compressor lm2500
lm2500 工作原理

lm2500 工作原理The LM2500 is a type of marine gas turbine engine thatis widely used in various naval and commercial applications. Understanding its working principle is crucial for anyone involved in the operation, maintenance, or design of systems that use this type of engine. The LM2500 works on the principle of converting the energy stored in the fuel into mechanical energy, which is then used to performuseful work such as propelling a ship or generating electricity. This process involves several key components and stages, each of which plays a critical role in the overall operation of the engine.At the heart of the LM2500's working principle is the gas turbine cycle, which is the thermodynamic process through which the engine produces power. The cycle begins with the intake of air, which is compressed and then mixed with fuel in the combustion chamber. The mixture is then ignited, causing it to expand rapidly and produce high-velocity exhaust gases. These gases are directed through aseries of turbine stages, where their energy is used todrive the engine's compressor and any connected mechanical loads. Finally, the exhaust gases are expelled from the engine, completing the cycle.The LM2500's working principle can also be understoodin terms of its major components and their respective functions. The engine consists of a compressor, combustion chamber, turbine, and various auxiliary systems, all of which work together to produce power. The compressor is responsible for drawing in and pressurizing air, which is then delivered to the combustion chamber. In the combustion chamber, fuel is injected and burned, producing high-pressure, high-temperature gases that drive the turbine.The turbine, in turn, is connected to the compressor andany other equipment being driven by the engine, allowing it to convert the energy of the exhaust gases into useful work.From a practical standpoint, the working principle ofthe LM2500 also involves considerations of control and operation. The engine must be carefully managed to ensure safe, efficient, and reliable performance. This involvesmonitoring and adjusting various parameters such as fuel flow, air intake, and exhaust temperature, as well as coordinating the operation of the engine with other systems. Additionally, the engine's working principle hasimplications for maintenance and servicing, as its components must be regularly inspected, repaired, and replaced to ensure continued operation.In conclusion, the working principle of the LM2500 is a complex and fascinating topic that encompasses thermodynamics, mechanical engineering, and practical considerations of operation and maintenance. Understanding how this type of engine functions is essential for anyone involved in its use, and it offers insight into the broader principles of energy conversion and power generation. Whether one is a sailor, an engineer, or simply an enthusiast, the LM2500's working principle is a subject worthy of study and appreciation.。
燃气轮机中国电动超跑配备坦克心脏
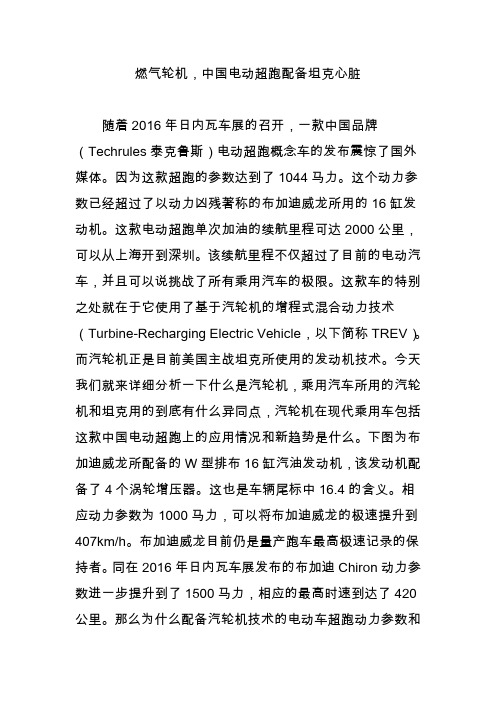
燃气轮机,中国电动超跑配备坦克心脏随着2016年日内瓦车展的召开,一款中国品牌(Techrules泰克鲁斯)电动超跑概念车的发布震惊了国外媒体。
因为这款超跑的参数达到了1044马力。
这个动力参数已经超过了以动力凶残著称的布加迪威龙所用的16缸发动机。
这款电动超跑单次加油的续航里程可达2000公里,可以从上海开到深圳。
该续航里程不仅超过了目前的电动汽车,并且可以说挑战了所有乘用汽车的极限。
这款车的特别之处就在于它使用了基于汽轮机的增程式混合动力技术(Turbine-Recharging Electric Vehicle,以下简称TREV)。
而汽轮机正是目前美国主战坦克所使用的发动机技术。
今天我们就来详细分析一下什么是汽轮机,乘用汽车所用的汽轮机和坦克用的到底有什么异同点,汽轮机在现代乘用车包括这款中国电动超跑上的应用情况和新趋势是什么。
下图为布加迪威龙所配备的W型排布16缸汽油发动机,该发动机配备了4个涡轮增压器。
这也是车辆尾标中16.4的含义。
相应动力参数为1000马力,可以将布加迪威龙的极速提升到407km/h。
布加迪威龙目前仍是量产跑车最高极速记录的保持者。
同在2016年日内瓦车展发布的布加迪Chiron动力参数进一步提升到了1500马力,相应的最高时速到达了420公里。
那么为什么配备汽轮机技术的电动车超跑动力参数和续航里程可以做到如此之高。
它又是什么样的一种黑科技呢?汽轮机从定义来说是一种撷取高温气体的动能转换为涡轮(叶片)转动动能的机械。
汽轮机按照大类来分可以分为蒸汽汽轮机、航空喷气发动机、燃气轮机三大类。
常见的主要用途则为发电或者直接传动。
一、蒸汽汽轮机Steam Turbine 离大家日常生活最近,却又是最难目睹的汽轮机技术就是蒸汽汽轮机。
因为每天我们使用的电力主要都来自火力发电厂中蒸汽汽轮机发电机组。
蒸汽汽轮机顾名思义就是将高温蒸汽中的动能转化为涡轮的动能再转化为电力的机组。
而高温蒸汽就来自火力发电厂中以煤为主要燃料的高压锅炉塔。
LM2500GasTurbineEngine:lm2500燃气涡轮发动机

LM2500 Gas Turbine Engine 101As the Navy proceeds into the twenty first century, gas turbine ships will become more and more abundant. GE's highly-successful, well-proven LM2500 aeroderivative gas turbine is directly derived from GE's CF6 family of commercial aircraft engines and GE's TF39 military engine. The CF6 family is used on DC-10, MD-11, A300, 747 and 767 aircraft, which have logged millions of flight hours. The TF39 military engine is employed on the U.S. Air Force's Galaxy C-5A/B transport aircraft. Currently more than 870 LM2500 gas turbines are in service on a variety of cruisers, frigates, destroyers and patrol boats for more than 24 international navies.In early applications, the LM2500 was rated at 21,500 bhp for the U.S. Navy's DD 963 and DDG 993 class destroyers, the CG 47 class cruisers, and the FFG 7 class frigates. General Electric uprated the LM2500 to 26,250 bhp for the DDG-51 destroyers and the AOE 6 class fast combat support ships. Each DDG-51 ship is powered by four LM2500 gas turbines which are in a combined gas and gas (COGAG) configuration. Each reduction gear combines the input of two LM2500 engines rated at 26,250 brake horsepower (bhp) for a total output of 105,000 bhp per ship. The LM2500 was again uprated in 1993 for use on the US Navy's newest Sealift gas turbine-powered ships. The uprate increased the LM2500 U.S. Navy military specification rating to 29,500 bhp, with the engine actually being rated at 32,000 bhp in the Sealift ships.The LM2500+ is an uprated version of LM2500 which provides lower installed dollar per horsepower and life-cycle costs than the LM2500. The 3600 rpm LM2500+ has been designed for 39,000 brake horsepower (bhp) with a simple cycle thermal efficiency of 39% at ISO conditions. The LM2500+ achieves increased power over the LM2500 primarily by increasing the compressor airflow 23%, with a minimal increase in combustor firing temperature by adding a compression stage (zero stage) to the front ofthe LM2500 compressor. The temperature capability of the hot section was alsoincreased by adding a thermal barrier coating to the combustor, upgrading turbine airfoilmaterials and by improving internal cooling designs.The LM2500 gas turbines drives controllable pitch propellers through a conventionalmain reduction gear, shaft and clutch. A 16 stage axial flow (air travel is parallel to theshaft) compressor increases the pressure and temperature of the working mass (air). Inthe combustor section, fuel is added through fuel nozzles and combustion occurs. A twostage high pressure turbine on the exhaust end of the combustor drives the compressor.The combination of the compressor, combustor, and high pressure turbine are oftencalled the gas generator. The exhaust from the high pressure turbine passes through alow pressure turbine which extracts the work required to drive the main reduction gear and ultimately the ship's propeller. The LM2500 module totally encloses the LM2500 toprovide thermal and acoustic insulation. A top hatch and a side door (DD/DDG/CG) ortwo side doors (FFG) provide access to and viewing of the engine. The module is shockmounted to reduce hull-borne noise transmission.LM2500 Gas Turbine Engine has a 16 stage axial flow compressor made up of a 16 stage Compressor rotor of moving blades driven by the high pressure turbine. The Compressor stator casing contains one stage of Inlet Guide Vanes (IGV), six stages of Variable Stator Vanes (VSV) and 10 stages of stationary stator vanes. The IGVs and stator vanes 1-6 are variable, meaning they are variable geometry. The angle of attack of the blades can be changed to prevent compressor stall. Bleed air is extracted from the compressor for use in the ship's bleed air system and for internal use in the engine.The combustor is an annular type with 30 fuel nozzles and 2 spark ignitors. Of the airfrom the compressor approximately 30% is mixed with fuel to support combustion. Theother 70% is used to cool and center the flame within the combustion liner.The ignition system produces a high intensity spark to ignite the fuel/air mixture during the start sequence. Once the engine is started the ignitors are no longer needed and will be de-energized.High pressure turbine section extracts enough energy from the hot expanding gasses to drive the compressor and accessory drive. The HP turbine is a two stage axial flow type which is mechanically coupled to the compressor rotor. The HP turbine uses approximately 65% of the thermal energy from the combustor to drive the compressor and engine mounted accessories.The accessory drive assembly is driven through the compressor rotor shaft via the inlet gearbox, radial drive shaft, and transfer gearbox. The Accessory gearbox provides mounting for the fuel pump, lube oil pump, air/oil separator, and pneumatic starter.The power turbine is a six stage axial flow type turbine. The power turbine extracts the remaining 35% of useable energy and uses this to drive the main reduction gear. The power turbine drives the reduction gear through a high speed flexible coupling shaft and clutch assembly. The high speed flexible coupling absorbs the radial and axial misalignment between the GTM and the main reduction gear.Foriegn Object Damage (FOD) is a major concern of gas turbine engines. FOD is simply debris of one form or other which can damage the internal components of a gas turbine engine. Propulsion and electrical generation turbines are no different than aircraft engines and the hazard FOD represents to the operation of these engines demands the attention of all personnel. On a flight deck periodic "FOD Walkdowns" keep the operating areas clear of debris. For shipboard engines FOD screens, wire mesh moisture separators, and if operating in a high air particulate environment "Scott" foam pads are used to filter incoming air and keep the engine operating.An advantage of a gas turbine engine is its ability to be removed from the ship for repair in a short period of time (approximately 72 hours). A set of rails is permanently installed in the intakes of each engine and a set of temporarily installed transition rails allow the disconnected engine to transit from its mounting attachments in the module onto the rails in the intakes. Crane service capable of extending over the soft patches in the intakes is required to pull the engine up the rails and out of the ship.。
考虑可调静叶压气机的船舶燃气轮机仿真优化

考虑可调静叶压气机的船舶燃气轮机仿真优化王志涛;白冰;李铁磊;范阔;李淑英【摘要】As an anti-surge technique , the adjustment scheme of the VSV compressor under off-design working con-ditions has a significant effect on the performance of a gas turbine .A variable-dimensions (0D-1D) system simula-tion model of a triaxial gas turbine was established , which considered the performance of variable-geometry com-pressor .To improve the operating efficiency of gas turbine , the optimized adjusting scheme of the first three rows of VSV and the steady-state performance of the gas turbine under different working conditions were obtained by using the system variable-dimensions simulation model .Simulation results show that compared with the original adjusting scheme for VSV , the optimized scheme can improve the economic benefit and stability of the gas turbine under vari -ous working conditions , which has a more positive effect on the overall performance of the gas turbine .%作为燃气轮机防喘措施之一,压气机可调静叶在变工况下的调节方案对燃机的运行性能具有重要影响.以某型三轴船舶燃气轮机为研究对象,建立了考虑变几何压气机的燃机系统仿真缩放(0维-1维)模型.以提高燃机运行效率为目标,通过系统仿真,得到了各个工况下低压压气机前三级可调静叶的最佳开度及整机稳态性能.仿真结果表明,与原始的可调静叶调节方案相比,采用优化方案可以提高燃机在各个工况下的经济性和稳定性,对燃机总体性能有更加积极的影响.【期刊名称】《哈尔滨工程大学学报》【年(卷),期】2017(038)011【总页数】6页(P1721-1726)【关键词】燃气轮机;压气机;可调静叶;控制;系统仿真;优化分析【作者】王志涛;白冰;李铁磊;范阔;李淑英【作者单位】哈尔滨工程大学动力与能源工程学院,黑龙江哈尔滨150001;哈尔滨工程大学动力与能源工程学院,黑龙江哈尔滨150001;哈尔滨工程大学动力与能源工程学院,黑龙江哈尔滨150001;哈尔滨工程大学工程训练中心,黑龙江哈尔滨150001;哈尔滨工程大学动力与能源工程学院,黑龙江哈尔滨150001;哈尔滨工程大学动力与能源工程学院,黑龙江哈尔滨150001【正文语种】中文【中图分类】TK479采用可调静叶(variable stator vane,VSV)变几何压气机是当下主流的燃气轮机防喘措施之一[1]。
GE_LM2500+DLE燃机节能运行研究及管理

中油国际管道公司海外某天然气项目运行压气站场13座,其中6座使用LM2500+DLE 燃机19台、7座使用西门子RB211-24G DLE 燃机23台。
随着天然气输气量的提高,燃机天然气消耗占比逐步升高。
目前项目燃机自耗气占比达到管线年度输气量的1.3%,自耗气已成为管道运行的最大成本。
近年来公司着力推行精细、集约化管理,持续推进降本增效[1-2]。
项目团队从实践情况出发,对GE LM2500+DLE 燃机运行效率及能耗开展研究。
经过长期实践发现能从2个方面降低自耗气:发现并确认LM2500+DLE 燃机的燃烧室在5种运行模式重叠区域的节能现象及原理;通过对LM2500+DLE 燃机燃烧室火焰温度热力学模型的研究,发现在燃气轮机压气机防喘排气阀(CDP 阀门)开度70%~GE LM2500+DLE 燃机节能运行研究及管理郑志明(中油国际管道公司)摘要:中油国际管道公司海外某天然气项目使用GE 公司干式低排放LM2500+DLE 燃气轮机驱动压缩机进行增输,燃气轮机自耗气占比达到管道年度输气量的1.3%及以上,自耗气已成为天然气管道运营最大成本。
为契合公司持续推进降本增效的管理理念,从生产实践过程中发现,机组从怠速至额定负荷转速燃烧室5种燃烧模式的重叠区域B、B+C/2、BC、AB、ABC 有明显的节能效果。
从DLE 机型的结构、工作原理,研究燃烧模式切换转速重叠区域的节能原理。
通过1a 多的运行证明燃烧模式切换安全有效,可以用来指导燃气轮机操作人员将机组在高效节能区域运行,达到每台机每小时最高791m 3/h 天然气的节能效果。
关键词:燃机;燃烧模式;火焰温度;节能减排DOI :10.3969/j.issn.2095-1493.2023.09.008Research and management on energy conservation operation of GE LM2500+DLE gas turbineZHENG ZhimingInternational Pipeline Company,CNPCAbstract:The overseas natural gas project of International Pipeline Company is used GE's low-emis-sion gas turbine LM 2500+DLE driven compressor to increase transmission.The self-consumption of gas turbine has been up to more than 1.3%of annual pipeline deliveries,and the self-consumption has become the largest cost of natural gas pipeline operation.In order to meet the company's management concept of continuously promoting cost reduction and efficiency,it is,from the process of production practice,found that there is obvious energy conservation effect in the overlapping area of five combus-tion modes in the combustion chamber from idle to full load speed:B,BC/2,BC,AB,ABC .From the structure and working principle of DLE model,the principle of energy conservation in the overlapping area of the combustion mode switching speed is studied.Through more than one year op-eration,it has proved that the method of combustion mode switching is safe and effective,which can be used to guide the gas turbine operators to operate the unit in a high-efficiency and energy conserva-tion zone,reaching energy conservation of up to 567.7kg of natural gas per hour per unit .Keywords:combustion engines;combustion mode;flame temperature;energy conservation and emission reduction作者简介:郑志明,工程师,2005年毕业于西北工业大学(飞行器动力工程),从事天然气管输企业燃驱压气站运行,188****4006,**********************.cn,北京市昌平区沙河镇西沙屯桥西科技园A12地块B2座,102206。
GE LM2500+

DescriptionThe LM2500-PV series gas turbine is a simple cycle, two shaft engine consisting of a gas generator and a two stage power turbine. Shaft power is extracted by means of a Purchaser supplied flexible coupling extending through a shaft tunnel within the Purchaser's exhaust collector. The gas generator consists of a variable geometry compressor; a single annular combustor; a high pressure turbine (HPT); an accessory drive gearbox; and controls and accessories. The power turbine (PT) is a six stage, low pressure turbine, aerodynamically coupled to the gas generator and driven by the gas generator exhaust gas.The cycle of the gas turbine begins with air entering the inlet bellmouth of the gas generator and directed into the compressor by the variable pitch inlet guide vanes (IGV's). Gas generator normal operating speed is 6,800 to 10,300 rpm. The compressed air leaving the compressor is directed into the single annular combustor section where it mixes with fuel. The fuel/air mixture is initially ignited by a single ignitor. Once initiated, combustion is self sustaining and the ignitor is turned off. The hot combustion gases are directed into the HPT, and the HPT drives the compressor rotor. Hot gases from the gas generator are then directed into the power turbine, and the PT drives the output shaft. Exhaust gases from the PT are turned 90° by the Purchaser's exhaust duct.The gas generator rotor is supported by three main roller bearings and one ball thrust bearing. The power turbine rotor is supported by two roller bearings and one thrust bearing.2.1 Inlet SectionThe inlet section consists of a bellmouth and a bulletnose and directs air into the inlet of the gas generator in such a manner as to provide smooth, non-turbulent airflow into the compressor. The bellmouth material is aluminum, and the bulletnose is constructed of graphite reinforced fiberglass. The standard bellmouth contains a spray manifold to inject liquid cleaning solutions into the compressor for crank-soak cleaning of the compressor while motoring the gas generator with the starter.2.2 Compressor SectionThe compressor is a 17 stage, high pressure ratio, axial flow design. Major components are: front frame, rotor, stator, and rear frame. The primary function of the compressor is to compress air for combustion; however, some air is extracted for engine cooling and bearing sump and seal pressurization. Air is taken in through the inlet, passes through successive stages of compressor rotor blades andstator vanes, and is compressed as it passes from stage to stage. After passingthrough 17 stages, the air has been compressed to a ratio as high as 23:1. The IGV's and the first seven stages of stator vanes are variable; angular position is changed as a function of compressor inlet temperature (T2) and compressor speed. This provides stall free operation of the compressor throughout the operating range.The steel front frame assembly forms a flowpath for compressor inlet air. Struts between the hub and outer case include lubrication supply and scavenge lines for the "A" sump end cover. The front frame provides mounting or attachment provisions for the gas turbine front mounts, handling mounts, compressor inlettemperature sensor, and transfer gearbox mounts. Air passages in the frame provide sump and seal pressurization and cooling. The lower frame strut houses a radial drive shaft that transfers power from the inlet gearbox to the accessory gearbox mounted on the bottom of the frame. See Figure 2-1.Figure 2-1. LM2500+ Front Frame Assembly2.2.2 Compressor Rotor2.1 Front Frame AssemblyThe compressor rotor is a spool/disk structure with circumferential dovetails. Use of spools makes it possible for several stages of blades to be carried on a single piece of rotor structure. There are seven major structural elements and four main bolted joints. The zero stage blisk (integral blade/disk) and forward shaft is bolted to the first stage disk. The first and second stage disks and Stages 3-9 spool are joined by a single bolted joint at Stage 2. The Stages 3-9 spool is bolted to the Stages 10-13 spool joint at Stage 9. The Stages 10-13 spool is followed by the rear shaft and the overhung Stages 14-16 spool, with a single bolted joint at Stage 13. Interfering rabbets are used in all flange joints for good positioning of parts and for rotor stability. See Figure 2-2.Figure 2-2. LM2500+ Compressor Rotor Assembly2.2.3 Compressor StatorThe compressor stator has one stage of IGV's and 17 stages of stator vanes (Stages 0-16). The IGV's and Stages 0-6 are variable. The IGV's and Stages 0 through 16 vanes are made of A286. The stator casing consists of four sections bolted together; casing material is M-152 steel. Borescope ports are located at each stage.The compressor stator casing contains two bleed manifolds. Bleed air extracted between the 9th and 10th stage vanes is used for sump pressurization and cooling, turbine frame cooling, and balance piston cavity pressurization. An air duct, supported by the front and rear shafts, routes Stage 9 air aft through the center of the rotor for pressurization of the "B" sump seals. Bleed air extracted between the 13th and 14th stage vanes is used for cooling the second stage HPT nozzles, interstage seal, first and second stage HPT blade shanks.The IGV's and Stages 0 through 2 vanes are shrouded. The shrouds are aluminum extrusions split into forward and aft halves that bolt together. The Stages 0 through 2 vane shrouds mate with rotor seal teeth. The variable vanes are actuated by a pair of torque tubes, one on each side of the engine. Each torque tube is rotated by a hydraulic actuator. Adjustable linkages connect directly from the torque tubes to the actuating rings to the variable vanes. Refer to Figure 2-3.Figure 2-3. LM2500+ Compressor Stator2.2.4 Variable Stator Control SystemThe variable stator vane (VSV) control is an electro-hydraulic system consisting of an engine mounted hydraulic pump, servovalve, and VSV actuators with integral linear variable differential transformer (LVDT) to provide feedback position signals to the main engine control. The system positions the IGV's and first seven stages of stator vanes (Stages 0 through 6) as a function of compressor inlet temperature and gas generator speed to maintain optimal compressor performance over the full range of operating conditions.2.2.5 Compressor Rear FrameThe compressor rear frame assembly is made from Inconel 718 and consists of the outer case, the struts, the hub, and the "B" sump housing. It's outer case supports the combustor, the fuel manifold, 30 fuel nozzles, one spark ignitor, and the Stage 1 high pressure turbine nozzle support. Bearing axial and radial loads and a portion of the Stage 1 nozzle load are taken in the hub and transmitted through 10 radial struts to the case. Six borescope ports located in the case just forward of the midflange permit inspection of the combustor, fuel nozzles, and the 1st stage turbine nozzle. Two borescope ports are provided in the aft portion of the case for inspection of the turbine blades and nozzles. See Figure 2-4.Figure 2-4. Compressor Rear Frame.2.3 CombustionThe combustor is annular and consists of four major components riveted together: cowl (diffuser) assembly, dome, inner skirt, and outer skirt.The cowl assembly, in conjunction with the compressor rear frame, serves as a diffuser and distributor for the compressor discharge air. It furnishes uniform air flow to the combustor throughout the operating range, thereby providing uniform combustion and even temperature distribution at the turbine.The combustor is mounted in the compressor rear frame on 10 equally spaced mounting pins in the forward (low temperature) section of the cowl assembly. These pins provide positive axial and radial location and assure centering of the cowl assembly in the diffuser passage. The mounting hardware is enclosed within the compressor rear frame struts so that it will not affect airflow.Thirty vortex inducing axial swirl cups in the dome (one at each fuel nozzle tip) provide flame stabilization and mixing of the fuel and air. The interior surface of the dome is protected from the high temperature of combustion by a cooling air film. Accumulation of carbon on the fuel nozzle tips is prevented by venturi-shaped spools attached to the swirler.The combustor liners are a series of overlapping rings joined by resistance welded and brazed joints. They are protected from the high combustion heat by circumferential film cooling. Primary combustion and cooling air enters through closely spaced holes in each ring. These holes help to center the flame and admit the balance of the combustion air. Dilution holes are employed on the outer and inner liners for additional mixing to lower the gas temperature at the turbine inlet. Combustor/turbine nozzle air seals at the aft end of the liners prevent excessive air leakage while providing for thermal growth. Refer to Figure 2-5.Figure 2-5. Combustor2.4 High Pressure TurbineThe HPT section consists of the HPT rotor, first and second stage turbine nozzle assemblies, and turbine midframe. The HPT extracts energy from the gas stream to drive the compressor rotor, with which it is mechanically coupled. The turbine nozzles direct the hot gas from the combustor onto the rotor blades at the optimum angle and velocity. The front end of the turbine rotor is supported at the compressor rotor rear shaft by the No. 4 bearings. The rear of the rotor is supported by the No.5 bearing in the turbine midframe. The turbine nozzles are contained in, and supported by, the compressor rear frame. The turbine midframe, in addition to supporting the aft end of the turbine rotor, supports the front end of the power turbine. It contains the transition duct through which the gas flows from the HPT section into the power turbine.2.4.1 RotorThe HPT rotor consists of a conical forward shaft, two disks with blades and retainers, a conical rotor spacer, a thermal shield, and a rear shaft. The forward shaft transmits energy to the compressor rotor. Two seals are on the forward end ofthe shaft. The front seal helps prevent compressor discharge pressure (CDP) air from entering the "B" sump. The other seal maintains CDP in the plenum formed by the rotor and the combustor. This plenum is a balance chamber that provides a corrective force and minimizes thrust load on the No.4 ball bearing. Turbine blades in both stages are internally air cooled and coated to improve erosion, corrosion, and oxidation resistance. See Figure 2-6.Figure 2-6. LM2500 High Pressure Turbine Rotor2.4.2 Rotor CoolingThe HPT rotor is cooled by a continuous flow of compressor discharge air that passes through holes in the Stage 1 nozzle support and forward turbine shaft. This air cools the inside of the rotor and both disks before entering the dovetails and out to the blades.2.4.3 Blade CoolingBoth stages of the HPT blades are cooled by compressor discharge air flowing through the dovetail and blade shanks into the blades. Stage 1 blades are cooled by internal convection and external film cooling. The convection cooling of the center area is accomplished through a labyrinth within the blade. The leading edge circuit provides internal convection cooling by airflow through the labyrinth then outthrough the leading edge, tip, and gill holes. The trailing edge is convection cooled by air flowing through the trailing edge exit holes. Stage 2 blades are cooled by convection, with all of the cooling air discharged at the blade tips. See Figure 2-7.Figure 2-7. LM2500 High Pressure Turbine Rotor Blade Cooling2.4.4 Stage 1 Turbine Nozzle AssemblyThe major parts of the first stage HPT nozzle assembly are the nozzle support, nozzles, inner seal, outer seal, and baffles. The nozzles are coated to improve erosion, corrosion, and oxidation resistance. They are bolted to the first stage nozzle support and receive axial support from the second stage nozzle support. There are 32 nozzle segments in the assembly, each segment consisting of 2 vanes. The vanes are cast and then welded into pairs (segments) to decrease the number of gas leakage paths. These partial penetration welds allow easy separation of the segments for repair and replacement of individual vanes. See Figure 2-8.Figure 2-8. LM2500 First Stage High Pressure Turbine Nozzle2.4.5 Stage 1 Turbine Nozzle Assembly CoolingThe Stage 1 nozzle assembly is air cooled (convection and film) by compressor discharge air flowing through each vane. Internally, the vane is divided into two cavities. Air flowing into the forward cavity is discharged through holes in the leading edge and on each side close to the leading edge to form a thin film of cool air over the length of the vane. Air flowing into the aft cavity is discharged through additional film holes and trailing edge slots. See Figure 2-9.Figure 2-9. LM2500 First Stage High Pressure Turbine Nozzle Cooling2.4.6 Stage 2 Turbine Nozzle AssemblyMajor parts of the Stage 2 assembly are the nozzles, nozzle support, first and second stage turbine shrouds, and interstage seal. The nozzle support is a conical section with a flange bolted forward between the flanges of the compressor rear frame and the turbine frame. The support mounts the nozzles, cooling air feeder tubes, and the Stages 1 and 2 turbine shrouds. The vanes (two per nozzle) direct the gas stream onto the mounting circle for the interstage seal attachment. See Figure 2-10.Figure 2-10. LM2500 Second Stage High Pressure Turbine Nozzle2.4.7 Stage 2 Turbine Nozzle Assembly CoolingThe Stage 2 nozzle assembly is air cooled by convection. The nozzle vane center area and leading edge are cooled by internal air (Stage 13) that enters through the cooling tubes. Some of the air is discharged through holes in the trailing edge; the remainder flows out through the bottom of the vanes and is used for cooling the interstage seals and the turbine blade shanks. See Figure 2-11.Figure 2-11. LM2500 Second Stage High Pressure Turbine Nozzle Cooling2.5 Turbine MidframeThe turbine midframe supports the aft end of the HPT rotor and the forward end of the PT rotor. It is bolted between the rear flange of the compressor rear frame and the front flange of the PT stator. The frame provides a smooth diffuser flow passage for HPT discharge air into the PT. Piping for bearing lubrication and seal pressurization is located within the frame struts. The frame contains ports for the HPT exhaust thermocouples and pressure probe. These ports also provide access for borescope inspection of the PT inlet area. Figure 12-12 shows the turbine mid frame.Figure 2-12. LM2500 Turbine Mid-Frame 2.6 Accessory Drive SectionThe accessory drive section consists of an inlet gearbox in the hub of thecompressor front frame, a radial drive shaft inside the 6 o'clock strut of the front frame, and a transfer gearbox bolted underneath the front frame. The optionalpneumatic starter, or optional hydraulic starter, and the lube and scavenge pump are mounted on the aft side of the transfer gearbox. The air/oil separator andcompressor stator servo valve control/hydraulic pump are mounted on the front of the gearbox. Figure 16-1 is a schematic of the accessory drive section.Power to drive the accessories is extracted from the compressor rotor through a large diameter hollow shaft that is spline connected to the rotor front shaft. A set of bevel gears in the inlet gearbox transfers this power to the radial drive shaft, which transmits the power to another set of bevel gears in the forward section of thetransfer gearbox. A short, horizontal drive shaft transmits the power to the accessory drive spur gears in the transfer gearbox.2.7 Power TurbineThe power turbine is a two stage high speed turbine aerodynamically coupled to the gas generator and driven by the gas generator exhaust gas. The hot gases leaving the gas generator are directed into the inlet liner of the power turbine that drive the output shaft. The exhaust gases leave the turbine through the diffuser, and then are turned 90° by the exhaust duct. The power turbine rotor shaft is supported by two hydrodynamic journal bearings and an hydrodynamic thrust bearing.Figure 2-12. LM2500+ HSPT Assembly2.7.1 High Speed Power Turbine AssemblyThe high speed power turbine assembly consists of a turbine rotor, turbine stator, turbine rear frame, diffuser and an inner barrel which supports the output shaft.The power turbine, which contains two stages of blades, is supported by the PT No.1 journal bearing housed in the forward end of the "barrel" (bearing housing), and the PT No.2 double thrust and journal bearing housed in the aft end of the barrel. The two stages of blades contain interlocking tip shrouds for low vibration levels, shanks to reduce the heat flow towards the disks, and are retained in the disks by dovetails. The innerspace between the platforms and the shanks is sealed by pins. To prevent hot gas ingestion in the rotating cavities between the disks, the blades contain two angel wing seals at the inlet side of the shank and one at the outlet side. The power turbine stator consists of a transition case, and two turbine casings; see Figure 2-13. The transition case consists of two flanges welded together; the forward flange is made of a nickel base alloy and mates with the gas generator interface flange, and the rear flange is made of carbon steel. The 1st stage turbine casing is a shell which contains 40 shrouds. Each shroud has a honeycomb surface which provides a close clearance seal between the rotating blades and the shroud, and also acts as a casing heat shield. The 2nd stage casing has the same configuration as the 1st stage casing. The nozzles of both stages consist of segments of three vanes each. The segments are supported by the shrouds.Figure 2-13. Power Turbine Stator2.8 Turbine Rear FrameThe Turbine Rear Frame is composed of two concentric casings connected by six equally spaced struts. The outer shell is connected to the exhaust plenum. The inner casing contains the inner diffuser and support the exhaust diffuser. A "barrel" contains the housing for the PT No. 1 and PT No. 2 bearings and is connected at the inner casing of the turbine rear frame by a bolted flange. The frame provides the rear mount for the gas turbine. See Figure 2-14.Figure 2-14. Turbine Rear frame2.9 Flexible Coupling AdapterThe power turbine rotor terminates with a bolted flange. The Purchaser's flexible coupling mates with this output flange. See Installation Interface Drawing L50102 for interface details.2.10 Lubrication SystemThe lubrication system on the gas generator consists of a shaft driven, positive displacement supply and scavenge pump, a distribution piping system, and a set of oil jets. The gas generator operates with dry sumps; oil from each sump and the accessory gearbox is scavenged by a separate positive displacement pump element. The engine oil seals are the labyrinth type with air pressurization to prevent leakage. The oil supply reservoir, oil filters, oil cooler, and the remainder of the system are provided by the Purchaser. A typical lubrication system is describedin Section 9.The power turbine lubrication system consists of oil passages for supply and return of oil to the bearings. The Purchaser is responsible for the off engine lube system, including the pumps, heat exchanger, filters and tank.2.11 Ignition SystemThe gas turbine ignition system consists of a single ignition unit that converts 115 volt, 60 or 50 Hz power to high voltage, a single high tension lead, and one ignitor.A second ignition unit, lead, and ignitor are optional (kit 682L510G02). The ignition components are shipped loose for mounting by the Purchaser. 2.12 InstrumentationThe LM2500+ gas turbine is equipped with the following instrumentation:2 Gas generator speed sensors, magnetic pickup type3 PT speed sensor magnetic pickup type1 Set (qty 8) PT inlet (T48) temperature sensors1 Gas generator mounted accelerometer1 PT mounted accelerometer1 GG Oil supply resistance temperature detector (RTD)4 GG Oil scavenge RTD5 GG Oil scavenge electrical chip detectors 1 Pressure tap for lube oil supply1 Pressure tap for lube oil scavenge2 Pressure taps for compressor discharge1 Pressure taps for any fuel manifold pressure1 Pressure tap for PT inlet (P48)2 Pressure taps for HP recoup2 Dual element T3 sensors (T/Cs)1 Redundant P2/T2 sensor (one sensor, two temperature RTD's, and one pressure tap)6 PT Bearing Temperature Sensors (RTD)7 PT Shaft Proximity Probes8 Power Turbine Wheelspace ThermocouplesAdditional instrumentation requirements are described in Section 10.2.13 Electrical SystemThe electrical system operates on 115 volt, 50 to 60 Hz, single phase power. The only electrically operated device normally furnished with the gas turbine is the ignition unit.2.14 Air Cooling and Pressurization System - Gas GeneratorThe gas generator sumps are pressurized and cooled by air bled from the 9th stage of the compressor. Higher pressure is maintained around each sump than inside the sump so that air flows into the sump across the seals and prevents oil leakage. Airthat flows into the sumps is vented to a common manifold and then to a mechanical air/oil separator mounted on, and driven by, the accessory gearbox. Separated oil is returned to the scavenge system, and the air is discharged.Ninth stage air used for sump cooling and pressurization is too hot for direct use, so ambient air is mixed with it by means of an aspirator.2.14.1 Air Cooling and Pressurization System - Power turbineFor cooling and pressurizing the high speed power turbine, stage 9 bleed air is cooled first down by a Purchaser-supplied air cooler and is then used to pressurize the sumps and to cool the disks and the rear frame struts. Thirty tubes bring the cooling air from an external manifold, through the first stage casing and the first stage nozzles, to the wheel spaces.The struts are cooled by a mix of 9th stage bleed air and ambient air to further reduce the temperature. Six ejectors are used for the mixing of the bleed air and ambient air.2.15 Starting SystemThe gas turbine can be equipped with a pneumatic (compressed air or natural gas) starter mounted on the accessory gearbox and integrated with the engine main lube system for continuous feed lubrication. An hydraulic starter is also available as optional equipment.。
用三种运放制作LP唱机的唱头放大器
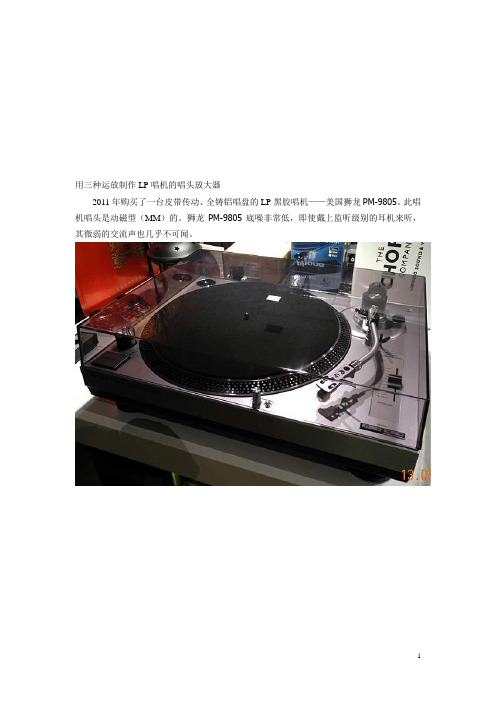
用三种运放制作LP唱机的唱头放大器2011年购买了一台皮带传动、全铸铝唱盘的LP黑胶唱机——美国狮龙PM-9805。
此唱机唱头是动磁型(MM)的。
狮龙PM-9805底噪非常低,即使戴上监听级别的耳机来听,其微弱的交流声也几乎不可闻。
但此唱机没有内置的唱头放大器,需要自己另外制作。
为了使用此唱机,DIY了MM唱头放大器。
先后用三种IC,实验了两种类型。
一、先用LT1057制作反馈型唱放。
LT1057是1992年专程去上海一家无线电/音响商店买的。
电路图和做好的实物及印版图片如下:该线路放大倍数计算:低频:【(0.68K+910K+56K+4.7K)/1.2K】+1=810中频:【(0.68K+56K+4.7K)/1.2K】+1 =52高频:(0.68K/1.2K)+1=1.57RIAA均衡网络转折频率的时间常数计算:高频(4.7K+56K)×1.2nF=72.84µS中频(4.7K+56K)×4.3nF=260µS低频910K×4.3nF=3913µS与RIAA标准转折频率的时间常数相比,有些误差。
RIAA标准转折频率的时间常数如下:t1=treble time constant, 75uS(2120 HZ)t2=medium time constant, 318uS (500.5HZ)t3=bass time constant, 3180uS (50.5HZ)这可能是此系成品机线路,采用非标准系列元件不方便所致。
由于我第一次DIY唱头放大器,没有经验,所以没有修改,照搬原线路的设计值挑选元件。
所有元器件都从手头已有的元件中挑选。
LT1057采用金属封装的。
±15V稳压电源用美国线性技术公司LT317和LT337制作,而不是常见的LM317、LM337。
LT317和LT337也是1992年在上海同一家无线电/音响商店购买的。
当时国内《无线电与电视》杂志介绍说,美国线性技术公司LT317和LT337的稳压性能特别好,共模抑制比很高,输出紋波极小,输出电压漂移极小,特别适合用来制作±稳压电源。
ManagerialAccountingMcgrawHillSolutionsManual

Managerial Accounting Mcgraw Hill Solutions ManualIf you are looking for a book Managerial accounting mcgraw hill solutions manual in pdf form, in that case you come on to theright site. We present the complete option of this book in doc, DjVu, txt, PDF, ePub formats. You can readManagerial accounting mcgraw hill solutions manual online managerial-accounting-mcgraw-hill-solutions-manual.pdf or download. In addition,on our site you may read the guides and different art eBooks online, either download them. We will to draw onyour attention what our site not store the book itself, but we provide link to the website wherever you candownload either reading online. If need to load Managerial accounting mcgraw hill solutions manual pdf managerial-accounting-mcgraw-hill-solutions-manual.pdf, thenyou've come to the correct site. We have Managerial accounting mcgraw hill solutions manual PDF,ePub, doc, txt, DjVu formats. We will be pleased if you will be back anew.solution for chapter 14 managerial accounting 6e - Tricia's Compilation for 'solution for chapter 14 managerial accounting 6e mcgraw hill' (McGraw Hill) Managerial Solution manual to Cost Accounting Amanagerial accounting 5e by mcgraw hill solutions - Managerial Accounting 5e By Mcgraw Hill Solutions Truck Nozzle. MANAGERIAL ACCOUNTING 5E BY MCGRAW HILL SOLUTIONS. DOWNLOAD: MANAGERIAL ACCOUNTING 5E BY MCGRAW HILLmcgraw hill managerial accounting chapter 3 - McGraw-Hill/Irwin 2005 The McGraw-Hill Companies, Inc. Managerial McGraw-Hill/Irwin 2005 The McGraw-Hill Companies, Inc. Managerial Accounting,financial and managerial accounting mcgraw hill - Mcgraw hill managerial accounting 3rd Edition solutions Mcgraw hill managerial accounting 3rd edition solutions free eBook download or read online on managerial accounting garrison 14th edition test bank - Cost and Management Accounting Multiple Choice Revision managerial accounting garrison 14th edition solutions manual managerial accounting by garrison 14thdownload mcgraw hill solutions manual accounting - Mcgraw Hill Solutions Manual Accounting pdf. View online or free download from . 76 Managerial Accountingdownload solutions manual for mcgraw hill - Accounting Solutions Manual Mcgraw Hill Tricias Compilation for chapter 9 solutions manual financial and Solutions Managerial Accountingloose-leaf for managerial accounting: ray - Loose-leaf for Managerial Accounting [Ray Garrison, solutions manual, McGraw Hill makes it sound like their Connect is a great tool.managerial accounting for managers mcgraw hill - Budgets force managers to Managerial Accounting, 12th Edition The Home > Document results for 'managerial accounting for managers mcgraw hill solutions manual' connect plus for garrison, managerial accounting, 14e - Garrison s Managerial Accounting is known for its relevance, McGraw-Hill Shop; Learning Solutions 2013 The McGraw-Hill Companies All rights reserved.chapter 2 - Managerial Accounting and Cost Concepts. Solutions Manual, Chapter 2 19 The McGraw-Hill Companies Solutions Manual, Chapter 2 3 The McGraw-Hill Companiesmanagerial accounting, 14th ed. learnsmart | mcgraw hill - courtesy of McGraw-Hill. Enterprise Solutions; About. use the managerial accounting concepts discussed within each chapter, Managerial Accounting,managerial accounting | mcgraw-hill connect - Products for Managerial Accounting. Management Accounting, 6e Kim Langfield-Smith; McGraw-Hill Shop; Learning Solutionsmcgraw-hill: managerial accounting : book - Overview Main description. Wild, Managerial Accounting responds to the market s need for an integrated solution with balanced managerial content that has asolutions managerial accounting 15th edition - Solution manual for Managerial Accounting 15th Managerial Accounting 15th edition by Garrison Solution manual. Publisher : McGraw-Hill Tools for Management.managerial accounting mcgraw hill solutions - Comaparitive ManualsChin, Solutions Manual We the People, 6th Edition, Thomas E, Patterson, McGraw Hill James M Reeve Jonathan Duchac Instructor Manualmanagerial accounting - scribd - Managerial Accounting, 12th Edition The McGraw-Hill Companies Managerial (Cost) Accounting Chapter's The solution manual is for Managerial Accounting 14Emanagerial accounting 14th edition textbook solutions | - Managerial Accounting 14th Edition. McGraw-Hill; Cengage; Pearson; Wiley; Solutions Manual; Scholarships; Career Search; Online Tutoring; mcgraw hill managerial accounting solution manual - Chapter 2. Managerial Accounting and The procedure outlined above is just one way in which the solution to the Solutions Manual, Chapter 2 19 The McGraw-Hillmcgraw hill managerial accounting 14th edition - Mcgraw Hill Managerial Accounting 14th Edition Mcgraw Hill Managerial Accounting 14th Edition Chapter 2 Solutions Read online and download mcgraw hill managerial managerial accounting for managers: eric noreen, peter brewer - Managerial Accounting for Managers 3rd edition by Noreen/Brewer/Garrison is based on the market-leading managerial accounting solution, McGraw-Hill Educationsolutions manual chapter 11 managerial accounting | tricia joy - Automatic vs. Manual Managerial accounting termed controlling is designed Filetype: The McGraw-Hill Companies, Inc., 2008. Solutions Manual,solutions to managerial accounting eric w - Dec 11, 2011 Chapter 1Managerial Accounting and the BusinessEnvironmentSolutions to Questions1-1 Managerial accounting is Chapter 1Managerial Accounting and solutions managerial accounting 10th edition hilton - Solution manual for Managerial Accounting: McGraw-Hill/Irwin; 10 edition ( 2013) Basic Cost Management Conceptsmcgrawhill managerial accounting chapter 17 solutions - Managerial Accounting. Managerial Accounting Twelfth Edition Ray H. Garrison, D.B.A., CPA Professor Emeritus Brigham Young University Eric W. Noreen, Ph.D., CMAmanagerial accounting 9th canadian edition - May 04, 2014 Managerial accounting 9th canadian edition solutions managerial accounting 9th edition managerial accounting 9th edition hilton mcgrawmanagerial accounting solutions manual: dr. larry - This Managerial Accounting Solutions Manual provides answers to all Basic and Involved Problems found in the textbook. The Managerial Accounting book covers a solution manual for managerial accounting | panezai khan - Solution manual for managerial accounting. Added by By Panezai Khan in Managerial Accounting. Log In; Sign Up; Solution manual for managerial accounting. Added byfinancial & managerial accounting 16th edition - Access Financial & Managerial Accounting 16th Edition solutions now. Our solutions are written by Chegg experts so you can be assured of the highest quality!managerial accounting 14e garrison test bank and solution manual - managerial accounting 14th edition garrison test bank, managerial accounting 14th edition garrison solution manual, test bank of managerial accounting 14th editionsolutions manual for fundamental managerial accounting 6th - Solutions Manual For Fundamental Managerial Accounting 6th Edition Price comparison. Compare and save at .mcgraw hill managerial accounting solutions - Mcgraw Hill Managerial Accounting Solutions Chapter 12 downloads at Cost Concepts Mcgraw Hill Managerial Accounting Managerial McGraw Hill Irwinmanagerial accounting 14e garrison test bank - Apr 17, 2014 Solution Manual or E-Book for Managerial Accounting 14th edition then click Solution Manual or E-Book for Managerial Accounting 14th editionmanagerial accounting fifth edition solution munual - Managerial Accounting Fifth Edition Solution Munual Mcgraw-hill Companies, Financial and Managerial Accounting Sixth Edition and Micro-Tech,mcgraw hill managerial accounting chapter 12 - Mcgraw Hill Managerial Accounting Chapter 12 Solutions downloads at - Download free doc files,ebooks and Solutions Manual . McGraw-Hill/Irwin managerial accounting solutions by mcgraw hill | - MANAGERIAL ACCOUNTING Thursday, August 08 14 / doc. TEXT: Hilton, Managerial Accounting, 6th ed., McGraw-Hill Companies Inc., 2005. My experience has shownmanagerial accounting and managerial accounting - What is Managerial Accounting, R. H., P. E. Noreen,'Managerial Accounting', Irwin McGraw Hill, 1999 The Rise and Fall of Management Accounting',managerial accounting - chapter 05 - scribd - Managerial Accounting The McGraw-Hill Companies, Inc., Managerial Accounting Chapter 2 Solutions. Lesley Velazquez. Chapter05 E7.managerial accounting with connect plus solution manual - Managerial Accounting with Connect Plus Solutions Manual Select your edition below to get access to Chegg s solutions manual for your textbook. financial and managerial accounting mcgraw hill - Financial And Managerial Accounting Solution Manual | Textbook Solutions Manuals Found Here! Financial & Managerial Accounting McGraw-Hill RyersonRelated PDFs:lm2500 technical manuals, yamaha fjr ser manual, suzuki carry dd51t service manual, policy and procedures manual beauty salon, passat b6 gearbox manual, yamaha vino 49cc manual, chevrolet volt service repair manual, manual atlas copco xahs 426, ford escort 91 manual, great wall workshop manual, 2015 burgman 400 abs manual suzuki, manual for canon mx882, acs solution manual organic chemistry, theory of aerospace propulsion solutions manual, service manual vespa px 150, toshiba aquilion ct user manual, hydrovane 250 air compressor service manual, 1991 ford ranger service manual, 143h motor grader service manual, dpi 610 manual, service manual for 97 kawasaki kdx 220, 80 hp 3 cylinder service manual, powermate portable generator manual, thermo king service manual old, cummins 4bt shop manuals, physical science lab manual answers investigation 11b, kazuma jaguar 500 repair manual, v280 repair manual, praxis 5015 study guide, ford 9030 operator manual, earth science 13th edition study guide, guide to notes 18 history alive, 1996 seadoo gsx service manual, mitsubishi canter engine workshop manual, landis staefa manuals, red hat system administration study guide, wileyplus solutions accounting manual, guide marrakech, canon irc3480 manual, otc 4000e manual。
- 1、下载文档前请自行甄别文档内容的完整性,平台不提供额外的编辑、内容补充、找答案等附加服务。
- 2、"仅部分预览"的文档,不可在线预览部分如存在完整性等问题,可反馈申请退款(可完整预览的文档不适用该条件!)。
- 3、如文档侵犯您的权益,请联系客服反馈,我们会尽快为您处理(人工客服工作时间:9:00-18:30)。
A.R.Wadia e-mail:aspi.wadia@D.P.WolfF.G.HaaserGE Aircraft Engines,Cincinnati,OH45215Aerodynamic Design and Testing of an Axial Flow Compressor With Pressure Ratio of23.3:1for the LM2500؉Gas TurbineThe LM2500ϩgas turbine,rated between39,000–40,200shaft horsepower(shp),was introduced forfield service in1998.This growth aero-derivative gas turbine is suitable for a variety of power generation applications,such as co-generation and combined cycle,as well as mechanical drive applications.At the heart of the LM2500ϩ25%power increase is an up-rated derivative17-stage axial compressor.This paper describes the aerody-namic design and development of this high-pressure ratio single-spool compressor for the LM2500ϩgas turbine.The compressor is derived by zero-staging the highly efficient and reliable LM2500compressor to increase theflow by23%at a pressure ratio of23.3:1. The aerodynamic efficiency of the compressor is further improved by using three-dimensional,custom-tailored airfoil designs similar to those used in the CF6-80C2high-pressure compressor.The compressor achieved a peak polytropic efficiency above91%, meeting all its operability objectives.The technical requirements and overall aerodynamic design features of the compressor are presentedfirst.Next,the zero stage match point selection is described and the procedure used to set up the vector diagrams using a through-flow code with secondaryflow and mixing is outlined.Detailed design results for the new transonic airfoils in the compressor using three-dimensional viscous analysis are presented.The compressor instrumentation and performance test results are discussed. The performance of the zero stage is separated from that of the baseline compressor with the CF6-80C2airfoils to show the improvement in efficiency with the new airfoils.͓DOI:10.1115/1.1464562͔IntroductionApplication of aero-engine technology to ground-based gas tur-bines has increased rapidly,especially in the last decade,as docu-mented in the works of Scalzo͓1͔,Kashiwabara͓2͔,Sehra͓3͔. Smed͓4͔,Janssen͓5͔,and Stringham͓6͔.The LM2500gas tur-bine,derived from the CF6-6/TF39aircraft engines,has also le-veraged off aircraft engine technology development to facilitate the increase in its industrial power rating from the original24,000 shp to the current31,200shp.Market studies initiated in the late eighties and early nineties showed that the LM2500industrial gas turbine needed additional power͑39,000shp at ISO conditions͒to meet customer requirements͑Farmer͓7͔͒.This up-rated power version of the LM2500was named the LM2500ϩgas turbine. The LM2500ϩgas turbine3-D cutaway presented in Fig.1high-lights the key modifications made to the engine relative to the LM2500base engine.In March1994,after a series of preliminary design studies on how to achieve the required power increase,it was decided to launch the LM2500ϩwhich was chosen from four candidate con-figurations based on a cost-and-risk assessment comparison.The preliminary design team evaluated power enhancement techniques such as inter-cooling,inlet supercharging,recuperation and other refinements.The team,however,decided on the basis of design simplicity,program schedule,technology risks and development cost and customer price that increasing the inlet massflow through the engine was the simplest and most conservative way of increasing the power output.The increased massflow could be achieved by zero-staging the current production LM2500com-pressor.Simultaneously,the increase in the turbine rotor inlet tem-peratures could be minimized to approximately35°C͑65°F͒͑Va-lent͓8͔͒by going to a more efficient compressor design using three-dimensional analytical tools and incorporating custom-tailored compressor airfoils from the CF6-80C2aircraft engine.It was apparent that this design approach best met the goals of using proven technology at minimal risk.Also,keeping a strong funda-mental LM2500design heritage facilitated product support while meeting the objectives of a base load hot section inspection inter-val of25,000h with engine overhauls at50,000h. Compressor Technical Requirements SummaryThe performance requirements for the LM2500ϩcompressor were less stringent relative to those required by commercial or military aircraft engines.While aircraft engines have multiple op-erating points such as take-off,cruise,etc.,where performance is crucial,the LM2500ϩis required to operate at close to its peak efficiency near its high-speed design point.While no specific per-formance requirements at other speeds were specified,it was de-sirable for the compressor to preserve good efficiency over a range of speeds.Additionally,the LM2500ϩcompressor was also required to operate stall-free with both a single annular combustor͑SAC͒, which results in a smooth compressor operating line,and with a dry low emissions͑DLE͒combustor,which results in a compres-sor operating line with steps corresponding to the staging in the combustor.The compressor operating line can vary by as much as 2%below and above the nominal operating line,from the start of the combustor staging to the end of the staging sequence,respec-tively.The customer-supplied inlet systems used with industrial gas turbines,such as the LM2500ϩ,are generally quite aerodynami-cally‘‘clean’’and use a light wire screen mesh to prevent anyContributed by the International Gas Turbine Institute and presented at the Inter-national Gas Turbine and Aeroengine Congress and Exhibition,Indianapolis,Indiana,June6–9,1999.Manuscript received by the IGTI,January1999;revised manuscriptreceived January24,2002.Paper No.1999-GT-210.Review Chair:D.Wisler.Copyright©2002by ASMEJournal of Turbomachinery JULY2002,Vol.124Õ331large objects being ingested by the compressor.Maneuvers and cross-wind inlet distortion issues are almost nonexistent on these land/marine-based engines,thus easing the operability require-ments.Installation design manuals suggest the inlet distortion in-dex to be of the order of 2%or less as most of the operation is with a straight bellmouth or radial volute.To account for any inlet distortion that might be encountered in the field,the compressor was designed with a slight tip radial ͑i.e.,total pressure deficit at the tip ͒inlet total pressure profile to realistically simulate the tip aerodynamic loading level on the zero stage blade.Acoustics plays an economic role in land/marine-based systems design,and the goal for the LM2500ϩwas to maintain the same inlet noise sound pressure level in spite of the 23%higher airflow.This requirement set the vane/blade ratios and the axial spacing between the rotor and the stator using an ‘‘acoustic cutoff’’design criteria.The compressor operating line was set with a minimum of 12%stall margin to account for any operating line migration that would occur in service during the life of the engine.Start times for the engine are of the order of 2min,which is less stringent than in aircraft engines.A 4-deg open stator stall margin requirement was conservatively set for the LM2500ϩto account for variable stator vanes ͑VSV ͒control/rigging variation and deterioration in the field.Compressor Aerodynamic Design FeaturesThe detailed aerodynamic design of the original CF6-6/LM2500compressor has been reported by Klapproth et al.͓9͔.To achieve the increased power output rating,the LM2500ϩrequired a 23%increase in airflow.The 23%increase in flow was achieved by adding an additional compression stage ͑zero stage ͒to the LM2500and flaring the flowpath in front of the existing compres-sor to form an overall 17-stage axial compressor unit.Figure 2shows the changes incorporated into the LM2500ϩrelative to the base compressor.As a result of zero staging of the compressor,the LM2500ϩincreased in length by 34.3cm ͑13.5in.͒and the weight of the engine increased by about 363kg ͑800lb ͒Table 1shows the comparison of key aerodynamic design parameters for the LM2500compressor with those selected for the design of the LM2500ϩcompressor.Zero Stage Match Point SelectionTechnical information on zero-staging compressors in the open literature is limited.Some of the principles in the development of front stages of axial flow compressors has been reported by Eisen-berg ͓10͔and Katoh ͓11͔.A recent compressor zero-staging appli-cation to the Taurus 60axial flow compressor that increases the inlet mass flow by approximately 20%and raises the pressure ratio from 11.2:1to 16:1has been reported by Van Leuven ͓12͔and Rocha et al.͓13͔.The CF6-6/LM2500compressor performance map has been presented in ͓9͔.The LM2500compressor achieved a peak poly-tropic efficiency of 90.7%along the engine operating line at a compressor inlet corrected flow of 60kg/s ͑132lb/s ͒and pressure ratio of 15:1.The 88.9%polytropic efficiency shown in Table 1͑does not include the compressor exit diffuser losses ͒represents the compressor performance at the maximum power operating point of the LM2500engine,which is different from the peak efficiency point on the compressor map.To achieve maximum compressor performance with the zero stage,the point corresponding to the peak efficiency of the exist-ing LM2500compressor would be selected as the match point for the LM2500ϩcompressor design.This sets the zero stage pres-sure ratio such that the LM2500ϩcompressor achieves its overall compression ratio goal.In order to achieve this optimum pressure ratio,the zero stage’s ‘‘stage effectivity,’’as calculated using the approach formulated by Koch ͓14͔,exceeded that demonstrated by the first stage of the compressor in GE Aircraft Engine’s energy efficient engine (E 3),which has a similar overall pressure ratio as that for the LM2500ϩ.The term ‘‘stage effectivity’’is a correlation that is used inter-nally within GE Aircraft Engines to assess a stage’s loading rela-tive to the loading at stall.It is synonymous to the peak stage static pressure rise coefficient and has been correlated versus a parameter involving stage average values of solidity and aspect ratio.The correlation serves as an aerodynamic loading limit,and accounts for factors such as blade speed,axial velocity,reaction ratio,clearance and Reynolds number to form a systematic method for analysis or prediction of compressor stall perfor-mance.The selection of the pressure ratio,for the zero stage,was an iterative process to achieve a balance between the design point pressure ratio and its ‘‘stage effectivity’’at stall.This iterative process yielded a zero stage pressure ratio of 1.438,which is slightly less than optimum.The efficiency potential of the zero stage was determined using the principles outlined by Koch and Smith ͓15͔and the corre-sponding work input assigned to it.The resultant exit temperature and pressure from Rotor 0provided the input to calculate the inlet conditions into the following stator.Inlet corrected flow and speed at Stator 0inlet were then calculated and compared to the mea-sured flow at speed along the base LM2500compressoroperatingFig.1LM2500¿gas turbine uniquefeaturesFig.2LM2500¿high pressure compressor improvements relative to the base …LM2500…compressorTable 1Compressor aerodynamic design operatingpoint332ÕVol.124,JULY 2002Transactions of the ASMEline.The calculations converged quickly to provide a realistic axial match between the new zero stage and the downstream ex-isting compressor.The aforementioned approach,substantiated by past experience on the E 3engine and test data from the LM2500compressor,resulted in matching the LM2500ϩzero stage to the original LM2500compressor at an inlet corrected flow of about 62.7kg/s ͑137lbs/s ͒͑corresponding to an inlet corrected speed of 8,950rpm ͒at 90.3%polytropic efficiency.Compressor Design Vector DiagramsThe vector diagrams used to design the new front stages of the LM2500ϩcompressor were derived from a data match of a fully instrumented,CF6-80C2core engine using the circumferentially averaged,through-flow code with secondary flow and mixing ͑Adkins and Smith ͓16͔͒.Next,the new zero stage was added to the through-flow analysis.The new set of vector diagrams ob-tained were such that the velocity triangle quantities—such as the inlet relative flow angle,inlet relative Mach number and inlet meridional Mach number into stage 2blade—were the same as the data match values.The axial distribution of solidity,aspect ratio,axial velocity,diffusion factor,Mach number,inlet and exit flow angles and air-foil camber and stagger angles for all the LM2500blading has been published ͓9͔.Table 2summarizes some of the key airfoil geometry and vector diagram quantities for the first three stages of the LM2500ϩcompressor.A preliminary design analysis resulted in the selection of 16blades ͑Rotor 0͒for the zero stage.The selection of the number of inlet guide vanes and the number of zero stage vanes ͑vane/blade cut-off ratio ͒,and the axial gaps between the inlet guide vanes,Rotor 0and Stator 0were set by the technical requirements for an ‘‘acoustic cut-off’’in order to prevent higher inlet noise levels.This resulted in larger-than-normal axial gaps on both sides of the zero stage blade,as shown in Fig.2.These large gaps are detri-mental to compressor performance,making the aerodynamic de-sign of the compressor even more challenging.The following sections summarize the detailed design of the new front stages of the LM2500ϩcompressor with emphasis on the zero stage and the first stage blade designs.Three-dimensional viscous analysis using the computer program developed by Jen-nions and Turner ͓17͔was used extensively in the design of the compressor blading.Front Frame and Inlet Guide Vane DesignThe LM2500ϩfront frame is very similar to the original engine frame.It is a five-strut ͑four thin struts and one thick strut ͒,17-4steel casting and retains the same inner and outer front forward flange configuration for inlet commonality as shown in Fig.2.The frame’s inner and outer flowpath walls were flared to increase the flow area through the frame to prevent a higher pressure loss due to a possible flow restriction.The original front frame struts are bi-convex airfoils,which for the LM2500ϩwere made more aerodynamic using NACA 65-series airfoils.Thickness and airfoil contour changes lowered the front frame losses as verified by three-dimensional viscous analysis of the frame.The inlet guide vane ͑IGV ͒airfoil design was done with a con-ventional profile.The correlation of NACA 63-series airfoil cas-cade data by Dunavant was used with the IGV solidity varyingfrom 0.89at the tip of 1.2at the hub.The IGV exit swirl was varied almost linearly from about 18deg of pre-swirl at the tip to Ϫ15deg of counterswirl at the hub.The tip pre-swirl provided Mach number relief to the downstream rotor at the tip,while the hub counterswirl helped lower the hub Mach number into the zero stage vane.The IGV design was important because it has to de-liver the required swirl distribution to the zero stage blade at the design condition and it has to be able to operate adequately at part speed when the airfoil is closed by as much as 60deg.The IGV airfoil was analyzed at the design point with the three-dimensional viscous analysis.This analysis was done to verify the magnitude and radial distribution of pressure loss assumed in the circumfer-entially averaged through-flow analysis and its ability to meet the exit swirl requirements.Zero Stage Blade DesignPreliminary mechanical design studies showed that dovetail stresses on a traditional zero stage blade design would limit the minimum radius ratio to 0.45.A blisk version of the rotor permit-ted a reduction in the radius ratio to 0.368.This reduction in radius ratio also provided some aerodynamic performance benefits by lowering the inlet specific flow.The blisk also provided a parts count reduction by replacing 40ϩparts with a single part,and eliminated the wear issue of a midspan shroud,blade and disk and dovetails.Although blisk technology has been in existence for 20ϩyears,its inclusion in the LM2500ϩrepresents the first in-troduction of a blisk to GE Aircraft Engines’Marine and Indus-trial engines product line.Table 3shows the comparison of the geometric and aerody-namic design parameters between the zero stage rotor for the LM2500ϩcompressor and the first stage blade from the GE Air-craft Engines E 3compressor.As illustrated by the thickness com-parisons in Table 3,the LM2500ϩblades were considerably thicker ͑ruggedized ͒to increase foreign object damage ͑FOD ͒tol-erance.The location of maximum thickness was also moved for-ward on the LM2500ϩairfoil,in a similar manner as illustrated in the paper by Wadia and Law ͓18͔,to provide improved resistance to leading edge foreign body impact.Rotor 0was designed to the vector diagrams created from a data match of the CF6-80C2core compressor as reported earlier.Transonic airfoil design principles presented in ͓18͔were applied to custom tailor the mean camber lines to alleviate some of the performance penalties associated with the ruggedization.The det-rimental effect on performance due to the large increase in thick-ness,especially near the hub,was also reduced by scalloping ͑area-ruling ͒the hub flowpath within the blade as shown in Fig.2.The inlet relative Mach number is transonic over most of the blade span of the LM2500ϩRotor 0.The efficiency of a transonicTable 2Rotor and stator pitch line design parameterssummaryTable 3Zero stage blade key aerodynamic designparametersJournal of Turbomachinery JULY 2002,Vol.124Õ333blade is heavily influenced by shock losses,which may exceed the losses due to cascade diffusion and secondaryflow effects.The Mach number just ahead of the leading edge passage shock can be influenced by the shape of the blade suction surface ahead of the shock.Increasing the average suction surface angle,as measured from axial,ahead of the shock reduces the average Mach number upstream of the shock through external compression and should reduce the shock losses.However,this type of airfoil can result in a reduced cascade throat area.If the throat is too small,the cas-cade will not pass the designflow and may not achieve the at-tached shock pattern desired for minimum loss.The lessons learned in transonic rotor performance studies by Wadia and Copenhaver͓19͔,with different cascade area ratios,were applied to set the throat margin,internal contraction and trailing edge camber of the zero stage blade.The blade was designed with a5% throat margin.The design was further analyzed with a three-dimensional vis-cous code to get more definitive results on the effect of custom tailoring the mean camber lines and to verify that the cascade would pass the designflow and deliver the design intent exit ra-dial profiles of total pressure and temperature.Theflow computed by the three-dimensional analysis was 1.05%higher than the designflow rate.This difference between the design and calculatedflow rate is consistent with that between the three-dimensional analysis and measuredflow on other similar transonic blade row designs.The radial profiles of total pressure,temperature and adiabatic efficiency͑at Stator0leading edge͒calculated by the three dimen-sional viscous analysis͑3-D͒are illustrated in Fig.3.The total pressure profile is hub strong and agrees well with the design intent also shown in Fig.3.The calculated efficiency was slightly higher relative to the design vector diagrams.Figure4shows the isentropic Mach number distribution on the pressure and suction surfaces of the LM2500ϩzero stage blade. Figure5shows the corresponding calculated shock structure at two immersions along the blade span.Near the tip,a two-shock system was selected over a single leading edge shock pattern to obtain a balance between the efficiency and stability of the blade. It was recognized that the peak efficiency would occur on a slightly higher operating line where the passage shock merged with the leading edge shock.At the midspan,Fig.5shows a single passage shock structure with the shock intersecting the pressure and suction surfaces at30and65%axial distance from the lead-ing edge of the airfoil,respectively.Figure6shows the isentropic blade surface Mach number dis-tribution near the hub of the blade.The hub scalloping provided the required relief to the13%thick hub section by lowering the average Mach number and resulted in a shock-free design by keeping the blade surface Mach numbers below unity.Noflow separation at the hub was observed in the three-dimensional cal-culations.Figure7shows the zero stage blisk used in thefirst build of the LM2500ϩengine.Zero Stage Vane DesignStator0on the LM2500ϩreplaces the inlet guide vane on the base machine but has aerodynamic characteristics similar to the first stage vane in the baseline compressor.As mentioned before, the stator hub loading levels and inlet absolute Mach numbers were controlled by usingϪ15deg counterswirl into the zero stage blade.Table4summarizes the geometric and aerodynamic design parameters for the vane.In the paper on three-dimensional relief,Wadia and Beacher ͓20͔have shown that the need to align the inlet metal angle pre-cisely with the skewed inletflow angles at the endwall͑at the riskof placing a significant spanwise twist gradient in the blade sur-face near the endwall͒appears to be less than might be implied from two-dimensional cascade analyses.While some recognition of the high air angles that exist at the endwalls was considered in the design of the zero stage vane,extreme leading edge angle gradients were not required.Figure8shows the calculated three-dimensional vane surface isentropic Mach number distribution at the tip,pitch and hub.A shock-free diffusion at the hub wasac-Fig.3Comparison of Stage0blade exit radial profiles of total pressure,total temperature,and adiabatic efficiency at the aerodynamic design pointTable4Zero stage vane key aerodynamic designparameters334ÕVol.124,JULY2002Transactions of the ASMEcomplished and the ability of the stator to deliver the required swirl to the following rotor was verified by the three-dimensional analysis.First Stage Blade DesignCF6-80C2and LM2500first stage compressor blades are de-signs that use midspan shrouds.The LM2500ϩfirst stage blade moved away from the shrouded design to a wide chord rotor de-sign.Some of the key geometric and aerodynamic design param-eters for the first stage blade are presented in Table 5.Similar to the zero stage blade,this airfoil was also ruggedized to improve FOD tolerance.Some amount of hub scalloping was also done to accommodate the large thickness increase in the hub due to the elimination of the midspan shroud and thicker tip sec-tions.Three-dimensional analysis was used extensively in the de-sign,and Fig.9illustrates the isentropic Mach number distribu-tion on the blade surface at the tip,pitch and hub immersions.As illustrated by the axial distribution of the blade surface Mach number at the hub and the midspan in Fig.9,most of the airfoil sections along the span were front loaded.However,the sections locally near the tip were more aft loaded to reduce tip leakage and improve performance as has been demonstrated in low-speed test-ing by Wisler ͓21͔.As in the zero stage blade analysis,the three-dimensional analysis was used to verify that the desired radial profiles of total pressure and efficiency were achieved by the first stage blade.Figure 10shows a photographic comparison of the current pro-duction first stage midspan shrouded blade and the new wide chord LM2500ϩfirst stage blade.The LM2500ϩblade has about 35%lower aspect ratio and 60%more midspan chord,but ap-proximately the same midspan solidity relative to the first stage blade in the base machine.First Stage Vane DesignThe first stage vane design was only a minor change from that in the CF6-80C2core compressor.The design incidences on the LM2500ϩStator 1were patterned after those from the CF6-80C2Stator 2as this would be the second stage of the LM2500ϩcom-pressor.The vane surface isentropic Mach number distributions on Stator 1were similar to those reported for the zero stage vane.The required inlet conditions into the next rotor stage,which is iden-tical to the CF6-80C2airfoil,were verified by the three-dimensional analysis.LM2500¿Variable Stator SystemTo ensure stall-free operation at part speed,the inlet guide vanes and the first six stators are variable in the LM2500ϩen-gine.The method of scheduling the variable stators was changed in the LM2500ϩ.Whereas the LM2500uses a pair of level arms powered by twin actuators,the LM2500ϩuses two torque shaft assemblies located 180deg apart to actuate the compressor vari-able stator vanes.Each torque shaft,which is cylindrically shaped,is mounted to the compressor casing along the axis of the engine with a bearing at each end to allow for rotation within a forward and aft mounting bracket.A hydraulic actuator attached to a lug near the front end of each shaft rotates the shaft.Additionallugs,Fig.4LM2500¿Rotor 0isentropic Mach number contours on the pressure and suctionsurfacesFig.5LM2500¿Rotor 0blade passage shock structure at 8and 45%immersionsFig.6Axial distribution of blade surface isentropic Mach number near the hub for LM2500¿RotorFig.7LM2500¿Rotor 0bliskJournal of TurbomachineryJULY 2002,Vol.124Õ335one for each variable stator stage,are bolted along the length of the shaft.As the shaft turns,a turnbuckle bolted to each lug is pushed or pulled to rotate a multipiece,360-deg ring to which each stator vane lever arm is connected,opening or closing theVSV .The key benefit derived by using the torque tube is its added flexibility to schedule each stage with stator angle schedules that are nonlinear to each other.The variable stator schedule is controlled as a function of the compressor inlet corrected speed,with the second stage stator angle used as the reference.Stage characteristic data sets acquired from core engine tests of the CF6-80C2and the LM2500com-pressor were used to assemble a pitch line off-design model of the LM2500ϩcompressor with the new inlet guide vane and zero stage,and the mixture of airfoils from the CF6-80C2and LM2500.This model was used to develop a pretest stator schedule for the LM2500ϩ.The change in Stator 2angle ͑pretest ͒from the design nominal as a function of compressor corrected speed is shown in Fig.11.The change in the setting angles from design for the inlet guide vanes and Stators 0,1,and 3–6are shown in Fig.12as a function of the Stator 2‘‘master’’angle.While the linear relationship of Stators 0–6with Stator 2was retained from the CF6-80C2and the LM2500experience,the inlet guide vane relationship was highly nonlinear with respect to the ‘‘master’’statorangle.Fig.8Axial distribution of Stage 0vane surface isentropic MachnumberFig.9Axial distribution of blade surface isentropic Mach number for Rotor 1Table 5First stage blade key aerodynamic designparameters336ÕVol.124,JULY 2002Transactions of the ASMETest Compressor Instrumentation SummaryThe first engine with the LM2500ϩcompressor was tested as a gas generator with a conic nozzle at GE Aircraft Engines test facilities in Evendale with a dry low emissions ͑DLE ͒combustion system.The overall compressor performance was measured using four five-element combined inlet total pressure and total temperature rakes and three five-element rakes at the compressor discharge.Other performance measurements included the compressor speed and inlet flow,which was measured with a calibrated bellmouth with inlet rakes.All compressor bleed flows were measured using calibrated pipes.Interstage compressor instrumentation was extensive.Each stage in the compressor had leading edge total pressure and total temperature instrumentation.All the compressor airfoils were in-strumented with either flame-sprayed or thin film strain gages,and light probe instrumentation was included over Rotors 0and 1.Two vane stem-mounted potentiometers per stage were used on all variable stators to monitor stator position during the test.Trim-mer motors were provided for all variable stators to individually vary the stator settings for performance/aeromechanical optimiza-tion.Tip clearance measurements were obtained over the rotors in stages 0,1,2,6,11,and 16.All the compressor airfoils in the LM2500ϩthat were common to the base engine were from alease pool engine ͑which had about 700h run time ͒,including the rear compressor case.The measured average clearance to blade height,at design speed,varied between 0.7–1.%,except for stage 16which had significantly larger clearances ͑ϳ5%͒.The clear-ances on the new airfoils and on the airfoils from the lease pool engine were somewhat larger than one would expect in a new engine.Compressor Test Performance ResultsFigure 13͑a ͒shows the comparison of the measured and pre-dicted compressor operating lines with the pretest variable stator schedule.The distinct steps in the compressor operating line rep-resent the different stages of operation of the DLE combustion system,which uses compressor discharge bleed to control the combustion flame temperature.The compressor achieved the de-sign flow at the design speed,and the agreement between the calculated and measured flow at speed with the pretest variable stator schedule as shown in Fig.13͑b ͒was very good.The com-pressor achieved its peak polytropic efficiency,slightly over 91%,near its aerodynamic design point as shown in Fig.13͑c ͒.The test data shown in Fig.13͑c ͒is as measured,while the pretest predic-tion line includes an estimated 0.5points derate in target effi-ciency due to compressor instrumentation,hardware quality and clearances.The individual performance for the blisk and that of the down-stream compressor with the mixture of CF6-80C2and LM2500airfoils was separated in the following manner.The zero stage performance was determined by using data from the inlet rakes and the zero stage,vane-mounted probes.In spite of the large clearances and the significant amount of ruggedization in the tran-sonic Rotor 0,the IGV-Rotor 0combination achieved a peak poly-tropic efficiency of 90.5%,which was 2.8%better than design intent.The downstream compressor performance with the mixed airfoils,as determined by using the zero stage,vane-mounted probes and the exit rakes ͑and referred to as the ‘‘rear block’’in this paper ͒,also achieved the desired match point for the flow and efficiency goal relative to the baseline compressor.The measured radial profile of total pressure and temperature at Rotor 0exit was in good agreement with the three-dimensional calculations and the measured efficiency was slightly higher than the calculations near the tip.Aeromechanically,the first two new stages performed per de-sign intent over the entire operating range including vane off-schedule operation.However,among all the other compressor blades,strain gage signals on Rotors 2,3,and 4indicated higher than desired stresses between 83–90%design speed.A small vari-able stator schedule adjustment,using the trimmer motors on the variable stators,provided an acceptable solution to theaerome-Fig.10Comparison between the LM2500¿wide chord Rotor 1and the LM2500Rotor 1with the midspanshroudFig.11LM2500¿compressor statorscheduleFig.12LM2500¿compressor pretest variable stator gang relationJournal of TurbomachineryJULY 2002,Vol.124Õ337。