吸塑工艺流程图
吸塑行业生产计划流程表

吸塑行业生产计划流程表吸塑产品生产工艺一、吸塑产品生产工艺流程图片材原材料->吸塑成型->半成品检验->包装冲切->成品检验->入库二、吸塑原材料简介吸塑原料的识别 1、看环保标识的方法:2. 密度和强度法:以液体为介质,检验其塑料在液体介质中的沉浮,以粗略辨别塑料的大类,如一块塑料放在水中,浮在水面可断定,原料不是PVC(因PVC的密度>1),折压片材手感其强度。
各片材密度和强度如下表:铜模制作流程铝模制作流程吸塑生产工艺流程一、吸塑模具选择吸塑模具一般有石膏模、电镀铜模和铝模三种石膏模:用石膏在半湿的状态下雕刻成型,然后烘干即成模具,石膏模成本低,易于修改,但石膏模精度不够高,表面不光滑而且易碎不耐用,因此它常用来打佯、做电镀铜模的模种或一些要求不高小批量生产的吸塑模具。
铝模:用铝锭通过机械(车床、铣床、C等)加工而成。
铝模精度高、表面光滑而且经久耐用,但价格非常贵,铝模一般用在精度要求较高铜模达不到的吸塑产品上。
电镀铜模:用石膏模种制成样品后,电镀一层铜壳即为电镀铜模,成本相对石膏模高,但比铝模便宜得多,因其表面光洁耐用、低成本的优点,电镀铜模是最常用的一种吸塑模具。
二、吸塑材料的选择吸塑产品的原材料只有塑胶片材,胶片厚度一般不超过1.5MM,常用的片材有:PVC、PET、PP、PS以及在此基础上的植绒片材、镀金片材和防静电片材。
PVC:最常用的吸塑材料,质软、韧性强、可塑性好,可做成透明和各种颜色,常用透明PVC包装电子、化装品、玩具礼品等产品。
PET(A-PET):质硬,韧性好、强度高、表面光亮、环保无毒,有透明和多种颜色的片材。
缺点是PET高周波热合比较困难,价格也比PVC贵很多,此材料常被要求产品高档和环保的用户取代PVC PS:密度小(质轻)、环保无毒,可塑性非常好,韧性差易脆,不可做成通明材料,因此只能做成底托类吸塑,因其易裂,此类吸塑不宜回收PP:材质特别软,韧性好,环保无毒、耐高温,常被做成餐饮器具或其他耐高温产品的包装;但其可塑性差,加工难度大,表面光泽度差,而且加工时颜色会变浅。
吸塑工艺流程图

吸塑工艺流程图标准化文件发布号:(9312-EUATWW-MWUB-WUNN-INNUL-DQQTY-吸塑生产工艺流程吸塑生产过程可包括:一.客户询价;二.业务部门报价;三.吸塑模具电脑辅助设计;四.泡壳模具的开发和打样;五.制作泡壳的生产模具;六.吸塑成型生产;七.冲床裁切;八.分检包装;一、客户发出询价请求:途径一打电话询价,途径二发传真询价,途径三发Email询价,途径四通过网络聊天工具询价。
客户必须提供吸塑制品的长、宽、高和所用材料的厚度、颜色和型号(PVC、PET、PS),产品数量和生产周期。
二、业务部门报价:吸塑制品单价的高低跟以下因素有关:吸塑制品的长、宽、高和吸塑成型的复杂程度;所用材料的类型、厚度和颜色;吸塑产品的后道加工工艺(折边、打孔、封边等)、订单数量和订单周期。
报价员会以客户的样品和描述有一个最初报价,最终报价会在打样之后报出。
三、吸塑模具的电脑辅助设计:客户对于报价基本认可后,会将要求、实物或是吸塑样品交到业务部,生产调度会要求电脑设计部将客户的实物扫描并结合印刷品的设计,制作出吸塑制品的平面设计图四、泡壳模具的开发和打样:客户认可电脑设计稿后,生产调度会根据吸塑产品的复杂程度决定采用哪种方式开发模具(石膏模、铜模、铝模),开发周期3-5天。
吸塑打样以石膏模打样居多,其操作步骤是:1.先将实物用手工泥糊出成型轮廓;2.放到吸塑打版机上成型泡壳毛胚;3.用配好的吸塑专用石膏倒入泡壳毛胚中,风干后形成石膏毛胚;4.采用电动铣床对石膏毛胚和规则形状进行深加工;5.手工打磨和手工添加部件;6.将各个抛光好的石膏部件粘合成完整的石膏模;7.再放入吸塑打版机吸塑成型完整的样品;8.按成品尺寸,手工切边、封边,完成全部打样过程。
如果有需求,印刷打样部门同时会将吸塑样品所用的纸卡、不干胶或彩盒一起制作,他们会借助全开的印刷数码打样机能将实际印刷结果反映出来,由深正电业伺服丝杆吸塑机阙龙宇提供,微信号:9。
吸塑的生产工艺(详细版)

吸塑产品生产工艺
一、吸塑产品生产工艺流程图
片材原材料->吸塑成型->半成品检验->包装冲切->成品检验->入库
二、吸塑原材料简介
原材料特性说明
材质
成型温度
冷却时间
热扭曲温度性质优点缺点用途
聚氯乙烯
PVC 65-75℃
24-30s
80℃
密度和强度法:以液体为介质,检验其塑料在液体介质中的沉浮,以粗略辨别塑料的大类,如一块塑料放在水中,浮在水面可断定,原料不是PVC(因PVC的密度>1),折压片材手感其强度。
各片材密度和强度如下表:
通称密度强度常用厚度
PS约20Mpa
约24Mpa
约54Mpa
约57Mpa
约57Mpa
约57Mpa
注聚合物是:还已烷二甲醇+对苯二甲酸+乙二醇的聚合体.
三、吸塑模具制作简介
依图纸石膏模制作流程
依实物石膏模制作流程铜模制作流程
铝模制作流程
四、吸塑成型简介
成型四大要素
吸塑成型工艺流程
进料->加热(300±250C)->塑化->真空吸附->保压->冷却->吹底风->脫模->刀闸裁断->頂出->刀模冲裁
成型工艺图(香港电业吸塑机)
五、裁切包装简介
裁切工艺图(华士裁切机)
六、未来发展目标无尘车间
树脂模采用树脂模的主要目的:较大程度的减少表面水纹
全自动吸塑成型裁切机。
吸塑生产工艺介绍

从材料,模具,吸塑,冲压各环节认识吸塑产品的全过程2021年6月目录CONTENTS01吸塑流程图02常用材料的认识03模具的介绍04吸塑成型介绍05裁切包装吸塑流程图打样流程图量产流程图吸塑工艺流程图与实物试装产品图纸/实物制作/修改石膏模石膏模材料吸塑打样冲压裁切不合格合格铜模/铝模量产1成品检验包装冲切半成品检验吸塑工艺流程图吸塑成型入库吸塑原材料2材料的认识材料种类材料的判认材料特性12345聚对苯二甲酸乙二醇酯Polyethylene terephthalate PET聚苯乙烯PolystyrenePS聚丙烯polypropylenePP聚对苯二甲酸乙二醇酯PETG聚氯乙烯Polyvinyl chloridePVC吸塑常用材料透明度高,不易破边,属环保材料,可周转使用。
优点高度结晶的聚合物,表面平滑有光泽。
耐疲劳性,耐摩擦性,尺寸稳定性好。
性质成型温度:70-80℃ 冷却时间:14-20s 熔化温度:120℃开始溶化温度要求吸塑常用材料易破碎,根据温度不同会有发白现象存在,有同厂家颜色有差异。
缺点用于包装电子、五金、玩具、食品、化妆品、学习用品等。
用途吸塑常用材料2.PS的认识透明度高,不易破边,属环保材料,可周转使用。
优点拉伸强度可达60Mpa 以上,冲击强度小,耐磨性差,力学性随温度升高而变大,收缩率为0.4-0.7%。
性质成型温度:75-85℃ 冷却时间:14-20s 熔化温度:95-150℃开始溶化温度要求易破边,周使用率底,不同厂家生产的颜色有差异。
缺点用于包装电子、五金、玩具、食品、化妆品、学习用品等。
用途吸塑常用材料刚硬有韧性、抗弯强度高、抗疲劳、抗应力开裂;质轻;在100-150℃仍能保持力学性。
优点半结晶性材料,比PE要更坚硬且有更高的熔点。
由于结晶度较高,表面的刚度和抗划痕特性很好。
收缩率为1.8-2.5%。
性质成型温度:140℃以上冷却时间:24-30s溶化温度:150-220℃开始熔化温度要求0℃以下变脆;耐侯性高。
吸塑生产的工艺流程

吸塑的工艺流程
热成型工艺流程图解
大致流程:塑料片材——切割——片材固定——加热——成型——脱模——裁切——成品
【吸塑成型对材料有哪些要求?】:
1.吸塑成型只能生产壁厚比较均匀的产品,(一般倒角处稍薄),不能生产壁厚相差悬殊的塑料制品
2.吸塑成型的壁厚一般在1到2mm范围之内或更加薄(小包装用吸塑包装的片材最常用的厚度为0.15到0.25mm)
3.吸塑成型制品的拉伸度受到一定的限制,吸塑成型的塑料容器直径深度比一般不超过1,极端情况下亦不得超过1.5
4.吸塑成型的尺寸精度差,其相对误差一般在百分之一以上,百分之三以下。
5.吸塑成型后的裁切成型的时候对于裁切人员的要求是:
1)裁切人员要能够准确的找到对应产品的刀模。
2)裁切人员要了解产品的裁切要求。
3)裁切中会碰到炸边的情况怎样去处理。
6.包装
1)包装人员要如何区分不良品
2)不良品的放置区域
3)包装数量填写。
吸塑模具制作流程TRAY课件
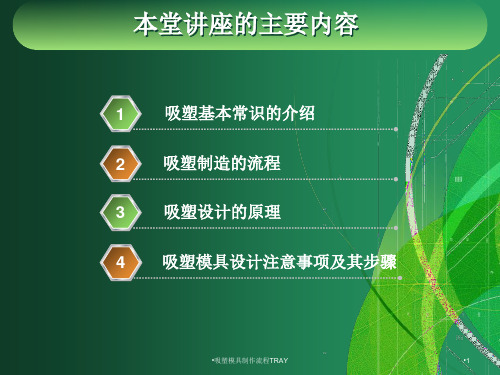
补充说明
当模具制作完成后,如需设变,需按设变原则: 1)如果穴位设变加大,在模具空间足够的情况下,可以在原模上加工. 2)如果穴位需要设变改小,原模报废,需重新开模.
二:植绒吸塑盘 是一种采用特殊材料的吸塑托盘,将普通的塑料硬片表面粘上一层绒质材料,从而使托盘表面有种绒质的手感,用来提高包装品档次。
三:抗静电吸塑盘 是一采用特殊材料的吸塑托盘,该材料表面的电阻值小于10的11次方欧姆。主要用于电子、IT产品的吸塑托盘。
吸塑盘的展示
双泡罩吸塑盒 工艺品植绒托 医疗器械包装
8
脱模斜度
脱模斜度一般为5°,零件高的为7°,要求晃动小的为3°。
9
排版
穴位形状的大小、高低、凹凸。一般情況下是根據零件的形狀來排的,這樣能保證零件在吸塑盤中的定位性,能保證共用性。
10时)。
吸塑模具设计注意事项
部分產品需要倒扣,即是上下、裏外需緊密扣牢。具體依客戶要求設計。因為有的扣是圓的,有的倒扣是方的,還有的倒扣是不規則的。
不论是铝模还是铜模,一旦模具完成,生产过程中不用担心尺寸会有变动,因为吸塑模是单模,稳定性比较好!
吸塑模具製作主要過程
設計
加工
打孔拋光
吸塑模具设计步骤
序号
步骤
要 求
1
确定材料
依客户要求、零件的大小、難易複雜程度、共用狀況、零件自身的品質要求确定用何种材料。
2
确定尺寸
依客户要求、依零件尺寸确定TRAY的外形和穴位的长、宽、高。
化妆品包装 电子类吸塑包装 手机托包装
医药托盘 纸卡塑料盒 mp3透明折边包装盒
吸塑盘的打樣流程
业务接单
吸塑的工艺流程

吸塑的工艺流程
首先呢,得准备好材料。
这材料可不能马虎,要根据你最终想要的吸塑产品的样子和用途来选哦。
我觉得这就像是盖房子打地基,材料选不好,后面可就麻烦啦。
接下来就是制作模具啦。
这个模具呀,它可是关键的一环呢!你可以根据设计的形状和尺寸来做。
这模具制作有时候挺考验耐心的,要是能找到有经验的师傅来做,那效果肯定好很多。
当然啦,如果你自己有这方面的经验和能力,自己做也完全可以呀。
然后呢,就到了加热片材这个步骤。
这一步要特别注意!温度得合适,不能太高也不能太低。
要是温度太高了,片材可能就被烤坏啦;温度太低呢,又达不到吸塑的效果。
我一般会先试一小块片材,看看这个温度是不是合适,这可是我的小经验哦。
再之后呀,就是把加热好的片材放到模具上,然后通过真空或者气压的作用,让片材紧紧地贴合在模具上。
这一步看起来简单,但实际操作的时候可能会遇到一些小问题呢。
比如说,片材和模具之间可能会有一些小气泡。
这时候怎么办呢?别慌,可以稍微调整一下气压或者位置。
在这个过程中,还有一个很重要的事情,就是冷却啦。
冷却的速度也会影响吸塑产品的质量哦。
不过这个环节可以根据实际情况自行决定,毕竟不同的材料和模具可能需要不同的冷却方式。
最后呢,就是把成型的吸塑产品从模具上取下来啦。
小提示:别忘了最后一步哦!刚开始可能会觉得整个吸塑工艺流程有点复杂,但习惯了就好了。
而且呀,在这个过程中你可以不断地尝试和调整,找到最适合自己的方法呢。
吸塑行业生产计划流程表

吸塑行业生产计划流程表吸塑行业生产计划流程表吸塑产品生产工艺一、吸塑产品生产工艺流程图片材原材料->吸塑成型->半成品检验->包装冲切->成品检验->入库二、吸塑原材料简介吸塑原料的识别 1、看环保标识的方法:2. 密度和强度法:以液体为介质,检验其塑料在液体介质中的沉浮,以粗略辨别塑料的大类,如一块塑料放在水中,浮在水面可断定,原料不是PVC(因PVC的密度>1),折压片材手感其强度。
各片材密度和强度如下表:铜模制作流程铝模制作流程吸塑生产工艺流程一、吸塑模具选择吸塑模具一般有石膏模、电镀铜模和铝模三种石膏模:用石膏在半湿的状态下雕刻成型,然后烘干即成模具,石膏模成本低,易于修改,但石膏模精度不够高,表面不光滑而且易碎不耐用,因此它常用来打佯、做电镀铜模的模种或一些要求不高小批量生产的吸塑模具。
铝模:用铝锭通过机械(车床、铣床、C等)加工而成。
铝模精度高、表面光滑而且经久耐用,但价格非常贵,铝模一般用在精度要求较高铜模达不到的吸塑产品上。
电镀铜模:用石膏模种制成样品后,电镀一层铜壳即为电镀铜模,成本相对石膏模高,但比铝模便宜得多,因其表面光洁耐用、低成本的优点,电镀铜模是最常用的一种吸塑模具。
二、吸塑材料的选择吸塑产品的原材料只有塑胶片材,胶片厚度一般不超过1.5MM,常用的片材有:PVC、PET、PP、PS以及在此基础上的植绒片材、镀金片材和防静电片材。
PVC:最常用的吸塑材料,质软、韧性强、可塑性好,可做成透明和各种颜色,常用透明PVC包装电子、化装品、玩具礼品等产品。
PET(A-PET):质硬,韧性好、强度高、表面光亮、环保无毒,有透明和多种颜色的片材。
缺点是PET高周波热合比较困难,价格也比PVC贵很多,此材料常被要求产品高档和环保的用户取代PVC PS:密度小(质轻)、环保无毒,可塑性非常好,韧性差易脆,不可做成通明材料,因此只能做成底托类吸塑,因其易裂,此类吸塑不宜回收PP:材质特别软,韧性好,环保无毒、耐高温,常被做成餐饮器具或其他耐高温产品的包装;但其可塑性差,加工难度大,表面光泽度差,而且加工时颜色会变浅。
- 1、下载文档前请自行甄别文档内容的完整性,平台不提供额外的编辑、内容补充、找答案等附加服务。
- 2、"仅部分预览"的文档,不可在线预览部分如存在完整性等问题,可反馈申请退款(可完整预览的文档不适用该条件!)。
- 3、如文档侵犯您的权益,请联系客服反馈,我们会尽快为您处理(人工客服工作时间:9:00-18:30)。
吸塑生产工艺流程吸塑生产过程可包括:
一.客户询价;
二.业务部门报价;
三.吸塑模具电脑辅助设计;
四.泡壳模具的开发和打样;
五.制作泡壳的生产模具;
六.吸塑成型生产;
七.冲床裁切;
八.分检包装;
一、客户发出询价请求:途径一打电话询价,途径二发传真询价,途径三发Email询价,途径四通过网络聊天工具询价。
客户必须提供吸塑制品的长、宽、高和所用材料的厚度、颜色和型号(PVC、PET、PS),产品数量和生产周期。
二、业务部门报价:吸塑制品单价的高低跟以下因素有关:吸塑制品的长、宽、高和吸塑成型的复杂程度;所用材料的类型、厚度和颜色;吸塑产品的后道加工工艺(折边、打孔、封边等)、订单数量和订单周期。
报价员会以客户的样品和描述有一个最初报价,最终报价会在打样之后报出。
三、吸塑模具的电脑辅助设计:客户对于报价基本认可后,会将要求、实物或是吸塑样品交到业务部,生产调度会要求电脑设计部将客户的实物扫描并结合印刷品的设计,制作出吸塑制品的平面设计图
四、泡壳模具的开发和打样:客户认可电脑设计稿后,生产调度会根据吸塑产品的复杂程度决定采用哪种方式开发模具(石膏模、铜模、铝模),开发周期3-5天。
吸塑打样以石膏模打样居多,其操作步骤是:1.先将实物用手工泥糊出成型轮廓;2.放到吸塑打版机上成型泡壳毛胚;3.用配好的吸塑专用石膏倒入泡壳毛胚中,风干后形成石膏毛胚;4.采用电动铣床对石膏毛胚和规则形状进行深加工;5.手工打磨和手工添加部件;6.将各个抛光好的石膏部件粘合成完整的石膏模;7.再放入吸塑打版机吸塑成型完整的样品;8.按成品尺寸,手工切边、封边,完成全部打样过程。
如果有需求,印刷打样部门同时会将吸塑样品所用的纸卡、不干胶或彩盒一起制作,他们会借助全开的印刷数码打样机能将实际印刷结果反映出来,由深正电业伺服丝杆吸塑机阙龙宇提供,微信号:412152899。
五、制作生产模具:样品被客户认可后,通常会下一定数量的生产订单。
生产调度会根据产量、吸塑成型的复杂程度决定采用哪种模具量产:采用石膏模生产,模具制作过程类似于吸塑打样,优点在于生产周期短,成本最低,制作一整版(60X110cm)模具只需一到两天时间,不足之处在于吸塑成品表面粗糙,生产中模具容易碎裂,耐用性差无法成型深度大、复杂度高、片材厚的产品。
采用电镀铜模,其工艺是将打好样的泡壳表面喷上一层导电剂,再放入电解槽内镀上厚厚的铜层,电镀过程需要72小时,接着要对铜模进行灌石膏(增加硬度)、抛光、打气眼处理,采用电镀铜模生产的优点是吸塑制品表面光滑,成本适中,耐用性强,缺点是模具制作周期长,无法完成精密吸塑制品的生产。
采用吸塑铝模生产,模具制作需要先采用电脑设计图纸,再采用CNC数控铣床加工,优点是制作周期适中,后期模具处理时间短(钻气眼工作在CNC加工时完成),吸塑产品尺寸精度高,模具耐用性强,缺点是成本高。
由于全自动高速吸塑成型机的成型范围是66X110cm左右,所以不管是石膏模、铜模还是铝模,都需要将单个的模具拼在一起,达到成型尺寸,我们都称这个过程为拼版,需要拼在打好气孔的铝板或木板上,拼好后的整版模具我们称之为底模。
对于吸塑成型深度大的产品,还需要制作上模,在底模将片材真空吸成型的同时,从片材上方施加压力,将片材均匀地拉伸到每一个部位,否则会引起局部厚度过薄。
生产模具的整个制作周期应为5至7天。
六、吸塑成型生产:采用全自动高速吸塑成型机生产,其基本原理是:将成卷的片材拉进电炉烘箱内加热至软化状态,乘热再拉到吸塑模具上方,模具上移并抽真空,将软化的片材吸附到模具表面,同时将冷却水以雾状喷于成型片材表面,使其硬化,成型的片材再自动被拉至贮料箱,气动裁刀将成型与未成型片材分离,从而完成全部过程。
吸塑产品出现的主要质量问题大多在此过程发生:1.吸塑不到位,是指形状变形,没有吸塑成与模具相同形状的产品;2.吸塑过度,是指产品过薄;3.拉线,是指成型产品上出现不应有的线痕;4.厚薄不均。
这些问题都需要在上好模具后,调试到位,包括:片材前进的时间、加热的温度和时间、抽真空的强度和时间、上模下落的位置、时间和深度、拼版中模具的摆放位置、模
具间是否加附件等等。
七、冲床加工:吸塑成型的大版面产品必须经过冲床,用一块刀版分割成为单一的产品。
其原理是在冲床的底台上有一大张塑料砧板,将大版面成型产品放在砧板上,并把事先做好的刀模卡在单一产品上,通过冲床的上下运动,裁断出单一的成品。
八、分检和包装:这是泡壳生产的最后一关,也是把住质量最重要的环节,每一个冲床配备一个包装工,同时也是质检员,对于成型并分切好的泡壳,以目视检验质量,质检的内容主要包括:1.是否按要求成型,2.泡壳上是否有拉线现象,3.泡壳上是否有大的晶点和气泡,4.是否有大的划痕,5.冲出的泡壳边缘是否光滑,没有毛刺.除了质检员外,还配有巡检员,每隔2小时对整个生产过程做一次质量检验,充分保证泡壳的质量合格率。
泡壳生产和包装工艺流程图。