齿轮轴的结构设计
传动齿轮轴的加工工艺设计说明书

摘要齿轮轴零件的主要作用是支撑回转零件、实现回转运动并传递转矩和动力。
齿轮轴具备传动效率高、结构紧凑和使用寿命长等一系列优点,是通用机械特别是工程机械传动中的重要零件之一。
齿轮轴加工材料、热处理方式、机械加工工艺过程的优化,将对提高齿轮轴的加工质量及寿命有着重要借鉴意义。
本设计首先分析了齿轮轴零件的作用和零件的材料,之后把加工传动齿轮轴所用的材料和生产类型确定下来。
然后确定毛坯的种类,绘制铸件零件图。
接下来设计零件的加工工艺性,包括零件表面的加工方法及热处理方法等。
最后进行工艺规程设计,选定加工所用的机床,刀具,夹具等。
齿轮轴零件的机械综合性能要求较高,一般选择锻件作为毛坯。
合理安排工艺路线,划分加工阶段对保证零件加工质量至关重要.关键词: 齿轮轴;工艺分析;工艺规程设计AbstractThe main function of the gear shaft is to support rotating parts, achieve rotary mo tion and transfer torque and power. Gear shaft has a series of advantages, such as high transmission efficiency, compact structure, long service life and so on. It is one of the important parts in the general machinery, particularly the engineering machinery tran smission. The optimization of the gear shaft’s machining materials, thermal treatmen t method and machining process will have great significance on the machining quality of the gear shaft and the service life.The first design of the gear shaft parts and parts of the material, then fix the processing gear shaft of the materials used and the type of production. And then determine the blank type, drawing casting parts diagram. The processing of the next design of parts, including the components surface processing method and heat treatment method. Finally, technological process design ,selection of the machine tool, cutting tool, fixture etc…Comprehensive mechanical performance requirements higher gear shaft parts, as general forging blank. Reasonable arrangements for the process, dividing the processing stage is very important to ensure the machining quality of parts.Keywords gear shaft; process analysis; process planning design目录摘要 (I)ABSTRACT (II)第1章绪论............................................................................................................. - 1 -第2章零件的分析 (2)2.1零件的作用 (2)2.1.1零件的作用 (2)2.1.2零件的结构特点及技术要求 (2)2.2零件材料分析 (3)2.3确定生产类型 (3)2.4毛坯的确定 (4)2.5绘制铸件零件图 (4)2.6本章小节 (5)第3章加工工艺过程分析 (5)3.1加工工艺过程的组成 (6)3.2定位基准的选择原则 (6)3.2.1基准的概念 (6)3.2.2 定位基准的选择 (7)3.2.3 定位基准的确定 (8)3.3零件表面加工方法的选择 (10)3.4加工工序安排 (10)3.5热处理工序的安排 (11)3.6工序的划分 (11)3.7加工余量及工序尺寸的确定 (12)3.7.1 加工余量的概念 (12)3.7.2 加工余量的确定方法 (12)3.8本章小结 (13)第4章选择加工设备及工艺设备 (14)4.1各机床的作用 (14)4.1.1车床的作用 (14)4.1.2铣床的作用 (15)4.1.3 磨床的作用 (16)4.1.4 零件加工中各机床的确定 (17)4.2刀具的选择 (17)4.2.1 刀具材料的确定 (17)4.2.2 刀具的分类 (17)4.2.3 常用车刀刀具的用途 (18)4.2.4 铣刀 (19)4.2.5 磨削 (20)4.2.6 加工零件刀具的确定 (20)4.3夹具的确定 (20)4.3.1 夹具的组成及作用 (20)4.3.2 夹具的分类 (21)4.3.3 选择夹具 (22)4.4量具的选择 (22)4.5本章小结 (23)第5章齿轮轴的工艺卡拟定 (24)5.1工艺卡的拟定 (24)5.2问题的提出 (28)5.3本章小结 (29)总结 (30)参考文献 (31)致谢 (32)第1章绪论本文设计的主要是齿轮轴的加工工艺,通过总结零件的的加工,提高所加工工件的质量,完善产品,满足要求,提高经济效益和劳动生产率。
单级圆柱齿轮传动机构设计(完整版)

机械设计课程设计计算说明书一、设计课题及任务要 (2)二、传动方案的拟定 (3)三、电动机选择 (4)四、确定传动装置的总传动比及其分配 (5)五、传动装置的运动和动力设计 (5)六、高速齿轮轴(第一轴设计) (7)七、第二轴大齿轮设计 (14)八、轴承选型与计算 (15)九、设计心得 (16)一、设计课题:单级圆柱齿轮传动机构设计二、设计任务要求:(设计步骤参考文献[1]第17章实例)(1)确定齿轮机构传动方案(参考[1]第2、第17章);根据所给数据,确定单级圆柱齿轮机构各轴的输入功率、转速和转矩(参考[1]中2.3和2.4);选择电动机的额定功率(W)和同步转速(r/min);(2)高速齿轮轴(第一轴)设计参考[1]中162页进行高速轴的结构设计、参考教材中“圆柱齿轮强度设计”的内容,对小齿轮进行设计与校核(齿轮模数选用[2]教材第75页表7-1,第一系列中的数值)、进行键的选择与校核、按[2]第16章204“对于既传递转矩又承受弯矩的轴”设计方法核公式,对该轴进行强度校核;(3)第二轴大齿轮设计计算确定大齿轮的参数并校核(选择硬齿面齿轮的材料和热处理方式)、计算大齿轮的几何尺寸,选择大齿轮的结构(参考[2]第7章)。
(4)轴承选型参考[2]第18章例18-3,选择并校核一轴和二轴的轴承型号。
(5)制图:绘制单级圆柱齿轮传动机构高速齿轮轴图1份(A3)、第二轴大齿轮图1份(A4);参考[1]的附图2和有关的设计资料。
要求:图纸表达清楚规范,标注尺寸完整,注有主要的公差或极限尺寸;图纸具有边框、标题栏、技术要求;手画或计算机制图均可。
(6)编写设计说明书1份,参考[1] 4.7节、第17章;要求:结构规范、层次清楚、图文并茂。
手写或计算机打字都可以。
(7)注:不设计箱体(8)课程设计为单独评分,是必修的学分。
计算过程及计算说明结果一、传动方案拟定设计单级圆柱齿轮传动机构1、工作条件:使用年限4年,工作为一班工作制,载荷平稳,环境清洁。
机械原理_齿轮传动
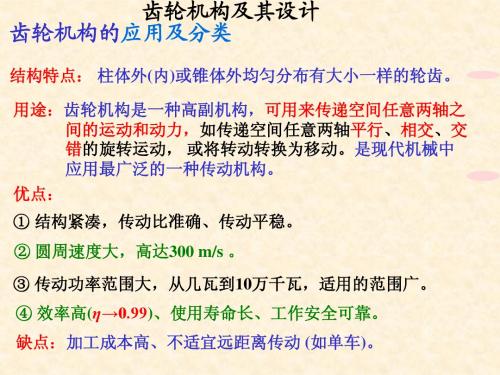
齿轮机构及其设计 渐开线直齿圆柱齿轮的啮合传动 一对轮齿的啮合过程及连续传动条件
1 [ Z1(tg a1 tg ) Z 2 (tg a 2 tg )] 外啮合 2 1 [ Z1 (tg a1 tg ) Z 2 (tg a 2 tg )] 内啮合 2 2ha Z1 (tg a1 tg ) 齿轮齿条 2 sin 2 与m无关,随Z增大而增大,当Z 也增大到无
齿轮机构及其设计 渐开线标准齿轮的基本参数和几何尺寸 标准齿条的特点
1) 各同侧齿廓均为相互平行的直线,且齿廓上各 点压力角α相等,均等于齿形角 2) 不同线上的齿距相等,均为pi=p =πm,但 只有分度线上e=s
ha 、 h f 、h 、e 、s 、p 、c 等 仍用表10—2中有关公式计算
齿轮机构及其设计 渐开线直齿圆柱齿轮的啮合传动 渐开线直齿圆柱齿轮传动的 啮合过程 N1N2—理论上可能 的最长啮合线段, 特称为理论啮合线 N1、N2为啮合极限点 B1B2—实际啮合线
齿轮机构及其设计 渐开线直齿圆柱齿轮的啮合传动 一对轮齿的啮合过程及连续传动条件 齿轮齿条啮合传动
PB1不变, ha 2 ha m PB2 且 sin sin 2 h 1 a [ Z1 (tg a1 tg ) ] 2 sin cos 2ha Z1 (tg a1 tg ) 2 sin 2
m1 m2 m 正确啮合条件 1 2
齿轮机构及其设计 渐开线直齿圆柱齿轮的啮合传动 齿轮传动的中心距与啮合角
1 a (d 1 d 2 ) 2 m ( Z1 Z 2 ) 2
c
c c m
标准安装
1 d2 ) a (d 1 2
齿轮与轴的三种连接方式

齿轮与轴的连接方式齿轮传动设计1、选择材料及确定许用应力考虑到传动功率不大(1P =2.85kw ),所以齿轮选择软齿面。
由已知条件(单向传动、载荷较平稳)通过查《机械设计基础》表11-1,小齿轮选用40Cr 调质,齿面硬度217~286HBS ,1lim H σ=730Mpa ,1FE σ=580Mpa ;大齿轮选用45钢调质,齿面硬度197~286HBS ,2lim H σ=600Mpa ,2FE σ=450Mpa 。
由表11-5,取H S =1.1,F S =1.25。
所以,[]1H σ=HH S 1lim σ=Mpa 1.1730=664Mpa[]2H σ=Mpa 1.1600=545Mpa[]1F σ=FFE S 1σ=Mpa 25.1580=464Mpa[]2F σ=Mpa 25.1450=360Mpa2、按齿面接触强度设计根据表11-2,设齿轮按8级精度设计。
由表11-3取载荷系数K=1.2,由表11-6取齿宽系数d φ=0.8,小齿轮转矩1T =0.48×510N·mm,由表11-4取EZ =188,又HZ ,所以[]3211112⎪⎪⎭⎫⎝⎛+≥H HE d Z Z KT d σμμφ=3255455.21886168.01048.02.12⎪⎭⎫⎝⎛⨯+⨯⨯⨯⨯≈49.99mm取1Z =20,2Z =01i 1Z =6×20=120(《机械设计指导》表16-2) 模数m=111Z d =2099.49㎜=2.5 齿宽b=d φ11d =0.8×49.99mm=39.99mm大齿轮的齿宽b=40mm 小齿轮的齿宽b=45mm取2b =45mm,1b =50mm,按表4-1取m=2.5mm,实际的11d =1Z m=20×2.5mm=50mm,12d =120×2.5mm=300mm 中心距1a =21211d d +=175mm 验算轮齿弯曲强度齿形系数1Fa Y =2.94(图11-8),1Sa Y =1.56(图11-9)2Fa Y =2.13,2Sa Y =1.811F σ=121112z bm Y Y KT Sa Fa =205.299.3956.194.21048.02.1225⨯⨯⨯⨯⨯⨯⨯=105.7Mpa ≤[]1F σ=464Mpa 2F σ=11221Sa Fa Sa Fa F Y Y Y Y σ=56.194.281.113.27.105⨯⨯⨯Mpa=88.85Mpa ≤[]2F σ=360Mpa,安全。
齿轮设计过程
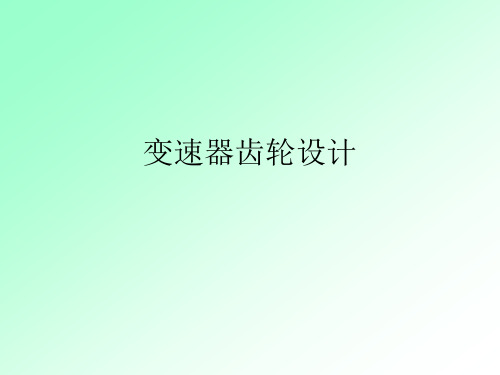
(二)根据接触强度计算确定中心距a或者小齿轮的直径d1, 根据弯曲强度计算确定模数。
1.渐开线圆柱齿轮受力分析及计算 (1)直齿受力分析
Fr Fn α
Ft
P
法向载荷Fn垂直于齿面,为计算方便Fn在节点P 处分解为两个互相垂直的分力,即圆周力Ft与Fr。
公式:
T1
9549
P n1
Ft
2T1 d1
T1——传递的转矩 d1——分度圆直径
α——啮合角
(2)斜齿受力分析
Fr Ft tan
Fn
Ft cos
Fr
αt
Ft
P
αn Fn Fr
F’ P
F’ Fa β
Ft P
如图所示:
圆周力 径向力
Ft
2T1 d1
,
F ' Ft ห้องสมุดไป่ตู้os
F'
F'
tan n
Ft tann cos
轴向力 Fa Ft tan
举例 名称:输出齿轮 材料:20CrMnTi 热处理技术条件:齿面渗碳淬火,渗碳层深度0.8~1.2mm,齿面硬度 HRC58~62,心部硬度HRC32~45。 加工工艺路线:下料→锻造→正火→加工齿形→局部镀铜(防渗)→渗 碳、淬火、低温回火→喷丸→磨齿。
热处理工艺:正火、渗碳、淬火及低温回火。
r1 r2
Fn1 FR1
β1
Fa1
1
2
Fa2
T
β2
FR2
Fn2
中间轴轴向力的平衡
由上图可知,欲使中间轴上两斜齿轮的轴向力平衡, 需满足下述条件: Fa1=Fn1tanβ1 Fa2=Fn2tanβ2
由于传递的转矩T=Fn1r1=Fn2r2,为使两轴向力平衡,必须满足
我的齿轮轴毕业设计

我的齿轮轴毕业设计
作为机械工程专业的一名毕业生,我在大学期间学习了许多有关机械设计方面的知识,其中齿轮轴设计是一个非常重要的课题。
因此,我的毕业设计便是以齿轮轴为主题。
我的齿轮轴毕业设计的目的是设计一种新型齿轮轴,以提高其功率传输效率和耐久性。
设计过程分为以下几个步骤:
步骤一:确定设计要求
首先,我需要确定齿轮轴的工作环境、工作载荷、转速和传动比等基本参数。
这些参数将会影响齿轮轴的尺寸和结构设计。
步骤二:进行齿轮轴的初始设计
在这一步骤中,我将会综合考虑设计要求和可行性,对齿轮轴的初始设计进行初步的确定,并推导齿轮的参数。
这一步骤旨在将齿轮轴设计的具体化,并在此基础上,建立齿轮轴的数学模型。
步骤三:制定齿轮轴的计算公式及程序
在此步骤中,我将会采用MATLAB等软件,建立齿轮轴的数学模型,并制定出与实际情况相符的计算公式和程序。
这一步骤将会为齿轮轴的设计提供实际参考数据,并为后续的仿真与实验提供基础。
步骤四:进行齿轮轴的仿真
在此步骤中,我将会运用ANSYS等软件,对齿轮轴进行有限元仿真,以验证齿轮轴的结构和参数设计是否满足设计要求,同时,通过仿真模拟实际工作环境,验证齿轮轴的耐久性和寿命。
步骤五:进行齿轮轴的实验
在齿轮轴的实验中,我将会进行齿轮轴的制作,并通过实验验证齿轮轴设计的可行性和有效性,同时,实验中对齿轮轴的耐久性和寿命进行检测。
最后,我将会对毕业设计的整个流程进行总结,并从设计、计算、仿真、实验等多个方面进行分析和总结,以期对齿轮轴的设计和研究提供有意义的参考。
双联齿轮轴机械加工工艺流程
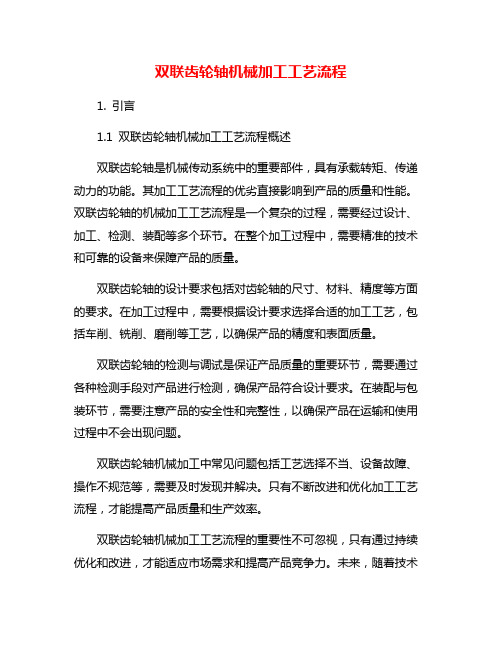
双联齿轮轴机械加工工艺流程1. 引言1.1 双联齿轮轴机械加工工艺流程概述双联齿轮轴是机械传动系统中的重要部件,具有承载转矩、传递动力的功能。
其加工工艺流程的优劣直接影响到产品的质量和性能。
双联齿轮轴的机械加工工艺流程是一个复杂的过程,需要经过设计、加工、检测、装配等多个环节。
在整个加工过程中,需要精准的技术和可靠的设备来保障产品的质量。
双联齿轮轴的设计要求包括对齿轮轴的尺寸、材料、精度等方面的要求。
在加工过程中,需要根据设计要求选择合适的加工工艺,包括车削、铣削、磨削等工艺,以确保产品的精度和表面质量。
双联齿轮轴的检测与调试是保证产品质量的重要环节,需要通过各种检测手段对产品进行检测,确保产品符合设计要求。
在装配与包装环节,需要注意产品的安全性和完整性,以确保产品在运输和使用过程中不会出现问题。
双联齿轮轴机械加工中常见问题包括工艺选择不当、设备故障、操作不规范等,需要及时发现并解决。
只有不断改进和优化加工工艺流程,才能提高产品质量和生产效率。
双联齿轮轴机械加工工艺流程的重要性不可忽视,只有通过持续优化和改进,才能适应市场需求和提高产品竞争力。
未来,随着技术的进步和需求的变化,双联齿轮轴机械加工工艺流程将会不断向更智能、高效的方向发展。
2. 正文2.1 双联齿轮轴的设计要求1. 双联齿轮轴的功能需求:双联齿轮轴通常用于传动机械设备中,因此在设计之前需要明确定义其功能需求,包括传递扭矩、转速、传动比等参数。
2. 双联齿轮轴的结构设计:在设计双联齿轮轴时,需要考虑其结构形式,包括轴的长度、直径、螺纹部分、轴承座、键槽等设计要素,确保其在工作时具有足够的强度和刚度。
3. 双联齿轮轴的材料选择:根据双联齿轮轴的工作环境和要求,需要选择适合的材料进行制造,通常选用优质的合金钢或不锈钢材料。
4. 双联齿轮轴的表面处理:为了提高双联齿轮轴的耐磨性和抗腐蚀性,通常需要对其表面进行适当的处理,如表面镀铬、氮化处理等。
(完整版)减速器的轴及轴上零件的结构设计

减速器的轴及轴上零件的结构设计一、轴的结构设计轴结构设计包括确定钢的结构形状和尺寸。
轴的结构是由多方面的因素决定的,其中主要考虑轴的强度、刚度、轴上零件的安装、定位、轴的支承结构以及轴的工艺性等,其设计方法和结构要素的确定,可参照教科书有关章节进行。
单级圆柱齿轮减速器的轴一般均为阶梯轴,确定阶梯轴各段的直径和长度是阶梯轴设计的主要内容。
下面通过图1-2-17和表1-2-2、表1-2-3来说明。
1、阶梯轴各段直径的确定图1-2-17中阶梯轴各段的直径可由表1-2-2确定。
符号确定方法及说明d1按许用扭转应力进行估算。
尽可能圆整为标准直径,如果选用标准联轴器,d1应符合联轴器标准的孔径。
d2d2= d1+2a,a为定位轴肩高度。
通常取a=3-10mmd2尽可能符合密封件标准孔径的要求,以便采用标准密封圈。
d3此段安装轴承,故d3必须符合滚动轴承的内径系列。
为便于轴承安装,此段轴径与d2段形成自由轴肩,因此,d3= d2+1~5mm,然后圆整到轴承的内径系列。
当此轴段较长时,可改设计为两个阶梯段,一段与轴承配合,精度较高,一段与套筒配d4d4= d3+1~5mm(自由轴肩),d4与齿轮孔相配,应圆整为标准直径。
d5d5= d4+2a,a为定位轴环高度,通常可取a=3~10mmd6d6= d3,因为同一轴上的滚动轴承最好选取同一型号。
图1-2-17中各阶梯长度可由表1-2-3确定。
符号确定方法及说明L1按轴上零件的轮毂宽度决定,一般比毂宽短2~3mm。
也可按(1.2~1.5)d1取定。
L2L2=l3+l4(l3为轴承端盖及联接螺栓头的高度)L3L3=B+l2+⊿2+(2~3) B轴承宽度L4L4按齿轮宽度b决定,L4=b-(2~3)mmL5 无挡油环时,L5=B 有挡油环时,L5=B+挡油环的毂宽注:表中l2、l3、l4、⊿2参见表1-2-4。
由表中计算式可知,各段长度的确定与箱外的旋转零件至固定零件的距离l4;轴承端盖及联接螺栓头高度的总尺寸l3;轴承端面至箱体内壁的距离l2;转动零件端面至箱体内壁的距离⊿2以及档油环的结构尺寸有关,这些尺寸又取决于轴承盖的类型、密封型式以及各零件在装配图中的相关位置。
- 1、下载文档前请自行甄别文档内容的完整性,平台不提供额外的编辑、内容补充、找答案等附加服务。
- 2、"仅部分预览"的文档,不可在线预览部分如存在完整性等问题,可反馈申请退款(可完整预览的文档不适用该条件!)。
- 3、如文档侵犯您的权益,请联系客服反馈,我们会尽快为您处理(人工客服工作时间:9:00-18:30)。
目 录7.轴类零件设计7.1 I 轴的设计计算1.求轴上的功率,转速和转矩由前面算得P 1=5.76KW ,n 1=440r/min ,T 1=1.3510⨯N mm ⋅ 2.求作用在齿轮上的力已知高速级小齿轮的分度圆直径为d 1=70mm 而 F t112d T =701300002⨯==3625N F r =F =αtan t 3625︒⨯20tan =1319N 压轴力F=1696N1—输送带2—电动机3—V 带传动4—减速器5—联轴器3.初步确定轴的最小直径现初步估算轴的最小直径。
选取轴的材料为45钢,调质处理据[2]表15-3,取A 0=110,于是得: d m in =A 0==33114400.75110n P 26mm 因为轴上应开2个键槽,所以轴径应增大5%-7%故d=20.33mm ,又此段轴与大带轮装配,综合考虑两者要求取d m in =32mm ,查[4]P 620表14-16知带轮宽B=78mm 故此段轴长取76mm 。
4.轴的结构设计(1)拟定轴上零件的装配方案通过分析比较,装配示意图7-1图7-1(2)据轴向定位的要求确定轴的各段直径和长度1)I-II 段是与带轮连接的其d II I -=32mm ,l II I -=76mm 。
2)II-III 段用于安装轴承端盖,轴承端盖的e=9.6mm (由减速器及轴的结构设计而定)。
根据轴承端盖的拆卸及便于对轴承添加润滑油的要求,取端盖与I-II 段右端的距离为38mm 。
故取l III II -=58mm ,因其右端面需制出一轴肩故取d III II -=35mm 。
3)初选轴承,因为有轴向力故选用深沟球轴承,参照工作要求并据dIIIII -=35mm ,由轴承目录里初选6208号其尺寸为d B D ⨯⨯=40mm ⨯80mm ⨯18mm 故d IV III -=40mm 。
又右边采用轴肩定位取ⅤⅣ-d =52mm 所以l ⅤⅣ-=139mm ,ⅥⅤ-d =58mm ,ⅥⅤ-l =12mm 4)取安装齿轮段轴径为d ⅦⅥ-=46mm ,齿轮左端与左轴承之间用套筒定位,已知齿轮宽度为75mm 为是套筒端面可靠地压紧齿轮,此轴段应略短于齿轮宽度故取l ⅦⅥ-=71mm 。
齿轮右边Ⅶ-Ⅷ段为轴套定位,且继续选用6208轴承,则此处d ⅧⅦ-=40mm 。
取l ⅧⅦ-=46mm (3)轴上零件的周向定位齿轮,带轮与轴之间的定位均采用平键连接。
按d II I -由[5]P 53表4-1查得平键截面b 810⨯=⨯h ,键槽用键槽铣刀加工长为70mm 。
同时为了保证带轮与轴之间配合有良好的对中性,故选择带轮与轴之间的配合为67n H ,同样齿轮与轴的连接用平键14639⨯⨯,齿轮与轴之间的配合为67n H 轴承与轴之间的周向定位是用过渡配合实现的,此处选轴的直径尺寸公差为m6。
(4)确定轴上圆角和倒角尺寸参考[2]表15-2取轴端倒角为2︒⨯45.其他轴肩处圆觉角见图。
5.求轴上的载荷先作出轴上的受力图以及轴的弯矩图和扭矩图7-2图7-2现将计算出的各个截面的M H ,M V 和M 的值如下: F 1NH =1402N F 2NH =1613N F 1NV =2761N F 2NV =864N M 1H =86924N mm ⋅ M H2=103457mm N ⋅ M V =171182N mm ⋅M 1=52210.717.80⨯+=510.02⨯N mm ⋅M 2=M H2=103457N mm ⋅ T 1=1.3510⨯N mm ⋅ 6.按弯扭合成应力校核轴的强度进行校核时,通常只校核危险截面的强度,从轴的结构图以及弯矩图和扭矩图中可以看出截面A 是轴的危险截面。
则根据[2]式15-5及上面的数据,取α=0.6轴的计算应力:WT M ca 2321)(ασ+=3522461.010)1.36.0(2.0⨯⨯⨯+==23.7MP 前面选用轴的材料为45钢,调制处理,由[2]表15-1 查得[1-σ]=60Mp ,][1-≤σσca ,故安全。
7.2 II 轴的设计计算1.求轴上的功率,转速和转矩由前面的计算得P 1=5.76KW ,n 1=440m inr ,T 1=1.3510⨯N mm ⋅2.求作用在齿轮上的力已知中间轴大小齿轮的分度圆直径为 d 2=327.5mm d 3=108mm而 F 1t 212d T =.5327103.125⨯⨯==767N F 1r =F =αtan 1t 767︒⨯20tan =279N 同理可解得:F 2t 422d T ===⨯⨯10810.652510498N ,F 2r =F =αtan 1t 1730N 3.初步确定轴的最小直径现初步估算轴的最小直径。
选取轴的材料为45钢,调质处理据[2]表15-3,取A 0=110,于是得: d m in =A 0=⨯=3322.192.55110n P 43.0mm因为轴上应开2个键槽,所以轴径应增大5%-7%故d m in =45.2mm ,又此段轴与轴承装配,故同时选取轴承,因为轴承上承受径向力,故选用深沟球轴承,参照工作条件可选6210其尺寸为:d B ⨯⨯D =502090⨯⨯故d II I -=50mm 右端用套筒与齿轮定位,套筒长度取24mm 所以l II I -=48mm 4.轴的结构设计(1)拟定轴上零件的装配方案通过分析比较,装配示意图7-4图7-4 (2)据轴向定位的要求确定轴的各段直径和长度1)II -III 段为高速级大齿轮,由前面可知其宽度为70mm ,为了使套筒端面与大齿轮可靠地压紧此轴段应略短于齿轮轮毂宽度。
故取l III II -=64mm ,d III II -=56mm 。
2)III-IV 段为大小齿轮的轴向定位,此段轴长度应由同轴条件计算得l IV III - =15mm ,d IV III -=68mm 。
3)IV-V 段为低速级小齿轮的轴向定位,由其宽度为113mm 可取l V IV -=109mm ,d V IV -=56mm4)V-VI 段为轴承同样选用深沟球轴承6210,左端用套筒与齿轮定位,取套筒长度为24mm 则 l VI V - =48mm d VI V -=50mm(3)轴上零件的周向定位两齿轮与轴之间的定位均采用平键连接。
按d ⅢⅡ-由[5]P 53表4-1查得平b 631016⨯⨯=⨯⨯L h ,按d V IV -得平键截面b L h ⨯⨯=1611010⨯⨯其与轴的配合均为67n H 。
轴承与轴之间的周向定位是用过渡配合实现的,此处选轴的直径尺寸公差为m6。
(4)确定轴上圆角和倒角尺寸参考[2]表15-2取轴端倒角为2︒⨯45.个轴肩处圆觉角见图。
5.求轴上的载荷先作出轴上的受力图以及轴的弯矩图和扭矩图如图7-4。
现将计算出的各个截面的M H ,M V 和M 的值如下:F 1NH =719N F 2NH =2822N F 1NV =4107N F 2NV =7158N M 1H =49611N mm ⋅M 1H =253980N ⋅mm M 1V =-283383N mm ⋅ M 2V =-644220N mm ⋅M 1=522100.58.2⨯+=284000N mm ⋅ M 2=52210)2.5(6.4⨯+=690000N mm ⋅T 2=5.6510⨯N mm ⋅图7-46.按弯扭合成应力校核轴的强度进行校核时,通常只校核危险截面的强度,从轴的结构图以及弯矩图和扭矩图中可以看出截面B和Ⅵ的右侧是轴的危险截面,对该轴进行详细校核,对于截面B则根据[2]式15-5及上面的数据,取α=0.6,轴的计算应力W TM ca2322)(ασ+=3522561.010).656.0(.96⨯⨯⨯+==50.6MP前面选用轴的材料为45钢,调制处理,由[2]表15-1查得[1-σ]=60Mp ,][1-≤σσca 。
对于Ⅵ的右侧33317561561.01.0mm d W =⨯=⨯= 3335123562.0mm W t =⨯=a b MP W M 3.3917561690000===σ a T T MP W T 1.1635123560000===τ由[2]表15-1查得a B MP 640=σ a MP 2751=-σ a MP 1551=-τ 由[2]表3-8查得64.2=σσεk11.2=ττεk由[2]附图3-4查得92.0==τσββ由[2]中13-ξ和23-ξ得碳钢的特性系数,取1.0=σϕ,05.0=τϕ 故综合系数为 73.2192.0164.211=-+=-+=σσσσβεk K 20.2192.0111.211=-+=-+=ττττβεk K 故Ⅵ右侧的安全系数为 56.201.03.3973.22751=⨯+⨯=+=-m a K S σϕσσσσσ56.821.1605.021.162.21551=⨯+⨯=+=-m a K S τϕτττττ46.256.856.256.856.22222=+⨯=+=τστσS SS S S ca >S=1.5故该轴在截面Ⅵ的右侧的强度也是足够的。
综上所述该轴安全。
7.3 III 轴的设计计算1.求轴上的功率,转速和转矩由前面算得P 3=5.28KW ,n 3=28.6r/min ,T 3=1.76610⨯N mm ⋅ 2.求作用在齿轮上的力已知低速级大齿轮的分度圆直径为 d 4=352mm而 F t 432d T ===⨯⨯352101.762610081N F r =F =αtan t 10081=︒⨯20tan 3669N 3.初步确定轴的最小直径现初步估算轴的最小直径。
选取轴的材料为45钢,调质处理据[2]表15-3,取A 0=110,于是得: d m in =A 0=⨯=3333.6288.25110n P 62.8mm 同时选取联轴器型号。
联轴器的计算转矩T ca =K 3T A 查[2]表14-1取K A =1.3.则:T mm N T K A ca ⋅=⨯⨯==2288000106.71.3163按计算转矩应小于联轴器的公称转矩的条件查[5]P 99表8-7可选用LX4型弹性柱销联轴器。
其公称转矩为2500000N mm ⋅。
半联轴器孔径d=63mm ,故取d II I -=63mm 半联轴器长度L=142mm ,半联轴器与轴配合的毂孔长度l 1=132mm 。
4.轴的结构设计(1)拟定轴上零件的装配方案通过分析比较,装配示意图7-5图7-5(2)据轴向定位的要求确定轴的各段直径和长度1)为满足半联轴器的轴向定位,I-II 右端需制出一轴肩故II-III 段的直径d III II -=65mm ;左端用轴端挡圈定位取轴端挡圈直径D=65mm 。