MULTIPLE HEAT STRAIGHTENING REPAIRS OF STEEL BEAM BRIDGES
清洁工我爱你作文英语

清洁工我爱你作文英语As a Cleaner, I Love You。
As a cleaner, I love you. These are the words that I want to say to all the cleaners in the world. We may not have the most glamorous job, but we play a crucial role in keeping our surroundings clean and hygienic. Our hard work often goes unnoticed, but we take pride in what we do and the difference we make.Every day, we wake up early and head to work, armed with our cleaning supplies and a strong work ethic. We scrub, mop, dust, and vacuum, ensuring that every nook and cranny is spotless. We clean offices, schools, hospitals, and public spaces, making sure that they are safe and inviting for everyone who enters.We face many challenges in our line of work. Sometimes, we encounter stubborn stains that refuse to budge, or we have to clean up after a big event where the mess seemsnever-ending. We have to deal with unpleasant odors and hazardous materials, all while maintaining a positive attitude and a professional demeanor.Despite the difficulties, we continue to workdiligently because we understand the importance of our job. Cleanliness is essential for preventing the spread of diseases and maintaining a pleasant environment. We take pride in knowing that our hard work contributes to thewell-being of others.In addition to our cleaning duties, we also serve as the eyes and ears of the places we clean. We notice when something is amiss or when repairs are needed, and wereport these issues to the appropriate authorities. We take on this responsibility because we care about the places we work in and the people who use them.We often go above and beyond our job description, taking the time to add personal touches to our cleaning. Whether it's arranging flowers in a vase or straightening up a messy desk, we strive to make the spaces we clean moreinviting and comfortable. We do this because we genuinely care about the well-being of others.Despite the challenges and the lack of recognition, we continue to show up for work each day with a smile on our faces. We take pride in our work and find fulfillment in knowing that we are making a difference. We may not receive praise or accolades, but we know that our efforts are appreciated by those who benefit from our hard work.So, to all the cleaners out there, I want to say: I love you. I appreciate the hard work that you do, and I know that it often goes unnoticed. But please know that your efforts are valued, and you are making a positive impact on the world. Keep up the good work, and neverforget the difference that you are making. Thank you forall that you do.。
A Wing and a Prafer折翼的蜜蜂
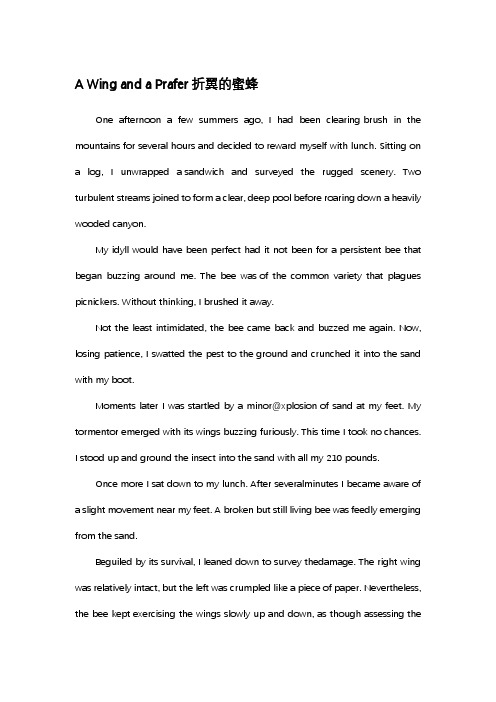
A Wing and a Prafer折翼的蜜蜂One afternoon a few summers ago, I had been clearing brush in the mountains for several hours and decided to reward myself with lunch. Sitting on a log, I unwrapped a sandwich and surveyed the rugged scenery. Two turbulent streams joined to form a clear, deep pool before roaring down a heavily wooded canyon.My idyll would have been perfect had it not been for a persistent bee that began buzzing around me. The bee was of the common variety that plagues picnickers. Without thinking, I brushed it away.Not the least intimidated, the bee came back and buzzed me again. Now, losing patience, I swatted the pest to the ground and crunched it into the sand with my boot.********************************************************** tormentor emerged with its wings buzzing furiously. This time I took no chances.I stood up and ground the insect into the sand with all my 210 pounds.Once more I sat down to my lunch. After severalminutes I became aware of a slight movement near my feet. A broken but still living bee was feedly emerging from the sand.Beguiled by its survival, I leaned down to survey thedamage. The right wing was relatively intact, but the left was crumpled like a piece of paper. Nevertheless, the bee kept exercising the wings slowly up and down, as though assessing thedamage. It also began to g room its sand-encrusted thorax and abdomen.Next the bee turned its attention to the bent left wing,rapidly smoothing the wing by running its legs down the length. After each straightening session, the bee buzzed its wings as if to test the lift. This hopeless cripple thought it could still fly!I got down on my hands and knees to better see thesefutile attempts. Closer scrutin y confirmed the bee was finished—it must be finished. As a veteran pilot, I knew a good deal about wings.But the bee paid no attention to my superior wisdom. Itseemed to be gaining strength and increasing the tempo of its repairs. The bent veins that stiffened the gossamer wing were nearly straight now.At last the bee felt sufficiently confident to attempt atrial flight. With an audible buzz it released its grip on the earth—and flew into a rise in the sand not more than three incheas away. The little cr eature hit so hard that it tumbled. More frantic smoothing and flexing followed.Again the bee lifted off, this time flying six inchesbefore hitting another mound. Apparently the bee had regained the lift in its wings but had not mastered the directional controls. Like a pilot learning the peculiarities of a strange airplane, it experimented with short hops that ended ignominiously After each crash the bee worked furiously to correct the newly discovered structural deficiencies.Once more it took off, this time clearing the sand butheading straight toward a stump. Narrowly avoiding it, the bee rechecked its forward speed, circled andthen drifted slowly over the mirrorlike surface of the pool as if to admire its own reflection. As the bee disappeared, I realized that I was still on my knees, and I remained on my knees for some time.几年前的一个下午,我在山上开垦荒地,接连干了几个小时。
HONDA 汽车综合维修指南说明书
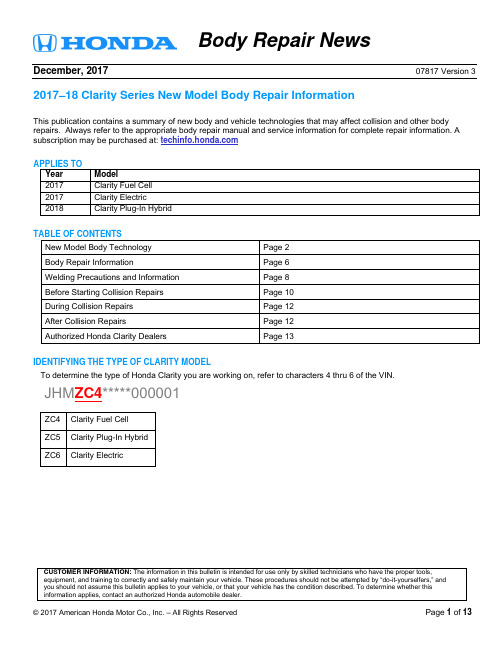
CUSTOMER INFORMATION: The information in this bulletin is intended for use only by skilled technicians who have the proper tools,equipment, and training to correctly and safely maintain your vehicle. These procedures should not be attempted by “do-it-yourselfers,” and you should not assume this bulletin applies to your vehicle, or that your vehicle has the condition described. To determine whether this information applies, contact an authorized Honda automobile dealer.Body Repair NewsDecember, 201707817 Version 32017–18 Clarity Series New Model Body Repair InformationThis publication contains a summary of new body and vehicle technologies that may affect collision and other body repairs. Always refer to the appropriate body repair manual and service information for complete repair information. A subscription may be purchased at: APPLIES TO Year Model2017 Clarity Fuel Cell 2017 Clarity Electric2018Clarity Plug-In HybridTABLE OF CONTENTS New Model Body Technology Page 2 Body Repair InformationPage 6 Welding Precautions and Information Page 8 Before Starting Collision Repairs Page 10 During Collision RepairsPage 12 After Collision RepairsPage 12 Authorized Honda Clarity DealersPage 13IDENTIFYING THE TYPE OF CLARITY MODELTo determine the type of Honda Clarity you are working on, refer to characters 4 thru 6 of the VIN.JHM ZC4*****000001ZC4 Clarity Fuel Cell ZC5 Clarity Plug-In Hybrid ZC6 Clarity ElectricOVERVIEW OF BODY FEATURES• The same basic body platform supports three electric-powered model variations.• Body construction using 52% lightweight materials, including aluminum and ultra-high-strength steel (UHSS - 980 MPa and higher).• World’s first Glass Fiber Reinforced Polymer/Plastic (GFRP) rear bumper beam.• Bolt-on resin composite front bulkhead assembly.• All models are equipped with Honda Sensing®, which includes these advanced safety and driver-assistive technologies: Adaptive Cruise Control with Low Speed Follow, Lane Keeping Assist System, Road Departure Mitigation, and Collision Mitigation Braking System™ with pedestrian sensing capability.WARNING• Compressed hydrogen gas is flammable and highly explosive. You could be killed or seriously injured if leaking hydrogen gas is ignited.• Keep heat, sparks, and flames away. In addition, keep electronic devices that can emit static discharge away.• Hydrogen burns very quickly and radiates less heat than gasoline or other fuels; its flames are invisible.• Always, have a fire extinguisher (dry powder type or carbon dioxide gas type) at the work location at all times.• Only properly trained technicians should inspect and repair the Clarity’s high-voltage and/or hydrogensupply systems.• The California Fire Code has specific requirements for welding and open flame repairs on hydrogenfueled vehicles like the Clarity Fuel Cell. Do not conduct welding or open flame repairs on the ClarityFuel Cell without first determining whether your facility is properly equipped and the vehicle is properlyprepared.NEW MODEL BODY TECHNOLOGYBody Construction and High-Strength Steel Content• Steel parts are color coded based on their tensile strength in megapascals (MPa).• High-strength steel (HSS) is defined as any steel with a tensile strength of 340 MPa or higher.• Ultra-high-strength steel (UHSS) is defined as any steel with a tensile strength of 980 MPa or higher.• Steel repair and welding procedures vary, depending on the tensile strength of the parts involved.NOTE: The following illustrations are for general reference only. Some body parts are made from multiple layers of different tensile strength steels. Refer to the Body Construction section of the body repair manual for specific steel tensile strengths.1500 MPa 980MPa780MPa270MPa440MPa1.500 MPa (Hot Stamp) Steel Locations1,500 MPa steel is stronger than ordinary steel, so it can help protect vehicle occupants while reducing overall vehicle weight to improve fuel efficiency.The numbered parts in the illustration below are made of 1,500 MPa steel.1 Front Inner Upper Panel 5 Side Sill Reinforcement2 Front Pillar Upper Stiffener 6 Center Pillar Upper Stiffener3 Front Side Frame Extension 7 Roof Side Stiffener4 Front Pillar Lower Stiffener 8 Floor Crossmember StiffenerNote: 1,500 MPa Stiffeners are located inside the front floor frame, front floor crossmember, and front floor rear crossmember.Resin Composite (Plastic) Front Bulkhead AssemblyThe Clarity has a front bulkhead assembly made from resin composite material.• The bulkhead design improves engine compartment access during factory assembly and service.• The front bulkhead is attached with multiple bolts and is sold and replaced only as a complete assembly.• The cooling fans, radiator, A/C condenser, hood lock, outside air temperature sensor, and related piping/components are attached to the front bulkhead using molded-in M6/M8 threaded inserts.• Over torqueing or using power tools may break these inserts loose, requiring front bulkhead replacement.• A damaged bulkhead must be replaced, not repaired.• For more information, refer to “Front Bulkhead Replacement” in the body repair manual.Aluminum Parts and ReparabilityThe following parts are made from aluminum alloy:Front Bumper Beam Rear Shelf PanelsHood Panel Trunk LidFront Fenders Front and Rear Subframe (Not shown)Front and Rear DoorsAluminumLaser-Brazed Roof AttachmentThe factory-installed roof panel is attached using a laser-brazed joint to the outer side panels.•Laser-brazed joints cannot be duplicated during roof panel replacement.•The original roof panel must be cut off near the laser-brazed joint and the remaining flange removed separately. •The service roof panel is attached using service replacement bolted clamp-type brackets (five per side) and panel bonding adhesive.•The roof panel, service brackets, and bolts must be ordered separately. Refer to the online parts catalog.•Refer to “Roof Panel Replacement” in the body repair manual.BODY REPAIR INFORMATIONNOTE: The following content is intended only to highlight new/special concerns. No body repairs should be attempted without first referencing the applicable body repair manual.Use of Heat During Body Straightening and RepairWhen you are doing body straightening and repair procedures, follow these guidelines:• Do not apply heat to any body part during straightening. This may compromise the internal structure and strength of high-strength steel parts.• Any part that has heat applied to it during straightening must be replaced with new parts.• Ignoring these instructions may significantly reduce occupant protection in any subsequent collision.Sectioning (Cut and Joint) GuidelinesVarious high-strength and ultra-high-strength steel materials with different sheet thicknesses and strengths are applied in many places that vary with body design in order to increase collision safety performance, body stiffness, and weight reduction. Stiffening members are also applied inside some steel parts (patches, reinforcements, stiffeners, etc.)Follow these guidelines to avoid an unsafe repair:• Outer body and floor panels may be sectioned as necessary. Specific sectioning procedures are not provided in the body repair manual.• Depending on the type of vehicle damage, steel parts with a tensile strength of 780 MPa or less may be sectioned, as long as all three of the following conditions are met:- Sectioning must be done in a single-layer area of the part.- Multi-layer internal steel reinforcements and stiffeners must not be cut.- Sectioning must be done in load bearing areas such as engine, transmission, or suspension mounting points.• If any of the above sectioning conditions cannot be met, replace those body structural components (stiffeners, reinforcements, and other multi-layered steel parts) as assemblies that match the replacement parts configuration. • Approved welding methods are shown in the table at below. • Refer to the body repair manual for complete procedures.• MAG plug welding is now allowed on 1,500 MPa (hot stamp) steel parts in select locations only as specified in the body repair manual.Welding Method for Steel PartsΟ= Approved X = Not Approved Ο* = Approved only if specified in BRMSteep Part TensileStrength Welding MethodSpot WeldingMAG WeldPlug ButtSectioning Area Examples<590 ΟΟΟ590 ΟΟΟ780 ΟΟΟ980 ΟΟX1,500 ΟΟ*X• Welding instructions must be followed exactly as specified to ensure adequate weld strength.WELDING PRECAUTIONS AND INFORMATIONREPAIRING 1,500 MPa STEEL PARTSObserve these precautions when repairing 1,500 MPa steel parts:• Never attempt to straighten damaged 1,500 MPa steel parts; they may crack.• 1,500 MPa steel parts must be replaced at factory seams using only approved repair methods. Do not section these parts.• MIG-brazed joints should be used only in locations not accessible by a spot welder.• To ensure adequate weld tensile strength, always manually set the spot welder to the specifications provided in the body repair manual.• Unapproved MAG welding procedures on 1,500 MPa steel may generate heat levels that will significantly reduce the strength and structural integrity of 1,500 MPa steel parts.• The photo below shows a tensile strength test results of an improperly MAG welded 1,500 MPa steel part. The 1,500 MPa side fractured first because excessive welding heat reduced its strength.• For more details, refer to “Basic Welding Information” the Body section of the service information.Parts made of Ultra-High-Strength Steel (UHSS/1,500MPa/USIBOR) must be installed as a complete part. No sectioning is allowed. Ultra-High-Strength Steel requires special welding equipment, procedures, and settings. See the welding section of the body repair manual. Failure to use the proper equipment or follow the proper procedures can result in an unsafe repair.MIG Brazing Guidelines for 1,500 MPa Steel PartsNOTE: Refer to the body repair manual for complete procedures.• MIG-brazed joint locations are specified in the body repair manual.• A single- or double-hole MIG braze may be specified, depending on the tensile strength of the parts being joined. • The size and number of holes are critical to achieving adequate joint strength.• A MIG welder with pulse control must be used. Refer to the equipment manufacturer’s instructions for welder voltage and current setup.• The photos below show the difference in results between pulsed and non-pulsed MIG brazing.MAG Welding Specifications for 590–980 MPa High-Strength Steel PartsNOTE: In this publication and the body repair manual, gas metal arc welding (GMAW) is referred to by its subtypes depending on requirements as follows:• MIG Welding/Brazing = This refers to metal inert gas welding or brazing where 100% argon (Ar) shielding gas is used. Argon is inert and does not react with the molten weld pool or brazing operation.• MAG Welding = This refers to metal active gas welding where the shielding gas being used contains a mixture of 80% argon (Ar) and 20% carbon dioxide (CO 2). It is considered active because the CO 2 undergoes a limited reaction with the molten weld pool.• For MAG welding, 80/20 shielding gas (C20) is preferred. However, 75/25 (C25) is acceptableParts made of high-strength steel (590-980 MPa) must often be installed as a complete part. Section only according to published repair information and guidelines. This high-strength steel requires special weldingequipment, procedures, and settings. See the Welding section of the body repair manual. Failure to use the proper equipment or follow the proper procedures can result in an unsafe repair.The body repair manual specifies the weld types and locations for each body panel as follows:• The welding wire used must have a tensile strength equal to or greater than the lowest tensile strength of the parts being welded. The conversion chart below shows the relationship of steel tensile strength (MPa) to the minimum welding wire tensile strength (in kilopound per square inch [ksi]).Steel Tensile (MPa) Wire Tensile (ksi)590 ≥86 780 ≥113 980 ≥142(1,000 psi = 1 ksi)• Typical ER70S-6 MIG wire has a minimum tensile strength of 70 ksi (483 MPa). It can be used when welding up to 440 MPa steel parts. Refer to the diagrams below:MAG Plug Welding Guidelines• MAG plug welding may be done when joining body components to 590–980 MPa steel parts.• MAG plug may also be used on 1,500 MPa steel parts only as specified in the body repair manual.• Follow the recommendations described in the body repair manual.MAG Butt Welding Guidelines• MAG butt welding may be done only on steel parts with a tensile strength of 780 MPa and lower.• Welding speed is critical to achieve the correct weld strength and minimize the heat affected zone (HAZ).• Follow the recommendations described in the body repair manual.BEFORE STARTING COLLISION REPAIRSWith any collision repairs, always refer to and follow the information outlined in the Generation Information section of the body repair manual. The following information outlines special consideration when repairing a Honda Clarity.IPU (Intelligent Power Unit) Leak Test After Airbag DeploymentApplies ToClarity Electric Clarity Plug-In HybridAn IPU leak test must be done on any Clarity Electric or Clarity Plug-In Hybrid involved in a collision severe enough to deploy the airbags. The test consist of pressurizing the IPU with shop air to check for any leaks. If the IPU does not pass leak check, it must be replaced.The Clarity Electric has a front and rear IPUs. Both of these units must be checked. If you have a vehicle with deployed airbags, take it to an authorized Honda dealer to have this test done before starting any repairs.High-Voltage System ComponentsApplies ToClarity Electric Clarity Plug-In Hybrid Clarity Fuel CellIf you are doing any repairs that require the removal of high-voltage system components, the vehicle must be taken to an authorized Honda dealer. Authorized Honda dealers have the training and equipment needed to remove and install high-voltage components.Refer to the Electrical Powertrain Component Location Index in the service information for a complete list of high-voltage system components.Hydrogen System/Fuel Cell System ComponentsApplies ToClarity Fuel CellAccording to California Fire Code, the hydrogen level in the hydrogen tanks must be less than 0.5 kg before the vehicle is brought inside the shop for repairs related to the hydrogen system. These rules do not apply for servicing/repair of non-hydrogen system components and collision repairs as long as no repairs involving welding or open flame are done and the hydrogen system components are not involved.If you are doing any repairs that involve any hydrogen system or fuel cell system related components or involve welding or open flame, the vehicle must be taken to an authorized Honda Clarity Fuel Cell dealer. For a list of authorized Honda dealers, for a list of authorized Honda dealers, refer to page 12.Refer to the Fuel Cell System Component Location Index in the service information for a complete list of hydrogen/fuel cell system components.DURING COLLISION REPAIRSWith any collision repairs, always refer to and follow the information outlined in the General Information section of the body repair manual. The following information outlines special consideration when repairing a Honda Clarity. Precautions When Using a Heated Paint BoothSystem PrecautionsSRS • Do not apply heat greater than 212°F (100°C) when drying painted surfaces anywherearound the SRS components.Fuel Cell • When drying paint in a heated paint booth, cover the air intake duct, exhaust pipe, andventilation ducts with a tape. Refer to the Fuel Cell System Component Location Indexin the service information for the location of these components.• High temperature may damage the fuel cell (FC) stack and the compressed hydrogengas (CHG) tank. When drying paint in a heated paint booth, make sure thetemperature does not exceed 149°F (65°C).Electric Powertrain • High temperature may damage the battery module. When drying paint in a heatedpaint booth, make sure the temperature does not exceed 149°F (65°C).AFTER COLLISION REPAIRSCollision Shut-off History Clear CommandWhen the battery condition monitor module receives a collision detection signal (CDS) from the SRS unit or the H2 (hydrogen) shut-off unit (Clarity Fuel Cell only), it updates the collision shut-off history and stores it in the module’s nonvolatile memory. The battery condition monitor module stops supplying power to the high-voltage circuits disrupting the control signal to be sent to the high-voltage contactor inside the battery module the next time the system is being turned on.The battery condition monitor module also stops supplying hydrogen to the FC stack by turning the FC cut relay at the same time. To resume power supply to the high-voltage circuits and hydrogen supply to the FC stack, the collision shut-off history must be cleared.Aiming Driving Support SystemsThe Honda Clarity is equipped with advanced safety driving support systems to help warn drivers and mitigate hazards. It is very important that the components making up this system are properly amied after a collision repair.Use the following table to determine what component requires aiming.Component When to AimMultipurpose Camera • Whenever the multipurpose camera unit is removed or replacedMillimeter Wave Radar • Whenever the millimeter wave radar unit is removed or replaced• After any front-end collision repairsLaneWatch™ Camera • Whenever the LaneWatch™ camera, right-side power mirror or right-front door isremoved or replaced• Whenever the right-front door is adjusted• Whenever the right-front door is repairedIf aiming is required, take the vehicle to an authorized Honda dealer.AUTHORIZED HONDA CLARITY DEALERSThe Clarity Electric and Clarity Plug-In Hybrid can be taken to any Honda dealer for service and repairs. To locate an authorized Honda dealer, contact Honda Customer Service at (800) 999-1009. Repairs to the Clarity Fuel Cell only should be undertaken by Authorized Clarity Fuel Cell dealers.For a list of authorized Honda Clarity Fuel Cell dealers, see below:Authorized Honda Clarity Fuel Cell DealersCity Dealer Name Telephone NumberCerritos, CA Norm Reeves Honda Superstore(888) 849-4466Culver City, CA Culver City Honda(424) 298-4875Irvine, CA Norm Reeves Honda Superstore Irvine(888) 721-4053Pasadena, CA Honda of Pasadena(866) 788-5832Torrance, CA Scott Robinson Honda(855) 725-2211Woodland Hills, CA Woodland Hills Honda(800) 494-1164City Dealer Name Telephone NumberColma, CA Honda of Serramonte (888) 892-5396Dublin, CA Dublin Honda (877) 412-7199Oakland, CA Honda of Oakland (800) 352-1859Palo Alto, CA Anderson Honda (650) 843-6041Roseville, CA AutoNation Honda Roseville (916) 467-8056San Jose, CA Honda of Stevens Creek (855) 357-6146END。
热处理专业术语中英文对照
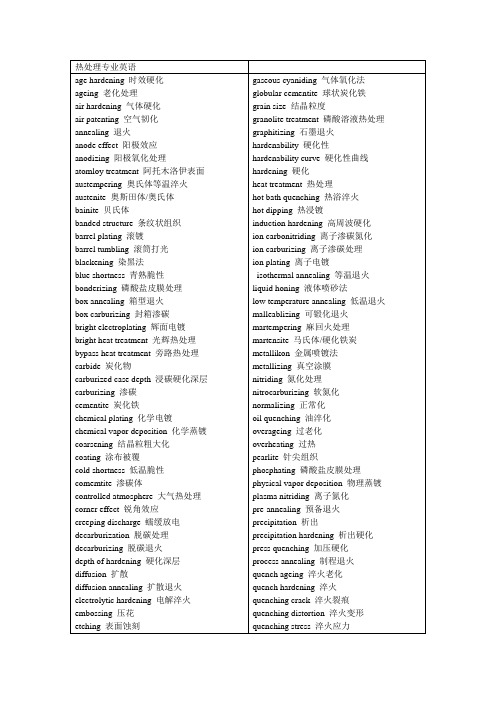
pearlite针尖组织
phosphating磷酸盐皮膜处理
physical vapor deposition物理蒸镀
plasma nitriding离子氮化
pre-annealing预备退火
precipitation析出
precipitation hardening析出硬化
press quenching加压硬化
process annealing制程退火
quench ageing淬火老化
quench hardening淬火
quenching crack淬火裂痕
quenching distortion淬火变形
quenching stress淬火应力
reconditioning再调质
95. inclusion夹杂物
96. segregation偏析
97. picking酸洗,酸浸
98. residual stress残余应力
99。remaining stress残余应力
100. relaxation of residual stress消除残余应力
101. stress relief应力释放
decarburization脱碳处理
decarburizing脱碳退火
depth of hardening硬化深层
diffusion扩散
diffusion annealing扩散退火
electrolytic hardening电解淬火
embossing压花
etching表面蚀刻
ferrite肥粒铁
80。drawing拉(件)
81。shot blasting喷丸(处理)
2017年Honda Canada公司版Acura NSX说明书

MODEL/YEAR MODÈLE /ANNÉEDATE OF ISSUE DATE EN VIGUEUR LETTER NUMBER NUMÉRO DE LA LETTRE2017 NSXJUNE 5, 2017J-1-172017 NSX: BODY REPAIR INFORMATIONINTRODUCTIONThe second generation Acura NSX utilizes a multi-material body structure, new materials and construction methods to achieve unprecedented dynamic rigidity, outstanding outward visibility and world-class collision performance. Making use of space-frame design, the new NSX is composed primarily of lightweight aluminum, with the strategic use of steel and carbon fiber in select areas. Because of this advanced body technology, complete and proper repair of any collision or body damage is critical. Should body and/or structural repairs become necessary, Acura recommends a unique two levels collision repair process (structural repairs and non-structural repairs) for the NSX described in this service letter.OVERVIEW OF BODY STRUCTURE1. The main NSX structure consists of an aluminum space frame that is primarily MIG weldedaluminum extrusions, joined at castings which act as nodes to link the extrusions 2. Additional structural components and sheet metal is held in place using Flow drill screws, (FDS)Self piercing rivets (SPR) bolts and traditional pop rivets.NSX Multi-Material Space FrameBody Repair NewsBODY STRUCTURE REPAIR CHALLENGESAluminium welding and space frame repair requires a very high investment in tools, materials and training to ensure the repair is done properly and safely. Some of the concerns with aluminium welding include:1. Risk of fire, explosion, fumes and other safety related concerns.• Mixing of fine aluminum dust with Iron oxide powder could result in a thermite explosion in the presence of a spark.• Mixing fine aluminum powder with water can create hydrogen gas which can lead to fire or explosion hazard.• Welding Fumes and UV hazards• A separate aluminum repair room, specialized dedicated repair tools, dust extraction equipment, fume extraction equipment, respirators. Welding mask, specialty fireextinguishers and other specific safety protocols need to be followed.2. Reliable aluminium Weld quality• Aluminium welding is generally more challenging than steel. The NSX repair involves joining differing wall thicknesses of material in the up down flat and overhead positions. Extremelyspecialized welding equipment and an expert level aluminum welding technician is neededto ensure the integrity of the repair. For NSX a costly ISO 9606-2 aluminium weldingcertification - (not common in the auto repair industry) was the minimum skill requirementneeded to proceed with further training on this vehicle.3. Corrosion• Galvanic corrosion will occur if uncoated steel comes in contact aluminium. The aluminium will preferentially corrode leaving black pitting or a white ash like coating or flaking/damageto any paint on the contaminated surface. Dedicated aluminium tools and rooms arerequired to prevent cross contamination of steel particles on aluminium body.4. Specialized equipment:• A high end compatible frame bench (Celette or Car-o-liner) and costly NSX specific jigs are needed to fixture the body prior to welding and reduce post weld distortion • Computerized measurement equipment from Celette or Car-o-liner) is required to assess damage areas needing repair and to confirm repair quality.5. Replace vs straightening:• No structural components on the NSX can be straightened sectioned or sleeved without affecting the strength or crash worthiness of the structure. Structural repairs are to beperformed by replacing the affected prefabricated assembly.• Specialized training repair methods and hands on skill• NSX certified structural repair technicians have received specialized repair information and have demonstrated their skill on NSX bodies to obtain an NSX specific repair certification For these reasons, only body shops already experienced in aluminium space frame repair with the necessary training and equipment were considered for certification as NSX structural repair centerNSX repairs can be divided into 2 different levels Structural Repairs and Non-Structural Repairs.STRUCTURAL REPAIRSDue to the high welding skill, specialized training, and specialized equipment required, structural repairs to NSX are limited to 2 body shops across Canada which have met the equipment, training, and skills requirements for NSX structural repair. To ensure repair quality structural replacement, parts will not be released from Acura to any other repair facility.The auto body centers are:427 Auto Collision Ltd Open Road Richmond Auto body 395 Evans Ave, Toronto, ON M8Z 1K8 2691 No 5 Road Richmond B.C. Canada V6X 2X8 Servicing MB, ON, PQ, NB, NS,NL,PEI Servicing BC,AB,SK,YK,NT,NU NON-STRUCTURAL REPAIRSThe non-structural or outer panels on NSX are a mixture of high temperature ABS plastic, Aluminum stampings, SMC (sheet molded composite) and CFRP (carbon fiber reinforced polymer) They are primarily bolted in place or held in placing using urethane adhesive.ALUMINUM PANEL REPAIRReplacement is often the preferred repair method. Repairs can be made to the aluminum sheet metal parts by shops that are aluminum certified. Many of the requirements and hazards associated with the aluminum structural repairs are still concerns if sanding or grinding aluminum panels. Aluminum repair centers have training and dedicate tools and repair areas for aluminum repair and refinishing.To prevent galvanic corrosion, most fasteners for aluminum parts are considered one-time use and must be replaced if removed. Refer to the body repair manual for more information. In addition, specialized tools and dedicated repair areas must be used to prevent steel contamination leading to corrosion.SMC REPAIRSMC is a fiber-reinforced plastic, or FRP, which are also called composites. FRP parts are usually considered a rigid part. These types of plastic have fiber strands that are inlaid into a plastic polymer to create the rigid part. Except for light scratches in the outer layer, SMC parts on the NSX are not repairable.CFRP REPAIROnly surface scratches should be repaired on CFRP parts. If the scratch is deep enough where it has reached the fibers, the part needs to be replaced. In addition to the carbon fiber floor pan shown above, A CFRP roof, engine cover, spoilers and diffuser are also available on NSX.DISTINGUISHING BETWEEN STRUCTURAL REPAIRS AND OUTER PANEL REPAIR • If the part has exclusively use of bolts or urethane adhesive, it is not considered a “structural repair”.• If the part is welded or put in place by a special tool such as flow drill screws or self-piercing rivets, it is considered a structural repair. The repair should be performed by the authorizedstructural repair center.WHAT TO DO IF AN NSX SUSTAINS BODY OR COLLISION DAMAGEIf your dealership becomes aware of an NSX client whose vehicle has sustained collision or body damage, please follow these steps:• Confirm the safety and health of the driver and passengers• Arrange for alternate transportation if necessary• Have the vehicle towed to the closest NSX dealer via Roadside Assistance to begin the repair processNSX BODY REPAIR PROCESS FLOWCHARTThe chart below outlines the process to repair body or collision damage to a next-generation NSX.NOTE: Due to the complexity and uniqueness of andaro paint (Nouvelle Blue Pearl and Valencia Red Pearl), it is difficult to find the match paint without extensive tests. For body repair using andaro paints, Acura strongly recommends to use PPG. Contact Techline for help to locate a body shop that uses PPG paint.。
材料科学与工程专业英语课后习题答案unit1-7
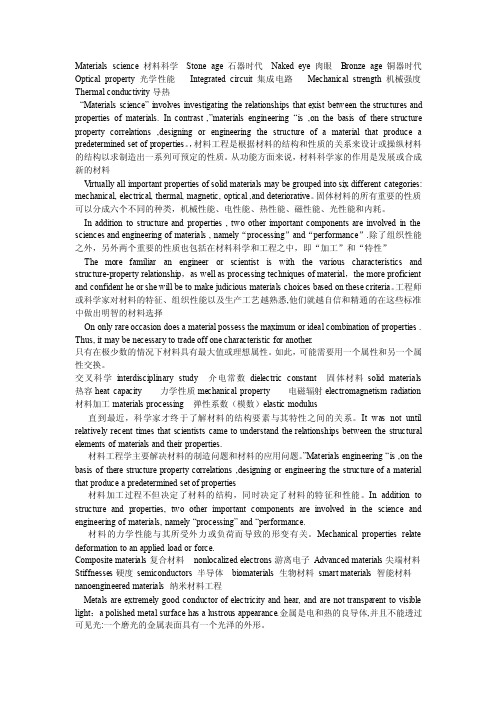
Materials science材料科学Stone age石器时代Naked eye肉眼Bronze age铜器时代Optical property光学性能Integrated circuit集成电路Mechanical strength机械强度Thermal conductivity导热“Materials science” involves investigating the relationships that exist between the structures and properties of materials. In contrast ,”materials engineering “is ,on the basis of there structure property correlations ,designing or engineering the structure of a material that produce a predetermined set of properties。
,材料工程是根据材料的结构和性质的关系来设计或操纵材料的结构以求制造出一系列可预定的性质。
从功能方面来说,材料科学家的作用是发展或合成新的材料V irtually all important properties of solid materials may be grouped into six different categories: mechanical, electrical, thermal, magnetic, optical ,and deteriorative。
固体材料的所有重要的性质可以分成六个不同的种类,机械性能、电性能、热性能、磁性能、光性能和内耗。
In addition to structure and properties , two other important components are involved in the sciences and engineering of materials , namely“processing”and“performance”.除了组织性能之外,另外两个重要的性质也包括在材料科学和工程之中,即“加工”和“特性”The more familiar an engineer or scientist is with the various characteristics and structure-property relationship,as well as processing techniques of material,the more proficient and confident he or she will be to make judicious materials choices based on these criteria。
2015 Honda Fit 新型车身维修信息说明书
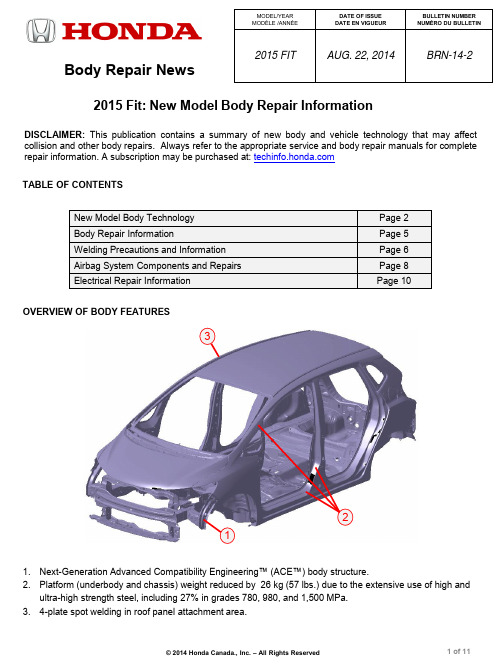
OVERVIEW OF BODY FEATURES1.Next-Generation Advanced Compatibility Engineering™ (ACE™) body structure.2.Platform (underbody and chassis) weight reduced by 26 kg (57 lbs.) due to the extensive use of high andultra-high strength steel, including 27% in grades 780, 980, and 1,500 MPa. 3.4-plate spot welding in roof panel attachment area.DISCLAIMER: This publication contains a summary of new body and vehicle technology that may affect collision and other body repairs. Always refer to the appropriate service and body repair manuals for complete repair information. A subscription may be purchased at: 2015 Fit: New Model Body Repair InformationTABLE OF CONTENTSNew Model Body TechnologyPage 2Body Repair InformationPage 5 Welding Precautions and Information Page 6 Airbag System Components and Repairs Page 8 Electrical Repair InformationPage 101 23 Body Repair NewsMODEL/YEAR MODÈLE /ANNÉE DATE OF ISSUE DATE EN VIGUEUR BULLETIN NUMBER NUMÉRO DU BULLETIN2015 FIT AUG. 22, 2014 BRN-14-2BODY CONSTRUCTION AND HIGH STRENGTH STEEL CONTENT•Steel parts are color-coded based on their tensile strength in mega-Pascals (MPa). •High strength steel is defined as any steel with a tensile strength of 340 MPa or higher.•Steel repair and welding procedures vary depending on the tensile strength of the parts involved.New Model Body Technology980 MPa 590 MPa440 MPa 1,500 MPa780 Mpa 270 MPa Steel Tensile Strength LegendThese illustrations are for general reference only. Some body parts are constructed from multiple layers of different tensile strength steels. Always refer to the body repair manual body construction section for specific steel tensile strength information.Important Information Lower ViewNote: 1,500 MPa Steel Reinforcement Inside Center PillarUpper View1,500 MPa (HOT STAMP) STEEL LOCATIONS1,500 MPa steel is stronger than ordinary steel, so it can help protect vehicle occupants while reducing overall vehicle weight to improve fuel efficiency.The numbered parts in the diagram below are constructed of 1,500 MPa steel:123All Fit Models1 Front Pillar Upper Stiffener2 Center Pillar Reinforcement3 Side Sill StiffenerLIFTING AND TOWING PRECAUTIONS•Flat bed towing equipment is the preferred method to transport this vehicle.•Front wheel lift towing equipment may also be used to tow this vehicle.For more information, refer to “Emergency Towing” inthe owner’s manual.•Lift or jack only at the specified points to avoid damaging the vehicle.•Do not lift or tow this vehicle by its bumpers, or serious damage will result.For more information, refer to “Lift and Support Points” in the service or body repair manual.4-PLATE SPOT WELDED ROOF PANEL ATTACHMENTThe body of this vehicle is assembled using new technology that welds the entire inner framework before the pre-welded outer body panels are attached. This creates a unique 4-plate spot weld at the roof panel side flanges.•Squeeze-type resistance spot welding (STRSW) is the required repair method because one of the 4 plates is constructed of 980 and 1,500 MPa steel (depending on location).•Any squeeze-type resistance spot welder meeting the specifications published in the body repair manual can make this 4-plate spot weld.•Refer to body repair manual section “Roof Panel Removal and Installation” for complete information.Roof Panel 4-Plate Spot Weld Area(980/1,500 MPa)No Spot Welds Roof Panel Section A - ARear Wheel Arch AreaREAR WHEEL ARCH FLANGE – NO SPOT WELDSThe rear wheel arch flange uses a new narrower design that eliminates spot welds to improve appearance. •The flange is attached and sealed using adhesive (3M AUTO MIX Panel Bonding 8115, or equivalent) •Refer to body repair manual section “Rear Side Outer Panel Removal and Installation” for complete information.Body Repair InformationUSE OF HEAT DURING BODY STRAIGHTENING AND REPAIR When you are doing body straightening and repair procedures: •DO NOT apply heat to any body part during straightening. This may compromise the internal structure and strength of high-strength steel parts.•Any part that has heat applied to it during straightening MUST be replaced with new parts.•Ignoring these instructions may significantly reduce occupant protection in any subsequent collision.SECTIONING (CUT AND JOINT) GUIDELINESVarious high-strength steel materials with different sheet thicknesses and strengths are applied in many places that vary by body design in order to increase collision safety performance, body stiffness, and weight reduction.Stiffening members inside each part (patch, stiffener, etc.) are also specified in detail.Follow these guidelines to avoid an unsafe repair:•Avoid sectioning (cut and joint) except for outer panels and floor panels unless a specific procedure is provided in the body repair manual.•However, depending on the type of vehicle damage, steel parts with a tensile strength ≤ 780 MPa may be sectioned (cut and weld) under the following conditions:– Sectioning must be done in a single-layer area of the part. – Multi-layer internal steel reinforcements and stiffeners must not be cut.– The repair is not in a load bearing area such as engine, transmission, or suspension mounting points.•Replace body structural components such as stiffeners, reinforcements, and other multi-layeredsteel parts as assemblies that match the replacementparts configuration. •Approved welding methods are listed in the table.•Refer to the body repair manual for complete information.NOTE: The following content is intended only to highlight new/special concerns. No body repairs should be attempted without first referencing the appropriate body repair manual for complete information.Steel Part Tensile Strength (MPa) Welding MethodSpot Weld MAG Welding Plug Butt<590590 780 980 X 1500XXWelding Methods For Steel Parts( = Approved X = Not Approved)Sectioning Area ExamplesWelding Precautions and Information REPAIRING 1,500 MPa STEEL PARTSObserve these precautions when repairing 1,500 MPa steel parts: •NEVER attempt to straighten damaged 1,500 MPa steel parts because they may crack.•1,500 MPa steel parts MUST be replaced at factory seams using squeeze-type resistance spot welding(STRSW).•MIG brazed joints should be used ONLY in locations not accessible by a spot welder.•To assure adequate weld tensile strength, always set the spot welder to the specifications provided inthe body repair manual.Important InformationParts made of Ultra High Strength Steel(UHSS/1,500MPa/ USIBOR) and must be installed asa complete part. No sectioning allowed. Ultra HighStrength Steel requires special welding equipment,procedures and settings. See the welding section ofthe appropriate body repair manual. Failure to use theproper equipment or follow the proper procedures canresult in an unsafe repair.•NEVER perform MAG welding on 1,500 MPa steel.The heat generated during welding will significantlyreduce the strength and structural integrity of1,500 MPa steel parts.•This photo shows tensile strength test results ofwelded 1,500 MPa steel. The 1,500 MPa steel fracturedfirst, because the welding heat reduced its strength tofar below 590 MPa.•For more information, refer to “Hot Stamp (1,500 MPa) Parts Welding Specifications” in the body repair manual.MIG BRAZING GUIDELINES FOR 1,500 MPa STEEL PARTS Refer to the body repair manual for complete information:•MIG brazed joint locations are specified in the body repair manual.• A single or double hole MIG braze may be specified in the body repair manual depending on the tensilestrength of the parts being joined.•The size and number of holes is critical to achieving adequate joint strength.• A pulsed MIG welder MUST be used. Refer to the equipment manufacturer’s instructions for weldervoltage and current setup.•Photos at right show the difference in resultsbetween pulsed and non-pulsed MIG brazing.MAG WELDING SPECIFICATIONS FOR 590-980 MPa HIGH-STRENGTH STEEL PARTS NOTE: In this publication and the body repair manuals,gas metal arc welding (GMAW) is referred to by itssubtypes depending on the welding/brazingrequirements:•MIG welding/brazing = Metal inert gas welding orbrazing where 100% argon (Ar) shielding gas isused. Argon is inert and does not react with themolten weld pool or brazing operation.•MAG welding = Metal active gas welding wherethe shielding gas being used contains a mixture of80% argon (Ar) and 20% carbon dioxide (CO2).It is considered active because the CO2 undergoesa limited reaction with the molten weld pool.The body repair manual specifies the weld types and locations for each body panel:•The welding wire used must have a tensile strength equal to, or greater than, the lowest tensile strength of the parts being welded. This conversion chartshows the relationship of steel tensile strength (MPa) to the minimum welding wire tensile strength (ksi). •Refer to the diagrams shown below:Steel Tensile (MPa) Wire Tensile (ksi)590 ≥86780 ≥113980 ≥142(1,000 psi = 1 ksi) Certain parts made of High Strength Steel (590-980 MPa) must be installed as a complete part. Refer to “Parts Sectioning (Cut and Joint) Guidelines” in the body repair manual for complete information.High-strength steel requires special welding equipment, procedures, and settings. See the welding section of the appropriate body repair manual. Failure to use the proper equipment or follow the proper procedures can result in an unsafe repair.Important InformationMAG PLUG WELDING GUIDELINES•MAG plug welding may be done when joining body components to 590-980 MPa steel parts.•Follow the recommendations described in the body repair manual section “MAG Welding Conditionsfor High-Strength Steel (Except 1,500 MPa) Parts.” MAG BUTT WELDING GUIDELINES•MAG butt welding may only be done on steel parts with a tensile strength of 780 MPa and lower. •Welding speed is critical to achieve the correct weld strength and minimize the heat affected zone (HAZ). •Follow the recommendations described in the body repair manual section “MAG Welding Conditionsfor High-Strength Steel (Except 1,500 MPa) Parts.”SmartVent Side AirbagAIRBAG SYSTEM COMPONENTSThe airbag system in this vehicle includesthe following components that may deploy in a collision:1.Driver and front passenger seat belt tensioners(may deploy independently from any airbags). 2.Driver and front passenger SRS airbags. 3.Side airbags mounted in the outer driver andfront passenger seat-backs.4.Side curtain airbags mounted above the leftand right side windows under the headliner.SMARTVENT™ SIDE AIRBAGSThis vehicle is equipped with SmartVent side airbag construction: •This airbag design helps mitigate the risk of excessive airbag deployment force and risk of injury to smaller seat occupants. •Eliminates the need for the Occupant Position Detection System (OPDS ) sensor located in the front passenger’s seat-back.As with all side airbags, the following service precautions apply: •Special seat covers and/or breakaway thread are used. to ensure proper deployment path.•Damaged front seat covers should be replaced, not repaired. •Do not install non-factory seat covers, because they may alter the airbag's intended deployment path.Airbag System Components and Repairs3421AIRBAG SYSTEM INDICATORSThere are two indicators used for the airbag system:Supplemental Restraint System (SRS) IndicatorWhen you turn the vehicle to the ON mode, this indicator should come on and then turn offafter about 6 seconds.•If the SRS indicator does not go off, or does not come on at all,there is a problem with the system.•DTCs must be read and cleared using the HDS (or equivalent)scan tool. Contact a Honda dealer for assistance if necessary.•If a vehicle is sent to the dealer for airbag system repair ortroubleshooting, include a copy of the repair estimate with partnumbers and the source for any replaced airbag system parts.Passenger Airbag OFF IndicatorThe indicator comes on to alert you that the passenger’s front airbag has been turned off.•This occurs when the front passenger’s weight sensors detectabout 29 kg (65 lbs.) or less, the weight of an infant or small child,on the seat.•If the indicator comes on with no front passenger and no objectson the seat, or with an adult occupying the seat, something maybe interfering with the seat weight sensors, or there may be aproblem with the system. Contact a Honda dealer for assistanceif necessary.AIRBAG SYSTEM REPAIRS REQUIRED AFTER DEPLOYMENTTo restore proper function and allow DTCs to be cleared, the airbag system MUST be repaired as specified in the service manual. Refer to “Component Replacement/Inspection After Deployment” for complete information. •DO NOT install used, refurbished, or modified airbag system parts!•When making airbag system repairs, only use new genuine replacement parts, which are manufactured to the same standards and quality as the original parts.•To ensure the correct replacement airbag system parts are installed, provide the vehicle’s VIN when ordering parts. Compare the part numbers on the new and removed parts to make sure they match. AIRBAG SYSTEM ELECTRICAL REPAIRSExcept when doing electrical inspections that require battery power, always turn the vehicle to the OFF (LOCK) mode, disconnect the negative battery cable, then wait at least 3 minutes before starting work.•For easier identification, electrical connectors that contain onlyairbag system wiring are yellow in color.•Many harnesses that contain primarily airbag wiring are alsowrapped in yellow tape.•Airbag system wiring that runs in a common harness, such as afloor harness, is generally not marked.•NEVER attempt to modify, splice, or repair airbag system wiring.If any part of the airbag system wiring is damaged, replace theaffected wiring harness(es).NOTE: Refer to the service manual for complete restraintsystems operation, diagnostic, and repair information.REPLACEABLE HEADLIGHT BRACKETSIf any of the headlight assembly attachment brackets are broken, service replacement brackets are available as service parts.A broken headlight assembly can be repaired usingservice brackets provided it meets the following criteria:•No damage to the headlight assembly•Sealing of the headlight lens and headlight housingis maintained.These service brackets are available:1.Upper front bracket2.Upper rear bracket3.Lower bracketRefer to “Headlight Bracket Replacement” in the body repair manual for complete information. 123 Service Headlight BracketsSYSTEMS THAT MAY REQUIRE DEALER ASSISTANCE WITH AIMINGSome models may be equipped with one or more of the following systems that require aiming after collision repairs. Special tools are required to complete the aiming procedures. Contact a Honda dealer for assistance. LaneWatch™:LaneWatch uses a camera and the center display to help drivers recognize objects in the blind spot of the passenger side door mirror.The LaneWatch camera must be aimed after one or more of the following procedures are done: •LaneWatch camera removal or replacement•Door mirror removal or replacement•Door panel removal or replacement•Door panel body repairLaneWatch does not set DTCs. Troubleshooting and camera aimingare done using the navigation system or center display self-diagnostics.LaneWatch doesn’t use an indicator to inform the driver of a malfunction.Electrical Repair InformationELECTRICAL GROUND WIRE PROTECTION•Painting over electrical ground locations may causeelectrical systems, such as Vehicle Stability Assist(VSA), to malfunction and set DTCs that may bedifficult to diagnose.•Protect the ground wire and the ground wire mountinghole threads with a bolt or silicone plug when primingor painting.。
ASTM A743-2017 一般用耐腐蚀铬铁及镍铬铁合金铸件

NOTE 1—For alloy castings for severe corrosion-resistant service, reference should be made to Specification A744/A744M. For general heat-resistant alloy castings, reference should be made to Specification A297/A297M. For nickel alloy castings for corrosion-resistant service, reference should be made to Specification A494/A494M.
- 1、下载文档前请自行甄别文档内容的完整性,平台不提供额外的编辑、内容补充、找答案等附加服务。
- 2、"仅部分预览"的文档,不可在线预览部分如存在完整性等问题,可反馈申请退款(可完整预览的文档不适用该条件!)。
- 3、如文档侵犯您的权益,请联系客服反馈,我们会尽快为您处理(人工客服工作时间:9:00-18:30)。
– Effects of heat-straightening on the structural properties of
undamaged steel plates
BACKGROUND
•
Limited research has been conducted on the effects of heat straightening on the structural properties of damage-repaired steel
RESEARCH PLAN
Task 1 - State of Knowledge and Practice Task 2 - Experimental Investigations of the Effects of Multiple
Damage-Repair Cycles Task 3 - Analytical Investigations of the Damaged and Repaired Beams Task 4 - Develop Guidelines and Recommendations
RESEARCH PROBLEM STATEMENT
• •
Heat straightening can be very cost effective as compared to replacing portions of the steel bridge Occasionally, the same fascia beams of steel bridges are damaged and repaired multiple times in their service lives Limited research has been conducted on the effects single or multiple damage-heat straightening repairs on the structural properties, fracture toughness, and microstructure of typical bridge steels.
•
•
•
Guidelines for evaluating and replacing (if necessary) steel beams subjected to multiple damage-repairs are lacking.
Guidelines for evaluating the serviceability and load capacities of damaged and repaired steel beams are also lacking
– Avent et al. (2000a) experimentally determined the effects of a
single damage-heat straightening repair cycle on the structural properties of A36 steel plates
MULTIPLE HEAT STRAIGHTENING REPAIRS OF STEEL BEAM BRIDGES
PRESENTATION OUTLINE
• • • •
RESEACH PROBLEM STATEMENT BACKGROUND
GOAL, OBJECTIVES, AND SIGNIFICANCE
• • •
Heat straightening - cost-effective and efficient technique for repairing steel members subjected to damage (plastic deformations) Most frequently used to repair the steel fascia beams of bridge girders damaged by overheight trucks Heat is applied with an oxygen-fuel torch. Steel yields at elevated temperatures due to material expansion and external restraining forces
BACKGROUND
•
Prior research on heat straightening has included the following topics:
– Developing efficient heat straightening repair techniques – Experimental studies measuring the plastic rotations and
• • • •
RESEARCH SCHEDULE
CURRENT PROGRESS AND STATUS OF EACH TASK GROUP (ORGANIZED AS ABOVE)
WORK REMAINING, TIME TO COMPLETION
ACKNOM STATEMENT
•
•
Significant research has been conducted on the heat straightening repairs of steel bridges.
Most prior research has focused on development of empirical equations and guidelines for conducting effective heat straightening repairs in the field