风电叶片-玻璃纤维
风电叶片铺布工艺
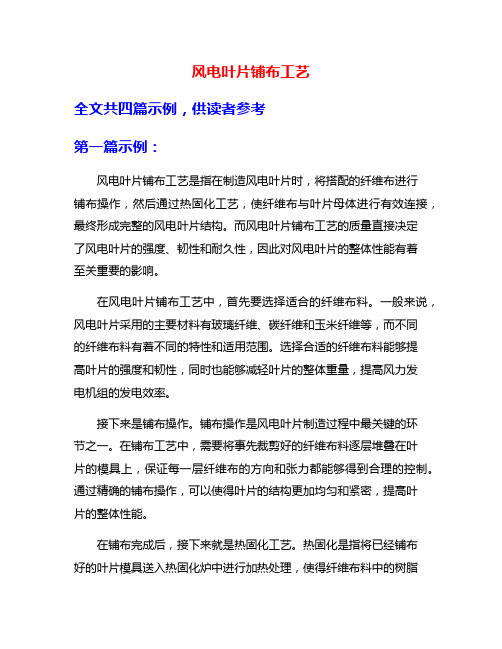
风电叶片铺布工艺全文共四篇示例,供读者参考第一篇示例:风电叶片铺布工艺是指在制造风电叶片时,将搭配的纤维布进行铺布操作,然后通过热固化工艺,使纤维布与叶片母体进行有效连接,最终形成完整的风电叶片结构。
而风电叶片铺布工艺的质量直接决定了风电叶片的强度、韧性和耐久性,因此对风电叶片的整体性能有着至关重要的影响。
在风电叶片铺布工艺中,首先要选择适合的纤维布料。
一般来说,风电叶片采用的主要材料有玻璃纤维、碳纤维和玉米纤维等,而不同的纤维布料有着不同的特性和适用范围。
选择合适的纤维布料能够提高叶片的强度和韧性,同时也能够减轻叶片的整体重量,提高风力发电机组的发电效率。
接下来是铺布操作。
铺布操作是风电叶片制造过程中最关键的环节之一。
在铺布工艺中,需要将事先裁剪好的纤维布料逐层堆叠在叶片的模具上,保证每一层纤维布的方向和张力都能够得到合理的控制。
通过精确的铺布操作,可以使得叶片的结构更加均匀和紧密,提高叶片的整体性能。
在铺布完成后,接下来就是热固化工艺。
热固化是指将已经铺布好的叶片模具送入热固化炉中进行加热处理,使得纤维布料中的树脂在高温下熔化,进而与叶片母体进行有效连接,最终形成坚固的叶片结构。
而热固化工艺的控制也是十分关键的,过高或者过低的温度都可能导致叶片的质量问题,因此需要在生产过程中进行精确的温度控制和监测,以确保叶片的质量和性能。
除了上述的主要工艺环节外,风电叶片铺布工艺中还包括了一系列的辅助工艺,如真空吸附、压延和修整等。
这些辅助工艺的目的是进一步提高叶片的质量和性能,确保叶片能够在恶劣的环境条件下具有较好的耐久性和稳定性。
风电叶片铺布工艺是风力发电行业中至关重要的一环,其质量和工艺水平直接关系到整个风力发电机组的发电效率和稳定性。
随着风力发电技术的不断发展和完善,风电叶片铺布工艺也在不断进步和改进,以满足日益增长的市场需求和技术要求。
相信随着技术的进步和工艺的提升,风电叶片铺布工艺将会更加完善,为清洁能源的发展做出更大的贡献。
风电叶片用玻纤材料解决方案

快速灌注与固化 提高生产效率
降低叶片生产成本
二、风电用聚氨酯玻纤介绍-性能
聚氨酯织物性能
PU与EP静态力学性能对比
添加 Items
0° tensile
90°tensile
0° compression
90° compression
Resin
PU EP PU EP PU EP PU EP
Wf
73.35 73.2 77.1 73.6 77.1 73.4 77.6 73.2
二、风电用聚氨酯玻纤介绍-FWF
聚氨酯叶片玻纤含量高,每只叶片减少树脂用量约240kg
添加
每只叶片节约 树脂约240kg
叶片主梁
~树脂节约200kg
叶片腹板
~树脂节约20kg
叶片叶根
~树脂节约20kg
叶片主梁 EP PU
叶片重量 5075kg 4877kg
FWF 74% 77%
叶片腹板 EP PU
添加
三、新一代高模风电环氧玻纤产品—老化性能
添加
Roving Result For 0,3,6,9,12,18 months aged (10℃ ~35℃,50%~90% Humidity
Natural environment of Chongqing )
Aging at 18 months, the performance decreases by less than 10%
三、新一代高模风电环氧玻纤产品—老化性能
添加
EKU1200 Fabric Result For 0,3,6,9,12,18 months aged (10℃ ~35℃,50%~90% Humidity
Liquid
风电叶片基础知识之复合材料篇三

2) 热固性玻璃钢 它是由60%~70%玻璃纤维(或玻璃布)和30%~40%热固性树脂 (环氧、聚酯树脂等)组成。 主要优点:密度小、强度高,耐蚀性、绝缘性、绝热性好;吸 水性、防磁、微波穿透性好,易于加工成型。 缺点:弹性模量低,热稳定性不高,只能在300℃以下工作。
(2)碳纤维―树脂复合材料 最常用的是碳纤维与聚酯、酚醛、环氧、聚四氟乙烯等树脂组 成的复合材料,具有高强度、高弹性模量、高比强度和比模量,还 具有优良的抗疲劳性能、耐冲击性能、自润滑性、减摩耐磨性、耐 蚀性及耐热性。缺点是纤维与基体结合力低。 (3)硼纤维―树脂复合材料 主要由硼纤维与环氧、聚酰亚胺等树脂组成。具有高的比强度、 比模量,良好的耐热性。其缺点是各向异性明显。 (4)碳化硅纤维树脂复合材料 由碳化硅纤维与环氧树脂组成的复合材料,具有高的比强度、 比模量。 (5)Kevlar纤维树脂复合材料 由Kevlar纤维与环氧、聚乙烯、聚碳酸酯、聚酯等树脂组成。 主要性能特点是抗拉强度大于玻璃钢,而与碳纤维―环氧树脂复合 材料相似;延性好,与金属相当;其耐冲击性超过碳纤维增强塑料; 其疲劳抗力高于玻璃钢和铝合金;减振能力为钢的8倍。
风电叶片基础知识之复合材料 篇三
6.3
1.常用增强纤维
常用的复合材料
一、纤维增强复合材料
主要有玻璃纤维、碳纤维、硼纤维、碳化硅纤维、Kevlar有机 物纤维等。
玻璃纤维布
玻璃纤维绳
玻璃纤维绳
纳 米 碳 管 纤 维 玻璃纤维纸
碳 纤 维 绳
(1)玻璃纤维 按玻璃纤维中 Na2O 和 K2O 的含量不同,可将其分为无碱纤维 (碱的质量分数<2%)、中碱纤维(碱的质量分数为2%~12%)、高 碱纤维(碱的质量分数>12%)。随着碱量的增加,玻璃纤维的强度、 绝缘性、耐蚀性降低。 特点:强度高,抗拉强度可达 1000 ~3000MPa ;弹性模量比金 属低得多,为( 3 ~ 5 )×104MPa ;密度小,为 2.5 ~ 2.7g/cm3 ;化 学稳定性好;不吸水、不燃烧、尺寸稳定、隔热、吸声、绝缘等。 缺点:脆性较大、耐热性低,250℃以上开始软化。 优点:价格便宜、制作方便
风电叶片用玻纤材料解决方案

风电叶片用玻纤材料解决方案近年来,风电产业得到了迅猛发展,成为清洁能源的重要组成部分。
而在风力发电系统中,风电叶片作为关键组件,承担着将风能转化为电能的重要任务。
然而,风电叶片的材料选择一直以来都是一个令人关注的问题。
为了提高叶片的强度和轻量化,纤维复合材料逐渐成为风电叶片的首选材料之一。
本文将介绍一种常见的风电叶片用玻璃纤维材料解决方案,以及其优势与应用。
一、玻璃纤维材料的特点玻璃纤维是一种常见的纤维增强复合材料,其主要成分是硅酸盐。
它具有重量轻、强度高、耐腐蚀性强等特点。
此外,玻璃纤维还具有优良的电绝缘性能和耐高温性能,能够适应风电叶片在各种恶劣环境下的使用要求。
二、玻璃纤维材料在风电叶片中的应用风电叶片的设计和制造需要兼顾强度和重量的平衡。
玻璃纤维材料作为一种轻质、高强度的材料,其应用在风电叶片中具有以下优势:1. 强度高:玻璃纤维材料具有较高的抗拉强度和抗压强度,能够承受较大的外部载荷,确保叶片在风力作用下的稳定运行。
2. 轻质化:相比金属材料,玻璃纤维材料的密度更低,重量更轻。
使用玻璃纤维材料可以减轻风电叶片的整体重量,提高叶片的转动效率。
3. 耐腐蚀性强:风电叶片长期暴露在海洋环境中,容易受到潮湿、高温和海水腐蚀。
而玻璃纤维材料具有出色的抗腐蚀能力,能够有效延长叶片的使用寿命。
4. 制造工艺灵活:玻璃纤维材料的加工性能好,能够适应各种形状和尺寸的需求。
制造风电叶片时,可以采用模压、自动化纺织、层压等工艺,使叶片具有复杂的结构和良好的一致性。
三、玻璃纤维材料的发展趋势随着风电产业的不断发展和技术的进步,玻璃纤维材料在风电叶片中的应用也在不断创新和改进。
目前,一些研究机构和企业正在致力于提高玻璃纤维材料的强度、耐久性和可回收性,以进一步提高风电叶片的性能和降低制造成本。
同时,新型纤维增强材料的研发也为风电叶片提供了更多选择。
碳纤维、蜂窝结构和生物质纤维等材料的应用正在逐渐发展。
这些材料具有更高的强度和更好的可持续性,为风电叶片的设计和制造提供了更广阔的空间。
风电叶片制造工艺

风电叶片材料及制造工艺学习总结——孙玲庆一、叶片材料一般对叶片的要求有:比重轻且具有最佳的疲劳强度和机械性能,能经受暴风等极端恶劣条件和随机负荷的考验;叶片的弹性、旋转时的惯性及其振动频率特性曲线都正常,传递给整个发电系统的负荷稳定性好;耐腐蚀、紫外线照射和雷击的性能好;发电成本较低,维护费用最低。
为了满足以上要求,目前最普遍采用的是玻璃纤维增强聚酯树脂、玻璃纤维增强环氧树脂和碳纤维增强环氧树脂。
据中国环氧树脂行业协会专家介绍:一般较小型的叶片(如22m长)选用量大价廉的E-玻纤增强塑料,树脂基体以不饱和聚酯为主,也可选用乙烯酯或环氧树脂,而较大型的叶片(如42m以上),一般采用CFRP或CF与GF的混杂复合材料,树脂基体以环氧为主。
GE风能的叶片工程的全球经理Ramesh Gopalakrishnan说,设计师们在寻找轻质高强度材料的过程中,选择了碳纤维应用于叶片设计中。
因此玻璃纤维和碳纤维,是目前叶片制造中最为重要的两种材料。
据专家介绍,研究表明碳纤维(carbon fiber,简称CF)复合材料叶片,刚度是玻璃钢复合叶片的2~3倍。
虽然碳纤维复合材料的性能大大优于玻璃纤维复合材料,但价格昂贵,影响了它在风力发电上的大范围应用。
因此全球各大复合材料公司,正在从原材料、工艺技术、质量控制等各方面深入研究,以求降低成本。
昨天,我们用的是木制或金属材料;今天,我们用的是玻璃钢;明天,我们用的是碳纤维;那么明天的明天,我们用的会不会是纳米材料?市场专家表示,完全可能,原因一是其成本可能降低,二是性能优越、使用寿命长,长期看似乎更经济。
二、叶片制造工艺叶片的结构设计与实际生产制造方法息息相关,两者都需要兼顾生产成本和叶片的可靠性。
两种主要的叶片制造方法有:预浸料法和灌注法。
尽管两种方法都适用于两种常见设计的叶片结构,但预浸料主要用于箱式粱的叶片结构。
1 树脂灌注技术灌注工艺的基本原则就是通过真空压力将树脂吸入预先铺好的增强纤维或纤维布中,真空操作降低纤维一面的压力后,大气压力会驱使树脂浸润增强纤维,纤维灌注的速度和距离取决于以下因素:树脂系统的黏度、增强纤维的渗透性、灌注树脂的压力梯度。
碳纤维及复合材料在风电叶片中的应用进展

碳纤维及复合材料在风电叶片中的应用进展随着风电行业的快速发展,对于风电叶片的要求也越来越高。
传统的风电叶片主要使用玻璃纤维增强塑料(Glass Fiber Reinforced Plastics, GFRP),但其在抗风荷载、承载能力、疲劳性能等方面存在一定的不足。
为了提高叶片的性能,碳纤维及复合材料得到了广泛研究和应用。
1.碳纤维增强塑料(Carbon Fiber Reinforced Plastics, CFRP):以碳纤维为增强体的塑料基质材料,能够显著提高叶片的强度和刚度。
与传统的GFRP相比,CFRP具有更高的拉伸强度和模量,能够有效地减缓叶片在风荷载下的振动,并提高承载能力。
2.碳纤维树脂复合材料(Carbon Fiber Reinforced Polymer, CFRP):由碳纤维和树脂组成的复合材料,具有优异的力学性能和耐久性。
CFRP在风电叶片中的应用可以大幅度减轻叶片的重量,提高叶片的结构强度和疲劳寿命。
3.纳米碳管/纤维复合材料:纳米碳管和纤维相结合的复合材料,具有高强度、高导热性和良好的阻尼效果。
纳米碳管/纤维复合材料在风电叶片中的应用可以提高叶片的力学性能和耐久性,特别是在复杂的风荷载环境下表现出优异的阻尼效果。
4.天然纤维增强复合材料:将天然纤维(如竹纤维、麻纤维等)与树脂相结合形成的复合材料,具有较低的成本和环境友好性。
天然纤维增强复合材料在风电叶片中的应用可以减少对有限资源的依赖,并降低生产过程的能耗和排放。
5.混合增强复合材料:将碳纤维、玻璃纤维和天然纤维等不同种类的纤维相结合,形成混合增强复合材料。
混合增强复合材料在风电叶片中的应用可以充分利用不同纤维的优势,提高叶片的综合性能。
总的来说,碳纤维及复合材料在风电叶片中的应用进展迅速,为提高叶片的性能和可靠性提供了新的解决方案。
随着技术的不断创新和进步,碳纤维及复合材料在风电叶片中的应用将会得到进一步推广和应用。
风电叶片生产过程及质量控制简述
风电叶片生产过程及质量控制简述1、模具清理叶片脱模后,用刀具清理模具上沾的真空膜以及残留的胶,或用吸胶毡擦拭模具上的粉层,擦拭洁净后会用洁膜剂清理模具(通常只是边缘)。
2、脱模剂模具清理好后,涂一层脱模剂,其固化需要等待一段时间方可铺层。
脱模剂的作用在于在模具表面形成一个致密层,使得模具更加简单和叶片分别,达到脱模的效果。
3、部件整只叶片一般可分为蒙皮、主梁、翻边角、叶跟、粘接角等各个部件,其中主梁、翻边角、叶跟、粘接角等用专用模具进行制作。
等将各个部件制好后,在主模具上进行胶接组装在一起,合模后加压固化后制成一整只叶片。
4、主梁主梁是在单独的模具上成型的,铺放主梁时需要工装对其进行精确定位,并保证经过打磨处理及表面清洁。
主梁在切割车间转运到蒙皮车间后需要人工脱模,然后要剥离脱模后残余的一些附着物。
最终用布擦拭表面。
5、腹板PVC泡沫有较高的剪切模量,组成的结构有良好的刚度特性,主要增加截面刚度。
上下两层纤维布,中间是泡沫板形成夹芯结构,铺放时需要保证各块PVC板材之间连接紧密。
6、玻璃纤维铺层制作首先铺脱模布,然后是掩盖整个模具的大布,叶根区域铺设错层,主梁的错层与叶根错层镶嵌。
主梁下面需要铺设连续毡,以便导流。
主梁通过工装定位后,两旁的轻木和泡沫的位置就有了基准,芯材的位置正确之后,才能保证前缘的单向布铺设正确。
此过程需要留意铺放位置正确,搭接尺寸足够。
另外还需留意(抽真空时也要留意),叶根增加铺层有几十层,是最简单产生对结构强度影响比较大的褶皱的地方。
7、真空材料纤维布铺设完成后,需要依次铺设脱模布、带孔隔离膜、导流网、导流管和螺旋管、溢流管、一层真空、吸胶毡、二层真空。
脱模布和隔离膜主要起真空灌注工艺结束后更好地去除真空辅料的作用。
导流网能更好地排解真空体系中残留的空气,并且能够使树脂匀称地渗透到所生产产品各部位,对灌注的效果和速度都有较大影响。
在导流网上方布置有导流管,导流管通过进胶盘连通进胶管;在远离且低于导流管的位置有流管,流管连接抽气管,抽气管连接真空泵和压力表。
浅谈风电叶片的特点及制造工艺
浅谈风电叶片的特点及制造工艺风电叶片是风力发电机组中最重要的组成部分之一,其特点主要体现在以下几个方面:1. 结构轻巧:风电叶片需要在强风环境下旋转产生动力,因此需要具备良好的轻量化特性。
叶片通常采用复合材料构造,如玻璃纤维、碳纤维等,具有重量轻、强度高、刚性好等特点。
2. 强度与稳定性:叶片需要能够承受强风的冲击和动力的作用,在运行中要保持稳定,不产生明显的振动或变形。
叶片需要具备较高的强度和稳定性,以确保风力发电机组的安全运行。
3. 高效能与高风速系数:风电叶片的设计主要追求高效能和高风速系数,即在相同的风速条件下,能够获得更大的功率输出。
这一特点需要通过优化叶片的空气动力学性能来实现,如采用特殊的叶片曲线和翼型,使得风能能够最大限度地被转化为机械能。
4. 抗腐蚀与耐候性:风电叶片通常需要长时间暴露在恶劣的气候环境中,如高温、高湿等。
叶片需要具备良好的抗腐蚀和耐候性能,以保证其使用寿命和性能稳定性。
风电叶片的制造工艺一般包括以下几个步骤:1. 原料准备:选择合适的复合材料,如玻璃纤维或碳纤维等,进行预处理,如去除杂质、干燥等。
2. 叶片模具制作:根据设计要求,制作适合叶片形状的模具。
模具通常采用金属材料,如铝合金或钢等。
3. 叶片制作:将原料与树脂或黏合剂混合,并注入叶片模具中。
通过真空吸取或压缩等方式,确保材料充分填充整个模具。
4. 固化与硬化:将叶片模具放置在恒温恒湿的环境中,进行固化和硬化处理。
这一步骤通常需要一定的时间,以确保叶片能够具备足够的强度和稳定性。
5. 后期加工:将叶片从模具中取出,并进行修整、抛光、涂装等后期加工处理。
这是为了确保叶片的表面光滑、防护层完好,同时保持叶片的整体美观性。
风电叶片具有结构轻巧、强度与稳定性好、高效能与高风速系数、抗腐蚀与耐候性好等特点,制造工艺包括原料准备、叶片模具制作、叶片制作、固化与硬化、后期加工等步骤。
这些特点和工艺的结合使得风电叶片能够在强风环境下高效转换风能,为风力发电做出了重要贡献。
建材-大国重材系列(二):玻纤碳纤双骄,共享风电增量时代
报告摘要:●风机大型化推动大丝束碳纤维需求近年来风机厂商大功率机型占比明显提升,风机大型化能从摊薄风机制造成本、摊薄风机非制造成本、提升发电效率等角度降低度电成本。
风机大型化叠加海上风电兴起使叶片长度不断突破,而叶片大型化带来的轻量化与强度刚度要求带动碳纤维需求。
●玻纤为主流风电叶片增强材料风电叶片增强材料主要包括玻纤、碳纤维,密度、拉伸强度、模量为增强材料关键指标。
与传统材料相比,玻纤密度满足轻量化需求、模量强度满足刚度与强度需求,兼具经济性,为主流风电叶片增强材料,玻纤约占风电叶片材料成本的28%。
●碳纤维更适用海上大叶片碳纤维可减轻叶片质量、增强叶片刚度、提高叶片抗疲劳性能,拉挤法应用是近年来叶片需求增加的主因之一,但叶片大规模应用碳纤维仍受制于成本因素。
此外Vestas碳梁保护专利2022年7月到期,国内厂商有动力加速布局拉挤法碳纤维。
●风电叶片领域,玻纤与碳纤将长期共存碳纤维产能规模无法支持对玻纤的大面积替代;碳纤维成本下降非一日之功;玻纤不断更新换代,高模量玻纤将成为风电纱拳头产品。
●投资建议玻纤与碳纤有望共享风电增量。
全球风电碳纤维需求从2014年0.6万吨快速上升到2020年3.06万吨,CAGR31%,增速明显快于整体。
行业性能与成本动态匹配,部分时点不可兼得,当前玻纤性价比优势依然显著。
风电领域,玻纤建议重点关注中国巨石、中材科技,碳纤维关注吉林碳谷、吉林化纤、中复神鹰(未上市)。
●风险提示大丝束碳纤维产能投放进度不及预期;国产拉挤法工艺研发不及预期;海上风电项目进展不及预期。
[Table_ProfitDetail]盈利预测与财务指标代码重点公司现价EPS PE评级12月1日2020 2021 2022 2020 2021 2022600176.SH中国巨石17.700.69 1.40 1.56 28.9 12.7 11.3 - 002080.SZ中材科技36.90 1.22 2.16 2.39 19.8 17.1 15.5 - 资料来源:wind、民生证券研究院(未评级公司使用wind一致预期)[Table_Invest]推荐维持评级[Table_QuotePic]行业与沪深300走势比较资料来源:Wind,民生证券研究院分析师:李阳执业证号:S0100521110008邮箱:******************相关研究1.【民生建材】大国重材系列(一):聚焦药玻,技术攻关与国产替代2.地产信贷边际放松,消费建材估值有望企稳—建筑材料行业周报202111283.【民生建材】本周观点211121:板块估值偏低,新材料应用提速建材行业研究/深度报告玻纤碳纤双骄,共享风电增量时代——大国重材系列(二)深度研究报告/建材2021年12月02日本公司具备证券投资咨询业务资格,请务必阅读最后一页免责声明证券研究报告1目录1. 风机大型化推动大丝束碳纤维需求 (3)1.1大功率风机占比明显提升 (3)1.2叶片大型化带动碳纤维需求 (5)2. 风电叶片材料:玻纤VS碳纤维 (6)2.1玻纤为主流风电叶片增强材料 (6)2.1.1 玻纤性价比高 (6)2.1.2 各类玻纤因性能差异应用于叶片不同结构 (7)2.2碳纤维更适用于海上大叶片 (8)2.2.1 碳纤维性能优异,短期大规模应用受制于成本 (8)2.2.2 风电叶片主要使用高性价比大丝束碳纤维 (10)2.2.3 拉挤法为风电叶片用碳纤维主要生产工艺 (12)2.3碳纤维产业链较长,生产工艺国产替代空间广阔 (14)3. 风电叶片领域,玻纤、碳纤将长期共存 (16)4. 风险提示 (17)插图目录 (18)表格目录 (18)1. 风机大型化推动大丝束碳纤维需求1.1 大功率风机占比明显提升风机厂商大功率机型占比明显提升。
风力发电系统的新型叶片设计
风力发电系统的新型叶片设计一、引言风力发电作为新能源的一种形式,已经成为了现代社会中不可或缺的一部分。
发电的过程中,风力叶片是非常重要的。
如今,随着技术的发展,人们对风力发电设备的性能和效率也提出了更高的要求,尤其是针对于风力叶片的设计。
本文将讨论风力发电系统中一种新型叶片设计方案。
二、传统风力叶片的设计传统风力叶片通常是由玻璃纤维和环氧树脂等材料制成的。
在设计中,主要考虑的因素包括减少噪音和提高叶片的力学强度。
叶片的形状和尺寸也是设计中需要考虑的一个重要因素,因为它们直接决定了叶片的效能。
三、新型叶片的设计近年来,研究人员在传统叶片基础上提出了一些新型叶片设计方案,以实现更高的效率和性能。
1. Vortex Bladeless西班牙的Vortex Bladeless公司开发出了一种不同于传统叶片的设计,他们称之为“无叶片叶轮”。
它不像传统的叶片那样具有固定的形状,而是由两个柱状物组成,通过压力波来达到捕捉风能的目的。
这种设计具有减少噪音、减少能源损失和较低的生产成本等优点。
2. Smart Blade德国的Smart Blade公司研究出了一种可以自适应改变形态的叶片,这种叶片搭载了传感器和电机,可以通过电子控制实现根据风力变化而自适应改变形态,以达到最佳效能。
这种智能叶片设计可以提高叶片的效率,并提高使用寿命。
3. Aerodyn德国的Aerodyn公司研究出了一种类似降落伞的风力叶片,其形状能更好地应对风力的变化,以及减少振荡和噪音。
这种“降落伞”形状叶片与传统的叶片相比效率提高了3%至5%,这是一个相当大的提高。
四、新型叶片设计的优点和挑战1. 优点新型叶片设计具有很多的优点,其中最显著的就是提高了效率、减少了噪音、缩短了制造周期,降低了生产成本。
此外,新型叶片的设计也使得输电线路的构建更加方便,这对于新型能源的推广具有非常重要的作用。
2.挑战新型叶片设计也面临一些挑战,例如实现该设计需要高精度的加工技术,这增加了生产成本和制造周期。
- 1、下载文档前请自行甄别文档内容的完整性,平台不提供额外的编辑、内容补充、找答案等附加服务。
- 2、"仅部分预览"的文档,不可在线预览部分如存在完整性等问题,可反馈申请退款(可完整预览的文档不适用该条件!)。
- 3、如文档侵犯您的权益,请联系客服反馈,我们会尽快为您处理(人工客服工作时间:9:00-18:30)。
2009 73 197
2010 91 238
2011 118 263
2012 130 270
2013 137 273
从今年上半年短切纤维进出两旺,反映了FRTP对玻纤需求的继续较大幅度增长。(见表)
我国短切玻纤2014年上半年进出口情况
进 项 目
数
量 (万T)
口
用
量 (亿)
出
汇
同比 (%)
口 创
量 (亿)
Airorne管道的结构
Airborne管道重量轻,可卷绕,耐疲劳性能优
3、我国巨石、CPIC、泰山玻纤等企业多年以浸润剂为重点,改进CS、LFT产品质量和扩大生产能力,
满足着增长的需求,但比较国际先进企业,还得努力。 OC发布对华供增强纱连续两年翻番,不但不断提质扩品,还和下游单位结成联盟,为预浸料产品提供 解决方案。 PPG也在CS、LFT用纱不断扩系列,提质量。
1、热塑性塑料在高分子材料中占比高(约70%)品种多,发展快。用玻纤增强改性明显, 而且相对于热固性树 脂复用性好,受到复合材料应用领域的欢迎。随着增强技术的改进,近些年来玻纤增强热塑性塑料(FRTP)的发展 速度高于玻纤增强树脂(FRSP)。(见表)
我国玻纤增强塑料发展表
(万吨)
年份 FRTP FRSP
2、高分子表面处理技术涉及 生产工艺水平 玻纤产品多样化 和玻纤的应用开发—更多涉及高分子领域 该项技术包含 浸润剂技术 粘结剂技术 处理(涂覆)剂技术
等技术环节,所以高分子表面处理技术成为行业核心技术之一,因此,贯彻“深加工,扩应用” 需
加速发展表面处理技术。
二、几个热点前沿的表面处理技术
(一)增强热塑性塑料
(三) 电气绝缘
电气绝缘是发挥玻纤特性的主要用途之一。随着电气化、信息化事业的发展,它在电气、电子的应用市场还 会发展。但会以高质量的增长代替现有的数量高速增长。对玻纤基材的要求是高质、细薄、均匀。 我国传统玻纤电绝缘产品如层压布、云母布是采用坩埚拉丝法、石蜡型浸润剂、中捻合股再进行织造而成。 后来提供给覆铜板用的电子布就采用先进池窑拉丝,淀粉型浸润剂、低捻单丝,浆纱、喷气织造并处理后成为产 品。相比而言,后者产品质量好、产效高。但工序多,成本高。 当前我国上述两种工艺都还存在,各自有的发展问题。焦点在对处理剂和工艺方面。老生产电绝缘布生产系 统想提高,局部换点织机等设备,不是全系统改造难以得到理想的电子布生产系统。另一方面,在激励的市场竞 争中,新的电子布生产系统如何提高更细更薄产品的生产效率。如何扩产低价的产业织物?是两种薄布生产企业 各自思考的问题。 最近有两个信息:1、日淀已将一种豌豆改性淀粉用于E225纱,开始批量生产。2、神州淀粉公司提供浸润剂 用改性淀粉的国产化并愿与生产企业合作,开发淀粉增强性浸润剂。 另外,一些企业在努力开发粘基电绝缘材料,它可以实现更薄的均匀化。但要实现也要有更加可控的材质、 工艺及相应粘结剂。
13.5
出 口
用汇量 (美元)
84
9.3
产品 (%)
产品量 (万T)
同比 (%)
同比 (%)
23.3
14.5
9.5亿
3.8
119.1
-1.6
19.2亿
-1.31
项目 运 营 情 况 玻纤 及制 品进 出口 情况
规模 以上 企业 数量 其中 亏损 企业 数量 玻纤纱总产量
量
同比 (%)
数
量 (亿)
量
同比 (%)
汇
同比 (%)
数值
38702
1441
5963
14.39
66707
2225
7069
1712
2、玻纤增强热塑性塑料的效果与玻纤的含量,玻纤的长度和分布,以及玻纤与塑料 的粘结强度等因素有关。因此在玻纤增强热塑性塑料技术发展中玻纤型态从玻纤粉—短切 纤维—长纤维—连续纤维及织物。为提高结合力从加偶联剂到专用浸润剂开发再到专用粘 结剂和预浸料再加上被增强塑料的改性。通过多年的配合综合开发特别近年来连续玻纤预 浸技术和装备的突破,使玻纤增强热塑性复合材料、纤维含量能超过60%,拉伸强度能达 500Mpa以上,成型工艺突破了注塑、挤塑,扩展到热压、缠绕及RTM。出现了典型产品, 如:增强热塑性高压管,50㎡拖车底板以及汽车结构件(见附图)等,在这个技术发展中 ,离不开高分子新技术结合应用,我国还得加油追赶。
10.3
8.58
4.7亿
3.84
64.6
8.15
10.3亿
7.67
(二)玻纤行业的调整升级要靠全行业的技术创新, 提高市场竞争力
1、玻纤行业由三大主体技术支撑: 玻纤技术—解决玻纤本体组成和成型 纺织技术—解决玻纤多种制品的结构 高分子表面处理技术—解决玻纤改性和应用
发展创新要的是三大领域前沿技术的融合
我国玻纤行业最近运行情况表
项目 运 营 情 况 玻纤 及制 品进 出口 情况
规模 以上 企业 数量 其中 亏损 企业 数量 玻纤纱总产量
量 (万T) 同比 (% )
2 0 1 3年
玻纤及制品主营收入
量(亿) 同比(%)
销售利润总额
量(亿) 同比(%)
734
62 进
285 口
用汇量 (美元)
-1
1310
(二) 风电叶片
发展风电是国家的战略,经过一段整顿已进入良性发展期,今年新增装机预计会在20%。拉动了玻纤的发展。 三大玻纤在提高叶片用纱的质量和认证及及产业链接延伸等方面的努力,扩大了风电用玻纤的市场。 我国风电叶片应用风电用玻纤市场还有一定比例为国外产品所占。我们从今年上半年无捻粗纱进口升福较大 (产品同比增长22.77%,用汇同比增幅37.01%)看出一些问题。我们更可以从国际先进企业的技术优势发挥学习 一些路子,例如OC公司为更适合叶片更长更轻提出解决方案,先后采用advabtex和Hipertex玻纤并在以合适的浸 润剂提供使用。达到比E玻纤强度提高30%,刚度提高17%,密度提高45%,耐疲劳性提高10倍,线膨胀下降30%。 PPG公司用于风电叶片的E玻纤Hybon2026粗纱,使用专用浸润剂也使拉伸强渡提高了20%,实现了浸润剂技术的先 进优势,他们还占有叶片涂料的领先地位。
量(万T) 同比(%)
2 0 14 年 上 半 年
玻纤及制品主营收入
量(亿) 同比(%)
销售利润总额
量(亿) 同比(%)
708
58
148.6
4.26
694
出 口
10.4
40.8
16.1
进 口
产品量 (万T) 同比 (%) 用汇量 (美元) 同比 (%) 产品量 (万T)
同比 (%)
用汇量 (美元)
同比 (%)
玻纤调整升级与表面处理
姜肇中 2014年11月
一、玻纤调整升级需加速发展表面处理技术 二、几个热点前沿的表面处理技术
一、玻纤调整升级需加速发展表面处理技术
(一)我国玻纤在调整中保持持续发展
1、08年前以突破池窑拉丝技术,低价扩大国际市场(出口率曾高 达67%)为特征,高速发展,成为世界玻纤生产,出口第一大国。 2、世界金融危机后,以积极满足内需为主导,深加工,扩应用继 续求得稳步发展。特别是效益的较快增长。08-13年五年玻纤纱产量由 211万吨到285万吨。业务主营收入由547亿元到1310亿元。今年上半年 运营形式继续好转(见附表)。 3、我国国民经济调整升级的战略和玻纤复材应用潜力大,差距大 的实际情况,要求行业继续贯彻“控总量、深加工、扩应用”的方针。 就是说要注重生产更多更好的产品,高水平的满足市场需求。