用的, 万能的versatility 多功能性versatility 多功能性,多用性VHF(very high frequency)甚高频vicinity 邻近,四周violate 违犯的,亵渎的,干扰,违反,阻碍, 侵害virtually 事实上,实质上viscosity 黏度volume fraction solid 固相体积分数vortex 涡流war 翘曲, 扭曲, 热变形warping 翘面, 扭曲, 变形web 连接板,薄片,腹板,网状物wedge 楔;楔入,楔进wettability 润湿性wheel caster 轮铸(Properzi process 普罗佩兹工艺)wide strip 宽带材windupreel 缠绕卷盘wiredrawing 拉线,拔丝with respect to 关于, 至于withdrawal chamber 退锭室withdrawal 放出workability 可使用性,可加工性wrought 锻件\轧材\冷拔产品的总称yield point 屈服点yield-stress 屈服应力yield 屈服zipper break 拉链式裂开。
矿物代号和岩石中英文名称

Ab = Albite 附录(Appendixes)一、矿物代号钠长石Kp = Kalinophilite 钾霞石Ac = AcmiteAct = ActinoliteAe = AegirineAf = Alkali feldspar Alm = AlmandineAls = Al2SiO5 mineral Am = AmphiboleAn = AnorthiteAnd = Andalusite Andr = AndraditeAnl = AnalciteAnn = AnniteAnt = AnthophylliteAr = AragoniteAug = AugiteBi = BiotiteBrc = BruciteCc = CalciteCh = ChloriteCld = ChloritoidCo=CorundumCoe = coesiteCpx = Clinopyroxene Crd = CordieriteCrs = CrossiteCum = Cummingtonite Der = DeeriteDi = DiapsideDia = DiamondDol = DolomiteEn = EnstatiteEp = EpidoteF = Fluid(H2O)Fa = FayaliteFo=ForsteriteFs = FerrosiliteGl = Glaucophane Gra = GraphiteGro = GrossularGt = GarnetHb = HornblendeHd = Hedenbergite Hu = HeulanditeHy = HyperstheneIll = IlliteJd=JadeiteJed=JedriteKao = KaoliniteKf = K-feldspar 锥辉石阳起石霓石碱性长石铁铝榴石Al2SiO5矿物角闪石钙长石红柱石钙铁榴石方沸石羟铁云母直闪石文石普通辉石黑云母水镁石方解石绿泥石硬绿泥石刚玉柯石英单斜辉石堇青石青铝闪石镁铁闪石迪尔石透辉石金刚石白云石顽火辉石绿帘石流体(H2O)铁橄榄石镁橄榄石铁辉石蓝闪石石墨钙铝榴石石榴石普通角闪石钙铁辉石片沸石紫苏辉石伊利石硬玉铝直闪石高岭石钾长石1Ky = KyaniteL = Liquid = meltLc=LeuciteLm = LaumontiteLw = LawsoniteMar=MargariteMc=MicaMgn = MagnesiteMi = MicroclineMm = MontmorilloniteMs = MuscoviteMt = MagnetiteNe = NepherineOl = OlivineOm =OmphaciteOpx = OrthophyroxeneOr = OrthoclasePg = ParagonitePhl = PhlogopitePhn = PhengitePie = PiemontitePig = PigeonitePl = PlagioklasePrh = PrehnitePrl = PyrophyllitePu = PumpellyitePx = PyroxenePyr = PyropeQ = QuartzRie = RiebeckiteSan = SanidineSps = SpessartineSt = StauroliteStp = StilpnomelaneTc=TalcTr=TremoliteTs=TschermakiteV =VapourVer=VermiculiteWm = White micaWo=WollastoniteWr=WairakiteSe = SericiteSer = SerpentineSil = SillimaniteSm=SmeciteSp = SpinelWu=WustiteZo = Zoisite蓝晶石液体= 熔体白榴石浊沸石硬柱石珍珠云母云母菱镁矿微斜长石蒙脱石白云母磁铁矿霞石橄榄石绿辉石斜方辉石正长石钠云母金云母多硅白云母红帘石易变辉石斜长石葡萄石叶腊石绿纤石辉石镁铝榴石石英钠闪石透长石锰铝榴石十字石黑硬绿泥石滑石透闪石契尔马克分子蒸汽蛭石白色云母硅灰石斜钙沸石绢云母蛇纹石夕线石蒙皂石尖晶石方铁矿黝帘石二、汉英对照岩石学名词索引AA′KF图(A′KF diagram)ACF图(ACF diagram)AFC 模式(assimilation and fractional crystallization)AFM图(AFM diagram)A 型花岗岩(A-type granites)I 型花岗岩(I-type granites)M 型花岗岩(M-type granites)P-T-t轨迹(P-T-t path)S 面(S-safaces 或S-planes)S 型花岗岩(S-type granites)阿波罗(Apollo)阿尔卑斯型超基性岩体(Alpine-type ultrabasic rocks)阿拉斯加型(Alaska-type)安山岩(andesite)岸礁(shore reef)暗拼岩(appinite)暗色体(melanosome)奥长花岗岩(tronndhjemite)B白榴石响岩(leucite phonolite)白榴岩(leucitite)白片岩(white schist)白云石化(dolomitization)斑点构造(spotted structure)斑脱岩(bentonite)斑杂构造(taxitic structure)斑状变晶结构(porphyroblastic texture)斑状结构(porphyritic texture)板块(plate)板劈理(slaty cleavage)板岩(slate)板状等粒结构(equant tabular texture)板状构造(slaty structure)板状交错层(plate cross-bedding)半晶质结构(hemicrystalline texture)半自形变晶(hypidioblastic)2 半自形晶粒状结构(hypidiomorphic-granular texture)包含结构(poikilitic texture)包卷层理(convoluted structure)包卷构造(convoluted structure)雹痕(hail print)堡礁(barrier reef)爆发(explosions)碧玄岩(basanite)碧玉岩(jasperite)变斑晶(porphyroblast)变晶(blast)变晶鲕(metacrystal ooid)变晶结构(blastic texture)变晶系(crystalloblastic series)变嵌晶(poikilolblast)变形(deformation)变形带(deformation band)变形结构(deformation texture)变形双晶(deformation twins)变形纹(deformation lamellae)变余构造(palimpsest structure)变余结构(palimpsest texture)变余糜棱岩(blastomylonite)变质带(metamorphic zone)变质反应(metamorphic reaction)。
- 1、下载文档前请自行甄别文档内容的完整性,平台不提供额外的编辑、内容补充、找答案等附加服务。
- 2、"仅部分预览"的文档,不可在线预览部分如存在完整性等问题,可反馈申请退款(可完整预览的文档不适用该条件!)。
- 3、如文档侵犯您的权益,请联系客服反馈,我们会尽快为您处理(人工客服工作时间:9:00-18:30)。
Materials Science and Engineering A485 (2008) 375–382Dynamic recrystallization of Mg and Mg–Y alloys:Crystallographic texture developmentR.Cottam a,∗,J.Robson a,G.Lorimer a,B.Davis ba School of Materials,Materials Science Centre,The University of Manchester,Grosvenor Street,Manchester M17HS,United Kingdomb Magnesium Elektron Ltd.,PO Box23,Rake Lane,Swinton,Manchester M270D,United KingdomReceived21June2007;received in revised form30July2007;accepted11August2007AbstractPure magnesium and three binary Mg–Y alloys(0.23,0.84and2.71wt%Y)have been deformed in plane strain compression under conditions where dynamic recrystallization(DRX)is observed.The development of crystallographic texture during deformation has been determined for both the parent and DRX grains.In all but the highest Y alloy,the texture of the DRX grains was found to follow that of the parent grains closely in all alloys,implying that the DRX texture is dominated by the deformation conditions,rather than preferred nucleation or growth.In the highest Y alloy,the DRX texture is randomized,which also suggests that preferred nucleation or growth is not responsible for texture formation in this alloy.A transition in macrotexture development was observed in going from pure Mg deformed at250◦C,to Mg–2.71wt%Y deformed at450◦C.This can be attributed to activation of additional slip modes,and a concomitant decrease in the contribution of twinning to deformation.© 2007 Elsevier B.V. All rights reserved.Keywords:Dynamic recrystallization;Magnesium;Texture;EBSD1.IntroductionImproving the poor low temperature formability of magne-sium alloys has been the focus of renewed research efforts in recent years,driven by a need for light weighting in the trans-portation sector.Low temperature formability of magnesium is limited by the plastic anisotropy of individual grains of mag-nesium[1–3],such that deformation of a polycrystal results in generation of incompatibility stresses between grains that cause premature failure[3,4].However,it has also been shown that by using non-conventional processing methods,such as equal channel angular extrusion,and producing a combination of a favourable texture andfine grain size,greatly improved tensile ductilities can be obtained[5,6].Current research is focussed on obtaining the desired microstructure and texture utilizing conventional methods com-bined with alloy and process optimization.To do this,it is essential to have a fundamental understanding of the processes that influence thefinal texture and grain structure in deformed magnesium alloys.Dynamic recrystallization(DRX)is one such ∗Corresponding author.Tel.:+441613063588;fax:+441613063586.E-mail address:ryan.cottam@(R.Cottam).process that is commonly observed during elevated temperature deformation of magnesium and its alloys.DRX in magnesium has been the focus of several studies[7–11]aimed at under-standing the fundamental DRX mechanisms.Little work has yet been done to investigate the effect of DRX on the overall texture evolution or the effect of changes in solute content on DRX.The focus of this paper is on the global(average)texture that results from DRX,and the effect of yttrium additions on this texture development.Yttrium has been used in this study since it is known to alter the relative activity of the deformation modes (slip and twinning)in magnesium alloys[12].One goal of this work was to investigate whether this effect has an influence on the texture of DRX grains that is distinct from that of the original (parent)grains and might thus be exploited for texture control.Studies of texture development during deformation in mag-nesium alloys under conditions of DRX are limited.Ion et al.[10]and Xiong and Davies[11]have addressed texture evo-lution of Mg–Al and AZ31alloys,respectively,in both cases finding that the DRX grains adopted the basal texture of the par-ent grains.Xiong and Davies also evaluated the effect of strain path changes,but again found the basal texture dominant in the DRX grains.Current understanding of texture evolution during DRX has been developed largely for cubic metals[13,14]undergoing0921-5093/$–see front matter© 2007 Elsevier B.V. All rights reserved. doi:10.1016/j.msea.2007.08.016376R.Cottam et al./Materials Science and Engineering A 485 (2008) 375–382“conventional”DRX.In such cases,strain induced bound-ary migration(SIBM)acts as a precursor to formation of DRX grains.However,in magnesium and its alloys,it is accepted that a number of other DRX mechanisms operate, such as continuous rotational DRX[10],which are quite dif-ferent from the conventional mechanism observed in cubic crystals.By changing deformation conditions,it is possible to change the dominant DRX mechanism(e.g.from rotation recrystallization at lower temperatures to SIBM at higher tem-perature[7]).The textures that result from the combinations of DRX mechanisms that operate in magnesium are not yet well characterized.By varying deformation temperature and solute yttrium,this study aims to determine the texture evolution during DRX of magnesium alloys across a range of conditions where the DRX mechanism and relative deformation system activity are expected to change.2.ExperimentalThree binary Mg–Y alloys and commercially pure Mg were prepared by Magnesium Elektron at the Manchester site with compositions showing in Table1.Impurity elements Zn,Si, Cu,Mn and Fe were all below0.01wt%.The alloys were pro-duced as billets7.5cm diameter,solution treated at525◦C for 8h and extruded into3cm diameter bar at390◦C.The initial textures of the extruded billets were measured by EBSD using a Philips XL30FEG SEM with a working distance of20mm and an accelerating voltage of20kV.Samples were prepared for EBSD by grinding and mechanically polishing to colloidal silica and then electro-polishing in a solution of30%nitric acid and ethanol solution,chilled to−30◦C,using a12V potential. The extruded grain size was determined using the linear intercept method.Channel die samples10mm×11mm×12mm were cut from the bar with the compression direction parallel to the extru-sion direction.The samples were coated in powdered graphite which acted as a lubricant during the deformation.An ini-tial strain rate of1×10−3s−1was employed to deform the samples.To obtain statistically useful texture data,it was necessary to choose deformation conditions that led to a significant frac-tion of DRX.Adding yttrium suppresses DRX,requiring higher deformation temperatures to achieve comparable DRX frac-tions.Therefore,it was not possible to vary the yttrium content and deformation temperature independently across the full com-position range studied,since when yttrium was added at high Table1Test temperatures used during channel die compression of pure magnesium and the three Mg–Y alloysAlloy Temperature(◦C)Mg200250300 Mg–0.23wt%Y250300 Mg–0.84wt%Y400 Mg–2.71wt%Y450levels,an increased in deformation temperature was needed to obtain DRX.The test temperatures used are shown in Table1.For each condition,samples were compressed to logarithmic strains of0.1,0.3,0.6and0.9.Channel5EBSD post-processing software was used to create subsets of texture data,based on grain size.A threshold size was determined by examining the grain size histogram after deformation and determining the grain size that divided the DRX grains from the parent grains.The transition size was chosen byfirst selecting a size just above the peak in the grain size histogram due to the DRX grains.This size was verified by identifying automatically all grains below this size and checking whether all of the DRX grains,but none of the parent grains,had been captured.It was apparent from the Euler maps that DRX grains do not undergo further DRX.3.Results3.1.Extruded billet characterizationAfter extrusion,Mg had a mean grain size of57m, Mg–0.23wt%Y51m,Mg–0.84wt%Y24m and Mg–2.71wt%Y21m.In pure magnesium and all three alloys the grain structure was fully dynamically recrystallized during extrusion.All the materials show a typical extruded magnesium texture [15]where the basal poles are radially distributed perpendicular to the extrusion axis(Fig.1).Increasing the yttrium concentra-tion from0.23to2.71wt%Y not only refines the grain structure of the material during dynamic recrystallization(DRX)that occurred during extrusion but also weakened the extruded tex-ture.3.2.Mechanical testingThe true stress–logarithmic strain response during channel die deformation is shown in Fig.2.All curves initially show hardening followed by a region of steady state deformation and then some secondary hardening up to the highest true strain used in the test(0.9).As expected,the addition of yttrium strengthens the material,even at the higher test temperatures used.It is notable that in both the pure magnesium and alloy specimens there is little evidence of the strain softeningthat Fig.1.Inverse polefigures for extruded magnesium alloys where the scale is times random:(a)Mg,(b)Mg–0.23wt%Y,(c)Mg–0.84wt%Y and(d) Mg–2.71wt%Y.R.Cottam et al./Materials Science and Engineering A 485 (2008) 375–382377Fig.2.True stress–logarithmic strain response for the three Mg–Y alloys and pure magnesium.often accompanies dynamic recrystallization[16](Fig.2). However,this softening is also in competition with harden-ing associated with dislocation accumulation,twin formation (Hall–Petch effect)and texture changes.For the initial tex-ture and deformation conditions employed here,this offsets the softening due to DRX,and gives theflat response observed in the stress–strain curve.Once DRX has refined the grain structure and twinning has reoriented the mate-rial(into a“hard”orientation;c-axis compression),work and texture hardening begin again to dominate the stress–strain response and the strain hardening exponent increases(secondary hardening).3.3.Optical micrographs after deformationOptical microscopy was performed to investigate the occur-rence of deformation twins in the microstructure after the initial deformation(Fig.3).Since the compression axis was along the extrusion direction,the majority of grains have their c-axes near perpendicular to the compression direction at the start of testing,a favourable orientation for formation of the{10¯12} c-axis tension twin.The presence of deformation twins can be found in the pure Mg at all deformation temperatures and in the Mg–0.23wt%Y alloy(Fig.3).In the Mg–0.84wt%Y alloy the microstructure shows small deformation twins,but these only occur in less than half of the grains.This alloy and deformation temperature therefore appears to produce a mixed (transition)mode of deformation,involving some twinning but also enhanced slip(most likely due to activation non-basal c+a slip).The Mg–2.71wt%Y alloy shows no evidence of twinning.3.4.Euler maps of initial DRXLocal microtexture EBSD maps,showing regions containing a mixture of parent and DRX grains are shown in Fig.4.The superimposed unit cells illustrate the orientation of each grain. From these examples,it is clear that the orientation of the DRX grains are generally similar of that of the original grains.Itcan Fig.3.Optical micrographs after channel die compression:(a)pure magnesium compressed to a logarithmic strain of0.1at250◦C;(b)Mg–0.23wt%Y compressed to a logarithmic strain of0.1at250◦C;(c)Mg–0.84wt%Y compressed to a logarithmic strain of0.1at400◦C;(d)Mg–2.71wt%Y compressed to a logarithmic strain of0.3at450◦C.378R.Cottam et al./Materials Science and Engineering A485 (2008) 375–382Fig.4.Euler maps after PSC to a true strain of 0.3:(a)pure magnesium deformed at 250◦C;(b)Mg–0.23wt%Y deformed at 250◦C;(c)Mg–0.84wt%Y deformed at 400◦C;(d)Mg2.71wt%Y deformed at 450◦C.Grains labelled ‘P’are the parent grains.also be seen that the orientation of neighbouring DRX grains can be quite different,showing different angles and axes of rotation from the parent grain.This will be discussed in detail in a future paper.Pole figures {0002}for the pure magnesium deformed at different temperatures are shown in Fig.5.Rather than plot-ting intensity contours,the position of individual measurement points is shown.This is done to identify whether any new orien-tations are created during DRX,to characterize the orientation spread of poles and to identify regions for which orientations are absent.As discussed already,pole figures for DRX and parent grains are plotted separately,with the two-grain classes distinguished on the basis of their size.Fig.6shows the evolution of the {0002}pole figures for the yttrium containing alloys with increasing strain.Again,data for the DRX and parent grains are plotted separately.Fig.7shows {0002}pole figures for the final texture (after compression to a logrithmic strain of 0.9).In this case,intensity contours are shown to give an indication of the sharpness of the final texture.4.Discussion of results4.1.The development of texture with strain and temperature for pure MgIn the pure magnesium,distinct differences can be observed in the texture evolution at the three test temperatures.Thesedifferences can be largely attributed to changes in the relative contribution of twinning and slip to deformation.Formation ofthe common {10¯12}c -axis tension twin will lead to rapid reori-entation of the {0002}pole towards the ND,whereas basal slip will lead to a progressive rotation of the {0002}poles from the TD–RD plane to the ND.The high concentration of {0002}poles oriented close to the ND after deformation to a strain of 0.3at 200◦C is indica-tive of the high level of twinning that has already occurred under these conditions.As the deformation temperature is increased (at a strain of 0.3),an increasingly pronounced ring type tex-ture forms,with an absence of poles aligned in the ND.The ring texture most probably arises from partial rotation of the basal poles towards the ND by basal slip,with the markedly reduced intensity of poles around the ND reflecting the sharp reduction in twin formation with increasing deformation temper-ature [17].For the highest deformation temperature and strain (300◦C,0.6),rotation of the basal poles towards the ND by slip is,as expected,most advanced,and a (reoriented)basal texture is obtained.Of most interest in this work is the comparison of the ori-entations of the parent and DRX grains.It is clear from Fig.5that in pure magnesium,the orientation distribution of the DRX grains is similar to that of the parent grains.On a local level it has been shown by Galiyev et al.[8]that under the condi-tions used in this study,DRX in pure magnesium occurs largely by a continuous rotation mechanism.What the present result shows is that although any given DRX grain is rotating awayR.Cottam et al./Materials Science and Engineering A 485 (2008) 375–382379Fig.5.{0002}polefigures generated form EBSD Euler maps for pure magnesium where the horizontal axis is the rolling direction and the vertical is the transverse direction.from its parent grain,the development of its orientation is dom-inated by the macroscopic plastic strain imposed,and thus no special new orientations are created by DRX.In other words, although each DRX grain may rotate away from its neighbour during deformation,taken globally these rotations follow those of the parent grains,This confirms on a microtexture scale the conclusions of Kawalla et al.[18]and Al-Samman and Gottstein [19]who performed bulk texture analysis of uniaxial compres-sion at increasing strain intervals and found similar behaviour. This conclusion is supported by recent texture modelling work applied to equal channel angular extrusion at elevated tempera-ture[20].This shows that even when DRX is ignored,prediction offinal textures is good.The results presented here suggest that the average response of the DRX grains to deformation follows that of the parent grains.4.2.The effect of yttrium on texture developmentAs with an increase in temperature for pure magnesium,the combined increase in yttrium and deformation temperature used in this study leads to a transition in deformation behaviour and texture development.Unfortunately,despite taking care to sam-ple a large number of grains(over6000),in some cases(as shown in Fig.6d,f and h in particular)it is clear that orientations that should be present from a consideration of symmetry have not been detected.Despite this limitation,the data are adequate to draw qualitative conclusions about the influence of yttrium on the texture evolution of the parent and DRX grains.Fig.7shows that thefinal texture after deformation to a strain of0.9is similar for the pure magnesium and Mg–0.23wt%Y deformed at250and300◦C.The most notable difference in tex-tures is after deformation at250◦C,where the Mg–0.23wt%Y shows a basal,rather than split basal texture,as observed in the pure Mg and the Mg–0.23wt%Y deformed at300◦C.The rea-son for this difference is not yet clear,but may be due to the observed change in the fraction and scale of twins with yttrium (Fig.3).The0.23and0.84wt%Y alloys show similar behaviour with respect to the relationship between DRX and parent grain ori-entations.As in the case of pure Mg,in these alloys,the DRX380R.Cottam et al./Materials Science and Engineering A485 (2008) 375–382Fig.6.{0002}pole figures generated form EBSD Euler maps for the three Mg–Y alloys compressed in plane strain compression at elevated temperature.The horizontal axis is the rolling direction and the vertical is the transverse direction.and parent grains show similar orientation distributions,with evidence that the spread of orientations in the DRX grains is slightly greater than in the parent grains.This is in contrast to pure Mg,where a similar spread in orientation is observed.DRX in these alloys randomizes the texture.The final texture observed in the 0.84wt%Y alloy (Fig.7)is relatively weak,and represents a transition in behaviour from the macroscopic textures observed in the both the pure Mg and Mg–0.23wt%Y to that observed in the Mg–2.71wt%Y alloy.Increasing the addition of Y to 2.71wt%Y and the defor-mation temperature to 400◦C results in a change in the texture formation of both the parent and DRX grains.This change in behaviour can most likely be attributed to a reduction in the relative critical resolved shear stress (CRSS)for c +a slip com-pared to basal slip and twinning deformation modes.The initial texture of the extruded material was relatively weak in this alloy,and this makes interpretation of the results for low strain defor-mation difficult.However,once a logarithmic strain of 0.6is reached,it can be seen that a strikingly different texture has developed,and this is reflected in the final texture intensity.In addition,the DRX grains show a different,and far more random distribution of orientations than the parent grains.The randomization of texture has been observed after the static recrystallization of Mg–Y containing alloy [21].In this work,it was argued that shear banding formed random nuclei,which during recrystallization led to the random texture.How-ever,this does not explain the results seen here,where DRX grains were found to form at grain boundaries,not shear bands,and are also subject to extensive deformation after forming.The most likely explanation comes form the effect of adding yttrium on the mechanism of DRX,which will be discussed in a future paper.It should also be noted that while the initial DRX texture is random,the macroscopic texture after deformation to 0.9log-arithmic strain is quite strong.This suggests that when the DRXR.Cottam et al./Materials Science and Engineering A 485 (2008) 375–382381Fig.7.Polefigures after channel die deformation to a logarithmic strain of0.9for the alloys and pure Mg at a range of temperatures.grains initially form in this alloy they do not have a strong pre-ferred orientation,but subsequent deformation causes them to rotate towards the TD,hence producing the strongfinal texture.A relatively random texture has also been observed after deformation of AZ61at elevated temperatures[22],under condi-tions where extensive DRX occurred.The origins of this texture were not given but,as in this work,it was noted that the random-ization process occurred only with higher solute levels,which again points to the influence of solute in randomizing the DRX texture.5.ConclusionsIn this study,the evolution of texture of DRX and parent grains was studied for pure magnesium at a range of temper-atures,and binary magnesium–yttrium alloys at temperatures where extensive DRX occurs.As yttrium suppresses dynamic recrystallization,it was necessary to deform the high yttrium containing alloys at higher temperatures to obtain comparable DRX fractions.Increasing deformation temperature and yttrium content had the effect of reducing the importance of twinning as a deforma-tion mode and increasing the activity of non-basal slip modes. This was reflected in the texture evolution.In pure magnesium and Mg–0.23wt%Y,basal or split basal textures were observed. In Mg–2.71wt%Y,a completely different texture was seen,with basal poles aligned in the TD and RD.In the Mg–0.84wt%Y alloy a transition texture between these extremes was observed.It has been shown that in pure magnesium,the texture of the DRX grains followed closely that of the parent grains,i.e. it is the deformation conditions that determine the texture of the DRX grains,rather than special conditions of nucleation or growth.The addition of yttrium at low levels(0.23wt%)appears to slightly randomize the texture of the DRX grains compared to that in pure magnesium deformed at the same temperature. This effect is also observed in Mg–0.84wt%Y alloy deformed at higher temperature.Addition of higher levels of yttrium (2.71wt%)combined with a higher deformation temperature lead to a change in behaviour,with a near random distribution of DRX grains being in contrast to strongly textured parent grains. AcknowledgementsThis work has been carried out as part as part of the‘Light Alloys Portfolio Partnership’EPSRC grant EP/C002210/1.The authors would like to thank Magnesium Elektron for theirfinan-cial and technical support,Mr.Michael Faulkner for his technical support.References[1]B.C.Wonsiewicz,W.A.Backofen,TMS-AIME(1967)1422–1431.[2]S.R.Agnew,O.Duygulu,Int.J.Plasticity21(2005)1161–1193.[3]S.R.Agnew,C.N.Tome,D.W.Brown,T.M.Holden,S.C.V ogel,ScriptaMater.48(2003)1003–1008.[4]D.W.Brown,S.R.Agnew,M.A.M.Bourke,T.M.Holden,S.C.V ogel,C.N.Tome,Mater.Sci.Eng.A399(2005)1–12.[5]J.Koike,T.Kobayashi,T.Mukai,H.Watanabe,M.Suzuki,K.Maruyama,K.Higashi,Acta Mater.51(2003)2055–2065.[6]S.R.Agnew,J.A.Horton,T.M.Lillo,D.W.Brown,Scripta Mater.50(2004)377–381.[7]A.Galiyev,R.Kaibyshev,G.Gottstein,Acta Mater.49(2001)1199–1207.382R.Cottam et al./Materials Science and Engineering A 485 (2008) 375–382[8]A.Galiyev,R.Kaibyshev,T.Sakai,Mater.Sci.Forum419–422(2003)509–514.[9]X.Yang,H.Miura,T.Sakai,Mater.Sci.Forum467–470(2004)531–536.[10]S.E.Ion,F.J.Humphreys,S.H.White,Acta Metall.30(1982)1909–1919.[11]F.Xiong,C.H.J.Davies,Magnesium Technology2005,TMS,San Fran-cisco,2005.[12]S.R.Agnew,M.H.Yoo,C.N.Tome,Acta Mater.49(2001)4277–4289.[13]A.M.Wusatowska-Sarnek,H.Miura,T.Sakai,Mater.Sci.Eng.A323(2002)177–186.[14]O.V.Mishin,V.Y.Gertsman,G.Gottstein,Mater.Character.38(1997)39–48.[15]M.R.Barnett,Z.Keshavarz,A.G.Beer,D.Atwell,Acta Mater.52(2004)5093–5103.[16]M.R.Barnett,D.Atwell,A.G.Beer,Mater.Sci.Forum467–470(2004)435–440.[17]A.Jain,S.R.Agnew,Mater.Sci.Eng.A462(2007)29–36.[18]R.Kawalla, C.Schmidt,H.Reidel, A.Prakash,DGM,Dresden,2006.[19]T.Al-Samman,G.Gottstein,DGM,Wiley-VCH,Dresden,2006.[20]S.R.Agnew,P.Mehrotra,T.M.Lillo,G.M.Stoica,P.K.Liaw,Acta Mater.53(2005)3135–3146.[21]J.W.Senn,S.R.Agnew,Magnesium Technology in the Global Age,Mon-treal,2006.[22]L.Helis,K.Okayasu,H.Fukutomi,DGM,Wiley-VCH,Dresden,2006.。