金刚石涂层学习课件.doc
金刚石表面特性和表面金属化专题培训课件

前言
• 金刚石由于具有高硬度、低摩擦系数、高热导率、 低膨胀系数、低放射性等许多优异的物理特性, 在许多工业领域都得到应用。尤其是由金刚石和 金属、陶瓷或高分子树脂结合在一起做成的金刚 石工具,不仅被广泛用于民用建筑与土木工程、 石材加工业、汽车工业、交通工业、地勘与国防 工业等领域和其它现代高新技术领域,而且在宝 石、医疗器械、木材、玻璃钢、石材工艺品、陶 瓷、复合金属和硬脆材料等众多新领域不断出现, 社会对金刚石工具的需求也逐年增加。
• 金刚石粒度越细,表面吸附杂质越多,纳 米金刚石更甚,这就为金刚石表面改性提 供了可能。
• 张书达、朱瑶华[1] 利用二次离子质谱法 (SIMS)对金刚石表面杂质元素N、Na、Mg、 Si进行了分析和测量,并用Ar+剥蚀金刚石 表面,发现杂质浓度最大值均位于最外的 一薄层内。
• 李颖、李焕锋等[2]用热分析和红外分析对爆 轰纳米金刚石进行了研究,发现空气中纳 米黑色金刚石在478℃~515℃开始氧化,N2 中加热到700℃之前失重很少;灰色纳米金 刚石在570℃开始氧化,N2中加热到950℃
天然金刚石形状图
天然金刚石图1
天然金刚石图2
立方体
歪斜八面体
曲面四六面体
带壳金刚石
天然金刚石形状图
1.3金刚石表面缺陷
• 金刚石在形成过程中表面会出现三角凹痕、三角 座(突起的三角形)、生长阶梯、纹理、结节 (纹理发生改变处)和凹角等生长特征,使金刚 石表面变得不平整。
三角凹痕
生长阶梯
纹理和结节
• 八面体与菱形十二面体聚形 及八面体与立方体聚 形:
人造金刚石形状
• 人造金刚石单晶呈平面状,具有清晰的晶 棱及顶角。人造金刚石比天然金刚石的晶 棱及顶角更明晰,晶面更平整。人造金刚 石立方体与八面体的聚形多见,很少见到 菱形十二面体。
聚晶金刚石涂层的元素含量
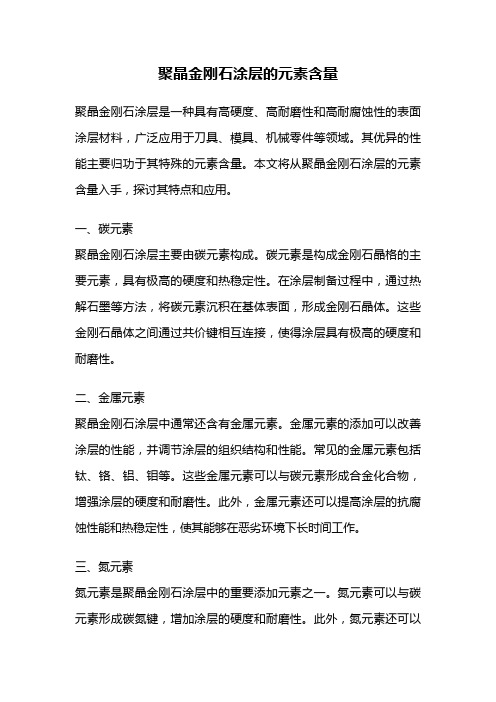
聚晶金刚石涂层的元素含量聚晶金刚石涂层是一种具有高硬度、高耐磨性和高耐腐蚀性的表面涂层材料,广泛应用于刀具、模具、机械零件等领域。
其优异的性能主要归功于其特殊的元素含量。
本文将从聚晶金刚石涂层的元素含量入手,探讨其特点和应用。
一、碳元素聚晶金刚石涂层主要由碳元素构成。
碳元素是构成金刚石晶格的主要元素,具有极高的硬度和热稳定性。
在涂层制备过程中,通过热解石墨等方法,将碳元素沉积在基体表面,形成金刚石晶体。
这些金刚石晶体之间通过共价键相互连接,使得涂层具有极高的硬度和耐磨性。
二、金属元素聚晶金刚石涂层中通常还含有金属元素。
金属元素的添加可以改善涂层的性能,并调节涂层的组织结构和性能。
常见的金属元素包括钛、铬、铝、钼等。
这些金属元素可以与碳元素形成合金化合物,增强涂层的硬度和耐磨性。
此外,金属元素还可以提高涂层的抗腐蚀性能和热稳定性,使其能够在恶劣环境下长时间工作。
三、氮元素氮元素是聚晶金刚石涂层中的重要添加元素之一。
氮元素可以与碳元素形成碳氮键,增加涂层的硬度和耐磨性。
此外,氮元素还可以提高涂层的热稳定性和抗氧化性能,使其能够在高温环境下长时间使用。
另外,氮元素还可以调节涂层的晶格结构,使其具有更好的机械性能和导热性能。
四、硅元素硅元素是聚晶金刚石涂层中的重要添加元素之一。
硅元素可以与碳元素形成硅碳键,增加涂层的硬度和耐磨性。
此外,硅元素还可以提高涂层的抗腐蚀性能和热稳定性,使其能够在恶劣环境下长时间工作。
另外,硅元素还可以调节涂层的晶格结构,使其具有更好的机械性能和导热性能。
五、其他元素除了上述几种主要元素外,聚晶金刚石涂层中还可能含有其他元素,如氧、氢、氩等。
这些元素的添加可以改善涂层的性能和结构,使其具有更好的机械性能、导热性能和抗腐蚀性能。
总结:聚晶金刚石涂层的元素含量对其性能具有重要影响。
碳元素是构成金刚石晶格的主要元素,金属元素的添加可以改善涂层的性能,氮元素和硅元素可以增加涂层的硬度和耐磨性。
超硬材料涂层

超硬材料涂层1.金刚石、类金刚石(DLC)涂层金刚石涂层是新型刀具涂层材料之一。
它利用低压化学气相沉积技术在硬质合金基体上生长出一层由多晶构成的金刚石膜,用其加工硅铝合金和铜合金等有色金属、玻璃纤维等工程材料及硬质合金等材料,刀具寿命是一般硬质合金刀具的50~100倍。
金刚石涂层采纳了很多金刚石合成技术,最一般的是热丝法、微波等离子法和DC等离子喷射法。
通过改进涂层方法和涂层的粘结,已生产出金刚石涂层刀具,并在工业上得到了应用。
近年来,美国、日本和瑞典等国家都已相继推出了金刚石涂层的丝锥、铰刀、铣刀以及用于加工印刷线路板上的小孔金刚石涂层硬质合金钻头及各种可转位刀片,如瑞典Sandvik公司的CD1810和美国Kennametal公司的KCD25等牌号产品。
美国Turchan公司开发的一种激光等离子体沉积金刚石的新工艺,用此法沉积金刚石,由于等离子场包围整个刀具,刀具上的涂层均匀,其沉积速度比常规CVD法快1000倍。
此法所成的金刚石涂层与基体之间产生真正的冶金结合,涂层强度高,可防止涂层脱落、龟裂和裂纹等缺陷。
CemeCon公司具有特色的CVD金刚石涂层技术,2000年建立生产线,使金刚石涂层技术达到工业化生产水平,其技术含量高,可以批量生产金刚石涂层。
类金刚石涂层在对某些材料(Al、Ti及其复合材料)的机械加工方面具有明显优势。
通过低压气相沉积的类金刚石涂层,其微观结构与天然金刚石相比仍有较大差异。
九十时代,常采纳激活氢存在下的低压气相沉积DLC,涂层中含有大量氢。
含氢过多将降低涂层的结合力和硬度,增大内应力。
DLC中的氢在较高的温度下会渐渐释放出来,引起涂层工作不稳定。
不含氢的DLC硬度比含氢的DLC高,具有组织均匀、可大面积沉积、成本低、表面平整等优点,已成为近年来DLC涂层讨论的热点。
美国科学家A.A.Voevodin提出沉积超硬DLC涂层的结构设计为Ti—TiC—DLC梯度变化涂层,使硬度由较软的钢基体渐渐提高到表层超硬的DLC涂层。
DLC(类金刚石膜层介绍)

RF or DC power supply
Cathode
Permanent magnets
N
SS
+E
N
Ring Electrode
Negative Glow Plasma
Sputtered atoms
Work piece
Ar+ 离子轰击靶材表面。
Al 原子自靶材表面溅射并沉积到塑料基 体表面。
– 通过施加一定的偏压, 使得等离子中 的离子获得一定的能量, 层积于基体 表面,
PVD (磁控溅射)
CVD (PECVD)
FCVA
镀膜粒子 能量峰值 镀膜气压 镀膜温度
原子 ~0.1eV 5E-3 Torr ~200 ºC
原子团 ~0.2eV 1E-2 Tor >200 ºC
离子 20 to 5000eV 1E-6 Torr <80 ºC
以碳膜为例:
膜层密度 (g/cm3) 膜层硬度 (GPa) 氢含量 工作温度 (无 O2) 工作温度 (有 O2)
(2)纳峰的主要业务: 采用FCVA技术, 制备和沉积C材料, 以获得最优良的DLC (taC)薄膜.
2. DLC (Diamond Like Carbon(DLC) 类金刚石碳膜
DLC 结构
Diamond
Graphite
DLC
Diamond structure (sp3)
Graphite structure (sp2)
1. 表面处理技术介绍
常规 真空层积
化 学 气 相 层 积
物 理 气 相 层 积
FCVA (阴极过滤弧) 真空镀膜
膜层(表面原子排列)有序可控 原子排练致密,
膜层(表面原子排列)有序可控
金刚石砂轮涂层技术应用

金刚石砂轮涂层技术应用一、项目起因2011年随着MAN项目的进展,公司内引进了等高齿锥齿轮加工技术。
MAN桥锥齿轮铣齿机所用SPIRON刀盘用硬质合金刀具由配套B27磨刀机精磨削成型,磨削精度高、稳定性好。
本机床所使用砂轮为德国进口金刚石颗粒砂轮,每盘砂轮价值7.8万元。
该机床所使用的金刚石砂轮为电镀涂层金刚石砂轮,在正常重磨的情况下(不包括刀条角度改型及毛坯刀条开刃),砂轮更换周期约为1500件刀条,每根刀条所耗费的砂轮成本52元。
如砂轮磨损后直接报废,则成本较高。
目前公司内大部分齿轮加工刀具均进行涂层,为此,决定进行金刚石砂轮涂层试验,以降低磨刀成本,提高生产效率。
二、金刚石砂轮涂层技术概述1.金刚石砂轮基础知识以金刚石磨料为原料,分别用金属粉、树脂粉、陶瓷和电镀金属作结合剂,制成各种形状的制品,用于磨削、抛光、研磨的工具叫金刚石磨具,包括砂轮、油石(珩磨油石)、钻具、据具、粉状修正工具、修正滚轮、内外圆切割锯片、砂轮刀、玻璃刀、车刀、木工圆盘锯片等。
其中以金刚石砂轮,金刚石锯片应用最广泛。
金刚石砂轮一般由工作层、基体、过渡层三部分组成。
工作层,又称金刚石层,由磨料、结合剂和填料组成,是砂轮的工作部分;过渡层,又称非金刚石层,由结合剂、金属粉和填料组成,是将金刚石层牢固地连接在基体上的部分;基体,用于承接磨料层,并在使用时用法兰盘牢固地把砂轮夹持在磨床主轴上。
制品成型质量的好坏和使用精度的高低都与基体有很大关系。
因此,基体应该有几何形状和尺寸精度以及表面粗糙度要求。
2.金刚石砂轮磨削修整原理金刚石砂轮磨损可以看作经历了这样几个阶段:砂轮与工件接触初始阶段。
金刚石砂轮在摩擦力和冲击力作用下,金刚石颗粒旋转,引起金刚石颗粒间结合剂的弹性变形,变形达到一定程度,结合剂出现裂纹,金刚石颗粒在摩擦力和冲击力的继续作用下旋转,造成结合剂裂纹的扩大,最终结合剂断裂,金刚石颗粒从砂轮表面脱落。
通常的金刚石砂轮整形主要是外圆、端面、斜面、外圆角和内、外圆弧面的整形,金刚石砂轮一般只有转动,而工具砂轮(一般是碳化硅砂轮、白刚玉砂轮,也可以选用金刚石砂轮)不仅仅有转动,还有进给运动和往复摆动。
金刚石薄膜
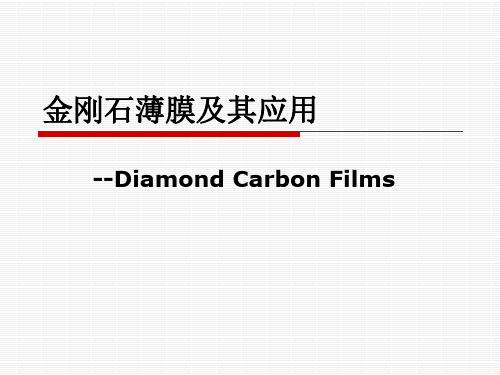
图1 碳的相图
各种动力学因素:
反应过程中输入的热能或射频功率等的等离子体能量、反 应气体的激活状态、反应气体的最佳比例、沉积过程中成 核长大的模式等对生成金刚石起着决定性的作用。 选用与金刚石有相同或相近晶型和点阵常数的材料作基片, 降低金刚石的成核势垒。却提高了石墨的成核势垒。 石墨在基片上成核的可能性仍然存在,并且一旦成核,就 会在其核上高速生长,还可能生成许多非晶态碳,因此, 需要有一种能高速除去石墨和非晶态碳的腐蚀剂,相比之 下,原子氢是最理想的腐蚀剂,它能同时腐蚀金刚石和石 墨,但它对石墨的腐蚀速率比腐蚀金刚石的速率高30~40 倍,这样就能有效地抑制石墨相的生长。
金刚石的性能
金刚石薄膜具有优异的机械、热、光、电、
半导体、声、生物及化学性能,下面只简要
介绍热敏特性及光学性能。
1.热敏特性
金刚石薄膜的电阻随温度的升高,下降得非常快。
未掺杂的金刚石薄膜计算得到的材料常数B值为 4443K,材料激活能E为0.38eV; 掺杂硼可改变B和E值,便于与二次仪表匹配。 因此金刚石薄膜可用于制造热敏电阻,具有灵敏度高、 工作温度范围宽、抗辐射能力强等优点。
类金刚石薄膜的制备方法
类金刚石薄膜的制法可以分为三类: 等离子体化学气相沉积法
离子束法
溅射法
类金刚石薄膜的性能
DLC的电阻率变化范围较宽(102~1014),一般含H 的DLC的电阻率比不含H的DLC高,这或许是H稳定 了 sp 3 键的缘故。 各种沉积法制备的DLC的硬度变化范围是很大的 2 ( H v 1500~ 10000kg/mm )。 内应力和黏附力决定着薄膜与基体结合的稳定性和薄 膜的寿命。内应力产生于沉积过程中的热膨胀差别或 由于杂质掺入界面,结构排列不完整或结构重排而致 的本征应力。DLC中一般都存在较大的压应力(GPa 量级),影响内应力的因素很多,如DLC中的H含量、 膜厚均匀性、膜层周围气氛等。
金刚石涂层刀具表面处理方法

金刚石涂层刀具表面处理方法
金刚石涂层刀具是当前最先进的刀具材料,能够用于切削加工,深度加工,磨削加工等业务。
但是,由于其高硬度,往往表面会变得失光、发粗和有氧化皮,因此,金刚石涂层刀具表面处理方法成为最重要的课题。
首先,对金刚石涂层刀具表面的处理通常都要清洁后进行,以期获得最佳效果。
在这一步之前,专门的腐蚀剂可以用来去除残留的油料,令表面干净平整。
接着,用清水和肥皂水将清洗完毕的表面清洗,以去除尘土和散装颗粒杂质,待干后,可以开始表面处理。
其次,常用的表面处理方法有拉丝法、抛光法和渗透涂层法。
以拉丝法为例,其处理程序大致是先用拉丝和抛光轮,将残留在金刚石涂层刀具表面的某些物质拉丝掉;接着,用抛光轮抛光表面,使其变得光滑,并减少断层,从而提高加工精度。
此外,抛光法也可以用于对金刚石涂层刀具表面进行处理。
采用抛光头抛光表面,使抛光头更加柔软,减少材料的磨耗,同时也起到反膨胀作用,使表面变得平整光滑。
特别是在定形加工中,采用抛光法可以消除表面毛刺,减少刀具的磨耗,提高加工精度和表面质量。
最后,渗透涂层处理也是对金刚石涂层刀具表面进行处理的一种方法,它将涂料放到表面上,然后用热涂技术进行处理,使表面形成深度渗透层,有效保护刀具金刚石涂层,提高表面耐擦损性能,减少氧化反响,延长刀具寿命。
综上所述,对金刚石涂层刀具表面的处理方法有拉丝法、抛光法
和渗透涂层法,它们都可以显著提高表面光泽度,延长刀具使用寿命,提高加工精度,从而使加工质量得到大大改善。
因此,金刚石涂层刀具表面处理是十分重要的,工程师和技术人员应当正确选择和适宜的处理方法,以提高加工质量,保证产品质量。
图层金刚石

三、涂层金刚石的发展研究现状
(2)硬质合金基体中的Co具有催石墨化的作用;
(3)金刚石与WC-Co硬质合金热膨胀系数不匹配导致 涂层内存在较大的残余应力。
选择合适的厚度是金刚石涂层刀具合理性价比的关键。
CVD金刚石薄膜太薄,磨损快,刀具使用寿命不高; CVD金刚石薄膜太厚,与硬质合金基体的粘附性变差 且制造成本增加。
但材料添加了硬质耐磨 颗粒作为强化剂,这无 疑增加了这些材料加工 难度,这些硬质颗粒会 造成刀具过早磨损产生 大量切削热。
一、涂层金刚石刀具出现的历史背景
因此,多数刀具用户认为, 普通刀具已经不能满足需 求,而迫切需要一种耐磨 性更高、能稳定实现高精、 高效、寿命更长的超硬刀 具。
金刚石涂层刀具因其具有 十分接近天然金刚石的硬 度和耐磨性、高的弹性模 量、极高的热导率、良好 的自润滑性和化学稳定性 等优异性能,成为加工难 加工材料的理想刀具。
三、涂层金刚石的发展研究现状
典型的硬质合金表面预处理方法主要有:
(1)除去或钝化刀具表面层的粘结相Co; (2)施加过渡层; (3)机械处理等。 在实际应用中,为了更好地提高金刚石薄膜与硬质合 金基体的结合强度,往往同时综合采用多种表面预处 理方法。
广东工业大学匡同春等人发表了《CVD金刚石涂层硬质
石的热膨胀系数最为接近,因此一直被认为是CVD金 刚石涂层较为理想的基体材料。 缺点:由于Si3N4陶瓷本身脆性大,抗冲击性能差,一
二、涂层金刚石刀具的含义及其组成
般认为,Si3N4基金
刚石涂层刀具仅宜 用于精加工,而不 宜进行冲击切削加工。
(2) WC系硬质合金
二、涂层金刚石刀具的含义及其组成
四、涂层金刚石刀具的发展前景展望
- 1、下载文档前请自行甄别文档内容的完整性,平台不提供额外的编辑、内容补充、找答案等附加服务。
- 2、"仅部分预览"的文档,不可在线预览部分如存在完整性等问题,可反馈申请退款(可完整预览的文档不适用该条件!)。
- 3、如文档侵犯您的权益,请联系客服反馈,我们会尽快为您处理(人工客服工作时间:9:00-18:30)。
化学气相沉积法制备金刚石涂层
金刚石是硬度最高的固体物质(HV= 100GPa),性质稳定,耐磨,但却难以加工成各种所需的零件和制品。
采用气相沉积法制备金刚石涂层,可以使金刚石性质得以从分利用,同时也节约了成本。
下面以金刚石涂层拉拔模具的制备为例,
简单介绍化学气相沉积法金刚石涂层的制备方法。
金属线材行业是我国的主要传统产业,而金属线材生产企业重要的易消品
就是拉拔模具,其使用方式如图 1 所示,拉拔模具的性能决定了金属线材的质量、生产效率和生产成本。
目前线材行业所用的模具主要为硬质合金模具和
聚晶金刚石模具两大类。
硬质合金模具寿命短,易粘料,生产效率低;聚晶金刚石模具价格高,制作较大尺寸模具和异形模具非常困难,且韧性较差。
本文应用化学气相沉积
(chemicMvaperdepsdition,CVD) 金刚
石涂层技术,制成金刚石涂层拉拔模
具,克服了硬质合金拉拔模具不耐磨
和聚晶金刚石拉拔模具韧性较差的缺
点,成为新一代的拉拔模具。
金刚石涂层拉拔模具的制备过
程:金刚石涂层拉丝模具是以YG6
硬质合金模具为基体,经过特殊的表
面处理后,用气相沉积方法,在硬质合金拉丝模具基体工作区域表面沉积10 —30p,m的多晶金刚石膜。
经修整、抛光、镶套后制作成成品,具体过程如图2 所示。
(1)准备工作
选择YG6 牌号硬质合金模具,坯料孔型和尺寸与所要制备的成品模具相适应,通过内孔研磨修整工艺将模具坯料修整为合适的形状,预留30u m 左右的尺寸余量,以配合涂层厚度尺寸。
将修整完毕的硬质合金模具进行喷砂处理,去除表面的污染物和疏松层,再使用蒸馏水、酒精在超声波清洗机中清洗。
最后将模具在配制好的酸、碱液中进行表面腐蚀处理,并采用蒸馏水、酒精超声波清洗,完毕后将试件装入自制的热丝CVD 金刚石沉积设备中。
(2)涂层沉积
通人H2 和CH4 ,将热丝加热至2500℃左右,调节气体流量、热丝温度、气压、基体温度等工艺参数,使模具表面沉积厚度约40 um 的金刚石膜,制成金刚石涂层拉拔模具。
制品可直接使用,也可通过精密修整抛光进一步提高
表面质量,从而满足不同使用环境对模具的不同要求。
金刚石涂层性能检测
(1)金刚石涂层的结合力
金刚石涂层与硬质合金基体具备高结合强度是金刚石涂层拉拔使用的基础,
如果结合强度不高,在用于高强度线材的拉拔中金刚石涂层会脱落,导致模具失效。
制作的金刚石涂层拉拔模具采
用金刚石压痕仪测试结合强度。
将
金刚石压头压入金刚石涂层表面,
其结果如图 3 所示,可见压痕周
围未发生金刚石涂层的崩裂和脱
落,压坑中心部位金刚石涂层仍牢
固结合在硬质合金表面测试中,在
1.5kN 压力下金刚石涂层破坏,而
在传统的金刚石涂层制备工艺中,
测试结合力载荷值最高未超过
600N,该结果表明本试验中制作的
金刚石涂层与硬质合金有着很高的
结合强度。
(2)金刚石涂层颗粒尺寸
拉拔模具的表面粗糙度对其性能极为关键。
金刚石涂层是多晶结构,晶体颗粒尺寸越小,加工后的表面粗糙度越低。
金刚石涂层应用于石墨加工工具中表明,当晶粒尺寸小于 1 um 时,加工工件的表面粗糙度R <1um,而普通金刚石
涂层加工工件粗糙度R >2.3um,且在使用中有颗粒脱落的现象。
本
金刚石涂层的断面和表面SEM 照片
实验制作的金刚石涂层由微米晶粒和超细颗粒两层构成,如上图所示,从断面SEM 照片可清晰分辨出基体、微米晶粒层和超细颗粒层,涂层表面的SEM 照片说明金刚石层表面颗粒平均尺寸约0.1 um,较粗大的微米晶体颗粒构成涂层
的支撑,表层的超细颗粒加工后可得到极低的粗糙度。
该尺寸金刚石涂层经精
密加工后可达极低的表面粗糙度,可以满足高性能拉拔模具的使用要求。
金刚石涂层模具的失效机制
金刚石涂层模具在使用中,由于金刚石涂层的磨损能力极强,大幅度提高了硬质合金拉拔模具的用寿命;但是由于涂层超长时间承受交变应力,作为基体的硬质合金表层以及金刚石涂层与硬质合金界面缺陷将被激发,逐渐演化成为裂
纹,造成细观尺度的断裂破坏,产生裂纹,使得金刚石涂层部分脱落暴露的粗
糙面使基体材表面划伤导致失效,而不是由于磨损导致尺寸变化过大而失效,与普通的硬质合金模具和聚晶金刚石模具的失效方式有本质区别。