无尘粉碎为中药材前处理在粉碎工序中的技术改造
药材粉碎标准操作规程

药材粉碎标准操作规程1生产前检查及准备1.1 车间班组长对工作区进行全面检查,确认上次生产后已清场合格,现场不存在与本次生产无关的物料、文件、记录等,生产设施、设备、使用的容器具均悬挂有符合生产的状态标志。
若清场时间已过规定的有效期,应对工作区重新进行清场,经QA检查达到生产要求后才准许开工。
1.2 准备好使用的容器具、工具、岗位记录及足够数量的标签;1.3 运送待粉碎物料至工作区域,并核对品名、批号、数量及合格标志。
2 操作步骤2.1 检查粉碎机组各运转部位灵活,无异常,不影响设备正常工作;2.2 在细粉下料口下放好盛放药粉的洁净容器;2.3 根据工艺要求选择适宜规格的筛网安装好,并根据粉碎物料的品种及工艺要求,调整冷却水的大小;2.4 将待粉碎物料置料槽内,开机开始粉碎作业;2.5 粉碎好的细粉计量,标识好,转中间站。
3 生产安全注意事项3.1 人员3.1.1 操作人员必须穿戴工作服、鞋、帽及口罩;3.1.2 开机运转后,操作人员要坚守工作岗位,不得脱岗、睡岗、串岗。
3.2 粉碎机组3.2.1 在更换粉碎品种时,要打开各清扫门用吹尘器或吸尘器清理干净;3.2.2 生产过程中不能将手或工具伸入料槽进料口和喂料器内,以免造成人身伤害或损坏设备;3.2.3 经常检查联轴器的弹性柱销是否有松动,避免螺母飞脱伤人。
4 异常情况处理4.1 如果运转时粉碎机电流过大,可能是被粉碎的物料太重,可以减少喂料;电流再过大,则停机待检修。
4.2 本机组分离器为高效式,一般滤袋内有少量超细粉。
如果运行几十分钟不下粉,可能是分离器下口或管道横向部分被粉堵塞,要开动转筛打开各清扫门清理。
但注意回渣口,要用容器接住粗渣,以免大量粗渣流入粉碎机内难起动。
(以上情况只在潮湿天气或加工的物料太湿或太油的情况下才可能发生。
)4.3 机组滤尘袋有两个作用:一是滤粉减尘,二是调整转筛内风压。
正常时转筛内应略带正压(2~5mm水柱),即在筛的回渣口,粗渣应顺利流下,而不是急喷而出(正压太大)或忽上忽下断续流出(有负压)。
中药GMP工厂 中药前处理车间粉碎室清洁规程
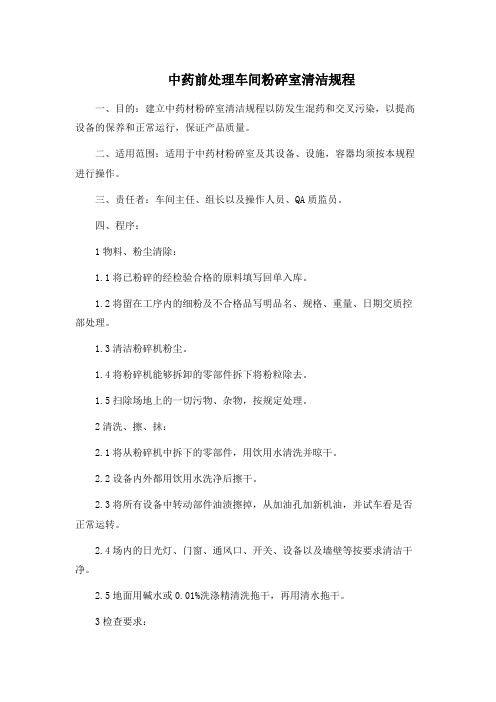
中药前处理车间粉碎室清洁规程
一、目的:建立中药材粉碎室清洁规程以防发生混药和交叉污染,以提高设备的保养和正常运行,保证产品质量。
二、适用范围:适用于中药材粉碎室及其设备、设施,容器均须按本规程进行操作。
三、责任者:车间主任、组长以及操作人员、QA质监员。
四、程序:
1物料、粉尘清除:
1.1将已粉碎的经检验合格的原料填写回单入库。
1.2将留在工序内的细粉及不合格品写明品名、规格、重量、日期交质控部处理。
1.3清洁粉碎机粉尘。
1.4将粉碎机能够拆卸的零部件拆下将粉粒除去。
1.5扫除场地上的一切污物、杂物,按规定处理。
2清洗、擦、抹:
2.1将从粉碎机中拆下的零部件,用饮用水清洗并晾干。
2.2设备内外都用饮用水洗净后擦干。
2.3将所有设备中转动部件油渍擦掉,从加油孔加新机油,并试车看是否正常运转。
2.4场内的日光灯、门窗、通风口、开关、设备以及墙壁等按要求清洁干净。
2.5地面用碱水或0.01%洗涤精清洗拖干,再用清水拖干。
3检查要求:
3.1地面应无积尘、无杂物、无死角并应拖干。
3.2日光灯、门窗、通风口、开关等应无积尘、污垢和水迹。
3.3工具和容器清洁后无杂物放入器具间。
3.4设备内外应无粒状、粉状等痕迹的异物。
3.5操作间内不应存放与生产无关的物品。
3.6清洁所用的工具:拖把、抹布、扫帚等,用后按规定清洗,并放入洁具间。
3.7清场完毕,当班应自查签名记录。
3.8组长检查复核后签名。
3.9QA质监员检查合格后发放清场合格证。
中药制药的前处理工艺技术
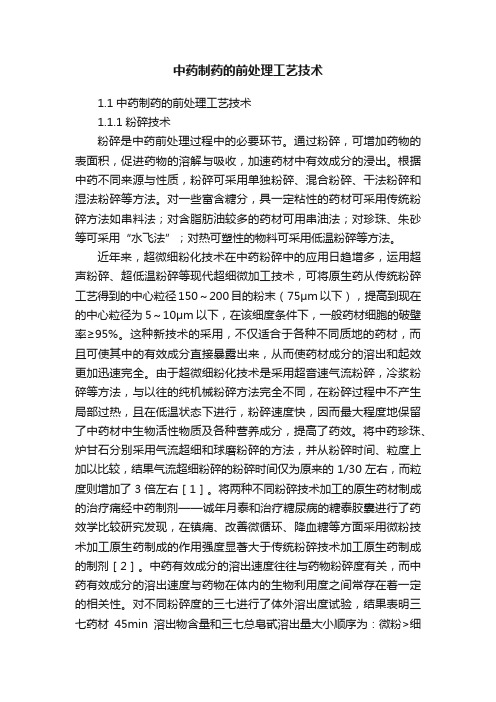
中药制药的前处理工艺技术1.1中药制药的前处理工艺技术1.1.1粉碎技术粉碎是中药前处理过程中的必要环节。
通过粉碎,可增加药物的表面积,促进药物的溶解与吸收,加速药材中有效成分的浸出。
根据中药不同来源与性质,粉碎可采用单独粉碎、混合粉碎、干法粉碎和湿法粉碎等方法。
对一些富含糖分,具一定粘性的药材可采用传统粉碎方法如串料法;对含脂肪油较多的药材可用串油法;对珍珠、朱砂等可采用“水飞法”;对热可塑性的物料可采用低温粉碎等方法。
近年来,超微细粉化技术在中药粉碎中的应用日趋增多,运用超声粉碎、超低温粉碎等现代超细微加工技术,可将原生药从传统粉碎工艺得到的中心粒径150~200目的粉末(75μm以下),提高到现在的中心粒径为5~10μm以下,在该细度条件下,一般药材细胞的破壁率≥95%。
这种新技术的采用,不仅适合于各种不同质地的药材,而且可使其中的有效成分直接暴露出来,从而使药材成分的溶出和起效更加迅速完全。
由于超微细粉化技术是采用超音速气流粉碎,冷浆粉碎等方法,与以往的纯机械粉碎方法完全不同,在粉碎过程中不产生局部过热,且在低温状态下进行,粉碎速度快,因而最大程度地保留了中药材中生物活性物质及各种营养成分,提高了药效。
将中药珍珠、炉甘石分别采用气流超细和球磨粉碎的方法,并从粉碎时间、粒度上加以比较,结果气流超细粉碎的粉碎时间仅为原来的1/30左右,而粒度则增加了3倍左右[1]。
将两种不同粉碎技术加工的原生药材制成的治疗痛经中药制剂——诚年月泰和治疗糖尿病的糖泰胶囊进行了药效学比较研究发现,在镇痛、改善微循环、降血糖等方面采用微粉技术加工原生药制成的作用强度显著大于传统粉碎技术加工原生药制成的制剂[2]。
中药有效成分的溶出速度往往与药物粉碎度有关,而中药有效成分的溶出速度与药物在体内的生物利用度之间常存在着一定的相关性。
对不同粉碎度的三七进行了体外溶出度试验,结果表明三七药材45min溶出物含量和三七总皂甙溶出量大小顺序为:微粉>细粉>粗粉>颗粒[3]。
医药原料无尘粉碎输送系统设计与探究

医药原料无尘粉碎输送系统设计与探究摘要:针对中小型制药企业现状,研究设计了医药原料无尘粉碎输送系统,此系统的特点是:实现自动上料、完全封闭的粉碎与输送、自动分装、自动称量的自动化系统,不仅能实现药品原料的无尘输送、提高药品的质量和精度,还能减轻员工的工作强度,对社会具有重要的现实意义。
关键词:无尘粉碎输送系统智能化据调查,目前在中小型制药企业中完全达到无污染、自动化的程度不是很高,物料加工生产有好多环节,一般用料斗或料桶运输进行干燥,干燥后,物料再用料斗或料桶运输至混合工序等。
在各工序之间物料需要有一个个周转料斗或料桶盛放并进行运输,在一个个物料装入倒出等过程中,很可能造成粉尘的飞扬,既浪费了物料,又污染了场地,还对工人的健康很不利。
与此同时,场地的清洁、料桶和运输设备的清洗,也给工作人员带来很大的工作量。
这就为企业生产高质量的药品带来了很多困难,由此可以看出,要尽量减少粉尘污染,使物料加工和各环节之间的运输的密闭是关键因素,让物料在各生产环节之间运输管道化。
这就要求中小型企业,结合自己的实际需要,认真设计出完全符合自己需要的设备,既要考虑经济条件的限制又要考虑场地的要求,常言说:适合的才是最好的,因此要求我们对本地某药厂进行适时的、合理的设计。
1 对目前存在问题的调查与分析:经过对部分药厂的调查,我们发现了以下几点问题。
(1)物料在传输过程中没有达到完全封闭,存在生产过程中人工配料和人工上料的生产方式,物料经过几个中间容器周转才能够用于下一步工序,这不仅增加了工人的劳动强度,增加了物料交叉污染的可能,还会造成大量的粉尘飞扬,污染环境,影响操作者的身体健康。
同时粉碎机在工作的时候会有一定的风量排出,这样在粉碎机的出料口处也会有粉尘扬起,物料与环境和操作人员存在接触,不能确保零泄漏、零污染,也不能有效地保护环境和操作人员的安全,在此情况下很有可能造成药物粉体物料原有特性发生改变。
(2)制药的整体系统智能化不强,原料的传输和每台设备上料还是手工操作,这样既增加了劳动的强度,又不能保证上料精度。
中药前处理

|
10
浓缩干燥技术
一是使药液快速流 过加热面进行蒸发。 如降膜式蒸发器、 刮板式薄膜蒸发器。
薄膜蒸发
二是使药液剧烈地沸 腾,产生大量泡沫, 以泡沫的内外表面为 蒸发面而进行蒸发。 如升膜式蒸发器。
|
11
带式干燥
超微粉碎技术
超微粉碎常有干法粉碎和湿法 粉碎之分。 根据粉碎过程中产生粉碎力
的原理不同,干法粉碎有气流式、
高频振动式、旋转球(棒)磨式、 锤击式和自磨式等几种形式。
超微粉碎技术 湿法粉碎主要是用胶体磨和均质 机粉碎,湿法粉碎是将原料悬浮于载 体液流(常用水)中进行粉碎。此法 可克服粉尘飞扬问题,并可采用淘析、 沉降或离心分离等水力分级方法分离
地保留粉体的生物活性成分,以利于制成所需的高质量产品。
(2)粒径细、分布均匀。由于采用超音速气流粉碎,其在
原料上外力的分布是很均匀的。分级系统的设置,既严格限 制了大颗粒,又避免了过碎,得到粒径分布均匀的超细粉, 同时很大程度上增加了微粉的比表面积,使吸附性、溶解性 等亦相应地增大。
超微粉碎技术的特点
|
12
沸腾干燥
工作原理:沸腾干燥又名流化干燥, 原理是利用从流化床底部吹入的热气 流使颗粒吹起悬浮,流化翻滚如“沸 腾状”,物料的跳动大大增加了蒸发 面,热气流在悬浮的颗粒间通过,在 动态下进行热交换,带走水分,达到 干燥目的。若采用减压沸腾干燥,干 燥效率更高。 特点:沸腾干燥效率高,速度快,干 燥均匀,产量大,适于大规模生产, 主要用于片剂、颗粒剂制备过程中的 制粒干燥,现也有报道用于丸剂的干 燥。
浸提技术
传统方法: 煎煮法 浸渍法 渗漉法 回流提取法 水蒸气蒸馏法
浅谈中药的粉碎方法及设备

浅谈中药的粉碎方法及设备粉碎是中药制剂的基础,中药材在制剂前大都要经过粉碎。
适宜的粉碎方法是保证制剂质量的前提之一。
现将传统中药粉碎四法介绍1.干法粉碎干法粉碎,也称常规粉碎,系指药物经过适当干燥处理后再进行粉碎。
例如用铁研船、球磨机、榔头机、万能粉碎机等进行粉碎,此法优点是操作简单,一次成粉,缺点是连续作业易产生热量而致燃。
在实际操作中据药物质地不同又分以下4种方法。
本文链接:(1)单独粉碎系指将一味药单独进行粉碎。
此法适用于树脂、胶质、贵重、毒剧及体积小的种子类药的粉碎。
(2)混合粉碎系指将处方中全部或部分药料掺合在一起进行粉碎。
适用于处方中质地相似的群药粉碎,此法可以避免咱些药物出于粘性或油性给粉碎过程所带来的困难。
如熟地、当归、杏十等药的粉碎。
(3)掺碾法又称串油,即将处方小“油性”大的药料先留下,将其他药物粉碎成粉,然后用此混合药粉陆续掺入台“油性,药料冉粉碎一次。
这样先粉碎的药物可及时将油性吸收,不粘着粉碎机与筛孔。
加火麻仁、杏仁、瓜萎仁、郁李仁等。
(4)串碾法又称串料,即将处方中“粘性”大的药料留下,先将其他药料混合粉碎成粗粉,然后用此混合药料陆续掺入合“粘性%药料,再行粉碎一次。
其“粘性”物质在粉碎过程中.及时被光粉碎的药粉分散并吸附.使粉碎和过筛得以顺利进行*例如生地、玄参、党参、龙眼肉等。
2湿法粉碎某些药物粉碎研磨时会粘结器具或再次聚结成块(如冰片),如在药物中加入适量水或其他液体进行9f原则易成细粉。
常用有研磨水飞法、湿法研磨法和共溶研磨法三种。
(1)研磨水飞法即利用药物的粗细粉末在水中悬浮性的不同来分离和提纯细粉,此法主要适用于某些不溶于水的矿物药及毒剧药。
如雄黄、朱砂、滑石、珍珠等药物。
(2)湿法研磨法又称加液研磨法G是将药物置于被湿润的粉碎容器中,或在药物上洒少许清水、乙醇或香油等再进行研磨粉碎,此法主要适用于一些干法粉碎易粘结成块的药物,如冰片、樟脑等。
(3)共溶研磨法当两种或更多种药物经混合研磨成细粉的过程中出现湿润或液化现象,称这种研磨成纫粉的方法为共溶研磨法。
中药GMP工厂 中药前处理车间粉碎岗位操作规程

中药前处理车间粉碎岗位操作规程
一、目的:掌握中药材粉碎操作规程。
二、适用范围:适用于药材粉碎岗位操作人员。
三、责任者:班组负责人、岗位操作人员、车间工艺员、QA质监员。
四、程序:
1根据生产计划,工艺员提前三天填写生产指令,检查生产所需中药材是否有检验报告单,并核对品名、批号等是否相符,检查外观质量,验收数量。
2除去药材中夹杂的异物、霉粒等,记录于批生产记录,然后称量物料,要进行复核。
3称量工具在使用前应校正,以求准确,称料时应做到取砝码时检查,称料时与记录核对,砝码还原时复查,使用后清洁干净,妥善保管。
4粉碎机开机前要对各部件进行检查。
把布袋扎紧在粉碎机出口处。
开机空转1-2分钟后,再投放药材,进行粉碎。
5开机时严禁异物如铁钉、镙丝、铁块等流入粉碎机内部,以防造成事故。
6每次粉碎药材后及时称重,真实记录,计算收率,交于下一工序。
并把粉碎机及室内打扫干净,清场。
7在更换品种前,要清场,原品种的药材全部进库,清洗粉碎机及集粉袋,打扫室内清洁卫生,经组长检查合格后才能更换。
8必须穿戴本岗位规定的工作服,才能进入生产区,不得穿离生产区。
粉碎操作时要带口罩。
9及时真实填写操作记录,要求填写字迹端正清晰,不得撕毁或任意涂改。
10下班前按工艺卫生要求进行清场打扫,下班时关闭门窗、水阀、电源开关等。
粉碎药材中药材粉碎标准
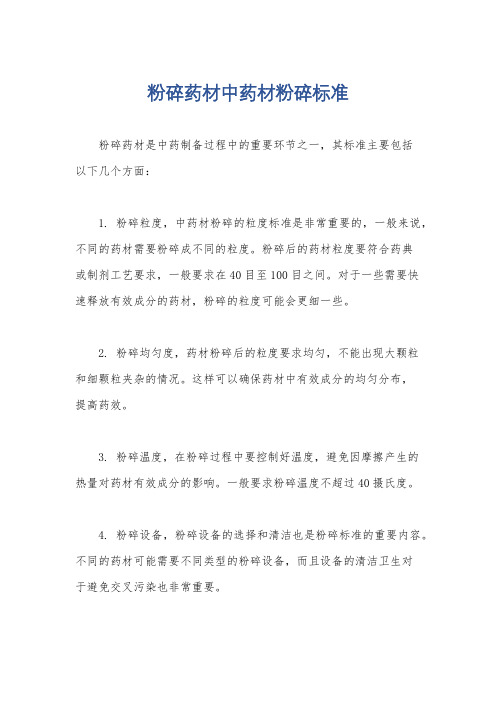
粉碎药材中药材粉碎标准
粉碎药材是中药制备过程中的重要环节之一,其标准主要包括
以下几个方面:
1. 粉碎粒度,中药材粉碎的粒度标准是非常重要的,一般来说,不同的药材需要粉碎成不同的粒度。
粉碎后的药材粒度要符合药典
或制剂工艺要求,一般要求在40目至100目之间。
对于一些需要快
速释放有效成分的药材,粉碎的粒度可能会更细一些。
2. 粉碎均匀度,药材粉碎后的粒度要求均匀,不能出现大颗粒
和细颗粒夹杂的情况。
这样可以确保药材中有效成分的均匀分布,
提高药效。
3. 粉碎温度,在粉碎过程中要控制好温度,避免因摩擦产生的
热量对药材有效成分的影响。
一般要求粉碎温度不超过40摄氏度。
4. 粉碎设备,粉碎设备的选择和清洁也是粉碎标准的重要内容。
不同的药材可能需要不同类型的粉碎设备,而且设备的清洁卫生对
于避免交叉污染也非常重要。
总的来说,粉碎药材的标准主要包括粉碎粒度、均匀度、温度和设备等方面的要求。
严格按照这些标准进行粉碎,可以确保中药制剂的质量和药效。
- 1、下载文档前请自行甄别文档内容的完整性,平台不提供额外的编辑、内容补充、找答案等附加服务。
- 2、"仅部分预览"的文档,不可在线预览部分如存在完整性等问题,可反馈申请退款(可完整预览的文档不适用该条件!)。
- 3、如文档侵犯您的权益,请联系客服反馈,我们会尽快为您处理(人工客服工作时间:9:00-18:30)。
系统设计和使用的要点
用一套真空负压管道装置将制粒 干燥、粉碎整粒、二维混合三个 工序连接起来,各个设备既能密 闭单独生产,又能在生产时封闭 传输物料,使整个工序连贯工作。
(1)解决粉碎拆粒时粉碎机尾风问题,粉碎 整粒能密闭生产。上料斗与粉碎机之间用 硬连接完全密闭,粉碎机所需空气由放空 阀提供,当出现粉碎机堵筛从放空阀反喷 时可以关闭放空阀及放料阀,消除堵筛现 象。在粉碎机下取消布袋连接至料桶的方 式,用硬连接的下料斗取代, 粉碎机所 需空气变为输送整粒后物料的所需空气, 下料斗要作技术处理使物料与空气作适度 分离,再用肘形阀连通,保证物料输送顺 畅,如此整粒过程完全密闭且在负压条件 下,没有粉尘的飞扬。用一套真空负压管 道装置将制粒干燥、粉碎拆粒、二维混合 连接起来实现管道化生产。
(4)过滤器:自动真空上料机的设置为抽料一段时 间后反吹过滤器再继续抽料,如此反复会造成整 粒过程不连续,而使粉碎机物料从放空阀反喷。 因而自动真空上料机必须设置为连续抽料,在这 种情况下,过滤器在停机时会反吹一次。上料斗 的容积必须根据此工况而决定,否则上料斗的容 积过大抽料能力不足,会造成恶性循环。为保险 起见对自动真空上料机进行改造:每一次操作后 对过滤器进行反吹,操作一次停机前自动对过滤 器进行多次反吹,确保自动真空上料机操作条件。 真空上料是利用真空上料机产生负压,负压带动 空气流动,空气流动引导物料运动,这个过程其 实就是空气传输,只不过是负压条件下的空气传 输,这样用作传输介质的空气必然带有大量的细 粉,因此,空气过滤是一个关键点,其作用是保 证整个生产过程内传输用的空气流量稳定在一定 的水平,以保证物料传输速度;并且换洗后能恢 复当初的通透量。购买多套过滤器作更换用,每 次更换的过滤器都使用超声波清洗,清洗后一定 要凉干,对恢复的空气通透量极为重要。
原创by 环球破碎机网: 如若转载请注明出处!!!谢 谢!!!
(2)上料斗作为负压载体最大真空度 达91%(-91kPa),刚性要足够。上 料斗的容量是由自动真空上料机的过 滤器性能而决定(在第4点过滤器内 表述)。最好是一炉干燥料对一个料 斗,否则要增加过滤器个数。上料斗 作为物料的载体,必须无堆积、无死 角,且易清洁,符合GMP要求。 (3)用一套真空负压管道装置将制粒 干燥、粉碎整粒、二维混合三个工序 连接起来,转换要方便,要用自动控 制。
ห้องสมุดไป่ตู้
(5)自动真空上料机的尾气排放要 出洁净区,以减小尾气对洁净区 空气洁净度以及操作室压差的影 响。
系统改造后的效能
(1)操作室地面无尘,同一个操作室内的二 维混合机表面无尘,粉碎机、回风过滤器上 滤布基本无尘。达到无尘粉碎及管道化输送 预期目的。 (2)压片制粒干燥混合工序的生产有了质的 提升,劳动生产率提高了二倍多,拆粒粉碎 生产速度比制粒干燥快。同时减少中间产品 的运输及污染,减轻操作人员的劳动强度; 极大地提高生产环境质量,解决了粉尘污染 问题。 (3)无尘粉碎为中药材前处理的粉碎工序的 技术改造提供坚实的基础。