1[1]JCMS精益生产I标准版.pptx
合集下载
1[1]JCMS精益生产I标准版
![1[1]JCMS精益生产I标准版](https://img.taocdn.com/s3/m/7ea0022f168884868662d60a.png)
59
周期时间
指该产品从原材料投入生产开始,经过加工,到产品完成的 全部时间。 周期时间必须小于或等于节拍时间(Takt Time) 否则……
60
Kaizen
Kai =改变 Change Zen =好、更好 Good ,for the better
20% (One Time准时)
61
1/10 of 1% Every Day每天
6
批量生产
美国汽车的平均售价也从1000美元左右,降到了360美元( 1907年)。
7
批量生产
大批量,单品种
无需高技能,每人只需做整个工作的一小部分 工作无自豪感、不满意 采用生产装配线 零部件可通用 批量单一产品 讲究产量,而非质量 价廉 生产周期短 生产投入高
8
丰田生产系统
生活中的kaizan
62
Kaizen的定义
以标准化工作为基础,团队通过运用PDCA戴明环的工具,进行持续 改进。
标准化工作 团队 PDCA
64
Kaizen的过程
6.指定新的计划
1.熟悉现状
5.决策或调整
Basic Tools 基础工具
JCMS Overview
Value Stream Mapping 价值流
图
Prefer by PBU 产品业务单元推荐工具
Culture & Awareness Problem Solving
问题解决
5S & Visual Management 目视管理/5s
Standard Operations 标准
纠正/返工
Overprocessing
过度加工
Waiting
等待
Making more than what the customer needs
周期时间
指该产品从原材料投入生产开始,经过加工,到产品完成的 全部时间。 周期时间必须小于或等于节拍时间(Takt Time) 否则……
60
Kaizen
Kai =改变 Change Zen =好、更好 Good ,for the better
20% (One Time准时)
61
1/10 of 1% Every Day每天
6
批量生产
美国汽车的平均售价也从1000美元左右,降到了360美元( 1907年)。
7
批量生产
大批量,单品种
无需高技能,每人只需做整个工作的一小部分 工作无自豪感、不满意 采用生产装配线 零部件可通用 批量单一产品 讲究产量,而非质量 价廉 生产周期短 生产投入高
8
丰田生产系统
生活中的kaizan
62
Kaizen的定义
以标准化工作为基础,团队通过运用PDCA戴明环的工具,进行持续 改进。
标准化工作 团队 PDCA
64
Kaizen的过程
6.指定新的计划
1.熟悉现状
5.决策或调整
Basic Tools 基础工具
JCMS Overview
Value Stream Mapping 价值流
图
Prefer by PBU 产品业务单元推荐工具
Culture & Awareness Problem Solving
问题解决
5S & Visual Management 目视管理/5s
Standard Operations 标准
纠正/返工
Overprocessing
过度加工
Waiting
等待
Making more than what the customer needs
《精益生产基础原》课件

流动制造
01
02
03
流动制造
通过采用拉动系统、单件 流等生产方式,实现生产 过程中的物料需求指令,实现按需 生产和减少在制品库存。
单件流
追求生产过程中的单件流 动,减少等待和搬运浪费 ,提高生产效率。
完美流程
完美流程
追求生产流程的完美化, 通过不断改进和优化,消 除浪费和降低成本。
解决方案
针对这些挑战,企业可以采取一系列的解决方案,如加强培训和宣传、优化资源 配置、引进先进技术等。这些解决方案有助于克服实施精益生产过程中的障碍, 确保企业能够顺利实现精益生产的目标。
对未来精益生产的展望
未来趋势
随着科技的不断进步和市场环境的变化,精 益生产将会继续发展并呈现出新的趋势。例 如,数字化和智能化技术的应用将进一步提 高生产效率和灵活性;可持续发展将成为企 业追求的重要目标;供应链协同和全球化的 趋势将要求企业更加注重跨组织的协作和共 赢。
整理
将工作场所内的物品进行分类, 保留需要的物品,移除不需要的 物品,使工作场所变得整洁有序 。
素养
培养员工良好的工作习惯和职业 素养,提高工作效率和品质意识 。
快速换模
快速换模是一种减少换模时间 、提高生产效率的精益工具。
通过减少换模时间,可以降低 生产成本、提高设备利用率和 灵活性,满足多品种、小批量 的生产需求。
总结词
快速换模技术应用,提高生产效率和灵活性
详细描述
某电子制造企业通过引入快速换模技术,缩短换模时间,提高生产效率。同时 ,采用标准作业和作业研究,优化生产流程,减少生产浪费。这种灵活性使得 企业能够快速应对市场变化和客户需求。
案例三:某机械制造企业的价值流图应用
总结词
《精益生产》PPT课件

• 得到改善。
• 工作强度和工作时间不变,通 过消除不增值的浪费。
精选课件ppt
20
整体效率比个体效率重要
• 整体:全公司、全厂、全车间、全班组。 • 个体:个人、班组、车间。 • 整体效益的提高:组织方式、市场预测、
完善计划,顺畅的物流和信息流等。各级 领导的重视、有效沟通、有力实施。 • 个体效益提高:个体是相对的,通过洗脑、 用脑和改习惯等消除浪费。
1. 对质量的误解 2. 以防万一的逻辑 3. 控制缺陷 4. 过于形式化 5. 缺乏沟通 6. 信息流混乱
精选课件ppt
14
库存浪费
任何超过客户按时所要求的必要的产品的供应
1. 跟踪系统复杂 2. 额外仓储及搬运 3. 多余货物的管理 4. 信息流误导 5. 中间体的管理 6. 过期物料的检验 7. 退货或不合格 8. 效期的约束
销售----成品库----包装----半成品----配料----原辅料库----管理部门。
如果各企业能够关注库存,分析库存,用数据表达库存占用的资 金和资金所发生的利息以及由于库存所造成的损失,那么企业的负责 人一定会发出惊叹“浪费太大”。
李选民
精选课件ppt
18
浪费对员工的影响
• 导致身体疲劳 • 导致精神疲劳 • 增加沮丧泄气 • 增加工作压力 • 导致责备他人 • 浪费你的时间
精选课件ppt
了多长时间。
• 市场有效信息。 • 确定每个产品的安全库存。(最初值) • 偏差分析,向实际靠拢。
精选课件ppt
27
均衡生产的优点
• 市场响应更快 • 有效降低库存 • 缩短制造周期 • 供应链平稳
精选课件ppt
28
均衡生产
• 适用于价值链相对稳定的产品。 • 多品种,多批量。 • 确定经济批量。符合现有设施、设备、人员和GMP要求的最
• 工作强度和工作时间不变,通 过消除不增值的浪费。
精选课件ppt
20
整体效率比个体效率重要
• 整体:全公司、全厂、全车间、全班组。 • 个体:个人、班组、车间。 • 整体效益的提高:组织方式、市场预测、
完善计划,顺畅的物流和信息流等。各级 领导的重视、有效沟通、有力实施。 • 个体效益提高:个体是相对的,通过洗脑、 用脑和改习惯等消除浪费。
1. 对质量的误解 2. 以防万一的逻辑 3. 控制缺陷 4. 过于形式化 5. 缺乏沟通 6. 信息流混乱
精选课件ppt
14
库存浪费
任何超过客户按时所要求的必要的产品的供应
1. 跟踪系统复杂 2. 额外仓储及搬运 3. 多余货物的管理 4. 信息流误导 5. 中间体的管理 6. 过期物料的检验 7. 退货或不合格 8. 效期的约束
销售----成品库----包装----半成品----配料----原辅料库----管理部门。
如果各企业能够关注库存,分析库存,用数据表达库存占用的资 金和资金所发生的利息以及由于库存所造成的损失,那么企业的负责 人一定会发出惊叹“浪费太大”。
李选民
精选课件ppt
18
浪费对员工的影响
• 导致身体疲劳 • 导致精神疲劳 • 增加沮丧泄气 • 增加工作压力 • 导致责备他人 • 浪费你的时间
精选课件ppt
了多长时间。
• 市场有效信息。 • 确定每个产品的安全库存。(最初值) • 偏差分析,向实际靠拢。
精选课件ppt
27
均衡生产的优点
• 市场响应更快 • 有效降低库存 • 缩短制造周期 • 供应链平稳
精选课件ppt
28
均衡生产
• 适用于价值链相对稳定的产品。 • 多品种,多批量。 • 确定经济批量。符合现有设施、设备、人员和GMP要求的最
精益生产概念与标准时间.pptx

项目 1)所需人力
大批量 精益生产
1
1/2
2)新产品开发周期
1
1/2-2/3
3)生产过程的在制品库存
1
1/10
4)工厂占用空间
1
1/2
5)成品库存
1
1/4
6)产品质量
1
3
工程分析
工程分析目的
检讨单一工程或工程系列的合理性,推动总体生产活动的改善
生产要素 Input 生产线 Output 5M
成品
加工 搬运 检查 存放 停滞
区分 生产业务 工 程 单位作业 要素作业 动 作
展
开 单位 技法
箱体拼装
蒸发器组装 内胆组装 侧帮组装
左侧帮 右侧帮
拿侧帮 放在夹具上 固定镙丝
将手伸开 回转 抓住 抬起 移动
日/小时
小时/分
工程分析
分/秒 作业分析
时间分析
秒以下 动作分析
工程分析
工程分析体系
根据分析的对象的不同而使用不同的分析方法
计 系
物 流
统系
7)‘零’灾害(Safety安全第一)
统
现均 场衡 IE 化 作与 业同 研步 究化
柔精 性益 生品 产质 系保 统证
与 自 动 化
生改 产革 的机 快制 速与 切标 换准 与化 维 护
意识改革 T5S
精益生产概念
大批量与精益生产
与大批量生产方式相比,精益生产方式的优越性主要表现在
平均活性指数的评价和改善着眼点
活性指数 评价
<0.5
0.5-1.3
因放在地面上 的时间多而使 浪费增加的现 场
地面已整理 现场
1.3-2.3
《精益生产》课件

电子制造业采用精益生产方法, 通过减少浪费和优化供应链,提 高生产效率和产品质量。
航空制造业
航空制造业采用精益生产方法, 通过优化生产流程和提高工厂效 率,实现生产能力的提升和交付 时间的缩短。
结论
精益生产的优势和不足
精益生产的优势包括提高效率、降低成本和改善质量,但也存在实施难度、需求变化风险等 不足之处。
3
5S
5S是一种创建清洁、整齐、有序和高效工作环境的方法,以促进工作效率和员工安全。
4
Kaizen
Kaizen是一种通过小步骤持续改进的方法,以实现生产过程的不断优化和卓越。
精益生产的应用
汽车制造业
汽车制造业采用精益生产方法, 通过优化生产流程和提高质量, 实现生产效率的提升和成本的降 低。
电子制造业《精益生产》Fra bibliotekPT课件"精益生产"是一种致力于最大限度减少浪费和提高效率的制造管理方法。本 课件将介绍精益生产的概念、核心工具和应用,并分享汽车制造、电子制造 和航空制造等领域的成功案例。
简介
什么是精益生产?
精益生产是一种致力于通过 减少浪费、提高效率和优化 流程来提高生产和运营绩效 的管理方法。
精益生产的未来发展趋势
随着技术的发展和市场的变化,精益生产将更加注重数字化、智能化和可持续发展。
如何应用精益生产提高企业生产效率?
企业可以通过培训员工、优化流程和引入先进技术来应用精益生产,以提高生产效率和竞争 力。
精益生产的主要特点
精益生产的主要特点包括价 值流导向、一次制品流动、 持续改善和员工参与。
精益生产的重要性
精益生产可以帮助企业提高 质量、降低成本、提升交付 速度,并增强市场竞争力。
精益生产的核心工具
航空制造业
航空制造业采用精益生产方法, 通过优化生产流程和提高工厂效 率,实现生产能力的提升和交付 时间的缩短。
结论
精益生产的优势和不足
精益生产的优势包括提高效率、降低成本和改善质量,但也存在实施难度、需求变化风险等 不足之处。
3
5S
5S是一种创建清洁、整齐、有序和高效工作环境的方法,以促进工作效率和员工安全。
4
Kaizen
Kaizen是一种通过小步骤持续改进的方法,以实现生产过程的不断优化和卓越。
精益生产的应用
汽车制造业
汽车制造业采用精益生产方法, 通过优化生产流程和提高质量, 实现生产效率的提升和成本的降 低。
电子制造业《精益生产》Fra bibliotekPT课件"精益生产"是一种致力于最大限度减少浪费和提高效率的制造管理方法。本 课件将介绍精益生产的概念、核心工具和应用,并分享汽车制造、电子制造 和航空制造等领域的成功案例。
简介
什么是精益生产?
精益生产是一种致力于通过 减少浪费、提高效率和优化 流程来提高生产和运营绩效 的管理方法。
精益生产的未来发展趋势
随着技术的发展和市场的变化,精益生产将更加注重数字化、智能化和可持续发展。
如何应用精益生产提高企业生产效率?
企业可以通过培训员工、优化流程和引入先进技术来应用精益生产,以提高生产效率和竞争 力。
精益生产的主要特点
精益生产的主要特点包括价 值流导向、一次制品流动、 持续改善和员工参与。
精益生产的重要性
精益生产可以帮助企业提高 质量、降低成本、提升交付 速度,并增强市场竞争力。
精益生产的核心工具
《精益生产基础培训》ppt课件pptx
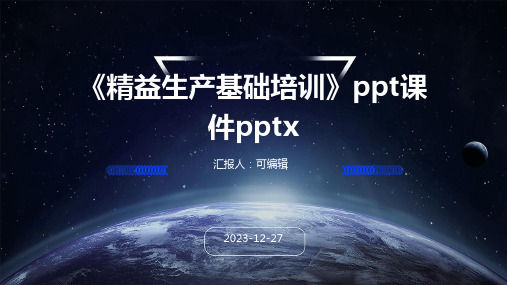
单元化生产
单元化生产是将生产线或设备按照产品族或工艺特点进行模块化设计,以提高生产 效率和灵活性的一种生产方式。
通过单元化生产,可以实现小批量、多品种的生产,满足市场需求的快速变化。同 时还可以提高设备的利用率和员工的技能水平。
单元化生产的实施需要提前进行生产线或设备的规划和设计,并注重员工培训和跨 部门协作。
竞争中获得优势。
促进可持续发展
精益生产注重环保和资源节约 ,有助于企业实现可持续发展
。
精益生产的历史与发展
起源
未来趋势
精益生产起源于日本丰田汽车公司的 生产方式,旨在消除浪费、提高效率 和效益。
随着科技的不断进步和应用,精益生 产将进一步与数字化、智能化相结合 ,实现更高水平的自动化和智能化。
发展历程
Straighten)、清扫(Shine)、清洁 (Standardize)、素养(Sustain)五
个方面。
通过实施5S管理,可以提高生产现场 的整洁度和效率,减少浪费,提高生产 质量、定期 检查和持续改进,确保管理效果的持久
性和有效性。
明确改进措施、时间表、责任人及所需资源。
风险评估与应对
预测潜在风险,制定应对措施,确保改进计划的顺利实施。
实施改进措施
1 2
培训与沟通
对相关人员进行培训,确保他们理解并掌握改进 措施。
资源配置
确保所需的人员、设备、材料和技术得到有效配 置。
3
实施改进措施
按照计划逐步实施改进措施,确保改进过程顺利 进行。
随着丰田生产方式的成功,精益生产 逐渐被全球范围内的企业所采纳和推 广。
02
精益生产的核心原则
价值导向
价值导向
强调从客户需求出发,识别并确 定客户认为有价值的流程和功能 ,消除非增值的环节和活动,实
精益生产概论(PPT132页)

针对主要的质量问题,由10名左右相关人员组 成改善小组,运用PDCA循环和质量改善工具,自主 进行不良分析并实施具体改善的质量活动。
推行QC小组活动的意义有: ● 通过小组式的学习型组织, 提高一线员工独立思考和相互启发的能力
● 通过QC手法的学习与运用, 加强企业的基础管理 ● 通过循序渐进的课题活动, 创造有活力的工作场所 ● 发挥群众智慧,全员参与经营
1、Genius only means hard-working all one's life. (Mendeleyer, Russian Chemist)
天才只意味着终身不懈的努力。21.5.265.26.202108:3008:30:57May-2108:30
2、Our destiny offers not only the cup of despair, but the chalice of opportunity. (Richard Nixon, American President )命运给予我们的不是失望之酒,而是机会之杯。二〇二一年五月二十六日2021年5月26 日星期三
现 代
IE 运 用
均 衡 化 同 步 化
7
9、要学生做的事,教职员躬亲共做; 要学生 学的知 识,教 职员躬 亲共学 ;要学 生守的 规则, 教职员 躬亲共 守。21 .6.3021 .6.30W ednesd ay , June 30, 2021 10、阅读一切好书如同和过去最杰出 的人谈 话。15:42:0015 :42:001 5:426/3 0/2021 3:42:00 PM 11、一个好的教师,是一个懂得心理 学和教 育学的 人。21. 6.3015:42:0015 :42Jun- 2130-J un-21 12、要记住,你不仅是教课的教师, 也是学 生的教 育者, 生活的 导师和 道德的 引路人 。15:42:0015:4 2:0015:42Wed nesday , June 30, 2021 13、He who seize the right moment, is the right man.谁把握机遇,谁就心想事成。21.6.3021.6.3 015:42:0015:42 :00Jun e 30, 2021 14、谁要是自己还没有发展培养和教 育好, 他就不 能发展 培养和 教育别 人。202 1年6月 30日星 期三下 午3时4 2分0秒 15:42:0 021.6.3 0 15、一年之计,莫如树谷;十年之计 ,莫如 树木; 终身之 计,莫 如树人 。2021 年6月下 午3时4 2分21. 6.3015:42June 30, 2021 16、提出一个问题往往比解决一个更 重要。 因为解 决问题 也许仅 是一个 数学上 或实验 上的技 能而已 ,而提 出新的 问题, 却需要 有创造 性的想 像力, 而且标 志着科 学的真 正进步 。2021 年6月30 日星期 三3时4 2分0秒 15:42:0 030 June 2021 17、儿童是中心,教育的措施便围绕 他们而 组织起 来。下 午3时42 分0秒 下午3时 42分15 :42:002 1.6.30
推行QC小组活动的意义有: ● 通过小组式的学习型组织, 提高一线员工独立思考和相互启发的能力
● 通过QC手法的学习与运用, 加强企业的基础管理 ● 通过循序渐进的课题活动, 创造有活力的工作场所 ● 发挥群众智慧,全员参与经营
1、Genius only means hard-working all one's life. (Mendeleyer, Russian Chemist)
天才只意味着终身不懈的努力。21.5.265.26.202108:3008:30:57May-2108:30
2、Our destiny offers not only the cup of despair, but the chalice of opportunity. (Richard Nixon, American President )命运给予我们的不是失望之酒,而是机会之杯。二〇二一年五月二十六日2021年5月26 日星期三
现 代
IE 运 用
均 衡 化 同 步 化
7
9、要学生做的事,教职员躬亲共做; 要学生 学的知 识,教 职员躬 亲共学 ;要学 生守的 规则, 教职员 躬亲共 守。21 .6.3021 .6.30W ednesd ay , June 30, 2021 10、阅读一切好书如同和过去最杰出 的人谈 话。15:42:0015 :42:001 5:426/3 0/2021 3:42:00 PM 11、一个好的教师,是一个懂得心理 学和教 育学的 人。21. 6.3015:42:0015 :42Jun- 2130-J un-21 12、要记住,你不仅是教课的教师, 也是学 生的教 育者, 生活的 导师和 道德的 引路人 。15:42:0015:4 2:0015:42Wed nesday , June 30, 2021 13、He who seize the right moment, is the right man.谁把握机遇,谁就心想事成。21.6.3021.6.3 015:42:0015:42 :00Jun e 30, 2021 14、谁要是自己还没有发展培养和教 育好, 他就不 能发展 培养和 教育别 人。202 1年6月 30日星 期三下 午3时4 2分0秒 15:42:0 021.6.3 0 15、一年之计,莫如树谷;十年之计 ,莫如 树木; 终身之 计,莫 如树人 。2021 年6月下 午3时4 2分21. 6.3015:42June 30, 2021 16、提出一个问题往往比解决一个更 重要。 因为解 决问题 也许仅 是一个 数学上 或实验 上的技 能而已 ,而提 出新的 问题, 却需要 有创造 性的想 像力, 而且标 志着科 学的真 正进步 。2021 年6月30 日星期 三3时4 2分0秒 15:42:0 030 June 2021 17、儿童是中心,教育的措施便围绕 他们而 组织起 来。下 午3时42 分0秒 下午3时 42分15 :42:002 1.6.30
《精益生产》PPT课件
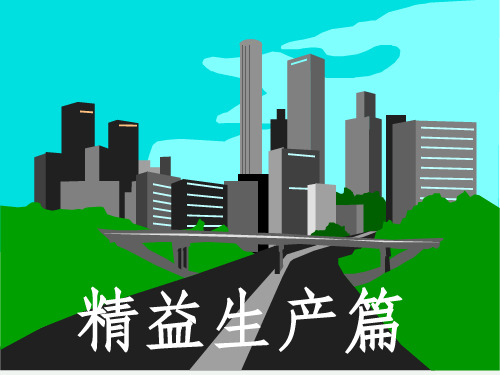
设备现场管理应用
在精益生产方式中,设备故障被视为无效劳动和浪费, 提出设备故障要向零进军,这就要求设备运行过程尽量 不发生故障,少发生故障。
实行全员维修和保养; 实行针对性预防检修; 实行改善性维修;
精益生产系统的五项原则
质量是 制造出来的
标准化
精益的 制造系统
持续改进
员工参与
短的制造周期
拉动式方法的特点:
坚持一切以后道工序需求出发,宁肯中断生产,也不搞超前超
1 量生产。拉动式生产的核心就是准时化,就是要求在需要的事
后,生产需要的产品和需要的数量,所以又把它称为准时化生 产(Just In Time)。
生产指令不仅仅是生产作业计划,而且还用看板进行为调节。
2 看板成为实施拉动式生产的重要手段。
看板来源于大野耐一从美国超级市场的启示。
拉动式方法 在生产制造过程中的具体运用
1 以市场需求拉动企业生产。
在企业内部,以后道工序拉动前道工序生产,以总装配拉动总
2 成装配,以总成装配拉动零件加工,以零件拉毛坯生产,用以
大幅度压缩在制品储备,消除无效劳动。
U型平面布置的“一个流”生产线; 多工序管理和多机床操作 成批轮番作业的生产线 快速换模技术,实现小批量多批次生产
jit以小批量生产为准则换模工作必须尽快完成消除浪费的方设计流程连接操作平衡工作站能力减小批量规减少安装换模时间2tqm全面质量管理尊重员工qcc小组合理化建议3稳定计划均衡计划不超过生产能力建立冻结区间指计划固定不弯一个时间区段4看板控制由后向前传送指令5与供应商紧密合作缩短提前期增加供货频率交货要及时保证质量可靠性6减少额外存货寻找其他区采用传送带运输机7改进产品设计产品标准化零件标准化及零件数减少改进过程设计产品质量期望jit七个前提条件61传统生产管理中的生产指令生产计划实际生产数量生产顺序表库存工序a工序b工序c库存完成生产指令计划生产数量与实际生产数量不同生产指令生产指令62jit生产计划实际生产数量生产顺序表看板工序a工序b工序c看板完成生产指令计划生产数量与实际生产数量相同63确定看板数量每个容器内数量64防止过量生产生产没有看板不能生产也不能运送目视管理看板必须附在实物上按照取下看板的顺序进行生产改善工具不能把不良品送往下一工序看板机能生产及运送的工作指令65生产系统
- 1、下载文档前请自行甄别文档内容的完整性,平台不提供额外的编辑、内容补充、找答案等附加服务。
- 2、"仅部分预览"的文档,不可在线预览部分如存在完整性等问题,可反馈申请退款(可完整预览的文档不适用该条件!)。
- 3、如文档侵犯您的权益,请联系客服反馈,我们会尽快为您处理(人工客服工作时间:9:00-18:30)。
Philosophy: Absolute Customer Focus • Zero Tolerance for Waste • Stable Production Environment 理念:完全关注客户.零浪费.稳定的生产环境
14
小结 精益生产源自丰田,丰田将其运用得最出色 精益生产的核心是消除浪费 JCMS江森制造系统,是江森自控学习精益生产后, 结合自己特色,完善形成自己的完整的生产系统。
石油危机以后,丰田生产方式在日本汽车工业企业中得 到迅速普及并体现了巨大的优越性。1980年以其1100万 辆的产量全面超过美国,成为世界汽车制造第一大国。
1985年美国麻省理工学院数位国际汽车计划组织(IMVP )的专家-17个国家的 专家、学者,花费5年时间,耗资 500万美元,考察90多家工厂,以研究丰田。
TPS
JIT •节拍时间 •单件流 •下游拉动
标准作业
5S SMED TPM
自働化
•品质内置
3P 目视管理 看板 •停线解决问题
•人机分离
创新提案系统
•防错
平准化
•每日产量和品种均衡化
•使生产排程平顺
持续改善
9
丰田做了什么?
美国
丰田
-1896年杜里埃兄弟制造并销售了 -1896年丰田汽车的创始人丰田佐吉
JCMS 精益生产
CSHR-TR-748
课程目标
了解精益生产历史
熟悉JCMS精益生产核心理念
掌握精益生产工具:5s&目视化管理
标准化作业和持续改进(合理化建议)
TPM
2
3
汽车制造的历史
• 手工生产 1900’s • Craftsmanship
• 批量生产 1930’s • Mass Production
6
批量生产
美国汽车的平均售价也从1000美元左右,降到了360美元( 1907年)。
7
批量生产
无需高技能,每人只需做整个工作的一小部分 工作无自豪感、不满意 采用生产装配线 零部件可通用 批量单一产品 讲究产量,而非质量 价廉 生产周期短 生产投入高
8
丰田生产系统
60年代初, 丰田生产系统(TPS) :
一盒蛋糕的成本
100元一盒
烤8糊元一次蛋糕 电话 预定
10元 运输
12元
20元 面粉
包装 10元
配料 40元
18
增值Vs.浪费 增值是指改变产品的基本性质 没有增值的工作,称之为浪费 第一种:“必要”的浪费 第二种:“不必要”的浪费
15
16
从经济学角度来看...
Basic Economics
成本+利润=价格
Cost + Profit = Price
市场决定价格-制造商控制成本=利润
Market Determined Price - Producer Controlled Cost = Profit
17
如果你预定一盒蛋糕,你会愿意支付…?
High Safety,Morale & Productivity 高度安全,高涨士气,高生产力
Zero
Defects
Produced零缺陷生产
Just-In-Time Production Adaptable to Demand按照需求即时生产
Core
Elements 核心要素
People人员
Six Sigma Product Quality 六西格玛产品质量
精益是关于消除浪费,永无止境地追求消除浪费
12
江森制造系统 零浪费
Zero Tolerance for Waste 稳定的制造环境
A Stable Production Environment 客户拉动/即时供货
Customer “Pull” / Just-in-Time
13
JCMS Mission使命
1995年,出版了《改造世界的机器》一书,将丰田生产 方式定名为精益生产(Lean Production)。
11
什么是精益?
精,少而精,不投入多余的生产要素 益,所有的经营活动都要有益有效 精益源于丰田生产系统
精益生产
通过消除企业所有环节上的不增值活动,来达到降低成本、 缩短生产周期和改善品质的目的。
Process Results 过程结果
JCMS Manufacturing Excellence:卓越制造 People Dev., Product Quality, Material Flow
人员发展,产品质量,物流
Produce at the Pace of Customer Demand with Six Sigma Quality以六西格玛的质量按照客户的节拍生产
• 精益生产 1960’s • Lean Manufacturing
• 江森制造系统 Today • JCMS
4
手工生产
▪ 戈特利布·戴姆勒 ▪ 卡尔.本茨 ▪ (Karl Friedrich
Benz,1844-1926)
5
手工生产
技术工人 高度工作自豪感和满意度 工位固定,每项工作都在同一工位做 手工制造手工安装-单件制造 产量低 质量好 价格高 生产周期长
13辆四轮汽车
刚刚发明了“丰田式木制织机”
-1908年共有485家汽车制造商 -1933年在丰田自动织机制作所设立
-1914年福特汽车实现了汽车流水 汽车部
线生产
-1936年丰田AA型轿车初次问世
-1928年通用公司雪佛兰汽车年产 -1937年丰田汽车正式成立,产量只
量达到120万辆
有4000辆
整整落后40年
美国
丰田
-1950年美国工业劳动生产率是日 -1950年汽车制造业的差距至少相差
本的8-9倍
10倍
32年后-1982年
-每年人均生产汽车11.5辆
-每年人均生产汽车54.6辆
10
精益生产来源
丰田汽车公司从成立到1950年的十几年间,总产量甚至 不及福特公司一天的产量。
从50年代到70年代,丰田公司虽以独特的生产方式取得 了显著的成就
Lean
Material Flow 精益物料流动FounΒιβλιοθήκη ation基础Enablers
Discipline: Best Business Practices (BBP Metrics) 原则:最佳业务实践(BBP指标)
Leadership: Driving Continuous Improvement •Teamwork •5S Discipline 领导力:推动改进、团队合作、5S
14
小结 精益生产源自丰田,丰田将其运用得最出色 精益生产的核心是消除浪费 JCMS江森制造系统,是江森自控学习精益生产后, 结合自己特色,完善形成自己的完整的生产系统。
石油危机以后,丰田生产方式在日本汽车工业企业中得 到迅速普及并体现了巨大的优越性。1980年以其1100万 辆的产量全面超过美国,成为世界汽车制造第一大国。
1985年美国麻省理工学院数位国际汽车计划组织(IMVP )的专家-17个国家的 专家、学者,花费5年时间,耗资 500万美元,考察90多家工厂,以研究丰田。
TPS
JIT •节拍时间 •单件流 •下游拉动
标准作业
5S SMED TPM
自働化
•品质内置
3P 目视管理 看板 •停线解决问题
•人机分离
创新提案系统
•防错
平准化
•每日产量和品种均衡化
•使生产排程平顺
持续改善
9
丰田做了什么?
美国
丰田
-1896年杜里埃兄弟制造并销售了 -1896年丰田汽车的创始人丰田佐吉
JCMS 精益生产
CSHR-TR-748
课程目标
了解精益生产历史
熟悉JCMS精益生产核心理念
掌握精益生产工具:5s&目视化管理
标准化作业和持续改进(合理化建议)
TPM
2
3
汽车制造的历史
• 手工生产 1900’s • Craftsmanship
• 批量生产 1930’s • Mass Production
6
批量生产
美国汽车的平均售价也从1000美元左右,降到了360美元( 1907年)。
7
批量生产
无需高技能,每人只需做整个工作的一小部分 工作无自豪感、不满意 采用生产装配线 零部件可通用 批量单一产品 讲究产量,而非质量 价廉 生产周期短 生产投入高
8
丰田生产系统
60年代初, 丰田生产系统(TPS) :
一盒蛋糕的成本
100元一盒
烤8糊元一次蛋糕 电话 预定
10元 运输
12元
20元 面粉
包装 10元
配料 40元
18
增值Vs.浪费 增值是指改变产品的基本性质 没有增值的工作,称之为浪费 第一种:“必要”的浪费 第二种:“不必要”的浪费
15
16
从经济学角度来看...
Basic Economics
成本+利润=价格
Cost + Profit = Price
市场决定价格-制造商控制成本=利润
Market Determined Price - Producer Controlled Cost = Profit
17
如果你预定一盒蛋糕,你会愿意支付…?
High Safety,Morale & Productivity 高度安全,高涨士气,高生产力
Zero
Defects
Produced零缺陷生产
Just-In-Time Production Adaptable to Demand按照需求即时生产
Core
Elements 核心要素
People人员
Six Sigma Product Quality 六西格玛产品质量
精益是关于消除浪费,永无止境地追求消除浪费
12
江森制造系统 零浪费
Zero Tolerance for Waste 稳定的制造环境
A Stable Production Environment 客户拉动/即时供货
Customer “Pull” / Just-in-Time
13
JCMS Mission使命
1995年,出版了《改造世界的机器》一书,将丰田生产 方式定名为精益生产(Lean Production)。
11
什么是精益?
精,少而精,不投入多余的生产要素 益,所有的经营活动都要有益有效 精益源于丰田生产系统
精益生产
通过消除企业所有环节上的不增值活动,来达到降低成本、 缩短生产周期和改善品质的目的。
Process Results 过程结果
JCMS Manufacturing Excellence:卓越制造 People Dev., Product Quality, Material Flow
人员发展,产品质量,物流
Produce at the Pace of Customer Demand with Six Sigma Quality以六西格玛的质量按照客户的节拍生产
• 精益生产 1960’s • Lean Manufacturing
• 江森制造系统 Today • JCMS
4
手工生产
▪ 戈特利布·戴姆勒 ▪ 卡尔.本茨 ▪ (Karl Friedrich
Benz,1844-1926)
5
手工生产
技术工人 高度工作自豪感和满意度 工位固定,每项工作都在同一工位做 手工制造手工安装-单件制造 产量低 质量好 价格高 生产周期长
13辆四轮汽车
刚刚发明了“丰田式木制织机”
-1908年共有485家汽车制造商 -1933年在丰田自动织机制作所设立
-1914年福特汽车实现了汽车流水 汽车部
线生产
-1936年丰田AA型轿车初次问世
-1928年通用公司雪佛兰汽车年产 -1937年丰田汽车正式成立,产量只
量达到120万辆
有4000辆
整整落后40年
美国
丰田
-1950年美国工业劳动生产率是日 -1950年汽车制造业的差距至少相差
本的8-9倍
10倍
32年后-1982年
-每年人均生产汽车11.5辆
-每年人均生产汽车54.6辆
10
精益生产来源
丰田汽车公司从成立到1950年的十几年间,总产量甚至 不及福特公司一天的产量。
从50年代到70年代,丰田公司虽以独特的生产方式取得 了显著的成就
Lean
Material Flow 精益物料流动FounΒιβλιοθήκη ation基础Enablers
Discipline: Best Business Practices (BBP Metrics) 原则:最佳业务实践(BBP指标)
Leadership: Driving Continuous Improvement •Teamwork •5S Discipline 领导力:推动改进、团队合作、5S