mt3dms_v5_supplemental
RexrothMTX简明调试手册
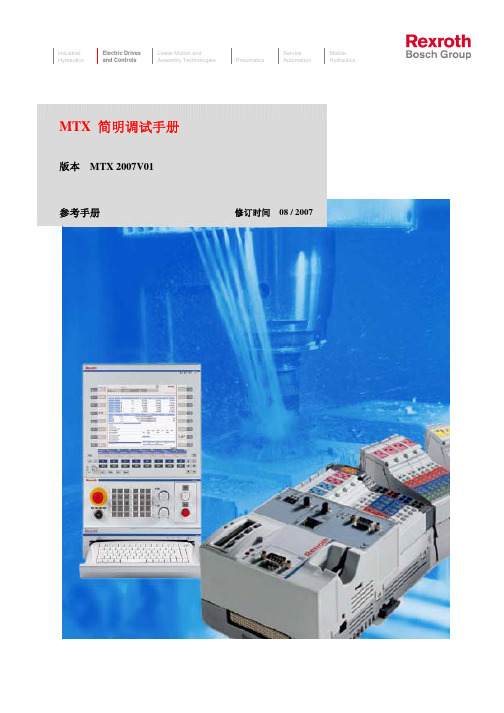
2.2.4 键盘------------------------------------------------------------------------------13 2.2.5 RECO Inline 模块-------------------------------------------------------------14 2.2.6 驱动器---------------------------------------------------------------------------17
修订时间 08 / 2007
前言
首先,欢迎您使用博世力士乐的产品,本手册主要面向机床及相似应用的 OEM 厂商所编制,里面主要介绍了 MTX 在应用方案中的常用配置、接线方式及一个简 单的工程实例,希望对您的设计有所帮助。如果您在设计初期,对安装尺寸有所 需求,可以直接参阅我们在附录中的硬件尺寸介绍。
2.2.2 工控机---------------------------------------------------------------------------7
2.2.3 操作面板------------------------------------------------------------------------10
3. PLC 主程序的编制-----------------------------------------------------------------------------40
5) 编译、下载及运行 PLC 程序--------------------------------------------------------40
六、螺距补偿----------------------------------------------------------------------------------------------56 七、数据的备份与恢复----------------------------------------------------------------------------------58
欣技CipherLAB 1500扫描器资料
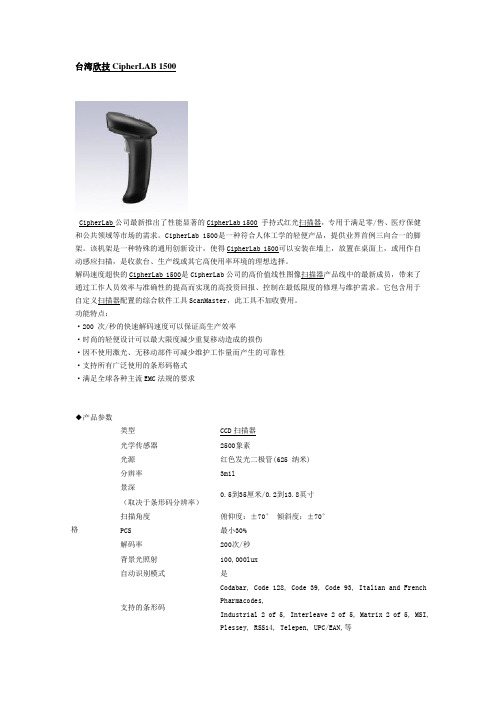
台湾欣技CipherLAB 1500CipherLab公司最新推出了性能显著的CipherLab 1500 手持式红光扫描器,专用于满足零/售、医疗保健和公共领域等市场的需求。
CipherLab 1500是一种符合人体工学的轻便产品,提供业界首例三向合一的脚架。
该机架是一种特殊的通用创新设计,使得CipherLab 1500可以安装在墙上,放置在桌面上,或用作自动感应扫描,是收款台、生产线或其它高使用率环境的理想选择。
解码速度超快的CipherLab 1500是CipherLab公司的高价值线性图像扫描器产品线中的最新成员,带来了通过工作人员效率与准确性的提高而实现的高投资回报、控制在最低限度的修理与维护需求。
它包含用于自定义扫描器配置的综合软件工具ScanMaster,此工具不加收费用。
功能特点:²200 次/秒的快速解码速度可以保证高生产效率²时尚的轻便设计可以最大限度减少重复移动造成的损伤²因不使用激光、无移动部件可减少维护工作量而产生的可靠性²支持所有广泛使用的条形码格式²满足全球各种主流EMC法规的要求◆产品参数格类型CCD扫描器光学传感器2500象素光源红色发光二极管(625 纳米)分辨率3mil景深0.5到35厘米/0.2到13.8英寸(取决于条形码分辨率)扫描角度俯仰度:±70° 倾斜度:±70°PCS最小30%解码率200次/秒背景光照射100,000lux自动识别模式是支持的条形码Codabar, Code 128, Code 39, Code 93, Italian and FrenchPharmacodes,Industrial 2 of 5, Interleave 2 of 5, Matrix 2 of 5, MSI,Plessey, RSS14, Telepen, UPC/EAN,等编程特性数据编辑、界面选择、符号组态语言支持美式英语和英式英语/法语/意大利语/比利时语/挪威语/瑞典语/西班牙语/葡萄牙语/德语外型重量145克/5.1盎斯颜色黑色开关接触开关電氣特性电压+5伏 10%能量消耗30毫安/170毫安/250毫安备用/扫描/最大值操作环境操作温度0℃to 50℃ / 32℉ to 122℉储藏温度-22℃to 60℃ / -4℉ to 140℉操作/储藏湿度不凝结10% to 90% / 5% to 95%抗震从1.5米(4.9英尺)高度多次撞击到混凝土面上防护等级IP30静电放电±8kV 接触±15 kV 气流EMC规范FCC / CE / C-tick / MIC / BSMI / IC配置设置选项包括以Windows授权为基础的CipherLab ScanMaster软件(包含),通过直接连接或印刷条形码配置。
MT Alliance V5.X WattsOn power monitor模型添加指南说明书

How to add the WattsOn power monitor model in MT Alliance V5.XThe 023-0293 WattsOn-1200-MSCT1-100A (120kW) is available in version 5.2The 023-0330 WattsOn-1200-MSCT1-200A (220kW) is available in version 5.2.1 Under ELKOR manufacturerFirst copy the diagram file “Elkor WattsOn-1200.bmp” (see Wiring diagram on page 4) in the folder Alliance\Images\Sensor Models\Click Sensor Model in the configure menuClick AddFill the form as described belowThese setting are for the WattsOn-1200-MSCT1-100A used with 3 MSCT1 CTs. For the WattsOn-1200-MSCT1-200A put 220 instead of 120.Click OKIf needed you can define the Power Factor Sensor Model as belowClick AddOnce completed you won’t have to repeat this step again for this site.To drop the Real Power reading, zoom in the appropriate viewDrag and drop a sensor from the Component boxMake the appropriate selection (120kW or 220kW) and click OK.Click on the new button and configure the name, disable or configure the alarm limits and the sensor node inputTo drop the Power Factor reading, zoom in the appropriate viewDrag and drop a sensor from the Component boxMake the following selection and click OK.Click on the new button and configure the name, disable or configure the alarm limits and the sensor node inputUser defined sensors are not available for a plug-in.Wiring diagramIf the CTs are not facing the same current direction the Power signal won’t be accurate and the Diag LED may not detect the fault.The WattsOn can be configured in different ways using a laptop with the appropriate software connected to the MODBUS port. So make sure you are using the respectively the WattsOn-1200-MSCT1-100A or 200A especially customized for this purpose or the output signals won’t reflect the expected values.For more information for the WattsOn installation see the Elkor WattsOn manual.。
新海滩显示器国际有限公司 5.0英寸HDMI TFT模块用户指南说明书

5.0” HDMI TFT ModulesNewhaven Display International2661 Galvin Court ▪ Elgin IL ▪ 60124Phone: 847.844.8795 Fax: 847.844.8796Sales:*************************** Technical Support:**************************U s e r G u i d ePart NumberingNHD - x.x - HDMI - N - xxxx - xxx1 2 3 4 5 61 Manufacturer –Newhaven Display2 Size (in inches)–5.0” Diagonal–7.0” Diagonal3 Interface –HDMI Interface4 Descriptor –800x480 Resolution, Video Only [HDMI audionot supported]5 Type –Premium MVA [Standard model for 7.0” size]–n/a [Only available in 7.0” size]–n/a [Only available in 7.0” size]6 Touch Panel–No Touch–Capacitive USB-HID [Pre-calibrated, No external drivers needed]–Resistive USB-HID [Pre-calibrated, No external drivers needed]Table of ContentsOverview (3)Functions and Features (3)Model Information (4)Electrical Characteristics (4)HDMI Receiver Information (4)Interface Description (4)Connecting with Windows/Windows Embedded (6)Connecting with Linux (8)Technical Resources (9)2D Drawings (9)3D Models (9)EDID Timing (9)Schematic (9)EDID Array (9)Quality Information (10)Precautions for Using LCDs/LCMs (10)Warranty Information (10)Document Revision History (11)OverviewThe HDMI interface has become the most popular video interface standard to date, and HDMI video sources are easier to come by now than ever before. Whether you need an HDMI TFT display for your Raspberry Pi/BeagleBone Black application, a Windows/Windows Embedded PC monitor, or a touch screen HMI for your Linux or other embedded system, the Newhaven Display HDMI TFT product line offers a solution.Our HDMI TFT Modules unite our existing high-quality TFT display panels with a custom PCB engineered in the USA by Newhaven Display. Assembled to the display, our PCB provides the user an all-in-one, plug-and-play HDMI + USB Touch solution for virtually any application.Functions and Features5.0” HDMI TFT Module w/ USB-HID Capacitive or Resistive Touch optionsOn-board Texas Instruments TFP401A HDMI/DVI ReceiverHDMI (Type-A) InputCompatible with PC (Windows/Linux)Compatible with Linux based SBCs such as Raspberry Pi, BeagleBone, etc.Plug-and-play USB-HID Touch, no external driver installation required24-bit True Color, 800x480 Resolution (WVGA)On-board Texas Instruments TPS61165 High Brightness LED Driver w/ PWM75° Viewing Angles all sides4 x 3.5mm Mounting Holes Enabling Standard M3 or #6-32 ScrewsOpen-Source Hardware, Engineered in Elgin, IL (USA)Model InformationHDMI Module P/N TFT Panel Used DisplayTypeLuminanceRatingOptimalViewingAngleTouchPanelNHD-5.0-HDMI-N-RTXL NHD-5.0-800480TF-ATXL# PremiumMVA500 cd/m² 75° all angles No TouchNHD-5.0-HDMI-N-RTXL-CTU NHD-5.0-800480TF-ATXL#-CTP PremiumMVA415 cd/m² 75° all anglesProjectedCapacitive(USB-HID)NHD-5.0-HDMI-N-RTXL-RTU NHD-5.0-800480TF-ATXL#-T PremiumMVA400 cd/m² 75° all angles4-WireResistive(USB-HID)For detailed information on the TFT Panel used, please view its Product Specification by accessing the product webpage link above. Electrical CharacteristicsItem Symbol Condition Min. Typical Max. Unit Operating Temperature Range T OP Absolute Max -20 - +70 ⁰C Storage Temperature Range T ST Absolute Max -30 - +80 ⁰C Backlight PWM Frequency f PWM - 5 - 100 kHz Module Supply Voltage V DD- 5.0 - 9.0 VModule Supply CurrentI DD V DD = 5V - 560 590 mA V DD = 9V - 420 450 mAHDMI Receiver InformationOn-board Texas Instruments TFP401A Receiver.To view the full TFP401A specification, please download it by accessing the link below: /lit/ds/slds190a/slds190a.pdfInterface Description(Capacitive Touch model shown above as reference)Num. Description1) (LED4)LED Indicator for Touch–Capacitive Touch models onlyThis is a Red LED that will illuminate when there is a touch sensed on the CTP.2) (LED2)LED Indicator for Touch–Resistive Touch models onlyThis is a Red LED that will blink slowly (once per second) if the RTP controller is powered ON, awake, and no touch isdetected. This LED will blink rapidly (5 times per second) if the RTP controller detects a touch.3) (CN4)Surface Mount Pin Header, 2.54mm pitch, for Backlight PWMThe pin labelled ‘PWM’ is connected directly to the LED driver’s CTRL pin (T.I. TPS61165). This is a multifunctional pin whi ch can be used for enable control, PWM, and digital dimming. A PWM frequency in the range of 5kHz – 100kHz must be used.4) (CN3)DC Jack (Center-Positive)This is used to supply power to the display module. A DC power supply in the range of 5V – 9V must be used.The output current rating of the DC power supply should be at least the maximum Supply Current (I DD) listed in the Electrical Characteristics section on the previous page.5) (LED3)LED Indicator for PowerThis is a Green LED that will illuminate when DC power is supplied to the module.6) (CN2)Micro-USB (Type-B) Connector for Touch–Touch Panel models onlyThis is to connect the Touch Panel of this module to a USB input to act as a USB-HID device.7) (LED1)LED Indicator for VideoThis is a Blue LED that will illuminate when there is an active video signal detected.8) (CN1)HDMI (Type-A) ConnectorThis is a full-size HDMI connector meant to connect the HDMI source signal (Video only) to this module.The on-board T.I. TFP401A HDMI/DVI Receiver does not scale video resolutions. Therefore, the output resolution of thesource must be 800x480 (WVGA). In most applications, this is automatically detected by the HDMI source.Connecting with Windows/Windows EmbeddedConnecting our HDMI TFT Modules to a Windows system is fully plug-and-play. Start by plugging in a DC power supply in the range of 5 - 9V, with at least 1A of output current. The green LED near the DC jack will illuminate when the board has power supplied to it. Next, connect the display to your system via HDMI cable. Due to the on-board EDID, the display will be detected automatically and the system’soutput resolution will set itself to 800x480.For Touch Panel models, once the display is connected to the system via USB, Windows willautomatically detect and install the necessary drivers.The above window is shown for the Capacitive Touch model. The Resistive Touch model will also install automatically, however it will be labelled ‘AR1100 HID-MOUSE’ instead of ‘Newhaven Display’.Once Windows has finished installing the drivers, the device will show as ‘Ready to use’.For reference, in Device Manager the USB-HID Touch device will show as below:Connecting with LinuxMost Linux applications with an HDMI source will also be fully plug-and-play, however when using our HDMI TFT Modules with the Raspberry Pi, the config.txt file on the Pi’s microSD card will need to beslightly modified by the user.The following highlighted lines need to be added in config.txt for proper display output:# For more options and information see# http://rpf.io/configtxt# Some settings may impact device functionality. See link above for details# uncomment if you get no picture on HDMI for a default "safe" mode#hdmi_safe=1# uncomment this if your display has a black border of unused pixels visible# and your display can output without overscan#disable_overscan=1# uncomment the following to adjust overscan. Use positive numbers if console# goes off screen, and negative if there is too much border#overscan_left=16#overscan_right=16#overscan_top=16#overscan_bottom=16# uncomment to force a console size. By default it will be display's size minus# overscan.#framebuffer_width=1280#framebuffer_height=720# uncomment if hdmi display is not detected and composite is being output#hdmi_force_hotplug=1# uncomment to force a specific HDMI mode (this will force VGA)#hdmi_group=1#hdmi_mode=1hdmi_group=2hdmi_mode=87hdmi_cvt=800 480 60 6 0 0 0# uncomment to force a HDMI mode rather than DVI. This can make audio work in# DMT (computer monitor) modes#hdmi_drive=2# uncomment to increase signal to HDMI, if you have interference, blanking, or# no display#config_hdmi_boost=4# uncomment for composite PAL#sdtv_mode=2#uncomment to overclock the arm. 700 MHz is the default.#arm_freq=800# Uncomment some or all of these to enable the optional hardware interfaces#dtparam=i2c_arm=on#dtparam=i2s=on#dtparam=spi=on# Uncomment this to enable the lirc-rpi module#dtoverlay=lirc-rpi# Additional overlays and parameters are documented /boot/overlays/README# Enable audio (loads snd_bcm2835)dtparam=audio=onTechnical Resources2D DrawingsEDID TimingNHD-5.0-HDMI-N-RTXL Array NHD-5.0-HDMI-N-RTXL-CTUNHD-5.0-HDMI-N-RTXL-RTU3D ModelsNHD-5.0-HDMI-N-xxxxNHD-5.0-HDMI-N-xxxx-CTUNHD-5.0-HDMI-N-xxxx-RTUSchematicNHD-5.0-HDMI-NEDID Arrayconst unsigned char NHD_HDMI5[] = {0x00, 0xFF, 0xFF, 0xFF, 0xFF, 0xFF, 0xFF, 0x00, 0x39, 0x04, 0x3B, 0x07, 0x00, 0x00, 0x00, 0x00,0x01, 0x11, 0x01, 0x03, 0x80, 0x0B, 0x07, 0x00, 0x0A, 0x00, 0x00, 0x00, 0x00, 0x00, 0x00, 0x00, 0x00, 0x00, 0x00, 0x00, 0x00, 0x00, 0x01, 0x01, 0x01, 0x01, 0x01, 0x01, 0x01, 0x01, 0x01, 0x01, 0x01, 0x01, 0x01, 0x01, 0x01, 0x01, 0x80, 0x0C, 0x20, 0x80, 0x30, 0xE0, 0x2D, 0x10, 0x28, 0x30, 0xD3, 0x00, 0x6C, 0x41, 0x00, 0x00, 0x00, 0x18, 0x00, 0x00, 0x00, 0xFC, 0x00, 0x4E, 0x48, 0x44, 0x2D, 0x35, 0x2E, 0x30, 0x20, 0x48, 0x44, 0x4D, 0x49, 0x0A, 0x00, 0x00, 0x00, 0x10, 0x00, 0x00, 0x00, 0x00, 0x00, 0x00, 0x00, 0x00, 0x00, 0x00, 0x00, 0x00, 0x00, 0x00, 0x00, 0x00, 0x00, 0x10, 0x00, 0x00, 0x00, 0x00, 0x00, 0x00, 0x00, 0x00, 0x00, 0x00, 0x00, 0x00, 0x00, 0x00, 0x00, 0x5A, 0x00, 0x00, 0x00, 0x00, 0x00, 0x00, 0x00, 0x00, 0x00, 0x00, 0x00, 0x00, 0x00, 0x00, 0x00, 0x00, 0x00, 0x00, 0x00, 0x00, 0x00, 0x00, 0x00, 0x00, 0x00, 0x00, 0x00, 0x00, 0x00, 0x00, 0x00, 0x00, 0x00, 0x00, 0x00, 0x00, 0x00, 0x00, 0x00, 0x00, 0x00, 0x00, 0x00, 0x00, 0x00, 0x00, 0x00, 0x00, 0x00, 0x00, 0x00, 0x00, 0x00, 0x00, 0x00, 0x00, 0x00, 0x00, 0x00, 0x00, 0x00, 0x00, 0x00, 0x00, 0x00, 0x00, 0x00, 0x00, 0x00, 0x00, 0x00, 0x00, 0x00, 0x00, 0x00, 0x00, 0x00, 0x00, 0x00, 0x00, 0x00, 0x00, 0x00, 0x00, 0x00, 0x00, 0x00, 0x00, 0x00, 0x00, 0x00, 0x00, 0x00, 0x00, 0x00, 0x00, 0x00, 0x00, 0x00, 0x00, 0x00, 0x00, 0x00, 0x00, 0x00, 0x00, 0x00, 0x00, 0x00, 0x00, 0x00, 0x00, 0x00, 0x00, 0x00, 0x00, 0x00, 0x00, 0x00, 0x00, 0x00, 0x00, 0x00, 0x00, 0x00, 0x00, 0x00, 0x00 };Quality InformationTest Item Content of Test Test Condition Note High Temperature storage Endurance test applying the high storage temperaturefor a long time.+80⁰C, 96hrs 2Low Temperature storage Endurance test applying the low storage temperaturefor a long time.-30⁰C, 96hrs 1,2High Temperature Operation Endurance test applying the electric stress (voltage ¤t) and the high thermal stress for a long time.+70⁰C, 96hrs 2Low Temperature Operation Endurance test applying the electric stress (voltage ¤t) and the low thermal stress for a long time.-20⁰C, 96hrs 1,2High Temperature / Humidity Operation Endurance test applying the electric stress (voltage ¤t) and the high thermal with high humidity stressfor a long time.+60⁰C, 90% RH, 96hrs 1,2Thermal Shock resistance Endurance test applying the electric stress (voltage ¤t) during a cycle of low and high thermal stress. -20⁰C, 30min -> 25⁰C, 5min -> 70⁰C, 30min = 1 cycle10 cyclesVibration test Endurance test applying vibration to simulatetransportation and use. 10-55Hz, 15mm amplitude.60 sec in each of 3 directionsX,Y,ZFor 15 minutes3Static electricity test Endurance test applying electric static discharge. VS=800V, RS=1.5kΩ, CS=100pFOne timeNote 1: No condensation to be observed.Note 2: Conducted after 4 hours of storage at 25⁰C, 0%RH.Note 3:Test performed on product itself, not inside a container.Precautions for Using LCDs/LCMsSee Precautions at /specs/precautions.pdfWarranty InformationSee Terms & Conditions at /index.php?main_page=termsDocument Revision HistoryRevision Date Comments1.0 1/4/2017 Initial Release[read caution below]SCHEMATIC/PART NUMBER:REVISION:SCHEMATIC/PART NUMBER:REVISION:SCHEMATIC/PART NUMBER:REVISION:。
迈特三维旋转连续变倍视频显微系统使用说明书

MZDR0850三维旋转连续变倍视频显微系统使用说明书桂林市迈特光学仪器有限公司使用前请注意:1. 操作:(1) 本仪器是一种精密仪器,在操作或运输过程中要轻拿轻放,避免碰撞。
(2) 避免阳光直接暴晒、高温、灰尘和震动。
(3) 镜片表面不应留有污物和手指印,以免降低本仪器成像清晰度。
2. 清洁和保管(1) 清洁光学零件表面应用脱脂纱布或棉花轻轻擦拭,如有手指印和油污,应用70%乙醚和30%酒精混合液沾湿脱脂纱布或棉花后轻轻擦拭。
!由于酒精和乙醚是高度易燃的溶剂,必须小心使用,一定要离开明火和可能产生电弧的地方,如电子设备的开和关。
同时也要记住应在有良好通风的房间使用这些化学试剂。
(2) 不要用有机溶剂擦拭其它元件表面,可用中性的清洁剂擦拭。
(3) 不要试图拆卸本仪器,以免降低精度。
(4) 在不使用仪器时请用防尘罩将仪器盖好,存放在干燥、无灰尘的地方。
3. 供电网络应有良好的接地。
目录:1. 简介 (1)2. 仪器清单 (1)3. 技术参数 (1)4. 各部件名称 (3)5. 仪器的安装 (3)6. 操作 (4)7. 故障维修指南 (5)1.简介MZDR0850三维旋转连续变倍视频显微系统,采用先进的光学技术和精密机械电子技术,使人们观察微观世界的角度从单一的正面观察扩展到三维全方位多角度观察,极大地提高了观察样品的细节程度。
无需倾斜就能360°全方位、大景深观察样品各个侧面的实时高分辨率动态图像,具有强烈的立体感和层次感,并且可以改变镜头的旋转速度,观察到传统镜头无法显示的位置,例如PCB贴片元器件下方、金属孔内部、侧壁等。
广泛应用于SMT、PCB、BGA等表面贴装工业。
为适合观察不同的物体,底端光轴与水平方向夹角有45°(标准型)、30°、60°、15°四种规格,此夹角越大,景深越大。
2.仪器清单本仪器标准配置包括下列部件:序号部件名称数量备注1 主机 12 底座 13 载物台 14 控制电源箱 15 输入电源线 16 内六角扳手 1 安装调整用7 CCD摄像头、视频线、CCD电源 1 选购件3. 技术参数总放大倍率=光学放大倍率×数字放大倍率数字放大倍率=显示器的显示屏对角线尺寸/CCD摄像头靶面对角线尺寸CCD摄像头靶面对角线尺寸:1/3” CCD:6mm;1/2”CCD:8mm;2/3” CCD:11mm.例如:14”监视器配1/3”CCD摄像头的数字放大倍率=64.2514×=59.2717”监视器配1/3”CCD摄像头的数字放大倍率=64.2517×=71.97 (1). 光学性能参数:CCD接头光学放大倍率总放大倍率视场范围(mm) 工作距离(mm)观察角度(与水平方向)0.3X 0.169X~1.125X 9.9X~66.6X 21.3X28.4~3.2X4.270.5X(标准配置)0.28X~1.875X 16.65X~111X 12.9X17.1~1.92X2.561X 0.56X~3.75X 33.3X~222X 6.4X8.6~0.96X1.281.5X 0.84X~5.625X 49.95X~333X 4.3X5.7~0.64X0.8520 45°注:总放大倍率、视场范围是以1/3”CCD摄像头、14”监视器计算CCD接头光学放大倍率总放大倍率视场范围(mm) 工作距离(mm)观察角度(与水平方向)0.3X 0.169X~1.125X 9.9X~66.6X 21.3X28.4~3.2X4.270.5X(标准配置)0.28X~1.875X 16.65X~111X 12.9X17.1~1.92X2.561X 0.56X~3.75X 33.3X~222X 6.4X8.6~0.96X1.281.5X 0.84X~5.625X 49.95X~333X 4.3X5.7~0.64X0.8511 30°注:总放大倍率、视场范围是以1/3”CCD摄像头、14”监视器计算(2). 输入电压:AC90~264V ,50Hz/60Hz(3). 保险管规格:2A(4). 载物台移动范围:X 方向100mmY 方向86mmCCD 接头 光学放大倍率 总放大倍率 视场范围(mm)工作距离(mm)观察角度(与水平方向) 0.5X(标准配置)0.1875X ~1.25X 11.1X ~74X 19.2X25.6~2.88X3.841X 0.375X ~2.5X 22.2X ~148.2X 9.6X12.8~1.44X1.92 1.5X 0.5625X ~3.75X 33.3X ~222.3X 6.4X8.5~0.96X1.28 6560°注:总放大倍率、视场范围是以1/3” CCD 摄像头、14” 监视器计算CCD 接头光学放大倍率总放大倍率视场范围(mm)工作距离(mm)观察角度(与水平方向) 0.5X(标准配置)0.1875X ~1.25X 11.1X ~74X 19.2X25.6~2.88X3.841X 0.375X ~2.5X 22.2X ~148.2X 9.6X12.8~1.44X1.92 1.5X 0.5625X ~3.75X 33.3X ~222.3X 6.4X8.5~0.96X1.28 815°注:总放大倍率、视场范围是以1/3” CCD 摄像头、14” 监视器计算4. 各部件名称5. 仪器的安装仪器的安装请看图1、图2a. 物镜主体与支架连接(图2)将托圈12从物镜主体9上旋下后,让主机自下往上从支架7中穿过,再将托圈12旋紧并拧紧止紧螺钉6。
MTL SD Series 过压保护设备说明书
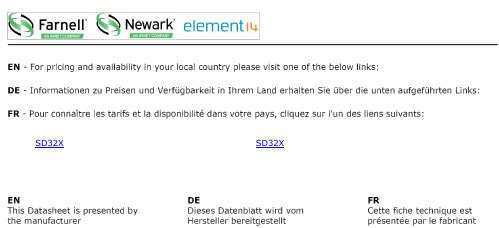
Eaton Electric Limited,Great Marlings, Butterfield, LutonBeds, LU2 8DL, UK.Tel: + 44 (0)1582 723633 Fax: + 44 (0)1582 422283E-mail:********************© 2017 Eaton All Rights Reserved Publication No. EPS 901-107 Rev U January 20171The SD range is a series of surge protection devices combine unparalleled packing densities, application versatility, proven reliable hybrid circuitry, simple installation and optional ‘loop disconnect’ facilities – features which make the range the ultimate surge protection solution for process equipment, I/O systems and communications networks.The exceptionally high packing densities are the consequence of an ultra slim ‘footprint’ for individual modules which can thus ‘double-up’ as feedback terminals. Each module provides full hybrid surge protection for 2 and 3 wire loop protection.Modules with a comprehensive range of voltage ratings cover all process related signals such as RTDs, THCs, 4 to 20mA loops, telemetry outstations, shut-down systems and fire and gas detectors.Optional ‘loop disconnect’, is a feature which allowscommissioning and maintenance to be carried out without removal of the surge protection device. This facility is provided by the SD07, SD16, SD32 and SD55 units. In addition, a third connection on the field and safe side of the protector is provided in order to terminate screens safely.protecting electronic equipment and systems against surges on signal and I/O cabling.For three wire applications the specially designed SDRTD (Resistance Temperature Detector) and the SD32T3, (for separately powered 4-20mA loops) provide full 3-wire protection in a single compact unit. The recommended choice for the protection of 3-wire pressure transducers on low power circuits is the SD07R3.For higher bandwidth applications , the SDR range has been developed to meet the demands of today’s highest speed communication systems.120V and 240V AC versions are available for I/O and power supplies up to three Amps of load current and telephone networks can be protected by the SDPSTN.One simple manual operation clamps modules securely onto DIN rail, which automatically provides the essential high-integrity earth connection.‘T op-hat’ (T -section) DIN rail is generally suitable for mounting SD modules although for adverse environments, a specially-plated version is available. A comprehensive range of mounting and earthing accessories can also be supplied, see page 7 for further details.• Range of ATEX Certified intrinsicallysafe surge protectors• Ultra-slim space-saving design;easy installation• Multistage hybrid protection circuitry – 20kAmaximum surge current• Range of voltage ratings – to suit allprocess I/O applications• High bandwidth, low resistance, RTD, PSTNand 3-wire transmitter versions available• 10 year product warranty2from protected circuitry without needing additional disconnect terminals. The standard fuse (which is replaceable) is rated 250mA with 50mA fuses also being available by special request. Where only the disconnect feature is required, solid links can be used.As an example, this feature is of particular value in applications in which an SPD is used with a bulk power supply feeding disconnect terminals. The following guide to selection suggests the most suitable SDs for a number of specific applications. For technical information, see the detailed specifications on the back page of this publication (some field circuit protection is shown for completeness).FIELD CIRCUIT PROTECTED CIRCUIT 2-wire transmitters 3-wire RTDs Photocells, THCs,mV sources andturbine flowmetersAnalogue inputs (high-level)2-wire transmitters, 4-20mA, conventionaland smartThe SPDs recommended for use with ‘conventional’ and ‘smart’ 4-20mA transmitters (fed by a well-regulated supply) are the SD32 and SD55, the choice depending upon the maximum working voltage of the system (32V and 55V respectively). The diagram illustrates a prime example of an application for which the fuse/disconnect facility is particularly useful, however, both models are available in ‘X’ versions without the optional fuse/disconnect feature.Analogue inputs (low-level)RTDsThese applications are best served using the SDRTD. For optimum accuracy, the energising current should be chosen to ensure the voltage across the RTD does not exceed 1V over the full measurement range. When using a PT100 device, we recommend an energising current of 1mA.Photocells, THCs, mV sources and turbineflowmetersThe SD07 or SD16 (depending upon the operational voltage) are the favoured choices for this application. SD07X and SD16X are also suitable. 3Controller outputs (I/P converters)Switches Alarms, LEDs, solenoid values, etc.T elecom line PLC, I/O systemsController outputs (I/P converters)For this application, the recommendations are the SD16, SD32 and SD55 (and the equivalent ‘X’ versions), the final choice depending upon the operating voltage.Digital (on/off) inputsSwitchesSuitable SPDs for switches include the SD07, SD16, SD32 and SD55 modules – the choice depending upon the operating voltage of the system. T he ‘X’ versions of these are also suitable.Digital (on/off) outputsAlarms, LEDs,solenoid valves, etcAlarms, LEDs, solenoid valves, etcThe recommended choice for this application is the SD32 or SD32X.T elemetry (PSTN)Telemetry outstationsThe SDPSTN has been designed specifically for the protection of signals transmitted on public switched telephone networks.AC supplied equipmentPLC, I/O systemsFor systems on 110-120V ac, the SD150X is the recommended choice and for 220-240V ac systems, the SD275X is recommended.cable entries. Where these entries are not available or 3-wire devices are used, the compact design and simple installation of the SD range makes it the obvious choice for transmitter protection.The SDs within the junction box should be installed no further than one metre away but as close as possible to the sensor or made by fixing the metallic transmitter housing to the plant structure. This bond ensures the voltage difference between the signal conductors and the transmitter housing is below the transmitter’s insulation rating. Please note that the transmitters or sensors are connected to the ‘Protected Equipment’ terminals of the SD and not the ‘Field Cables’.2-wire transmitter or sensor 3-wire transmitter or sensor 4-wire transmitter or sensor TO HOST CIRCUITSD PROTECTED FIELD CIRCUIT 2-wire transmitters or sensors4-20mA transmitters, conventional and smartWhere the TP48 is not an acceptable solution,either because of technical suitability ordifficulties in mounting, the SD16X, SD32Xand SD55X are an excellent alternative.3-wire transmitters or sensorsVibration Sensors and 4-20mA loop processcontrol systems invariably require threewire connections, when powered from anexternal source.This may be accomplished in one unit byusing the SD32T3 three terminal SurgeProtection Device (SPD).Because the SD32T3 protects all threeconductors within the same unit, higherprotection is achieved, as the SPD hybridcircuitry is common to all three wires.The SD07R3 is available for the protection of3-wire pressure transducers on low powercircuits.4-wire transmitters or sensorsFlow meters, level detectors, etc.4-wire systems such as level detectors requiretwo SDs, one for the supply and the otherfor the transmitter output. Generally thevoltages across the pairs are similar and sothe recommended choice would be a pair ofSD16X, SD32X or SD55Xs. However, mainspowered transmitters should be protectedwith an SD150X or 275X (depending uponsupply voltage) for the supply inputs.Loadcells are catered for by MTL SurgeTechnologies’ LC30 which is suitable for both4- and 6-wire load cells.4 5TP PROTECTED FIELD CIRCUIT SD PROTECTED HOST CIRCUIT RS232, RS422, RS485SD PROTECTED HOST CIRCUIT PROTECTED FIELD CIRCUIT Bus powered systems Communication systems RS232, RS422, RS485The recommended choice for these applications is the SD16R or SD32R depending on the maximum driver signal.Bus powered systems There are a variety of bus powered systems specially designed for the process industry. The ideal surge protection device for these systems is the SD32R as it has a very high bandwidth and a modest in-line resistance.T ypical Applications Table 1 shows suitable SD devices for different applications. In some applications alternative devices may be used, for example, where lower in-line resistance or a higher voltage power supply is used.MTL Surge Technologies has operationally tested the recommended SD range with representative highways listed but no formal approval for their use in systems by therespective bodies has been sought.T able 1 6P i = 1.2W (–30°C to +60°C)P i = 1.3W (–30°C to +40°C)The SD** range is classified as simple apparatus and are intended for use in Zone 2 or safe areas only, because their fuses are not fully encapsulated.Installation Positioning The SDs should be mounted on the field wiring side to ensure that any surges entering from the field do not damage any intrinsically safe barriers or galvanic isolators in the system. The SDs and IS interfaces should be mounted close to each other but on separate DIN rails in order to maintain the required 50mm clearance between safe area and hazardous area terminals.Earthing The recommended earthing for field mounted devices has been illustrated pre-viously but it is the earthing at the control panel that is more critical as there are usually a number of earthing systems, each with their own requirements. The earthing system illustrated here replaces the instrument 0V bond, the control system PSU bond and the IS earth with one single earth connection to meet all the design requirements and give the most effective protection against the effects oflightning induced surges.(1996-12) Electrical apparatus for explosive gas atmospheres Part 14: Electrical installations in hazardous areas (other than mines) stresses the importance of SPDs in hazardous areas. An outdoor installation, where there is a high likelihood of both lightning induced transients and combustible gases, requires the installation of SPDs to prevent possible ignition of the gases. Areas seen particularly at risk include flammable liquid storage tanks, effluent treatment plants, distillation columns in petrochemical works and gas pipelines.SPDs for transmitter protection should be installed in Zone 1 but sufficiently close to the Zone 0 boundary to prevent high voltages entering Zone 0. The distance from the SPD to Zone 0 should be less than one metre where possible. However, in practice the SPD would normally be mounted on the transmitter or sensor housing which usually lies in Zone 1 and is very close to Zone 0. Because there is only a very small free volume, the SD range is suitable for mounting in flameproof or explosion proof enclosures.Zone 2The SD range is suitable for protecting electrical circuits in Division 2, Zone 2 and can be used without affecting the safety aspects of the circuit. Non-incendive (low-current) circuits can be protected using any SD range unit mounted in either the safe or hazardous area including those with the fuse disconnect facility. Non arcing (high current) circuits can also be protected except that SPDs with the fuse disconnect facility may only be mounted in the safe area. For use in these circuits the units must be mounted in a suitable enclosure, normally the minimum requirements are IP54 and 7Nm resistance to impact. The SD range is self-certified by MTL Surge Technologies as being suitable for this purpose.Certification Introducing surge protection into Intrinsically Safe (IS) circuits is trouble free as long as the current and power parameters are not exceeded. In the SD range, the SD**X, SD**R, SD**R3, SDRTD and SD**T3 all have ATEX certification for use in IS circuits located in Zones 0, 1 or 2. The certification parameters for the SD**X and SD**T3 are:Ex ia IIC T4 Ga, Li = 0.22mH I i = 260mA for Ui up to 20V I i = 175mA for Ui up to 26V I i = 140mA for Ui up to 28V I i = 65mA for Ui up to 60VThe certification parameters for the SD**R, SD**R3 and SDRTD are:Ex ia IIC T4 Ga, Li = 0I i = 260mA for Ui up to 60V7practice. These are placed at regular intervals along the rail or at each end as required. Earth connections can be made to the DIN rail via the earth terminal (ETL7000). Weatherproof enclosures are also available with all the necessary mounting accessories to install the SD range of surge protection devices.on the tops of individual SPDs. Both methods can be used conjointly. Replaceable fuses or solid links are available in packsof 5 (SD-F25, SD-F05 and SD-LNK).DIMENSIONSMounting accessories ISP7000 Insulating spacer THR2 Standard DIN rail, 35mm x 7.5mm THR7000 T -section DIN rail, specially nickel plated, 35mm x 7.5mm, 1m lengthEarthing/earth rail accessories ETL7000 Earth terminal, DIN rail mounted IMB57 Insulated mounting block (two needed)ERB57S Earth rail bracket, straight ERB57O Earth rail bracket, offset ERL7 Earth rail, 1m length ETM7 Earth terminal, pack of 50T agging accessories TAG57 Tagging strip, 1m length TGL57 Tagging strip labels, set of 10 x 0.5m BRI7000 Barrier identifier BIL7000 Barrier identification labels, sheet of 120BIL7000L Barrier identification labels, A4 sheet of 126Enclosures DX070 Enclosure for up to 9 x SD range SPDs DX170 Enclosure for up to 22 x SD range SPDs DX430 Enclosure for up to 58 x SD range SPDs Accessories (replacement)SD-F25 Replaceable fuse pack - 250mA standard (available in packs of 5)RLA7050 Replaceable fuse pack - 50mA special (available in packs of 5)RLA7000 Solid Link (available in packs of 5)SIL informationThe user of the SD range can utilize these failure rates in a probabilistic model of a safety instrumented function (SIF) to determine the suitability in part for safety instrumented system (SIS) usage in a particular safety integrity level. A full table of failure rates in presented in the EXIDA report (section 4.4) along with all assumptions.*The Residual Effect failures are included in the Safe Undetected failure category according to IEC 61508. Note that these failures alone will not affect system reliability or safety and should therefore not be included in spurious trip calculations.Safe Failure Fraction needs to be calculated on (sub)system level.A complete copy of the EXIDA report can be downloaded at .EUROPE (EMEA): +44 (0)1582 723633 ********************THE AMERICAS: +1 800 835 7075 *********************ASIA-PACIFIC: +65 6 645 9888***********************The given data is only intended as a product description and should not be regarded as a legal warranty of properties or guarantee. In the interest of further technical developments, we reserve the right to make design changes.Eaton Electric Limited,Great Marlings, Butterfield, LutonBeds, LU2 8DL, UK.Tel: + 44 (0)1582 723633 Fax: + 44 (0)1582 422283E-mail:********************© 2017 Eaton All Rights Reserved Publication No. EPS 901-107 Rev U 230117January 20178Note : all figures are typical at +25°C unless otherwise stated; *standard fuse; +over full working temperature range; †at 20mA with a 250mA standard fuse; ‡these units need external 3A fuses; ^Signal; **Power & Common; <maximum energizing current depends upon RTD resistance. See page 2 for details.Max discharge surge current (I max ) (8/20µs)20kA (8/20µs)6.5kA (SD150X and SD275X only)Nominal discharge surge current (i sn )3kA (8/20µs)Lightning impulse current (I imp ) (10/350µs)2.8kA 1.0kA (SD150X and SD275X only)Response time <1ns RTD resistance range (SDRTD)10 to 1500 Degradation accuracy (SDRTD at 1mA)0.1% (RTD resistance > 100 )0.1W (RTD resistance < 100 )Ambient temperature –40°C to +80°C / -40°F to 176°F storage –40°C to +80°C / -40°F to 176°F working For IS working applications:P i = 1.0W (–30°C to +75°C / -22°F to 167°F)P i = 1.2W (–30°C to +60°C / -22°F to 140°F)P i = 1.3W (–30°C to +40°C / -22°F to 104°F)Humidity 5 to 95% RH (non-condensing)Category tested A2, B2, C1, C2, C3Overstressed fault mode in=3kA 12kA 9kA (SD150X and SD275X only)Impulse durability (8/20µs)10kA 6.5kA (SD150X and SD275X only)Terminals 2.5mm 2 (12 AWG)Mounting T-section DIN-rail 35 x 7.5 or 35 x 15mm rail (1.38” x 0.3” x 0.6”)Weight 70g approximately (2.5oz)Case flammability UL94 V-2AC durability 1A rms , 5T Service conditions 80kPa - 160kPa 5% - 95% RHEMC compliance To Generic Immunity Standards, EN 61326-1, part 2 for industrial environmentsR&TTE compliance EN 61326-1, EN 41003 : 1999EN 60950 - 1 : 2006(not applicable to SD150X and SD275X)LVD compliance SD150X & SD275X EN 60950 - 1 : 2006, EN 61010 : 2010SDPST EN 41003 : 1999IEC compliance EN 61643-21:2001ANSI/IEEE testing C62.41-1-2002C62.41-2-2002C62.45-2002T o order - Order by module, as listed in the specification table and/or accessory part numbers, as defined on page 7.Products highlighted in blue are ATEX certified Ex ia IIC T 4 Ga.Approvals Authority (Country)Standard Certificate/File No.Approved for Product Baseefa [ATEX](EU)EN 60079-0:2009EN 60079-11:2007Baseefa02ATEX0211X Ex ia IIC T 4 Ga Ta = -30°C to See Schedule SD07X, SD16X, SD32X, SD55X,SD07R, SD16R, SD32R, SD55R,SDRTD, SD32T3, SD07R3, SD16R3, SD32R3, SD55R3Eaton (EU)EN 60079-15:2005EN 60079-14:2003MTL03ATEX0755X Ex nA IIC T 4SD07, SD16, SD32, SD55, SD07X, SD16X, SD32X, SD55X, SD07R, SD16R, SD32R, SD55R, SD32T3, SD07R3, SD16R3, SD32R3, SD55R3, SDRTD Baseefa [IECEx](International)IEC 60079-0: 2007-10IEC 60079-11: 2006IECEx BAS 12.0003X Ex ia IIC T 4 Ga SD07X, SD16X, SD32X, SD55X, SD07R, SD16R, SD32R, SD55R, SDRTD, SD32T3, SD07R3, SD16R3, SD32R3, SD55R3CSA/C/US (Canada, USA)CSA C22.2 No. 0-M1991CSA C22.2 No. 157-M1992UL 913, 5th edition CSA C22.2 No. 142-M1987CSA C22.2 No. 213-M1987LR 36637EEx ia Class 1,Groups A, B C and D, T 4Class 1, Div 2Groups A,B,C, D T 4SD07, SD16, SD32, SD55, SD07X, SD16X, SD32X, SD55X, SD07R, SD16R, SD32R, SD55R, SDRTD, SD32T3, SD07R3, SD16R3, SD32R3, SD55R3 UL (USA)UL 497B Listed E220693Isolated loop communication circuits SD07, SD16, SD32, SD55, SD07X,SD16X, SD32X, SD55X, SD07R,SD16R, SD32R, SD55R, SD07R3, SD16R3, SD32R3, SD55R3, SD32T3, SD55T3, SD07X3, SD16X3, SD32X3, SD55X3, SDRTDAustel (Australia)AS/NZ3548:1995AS/NZS4117:1996TS001: 1997__Private WireSD07R。
Maritime RobotX Challenge WAM-V USVx 使用与保养手册说明书

Owner’s Operation and Service ManualMaritime RobotX Challenge WAM-V® USVxRead & Completely Understand this OWNER’S OPERATION AND SERVICE MANUAL Prior to Operating.Table of ContentsSafety Precautions (3)Included With Your Vessel (4)Design Specifications and Construction (5)Major Dimensions and Payload Requirements: (5)Sub Assembly Specifications and Construction (6)Assembly Procedure: (8)Hull Inflation (8)Assembly Steps (10)Disassembly (17)Hinge System and Propulsion Interface (18)Suspension System and Payloads (23)Setting Your Spring Pressure (23)Setting Your Damping Rate (25)Pre-Launch Checklist: (26)Vessel Launching (27)Trailer Launching (27)Side Davit/Hoist Launching (27)Towing: (29)Periodic Maintenance: (30)Inflatable Hull Care, Maintenance & Repair (32)Packing For Shipment (33)Vendors: Component Specifications and Manuals (40)Cane Creek: (40)SKS: (40)Gommorizzo: (40)Safety PrecautionsThis vessel is designed for a maximum payload capacity of 300 lbs (136 kg).DO NOT EXCEED.The inflatable hulls should be inflated to a pressure of 2.0 – 2.2 psi (140 – 150 millibar). Maximum pressure rating is 3.0 psi (205 millibar), DO NOTEXCEED.After operation, deflate both hulls to 1.0 psi (70 millibar) to avoid over pressurization and internal baffle rupture due to temperature changes.CRITICAL: Inspect all push button quick release pins to ensure that the spring loaded retaining ball is functioning properly. Replace immediately if there is any sign of damage or if the internal spring mechanism is notfunctioning properly. Failure to do so may result in catastrophic damage or loss of the vessel.Hoisting: Always lift RobotX WAM-V USVx by securely attaching to all 4 payload tray lift points using hardware and slings that are appropriatelyrated for the load being lifted. See “Side Davit/Hoist Launching” section of this manual for the location of the hoist points on the payload tray. Do not walk beneath the vessel during lifting. Improper use of hoisting hardware, slings, or lift points may result in injury or death.The payload tray has attachment points for securing payloads. Please make sure payloads are always secured prior to operation.Included With Your VesselThe following spare parts and tools are included with your RobotX WAM-V USVx.2 x ¼” diameter, 1.5” long stainless steel quick release locking pin1 x ¼” diameter, 4.0” long stainless steel quick release locking pin1 x ¼” diameter, 1.75” long stainless steel quick release locking pin, with lanyard attached1 x 3/8” diameter, 3.0” long stainless steel quick release locking pin8 x retaining rings for ½” shaft size8 x ¼”-20 set screws w/ nylon patch4 x 8-32 set screws w/ nylon patch1 x wrench set: 3/8” – 1”1 x allen key set w/ vinyl pouch: 11 piece, 0.05” – 3/8”1 x double open ended wrench, 7/16” – 9/16”1 x double open ended wrence, 7/16” – ½”1 x T27 torx drive bit4 x 2500 lb load rated lifting sling, 3’ length6 x 1 ton lifting shackle, 3/8” screw pin1 x 3300 lb load rated high depth shackle1 x West Marine hand operated inflator pump1 x SKS SAM suspension pump2 x replacement fill valves for hypalon hulls1 x Cane Creek DBair shock absorber w/ adjustment tool [shipped separately]2 x Cane Creek DBair shock absorber valve cap w/o-ring [shipped separately]2 x IGUS KSTM-30 pillowblock bearing [shipped separately]1 x IGUS KSTM-GT35 pillowblock bearing [shipped separately]Design Specifications and Construction Major Dimensions and Payload Requirements: Beam: 96” (244 cm) [outside to outside]Overall Hull Length: 154” (391 cm)Ski Length: 112” (284 cm)Hull Diameter: 16.75” (42.6 cm)Payload: 300 lbs. (136 kg) maximumFull Load Displacement: 560 lbs. (255 kg) (estimated)Draft: 6.5” (16.5 cm) (estimated)Primary drawing dimensions in inchesPrimary drawing dimensions in inchesSub Assembly Specifications and Construction1.Payload TrayMaterial and Construction: Riveted tube frame and stress skin construction using 5086 and 6061-T6 series aluminum components anodized to MIL-A-8625 Type III. Rear Arch and Front Arch Assembly bearing surfaces are Delrin and reinforced nylon respectively.Weight: 54.5 lbs (24.7 kg).Primary drawing dimensions in inches2.Rear ArchMaterial and Construction: CNC bent tube construction using 6061-T6 series extruded and machined aluminum components anodized to MIL-A-8625 Type III. Inserts and reinforcements riveted in place.Weight: 33.5 lbs (15.2 kg).3.Front ArchMaterial and Construction: CNC bent tube construction using 6061-T6 series extruded and machined aluminum components anodized to MIL-A-8625 Type III. Inserts and reinforcements riveted in place.Weight: 11 lbs (5.0 kg).4.SuspensionMaterial and Construction: Structurally riveted construction consisting of water-jet cut 6061-T6 aluminum plate and extruded sections. CNC machined mounting brackets for all suspension component attachments. All components anodized to MIL-A-8625 Type III. Shock absorbers provided by Cane Creek feature integrated air spring and damper combination with all stainless steel and anodized aluminum construction. Custom valving optimized for WAM-V suspension dynamics featuring external adjustability of spring and damping rates via Schrader valve and barrel adjusters respectively.Weight: 16.5 lbs (7.5 kg). (each)5.SkiMaterial and Construction: Custom 6061-T6 series aluminum extrusion with water-jet cut and CNC machined mounting brackets and reinforcements. Ski-Can is constructed of rolled and welded 0.080” (2 mm) Aluminum 6061-T6 sheet. Can is attached to Ski extrusion via water-jet cut and bent 5086 Aluminum brackets and structural rivets. All components anodized to MIL-A-8625 Type III.Weight: 42.5 lbs (19.3). (each)6.HullMaterial and Construction: Hypalon/polyester (Orca 866 manufactured by Pellel & Flipo).Weight: 20 lbs (9 kg). (each)Assembly Procedure:Hull InflationThe RobotX WAM-V USVx is equipped with hypalon fabric hulls mounted to a rigid aluminum ski. Your RobotX WAM-V USVx was shipped with hull valves locked open. Hull valves must be unlocked before inflation. To unlock the valves, depress and rotate the green button clockwise until green button extends fully. The hulls must be inflated before assembly. Each hull contains a central baffle separating two independent inflation chambers. To inflate, remove the valve cover by rotating the cover counterclockwise.Insert the hand pump valve and rotate clockwise to lock and seal the pump to the hull valve.Inflate each chamber to 2.0 – 2.2 psi (140 – 150 millibar). Replace valve covers by inserting cover and rotating clockwise until locked. In the event of over inflation, depress the green valve release button until desired pressure is reached.To deflate fully, depress the green release button and rotate clockwise until release valve is locked in the open position. After deflation, rotate green release button counterclockwise to close valve.Assembly Steps1. Clear an 8’ x 14’ (2.4 m x 4.3 m) space on the ground (or trailer) and lay out both hulls roughly80” (2 m) apart (centerline to centerline).2.Remove both foot pins by retracting the ¼” (6.3 mm) locking pin and pulling the pin free fromthe foot clevis. Set foot pin aside.3. Set both rear arch foam wedges over the aft most handle on the top of each ski. Line eachwedge up with the inboard edge of each ski.4. Carefully insert the base of the rear arch into the each foot clevis until the pin hole is aligned.Insert foot pin through both ends of the clevis and lock by inserting the ¼” (6.3 mm) locking pin vertically into the locking side of the foot clevis.5.IMPORTANT: Lay the rear arches back until they are resting on the rear arch foam wedgesinstalled in step 3. Failure to do so will result in damage to the rear arch and/or foot assemblies.6. While holding the front arch in between the forward portion of the hulls, slide the front archclevis over the forward balljoint of the suspension assembly and insert 3/8” (9.5 mm) locking pin.7. Repeat this procedure (6) for the opposite hull, laying the front arch forward after both pins arein place.8.Lift the payload tray in between the two arches. Insert the front balljoint shaft into thepillowblock balljoint mounted in the center of the front arch. Place the balljoint shaft cap on the front of the shaft, and secure with the ¼” (6.3 mm) retaining pin attached to the payload tray by inserting the retaining pin vertically through both the shaft and shaft cap.9.Lift the aft end of the payload tray until it is roughly level with the ground. While holding thetray, rotate the rear arch into place. Secure each arch tube in the C-shaped arch mounts.10.Rotate the plastic clamp so that it makes contact with the inside walls of each arch tube. Insertthe ¼” (6.3 mm) locking pin into the pin guide hole at the aft-most arch mounts, locking the clamp in place.11.Remove and store the rear arch foam wedges.DisassemblyDisassembly of the RobotX WAM-V USVx is conducted in the reverse order from the Assembly procedure. For step by step directions, follow the procedure laid out in the “Assembly Procedure” portion of this manual in reverse.Hinge System and Propulsion InterfaceThe RobotX WAM-V USVx is equipped with a quick release hinge system at the transom of each hull. This system allows easy and secure attachment of various propulsion units, independent of propulsion unit design. Each hinge system is composed of a locking handle, accessible on the upper aft portion of the ski, which controls the extension of a pair of locking pins. These locking pins extend into a pair of hinge tongues, mounted on the hinge tongue plate (show below), which is bolted securely to the propulsion unit.Hinge Tongue Plate AssemblyHinge TonguesBolt this face topropulsion unitHinge Tongue Plate Assembly is locked in place by these pins. Pins extend outward into Hinge Tongues via clockwise rotation of control handle at the top of the hull (see pictures on page 22).Rear View of Assembled UnitRear IsometricView of Assembled UnitUnlocked position ofhandleLocked position ofhandle with retainingpin installedSuspension System and PayloadsThe RobotX WAM-V USVx is equipped with a highly adjustable suspension system. Both the spring rate and damping are adjustable through the Cane Creek DBAir shock absorbers equipped on each hull. The RobotX WAM-V USVx can accommodate payloads up to 300 lbs (136 kg). All payloads should be securely fastened to the payload tray via straps or other load rated fasteners.Setting Your Spring PressureNOTE:When removing the valve cap to your DBAir shock absorbers, ensure that the sealing o-ring stays in the cap body. Replace o-ring immediately if lost or damaged.Due to the variability of the payload and payload weight distribution, suspension air pressure must be adjusted to accommodate various payloads. Air pressure can be adjusted using the SKS SAM Schrader valve hand pump supplied with your vessel. IMPORTANT: This pump is outfitted with a zero loss Schrader valve. Please refer to the SKS SAM pump packaging for instructions on the proper use of this valve. Proper use of this valve is essential to charging your DBAir spring to the desired pressure.Zero loss SchradervalveAir pressureadjustment valvePlease refer to page 19 of the DBAir owner’s manual for instructions on how to pressurize the shock. The DBAir contains an internal negative air spring, so care must be taken to set the suspension pressure accurately. Additional service and adjustment information can be found in the DBAir manual included with your vessel or via the link included in the “Vendors: Component Specifications and Manuals” section of this manual.Port and Starboard suspension pressures must be matched such that there is no front view rotation of the front arch.Setting Your Damping RateThe Cane Creek DBAir shock absorbers allow simple external adjustability of compression and rebound settings for both high and low speed damping. The DBAir dampers on your vessel have been adjusted to the following initial setting: HSC – 2 turns +, LSC – 1 turn +, HSR – maximum +, LSR – maximum +Please refer to the Cane Creek DBAir Tuning Field Guide included with your vessel for information on how to adjust your damper settings. Adjustment tools can be found in the spare parts box included with your vessel.Compression Adjustment Side Rebound Adjustment SidePre-Launch Checklist:All locking pins are properly installed and retaining mechanism is functioning properly.Hulls are inflated to 2.0 – 2.2 psi (140 - 150 millibar).Payload is secured to payload tray.Hinge system is properly greased and in locked position with retaining pin installed correctly.Suspension system is properly charged and greased with Schrader valves and O-rings installed correctly.Suspension system pins are installed correctly with C-Clips in place.All fasteners are tightened fully with nuts in place.Vessel LaunchingTrailer Launching1.Before backing down launch ramp, ensure that all tie-down straps holding the vessel to thetrailer are removed and stowed.2.Reverse tow vehicle down the launch ramp until both hulls are sufficiently submerged to lift thevessel off the trailer deck.3.Push or pull the vessel off the trailer and secure to the dockside.Side Davit/Hoist LaunchingThe RobotX WAM-V USVx is equipped with four (4) hoist point connections on the corners of the payload tray. Additionally, a hoisting bar, lifting straps and shackles are included with your vessel.The hoisting bar is designed such that the center lifting shackle can be moved fore and aft to accommodate the change in vessel center of gravity due to various payloads and propulsion unit configurations. When lifting, be sure to secure all payloads as the boat may tilt depending on shackle location. A properly load rated lifting strap must be secured at each hoist point connection in such a way that the majority of the load through the hoist point is in the vertical direction. An example of proper lifting rigging is shown on the following page.Towing:The RobotX WAM-V USVx is equipped with tow point connections on the front inboard side of each ski (shown below).In order to tow the RobotX WAM-V USVx, a tow bridle must be connected to BOTH tow point connections. Do not attempt to lift the vessel using the tow points.Periodic Maintenance:1.Spray down the boat thoroughly after each use.2.Wash down Cane Creek DBAir shock absorbers with soapy water. Rinse clean.3.Ensure all suspension pins are properly greased. If not, apply fresh marine grease via pinmounted zirc fittings.Apply grease here4.Ensure hinge system is properly greased. If not, apply fresh marine grease via hinge shaftmounted zirc fittings.Apply grease here5.Inspect suspension system C-Clips. Replace if damaged or not seated properly.Replace ifdamaged6.Inspect all quick release retaining pins for proper spring retention mechanism function. Test bytrying to remove each pin without depressing the release button. If the pin comes free, replace immediately.7.Every three months, thoroughly clean both hulls and apply an inflatable hull protectant forhypalon boats.pin to work properly. Replace immediatelyif damaged or seized.Inflatable Hull Care, Maintenance & RepairHulls are made of hypalon fabric. In the unlikely event of damage or puncture, please contact a local inflatable hull service center or manufacturer for repair. Do not attempt to patch the hulls. Every three months, thoroughly clean both hulls and apply an inflatable hull protectant for hypalon boats. This will reduce fading and drying caused by repeated UV exposure.Packing For ShipmentPlease refer to the following instructions when packing your RobotX WAM-V USVx for shipment.y font arch and rear arch into shipping box.2.Insert arch foam supports.3.Place payload tray upside down on 4x4 wooden standoffs, ensuring that the tray is constrainedlaterally and longitudinally.4.Secure the payload tray and arches with a single ratchet strap around the payload tray.5.Wrap ratchet strap handle to prevent scratching and damage to hulls during transit.6.Attach hull protection foam to the payload tray.7.Install front cross brace.8.With hulls deflated and suspension air pressure removed, rest skis in the foam saddles withforward portion resting on the cross brace.IMPORTANT: Ensure that the hull is not pinched when ratcheting down the skis.lifting handle.Secure the rear capture crossbar with a ratchet strap.11.Secure the front capture crossbar with a ratchet strap.12.Check to make sure all components are secure and that suspension systems are deflated enoughfor lid clearance.13.Place lid on shipping box. Be sure to line up the lid properly as indicated by the black paintmarking at the corner of the box14.Secure the lid by locking all fasteners.Vendors: Component Specifications and ManualsHardcopies for all commercial off the shelf components are included with this manual. If hard copies are unavailable, digital copies may be downloaded via the links provided below (if available).Cane Creek:DB Air: /tech-center/suspension/manualsSKS:SAM Pump: See backside of included packaging for instructions on how to use, or contact an SKS representative via /index.php.Gommorizzo:Hulls: http://www.gommorizzo.it/index.asp40。
MT3DMS基础

培训参考资料MT3DMS 基础北 京2007年10月第1章前言模块化三维溶质运移模型MT3D是C. Zheng(郑春苗)在S. S. Papadopulos & Associates公司工作期间开发的模拟软件(1990),美国环境保护署Robert S. Kerr环境研究实验室资助。
此后几年,MT3D在污染物迁移和治理评估研究中得到广泛应用。
第二代MT3D称为MT3DMS,其中MT3D仍然代表Modular 3-Dimensional Transport model (模块化三维溶质运移模型),而MS表示可插入多种污染物组分生化反应模块的程序结构。
其功能得到显著改善,包括:(1)利用三阶总变差缩减法(TVD)能够在保证质量守恒的基础上尽可能减小数值弥散和人工振荡引起的误差;(2)使用一种基于广义共轭梯度法的迭代算法,这种迭代法可以有效地避免对运移时间步长的限制;(3) 增加了处理非平衡吸附和双重介质中对流-扩散问题的处理方法;(4)程序采用多组件结构,从而可以随时插入模拟生物化学反应的模块。
MT3DMS的功能全面,既可以模拟常规水文地质条件下地下水流系统中污染物的对流、弥散\扩散过程,也可以模拟污染物在在迁移过程中的生物和化学反应。
下面简要介绍MT3DMS的主要特征。
MT3DMS的独特性在于它囊括了三种主要的运移问题求解技术:标准有限差分法;基于粒子跟踪的欧拉-拉格朗日法;以及高阶有限容量TVD法。
由于没有一种单独的技术对所有运移条件都适用,总是既有优点又有缺陷,有理由相信,把这些技术综合起来是解决各种的溶质运移问题的最有效途径。
作为MT3D原代码中显式公式的补充,MT3DMS含有隐式公式,并采取一种有效的通用迭代算法进行求解。
该算法基于广义共轭梯度法(GCG),有三种预处理选项,采用Lanczos/ORTHOMIN加速算法处理非对称矩阵。
如果选择GCG 解法,默认隐式公式计算弥散项、源汇项和反应项,无须施加约束条件。
- 1、下载文档前请自行甄别文档内容的完整性,平台不提供额外的编辑、内容补充、找答案等附加服务。
- 2、"仅部分预览"的文档,不可在线预览部分如存在完整性等问题,可反馈申请退款(可完整预览的文档不适用该条件!)。
- 3、如文档侵犯您的权益,请联系客服反馈,我们会尽快为您处理(人工客服工作时间:9:00-18:30)。
Supplemental User’s Guide
Chunmiao Zheng
Department of Geological Sciences The University of Alabama
Technical Report February 2010
MT3D MS v5.3
Supplemental User’s Guide
By Chunmiao Zheng Department of Geological Sciences The University of Alabama Tuscaloosa, Alabama 35487
a modular three-dimensional multispecies transport model for simulation of advection, dispersion and chemical reactions of contaminants in groundwater systems
ii
Preface
This document describes the cumulative changes and enhancements made since Version 5.0 of the MT3DMS solute fate and transport model. It is intended as a supplement to the original MT3DMS Documentation and User’s Guide published by the U.S. Army Corps of Engineers (Zheng and Wang, 1999; available at /mt3d). Readers should refer to Zheng and Wang (1999) for complete information on the theoretical background, numerical implementation, input instructions, and application examples for the MT3DMS model. Funding for the development of MT3DMS was provided in part by the U.S. Army Engineer Research and Development Center of the U.S. Army Corps of Engineers (USACE) in Vicksburg, Mississippi. The author is deeply grateful to Mark Dortch of USACE for his continuing support for MT3DMS development and enhancement. The development of the Transport Observation Package benefited from numerous discussions with Norm Jones and John Doherty. Keith Halford and Mary Hill were instrumental in enabling the Multi-Node Well Package in MODFLOW-2000 to interface with MT3DMS. Finally, the author acknowledges the assistance from Chris Neville, Matt Tonkin, Henning Prommer, Chris Langevin, Ned Banta, Eileen Poeter, and Rui Ma in various aspects of MT3DMS development.
iii
Table of Contents
Preface.......................................................................................................................... iii 1. Introduction ................................................................................................................1 2. Running MT3DMS Using the Name-File Method ....................................................3 3. Using the New Transport Observation (TOB) Package ............................................8 4. Simulating the Effect of Multi-Node Wells on Solute Transport ............................18 5. Support for Additional MODFLOW-2000 Sink/Source Packages ..........................22 6. Simulating Zeroth-Order Reactions in Single- and Dual-Domain Systems ............25 7. Using the Component-Dependent Diffusion Option ...............................................31 8. Simulating the Effect of a Recirculation Well .........................................................33 9. Arbitrary Time-Varying Mass Loading Source or Boundary Condition* ...............35 10. Running MT3DMS in Steady-State Mode ............................................................38 11. Using MT3DMS for Heat Transport Simulation ...................................................41 References ....................................................................................................................44 Appendix A. Changes to the Input Instructions since MT3DMS v5.0 ........................46
(*The blue color indicates new documentation added for Version 5.3.)
iv
1 Introduction
This document describes the cumulative changes and enhancements made since Version 5.0 of the MT3DMS solute fate and transport model and discusses all the new features that have become available since Version 5.0. It is intended as a supplement to the original MT3DMS Documentation and User’s Guide (Zheng and Wang, 1999). For the most up-to-date information on MT3DMS, refer to the README file included with the distribution files. There are a couple of significant organizational changes to Version 5 compared to the previous Version 4. First, the Name-File procedure becomes the only method to start a MT3DMS simulation run since v5.0. A Name-File specifies the names of most input and output files used in a model simulation. In addition, it controls the parts of the model program that are active, i.e., the “packages” that are used in the current simulation. Second, the implicit matrix solver, the General Conjugate-Gradient (GCG) solver, must be used in every simulation since v5.0. In other words, the dispersion, sink/source and reaction terms are now always solved by the implicit finite-difference method, regardless of whether the advection term is solved by the implicit finite-difference method, the mixed Eulerian-Lagrangian methods, or the third-order TVD method. A major new feature for MT3DMS since v5.0 is the Transport Observation (TOB) Package to save the calculated concentration at any observation location within the model domain and the calculated mass flux at any sink/source location. The calculated values are saved to output files, and optionally, along with the statistics of residuals between the calculated and observed values at the observation locations. The calculated concentrations can be interpolated from the nodal values if the observation point does not coincide with a model node. The calculated mass flux can be defined over any arbitrary group of sink/source cells referred to as a mass flux object. Another important addition to MT3DMS since v5.0 is the support for the MultiNode Well (MNW) Package (Halford and Hanson, 2002) used by MODFLOW-2000 (Harbaugh et al., 2000) and MODFLOW-2005 (Harbaugh, 2005) to simulate the flow to a well screened over multiple nodes (layers). The MNW Package automatically partitions the total flow prescribed for a MNW into individual nodes (layers) and determines a single head value in the wellbore. Accordingly, MT3DMS computes a single composite concentration for the same wellbore based on the flux-weighted concentrations of the injected fluid (if any) and the flow rates from different layers. Since Version 5.0, MT3DMS has also added support for more new MODFLOW sink/source packages, including Drain with Return Flow (DRT) and Evapotranspiration with a Segmented Function (ETS), both documented in Banta (2000). The DRT Package in MODFLOW-2000 simulates the re-injection of a portion of the outflow from a drain cell back into the aquifer. MT3DMS assigns the concentration at the outflow cell as that