冰箱内胆吸塑成型
美菱冰箱制造流程
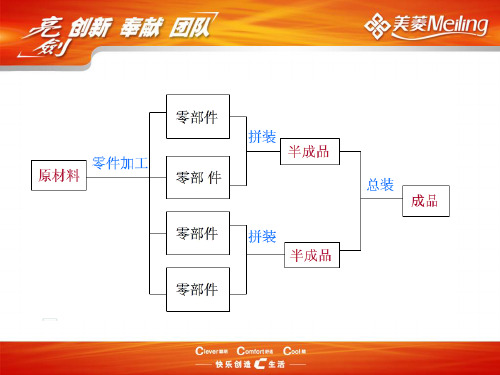
管路焊接
控制系统
装压缩机:注意压缩机型号和冰箱型号的统一。 装冷冻蒸发器:不同的冰箱结构,有不同的安装工序。 管路连接:配管,注意管路暴露空气不要超过15min、不要造成管路折 和管口变形。 焊接:铜、铝、钢管(见专项培训)。 控制系统连接:温控器、压缩机、灯、控制板等。 装门体:根据工艺布局而定 箱体零部件安装:根据箱体结构而定
2、吸塑成型
板材烘干——备料(ABS:丙烯晴、丁二烯和苯乙烯三元共聚塑料 、纳米 HIPS、高光HIPS、普通HIPS)——启动设备——预热——加热——吹泡/预 拉升——吸塑成型——剪板——冲孔 板材烘干 专用烘箱,温度在55-65℃,时间600min,自然冷却180-300min备用, 一般现场加工并马上用来吸塑的板材不需烘干。烘干主要指ABS,一般 HIPS不需烘干。因为它们的吸水率不一样,ABS为0.3%,HIPS为0.08%。 备料 检查板材规格、生产时间、牌号、生产厂家、HIPS电晕面 启动设备 调整夹钳、预设工艺参数
固化:190±5℃
4、热交换器成型: 冷凝器、蒸发器总成外协;防凝管自制。 冷凝器:钢管(镀铜、镀锌) 蒸发器总成:冷蒸使用铝管,冷冻使用钢管/铝管. 防凝管:铜管、钢管
5、门体/箱体预装 门体预装:冰箱的最大变化就在门体上,不同的结构会有不同的预 装流程。最基本的就是:预装 堵漏 预热 待发泡。 箱体预装:是以侧板组装为主流程的工艺路线 内衬准备 冷藏蒸发器安装 控制系统布置 待用 箱壳准备 贴冷凝管 箱壳堵漏 内衬和壳体组装 发泡
表面活性剂 特征 在发泡过程中,降低化学系统内的表面张力 在发泡过程中,稳定化学系统 控制泡孔的大小和形状 控制泡孔的闭孔率 影响泡沫的流动性 对泡沫的物理性能起重大的影响
崔化剂 特征 影响反应的速度及产生特殊的性能。 不同类型或不同量的催化剂可能产生不同的性能。 催化剂的用量可以影响: 反应速度 脱模性能 流动性 脆性
吸塑基础知识
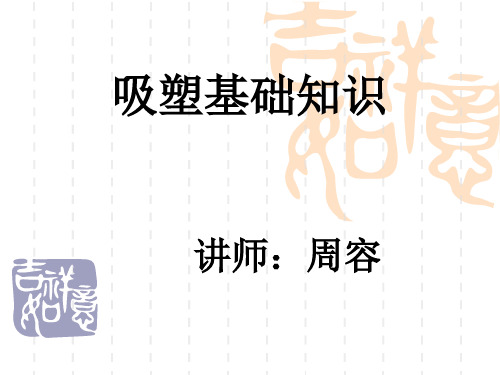
试样放入150℃的鼓风烘箱中,升温到(200+3) ℃,并在此条件下保持(30+1)min,开关电源, 在鼓风条件下降温到120℃,取出样品,于室温 放置1小时,测定尺寸变化率S;
公式中L。为原试样的长度,L为加热后试 样长度,为使试样测试时不受阻碍,试样 在烘箱中放置在约3mm厚的滑石粉托物上
PVC硬片韧性适中,不易燃烧,燃烧时会产 生氯气,对环境造成一定影响,PVC易热合,可 采用封口机和高频机封边,是生产透明吸塑制品 的主要原料。
PS硬片密度低,韧性差,易燃烧,燃烧时 会产生苯乙烯气体(属有害气体),所以一般用 来生产各种工业用的吸塑托盘。 PET硬片韧性好,透明度高,易燃烧,燃烧 时不产生有害气体,属于环保材料,但价格高, 适宜做高档的吸塑制品,欧美国家的吸塑泡壳一 般要求采用PET硬片,但其不易热合,给封装带 来很大困难,为了解决这一问题,人们在PET表 面复合上一层PVC膜,取名为PETG硬片,但价 格更高一些
三、吸塑制品的相关模具
1、石膏模、胶模
石膏模主要是采用黄色的吸塑手板石膏粉; 若提供图纸,则按图纸数据及要求,将石膏材料, 经铣床及手工完成模具制作;若提供实物,则先 将实物用手工泥完成模具之轮廓,真空成型成真 空罩,再复出石膏模具,并将该模具进行修改完 成;约需2-4天时间;石膏模具制作容易,时间 较短,有利于产品包装的修改,价格较低,但耐 用程度较低,经过一段时间使用后,较易损坏, 所生产之产品透明度较差;主要适用于首板确认 以及外包装透明度要求不高之产品。
吸塑裁切:吸塑成型后的塑料产品,经过冲床, 将大张的片材用刀模分切成单个产品。
吸塑折边:吸塑包装品中有一种叫插卡包装,需 要将泡壳的三个边用折边机折到背后,以便在下 一道封装工序中,将纸卡插入折边内,形成插卡 包装。
家用冰箱的基础知识及生产工艺流程
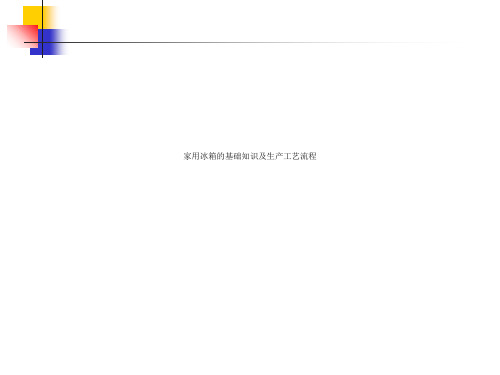
发泡前, 将门壳加 热 到 40℃ , 已防止门 体发泡时 缩泡、离 泡
工艺参数
1.原料温度 18-28 (℃)
2.灌注压力 10-13 (Mpa)
3.夹具、模具温度 40-50(℃)
异氰酸酯 聚醚、 环戊烷( R141B)
三、冰箱生产工艺2—门体成型
三、冰箱生产工艺3—钣金、喷涂
版仅取03标准下能效为前80%的产品,然后划分5个等级来销售。即,淘汰能效靠后20%的低能效产品。
三\冰箱生产工艺流程
国内冰箱生产线几乎都是引进欧洲的冰箱生产工艺, 产品的结构为拼装式结构,冰箱生产工艺主要有以下 几个流程:
一、胆成型(吸塑) 二、门体成型 三、钣金、喷涂 四、前预装生产工艺 五、箱体发泡 六、后预装生产工艺 七、总装生产工艺 八、包装生产工艺
➢ 总装采用自动传动链板生产线,自动化程度较高,可实现多种规格的产品混 合生产(柔性生产技术)。
➢ 制冷系统管路和压缩机连接、焊接后进行多次检漏: 第一次检漏:在充注制冷剂之前对内外部焊点进行氦介质检漏,氦介质检漏 精度高, 可检查出制冷系统中的任何微小漏点。 第二次检漏:在抽真空、充制冷剂之后,对外部焊点进行第二次检漏,检测 精度高于国家标准。 第三次检漏:包装前再进行第三次检漏,所用仪器与第二次检漏相同。 通过制冷系统的三次检漏,使出厂的产品质量有可靠的保证。 冰箱的防漏一直是冰箱质量最关键的环节,假如防漏不合格,冰箱制冷、 节电性能将受严重影响。
德国多工质 检漏仪对各 管路焊点进 行检漏 R600a泄露值
≥0.5克/年,检 漏仪报警
三、冰箱生产工艺7—总装
制冷性能检 测,机械温控 冰箱检测时间 90分钟,电脑 冰箱检测240 分钟
厚板吸塑工艺及应用说明(1)
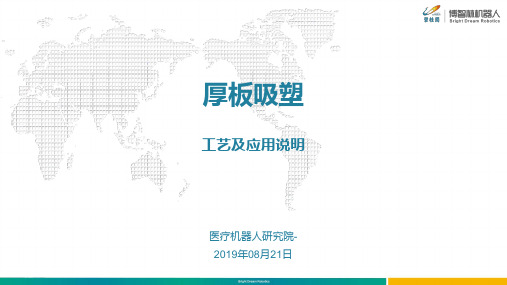
一.通过模具的分析,我们可以清楚明白产品的成型过程,在这个过程中,要出现一定的拔模角度(3度),表面要一定的圆角(R>3.5),侧面可 以出现一定的行位、碰穿. 装配位(boss柱、卡扣)不适合,怎么样实现装配位:1:转接件粘接;2:转接件锁螺丝,精度不是很好,需做定位 治具,对于精度特别高的,无法实现,一般大部分的反插骨可以通过这种方法去实现 二:这种产品的实现有点类似于钣金的冲压和拉伸(缺少加热系统),拉伸的过程相当于吸塑加热的过程;跟碳纤维的热压工艺也类似
02 概念及应用
薄板吸塑跟厚板吸塑的原理
厚片吸塑机是以塑料板材为原料、通过真空吸塑成型工艺制取吸塑成型塑料件的关键工艺设备,它以热 塑性塑料片材为原料,通过烘箱加热至软化温度,再通过塑料板材与吸塑成型模具之间的真空负压作用, 使处于热塑性状态的塑料板材吸附在吸塑成型模具工作面上再冷却成型。
厚片吸塑机一般由板材定位系统、吸塑模具定位系统、框架系统、加热系统、冷却系统以及电气控制系统组成。 (1)板材定位系统一般由井字型材压料框、动力气缸或油缸以及平衡同步机构组成。其作用对塑料板材起到 加紧定位。走架式加热方式的压料框为上下结构,并加有横向锁紧机构,确保压料框能与板材垫板靠紧密封。 框架可根据模具大小做对应调整,分手动和自动调整; (2)吸塑模具定位系统一般由上下模台、上下模气缸或油缸以及同步机构组成。其作用是对吸塑模具起到加 紧定位,并对模具与真空管道连接。定位方式手动螺丝锁紧或气动自动锁紧两种方式。同步机构能确保上下模 同步升降,确保吸塑成型精度 (3)框架系统一般由型材机架,密封箱,防护门组成。防护门由自动和手动之分; (4)加热系统一般由加热砖或加热管、烘箱架体以及动力气缸或电机组成; (5)冷却系统一般由气、水管道以及喷雾头组成; (6)电气系统 电气控制系统与气压或液压系统理配合,可实现吸塑机的工艺过程要求(温度、速度、时间) 和各种程序动作。主要由PLC及触摸屏、接触器、电子元器件、调温仪表、电磁阀、传感器等组成。一般有三 种控制方式,手动、自动、调整。、
冰箱内胆成型工艺与模具设计_陈义兵

6 结束语 该设计最大的特点是在同一斜导柱驱动下,实
现相互垂直的 2 个方向的抽芯动作,并且结构紧凑, 动作可靠。同时,该结构设计不仅局限于具有上述 特殊结构塑件的成型,对于其他需要不同方向抽芯 的塑件也同样适用。
成型区域板料的体积与吸塑成型后的塑件体 积应相同,按照体积不变的原则和经验确定内胆吸 塑成型后各区域的大致壁厚,各区域壁厚设计值如
图 4 所示。 为使型腔主体设计达到图 4 所示各区域壁厚的
要求,应用三维软件进行设计,首先复制出内胆内 表面的 3D 数据,将复制出的面偏置 0.7 mm,对复制 出的各侧面进行旋转变换处理,靠近内胆底部壁厚 设置为 0.7 mm,靠近内胆口部壁厚设置为 1.6 mm, 在三维软件中将各区域面进行编辑、连接和缝合, 生成型腔主体的 3D 实体。
辅模采用干燥的实木拼块制作,拼装后上数控 机床整体加工型面,表面粘贴白色棉布,棉布粘贴 时应平整、光滑,接缝平齐,保证辅模在对板料拉伸 过程中塑件表面不产生痕迹。
图 10 辅模 3D 模型
4 模具工作过程 模具结构如图 11 所示。模具工作过程:板材由
夹料装置夹紧移动至下模上方,真空吸塑设备辐射 加热器移动至板材上方加热,板材软化后,辐射加 热器移出,下模向上移动到位,辅模向下移动到位, 设备开始抽真空,板材在大气压强作用下与下模型 腔主体贴合成型,吸塑完成后,设备开始消真空、吹 气脱模,此时下模向下运动,程序控制抽芯脱模机 构动作,下模继续下行,与塑件逐步脱离、分开,下 模下行到位后,程序控制抽芯机构复位,取出制件, 完成一个成型周期。
斜滑块材料选用 A5052,将斜滑块设计小一些, 可以减少斜滑块在脱模时对冰箱内胆的的重力作 用,防止脱模时冰箱内胆倒扣处产生变形。
吸塑知识培训资料

走访有关工艺技术人员和生产人员, 了解设备实际使用情况、操作人员技术水平、 最常出现的与模具有关的成型质量问题等, 为模具设计准备更充分的第一手资料。 2.2、制定成型工艺。
通常由成型工艺人员根据制品成型要求制定成型工艺, 并提出模具设计任务 书, 由模具设计人员进行模具设计, 但有时工厂往往会将这两项工作合并起来做, 也就是说, 模具设计人员在进行模具设计之前, 还应制定合理的成型工艺, 为后面 的模具设计打下基础。此时, 应结合节中提出的问题进行综合考虑。 2.3、熟悉成型设备技术规范:
吸塑件工艺性简介
4、拉深比的确定: 拉深比是指箱胆成型后总表面积比上参与成型的板材表面之和,通常情况
下,此值在3-3.5范围内,成型后产品厚薄差异不会太大,有利于保证产品质 量。我公司内胆深度最大620mm(吸塑机极限尺寸)。
5、胆口部设计成喇叭口状. 箱胆口部圆角不可能做得很大, 一般为R4-R6,小于R4胆口易开裂。如果
如果成型工艺控制不严, 或者模具结构不合理, 冰箱内胆容易造成制品轮廓 不清晰。为了顺利脱模, 往往需要设置抽芯机构, 使模具设计制造复杂化。另外, 为提高薄壁强度而设置的加强筋会使模具结构更复杂、成型困难。 (3) 内胆深, 成型拉伸比大.
成型拉伸比大易造成制品壁厚不均匀、内应力大, 制品的某些部位很容易 被拉破。这就要求从选材、成型工艺制定到模具设计都要充分考虑这一因素, 并采取相应措施。比如, 工艺上采取吹泡预拉伸, 模具设计上采取加大圆角半径、 合理设计抽气孔等。 四、冰箱内胆真空成型模具设计方法.
②成型体的表面粗糙度对塑料件质量和脱模有很大影响。因真空成型模具一般
冰箱制造加工工艺流程简介
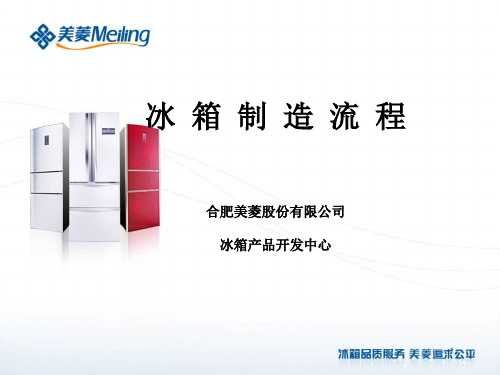
3、箱体:分拼装式、整体式。
绝热材料 电冰箱发展至今,其绝热材料经历了木屑、硅藻土、超细玻璃
棉、聚苯乙烯泡沫,直至现在的硬质聚氨脂泡沫,其导热系数越低,绝 热性越来越好,使电冰箱绝热层越来越薄。
聚氨脂泡沫:多异氰酸脂、多元醇、崔化剂、稳定剂、发泡剂等。 聚氨脂泡沫老化情况:
美菱公司冰箱制造工艺流程
一、冰箱知识简介
1、电冰箱定义
家用冰箱,不管是单门还是双门,不管是直冷还是间冷,不管是 普通CFC还是无CFC环保冰箱,虽然其外形多样,千差万别,但主要结 构大致相同,即家用电冰箱一般均由以下四部份组成: 箱体(包括门体) 制冷系统 电气系统 附件
2、家用电冰箱的分类
1)按门体分类 单门:一个门、冷藏室(0℃-8℃)、冷冻(-6℃— -12 ℃),可冷冻食品
及制冰。 双门:其冷冻室和冷藏室各有一个门,冷冻室< -18℃,具有速冻功能。
冷藏室:0-10 ℃ 三门:冷冻、冷藏、果菜盒(8-14 ℃ )、冰温室(-2-3 ℃)或变温
室。 四门:各温度度点下的保质、保鲜室 五门:各温度度点下的保质、保鲜室
4、制冷系统
5)干燥过滤器
分为两种:单孔进口、双孔进口 铜制壳体两端设置过滤网(80-120目的金属网)。
4、制冷系统
电冰条用的过滤器器都采用球状分子筛作为干燥剂,根据所用工质的不 同选用不同的分子筛吸附口么径。
小
分子大小
大
XH-9(3A)
XH-7
XH-5(4A)
选择的原则:比水分子直径大,比制冷剂分子直径小
开始 0.018 W/m.K
一个星期 0.025 W/m.Kຫໍສະໝຸດ 一个月 0.025 W/m.K
冰箱内胆生产工艺

冰箱内胆生产工艺冰箱内胆是冰箱的重要组成部分,其质量直接关系到冰箱的性能和使用寿命。
下面介绍冰箱内胆的生产工艺。
首先,冰箱内胆的材料主要有塑料和不锈钢两种。
其中,塑料内胆主要采用注塑工艺生产,而不锈钢内胆主要采用冲压和焊接工艺生产。
塑料内胆的生产工艺如下:1. 原料准备:选择合适的塑料材料,经过混合、熔化和造粒处理,制成塑料颗粒。
2. 注塑成型:将塑料颗粒放入注塑机的进料口,经过加热和高压注射,将熔化的塑料注入内模具中,冷却固化后得到塑料内胆。
3. 配件加工:根据冰箱的功能和设计要求,对塑料内胆进行钻孔、切割和加工,制作出各种配件,如风道和隔板等。
4. 组装与安装:将塑料内胆和配件进行组装,安装到冰箱的外壳上,形成完整的冰箱内胆。
5. 检测与质量控制:对成品进行检测,包括尺寸、外观和性能等方面的检测,确保内胆的质量符合标准要求。
不锈钢内胆的生产工艺如下:1. 材料准备:选择合适的不锈钢板材,经过切割和冲压,制成内胆的各个零部件。
2. 焊接:将切割好的不锈钢零部件进行焊接,通过氩弧焊接或者激光焊接等工艺,将内胆的各个部分焊接到一起。
3. 表面处理:对焊接好的内胆进行表面处理,主要包括抛光、喷漆和电镀等,提高内胆的表面质量和耐腐蚀性。
4. 组装与安装:将焊接和处理好的不锈钢内胆进行组装,安装到冰箱的外壳上,形成完整的冰箱内胆。
5. 检测与质量控制:对成品进行检测,包括尺寸、外观和性能等方面的检测,确保内胆的质量符合标准要求。
总之,冰箱内胆的生产工艺主要包括材料准备、成型加工、配件制作、组装安装和质量控制等环节。
通过科学的生产工艺和严格的质量控制,可以制造出质量优良的冰箱内胆,提高冰箱的性能和使用寿命。
- 1、下载文档前请自行甄别文档内容的完整性,平台不提供额外的编辑、内容补充、找答案等附加服务。
- 2、"仅部分预览"的文档,不可在线预览部分如存在完整性等问题,可反馈申请退款(可完整预览的文档不适用该条件!)。
- 3、如文档侵犯您的权益,请联系客服反馈,我们会尽快为您处理(人工客服工作时间:9:00-18:30)。
冰箱内胆吸塑成型
一、塑料成型加工:
一次成型能得到现状相对复杂的精密制件,但不适合大型、薄壁制件
二次成型,如吸塑是是将将加热软化后的塑料制件如板制成大型薄壁,形状
复杂但相对精度要求较低的胆壳类塑料制件,二次成型包括吸塑、吹塑、固相
成型等
冰箱内胆吸塑成型模是真空吸塑成型模的一种。
首先,利用夹紧装置对热塑性塑料板或者塑料片进行固定,用辐射加热的方法对其进行加热,当加热至塑料软化温度后,利用压缩空气对塑料板中心位置进行吹气,使之形成真空气泡,将该真空气泡覆盖在凸模上(或者在凹模内),用真空泵抽真空的方法将塑料板与模具之间的空气抽空,借助塑料板上下面之间的压差,使塑料板紧贴在模具表面而成型,经过保压冷却等步骤,最终,凭借吹入的压缩空气以及吸塑模模具中的脱模装置,将冰箱内胆制件从模具中脱落。
二、吸塑产品的主要缺陷
(1)制件表面有起泡点:主要原因是片材受潮,需在100度温度下对片材
加热约5h;
(2)制件厚薄不均:主要原因是加热温度不均匀或起泡不够,片材局部拉
伸太大;
(3)制件成型不良:a)真空度不够,片材与模具间未密封存在漏气,片材
不能很好贴在模具上;b)模具设计问题,如结构不合理,尤其是死角部位
真空孔堵塞或者数量不够或者孔径太小;
(4)制件局部起皱:主要在制件的死角部位,原因可能是该部位模具温度
过低;
(5)制件局部起筋条:主要在台阶部位,原因可能是吹泡太高,或该部位
加热温度过高,可选用辅助压料框将筋条部位进行预先定位,避免吹泡过大。
(6)局部翘曲变形
A: 模温过高
B: 脱模力过大
冰箱吸塑模工艺设计中的关键部位:
型腔部位、抽真空部位、抽芯部位以及加热冷却部位
三、吸塑成型主要考虑因素
1.宽深比与引伸比
2. 板料厚度、
3. 圆角半径、
2.起泡时间 5. 成型方法、 6. 成型速度
四.板材与模具加热温度选择原则
分为单面加热与双面加热。
当板片材厚度小于2mm时常采用单面加热,加热器应放置于片材下方。
大于2mm时则应采用双面同时加热。
采用单面加热时,;采用双面加热时,下方加热器的温度应低于上方加热器的温度,且应为上方加热功率的0.5~0.8。
加热距离通常取80~120mm。
五、起泡时间
在整个真空吸塑成型的过程中,起泡时间的长短是成型的关键
起泡时间短会导致制件厚度局部变薄不均匀,
但是,当起泡过长,就会出现局部折皱和折叠
根据具体制品的设计结构,考虑宽深比与引伸比选取合适的起泡时间参数
六、内胆圆角设计
冰箱内胆制件的圆角设计时,不允许出现锐角,且圆角处的圆弧R要尽可
能大,至少要大于片材厚度的5~10倍;否则制件在圆角处很容易发生减薄和应力集中现象
七、宽深比与引伸比
内胆制件的宽深比是指制件有效的最小宽度与制件高度之比,宽深比是衡量内胆制件成型难度的一个常用参数
宽深比越大,制件成型越易,反之越困难
内胆制件的引伸比是指拉伸后制件表面积与拉伸前片材有效面积之比,引伸比是衡量制件拉伸过程中的实际变形程度,即引伸比越大,变形程度越大,成型就越困难,反之就越容易,引伸比一般采用0.5~0.85
当引伸比和制件平均壁厚确定后,计算板材原始厚度厚度
To(板材厚)=Ls(引伸比)×Tp(平均厚度)
八、成型方法:
吸塑成型方法主要有
A、无模吸塑成型、
B、单凹模吸塑成型、
C、单凸模吸塑成型、
D、对模吸塑成型、
E、预吹吸塑成型、
F、模塞辅助吸塑成型、
G、预吹模塞辅助吸塑成型、
H、真空回吸成型等多种方法、
冰箱吸塑常用的有预吹模塞辅助吸塑成型和真空回吸成型两种。
九、成型速度
成型速度与模具抽真空速度相关
一般来说,成型温度越高,采用成型速度的越快;
但对于大尺寸制品,尤其是冰箱内胆制件,应采用慢速成型。
具体的成型速度需根据实际生产时的制件大小、尺寸厚薄、模具温度以及
成型质量等情况具体而定。
十、辅助模塞圆角
辅助模塞的材料必须满足以下要求:
(1)接触时不能使热片材过于变冷:
(2)运动时与片材之间具备良好的滑动及摩擦行为;
(3)成本合理易加工且具备一定的热性能要求
木质材料是多数设计者优先选用的辅助模塞材料。
木质辅助模塞具有良好的滑动性能,不会因为摩擦而给内胆留下划痕,
在木质辅助模塞表面覆上软质的纺织品,可以有效减少接触时的冷却性能和增加滑动性能。