150万吨年渣油催化裂化反应再生系统工艺设计毕业设计
催化裂化装置反应再生及分馏系统工艺设计方案
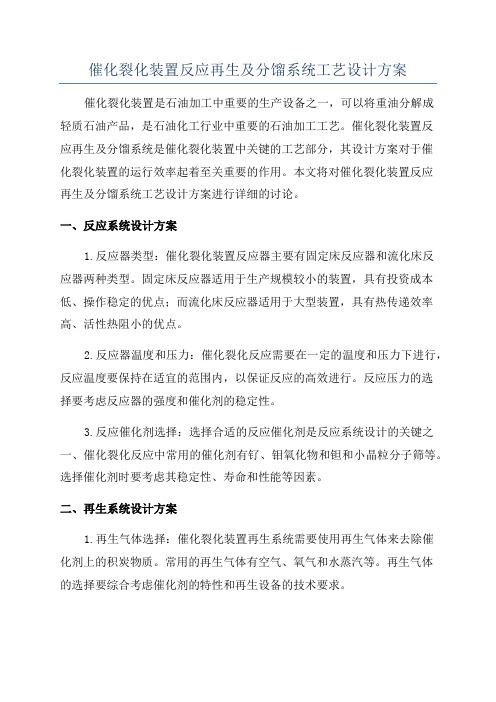
催化裂化装置反应再生及分馏系统工艺设计方案催化裂化装置是石油加工中重要的生产设备之一,可以将重油分解成轻质石油产品,是石油化工行业中重要的石油加工工艺。
催化裂化装置反应再生及分馏系统是催化裂化装置中关键的工艺部分,其设计方案对于催化裂化装置的运行效率起着至关重要的作用。
本文将对催化裂化装置反应再生及分馏系统工艺设计方案进行详细的讨论。
一、反应系统设计方案1.反应器类型:催化裂化装置反应器主要有固定床反应器和流化床反应器两种类型。
固定床反应器适用于生产规模较小的装置,具有投资成本低、操作稳定的优点;而流化床反应器适用于大型装置,具有热传递效率高、活性热阻小的优点。
2.反应器温度和压力:催化裂化反应需要在一定的温度和压力下进行,反应温度要保持在适宜的范围内,以保证反应的高效进行。
反应压力的选择要考虑反应器的强度和催化剂的稳定性。
3.反应催化剂选择:选择合适的反应催化剂是反应系统设计的关键之一、催化裂化反应中常用的催化剂有钌、钼氧化物和钽和小晶粒分子筛等。
选择催化剂时要考虑其稳定性、寿命和性能等因素。
二、再生系统设计方案1.再生气体选择:催化裂化装置再生系统需要使用再生气体来去除催化剂上的积炭物质。
常用的再生气体有空气、氧气和水蒸汽等。
再生气体的选择要综合考虑催化剂的特性和再生设备的技术要求。
2.再生温度和压力:再生温度对催化剂的再生效果有重要影响,要选择合适的再生温度,以保证催化剂的活性能得到有效的恢复。
再生压力的选择要考虑再生设备的设计和操作要求。
3.再生设备选择:再生设备主要有再生炉和再生器两种类型。
再生炉适用于小型装置,具有结构简单、操作方便的优点;再生器适用于大型装置,具有稳定的再生效果和高效的催化剂循环的优点。
三、分馏系统设计方案1.分馏塔类型:催化裂化装置的分馏塔主要有常压塔和减压塔两种类型。
常压塔适用于生产重质油品,具有生产成本低、操作稳定的优点;减压塔适用于生产轻质油品,具有产品质量好、产品收率高的优点。
催化裂化装置反应再生系统工艺流程
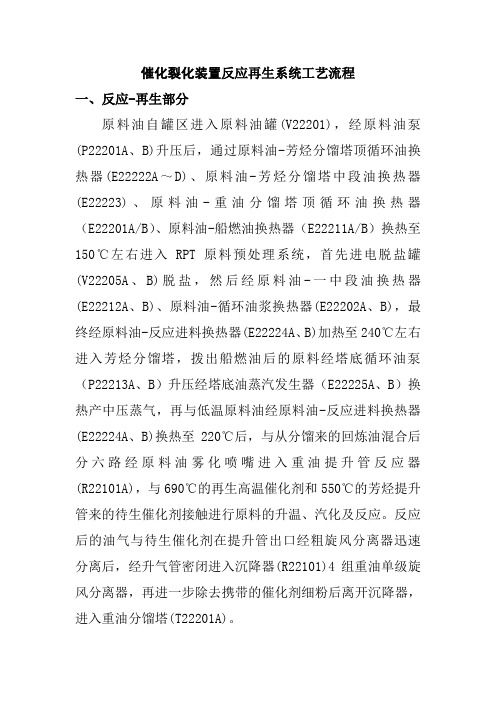
催化裂化装置反应再生系统工艺流程一、反应-再生部分原料油自罐区进入原料油罐(V22201),经原料油泵(P22201A、B)升压后,通过原料油-芳烃分馏塔顶循环油换热器(E22222A~D)、原料油-芳烃分馏塔中段油换热器(E22223)、原料油-重油分馏塔顶循环油换热器(E22201A/B)、原料油-船燃油换热器(E22211A/B)换热至150℃左右进入RPT原料预处理系统,首先进电脱盐罐(V22205A、B)脱盐,然后经原料油-一中段油换热器(E22212A、B)、原料油-循环油浆换热器(E22202A、B),最终经原料油-反应进料换热器(E22224A、B)加热至240℃左右进入芳烃分馏塔,拨出船燃油后的原料经塔底循环油泵(P22213A、B)升压经塔底油蒸汽发生器(E22225A、B)换热产中压蒸气,再与低温原料油经原料油-反应进料换热器(E22224A、B)换热至220℃后,与从分馏来的回炼油混合后分六路经原料油雾化喷嘴进入重油提升管反应器(R22101A),与690℃的再生高温催化剂和550℃的芳烃提升管来的待生催化剂接触进行原料的升温、汽化及反应。
反应后的油气与待生催化剂在提升管出口经粗旋风分离器迅速分离后,经升气管密闭进入沉降器(R22101)4组重油单级旋风分离器,再进一步除去携带的催化剂细粉后离开沉降器,进入重油分馏塔(T22201A)。
重油分馏塔分馏后的塔顶油气经冷凝冷却后进入油气分离器(V22203A),分离出的粗轻燃油分四路经雾化喷嘴进入芳烃提升管反应器(R22101B),与690℃催化剂接触进行原料的升温、汽化及反应。
反应后的油气与待生催化剂在提升管出口经粗旋风分离器迅速分离后,经升气管密闭进入沉降器内轻燃油单级旋风分离器,再进一步除去携带的催化剂细粉后离开沉降器,进入芳烃分馏塔(T22201B)。
油气分离出来的待生催化剂与重油部分的待生催化剂一起进入反应沉降器的汽提段。
150万吨年渣油催化裂化反再系统工艺设计
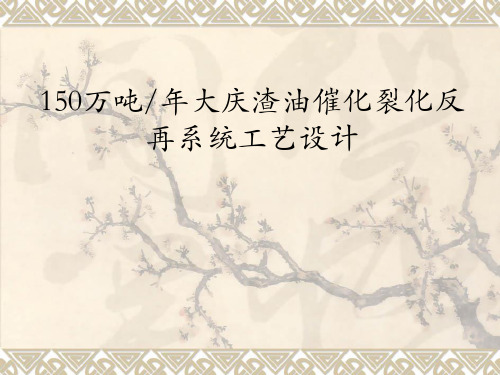
2.催化裂化研究方向
由于世界性的能源紧张,尤其是在石油这一不可再生 资源上表现更为明显,随着世界原油重质化趋势加剧,并 且随着科技的发展,以渣油为原料进行催化裂化生产轻质
油品成为世界石油工业一个很好的选择。但是,渣油与馏
分油相比,原料重,胶质、沥青质、残炭和金属含量高、 原料重,不宜于雾化;胶质、沥青质和残炭高,会显著增 加焦炭产率,使产品分布变差,同时给催化剂的汽提和再 生带来困难;对于不含沥青质的抽提油,其胶质含量与催 化裂化反应的焦炭产率之间呈直线关系;Ni、V等金属的 含量高,直接影响到催化剂的活性、选择性和稳定性。因 而,重油催化裂化使传统的催化裂化过程面临严峻挑战
150万吨/年大庆渣油催化裂化反 再系统工艺设计
一.文献综述
1.重油轻质化研究现状
(1)重油轻质化重要性
目前,世界轻质低硫原油的可供利用量正在减少,而重质 原油在全球资源量中的比例则呈逐年增加之势。如何转化产 量日益增长的重质原油和其中的大量高硫减压渣油,满足经 济发展对清洁燃料和低硫锅炉燃料油日益增长的需求,满足 日益严格的环保要求,已成为21世纪我国炼油业的重要课题 。
⑶快速分离装置
A粗旋风分离器 B粗预提升挡板式粗旋快分 C预汽提升旋流式快分 D密相环流预汽提升快分
⑷喉管式高效进料雾化喷嘴
其特点是压降较小,雾化效果较好,结构简单不易阻塞。
⑸空气分布器
使空气沿整个流化床截面分配均匀,创造一个良形式的选择
⑴加工方案的确定
(2)重油轻质化工艺比较
延迟焦化
焦化汽油馏分的辛烷值很低,仅60左右,溴价在40~60之 间,而且含氮量高,能达到1100~1900ppm,需要经过加氢精 制后才能成为合格产品,焦化馏分油的硫、氮含量较高,焦化 生产的石油焦价格低等。只适于减压渣油,且产品需要精制。
200万吨-年重油催化裂化反—再系统的设计

200万吨-年重油催化裂化反—再系统的设计200万吨/年重油催化裂化反—再系统的设计引言:随着工业化和城市化进程的加速发展,我们对石油产品的需求日益增长。
然而,石油资源的有限性使得石油加工工艺的研究显得尤为重要。
本文旨在探讨200万吨/年重油催化裂化反—再系统的设计。
一、催化裂化反—再系统的意义催化裂化是将较重、难以利用的石油馏分转化为高附加值的轻质石油产品的重要工艺之一。
200万吨/年的重油催化裂化反—再系统相当于每年从废旧物质中生产出200万吨的高附加值石油产品,对于节约资源、提高能源效率具有重要意义。
二、系统设计的基本原则1. 去除杂质:在重油催化裂化反应前,需要通过一系列处理步骤去除重油中的硫、氮等污染物,以保证反应的高效进行。
2. 催化剂选择:在催化裂化反应中,选择合适的催化剂对于提高反应效率非常关键。
我们可以选择活性高、稳定性好的催化剂,并结合新型载体材料、表面改性技术来改善催化剂性能,延长催化剂使用寿命。
3. 反应温度控制:催化裂化反应是一个高温反应,控制反应温度的适度升降,能够有效提高反应速率和产物分布,减少不良反应的发生,提高产品质量和数量。
4. 步骤合理性:合理地选择反应器结构和组件布置,能够有效地提高催化裂化反应的效果。
此外,选择合适的分离和再生工艺对产品质量的改善也至关重要。
三、系统设计的具体内容1. 前处理单元:主要包括在反应前对重油进行加热、脱水、除杂、除硫、除氮等步骤。
这些步骤旨在提高重油的质量,为后续的催化裂化反应做好准备。
2. 反应器单元:反应器单元是系统的核心部分,其中包括催化剂床、烟气分布器等。
在这个单元中,油与催化剂发生接触,经过裂化反应获得轻质石油产品。
合理地选择反应器结构和组件布置,能够提高催化裂化反应过程的效果。
3. 分离单元:分离单元是将裂解产物中的不同组分分离出来的过程。
通过减压蒸馏、消除剂分离等方法,可以将裂解产物中的轻质石油产品、液体石油气、重油等进行有效地分离。
催化裂化装置反应再生部分控制系统设计毕业设计
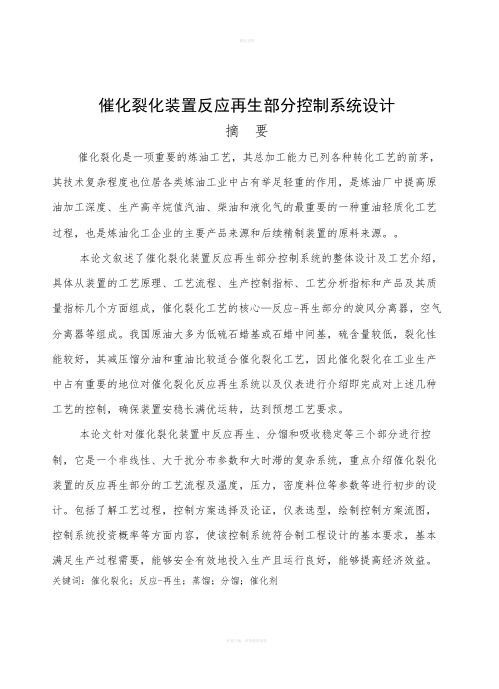
催化裂化装置反应再生部分控制系统设计摘要催化裂化是一项重要的炼油工艺,其总加工能力已列各种转化工艺的前茅,其技术复杂程度也位居各类炼油工业中占有举足轻重的作用,是炼油厂中提高原油加工深度、生产高辛烷值汽油、柴油和液化气的最重要的一种重油轻质化工艺过程,也是炼油化工企业的主要产品来源和后续精制装置的原料来源。
本论文叙述了催化裂化装置反应再生部分控制系统的整体设计及工艺介绍,具体从装置的工艺原理、工艺流程、生产控制指标、工艺分析指标和产品及其质量指标几个方面组成,催化裂化工艺的核心—反应-再生部分的旋风分离器,空气分离器等组成。
我国原油大多为低硫石蜡基或石蜡中间基,硫含量较低,裂化性能较好,其减压馏分油和重油比较适合催化裂化工艺,因此催化裂化在工业生产中占有重要的地位对催化裂化反应再生系统以及仪表进行介绍即完成对上述几种工艺的控制,确保装置安稳长满优运转,达到预想工艺要求。
本论文针对催化裂化装置中反应再生、分馏和吸收稳定等三个部分进行控制,它是一个非线性、大干扰分布参数和大时滞的复杂系统,重点介绍催化裂化装置的反应再生部分的工艺流程及温度,压力,密度料位等参数等进行初步的设计。
包括了解工艺过程,控制方案选择及论证,仪表选型,绘制控制方案流图,控制系统投资概率等方面内容,使该控制系统符合制工程设计的基本要求,基本满足生产过程需要,能够安全有效地投入生产且运行良好,能够提高经济效益。
关键词:催化裂化;反应-再生;蒸馏;分馏;催化剂The Satalyst Splits to Masquerade to Place to Respond Reborn Parts of Control System to DesignAbstractCatalyst crack's turning is an important xylene craft, its total process capability already row before various conversion technical Mao, its technique complicated degree also the potential reside to occupy a prominent action in each kind of xylene industry, The most important kind of heavy oil that raises the crude oil transform depth, capacity high octane value petrol, diesel and gasol in the oil refinery light guilder chemical engineering skill process, is also refine oil the staple products source of the chemical engineering business and the raw material source of the follow-up refined device. The our country crude oil is mostly low sulfur paraffin wax radicle or paraffin wax medium radicle, the sulfur contents is lower, crack turn performance better, its pressure reduction Liu deci the oil and heavy oil relatively suit a catalyst crack chemical engineering skill, therefore the catalyst crack turns in the industrial production to occupy an important stance.This text described a catalyst to split masquerade to place the overall design of responding reborn parts of control systems, from device of craft priniple, process flow, production control beacon and craft analysis beaconand product and it mass beacon a few aspects carry on introduction and concretely introduce catalyst crack to turn related up,crack-reaction-regenerate fraction and device progress introduction.Turn to respond that reborn system and meter carries on introduction and treatise to the catalyst crack.Regenerate, divide Liu and absorption to stabilize...etc. to be three to is part of to constitute, it is a nonlinear, change, strong coupling, big jam rayleing distribution rayleigh parameter and big the complicated system , The catalyst splits masquerades to place to press the craft priniple to dividing can is divided into regard chemical reaction as principle of reaction reborn fraction with with distil, the absorption compromise absorb physical process of etc. for lord of deci Liu and stabilization two fractions. On the Zong say, respond regenerate fraction again can is divided into the catalyst crack under the heat to turn reaction oil article fraction and take being burned as main of catalyst activity regenerate fraction.Key word:The catalyst crack turns;Reaction-regenerate;Distil;Divide ;Catalyst目录摘要 (I)ABSTRACT (II)第1章前言 (1)第2章催化裂化工艺流程 (3)2.1工艺概述 (3)2.2工艺组成 (5)2.2.1 反应-再生系统 (5)2.2.2 分馏系统 (6)2.2.3 吸收稳定系统 (7)2.2.4反应—再生系统流程 (8)第3章控制方案设计及论证 (13)3.1控制系统的控制目标 (13)3.2设计控制系统应遵循的原则 (13)3.3自动控制系统的基本方案 (15)3.4控制方案的设计及论证 (16)3.4.1 加热炉控制 (19)3.4.2 反应—再生系统工艺参数控制 (22)第4章主要仪表及选型 (27)4.1仪表的选型 (27)4.1.1 温度测量仪表 (27)4.1.2 压力测量仪表 (28)4.1.3 流量测量仪表 (28)4.1.4 液位测量仪表 (30)4.2调节阀的选择 (31)4.3DCS系统选型 (32)4.4系统概算 (34)第5章总结 (35)参考文献 (36)谢辞 (37)第1章前言石油炼制工艺的根本目的,一是提高原油加工深度,得到更多数量的轻质油产品;二是增加品种,提高产品质量。
115万吨每年催化裂化装置反应再生系统工艺设计毕业论文

115万吨每年催化裂化装置反应再生系统工艺设计毕业论文目录摘要................................................................................................ 错误!未定义书签。
Abstract......................................................................................... 错误!未定义书签。
1 概述 (1)1.1 重油催化裂化的发展概述 (1)1.2 常压重油催化裂化的可行性 (2)1.3 同轴式催化裂化装置特点 (2)1.4 重油催化裂化现状以及未来发展趋势 (3)2 催化裂化生产参数和装置设备的说明 (5)2.1 生产方案详述 (5)2.2 装置形式及特点 (6)2.3 生产流程简述 (7)2.3.1 反应—再生系统 (7)2.3.2 分馏系统 (8)2.3.3 吸收稳定系统 (8)2.3.4 烟气能量回收系统 (8)2.4主要操作条件的选择依据 (9)2.4.1 反应温度 (9)2.4.2 再生温度 (9)2.4.3 反应压力 (10)2.4.4 再生压力 (10)2.4.5 原料预热温度 (11)2.4.6 反应时间 (11)2.4.7 反应器藏量 (11)2.4.8 再生器藏量 (11)2.4.9 再生烟气中含氧量 (12)2.4.10 CO2/CO (12)2.4.11 H/C (12)2.5 装置设计特点 (12)2.5.1 采用倒L型快速分离器 (13)2.5.2 预提升段 (13)2.5.3 进料喷嘴 (13)2.5.4 采用耐磨弯头 (13)2.5.5 旋风分离器 (13)2.5.6 汽提段挡板 (14)2.5.7 空气分布管 (14)2.5.8 辅助燃烧室 (14)2.5.9 折叠式提升管 (14)2.5.10 用外集气管 (14)2.5.11 塞阀 (14)2.5.12 两器两段完全再生 (15)2.5.13 取热器 (15)2.6 催化剂和助剂的选取 (15)2.6.1 OB—300型催化剂 (15)2.6.2 DNFVN—1复合金属钝化剂 (15)3 能量回收和环境保护 (17)3.1 能量回收 (17)3.2 环境保护 (17)3.2.1 污水的来源及治理 (17)3.2.2 污水的治理 (17)3.3 废气的来源及治理 (18)3.3.1 废气的来源 (18)3.3.2 废气的治理 (18)3.3.3 粉尘的防治 (18)3.3.4 烃类损失及措施 (18)3.4 废渣的来源及治理 (18)3.4.1 废渣的来源 (18)3.4.2 废渣处理 (18)3.5.1 噪音的来源 (19)3.5.2 噪声的防治 (19)3.6 清洁生产 (19)3.6.1 清洁生产的基本思想 (19)3.6.2 清洁生产的基本内容 (19)3.6.3 清洁生产的对催化裂化的意义 (19)4 催化裂化反应-再生系统工艺计算 (20)4.1 燃烧计算 (20)4.1.1 再生器物料平衡 (20)4.1.2 再生器热平衡 (22)4.2 反应器热平衡 (25)4.2.1 反应系统供热方 (25)4.2.2 反应系统耗热方 (25)4.2.3 求催化剂循环量 (27)4.2.4 剂油比 (27)4.2.5 待生剂含碳量 (27)4.3 外取热器计算 (28)4.3.1 计算Q取 (28)4.3.2取热分配 (28)4.3.3 管根数的确定 (29)4.3.4 过热蒸汽管计算 (29)4.3.5 外取热器管径 (30)4.3.6 外取热器高H (30)4.4 再生器结构计算 (30)4.4.1 密相段直径D (31)4.4.2 密相段高度H (31)4.4.3 稀相段直径D’ (32)4.4.4 稀相段高度H (32)4.5 再生器空气分布管 (32)4.5.1 分布管内气体流量 (32)4.5.3 开孔面积计算 (33)4.6 催化剂输送 (34)4.6.1 待生立管的直径和长度 (34)4.7 旋风分离器计算 (34)4.7.1 选型 (34)4.7.2 计算旋风分离器的组数 (35)4.7.3 核算料腿的负荷 (36)4.7.4 旋风分离器压力平衡 (36)4.7.5 旋风分离器效率 (38)4.7.6 旋风分离器工艺计算结果 (38)4.8 辅助燃烧室 (38)4.8.1 热负荷 (38)4.8.2 结构尺寸 (39)4.8.3 二次空气分配 (39)4.8.4 辅助燃烧室环隙面积 (39)4.8.5 空气进口管线的直径 (40)4.9 反应系统工艺计算 (40)4.9.1 提升管反应器基础数据 (40)4.9.2 提升管进料处的工艺计算 (42)4.9.3 沉降器 (45)4.9.4 气提段工艺计算 (45)4.9.5 旋风分离器 (46)4.9.6 两器压力平衡数据 (47)5 计算结果汇总 (51)结束语 (54)参考文献 (55)谢辞 (56)1 概述1.1 重油催化裂化的发展概述我国原油一般较重,常压渣油占原油的60%~75%,减压渣油占原油的40%~50%,又因为我国渣油充足,所以发展重油的催化裂化是提高轻质油产量的有效途径。
万吨年新疆渣油催化裂化反再系统工艺设计

万吨年新疆渣油催化裂化反再系统工艺设计引言本文将介绍万吨年新疆渣油催化裂化反再系统的工艺设计。
催化裂化是一种常用的炼油技术,可将重质原油转化为高附加值的轻质产品。
本设计旨在提高反应转化率、优化产品分布并减少能耗。
首先,将会介绍系统的基本原理和工艺流程,然后深入讨论关键设备的选择和设计参数的优化。
最后,对设计方案进行总结和展望。
基本原理和工艺流程催化裂化反再系统是一种将重质原油转化为轻质产品的工艺,通过使用催化剂在高温下进行催化裂化反应。
基本原理是将原油在催化剂的作用下进行热解,产生大量的气体和液体产品。
该工艺流程通常包括以下步骤:1.反应器:原油和催化剂在高温下反应,产生裂解产物。
反应器通常采用流化催化床或移动床反应器。
2.分离器:将反应产物进行分离,得到轻质产品(如汽油、柴油)和重质产物(如渣油)。
3.催化再生:将用于反应的催化剂中吸附的杂质和积碳进行燃烧,恢复催化剂活性。
4.裂解气体处理:对裂解气体进行处理,如脱硫、脱氮、脱氢等。
设备选择和设计参数的优化反应器选择在选择反应器时,应综合考虑以下因素:•反应器类型:流化催化床反应器和移动床反应器是常用的选择。
流化催化床反应器具有较高的传热和传质效率,适合处理高含硫原料油;移动床反应器则适用于处理低含硫原料油。
•反应器尺寸:需要根据预计的产量和催化剂的重量来确定反应器的尺寸。
较大的反应器容器可以提高生产效率和运行稳定性。
•反应器温度和压力:反应器的温度和压力会影响反应的转化率和选择性。
应根据催化剂的性质和裂化产物的需求来确定最佳的反应条件。
分离器设计分离器的设计应考虑以下因素:•分离器类型:常见的分离器类型包括闪蒸塔、吸附分离塔和精馏塔。
根据不同的产品需求和分离要求,选择合适的分离器类型。
•收率和选择性:通过调整分离器的操作条件,如温度、压力和塔板,来达到所需的产品收率和选择性。
•分离器尺寸:分离器的尺寸应根据预计的产量和产品质量要求来确定。
较大的分离器可以提高分离效率和产品质量。
催化裂化装置反应再生部分控制系统设计
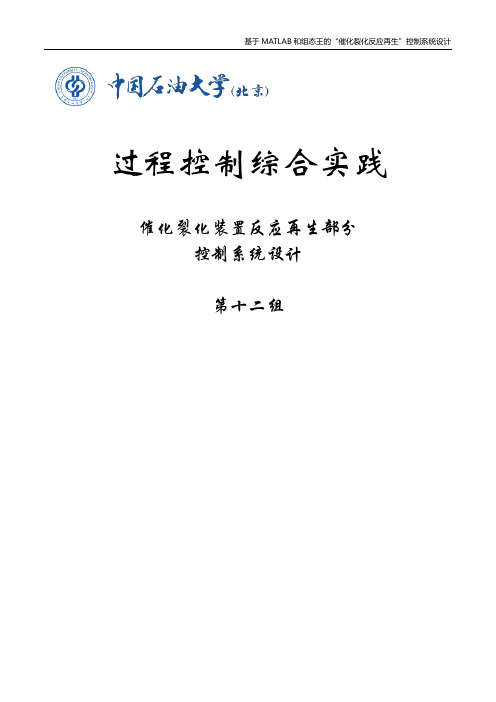
过程控制综合实践催化裂化装置反应再生部分控制系统设计第十二组目录第一章系统分析 (1)一、工艺流程 (1)二、控制需求分析 (2)三、对象特性分析 (2)1.控制系统特点 (2)2.控制系统扰动 (2)3.控制难点 (2)第二章控制系统详细的设计 (3)一、系统变量设置 (3)二、控制回路设计 (3)三、安全联锁报警设计 (4)四、I/O表 (5)第三章设备选型与图纸绘制 (6)一、控制器选型 (6)二、调节阀选型 (6)三、测量变送装置选型 (7)四、PLC接线图 (7)1.CPU224接线端子图 (7)2.EM235接线端子图 (8)3.控制柜接线图 (8)4.控制柜柜门设计图 (9)五、系统图纸绘制 (9)1.P&ID图图纸规格 (9)2.P&ID图的内容 (9)3.P&ID图中设备 (10)4.P&ID图中管道 (10)5.P&ID图代号和图例 (10)6.其它 (10)第四章MATLAB仿真研究 (11)一、基于MATLAB的控制对象仿真 (11)1.参考模型FCC——Linear (11)2.对象特性的阶跃响应测试 (12)二、数字控制器的设计 (12)三、控制参数对控制性能的影响及参数整定 (13)1.PID的三个调整参数对控制系统的影响 (13)2.参数整定结果 (14)第五章MATLAB与组态王的DDE连接 (17)一、动态数据交换 (17)二、组态王DDE功能 (17)三、MATLAB与组态王建立连接 (17)第六章组态王监控软件的详细设计 (20)一、组态王监控软件的界面设计 (20)二、监控软件功能设计 (20)1.工艺流程画面 (20)2.总体实时监控画面 (21)3.各个回路独立监控画面 (21)4.数据报表画面 (22)5.报警画面及报警查询画面 (23)6.总控制室画面 (23)7.标签画面 (23)三、设计过程 (23)1.建立组态王新工程 (23)2.创建组态画面 (24)3.定义I/O设备 (24)4.构造数据库 (24)5.建立动画连接 (24)6.运行和调试 (24)第七章实验结果及分析 (25)一、系统使用流程 (25)二、实际运行效果 (25)1.阶跃响应实时曲线 (26)2.性能指标整理 (26)3.鲁棒性实验 (27)三、控制系统性能分析 (28)1.控制方案优点 (28)2.控制方案缺点 (28)3.模型改进 (29)第八章感受和建议 (30)一、设计感受 (30)二、遇到的一些问题 (30)第一章系统分析催化裂化(Fluid Catalytic Cracking)是原油二次加工的核心工艺。
- 1、下载文档前请自行甄别文档内容的完整性,平台不提供额外的编辑、内容补充、找答案等附加服务。
- 2、"仅部分预览"的文档,不可在线预览部分如存在完整性等问题,可反馈申请退款(可完整预览的文档不适用该条件!)。
- 3、如文档侵犯您的权益,请联系客服反馈,我们会尽快为您处理(人工客服工作时间:9:00-18:30)。
150万吨/年渣油催化裂化反应再生系统工艺设计毕业设计目录1 文献综述 (1)1.1催化裂化工艺产生的背景及意义 (1)1.1.1国外催化裂化 (1)1.1.2国内催化裂化 (2)1.2催化裂化技术的现状及发展 (2)1.2.1国外催化裂化技术的现状及发展 (3)1.2.2我国催化裂化技术的现状及发展 (5)1.3重油催化裂化 (7)1.3.1重油催化裂化的原料 (8)1.3.2重油催化裂化的产品 (8)1.3.3重油催化裂化装置特点 (8)1.4催化裂化装置研究进展 (11)1.4.1催化裂化再生装置形式 (11)1.4.2催化裂化反应装置形式 (15)1.4.3催化裂化反应—再生两器排布方式 (19)1.4.4提升管末端快速分离器 (21)1.4.5进料雾化喷嘴 (24)1.4.6空气分布器 (26)1.4.7结语 (29)12 设计说明 (30)2.1 加工方案的确定及装置形式的选择 (30)2.1.1 加工方案 (30)2.1.2 装置形式的选择 (30)2.2 流程说明 (30)2.2.1 反应再生系统 (30)2.2.2 分馏系统 (32)2.2.3 吸收稳定系统 (34)2.3 主要操作条件 (35)2.3.1 再生温度 (35)2.3.2 再生压力 (36)2.3.3 再生烟气中过剩氧含量 (36)2.3.4 反应温度 (36)2.3.5 反应压力 (37)2.3.6 焦中氢碳比(H/C) (37)2.3.7 反应时间 (38)2.3.8 烟气中CO与CO2比值(CO/CO2) (38)2.3.9 原料的预热温度 (38)2.3.10 再生剂含碳量(定碳) (39)2.4 装置设备的特点 (39)2.5 能量回收 (40)22.6 环境保护 (40)3 设计计算 (42)3.1 基础数据 (42)3.2 再生部分计算 (43)3.2.1 燃烧计算 (43)3.2.2 反应系统热平衡计算 (48)3.2.3 再生系统热平衡计算 (53)3.2.4 取热器的设计 (56)3.2.5 催化剂外循环管设计计算 (58)3.2.6 再生器结构尺寸计算 (59)3.2.7 催化剂输送管线 (64)3.2.8 旋风分离器的设计计算 (67)3.2.9 主风分布板的设计计算 (72)3.2.10 辅助燃烧室的设计计算 (73)3.2.11 能量回收的计算 (76)3.3 反应器部分计算 (78)3.3.1 提升管反应器的设计计算 (78)3.3.2 预提升管尺寸计算 (86)3.3.3 沉降器和汽提段尺寸计算 (86)3.3.4 旋风分离器的选型与核算 (91)3.4两器压力平衡计算 (93)34 工艺设计计算结果汇总 (98)4.1 反再系统主要操作参数计算结果汇总 (98)4.2 反应系统物料平衡 (103)4.3 反应系统水平衡 (105)4.4再生器物料平衡 (106)4.5 再生器水平衡 (106)4.7 再生系统热平衡 (107)4.8 再生器外取热器设计结果汇总 (108)4.9 再生催化剂线路 (109)4.10 待生催化剂路线 (109)4.11 反再系统主要操作条件 (110)致谢 (111)参考文献 (112)4130万吨/年渣油催化裂化反再系统工艺设计1 文献综述1.1催化裂化工艺产生的背景及意义一般原油经常减压蒸馏后可得到10~40%的汽油,煤油及柴油等轻质油品,其余的是重质馏分和残渣油。
如果不经过二次加工它们只能作为润滑油原料或重质燃料油。
但是国民经济和国防上需要的轻质油量是很大的,由于内燃机的发展对汽油的质量提出更高的要求.而馏汽油(辛烷值较低40)则一般难以满足这些要求。
原油经简单加工所能提供的轻质油品的数量和质量同生产发展所需要的轻质油品的数量和质量之间的矛盾促使了二次加工过程的产生和发展。
催化裂化是重质油轻质的主要手段。
在目前我们国家的汽油中,80%来自于催化裂化。
可见催化裂化在我国石化工业中占有极其重要的地位。
我国FCC加工能力占原油加工能力的26%.约有70%的汽油来自FCC装置。
最近几年,我国在渣油裂化、催化剂再生、工程设计、研究和开发等方面发展很快。
渣油FCC成为渣油转化有效而经济的方法[1]。
1.1.1国外催化裂化催化裂化的研究开始于19世纪90年代,随着固体酸性催化剂的问世,于1936年在美国诞生了世界上第一套固定床催化裂化工业装置。
固定床催化裂化存在设备结构复杂、操作繁琐,控制困难的缺点。
为了克服固定床的缺点,需要两项革新,即催化剂在反应和再生操作之间循环和减小催化剂粒径。
第一项革新结果出现了移动床,两项革新的结合得到了流化床。
最初移动床催化裂化定名为1ThermoforCatalyticCarcking(TCC),1943年,Maguolia石油公司投产了一套0.5Mt/a 的TCC装置。
1944年开发成功的小球合成硅酸铝催化剂是催化裂化过程的重大改进。
HPC公司开发的第一套Houdriflow移动床催化裂化工业化装置于1950年在美国投产。
第一套流化催化裂化装置于1942年在美国建成投产,而1946年硅铝微球催化剂的问世,更促进了催化裂化技术的发展。
至20世纪50年代前后采用密相床反应的流化催化裂化技术趋向成熟。
60年代中期,随着分子筛催化剂的推出,全提升管流化催化裂化工艺的地位得到了确立并延续发展至今。
[2]1.1.2国内催化裂化自我国第一套流化催化裂化(FCC)装置1965年5月在抚顺投产以来,我国催化裂化技术,特别是重油催化裂化技术取得了重大进展显著成绩,催化裂化已成为我国重油加工最基的手段和各炼油企业经济效益最重要的支柱.催化裂化技术在我国炼油工业中占有的地位,首先是和我国原油性质密切相关的.与中东地区古硫原油相比,我国绝大多数原油均属重质原油,大于350℃的重油产率一般占原油的70%~75%,因此,必须有足够的二次加工能力,才能有效利用原油,最大限度获得轻质油品.另一方面,我国绝大多数原油都属于氢含量较高的低硫低金属的石蜡基原油,最适合于采用重油催化裂化进行加工.针对我国原油的特点,采用催化裂化的加工方法,投资少,效益高,并能为化工综合利用提供多种原料.这正是催化裂化在我国炼油技术中占有极其重要的位置并在30年来取得迅速发展的根本原因[3]。
1.2催化裂化技术的现状及发展21.2.1国外催化裂化技术的现状及发展渣油催化裂化(RFCC)工艺主要有UOP公司的MSCC技术(毫秒催化裂化技术),在Mscc过程中,催化剂向下流动形成催化剂帘,原料油水平注入与催化剂垂直接触,实现毫秒催化反应。
反应产物和待生催化剂水平移动,依靠重力作用实现油气与催化剂的快速分离。
这种毫秒反应以及快速分离,减少了非理想的二次反应,提高了目的产物的选择性,汽油和烯烃产率增加、焦炭产率减少,能更好地加工重质原料,且投资费用较低同。
多产烯烃的FCC工艺技术该技术的主要特点:(1)设立第二提升管进行汽油二次裂化;(2)使用高ZSM-5含量的助剂;(3)采用密闭式旋风分离器。
中试结果表明,以Minas蜡油为原料可以得到18.37%的丙烯产率。
LCO改质——MAK工艺MAK轻循环油改质工艺是由Mobil、AKZO和Kellogg3家公司聪合开发的中压单段加氢裂化工艺,生产高辛烷值汽油和高质量柴油。
经MAK工艺改质后可明显提高其质量。
生成柴油馏份的十六烷值达到34—40。
轻烃预提升技术U0P公司和Ashland石油公司的干气预提升技术是目前应用效果较好的轻烃预提升技术。
UOP公司的预提升技术是在提升管底部用稀释剂(干气或蒸汽或者3是二者并用)对再生催化剂进行预加速、使催化剂的密度降低,这样从进料喷嘴喷出的油滴就能穿透催化剂覆盖整个提升管截面,达到良好的剂油混合效果,使油滴得到良好的汽化,从而获得较好的产品分布。
对于加工渣油的装置来说用轻烃代替蒸汽作为预提升介质除了具有上述作用外还能钝化催化剂上的重金属,从而起到了改善反应选择性的作用。
目前国内已有洛阳石化总厂、天津石化公司炼油厂、济南炼油厂和锦西炼化总厂等厂家的催化裂化装置应用了轻烃预提升技术。
提升管反应苛刻度控制技术为了确保提升管进料全部汽化、减少不希望的热裂化和过度裂化反应的发生,法国石油研究院(IFP)在其设计的R装置中应用了混合温度控制(~frC)技术。
采用混合温度控制技术可以改进原料油的汽化,并相应减少焦炭的产率。
混合温度控制技术将提升管分成了两个反应区,其中上游区混合温度高、剂油比大、剂油接触时问短;下游区在常规催化裂化反应条件下进行。
Kellogg公司设计的提升管急冷技术是在进料喷嘴以后通过专有的急冷油喷嘴打入部分急冷油来控制提升管剂油混合区的温度。
工业装置应用表明在保持相同的提升管出口温度时,采用急冷油技术后提升管精油混合段的温度提高了27.8--41.7℃。
催化剂循环增强技术CCETShell石油公司开发了自己的CCET技术。
该技术的核心是显著提高立管的稳定性,在立管入口附近优化催化剂条件以增加蓄压,使滑阀维持高压差来提高催化剂循环量这样就能提高装置处理量,而不必对催化剂输送管线和滑阀进行昂贵的改动。
采用CCET技术后,滑阀压差增大,催化剂循环量提高了50%。
41.2.2我国催化裂化技术的现状及发展渣油催化裂化(RFCC)工艺技术VRFCC是中国石化集团公司石油化工科学研究院、北京设计院和北京燕山石化公司合作开发的一项加工大庆减压渣浊的催化裂化新工艺。
多产柴油和液化气的MGD技术MGD技术是中国石油化工股份有限公司石油化工科学研究院(RIPP)开发的以重质油为原料.多产柴油的催化裂化MDP技术RIPP在传统增产柴油工艺技术的基础上开发了催化裂化增产柴油的新工艺MDP。
多产烯烃和高辛烷值汽油的DCC工艺技术近年来,DCC技术还在不断发展和完善,这些新进展主要有两个方面:一个是开发系列催化剂产品;另一个是改进工艺以进一步提高轻烯烃、特别是丙烯的产率。
在催化剂开发方面尽量使品种多样化以满足不同用户的需要,而新开发的渣油催化裂解催化剂已经在全常压渣油催化裂解装置上使用。
在工艺改进方面也已经取得很好的实验室结果,以大庆蜡油掺渣油为原料可以得到28%的丙烯产率,同现有Dcc技术相比丙烯产率可以提高6个单位以上。
多产异构烷烃的MIP技术我国催化裂化汽油中烯烃含量高达40%--65%,远远高于我国车用汽油烯烃不大于35%的指标。
由中石化石科院和中石化上海高桥分公司、洛阳石化工程公司联合攻关的多产异构烷烃的催化裂化技术(MIP),具有我国自主知识产权,是既5可促进重油转化、又可改善催化汽油质量以满足燃料清洁化需求的技术。
MIP技术先期于2002年在高桥分公司炼油厂140万t/aFCC装置上成功应用。