钻头及钻削技术下
车工工艺与技能练习--钻中心孔、钻孔

(8)在车床上钻孔的教学视频
主要内容: 1、基本操作技术 2、钻孔 3、容易产生的问题及原因
(9)群钻
群钻是利用标准麻花钻头合理刃磨而成的 生产率和加工精度较高、适应性强、寿命 长的新型钻头。 群钻主要用来钻削碳钢和各种合金钢。 群钻是把标准麻花钻的切削部分磨出两条 对称的月牙槽,形成圆弧刃,并在横刃和 钻心处经修磨形成两条内直刃。这样,加 上横刃和原来的两条外直刃,就将标准麻 花钻的“一尖三刃”磨成了“三尖七刃”
(4)中心孔的标注意义
(5)在车床上钻中心孔的教学视频
主要内容: 1、基本操作技术 2、钻中心孔 3、容易产生的问题及原因
2、钻孔
用钻头在实体材料上加工孔的方法叫钻孔。钻孔 属于粗加工,其尺寸精度一般可达IT11~IT12,表 面粗糙度Ra12.5~25mm。
麻花钻是钻孔的常用刀具,材料一般用高速钢制 成,由于高速切削的发展,镶硬质合金的钻头也 得到了广泛的应用。这里介绍高速钢麻花钻及其 钻孔方法。 对于精度要求不高的孔,可用麻花钻直接钻出, 对于精度要求较高的孔,钻孔后还要经过精加工 才能完成(在以后的课程中要涉及到孔的精加 工)。
课题说明
在工件安装中,一夹一顶或两顶都要先预制中心 孔,在钻孔时为了保证同轴度也往往要先钻中心 孔来决定中心位置。 在车床上钻孔加工也是比较常见的工艺,如齿轮、 轴套、带轮、盘盖类等零件的孔,都必须要先进 行钻孔加工。 钻中心孔和钻孔是车工必须要首先掌握的基本技 能。 在传统的教材教学中,这两项内容是在不同的单 元中进行的。本学期在教学改革活动中,我们以 典型零件加工为载体,本着“急用先学”的原则, 对这两项教学内容作了调整性的整合,以满足后 续课的需要,希望能达到预期的效果。
05第五章 钻削、镗削、铰削与拉削
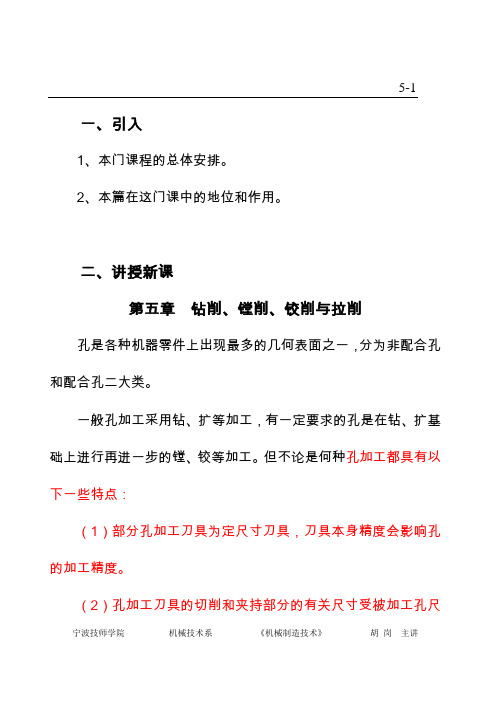
5-1一、引入1、本门课程的总体安排。
2、本篇在这门课中的地位和作用。
二、讲授新课第五章钻削、镗削、铰削与拉削孔是各种机器零件上出现最多的几何表面之一,分为非配合孔和配合孔二大类。
一般孔加工采用钻、扩等加工,有一定要求的孔是在钻、扩基础上进行再进一步的镗、铰等加工。
但不论是何种孔加工都具有以下一些特点:(1)部分孔加工刀具为定尺寸刀具,刀具本身精度会影响孔的加工精度。
(2)孔加工刀具的切削和夹持部分的有关尺寸受被加工孔尺寸的限制,会使刀具的刚性变差。
(3)孔加工时,刀具一般是封闭或半封闭状态下进行工作,对加工质量和刀具耐用度都会产生不利的影响。
宁波技师学院机械技术系《机械制造技术》胡岗主讲5-2 基于以上原因,在机械设计过程中选用孔和轴配合的公差等级时,经常把孔的公差等级定得比轴低一级。
孔加工的方法很多,常用的有钻孔、扩孔、锪孔、铰孔、镗孔、拉孔、磨孔等,还有金刚镗、珩磨、研磨、挤压及特种加工孔等方法。
其加工孔直径Φ0.01~Φ1000mm,加工精度可达到IT13~IT5,表面粗糙度Ra12.5~0.006μm;可在金属或非金属材料上加工,也可在普通材料或高硬度材料上加工。
在加工中可根据不同要求,合理进行选择最佳的加工方案,达到加工质量能符合要求。
第一节钻削加工(一)一、概述用钻头作回转运动,并使其与工件作相对轴向进给运动,在实体工件上加工孔的方法称为钻孔;在已有孔的情况下,用扩孔钻对孔径进行再扩大的加工称为扩孔;钻孔与扩孔统称为钻削。
钻削可以在各种钻床上进行,也可以在车床、铣床、镗床和组宁波技师学院机械技术系《机械制造技术》胡岗主讲5-3合机床、加工中心上进行,但大多数情况下,尤其是在大批量下生产时,主要还是在钻床上进行。
二、钻床主要用钻头在工件上加工孔的机床称为钻床。
通常以钻头的回转运动为主运动,钻头的轴向移动为进给运动。
钻床的分类:坐标镗钻床、深孔钻床、摇臂钻床、台式钻床、立式钻床、卧式钻床、铣钻床、中心孔钻床等八大类。
浅谈标准麻花钻头的钻削特点和耐用度及刃磨方法
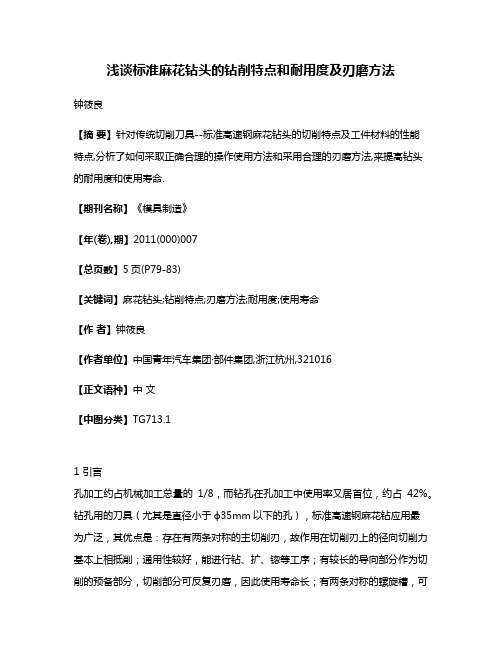
浅谈标准麻花钻头的钻削特点和耐用度及刃磨方法钟筱良【摘要】针对传统切削刀具--标准高速钢麻花钻头的切削特点及工件材料的性能特点,分析了如何采取正确合理的操作使用方法和采用合理的刃磨方法,来提高钻头的耐用度和使用寿命.【期刊名称】《模具制造》【年(卷),期】2011(000)007【总页数】5页(P79-83)【关键词】麻花钻头;钻削特点;刃磨方法;耐用度;使用寿命【作者】钟筱良【作者单位】中国青年汽车集团·部件集团,浙江杭州,321016【正文语种】中文【中图分类】TG713.11 引言孔加工约占机械加工总量的1/8,而钻孔在孔加工中使用率又居首位,约占42%。
钻孔用的刀具(尤其是直径小于ϕ35mm以下的孔),标准高速钢麻花钻应用最为广泛,其优点是:存在有两条对称的主切削刃,故作用在切削刃上的径向切削力基本上相抵削;通用性较好,能进行钻、扩、锪等工序;有较长的导向部分作为切削的预备部分,切削部分可反复刃磨,因此使用寿命长;有两条对称的螺旋槽,可增大实际工作前角。
但由于钻孔属半封闭切削,加工条件苛刻,钻削时容易导制钻头磨损,当钻头磨损到一定程度后就不能继续使用,必须重新刃磨后才能恢复切削性能。
在钻孔中若能合理地减少磨损现象及采取相应措施并采用正确、合理的刃磨方法,可以有效地提高钻头耐用度和使用寿命,有助于提高生产效率和降低生产成本。
2 钻削特点(1)切削刃上各点的切屑流出方向不同:钻削时,主切削刃上各点的切削速度方向及切屑流出方向均不相同,这造成切削刃上各点切屑卷曲的差异,增加了切屑上各点间的互相牵制和切屑的附加变形。
(2)切削刃上各点前角不同:标准麻花钻切削刃上各点静态前角均不相同,而且相差悬殊,造成切削条件的差别。
工作时,因为各点切屑流出方向的不同,实际工作前角也发生不同的变化,如图1所示,实际工作前角roe不仅与半径有关,而且也与钻头转速有关。
图1 钻削钢时不同转速下的主刃前角R——钻头半径(3)横刃切削条件极差:因横刃前角为极大的负值,在切削中引起的轴向力占45%~55%,转矩占15%,切屑变形十分剧烈,形成大的轴向力使钻头工作很不稳定,且横刃过长,钻削时定心也不好。
机械制造基础(第二版)第6章z钻、铰、镗和拉削加工

6.3 铰削加工
三、铰孔时应注意事项
1. 铰刀的选择 铰刀是定尺寸刀具,铰孔的精度在很大程度上决定于铰刀的 精度。故在使用铰刀前,应仔细测量铰刀的直径是否与被铰 孔相符,刃口有无磨损、裂纹、缺口等缺陷,经试铰合格后 方能使用。
2. 铰刀的安装 铰孔作为精加工,切削余量很小。若安装后铰刀轴线与原工 件孔中心线发生偏斜,将会使孔径铰削后尺寸扩大超差和产 生形状误差。因此,铰刀与机床应采用浮动联接。
6.2 钻削加工
三、钻削要素
1.钻削用量
切削速度c 钻削时的切削速度指钻头外缘处的线速度
c
d o n
1000
进给量f、每齿进给量fz及进给速度f
f nf2nfz
背吃刀量ap 对钻头而言,它就是钻头直径的一半
ap d0 2
6.2 钻削加工
2.切削层截面尺寸
钻削时切削层尺寸平面为过 基点D的基面PD
6.3 铰削加工
3. 铰削用量的选择 合理选择铰削用量,可以提高铰孔精度。 精铰时,一般半径上铰削余量为0.03~0.15mm,其值取决
于工件材料及对孔要求的精度和表面粗糙度。一般铰削钢体
时,切削速度c=1.5~5m/min;铰铸铁件时c=8~l0m/min,
进给量不能取得过小,否则切削厚度hd过薄,铰刀的挤压作 用会明显加大,加速铰刀后刀面的磨损。—般铰制钢件时f= 0.3~2mm/r,铰削铸铁件时f=0.5~3mm/r。
铰刀齿槽方向有直槽和螺旋槽两种。直槽铰刀刃磨、检验方 便,生产中常用;螺旋槽铰刀切削过程平稳。加工铸铁等取 β=7~8;加工钢件取β=12~20;加工铝等轻金属取 β=35~45。
6.3 铰削加工
铰刀的几何角度
前角γo和后角o 一般取γo=0。粗铰塑性材料时,为
钻头的磨法
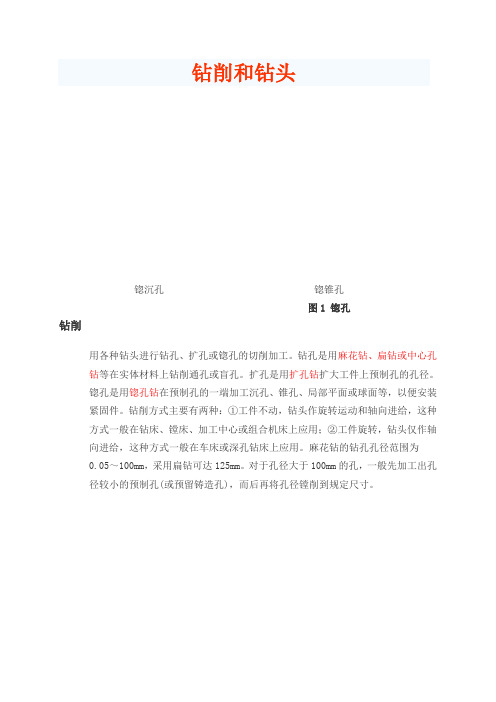
钻削和钻头锪沉孔锪锥孔图1 锪孔钻削用各种钻头进行钻孔、扩孔或锪孔的切削加工。
钻孔是用麻花钻、扁钻或中心孔钻等在实体材料上钻削通孔或盲孔。
扩孔是用扩孔钻扩大工件上预制孔的孔径。
锪孔是用锪孔钻在预制孔的一端加工沉孔、锥孔、局部平面或球面等,以便安装紧固件。
钻削方式主要有两种:①工件不动,钻头作旋转运动和轴向进给,这种方式一般在钻床、镗床、加工中心或组合机床上应用;②工件旋转,钻头仅作轴向进给,这种方式一般在车床或深孔钻床上应用。
麻花钻的钻孔孔径范围为0.05~100mm,采用扁钻可达125mm。
对于孔径大于100mm的孔,一般先加工出孔径较小的预制孔(或预留铸造孔),而后再将孔径镗削到规定尺寸。
钻削时,钻削速度v是钻头外径的圆周速度(米/分);进给量f是钻头(或工件)每转钻入孔中的轴向移动距离(mm/r)。
图2是麻花钻的钻削要素,由于麻花钻有两个刀齿,故每齿进给量a=f/2(mm/齿)。
切削深度a p有f两种:钻孔时按钻头直径d的一半计算;扩孔时按(d-d0)/2计算,其中d0为预制孔直径。
每图2 麻花钻的钻削要素个刀齿切下的切屑厚度a=a f sin K r,单位为mm。
式中K r为钻头顶角的一半。
使用高速钢麻花钻钻削钢铁0材料时,钻削速度常取16~40米/分,用硬质合金钻头钻孔时速度可提高1倍。
钻削过程中,麻花钻头有两条主切削刃和一条横刃,俗称“一尖(钻心尖)三刃”,参与切削工作,它是在横刃严重受挤和排屑不利的半封闭状态下工作,所以加工的条件比车削或其他切削方法更为复杂和困难,加工精度较低,表面较粗糙。
钻削钢铁材料的精度一般为IT13~10,表面粗糙度为R a20~1.25µm,扩孔精度可达IT10~9,表面粗糙度为R a10~0.63µm。
钻削加工的质量和效率很大程度上决定于钻头切削刃的形状。
在生产中往往用修磨的方法改变麻花钻头切削刃的形状和角度以减少切削阻力,提高钻削性能,中国的群钻就是采用这种方法创制出来的。
磨麻花钻头的技巧和方法
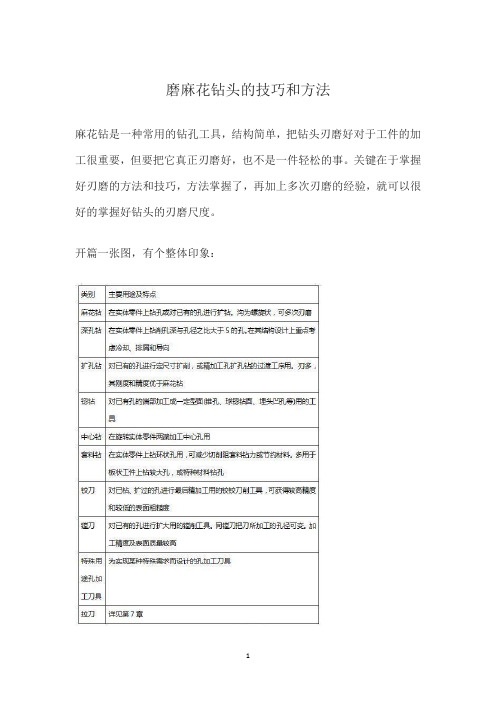
磨麻花钻头的技巧和方法麻花钻是一种常用的钻孔工具,结构简单,把钻头刃磨好对于工件的加工很重要,但要把它真正刃磨好,也不是一件轻松的事。
关键在于掌握好刃磨的方法和技巧,方法掌握了,再加上多次刃磨的经验,就可以很好的掌握好钻头的刃磨尺度。
开篇一张图,有个整体印象:麻花钻刃磨步骤麻花钻的顶角一般是118°,也可把它当作120°来看待。
刃磨钻头能掌握好以下6个技巧一般就没有什么问题了。
1. 磨钻头前,先要将钻头的主切削刃与砂轮面放置在一个水平面上,也就是说,保证刃口接触砂轮面时,整个刃都要磨到。
这是钻头与砂轮相对位置的第一步,位置摆好再慢慢往砂轮面上靠。
2. 这个角度就是钻头的锋角,此时的角度不对,将直接影响钻头顶角的大小及主切削刃的形状和横刃斜角。
这里是指钻头轴心线与砂轮表面之间的位置关系,取60°就行,这个角度一般比较能看得准。
这里要注意钻头刃磨前相对的水平位置和角度位置,二者要统筹兼顾,不要为了摆平刃口而忽略了摆好度角,或为了摆好角度而忽略了摆平刃口。
3. 刃口接触砂轮后,要从主切削刃往后面磨,也就是从钻头的刃口先开始接触砂轮,而后沿着整个后刀面缓慢往下磨。
钻头切入时可轻轻接触砂轮,先进行较少量的刃磨,并注意观察火花的均匀性,及时调整手上压力大小,还要注意钻头的冷却,不能让其磨过火,造成刃口变色,而至刃口退火。
发现刃口温度高时,要及时将钻头冷却。
4. 这是一个标准的钻头磨削动作,主切削刃在砂轮上要上下摆动,也就是握钻头前部的手要均匀地将钻头在砂轮面上上下摆动。
而握柄部的手却不能摆动,还要防止后柄往上翘,即钻头的尾部不能高翘于砂轮水平中心线以上,否则会使刃口磨钝,无法切削。
这是最关键的一步,钻头磨得好与坏,与此有很大的关系。
在磨得差不多时,要从刃口开始,往后角再轻轻蹭一下,让刃后面更光洁一些。
5. 一边刃口磨好后,再磨另一边刃口,必须保证刃口在钻头轴线的中间,两边刃口要对称。
磨钻头的方法

磨钻头的方法磨钻头是一项重要的工艺,它能够有效地提高钻头的使用寿命和钻削效率。
下面将介绍一种常用的磨钻头的方法,希望对读者有所帮助。
我们需要准备磨钻头的工具。
通常情况下,我们需要一台磨头机和相应的磨头盘。
磨头盘的选择要根据钻头的直径和材质来确定,以确保磨削效果的最佳。
接下来,我们需要将钻头安装到磨头机上。
在安装过程中,要确保钻头固定牢固,避免在磨削过程中产生晃动或脱落的情况。
在开始磨削之前,我们需要调整磨头机的参数。
主要包括转速和进给速度。
转速的选择要根据钻头的材质和直径来确定,一般来说,硬质合金钻头的转速要相对较高,而普通钢材钻头的转速要适当降低。
进给速度的选择要根据钻削的深度和材料来确定,一般来说,进给速度要适中,既要保证磨削效果,又要避免过度磨削。
当调整好参数后,我们可以开始磨削钻头了。
首先,我们要将钻头与磨头盘接触,然后轻轻地推动钻头,使其与磨头盘保持一定的接触面积。
在推动钻头的同时,要保持一定的均匀力度,避免过度集中力量而导致钻头损坏或磨削不均匀。
在磨削过程中,要注意观察钻头的状态。
如果钻头表面出现明显的磨损或变形,就需要及时停止磨削,以免影响钻头的使用效果。
此外,还要定期清理磨削产生的金属屑和磨削液,以保持磨头机的清洁和正常运行。
完成磨削后,我们要对钻头进行检查。
主要包括以下几个方面:第一,检查钻头的外观是否光滑,表面是否有明显的划痕或凹凸不平的现象;第二,检查钻头的尺寸是否符合要求,包括直径和长度等;第三,用手触摸钻头的刃口,感受其锋利度和光滑度。
如果发现钻头有明显的问题,就需要重新进行磨削。
磨钻头是一项技术要求相对较高的工艺。
只有掌握了正确的磨削方法和技巧,才能够有效地提高钻头的使用寿命和钻削效率。
希望通过本文的介绍,读者对磨钻头的方法有了更深入的了解,并能够在实际操作中运用到。
钻头横刃修磨技巧
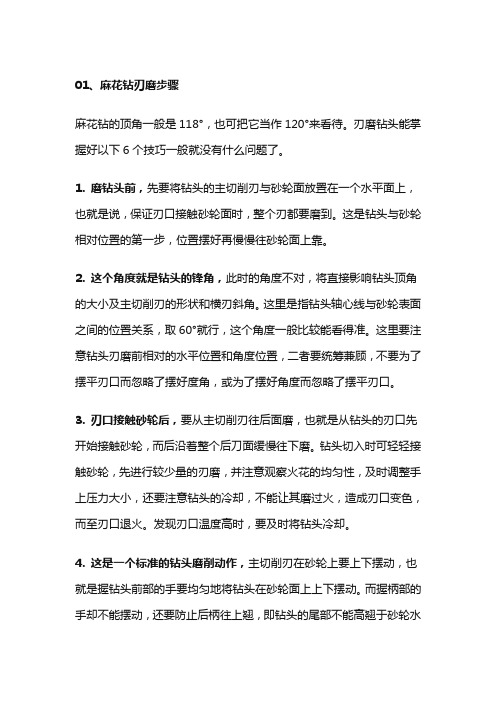
01、麻花钻刃磨步骤麻花钻的顶角一般是118°,也可把它当作120°来看待。
刃磨钻头能掌握好以下6个技巧一般就没有什么问题了。
1. 磨钻头前,先要将钻头的主切削刃与砂轮面放置在一个水平面上,也就是说,保证刃口接触砂轮面时,整个刃都要磨到。
这是钻头与砂轮相对位置的第一步,位置摆好再慢慢往砂轮面上靠。
2. 这个角度就是钻头的锋角,此时的角度不对,将直接影响钻头顶角的大小及主切削刃的形状和横刃斜角。
这里是指钻头轴心线与砂轮表面之间的位置关系,取60°就行,这个角度一般比较能看得准。
这里要注意钻头刃磨前相对的水平位置和角度位置,二者要统筹兼顾,不要为了摆平刃口而忽略了摆好度角,或为了摆好角度而忽略了摆平刃口。
3. 刃口接触砂轮后,要从主切削刃往后面磨,也就是从钻头的刃口先开始接触砂轮,而后沿着整个后刀面缓慢往下磨。
钻头切入时可轻轻接触砂轮,先进行较少量的刃磨,并注意观察火花的均匀性,及时调整手上压力大小,还要注意钻头的冷却,不能让其磨过火,造成刃口变色,而至刃口退火。
发现刃口温度高时,要及时将钻头冷却。
4. 这是一个标准的钻头磨削动作,主切削刃在砂轮上要上下摆动,也就是握钻头前部的手要均匀地将钻头在砂轮面上上下摆动。
而握柄部的手却不能摆动,还要防止后柄往上翘,即钻头的尾部不能高翘于砂轮水平中心线以上,否则会使刃口磨钝,无法切削。
这是最关键的一步,钻头磨得好与坏,与此有很大的关系。
在磨得差不多时,要从刃口开始,往后角再轻轻蹭一下,让刃后面更光洁一些。
5. 一边刃口磨好后,再磨另一边刃口,必须保证刃口在钻头轴线的中间,两边刃口要对称。
有经验的师傅会对着亮光察看钻尖的对称性,慢慢进行修磨。
钻头切削刃的后角一般为10°-14°,后角大了,切削刃太薄,钻削时振动厉害,孔口呈三边或五边形,切屑呈针状;后角小了,钻削时轴向力很大,不易切入,切削力增加,温升大,钻头发热严重,甚至无法钻削。