高通量循环流化床上升管气固流动特性实验研究
实验十三 流化床演示实验

实验十三 流化床演示实验一、实验目的流化床反应器,由于其结构上的特点,具有床内温度分布均匀,传热、传质效率较好,因此广泛地应用在石油、化工、煤炭、医药等部门,流态化技术日益受到重视。
通过本演示实验,要求了解气固相的运动特征,固定床、流化床的压降,如何表示临界流化速度及最大流化速度。
二、实验原理气体通过固定床时,压力降随着流速不断增大。
当压力降达到最高值时,床层开始松动,即开始流化。
此时的流速称为临界流化速度u mf ,当流速继续增大,以致使床层的固体颗粒带出,不再停留床内,此地的流速称为最大流化速度,u mf 因此测量压力降可直接反映流化速度。
流速与压力降的关系可用图13-1表示。
当流体通过床层固体颗粒时,由于流体与床层固体颗粒间的摩擦及流体的紊流作用产生压降。
压力降随空塔流速增大而增大。
如AB 线所示,AB 为未流化的固定床。
达到接近临界流化速度B 点时,固体颗粒层开始膨胀而不流化,由于空隙率增大,压力降较前降低。
在B 点后,颗粒可以在小范围内重新排列,空隙率略有增大。
在C 点后,全部床层流态化,若再增大流速,当流体的向上流速大于颗粒的沉降速度时,则固体颗粒被流体带出,此时的压力降将减少。
通过压力降的测量可以清楚表示它们的关系。
关于临界流休速度及最大流化速度,文献介绍的计算公式很多,但误差也很大,一般都采用实验方法实测求得。
流量用孔板流量计测量:ρρρ)(2-=R gR oAo C Vs式中:Vs ——流体的体积流量,m 3/s ;R ——U 型管压差计读数,m ;ρR ——压差计中指示液密度,kg/m 3; C o ——孔流系数。
图13-1 流速与压强的关系示意图Vs Aw V sw =∝∝压降:22f p l u h h f fg d gR p g λρρ∆==∙∝∆∆=△p=ΔR(ρ指-ρ)g其中:ρ指——压差计中指示液密度,kg/m 3。
ΔR ——U 型管中位差,m 。
g ——重力加速度,g=9.81m/s 2。
固体流态化的流动特性实验

固体流态化的流动特性实验(示范实验)1、实验目的在环境工程专业,经常有流体流经固体颗粒的操作,诸如过滤、吸附、浸取、离子交换以及气固、液固和气液固反应等。
凡涉及这类流固系统的操作,按其中固体颗粒的运动状态,一般将设备分为固定床、移动床和流化床三大类。
近年来,流化床设备得到愈来愈广泛的应用。
固体流态化过程又按其特性分为密相流化和稀相流化。
密相流化床又分为散式流化床和聚式流化床。
一般情况下,气固系统的密相流化床属于聚式流化床,而液固系统的密相流化床属于散式流化床。
①通过本实验,认识与了解流化床反应器运行。
掌握解流化床反应器启动中物料的连续流化方法及其测定的主要内容,掌握流化床与固定床的区别,掌握鼓泡流化床与循环流化床在本质上的差异。
②测定流化床床层压降与气速的关系曲线本实验的目的,通过实验观察固定床向流化床转变的过程,以及聚式流化床和散式流化床流动特性的差异;实验测定流化曲线和流化速度,并试验验证固定床压降和流化床临界流化速度的计算公式。
通过本实验希望能初步掌握流化床流动特性的实验研究方法,加深对流体流经固体颗粒层的流动规律和固体流态化原理的理解。
2、实验装置与实验原理介绍流化床反应器是一种易于大型化生产的重要化学反应器。
通常是指反应物料悬浮于从下而上的气流或者液流之中,气体或者液体中的成分在与反应物料的接触中发生反应。
流化床反应器在现代工业中的早期应用为20世纪20年代出现的粉煤气化的温克勒炉(见煤气化炉)。
目前,流化床反应器已在电力、化工、石油、冶金、核工业等行业得到广泛应用。
与固定床反应器相比,流化床反应器的优点是:①可以实现固体物料的连续输入和输出;②流体和颗粒的运动使床层具有良好的传热性能,床层内部温度均匀,而且易于控制,特别适用于强放热反应;③便于进行催化剂的连续再生和循环操作,适于催化剂失活速率高的过程的进行,石油流化床催化裂化的迅速发展就是这一方面的典型例子。
然而,由于流态化技术的固有特性以及流化过程影响因素的多样性,对于反应器来说,流化床又存在明显的局限性:①由于固体颗粒和气泡在连续流动过程中的剧烈循环和搅动,无论气相或固相都存在着相当广的停留时间分布,导致不适当的产品分布,阵低了目的产物的收率;②反应物以气泡形式通过床层,减少了气-固相之间的接触机会,降低了反应转化率;③由于固体反应物料在流动过程中的剧烈撞击和摩擦,使物料加速粉化,加上床层顶部气泡的爆裂和高速运动、大量细粒反应物料的带出,造成明显的反应物料流失;④床层内的复杂流体力学、传递现象,使过程处于非定常条件下,难以揭示其统一的规律,也难以脱离经验放大、经验操作。
大颗粒流化床上升管内两相流动的数值模拟
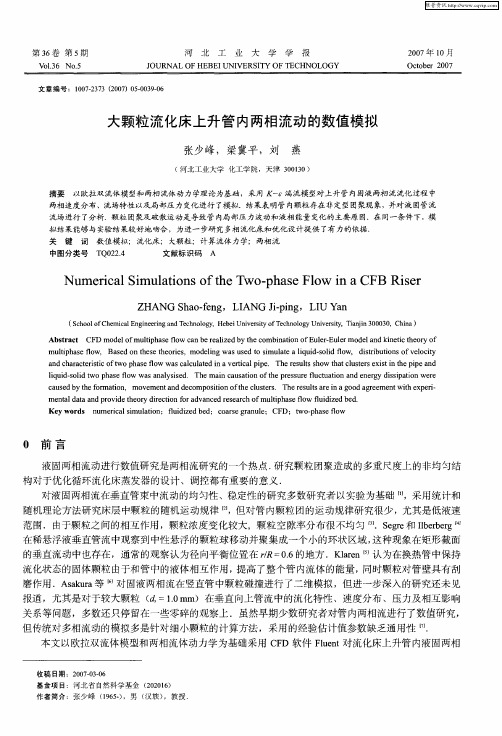
0 前 言
液固两相流动进行数值研究是两相流研 究的一个热 点. 研究颗粒团聚造成的多重尺度上的非均匀结
构 对于优化循 环流化床蒸发器 的设计 、调控 都有重要 的意义 .
对液 固两相流在垂直管束 中流动的均匀性 、稳定性 的研究多数研究者以实验 为基础 “ ,采用统计和 随机理论方法研 究床层 中颗粒 的随机运动规律 ,但对管 内颗粒 团的运动规律研究很少 , 尤其是低液速 范围.由于颗粒之 间的相互作用 ,颗粒浓度变化较大,颗粒 空隙率分布很不均匀 .Sg 和 I e e er e lrr bbg 在稀悬浮液垂直管流 中观察到 中性 悬浮的颗粒球移动并聚集成一个小的环状 区域 , 这种现象在矩形截面 的垂直流动中也 存在 ,通常的观察认 为径 向平衡位置在 = .的地方 .Ka n 认为在换热管中保持 0 6 l e r 流化状态的固体颗粒 由于和管 中的液体相互作用 , 提高 了整个管 内流体的能量 , 同时颗粒对 管壁具有刮 磨作用 . skr 等 同对 固液两相流在竖直管 中颗粒碰撞进行 了二维模拟 ,但进一步深入的研 究还未 见 A aua 报道 ,尤其是对于较大颗粒 ( =1 m .m )在垂直 向上管流中的流化特性 、速度分布 、压力及 相互影 响 0
Abs r c CFD o lo uliha efo c e lz d b hec m b n to e - l rm o l ndkie i o y f ta t m de fm tp s w anber a ie y t o i a in ofEulrEu e de n tct r o l a he muli a efo tph s w, Ba e n t s he re ,m od lngw a s d t i u ae alq d-ol fo l s d o he e t o is e i su e o sm l t iui s i l w, ditiuton e o iy d srb i sofv l ct a d c r ce itco wo p s o w a a c ae nave tc l pe Th e ulss w ha l t r xiti pea n ha a trsi ft ha ef w sc lult d i ri a l pi . er s t ho t tcuse se s nt pi nd he
流化床煤气化技术的分析研究进展

流化床煤气化技术的研究进展煤气化技术有多种分类法,按煤的进料状态可分为干块进料、干粉进料和煤浆进料。
煤层中燃料运动状态,可分为固定床<亦称移动床)、流化床、气流床和熔融床. 按床层压力等级,可分为低压< < 0.3MPa)、中压<0.3 MPa ~4.5 MPa)和高压< > 4.5MPa)。
按排渣状态,可分为干法<固态)、熔聚和熔渣<液态)。
目前,应用较广泛的煤气化技术有如下几种:1)加压固定床气化技术加压鲁奇炉是典型的加压固定床气化技术,技术成熟,能利用高灰分煤,并且能在2.41 MPa 压力下运行,适合合成液体燃料合成所需要的操作压力,可节约投资和能耗,但过程中产生大量的焦油和酚。
为克服上述缺点,又进行了新的开发,主要技术升级包括进一步提高压力、提高温度和两段引气。
2)流化床气化技术温克勒气化工艺是典型的流化床技术,最早用于工业生产,第一台工业生产装置于1926 年投入运行。
这种炉型存在严重的缺陷,只能利用高活性褐煤,排灰含碳多,飞灰带出碳损失严重,致使碳利用率降低。
针对这些问题开发了新的流化床技术,如高温温克勒<HTW)、灰熔聚气化<KRW ,U-gas)和循环流化床气化工艺。
3)水煤浆气流床气化技术水煤浆气流床气化又称湿法进料气流床气化,其中Texaco 炉是一种率先实现工业化的水煤浆气流床气化技术,其进料方式简单,工程问题较少,具有大的气化能力,可以实现高压力<8 MPa ~ 10MPa)操作。
但冷煤气效率较低,氧耗较高。
为了降低过程氧耗,提高冷煤气效率,在Texaco 气化技术基础上发展了两段进煤煤气化工艺。
4)干粉进料气流床气化技术干粉进料气流床气化技术相对湿法进料具有氧耗低,煤种适应广和冷煤气效率高等优点. 其代表技术有Shell,Prenflo 和日立气流床等。
Shell SCGP 工艺是在K-T炉的基础上所开发的加压K-T气化炉。
朱治平丨中国科学院工程热物理研究所
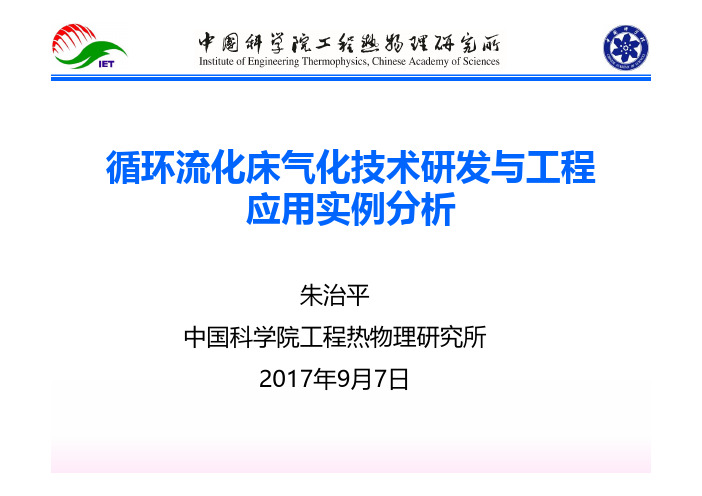
循环流化床气化技术研发与工程应用实例分析朱治平中国科学院工程热物理研究所2017年9月7日报告提纲中科院循环流化床技术简介1循环流化床煤气化技术工程应用3循环流化床煤气化技术研发2煤气化残碳处理技术研发与应用4中国科学院工程热物理研究所简介中国科学院直属科研机构,由中国工程热物理学科的奠基人吴仲华先生创建于1956年的中国科学院动力研究室发展而来主要从事能源、动力和环境等领域的基础研究与应用发展相结合的战略高技术研究获国家级和院、部级一、二等奖以上奖项40余项,研究所正高级科研人员45人,其中院士2人,国家杰青、百人计划、千人计划等22人拥有中关村本部、合肥分所、青岛分所、毕节分所、廊坊研发中心、连云港基地重大突破—煤炭清洁高效利用循环流化床技术实力中国重要的循环流化床技术研发基地•率先在中国开展循环流化床技术研发•拥有中国最大规模的循环流化床技术研发人员团队•拥有2400m 2试验用房,建有大中型冷热态试验平台近20套•拥有30多台套先进的测试和分析仪器循环流化床技术实力已形成具有自主知识产权的循环流化床技术研发平台•对循环流化床技术在煤及多种燃料和废弃物的燃烧、热解、气化等转化和利用方面的应用进行了30年系统研究•建立了中国典型煤种和典型生物质在循环流化床中的燃烧和排放特性数据库,正在建立典型煤种的循环流化床气化特性数据库•完成的技术创新已申报130多项国内外专利,其中100余项已获授权技术成果实现产业化应用•与锅炉行业有着广泛合紧密的长期合作,与多家锅炉生产企业建立了长期紧密的合作开发关系•2500余台产品级应用,循环流化床锅炉机组等级全面覆盖12MW-25MW-50MW-150MW-200/300MW基本炉型•以粉煤(0~12mm)核心目标煤质适应性强煤气中不含焦油和酚;无废水空间循环气化,易放大面向工业燃气、系统解决方案技术应用分类循环流化床煤制清洁工业燃气✓气化剂:空气+水蒸汽煤气热值:1200~1500 kcal/Nm3 规模15k~60km3/h台✓煤种适应性广泛,工业燃气成本0.1~0.15元/Nm3,折合天然气同热值<1元/Nm3✓连续运转率95%以上,无焦油酚水、化工废水排放面向中小合成氨改造—循环流化床富氧气化制合成气✓气化剂:富氧(~40%)+水蒸汽煤气组分:CO+H2~65% (CO+H2)/N2≈3✓0~12mm粉煤,煤种适应性广,吨氨煤耗、吨氨氧耗低,系统能将高✓煤气无焦油、无废水产生,清洁环保,大幅降低综合成本循环流化床纯氧气化制合成气✓直接使用0~12mm粉煤,焦末等,使用煤种不受灰熔点限制✓气化剂高温预热回收煤气热量,降低氧耗及氧气成本报告提纲中科院循环流化床技术简介1循环流化床煤气化技术工程应用3循环流化床煤气化技术研发2煤气化残碳处理技术研发与应用4✓14个用户,30台套工业应用✓数十种不同性质的煤为原料✓日处理煤量8600余吨✓稳定产出热值为1100~1450 kcal/Nm 3的煤气2580万Nm 3/d0.2t/d(2004)5t/d 中试(2012)25000Nm 3/h 冷煤气(2011)25000Nm 3/h 热煤气(2013)40000Nm 3/h 冷煤气(2014)60000Nm 3/h 冷煤气(2015)循环流化床煤气化技术研发来源工业分析/%收到基热值元素分析/%M ar A ar V ar V daf FC ar (MJ/kg)C ar H ar N ar O ar S ar 港口20.8 3.9633.9145.0741.3321.5758.44 3.580.7814.10.34内蒙17.213.2928.738.442.8219.8553.59 3.030.7211.340.84试验运行曲线试验用煤质产品级技术研发新式高温空气预热器技术大截面风帽以及无风室布风技术静态料层密封和逆流排渣技术高通量双级返料技术高效旋风分离技术高效间冷技术布袋除尘器前部温度保护和预分离联合技术横置锅筒无腔余热锅炉技术循环流化床气化炉技术产品开发:融合八大核心技术的系统集成已发表论文60余篇;申报国家发明专利24项,已获授权20项技术研发成果——第三方评价40000Nm 3/h 煤制工业燃气技术经中国石化联合会组织的鉴定被评价为达到国际领先水平(2015)25000Nm 3/h 煤制工业燃气技术经中国电机工程学会组织的鉴定被评价为达到国际先进水平(2015)0.1 t/d 小试试验台(2005年)8t/d 中试研究平台(2014年)金化500t/d 示范工程循环流化床加压煤气化技术研发报告提纲中科院循环流化床技术简介1循环流化床煤气化技术工程应用3循环流化床煤气化技术研发2煤气化残碳处理技术研发与应用4印尼W. H. Winning 4×30000Nm 3/h项目(2016年)我国首个海外运行的煤清洁制工业燃气项目中国铝业集团5×40000Nm 3/h 项目(2015年)我国一次建成的规模最大的工业燃气站信发集团分三期建成1×40000Nm 3/h (2014年)、2×40000Nm 3/h、2×60000Nm 3/h项目目前在建第四期2×60000Nm 3/h项目技术验证✓以华东、华北、华南、西北、印尼的十多种煤为原料✓技术产品已应用于国内和印尼的13个用户、共30台,产值11亿元,产气能力107.5万方/时产业化应用✓服务于铝业、镁业、焦化等行业(1+2)×40000Nm 3/h——冷煤气——350t/d (2+2)×60000Nm 3/h——600t/d ◆项目一期1台2014年5月投运,二期2台2015年7月投运,已经签订四期合同◆项目累计运行:1000天+,单次连续244天,连续运转率>92%◆国内首次完成此容量等级的工程示范及冷煤气工艺流程验证◆首次完成40~45%浓度的循环流化床富氧气化工业示范运行通过中国石油和化工联合会科技成果鉴定—达到国际领先水平信发华宇40000Nm 3/h 项目1.23.29.71075原料成本水电气人员固定资产折旧循环流化床煤制工业燃气与两段炉相比,单位体积煤气成本低0.15元/Nm3,以单气化炉满负荷年运行8000小时计算,累积节约成本5400万元/年本技术与两段炉相比,没有焦油酚水排放,劳动环境明显改善1×60000Nm 3/h——500t/d——替代焦炉煤气用于生产LNG ,焦未气化◆项目2015年8月投运,国内目前最大容量的常压循环流化床气化炉◆项目一次投运即通过168小时考核国内首台此容量等级、首次用于替换焦炉煤气制LNG迁安九江焦化60000Nm 3/h 项目工程应用实例——九江焦化工程应用实例——九江焦化5×40000Nm 3/h——350t/d——广泛应用高灰高水低阶煤◆项目2015年5月投运,当时国内最大容量的常压循环流化床煤气站◆中国铝业集团公司2016年标杆工程,单次连续运行310天,连续运转率95%广西平果铝5×40000Nm 3/h 循环流化床煤气化项目工程应用实例——广西平果铝典型应用业绩——广西平果铝原生产线基本情况规模:目前合成氨生产能力为年产8万吨合成氨,实际产能约为6万吨,计划目标为年产10万吨合成氨造气:间歇式制气,原料为石灰碳化煤球,半水煤气各成分含量为CO(28%~32%)、H2(33%~34%)、CO2(11.6~12.6%)、CH4(1.8~2.4%)、N2(19~22%)、H2S(1~2%)。
实验-4 气固流化床反应器的流化特性测定

实验四 气固流化床反应器的流化特性测定一、 实验目的1. 观察了解气固流化床反应器中不同气速下固体粒子的流化状况,建立起对流态化过程的感性认识。
2. 了解和掌握临界流化速度U mf 和起始鼓泡速度U mb 的测量原理、方法和步骤,明确细粒子流化床的基本特性。
3. 通过对U mf 和U mb 的测定,进一步理解两相理论以及临界流化速度与起始鼓泡速度的区别。
二、实验原理1.在气固流化床反应器中,气体通过床层的压力降△P 与空床速度U 0之间的关系能够很好地描述床层的流化过程。
如图1所示:气体自下向上流过床层。
当气速很小时,气体通过床层的压力降△P 与空床速度U 0在对数坐标图上呈直线关系(图1中的AB 段);当气速逐渐增大到△P 大致等于单位面积的重量时,△P 达到一极值(图1中P 点);流速继续增大时,△P 略有降低;此后床层压力降△P 基本不随流速而变。
此时将流速慢慢降低,开始时与前一样△P 基本不变,直到D 点以后,△P 则随流速的降低而降低,不再出现△P 的极大值,最后,固体粒子又互相接触,而成静止的固定床。
2.在一正常速度下,处于正常流化的流化床,如果突然关闭气源,则由于床层中有气泡存在,以气泡形式存在的气体首先迅速逸出床层,床层高度迅速下降;而后是浓相中的气体逸出,床层等速下降;最后是粒子的重量将粒子间的部分气体挤出,床层高度变化很小。
由此可得其床层高度随时间变化的崩溃曲线(如图2所示)。
因此,可以设想,如果床层中图1 △P ~ U 关系log Ul o g △P12 3465t (sec)260270 280 290 300 H T H D H D图2 H T ~ t 关系没有气泡,则床层一开始就随时间等速下降,所以,将上述崩溃曲线中的等速部分外推到t=0处时的床层高度,即为浓相床层的高度H D 。
这样,只要重复上述过程,多做几条崩溃曲线,总可以找到一条曲线,这条曲线正好无气泡逸出段,开始就是等速下降的起点。
提升管内的气固两相流动
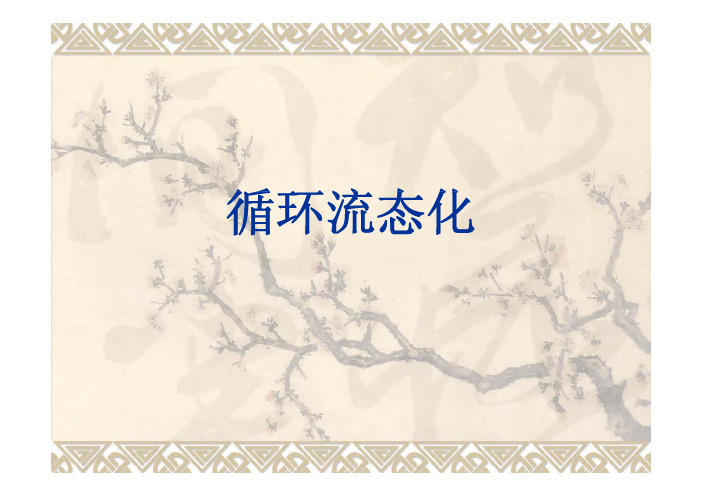
循环流态化循环流态化的存在区域 气、固流动规律气、固流动模型在垂直系统中,气、固接触形式及其流动状况不仅受设备的结构及气、固物性的影响,而且更直接和重要的是受操作条件的影响随着操作气速的提高垂直气固流动系统可条件的影响。
随着操作气速的提高,垂直气、固流动系统可出现散式流态化→鼓泡流态化→湍动流态化→快速流态化→密相气力输送→稀相输送等流动状态密相气力输送→稀相输送等流动状态。
循环流态化是指操作气速较高,并伴有颗粒循环的气、固两相并流向上的流动过程,是一种高效的、无气泡的气、固两相并流向上的流动过程,是种高效的、无气泡的气、固接触技术。
循环流化床广泛的应用于石油、化工、冶金、能源、环保循环流化床广泛的应用于石油化冶金能源环保等工业领域。
循环流态化的存在区域对垂直气固流动系统,当由湍动流态化进一步增大气速时,颗粒夹带速率愈益增大,床层界面愈趋弥散。
当气速增大至临界值时,颗粒夹带速率达到气体饱和携带能力。
在没有颗粒补入的情况下,床层颗粒将被很快吹空。
因此,为维持正常操作,必须向床中补入颗粒。
若补入速率太小,则床层发生由湍动流态化向稀相气力输送的直接过渡。
若补入速率增大则床层进入典型的快速流态化状态大,则床层进入典型的快速流态化状态。
在快速流态化区,气、固两相由湍动流态化时气体为分散相(气泡)颗粒为连续相的流动形态发生逆转,变为气体为连相(气泡)颗粒为连续相的流动形态发生逆转变为气体为连续相、颗粒为分散相(絮状物)的流动形态。
快速流态化的典型特征为床层压降主要用于悬浮和输送 快速流态化的典型特征为:床层压降主要用于悬浮和输送颗粒并使颗粒加速,颗粒密度沿轴向呈上稀下浓分布。
并且平均空隙率般为颗粒速度在床层中区向平均空隙率ε一般为0.75~0.95。
颗粒速度在床层中心区向上,在边壁区向下,呈现明显的内循环流动。
继续增大气速,则床层颗粒浓度不断变稀,轴向分布愈趋均匀。
到某一临界条件,空隙率轴向呈均匀的单一稀相,固相上稀下浓的复合状态消失,床内密度上下均匀,ε为0.95稀的复合态消失床内密度均匀左右分布,这就标志着快速流态化向密相气力输送的过渡。
气固流化床反应器的设计与优化
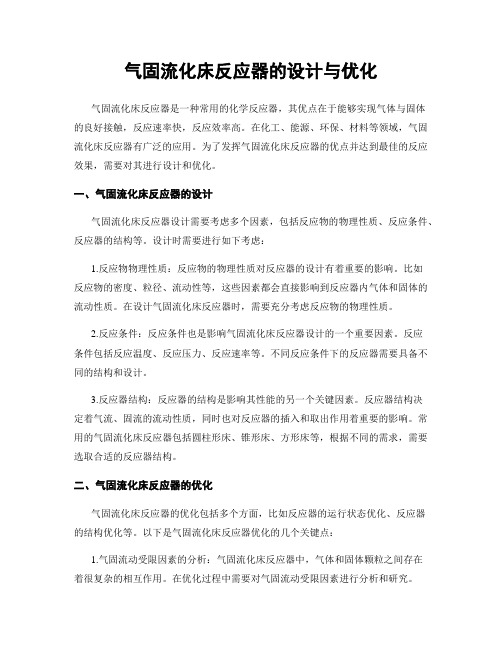
气固流化床反应器的设计与优化气固流化床反应器是一种常用的化学反应器,其优点在于能够实现气体与固体的良好接触,反应速率快,反应效率高。
在化工、能源、环保、材料等领域,气固流化床反应器有广泛的应用。
为了发挥气固流化床反应器的优点并达到最佳的反应效果,需要对其进行设计和优化。
一、气固流化床反应器的设计气固流化床反应器设计需要考虑多个因素,包括反应物的物理性质、反应条件、反应器的结构等。
设计时需要进行如下考虑:1.反应物物理性质:反应物的物理性质对反应器的设计有着重要的影响。
比如反应物的密度、粒径、流动性等,这些因素都会直接影响到反应器内气体和固体的流动性质。
在设计气固流化床反应器时,需要充分考虑反应物的物理性质。
2.反应条件:反应条件也是影响气固流化床反应器设计的一个重要因素。
反应条件包括反应温度、反应压力、反应速率等。
不同反应条件下的反应器需要具备不同的结构和设计。
3.反应器结构:反应器的结构是影响其性能的另一个关键因素。
反应器结构决定着气流、固流的流动性质,同时也对反应器的插入和取出作用着重要的影响。
常用的气固流化床反应器包括圆柱形床、锥形床、方形床等,根据不同的需求,需要选取合适的反应器结构。
二、气固流化床反应器的优化气固流化床反应器的优化包括多个方面,比如反应器的运行状态优化、反应器的结构优化等。
以下是气固流化床反应器优化的几个关键点:1.气固流动受限因素的分析:气固流化床反应器中,气体和固体颗粒之间存在着很复杂的相互作用。
在优化过程中需要对气固流动受限因素进行分析和研究。
2.反应器结构优化:反应器结构是影响其性能的另一个重要因素,选择合适的反应器结构可以优化其性能,加强其固体和气体之间的接触。
例如改变反应器的高宽比,调节反应器锥度等,都可以对反应器的性能进行优化。
3.气固流动数值模拟:使用CFD(计算流体动力学)软件对反应器进行数值模拟,可以帮助了解反应器内的流动性质和固体颗粒的分布情况。
对反应器运行状态进行数值模拟,可以有效地指导优化过程。
- 1、下载文档前请自行甄别文档内容的完整性,平台不提供额外的编辑、内容补充、找答案等附加服务。
- 2、"仅部分预览"的文档,不可在线预览部分如存在完整性等问题,可反馈申请退款(可完整预览的文档不适用该条件!)。
- 3、如文档侵犯您的权益,请联系客服反馈,我们会尽快为您处理(人工客服工作时间:9:00-18:30)。
第29卷第17期中国电机工程学报 V ol.29 No.17 Jun. 15, 20092009年6月15日 Proceedings of the CSEE ©2009 Chin.Soc.for Elec.Eng. 27 文章编号:0258-8013 (2009) 17-0027-05 中图分类号:TK 222 文献标志码:A 学科分类号:470·20高通量循环流化床上升管气固流动特性实验研究王小芳,金保升,钟文琪(东南大学能源与环境学院,江苏省南京市 210096)Experimental Study on Gas-solid Flow Characteristic in High-fluxCirculating Fluidized Bed RiserWANG Xiao-fang, JIN Bao-sheng, ZHONG Wen-qi(School of Energy and Environment, Southeast University, Nanjing 210096, Jiangsu Provice, China)ABSTRACT: The gas-solid flow characteristics under high-flux and high superficial gas velocity were investigated with the experimental data of pressure gradients of gas-solid two-phase flow in high-flux CFB riser with diameter of 60mm and height of 5000mm. Geldart group B particles with mean diameter of 140μm and density of 2700kg/m3 were used as bed materials. It was found that the apparent solids holdups decrease with the increase of axial height of riser, and it decreased with increasing superficial gas velocity. The increase of solids mass flux results in the upward extend of dense suspension upflow (DSU) structure. There were significant correlations between the dimensionless apparent slip velocity, apparent solids holdup and slip factor. The riser total pressure drop and apparent solids holdup increase with the solids-to-air mass flow ratio, and there is greater effect of solids-to-air mass flow ratio on apparent solids holdups in lower part of riser.KEY WORDS: circulating fluidized bed; high-flux; riser; gas-solid two-phase flow摘要:以直径0.06m、高5m的高通量循环床提升管中气固两相流大量试验数据为基础,考察在高颗粒循环量和较高气体表观流速下,平均粒径为140μm、密度为2700kg/m3的Geldart B 类颗粒气固流动特性。
试验发现,截面平均颗粒浓度分布总体上为下浓上稀,并随操作气速的增大而减小,悬浮上升流动结构区域随着颗粒循环速率的增大而向上延伸。
滑移因子、截面平均颗粒浓度与无量纲滑移速度之间存在显著相关性。
此外,床层总压降和截面平均颗粒浓度随固气质量比的增加而增加,在上升管下部截面平均颗粒浓度受基金项目:国家高技术研究发展计划(863计划)(2006AA05A103);国家自然科学基金项目(50706007);江苏省高等学校研究生创新计划(CX08B-060Z);东南大学优秀博士论文基金。
The National High Technology Research and Development of China(863 Programme)(2006AA05A103); Project Supported by National Natural Science Foundation of China(50706007).固气质量比的影响比上部大。
关键词:循环流化床;高通量;上升管;气固两相流0 引言循环流化床由于其高效、低污染的优点,在煤燃烧和气化、生物质资源化利用、固体废弃物处理等方面已经得到广泛的应用[1-5]。
近年来,高通量循环流化床也在能源和化工领域受到重视,如催化裂化[6]、煤的燃烧[7]和气化[8]。
基于整体煤气化联合循环(integrated gasification combined cycle,IGCC)的发展要求,美国近年提出了运行于输运状态的高通量循环流化床气化工艺,目前已经完成煤处理量为48t/d的中试规模研究,计划于2010年进行空气气化285MW IGCC的商业示范[9]。
在我国,“十一五”国家863计划先进能源技术领域“以煤气化为基础的多联产示范工程”重大项目中提出了采用高通量循环流化床的加压密相输运床煤气化技术路线。
与常规的循环流化床相比,高通量循环流化床具有更高的颗粒循环速率(固体通量G s>200kg/ (m2⋅s)),更大的表观速度和提升管颗粒浓度,以及相对较小的Geldart B类颗粒,有利于进一步增强反应器内的气固混合接触,促进流体和颗粒之间的传热、传质,从而有效提高反应效率并减少污染物的排放。
良好的气固流动是组织和实现反应器内高效传热传质和化学反应的关键。
国内外研究者[10-13]对高通量循环流化床的气固流动进行了较深入研究,得到了许多有价值的结论。
然而,这些研究都大多是以催化裂化为背景,以Geldart A类颗粒为对象的,迄今为止极少有针对采用Geldart B类颗粒高通量循环流化床的研究报道。
尽管在Geldart B28 中国电机工程学报第29卷类颗粒高通量循环流化床气化上,南方公司已经取得了重要进展,但尚未有公开发表其基础研究数据;而我国该研究刚起步。
本文建立了高通量循环流化床气化炉的冷态试验装置,采用平均粒径为140μm、密度为2700kg/m3的 Geldart B类颗粒,在气体表观流速U g为7.6~10.2m/s的条件下,进行固体通量G s为108~395kg/(m2⋅s)的气固流动特性的试验研究。
重点考察上升管的截面平均颗粒浓度、气固的表观滑移速度、固气质量比等参数随固体通量和气体表观流速的变化规律,获得基础数据,为高通量循环流化床气化炉的结构设计、运行和优化提供参考。
1 试验系统高通量循环流化床冷态实验系统如图1所示。
系统主要包括有机玻璃上升管(直径0.06m,高5m),两段有机玻璃下降管(直径0.04m,高3.5m 和直径0.1m,高3m),惯性分离器,旋风分离器,布袋除尘器及2个返料阀。
来自罗茨风机的空气经由布风板引入上升管,将颗粒流化后,气体携带颗粒进入惯性分离器,在此大部分固体颗粒被分离,经第2级返料装置送回主床,少数未被分离的细颗粒随气体进入旋风分离器,经过再次气固分离,气20191817SSSSSSSS7S81—上升管;2—下降管1;3—惯性分离器;4—下降管2;5—旋风分离器;6—一级返料器;7—二级返料器;8—布袋除尘器;9—蝶阀1;10—蝶阀2;11—加料仓;12—罗茨风机;13—转子流量计;14—气室;15—风室;16—测压孔;17—差压传感器;18—差压变送器;19—A/D转换器;20—数据采集计算机。
图1试验系统图Fig. 1 Schematic diagram of experimental system体经布袋除尘器排入大气,颗粒经第2级返料装置送回主床形成循环,在布袋除尘器中积累的细颗粒也定期送入上升管进行循环。
系统运行稳定后,颗粒循环速率通过安装在下降管上的蝶阀测量。
蝶阀的碟片上钻有小孔并覆以筛网以减小阀门关闭时对系统压力分布的影响并保证没有固体颗粒通过阀门。
在测量时迅速关闭阀门,然后测量阀门下颗粒的减少速度从而得到固体颗粒的通量。
截面平均颗粒浓度通过两个截面间静压差Δp获得。
根据相关试验研究[11,14-15],在与颗粒静压头相比,颗粒加速度及与壁面的摩擦力可以忽略的情况下,可以认为p s g s/[(1)]p z gρερεΔΔ≈+−(1)式中:Δp为床内两点间的压差;Δz为两点间距离;ρp、ρg分别为颗粒、气体密度;εs为截面平均颗粒浓度;g为重力加速度。
在上升管壁面,沿床高开有测压孔,用来测量截面间静压差,试验中测得的差压信号被送入多通道差压变送器,输出信号经A/D转换后,由计算机采集。
试验物料为石英砂,密度ρp=2700kg/m3,平均粒径d p=140μm。
实验中采用的表观气速u g=7.6~10.2m/s,颗粒循环速率G s为108~395kg/(m2⋅s)。
2 试验结果与讨论2.1 颗粒浓度颗粒浓度是高通量、高密度循环流化床的关键特征参数[16-17]。
图2为表观气速为7.6m/s时颗粒循环速率对截面平均颗粒浓度轴向分布的影响。
由图可见,颗粒浓度沿轴向呈上稀下浓分布,并在很大程度上受到颗粒循环速率的影响。
在接近上升管顶部区域,由于T型出口结构导致颗粒浓度有一定程度的增加。
正如已有的研究表明[10,18],对于T型等强约束类出口结构,当气速较高时,颗粒在巨大的12345高度z/mεs图2截面平均颗粒浓度的轴向分布Fig. 2 Axial profiles of apparent solids holdups along theriser column第17期 王小芳等: 高通量循环流化床上升管气固流动特性实验研究 29惯性作用下冲向上升管顶部。
运动受阻后,颗粒折流向下,部分颗粒沿床壁向下运动,并逐渐与气固主体运动相融合,颗粒浓度增加。
此外,在一定操作气速下,随着颗粒循环速率的提高,床层各截面上平均颗粒浓度都逐渐增加。
如图所示,当颗粒循环速率大于200 kg/(m 2⋅s),在上升管中下部的截面平均颗粒浓度大于10%,但是在上部仍小于10%。