毕设论文 承轴内圆磨床自动上下料系统设计正文
M2110A内圆磨床毕业设计论文
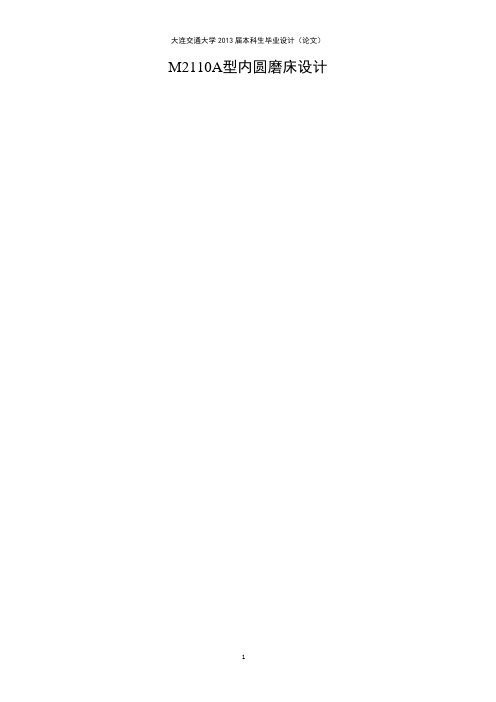
M2110A型内圆磨床设计摘要磨床是应用于零件精加工,尤其是淬硬钢件和高硬度特殊材料精加工的一种机床。
近年来由于科学技术的发展,现代机械零件的精度和表面粗糙度要求越来越高,各种硬度材料日益增多,所以磨床的应用越来越广泛。
基于市场对内圆磨床的变速要求高,磨削内圆直径大的要求,经过重新布局和对主轴箱的设计后,M2110A 型内圆磨床的加工性能得到了很大的提高,外形更加美观,结构更紧凑,操纵也更方便,更省力。
设计的该型磨床主要用于磨削精密圆柱孔和圆锥孔,适用于单件小批量生产。
同时该磨床工作台由液压无级传动,工作台的工作进给、快速进给及退回、修整砂轮时的进给等均能自动变换。
砂轮微量横进给可以手动或液动,液动进给即工作台每一个往复行程,砂轮作一次自动进给。
修整砂轮用液压手柄操纵。
关键词:内圆磨床进给机构砂轮修整器ABSTRACTGrinding machine is used in parts finishing,in particular hardened steel and special materials of high hardness of a machine tool for finishing.In recent years,due to the development of science and technology, modern machinery parts of the surface roughness and precision demand is higher and higher, the hardness of material is increasing,so the Grinding machine is more and more widely applied.Based on high speed requirements of market for internal grinder and grinding inside diameter big request,after a new layout and design of spindle box,type M2110A internal grinder in the processing performance has been greatly improved, the appearance is more beautiful, more compact in structure,operation more convenient, also is more efficient.Design of this type of grinding machine is mainly used for grinding precision cylindrical bore and conical bore, suitable for single piece and small batch production.Meanwhile, the grinding table by the hydraulic stepless transmission,bench work feeding, rapid feed and return,dressing grinding wheel feed, etc all can automatically transform.. Trace wheel infeed can be manual or hydraulic,hydraulic table feed that each reciprocating stroke,wheel as an automatic feed.Dressing grinding wheel with a hydraulic lever to manipulate.Key word: internal grinder feed mechanism grinding wheel grinding wheel dresser第一章绪论1.1磨床的类型与用途机械制造业的生产能力和制造水平,主要取决于机械制造装备的先进程度。
轴承内圆磨床自动上下料系统设计_毕业设计 精品

轴承内圆磨床自动上下料系统设计目次1 轴承内圆磨床自动上下料系统概述 (1)1.1 课题的来源与意义 (1)1.2 课题研究现状和发展趋势 (2)1.3 课题的设计任务与技术要求 (5)2 轴承内圆磨床总体设计与布局 (7)2.1 轴承内圆的磨削原理与特点 (7)2.2 轴承内圆磨床的加工对象,范围及要求 (8)2.3 机床的主要运动参数分析 (9)2.4 影响机床加工精度和效率的工艺因素 (10)2.5 机床主要部件结构方案评价 (11)2.6 机床的工作循环过程 (12)2.7 机床的造型设计 (13)2.8 机床的总体布局 (15)3 轴承内圆磨床自动上下料系统设计 (16)3.1 上下料方案设计 (16)3.2 上料机构“双料”故障的成因和预防 (17)3.3 输料槽的设计 (23)3.4 气缸的选择 (23)设计总结 (27)致谢 (29)参考文献 (30)1 轴承内圆磨床自动上下料系统概述1.1 课题的来源与意义1.1.1 课题的来源现今轴承生产中,套圈磨削工艺及专用磨床不能满足高精度,高效率的要求,与国外相比存在着一定的差距。
工艺设备的落后是国产轴承精度低,性能差,成本高以及在国际市场上竞争力低的主要原因。
在所有轴承加工设备中,内表面磨床的水平具有表征意义。
这主要是磨削孔径限制了砂轮尺寸及相应的系统结构和几何参数,从根本上限制了工艺系统的的刚性。
内圆磨削速度要从砂轮主轴的转速的提高寻找出路,相应的就带来了高速主轴轴承的制造,应用装配技术和高速下的振动及动平衡一系列要求。
轴承套圈内径公差严格,在大批量与高效率的生产条件下,难以用定程控制尺寸,必须配用各式主动测量系统,从而增加了内圈磨床结构及尺寸的复杂性。
该课题来源于生产实践。
在深沟球轴承内圈的加工中,内圆磨削是一道关键工序。
其原因是:受孔径限制,砂轮尺寸小,砂轮消耗快,影响磨削效率和质量。
现代磨削技术在不断的发展和提高,对于轴承内圈内圆的磨削,越来越要求磨床具有高精度、高效率和高可靠性,而传统的手动和半自动内圆磨床难以满足使用要求,因此设计开发全自动内圆磨床则显得尤为重要。
磨床机器人自动上下料方案
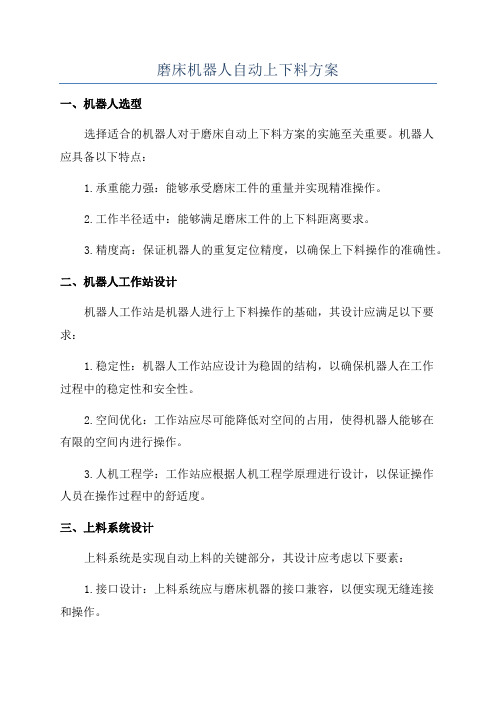
磨床机器人自动上下料方案一、机器人选型选择适合的机器人对于磨床自动上下料方案的实施至关重要。
机器人应具备以下特点:1.承重能力强:能够承受磨床工件的重量并实现精准操作。
2.工作半径适中:能够满足磨床工件的上下料距离要求。
3.精度高:保证机器人的重复定位精度,以确保上下料操作的准确性。
二、机器人工作站设计机器人工作站是机器人进行上下料操作的基础,其设计应满足以下要求:1.稳定性:机器人工作站应设计为稳固的结构,以确保机器人在工作过程中的稳定性和安全性。
2.空间优化:工作站应尽可能降低对空间的占用,使得机器人能够在有限的空间内进行操作。
3.人机工程学:工作站应根据人机工程学原理进行设计,以保证操作人员在操作过程中的舒适度。
三、上料系统设计上料系统是实现自动上料的关键部分,其设计应考虑以下要素:1.接口设计:上料系统应与磨床机器的接口兼容,以便实现无缝连接和操作。
2.操作灵活:上料系统应具备多种上料方式,以适应不同形式和尺寸的工件。
3.安全性:上料系统应配备相应的安全装置,以防止操作过程中的意外事故。
四、下料系统设计下料系统是实现自动下料的关键部分,其设计应符合以下原则:1.工件收集:下料系统应具备良好的工件收集功能,以便将磨完的工件快速收集起来。
2.传送带设计:下料系统应配备高速传送带,以加快工件的下料速度。
3.产品分类:下料系统应根据产品的特性进行分类,以方便后续的工序处理。
五、安全保护系统六、系统集成与优化将机器人、上料系统、下料系统和安全保护系统进行有效的集成与优化,保证整个自动上下料方案的稳定性和可靠性。
总结:磨床机器人自动上下料方案是实现磨床机器自动化的一项重要技术,在提高生产效率的同时也减少了人工操作的误差。
通过机器人选型、工作站设计、上料系统和下料系统的设计,以及安全保护系统的应用,可以实现磨床机器的自动上下料操作,从而提高生产效率和质量。
机械毕业设计830机车轴承座自动上下料机构

机车轴承座自动上下料机构及其控制系统设计第一章自动上下料机构的总体构想该装置是机车轴承座自动生产线上的辅助装置之一,主要完成抓取工件,提升一定高度,旋转,移位,松开工件等几个基本功能。
其主要技术指标如下:1. 工件重量约为70Kg;2. 工件最大尺寸(长,宽,高):440×92×290(具体见零件图);3. 最大操作范围:提升高度为70mm,转动角度为90°,水平移动为400mm;4. 机械手的自由度数为3(上升,转动,平移);5.定位精度:属于上下料机构,本身精度要求不高;6.装料高度:1050mm;7.性能要求:抓取可靠、灵活,松放平稳,定位可靠。
在满足上述各项功能的前提下,我们尽量采用结构简单,制造方便的零部件来组成该机车轴承座的自动上下料专用机构即机械手。
根据机械手所要实现的基本功能,我们采用圆柱坐标式机械手。
其手臂的运动系由两个直线运动和一个回转运动所组成,即沿X轴的平移、沿Z轴的升降和绕Z轴的回转,而手部的夹放动作不能改变工件的位置和方位,故它不计为自由度数,因此该机械手具有三个自由度数即可满足使用要求。
根据实际需要我们选用液压传动机械手:以油液的压力来驱动执行机构运动。
其主要特点是:抓重可达几百公斤以上、传动平稳、结构紧凑、动作灵敏。
安排夹紧液压缸,升降液压缸,回转液压缸和移动液压缸来分别实现夹紧松开、升降、转动和平移各项功能。
为了实现对机械手的各个动作的顺序控制,我们采用PLC控制各动作的执行元件。
该机械手的具体结构为:使用两个立柱作为支撑架,在支架上钻两个孔,把装有滑板及连接板和平移液压缸的导轨装于支架的孔里,采用螺钉进行紧固。
滑板上装有由升降缸和回转缸组成的臂部及手指式手部和驱动手部夹紧、松开的夹紧液压缸。
滑板带动工件一起移动实现平移,移动液压缸与滑板的运动可以由齿轮与齿条的传动来实现。
第二章 机械手的具体设计2.1 手部的设计2.1.1 类型选择根据工件形状、尺寸、重量、材料和表面等状况,选用回转型两指式手部。
机床自动化上下料解决方案之进阶版【至工机电2013】
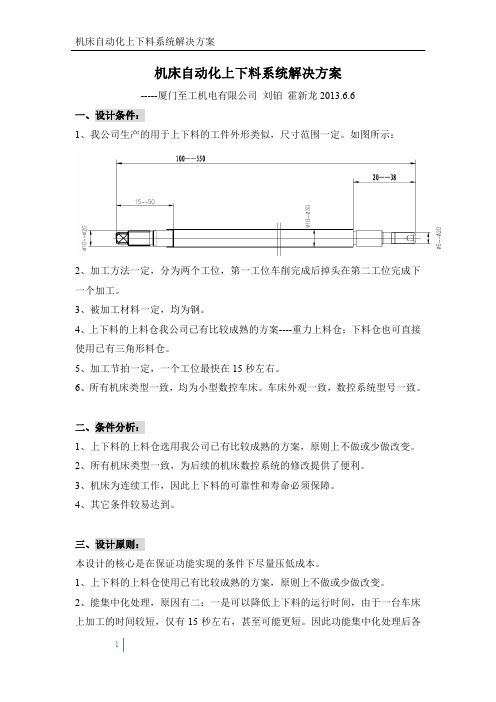
机床自动化上下料系统解决方案-----厦门至工机电有限公司刘铂霍新龙2013.6.6一、设计条件:1、我公司生产的用于上下料的工件外形类似,尺寸范围一定。
如图所示:2、加工方法一定,分为两个工位,第一工位车削完成后掉头在第二工位完成下一个加工。
3、被加工材料一定,均为钢。
4、上下料的上料仓我公司已有比较成熟的方案----重力上料仓;下料仓也可直接使用已有三角形料仓。
5、加工节拍一定,一个工位最快在15秒左右。
6、所有机床类型一致,均为小型数控车床。
车床外观一致,数控系统型号一致。
二、条件分析:1、上下料的上料仓选用我公司已有比较成熟的方案,原则上不做或少做改变。
2、所有机床类型一致,为后续的机床数控系统的修改提供了便利。
3、机床为连续工作,因此上下料的可靠性和寿命必须保障。
4、其它条件较易达到。
三、设计原则:本设计的核心是在保证功能实现的条件下尽量压低成本。
1、上下料的上料仓使用已有比较成熟的方案,原则上不做或少做改变。
2、能集中化处理,原因有二:一是可以降低上下料的运行时间,由于一台车床上加工的时间较短,仅有15秒左右,甚至可能更短。
因此功能集中化处理后各功能实现的时间重叠;二是功能集中,可以减少空间占用,起到降低成本的目的。
四、方案解释:1、整体布局:如下图所示,这样的整体布局可以达到桁架行程最短。
取放料集中等优点(图中所示料仓为概念示意图,不代表实物。
)。
2、料仓:我公司在长期的生产中使用的重力上料仓和成品料仓基本符合工厂的实际情况。
因此原则上依然使用这种料仓,尽在必要时对此料仓进行适应新型自动上下料系统的改动。
3、桁架:如图所示:导轨机械部分分为三部分,即支柱、水平导轨和垂直导轨。
水平导轨长4000,垂直导轨视机床工作台高度决定,约1500。
支柱高2000。
具体尺寸以产品为准。
移动速度为120m/s。
根据我们多年的经验,水平导轨和垂直导轨基材选用钢材。
不用国产铝型材的原因是铝型材在挤压成型过程中不可避免的有内应力产生,放置一段时间后会出现扭曲变形。
内圆磨床进给系统的设计
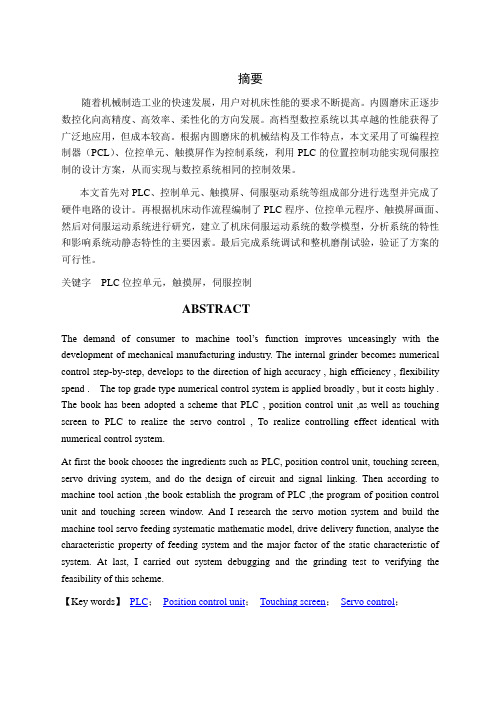
摘要随着机械制造工业的快速发展,用户对机床性能的要求不断提高。
内圆磨床正逐步数控化向高精度、高效率、柔性化的方向发展。
高档型数控系统以其卓越的性能获得了广泛地应用,但成本较高。
根据内圆磨床的机械结构及工作特点,本文采用了可编程控制器(PCL)、位控单元、触摸屏作为控制系统,利用PLC的位置控制功能实现伺服控制的设计方案,从而实现与数控系统相同的控制效果。
本文首先对PLC、控制单元、触摸屏、伺服驱动系统等组成部分进行选型并完成了硬件电路的设计。
再根据机床动作流程编制了PLC程序、位控单元程序、触摸屏画面、然后对伺服运动系统进行研究,建立了机床伺服运动系统的数学模型,分析系统的特性和影响系统动静态特性的主要因素。
最后完成系统调试和整机磨削试验,验证了方案的可行性。
关键字PLC位控单元,触摸屏,伺服控制ABSTRACTThe demand of consumer to machine tool’s function improves unceasingly with the development of mechanical manufacturing industry. The internal grinder becomes numerical control step-by-step, develops to the direction of high accuracy , high efficiency , flexibility spend . The top grade type numerical control system is applied broadly , but it costs highly . The book has been adopted a scheme that PLC , position control unit ,as well as touching screen to PLC to realize the servo control , To realize controlling effect identical with numerical control system.At first the book chooses the ingredients such as PLC, position control unit, touching screen, servo driving system, and do the design of circuit and signal linking. Then according to machine tool action ,the book establish the program of PLC ,the program of position control unit and touching screen window. And I research the servo motion system and build the machine tool servo feeding systematic mathematic model, drive delivery function, analyse the characteristic property of feeding system and the major factor of the static characteristic of system. At last, I carried out system debugging and the grinding test to verifying the feasibility of this scheme.【Key words】PLC;Position control unit;Touching screen;Servo control;1绪论国内外轴承内圆磨床设计概况滚动轴承是一种量大面广、高精度的机械基础件,广泛应用于机械、电子、航空航天、运输、纺织、医疗、冶金、IT等国民经济各部门各行业。
(完整版)半自动轴承圈内圆磨床毕业设计

以下文档格式全部为word格式,下载后您可以任意修改编辑。
毕业设计(论文)题目: 半自动轴承圈内圆磨床专论文摘要随着高速磨削和强力磨削工艺的发展,进一步提高了磨削的效率。
因此,磨床的使用范围日益扩大,在金属切削机床中占的比重不断上升,在工业发达国家占金属切削机床的13%~27%。
目前,我们对轴承加工设备,尤其是高精度、高效率、高可靠性的轴承磨床需求量十分庞大。
轴承,作为机械工业的基础件,其加工设备的重要性非常突出。
本文介绍了如何用可编程序控制器与磨床结合起来,对3MB2024型半自动轴承套圈内圆磨床的电气系统进行设计,它包括了硬件及软件的设计。
对目前在工业生产中大量使用此类设备都具有很好的参考价值。
关键词:磨削机床轴承可编程序控制器内圆磨床AbstractAlong with our country machine equipments, car industry etc. profession of fast development, also along with our country automation technique of exaltation, automation factory also top a new of step, the PLC be one newly arisen of industry controller, with its physical volume small, the function be well-found, the price be cheap, credibility Gao Deng3, .In the meantime, we process an equipments to the bearings, particularly is a Gao accuracy, piece of machine industry, it process the importance of equipments very outstanding.This text introduction design, it included .Rightness a great deal of currently in the industry the production usage this kind the equipments all 。
自动外圆磨床自动上料系统设计(机械CAD图纸)
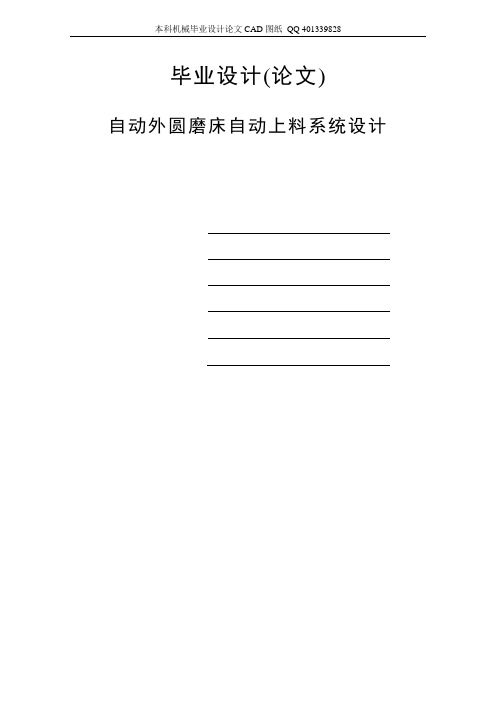
(4)按控制方式分:
(a)固定程序自动送料机构:控制系统是一个固定程序的控制器。程序简单,程序数少,而且是固定的,行程可调但不能任意点定位。
(b)可编程序自动送料机构:控制系统是一个可变程序控制器。其程序可按需要编排,行程能很方便改变[9]。
控制系统是支配自动送料机构按规定程序和要求进行运动的装置,他们主要用来控制:位置(点位控制或连续轨迹控制)、
时间、速度和加速度等参数。
自动送料机构与主机及其它有关装置之间的联系[3]。
2.3
按自动送料机构布局形式分可分为:架空式自动送料机构、附机式自动送料机构、落地式自动送料机构三种。此外,还有安装在自动线料道上或料道旁,实现工件上、下料、传递转位、转向等用途的自动送料机构,他们具有运动单一、结构简单,位置灵活及精度一般要求较低的特点。
在工业机器人的诸多功能中,抓取和移动是最主要的功能。这两项功能实现的技术基础是精巧的机械结构设计和良好的伺服控制驱动。本次设计就是在这一思维下展开的。根据设计内容和需求确定圆柱坐标型工业机器人,利用锥齿轮传动实现机器人的旋转,利用液压缸实现其移动以及对零件的抓取。在步进电机的控制下,机器达到精确的回转运动。
工业机器人是一种机体独立,动作自由度较多,程序可灵活变更,能任意定位,自动化程度高的自动操作机械。主要用于加工自动线和柔性制造系统中传递和装卸工件或夹具[1]。
工业机器人以刚性高的手臂为主体,与人相比,可以有更快的运动速度,可以搬运更重的东西,而且定位精度相当高,它可以根据外部来的信号,自动进行各种操作。
1.3
(1)培养学生综合分析和解决本专业的一般工程技术问题的独立工作能力,拓宽和。
- 1、下载文档前请自行甄别文档内容的完整性,平台不提供额外的编辑、内容补充、找答案等附加服务。
- 2、"仅部分预览"的文档,不可在线预览部分如存在完整性等问题,可反馈申请退款(可完整预览的文档不适用该条件!)。
- 3、如文档侵犯您的权益,请联系客服反馈,我们会尽快为您处理(人工客服工作时间:9:00-18:30)。
轴承内圆磨床自动上下料系统设计目次1 轴承内圆磨床自动上下料系统概述 (1)1.1 课题的来源与意义 (1)1.2 课题研究现状和发展趋势 (2)1.3 课题的设计任务与技术要求 (5)2 轴承内圆磨床总体设计与布局 (7)2.1 轴承内圆的磨削原理与特点 (7)2.2 轴承内圆磨床的加工对象,范围及要求 (8)2.3 机床的主要运动参数分析 (9)2.4 影响机床加工精度和效率的工艺因素 (10)2.5 机床主要部件结构方案评价 (11)2.6 机床的工作循环过程 (12)2.7 机床的造型设计 (13)2.8 机床的总体布局 (15)3 轴承内圆磨床自动上下料系统设计 (16)3.1 上下料方案设计 (16)3.2 上料机构“双料”故障的成因和预防 (17)3.3 输料槽的设计 (23)3.4 气缸的选择 (23)设计总结 (27)致谢 (29)参考文献 (30)1 轴承内圆磨床自动上下料系统概述1.1 课题的来源与意义1.1.1 课题的来源现今轴承生产中,套圈磨削工艺及专用磨床不能满足高精度,高效率的要求,与国外相比存在着一定的差距。
工艺设备的落后是国产轴承精度低,性能差,成本高以及在国际市场上竞争力低的主要原因。
在所有轴承加工设备中,内表面磨床的水平具有表征意义。
这主要是磨削孔径限制了砂轮尺寸及相应的系统结构和几何参数,从根本上限制了工艺系统的的刚性。
内圆磨削速度要从砂轮主轴的转速的提高寻找出路,相应的就带来了高速主轴轴承的制造,应用装配技术和高速下的振动及动平衡一系列要求。
轴承套圈内径公差严格,在大批量与高效率的生产条件下,难以用定程控制尺寸,必须配用各式主动测量系统,从而增加了内圈磨床结构及尺寸的复杂性。
该课题来源于生产实践。
在深沟球轴承内圈的加工中,内圆磨削是一道关键工序。
其原因是:受孔径限制,砂轮尺寸小,砂轮消耗快,影响磨削效率和质量。
现代磨削技术在不断的发展和提高,对于轴承内圈内圆的磨削,越来越要求磨床具有高精度、高效率和高可靠性,而传统的手动和半自动内圆磨床难以满足使用要求,因此设计开发全自动内圆磨床则显得尤为重要。
1.1.2 课题的背景与意义轴承内圆内圈磨床是指用于磨削轴承内圆的专用磨床。
五十年代,开始逐步发展了切入式轴承专用内圆和外圆磨床;至八十年代,随着机床基础元件技术的发展,特别是电子技术的高速发展,轴承套圈内圆和外圆磨床的技术的日趋完善,相继出现了PC和CNC控制轴承套圈内圆和外圆磨床及CAC控制的轴承套圈内圆磨床,使现代控制技术与先进的机床功能组件相得益彰,大大提高了机床的自动化程度、可靠性、工作精度和生产效率。
迄今为止,较著名的轴承磨床制造厂主要有:美国的勃兰恩特、希尔德;西德的奥佛贝克;意大利的西马特、法米尔、诺瓦;日本的精工精机、东洋工业公司;东德的柏林机床厂、卡尔马克思城磨床厂等。
本课题为生产轴承的企业提出的实际课题。
小型深沟球轴承是使用量较大的轴承产品。
其生产方式为大批量生产。
由于行业的竞争日益激烈,生产厂家特别重视产品的质量和加工效率。
在深沟球轴承内圈的加工工序中,内圈磨削是一种瓶颈工序,也是关键工序。
传统的手动和半自动内磨床难以满足使用要求。
因此,有必要设计开发以提高加工效率和质量为目的的全自动轴承内圈内圆磨床。
通过设计改进的预期成果是将此深沟球轴承内圆磨床制造出来并投入到实际生产轴承圈的生产中,达到提高精度、加工效率和质量的目的。
1.1.3 课题设计要解决的问题轴承加工是以大批量为特征的,因此加工设备不仅要保证轴承所要求的各项精度而且效率也是一个很重要的指标。
所以上下料的辅助时间是可以考虑缩短来提高效率的。
而随着轴承工业的发展,对轴承磨床的加工精度也提出了更高的要求。
尺寸精度是轴承加工中控制的一项关键之一。
所以我们有必要去对上下料及进给进行研究。
在学校翻阅图书馆大量文献,研究出初步的设计方案。
去工厂进行实地考察,结合书本知识,得出最佳设计方案。
根据任务分工,我主要负责设计机床的上下料系统。
设计过程中,通过翻阅大量的通用机床的设计资料,并总结设计机床的主要特点,从而得出了该机床的上下料装配图和机床装配图。
虽然各种机床的功能和要求不同,但就其磨削原理而言,同属于内表面磨削,其运动方式和总体布局也基本相同,大多数部件通用。
目前,国内各厂对中高级精度轴承多采用二次磨削,为了改变这种情况,拟用一次磨削代替且达到终磨技术要求。
要在大批生产高效的条件下,满足上述技术要求,从磨床设计的观点来看,可以归结为磨削几何精度、尺寸精度及效率三个方面的要求。
用因果分析尺寸精度、几何尺寸及磨削效率的影响因素,从而选择最佳装夹部件方案,在考虑运动图的设计布局及造型设计,最后决定最佳的方案。
1.2 课题研究现状和发展趋势1.2.1 课题研究现状随着轴承工业的迅速发展,对轴承磨床的加工精度、效率、可靠性提出了更高的要求。
尺寸精度是轴承加工中控制的一项关键精度之一,而磨床的进给机构直接影响轴承套圈加工的尺寸精度。
因此,随着轴承质量要求的不断提高,需要更加精密高效的磨床进给机构。
磨床能加工硬度较高的材料,如淬硬钢、硬质合金等;也能加工脆性材料,如玻璃、花岗石。
磨床能作高精度和表面粗糙度很小的磨削,也能进行高效率的磨削,如强力磨削等。
小型深沟球轴承是使用量较大的轴承产品。
其生产方式为大批量生产。
由于行业的竞争日益激烈,生产厂家特别重视产品的质量和加工效率。
在深沟球轴承内圈的加工工序中,内圈磨削是一种瓶颈工序,也是关键工序。
传统的手动和半自动内磨床难以满足使用要求。
因此,有必要设计开发以提高加工效率和质量为目的的全自动轴承内圈内圆磨床。
1.2.2 课题国内外研究的概况作为整个工业基础的机械制造业,正在朝着高精度、高效率、智能化和柔性化的方向发展。
磨削、超精研加工(简称“磨超加工”)往往是机械产品的终极加工环节,其机械加工的好坏直接影响到产品的质量和性能。
作为机械工业基础件之一轴承的生产中,套圈的磨超加工是决定套圈零件乃至整个轴承精度的主要环节,其中滚动表面的磨超加工,则又是影响轴承寿命以及轴承减振降噪的主要环节。
因此,历来磨超加工都是轴承制造技术领域的关键技术和核心技术。
国外轴承工业,60年代已形成一个稳定的套圈磨超加工工艺流程及基本方法,即:双端面磨削——无心外圆磨削——滚道切入无心磨削——滚道超精研加工。
除了结构特殊的轴承,需要附加若干工序外,大量生产的套圈均是按这一流程加工的。
几十年来,工艺流程未出现根本性的变化,但是这并不意味着轴承制造技术没有发展。
简要地说,60年代只是建立和发展“双端面——无心外圆——切入磨——超精研”这一工艺流程,并相应诞生了成系列的切入无心磨床和超精研机床,零件加工精度达到3~5um,单件加工时间13~18s(中小型尺寸)。
70年代则主要是以应用60m/s 高速磨削、控制力磨削技术及控制力磨床大量采用,以集成电路为特征的电子控制技术的数字控制技术被大量采用,从而提高了磨床及工艺的稳定性,零件加工精度达到1~3um,零件加工时间10~12s。
80年代以来,工艺及设备的加工精度已不是问题,主要发展方向是在稳定质量的前提下,追求更高的效率,调整更方便以及制造系统的数控化和自动化。
而目前国内经过多年的发展,特别是近年主机发展的需要,从而带动了汽车轴承、精密机床轴承、铁路轴承、家电用轴承的快速发展,特别是轿车轴承发展迅猛,这无形带动了自动轴承内圈内圆磨床的技术和硬件的更新,目前国内大部分磨床的系统由液压进给补偿系统改成步进电机进给补偿系统,步进电机替代了原来的复杂的液压进给补偿系统,将原来液压波动和机械零件加工传动链的误差消除了,并且步进电机可以把进给过程分成几个阶段,每个阶段可以选用不同的脉冲频率控制进给速度,可以用脉冲数来控制机床工作台精进给,大大提高了轴承的精度。
不过相比国外先进的伺服电机控制系统,能将快跳油缸和谐波减速器去掉,采用滚珠丝杠和伺服电机直联结构,使得机械系统误差最小,步进电机又在抗干扰能力和重复定位精度能力上比伺服电机上差了一截,以致国内的轴承在寿命和可靠度上面还是比不上国外,不过相信随着轴承工业的进一步发展,我们与国外的差距会越来越来小。
十八世纪30年代,为了适应钟表、自行车、缝纫机和枪械等零件淬硬后的加工,英国、德国和美国分别研制出使用天然磨料砂轮的磨床。
这些磨床是在当时现成的机床如车床、刨床等上面加装磨头改制而成的,它们结构简单,刚度低,磨削时易产生振动,要求操作工人要有很高的技艺才能磨出精密的工件。
1876年在巴黎博览会展出的美国布朗-夏普公司制造的万能外圆磨床,是首次具有现代磨床基本特征的机械。
它的工件头架和尾座安装在往复移动的工作台上,箱形床身提高了机床刚度,并带有内圆磨削附件。
1883年,这家公司制成磨头装在立柱上、工作台作往复移动的平面磨床。
1900年前后,人造磨料的发展和液压传动的应用,对磨床的发展有很大的推动作用。
随着近代工业特别是汽车工业的发展,各种不同类型的磨床相继问世。
例如20世纪初,先后研制出加工气缸体的行星内圆磨床、曲轴磨床、凸轮轴磨床和带电磁吸盘的活塞环磨床等。
自动测量装置于1908年开始应用到磨床上。
到了1920年前后,无心磨床、双端面磨床、轧辊磨床、导轨磨床,珩磨机和超精加工机床等相继制成使用;50年代又出现了可作镜面磨削的高精度外圆磨床;60年代末又出现了砂轮线速度达60~80米/秒的高速磨床和大切深、缓进给磨削平面磨床;70年代,采用微处理机的数字控制和适应控制等技术在磨床上得到了广泛的应用。
随着高精度、高硬度机械零件数量的增加,以及精密铸造和精密锻造工艺的发展,磨床的性能、品种和产量都在不断的提高和增长。
内圆磨床和其他磨床一样,在提高效率、自动化程度和万能性方面有较大的发展。
但精度提高得很慢。
十多年来,内孔不圆度最佳值一直保持在0.3~1μm之间,最高表面粗糙度Ra0.08。
为了适应大批量生产,各国都出现一批自动内圆磨床,如美国海尔特公司的OCF 型内圆磨床,美国Bryant公司的C-2型内圆磨床,德国SIP200X315型内圆磨床。
1.2.3 课题的发展趋势与应用对象磨床是各类金属切削机床中品种最多的一类,主要类型有外圆磨床、内圆磨床、平面磨床、无心磨床、工具磨床等。
外圆磨床是使用的最广泛的,能加工各种圆柱形和圆锥形外表面及轴肩端面的磨床。
万能外圆磨床还带有内圆磨削附件,可磨削内孔和锥度较大的内、外锥面。
不过外圆磨床的自动化程度较低,只适用于中小批单件生产和修配工作。
内圆磨床的砂轮主轴转速很高,可磨削圆柱、圆锥形内孔表面。
普通内圆磨床仅适于单件、小批生产。
自动和半自动内圆磨床除工作循环自动进行外,还可在加工中自动测量,大多用于大批量的生产中。
平面磨床的工件一般是夹紧在工作台上,或靠电磁吸力固定在电磁工作台上,然后用砂轮的周边或端面磨削工件平面的磨床;无心磨床通常指无心外圆磨床,即工件不用顶尖或卡盘定心和支承,而以工件被磨削外圆面作定位面,工件位于砂轮和导轮之间,由托板支承,这种磨床的生产效率较高,易于实现自动化,多用在大批量生产中。