制粒工艺过程的水分控制
制粒工艺过程水分的控制

制粒工艺过程水分的控制1、水分控制目的优化蒸汽湿热处理条件,以提高颗粒饲料质量,降低加工成本,并减少环模/压辊磨损。
在蒸汽湿热处理前混合物水分较低,给粉料添加少量的水,有利于蒸汽处理中的热传导,从而降低电力消耗,提高生产效率,改进颗粒饲料质量。
2、水分控制原则(1)进厂原料的水分检验,看是否符合饲料原料质量标准。
(2)检测每班生产的首批混合粉料(混合机内的混合粉料)的初始水分(蒸汽处理之前)。
另一个办法,是根据日粮各种原料的水分(蒸汽处理之前)。
如果该粉料水分低于13%,在混合时给粉料喷添适当数量的水分,所添加的水分可以促进热传导,从而改进蒸汽处理和制粒作业。
如果粉料初始水分已达13%或更高,则不要添加水分。
(3)目标温度。
多数情况下,混合粉料温度(制粒之前)越高,颗粒饲料质量越好,电力消耗越少,机器磨损也越小。
常规制粒条件下,可以达到的最高混合粉料温度受制于混合物料的初始温度和能给混合料注入多少蒸汽。
根据经验,凝结1%优质蒸汽(饱和干蒸汽)可使混合物料升温15 ℃。
蒸汽处理后的混合粉料水分可以增加到16.5—17%。
因此,多数情况下混合粉料温度升幅可达到45℃(注入大约3%的蒸汽)。
譬如说,混合物料初始温度是30℃,蒸汽处理后物料温度应达到75℃。
如果达不到这个目标温度,则应检查蒸汽中是否含水(湿蒸汽)。
(4)控制最终产品水分。
对大多数制粒产品来说,最大水分最好设定在12.5%。
任何时候最终产品水分都不应超过13%,否则可能发霉,特别是暖季。
当混合粉料初始水分低于12.5%时,目标水分应设定在高于初始水分2%,而不是12.5%。
(5)要检测最终产品水分,在每种日粮每批生产初期更要检查,根据检测结果调整冷却器停留时间以达到目标水分。
如果已经没有调节余地而最终产品水分仍然过高的话,为了让最终产品水分降到目标水分,在并未向混合机加水的情况下,则只能减少蒸汽用量从而降低混合粉料的温度。
这是不得已的办法。
挤压制粒工艺流程
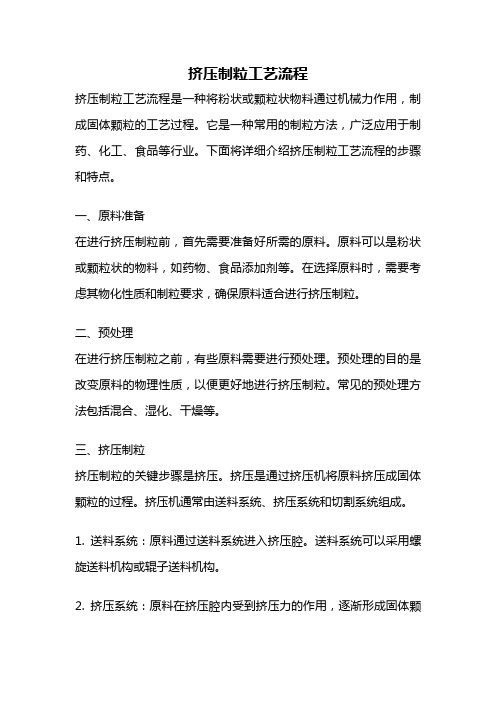
挤压制粒工艺流程挤压制粒工艺流程是一种将粉状或颗粒状物料通过机械力作用,制成固体颗粒的工艺过程。
它是一种常用的制粒方法,广泛应用于制药、化工、食品等行业。
下面将详细介绍挤压制粒工艺流程的步骤和特点。
一、原料准备在进行挤压制粒前,首先需要准备好所需的原料。
原料可以是粉状或颗粒状的物料,如药物、食品添加剂等。
在选择原料时,需要考虑其物化性质和制粒要求,确保原料适合进行挤压制粒。
二、预处理在进行挤压制粒之前,有些原料需要进行预处理。
预处理的目的是改变原料的物理性质,以便更好地进行挤压制粒。
常见的预处理方法包括混合、湿化、干燥等。
三、挤压制粒挤压制粒的关键步骤是挤压。
挤压是通过挤压机将原料挤压成固体颗粒的过程。
挤压机通常由送料系统、挤压系统和切割系统组成。
1. 送料系统:原料通过送料系统进入挤压腔。
送料系统可以采用螺旋送料机构或辊子送料机构。
2. 挤压系统:原料在挤压腔内受到挤压力的作用,逐渐形成固体颗粒。
挤压腔内的温度、压力和转速等参数需要根据原料的性质和制粒要求进行调节和控制。
3. 切割系统:挤压后的颗粒通过切割系统进行切割。
切割系统可以采用切割刀、切割板等形式,将挤压出的长条状颗粒切割成所需长度的颗粒。
四、干燥挤压制粒后的颗粒含有一定的水分,需要进行干燥处理。
干燥的目的是去除颗粒中的水分,提高颗粒的稳定性和质量。
常用的干燥方法包括自然风干、烘箱干燥、流化床干燥等。
五、筛分和包装经过干燥处理后的颗粒需要进行筛分和包装。
筛分是将颗粒按照一定的粒径范围进行分级,得到所需的颗粒尺寸。
包装是将制粒好的颗粒按照一定的重量或容量进行包装,以便存储和销售。
挤压制粒工艺流程的特点:1. 操作简单:挤压制粒工艺流程相对简单,操作方便,适用于大批量生产。
2. 颗粒均匀:挤压制粒能够使原料均匀地分布在挤压腔内,从而制得颗粒均匀、一致。
3. 粒径可调:通过调节挤压机的参数,可以控制颗粒的粒径范围,满足不同的制粒要求。
4. 节能环保:挤压制粒过程中不需要加热和添加溶剂,能够节约能源,减少环境污染。
制粒工艺过程的水分控制
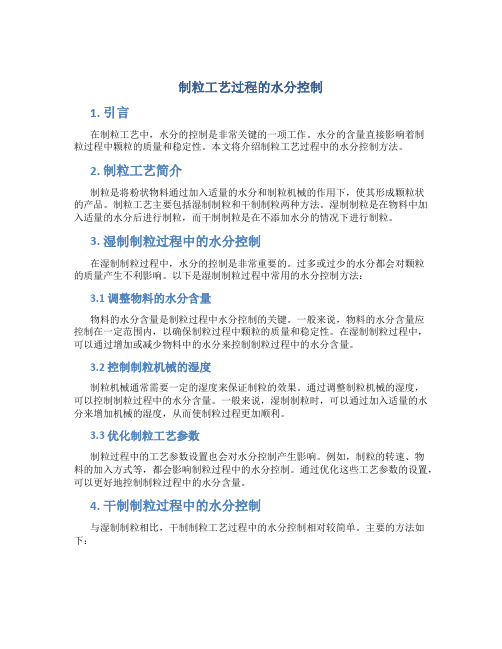
制粒工艺过程的水分控制1. 引言在制粒工艺中,水分的控制是非常关键的一项工作。
水分的含量直接影响着制粒过程中颗粒的质量和稳定性。
本文将介绍制粒工艺过程中的水分控制方法。
2. 制粒工艺简介制粒是将粉状物料通过加入适量的水分和制粒机械的作用下,使其形成颗粒状的产品。
制粒工艺主要包括湿制制粒和干制制粒两种方法。
湿制制粒是在物料中加入适量的水分后进行制粒,而干制制粒是在不添加水分的情况下进行制粒。
3. 湿制制粒过程中的水分控制在湿制制粒过程中,水分的控制是非常重要的。
过多或过少的水分都会对颗粒的质量产生不利影响。
以下是湿制制粒过程中常用的水分控制方法:3.1 调整物料的水分含量物料的水分含量是制粒过程中水分控制的关键。
一般来说,物料的水分含量应控制在一定范围内,以确保制粒过程中颗粒的质量和稳定性。
在湿制制粒过程中,可以通过增加或减少物料中的水分来控制制粒过程中的水分含量。
3.2 控制制粒机械的湿度制粒机械通常需要一定的湿度来保证制粒的效果。
通过调整制粒机械的湿度,可以控制制粒过程中的水分含量。
一般来说,湿制制粒时,可以通过加入适量的水分来增加机械的湿度,从而使制粒过程更加顺利。
3.3 优化制粒工艺参数制粒过程中的工艺参数设置也会对水分控制产生影响。
例如,制粒的转速、物料的加入方式等,都会影响制粒过程中的水分控制。
通过优化这些工艺参数的设置,可以更好地控制制粒过程中的水分含量。
4. 干制制粒过程中的水分控制与湿制制粒相比,干制制粒工艺过程中的水分控制相对较简单。
主要的方法如下:4.1 控制物料的初始水分含量在干制制粒过程中,物料的初始水分含量是影响制粒质量的重要因素。
过高的水分含量会导致颗粒结块、不易干燥,而过低的水分含量则会导致制粒困难。
因此,在干制制粒过程中,需要准确控制和调整物料的初始水分含量。
4.2 优化干制制粒机械在干制制粒过程中,采用适用的制粒机械也能对水分控制起到一定的作用。
例如,通过调整干制制粒设备的温度和湿度,可以调控制粒过程中的水分含量。
烧结球团工艺流程
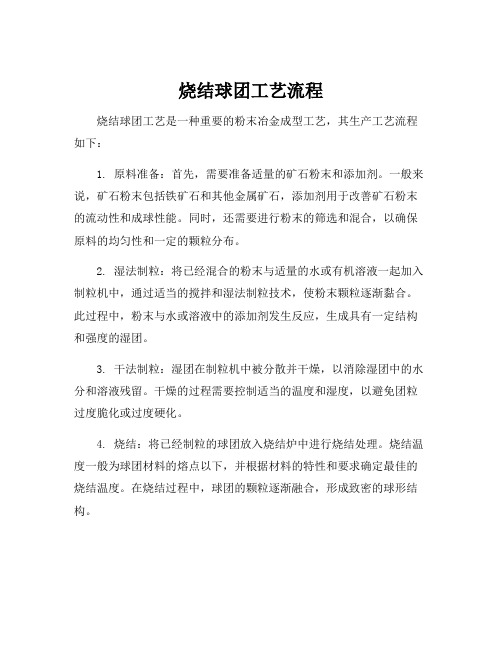
烧结球团工艺流程烧结球团工艺是一种重要的粉末冶金成型工艺,其生产工艺流程如下:1. 原料准备:首先,需要准备适量的矿石粉末和添加剂。
一般来说,矿石粉末包括铁矿石和其他金属矿石,添加剂用于改善矿石粉末的流动性和成球性能。
同时,还需要进行粉末的筛选和混合,以确保原料的均匀性和一定的颗粒分布。
2. 湿法制粒:将已经混合的粉末与适量的水或有机溶液一起加入制粒机中,通过适当的搅拌和湿法制粒技术,使粉末颗粒逐渐黏合。
此过程中,粉末与水或溶液中的添加剂发生反应,生成具有一定结构和强度的湿团。
3. 干法制粒:湿团在制粒机中被分散并干燥,以消除湿团中的水分和溶液残留。
干燥的过程需要控制适当的温度和湿度,以避免团粒过度脆化或过度硬化。
4. 烧结:将已经制粒的球团放入烧结炉中进行烧结处理。
烧结温度一般为球团材料的熔点以下,并根据材料的特性和要求确定最佳的烧结温度。
在烧结过程中,球团的颗粒逐渐融合,形成致密的球形结构。
5. 冷却:烧结完成后,将球团从烧结炉中取出并迅速冷却。
此过程可以通过自然冷却或使用冷却设备来实现。
冷却过程中,球团的温度逐渐降低,使其结构更加稳定和坚固。
6. 筛分和包装:经过冷却的球团经过筛分,将不符合规格的球团重新破碎与再制粒,符合规格的球团进行必要的包装和标识。
同时,还需对产品进行质量检查,确保产品达到指标要求。
烧结球团工艺流程的实施需要注意以下几点:1. 原料的选择和准备是保证产品质量的关键。
需要选择高质量的矿石粉末和合适的添加剂,并进行充分的筛选和混合,以确保原料的均匀性和颗粒分布。
2. 制粒过程需要控制适当的湿度和搅拌强度,以确保粉末颗粒的黏结和团粒的形成。
同时,制粒后的干燥也需要控制适当的温度和湿度,避免团粒过度脆化或过度硬化。
3. 烧结条件的选择要考虑材料的熔点和烧结性能,以确保球团的致密性和强度。
同时,烧结过程中的温度和时间也需要精确控制,以避免烧结不完全或过度烧结。
4. 冷却过程需要迅速进行,以避免球团受热应力影响产生开裂和变形。
湿法制粒的工艺流程

湿法制粒的工艺流程
《湿法制粒的工艺流程》
湿法制粒是一种常用的制粒工艺,在化工、食品、医药等行业中广泛应用。
其工艺流程一般包括以下几个步骤:
1. 原料准备:首先需要准备好所需的原料,包括主要成分以及辅助成分。
这些原料需要按照一定的配方和比例进行混合,以满足产品的要求。
2. 湿混合:将原料加入到混合机中进行湿混合,加入适量的溶剂或添加剂,使得原料颗粒间相互粘合,形成颗粒结构。
3. 初次制粒:湿混合后的原料送入制粒机中,通过挤压、剪切或者滚动的方式进行初次制粒,使得原料形成较大的颗粒结构。
4. 干燥:将初次制粒后的颗粒送入干燥设备中,通过热风或者真空手段将颗粒中的水分蒸发掉,使得颗粒表面变得干燥。
5. 再制粒:干燥后的颗粒再次送入制粒机中进行再次制粒,使得颗粒的形态更加均匀和稳定。
6. 筛分:对再制粒后的颗粒进行筛分,去除不合格的颗粒,保留符合要求的颗粒作为成品。
7. 包装:最后将成品颗粒通过包装设备进行包装,以便于运输和销售。
湿法制粒的工艺流程可以根据不同产品的要求进行调整和改进,但以上步骤是基本的操作流程。
通过严格的操作控制和技术改进,可以生产出优质的颗粒制品,满足市场的需求。
顶喷制粒工艺控制
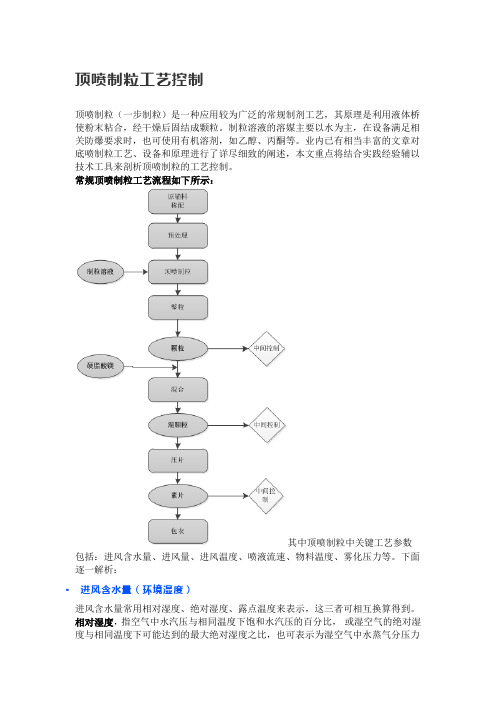
顶喷制粒工艺控制顶喷制粒(一步制粒)是一种应用较为广泛的常规制剂工艺,其原理是利用液体桥使粉末粘合,经干燥后固结成颗粒。
制粒溶液的溶媒主要以水为主,在设备满足相关防爆要求时,也可使用有机溶剂,如乙醇、丙酮等。
业内已有相当丰富的文章对底喷制粒工艺、设备和原理进行了详尽细致的阐述,本文重点将结合实践经验辅以技术工具来剖析顶喷制粒的工艺控制。
常规顶喷制粒工艺流程如下所示:其中顶喷制粒中关键工艺参数包括:进风含水量、进风量、进风温度、喷液流速、物料温度、雾化压力等。
下面逐一解析:▪进风含水量(环境湿度)进风含水量常用相对湿度、绝对湿度、露点温度来表示,这三者可相互换算得到。
相对湿度,指空气中水汽压与相同温度下饱和水汽压的百分比,或湿空气的绝对湿度与相同温度下可能达到的最大绝对湿度之比,也可表示为湿空气中水蒸气分压力与相同温度下水的饱和压力之比。
绝对湿度,指每单位容积的气体所含水分的重量,常用单位为g/kg或mg/L。
露点温度,指空气在水汽含量和气压都不改变的条件下,冷却到饱和时的温度。
形象地说,就是空气中的水蒸气变为露珠时候的温度叫露点温度。
目前已有便捷的空气焓湿计算APP可实现上述3个参数的换算。
(图例:在海拔高度为10m,干球温度即气温为25℃,相对湿度为65%时,空气中含水量为12.9208g/kg,露点温度为18.0℃)有文献报道,环境湿度增加,物料温度线性增加,原因是湿空气加热能力大于干空气。
与湿空气条件下制得的颗粒相比,干空气条件下制得的颗粒偏细,主要原因是液-固之间的联结减少最终引起颗粒间固-固的联结也减少。
在流化床进风处理单元可通过表冷除湿、冷冻除湿、转轮除湿或联用等方式来实现目标进风含水量的控制,以使其符合工艺要求。
表冷除湿常规可控制进风含水量在10g/kg以内,冷冻除湿和转轮除湿常规可控制进风含水量在3g/kg以内,1g/kg以内也能实现但是经济效益相对较差且顶喷制粒工艺通常不需要控制到这么低的进风含水量。
生物饲料的生产工艺

生物饲料的生产工艺生物饲料的生产工艺是指将各种原料经过一系列工艺处理和技术调控,最终制成适合动物饲养的饲料产品的过程。
下面以鱼饲料的生产工艺为例,简要介绍一下典型的生物饲料生产工艺。
第一步是原料的准备和混合。
鱼饲料的主要原料包括鱼粉、豆粕、玉米、小麦等。
这些原料需要按照一定的配方比例称量,并进行预处理。
例如,将鱼粉、豆粕等粉状原料进行筛分和研磨,玉米等颗粒状原料进行破碎和清洗等。
然后将各种原料按照一定的比例放入混合机进行充分混合,确保各种成分均匀分布。
第二步是造粒。
将混合好的原料送入制粒机,通过机械挤压和摩擦的作用进行造粒。
在这个过程中,适当添加一些辅料和添加剂,如脂肪、维生素、氨基酸等,以提高饲料的营养价值和可消化性等。
制粒过程中需要控制好湿度和温度,使得原料能够在适当的状态下形成均匀且有一定机械强度的颗粒。
第三步是干燥和冷却。
造粒后的饲料颗粒还含有一定的水分,需要进行干燥处理以提高饲料的保存性和质量稳定性。
一般采用流化床干燥机进行干燥,将湿饲料颗粒在高温高湿气流中进行快速干燥,使水分含量降到适当的水平。
干燥后的饲料颗粒还需要通过冷却机进行降温处理,使其温度适宜存储和包装。
第四步是包装和储存。
经过干燥和冷却的饲料颗粒一般需要通过振动筛分和除尘器进行筛分和除尘处理,去除杂质和细粉,然后进行包装。
常见的包装方式有散装和袋装两种,根据市场需求选择不同的包装方式。
最后,将包装好的饲料产品存放在干燥通风、阴凉干燥的仓库中,以保持其质量和营养成分。
综上所述,生物饲料的生产工艺是一个涉及原料准备、混合、造粒、干燥、冷却、包装和储存等一系列工序的过程。
通过科学合理地控制各个环节和采用适当的加工技术,可以制备出营养丰富、适口性好、质量稳定的生物饲料产品,满足不同动物的饲养需求。
干法制粒的工艺流程
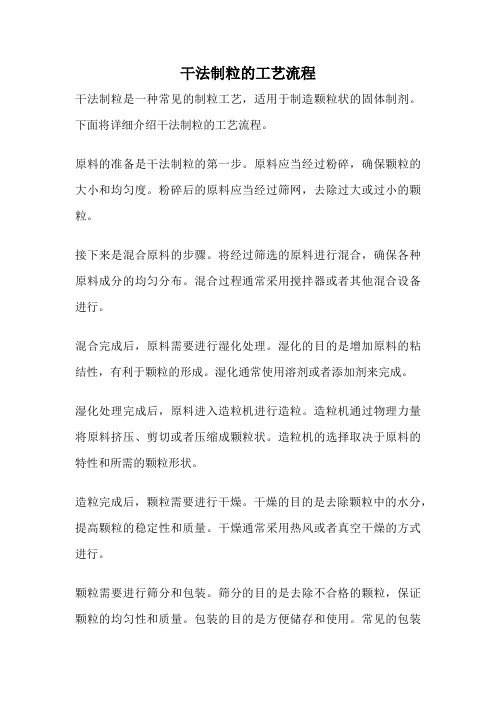
干法制粒的工艺流程
干法制粒是一种常见的制粒工艺,适用于制造颗粒状的固体制剂。
下面将详细介绍干法制粒的工艺流程。
原料的准备是干法制粒的第一步。
原料应当经过粉碎,确保颗粒的大小和均匀度。
粉碎后的原料应当经过筛网,去除过大或过小的颗粒。
接下来是混合原料的步骤。
将经过筛选的原料进行混合,确保各种原料成分的均匀分布。
混合过程通常采用搅拌器或者其他混合设备进行。
混合完成后,原料需要进行湿化处理。
湿化的目的是增加原料的粘结性,有利于颗粒的形成。
湿化通常使用溶剂或者添加剂来完成。
湿化处理完成后,原料进入造粒机进行造粒。
造粒机通过物理力量将原料挤压、剪切或者压缩成颗粒状。
造粒机的选择取决于原料的特性和所需的颗粒形状。
造粒完成后,颗粒需要进行干燥。
干燥的目的是去除颗粒中的水分,提高颗粒的稳定性和质量。
干燥通常采用热风或者真空干燥的方式进行。
颗粒需要进行筛分和包装。
筛分的目的是去除不合格的颗粒,保证颗粒的均匀性和质量。
包装的目的是方便储存和使用。
常见的包装
方式有袋装、瓶装等。
通过以上的工艺流程,干法制粒可以将原料制成颗粒状的固体制剂。
这种制粒方法具有工艺简单、成本低廉、生产效率高等优点,被广泛应用于制药、化工、冶金等领域。
希望以上的介绍能够帮助您对干法制粒的工艺流程有更加深入的了解。
- 1、下载文档前请自行甄别文档内容的完整性,平台不提供额外的编辑、内容补充、找答案等附加服务。
- 2、"仅部分预览"的文档,不可在线预览部分如存在完整性等问题,可反馈申请退款(可完整预览的文档不适用该条件!)。
- 3、如文档侵犯您的权益,请联系客服反馈,我们会尽快为您处理(人工客服工作时间:9:00-18:30)。
蒸汽表
压力
kg/cm2
over
总热 kcal/kg - - - 531 526 521 517 643 646 648 651
温度
0
表观热 潜热
Fuel Type
• 锅炉的功率或供气量要留有余地
Boiler Size: Leave sufficient room
• 尽可能缩短锅炉与用汽设施之间的距离
Location of the boiler: close to the pellet mill
输汽管道内径的确定
Sizing the Pipe ID (cm) = W x 3.53 v/30 W=蒸汽流量 (Steam flow),kg/min v=给定气压下的比体积 (Specific volume under given steam pressure),m3/kg (查表) 30 = 最大流速 (allowed steam flow velocity),m/s
• 一般推荐: 3.5-4:1
General Recommendation: 3-4 to 1
进入调制室的蒸汽压力设定
Steam Pressure Setting before Conditioner
• 调制时间短,蒸汽质量好,宜采用低蒸汽压 (1.5 -0.5 kg /cm2 或 更 低), 以争取热 交换时间(并降低能耗).
影响颗粒稳定度的因素
粉碎粒度 20%
调制 20%
环模 15%
配方/原料 40%
冷却 5%
蒸汽调制的关键
• 蒸汽质量:什么是蒸汽质量?如何得到
高质量蒸汽
• 根据饲料类型和调制时间长短正确设定
调制气压 • 原料与成品水分控制
蒸汽调制过程的热交换
• 蒸汽热量的组成:表观热与潜热
• 潜热---物料升温的主要热量来源:
Low pressure (0.5-1.5 kg/cm2) is preferred if retention time is short (20 sec or less).
• 调制时间长,可采用较高蒸汽压力。
Higher pressure works well (2-4 kg/cm2) if retention time is long (40 sec or more).
• 夹层(间接)蒸器的作用
The role of indirect steam .
Extending Retention Time by Adjusting Pitch Angle
• Mash fill before adjustment
•thermomet er
Conditioner Paddle Pitch Adjustment (Top View)
• 疏水阀应不时启闭使一定压力下的凝积 水移到常压的回收系统且不丢失蒸気.
It must periodically open and close to allow the pressurized condensate to be removed in to an atmospheric condensate return system without losing steam.
Keep mash temperature≤700C to avoid moisture increase caused stickiness
• 可考虑采用较高蒸汽压力甚至过热蒸汽
Higher steam pressure - low steam flow, or supper heated steam may help
• 对于一般饲料配方,应在不塞机的前提下,尽 可能提高料温.
In general, mash temperature should be conditioned “as high as possible” before reaching the “chock point”.
减压前后的压力比
Pressure Ratio before –after Pressure Reducing Valve
Moisture adjusted mash weight in conditioner, kg
P = 产量, MT/h
Production rate, MT/h
蒸汽调制时间
Retention Time
• 延长常规调制器调制时间的简易办法: 通过调节 浆片角度提高物料在调制器内的充满度.
Extending Retention Time by Adjusting Pitch Angle
Good separator can remove more than 98% of the water drip-lets
疏水阀
Check Valve
• 其功能为将凝积水(在进入调制器前)从 蒸汽系统中排出.
To remove water condensate out of the steam system (before the steam going into the conditioner).
Mash Fill after Adjustment
延长调制时间的设备
• 多层调制器 • 可变仰角调制器
• 熟化调制器
Ripenner
• DDC
制粒过程的自动控制
• 料流控制 • 蒸汽流控制 • 料温反馈控制,电流反馈控制
常规蒸汽调制的局限性
Limits to Traditional Steam Conditioning
• 减压有助于提高蒸汽质量.
Pressure reduction helps improving steam quality.
• 减压(稳压)器的主要参数:流量、调压范围及控 制的稳定性(可用变异系数度量).
Parameters for consideration: Maximum flow (kg/hour), pressure range, pressure stability (expressed as CV%).
What’sPellets -
制粒工艺过程的水分控制
控制关键点
• 调制前粉料水分: 水分低于12%在混合物机 加水(一般不超过一个百分点)
• 调制后水分可通过料温上升估测
• 成品水分: 通过冷却时间-料层高度调节
关键设备
• 以电容为基础的快速水分测定器: –不需样品粉碎 –不需称量 –测定误差不超过0.5百分数单位 –手工操作系统,六秒中得结果,电脑自 动监测系统,每秒20个以上读数
–每凝结一个百分数单位的优质蒸汽,物料
温度大约上升 15 0C
• 蒸汽表
• 蒸汽质量
蒸汽表
压力
kg/cm2
over
总热 kcal/kg - - - 531 526 521 517 643 646 648 651
温度
0
表观热 潜热
----
C
0.5 1.0 1.5 2.0
112 120 127 134
-
蒸汽调制系统参数的设定
Parameter Settings in Steam Conditioning
• 考虑因素:调制时间、蒸汽质量、饲料配方.
Factors to be considered: Retention time, steam quality and formulation/ingredients.
气水分离器
Steam Separator • 根据机械原理将蒸汽中的水滴与蒸气分 开以得到优质蒸汽.
Using a mechanical advice to remove water driplets from the steam and obtain high quality steam.
• 好的气水分离器可移走98%的水滴.
• 关键在于有足够时间完成热交换-释放潜热.
The key is to give sufficient time for heat transfer releasing latent heat.
高乳清粉乳猪料蒸汽参数的设定
Steam Setting for High Whey Diet
• 调制温度≤700C 以控制水分避免塞机
• 调制器操作与流量应是线性关系.
A linear response is required between control valve and steam flow.
• 一般的控制阀的操作与实际流量不是线性关系.
The gate valve is non-linear - at half opening, small changes in setting results large steam flow variation.
Cospect Valve
• 减压、分水、气压控制三合一
A separator - trap - pressure regulator “three in one”device.
• 流量控制阀在自动和手动控制条件下均与 流量呈线性关系.
Linear steam flow control valves for both manual and automatic control system
112 120 127 134
蒸汽质量
• 湿蒸汽-蒸汽中含液态水, 热量低,易堵 塞模孔
• 蒸汽质量可用气态水在蒸汽中的百分数来 表示 • 测定蒸汽质量的方法
• 过热蒸汽或不饱和蒸汽
• 判定过热蒸汽的方法
• 理想的蒸汽:100%饱和蒸汽
蒸汽质量的计算
蒸汽质量% ={[(W2xT2-W1xT1)/(W2-W1)-Hf]/Hfg}x100%